Synthesis and Characterization of NiMo Catalysts Supported on Fine Carbon Particles for Hydrotreating: Effects of Metal Loadings in Catalyst Formulation
- 1Catalysis and Chemical Reaction Engineering Laboratories, Department of Chemical Engineering, University of Saskatchewan, Saskatoon, SK, Canada
- 2Syncrude Edmonton Research Centre, Edmonton, AB, Canada
The by-products collected during the synthesis of carbon nanohorns via the arc discharge synthesis method is comprised of other carbon particles (OCP). At a hydrotreating operating temperature of 370°C, preliminary investigations using a bimetallic catalyst with support originating from the fine fractions of other carbon particles (OCPf) and containing 13 wt% Mo and 2.5 wt% Ni resulted in an HDS and HDN conversion of 78 and 25%, respectively. Variation of metal compositions in catalyst formulation and its impact on hydrotreating activity was therefore considered in this study to enhance the hydrotreating activity of OCPf–supported catalyst, and to determine if the best NiMo/OCPf catalyst achieved from this study could be a viable catalyst for hydrotreating applications. The co-incipient wetness impregnation was used in preparing series of hydrotreating catalysts with Ni and Mo loadings within the range of (2.5–5.0 wt%) and (13–26 wt%) respectively. Overall, the catalyst samples with maximum Ni loading of 5.0 wt% and Mo loadings of either 13 or 19 wt% showed higher dispersion and the ability to form a Type II Ni-Mo-S phase with enhanced activity. The effects of metal compositions on both HDS and HDN activities were correlated with their physicochemical properties.
Introduction
Hydrotreating is a catalytic hydrogenation process that is globally used to upgrade highly contaminated crude oil into high quality products with reduced sulfur, nitrogen, oxygen, and metal content. The hydrotreating process also leads to the conversion of aromatics and olefins in the crude oil into saturated products. Hydrotreating therefore helps to meet the demands for cleaner environment and stricter regulations. Since this process is catalytically driven, development of a hydrotreating catalyst is one way of achieving optimal hydrotreating effect. Apart from the support other key components of the catalyst are the active metals and promoters. Commonly used hydrotreating catalysts are supported-CoMo and -NiMo sulfides, and typical metal loading compositions for Ni (Co) and Mo are within the range of (3–8 wt%) and (10–30 wt%), respectively (Robinson and Dolbear, 2006; Jarullah et al., 2012).
For a hydrotreating catalyst such as NiMo/Al2O3 the main catalytic active sites are the MoS2 edges, and addition of a Ni promoter aids in increasing vacant sites by lowering the binding energy of sulfur present at the edges of MoS2 (Byskov et al., 1997; Grimblot, 1998; Afanasiev and Bezverkhyy, 2007). To some extent, some research work has revealed that the final sulfided phase of the active catalyst is dependent on the extent to which the supported NiMo catalyst in its oxide form becomes sulfided since, sulfidation partially converts these oxide species into their equivalent active Ni (Co)-Mo-S structures. As a result, during catalyst formulation it is important to use a suitable metal composition that would optimize the metal loading on the support, and consequently result in the achievement of maximum hydrotreating activity (Prins et al., 1989; Furimsky, 1998; López and López, 2000).
The Ni (Co)-Mo-S structures exist in two forms (Type I and Type II). Usually, the Type II structure is more active than the Type I structure because, it is rarely attached to the support via Mo-O-Al linkages unlike, the Type I structure which is more bonded to the support. The linkages with the support create some steric hindrances during reactions and in the case of the Type II structure less linkage with the support results in less effect from steric hindrance which makes it easier for reactant molecules to access catalytic active sites. Comparatively, reactant molecules are more hindered from getting to the catalytic active sites in a Type I structure than a Type II structure. During hydrotreating an increase in temperature during sulfidation favors a Type II structure and hydrotreating activities since, stacking is enhanced as temperature increases and this further creates a highly active Type II structure (Vissers et al., 1987; Van Veen et al., 1993). Also, the presence of Type II structures can result in high activities because of their weak metal-support-interactions. Due to this, the use of carbon-supported catalyst in hydrotreating appears to be a good choice in terms of Type II structure formation because, the minimal support interaction that likely occurs makes it possible to sulfide these catalysts even under low temperature conditions into readily transformed Type II structures. On the other hand, for NiMo/γ-Al2O3 catalysts due to the strong metal support interaction sulfidation to Type II structures can be obtained using high sulfidation temperatures. Additionally, the properties at the active sites can be impacted by Mo loading since low Mo loadings are known to be dominated by Type I structures whereas, higher Mo loadings are dominated by Type II structures (Candia et al., 1984; Scheffer et al., 1986).
Use of carbon as a support in heterogenous catalysis has also attracted numerous attentions because of its relative chemical inertness, high porosity, high surface area, retention of its structural integrity, existence in various physical forms and ability to functionalize the carbon material to enhance catalytic activity. Many studies have also demonstrated that the use of carbon-supported catalysts leads to high HDS activities (Duchet et al., 1983; Rana et al., 2020). When given the choice to use carbon as a hydrotreating catalyst support, most researchers resort to carbon black or activated carbon because of their mass availability, low cost, and high surface area. In recent times a plethora of research related to the use of carbon in catalysis is centred around carbon nanotubes and fullerenes, and investigations about their properties and possible applications are still in progress. Use of carbon nanohorns (CNH) as a catalyst support is also in the limelight (Rodriquez-Reinoso, 1998; Falcao and Wudl, 2007; Titirici and Antonietti, 2010; Aryee et al., 2014; Lam and Luong, 2014; Aryee et al., 2021).
CNH is commonly produced using the arc-discharge method and is accompanied by the formation of a chunk by-product (termed OCP), and a fine fraction denoted as OCPf in this study. For anodic type of arcs in which ablation of the anode is prevalent, these by-products usually form on the cathode and fall off or build up with time. Keidar et al. (2011) also added that for anodic arc, a carbonaceous deposit (∼60–70% of the ablated material) inevitably forms on the cathode surface by reason of low thermal conductivity. This carbonaceous deposit can be described as having a crust-like texture with an inner black core that could contain carbon nanotubes, carbon nanoparticles and some graphitic particles. It is also noted to consist of a greyish metallic hard shell on the exterior with no nanotubes present. The appearance of this by-products after an arc experiment was also noted by Saito et al. (1993). In their work, they mentioned that a carbonaceous deposit made up of graphitic tubules and polyhedral particles accumulated on the face of the cathode electrode (Ebbesen and Ajayan, 1992; Saito et al., 1993; Tang et al., 2005; Keidar et al., 2011). Gattia et al. (2006) were of the view that the deposits collected on the cathode after conducting arc-discharge experiments comprised of CNH, CNT, amorphous carbon and carbon nanocages, and their results were not far-fetched from the observations from many arc discharge experiments that mentioned the formation of a rich multiwalled carbon nanotube (MWCNT) among the deposits on the surface of the cathode (Gattia et al., 2006; Arora and Sharma, 2014; Ng and Raitses, 2014; Yeh et al., 2016; Zhang et al., 2019). Yeh et al. (2016) also added that during the arc discharge process, the deposited carbonaceous material on the surface of the cathode and the walls of the reactor vessel contributed to the formation of nanoparticles by acting as an effective cathode electrode that sustained the arc discharge and reaction process. Results from their work also showed that a strong correlation exists between the radial distribution of the arc discharge current, temperature at the surface of the cathode deposit and the various morphologies of the deposits formed on the cathode. The complex nature of the formed nanoparticles is attributed to spatial variations of particle, plasma and heat fluxes from the arc to the deposit. The purity of the nanoparticles within the core area of the deposit are dependent on particle and heat flux from the plasma (Yeh et al., 2016).
The characteristics of the OCP produced in our laboratory and used in this phase of work matches the descriptions in the aforementioned paragraph. Our laboratory synthesis of CNH revealed that the OCPf material can be simultaneously produced with CNH and the yield of OCPf was more than twice the CNH material of interest. Also, from TEM analysis a micrograph of the OCPf material showed that it comprises of CNH structures. Moreover, a feasibility study using OCPf as a hydrotreating catalyst with Ni and Mo compositions of 2.5 wt% and 13 wt%, respectively resulted in an HDS activity of 78% and an HDN activity of 25% (Aryee, 2019; Aryee et al., 2021). Thus, knowing the benefits of using carbon as a support, and having been convinced from other researchers that the by-products are mainly carbon-based particles. Our goals were to 1) enhance the hydrotreating performance of NiMo/OCPf catalyst by experimenting different combinations of Ni and Mo that would lead to higher HDS and HDN activities and 2) to add value to an otherwise low-value by-product. To our knowledge, this low value by-product has not been attempted for utilization in the past. In addition, since the OCPf material contains CNH materials, results from this hydrotreating study would help to determine the best bimetallic compositions to focus on in developing the best NiMo/CNH catalyst for hydrotreating.
Materials and Methods
The average particle diameter of the OCPf material used as the hydrotreating catalyst support in this study was 250 microns, and it was obtained after a particle separation step following a CNH arc discharge synthesis. In preparation for catalyst formulation, oxygenated functional groups were created on the OCPf support by liquid oxidation. This step is important because it enhances the solubility of the support material and guarantees efficient wettability for metal anchorage since the catalyst preparation involved contacting the OCPf material with catalyst precursor metals in solution. 30 min functionalization time emerged as the best duration for functionalizing OCPf support material based on the results of a series of experimental runs to determine the best condition for OCPf functionalization. Additionally, all OCPf support material was functionalized for 30 min using the same method from a previous description (Aryee et al., 2014). The functionalized supports were then impregnated with Ni (2.5, 3.5 and 5.0 wt%) and Mo (13, 19 and 26 wt%) via the incipient wetness co-impregnation method from their respective aqueous metal precursor solutions containing requisite amount of nickel nitrate hexahydrate [Ni(NO3)2·6H2O], and ammonium heptamolybdate tetrahydrate [(NH4)6Mo7O24·4H2O].
Seven (7) different OCPf-supported catalysts were formulated for this study that were dependent on desired Ni and Mo loading combinations hence, for easy referencing the prepared catalysts were named as xNiyMo/OCPf where; x is the wt% Ni composition and y is the wt% Mo composition used. The wet catalysts that were formulated were oven dried at 110°C overnight. Subsequently, each dried oxidic catalyst was ground and calcined in a furnace at 450°C for 5 h using argon as a carrier gas at 50 ml/min flow rate. Prior to hydrotreating experiments, 5 ml of each powdered catalyst was diluted with 12 ml of 90 mesh inert silicon carbide by way of loading into the reactor in 10–12 layers. Loading was done by alternating between catalyst and SiC and this method of loading in layers was utilized to ensure that both catalyst and inert material were distributed uniformly and can be reproduceable. Consequently, hydrodynamic conditions in the reactor are improved (Al-Dahhan et al., 1995; Mapiour et al., 2010). The top and bottom of the diluted catalyst mix was also packed with 3 mm glass beads, and different mesh sizes (16, 46 and 60) of silicon carbide. The packing was done in such a way that the diluent size increased as it approaches the top and bottom end of the reactor. After the reactor had been loaded, it was sealed firmly, and then transferred and mounted into the hydrotreater assembly. The hydrotreater was pressurized to ∼9.3–9.7 MPa with helium and tested for leaks over 24 h.
In preparation for the hydrotreating experiments, the operating pressure was reduced to 9.0 MPa and kept constant throughout all experimental runs. The catalyst was wetted with a mixture of approximately 100 ml butanethiol (2.9 vol%) and insulating oil (500 ml). A sulfidation process continued for two consecutive days (48 h) after completion of catalyst wetting. Sulfidation temperatures of 193 and 343°C, respectively were used for each of the days, and an LHSV of 1 h−1 was maintained throughout the sulfidation process. Once sulfidation was complete, the sulfiding solution was switched to light gas oil and the catalyst was precoked for 3 days at an LHSV of 2 h−1 and a temperature of 370°C. Thereafter, the hydrotreating tests were executed at three different temperatures (i.e., 330, 350 and 370°C). Each experimental temperature condition was run for 1.5 days and a constant LHSV and pressure of 2 h−1 and 9.0 MPa, respectively were maintained for all the runs. Hydrotreated liquid samples were collected after every 12 h. However, a change in experimental temperature condition led to the discarding of collected samples for the initial 12 h of run before any further storage was done. The collected samples were stripped for 2 h with N2 gas to eliminate the presence of any residual traces of NH3 and H2S in the liquid sample. Sulfur and nitrogen concentrations in the stripped liquid products were further analyzed with the Antek 9000 NS analyzer.
Characterization
N2 Adsorption-Desorption Isotherms
The porous structure of all calcined catalysts was determined using the BET-Micromeritics ASAP 2020 surface area and porosity analyzer. Both the adsorption and desorption isotherm branches, and nitrogen gas adsorbed at 77 K were taken into consideration in the analysis. The Brunauer-Emmett-Teller (BET) method was used in calculating the surface areas whereas, the total pore volume and pore size distribution were determined by the Barett-Joyner-Halenda (BJH) method. Approximately 0.1 g of each sample was outgassed at 200 °C to a residual pressure of <6.6 × 10−4 Pa prior to adsorption.
Thermogravimetric Analysis (TGA)
Thermal stabilities of catalyst samples that had been dried and calcined were analyzed using a TA Q500 series instrument with simultaneous thermogravimetric analysis (TGA)/differential scanning calorimeter (DSC) application. The analysis was carried out by heat treating approximately 15 mg of sample from room temperature to 700 °C at 10°C/min ramp rate and the flow rate of nitrogen used was 60 ml/min.
X-Ray Diffraction (XRD) Analysis
The structure, crystallinity and phase of catalyst samples were examined by XRD analysis with the Bruker D8 Advance powder X-ray diffractometer using CuKα radiation (λ = 0.1541 nm). The X-ray gun was powered at 30 mA and 40 kv. Bragg angle (2θ) was scanned from 1.5 to 10° for low angle X-ray diffraction, and from 10 to 80° for wide angle X-ray diffraction. The sample weight for analysis was about 0.25 g.
CO-Chemisorption
An ASAP 2020 micrometrics instrument was used in conducting CO chemisorption analysis and this enabled the percentage metal dispersion to be calculated in relation to carbon monoxide uptake measured on each catalyst. About 0.10 g of each catalyst sample which had previously undergone a degassing step for 60 min at 110°C was further reduced in situ under hydrogen flow for 2 h at 350°C. Thereafter, the reduced sample was cooled to 35°C and consequently evacuated after attaining a static pressure of less than 1.3 × 10−5 Pa. CO chemisorption measurements corresponding to CO uptake at 35°C were done after CO pulses had passed over the sample. For bimetallic catalysts, Eq. (1) was used in calculating the percentage metal dispersion of the active metals that are available and interact with the adsorbate.
where, %MDISP = percentage metal dispersion, SFCALC = calculated stoichiometry factor, WATOMIC, Mo = atomic weight of first metal, Mo (g/mole), WATOMIC, Ni = atomic weight of second metal, Ni (g/mole), V = volume intercept that was obtained from the line of best fit to the differences in volume between the selected points of the first analysis and the repeated analysis (cm3/g STP), *The volume occupied by 1 mol of gas (cm3 STP/mole of gas) (Micromeritics ASAP, 2020).
High Resolution Transmission Electron Microscopy (HRTEM)
The morphology of each catalyst was analyzed using a JEOL 2011 (200 kv) scanning transmission electron microscope (STEM). In preparation for the analysis, catalyst samples were ground to fine particle size and then a minute quantity was dispersed onto a 200-mesh holey carbon-coated TEM support grid. For every sample, about 5–10 representative images were taken at low to high magnification ranging from 20–250 k times magnification.
Temperature Programmed Reduction (TPR)
H2-temperature programmed reduction (H2–TPR) analysis was conducted in a TPD/TPR Quantachrome AutosorbiQ (United States) equipment to evaluate how the reducibility of the metal species in the catalyst behaved. The gas mixture used in conducting the analysis comprised of 3% H2/N2 (v/v). A catalyst sample weight of 0.1 g was used for the analysis. The TPR analysis procedure involved these steps i.e., purging the sample with helium (He) at 400 °C for an hour to pre-treat the sample, cooling to room temperature, followed by ramping the program from room temperature to 800°C at a ramp rate of 10°C/min as the reducing gas mixture flowed at 30 ml/min. A thermal conductivity detector enabled the monitoring of the hydrogen consumption within the temperature range of interest.
Sulfur and Nitrogen Removal
Total S and N compositions for both untreated and treated gas oil samples were determined using the Antek 9000 NS analyzer. A combustion/fluorescence technique together with the ASTM D5463 standard procedure was used in analyzing the sulfur removal whereas, a combustion/chemiluminescence technique and the ASTM D4629 standard procedure was used to analyze the nitrogen removal.
Results and Discussion
BET Analysis of Pristine OCPf, Functionalized OCPf and OCPf-Supported NiMo Catalysts
Table 1 shows the surface area, pore volume and pore diameter of as-synthesized OCPf, functionalized OCPf, and NiMo/OCPf catalysts with varying Ni and Mo compositions. The functionalized OCPf material was found to be of higher surface area and pore volume than the pristine OCPf due to the presence of defects after functionalization. Contrarily, a decrease in pore diameter was rather observed as the pristine OCPf material was functionalized, and this was due to the breaking of bigger pores, with the average pore diameter being more representative of smaller pores (Karousis et al., 2016). For the different catalysts it was observed that the surface area and pore volume of all the catalysts decreased from the functionalized material due to the plugging of pores by metals. An increment in pore diameter however, occurred after the functionalized OCPf samples had been impregnated with metals to form different catalysts.
There was no significant change in surface area at constant Ni composition of 2.5 wt% as Mo composition was raised from 13 wt% to 19 wt%. On the other hand, as the Ni loading was kept constant at higher compositions (either 3.5 wt% or 5.0 wt%), increased in Mo composition from 13 wt% to 19 wt% resulted in ∼16% decrease in surface area. This is because more pores were blocked as higher Mo loadings were impregnated on the support. Keeping the Mo loading constant at a lower composition of 13 wt% did not bring about any significant change in surface area and pore diameter at increasing Ni composition from 2.5 wt% to 3.5 wt%. However, at a constant Mo loading of 19 wt% both the surface area and pore diameter decreased steadily as Ni compositions increased from 2.5 to 3.5 wt%. Also, the decrease in surface area was significant under this condition. Overall, almost all the catalysts exhibited mesoporous pore diameters and constant pore volume. Unlike all other catalysts, the 5.0wt%Ni26wt%Mo/OCPf catalyst with the highest Ni and Mo compositions exhibited the lowest surface area since its pores were filled with metals having the highest weight compositions during catalyst formulation. Consequently, its pore diameter was high since it was more likely for its micropores to be blocked making its mesopores the major representative of its pore diameter.
The adsorption-desorption isotherms of pristine OCPf, functionalized OCPf and all the NiMo/OCPf catalysts used in this study are shown in Figure 1.
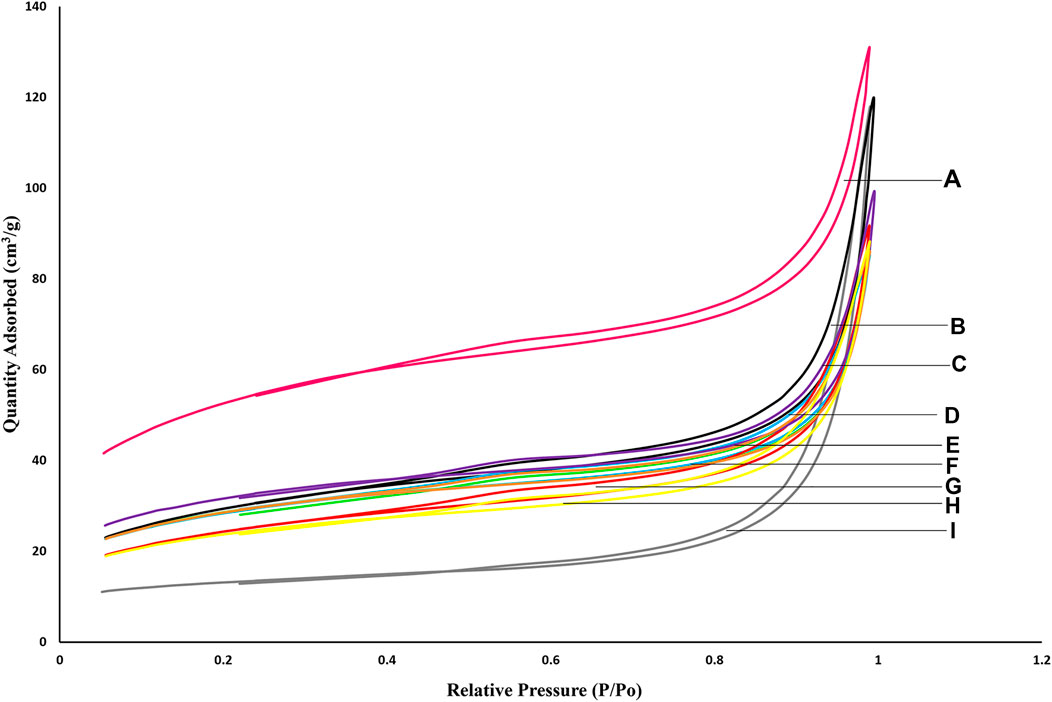
FIGURE 1. Adsorption-desorption isotherms of OCPf-supported NiMo catalysts (A) Functionalized OCPf (B) 2.5wt%Ni19wt%Mo/OCPf (C) 5.0wt%Ni13wt%Mo/OCPf (D) 2.5wt%Ni13wt%Mo/OCPf (E) 5.0wt%Ni19wt%Mo/OCPf (F) 3.5wt%Ni13wt%Mo/OCPf (G) 3.5wt%Ni19wt%Mo/OCPf (H) 5.0wt%Ni26wt%Mo/OCPf, (I) Pristine OCPf.
From Figure 1 all the samples tested displayed Type IV isotherm which is typical of mesoporous materials but with H3 hysteresis loop. Among all the samples, the functionalized OCPf exhibited higher adsorption capabilities because of the nanowindows created on the support material as well as the consequent increase in surface area after acid treatment. The pristine OCPf sample showed minimal adsorption capabilities compared to the rest of the samples. From Figure 1, the shapes of the functionalized adsorption-desorption isotherm and that of the various catalysts were similar and this implies that the pore structure of the functionalized OCPf material remained intact in all the catalysts (Sing et al., 1985). The highly loaded catalysts are practically a mixture of well dispersed catalysts and some remnants of crystalline NiMo phase.
TGA Analysis of the OCPf-Supported NiMo Catalysts
Since all OCPf catalysts were prepared from a by-product support and there is an instant negativity surrounding by-products, the thermal stability of the catalysts had to be tested with TGA at the hydrotreating temperature conditions (330, 350 and 370°C) being experimented to ensure that the catalysts would not burn out during the hydrotreating process. Thus, Figure 2 displays the TGA profiles of all the calcined OCPf-supported NiMo catalysts utilized in this study.
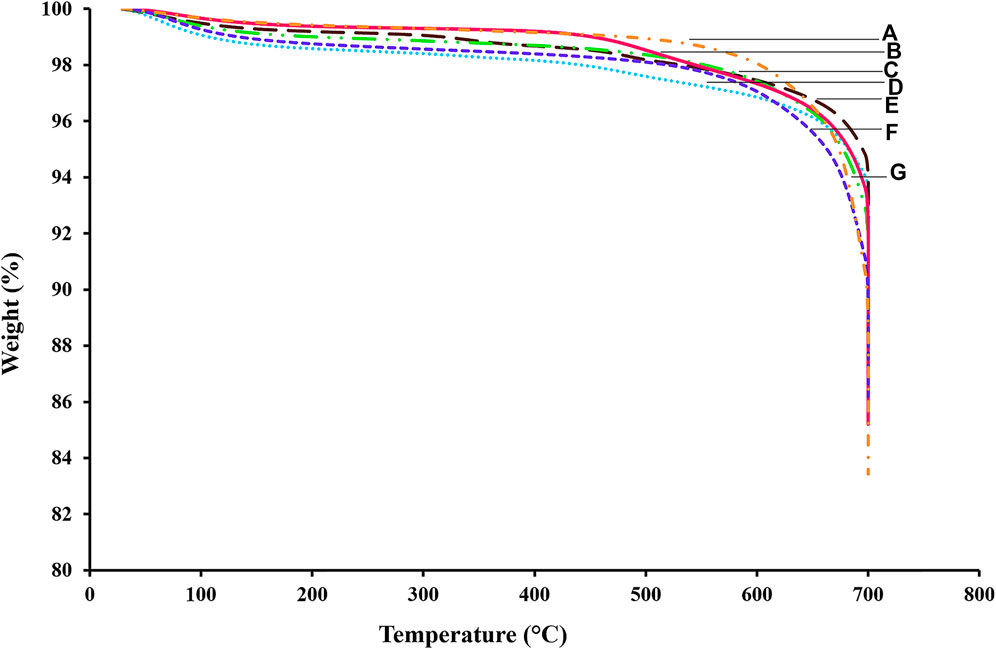
FIGURE 2. TGA profiles of OCPf-supported NiMo catalysts (A) 5.0wt%Ni19wt%Mo/OCPf (B) 3.5wt%Ni19wt%Mo/OCPf (C) 3.5wt%Ni13wt%Mo/OCPf (D) 2.5wt%Ni13wt%Mo/OCPf (E) 2.5wt%Ni19wt%Mo/OCPf (F) 5.0wt%Ni13wt%Mo/OCPf (G) 5.0wt%Ni26wt%Mo/OCPf.
Removal of nitrates, ammonia and water in an impregnated catalyst sample is prevalent during TGA analysis, and nitrates present in carbon-supported catalysts could cause oxidation of carbon support. It is also worth noting that with respect to calcination, carbon supports are prone to oxidation as NH3 is removed during a calcination step which is catalyzed by Mo deposits. Thus, oxidation of carbon supports can be prevented by low temperature calcination of the catalyst in air or by calcination in an inert environment. Another way to prevent oxidation of the catalyst is to use a presulfided catalyst that does not decompose (NH4)6Mo7O24. Additionally, oxidation of carbon supports can be prevented by impregnation of the support with a MoO3/water slurry in place of (NH4)6Mo7O24/water solution. For the MoO3/water slurry or slurry, impregnation method calcination is not required because although the solubility of MoO3 is low, molybdena species are gradually transported and adsorbed onto the carbon surface because of electrostatic attraction between molybdate anions and positively charged carbon surfaces (Vissers et al., 1987; Kaluža, and Zdražil, 2001). Work by Vissers et al., 1987 confirmed that direct sulfidation of an uncalcined carbon-supported catalyst with a sulfiding agent preferably H2S/H2 mixture impedes carbon destruction due to the lack of gasification of the carbon support to methane or CO (Vissers et al., 1987).
From Figure 2 the desorption of water that had been physically adsorbed led to a weight loss of about 1% up to 120°C. Afterwards, the weight loss was almost constant up to about 400°C and mostly stable until ∼600°C. The stability of the thermal properties from 120–400°C may be due to less concentration of surface defects on the catalysts. A slight loss in weight from 120–400°C can be attributed to the loss of impurities that remain on the sample after catalyst preparation, or loss due to MoO3 decomposition into MoO2 or Mo4O11 intermediate compounds (Spevack and Mcintyre, 1992; Serp et al., 2003). Beyond 500°C–700°C carbothermal reductive decomposition of NiO or NiMoO4 may contribute to the weight loss (Lebukhova and Karpovich, 2008). The drastic drop in weight for all the NiMo/OCPf catalyst samples at about 700°C can also be attributed to the findings from Bekyarova et al. (2002) which showed that at higher temperatures of at least 500°C, carbon nanomaterials are prone to burn-off due to instability. Although, an inert gas (nitrogen) was used to carry out the TGA experiments the thermal stability of the catalyst in terms of thermal sintering is the same regardless of the reactive gas environment (H2) used during hydrotreating since, exposure to higher (>500°C) gas-phase temperatures is the main factor that influences catalyst deactivation by thermal sintering (Bartholomew, 2001; Bekyarova et al., 2002; Fogler, 2006). Based on the above information the thermal stability of all the catalysts in terms of thermal sintering is assured for the hydrotreating temperatures (330–370°C) being studied.
XRD Analysis of the OCPf-Supported NiMo Catalysts
Low angle XRD profile patterns of all the different NiMo/OCPf catalysts displayed in Figure 3 shows a hexagonal mesoporous structure with well resolved strong (2θ = 0.9) and weak (2θ = 1.7) peaks that were identical for every catalyst used in this study. The peaks were indexed at d (100) and d (110). This identical characteristic implied that variation in metal loading composition did not influence the hexagonal mesoporous structure.
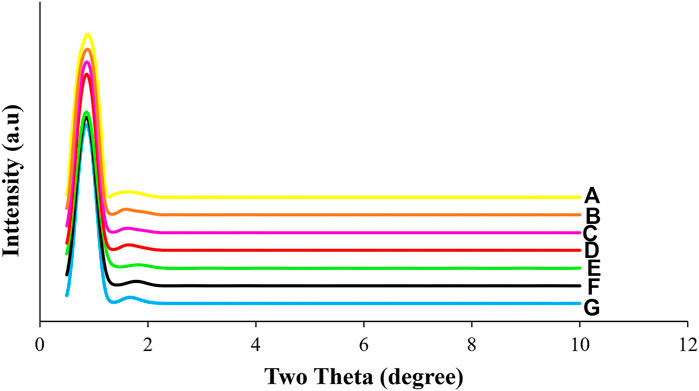
FIGURE 3. Low angle XRD patterns of OCPf-supported NiMo catalysts (A) 5.0wt%Ni26wt%Mo/OCPf (B) 5.0wt%Ni19wt%Mo/OCPf (C) 5.0wt%Ni13wt%Mo/OCPf (D) 3.5wt%Ni19wt%Mo/OCPf (E) 3.5wt%Ni13wt%Mo/OCPf (F) 2.5wt%Ni19wt%Mo/OCPf (G) 2.5wt%Ni13wt%Mo/OCPf.
Figure 4 shows the high angle XRD profile patterns of all the NiMo/OCPf catalysts, and the XRD diffractograms revealed crystalline phases for all samples. The 2θ diffraction peak at ∼ 26° represents, (002) plane characteristic of a hexagonal carbon structure. This 2θ diffraction peak at ∼26° also corresponds to an intense MoO3 and NiMoO4 peak. Thus, the peak at this position can be associated to an overlap of carbon (OCPf), MoO3 and NiMoO4 material. Other small intensity peaks occurred at ∼37° and ∼54° on all the catalysts which corresponded to NiO and NiMoO4, respectively. The appearance of these characteristic crystalline peaks relating to MoO3, NiO and NiMoO4 on the OCPf-supported NiMo catalysts implied that the metals were not well dispersed on the support. A small diffraction peak relating to molybdenum carbide (Mo2C) was also observed at 2θ = ∼61° (Quanli et al., 2003; Gattia et al., 2006; Liu et al., 2011; Aryee et al., 2021). The crystal sizes of all the catalysts were calculated from all XRD patterns using the Derbye-Scherrer equation. These values ranged from 8 to 14 nm. For the 5.0wt%Ni19wt%Mo/OCPf catalyst, the crystal sizes were calculated using peaks at two theta values of 26°, 37°, 54° and 61° in Figure 4. Also, the crystal sizes of the NiO phase for 2.5wt%Ni13wt%Mo/OCPf, 2.5wt%Ni19wt%Mo/OCPf, 3.5wt%Ni13wt%Mo/OCPf, 3.5wt%Ni19wt%Mo/OCPf, 5.0wt%Ni13wt%Mo/OCPf, 5.0wt%Ni19wt%Mo/OCPf and 5.0wt%Ni26wt%Mo/OCPf catalysts were calculated, which varied from 11–13 nm.
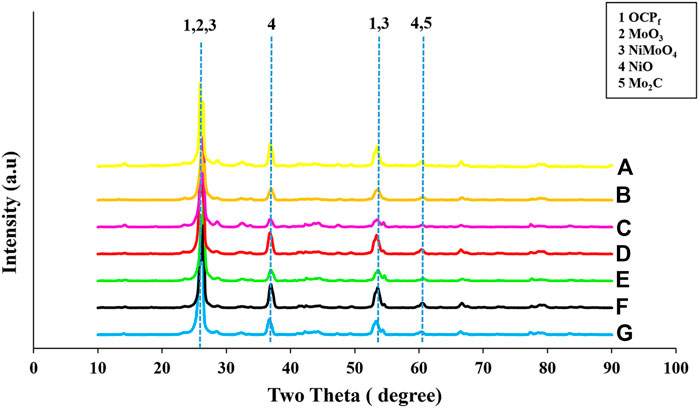
FIGURE 4. High angle XRD patterns of OCPf-supported NiMo catalysts (A) 5.0wt%Ni26wt%Mo/OCPf (B) 5.0wt%Ni19wt%Mo/OCPf (C) 5.0wt%Ni13wt%Mo/OCPf (D) 3.5wt%Ni19wt%Mo/OCPf (E) 3.5wt%Ni13wt%Mo/OCPf (F) 2.5wt%Ni19wt%Mo/OCPf (G) 2.5wt%Ni13wt%Mo/OCPf.
The crystalline peak intensities exhibited by the 5.0wt%Ni13wt%Mo/OCPf, 5.0wt%Ni19wt%Mo/OCPf, 3.5wt%Ni13wt%Mo/OCPf and 2.5wt%Ni13wt%Mo/OCPf catalysts were smaller than the rest of the catalysts hence, it is expected that the dispersion of the metal components in these catalysts would be much improved compared to the remaining OCPf-supported NiMo catalysts used in this study. Additionally, this result implies that an improved dispersion can be obtained if a catalyst is formulated using a combination of Ni compositions varying from 2.5 to 5.0 wt% and a low Mo composition of 13 wt%. However, for a high Mo composition of 19 wt% an improved dispersion can also be achieved with a high Ni composition of 5.0 wt%.
CO-Chemisorption Analysis of the OCPf-Supported NiMo Catalysts
Results from CO-chemisorption analysis are displayed in Table 2, and these results show that at constant Ni composition of 2.5 and 5.0 wt%, an increase in Mo composition from 13 wt% to 19 wt% resulted in a decrease in dispersion and a corresponding increase in CO uptake. Nonetheless, no change in dispersion occurred at constant Ni composition of 3.5 wt% as the Mo varied from 13 to 19 wt%. However, at constant Mo loadings of 13 wt% or 19 wt%, metal dispersion and CO uptake increased steadily with increasing Ni compositions from 2.5 to 5.0 wt%. This positive impact is ascribed to the fact that increase in Ni loadings increases the amount of Ni release during sulfidation, and this effect simultaneously enhances the redistribution of MoO3 which further results in a decrease in crystallite size with a corresponding increase in metal dispersion (Badoga et al., 2014). Results from Table 2 also indicate that of all the catalyst under study a significant improvement in both metal dispersion and CO uptake can be achieved by using a catalyst with high Ni composition (5.0 wt%) and an Mo composition of either 13 wt% or 19 wt%. Thus, the 5.0wt%Ni13wt%Mo/OCPf and 5.0wt%Ni19wt%Mo/OCPf catalysts exhibited maximum metal dispersions whereas, the 5.0wt%Ni26wt%Mo/OCPf catalyst showed the least metal dispersion since, the Mo loadings of 26 wt% was too high for the 5.0 wt% Ni to have any positive influence on the redistribution of MoO3 to form smaller crystallite size with enhanced dispersion.
The average diameter (nm) of the crystallites (assumption-spherical) is given by this equation
HRTEM Examination of the Morphology of the Various OCPf-Supported NiMo Catalysts
The morphology of the different NiMo/OCPf catalysts used for this study are displayed in Figure 5. The TEM micrographs of all the catalysts showed dark spots that signified that indeed metals have been impregnated on the support. However, the micrographs suggest that metals were not evenly dispersed on the support. Additionally, apart from CNH structures, some of the catalysts also revealed CNT and other embedded structures typical of an OCPf material (Gattia et al., 2006; Zhang et al., 2019).
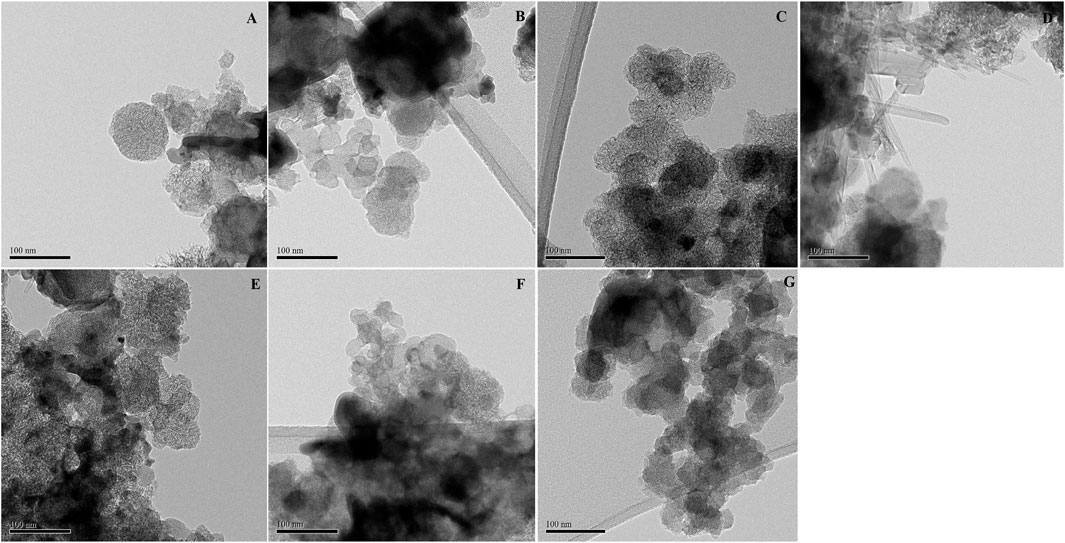
FIGURE 5. Morphology of different NiMo/OCPf catalysts (A) 2.5wt%Ni13wt%Mo/OCPf (B) 2.5wt%Ni19wt%Mo/OCPf (C) 3.5wt%Ni13wt%Mo/OCPf (D) 3.5wt%Ni19wt%Mo/OCPf (E) 5.0wt%Ni13wt%Mo/OCPf (F) 5.0wt%Ni19wt%Mo/OCPf (G) 5.0wt%Ni26wt%Mo/OCPf.
TPR Analysis of the Various OCPf-Supported NiMo Catalysts
The TPR results of all the NiMo/OCPf catalysts are shown in Figure 6. Two Mo reduction peaks at low (320–394°C) and high (570–660°C) temperature values were detected. The first peak corresponded to a partial reduction of Mo6+ to Mo4+ whereas the second peak was from a combination of a complete reduction of Mo6+ to Mo4+ and Mo4+ to Mo0+. Reduction of Ni2+ also contributed to the low temperature reduction peak in the range of 250–375°C whereas, NiMoO4 also contributed to the reduction peak that ranged from 375 to 480°C (Hurst et al., 1982; Brito et al., 1989; Calafat et al., 1996; Aryee et al., 2021). All the catalysts revealed the presence of crystalline MoO3 in the shoulder of the first peak and on the high temperature side. This is a typical position for crystalline MoO3 and normally the absence of this peak signifies that MoO3 is amorphous and/or well dispersed. As a result, it is obvious that the most overloaded catalyst is 5.0wt%Ni26wt%Mo/OCPf due to the high intensity of the MoO3 crystalline peak and the shift of this peak towards a higher temperature. The preceding information correlates well with the XRD patterns, CO chemisorption dispersion results as well as the overall activity results from all catalysts (Regalbuto and Ha, 1994; Qu et al., 2003).
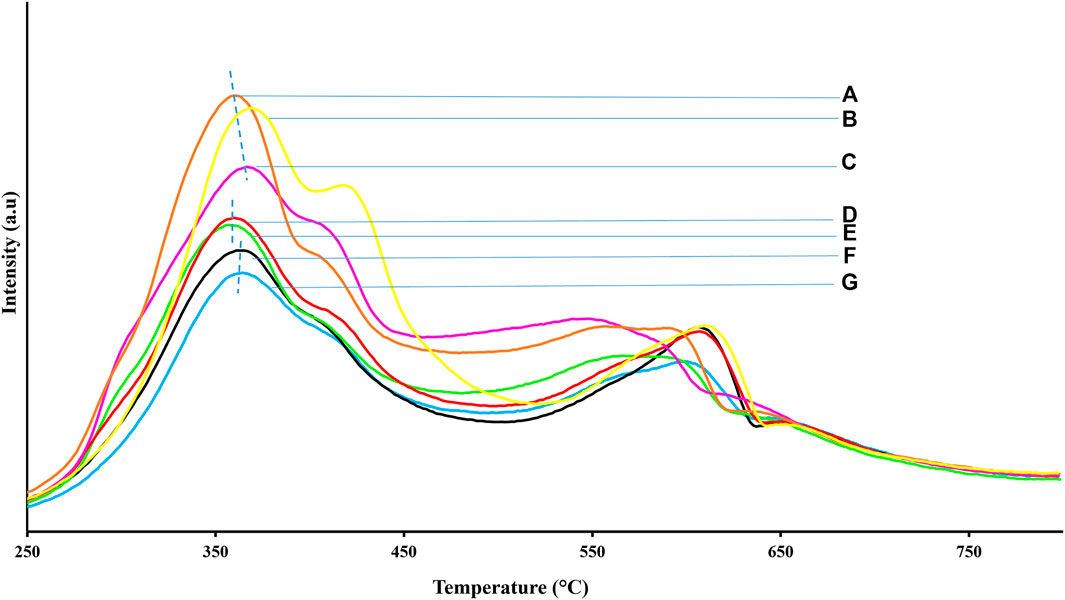
FIGURE 6. TPR results of NiMo/OCPf catalysts; (A) 5.0wt%Ni19wt%Mo/OCPf, (B) 5.0wt%Ni26wt%Mo/OCPf, (C) 5.0wt%Ni13wt%Mo/OCPf, (D) 3.5wt%Ni19wt%Mo/OCPf, (E) 3.5wt%Ni13wt%Mo/OCPf, (F) 2.5wt%Ni19wt%Mo/OCPf, (G) 2.5wt%Ni13wt%Mo/OCPf.
Overall, except for the 5.0wt%Ni26wt%Mo/OCPf catalyst that revealed a first peak reduction temperature at 372°C, the first peak reduction temperature for all the remaining catalysts under study was centered around 362°C. Thus, the 5.0wt%Ni26wt%Mo/OCPf catalyst with the highest Ni and Mo composition among all the catalysts under study exhibited the greatest difficulty in reduction. Also, for the remaining catalysts it can be inferred that variation of Ni and Mo in any of these catalyst combinations only resulted in a slight change in the first peak reduction temperature and consequently the effect of metal support interaction from these catalysts may have similar impact on hydrotreating performance. However, the hydrogen consumption intensity increased drastically as Ni compositions increased from 2.5 to 5.0 wt% as compared to the slight jump in hydrogen consumption intensity with increasing Ni composition from 2.5 to 3.5 wt%. From Figure 6, it was obvious that hydrogen consumption intensities were also higher for the catalysts with 19 wt% Mo compositions than catalysts with Mo compositions of 13 wt% since more active sites were present in the former than the later. (Grimblot, 1998; Afanasiev and Bezverkhyy, 2007). Additionally, the high MoS2 active sites accompanying high compositions aided in shifting the peaks to lower temperatures as in the case of the 5.0wt%Ni13wt%Mo/OCPf and 5.0wt%Ni19wt%Mo/OCPf catalysts.
The catalysts with 5.0 wt% Ni composition are expected to have high HDS and HDN activities because, the highest hydrogen consumption intensities displayed by these catalysts especially in the case 5.0wt%Ni19wt%Mo/OCPf catalyst is advantageous since this characteristic renders the MoO3 present in these catalysts, to undergo rapid transformation to a Type II Ni-Mo-S phase associated with enhanced activity (Park et al., 1997; Yin et al., 2011). This assertion from TPR analysis implies that the hydrogen consumption intensities, which indicate higher extent of reducibility of MoO3 species, can have a significant impact on creating Type II Ni-Mo-S phase and inducing higher hydrotreating performance. From the TPR study, it is also noted that the metal-support-interaction is slightly impacted by variation in metal loadings on OCPf-supported catalysts due to similarities in the first peak reduction temperature values displayed by these catalysts in Figure 6.
HDS and HDN Activities of the Various OCPf-Supported NiMo Catalysts
Figure 7 and 8 show the results of the effects of temperature on the HDS and HDN activities of all the different catalysts after a rigorous long-lasting test. Overall, although small differences in activity results were realized the results are very meaningful. In all cases, both HDS and HDN activities increased with increasing temperature. A rise in HDS and HDN activities with increasing temperature is attributed to higher reaction rates and conversions accompanying an increase in temperature (Speight, 2000). Thus, maximum HDS and HDN activities were obtained at the highest operating temperature of 370°C. Overall, the activity results of all catalysts revealed that HDS processes exhibited higher activities than the HDN processes under the different temperature conditions. This trend is acceptable because, it is much easier to convert sulfur compounds with less refractory linkages than total nitrogen compounds comprising of the most refractory compounds. Total nitrogen compounds in gas oils exist in two forms i.e. basic and non-basic nitrogen compounds, and in terms of activity the non-basic nitrogen compounds contribute to the low activities exhibited by total nitrogen compounds since they are less reactive (Laredo et al., 2001; Botchwey et al., 2003; Sano et al., 2004).
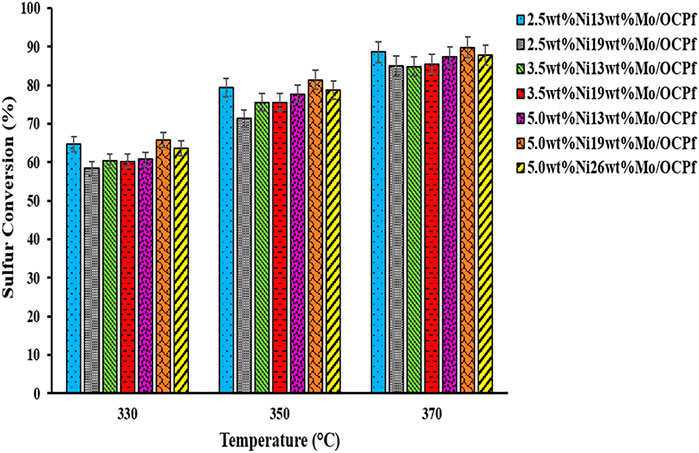
FIGURE 7. HDS activities of NiMo/OCPf catalysts with LGO at 330, 350, and 370°C (Catalyst = 5 cm3, LHSV = 2 h−1, P = 9.0 MPa, and H2/oil ratio = 600 (ml/ml)).
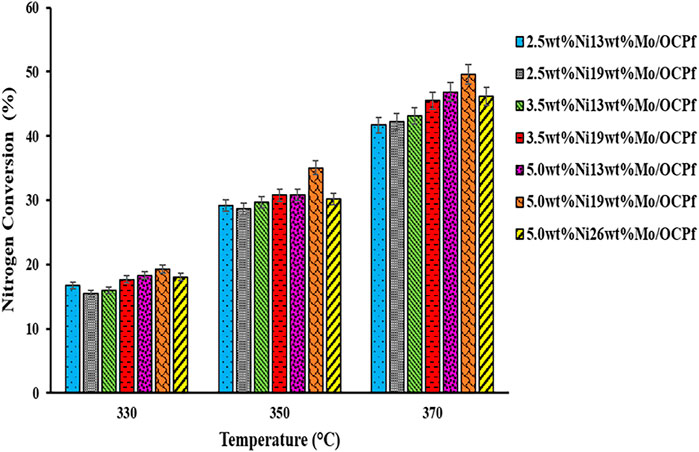
FIGURE 8. HDN activities of NiMo/OCPf catalysts with LGO at 330, 350, and 370°C (Catalyst = 5 cm3, LHSV = 2 h−1, P = 9.0 MPa, and H2/oil ratio = 600 (ml/ml)).
Results from Figure 7 shows that at 370°C, the HDS activities for the 2.5wt%Ni19wt%Mo/OCPf, 3.5wt%Ni13wt%Mo/OCPf, and 3.5wt%Ni19wt%Mo/OCPf catalysts were almost the same (∼85%). However, these catalysts exhibited a steady increase in HDN activities as depicted in Figure 8. Also, from Figure 7 doubling the compositions of Ni and Mo as in the case of the 2.5wt%Ni13wt%Mo/OCPf catalyst and 5.0wt%Ni26wt%Mo/OCPf catalyst did not double the conversions in a direct scale up manner. Activity results from these two catalysts indicated that a slight decrease (∼1%) in HDS activities occurred when the Ni and Mo compositions were doubled, whereas a slight increase (∼4%) in HDN activities occurred by doubling the metal compositions. This implies that doubling the metal compositions have insignificant impact on the conversions as it overloads the support with crystalline phase, therefore not a good choice in catalyst formulation.
For the 2.5wt%Ni13wt%Mo/OCPf catalyst, although the use of this catalyst in the preliminary study mentioned in the abstract and reported elsewhere resulted in an HDS and HDN activity of 78 and 25%, respectively the HDS and HDN activities further increased to 89 and 42% using the same catalyst composition and light gas oil in this study. The enhancement of the catalyst activities in this study can be attributed to an improvement in textural properties, percentage dispersion and reducibility brought about by a reduction in particle size after sieving since, more fine materials with better characteristics were collected and used for catalyst formulation by using a particle cut-off size of 250 microns in this study versus a particle cut-off size of 297 microns used in the preliminary study. Additionally, the improvement in HDS and HDN activities for the 2.5wt%Ni13wt%Mo/OCPf catalyst used in this study may be due to the LHSV value 1 h−1, which was used in sulfiding the catalyst in this study prior to all hydrotreating experiments compared to LHSV value of 2 h−1 used in sulfiding a similar catalyst composition in the preliminary study (Aryee et al., 2021). Less LHSV means more contact time between the catalyst and liquid during sulfidation, and this increases the active sites with subsequent increase in activities (Satterfield, 1991). Findings from this work also demonstrated that high HDS activities can be achieved with a NiMo/OCPf catalyst having lower metals loading (2.5 wt% Ni and 13 wt% Mo) and/or higher metals loading (5.0 wt% Ni and 19 wt% Mo).
On the other hand, it was found that among all the catalyst used in this study use of the 5.0wt%Ni19wt%Mo/OCPf catalyst led to the highest hydrotreating performance for both HDS (90%) and HDN (50%) activities due to its high ability to consume hydrogen (TPR results) that translates to easier formation to a Type II Ni-Mo-S phase with enhanced activity (Yin et al., 2011; Park et al., 1997). Additionally, this catalyst exhibited a high metal dispersion and optimal pore diameter from Co-chemisorption and XRD analysis. The minimum HDS (84%) and HDN (42%) conversions were also obtained with the 2.5wt%Ni19wt%Mo/OCPf catalyst because, of its low percentage dispersion (4.4%) coupled with it having the highest pore diameter (∼13 nm). Even though this pore diameter was the highest amongst all the catalysts, it may not be the optimal. This is because, it would allow reactant molecules to access the catalytic sites without making maximum contact at the active sites for maximum activity results. Although the 5.0wt%Ni26wt%Mo/OCPf catalyst had the lowest surface area of ∼78 m2/g and exhibited the lowest percentage metal dispersion of 3.8% and highest reducibility temperature, these properties did not have any negative impact on its corresponding HDS and HDN activities as the effect from its high hydrogen consumption intensity from TPR result in Figure 6 outweighed or nullified the effect from the other characteristics. High hydrogen consumption also implied that the 5.0wt%Ni26wt%Mo/OCPf catalyst had a high propensity of forming a Type II Ni-Mo-S with enhanced activity as confirmed by Yin et al., 2011 (Park et al., 1997; Yin et al., 2011).
Conclusion
In this study, seven catalysts with different combinations of Ni and Mo compositions were formulated, characterized, and used to hydrotreat light gas oil to ascertain how the OCPf-supported catalysts contribute to the achievement of highest HDS and HDN activities. Characterization results from this study showed that although all the catalysts displayed mesoporous pore diameters ranging from 10–13 nm, the surface areas (<110 m2/g) and pore volumes ( ̴0.12 cm3/g) of all catalysts were low. Additionally, TGA analysis confirmed that all catalysts formulated from an OCPf by-product support material can attain high thermal stability with low weight loss (1%) within the hydrotreating operating temperatures (330–370°C) experimented. CO-chemisorption results concludes that high Ni composition of 5.0 wt% played a dominant role in decreasing crystallite sites and enhancing the percentage metal dispersion and CO uptake. TPR analysis indicates that for catalysts with similar metal-support-interaction their HDS and HDN activities can be high if they exhibit high hydrogen consumption intensities. In this regard, amongst all the catalysts under study, the 5.0wt%Ni19wt%Mo/OCPf demonstrated the highest HDS and HDN activities of 90 and 50%, respectively with light gas oil at a hydrotreating operating pressure of 9.0 MPa, temperature of 370°C and LHSV of 2 h−1. As evidence from XRD, CO chemisorption, and TPR results, the HDS and HDN catalytic activities were influenced by the presence of crystals such as MoO3 and NiO in all the catalyst samples. At the highest operating temperature of 370°C, the effect of variation in metal loading compositions on HDS activities was not significant since some catalysts displayed similar HDS activities. However, in the case of the HDN activities apart from the 5.0wt%Ni26wt%Mo/OCPf catalyst, a steady increase in activity occurred as the metal loading compositions on the OCPf support increased. In situations, where physical separation of materials precedes catalyst formulation the particle cutoff size has an impact on HDS and HDN activities since finer materials are more likely to have better physiochemical characteristics suitable for the development of a hydrotreating catalyst. Use of a lower LHSV for sulfidation can also lead to an improvement in HDS and HDN activities. Outcome from this study demonstrates that the NiMo/OCPf catalyst can be improved and used in catalysis for hydrotreating or other similar catalytic reactions.
Data Availability Statement
The raw data supporting the conclusion of this article will be made available by the authors, without undue reservation.
Author Contributions
EA designed and conducted all experiments, analyzed experimental results, wrote the draft of the manuscript and revised the final submission. AKD and JA approved the experimental plan, supervised the work, reviewed and modified the final submission. All authors listed have made a substantial, direct and intellectual contribution to the work and approve it for publication.
Conflict of Interest
Author JA was employed by company Syncrude Edmonton Research Centre.
The remaining authors declare that the research was conducted in the absence of any commercial or financial relationships that could be construed as a potential conflict of interest.
Publisher’s Note
All claims expressed in this article are solely those of the authors and do not necessarily represent those of their affiliated organizations, or those of the publisher, the editors and the reviewers. Any product that may be evaluated in this article, or claim that may be made by its manufacturer, is not guaranteed or endorsed by the publisher.
Acknowledgments
The financial support from Syncrude, Canada Research Chair (CRC) Program, University of Saskatchewan, MITACS and Natural Sciences and Engineering Research Council of Canada (NSERC) are gratefully acknowledged.
References
Afanasiev, P., and Bezverkhyy, I. (2007). Ternary Transition Metals Sulfides in Hydrotreating Catalysis. Appl. Catal. A: Gen. 322, 129–141. doi:10.1016/j.apcata.2007.01.015
Al-Dahhan, M. H., Wu, Y., and Dudukovic, M. P. (1995). Reproducible Technique for Packing Laboratory-Scale Trickle-Bed Reactors with a Mixture of Catalyst and Fines. Ind. Eng. Chem. Res. 34, 741–747. doi:10.1021/ie00042a005
Arora, N., and Sharma, N. N. (2014). Arc Discharge Synthesis of Carbon Nanotubes: Comprehensive Review. Diamond Relat. Mater. 50, 135–150. doi:10.1016/j.diamond.2014.10.001
Aryee, E., Dalai, A. K., and Adjaye, J. (2014). Functionalization and Characterization of Carbon Nanohorns (CNHs) for Hydrotreating of Gas Oils. Top. Catal. 57, 796–805. doi:10.1007/s11244-013-0236-6
Aryee, E., Essilfie-Dughan, J., Dalai, A. K., and Adjaye, J. (2021). Comparative Studies of Carbon Nanomaterial and γ-Alumina as Supports for the Ni-Mo Catalyst in Hydrotreating of Gas Oils. Energy Fuels 35, 6153–6166. doi:10.1021/acs.energyfuels.0c02394
Aryee, E. (2019).Hydrotreating of Gas Oils Using Ni-Mo Catalyst Supported on Carbon Nanohorns and Associated Carbon Materials. Doctor of Philosophy Thesis. University of Saskatchewan. Available at: http://hdl.handle.net/10388/12383.
Badoga, S., Sharma, R. V., Dalai, A. K., and Adjaye, J. (2014). Hydrotreating of Heavy Gas Oil on Mesoporous Zirconia Supported NiMo Catalyst with EDTA. Fuel 128, 30–38. doi:10.1016/j.fuel.2014.02.056
Bartholomew, C. H. (2001). Mechanisms of Catalyst Deactivation. Appl. Catal. A: Gen. 212, 17–60. doi:10.1016/s0926-860x(00)00843-7
Bekyarova, E., Kaneko, K., Kasuya, D., Murata, K., Yudasaka, M., and Iijima, S. (2002). Oxidation and Porosity Evaluation of Budlike Single-wall Carbon Nanohorn Aggregates. Langmuir 18, 4138–4141. doi:10.1021/la0117348
Botchwey, C., Dalai, A. K., and Adjaye, J. (2003). Product Selectivity during Hydrotreating and Mild Hydrocracking of Bitumen-Derived Gas Oil. Energy Fuels 17, 1372–1381. doi:10.1021/ef020214x
Brito, J. n. L., Laine, J., and Pratt, K. C. (1989). Temperature-Programmed Reduction of Ni-Mo Oxides. J. Mater. Sci. 24, 425–431. doi:10.1007/bf01107422
Byskov, L. S., Hammer, B., Nørskov, J. K., Clausen, B. S., and Topsøe, H. (1997). Sulfur Bonding in MoS2 and Co-mo-S Structures. Catal. Lett. 47, 177–182. doi:10.1023/A:1019009105792
Calafat, A., Laine, J., López-Agudo, A., and Palacios, J. M. (1996). Effect of Surface Oxidation of the Support on the Thiophene Hydrodesulfurization Activity of Mo, Ni, and NiMo Catalysts Supported on Activated Carbon. J. Catal. 162, 20–30. doi:10.1006/jcat.1996.0256
Candia, R., Sørensen, O., Villadsen, J., Topsøe, N.-Y., Clausen, B. S., and Topsøe, H. (1984). Effect of Sulfiding Temperature on Activity and Structures of CO-MO/AL2O3 Catalysts. Ii. Bull. Soc. Chim. Belges. 93, 763–774. doi:10.1002/bscb.19840930818
Duchet, J., van Oers, E. M., de Beer, V. H. J., and Prins, R. (1983). Carbon-supported Sulfide Catalysts. J. Catal. 80, 386–402. doi:10.1016/0021-9517(83)90263-4
Ebbesen, T. W., and Ajayan, P. M. (1992). Large-scale Synthesis of Carbon Nanotubes. Nature 358, 220–222. doi:10.1038/358220a0
Falcao, E. H., and Wudl, F. (2007). Carbon Allotropes: beyond Graphite and diamond. J. Chem. Technol. Biotechnol. 82, 524–531. doi:10.1002/jctb.1693
Fogler, H. (2006). Elements of Chemical Reaction Engineering. 4th Edition. Upper Saddle River, NJ: Prentice Hall International Series.
Furimsky, E. (1998). Selection of Catalysts and Reactors for Hydroprocessing. Appl. Catal. A: Gen. 171, 177–206. doi:10.1016/S0926-860X(98)00086-6
Grimblot, J. (1998). Genesis, Architecture and Nature of Sites of Co(Ni)-MoS2 Supported Hydroprocessing Catalysts. Catal. Today 41, 111–128. doi:10.1016/S0920-5861(98)00042-X
Hurst, N. W., Gentry, S. J., Jones, A., and McNicol, B. D. (1982). Temperature Programmed Reduction. Catal. Rev. 24, 233–309. doi:10.1080/03602458208079654
Jarullah, A. T., Mujtaba, I. M., and Wood, A. S. (2012). Improving Fuel Quality by Whole Crude Oil Hydrotreating: A Kinetic Model for Hydrodeasphaltenization in a Trickle Bed Reactor. Appl. Energ. 94, 182–191. doi:10.1016/j.apenergy.2012.01.044
Kaluža, L., and Zdražil, M. (2001). Carbon-supported Mo Catalysts Prepared by a New Impregnation Method Using a MoO3/water Slurry: Saturated Loading, Hydrodesulfurization Activity and Promotion by Co. Carbon 39, 2023–2034. doi:10.1016/s0008-6223(01)00018-5
Karousis, N., Suarez-Martinez, I., Ewels, C. P., and Tagmatarchis, N. (2016). Structure, Properties, Functionalization, and Applications of Carbon Nanohorns. Chem. Rev. 116, 4850–4883. doi:10.1021/acs.chemrev.5b00611
Keidar, M., Shashurin, A., Li, J., Volotskova, O., Kundrapu, M., and Zhuang, T. S. (2011). Arc Plasma Synthesis of Carbon Nanostructures: where Is the Frontier. J. Phys. D: Appl. Phys. 44, 174006–174011. doi:10.1088/0022-3727/44/17/174006
Lam, E., and Luong, J. H. T. (2014). Carbon Materials as Catalyst Supports and Catalysts in the Transformation of Biomass to Fuels and Chemicals. ACS Catal. 4, 3393–3410. doi:10.1021/cs5008393
Laredo S, G. C., De los Reyes H, J. A., Luis Cano D, J., and Jesús Castillo M, J. (2001). Inhibition Effects of Nitrogen Compounds on the Hydrodesulfurization of Dibenzothiophene. Appl. Catal. A: Gen. 207, 103–112. doi:10.1016/S0926-860X(00)00620-7
Lebukhova, N. V., and Karpovich, N. F. (2008). Carbothermic Reduction of Copper, Nickel, and Cobalt Oxides and Molybdates. Inorg. Mater. 44, 890–893. doi:10.1134/s0020168508080207
Liu, F., Xu, S., Chi, Y., and Xue, D. (2011). A Novel Alumina-Activated Carbon Composite Supported NiMo Catalyst for Hydrodesulfurization of Dibenzothiophene. Catal. Commun. 12, 521–524. doi:10.1016/j.catcom.2010.11.018
López, C. R., and López, A. A. (2000). Effect of Water Extraction on the Surface Properties of Mo/Al2O3 and NiMo/Al2O3 Hydrotreating Catalysts. Appl. Catal. A: Gen. 202, 23–35. doi:10.1016/S0926-860X(00)00449-X
Lynch, J. (2003). Physico-chemical Analysis of Industrial Catalysts - A Practical Guide to Characterization. Paris: Editions TECHNIP, 1–309.
Mapiour, M., Sundaramurthy, V., Dalai, A. K., and Adjaye, J. (2010). Effects of the Operating Variables on Hydrotreating of Heavy Gas Oil: Experimental, Modeling, and Kinetic Studies. Fuel 89, 2536–2543. doi:10.1016/j.fuel.2010.02.024
Mirabile Gattia, D., Vittori Antisari, M., Marazzi, R., Pilloni, L., Contini, V., Montone, A., et al. (2006). Arc-discharge Synthesis of Carbon Nanohorns and Multiwalled Carbon Nanotubes. Materials Science Forum 518, 23–28. doi:10.4028/www.scientific.net/msf.518.23
Ng, J., and Raitses, Y. (2014). Role of the Cathode deposit in the Carbon Arc for the Synthesis of Nanomaterials. Carbon 77, 80–88. doi:10.1016/j.carbon.2014.05.007
Park, Y.-C., Oh, E.-S., and Rhee, H.-K. (1997). Characterization and Catalytic Activity of WNiMo/Al2O3 Catalyst for Hydrodenitrogenation of Pyridine. Ind. Eng. Chem. Res. 36, 5083–5089. doi:10.1021/ie970386v
Prins, R., de Beer, V. H. J., and Somorjai, G. A. (1989). Structure and Function of the Catalyst and the Promoter in Co-mo Hydrodesulfurization Catalysts. Catal. Rev. 31, 1–41. doi:10.1080/01614948909351347
Qu, L., Zhang, W. P., Kooyman, P. J., and Prins, R. (2003). MAS NMR, TPR, and TEM Studies of the Interaction of NiMo with Alumina and Silica-Alumina Supports. J. Catal. 215, 7–13. doi:10.1016/s0021-9517(02)00181-1
Quanli, Z., Bing, Z., Jian, Y., Jiaxin, W., Jun, Z., Shengfu, J., et al. (2003). The Promotion of Nickel to Mo2C/Al2O3 Catalyst for the Partial Oxidation of Methane to Syngas. New J. Chem. 27, 1633–1638. doi:10.1039/b306485a
Rana, M. S., Torres‐Mancera, P., and Ancheyta, J. (2020). Experimental Methods for Evaluation of Hydrotreating Catalysts//Experimentation in Glass Reactors with Model Compounds. 1st Edition, 11–45. doi:10.1002/9781119518037.ch2
Regalbuto, J. R., and Ha, J.-W. (1994). A Corrected Procedure and Consistent Interpretation for Temperature Programmed Reduction of Supported MoO3. Catal. Lett. 29, 189–207. doi:10.1007/bf00814265
Robinson, P. R., and Dolbear, G. E. (2006). “Hydrotreating and Hydrocracking: Fundamentals,” in Practical Advances in Petroleum Processing. Editors C. S. Hsu, and P. R. Robinson (New York, NY: Springer), 177–218. doi:10.1007/978-0-387-25789-1_7
Rodriquez-Reinoso, F. (1998). The Role of Carbon Materials in Heterogenous Catalysis. Carbon 36, 159–175. doi:10.1016/S0008-6223(97)00173-5
Saito, Y., Yoshikawa, T., Inagaki, M., Tomita, M., and Hayashi, T. (1993). Growth and Structure of Graphitic Tubules and Polyhedral Particles in Arc-Discharge. Chem. Phys. Lett. 204, 277–282. doi:10.1016/0009-2614(93)90009-P
Sano, Y., Choi, K., Korai, Y., and Mochida, I. (2004). Adsorptive Removal of Sulfur and Nitrogen Species from a Straight Run Gas Oil over Activated Carbons for its Deep Hydrodesulfurization. Appl. Catal. B: Environ. 49, 219–225. doi:10.1016/j.apcatb.2003.12.007
Satterfield, C. (1991). Heterogeneous Catalysis in Industrial Practice. 2nd Edition. New York: McGraw-Hill.
Scheffer, B., van Oers, E. M., Arnoldy, P., de Beer, V. H. J., and Moulijn, J. A. (1986). Sulfidability and HDS Activity of Co-Mo/Al2O3 Catalysts. Appl. Catal. 25, 303–311. doi:10.1016/S0166-9834(00)81248-8
Serp, P., Corrias, M., and Kalck, P. (2003). Carbon Nanotubes and Nanofibers in Catalysis. Appl. Catal. A: Gen. 253, 337–358. doi:10.1016/s0926-860x(03)00549-0
Sing, K., Everett, D., Haul, R., Moscou, L., Pierotti, R., Rouquerol, J., et al. (1985). Reporting Physisorption Data for Gas/solid Systems with Special Reference to the Determination of Surface Area and Porosity. Pure Appl. Chem. 57, 603–619. doi:10.1002/9783527610044.hetcat0065
Speight, J. G. (2000). The Desulfurization of Heavy Oils and Residua. 2nd Edition. New York: Marcel Dekker.
Spevack, P. A., and Mcintyre, N. S. (1992). Thermal Reduction of Molybdenum Trioxide. J. Phys. Chem. 96, 9029–9035. doi:10.1021/j100201a062
Tang, D., Sun, L., Zhou, J., Zhou, W., and Xie, S. (2005). Two Possible Emission Mechanisms Involved in the Arc Discharge Method of Carbon Nanotube Preparation. Carbon 43, 2812–2816. doi:10.1016/j.carbon.2005.05.034
Titirici, M.-M., and Antonietti, M. (2010). Chemistry and Materials Options of Sustainable Carbon Materials Made by Hydrothermal Carbonization. Chem. Soc. Rev. 39, 103–116. doi:10.1039/B819318P
Van Veen, J. A. R., Colijn, H. A., Hendriks, P. A. J. M., and van Welsenes, A. J. (1993). On the Formation of Type I and Type II NiMoS Phases in NiMo/Al2O3 Hydrotreating Catalysts and its Catalytic Implications. Fuel Process. Techn. 35, 137–157. doi:10.1016/0378-3820(93)90089-M
Vissers, J., Scheffer, B., de Beer, V., Moulijn, J., and Prins, R. (1987). Effect of the Support on the Structure of Mo-Based Hydrodesulfurization Catalysts: Activated Carbon versus Alumina*1. J. Catal. 105, 277–284. doi:10.1016/0021-9517(87)90058-3
Yeh, Y.-W., Raitses, Y., and Yao, N. (2016). Structural Variations of the Cathode deposit in the Carbon Arc. Carbon 105, 490–495. doi:10.1016/j.carbon.2016.04.074
Yin, H., Zhou, T., Liu, Y., Chai, Y., and Liu, C. (2011). NiMo/Al2O3 Catalyst Containing Nano-Sized Zeolite Y for Deep Hydrodesulfurization and Hydrodenitrogenation of Diesel. J. Nat. Gas Chem. 20, 441–448. doi:10.1016/s1003-9953(10)60204-6
Keywords: carbon-supported catalysts, arc discharge, by-products, metal compositions, type II Ni-Mo-S phase, hydrodesulfurization, hydrodenitrogenation, characterizations
Citation: Aryee E, Dalai AK and Adjaye J (2022) Synthesis and Characterization of NiMo Catalysts Supported on Fine Carbon Particles for Hydrotreating: Effects of Metal Loadings in Catalyst Formulation. Front. Chem. Eng. 3:764931. doi: 10.3389/fceng.2021.764931
Received: 26 August 2021; Accepted: 10 December 2021;
Published: 12 January 2022.
Edited by:
Jose Escobar, Mexican Institute of Petroleum, MexicoReviewed by:
Mohan Rana, Kuwait Institute for Scientific Research, KuwaitLuděk Kaluža, Institute of Chemical Process Fundamentals (ASCR), Czechia
Copyright © 2022 Aryee, Dalai and Adjaye. This is an open-access article distributed under the terms of the Creative Commons Attribution License (CC BY). The use, distribution or reproduction in other forums is permitted, provided the original author(s) and the copyright owner(s) are credited and that the original publication in this journal is cited, in accordance with accepted academic practice. No use, distribution or reproduction is permitted which does not comply with these terms.
*Correspondence: Ajay Kumar Dalai, ajay.dalai@usask.ca