Baseline investigation on enzyme induced calcium phosphate precipitation for solidification of sand
- 1Department of Engineering Technology, Faculty of Technology, University of Jaffna, Kilinochchi, Sri Lanka
- 2Department of Socio-Environmental Engineering, School of Engineering, Hokkaido University, Sapporo, Japan
- 3Division of Sustainable Resources Engineering, Graduate School of Engineering, Hokkaido University, Sapporo, Japan
- 4Division of Sustainable Resources Engineering, Faculty of Engineering, Hokkaido University, Sapporo, Japan
Introduction: Bio-cementation processes [namely, microbial induced carbonate precipitation (MICP) and enzyme induced carbonate precipitation (EICP)] have recently become promising techniques for solidifying loose sands. However, these methods release gaseous ammonia to the atmosphere, which is not desirable for real-scale applications. This study aims to propose an enzyme induced calcium phosphate precipitation (EICPP) method as a sustainable direction for the solidification of sand.
Methods: Precipitation of calcium phosphate compound (CPC) was driven through pH-dependent mechanism regulated by enzymatic hydrolysis of urea. The baseline study was designed to consist of a series of precipitation tests and sand column tests, evaluating the influence of various recipes of cementation media (CM) on treatment efficiency. The evaluation program consisted of Unconfined compression tests, precipitation content measurement, scanning electron microscopy (SEM), energy-dispersive X-ray spectroscopy (EDS) and X-ray diffraction.
Results: The observations showed that the content of urea had an important role in proposed EICPP treatment, which determined the extent of the pH increase. This increase had a great influence on 1) utilization of soluble calcium, 2) precipitation content of calcium phosphate, and 3) the morphology of the precipitates. Results of sand column test suggested that injecting CM that consisted of acid-dissolved bone meal, urea and urease enzyme could result in the deposition of insoluble CPC that enabled the solidification of sand particles.
Discussion: The precipitation quantity was found to increase with the increase in urea content; however, the treatment media with high urea content resulted amorphous-like crystals. The plate-like crystals were evidenced in CM with [Ca]/[urea] molar ratio between 1.5–2.0. X-ray Diffraction (XRD) analysis revealed that irrespective of the urea contents, the formed crystals were identified as brushite. Since the final pH of proposed EICPP method could be controllable within acidic-neutral conditions, the emission of ammonia gas would be eliminated.
1 Introduction
The soil improvement projects have been consistently in high demand of ordinary Portland Cement (OPC). The industrial demand of OPC has already exceeded over five billion tons, yet the manufacturing produces 0.81 ton of CO2 for each ton OPC produced, accounting for up to 10% of the global CO2 production (Benhelal et al., 2012). Adopting the principles of sustainable development has therefore become inevitable these days to address various dimensions of environmental concerns such as global warming, greenhouse gas emissions and depletion of non-renewable earth resources. Over the past several years, efforts have been made to develop new construction materials with low embodied energy processes and eco-friendly methodologies (Gomes Correia et al., 2016).
Bio-cementation is a recently emerged soil improvement technology that requires low energy and minimal carbon footprint for the production of cementitious binding agent. 1) Microbial induced carbonate precipitation (MICP) and 2) Enzyme induced carbonate precipitation (EICP) are two popular bio-cementation methods that are contemporarily investigated all over the world for soil improvement and other geotechnical and geo-environmental problems (Hamdan and Kavazanjian, 2016; Almajed et al., 2018; Liu et al., 2019; Mwandira et al., 2019; Chen et al., 2022). The MICP and EICP processes principally rely on the hydrolysis of urea facilitated by urease-positive bacteria and urease enzyme, respectively. During their applications, the source of urease is introduced at the soil surface together with the soluble calcium and urea. When the urea molecules are exposed to the source of urease, they undergo breakdown into ammonium (
In spite of the substantial interest, only a very few studies were loomed up to the field-scale (Omoregie et al., 2020; Sun et al., 2021; Gowthaman et al., 2023). Ivanov et al. (2019) once mentioned that the release of ammonium by-products is a serious drawback of MICP/EICP, which questions the recognition of the technique and confines their progressions at laboratory-scale. As mentioned earlier, ammonium ions are released concurrently with the carbonate ions as the result of urea hydrolysis. The process tends to elevate the pH of the reaction media to above 8.0, providing a favourable condition to the formation of
Few researchers have undertaken an effort to propose solutions against the release of ammonium by-products. For instance, Keykha et al. (2019) demonstrated the use of zeolite to remove ammonium by-products from bio-cement solution prior to its application. Likewise, electro-biocementation was also shown to eliminate the harmful substances (Keykha and Asadi, 2017). To remove the aqueous ammonium remaining in bio-cemented soil, an effective rinsing method was proposed and demonstrated by Lee et al. (2019). Another set of researchers attempted to precipitate the ammonium products as struvite (Yu et al., 2020; Mohsenzadeh et al., 2021). However, become conscious of the fact that most of the above proposals require additional equipment and energy, while some of them make the process more complicated.
Calcium phosphate bio-cementation is relatively a new proposal, in which processes do not involve the release of any harmful substances to the environment (Ivanov et al., 2019). Calcium phosphate compounds (CPCs) are generally sustainable materials (Kohn et al., 2002) and are also known to be a typical construction material with desirable strength characteristics (Ginebra et al., 1997). It is worth bearing in mind that the bone skeleton, teeth and most of the human hard tissues are the constitutes of CPCs (Toshima et al., 2014), indicating that they risk-free to be established as geo-material. The interesting point is that the solubility of CPCs is reliant on the pH of the medium (Tung, 1998). That is to say, the acidic medium entailing of soluble calcium and phosphate would result in the deposition of insoluble CPCs when the chemical condition of the medium is transitioned to alkaline. It was also once highlighted by Ginebra et al. (1997) that attributing to self-setting, the CPCs continue to get strengthening over the time. It is noteworthy, in contrary to OPC, the CPCs can be recuperated by re-excavating and can be reused as agricultural fertilizer (Akiyama and Kawasaki, 2012).
Early research works focused on chemical derivation of CPCs for improving sandy materials. For instance, diammonium phosphate and calcium acetate solutions were mixed together with the sand to mineralize CPCs within pore voids; additives were also combined occasionally to further enhance the stiffness characteristics (Akiyama and Kawasaki, 2012; Kawasaki and Akiyama, 2013). There were two major obstacles reported in the above approach: 1) difficulty in regulating the pH and reaction rate and 2) inadequate formation of CPCs during pre-mix method, indicating that there is still a need for an effective cementation mechanism that is competent to regulate and control the reaction extents and to achieve desirable treatment level.
Enzymatic urea hydrolysis is an energy-efficient process and has high potential to govern the pH at varying levels, thereupon effectively regulating the reactions. This study aims to propose a bio-cement method referred to as “enzyme induced calcium phosphate precipitation (EICPP)” as a promising pathway for solidifying the sand. Bone meal was used herein as the source of calcium and inorganic phosphate. Precipitation of CPCs was systematically driven through pH-dependent mechanism regulated by enzymatic hydrolysis of urea. The baseline study was designed to consist of a series of precipitation tests and sand column tests, evaluating the influence of various recipes of cementation media (CM) on treatment efficiency. It should be noted that the proposal might resolve the long-standing problem in typical bio-cement processes (i.e., the release of gaseous ammonia), while making it more viable for large-scale implications.
2 Materials and methods
2.1 Acid urease and activity measurement
The commercially available acid urease, called Nagapshin, was used in this research work; the manufacturer of the product was Nagase Chemtex Corporation (Kyoto, Japan). The urease activity of the acid urease under different concentrations of urea and at different pH levels were assessed by indophenol spectrophotometry method (Bolleter et al., 1961).
The enzyme solution (hereinafter referred to as ES) was prepared by dissolving 4 g acid urease into 1 L distilled water (i.e., the concentration of 4 g/L). 1 mL of the ES was then added to urea prepared in phosphate buffer solution (50 mL) to evaluate the activity of acid urease at different pH levels (pH ranged between 4–8). At each pH condition, the buffer solutions were prepared with three different urea concentrations, ranging from 0.025 mol/L–1.0 mol/L. The ammonium ions produced as the consequence of urea hydrolysis tend to react with phenol in the presence of hypochlorite, resulting in the formation of blue color indophenol dye. To determine the rate of change in intensity of the dye, the optical density of the solutions that had been sampled at every 5 min interval were measured at the wave length of 630 nm (OD630). Consequently, the rate of the hydrolysis of urea was determined with the aid of the calibration curve that had been developed between the intensity of the dye and concentration of ammonium ions.
2.2 Preparation of bonemeal solution
Bone meal powder used in this research work was bought from Tamagoya Company (Ibaraki, Japan). The bone meal powder is basically produced by crushing the steamed cow bones into fines, consisting of calcium and phosphate in the chemical form of hydroxyapatite
The preparation procedure of bone meal solution is sequentially illustrated in Figure 1A. 50.0 g of bone meal powder was added into 200 mL of distilled water, and subsequently, 60 mL of 2 mol/L concentrated HCl was added to the solution at the rate of 5 mL per every 5 min while keeping the solution in stirring condition. The dissolution of bone meal in HCl in presented in Eq. 1. During the addition of HCl, the pH and concentration of Ca2+ were continuously monitored. The measurements suggested that the pH of the bone meal solution noticeably decreased with the adding of HCl, while the concentration of Ca2+ showed a gradual rise. Once the reading showed negligible changes (i.e., on completion of the dissolution of bone meal), the solution was subjected to vacuum filtering to remove the insoluble residues that remained unreacted. The final pH and concentration of Ca2+ in the produced bone meal solution were found to be 3.4 and 0.22 ± 0.02 mol/L (8.8 g/L) respectively. The concentration of mono-hydrogen phosphate (
2.3 Precipitation test
To study the effect of the concentration of urea used in cementation media (hereinafter referred to as CM) on the efficiency of calcium phosphate precipitation, a set of precipitation tests were performed using standard centrifuge tubes (of 50 mL) without involving any sand material. Table 1 presents the summary of testing cases considered for the precipitation tests. The urea concentration was essentially varied from 0.00 mol/L–0.88 mol/L, and the concentrations were designed in such a way covering the [Ca2+]/[urea] ratios ranging from 0.25–6.0 (Cases 1–8). The CM was prepared by adding the urea and ES into bone meal solution in the following sequence. The urea was first dissolved in 50 mL of bone meal solution, followed by the addition and mixing of 1 mL ES. The added quantity of urea in each testing case is itemized in Table 1. The control test (Case 9) was performed without adding urea to the bone meal solution.
The test tubes were subjected to shaking incubation at 160 rpm and 30°C for 48 h until the completion of any reactions. During the incubation, the changes in 1) concentration of Ca2+ (with the use of LAQUA-twin calcium meter manufactured by HORIBA Advanced Techno Co., Ltd., Japan) and 2) pH (with the use of LAQUA-9615S pH meter manufactured by HORIBA Advanced Co., Ltd., Japan) were continually monitored in all the testing cases. Following the incubation, the solution of each test tube was subjected to filtering using clean filter paper to collect the precipitates. The collected precipitates were then carefully rinsed with distilled water, oven-dried at 60°C for 24 h, and their dry mass were measured. Scanning electron microscopy (SEM) analysis was carried out to assess the precipitates morphology.
2.4 Sand columns and testing
2.4.1 Preparation of sand columns and treatment
The sand used in this study was Toyoura sand. The Toyoura sand is a clean silica sand, classified as poorly graded fine sand as per the Unified Soil Classification System (USCS) (ASTM, 2017), and its mean particle diameter (D50), particle density (ρs), minimum density (ρmin) and maximum density (ρmax) are respectively 0.2 mm, 2.64 g/cm3, 1.335 ± 0.005 g/cm3 and 1.645 ± 0.010 g/cm3.
The sand columns were prepared using syringe molds of 30 mm in diameter and 70 mm in height (refer Figure 1B). The sand was placed into the mold in three layers and compacted uniformly to achieve an average density of 1.5 ± 0.05 g/cm3. In total, nine no. of sand columns were prepared and subjected to calcium phosphate bio-cement treatment. The CM that had been prepared by adding the urea and ES into bone meal solution was simply introduced at the surface of the column (at the rate of 10 mL/min) and permitted to infiltrate under gravitational and capillary effects. The sand columns were treated using CM prepared with different [Ca2+]/[urea] molar ratio varied between 0.25–6.0, and the recipes of CM were essentially kept to be in line with those of precipitation test cases (refer Table 1). Each column was subjected to the percolation of 20 mL of CM for every 24 h, until experiencing a considerable decrease in permeation of CM. It should be noted, however, 20 no. of treatments were targeted for each sand column. For the comparison purpose, a control column was simultaneously treated using CM prepared with no urea content.
At the end of the treatment process, sufficient amount of distilled water was percolated through the sand columns in order to eliminate the unreacted chemicals which might yield additional products with the time. The molds were then carefully cut longitudinally in both sides, and the sand columns were recovered from the molds without any disturbances.
2.4.2 Needle penetration test
Needle penetration test was performed in accordance with the methods recommended by Japanese Geotechnical Society (JGS) (JGS, 2012) to determine the unconfined compressive strength (UCS) of treated sand columns. The penetrometer used in this study was SH-70 manufactured by Maruto Testing Machine Company, Tokyo. The sand columns were positioned laterally, and the needle held upright was penetrated into the columns at three different depth levels (i.e., 1 cm, 3.5 cm and 6 cm measured from the surface of the columns). The maximum penetration resistance and depth of penetration that had been read from the penetrometer scale during the testing were used to determine the UCS values.
2.4.3 Determination of precipitation contents
The acid-reaction method was used to measure the quantity of the precipitates, in compliance with the methodology proposed in the previous work (Fukue et al., 1999). In this method, the representative cemented sand with known dry weight was subjected to the reaction with hydrochloric acid (2 mol/L concentrated) in a closed system. Any changes in the internal pressure during the reaction process were scrutinized with the aid of manometer assembled with the closed system. Following the reaction, the remaining sand material was rinsed well using distilled water, and the dry weight was measured again. It is known that the compounds of calcium (e.g., carbonates, phosphates, and sulfates) are intrinsically soluble in concentrated hydrochloric acid; thus, the total weight of the precipitates was assessed by the difference between the dry weights of the sand before and after subjected to acid-reaction. Although the calcium phosphate compounds were expected to be the prime precipitates, there had been a likelihood for trivial formation of calcium carbonate, as the result of urea hydrolysis. Pressure variations recorded during the acid reaction (attributed to the release of CO2 gas) were used to estimate the mass of the crystallized calcium carbonate. Consequently, the precipitated quantity of CPCs was determined by deducting the quantity of calcium carbonate from the total precipitation quantity.
2.5 Microscale and identification analysis
The representative samples collected in different experimentations were oven-dried at 60°C for 48 h and subjected to scanning electron microscopy (SEM), energy-dispersive X-ray spectroscopy (EDS) and X-ray diffraction (XRD) analyses. The SEM-EDS analysis was carried out using energy dispersive X-ray fluorescence spectrometer (Model: JSM-IT200-JEOL; manufactured in Tokyo, Japan), at an accelerating voltage of 15 kV. Before subjecting to the analysis, the samples were coated using the carbon coater (Model: EC-32010CC-JEOL; manufactured in Tokyo, Japan). XRD analysis was performed on the samples using diffractometer (Model: MultiFlex-Rigaku; manufactured in Tokyo, Japan); under CuKα X-ray source that operates at 40 kV and 40 mA. The powdered samples were subjected to testing at the scan rate of 6.5°/min and at angles between 5 and 70° (2θ).
3 Results
3.1 Enzymatic response of acid urease
It is known that the solubility of CPCs greatly relies on the pH of the neighboring environment, and the pH is controlled herein by varying the content of urea. It was therefore inevitable to evaluate the performance of acid urease under different 1) pH conditions and 2) urea concentrations, and which was determined by indophenol spectrophotometry method.
Figure 2 presents the variation of urease activity under different pH levels (4.0–8.0) and different concentrations of urea (0.025 mol/L ∼ 1.0 mol/L). It could be seen that the optimum activity of acid urease falls in the pH range between 4.0 and 5.0. There is a marginal increase in the urease activity when the pH increases from 4.0 to 5.0; however, the activity drops drastically when the pH increases to above 5.0, indicating the denaturing of acid urease towards alkaline conditions. For instance, 38.6% and 77% performance decrease are observed when the pH varies from 5.0–6.0 and 6.0–7.0 respectively. The enzymatic response observed herein for acid urease is indeed unique, because most of the urease enzymes used in previous studies showed optimal urea hydrolysis under alkaline conditions and severe denaturing under acidic conditions (Neupane et al., 2013; Imran et al., 2021). Since the precipitation of CPCs are projected as the result of pH raise from acidic to neutral/alkaline conditions, the acid urease might be an effective and better choice compared to typical urease products. At the same time, the performance of acid urease appears to be less influenced by the concentration of urea, regardless of the pH conditions. For example, the activities of the acid urease at its optimum pH condition are 66.7, 68.6 and 63.3 U/mg under the urea concentrations of 0.025, 0.1 and 1.0 mol/L respectively.
3.2 Precipitation test
3.2.1 Observations
A series of precipitation tests was performed to evaluate the desired molar ratio of [Ca2+]/[urea] in CM for an effective treatment. The pH and concentration of Ca2+ of the test tube media were measured before and after the 48 h of shaking incubation. Figure 3A shows the pH measurements of the testing cases considered. The pH of the CM before the test was around 3.4, and a considerable increase was noticed in almost all the cases (Case 1–8), except the control (Case 9). The contributory for the observed pH escalation could be the hydrolysis of urea facilitated by acid urease. In technical words, the ammonium that are produced during urea hydrolysis tend to dissolve, hence releasing hydroxide ions; the subsequent consumption of protons by hydroxide ions results in the increase of pH in reaction medium (Martinez et al., 2013; Choi et al., 2017). It could also be seen that more or less of the [Ca2+]/[urea] ratio would result in decrease or increase in the final pH, respectively. For example, the final pH in Case 1 ([Ca2+]/[urea] = 0.25) was around 7.2, while it was only around 3.6 in the case of [Ca2+]/[urea] = 6.0 (Case 8). Apparent pH increase was not observed in the control testing case (Case 9), in which no urea was added.
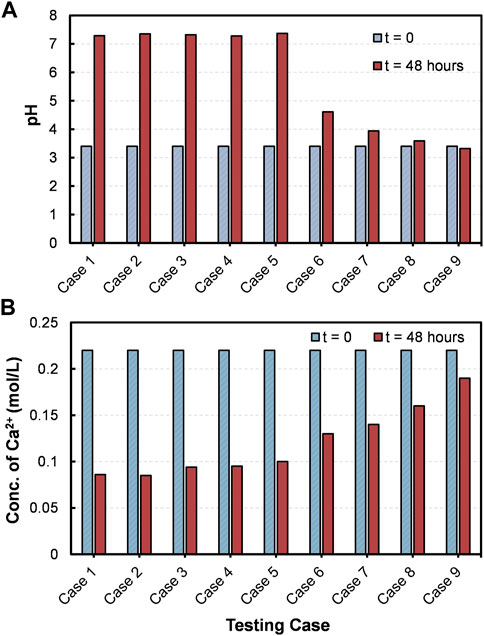
FIGURE 3. (A) pH and (B) Concentration of Ca2+ measured in CM of different cases before and after precipitation test.
Figure 3B presents the measurements of Ca2+ concentration. The initial concentration of Ca2+ was 0.22 ± 0.02 mol/L, and an observable decrease in the final concentration was observed in all the testing cases (Case 1–9). This could possibly be attributed to the consumption of Ca2+ ions for the reactions in CM. However, the consumption discloses a decreasing tendency with increasing [Ca2+]/[urea] molar ratio, which is in contrary to the tendency observed for pH. Around 61% consumption of Ca2+ was witnessed in the case of [Ca2+]/[urea] = 0.25 (Case 1), whereas, for the case of [Ca2+]/[urea] = 6.0 (Case 8), it was only about 27% (the % value is approximately 2.3-fold lower than that of Case 1).
Before the addition of ES, as seen in Figure 4A, a clear transparent CM could be noticeable in the centrifuge tubes. Once the ES was added to CM, the clarity of the media decreased at varying rates depending on the testing cases. A rapid loss of solution transparency could be seen in Case 1, suggesting that the formation of precipitates had begun immediately. By the end of the testing (i.e., after 48 h), whitish color precipitates were perceived at the bottom of all the tubes, but with varying quantities (Figure 4B). The results of the quantitative analysis are presented in Figure 5. The optimum quantity of precipitation, 1.39 g for 50 mL CM, was achieved in the Case 4 ([Ca2+]/[urea] of 1.5). Besides, precipitated quantity of above 1.30 g were achieved all together in five number of cases, Cases 1–5.
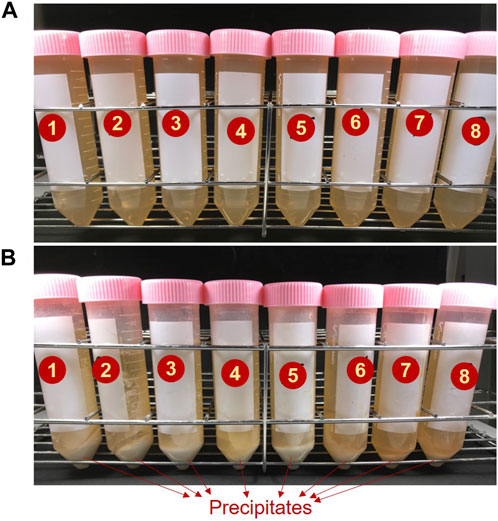
FIGURE 4. The appearance of the CM in centrifuge tubes, (A) before and (B) after subjected to 48 h of shaking incubation.
The observations indicate that the content of urea had a great influence in the chemical changes of CM, determined the following: 1) extent of pH increase, 2) consumption of Ca2+ and 3) quantity of precipitation. Owing to the hydrolysis of urea, the higher the urea added, the higher the pH increased. As the solubility of CPCs is largely reliant on the pH, the consumption of Ca2+ ions and the quantity of precipitation were also regulated by the content of urea. In another words, the solubility of calcium phosphate tended to decline depending upon the extent of pH increase, thus the Ca2+ ions got crystallized as CPCs.
3.2.2 Morphology of the precipitates
To evaluate the morphology of the precipitates, the SEM analysis was carried out to the precipitates from different testing cases, and the images are compared in Figure 6, at two different magnification scales (×500 and ×1,000) for a clear view. Interestingly, different morphologies could be observed for different cases. The precipitates formed in the Cases 1 and 2 are depicted in Figures 6A, B respectively. It could be perceived that the cases with smaller [Ca]/[urea] ratios (i.e., Cases 1–2, wherein the ratios varied between 0.25–0.5) resulted in the formation of non-crystalline amorphous-like nanoparticles. With the increase of [Ca]/[urea] ratio, the precipitates were found to form in defined shapes, indicating the likelihood of crystalline formation. For instance, a combination of plate-like crystals and amorphous-like nanoparticles were observed in Case 5 ([Ca]/[urea] = 2.0) (Figure 6C), while, the precipitates were found to be completely in plate-like and blade-like microstructure for the Case 8 ([Ca]/[urea] = 6.0) (Figure 6D).

FIGURE 6. Micrographs of the precipitates obtained in precipitation tests for the cases with (A) [Ca]/[urea] = 0.25 (Case 1), (B) [Ca]/[urea] = 0.5 (Case 2), (C) [Ca]/[urea] = 2.0 (Case 5) and (D) [Ca]/[urea] = 6.0 (Case 8) at two different magnification scales.
Previous studies disclosed that several factors govern the final size and the morphology the precipitates, such as reaction rate, concentration of Ca2+, ionic effects, supply frequency and interval of resources (Tang et al., 2015; Nawarathna et al., 2018; Wang et al., 2019). The observation suggests that when the concentration of Ca2+ remains constant, the content of urea appears to be the determining factor of precipitate morphology. Attributing to higher final pH, the conversion rate of resources into CPCs was relatively faster in the Cases 1–2, which led to the bulk formation of amorphous-like granular precipitates (with the mean size of <2 μm). Similar formation of precipitates was also witnessed in previous studies for calcium carbonate when subjected to increased rate of reaction (Fujita et al., 2000; Tang et al., 2020). On the other hand, slower conversion rate in Case 8 resulted the formation of plate-like and blade-like crystals (>10 μm in length).
3.3 Sand column test
3.3.1 Observations
With the knowledge obtained from the finding of precipitation tests, a series of sand columns were treated to investigate the applicability and efficiency of the treatment. The CMs established for the precipitation tests were applied to the sand columns (the composition of the CMs can be found in Table 1) once in 24-h basis. It was perceptible that the percolation rate of applied CMs decreased with the increasing treatment number in all the cases (Cases 1–8), except the control column (Case 9). This could possibly be attributed to the formation of precipitates in the pore spaces, resulting in the narrow down of microchannels through which the solution flows. It should be noted that the reduction in percolation rate was more pronounced in the Cases 1 and 2, the columns treated using the CMs with [Ca]/[urea] of 0.25 and 0.5, respectively; by the end of 18 no. of treatments, the above sand columns got clogged and were unable to facilitate further through-flow. For the Cases 3–8, twenty number of treatments were continued as per the experimental design.
Figure 7A exhibits the physical appearance of the sand columns after the treatment. The observation disclosed the cementation of sand throughout the columns in most of the cases, demonstrating the success of the proposed treatment. It is also noticeable that the columns treated using CMs with lower urea content (Cases 7 and 8) posed relatively weaker cementation profile compared to those treated with higher content of urea (Cases 1–6). The bottom column was found to be weakly cemented in the Case 7. The cemented profile of Case 8 was almost same with the appearance of the control column (Case 9) that remained unsolidified.
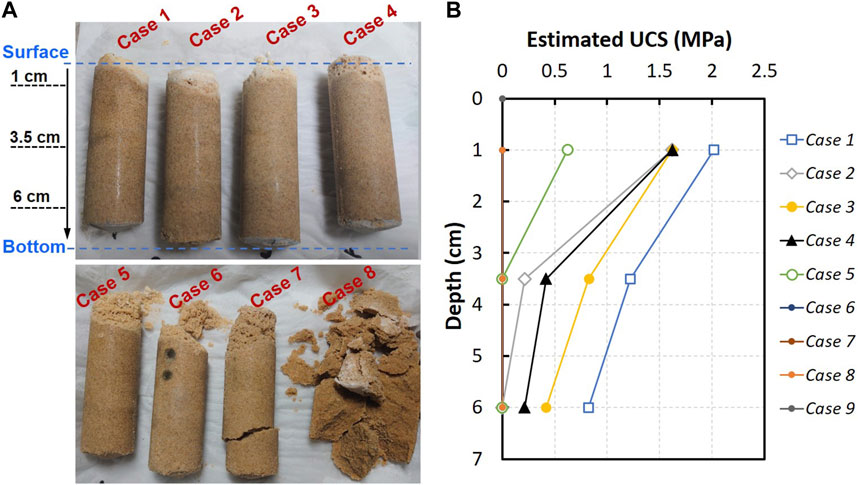
FIGURE 7. (A) Physical appearance of the treated sand columns after recovered from molds and (B) Profile of the estimated UCS with the depth of columns for different testing cases.
3.3.2 Unconfined compressive strength and cementation profile
Figure 7B compares the unconfined compressive strength profiles of the columns treated using different [Ca]/[urea] recipes. Two important things could be perceived: 1) a decrease in the UCS of columns with the increasing [Ca]/[urea] ratio and 2) a decrease in the UCS with the depth of the columns. The sand column treated using CM prepared at [Ca]/[urea] molar ratio of 0.25 (Case 1) exhibited the highest UCS, although lower number of treatments were applied compared to other testing cases. It is perceived that the Case 2 does not follow the trend, although a general trend of decrease in UCS with the increasing [Ca]/[urea] ratio could be observed. One possible reason might be the generation of preferential flow paths through the column of Case 2. Since the surface percolation facilitates a free-draining environment, there is a likelihood for the generation of preferential flow paths, in which the resistance to the percolation is relatively lower than in other flow channels. The soil exposed to these preferential flow paths abundantly receive reagents, often leading to heterogeneity and strange cementation patterns along the flow direction. On the other hand, measurable UCS was not attained all over the specimens in the Cases 6–9. In the Case 5, the UCS was measurable only at the near-surface of the column, while the penetration resistance at further depths appeared to be inadequate for measurement.
Since the cementation is achieved via the surface percolation method in this research work, it is inevitable to quantitatively evaluate the uniformity of cementation. Following the penetration tests, each column was divided into sections along the height, and the quantity of the precipitates were measured at three depth levels (1 cm, 3.5 cm and 6 cm), the same as those tested for UCS. The measured total precipitation content is plotted in Figure 8 against the varying depths measured from the surface. It needs to be mentioned that the tendencies observed in cementation profiles was likely to be in consonance with those of UCS. A heterogeneous cementation profile could be seen in most of the cases: high cementation content was found near the top of the column, and that decreased with the increase in depth. For example, the cementation content found at 1 cm depth of the column treated in Case 1 (CM of [Ca]/[urea] = 0.25) was 12.4%, and which was about 1.9-fold and 2.3-fold higher compared to those found at 3.5 cm and 6 cm depths, respectively.
The heterogeneity observed in the profiles of UCS and cementation content can be elucidated by the localized clogging. As a matter of fact, the formation of cementing agent starts occurring as soon as the ES is mixed with prepared CM (this was evidenced in precipitation test), thus, it is conspicuous that the cementation process had already commenced during the application of CM onto columns. As the CM travelled through the pore spaces of the sand, the precipitates were tended to filter along the flow path with a long-linear reduction. During repeated applications of CM, the accumulation of precipitates caused clogging near the sand surface. A whitish colour layer formed above the column surface further confirmed the occurrence of clogging in most of the specimens (refer to Figure 7A).
It is manifest that the formation of cementing agent is supposed to offer the following two things: 1) cement the soil particles together and 2) fill and reduce the void spaces, thus contributing to the development of mechanical strength (DeJong et al., 2010; Sharma et al., 2022). To envisage how the precipitation quantity influence on strengthening of sand, the UCS values are compiled and plotted against the cementation content in Figure 9. As seen, the UCS revealed a likelihood of linear increase (R2 = 0.8275) with the increase in the quantity of cementing agent. It has to be noted that there may be a threshold quantity of cementation needed to bridge the spaces between sand particles at particle-particle contact points (Lin et al., 2016). In pursuance of the obtained results (Figure 7B; Figure 8), a threshold content of about 4–6% CPC (w/w%) shall be a requisite for a measurable increase in the UCS of EICPP-treated fine sand. It is worthy of note that the required threshold amount was about 1–3% for the case of MICP-treated fine sand (Whiffin, 2004; Lin et al., 2016).
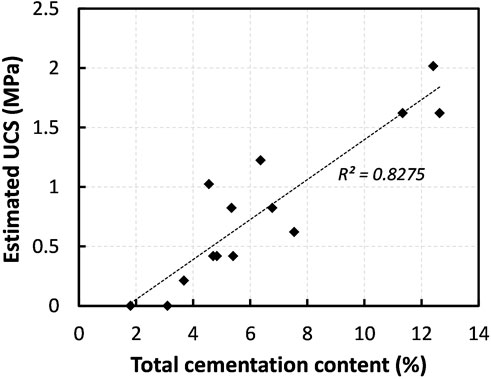
FIGURE 9. Relationship between UCS verses total precipitation content in sand tested (D50 = 0.2 mm) (the compilation of the data).
The results of the quantitative analysis carried out to distinguish the precipitates in each testing case are summarized in Table 2. Regardless of different [Ca]/[urea] ratios, the component that eminently formed in all the cases was found to be calcium phosphate. As suspected, there was also a minor formation of calcium carbonate; this could possibly form as a result of the reaction between the carbonates (released during the hydrolysis of urea) and soluble calcium (already been available in CM). The highest content of calcium carbonate (1.35% ± 0.73% by weight) was attained in Case 1 (the case with highest urea content), whilst the formation became negligible when the added urea content was less (for example, in the Cases 4–9). In fact, the formation of calcium carbonate is highly reliant on pH that determines the speciation of carbonates (Jacob, 1999). A mild-alkaline environment is imperative for the speciation of
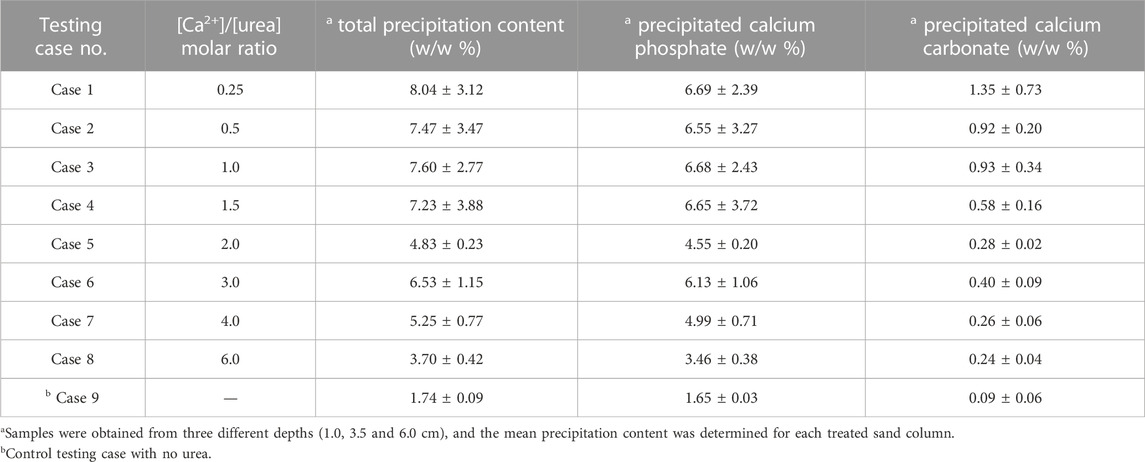
TABLE 2. The average contents of calcium phosphate and calcium carbonate precipitated in treated sand columns.
3.3.3 Characteristics of precipitates
Figure 10 compares SEM images of the sand matrix treated using different CMs (prepared at different [Ca]/[urea] molar ratios). A well aggregated microstructure could be seen for the sand treated using [Ca]/[urea] of 0.25 and 0.5 (refer Figures 10A, B respectively). It should be noted that the typical crystalline microstructures of CPCs were not spotted in whatever the place of treated matrix. Instead, an amorphous-like granules were found to be localized both at intergranular contact points and surface of the sand particles. A blend of amorphous-like and plate-like precipitates were observed in Figure 10C, the micrograph of [Ca]/[urea] of 1.0. Interestingly, the formation of plate-like precipitates could be seen in the cases treated with [Ca]/[urea] of 1.5 and 2.0 (Figures 10D, E). With further increase in [Ca]/[urea] molar ratio, the formation of needle-like crystals was found to be dominant, while a secondary formation of plate-like precipitates was also perceived (refer Figure 10F–H). The formation of similar plate-like and needle-like crystals were also observed in a previous work when the CPCs were derived by mixing diammonium phosphate and calcium acetate in varying concentrations (Akiyama and Kawasaki, 2012). In the case of control (Figure 10I), no crystallization was occurred, yet a net-like deposition was found on surface of sand grains; nevertheless, the sand matrix remained loose as same as the untreated one.
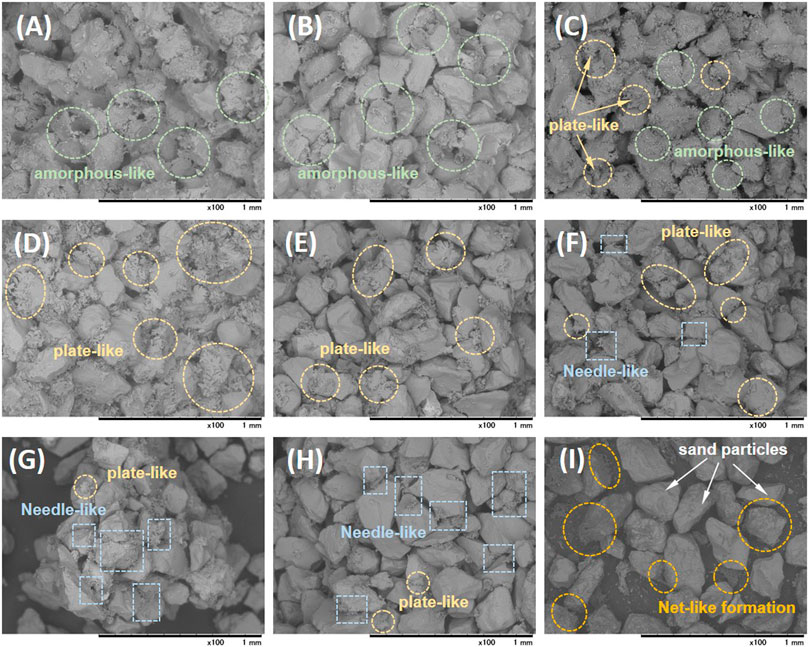
FIGURE 10. The SEM images of the treated sand matrix for the (A) [Ca]/[urea] = 0.25 (Case 1), (B) [Ca]/[urea] = 0.5 (Case 2), (C) [Ca]/[urea] = 1.0 (Case 3), (D) [Ca]/[urea] = 1.5 (Case 4), (E) [Ca]/[urea] = 2.0 (Case 5), (F) [Ca]/[urea] = 3.0 (Case 6), (G) [Ca]/[urea] = 4.0 (Case 7), (H) [Ca]/[urea] = 6.0 (Case 8) and (I) control (Case 9).
Figure 11 presents the results of SEM-EDS analysis for the sand treated using CMs with different [Ca]/[urea] molar ratios. The spectra indicate the major elements that present - calcium (C) and phosphorous (P). Distributions of calcium and phosphorous were found to overlap to the distribution of precipitation in the SEM images. This clearly suggest that the sand particles were bridged by the CPCs. It could also be observed that the content of precipitated CPCs tends to decrease with the increase in [Ca]/[urea] molar ratio of CM; this observation reveals a good agreement with the results obtained in quantitative analysis (summarized in Table 2).
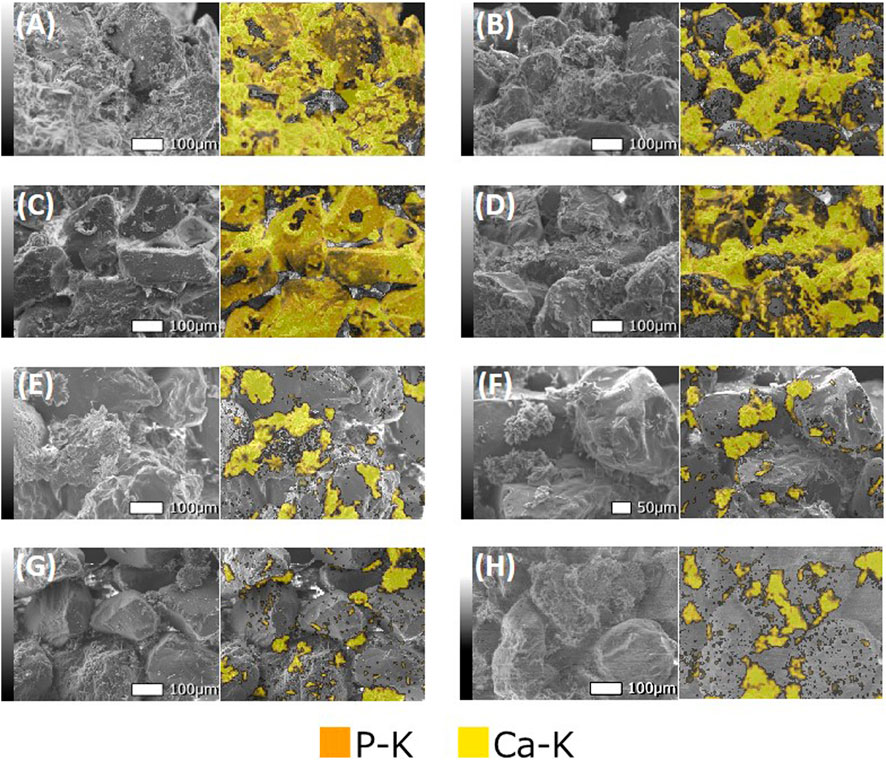
FIGURE 11. The elemental mappings (for Ca and P) of treated sand matrix for the (A) [Ca]/[urea] = 0.25 (Case 1), (B) [Ca]/[urea] = 0.5 (Case 2), (C) [Ca]/[urea] = 1.0 (Case 3), (D) [Ca]/[urea] = 1.5 (Case 4), (E) [Ca]/[urea] = 2.0 (Case 5), (F) [Ca]/[urea] = 3.0 (Case 6), (G) [Ca]/[urea] = 4.0 (Case 7), (H) [Ca]/[urea] = 6.0 (Case 8).
The XRD spectra presented in Figure 12 revealed that the CPC which formed during the treatment was brushite, regardless of different [Ca]/[urea] molar ratios. The chemical reaction for the formation of brushite cement is presented in Eq. 2. It is worth mentioning that brushite precipitates have a number morphologies, and their formation reported to be governed by several factors such as initial pH of the medium, fluctuations in pH, initial concentration of soluble calcium and phosphate (Toshima et al., 2014). It is therefore clear that the difference observed in precipitates’ morphology might possibly be attributed to the changes in pH.
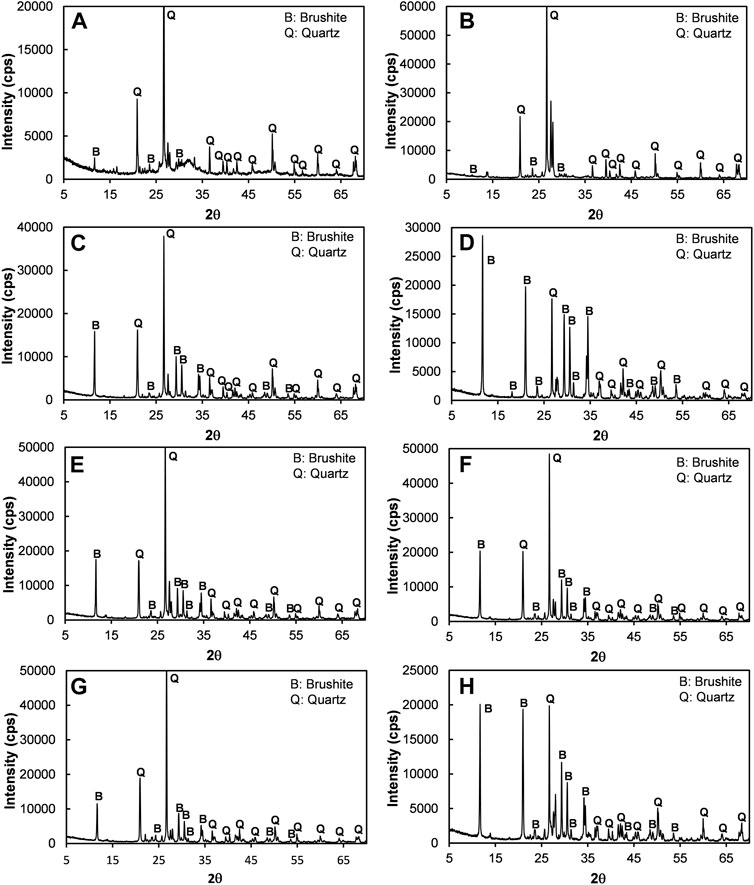
FIGURE 12. The XRD analysis for the test cases of (A) [Ca]/[urea] = 0.25 (Case 1), (B) [Ca]/[urea] = 0.5 (Case 2), (C) [Ca]/[urea] = 1.0 (Case 3), (D) [Ca]/[urea] = 1.5 (Case 4), (E) [Ca]/[urea] = 2.0 (Case 5), (F) [Ca]/[urea] = 3.0 (Case 6), (G) [Ca]/[urea] = 4.0 (Case 7), (H) [Ca]/[urea] = 6.0 (Case 8).
4 Discussion
It is manifest that the acid urease played a vital role, induced the hydrolysis of urea in the early stage of the reactions (i.e., under acidic conditions) and contributed to the increase of solution pH. The insoluble CPCs tended to precipitate once the pH of the bone-meal medium was subjected to an increase. When the solution pH surpassed neutral conditions, the ureolytic performance of acid urease became trivial, resulted in the instinctive hindering of urea hydrolysis.
The desired content of urea in CM can generally be defined as the content that resulted in both high precipitation mass and high precipitation efficiency (Almajed et al., 2018). The summary of the vital data sets is detailed in Table 3. It can be seen that with the increase of the urea content, 1) the consumption of Ca2+, 2) precipitation content and 3) UCS were found to increase. However, the cases with higher urea content ([Ca]/[urea] of 0.25–0.5) exhibited the formation of amorphous brushite. Worth mentioning, the stability of the crystals would vary depending on the morphology developed. Since the amorphous brushite is the least stable form of brushite, the cases with higher urea content cannot be concluded as optimum. This indicates that a careful attention must be paid in choosing the content of urea. For an effective application of EICPP, the content of urea needs to be maintained at possible low level in the CM. The CMs with [Ca]/[urea] of 1.5–2.0 are likely to show the optimum response, wherein the brushite precipitates formed as regular plate-like crystals which is the most stable crystalline form of brushite. Relatively higher UCS and cementation content were also achieved in those cases, suggesting that the recipes can be reliable for any recommendations.
Considering the typical bio-cementation methods (such as MICP and EICP), the proposal offers two major advantages: 1) reduced production of ammonium ions and 2) substantial minimizing in the release of harmful ammonia gas. The concentrations of urea and calcium used in the MICP/EICP cementation media are generally in the range between 0.5–1.0 mol/L (at [Ca]/[urea] mola ratio of 1.0) (Putra et al., 2020; Tang et al., 2020). Given consideration to the optimum case, the concentration of urea used herein to prepare CM was 0.22 mol/L ([Ca]/[urea] of 1.0). The comparison suggest that the proposed method can potentially decrease the production of total ammonium by around 50%–75%. Since the maximum pH observed in CMs of different testing cases was lesser than 7.5 (refer Table 3), the speciation of aqueous ammonium into gas was unobtainable. It was once reported that about 5.8 g of ammonia gas is released to the environment during the injection of 1 L MICP/EICP cementation solution (Yu et al., 2020).
The requirement of urea in MICP/EICP processes was generally in the range between 0.5–1.0 mol/L (equivalent to 30–60 g/L), while the requirement in the proposal was only around 0.22 mol/L (equivalent to 13.2 g/L). This indicates that the proposed EICPP method could reduce the requirement of urea by 2.2–4.5 times when compared with MICP/EICP processes. Unlike MICP/EICP methods those need calcium source for cementation, the EICPP method revealed the successful utilization of bone meal as the source of calcium and phosphate. The urease enzymes are extremely expensive, and the price of the acid urease was once reported to be 375 JPY/g (Gowthaman et al., 2021). One thing should be noted, the effectiveness of bio-cementation method depends not only on technical aspects, but also on the economic status. Since the cost of the acid urease appear to be unaffordable, thus necessitating the search for possible cheaper alternatives. As emphasized by Ivanov et al. (2019), a substantial cost-cut can be expected if the commercial acid urease is replaced by acidotolerant urease producing bacteria. The use of ureolytic lactic acid bacteria (such as Lactobacillus reuteri and Lactobacillus fermentum) is one potential options (Suzuki et al., 1979). Nevertheless, a careful investigation on bio-safety aspects is inevitable prior to the use of those bacteria.
In regards to the real-scale applications, appropriate treatment schemes and optimization are essential for a uniform treatment. The heterogeneity that was evidenced in cemented profiles of all the treated soil columns appears to confine the application level of the proposal. It was previously reported that the uniformity across the treatment zone largely depends on the pore-throat size of the soil (Cheng and Cord-Ruwisch, 2014). The observations herein confirmed that the fine sand, owing to its smaller pore-throat size, is more prone to the localized clogging and may be more compatible for the applications such as erosion control, infiltration control and near-surface stabilizations. If deeper treatments in fine-grained soils is desired, mechanical mixing (either in situ or ex situ) may be suitable, rather the surface percolation methods. A future work may also be recommended to investigate the viability of EICPP on gravels and coarse-grained sands, which would help to disclose the complete knowledge of the proposal.
There may be a concern that how the bone-derived cementing agent compete with the industrial requirement. As per the statistics, the demand of the industrial cement has already exceeded five billion tons, whereas, one hundred and thirty million tons of bone residues are produced by global slaughter industries in every year. Though the proposed EICPP method cannot satisfy the demand of the industrial cement, it can still partly eliminate the use of OPC, thus contributing for a sustainable built environment.
5 Conclusion
In this baseline study, an enzyme induced calcium phosphate precipitation (EICPP) method was proposed and demonstrated at the elementary-scale for the solidification of sand. The urea hydrolysis was systematically utilized to elevate the pH from acidic to neutral levels, hence facilitating the precipitation of insoluble CPCs. The study was designed to consist of a series of precipitation tests and sand column tests, and various recipes of CM were comprehensively studied. The following key conclusions were drawn from this study.
i) Precipitation test suggested that the content of urea in CM is the key factor that determines the extent of pH increase during the reaction. The pH increase is found to influence the following: consumption of Ca2+, precipitation content and the morphology of the formed crystals.
ii) Sand column test demonstrated that injecting CM that consisted of acid-dissolved bone meal, urea and ES could result in the formation of insoluble CPCs that bind the sand particles together. The UCS and precipitation quantity was found to increase with the increasing urea content in CM. The UCS and the content of cementation were achieved up to 2.0 MPa and 12.6% in treated sand columns. However, a heterogeneity was observed in the profiles of UCS and cementation content. Moreover, the threshold content of about 4–6% CPC was found to be a requisite for a measurable increase in the UCS of EICPP-treated fine sand.
iii) SEM analysis indicated that the precipitates could cement the adjacent sand particles, coat the grain surface, and fill the void spaces, thus contributed to the stiffening of skeleton. Different morphologies of CPCs were attained when treated by CM prepared at different [Ca]/[urea] molar ratios. XRD analysis showed that the crystals formed at different [Ca]/[urea] were brushite. The formation of regular plate-like crystals, the stable crystalline form of brushite, was witnessed in the cases with [Ca]/[urea] of 1.5 and 2.0.
iv) Compared with typical bio-cement methods, the proposed EICPP offers the following benefits: 1) reduced production of ammonium, 2) eliminating the release of gaseous ammonia, 3) sustainable utilization of bone waste as cementing resource for sand solidification, and 4) reduced treatment cost. With numerous environmental and economical benefits, more future works are recommended for promoting the proposed EICPP towards field-scale.
Data availability statement
The raw data supporting the conclusion of this article will be made available by the authors, without undue reservation.
Author contributions
SG: Conceptualization, Investigation, Methodology, Writing–original draft. MY: Data curation, Methodology, Writing–review and editing. MC: Data curation, Methodology, Writing–review and editing. KN: Supervision, Writing–review and editing. SK: Funding acquisition, Supervision, Writing–review and editing.
Funding
The author(s) declare financial support was received for the research, authorship, and/or publication of this article. This research work was partly supported by JSPS KAKENHI, grant number JP19H02229, Japan, and the authors greatly acknowledge the support.
Acknowledgments
This article may be a tribute to the late Professor, Prof. Volodymyr Ivanov, who was the inspiration for the success of the presented work, during his visit to Hokkaido University, Japan [FY2019JSPS Invitational Fellowships for Research in Japan (Short-term)—ID S19124]. The authors would like to express sincere gratitude.
Conflict of interest
The authors declare that the research was conducted in the absence of any commercial or financial relationships that could be construed as a potential conflict of interest.
The handling editor HAK declared a past co-authorship with the author SK.
Publisher’s note
All claims expressed in this article are solely those of the authors and do not necessarily represent those of their affiliated organizations, or those of the publisher, the editors and the reviewers. Any product that may be evaluated in this article, or claim that may be made by its manufacturer, is not guaranteed or endorsed by the publisher.
References
Akiyama, M., and Kawasaki, S. (2012). Novel grout material comprised of calcium phosphate compounds: in vitro evaluation of crystal precipitation and strength reinforcement. Eng. Geol. 125, 119–128. doi:10.1016/j.enggeo.2011.11.011
Almajed, A., Khodadadi Tirkolaei, H., and Kavazanjian, E. (2018). Baseline investigation on enzyme-induced calcium carbonate precipitation. J. Geotechnical Geoenvironmental Eng. 144, 04018081. doi:10.1061/(asce)gt.1943-5606.0001973
ASTM (2017). Standard practice for classification of soils for engineering purposes (unified soil classification System). West Conshohocken, PA: American Society for Testing and Materials.
Benhelal, E., Zahedi, G., and Hashim, H. (2012). A novel design for green and economical cement manufacturing. J. Clean. Prod. 22, 60–66. doi:10.1016/j.jclepro.2011.09.019
Bolleter, W. T., Bushman, C. J., and Tidwell, P. W. (1961). Spectrophotometric determination of ammonia as indophenol. Anal. Chem. 33, 592–594. doi:10.1021/ac60172a034
Chen, M., Gowthaman, S., Nakashima, K., and Kawasaki, S. (2022). Influence of humic acid on microbial induced carbonate precipitation for organic soil improvement. Environ. Sci. Pollut. Res. 30, 15230–15240. doi:10.1007/s11356-022-23157-8
Cheng, L., and Cord-Ruwisch, R. (2014). Upscaling effects of soil improvement by microbially induced calcite precipitation by surface percolation. Geomicrobiol. J. 31, 396–406. doi:10.1080/01490451.2013.836579
Choi, S. G., Chu, J., Brown, R. C., Wang, K., and Wen, Z. (2017). Sustainable biocement production via microbially induced calcium carbonate precipitation: use of limestone and acetic acid derived from pyrolysis of lignocellulosic biomass. ACS Sustain Chem. Eng. 5, 5183–5190. doi:10.1021/acssuschemeng.7b00521
DeJong, J. T., Mortensen, B. M., Martinez, B. C., and Nelson, D. C. (2010). Bio-mediated soil improvement. Ecol. Eng. 36, 197–210. doi:10.1016/j.ecoleng.2008.12.029
Feng, K., and Montoya, B. M. (2014). “Behavior of bio-mediated soil in k 0 loading,” in New Frontiers in geotechnical engineering (Reston, VA: American Society of Civil Engineers), 1–10. doi:10.1061/9780784413456.001
Fujita, Y., Grant Ferris, F., Daniel Lawson, R., Colwell, F. S., and Smith, R. W. (2000). Subscribed content calcium carbonate precipitation by ureolytic subsurface bacteria. Geomicrobiol. J. 17, 305–318. doi:10.1080/782198884
Fukue, M., Nakamura, T., and Kato, Y. (1999). Cementation of soils due to calcium carbonate. Soils Found. 39, 55–64. doi:10.3208/sandf.39.6_55
Ginebra, M. P., Fernández, E., De Maeyer, E. A. P., Verbeeck, R. M. H., Boltong, M. G., Ginebra, J., et al. (1997). Setting reaction and hardening of an apatitic calcium phosphate cement. J. Dent. Res. 76, 905–912. doi:10.1177/00220345970760041201
Gomes Correia, A., Winter, M. G., and Puppala, A. J. (2016). A review of sustainable approaches in transport infrastructure geotechnics. Transp. Geotech. 7, 21–28. doi:10.1016/j.trgeo.2016.03.003
Gowthaman, S., Koizumi, H., Nakashima, K., and Kawasaki, S. (2023). Field experimentation of bio-cementation using low-cost cementation media for preservation of slope surface. Case Stud. Constr. Mater. 18, e02086. doi:10.1016/j.cscm.2023.e02086
Gowthaman, S., Nakashima, K., and Kawasaki, S. (2020). Freeze-thaw durability and shear responses of cemented slope soil treated by microbial induced carbonate precipitation. Soils Found. 60, 840–855. doi:10.1016/j.sandf.2020.05.012
Gowthaman, S., Yamamoto, M., Nakashima, K., Ivanov, V., and Kawasaki, S. (2021). Calcium phosphate biocement using bone meal and acid urease: an eco-friendly approach for soil improvement. J. Clean. Prod. 319, 128782. doi:10.1016/j.jclepro.2021.128782
Hamdan, N., and Kavazanjian, E. (2016). Enzyme-induced carbonate mineral precipitation for fugitive dust control. Geotechnique 66, 546–555. doi:10.1680/jgeot.15.P.168
Imran, M. A., Nakashima, K., and Kawasaki, S. (2021). Bio-mediated soil improvement using plant derived enzyme in addition to magnesium ion. Cryst. (Basel) 11, 516. doi:10.3390/cryst11050516
Ivanov, V., Stabnikov, V., and Kawasaki, S. (2019). Ecofriendly calcium phosphate and calcium bicarbonate biogrouts. J. Clean. Prod. 218, 328–334. doi:10.1016/j.jclepro.2019.01.315
Jacob, D. (1999). in Introduction to atmospheric chemistry (United States: Princeton University Press), 87–114.Geochemical cycles
JGS (2012). Japanese standards and explanations of geotechnical and geoenvironmental investigation methods (3431-2012. Tokyo: Japanese Geotechnical Society, 426–432.
Jiang, N.-J., Tang, C.-S., Yin, L.-Y., Xie, Y.-H., and Shi, B. (2019). Applicability of microbial calcification method for sandy-slope surface erosion control. J. Mater. Civ. Eng. 31, 04019250. doi:10.1061/(ASCE)MT.1943-5533.0002897
Kawasaki, S., and Akiyama, M. (2013). Enhancement of unconfined compressive strength of sand test pieces cemented with calcium phosphate compound by addition of various powders. Soils Found. 53, 966–976. doi:10.1016/j.sandf.2013.10.013
Keykha, H. A., and Asadi, A. (2017). Solar powered electro-bio-stabilization of soil with ammonium pollution prevention System. Adv. Civ. Eng. Mater 6, 20170001. doi:10.1520/ACEM20170001
Keykha, H. A., Mohamadzadeh, H., Asadi, A., and Kawasaki, S. (2019). Ammonium-free carbonate-producing bacteria as an ecofriendly soil biostabilizer. Geotechnical Test. J. 42, 20170353. doi:10.1520/GTJ20170353
Kohn, M. J., Rakovan, J. F., and Hughes, J. M. (2002). Phosphates: geochemical, geobiological and materials importance (reviews in mineralogy and geochemistry). Washington, DC 20036: The Mineralogical Society of America.
Lee, M., Gomez, M. G., San Pablo, A. C. M., Kolbus, C. M., Graddy, C. M. R., DeJong, J. T., et al. (2019). Investigating ammonium by-product removal for ureolytic bio-cementation using meter-scale experiments. Sci. Rep. 9, 18313. doi:10.1038/s41598-019-54666-1
Lin, H., Suleiman, M. T., Brown, D. G., and Kavazanjian, E. (2016). Mechanical behavior of sands treated by microbially induced carbonate precipitation. J. Geotechnical Geoenvironmental Eng. 142, 04015066–4015071. –13. doi:10.1061/(ASCE)GT.1943-5606.0001383
Liu, S., Wen, K., Armwood, C., Bu, C., Li, C., Amini, F., et al. (2019). Enhancement of MICP-treated sandy soils against environmental deterioration. J. Mater. Civ. Eng. 31, 1–13. doi:10.1061/(ASCE)MT.1943-5533.0002959
Martinez, B. C., DeJong, J. T., Ginn, T. R., Montoya, B. M., Barkouki, T. H., Hunt, C., et al. (2013). Experimental optimization of microbial-induced carbonate precipitation for soil improvement. J. Geotechnical Geoenvironmental Eng. 139, 587–598. doi:10.1061/(ASCE)GT.1943-5606.0000787
Mohsenzadeh, A., Aflaki, E., Gowthaman, S., Nakashima, K., Kawasaki, S., and Ebadi, T. (2021). A two-stage treatment process for the management of produced ammonium by-products in ureolytic bio-cementation process. Int. J. Environ. Sci. Technol. 19, 449–462. doi:10.1007/s13762-021-03138-z
Mwandira, W., Nakashima, K., Kawasaki, S., Ito, M., Sato, T., Igarashi, T., et al. (2019). Efficacy of biocementation of lead mine waste from the Kabwe Mine site evaluated using Pararhodobacter sp. Environ. Sci. Pollut. Res. 26, 15653–15664. doi:10.1007/s11356-019-04984-8
Nawarathna, T. H. K., Nakashima, K., Fujita, M., Takatsu, M., and Kawasaki, S. (2018). Effects of cationic polypeptide on CaCO3 crystallization and sand solidification by microbial-induced carbonate precipitation. ACS Sustain Chem. Eng. 6, 10315–10322. doi:10.1021/acssuschemeng.8b01658
Neupane, D., Yasuhara, H., Kinoshita, N., and Unno, T. (2013). Applicability of enzymatic calcium carbonate precipitation as a soil-strengthening technique. J. Geotechnical Geoenvironmental Eng. 139, 2201–2211. doi:10.1061/(ASCE)GT.1943-5606.0000959
Omoregie, A. I., Palombo, E. A., Ong, D. E. L., and Nissom, P. M. (2020). A feasible scale-up production of Sporosarcina pasteurii using custom-built stirred tank reactor for in-situ soil biocementation. Biocatal. Agric. Biotechnol. 24, 101544. doi:10.1016/j.bcab.2020.101544
Putra, H., Yasuhara, H., Erizal, S., and Fauzan, M. (2020). Review of enzyme-induced calcite precipitation as a ground-improvement technique. Infrastructures (Basel) 5, 66. doi:10.3390/infrastructures5080066
Sharma, M., and Satyam, N. (2021). Strength and durability of biocemented sands: wetting-drying cycles, ageing effects, and liquefaction resistance. Geoderma 402, 115359. doi:10.1016/j.geoderma.2021.115359
Sharma, M., Satyam, N., and Reddy, K. R. (2022). Large-scale spatial characterization and liquefaction resistance of sand by hybrid bacteria induced biocementation. Eng. Geol. 302, 106635. doi:10.1016/j.enggeo.2022.106635
Sun, X., Miao, L., Wang, H., Yin, W., and Wu, L. (2021). Mineralization crust field experiment for desert sand solidification based on enzymatic calcification. J. Environ. Manage 287, 112315. doi:10.1016/j.jenvman.2021.112315
Suzuki, K., Benno, Y., Mitsuoka, T., Takebe, S., Kobashi, K., and Hase, J. (1979). Urease producing species of intestinal anaerobes and their activities. Appl. Environ. Microbiol. 37, 379–382. doi:10.1128/aem.37.3.379-382.1979
Tang, B., Yuan, H., Cheng, L., Zhou, X., Huang, X., and Li, J. (2015). Effects of gallic acid on the morphology and growth of hydroxyapatite crystals. Arch. Oral Biol. 60, 167–173. doi:10.1016/j.archoralbio.2014.09.011
Tang, C. S., Yin, L. Y., Jiang, N. J., Zhu, C., Zeng, H., Li, H., et al. (2020). Factors affecting the performance of microbial-induced carbonate precipitation (MICP) treated soil: a review. Environ. Earth Sci. 79, 94. doi:10.1007/s12665-020-8840-9
Toshima, T., Hamai, R., Tafu, M., Takemura, Y., Fujita, S., Chohji, T., et al. (2014). Morphology control of brushite prepared by aqueous solution synthesis. J. Asian Ceram. Soc. 2, 52–56. doi:10.1016/j.jascer.2014.01.004
Tung, M. S. (1998). “Calcium phosphates: structure, composition, solubility, and stability,” in Calcium phosphates in biological and industrial systems (Boston, MA: Springer US), 1–19. doi:10.1007/978-1-4615-5517-9_1
Türker, M., and Çelen, I. (2007). Removal of ammonia as struvite from anaerobic digester effluents and recycling of magnesium and phosphate. Bioresour. Technol. 98, 1529–1534. doi:10.1016/j.biortech.2006.06.026
van Paassen, L. A., Ghose, R., van der Linden, T. J. M., van der Star, W. R. L., and van Loosdrecht, M. C. M. (2010). Quantifying biomediated ground improvement by ureolysis: large-scale biogrout experiment. J. Geotechnical Geoenvironmental Eng. 136, 1721–1728. doi:10.1061/(ASCE)GT.1943-5606.0000382
Wang, Y., Soga, K., Dejong, J. T., and Kabla, A. J. (2019). Microscale visualization of microbial-induced calcium carbonate precipitation processes. J. Geotechnical Geoenvironmental Eng. 145, 1–13. doi:10.1061/(ASCE)GT.1943-5606.0002079
Whiffin, V. S. (2004). Microbial CaCO3 precipitation for the production of biocement. Austrlia: Murdoch University.
Keywords: bio-cementation, enzyme induced calcium phosphate precipitation (EICPP), urea hydrolysis, cementation media, PH dependency, brushite
Citation: Gowthaman S, Yamamoto M, Chen M, Nakashima K and Kawasaki S (2023) Baseline investigation on enzyme induced calcium phosphate precipitation for solidification of sand. Front. Built Environ. 9:1307650. doi: 10.3389/fbuil.2023.1307650
Received: 05 October 2023; Accepted: 11 December 2023;
Published: 21 December 2023.
Edited by:
Hamed Abdeh Keykha, Buein Zahra Technical University, IranReviewed by:
Nitish Venkateswarlu Mogili, National Institute of Technology, Andhra Pradesh, IndiaHadi Mohamadzade, Buein Zahra Technical University, Iran
Copyright © 2023 Gowthaman, Yamamoto, Chen, Nakashima and Kawasaki. This is an open-access article distributed under the terms of the Creative Commons Attribution License (CC BY). The use, distribution or reproduction in other forums is permitted, provided the original author(s) and the copyright owner(s) are credited and that the original publication in this journal is cited, in accordance with accepted academic practice. No use, distribution or reproduction is permitted which does not comply with these terms.
*Correspondence: Sivakumar Gowthaman, gowtham@tech.jfn.ac.lk