A holistic digital twin simulation framework for industrial facilities: BIM-based data acquisition for building energy modeling
- Department of Integrated Planning and Industrial Building, Institute of Interdisciplinary Construction Process Management, Faculty for Civil Engineering, TU Wien, Vienna, Austria
Energy and resource efficiency as well as reduction of emissions are nowadays significant objectives for production companies. Industry 4.0, through extensive digitalization along the value chain, enables the achievement of these objectives not only in the construction of new facilities but also in existing facilities as well. This requires an interdisciplinary approach, extending over production and logistic processes as well as the building, technical building services, and energy supply systems, consolidated through integrated modeling and simulation-based optimization. The research question this study addresses is how to digitally couple these subsystems and optimize the overall system’s performance in terms of energy and resource efficiency, by distancing from silo-field thinking while using an integrated analysis approach. The article briefly presents a holistic modeling and simulation framework, utilizing modular digital twins (DTs) of all elements that may constitute a given industrial unit. The integration of multiple DTs of these subsystems in a hybrid (continuous and discrete) simulation forms a holistic DT ecosystem of an existing facility. The particular focus of the study is the building representation in this DT ecosystem for energy-efficient production. Based on a methodology including hybrid simulation, building information modeling (BIM), and visual programming, a semi-automated data acquisition workflow was proposed. The hybrid simulation is based on Discrete Event System Specification (DEVS) formalism, where the building is incorporated as a building energy model (BEM). Within the abstracted representation of the overall system, the article explores the possibilities of parametrizing the DT of the building, interconnected with the rest of the factory elements, by acquiring information directly from existing BIM models. Through a comparative case study, the proposed workflow is compared to a manual one in terms of integrity and benefits. The study’s contribution lies in: 1) the detection of the required building level of abstraction for a holistic DT ecosystem, 2) the definition of the interconnections between the building-related counterparts and the rest of the virtual environment as well as the data required for their parameterization, and 3) proposing a semi-automated workflow via virtual programming, for BIM-based creation of the building model within a holistic DT ecosystem.
Introduction
Traditionally, four objectives have determined the criteria for decision-making in the manufacturing sector, namely costs, time, quality, and flexibility (Chryssolouris, 1992). However, increasing energy and raw material prices, necessary investments for compliance with environmental and political targets as well as raising public awareness of resource consumption and climate change, posing a challenge to corporate images, have led production companies to include energy and resource efficiency as an additional decision-making objective.
Significant benefits can be gained by utilizing simulations for predicting the energy consumption of the whole manufacturing process, including production chains as well as auxiliary systems (Thiede et al., 2013). It requires the modeling of complex systems, with both continuous and discrete aspects, to assess the performance and interaction of machinery and manufacturing processes with auxiliary components such as the technical building services (TBS) and the industrial building itself. These are thus considered subsystems of the overall system of an industrial unit. Using one model executed by a single simulation engine is regarded as a classic simulation, whereas co-simulation uses different sets of models simulated by their accompanying simulation engines, results of which are interconnected and refeed the models’ parameters (Steinbrink et al., 2018). Furthermore, hybrid simulation refers to the existence of multiple models, which are though executed by one simulation engine. Previous comprehensive simulation-based approaches have combined and assessed the multiple subsystems of industrial environments, utilizing co-simulation of separate tools (Bleicher et al., 2014; Sun et al., 2016; Thiede et al., 2016; Herrmann and Thiede, 2019) or by combining different applications in a single environment simulation (Despeisse et al., 2013). The first combine best-of-class tools under technically challenging conditions of combining continuous time-driven with discrete event simulation models, for example, building performance simulation with manufacturing process simulation, which poses a challenge in terms of practical implementation. On the contrary, the second approach included manufacturing procedures in a building energy modeling (BEM) tool. However, this faces the limitations of simplistic modeling of manufacturing processes, incorporated in the time-driven continuous simulation, modeled as thermal zones or assumed as internal thermal load with a defined operating schedule, based on external process level simulations (Garwood et al., 2018a). Hybrid simulation approaches in industrial engineering, where discrete and continuous sub-models are solved simultaneously are not known to the authors. Furthermore, previous efforts focused exclusively on the analysis and planning of new industrial facilities, lacking the ability to assess and optimize energy and resource flows during actual operation, where initial models can be continually updated by monitoring data.
In the course of the Industry 4.0 developments, there is rapidly evolving research concerning the implementation of virtual models of physical systems, which are updated by real-time data obtained from sensors, commonly known as digital twins (DTs), as first proposed by Grieves (2014). The primary utilization of DTs in manufacturing-related research and applications includes engineered products, production machines, or manufacturing processes and focuses on production planning and monitoring, resource management, and predictive maintenance (Lo et al., 2021). Much of the already conducted research is asset specific, where the various physical assets of an industrial facility are represented by a set of very detailed but separated DTs, addressing from single components or machines up to production lines or shop floors (Melesse et al., 2021). Comprehensive modeling and simulation of industrial DT concepts are scarce, as the one proposed by Becue et al. (2020) refers to production and logistics processes within a factory unit or even among more industrial units. However, the relation of the manufacturing process with the industrial building that houses it has not yet been addressed in such concepts.
Scaling up from the machines’ level to the building, building information modeling (BIM), defined as “a digital representation of physical and functional characteristics of a facility” (BuildingSMARTalliance, 2007), forms the source of information for a DT of the building. BIM-based DTs in an industrial context have been studied principally in terms of a detailed geometric representation of existing facilities, linked with a navigation framework supporting human and robot movements (Delbrügger et al., 2017), or real geometric configuration of the DT regarding complicated shapes (Agapaki & Brilakis, 2022). No research regarding BEM as well as energy and thermal performance of an industrial building assessed via BIM-based DTs is known to the authors. It should be also noted that the process of BIM-based BEM is not yet standardized, as recent studies showed that there is no solid workflow able to generate reliable models ready for analysis (Bastos Porsani et al., 2021) and BIM tools as well as data transfer formats should be further developed to contain and transfer all required data (Gao et al., 2019).
Taking the aforementioned particulars into account, a gap is identified within the interdisciplinary research domain, integrating production and logistic processes as well as the building, technical building services, and energy supply systems, thus allowing integrated modeling and holistic simulation-based optimization. The research problem is how to digitally couple these subsystems and optimize the overall system’s performance in terms of energy and resource efficiency, instead of insular optimizations of singular domains, as it still is the state-of-the art; which does not lead to an overall achievement of sustainable production. Therefore, a holistic framework and an accompanying prototypical toolchain for DT-based hybrid simulation and optimization of existing manufacturing facilities’ operations were proposed within the research project Balanced Manufacturing (BaMa). The goal was to couple the objectives of sustainability with competitiveness taking into account energy consumption and related carbon emissions, production costs, and time (BaMa, 2018). The holistic nature of the approach lies in the incorporation of all elements of a factory, including the building and TBS together with the manufacturing processes and logistics. The hybrid nature of the simulation lies in the fact that both continuous and discrete aspects are addressed in a single environment of interconnected DT components of all subsystems, forming a holistic DT ecosystem of the whole facility. This has the advantage that the various sub-models must not be split into different simulation environments along the boundaries of discrete and continuous modeling, where important synergies may be neglected or partially evaluated (Heinzl et al., 2018). In this respect, the inclusion of various aspects of each subsystem involved requires a certain level of abstraction so that the DT sub-models can be combined and solved by a single simulation engine. About building-related attributes can serve as a knowledge database and input information to the holistic DT models and the hybrid simulation. Still, data-rich BIM models need to be simplified to provide only certain information, essential for the accomplishment of the integrated hybrid simulation analysis. The building DT in the proposed framework differentiates from common building DTs, as it does not utilize a BIM model as the DT by itself, but creates an abstracted representation of the building’s spatial relations with the production and logistic processes as well as a BEM, by extracting information from a BIM model.
The scope of the article is the building representation of the proposed holistic DT-based framework for modeling and simulating industrial facilities. It presents the proposed framework and further focuses on the use of BIM models for creating and parametrizing the building-related part in the hybrid simulation environment. Data exchange requirements from BIM models are defined and model simplification principles are analyzed. It is examined, how and to which extent building-related attributes regarding BEM can be integrated into the modular hybrid simulation models via a semi-automated data acquisition workflow. The novelty of the work lies in the creation of the building component of the hybrid simulation model of an industrial facility, in the holistic BaMa DT ecosystem, with data acquired directly from a BIM model. Therefore, the feasibility of the proposed semi-automated data acquisition workflow based on visual programming is investigated and tested for its integrity in a comparative case study against a manual process of acquiring the necessary building-related data.
Figure 1 shows the structure of the study. Theoretical background provides a theoretical background on the related topics of DTs in the manufacturing and AEC industries, holistic energy modeling and simulation of industrial facilities, BIM-based BEM, and the potential of coupling visual programming with BIM. BaMa: a framework for a holistic digital twin ecosystem gives an overview of the BaMa framework for a holistic DT ecosystem in industrial facilities, explaining the role of the building in the hybrid simulation environment. Scope of research, tools, and methods presents the methodology and sets the research questions. Building energy modeling procedure within the BaMa digital twin framework then proposes a workflow for BIM-based data acquisition for the abstracted building representation and the BEM model within the BaMa DT ecosystem. In Evaluation of the proposed data acquisition workflows the proposed workflow is evaluated by a comparative case study. Finally, the results of the comparative case study application, identifying strengths and limitations of the suggested procedure are discussed together with the challenges and opportunities for holistic modeling and simulation as of the proposed framework.
Theoretical background
This section outlines the key related works in four main research areas relevant to this study: 1) digital twins (DTs) in the manufacturing and AEC industries, 2) holistic energy modeling and simulation of industrial facilities, and 3) BIM-based BEM and 4) the potentials of coupling visual programming with BIM.
Digital twins in manufacturing and AEC
The original concept of a digital twin was introduced by Grieves in 2003 on product lifecycle management in the field of manufacturing engineering (Grieves, 2014). Since then, it has grown across various industries and it has been given a variety of definitions and characterizations. A generalized and consolidated definition, avoiding industry-specific characteristics was recently provided by VanDerHorn and Mahadevan (2021), where a DT is “a virtual representation of a physical system (and its associated environment and processes) that is updated through the exchange of information between the physical and virtual systems.” This virtual representation is an idealized form of the physical reality, based on the interpretation of the data collected from the physical world, considering a certain level of abstraction imposed by the scope of the created model. The primary motivation for the use of a DT is the monitoring of the system of interest as it changes over time. The DT virtual representation describes a single instance of the physical system and is updated at frequent intervals (VanDerHorn and Mahadevan, 2021).
Manufacturing-related DT research is mainly focusing on products’ design and lifecycle (Tao et al., 2018; Lo et al., 2021), production lines and machinery, (Cimino et al., 2019), predictive maintenance (Aivaliotis et al., 2019), and equipment energy consumption management (Zhang et al., 2018). Applications of DTs also considering the auxiliary components of a factory are less common, such as the study by Blume et al. (2020) on DTs for TBS operation in factories, on a case study of a cooling tower. Manufacturing-related DTs are usually high-fidelity virtual representations of systems and processes and are monitored in real-time, with DT update frequencies in the scale of seconds or less. Furthermore, they generally focus on the low field level of the automation pyramid, (Martinez et al., 2021), that of sensors and actuators for collecting production data and executing commands (ANSI/ISA-95, 2018).
DTs in the AEC industry are up-to-date dynamic models of a physical asset or a facility, including all structured and unstructured information of the project used to model, simulate, understand, predict, and optimize aspects of the physical asset (Alizadehsalehi and Yitmen, 2021). BIM as a digital platform is directly related to the implantation of DTs in the AEC, as the latter evolve from detailed BIM models by integrating simulations, real-time monitoring, and AI. As in product design applications, DTs in the AEC can be utilized before the physical system really exists. In the design phase, they can create a solution virtually and accurately assess its operation (Deng et al., 2021). In the build phase, DTs can provide the construction specifications to the different providers and enhance the procurement process (Shirowzhan et al., 2020). Finally, in the operation phase, when the physical asset is equipped with enough sensors, backed by AI, they provide predictive maintenance and performance optimization by enabling the system to automatically modify its operation or indicate the need for human intervention (Boje et al., 2020).
It should be noted, that in the case of DTs referring to the built environment, the physical system of interest is usually a whole construction project, building, or even part of a city, with various aspects and interconnections to be considered. Unlike manufacturing DTs, where the model may consist of a single machine or production line (modeled in detail as a system together with its environment influences), AEC DTs are usually extensive and detailed virtual representations of the physical reality, resulting in very high levels of model fidelity. However, a DT is not destined to be an exact representation of reality, as the level of model detail directly relates to the level of abstraction of reality chosen for the virtual representation, defined by the scope and required outcomes of the particular use case (VanDerHorn and Mahadevan, 2021). Considering this position, a building DT can also be outlined by a greater abstraction level, if this complies with the intended use of the model.
Holistic energy modeling and simulation of industrial facilities
Although the utilization of BEM for assessing the building energy performance is a common practice in the AEC industry, in the field of industrial buildings is still a relatively young approach (Moynihan and Triantafillu, 2012; Wright et al., 2013; Lee et al., 2014; Gourlis and Kovacic, 2016; Del Giudice et al., 2021). Assessing and optimizing industrial facilities from an energy use perspective are more challenging than buildings in the residential and tertiary sector, as internal heat gains from manufacturing activities can have a significant impact on the indoor conditions and their scheduling can vary greatly over time, given production demand and economic cycles (Liu et al., 2013; Gourlis and Kovacic, 2017a). Production-related internal gains can be assumed based on installed equipment or directly measured in the case of an operating facility, with the first potentially leading to disputable results and the second being restrictive to existing production configurations. In any case, when using BEM software, simplistic operating schedules defining either maximum loads (Moynihan and Triantafillu, 2012; Lee et al., 2014) or daily patterns (Gourlis and Kovacic, 2016) can be considered within the software environment of BEM tools, as current software cannot accurately incorporate industrial processes (Wright et al., 2013).
Hesselbach et al. (2008) were one of the first to point out that the complex and dynamic interdependencies of machines and production processes, operational management, technical building services, and the building climate could only be analyzed via a holistic view of the facility. According to Duflou et al. (2012), a holistic understanding of the different levels of manufacturing processes, from unit-processing and multi-machine levels to a factory level or even further on multi-factory and supply-chain levels are essential for developing the next generation of manufacturing facilities. Coupling of BEM capabilities with manufacturing process simulation (MPS), generally used for optimizing manufacturing process line and plant’s throughput, offers such a solution, up to the whole factory level. Garwood et al. (2018a) produced a comprehensive review of energy simulation tools and methods for the manufacturing sector, focusing on the combination of BEM with MPS. They categorize holistic approaches into two types, co-simulation and hybrid simulation solutions. Co-simulation uses a state-of-the-art software platform for each discipline and couples them to share data between simulation iterations. The hybrid simulation uses a single solver platform capable of modeling all entities, flows, and interdependencies achieving a maximum level of interaction between various processes. This level of high interaction between systems may not be achieved by a compartmentalized co-simulation solution, as information, for example, about internal heat gains, can be only unidirectional from one software to another (MPS to BEM) and is not modeled in a bidirectional manner among different facility subsystems, being the case in coupling Simulink/MATLAB with EnergyPlus (Brundage et al., 2014).
It is worth noting, however, that holistic simulation solutions may not be suitable for small- or medium-sized enterprises, as these usually require considerable effort in the modeling process, and in the case of simpler systems, energy metering and static numerical calculations would be more appropriate. For more complex systems and large automated production lines, holistic simulations can reveal synergies and optimization potential on multiple levels, from machine to production line and the whole factory. Large enterprises may already have BIM models of their facilities containing the information required for the holistic analysis; however, this does not entail a de facto faster modeling of the necessary simulation model, due to the required simplification and filtering of provided data as well as interoperability issues of the different discipline-oriented software applications.
Challenges in BIM-based building energy modeling
The use of BIM data for facilitating the creation of BEM models to asses building thermal and energy performance has been a topic of thorough research, both academic and industrial, barring a huge potential for building design process optimization. BIM models, considered knowledge databases, can contain most information required for a BEM analysis; however, BIM-based BEM still poses great challenges. These can be briefly sorted into two main fields, being the discipline-specific requirements between the BIM and BEM authoring sides, resulting in the necessity of BIM simplification for performing BEM simulations, and the interoperability issues between BIM and BEM software.
It is known that different software applications typically reflect different “views” of the same building and each must deal with issues unique to its discipline (Bazjanac and Kiviniemi, 2007). These essential discipline-specific differences in the “view” of the building, with usually that of the architect creating the original BIM model not complying with that of the simulation expert further utilizing the BIM model for BEM analysis, can be exceeded by following guidelines during the creation of the initial BIM model (Maile et al., 2013; Senave and Boeykens, 2015). However, such an approach is hard to implement in practice, especially in large industrial building projects where the shared BIM model is altered by various disciplines. The major challenge here lies in the geometrical representation of the building, as BEM requires a much simpler geometry than computer-aided design (CAD) software. BEM implements a finite volume model (FVM) of buildings and room envelopes to simulate the thermal performance of each thermal volume relative to each other and the surrounding environment of the building. The highly detailed and accurate modeling of the building is not required in BEM as small discrepancies will not have a significantly detrimental effect on the overall building performance (Garwood et al., 2018b). BIM-originated geometry must, therefore, be simplified and reduced to be used for BEM, also contributing to shorter computational times in simulating complex models (Lagüela et al., 2014; Choi et al., 2016). The preparation or simplification can be performed automatically to some extent but also needs manual efforts (Ladenhauf et al., 2016; Pinheiro et al., 2018). Furthermore, insufficient construction or material information in BIM objects, not defined by the original BIM authoring side, poses another barrier for BIM-based BEM (Kim et al., 2016).
Concerning data interoperability, the two prevalent data exchange schemata for BIM-based BEM are IFC (Industry Foundation Classes) and gbXML (Green Building Extensible Markup Language), developed by BuildingSmart and Green Building Studio Inc., respectively. Although IFC, being the only ISO-certified schema (ISO EN, 2016), has been developed with a wider scope for providing BIM interoperability among different domains and disciplines from building construction to building operation, gbXML is focused on the energy simulation domain, adopted by several BEM software vendors as a de facto standard for importing BIM data (Bahar et al., 2013). Since the IFC version IFC4 add2 in July 2016 (BuildingSmart, 2022), both exchange schemata can contain the necessary information for a BEM analysis as building geometry, thermal zones, construction types, and material properties, whereas only limited data related to HVAC systems (Kamel and Memari, 2019). Differences lie in the fact that gbXML can only export rectangular geometry from BIM models, which is not the case for IFC, but it is the only one to provide information on the location of the building (Kamel and Memari, 2019). Further on, geometry in gbXML is defined utilizing centerline representation (Pinheiro et al., 2018), while IFC is capable of exporting second-level space boundaries by using standardized Model View Definitions (MVDs), which specify how each object or information should be represented for a particular, discipline-specific view (Venugopal et al., 2012). The first can lead gbXML-generated BEM to an increased zone volume and a potential overestimation of the resulting energy consumption (Bazjanac et al., 2016), however, second-level space boundary data in IFC are often missing or incorrect, hindering the BEM creation process with manual corrections or requiring specific algorithms to produce valid data (Lilis et al., 2017).
Regardless of the selected schema, information loss during data exchange from BIM to BEM is a frequently reported problem (El Asmi et al., 2015; Sanhudo et al., 2018; Gao et al., 2019; Kamel and Memari, 2019). Kamel and Memari (2019) divide the causes of interoperability issues into four categories where 1) the BIM software may not transfer all the required information in the exchange file, for example, the IFC exporter of Revit (version 2018) is not exporting information about thermal and optical properties of construction materials, although IFC can incorporate them (Lilis et al., 2018); 2) the exchange file may not be able to save all the information properly, for example, building location, HVAC properties, and building usage; 3) the BEM software may not be able to read all the information in the data exchange file; 4) information may not be mapped and transferred properly to the BEM and energy simulations engine’s file format.
Potentials of visual programming and BIM
Taking the aforementioned particulars into account, we conclude that BIM-based BEM is undergoing rapid and intense development but there is no guarantee in generating automated or with limited additional effort reliable BEM models. Considering also that currently available BEM solutions are not capable of modeling manufacturing processes in industrial facilities, and a further examination of alternative methods to retrieve information from digital building models for holistic energy efficiency industrial applications is performed.
In this scope, the utilization of visual programming in the AEC industry can lower the hurdle for acquiring essential data from BIM models and simultaneously reveal great potential for data analysis and processing tasks (Preidel et al., 2017). Being more user-friendly than typical programming languages, visual programming is mainly used in the AEC field for generative purposes of parametric geometry and semantic information (Hummpi and Österlud, 2016), as well as for checking or querying information on existing models (Amann et al., 2018). Dynamo is a graphical algorithm editor linked with Autodesk Revit using the Revit API and allowing users to create algorithmic scripts by connecting nodes. As a parametric modeling engine, Dynamo extends Revit’s capabilities by adding a level of associativity that does not exist in the off-the-shelf application, including driving parameters based on external inputs (Kensek, 2014). One of its features is the facilitation of categorizing and managing information from large amounts of components in a BIM model, as in the case of high-rise buildings (Gan et al., 2018). In the field of building energy analysis, Dynamo has been used as a medium to facilitate interoperability via gbXML between the BIM model and BEM tools concerning adaptive facades with building integrated photovoltaics (Somboonwit et al., 2017); or functioning as a platform for deploying algorithmic building performance simulations directly in the BIM environment of Revit, without the need of two separate models and a data exchange schema (Kensek, 2015; Dong et al., 2021).
BaMa: a framework for a holistic digital twin ecosystem
In the course of previous research within a funded research project Balanced Manufacturing (BaMa) a DT framework for software architecture and a prototypical toolchain were proposed, enabling large industrial facilities to integrate energy-related planning into the actual plant operation. A holistic approach addressing all subsystems of a facility (production process, logistics, TBS, and the building itself) was chosen, considering both ecological and economic aspects as optimization targets. The DT simulation-based framework enables monitoring, predicting, and optimizing energy demand and the associated carbon emissions as well as costs, to be linked to the existing industrial automation systems of the facility. BaMa, therefore, does not just assess the optimization potential of designed or existing production but introduces energy efficiency as a steering value into a factory’s operational planning and can be utilized iteratively, such as an advanced planning and scheduling system would support a cost and/or time-efficient production process (Chryssolouris, 1992). The novelty of the BaMa framework lies in the fact that it addresses existing operation facilities and utilizes a holistic hybrid simulation approach with discrete and continuous models solved simultaneously in a single solver platform. These form a holistic DT ecosystem of all factory subsystems, which are continually updated by monitoring data for a simulation-based optimization.
The BaMa holistic DT ecosystem consists of three main parts: constant monitoring, simulation-based predictions, and multicriteria genetic algorithmic optimization. Figure 2 shows a schematic representation of the system’s components and interconnectivity. BaMa acquires real-time data from various sensors attached to the production process and the building technical systems, referring to the logistic flows and storage as well as monitoring the space’s indoor conditions or outdoor weather data. It reports back on the planning and management levels, automation pyramid level 3: manufacturing execution system (MES) and level 4: enterprise resource planning (ERP), as defined by standard ANSI/ISA-95 (2018). However, offline data collection is also relevant, including physical inspections and changes regarding the physical relations of the modeled subsystems (e.g., machinery is removed from a certain space or a big hall is structurally and thermally divided into smaller ones). The monitoring of resource consumption and required conditions of all subsystems is compatible with the energy management standard ISO 50001. The prediction of the energy and resource demand, performed by the hybrid simulation, is based on the real-time monitoring data from the four subsystems comprising a factory—production equipment and processes, logistics, TBS, and the building—extended by day-ahead production plans and forecasting data (e.g., weather information). The optimization of the plant operation via a genetic algorithm (GA) regards the targets of energy, time, and costs as well as restrictions resulting from given degrees of freedom, resource availability, and product quality. The GA’s primary aim is to minimize energy demand with the utilization of synergies, peak load management, and efficient use of available equipment (Sobottka et al., 2017). Its prototypical deployment in an operating industrial baking facility indicated a reduction of the overall energy consumption by up to 30% (Sihn et al., 2018).
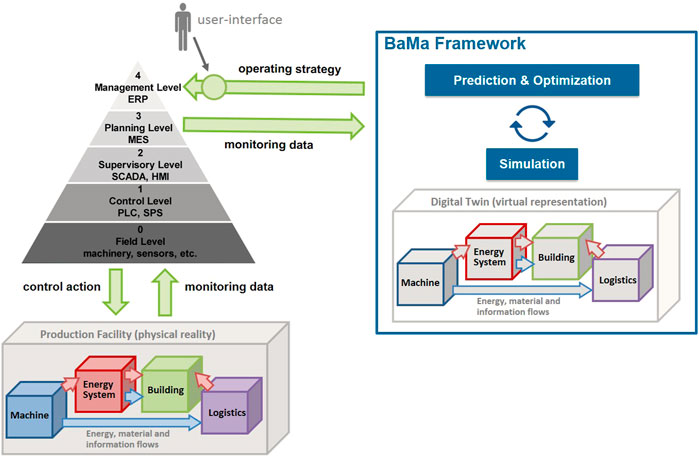
FIGURE 2. Schematic representation of the BaMa framework’s components and interconnectivity (adapted from BaMa, 2018).
BaMa digital twin: the modular cubes
BaMa implements a generic modular approach to create a facility’s DT and models a unified virtual representation of all four factory subsystems in a single solver platform, aiming for the flexibility and reusability of the modular models for a variety of industrial facility types. The core modular element of BaMa DT is the cube. Cubes are the components of the DT, representing physical parts of the facility, and are mapped into mathematically formulated virtual counterparts in the DT. They decompose the overall physical system into manageable elements with well-defined interfaces at a chosen level of abstraction and are assembled each time in virtual constellations representing a unique plant, enabling the analysis of complex and heterogeneous processes. From a top-down view, cubes can be considered as black box models of, for example, a machine, a room, or a piping grid, arranged hierarchically, meaning that a cube can be contained in another cube. The level of abstraction of each cube must correspond to the intended use of the resulting model. The data abstraction process requires, thus, a detailed observation and understating of the reality and a further interpretation process of the data which will consist of the idealized virtual representation, providing the relevant evidence about the reality. The resulting cube models have interfaces consisting of three distinct types of data exchange: energy flow, material flow, and information flow. Energy flows are described by continuous values that require a time-driven modeling approach, whereas material and product flows are discrete entities demanding event-driven modeling. Both carry related carbon emissions and cost weights for assessing the ecological and economic performance of the production. Last, information flows can exchange various information needed for the internal calculations of a cube. The process of determining the modular parts that consists of the entire facility, as well as their interrelationships, is defined inside BaMa as cubing. For example, cubing is performed to analyze a production line in all its stages as well as for defining the thermal view of the building envelope. Data of the relevant physical system, parameters outside the selected physical system that affect it, and also its interconnections to other physical systems, are collected, interpreted, and stored in the virtual representation. A detailed description of the BaMa methodology is available in Leobner et al. (2015) and Leobner (2016).
BaMa cubes are divided into four classes, which include different generic cube types aiming to be able to model all the functions within the factory (Figure 3). The building-related cubes are further explained in Building model within the BaMa digitaltwin ecosystem; however, a detailed description of all other cube models would be beyond the scope of this study. Further information is available in Raich et al. (2016), Smolek et al. (2017), and Smolek et al. (2018).
BaMa hybrid simulation
Although attempts have been made for a holistic simulation of industrial facilities, most of them focus on machine and process levels, neglecting details and interdependencies with the built environment of an industrial facility (Mawson and Hughes 2019). Furthermore, a recent review acknowledged that no simulation software is capable of performing holistic modeling in a single solver platform across all production facility partial systems and linking those models together (Garwood et al., 2018a). Despeisse et al. (2013) have presented an approach for holistic industrial facility simulation within single time-driven BEM software. However, this approach is limited to simple production processes that can be modeled as thermal zones and is not capable of managing intricate production lines. Those could be simulated in separate software and be given afterward as a simplistic schedule for internal thermal loads back in the BEM software. In the scope of BaMa, the necessity of combing time-driven (continuous state) with event-driven (discrete state) modular cube interfaces in a single modeling environment led to the implementation of the Discrete Event and Differential Equation System Specification (DEV&DESS) (Zeigler et al., 2000), as a hybrid Discrete Event System Specification DEVS formalism (Zeigler, 2006), based on Parallel DEVS (P-DEVS) (Chow and Zeigler, 1994). Such kind of simulation environment is increasingly being adopted as the preferred approach to intelligent hybrid (continuous and discrete) cyber-physical system design (Zeigler, 2021).
The desired flexibility of cubes as modular elements further required a strict interface definition. Since none of the existing building performance simulation tools and data exchange schemata such as IFC and gbXML are compliant with the BaMa interface definitions, a new building thermal simulation solution was created inside the BaMa framework and required input information had to be defined and structured to apply the cube approach. The capabilities of the BaMa hybrid simulation, originally implemented in MATLAB, were tested with a simple prototype (Smolek et al., 2018) and were validated against EnergyPlus (Gourlis et al., 2017). The simulation results of an actual facility modeled with the hybrid BaMa approach, including the building, ventilation systems, and manufacturing procedures, were also found to comply with available monitoring data, proving the reliability of the models (Smolek et al., 2017).
Building model within the BaMa digital twin ecosystem
Industrial buildings’ main function is to house the necessary equipment and provide an appropriate indoor environment for production and its accompanying activities, for both employees and industrial operations. The first is achieved by the spaces’ layout and the building structure, while the second is by the performance of the building envelope in combination with the use of TBS and the impact of production processes. The proposed BaMa framework does not aim to optimize the building design or the envelope quality and actual building performance, but considers the building as a fixed boundary of the examined overall system, influenced by external and internal conditions and having an impact on the final overall energy demand. Thus, the objective is the actual performance of the building which is assessed in the three parts of the BaMa framework as follows: 1) by monitoring space conditions to avoid violations of required conditions and comfort, 2) by predicting heating or cooling demand based on current weather conditions or forecast data and the actual production schedule via the hybrid simulation models, and 3) by optimizing the heating or cooling schedules according to the proposed production plan.
Crucial points in the creation of the building component of the facility’s DT are the identification of the intended outcomes and the definition of the model scope. Identifying the target outcomes enables the scope of the modeled DT to be realistically bounded to achieve these outcomes, which should be measurable and quantifiable (VanDerHorn & Mahadevan, 2021). Outcomes of the building components of the BaMa DT implementation are primarily the actual energy demand for heating and cooling of the industrial facility and secondarily the maintenance of the required indoor climate conditions. Based on these targets, the DT scope regarding the building-related physical system is the definition of the building geometry and structure in a multi-zoned thermal model of the facility (as in typical BEM applications), at a certain level of abstraction though, so that it will not add additional complexity to the whole holistic DT ecosystem of the facility.
On the inputs side, the DT models are fed with statistical parameters and state variables. The first does not usually change over the course of the simulation unless an adaptation of the model behavior is needed, whereas the second refers to dynamic values, collected by sensors. In the case of the building DT, the real-time data deriving from sensor monitoring space conditions (e.g., air temperature, relative humidity, CO2, and air quality levels) feed constantly the hybrid simulation as state variables. Furthermore, monitoring information of the TBS is also fed to the BEM part of the hybrid simulation, such as temperature and air speed of the air supply ducts or, for example, temperature and flow rates from the circulating medium of ceiling radiant panels. Last, heat gains from machinery and the production processes are collected and fed to the building DT by sensors measuring the electrical consumption of motors and thermometers in the case of heat-intensive processes, such as ovens. This kind of state variables, combined with the fixed parameters already provided to the models (e.g., the air volume of a thermal zone, the air volume of the industrial oven, product size, and temperature after exiting the oven process) manage to depict the actual physical reality in the holistic DT ecosystem, serving as the base of simulation-based optimization.
The building is analyzed in BaMa, such as the other three subsystems of the factory, by the previously described modular concept of cubes to form the holistic DT of the facility. The building is thus virtually represented by the building and the thermal zone cubes. Building-related cubes have no discrete entities directly interacting with them, thus there is no need for discrete interfaces and models to handle explicitly continuous flows of information and energy. For the assessment of the building-related energy demand, the facility is divided into thermal zones, as is the usual practice in BEM. At the building level, the BEM part of the hybrid simulation, such as other commercial BEM tools, delivers the required heating and cooling demands for each zone, which is then provided, or not, by the TBS cubes, such as the HVAC models inside other BEM tools.
The “building cube” constitutes the construction elements of the facility. It describes the heat transfer through the building envelope into the thermal zones, natural and forced convection on the walls, and solar irradiance on opaque and transparent elements. Inputs are the temperatures of all thermal zones coming according to the occasion either from monitoring data or simulation outcomes, as well as the thermal boundary conditions (outdoor, ground, or other non-simulation temperatures), which are constant parameters. Other inputs are the solar radiation per square meter and the forced convection heat transfer coefficients; the latter, depending on exterior wall perimeter, roughness, area, wind speed, and wind direction, are not calculated inside the cube model due to time efficiency. The net heat gain or loss is calculated as an output result for all thermal zones. The basis underneath the building cube is a resistance-capacitance model, using one capacitance representing the thermal storage potential of the wall or slab and two resistances. The thermal capacity is lumped together, resulting in a single thermal storage potential parameter per wall or slab element. The topology of the building elements is handled by matrices, which relate the position of zones and boundary conditions to each other.
The “thermal zone cube” defines the thermal capacity of the thermal zone’s content with a single internal temperature, considered to have a homogeneous air distribution throughout its volume. Inputs present are the heat transfer via zone boundaries, which is calculated in the building cube, the ambient temperature, which affects the zone infiltration, waste heat internal gains calculated by the production process cubes based on real-time sensor data, and the provided heating and cooling load capacities by the TBS cubes. The temperature in the thermal zone is calculated from the balance of the heat flows over the system boundary as an output. Additional outputs are the heating, cooling, and ventilation demand, as determined by the thermal zone cube for the next time step. To carry out the necessary calculations, both cube types need to have several parameters defined, resulting in the aforedescribed outputs as new state variables of the DT in the optimization procedure (Figure 4).
The use of the hybrid simulation models composed of interconnected cubes results in predicting heating and cooling demands for the virtual counterpart of an operating industrial facility with the actual production plan and occurring process waste heat being integrated into the dynamic model. This poses a clear advantage to methods using co-simulation solutions with assumed internal gains or averaged measurement values, by having to integrate only one model in the facility’s automation system for providing optimized production and auxiliary equipment schedules. However, the BaMa building simulation solution has limitations compared to traditional BEM software due to its rather abstract perception of the building. The impact of shading geometry on the building envelope or dynamic shading options is not addressed, as in the case of shades, only a total g-factor can be defined, based on a set diminution factor (Fc value), and applied to the transparent element. Moreover, natural ventilation strategies cannot be thoroughly examined, being limited to predefined increases or decreases of infiltration rates. Another point is that BaMa cube models cannot address thermally activated building components (Gourlis and Kovacic, 2020) Nevertheless, BaMa is not a framework for optimizing the design or technology of the industrial building itself or of available TBS but focuses on the interaction of all subsystems in terms of energy efficiency. To this extent, it allows a qualitative and quantitative analysis of the whole industrial facility.
Scope of research, tools, and methods
The scope of research is the building representation in the proposed holistic DT ecosystem for energy-efficient manufacturing. The novel contribution of the study is the creation of the building-related components within the presented holistic DT simulation-based framework using BIM models for acquiring data for the building representation and parameterization, as presented in Building model within the BaMa digital twin ecosystem. This study explores the potential of utilizing visual programming for extracting information from BIM models to the building-related part of the hybrid simulation to form the building DT, as defined in the proposed framework in BaMa hybrid simulation and Building model within the BaMa digital twin ecosystem. The utilization of a common data exchange schema for BIM to BEM interoperability, described in Challenges in BIM-based building energy modeling, is not selected by this study, as the data structure of such schemata is incompatible with the building representation of a DT with a high level of abstraction compared to that of traditional BIM-based DTs. The abstracted DT of the building maintains the spatial relations with the production and logistic processes as well as an appropriate BEM representation by extracting information from a BIM model, functioning as a knowledge database. A workflow linking BIM data with the hybrid simulation models via visual programming is proposed and subsequently, a comparative case study is utilized as a testbed for evaluation. The development of the proposed workflow has included the modeling of various industrial use cases to identify the necessary simplification stages for pre-processing an existing architectural BIM model, to be used as an input for an abstracted building representation in the hybrid simulation. Thereupon resulting are building-related data exchange requirements and a semi-automated data acquisition workflow, continuing previous work on data transfer from BIM to BEM for industrial buildings (Gourlis and Kovacic, 2017b) and further the holistic DT hybrid simulation via a manual information workflow (Gourlis et al., 2017).
The proposed workflow and comparative study should answer the research questions:
1. To what extent can the creation of the idealized digital representation of the building in the holistic DT ecosystem be automated based on available BIM models?
2. Does the proposed data acquisition and modeling workflow deliver an accurate BEM representation of the building in the holistic DT ecosystem?
3. Can the proposed workflow facilitate the implementation of the BaMa DT framework in industrial facilities?
The tools used in this study are Autodesk Revit as a BIM authoring tool, Dynamo for visual programming to scripting the proposed algorithm, and MS Excel as a post-processing database and input structuring tool for the BaMa framework and its accompanying prototypical toolchain. Revit is selected for being one of the most utilized BIM software worldwide and Dynamo for the fact that allows visual programming within the Revit environment. In Revit physical properties such as thickness (m), density (kg/m³), thermal conductivity (W/m·K), and specific heat capacity (J/kg·K) can be assigned to all material layers of construction elements, as well as specific details for windows as g-factor and visible transmittance. With this information, Revit allows the calculation of thermal resistance and thermal mass of the used constructions. These as well as building geometry and topology information, together with space-related data can be managed and structured with Dynamo and then exported in a spreadsheet database for further processing. Information related to the building and thermal zone cube types, as described in Building model within the BaMa digital twin ecosystem, can be then formatted in.csv data, ready to be read by the hybrid simulation, and implemented in MATLAB or C++ applications.
Building energy modeling procedure within the BaMa digital twin framework
The proposed workflow is formulated as follows: definition of data exchange requirements, BIM model simplification, model pre-processing; visual programming for accumulating and managing information of the BIM model, and post-processing. The aim was to provide a data structure that retains all the variables describing the physical reality at the level of abstraction chosen for the building component of the holistic hybrid simulation. The defined cube computational models will then describe how the parameters and variables of interest relate to each other within the holistic DT hybrid simulation.
Analysis and definition of data required for the building energy modeling
A set of use cases has been used to define building-related information exchange requirements, along with information about TBS, production processes, and logistics, needed for the hybrid simulation models. First simple prototypes were developed to test modular cubes (Raich et al., 2016; Smolek et al., 2018), which then evolved into models of real manufacturing facilities from project partners (Gourlis et al., 2017; Smolek et al., 2017). For the domain of BEM inside the hybrid simulation, necessary input for the two related cube types, as described in Building model within the BaMa digital twin ecosystem and Figure 4, was identified based on traditional requirements of BEM tools assorted appropriately to the cube approach.
Table 1 summarizes the necessary building-related data input in the BaMa DT framework. Information is divided into two categories, those related to the building elements such as walls, slabs, and windows and those related to the thermal zones. The first contains information on geometry, element topology and type, space boundaries, and material properties, while the second space-related information, zone set-point temperatures, occupancy, non-dynamic lighting gains, and air change requirements. The table outlines whether necessary information is provided by or can be defined in the BIM model, if it is required to develop a functional hybrid simulation model and whether data can be acquired in an automated way. BIM models can contain the required information directly as needed for the input in the hybrid simulation model, for example, construction type, or include the necessary data and additional information so that the desired value can be calculated afterward, for example, boundary condition. Any additional information defined in BIM, for example, zone set-point temperatures, can facilitate the post-processing. All material properties of opaque and transparent elements must be defined in the BIM model, otherwise default values will be applied, which may though lead to calculation errors.
The last column of Table 1 informs on which input values can be acquired “as they are” from the BIM model and which require additional mapping or further post-processing. The difference between these two procedures lies in the required level of data modification. For additional mapping, the required data exist in the correct form in the BIM model but are not correlated with each element to be used in BaMa. This applies to the material and type-related attributes that are defined for an object type (e.g., wall or window) but the actual elements placed in the model do not have these details as attributes. A simple mapping of the object type parameters with the model elements’ topology is thus required. In the case of post-processing, the necessary information is not contained in the desired form in the BIM model but can be calculated or defined based on other information acquired from the BIM model. The workflow is described in detail in Data acquisition workflows.
BIM model simplification
A common practice in every simulation approach is to reduce the complexity of the model and therefore parameters input while maintaining the validity of the simulation results, concerning the question that the simulation is being used to address (Frantz, 1995). An as-built BIM model of an industrial facility contains a significant amount of information irrelevant to the required data for a thermal building simulation, as it is not originally developed for such a purpose. Applying the cube approach requires an appropriate definition of thermal zones according to a BEM discipline view, as discussed in Challenges in BIM-based building energy modeling, based on space usage and type of production processes, conditioning requirements as well as building geometry and construction properties. This constitutes the first stage of model abstraction in BIM by redefining the model’s room-stamps used in the architectural plans with new, representing the necessary thermal zones. The original geometry (e.g., interior partitions) may also be simplified as it is usually too rich and not relevant in the context of building simulation (Choi et al., 2016). This leads to a redefinition of internal boundaries and simplification of construction types in case different wall types with similar thermal properties are used, being the second stage of abstraction. Extensive geometric simplification of the building envelope can affect the building’s performance and must be avoided. The described model abstraction is manual work performed in the pre-processing phase and results in a new “simple” BIM. This is utilized then as the knowledge database from where input values for creation and parameterization of the simulation model are acquired. Further pre-processing actions at the BIM model level are discussed in the following section.
Data acquisition workflows
The procedure of acquiring building-related information from the as-built BIM model of an industrial building and transforming these into cube-structured data, readable by the BaMa hybrid simulation implemented in MATLAB, was performed utilizing two different workflows (Figure 5). The type of data acquired is analyzed in Analysis and definition of data required for the building energy modeling and Table 1.
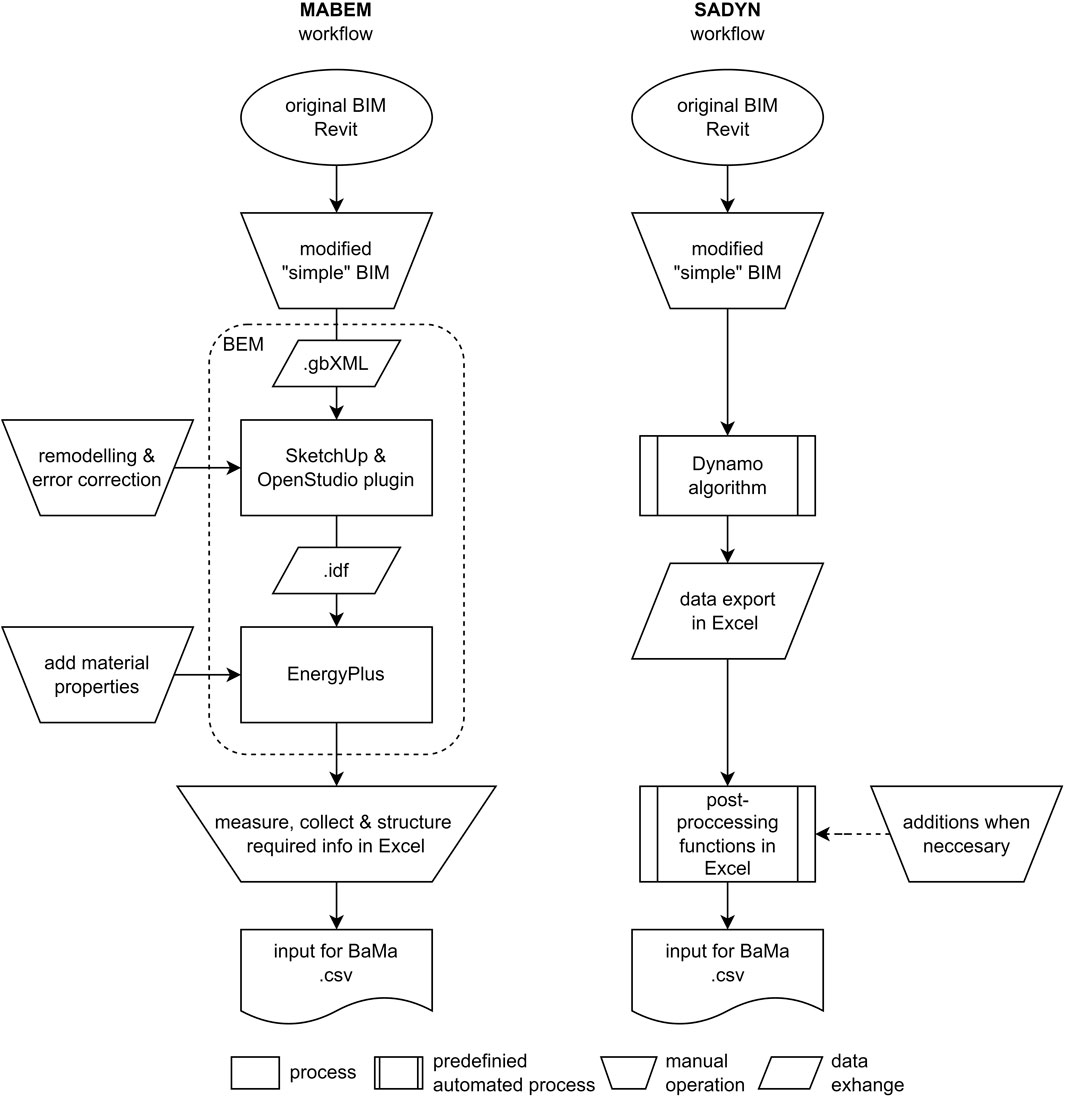
FIGURE 5. Workflows: (left) manual BEM-based data acquisition–MABEM, (right) semi-automated dynamo-based data acquisition–SADYN.
The first workflow is a manual process, based on a developed BEM in EnergyPlus that has been used for validating the results of the thermal building simulation solution inside the BaMa DT framework. However, the so-called manual BEM-based workflow (MABEM) is a time-intensive process, which includes the interoperability problems from BIM to BEM and extensive remodeling and redefinition of element properties, analyzed in previous related work (Gourlis and Kovacic, 2017b). Through the MABEM workflow, a fully functional BEM model is created in EnergyPlus, although such a model is not necessary when applying the BaMa holistic DT framework in an industrial facility. It is only used for providing the required building-related data, categorized as building element and thermal zone data as of Table 1. These are collected or measured manually and are structured in input lists for the BaMa hybrid simulation. The MABEM workflow is not further presented in this section as the steps for creating a BEM model are already published (Gourlis and Kovacic, 2017b) and the rest is a non-standardized manual data collection work.
The second workflow, presented in detail in the following subsections, was created to accelerate the process, allowing a direct acquisition of necessary information from BIM to BaMa. It utilizes a visual programming script for extracting and structuring data directly from a simplified BIM model in a spreadsheet database. Predefined post-processing functions subsequently correct inconsistencies and arrange the data so they can be imported into the hybrid simulation model. If needed, additional information is integrated manually. The semi-automated Dynamo workflow (SADYN) counts three parts—pre-processing in the BIM environment, the Dynamo script, and post-processing in Excel.
Pre-processing in BIM
As the original BIM models are too detailed for either a BEM simulation or for the BaMa framework, both workflows require manual abstraction and editing. The thermal zone separation according to the cube concept requires new room stamps. For the BaMa hybrid simulation, all zones, corresponding to the defined cubes, must have physical boundaries, meaning that the use of room separation lines is to be avoided as no fictional partitions are considered, contrary to the air-wall approach utilized in many BEM tools. Moreover, columns, beams, and freestanding partitions inside zones must be set as non-bounding objects. Elements such as walls and slabs should be modeled as compound objects, as with non-compound elements (separate parallel laid layers); problems arise with adjacencies between zones and inaccurate thermal properties when only the room-stamp bounding construction layer is considered. Curtain walls are to be avoided, since they are managed as walls by BIM authoring tools, without thermal mass or visual light transmittance values, and cause problems regarding their orientation faces. Finally, for elements used in the thermal envelope, an additional property should be set defining their role as an exterior element or element to ground. This can be also determined by the element’s function, which categorizes each element as exterior and interior, given the fact that only appropriate element types are used at the right positions in the model.
Furthermore, in case of an incomplete definition of element properties in the BIM model, missing information must be provided. This is crucial concerning material semantic properties of all elements, which should be defined accordingly, as BIM software calculates thermal mass and resistance based on the construction layers. For an accurate thermal analysis, default values should be replaced appropriately. This affects information such as material roughness and absorptance as well as glazing g-factor and visible transmittance , which are defined in the BIM model material database. Last, zone-related properties, such as space conditioning state, set-point temperatures, and air change rates can be easily determined in the pre-processing stage in BIM and then automatically sorted in input information to the BaMa hybrid simulation.
BIM visual programming script
The main function of the proposed visual programming script in Dynamo is to accumulate, organize, and link together the appropriate building-related information (Analysis and definition of data required for the building energy modeling) contained in the BIM model. This is achieved via managing data lists with built-in dynamo nodes as well as custom nodes provided by “packages” of freely available, open-source collections of custom nodes. Figure 6 depicts an overview of the nodes consisting of the visual programming script with a description of the function of each section. Thermal zone and building element information is managed and arranged according to the model’s room stamps. The light blue section of the script reads and organizes all the necessary thermal zone attributes. The green sections of the script handle the geometry, type, and topology of the building elements (walls, slabs, windows, and doors) that correspond to each thermal zone. This means that although in a BIM Revit model a single element, for example, an exterior wall, can be the boundary of multiple zones, its area is, respectively, divided and allocated to each zone. Wall orientation is obtained separately and is assigned to each wall element and its nested doors and windows in the post-processing phase. The turquoise-colored sections collect the object type parameters and material properties corresponding to the appropriate building elements available in the BIM model (construction type, R-value, thermal mass, roughness, absorptance, g-factor, and visible transmittance). However, this information is not allocated based on room stamps but is mapped in the post-processing phase to the actual building elements of each zone. Last, the orange section exports the obtained data to MS Excel.
The visual programming script is capable of automatically acquiring the required information from the BIM model; however, the following limitations must be acknowledged. First, the produced output fails to provide unique IDs for each building element. This results in elements situated in different zones, with different surface areas having the same ID. Using again the exterior wall example, a single element in Revit with a unique ID will be divided into multiple elements, corresponding to the actual thermal zones, but with the same ID (Figure 7). Additionally, this zone division of the host elements (walls and ceilings) does not consider the area of their nested elements (windows and doors) when calculating the final surface area, leading to inconsistencies. Furthermore, in the case of interior elements, the script does not automatically define the adjacent elements of the neighbor zone. Nevertheless, these problems can be resolved in the following post-processing phase.
Finally, the unrestricted application of the proposed algorithm can be hindered by the fact that compatibility cannot be guaranteed for the evolving Dynamo versions in all systems and due to the condition, that processed parameters must be called by the name. Even for such general parameters, there can be differences in terminology among object families in the BIM authoring software (e.g., for a door: height—rough height). Thus, depending on the used family attributes’ names, the script should be adjusted to deliver all necessary information.
Post-processing by spreadsheet functions
For overcoming the limitations of the visual programming script and completing all required information on the building elements, the data output requires further processing for an automated input to the BaMa DT. Thus, mapping or post-processing is conducted via an Excel tool, containing predefined functions.
Mapping refers to the process of correlating the material properties as object type parameters of each construction type, namely, R-value, thermal mass, roughness, absorptance, g-factor, and visible transmittance, with the actual building element of each zone. The data here are extracted from BIM by the visual programming script in different lists and only require a simple name-based matching of the construction types to enrich the information of each building element.
Post-processing actions correct inconsistencies of the BIM exported data or add further information by using additional exported properties, which are not used directly in the final data lists for BaMa, such as host elements, exterior or ground elements, and element level. First, all building elements obtain new unique IDs sorting out the problem described in 5.3.2. This is crucial for assigning later correct adjacencies for interior building elements. Regarding element orientation, based on their host element information, windows and doors are assigned the appropriate orientation given the fact that they are hosted in exterior building elements. In the case of curtain walls, BIM extracted orientation properties are incorrectly inversed and are adjusted when required. Moreover, post-processing functions calculate the correct surface area of each wall element, subtracting hosted doors and windows when necessary.
Determinative is the process of defining boundary conditions and element adjacencies. After classifying exterior and ground elements, the remaining interior elements are compared in terms of having the same construction type, surface area, and original element ID but belonging to different zones. Here, the initial drawback of the Dynamo export is positively used to help identify adjacent elements and the building topology. In case all comparisons, including the thermal zone, are equal, the element is regarded as an internal zone partition, not belonging to the zone thermal boundary, and is omitted from the final data. Exported wall elements with a surface area smaller than the product of “room height × 0.30 cm” are regarded as adiabatic and are also omitted from the final data lists for BaMa, as they mostly refer to the wall thickness dividing two rooms adjacent to the room where this wall is located, for example, the magenta-colored wall surface in Figure 8, or are surfaces of internal partitions. In the case of remaining elements with no set boundary conditions, either as exterior, ground, or adjacent to specific construction, these are also regarded as adiabatic.
Last, the air resistance values Rse and Rsi are added to each building element according to its position in the zone. According to EN ISO 6946, Rse is determined for exterior elements with 0.4 m2∙K/W and for ground elements with 0 m2∙K/W. Rsi determined for at top positioned exterior elements is 0.1 m2∙K/W and for bottom positioned exterior or ground elements is 0.17 m2∙K/W. In all other cases, Rsi is set to 0.13 m2 K/W. Here, it should be mentioned that although it would be possible to add an air material to the construction types originally in the BIM model in the pre-processing phase and edit the thermal resistance Rsi and Rse as appropriate to have their values already calculated, it would not be feasible, as it would require the creation of different structures for floors according to the correct Rsi. Therefore, the calculation during post-processing was preferred.
Evaluation of the proposed data acquisition workflows
Βoth workflows, as of Data acquisition workflows, were applied in a case study to test the feasibility and reliability of the proposed semi-automated workflow (SADYN) at extracting information from a BIM model and structuring them as input for the holistic hybrid simulation. The goal was to compare the input information that results from both workflows. Data produced by the manual workflow (MABEM) are regarded as the reference point. We examined if SADYN results in a valid representation of the building model, so that the holistic BaMa framework and its accompanying toolchain can be implemented based directly on BIM model data, without the middle step of creating a BEM model. Differences between the results of the two workflows are identified and evaluated, assessing data consistency and implementation times.
Comparative case study
An industrial bakery building in Austria was used as a case study. The building has a rectangular shape housing its production areas mainly in double-height spaces on the ground floor, with peripheral and administration areas in the mezzanine and upper level (Figure 9). The BIM model, originally modeled in Revit, displayed a detailed representation of the building for the construction stage in LOD 400 (level of development), thus providing comprehensive information on the material properties of the building elements and constructions, and information regarding space conditioning, lighting and occupancy loads of the factory’s spaces. It also included numerous geometrical elements non-relevant for the thermal representation of the building in the abstracted DT representation, as well as a high room-stamp partition, concerning the architectural room schedule. For enabling further processing via the visual programming script, an extended manual effort in the initial pre-processing phase was required. Existing room stamps were deleted or modified and new ones were defined to correspond with the desired thermal zone separation of the building, according to the required BaMa cubes.
Both data acquisition workflows, namely, MABEM and SADYN, have been implemented in the case study building model, comparing the geometric characteristics of the thermal zones and the building elements defining them, thus the whole building (Table 2). Having as a reference the results of the MABEM workflow, the relative change in the SADYN workflow results shows the visual-script-computed building has a net floor area of all thermal zones smaller than that manually calculated by 1% and their volume by 8.4%. Thus, SADYN is producing a reliable representation of the building for its use in BaMa, with a negligible variation from the BEM model size. The small net floor area deviation is caused by the definition of thermal zones in the MABEM workflow at the walls or slabs centerlines, which is not the case for room-stamp size calculation in Revit. This factor also affects the space volume, together with the fact that internal wall partitions in zones, when present, are also subtracted from the net zone volume, not considered in the BEM modeling of the MABEM workflow.
Table 2 further compares the actual building elements measured from the BEM model or calculated by the visual programming script and post-processing functions in the two workflows respectively. A great difference is noted in the number of actual elements forming each zone. In total, the elements to be imported in the hybrid simulation are 3.5 times more, that is, an increase of 251.3% . The explanation for this is that the instances of the same building construction, for example, a brick wall, an interior door, or a double-glazed window, between two adjacent zones or to the outside have been aggregated in one element with the equivalent surface area during the manual compilation of the data lists in the MABEM workflow. For interior elements, this is performed regardless of their orientation and position. Exterior elements are aggregated considering the different orientations. For example, in Figure 10 walls “a” and “b” are aggregated in the walls “1–2,” whereas windows “a, b, c, d” and “e, f, g” in windows “2a” and “2b” respectively.
Despite the significantly increased number of building elements, the total surface area of all elements is only deviating by 2.4% from the BEM-based data, being slightly smaller. Though the deviation of horizontal elements, mainly floor slabs, is 1% smaller with SADYN, vertical elements vary more regarding the BEM-based element data. The walls’ surface of the semi-automated workflow is 8% smaller with a factor contributing to this difference being the omission of adiabatic surfaces, as described in 5.3.3, and the use of interior elements boundaries instead of centerlines. On the other hand, windows and doors are calculated with larger areas, which are to be attributed to the framing of these elements, not considered in the MABEM workflow.
Finally, the results show that the time required for creating the building input data for the BaMa hybrid simulation model dramatically decreased when using SADYN. The main process and post-processing time were reduced to about 1/10 of the equivalent MABEM time. The whole creation of the building component of the holistic DT simulation with SADYN requires approximately one-third of the time required for the MABEM workflow.
Discussion
This study explored the possibilities of automated creation of the building competent for a holistic DT modeling and simulation framework for industrial facilities, as proposed in the BaMa research project, to enhance its implementation for energy and recourse efficient production. It analyzed the use of existing BIM models as the required data sources for the abstracted representation of the building in a holistic DT ecosystem. Although data management and analysis via visual programming is not a novelty in the AEC industry, it has never been used in the frame of a holistic simulation framework of energy and resource-efficient manufacturing, where thermal energy synergies of the production processes, the building space around them, and the TBS systems are constantly assessed to be optimized. The main theoretical contributions of the current study to the knowledge domain are: 1) the defection of the required building level of abstraction in a holistic DT representation of all subsystems of an industrial facility, 2) the definition of the interconnections of the building-related counterparts of the DT to the rest of the virtual environment as well as the data required for their parameterization, and 3) the proposed semi-automated workflow for BIM-based creation of the building model within the holistic DT ecosystem. The last could also be utilized outside the BaMa concept, when a building representation is required in a hybrid cyber-physical system simulation, based on DEVS formalism (Zeigler, 2021). The parameterization of the building component of the hybrid simulation could be thus linked directly with a BIM model via the proposed SADYN workflow.
A discussion of the research questions set in Scope of research, tools, and methods is provided below.
Research question 1 on the extent of automated creation of the idealized digital representation of the building in the holistic DT ecosystem, based on available BIM models, is answered as follows. The comparative study of the proposed SADYN workflow proves the feasibility of acquiring directly from a BIM model the required data for the building representation of an industrial facility in the proposed holistic approach of the BaMa DT framework. The process is not fully automated, as it requires manual user intervention, at a great amount in the initial phase and much less later. The required existence of physical boundaries in the BIM models, as described in Pre-processing in BIM may pose a limitation to handling federated BIM models of large facilities, where large halls may be modeled divided into different files. However, if these models correspond to stand-alone thermal views of the facility accompanied by a certain production process, information from each of the BIM sub-models can be extracted separately and assessed as a group of buildings in the holistic DT ecosystem.
The main achievement of the SADYN workflow is omitting the need for the creation of an additional BEM model of the building for performing integrated hybrid simulations (including manufacturing processes, logistics, TBS, and the building). In other words, the thermal view of the building according to required thermal zoning, corresponding to the previously defined cubes, can be performed in BIM at the pre-processing simplification stage. This is the only stage where expert knowledge is required and must be carried out “manually.” Parallelly, the building model is enriched with all other information required for further analysis. Ascribed to the scope and target outcomes of the BaMa DT, no virtual visualization of the building itself is required for the analysis, thus no 3D model is created in the building DT, as is regularly the case in DTs of the built environment. The building in the holistic DT ecosystem consists of fixed information regarding the space geometry, structures, and thermal zones’ topography, as well as real-time updated built environment data. These are indoor space temperatures, humidity, and air quality levels; outdoor climate data; and thermal comfort indices together with real-time production process data in terms of internal heat gains.
Research question 2 addresses the ability of the proposed data acquisition and modeling workflow to deliver an accurate BEM representation of the building in the holistic DT ecosystem. The results of the SADYN workflow showed a satisfactory correlation with the data collected manually from a developed BEM model of the same facility. The small deviation of the building’s size does not have a noticeable impact on the hybrid simulation results, allowing the intended level of a qualitative and quantitative assessment of the building as a part of the whole industrial system under examination. However, a drawback of the SADYN workflow is the larger number of data inputs, as the building surfaces and elements are more fragmented. In MABEM for example, all window surfaces of a zone with the same direction are gathered and reported as one element, which is not the case with SADYN. Contributing to this larger data number is the initial modeling of the building in the BIM software, as one wall may consist of more aligned elements which are then exported separately. Additionally, if two zones have adjacencies with varying element topology, MABEM sums up all walls of the same type in one export element with an appropriate surface. SADYN again lists all separate adjacent elements between the two zones. This can increase the computational time, though it is not expected to reduce the overall runtime efficiency of the simulation below the acceptable point for coupling it with the optimization functions of the GA (Sihn et al., 2018). Furthermore, the proposed visual programming script may not apply to every BIM model, as different BIM object families can differ in the way they define essential parameters, thus requiring adjustment of the script.
Research question 3 examines if the proposed workflow can facilitate the implementation of the BaMa DT framework in industrial facilities. The results of the comparative case study showed the BIM-based creation of the building counterpart as a subsystem in the BaMa DT framework with SADYN required approximately one-third of the time required for the MABEM workflow. This assists a time-efficient implementation of the BaMa toolchain in production companies by using existing BIM models as the basis for the modular cube approach, as of Building model within the BaMa digital twin ecosystem, and then exporting the appropriately structured data in the hybrid simulation. An additional effort to import the data in a BEM tool and repair any inconsistencies is thus omitted, reducing the total model editing time. From this point onward, the SADYN workflow is much more time efficient as required data for the holistic hybrid simulation can be quickly produced via the next two stages of exporting data via the proposed visual programming script and adjusting them by predefined spreadsheet functions, to be finally given as an input parameter to the general simulation model.
Conclusion
The study presented an integrated approach for simulation and optimization of industrial facilities and processes, thereby addressing an interdisciplinary research domain. Through a holistic simulation framework, energy and resource consumption can be reduced while maximizing energy efficiency and production throughput. The novelty of the proposed framework is the integration of DTs of the various disciplines (production planning, building planning, logistics, and energy management) in a holistic DT ecosystem via hybrid simulation, capable of incorporating both continuous and discrete aspects of different discipline models in a single solver platform. The BaMa framework is built upon a generic and modular logic for modeling the DTs of physical reality, aiming to address as many industrial conditions as possible, making it easily adaptable and applicable to various industrial manufacturing types. This approach requires a certain level of abstraction, which always corresponds to the intended use of the resulting DT.
Focusing on the building DT within the proposed holistic DT modeling and simulation framework, this study presented a semi-automated workflow to acquire all necessary data for the representation of the building directly from a BIM model. This was achieved in three steps by simplifying the original BIM model to meet the scope of the building DT in the holistic ecosystem; by using visual programming to gather, organize and export structured building data directly from the BIM model; and finally, by post-processing of the data with spreadsheet functions, rendering them ready for import in the hybrid simulation. A comparative case study proved the feasibility of the proposed semi-automated workflow, identifying the omission of a BEM model creation of the facility as its main advantage.
The first contribution of this study lies in the detection of the required level of abstraction for building models for a holistic DT ecosystem. A highly abstracted BEM representation, outside of the typical BEM tools was analyzed and the definition of the interconnections between the building-related counterparts and the rest of the virtual environment as well as the data required for their parameterization were highlighted. This can help future research in the field of hybrid industrial simulations to prioritize the essential building-related information in the creation of the building DT models, to enable reaching the desired complexity of a holistic DT-based facility representation while omitting unnecessary domain-specific information and thus increasing the error rates and computational time of such models.
Moreover, in the field of holistic industrial production concepts, the study contributes a DT-based application of such a concept, enabled through a semi-automated workflow for BIM-based creation of the building DT model via visual programming. This provides efficient data exchange and time-saving DT modeling and simulations through simplified BIM models. It facilitates the creation of the holistic DT ecosystem through direct production and parameterization of the building DT and thus provides an additional incentive to companies’ decision makers implementing an approach such as the BaMa framework. Furthermore, the proposed workflow contributes to the wider knowledge domain of hybrid simulation for both discrete and continuous cyber-physical system insights for linking BIM models with the hybrid DEVS-based models and directly parametrizing the building component for the simulation. Such hybrid models can incorporate multiple engineering domains, for example, built environment and manufacturing in complex integrated DT representations, amending the assessment of interactions and synergies of the different systems’ components. The translation of the building-related part from a BIM model to the generic DEVS formalism, also adopted in BaMa, could therefore be assisted by the proposed workflow. The current implementation of the workflow via a Dynamo script and predefined post-processing spreadsheet functions can be regarded as a prototype for an automated data acquisition tool. In future, the proposed workflow can be implemented in a single programming environment by developing a tool to provide direct connectivity between BIM models and future software implementation of the BaMa prototypical toolchain and thus a time-efficient exchange of information from BIM to the hybrid simulation models.
Scaling back up to the BaMa holistic DT framework, it must be noted that it is not an off-the-shelf DT framework, such as solutions provided by the original equipment manufacturer for common industry cases. It lacks complex software constellations through different interconnected software platforms and thus has much shorter run times. However, the development of the DT ecosystem by the combination of the modular parts of the hybrid simulation surely poses a challenge for the actual implementation of the framework. Therefore, large and more complex industries rather than small or medium enterprises are more suitable for its application, where the necessary automation infrastructure is available and the implementation effort corresponds to the size of the resulting savings in absolute terms. In future, such holistic solutions could be fully integrated into the ERP system of an industrial facility for an entirely automated energy and resource efficiency optimization.
Data availability statement
The original contributions presented in the study are included in the article/Supplementary Material; further inquiries can be directed to the corresponding author.
Author contributions
Conceptualization, GG; methodology, GG and IK; workflows and case study implementation and writing–original draft preparation, GG; contribution to contents, review, editing, and supervision, IK.
Funding
The authors acknowledge TU Wien Bibliothek for financial support through its Open Access Funding Program. The research presented has been funded by the Austrian Climate and Energy Funds–program e!MISSION.at–as part of the research program Balanced Manufacturing (project number 840746).
Acknowledgments
The authors would like to thank all project partners for their contributions, and especially Peter Smolek for his work on the development of the building and TBS-related DT components of the BaMa framework.
Conflict of interest
The authors declare that the research was conducted in the absence of any commercial or financial relationships that could be construed as a potential conflict of interest.
Publisher’s note
All claims expressed in this article are solely those of the authors and do not necessarily represent those of their affiliated organizations, or those of the publisher, the editors, and the reviewers. Any product that may be evaluated in this article, or claim that may be made by its manufacturer, is not guaranteed or endorsed by the publisher.
Abbreviations
AEC, architectural engineering construction; API, application programming interface; BEM, building energy modeling; BIM, building information modeling; CAD, computer-aided design; DESS, Differential Equation System Specification; DEVS, Discrete Event System Specification; DT, digital twin; ERP, enterprise resource planning; FVM, finite volume model; GA, genetic algorithm; gbXML, Green Building Extensible Markup Language; IFC, Industry Foundation Classes; MABEM, manual BEM-based workflow; MES, manufacturing execution system; MPS, manufacturing process simulation; SADYN, semi-automated Dynamo-based workflow; TBS, technical building services.
References
Agapaki, E., and Brilakis, I. (2022). Geometric digital twinning of industrial facilities: Retrieval of industrial shapes. Available at: https://arxiv.org/abs/2202.04834.
Aivaliotis, P., Georgoulias, K., and Chryssolouris, G. (2019). The use of Digital Twin for predictive maintenance in manufacturing. Int. J. Comput. Integr. Manuf. 32 (11), 1067–1080. doi:10.1080/0951192X.2019.1686173
Alizadehsalehi, S., and Yitmen, I. (2021). Digital twin-based progress monitoring management model through reality capture to extended reality technologies (DRX). Smart Sustain. Built Environ. doi:10.1108/SASBE-01-2021-0016
Amann, J., Preidel, C., Tauscher, E., and Borrmann, A. (2018). “BIM programming,” in Building information modeling. Editors A. Borrmann, M. König, C. Koch, and J. Beetz (Cham: Springer), 217–231. doi:10.1007/978-3-319-92862-3_12
ANSI/ISA-95 (2018). Enterprise-control system integration-Part 5: Business to manufacturing transactions. Research Triangle Park, NC, USA: The International Societ of automation.
Bahar, Y. N., Pere, C., Landrieu, J., and Nicolle, C. (2013). A thermal simulation tool for building and its interoperability through the Building Information Modeling (BIM) Platform. Buildings 3 (2), 380–398. doi:10.3390/buildings3020380
BaMa (2018). BaMa – balanced manufacturing research project. Available at: https://energieforschung.at/wp-content/uploads/sites/11/2020/12/02-Bama-publizierbarer-endbericht2.pdf (Accessed 02 02, 2022).
Bastos Porsani, G., Del Valle de Lersundi, K., Sánchez-Ostiz Gutiérrez, A., and Fernández Bandera, C. (2021). Interoperability between building information modelling (BIM) and building energy model (BEM). Appl. Sci. 11 (5), 2167. doi:10.3390/app11052167
Bazjanac, V., and Kiviniemi, A. (2007). Reduction, simplification, translation and interpretation in the exchange of model data. Proc. CIB W78, 163–168.
Bazjanac, V., Maile, T., and Nytsch-Geusen, C. (2016). Generation of building geometry for energy performance simulation using modelica. Dresden: BauSim, 361–368.
Becue, A., Maia, E., Feeken, L., Borchers, P., and Praca, I. (2020). A new concept of digital twin supporting optimization and resilience of factories of the future. Appl. Sci. 10 (13), 4482. doi:10.3390/app10134482
Bleicher, F., Duer, F., Leobner, I., Kovacic, I., Heinzl, B., and Kastner, W. (2014). Co-simulation environment for optimizing energy efficiency in production systems. CIRP Ann. 63 (1), 441–444. doi:10.1016/j.cirp.2014.03.122
Blume, C., Blume, S., Thiede, S., and Herrmann, C. (2020). Data-driven digital twins for technical building services operation in factories: A cooling tower case study. J. Manuf. Mater. Process. 4 (4), 97. doi:10.3390/jmmp4040097
Boje, C., Guerriero, A., Kubicki, S., and Rezgui, Y. (2020). Towards a semantic construction digital twin: Directions for future research. Automation Constr. 114, 103179. doi:10.1016/j.autcon.2020.103179
Brundage, M. P., Chang, Q., Li, Y., Xiao, G., and Arinez, J. (2014). Energy efficiency management of an integrated serial production line and HVAC system. IEEE Trans. Autom. Sci. Eng. 11 (3), 789–797. doi:10.1109/TASE.2013.2284915
BuildingSmart (2022). IFC specifications database. Available at: https://technical.buildingsmart.org/standards/ifc/ifc-schema-specifications/ (Accessed 02 04, 2022).
BuildingSMARTalliance (2007). United States national building information modeling standard version 1 - Part 1: Overview, principles and methodologies. Washington D.C: National Institute of Building Science.
Choi, J., Shin, J., Kim, M., and Kim, I. (2016). Development of openBIM-based energy analysis software to improve the interoperability of energy performance assessment. Automation Constr. 72, 52–64. doi:10.1016/j.autcon.2016.07.004
Chow, A. C. H., and Zeigler, B. P. (1994). “Parallel DEVS: A parallel, hierarchical, modular, modeling formalism,” in Proc. 26th conference on Winter simulation, Orlando, FL, United States, December 11–14, 1994 (Society for Computer Simulation International), 716–722.
Chryssolouris, G. (1992). Manufacturing systems: Theory and practice. 1st ed. New York: Springer Science & Business Media.
Cimino, C., Negri, E., and Fumagalli, L. (2019). Review of digital twin applications in manufacturing. Comput. Industry 113, 103130. doi:10.1016/j.compind.2019.103130
Del Giudice, M., Dettori, M., Magnano, S., and Osello, A. (2021). “A BIM to BEM approach for data exchange: Advantages and weaknesses for industrial buildings energy assessment,” in ECPPM 2021–eWork and eBusiness in architecture, engineering and construction (London, United Kingdom: CRC Press), 98–105. doi:10.1201/9781003191476-13
Delbrügger, T., Lenz, L. T., Losch, D., and Roßmann, J. (2017). “A navigation framework for digital twins of factories based on building information modeling,” in 2017 22nd IEEE International Conference on Emerging Technologies and Factory Automation (ETFA), Limassol, Cyprus, 12-15 September 2017, 1–4. doi:10.1109/ETFA.2017.8247712
Deng, M., Menassa, C. C., and Kamat, V. R. (2021). From BIM to digital twins: A systematic review of the evolution of intelligent building representations in the AEC-FM industry. ITcon. 26 (5), 58–83. doi:10.36680/j.itcon.2021.005
Despeisse, M., Oates, M. R., and Ball, P. D. (2013). Sustainable manufacturing tactics and cross-functional factory modelling. J. Clean. Prod. 42, 31–41. doi:10.1016/j.jclepro.2012.11.008
Dong, Y., Sun, C., Han, Y., and Liu, Q. (2021). Intelligent optimization: A novel framework to automatize multi-objective optimization of building daylighting and energy performances. J. Build. Eng. 43, 102804. doi:10.1016/j.jobe.2021.102804
Duflou, J. R., Sutherland, J. W., Dornfeld, D., Herrmann, C., Jeswiet, J., Kara, S., et al. (2012). Towards energy and resource efficient manufacturing: A processes and systems approach. CIRP Ann. 61 (2), 587–609. doi:10.1016/j.cirp.2012.05.002
El Asmi, E., Robert, S., Haas, B., and Zreik, K. (2015). A standardized approach to BIM and energy simulation connection. Int. J. Des. Sci. Technol. 21 (1), 59–82.
Frantz, F. K. (1995). “A taxonomy of model abstraction techniques,” in Proceedings of the 27th conference on Winter simulation (Arlington, VA, United States: IEEE Computer Society), 1413–1420.
Gan, V. J., Deng, M., Tse, K. T., Chan, C. M., Lo, I. M., and Cheng, J. C. (2018). Holistic BIM framework for sustainable low carbon design of high-rise buildings. J. Clean. Prod. 195, 1091–1104. doi:10.1016/j.jclepro.2018.05.272
Gao, H., Koch, C., and Wu, Y. (2019). Building information modelling based building energy modelling: A review. Appl. Energy 238, 320–343. doi:10.1016/j.apenergy.2019.01.032
Garwood, T. L., Hughes, B. R., O'Connor, D., Calautit, J. K., Oates, M. R., and Hodgson, T. (2018b). A framework for producing gbXML building geometry from Point Clouds for accurate and efficient Building Energy Modelling. Appl. Energy 224, 527–537. doi:10.1016/j.apenergy.2018.04.046
Garwood, T. L., Hughes, B. R., Oates, M. R., O’Connor, D., and Hughes, R. (2018a). A review of energy simulation tools for the manufacturing sector. Renew. Sustain. Energy Rev. 81, 895–911. doi:10.1016/j.rser.2017.08.063
Gourlis, G., and Kovacic, I. (2016). A study on building performance analysis for energy retrofit of existing industrial facilities. Appl. Energy 184, 1389–1399. doi:10.1016/j.apenergy.2016.03.104
Gourlis, G., and Kovacic, I. (2017b). Building Information Modelling for analysis of energy efficient industrial buildings – a case study. Renew. Sustain. Energy Rev. 68 (2), 953–963. doi:10.1016/j.rser.2016.02.009
Gourlis, G., and Kovacic, I. (2020). Energy efficient operation of industrial facilities: The role of the building in simulation-based optimization. IOP Conf. Ser. Earth Environ. Sci. 410 (1), 012019. doi:10.1088/1755-1315/410/1/012019
Gourlis, G., and Kovacic, I. (2017a). Passive measures for preventing summer overheating in industrial buildings under consideration of varying manufacturing process loads. Energy 137, 1175–1185. doi:10.1016/j.energy.2017.05.134
Gourlis, G., Smolek, P., Heinzl, B., Leobner, I., and Kovacic, I. (2017). “From BIM models to integrated energy efficiency applications for industrial facilities,” in LC3 2017: Volume I – Proc. of the Joint Conference on Computing in Construction (JC3), Heraklion, 245–253. doi:10.24928/JC3-2017/0181
Grieves, M. (2014). Digital twin: Manufacturing excellence through virtual factory replication. White Pap. 1, 1–7.
Heinzl, B., Raich, P., Preyser, F., and Kastner, W. (2018). Simulation-based assessment of energy efficiency in industry: Comparison of hybrid simulation approaches. IFAC-PapersOnLine 51 (2), 689–694. doi:10.1016/j.ifacol.2018.03.117
Herrmann, C., and Thiede, S. (2019). Process chain simulation to foster energy efficiency in manufacturing. CIRP J. Manuf. Sci. Technol. 1 (4), 221–229. doi:10.1016/j.cirpj.2009.06.005
Hesselbach, J., Herrmann, C., Detzer, R., Martin, L., Thiede, S., and Lüdemann, B. (2008). “Energy efficiency through optimised coordination of production and technical building services,” in Proc. 15th CIRP international conference life cycle engineering, Sydney, 624–629. ISBN: 1877040673.
Hummpi, H., and Österlud, T. (2016). “Algorithm-aided BIM,” in Proceedings of the 34th eCAADe Conference, 601–609.
I.S.O. EN (2016). EN ISO 16739:2016 — industry foundation classes (IFC) for data sharing in the construction and facility management industries (ISO 16739:2013) (Brussels, Belgium: CEN-CENELEC).
Kamel, E., and Memari, A. M. (2019). Review of BIM's application in energy simulation: Tools, issues, and solutions. Automation Constr. 97, 164–180. doi:10.1016/j.autcon.2018.11.008
Kensek, K. M. (2014). Integration of environmental sensors with BIM: Case studies using arduino. Dynamo, and the Revit API. Inf. Constr. 66 (536), e044–39. doi:10.3989/ic.13.151
Kensek, K. M. (2015). Visual programming for building information modeling: Energy and shading analysis case studies. J. Green Build. 10 (4), 28–43. doi:10.3992/jgb.10.4.28
Kim, H., Shen, Z., Kim, I., Kim, K., Stumpf, A., and Yu, J. (2016). BIM IFC information mapping to building energy analysis (BEA) model with manually extended material information. Automation Constr. 68, 183–193. doi:10.1016/j.autcon.2016.04.002
Ladenhauf, D., Berndt, R., Krispel, U., Eggeling, E., Ullrich, T., Battisti, K., et al. (2016). Geometry simplification according to semantic constraints. Comput. Sci. Res. Dev. 31 (3), 119–125. doi:10.1007/s00450-014-0283-7
Lagüela, S., Díaz-Vilariño, L., Armesto, J., and Arias, P. (2014). Non-destructive approach for the generation and thermal characterization of an as-built BIM. Constr. Build. Mater. 51, 55–61. doi:10.1016/j.conbuildmat.2013.11.021
Lee, B., Trcka, M., and Hensen, J. L. (2014). Building energy simulation and optimization: A case study of industrial halls with varying process loads and occupancy patterns. Build. Simul. 7 (3), 229–236. doi:10.1007/s12273-013-0154-3
Leobner, I. (2016). Modeling of energy systems for complex situations. Ph.D. Dissertation. Vienna: TU Wien.
Leobner, I., Smolek, P., Heinzl, B., and Kovacic, I. (2015). “Balanced manufacturing – A methodology for energy efficient production plant operation,” in 10th Conference on Sustainable Development of Energy, Water and Environment Systems. ISSN: 1847-7178, paper-nr. 2015.0268.
Lilis, G. N., Giannakis, G. I., Katsigarakis, K., and Rovas, D. (2018). “A tool for IFC building energy performance simulation suitability checking,” in eWork and eBusiness in Architecture, Engineering and Construction, Proc. 12th European Conference on Product and Process Modeling (ECPPM 2018) (Copenhagen: CRC Press). doi:10.1201/9780429506215-8
Lilis, G. N., Giannakis, G. I., and Rovas, D. V. (2017). Automatic generation of second-level space boundary topology from IFC geometry inputs. Automation Constr. 76, 108–124. doi:10.1016/j.autcon.2016.08.044
Liu, H., Zhao, Q. C., Huang, N. J., and Zhao, X. (2013). A simulation-based tool for energy efficient building design for a class of manufacturing plants. IEEE Trans. Autom. Sci. Eng. 10, 117–123. doi:10.1109/TASE.2012.2203595
Lo, C. K., Chen, C. H., and Zhong, R. Y. (2021). A review of digital twin in product design and development. Adv. Eng. Inf. 48, 101297. doi:10.1016/j.aei.2021.101297
Maile, T., O’Donnell, J., Bazjanac, V., and Rose, C. (2013). “BIM-Geometry modeling guidelines for building energy performance simulation,” in Proc. 13th Conference of International Building Performance Simulation Association, Chambéry, 3242–3249.
Martinez, E. M., Ponce, P., Macias, I., and Molina, A. (2021). Automation pyramid as constructor for a complete digital twin, case study: A didactic manufacturing system. Sensors 21 (14), 4656. doi:10.3390/s21144656
Mawson, V. J., and Hughes, B. R. (2019). “The development of modelling tools to improve energy efficiency in manufacturing processes and systems. J. Manuf. Syst. 51, 95–105. doi:10.1016/j.jmsy.2019.04.008
Melesse, T. Y., Di Pasquale, V., and Riemma, S. (2021). Digital Twin models in industrial operations: State‐of‐the‐art and future research directions. IET Collob. Intell. Manuf. 3 (1), 37–47. doi:10.1049/cim2.12010
Moynihan, G. P., and Triantafillu, D. (2012). Energy savings for a manufacturing facility using building simulation modeling: A case study. Eng. Manag. J. 24 (4), 73–84. doi:10.1080/10429247.2012.11431957
Pinheiro, S., Wimmer, R., O’Donnell, J., Muhic, S., Bazjanac, V., Maile, T., et al. (2018). MVD based information exchange between BIM and building energy performance simulation. Automation Constr. 90, 91–103. doi:10.1016/j.autcon.2018.02.009
Preidel, C., Daum, S., and Borrmann, A. (2017). Data retrieval from building information models based on visual programming. Vis. Eng. 5 (1), 18. doi:10.1186/s40327-017-0055-0
Raich, P., Heinzl, B., Preyser, F., and Kastner, W. (2016). “Modeling techniques for integrated simulation of industrial systems based on hybrid PDEVS,” in 2016 Workshop on Modeling and Simulation of Cyber-Physical Energy Systems (MSCPES), Vienna. doi:10.1109/MSCPES.2016.7480221
Sanhudo, L., Ramos, N. M., Martins, J. P., Almeida, R. M., Barreira, E., Simões, M. L., et al. (2018). Building information modeling for energy retrofitting–A review. Renew. Sustain. Energy Rev. 89, 249–260. doi:10.1016/j.rser.2018.03.064
Senave, M., and Boeykens, S. (2015). “Link between BIM and energy simulation,” in Building information modeling (BIM) in design, construction and operations (Southampton, United Kingdom: Wessex Institute of Technology (WIT) Press), 341–352. doi:10.2495/BIM150291
Shirowzhan, S., Tan, W., and Sepasgozar, S. M. (2020). Digital twin and CyberGIS for improving connectivity and measuring the impact of infrastructure construction planning in smart cities. ISPRS Int. J. Geoinf. 9 (4), 240. doi:10.3390/ijgi9040240
Sihn, W., Sobottka, T., Heinzl, B., and Kamhuber, F. (2018). Interdisciplinary multi-criteria optimization using hybrid simulation to pursue energy efficiency through production planning. CIRP Ann. 67 (1), 447–450. doi:10.1016/j.cirp.2018.04.059
Smolek, P., Gourlis, G., Mörzinger, B., Leobner, I., and Ponweiser, K. (2017). “Thermal building simulation of an industrial production facility using the balanced manufacturing approach,” in Proc. 12th Conference on Sustainable Development of Energy, Water and Environment Systems, Dubrovnik. ISSN: 1847-7178, paper-nr. 2017.0166.
Smolek, P., Leobner, I., Gourlis, G., Mörzinger, B., Heinzl, B., and Ponweiser, K. (2018). Hybrid building performance simulation models for industrial energy efficiency applications. J. Sustain. Dev. energy water Environ. Syst. 6 (2), 381–393. doi:10.13044/j.sdewes.d6.0194
Sobottka, Τ., Kamhuber, F., and Sihn, W. (2017). Increasing energy efficiency in production environments through an optimized, hybrid simulation-based planning of production and its periphery. Procedia CIRP 61, 440–445. doi:10.1016/j.procir.2016.11.151
Somboonwit, Ν., Boontore, Α., and Rugwongwan, Υ. (2017). “Obstacles to the automation of building performance simulation: Adaptive building integrated photovoltaic (BIPV) design,” in 5th AMER International Conference on Quality of Life, Bangkok. doi:10.21834/e-bpj.v2i5.619
Steinbrink, C., Schlögl, F., Babazadeh, D., Lehnhoff, S., Rohjans, S., and Narajan, A. (2018). “Future perspectives of Co-simulation in the smart grid domain,” in 2018 IEEE International Energy Conference (ENERGYCON), Limassol, Cyprus, 2–7 June 2018, 1–6. doi:10.1109/ENERGYCON.2018.8398830
Sun, Y., Li, L., and Dababneh, F. (2016). Plant-level electricity demand response for combined manufacturing system and heating, venting, and air-conditioning (HVAC) system. J. Clean. Prod. 135, 1650–1657. doi:10.1016/j.jclepro.2015.12.098
Tao, F., Cheng, J., Qi, Q., Zhang, M., Zhang, H., and Sui, F. (2018). Digital twin-driven product design, manufacturing and service with big data. Int. J. Adv. Manuf. Technol. 94 (9), 3563–3576. doi:10.1007/s00170-017-0233-1
Thiede, S., Schönemann, M., Kurle, D., and Herrmann, C. (2016). Multi-level simulation in manufacturing companies: The water-energy nexus case. J. Clean. Prod. 139, 1118–1127. doi:10.1016/j.jclepro.2016.08.144
Thiede, S., Seow, Y., Andersson, J., and Johansson, B. (2013). Environmental aspects in manufacturing system modelling and simulation—state of the art and research perspectives. CIRP J. Manuf. Sci. Technol. 6 (1), 78–87. doi:10.1016/j.cirpj.2012.10.004
VanDerHorn, E., and Mahadevan, S. (2021). Digital twin: Generalization, characterization and implementation. Decis. support Syst. 145, 113524. doi:10.1016/j.dss.2021.113524
Venugopal, M., Eastman, C. M., Sacks, R., and Teizer, J. (2012). Semantics of model views for information exchanges using the industry foundation class schema. Adv. Eng. Inf. 26 (2), 411–428. doi:10.1016/j.aei.2012.01.005
Wright, A. J., Oates, M. R., and Greenough, R. (2013). Concepts for dynamic modelling of energy-related flows in manufacturing. Appl. Energy 11, 1342–1348. doi:10.1016/j.apenergy.2013.01.056
Zeigler, B. (2021). DEVS-based building blocks and architectural patterns for intelligent hybrid cyberphysical system design. Information 12 (12), 531. doi:10.3390/info12120531
Zeigler, B. P. (2006). “Embedding DEV&DESS in DEVS,” in Proc. DEVS Integrative Modeling & Simulation Symposium.
Zeigler, B. P., Praehofer, H., and Kim, T. G. (2000). Theory of modeling and simulation: Integrating discrete event and continuous complex dynamic systems. Academic Press.
Zhang, M., Zuo, Y., and Tao, F. (2018). “Equipment energy consumption management in digital twin shop-floor: A framework and potential applications,” in 2018 IEEE 15th International Conference on Networking, Sensing and Control (ICNSC), Zhuhai, China, 27-29 March 2018, 1–5. doi:10.1109/ICNSC.2018.8361272
Keywords: building information modeling, modular digital twins, hybrid simulation, dynamo, energy modeling, holistic industrial modeling, industrial facilities
Citation: Gourlis G and Kovacic I (2022) A holistic digital twin simulation framework for industrial facilities: BIM-based data acquisition for building energy modeling. Front. Built Environ. 8:918821. doi: 10.3389/fbuil.2022.918821
Received: 12 April 2022; Accepted: 05 September 2022;
Published: 28 September 2022.
Edited by:
Abid Nadeem, Nazarbayev University, KazakhstanReviewed by:
Saeed Reza Mohandes, The University of Manchester, United KingdomHande Aladağ, Yıldız Technical University, Turkey
Copyright © 2022 Gourlis and Kovacic. This is an open-access article distributed under the terms of the Creative Commons Attribution License (CC BY). The use, distribution or reproduction in other forums is permitted, provided the original author(s) and the copyright owner(s) are credited and that the original publication in this journal is cited, in accordance with accepted academic practice. No use, distribution or reproduction is permitted which does not comply with these terms.
*Correspondence: Georgios Gourlis, georgios.gourlis@tuwien.ac.at