Sulfurized carbon: a class of cathode materials for high performance lithium/sulfur batteries
- Electrochemistry Branch, RDRL-SED-C, Sensors and Electron Devices Directorate, U.S. Army Research Laboratory, Adelphi, MD, USA
Liquid electrolyte lithium/sulfur (Li/S) batteries cannot come into practical applications because of many problems such as low energy efficiency, short cycle life, and fast self-discharge. All these problems are related to the dissolution of lithium polysulfide, a series of sulfur reduction intermediates, in the liquid electrolyte, and resulting parasitic reactions with the Li anode. Covalently binding sulfur onto carbon surface is a solution to completely eliminate the dissolution of lithium polysulfide and make the Li/S battery viable for practical applications. This can be achieved by replacing elemental sulfur with sulfurized carbon (SC) as the cathode material. This article reviews the current efforts on this subject and discusses the syntheses, electrochemical properties, and prospects of the SC as a cathode material in the rechargeable Li/S batteries.
Introduction
Rechargeable lithium/sulfur (Li/S) batteries have recently received significant attention due to their high theoretical energy density (2600 Wh/kg or 1256 Wh/L based on sulfur) as well as low cost and natural abundance of elemental sulfur. Major problems with the Li/S battery are low energy efficiency, fast capacity fading, and high self-discharge rate, all of which are related to the dissolution of long-chain lithium polysulfide (PS, Li2Sn, n ≥ 4) into liquid electrolyte and resulting parasitic reactions with the Li anode. In fact, dissolution in organic electrolytes is the intrinsic nature of long-chain PS and is unavoidable as long as a non-aqueous liquid electrolyte is used in the battery (Zhang, 2013). The only solution to making the rechargeable Li/S batteries commercially successful is to reduce or eliminate the resultant adverse effect of PS dissolution. As a solution, sulfur-carbon (S-C) composites have been intensively investigated to trap dissolved PS within the cathode. This approach has been well summarized by many recent review articles (Evers and Nazar, 2013; Park et al., 2013; Wang et al., 2013; Yang et al., 2013). Theoretically, the S-C composite cannot prevent the dissolution of long-chain PS, instead trap in some degree the dissolved PS within the carbon pores before reduction to insoluble products (Li2S2 or Li2S). In this case, the parasitic reactions between the dissolved PS and solvents still remain and more importantly large amounts of carbon must be incorporated into the battery, which significantly reduces energy density of the battery. On the other hand, the electromigration of PS anions, which is driven by the electrical field within the battery, is hard to be overcome by the physical absorption or adsorption of carbon. A complete solution to the dissolution of PS is to chemically bind the sulfur species onto a polymer backbone or carbon surface. This can be achieved by using sulfurized carbon (SC) as the cathode material of Li/S batteries. In this review, the current status, existing problems and prospects of this type of materials will be summarized and discussed.
Properties and Manufacture of Sulfurized Carbon
Sulfurized carbon is a compound in which short sulfur chains are covalently bound onto the surface of carbon particles. The chemical C–S and C =S bonds have been identified by the XPS spectra (C1s at 284.3 eV and S2p3/2 at 163.7 eV) and FTIR spectra (1180 and 550 cm−1). Due to these covalent bonds, the SCs are chemically stable in strong bases and acids. They are insoluble in organic solvents and thermally stable up to 700°C (Chin, 1981). Therefore, sulfur in SC cannot be removed by the normal processes widely used for the removal of elemental sulfur, such as vaporization above melting point (293°C) of sulfur and solvent extraction using CS2 or toluene. The SCs have long been investigated as a highly efficient sorbent for the removal of heavy metal ions in environmental pollution controlling systems (Krishnan and Anirudhan, 2002), and were first proposed as a cathode material for rechargeable Li/S batteries in 1980 (Chang, 1980).
The SCs are manufactured in large scale by reacting the functional groups, such as C–H, –OH, >C =O, –C(=O)OH, and >C =C <, on the surface of carbon with sulfur at elevated temperature. The reactions are heavily dependent on the surface functional groups and pore structure (Puri and Hazra, 1971). These reactions may involve any of radical reaction, electrophilic addition, and nucleophilic substitution. The sulfur source can be elemental sulfur, H2S, SO2, or CS2, the latter three of which generate elemental sulfur through either oxidization or reduction by the surface functional groups of carbon. In addition to the commercially available carbon, synthetic or natural polymers can also be used as the precursor for the carbon or can be directly pyrolyzed in the presence of sulfur. In these cases, the type of polymers affects the chemistry of the SCs and the content of sulfur in the SCs. More interestingly, scrap tires that already contain small amounts of sulfur are also a good precursor for the SCs, which offer a beneficial means for the recycling of waste tires (Yuan et al., 2004).
Sulfurization of carbon with elemental sulfur at elevated temperatures is the most common practice for the laboratory preparation of SCs. In this context, it is of particular importance to understand the thermal behavior of the molten sulfur. Between the melting point (119°C) and boiling point (293°C), the molten sulfur is present in the form of equilibrium of various sulfur species (Sn) with n ranging from 5 to 33. There is a critical temperature at 159.4°C, at which all physical properties, such as viscosity, density, surface tension, color, and so on, of the molten sulfur are discontinued due to the polymerization of sulfur and the followed depolymerization at higher temperature (Meyer, 1976). In the vapor, the equilibrium is dominated by small sulfur species (Sn with n = 2–5), depending on the temperature and pressure. Therefore, the temperature and pressure are two major factors to control the content of sulfur and the length of – Sn– chains for the preparation of SC materials. High temperature generally results in shorter sulfur chain and more uniform sulfur distribution (Korpiel and Vidic, 1997; Kwon and Vidic, 2000). During sulfurization, elemental sulfur is not only a sulfur source but also a dehydrogenating agent.
Electrochemistry of Sulfurized Carbon
Sulfurs (–Sn–) in a polysulfide chain are electrochemically active, however, the activity of those bound to carbon depends on the type of S-C bond. Sulfurs in a double bond, such as >C =S and –C(=S)–S–, are electrochemically inactive, whereas the activity of those in the C–S single bond depends on the stability of the radical or carbanion formed by the elimination of sulfur, as described by Eqs 1 and 2:
The C–S bond is inactive when bound to an sp3 carbon, which is unable to stabilize the radical and carbanion, however, it becomes electrochemically active when bound to a conjugated sp2 carbon, which is able to delocalize the radical and carbanion. The reduction potentials of Eqs 1 and 2 are generally declined with the degree of delocalization, for example, ∼1.3 V vs. Li/Li+ for long linear polyacetylene (Shacklette et al., 1983) and 0.1–0.3 V vs. Li/Li+ for large plane graphite.
Beside sulfur, the single or conjugated >C =C < bonds in the SC may also be electrochemically active, which often contributes extra capacity to the Li/S battery (Fanous et al., 2011; Wang et al., 2012a). The length of the –Sn– chains must be suitable for reliable cycling of the Li/S battery. Long –Sn– chain will rearrange to release elemental sulfur or break down into soluble polysulfides, whereas short –Sn– chain results in lower capacity but good capacity retention. In order to obtain high capacity and good cycling reliability, it is necessary to increase the content of sulfur and optimize the length of sulfur chain. This can be achieved by modifying the surface functional groups on the carbon and controlling the conditions of sulfurization.
Due to the substantial insolubility of SC and Li2S in organic electrolytes, the SC is discharged and charged entirely through a solid-to-solid phase transition from the SC to Li2S phase. In discharge, the SC is directly reduced into Li2S on the surface of conducting carbon. In charge, the –C− carbanion linking to a conjugated sp2 carbon and the –C–S− anion linking to a non-conjugated sp3 carbon preferentially lose an electron to form an anionic radical, onto which sulfur is grafted and grown. Beside this, Li2S also has the possibility to form long-chain PS on the surface of the conducting carbon, which is affected by the nature of electrolyte solvents and the charge rate. The most important advantages of the Li/SC batteries over conventional Li/S batteries are nearly 100% coulombic efficiency except for the first cycle, stable capacity retention, extremely low self-discharge rate, and excellent safety.
Sulfurized Carbon Versus S-C Composite
The S-C composites are a class of porous carbon materials with elemental sulfur impregnated into the meso- or micro-sized pores. These materials are generally made by infiltrating molten sulfur into the pores of carbon near the critical temperature (159.4°C), at which the molten sulfur has lowest viscosity (Meyer, 1976). A post treatment by heating the product above boiling point of sulfur for a few hours is often applied to vaporize the residual sulfur on the outer surface of carbon particles. For this purpose, an around 300°C temperature has been widely used. This process must initiate the reaction of sulfur and functional groups present on the interior walls of the carbon pores. Therefore, there is no distinct boundary in the chemical composition between the SCs and the S-C composites. The most significant differences are the discharge voltage profile and the chemical compatibility with liquid electrolyte, as stated below.
Discharge Voltage Profile
Electrochemical characteristics of the S-C composites and SC compounds are compared in Figure 1. The S-C composites feature two reduction current peaks at ∼2.3 and ∼2.0 V in CV (Figure 1A), and two voltage plateaus at ∼2.3 and ∼2.0 V in discharge curve (Figure 1B), respectively. These are the typical characteristics of elemental sulfur in liquid electrolyte, in which the reduction at ∼2.3 V corresponds to a solid-to-liquid (from S8 to dissolved Li2S8) phase transition and the one at ∼2.0 V to a liquid-to-solid (from the dissolved Li2S6 to Li2S2 or Li2S) phase transition (Zhang, 2013). The SC compounds feature only a single and broad reduction current peak starting at 2.1 V and ending at 1.5 V in CV (Figure 1C), and a sloping voltage plateau near 2 V with a significant voltage hysteresis and a much larger capacity for the first discharge (Figure 1D). Both the single reduction current peak in CV and the single sloping voltage plateau in discharge curve suggest a solid-to-solid (i.e., from SC to Li2S) phase transition. The voltage hysteresis and much larger capacity in the first discharge are also observed in many conversion-type cathode materials (Cabana et al., 2010). The voltage hysteresis is due to the over-potential, i.e., slow reaction kinetics, caused by the poorly conducting interface between the particles of SC and the conducting carbon. The extra irreversible capacities are mainly caused by the catalytic reduction of electrolyte solvents on the fresh surface of SC and carbon particles. Other possible sources are the reduction of surface groups on the conducting carbon and of the unreacted surface groups on the SC. It is noted that the solvent reduction potentials here are much higher than those (generally at 0.8–1.0 V vs. Li/Li+) observed from the graphite anode of Li-ion batteries. This is due to the catalytic effect of the SC surface, which significantly reduces the reduction over-potential. A similar phenomenon has been observed from a Fe/Cu catalyzed carbon, on which the reduction of carbonate solvents takes place at ∼1.7 V vs. Li/Li+ (Zhang et al., 2012).
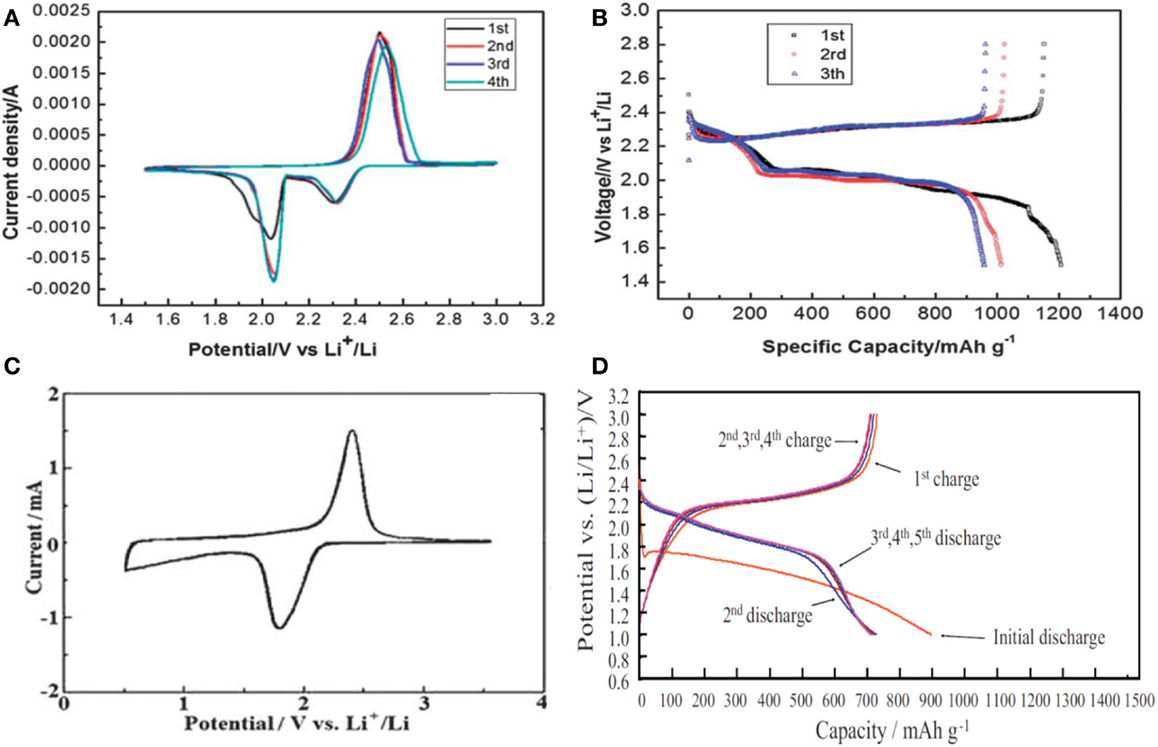
Figure 1. Typical electrochemical characteristics of Li/S cells. (A,B) S-C composite, and (C,D) SC compound. Reproduced with permission of Wang et al. (2012b), Duan et al. (2013), Miao et al. (2013).
Chemical Compatibility of Liquid Electrolyte
The other significant difference between the S-C composite and the SC compound is the chemical compatibility with liquid electrolytes. Because of the strong nucleophilic reactivity, polysulfide anions react with carbonate solvents and LiPF6 used in the state-of-the-art Li-ion batteries (Gao et al., 2011; Yim et al., 2013). As a result, only components that are stable against the nucleophilic attack can be used for the electrolyte of S-C composite cathodes, for example, LiTFSI or LiSO3CF3 for salt and DME or DOL for solvent. On the contrary, the LiPF6-carbonate electrolytes are quite chemically compatible with SC cathodes, and even outperform the ether-based counterparts. This is attributed to two facts: (1) the substantial insolubility of SC significantly reduces the nucleophilic reactivity of polysulfide anions, and (2) the insoluble reaction products formed by the limited nucleophilic reaction of PS with carbonate solvents build up a stable surface layer (or called solid electrolyte interphase) to prevent further reaction. It has been repeatedly reported that the Li/SC batteries perform worse in ether-based electrolytes than in carbonate-based ones (Fanous et al., 2011; Wang et al., 2012b; Zhang et al., 2013). This is because the SC does not form an insoluble surface layer with more stable ethers, instead, the high dissolving ability of ether solvents promotes the formation of soluble PS (Li2Sn, n ≥ 4) in charge, as described by Eq. 3.
As an example, Zhang et al. (2013) compared the cycling performance of Li/SC cells with a 1 M LiPF6-PC-EC-DEC electrolyte and a 1 M LiTFSI-DME-DOL electrolyte, respectively. It is shown in Figures 2A–D that the Li/SC cell performed much better in the carbonate-based electrolyte (Figures 2A,C) than in the ether-based electrolyte (Figures 2B,D) for both the specific capacity and capacity retention. The poor performance of Li/SC cell in the ether-based electrolyte is attributed to the formation of soluble PS as indicated by Eq. 3, which is verified by a long upper voltage plateau at ∼2.3 V in the discharge voltage profile (see Figure 2D).
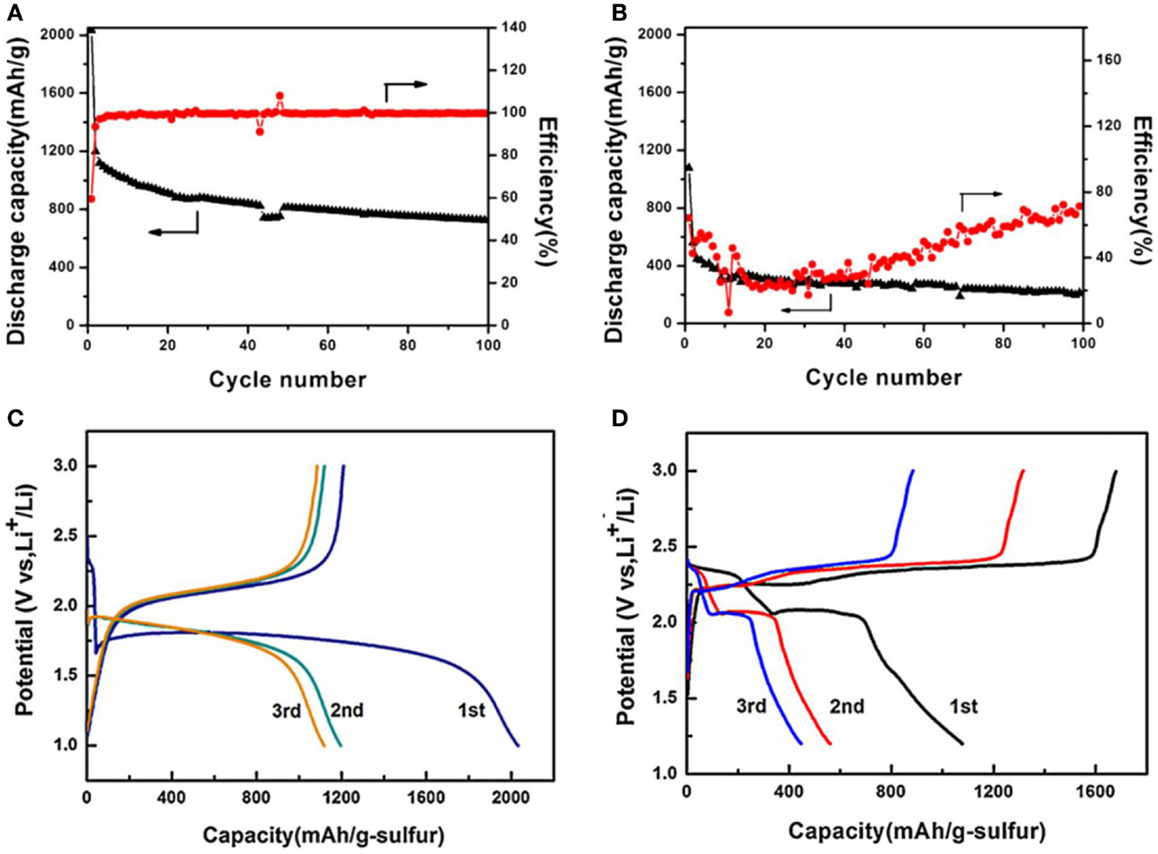
Figure 2. Cycling performance of Li/SC cells at 100 mA/g in a 1 M LiPF6-PC-EC-DEC electrolyte (A,C) and a 1 M LiTFSI-DME-DOL electrolyte (B,D), respectively. Reproduced with permission of Zhang et al. (2013).
Classes of Sulfurized Carbons
To date, all SCs for use as the cathode material in Li/S batteries are made through the reaction of carbon with elemental sulfur at elevated temperatures. Based on the source of carbon, the SCs can be classified as follows.
Commercial Carbon
The first SC material for the application in rechargeable Li/S batteries was made by reacting carbon with SO2 at 600°C for a period of several hours (Chang, 1980). In this work, three SC compounds with sulfur content of 24.8, 26.0, and 38.1%, respectively, were prepared and tested using more than 10 organic and inorganic electrolytes. It was demonstrated that all Li/SC cells had a 3.2–3.4 V of OCV range and a ∼1.7 V discharge voltage plateau with up to 96% sulfur utilization based on the two-electron reduction. Apparently, the observed OCVs are much higher than the theoretical value of Li/S cells. This can be attributed to the fact that the SC had low sulfur content and the measured OCV was a combined value of the SC and carbon. A similar concept was pursued by Wang et al. (2002a), who made SC by first heating a 1:5 (wt.) mixture of active carbon and sulfur at 200°C for 6 h to infiltrate the molten sulfur into the pores of active carbon and then holding the mixture at 300°C for 3 h to promote sulfurication and vaporize residual sulfur. This work led to a gel polymer Li/SC cell capable of providing a stable capacity of 440 mAh/g at 0.3 mA/cm2. Owing to the presence of small amount of elemental sulfur, about 60 mAh/g capacity for discharge voltage plateau at ∼2.4 V was present in the first discharge. Most recent work was reported by Kim et al. (2013), who heated a 1:5 (wt.) mixture of mesoporous hard carbon spheres and sulfur at 150°C for 7 h and held the mixture at 300°C for another 2 h. They built Li/SC cells using a 1:1 (mol.) LiCF3SO3-TEGDME electrolyte (a RTIL-like complex) and cycled the cells at 0.1 A/g-S. Based on the discharge voltage profile of the Li/SC cells, they concluded that pure SC could be formed only at low sulfur content (20 wt. %), significant amounts of elemental sulfur were present in the sample with 52% sulfur. Common characteristics of the above Li/SC cells are the significant voltage hysteresis and large irreversible capacity in the first discharge as well as the absence of upper discharge voltage plateau. Since the sulfurization is strongly affected by the surface chemistry of the carbon and there are large variations in the surface chemistry among different carbon sources, consistent results using this approach by different authors have never been reached.
Synthetic Polymer Resins
Efficiency of sulfurization is greatly affected by the surface chemistry of carbon. A high concentration of surface functional groups is needed to increase the content of covalently bound sulfur. Pyrolysis of polymer resins provides a great opportunity for making a carbon with desirable surface functional groups and pore structure. At high temperature, the S8 ring breaks down into smaller and much more active Sn (n = 2–6) molecules. These small sulfur molecules can readily dehydrogenate and substitute for oxygen atoms in the surface groups such as –OH, –O–, >C =O, and –C(=O)O–. Therefore, the oxygen-containing natural or synthetic polymer resins have been preferentially selected as the carbon precursor for making the SCs with high sulfur content. Table 1 summarizes the recent efforts on the syntheses of SCs from the pyrolyzed carbon of polymer resins and the cycling performance of the resulting Li/SC batteries. Beside the common features of Li/SC batteries, such as excellent chemical compatibility with LiPF6-carbonate electrolytes, single discharge voltage plateau, and large initial irreversibility, the following conclusions can be drawn:
(1) Temperature is an essential factor to determine the specific capacity and capacity retention of the Li/SC cells. Temperature affects the concentration of surface functional groups and the degree of carbonization in the resin pyrolysis step, and the sulfur content and sulfur chain length in the sulfurization step. Wang et al. (2012c) showed that only 16 wt. % sulfur could be covalently bound to carbon at 155°C even if a long reaction time (12 h) was applied. Since the SCs are thermally stable up to 700°C, a temperature range of 300–600°C would be appropriate for the sulfurization of carbon.
(2) Functional groups on the carbon surface significantly affect the content of covalently bound sulfur. Unsaturated carbon–carbon bonds are among the most active surface functional groups to react with sulfur, which allows lower sulfurization temperature and results in high sulfur content. Therefore, the polymer resins that potentially produce more unsaturated bonds by pyrolysis are highly desirable for increasing the sulfur content of SCs. This approach has been well verified by Duan et al. (2013), who utilized a polyyne, made by KOH-assisted dehydrochlorination of poly(vinylidene chloride), as the starting carbon, and successfully prepared a SC with 54.1% sulfur. Results showed that the Li/SC cells could be stably cycled in both the carbonate-based (LiPF6-EC-DEC) and ether-based (LiTFSI-DOL-DME) electrolytes. In particular, the cells retained capacities of 960 and 800 mAh/g after 200 cycles at 0.1 C in the carbonate-based and ether-based electrolyte, respectively. Except for 54.1% sulfur for polyyne, the maximum content of the covalently bound sulfur by the sulfurization of pyrolyzed carbon with elemental sulfur was 42% (Zhang et al., 2010). Duan et al.’s work very likely led to a new direction for the development of SCs with high sulfur content and reliable cycling performance.
(3) The effect of carbon architecture or morphology is not as significant as the temperature and carbon surface chemistry on the sulfurization. Table 1 indicates that the maximum sulfur contents for these carbons in the forms of spheres (Zhang et al., 2010), carbon-modified fibers (Zhang et al., 2013), and nanotubes (Xin et al., 2012) are 40–42 wt. %, which is independent of carbon architecture or morphology.
Polyacrylonitrile
Polyacrylonitrile (PAN) has been intensively studied as the carbon precursor for SCs because of the easiness to dehydrogenate and cyclize into conjugated carbon backbones. With an increase in temperature, PAN undergoes three stages of structural changes as illustrated in Figure 3 (Rahaman et al., 2007): (1) dehydrogenation and cyclization into a ladder-structural polymer by the mild oxidization of oxygen or sulfur in the 300–400°C range, (2) deamination to form a ribbon-structural polymer in the 400–600°C range, and (3) carbonization and further graphitization above 600°C. The conjugated carbon backbones formed by the pyrolysis of PAN react with both the radicals and ions of sulfur to produce C-S bonds. Sulfurized polyacrylonitrile (SPAN, although the name cannot reflect the true chemical structure of the product) can be prepared in an inert atmosphere either though the reaction of pyrolyzed PAN (carbon) with sulfur or through direct reaction of the PAN polymer with sulfur, which are summarized as follows.
Sulfurization with pyrolyzed PAN
This approach consists of two steps: (1) pyrolysis of PAN resin to form carbon, and (2) sulfurization with elemental sulfur to form SPAN. To demonstrate this, Lai et al. (2009) first made a highly porous carbon by Na2CO3-assisted pyrolysis of PAN at 750°C for 2 h and then conducted reaction of the resultant carbon with sulfur at 300°C for 3 h. This process gave SPAN with a 57 wt. % sulfur. The Li/SPAN cell with a 1 M LiPF6 1:4:5 (vol.) PC-EC-DEC electrolyte showed a single discharge voltage plateau and a stable capacity of 770 mAh/g for 110 cycles at 40 mA/g between 1.0 and 3.0 V. In a similar manner, Guo et al. (2011) first pyrolyzed PAN into disordered carbon nanotubes using a template nanotechnology, and then reacted carbon nanotubes with sulfur at 500°C for 3 h. The resulting SPAN contained 40 wt. % sulfur and was thermally stable up to 700°C, indicating a strong evidence that sulfur was covalently combined with carbon. Even with a 1 M LiTFSI TEGDME electrolyte, the Li/SPAN cell still showed stable capacities of nearly 700 mAh/g for 100 cycles at 10 mA/g between 1.5 and 3.0 V. This work also revealed that low temperature led to incomplete sulfurization so that a short upper voltage plateau at ∼2.4 V appeared even in the second discharge of the Li/SC cell.
Sulfurization with PAN polymer
One-pot reaction of PAN resin with elemental sulfur provides a facile approach for the preparation of SPAN. During sulfurization, sulfur plays two roles: (1) acting a mild oxidant to dehydrogenate PAN and (2) offering a sulfur source to sulfurize the dehydrogenated PAN. These two processes happen simultaneously and promote each other. This approach was first reported by Wang et al. (2002b), who heated a mixture of PAN and sulfur at 280–300°C in Ar for 6 h, and later intensive investigations into this type of materials and resulting rechargeable Li/SPAN batteries were followed by He’s group of Tsinghua University, China (He et al., 2005, 2009; Wang et al., 2012a,b). Cross structural characterizations using FTIR, Raman, XPS, and TOF-SIMS spectra, respectively, consistently identified the presence of C–S, S–S, C =C, >C =S, C =N, and –C(=N)–NH2 bonds/groups in the resulting SPAN (Yu et al., 2004, 2005; Fanous et al., 2011). It is shown that temperature critically affects the content of sulfur as well as the length and distribution of sulfur chains, and further determines the electrochemical properties of SPAN. The suitable reaction temperature is in a range of 280–550°C, which typically generates SPAN with a 30–55 wt. % of covalently bound sulfur. From a comprehensive viewpoint of the specific capacity and capacity retention, the best sulfur content is 42–44 wt. % (Fanous et al., 2012; Wang et al., 2012a). However, the optimum reaction temperatures were reported differently by independent authors, namely 350°C (Wang et al., 2012a), 450°C (Yu et al., 2005), and 550°C (Fanous et al., 2012). These discrepancies might be associated with the different heating procedure and S to PAN ratio in the starting mixture, which are known to significantly affect the cyclization of PAN (Rahaman et al., 2007). In general, high temperature produces low sulfur content and short sulfur chain, leading to low specific capacity but stable capacity retention (Fanous et al., 2012), whereas low temperature neither breaks down the S8 ring into small Sn molecules nor makes the polymer dehydrogenating effectively, resulting in high specific capacity but fast capacity fading due to the presence of elemental sulfur (Yu et al., 2005). Since the sulfur chains are chemically bound to the polymer backbone, the SPANs are thermally stable at 450°C and do not form soluble PS (Li2Sn, n ≥ 4) in discharge, providing very stable capacity retention and extremely low self-discharge rate.
Due to the novel structure of dehydrogenated PAN, short sulfur chains are grafted onto the conjugated carbon as illustrated by Figure 4. As stated in the section of SC electrochemistry, the unsaturated conjugated carbons also contribute to the capacity. Therefore, the SPANs are frequently able to provide capacities of more than the theoretical value of sulfur (Fanous et al., 2011; Wang et al., 2012a), and such cells do not show self-discharge over a month storage (Wang et al., 2002b). The SC cathodes are highly flexible to any type of electrolyte from liquid electrolyte through gel polymer to solid state electrolyte. Table 2 summarizes the cycling performance of Li/SPAN cells in various types of electrolytes. It is important to note that two liquid electrolyte cell systems by Wang et al. (2012a) and Fanous et al. (2013) are very similar in the sulfur content of SPAN and the composition of electrolyte, however, their specific capacities are significantly different (795 vs. 440 mAh/g). This discrepancy is likely because the SPAN made at 350°C has higher ratio of the ladder-structural backbones to the ribbon-structural backbones (see Figure 3). The ladder-structural backbones favor the formation of electrochemically active C–S bonds and resulting C–S bonds contribute to the capacity. Very similar results by Wang et al. (2003) and He et al. (2005) suggest that the lithium salt in gel polymer electrolytes does not affect the specific capacity and capacity retention of the Li/SPAN cells. Using a SPAN with 42.0 wt. % sulfur and a 1 M LiPF6-EC-DEC electrolyte, Wang et al. (2012b) built a 100 mAh Li/SPAN prototype cell in the size of 1 mm × 40 mm × 26 mm, showing that the cell was able to deliver a 437 Wh/kg of energy density (excluding the weight of package) and retained 90.4% capacity after 30 cycles at 100% depth of discharge. The most encouraging finding was that the loading of sulfur in the SC cathode reached as much as 6 mg/cm2, a level that has never been reported for the S-C composite systems. This feature makes it possible to develop the Li/SC batteries with high energy density and excellent safety.

Figure 4. Schematic chemical structure of SPAN. Modified from Fanous et al. (2011).
The most exciting advancement on the research of SPAN as the cathode material would be the success of a prototype Li-ion cell (He et al., 2009). In this practice, He et al. first electrochemically lithiated SPAN by cycling a Li/SPAN cell for three times, and then coupled the prelithiated SPAN with a graphite anode and a 1 M LiPF6 1:1 (vol.) EC-DEC electrolyte. As shown by the voltage profile of charge and discharge in Figure 5, such a cell can be repeatedly cycled between 1 and 3 V without visible capacity fading. This result, although preliminary, strongly suggests that the SCs would be a class of high energy density cathode materials for the next generation of Li-ion batteries, which enable electric vehicles to drive longer distance.
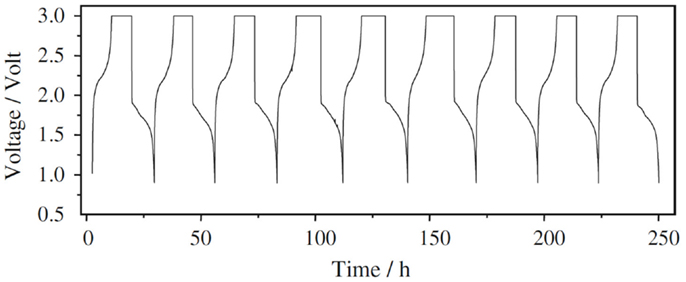
Figure 5. Voltage profile of charge and discharge for a prototype Li-ion cell using a prelithiated SPAN cathode, a graphite anode, and a 1 M LiPF6 1:1 (vol.) EC-DEC electrolyte, cycled at 0.1 C. Reproduced with permission of He et al. (2009).
Concluding Remarks
Sulfurized carbons offer a grand opportunity for developing low cost Li/S batteries with high energy density, good safety, and reliable performance. Use of SCs as the cathode material entirely solves the problem of lithium polysulfide dissolution in Li/S batteries. In addition to the high theoretical capacity, the SCs are suitable for highly loaded cathodes, which make the energy density of Li/SC batteries even higher. The high thermal stability of SCs and low cost of raw materials make the Li/SCs batteries safe and cost competitive. More importantly, the SC cathodes are chemically compatible with LiPF6-carbonate-based electrolytes, which enable them to couple with the lithiated graphite or silicon anode for the development of low cost Li-ion batteries with high energy density and good safety. Furthermore, the SCs are environmentally friendly, the cycled SCs are themselves an excellent sorbent for many heavy metal ions, can be directly disposed into the environment for the removal of heavy metal ions. However, the low sulfur content and the initial high irreversibility remain challenges. The concentration of surface functional groups in commercially available carbons is not high enough to meet the criterion of high sulfur content. In consideration of the sulfur’ strong dehydrogenating ability and the wide availability of polymer resins, one-pot sulfurization may be the most cost-efficient approach for the manufacture of SCs. In order to further increase the sulfur content and lower the cost, better sulfurization technology should be identified, including polymer resin for carbon precursor, sulfur source for more effective sulfurization, and reaction process for denser SC material. Surface modification on the SCs and the use of electrolyte additives may play a crucial role in reducing the initial irreversibility of the SC cathodes. Scrap tires are a solid waste, H2S and SO2 are by-products of the oil/petroleum refinery, the concept of using them as the carbon precursor and sulfur source is of particular significance as it not only leads to a cheap SC cathode material but also is beneficial to saving our environment.
Conflict of Interest Statement
The author declares that the research was conducted in the absence of any commercial or financial relationships that could be construed as a potential conflict of interest.
Acknowledgments
The author thanks Drs. J. Read and C. Lundgren for their critical reading of the manuscript and valuable suggestions.
Abbreviations
CV, cyclic voltammogram; DEC, diethyl carbonate; DMC, dimethyl carbonate; DME, dimethyl ether; DOL, 1,3-dioxolane; EC, ethylene carbonate; EMC, ethylene methyl carbonate; FTIR, Fourier transform infrared spectroscopy; LiTFSI, lithium bis(trifluoromethanesulfonyl)imide; OCV, open-circuit-voltage; PAN, polyacrylonitrile; PC, propylene carbonate; PMMA, poly(methyl methacrylate); PVC, poly(vinylidene chloride); P(VDF-HFP), poly(vinylidene fluoride-co-hexafluoropropylene); RTIL, room temperature ionic liquid; TEGDME, tetraglyme; THF, tetrahydrofuran; TOF-SIMS, time-of-flight secondary ion mass spectrometry; XPS, X-ray photoelectron spectroscopy.
References
Cabana, J., Monconduit, L., Larcher, D., and Palacin, M. R. (2010). Beyond intercalation-based Li-ion batteries: the state of the art and challenges of electrode materials reacting through conversion reactions. Adv. Mater. 22, E170–E192. doi: 10.1002/adma.201000717
Chang, C. H. (1980). “Carbon-sulfur compounds as cathodes for lithium high energy secondary cells,” in Proceedings of 29th Power Sources Conference (Pennington, NJ: The Electrochemical Society, Inc.), 208–211.
Chin, H. C. (1981). Preparation and characterization of carbon-sulfur surface compounds. Carbon 19, 175–186. doi:10.1016/0008-6223(81)90040-3
Duan, B., Wang, W., Wang, A., Yuan, K., Yu, Z., Zhao, H., et al. (2013). Carbyne polysulfide as a novel cathode material for lithium/sulfur batteries. J. Mater. Chem. A 1, 13261–13267. doi:10.1039/c3ta12634j
Evers, S., and Nazar, L. F. (2013). New approaches for high energy density lithium-sulfur battery cathodes. Acc. Chem. Res. 46, 1135–1143. doi:10.1021/ar3001348
Fanous, J., Wegner, M., Grimminger, J., Andresen, A., and Buchmeiser, M. R. (2011). Structure-related electrochemistry of sulfur-poly(acrylonitrile) composite cathode materials for rechargeable lithium batteries. Chem. Mater. 23, 5024–5028. doi:10.1021/cm202467u
Fanous, J., Wegner, M., Grimminger, J., Rolff, M., Spera, M. B. M., Tenzer, M., et al. (2012). Correlation of the electrochemistry of poly(acrylonitrile)-sulfur composite cathodes with their molecular structure. J. Mater. Chem 22, 23240–23245. doi:10.1039/c2jm34487d
Fanous, J., Wegner, M., Spera, M. B. S., and Buchmeiser, M. R. (2013). High energy density poly(acrylonitrile)-sulfur composite-based lithium-sulfur batteries. J. Electrochem. Soc. 160, A1169–A1170. doi:10.1149/2.052308jes
Gao, J., Lowe, M. A., Kiya, Y., and Abruna, H. D. (2011). Effects of liquid electrolytes on the charge-discharge performance of rechargeable lithium/sulfur batteries: electrochemical and in-situ X-ray absorption spectroscopic studies. J. Phys. Chem. C 115, 25132–25137. doi:10.1021/jp207714c
Guo, J., Xu, Y., and Wang, C. (2011). Sulfur-impregnated disordered carbon nanotubes cathode for lithium sulfur batteries. Nano Lett. 11, 4288–4294. doi:10.1021/nl202297p
He, X., Shi, Q., Zhou, X., Wan, C., and Jiang, C. (2005). In situ composite of nano SiO2–P(VDF-HFP) porous polymer electrolytes for Li-ion batteries. Electrochim. Acta 51, 1069–1075. doi:10.1016/j.electacta.2005.05.048
He, X. M., Ren, J. G., Wang, L., Pu, W. H., Wan, C. R., and Jiang, C. Y. (2009). Electrochemical characteristics of sulfur composite cathode for reversible lithium storage. Ionics 15, 477–481. doi:10.1007/s11581-008-0267-3
Kim, J., Lee, D. J., Jung, H. G., Sun, Y. K., Hassoun, J., and Scrosati, B. (2013). An advanced lithium-sulfur battery. Adv. Funct. Mater. 23, 1076–1080. doi:10.1002/adma.201303166
Korpiel, J. A., and Vidic, R. D. (1997). Effect of sulfur impregnation method on activated carbon uptake of gas-phase mercury. Environ. Sci. Tech. 31, 2319–2325. doi:10.1021/es9609260
Krishnan, K. A., and Anirudhan, T. S. (2002). Uptake of heavy metals in batch systems by sulfurized steam activated carbon prepared from sugarcane bagasse pith. Ind. Eng. Chem. Res. 41, 5085–5093. doi:10.1021/ie0110181
Kwon, S., and Vidic, R. D. (2000). Evaluation of two sulfur impregnation methods on activated carbon and bentonite for the production of elemental mercury sorbents. Environ. Eng. Sci. 17, 303–313. doi:10.1089/ees.2000.17.303
Lai, C., Gao, X. P., Zhang, B., Yan, T. Y., and Zhou, Z. (2009). Synthesis and electrochemical performance of sulfur/highly porous carbon composites. J. Phys. Chem. C 113, 4712–4716. doi:10.1021/jp809473e
Miao, L. X., Wang, W. K., Wang, A. B., Yuan, K. G., and Yang, Y. S. (2013). A high sulfur content composite with core-shell structure as cathode material for Li-S batteries. J. Mater. Chem. A 1, 11659–11664. doi:10.1039/c3ta12079a
Park, J. S., Cho, G. B., Ryu, H. S., Ahn, J. H., Ahn, H. J., and Kim, K. W. (2013). Sulphur-carbon composites for Li/S batteries. Mater. Tech. 28, 270–275. doi:10.1179/175355513X13621548393253
Puri, B. R., and Hazra, R. S. (1971). Carbon-sulphur surface complexes on charcoal. Carbon 9, 123–134. doi:10.1016/0008-6223(71)90125-4
Rahaman, M. S. A., Ismail, A. F., and Mustafa, A. (2007). A review of heat treatment on polyacrylonitrile fiber. Polym. Degrad. Stab. 92, 1421–1432. doi:10.1016/j.polymdegradstab.2007.03.023
Shacklette, L. W., Elsenbaumer, R. L., and Baughman, R. H. (1983). Electrochemical cells employing polacetylene and poly(p-phenylene) as active materials. J. Phys-Paris 44, 559–565.
Trevey, J. E., Gilsdorf, J. R., Stoldt, C. R., Lee, S. H., and Liu, P. (2012). Electrochemical investigation of all-solid-state lithium batteries with a high capacity sulfur-based electrode. J. Electrochem. Soc. 159, A1019–A1022. doi:10.1149/2.052207jes
Unemoto, A., Gambe, Y., Komatsu, D., and Honma, I. (2013). Development of high capacity all-solid-state lithium battery using quasi-solid-state electrolyte containing tetraglyme – Li-TFSA equimolar complexes. Solid State Ionics. doi:10.1016/j.ssi.2013.09.043
Wang, D. W., Zeng, Q., Zhou, G., Yin, L., Li, F., Cheng, H. M., et al. (2013). Carbon-sulfur composites for Li-S batteries: status and prospects. J. Mater. Chem. A 1, 9382–9394. doi:10.1039/c3ta11045a
Wang, J. L., Yang, J., Wan, C. R., Du, K., Xie, J. Y., and Xu, N. X. (2003). Sulfur composite cathode materials for rechargeable lithium batteries. Adv. Funct. Mater. 13, 487–492. doi:10.1002/adfm.200304284
Wang, J. L., Yang, J., Xie, J. Y., Xu, N. X., and Li, Y. (2002a). Sulfur-carbon nano-composite as cathode for rechargeable lithium battery based on gel electrolyte. Electrochem. commun. 4, 499–502. doi:10.1016/S1388-2481(02)00358-2
Wang, J. L., Yang, J., Xie, J. Y., and Xu, N. X. (2002b). A novel conductive polymer-sulfur composite cathode material for rechargeable lithium batteries. Adv. Mater. 14, 963–965. doi:10.1002/1521-4095(20020704)14:13/14<963::AID-ADMA963>3.0.CO;2-S
Wang, L., He, X., Li, J., Gao, J., Guo, J., Jiang, C., et al. (2012a). Analysis of the synthesis process of sulphur-poly(acrylonitrile)-based cathode materials for lithium batteries. J. Mater. Chem. 22, 22077–22081. doi:10.1039/c2jm30632h
Wang, L., He, X., Li, J., Chen, M., Gao, J., and Jiang, C. (2012b). Charge/discharge characteristics of sulfurized polyacrylonitrile composite with different sulfur content in carbonate based electrolyte for lithium batteries. Electrochim. Acta 72, 114–119. doi:10.1016/j.electacta.2012.04.005
Wang, D. W., Zhou, G., Li, F., Wu, K. H., Lu, G. Q., Cheng, H. M., et al. (2012c). A microporous-mesoporous carbon with graphitic structure for a high-rate stable sulfur cathode in carbonate solvent-based Li-S batteries. Phys. Chem. Chem. Phys. 14, 8703–8710. doi:10.1039/c2cp40808b
Xin, S., Gu, L., Zhao, N. H., Yin, Y. X., Zhou, L. J., Guo, Y. G., et al. (2012). Smaller sulfur molecules promise better lithium-sulfur batteries. J. Am. Chem. Soc. 134, 18510–18513. doi:10.1021/ja308170k
Yang, Y., Zheng, G., and Cui, Y. (2013). Nanostructured sulfur cathodes. Chem. Soc. Rev. 42, 3018–3032. doi:10.1039/c2cs35256g
Yim, T., Park, M. S., Yu, J. S., Kim, K. J., Im, K. Y., Kim, J. H., et al. (2013). Effect of chemical reactivity of polysulfide toward carbonate-based electrolyte on the electrochemical performance of Li-S batteries. Electrochim. Acta 107, 454–460. doi:10.1016/j.electacta.2013.06.039
Yu, X., Xie, J., Li, Y., Huang, H., Lai, C., and Wang, K. (2005). Stable-cycle and high-capacity conductive sulfur-containing cathode materials for rechargeable lithium batteries. J. Power Sources 146, 335–339. doi:10.1016/j.jpowsour.2005.03.021
Yu, X. G., Xie, J. Y., Yang, J., Huang, H. J., Wang, K., and Wen, Z. S. (2004). Lithium storage in conductive sulfur-containing polymers. J. Electroanal. Chem. 573, 121–128. doi:10.1016/S0022-0728(04)00345-6
Yuan, C. S., Lin, H. Y., Wu, C. H., Liu, M. H., and Hung, C. H. (2004). Preparation of sulfurized powdered activated carbon from waste tires using an innovative compositive impregnation process. J. Air Waste Manag. Assoc. 54, 862–870. doi:10.1080/10473289.2004.10470954
Zhang, B., Qin, X., Li, G. R., and Gao, X. P. (2010). Enhancement of long stability of sulfur cathode by encapsulating sulfur into micropores of carbon spheres. Energy Environ. Sci. 3, 1531–1537. doi:10.1002/chem.201202127
Zhang, S. S. (2013). Liquid electrolyte lithium/sulfur battery: fundamental chemistry, problems, and solutions. J. Power Sources 231, 153–162. doi:10.1016/j.jpowsour.2012.12.102
Zhang, S. S., Ren, X., Tran, D. T., and Read, J. (2012). Catalytic effect of heat-treated iron and copper phthalocyanines in non-aqueous electrolyte Li/air batteries – a review. Green 2, 63–69. doi:10.1515/green-2012-0004
Keywords: sulfurized carbon, sulfurization, sulfur-carbon composite, sulfurized polyacrylonitrile, cathode material, polysulfide, lithium/sulfur battery
Citation: Zhang SS (2013) Sulfurized carbon: a class of cathode materials for high performance lithium/sulfur batteries. Front. Energy Res. 1:10. doi: 10.3389/fenrg.2013.00010
Received: 14 November 2013; Paper pending published: 25 November 2013;
Accepted: 28 November 2013; Published online: 16 December 2013.
Edited by:
Xiangming He, Tsinghua University, ChinaReviewed by:
Jiulin Wang, Shanghai Jiao Tong University, ChinaJinbao Zhao, Xiamen University, China
Li Wang, Tsinghua University, China
Xueping Gao, Nankai University, China
Jian Chen, Chinese Academy of Sciences, China
Copyright: © 2013 Zhang. This is an open-access article distributed under the terms of the Creative Commons Attribution License (CC BY). The use, distribution or reproduction in other forums is permitted, provided the original author(s) or licensor are credited and that the original publication in this journal is cited, in accordance with accepted academic practice. No use, distribution or reproduction is permitted which does not comply with these terms.
*Correspondence: Sheng S. Zhang, Electrochemistry Branch, RDRL-SED-C, Sensors and Electron Devices Directorate, U.S. Army Research Laboratory, Adelphi, MD 20783-1197, USA e-mail: shengshui.zhang.civ@mail.mil; shengshui@gmail.com