Techno-Economic Assessment of a Chopped Feedstock Logistics Supply Chain for Corn Stover
- 1Idaho National Laboratory, Idaho Falls, ID, United States
- 2Harris Group, Seattle, WA, United States
Storing corn stover in wet, anaerobic conditions is an active management approach to reduce the risk of significant aerobic degradation and catastrophic loss due to fire. An estimated 50% of the corn stover available in the U.S. is too wet at the time of harvest to be stored safely in baled formats and is compatible with wet, anaerobic storage through ensiling. A logistics system based on field-chopping and particle size reduction early in the supply chain removes the dependency on field-drying of corn stover prior to baling, allows for an expanded harvest window, results in diminished size reduction requirements at the biorefinery, and is compatible with ensiling as a storage approach. The unit operations were defined for this chopped logistics system, which included field chopping, bulk transportation to a biorefinery site, on-site preprocessing to meet biorefinery size and ash specifications, industrial-scale storage through ensiling, and delivery of corn stover at a rate of 2,000 tonnes per day for ~50% of the year. The chopped system was compared to the conventional bale system for 30% moisture (wet basis) corn stover, a likely delivered moisture content for baled corn stover harvested wet. Techno-economic analysis showed that the chopped logistics system is cost competitive, costing only 10% more than the baled logistics system, meanwhile reducing the energy consumption by 48% and greenhouse gas release by 60%. In summary, a chopped logistics system utilizing on-site preprocessing and storage at a biorefinery gate is an economically viable approach to provide a stable source of corn stover for use when dry bales are not available, meanwhile reducing the risk of loss in long-term storage.
Introduction
Agricultural residues, such as corn stover, could potentially supply >180 million tonnes of biomass feedstock for bioenergy conversion by 2040 (Langholtz et al., 2016), resulting in the production of nearly 16 billion U.S. gallons of liquid transportation fuel for the United States based on recent yield estimates (Humbird et al., 2011). As with all agricultural products, seasonal harvest necessitates long-term storage in order to provide the emerging bioenergy industry with a continuous feedstock supply throughout the year. Presently, herbaceous feedstock supply logistics operations and associated models are centered around dry bales, with long-term storage existing as a field-side operation, in satellite storage facilities, or at a centralized storage facility at the biorefinery gate (Hess et al., 2009; Shah et al., 2017; Zandi Atashbar et al., 2017). The challenge with agricultural residues is that harvest conditions are optimized for the primary product, and thus there is less flexibility to control properties such as moisture content. In the case of corn stover, one of the primary agricultural residues available for bioenergy use, harvesting occurs at optimal moisture contents for the corn grain, generally <25% moisture (wet basis, wb), which corresponds to stover moisture contents about twice as wet as the grain and can range from 40 to 75% moisture (wb) (Pordesimo et al., 2004; Shinners and Binversie, 2007). During multi-pass corn stover harvest, the stover is allowed to dry in the field until 15–20% moisture (wb) is reached, followed by windrowing and baling (Darr and Shah, 2012); however, in-field drying is not possible in all climates and in all harvest years. A recent study by Oyedeji et al. calculated that only 37% of corn stover harvested in the U.S. is <20% moisture (wb) (Oyedeji et al., 2017). Likewise, the moisture content of corn stover residue was shown to vary significantly in the Midwestern U.S. Corn Belt over two harvest years. During a dry harvest year, the majority of harvested stover met the 20% moisture target; yet in the prior year, high grain moisture and wet field conditions resulted in stover baled and stored at moisture contents exceeding the 20% target (Kenney et al., 2013b).
In situations where field drying is not sufficient for meeting the moisture target for baling, the resulting high-moisture bales can suffer dry matter losses ranging from 10 to 30% (Shah et al., 2011; Smith et al., 2013; Wendt et al., 2014). Aerobic microbial degradation by bacteria, yeast, and fungi consumes valuable carbohydrates, leaving behind material enriched in non-fermentable biomass components such as lignin and ash. Bales also are at risk of significant microbial degradation and associated losses if they get wet during storage (Kenney et al., 2013b; Smith et al., 2013). Sahoo and Mani identified significant cost implications when bales suffered elevated dry matter losses due to degradation (Sahoo and Mani, 2017). Bales degraded during storage also lose their physical structure, which results in increased physical material losses during handling and transportation. Twines in degraded square bales may become loose and often are not cut in bale de-stringers, and twines can cause fires in grinders if they are not removed prior to size reduction operations. Another significant issue associated with dry bales is the fire risk during storage and preprocessing, as the bales are a large source of combustible material. Storage fires may be caused naturally, by lightning strikes or wild-fires, or by human activities such as sparks from adjacent mowing, welding, off-road vehicle activity, or arson. Increased moisture in corn plants also relates negatively to grinding performance, resulting in reduced throughput and increased energy consumption in hammer-mills (Probst et al., 2013; Cao and Rosentrater, 2015). Drying between first and second stage hammer-milling is assumed as a requirement for maintaining operational efficiency in recent designs for preprocessing biomass (Kenney et al., 2013a), yet this results in significant cost implications (Yancey et al., 2013).
While wet climates are more commonly associated with the Corn Belt and northeastern U.S., moisture management in corn stover is also a consideration in southern geographical locations as well, specifically where double-cropping is available to farmers. An example is winter wheat in Kansas, where it is advantageous to harvest the corn crop early in the season and subsequently remove the stover from the field as soon after harvest as possible to facilitate planting the winter crop (Heggenstaller et al., 2008). Current estimates of the Billion Tons of bio-based resources available for conversion to biofuels neglect the influence of double-cropping, and enabling this practice could increase not only resources for bioenergy but for human consumption as well.
Wet anaerobic storage (i.e., ensiling) is an alternative to dry bale storage. Wet storage is one of the lowest risk and most potentially flexible biomass storage options available. It accommodates preprocessing early in the supply chain through forage chopping, utilizes low cost but scalable storage facilities, preserves biomass with minimal losses over time, and can accommodate wet or dry biomass (water can be added on site if needed). Ensiling effectively preserves biomass through storage conditions that limit oxygen availability, which encourages lactic acid bacteria to ferment soluble sugars into organic acids; the resulting low pH environment further preserves biomass from microbial degradation during storage (McDonald et al., 1991). Wet anaerobic storage can occur in a range of different formats including silage bags, bunkers, and drive-over piles, which provides flexibility for the end-user. Common among these storage options is oxygen limitation during construction, such as packaging the chopped biomass into plastic silage bags or by compacting with a tractor during construction of a drive-over pile or bunker. Centralized wet storage at a biorefinery gate is an additional storage option that has received little attention but is common in the pulp and paper industry as well as in the case of sugarcane bagasse that is used by the sugarcane industry to heat boilers.
Wet-based systems utilizing field chopping for particle size reduction and ensiling for stable storage have been evaluated for corn stover (Shinners et al., 2011), sorghum (Henk and Linden, 1996; Shinners and Binversie, 2003; Williams and Shinners, 2012), and grasses (Oleskowicz-Popiel et al., 2011) destined for bioenergy use. However, techno-economic assessments on fully wet, bulk logistics systems for corn stover are limited to a handful of studies (Turhollow and Sokhansanj, 2007; Cook and Shinners, 2011), and none of these studies assess centralized storage at the biorefinery gate. The primary drawback of chopped logistics systems is that the transportation costs increase compared to bale systems, as trucks reach the maximum allowable load weights before volumetric capacity has been reached due presence of water, such that long distance transportation is generally thought to be cost prohibitive. However, chopped, wet logistics systems offer multiple advantages over bale systems primarily due to the fact that they have consistently and successfully demonstrated biomass preservation of >95% over 6–12 months (Shinners et al., 2003, 2011) compared to the 10–30% seen in aerobic systems (Smith et al., 2013; Emery and Mosier, 2014; Wendt et al., 2014, 2018). Wet storage systems also reduce the fire risk relative to dry bales in storage and preprocessing. Storage of high-moisture materials result in a product that is more difficult to ignite, either accidentally, or intentionally. Centralized wet storage allows for greater access, control and restriction of operational activities that increase fire risks. Additionally, chopped biomass handling eliminates bale twine related issues, including failed cuts, reducing the risk of grinder fires.
This research defines an approach for managing the >50% of corn stover that Oyedeji et al (Oyedeji et al., 2017) assert is too wet for stable storage in bales and can be problematic for existing preprocessing approaches for low-moisture bales. The chopped logistics system scenario provides the quantity of feedstock sufficient to satisfy the biorefinery demand (2,000 dry tonnes of biomass per day) to the throat of the biochemical reactor. The chopped system was compared to a bale logistics system that utilizes higher moisture content bales, 30% wb, which require drying to 20% to maintain efficient preprocessing throughput. The existing low-moisture dry bale infrastructure was assumed to be utilized for bales that can be harvested later in the year, stored field-side at low moisture contents and with low corresponding dry matter losses, and delivered to the biorefinery at 20% moisture (wb). Laboratory- and field-based storage studies, described in Wendt et al. (Wendt et al., 2018), were used to characterize the performance of the industrial-scale ensiling storage and to inform the final design and associated techno-economic analysis of the chopped feedstock logistics systems. Costs, energy consumption, greenhouse gas emissions, and water consumption were evaluated for the chopped system in comparison to the 30% moisture bale logistics system to estimate the full economic and environmental impact of the described approach.
Methods
Biomass Supply Scenarios
In this study, a hybrid feedstock supply chain scenario was assumed where approximately half of harvested corn stover is compatible with stable storage in bales (<20% moisture, wb). The remaining half of the corn stover is not able to be field-dried to 20% moisture (wb) and assumed to be delivered to the biorefinery at 30% moisture (wb) bales, as reported in Cook et al. (Cook and Shinners, 2011). Alternatively, the chopped logistics system is used for the high-moisture fraction of corn stover. The chopped logistics system design includes infrastructure to store 200,000 dry tonnes at the biorefinery gate (delivers 188,500 tonnes after 5% dry matter loss) in order to maintain consistency with previously reported costs for large, scale corn stover storage piles (Turhollow and Sokhansanj, 2007). Additional feedstock would also be brought into the biorefinery during the harvest season to supply the bioreactor with freshly-harvested biomass during the week (131,429 tonnes) and during weekends (52,571 tonnes). Tonnages are presented in Table 1. Annual biorefinery demand to supply 2,000 tonnes (2,205 U.S. tons) per day at 96% uptime is 701,254 tonnes (773,000 U.S. tons) (Humbird et al., 2011).
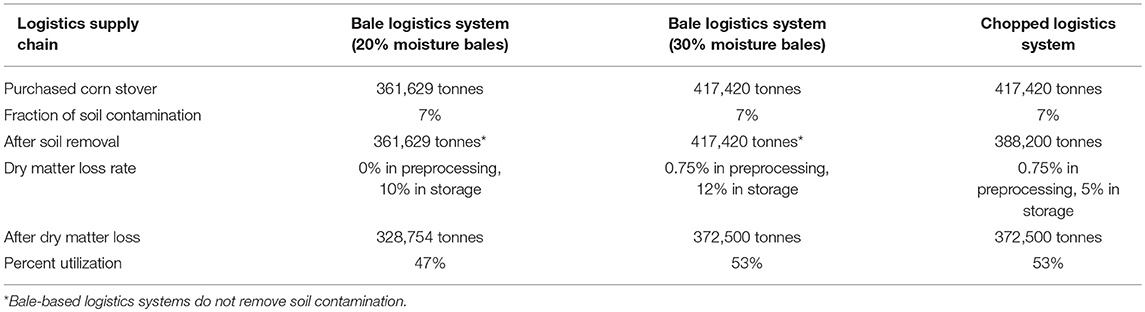
Table 1. Annual tonnages required to supply a biorefinery with 2,000 dry tonnes corn stover per day.
Logistics Supply Chain Modeling
Both bale logistics scenarios are based on the parameters described in Jacobson et al. (Jacobson et al., 2014) for three-pass harvesting systems to deliver 2,000 dry tonnes of corn stover to the throat of a biochemical reactor per day with the exception that pelleting is omitted. Following the grain harvest, a flail shredder pulled by a tractor is used for initial stover harvesting and collects the material into a windrow, and then a baler collects the material from the windrow into bales. Feedstock yield is assumed at 2.7 tonnes/hectare with resulting moisture content assumed at either 20 or 30% (wb). Bales are stored field-side in tarped stacks, and an assumed 10 or 12% dry matter loss occurs during the year of storage for 20% moisture (Hartley et al., 2015) and 30% moisture bales (Vadas and Digman, 2013), respectively. Bales are transported an average of 82 km using flatbed trucks to a preprocessing facility at the biorefinery gate. The bales are stored field-side, and therefore transportation operations occur year round. Transportation and handling costs include all processes involved in the movement of material from multiple local locations to the biorefinery gate and include processes such as loading, trucking, rail transport, and unloading and conveyance. A two-stage hammer mill system is used to reduce particle size in order to meet reactor in-feed size requirements, with a rotary dryer used for wet bales to reduce moisture content from 30 to 20% (wb) between first and second stage grinding. This is accomplished in order to maintain operating efficiency in the second stage grinder (Kenney et al., 2013a).
The chopped logistics system was designed such that the corn stover is transported to the centralized facility at the biorefinery gate during the annual 92 day harvest period at a rate sufficient to both provide continuous feed to the biochemical reactor as well as construct the wet storage piles. Harvesting occurs over a 92 day period in the fall season with operations occurring 5 days per week and 16 h per day, and stover moisture is assumed to be 45% (wb) due to the extension of the harvesting window earlier in the season prior to dry down of the corn stover. Harvesting is identical to the baled logistic system up to the point of baling, which is replaced by collection using a forage harvester with a chopping head. The forage harvester is tended by high-dump wagons pulled by tractors, which are used to transport and load the chopped material into waiting semi-trucks. Semi-trucks pulling open top possum belly trailers are used to transport the corn stover to the centralized preprocessing and storage facility co-located with the biorefinery. As in the baled logistics case, a yield of 2.7 tonnes/hectare and an average draw radius of 82 km are assumed. A comparison of the baled and chopped logistics systems is provided in Table 2.
Centralized Wet, Bulk Operations for the Chopped Logistics System
The unit operations in the centralized wet storage design include receiving, screening and shredding, storage pile formation and reclaiming, and delivery to the reactor throat (Figure 1), and general design parameters are presented in Table 3. The reactor feed requirements include up to 50% moisture content, a particle size of <2.54 cm (1 inch), and 5% or less structural ash. The centralized operations necessary to provide 2,000 dry tonnes per day of as-harvested biomass feedstock while simultaneously forming a 200,000 dry tonnes storage pile for later utilization were determined through development of a mass balance of material flows through the unit operations. All proposed unit operations are designed to include 20% surge capacity. Surge capacity for providing a continuous biorefinery feed stream is achieved through the use of day piles (interruptions of 8 h or less in the receiving operations) and reclaiming material from the ensiled biomass storage pile (interruptions of >8 h in the receiving operations), as described in the following paragraph. A listing of all equipment quantities, capacities, power requirements, and costs are presented in Table S1.
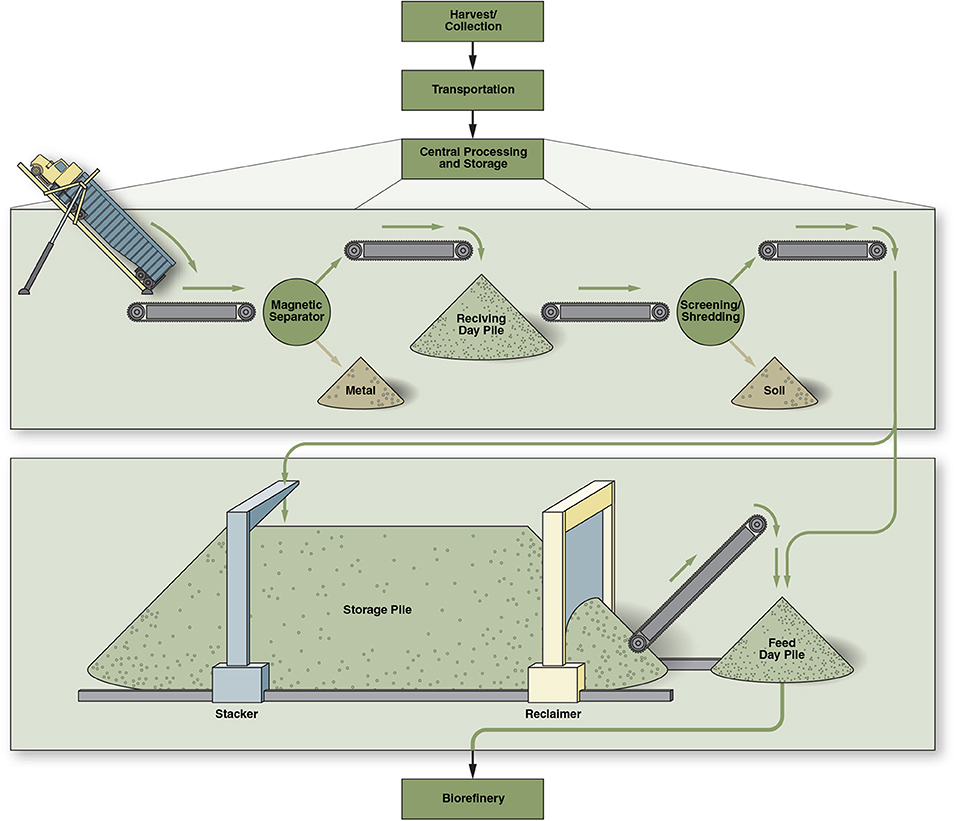
Figure 1. Centralized processing and storage operations in the chopped feedstock logistics supply system.
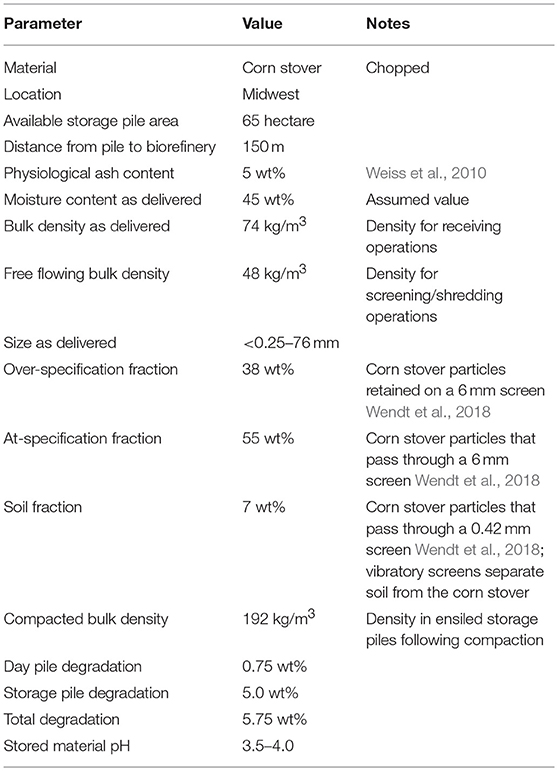
Table 3. General design parameters for the preprocessing & storage operations of the chopped logistics system.
Incoming trucks enter past one of four gatehouses located at separate entry points to reduce traffic congestion, each gatehouse equipped with inbound and outbound electronic scales. Corn stover is emptied via truck tippers into receiving hoppers. Stover is then conveyed through a magnetic separator and delivered to one of two day piles that enables 24 h utilization of downstream equipment given the 16 h receiving period. The circular day piles are formed by stackers and recovered with screw reclaimers. Losses of 0.75% are assumed in the day piles due to biological degradation, as measured in previous studies of high-moisture corn stover stored aerobically (Wendt et al., 2014). Receiving and day pile construction design parameters are summarized in Table 4.
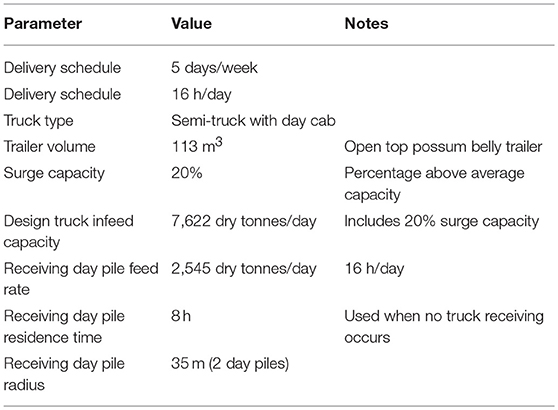
Table 4. Truck receiving/day pile design parameters for preprocessing & storage operations of the chopped logistics system.
Eight multi-stage screening processes are operated in parallel. Each multi-stage screening process uses first-stage disc screening to separate the oversize fraction from the fraction that meets biorefinery size specification; the oversized fraction is subject to additional size reduction via shredding prior to being combined with the at-specification fraction. Soil is removed from the at-specification sized fraction via vibratory screening. Screening and shredding design parameters are summarized in Table 5.
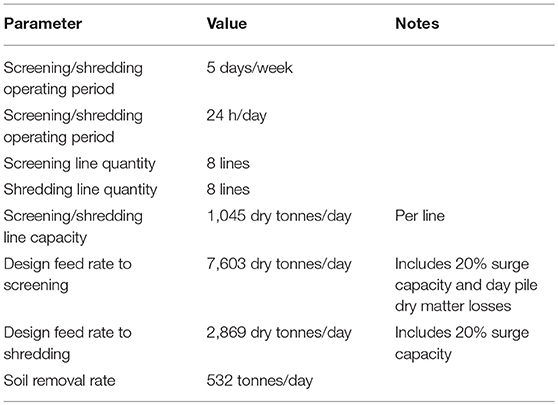
Table 5. Screening/shredding system design summary for preprocessing operations of the chopped logistics system.
Preprocessed, as-harvested stover that will directly be utilized by the biorefinery is conveyed to the feed day pile, which operates in a similar fashion to the receiving day pile by allowing for continuous corn stover being conveyed to the biorefinery at a rate of 2,000 dry tonnes/day. The remaining biomass is diverted to four storage piles with a total capacity of 200,000 dry tonnes. In addition to providing long-term storage, the storage piles provide biorefinery feed for time intervals in the harvest season when the receiving operations are offline for longer than 8 h (weekends and/or periods when weather or other factors prevent collection, transportation, or receiving operations from operating at full capacity). As such, a total of 255,800 dry tonnes are stored in the piles, and the first piles that are constructed are partially utilized and then filled again at the end of the harvest window. Storage piles are constructed using a pair of stacking conveyors, which move on rails and construct the entire length of one pile before beginning the second. Landfill compactors are continuously operated during pile construction to compress the stover as well as to mechanically exclude oxygen. Corn stover is removed from the storage pile using a scraper-style reclaimer mounted on rails. The reclaimer draws material off the pile in slices ~1 m in width as it moves down the length of the pile to limit the amount of pile that is exposed to oxygen prior to use and to provide some mixing of the reclaimed material. The reclaimed stover from the storage pile is conveyed to the feed day pile for further mixing and 24 h queuing prior to being conveyed to the biorefinery. Dry matter losses of 5% are assumed for the ensiling storage design, as reported in Wendt et al. (2018). Storage pile design parameters are summarized in Table 6.
The storage pile area is lined with ultra-high-molecular-weight (UHMW) polyethylene, a layer of sand and gravel to protect the liner, and a layer of sacrificial biomass to prevent the introduction of gravel into the reclaimed corn stover. The storage pile is designed with a water collection system to accommodate runoff due to rainfall. The surface under the piles is inclined to route drainage water into catch basins positioned along the centerline of the pile. The catch basins connect to a common drainage pipe that diverts water to the end of the pile and into a collection basin. Collection basin water may be used to adjust moisture content or to deliver additives, such as microbial inoculum or acids commonly used in ensiling, to the biomass during pile construction. Excess runoff water from the collection basins is stored onsite in UHMW-lined water collection ponds. It is assumed that excess recovered water from the storage systems can be field-applied to nearby farmland and that wastewater treatment is not required. Water management system design parameters are summarized in Table S3.
Techno-Economic Analysis
The Biomass Logistics Model (BLM) framework as described previously (Cafferty et al., 2013) (Lamers et al., 2015) was used to determine costs for harvest & collection and transportation in the chopped logistics systems as well as the corresponding costs for the baled logistics system (harvest & collection, field-side storage, transportation, preprocessing, and dockage). Costs in the BLM model are calculated using American Society of Agricultural and Biological Engineers (ASABE) standards, which provide guidelines on ownership costs, hours of equipment use, and salvage value. This approach assumes costs and returns consistent with agricultural economic practices, where purchased machinery is replaced roughly every 10 years and labor costs are based on salaried or seasonal employees leveraged across multiple crops. Grower payment was based on anticipated levels required to incentivize farmer participation (Hartley et al., 2015).
The centralized preprocessing & storage operations in the chopped logistics system is located at a biorefinery, and therefore they are costed in a manner similar to other DOE Bioenergy Technology Office design cases including Humbird et al. (Humbird et al., 2011), which use a discounted cash flow analysis based on estimates of capital and operating costs. Industrial-scale operations, such as the centralized preprocessing & storage facility described here, require installation of permanent infrastructure and ancillary equipment as well as indirect cost items such as engineering and permitting. Likewise, full-time supervision and maintenance staff are required in order to meet the throughput and capacity requirements of a centralized processing facility.
The centralized preprocessing & storage total installed cost (TIC) was determined by multiplying the total purchase cost for each equipment item by the selected installation factor (Table S1). Centralized preprocessing and storage total direct costs (TDC) include TIC plus other direct costs including a warehouse (4% of TIC) and site development (10% of TIC), along with design-specific costs for the storage pile area and water collection ponds. Indirect costs are calculated as a percentage of TDC using the parameters defined by Lamers et al. for estimating biomass preprocessing facility costs, including engineering (4%), construction expenses (4%), contractor's fee (2%), and contingency (5%) (Lamers et al., 2015). The fixed capital investment (FCI) is the sum of direct and indirect costs, which is combined with a 5% working capital cost to result in a total capital investment (TCI).
The centralized preprocessing & storage fixed operating costs include labor, land rent, maintenance and property insurance (Table S2). Labor and supervision personnel include a plant engineer, maintenance technicians, gatehouse attendants, shift operators, and loader drivers; all positions are either shared with the adjacent biochemical refinery or are seasonal hires. Labor and supervision costs were calculated using Bureau of Labor and Statistics rates (U.S. Department of Labor, 2015). A 90% labor burden charge is applied to the total salary cost to obtain the fully loaded salary cost. Land rent was assumed to be an annual rate of $70.54 per hectares for 65 hectares based on 2014 cash rents for non-irrigated land in Stevens County, KS (U.S Department of Agriculture, 2015). Maintenance costs were assumed at 3% of total installed equipment costs, and property insurance was assumed at 0.7% of Fixed Capital Investment as in Humbird et al. (2011).
Centralized preprocessing & storage variable operating costs include energy and mobile equipment operating costs (Table S2). Power requirements for each equipment item are listed in Table S1. Annual electricity usage for each equipment item was calculated by applying an operating load factor of 0.7 to the product of the equipment power rating and specified annual operating hours. Electricity costs for operation of the warehouse and other supporting infrastructure was also considered. Total electricity cost was calculated assuming an electricity price of $0.0665/kWh (U.S Energy Information Administration, 2016b). Mobile equipment operating costs include lease (Wyoming Machine Company, 2016), maintenance (Caterpillar Incorporated, 2012), repair (Jackson, 2010), and fuel (American Petroleum Industry, 2016; U.S Energy Information Administration, 2016a) for two landfill compactors used for 3 months a year for storage pile construction.
The centralized preprocessing & storage capital and operating costs were annualized using a discounted cash flow analysis, assuming identical economic parameters and discounting as described elsewhere (Humbird et al., 2011). This economic scenario assumes a 10% discount rate, 10% internal rate of return, and a 30 year plant life. Equity financing was assumed at 40% with a loan at 8% interest for 10 years assuming nth-plant designs. Depreciation was set at a 7-year schedule, and federal corporate taxes were assumed at 35%. Construction time was assumed at 3 years, with a 6 month start-up time assuming 50% production, 75% variable expenses, and 100% of fixed expenses. Total capital and operating costs are reported in Table S4. Feedstock sales to the conversion facility were considered income for the storage facility, and the feedstock pricing was varied to result in a net present value of zero. The total income was divided by the amount of corn stover purchased to calculate overall cost per dry tonne. The discounted cash flow analysis for the chopped logistics system is presented in Table S5 to demonstrate the application of this costing approach.
Sensitivity Analysis
A sensitivity analysis was performed in order to determine the key drivers for cost and energy consumption of the chopped logistics system. High impact inputs were determined by varying each input factor in isolation and measuring the change in feedstock cost ($/tonne) and energy consumption (MJ/tonne) in harvest and collection, transportation, and preprocessing and storage. Harvest yield was varied from 1.7 tonnes/hectare, a conservative estimate based on (Wendt et al., 2018), to 4.5 tonnes/hectare (Shah and Darr, 2016). Bulk density in transportation was varied from the 48 kg/m3, the density of 28 cm chopped corn stover (Shinners and Binversie, 2003), to the upper range of 96 kg/m3 for freshly cut forage (Wiersma and Holmes, 2000). Harvest window was varied from the most active harvest period for corn grain of 42 days (U.S. Department of U.S Department of Agriculture, 2010) to a 123 day window that prioritizes grain harvest over stover harvest (Lizotte and Savoie, 2011). Size reduction requirements were based on (Wendt et al., 2018) and were either doubled as a conservative estimate or eliminated based on reports that forage chopping eliminates the need for additional size reduction (Lisowski et al., 2017). Dry matter loss ranged from 2 to 10%, typical ranges for silage (Borreani et al., 2018). Diesel and electricity cost were varied by 25%.
Sustainability Metrics
Energy consumption, weighted by type (diesel, natural gas, and electricity) for each unit operation, was input into Argonne National Laboratory's Greenhouse Gases, Regulated Emissions, and Energy use in Transportation (GREETTM) model (Wang et al., 2015). GREET computes fossil, petroleum, and total energy use (including renewable energy in biomass), emissions of GHGs (CO2, CH4, and N2O), and emissions of six air pollutants: carbon monoxide (CO), volatile organic compounds (VOCs), nitrogen oxides (NOx), sulfur oxides (SOx), and particulate matter with a diameter below 10 micrometers (PM10) and below 2.5 micrometers (PM2.5). Biogenic emissions of CO, NOx, and N2O measured in ensiled corn stover were also included (Wendt et al., 2018). Energy consumption and GHG release was summarized on a dry tonne basis for each unit operation presented.
Results
Techno-Economic Analysis
In this study, a chopped feedstock logistics system for corn stover was defined that utilizes on-farm harvest and collection through forage chopping, transportation to a central facility located at a biorefinery gate, preprocessing to meet size and ash specifications, automated storage pile construction using industrial-scale ensiling to manage seasonal variability, and delivery of corn stover to a biorefinery reactor throat at a rate of 2,000 dry tonnes per day. This system was compared to a conventional baled system. Both logistics systems assume that a biorefinery will employ a third party aggregator to harvest and deliver the corn stover to the biorefinery gate in order to be consistent with recent models (Kemp and Stashwick, 2015; Shinners et al., 2017; Mertens et al., 2018). Operations within the biorefinery gate including preprocessing and the centralized wet storage system were considered add-ons to the biorefinery as described elsewhere (Humbird et al., 2011), with the chopped logistics systems employing additional supervisory staff and infrastructure due to the extensiveness of the automated design. This differs from the conventional bale system in that initial size reduction occurs prior to storage, the corn stover is stored on-site rather than farm-side or at satellite locations, and that the corn stover is stored anaerobically and at a moisture content that reduces the risk of fire and microbial degradation.
Costs for both the chopped logistics scenario and the 30% moisture bale system are compared in Table 7. A grower payment of $37.64/tonne was used in each scenario for consistency and contributed to nearly 30% of the total costs. For the chopped logistics system, harvest & collection and transportation costs totaled $44.68/tonne and contributed to 32% of the total costs. The centralized preprocessing & long-term storage costs for the chopped system were estimated at $46.88/tonne and 21% of the total costs, of which size reduction, ash removal, and handling constituted ~55% of the total and storage and queueing accounted for the remaining 45%. A quality dockage, described in the following paragraph, of $8.84/tonne cost was applied to this system. Total costs for the chopped logistics system were $137.86/tonne. In comparison, harvest, collection, field-side long-term storage, and transportation costs for the 30% moisture bale logistics system were estimated at $41.95/tonne or 30% of the total. Biorefinery operations including short-term storage, handling, and preprocessing were $27.47 or 22% of the total. Dockage in this system was $18.62/tonne. Total costs for the 30% moisture bale logistics system were $125.70/tonne, ~10% lower than the chopped system.
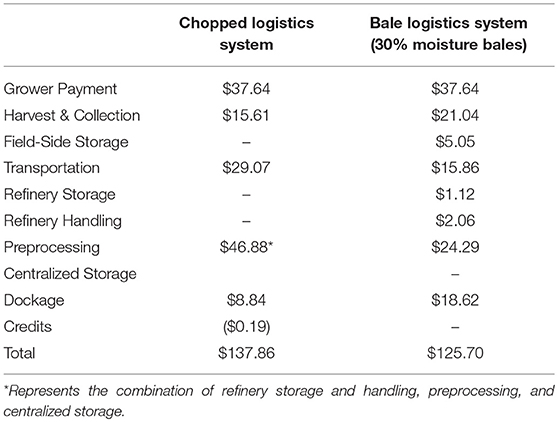
Table 7. Comparison of costs in chopped and baled logistics systems (2015 US dollars per dry tonne).
Dockage cost is incurred in each logistics system in order to account for losses in the feedstock supply chain, primarily due to the displacement of biomass by contaminating soil and the loss of material due degradation in long-term storage. The ash specification at the biochemical refinery is 4.9% (Humbird et al., 2011) which is based on the physiological content of ash in corn stover (Weiss et al., 2010). Dockages account for both ash disposal costs as well as the purchase of additional feedstock to meet tonnage targets at the biorefinery. In this study, the chopped logistics system incurred a total dockage of $8.84/tonne, whereas dockage in the bale system was $18.62/tonne. This difference is related to the higher ash content and higher degradation rate in storage for the 30% moisture bale system. Ash contents of 12% are assumed for multi-pass corn stover bales delivered to the biorefinery gate (Jacobson et al., 2014), whereas the preprocessing operations in the chopped system actively remove this ash related to soil contamination. Dry matter loss of 12% is assumed during aerobic bale storage in the 30% moisture case (Jacobson et al., 2014). However, dry matter loss is reduced to 5% in the chopped logistics system due to the use of ensiling as a storage approach (Wendt et al., 2018), further reducing total dockage in this system.
Sustainability Metrics
Energy consumption and GHG release were determined for the unit operations in each logistics system (Table 8). The energy consumption data indicate that the chopped harvest and collection operations are more energy intensive compared to the baled system because they involve in-field size reduction through forage chopping. Likewise, energy consumption and GHG release for transportation of the chopped biomass increases significantly compared to the bale system due to the lower bulk density of the chopped biomass compared to bales. However, preprocessing energy requirements account for the majority of the energy consumed in the bale logistics system. Of the 1670 MJ/tonne required in preprocessing for the bale system, roughly 80% are required for drying from 30 to 20% moisture (Table S6, Supplementary Information); the dryer energy consumption alone is greater than the total energy usage in the chopped logistics system. Overall, the energy consumption of the chopped logistics system is 48% less than that of the energy consumption of the 30% moisture bale logistics system. The reduction in overall energy consumption also leads to a reduction in total of GHG emissions of over 60% for the chopped system, as shown in Table 8.
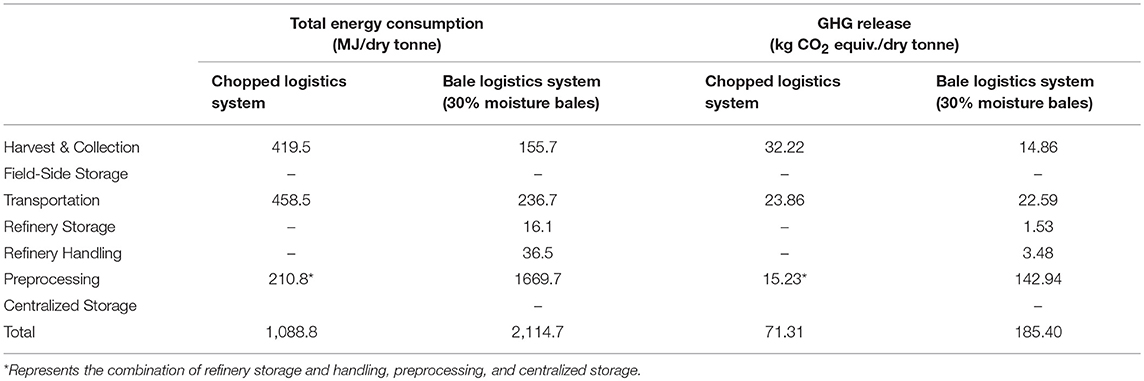
Table 8. Estimated energy consumption and GHG release for corn stover in the chopped and baled logistics systems.
Gasses released during storage are a concern from a GHG emission perspective, as they can potentially be significant GHG sources or air pollutants (Emery and Mosier, 2012, 2014). Storage studies performed in laboratory reactors provided gas release data for the storage conditions used in the chopped and bale logistics systems (Jacobson et al., 2014; Wendt et al., 2018). Biogenic storage gasses (CO, NOx) detected in laboratory experiments were added to the total GHG emissions but did not have a significant impact on overall GHG release. On the other hand, CO2 released during storage as a result of microbial degradation can be significant, especially in the case of high-moisture aerobic storage. Biogenic CO2 released during storage due to degradation would have ultimately been emitted during fuel combustion, and therefore it is not included in the overall GHG emissions listed in Table 8. However, carbon utilization efficiency is highly reduced in the aerobic bale storage case compared to the chopped system which utilizes ensiling to prevent excessive degradation. The chopped system resulted in 6.5 kg CO2 released per dry tonne biomass while the bale logistics system released 159.7 kg CO2 per dry tonne biomass assuming aerobic, field-side storage of corn stover bales at 30% moisture with 12% dry matter loss. In summary, aerobic storage in 30% moisture bales releases 25 times more biogenic CO2 to the atmosphere compared to ensiling, resulting in poor carbon utilization and ultimately lower fuel yield.
Biochemical conversion of cellulosic biomass to fuels is a water intensive process considering that 30% solids content, or 70% moisture content (wb), is desired in dilute acid pretreatment (Humbird et al., 2011), yet incoming dry stored biomass is ideally <20% moisture (wb) in tarped, stacked bales (Darr and Shah, 2012). One advantage of the chopped logistics system is that the water is maintained within the biomass and therefore can reduce the water burden at the pretreatment reactor. Assuming 50% moisture content (wb) at the time of conversion, the chopped logistics scenario requires an additional 1,330 L of water per dry tonne biomass. In comparison, the baled logistics system would require 2,080 L per dry tonne biomass to increase moisture content from 20% (wb) to 30% solids in a pretreatment reactor. Overall, the chopped systems require less water input at the biorefinery gate, resulting in a small cost reduction. Assuming the reduction of water consumption necessary at the reactor throat for the chopped logistics systems compared to the baled system and a water cost of $0.22/m3 (Peters and Timmerhaus, 2003), a credit of $0.19/tonne of corn stover was applied to the chopped logistics system as indicated in Table 7.
Sensitivity Analysis
A sensitivity analysis was performed in which yield, harvest window, bulk density in transportation, particle size reduction at the biorefinery gate, dry matter loss, electricity cost, and diesel fuel price were varied in isolation. Changes in cost and energy consumption in harvest & collection, transportation, and preprocessing & storage operations in the chopped logistics system were assessed as a result of changes to these variables (Figure 2). The largest reductions in the total feedstock cost resulted from eliminating particle size reduction beyond forage harvesting ($7.80/tonne total feedstock cost decrease). The second largest cost driver is harvest yield, with significant cost fluctuations observed with an increase in the yield from 2.7 to 4.5 tonnes per hectare ($7.74/tonne decrease) or a decrease in the yield to 1.7 tonnes per hectare ($9.78/tonne increase). Bulk density during transportation was another primary cost driver; decreased costs were predicted by increasing bulk density from 73.7 to 96 kg/m3 ($6.78/tonne decrease). Likewise, transportation costs could increase when bulk density was decreased from 73.7 to 48 kg/m3 ($15.47/tonne increase). The influence of harvest yield and bulk density on total feedstock costs of the chopped system are consistent with reported cost drivers for baled corn stover (Shah and Darr, 2016).
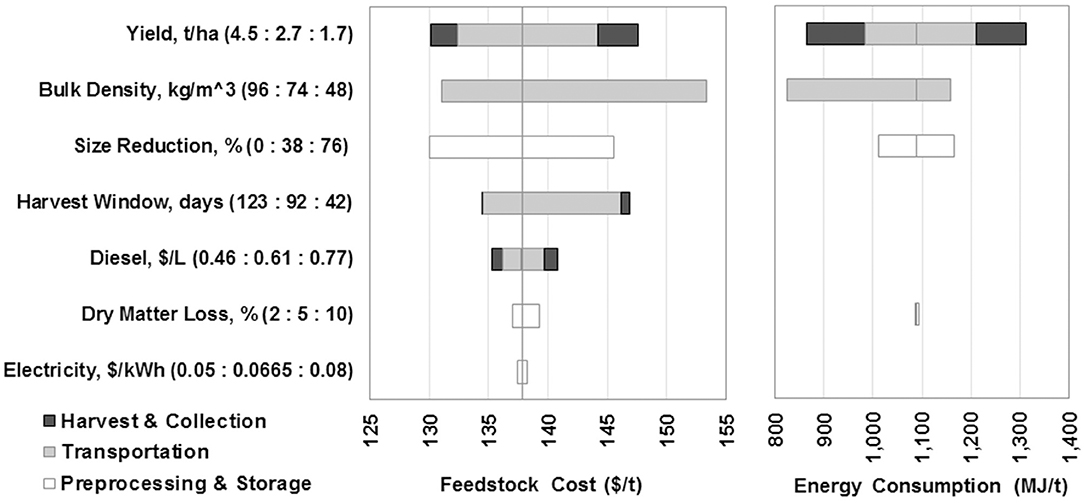
Figure 2. Sensitivity analysis of feedstock cost and energy consumption to changes in yield, bulk density, size reduction necessary before conversion, harvest window, diesel fuel cost, dry matter loss in storage, and electricity cost in the chopped logistics system. Values in parenthesis represent the minimum, baseline, and maximum assumptions. Costs reported in 2015$.
The duration of the harvest window in harvest & collection impacted costs significantly, with a moderate cost decrease when the window was increased from 92 to 123 days ($3.45/tonne decrease) and a drastic increase experienced with the decrease in the window from 92 to 42 days ($8.98/tonne increase). Reported harvest windows for corn grain vary widely by state (U.S Department of Agriculture, 2010; Oyedeji et al., 2017) and the corn stover harvest expands that window based on the reliance of field drying in windrows; one advantage of the proposed chopped logistics system is that the harvest window can be expanded due to the fact that it is not reliant on field drying of the stover (Shinners and Binversie, 2003; Cook et al., 2014). The remaining variables presented in the sensitivity analysis, including diesel and electricity price as well as dry matter loss in storage, resulted in fluctuations of <$3/tonne. Overall, the results of the sensitivity analysis indicate that operations in harvesting and transportation operations have the greatest impact in cost fluctuations of the proposed chopped logistics system. Similarly, harvest yield and bulk density in transportation were the primary drivers in reducing energy consumption.
Discussion
Chopped logistics systems offer many benefits for the bioenergy industry, primarily the removal of dependence on field-drying to provide stable, low moisture storage conditions in bales. A recent analysis assessed the practicality of corn stover to be field-dried to a moisture content of 20% and determined that this is possible an average of only 36% of the time in the top 10 corn stover producing states, ranging from 16 to 67% depending on the state (Oyedeji et al., 2017). Bales with moisture content >20% are subject to increased dry matter loss during storage and require supplemental drying for the preprocessing grinding operations to maintain operating efficiency. The chopped logistics system does not require the feedstock to be dried prior to the preprocessing operations and can consistently reduce dry matter losses in long term storage by utilizing ensiling. Therefore, the chopped logistics system was evaluated for its overall competitiveness for providing the biorefinery feed that the bale logistics system would be unable to provide unless moisture contents of 20% or less could be achieved at the time of harvest.
The cost for the chopped logistics system described in this study was 10% higher than a bale-based logistics system with a moisture content of 30%. A number of differences are apparent when comparing the unit operation specific costs of each logistics system. Harvest and collection costs were reduced for the chopped system because of increased harvest efficiency for forage chopping compared to baling, which is consistent with previous reports (Shinners and Binversie, 2003; Cook and Shinners, 2011). However, transportation costs for the chopped system are almost double compared to the bale system due to the reduction in bulk density during truck transport. The dockage cost in the bale scenario is over twice that of the chopped system primarily due to the cost of procuring replacement feedstock either displaced by contaminating soil or lost during storage. While both systems experience a dockage for disposal of ash, a positive attribute of the chopped system is that it includes active ash removal during preprocessing such that the biorefinery receives a lower ash feedstock. Removing the ash prior to preprocessing and conversion has unquantified benefits in terms of reduction of abrasion and it also increases the amount of organic material that can enter the biorefinery, ultimately increasing conversion yield. Of similar importance, the reduced water demand in the chopped system has positive environmental implications due to the reduced water consumption at the biorefinery, and water shortages are predicted in at least a portion of the majority of U.S. States within the next 10 years (U.S Government Accountability Office, 2014).
The assumption in the 30% moisture bale logistics system that drying was necessary to maintain the efficiency and biomass throughput in the second stage grinding operation is consistent with previously reported approaches for managing moisture in preprocessing (Hess et al., 2009; Kenney et al., 2013a). Drying increases costs of this system by $9.10/tonne compared to a 20% moisture system with no drying (Table S6, Supplementary Information), but it is necessary for maintaining efficiency in the two-stage hammer milling operations. Hammer milling operations are most effective with low moisture (<20%, wb) biomass because they use impact as a means to deconstruct biomass, and moisture increases the shear strength of the biomass such that it does not break upon impact (Himmel et al., 1985). Although hammer milling may not be the most effective approach for size reducing high moisture baled corn stover, it has been used in the first-of-a-kind cellulosic biorefineries and thus was used as the baseline in this analysis. Rotary shear milling is an alternative size reduction approach that is less affected by moisture and could be substituted for the second stage hammer mill in the 30% moisture bale scenario, which would eliminate the rotary dryer in the high-moisture bale scenario and result in a combined cost savings of $9.24/tonne. However, rotary shearer mills are not yet commonly utilized at the commercial scale for biomass deconstruction and were therefore not considered in this analysis.
The centralized storage operation in the described chopped logistics system is associated with significantly higher storage and handling costs than the field-side storage operation in the 30% moisture bale scenario as well as in previously described chopped logistics systems utilizing on-farm storage through ensiling (Shinners and Binversie, 2003; Cook and Shinners, 2011; Vadas and Digman, 2013). The primary factor for increased cost in the described chopped logistics system is the high infrastructure costs of the automated pile formation and reclaiming equipment (> $30,000,000 installed, Table S1). Significant cost savings could be achieved through less expensive automated designs or by utilizing the storage pile for multiple biomass sources harvested in different seasons. Commercially available front end loaders and silage facers could replace the automated design in this system, yet the reduction in capital costs would be replaced with higher operating costs. A similar chopped logistics system has been reported for corn stover stored in a 25,000 tonne pile, with identical unit operations for harvest, collection, transportation, and preprocessing of corn stover (Wendt et al., 2017). Manual storage pile formation and deconstruction was used in this prior study, which resulted in higher operating costs associated with labor and equipment rental but lower capital costs; final storage costs were reduced to $15.61/tonne compared to $21.10/tonne in the present study. Another contributing factor to the high cost of the chopped system are the costs associated with the centralized preprocessing and storage operation including site-development, a warehouse, and on-site water collection ponds, all of which are limited or eliminated with field-side, on-farm storage used in the bale scenario. The chopped system also requires additional land rent costs for the centralized operations; land rent costs vary widely across geographical region. This study assumes a conservative land rent cost for southwest Kansas; however, increasing the land rent cost to the average cost for non-irrigated land in Iowa ($570.8/hectare) (U.S Department of Agriculture, 2017) only increases the total costs of the chopped system by $0.10/tonne. Overall, a consistent, readily available feedstock source at the biorefinery gate reduces the risk that gaps in supply can occur, ultimately reducing risk, for which the cost implications have not yet been defined.
Chopped feedstocks logistics systems are widely used across the U.S, with an estimated 147 million U.S. tonnes of forage-chopped wet biomass harvested annually as animal feed (U.S Department of Agriculture, 2016), yet only a handful of chopped logistics systems have been reported for corn stover. Sensitivity analysis of the chopped logistics system presented in this study identified two primary variables in harvest and collection operations that would result in significant cost reductions: (1) increased harvest yield, and (2) meeting biorefinery size specifications through forage chopping. Harvesting yields range between 1.4 to 5.9 tonnes/hectare for corn stover depending on factors specific to a geographical region, such including harvesting approach, growth year, and geographical location (Sokhansanj et al., 2002). In this study, a conservative yield of 2.7 tonnes/hectare was assumed, and increasing yields would specifically impact the transportation in the chopped logistics system due to a reduced supply radius for the biorefinery. Likewise, increasing size reduction during harvest and the corresponding increase in bulk density during transportation are important cost drivers for chopped logistics systems (Turhollow and Sokhansanj, 2007). The majority of economic assessments for chopped, wet logistics systems assume that forage harvesting is capable of doing all the necessary size reduction required (Shinners and Binversie, 2003; Vadas and Digman, 2013) or that the cost will be less than $6/tonne (Cook and Shinners, 2011) (Turhollow and Sokhansanj, 2007). This study conservatively assumes size reduction at the biorefinery gate is necessary for ~40% of the biomass, and $7.80/tonne in cost reductions could be achieved by eliminating size reduction beyond forage chopping. Cook et al. suggest that costs for chopped logistics systems could be as low as $86-$113/tonne, which is achieved through a reduced grower payment, field-side storage in silage bags, and minimal preprocessing costs beyond forage chopping (Cook and Shinners, 2011). Overall, multiple opportunities exist for cost reductions in the chopped logistics system described in this study.
Although the chopped logistics system requires a price premium of 10% relative to 30% moisture bales, this system provides benefits that are less easily quantified in addition to the previously listed operational flexibility, energy use, and water utilization benefits. The proposed chopped logistics system is compatible with not only existing feedstock supply logistics operations and vendor recommended preprocessing and storage pile infrastructure, but also available conversion technologies, leading to a quick entry into the marketplace. Specifically, today's commercially-available forage choppers can harvest and concurrently size-reduce material in the field, and the chopped logistics system delivers a feedstock that is compatible with existing biochemical sugar conversion pathways and is on-spec with regard to size, reactivity, ash content, and tonnage. Furthermore, this system provides solutions to the material handling issues experienced at current commercial-scale cellulosic biorefineries, including a reduction in fire risk in storage and preprocessing, a reduction in fines generated during single-stage low moisture grinding, a narrow particle size distribution of delivered feedstock, and a reduction of soil contamination and fines production in the pretreatment reactor achieved through screening in preprocessing.
Conclusion
A chopped logistics system for processing the high-moisture content portion of a biorefinery's annual corn stover supply was designed and compared to a 30% moisture bale corn stover logistics operation. The chopped logistics system provides a flexible method for utilizing biomass with high moisture content from non-ideal harvesting or field conditions. The dry matter loss associated with ensiled biomass in storage is significantly reduced compared to that of high-moisture bales stored aerobically, resulting in more efficient carbon utilization. The use of a chopped feedstock logistics system in combination with a dry bale system can mitigate risks associated with harvest or weather conditions that preclude all biomass from being stored field-side under conditions that maintain moisture contents of ≤ 20%, where dry matter loss is limited. Additionally, storage using ensiling in the chopped logistics system can reliably limit the risks of losses from fires in storage and preprocessing operations.
The net costs to the throat of the reactor for the chopped logistics system were 10% greater than the corresponding 30% moisture bale logistics system. Harvest and collection costs were lower for the chopped system compared to baled corn stover, but transportation and preprocessing costs were significantly greater for the chopped system. Cost offsetting benefits of the chopped system include removal of the ash in preprocessing, reduction of the dockage associated with dry matter lost due to degradation in aerobic storage, and credits for offsetting water use required in pretreatment. Direct benefits of the chopped logistics system also include reduced energy consumption and GHG emissions relative to the dry bale system due to the elimination of drying in order manage moisture during size reduction. The centralized preprocessing & storage design for the chopped logistics design presented in this study describes a baseline on which cost and performance improvements can be measured against. The system is flexible such that any equipment piece can be substituted to describe newly developing approaches for handling, size reducing, and storing corn stover. Further research is warranted to adapt existing high-moisture forage harvest, collection, storage, and preprocessing operations to serve the requirements of emerging biorefineries.
Author Contributions
LW, JR, DS, JL, DH, and DW designed the wet, bulk logistics system. DH and WS designed the dry bale systems. WS, KK, and QN advised on the selection of the wet and dry logistics systems. DH, LW, and JM performed sustainability analysis. LW drafted the manuscript with contributions from all co-authors.
Conflict of Interest Statement
The authors declare that the research was conducted in the absence of any commercial or financial relationships that could be construed as a potential conflict of interest.
Acknowledgments
The research was supported by the U.S. Department of Energy (DOE), Office of Energy Efficiency and Renewable Energy (EERE), Bioenergy Technologies Office (BETO), under Award No. DE-AC07-05ID14517. The views expressed in the article do not necessarily represent the views of the U.S. Department of Energy or the United States Government.
The authors thank Thomas Robb and Kirk Spikes for their contributions to the wet logistics design scenario and Vicki Thompson for her review of the manuscript.
Supplementary Material
The Supplementary Material for this article can be found online at: https://www.frontiersin.org/articles/10.3389/fenrg.2018.00090/full#supplementary-material
References
American Petroleum Industry. (2016). Diesel Tax by State. Available online at: http://www.api.org/oil-and-natural-gas/consumer-information/motor-fuel-taxes/diesel-tax (Accessed June 15, 2016).
Borreani, G., Tabacco, E., Schmidt, R. J., Holmes, B. J., and Muck, R. E. (2018). Silage review: factors affecting dry matter and quality losses in silages. J. Dairy Sci. 101, 3952–3979. doi: 10.3168/jds.2017-13837
Cafferty, K. G., Muth, D. J., Jacobson, J. J., and Bryden, K. M. (2013). “Model based biomass system design of feedstock supply systems for bioenergy production,” in ASME International Design Engineering Technical Conference. (Portland, OR).
Cao, X., and Rosentrater, K. A. (2015). “Energy consumption of corn stover size reduction,” in 2015 ASABE Annual International Meeting. (St. Joseph, MI: ASABE).
Caterpillar Incorporated (2012). Caterpillar Performance Handbook, 42nd Edn. Deerfield, IL: Wheeler Machinery Co.
Cook, D. E., and Shinners, K. J. (2011). “Economics of alternative corn stover logistics systems,” in 2011 Louisville, Kentucky, August 7-10, 2011. (St. Joseph, MI: ASABE).
Cook, D. E., Shinners, K. J., Weimer, P. J., and Muck, R. E. (2014). High dry matter whole-plant corn as a biomass feedstock. Biomass Bioenergy 64, 230–236. doi: 10.1016/j.biombioe.2014.02.026
Darr, M. J., and Shah, A. J. (2012). Biomass storage: an update on industrial solutions for baled biomass feedstocks. Biofuels 3, 321–332. doi: 10.4155/bfs.12.23
Emery, I., and Mosier, N. (2014). Direct emission of methane and nitrous oxide from switchgrass and corn stover: implications for large-scale biomass storage. GCB Bioenergy 7, 865–876. doi: 10.1111/gcbb.12196
Emery, I. R., and Mosier, N. S. (2012). The impact of dry matter loss during herbaceous biomass storage on net greenhouse gas emissions from biofuels production. Biomass Bioenergy 39, 237–246. doi: 10.1016/j.biombioe.2012.01.004
Hartley, D., Searcy, E. M., Roni, M., and Bonner, I. J. (2015). Herbaceous Feedstock 2015 State of Technology. (Idaho Falls, ID: Idaho National Laboratory).
Heggenstaller, A. H., Anex, R. P., Liebman, M., Sundberg, D. N., and Gibson, L. R. (2008). Productivity and nutrient dynamics in bioenergy double-cropping systems. Agron. J. 100, 1740–1748. doi: 10.2134/agronj2008.0087
Henk, L. L., and Linden, J. C. (1996). Solid-state production of ethanol from sorghum. Appl. Biochem. Biotechnol. 57–58, 489–501. doi: 10.1007/BF02941729
Hess, J. R., Wright, C. T., Kenney, K. L., and Searcy, E. M. (2009). Uniform-Format Solid Feedstock Supply System: A Commodity-Scale Design to Produce an Infrastructure-Compatible Bulk Solid from Lignocellulosic Biomass-Section 4: Advanced Uniform-Format. INL Report No: INL/EXT-08-14752, Idaho National Laboratory, Idaho Falls, ID.
Himmel, M., Tucker, M., and Baker, J. (1985). Comminution of biomass: hammer and knife mills. Biotechnol. Bioeng. Symp. 15, 39–58.
Humbird, D., Davis, R., Tao, L., Kinchin, C., Hsu, D., Aden, A., et al. (2011). Process Design and Economics for Biochemical Conversion of Lignocellulosic Biomass to Ethanol. (Golden, CO: National Renewable Energy Laboratory).
Jackson, T. (2010). “Track loaders: multi-purpose machine with low lifetime costs,” in Equipment World. Available online at: http://www.equipmentworld.com/owning-and-operating-costs-9/ (Accessed September 15, 2016).
Jacobson, J., Roni, M., Lamers, P., and Cafferty, K. (2014). Biomass Feedstock and Conversion Supply System Design and Analysis. (Idaho Falls, ID: Idaho National Laboratory). doi: 10.2172/1169237
Kemp, L., and Stashwick, S. (2015). Cellulosic ethanol from Corn Stover: Can We Get It Right? Natural Resources Defense Council Report. Available online at: https://www.nrdc.org/sites/default/files/corn-stover-biofuel-report.pdf (Accessed August 2, 2018).
Kenney, K., Cafferty, K. G., Jacobson, J. J., Bonner, I. J., Gresham, G. L., Smith, W. A., et al. (2013a). Feedstock Supply System Design and Economics for Conversion of Lignocellulosic Biomass to Hydrocarbon Fuels: Conversion Pathway: Biological Conversion of Sugars to Hydrocarbons The 2017 Design Case. Idaho National Laboratory (INL).
Kenney, K. L., Smith, W. A., Gresham, G. L., and Westover, T. L. (2013b). Understanding biomass feedstock variability. Biofuels 4, 111–127. doi: 10.4155/bfs.12.83
Lamers, P., Roni, M. S., Tumuluru, J. S., Jacobson, J. J., Cafferty, K. G., Hansen, J. K., et al. (2015). Techno-economic analysis of decentralized biomass processing depots. Bioresour. Technol. 194, 205–213. doi: 10.1016/j.biortech.2015.07.009
Langholtz, M. H., Stokes, B. J., and Eaton, L. M. (2016). 2016 U.S. Billion-Ton Report: Advancing Domestic Resources for a Thriving Bioeconomy. Volume 1: Economic Availability of Feedstocks. (Oak Ridge, TN: Oak Ridge National Laboratory).
Lisowski, A., Bulinski, J., Gach, S., Klonowski, J., Sypuła, M., Chlebowski, J., et al. (2017). Biomass harvested at two energy plant growth phases for biogas production. Ind. Crops Prod. 105, 10–23. doi: 10.1016/j.indcrop.2017.04.058
Lizotte, P. L., and Savoie, P. (2011). Spring harvest of corn stover. Appl. Eng. Agric. 27, 697–703. doi: 10.13031/2013.39567
McDonald, P., Henderson, A. R., and Heron, S. J. E. (1991). The Biochemistry of Silage. Aberytstwyth: Cambrian Printers Ltd.
Mertens, A., Van Meensel, J., Willem, L., Lauwers, L., and Buysse, J. (2018). Ensuring continuous feedstock supply in agricultural residue value chains: a complex interplay of five influencing factors. Biomass Bioenergy 109, 209–220. doi: 10.1016/j.biombioe.2017.12.024
Oleskowicz-Popiel, P., Thomsen, A. B., and Schmidt, J. E. (2011). Ensiling–Wet-storage method for lignocellulosic biomass for bioethanol production. Biomass Bioenergy 35, 2087–2092. doi: 10.1016/j.biombioe.2011.02.003
Oyedeji, O., Sokhansanj, S., and Webb, E. (2017). Spatial analysis of stover moisture content during harvest season in the U.S. Trans ASABE 60, 1015–1023. doi: 10.13031/trans.11898
Peters, MS., and Timmerhaus, KD. (2003). Plant Design and Economics for Chemical Engineers. New York, NY: McGraw-Hill.
Pordesimo, L. O., Sokhansanj, S., and Edens, W. C. (2004). Moisture and yield of corn stover fractions before and after grain maturity. Trans ASABE 47, 1597–1603. doi: 10.13031/2013.17589
Probst, K. V., Kingsly Ambrose, R. P., Pinto, R. L., Bali, R., Krishnakumar, P., and Ileleji, K. E. (2013). The effect of moisture content on the grinding performance of corn and corncobs by hammermilling. Trans. ASABE 56, 1025–1033. doi: 10.13031/trans.56.9996
Sahoo, K., and Mani, S. (2017). Techno-economic assessment of biomass bales storage systems for a large-scale biorefinery. Biofuels Bioproducts Biorefining 11, 417–429. doi: 10.1002/bbb.1751
Shah, A., and Darr, M. (2016). A techno-economic analysis of the corn stover feedstock supply system for cellulosic biorefineries. Biofuels Bioproducts Biorefining 10, 542–559. doi: 10.1002/bbb.1657
Shah, A., Darr, M., Khanal, S., and Lal, R. (2017). A techno-environmental overview of a corn stover biomass feedstock supply chain for cellulosic biorefineries. Biofuels 8, 59–69. doi: 10.1080/17597269.2016.1200864
Shah, A., Darr, M. J., Webster, K., and Hoffman, C. (2011). Outdoor storage characteristics of single-pass large square corn stover bales in Iowa. Energies 4, 1687–1695. doi: 10.3390/en4101687
Shinners, K. J., and Binversie, B. N. (2003). “Whole-plant corn harvesting for biomass: comparison of single-pass and multiple-pass harvest systems,” in 2003 ASAE Annual Meeting. (Las Vegas, NV: American Society of Agricultural and Biological Engineers).
Shinners, K. J., and Binversie, B. N. (2007). Fractional yield and moisture of corn stover biomass produced in the Northern US Corn Belt. Biomass Bioenergy 31, 576–584. doi: 10.1016/j.biombioe.2007.02.002
Shinners, K. J., Binversie, B. N., and Savoie, P. (2003). “Harvest and storage of wet and dry corn stover as a biomass feedstock. ASAE Paper No. 03-6088,” in 2003 ASAE Annual Meeting. (Las Vegas, NV: American Society of Agricultural and Biological Engineers).
Shinners, K. J., Sabrowsky, B. K., Studer, C. L., and Nicholson, R. L. (2017). Switchgrass harvest progression in the North-Central USA. Bioenergy Res. 10, 613–625. doi: 10.1007/s12155-017-9848-1
Shinners, K. J., Wepner, A. D., Muck, R. E., and Weimer, P. J. (2011). Aerobic and anaerobic storage of single-pass, chopped corn stover. Bioenerg. Res. 4, 61–75. doi: 10.1007/s12155-010-9101-7
Smith, W. A., Bonner, I. J., Kenney, K. L., and Wendt, L. M. (2013). Practical considerations of moisture in baled biomass feedstocks. Biofuels 4, 95–110. doi: 10.4155/bfs.12.74
Sokhansanj, S., Turhollow, A., Cushman, J., and Cundiff, J. (2002). Engineering aspects of collecting corn stover for bioenergy. Biomass Bioenergy 23, 347–355. doi: 10.1016/S0961-9534(02)00063-6
Turhollow, A. F., and Sokhansanj, S. (2007). Costs of harvesting, storing in a large pile, and transporting corn stover in a wet form. Appl. Eng. Agric. 23, 439–448. doi: 10.13031/2013.23478
U.S Department of Agriculture National Agricultural Statistics Service. (2010). Field Crops Usual Planting and Harvesting Dates. Available online at: http://usda.mannlib.cornell.edu/usda/current/planting/planting-10-29-2010.pdf (Accessed Ausust 8, 2018).
U.S Department of Agriculture National Agricultural Statistics Service. (2016). Agricultural Statistics 2016. Available online at: https://www.nass.usda.gov/Publications/Ag_Statistics/2016/Complete%20Ag%20Stats%202016.pdf (Accessed October 10, 2017).
U.S Department of Agriculture National Agricultural Statistics Service. (2017). Iowa Ag News-Country Cash Rent. Available online at: https://www.nass.usda.gov/Statistics_by_State/Iowa/Publications/County_Estimates/2017/IA_County_Cash_Rent_09_2017.pdf (Accessed August 8, 2018).
U.S Department of Agriculture National Agricultural Statistics Service, Kansas Field Office. (2015). County Estimates. Available online at: http://www.nass.usda.gov/Statistics_by_State/Kansas/index.asp (Accessed August 26, 2015).
U.S Department of Labor Bureau of Labor Statistics. (2015). May 2015 State Occupational Emplyoment and Wage Estimates, Kansas. Available online at: http://www.bls.gov/oes/current/oes_ks.htm (Accessed September 15, 2016).
U.S Energy Information Administration (2016a). 2010-2015 Retail Gasoline and Diesel Prices. Available online at: http://www.eia.gov/dnav/pet/pet_pri_gnd_a_epd2d_pte_dpgal_a.htm (Accessed September 15, 2016).
U.S Energy Information Administration (2016b). Electric Power Monthly: Table 5.6.A. Average Price of Electricity to Ultimate Customers by End-Use Sector. Available online at: http://www.eia.gov/electricity/monthly/epm_table_grapher.cfm?t=epmt_5_6_a (Accessed September 1, 2015).
U.S Government Accountability Office. (2014). Supply Concerns Continue, and Uncertainties Complicate Planning: GAO Highlights. (Washington, DC).
Vadas, P. A., and Digman, M. F. (2013). Production costs of potential corn stover harvest and storage systems. Biomass Bioenergy 54, 133–139. doi: 10.1016/j.biombioe.2013.03.028
Wang, M., Sabbisetti, R., Elgowainy, A., Dieffenthaler, D., Anjum, A., and Sokolov, V. (2015). GREET Model: The Greenhouse Gases, Regulated Emissions and Energy Use in Transportation Model. Lemont, IL: Agronne National Laboratory.
Weiss, N. D., Farmer, J. D., and Schell, D. J. (2010). Impact of corn stover composition on hemicellulose conversion during dilute acid pretreatment and enzymatic cellulose digestibility of the pretreated solids. Bioresour. Technol. 101, 674–678. doi: 10.1016/j.biortech.2009.08.082
Wendt, L. M., Bonner, I. J., Hoover, A. N., Emerson, R. M., and Smith, W. A. (2014). Influence of airflow on laboratory storage of high moisture corn stover. Bioenergy Res. 7, 1212–1222. doi: 10.1007/s12155-014-9455-3
Wendt, L. M., Murphy, J. A., Smith, W. A., Robb, T., Reed, D. W., Ray, A. E., et al. (2018). Compatibility of high-moisture storage for biochemical conversion of corn stover: storage performance at laboratory and field scales. Front. Bioeng. Biotechnol. 6:30. doi: 10.3389/fbioe.2018.00030
Wendt, L. M., Wahlen, B. D., Li, C., Ross, J. A., Sexton, D. M., Lukas, J. C., et al. (2017). Evaluation of a high-moisture stabilization strategy for harvested microalgae blended with herbaceous biomass: part II—techno-economic assessment. Algal Res. 25(Suppl. C), 558–566. doi: 10.1016/j.algal.2017.04.015
Wiersma, D. W., and Holmes, B. J. (2000). Estimating the weight of forage in a forage wagon. Wisconsin Team Forage, UW Extension and College of Agricultural & Life Sciences. Available online at: https://fyi.uwex.edu/forage/files/2014/01/ForageBox.pdf (Accessed August 15, 2016).
Williams, S. D., and Shinners, K. J. (2012). Farm-scale anaerobic storage and aerobic stability of high dry matter sorghum as a biomass feedstock. Biomass Bioenergy 46, 309–316. doi: 10.1016/j.biombioe.2012.08.010
Wyoming Machine Company (2016). Caterpillar 815F Series 2 Soil Compactor. Available: http://www.cat.com/en_US/products/new/equipment/compactors/soil-compactors/14133405.html (Accessed September 15, 2016).
Yancey, N. A., Tumuluru, J. S., and Wright, C. T. (2013). Drying, grinding and pelletization studies on raw and formulated biomass feedstock's for bioenergy applications. J. Biobased Mater. Bioenergy 7, 549–558. doi: 10.1166/jbmb.2013.1390
Keywords: corn stover, forage chopping, ensiling, techno-economic analysis, sustainability
Citation: Wendt LM, Smith WA, Hartley DS, Wendt DS, Ross JA, Sexton DM, Lukas JC, Nguyen QA, Murphy JA and Kenney KL (2018) Techno-Economic Assessment of a Chopped Feedstock Logistics Supply Chain for Corn Stover. Front. Energy Res. 6:90. doi: 10.3389/fenrg.2018.00090
Received: 11 May 2018; Accepted: 21 August 2018;
Published: 18 September 2018.
Edited by:
Timothy G. Rials, University of Tennessee, Knoxville, United StatesReviewed by:
Xifei Li, Xi'an University of Technology, ChinaBurton C. English, University of Tennessee, Knoxville, United States
Copyright © 2018 Wendt, Smith, Hartley, Wendt, Ross, Sexton, Lukas, Nguyen, Murphy and Kenney. This is an open-access article distributed under the terms of the Creative Commons Attribution License (CC BY). The use, distribution or reproduction in other forums is permitted, provided the original author(s) and the copyright owner(s) are credited and that the original publication in this journal is cited, in accordance with accepted academic practice. No use, distribution or reproduction is permitted which does not comply with these terms.
*Correspondence: Lynn M. Wendt, lynn.wendt@inl.gov