Impact of ultrasonic mixing on virgin and waste vegetable oils for biodiesel production
- 1Department of Mechanical Engineering, George Mason University, Fairfax, VA, United States
- 2Department of Chemistry, Tennessee Technological University, Cookeville, TN, United States
- 3Department of Mechanical Engineering, Tennessee Technological University, Cookeville, TN, United States
This paper investigates the use of waste vegetable oil (WVO) for production of biodiesel. The study explores the improvement of biodiesel production using ultrasonic mixing to achieve high yields. Different oil streams, including virgin canola oil and WVO, were used as the raw material for the transesterification processes. These oils had different fatty acid contents as a result of environmental or previous processing conditions. The impact of free fatty acid (FFA) content on the resulting yield was assessed. It was demonstrated that the yield was influenced by production parameters such as reaction time, reaction temperature, molar/volume ratios of oil to alcohol, catalyst amount, and mechanical mixing. This was accomplished by automating the biodiesel production from WVO, thereby achieving improved processing and requiring minimal direct human involvement. A biodiesel production apparatus was developed with a Raspberry Pi 3 microcomputer to control the process. The particular choice of these process parameters depended on the particular oil type. This research used mixtures of virgin and waste vegetable oils at different volume ratios (oil to alcohol) of 4:1, 6:1, and 8:1, which was determined by the FFA content of the oil. In addition to mechanical mixing, ultrasonication rated at 500 W, 20 kHz was used to enhance mixing by adding 450 kJ to the process, thereby reducing both the processing time and the amount of methoxide needed to perform a base-catalyzed transesterification. This research demonstrated that optimal yield depends on temperature, catalyst concentration, FFA content of the oil, and the energy introduced by sonication.
1 Introduction
This paper describes using mixtures of virgin canola oil and waste vegetable cooking oils (WVO) obtained from a cafeteria facility for production of biodiesel utilizing a transesterification process. The system and procedures that were developed were designed to be suitable for biodiesel production in remote areas with limited access to advanced technology, and where minimal operator intervention would be required. This was achieved by utilizing a Raspberry Pi 3-based control approach. Transesterification is a widely accepted process that provides good fatty acid conversion and produces acceptable viscosity values suitable for biodiesel. Transesterification is straightforward to use for such small-batch biodieselproduction because the processes, apparatus, and materials needed do not require sophisticated equipment or complex procedures. Biodiesel production can be a time-consuming reaction, but the process rate can be enhanced using microwave assistance irradiation (as a substitute for heating coils), ultrasonic mixing, chemical titration (to achieve optimal reaction component ratios), heating and (mechanical mixing by convection). Other methods for biodiesel production include blending, catalytic cracking, pyrolysis, gasification, hydrolysis, micro-emulsion, enzymatic processing, catalytic cracking, and supercritical processing. Some of these methods require high temperature and pressure. Higher reaction temperatures leads to the evaporation of the alcohol, resulting in lower yield. Depending on the kind of oil, it is generally agreed that the optimum reaction temperature ranges from 50°C to 65°C (under the flash point of methyl alcohol/oil mixture). The maximum temperature for methanol is approximately 65°C, and when this is exceeded it results in a boiling off of alcohol. The reaction time plays a vital role in any reaction such that insufficient time results in unreacted reactants causing lower ester yield. Sustainability, practicality, applicability, and costs were key factors that influenced the decision to use the transesterification process described in this paper; other biodiesel production methods were deemed to be beyond the scope of the present investigation. A complete description of the sonication mixing schedules and the oil-to-alcohol volume ratios that were employed is presented. The present investigation was performed to provide further details regarding the magnitude of the sonication energy added to the reactant mixture during the biodiesel production process, and to clearly establish whether the additional energy input is beneficial or detrimental to the biodiesel production process. The goal was to study whether it was possible to increase the production rate and yield of biodiesel using sonication. Likewise, this research was intended to further examine if optimum yields of biodiesel production can be achieved using ultrasonic mixing for different feedstock qualities.
2 Literature search
Biodiesel produced from a transesterification process using vegetable oil as a reactant yields glycerin as a by-product. These vegetable oils contain free fatty acids whose presence is a critical factor affecting biodiesel production (Ityokumbul Igbax et al., 2022). Showed that yields of biodiesel are affected by the FFA content of the vegetable oil used. Mixing and heating affected the production rate, the biodiesel volumetric yield, and the viscosity and quality of the produced biodiesel. A 96% yield (based on volume) was achieved with a WVO to methanol volume ratio of 6:1, a 0.6% weight concentration of catalyst (NaOH) at 6.25g, and FFA values of approximately 5%. The procedure to assess the FFA content and the required catalyst amount was thoroughly elucidated in Ityokumbul Igbax et al. (2022). During the production runs it was observed that when too little catalyst was used the mixture began to foam and gradually became more viscous. Similarly, when too much catalyst was utilized, the mixture began to form soap. The glycerin must be separated from the biodiesel that is produced; this is discussed in greater detail by the paper titled; Comparison of Biodiesel/Glycerin separation by gravitational settling and electrostatic settling by Igbax and others in the 2023 American Society of Engineers Conference. It was shown that use of electrostatic coagulation yielded significant reductions in the time required to fully separate the biodiesel and glycerin, as compared to gravitational settling.
Gashaw and Teshita (2014) demonstrated that transesterification of oils having higher free fatty acid content was difficult when an alkaline base catalyst was used, and this often resulted in soap formation (Huang et al., 2023), used transesterification with an in situ extraction of product to produce a more efficient biodiesel yield (Mahmoodi et al., 2019; Zhang et al., 2022). Acknowledged the need for esterification/transesterification of FFA for different oils using heterogenous or homogenous catalysis. To enhance the efficiency of production (Mousavi et al., 2020), emphasized the need of using improved production methods (Gao et al., 2023), identified the need to optimize the biodiesel production process, and noted that transesterification resulted in improved biodiesel yield (Fadhil et al., 2012), considered the pretreatment of oil with an acid dissolved in methanol. The second step of the process was base catalyzed transesterification, in which oil was reacted with methanol in the presence of an alkaline catalyst to form ester and glycerol (Lam et al., 2010), demonstrated that when waste vegetable oil was used, pretreatment was needed to ensure the feedstock was at appropriate FFA content levels, which did not require drastic adjustment of process parameters. Free fatty acid content significantly affects the transesterification process. Higher FFA content may render the oil useless for biodiesel production, but it may be utilized for grease making, or generation of coolants and other base products. Production of biodiesel often requires the use of different mixture grades of vegetable oils, which causes different chemical and thermal properties of the fluid. These changes are based on the environmental exposure, processing, conditions, and constituents/impurities of the source. This affects the FFA, viscosity, density, impurities, and water content of the reactants. Transesterification is the most viable method and remains the most efficient process for the large-scale production/formation of biodiesel (Thirumarimurugan et al., 2012), observed that transesterification is the best process used to make biodiesel. The process involves the combination of various oils, alcohol, and a primary catalyst. Vegetable oil consists of triglycerides that are composed of three chains of fatty acids, all connected by a glycerin molecule. A triglyceride is an ester comprised of a chain of glycerol and three fatty acids (Mittelbach and Remschmidt, 2004), noted that methanolysis (where one reactant is methanol) helps to enhance the emulsification process and improves the reaction rate. This process produces glycerol and fatty acid methyl esters (FAME) which are immiscible, and thus form separate layers of biodiesel and glycerol. Methanol is a widely preferred component used in transesterification, owing to its availability, reactive properties, and its relatively cheap cost. The fatty acids are then esterified through the process of transesterification, which produces biodiesel with a by-product of glycerin. Vegetable oil or animal fat is reacted with methanol in the presence of the catalyst sodium hydroxide (lye) to produce a mixture of glycerin and fatty acid esters (Agee et al., 2014), incorporated solar reflectors developed from satellite dishes into the synthetic procedure for biodiesel production. The generation of carbon dioxide waste during biodiesel production was eliminated. Their technique used recovered biodiesel waste glycerol as the solvent system for Wolff-Kishner reduction reactions. It was shown that different energy inputs used for biodiesel production had an impact on the yield, and it was noted that it is therefore imperative to quantity the energy added for biodiesel production.
The use of catalysts in chemical reactions was discussed by Wang et al. (2023) According to Sanli and Canakci (2008) catalyst amount is estimated based on the oil type. Oils having high fatty acids may require more catalyst by volume, and acid catalysis is beneficial when the FFA is high (Chen et al., 2023). Supported the used of heterogenous catalysis for the optimization of biodiesel production to achieve a yield of 93% with studies that favor acid activated catalyst for biodiesel production (Huang et al., 2023). Carried out a controllable study which favored the use of acidic catalyst for biodiesel production using Jatropha to produce a high yield of 97.2% (Li et al., 2023). Used other method such solid acid for green efficient catalytic esterification to achieve a yield of 98.6%. Generally, this catalyst could either be alkaline or acidic. Both have advantages and disadvantages regarding the reaction combination, which consequently impacts the yield of biodiesel (Sanli and Canakci, 2008; Jagadale et al., 2012; Gebremariam and Marchetti, 2017), among many researchers, preferred the use of a catalyst with a basic composition, because it offers high conversion rates and shorter reaction time. Acid catalysts are used to break down oils with high fatty content and this can also be some part of pre-processing. Preprocessing is preparing the feedstock oil to the appropriate condition needed for biodiesel production. Hence, the alkali-catalyzed transesterification operations are efficient with high-quality, low-acidic vegetable oils, which usually are a better grade source material than waste oils. The use of sodium hydroxide is the best choice as it offers smooth mixing, ease of reaction and overall favorable reaction conditions. However, due to the caustic nature of the solution, it tends to affect the rubber components of the equipment such as the pumps, valves and more directly the seals. The use of specific catalysts depends on other factors of operation such as the temperature, mass/volume of reactants (oil and alcohol), and fatty acid content (Freedman et al., 1984). Investigated a mixture ratio of 6:1 with alkaline catalysts (either sodium hydroxide or methoxide), temperatures of 60°C or higher, and fully refined oils. The reaction was complete in 1 h, whereas when the reaction temperature was maintained at 32°C it required 4 h for the transesterification process to be completed. Transesterification by acid catalysis was much slower than by alkali catalysis. This is the reason why NaOH is the often choice of catalyst to be used. Furthermore, this clearly demonstrates that the temperature of reaction affects processing time.
Different vegetable oils then have different composition (Anastopoulos et al., 2015). Studied transesterification reactions of four different vegetable oils (sunflower, rapeseed, olive oil, and used frying oil) with ethanol, using sodium hydroxide as the catalyst. The amount of catalyst ranged from 0.25% to 1.5% by weight, and molar ratios of ethanol to sunflower oil ranging from 6:1 to 12:1 were evaluated at reaction temperatures that were varied between 35°C and 90°C using sunflower oil. The other vegetable oils were converted to ethyl esters under optimum reaction conditions. The ideal conditions for first stage transesterification were an ethanol/oil molar ratio of 12:1, NaOH amount (1% by weight), and 80°C temperature, whereas the maximum yield of ethyl esters reached 81.4% by weight. In the second stage, the yield of ethyl esters was improved by 16% in relation to the one-stage transesterification, which was obtained using a catalyst concentration of 0.75% and an ethanol/oil molar ratio of 6:1.
One significant innovation related to the processing of biodiesel is the use of ultrasound to increase the reaction rate. Ultrasound is a sound effect impacted by cyclic pressure moving with a frequency and amplitude that is not audible to the human ear. It ranges from 20 Hz to 20 kHz, and in liquids it exhibits an acoustic wavelength of roughly 100–0.15 mm; see (Suslick et al., 1999). The use of ultrasound is the concept called sonochemistry, which relates to the use of mechanical activation and acoustic cavitation that causes an increase in area of contact between fluids, thus making it easier for the reactants to mix, combine, and form new substances. The utilization of ultrasound in chemical processing enhances both the mass transfer (transport) and chemical reactions (kinetics), offering the potential for shorter reaction times, cheaper reagents, and less extreme physical conditions. Ultrasound energy is well known as a useful tool to make fine emulsions from immiscible liquids. The goal of ultrasound in fluid kinetics is to break the particles into smaller fragments so that mixing is enhanced. This process enables the reaction to take place faster, and as a result, the processing time is reduced. Ultrasound generates activation energy to speed up a chemical reaction by acoustic cavitation, which is responsible for breaking the bonds holding the molecules in the liquid phase. The reaction works in two ways: compression of the liquid is followed by rarefaction (expansion), which causes a pressure drop to create small, oscillating bubbles of gaseous substances. During the collision of these bubbles, there is an increased area of contact between the immiscible fluids which collide and collapse violently. Increased mechanical action involves stirring, circulation, and sonication, which has been proven to enhance the biodiesel production process; refer to (Ho et al., 2016; Sivaramakrishnan and Incharoensakdi, 2018a; Malani et al., 2019). A recent investigation on ultrasound used in conjunction with biodiesel production by Oliveira et al. (2018) showed that its use had a significant influence on the conversion of the raw material. Their results were obtained on various oil samples that produced different yields. However, they did not mention the factors that could cause a batch failure. The importance of ultrasound was highlighted by Almasi et al. (2021) who demonstrated that its use resulted in a reduction of energy required for processing biodiesel.
The utilization of ultrasound tends to dissociate the molecular forces binding components by compressing and stretching the bonds, thus causing a series of compression and rarefaction waves; refer to Jambrak et al. (2008); Bucham et al. (2022). Ultrasonic mixing has been observed to improve blends of immiscible liquids of similar viscosities, liquids of different viscosity, or more viscous liquids that may require high mechanical shear for fast and complete blending. With the various changes associated with viscosity and density, ultrasound is applied to a process by adjusting the flow rate; refer to Towerton (2007). According to Khan et al. (2017), there are numerous applications of ultrasound because of the resulting intense mixing and cavitation. One reason producers have chosen ultrasound technology is so they can move away from batch processing. The use of ultrasound can reduce the processing time from one to 4 h needed in batch processing, to less than 60 min. Also, it reduces separation time from more than 10 h down to 1 h. However, these improvements are not always attained at different yields. The existing literature linked to the amount of auxiliary energy needed to match the suitable applications for different oils is an ongoing area of research. Mixing devices (including recirculation pumps and ultrasonic mixers) are needed in a reactor for the reaction to occur efficiently.
Ultrasonic mixing is regarded as a time-efficient and economical method for biodiesel production, and is capable of reducing the process time to a few hours; refer to Zore et al. (2021). Ultrasonic mixing of the reactants can be achieved by the application of sound waves at a frequency of 20 kHz-10 MHz; refer to Mason et al. (2015). This causes rapid small-scale movement of fluids due to the variation of sonic pressure resulting from the compression and rarefaction cycles, leading to localized cavitation. During this process of cavitation, the micro-bubbles raise the energy levels in the mixture and causes a rise in temperature. This energy added to the biodiesel process by the ultrasonic device maintains the operating temperature is important and should be quantified. Consequently, enhanced mixing has the effect of reducing the required reaction time. A benefit of this technology is that it is practical to utilize, and can be scaled up to higher production rates. It is imperative to identify the impacts of using different ultrasound schedules and power ratings (Khan et al., 2017). Itemized several conditional factors that affect the use of ultrasound such as the volume of the mixture, the temperature, the rating of ultrasound, and the duration of application. It has now become imperative to devise methods to process vegetable oils with different levels of FFA using improved methods such as ultrasound. Heating is a fundamental aspect of the biodiesel production process, and it can be accomplished in one or two steps, i.e., during the pretreatment and also during the process mixing of reactants. The requirements of the heating process depend in part on the FFA content of the oil as confirmed by Towerton (2007). The need to supply heat to drive the process inevitably adds to the required processing time and cost. In addition, the characteristics of the feedstock may require pretreatment procedures, which further results in lengthy periods of operation.
Research by Sáez-Bastante et al. (2014) raised concerns about the absence of information on ultrasound mixing, and how it affects production. Similarly (Fayyazi et al., 2015), showed optimized conditions of ultrasound on biodiesel production, but they did not provide details on the vegetable oil used. The difficulty in evaluating the amount of energy needed was noted by Sáez-Bastante et al. (2014). Production optimization was also researched by Fayyazi et al. (2015), but they provided no significant discussion of the added energy. Biodiesel production using eucalyptus oil was investigated in Khan et al. (2017). They showed that parameters such as ultrasonic frequency, ultrasonic power, molar ratio, and reaction temperature and time all affected the reaction efficiency for that particular process. Oil/fat type influences the progress of the reactions, hence there is a need to adjust production parameters. Other factors that were considered included the FFA content and moisture levels contain in the feedstock. What possess the risk to biodiesel success, is the proportion of these parameter, however there are some constituents (impurities) that cause the biodiesel production to be successful or result in failure. The use of ultrasonic energy permits the transesterification reaction between vegetable oil and alcohol to reach equilibrium in a relatively shorter reaction time, with a high yield of alkyl esters even at low temperatures; see (Stavarache et al., 2007; Hanh et al., 2009). Research work carried by Oliveira et al. (2018) investigated the energy balance associated with comparing the three methods of agitation: ultrasound, magnetic, and mechanical mixing. The utilization of ultrasound resulted in giving the best efficiencies with low energy costs (Thanh et al., 2010). Performed biodiesel production with the ultrasonic probe at low frequency (24 kHz; 200 W) (Naveena et al., 2015; Shinde and Kaliaguine, 2019). Claimed that most ultrasound frequencies selected for biodiesel production are 20, 40, 60, 80, and 100 kHz. Sonochemistry has been used for biodiesel production from different vegetable oils; see (Stavarache et al., 2005; Koc and McKenzie, 2010; Teixeira et al., 2014), who studied the effects of temperature and the impact of ultrasonic frequency and time on the separation of glycerin during transesterification of soybean oil. The shortest glycerin separation time of 7.9 min was recorded at a process temperature of 50°C and ultrasound time of 5 min when the ultrasound was operated at 90% of the allowable amplitude. Sonication at high amplitudes and longer durations was found to increase the reaction temperature, and enhancement of emulsification of the oil and potassium methoxide mixture. These procedures focused on achieving the best regime for efficient ultrasound application, but they were applicable only for a specific oil, and the results could not readily be extended to situations involving different vegetable oils having diverse compositions or FFA values.
Koc et al. (2011) discussed the uses of high-intensity ultrasound in processing soybeans for biodiesel production (Cravotto et al., 2008). Showed that the time required to achieve a 96% yield was reduced by several fold when ultrasonic treatment in a pulse mode was used. In continuous sonication mode, reaction yields began in 15 s and resulted in 87% biodiesel yield. Overall, the impact of ultrasound reduced process time from 2 h down to less than 60 min (Mahamuni and Adewuyi, 2009). Carried out optimization of the synthesis of biodiesel with soybean oil, and observed a 90% yield in less than 30 min using 0.5 wt% KOH, a methanol/oil molar ratio of 6:1, a frequency of 11 kHz, and a 139 W power input (Stavarache et al., 2005). Showed that sonication had a positive effect on transesterification process, both reducing the processing time and saving energy in biodiesel production (Santos et al., 2021). Described the positive effect of ultrasound on biodiesel yield enhancement, extraction, and the final product quantity (Gröschl, 1998). Reported on research related to ultrasonic separation of suspended particles and discussed some of the latest developments of separation devices based on piezoelectric resonators. The acoustic forces on particles suspended in a liquid and the acoustic forces on suspended spherical particles in liquids were reviewed. The work presented the physical fundamentals of ultrasonic separation technology for utilizing piezoelectric resonators, with special emphasis on resonator analysis and optimization. It was found that efficiency depends strongly on the frequency and the properties of the suspension. The ultrasonic-assisted optimization of biodiesel production from eucalyptus oil was researched by Khan et al. (2017). They showed the mathematical relationships between process parameters and desired response in terms of increased biodiesel yields. They used a pulse frequency of 29.6 kHz, ultrasonic power of 110.25 W, a molar ratio (methanol:oil) of 6.36:1, a reaction temperature of 34.31°C, and a reaction time of 7.4 min that produced a reaction yield of 95.7%. The methyl ester yield was also characterized by physicochemical properties that were found to be in good agreement with ASTM D 6751 and EN 14214 standards (Chen et al., 2014). Used ostrich eggs as CaO catalyst on palm oil with ultrasonic-assisted transesterification and using a molar ratio of 9:1. In their study, this produced a yield of 92.7%. However, they did not clearly state the amount of free fatty acid present in the oil (Oliveira et al., 2018). Reported extensively on the effects of ultrasonic mixing on a variety of oil stocks. They investigated the influence of ultrasonic frequency and power, the amount of catalyst, varying molar ratios, and reaction time of the different oils types were investigated. It was demonstrated that the volumetric yield with WVO was 89% when 9.2 g of KOH catalyst were employed in conjunction with 200 W of ultrasonic mixing at a frequency of 20 kHz. Under similar circumstances the biodiesel yield obtained from virgin canola oil was 87% when 4.63 g NaOH catalyst was used. However, they noted that an increase in ultrasonic power supported a notable increase in the yield of biodiesel. Generally, their research did not clearly identify the amount of oil, the FFA content of the oil, or the specific sonication schedule. This raises many questions regarding how the ultrasound frequency, amplitude, and whether such power setting impact the production process. In summary, the literature search indicated that most previous investigators did not clearly characterize the exact composition of vegetable oils used for biodiesel production (particularly regarding the FFA content), and likewise they did not unambiguously describe how the oil composition influenced the application of different technological means to enhance yield. The main contribution of this paper is to highlight the instances where utilization of ultrasonic mixing when using waste vegetable oils is beneficial. The present research clearly quantifies the amount of ultrasound used for various WVO values, and clarifies how its use impacts the yield.
3 Experimental apparatus and procedures
The experimental apparatus utilized in the present study is shown in Figure 1. The procedures utilized in this investigation were designed for optimal production (i.e., maximum yield) while attempting to maintain minimal cost of producing biodiesel from WVO. This is described in greater detail in Ityokumbul Igbax et al. (2022). In some instances, virgin canola oil was also utilized to produce biodiesel, thereby serving as a baseline case for comparison to WVO. The setup consisted of four tanks, i.e., a reaction tank, a methoxide (i.e., a mixture of NaOH and CH3OH) tank, and two separation tanks, all of which were connected with pipes and valves. An in-line temperature-controlled heater and an ultrasound mixing device were incorporated in the apparatus to reduce the operation time and control the quality of product. The production system was automated using code written in Python programming language to control the process. As a precaution to avoid contamination and infiltration, methanol was flushed throughout the system after each run to ensure that the channel was clean. The reactants were transferred to the tanks via pumps and valves, which were designed to open and close depending on the flow situation. The WVO was initially filtered to remove loose particles, and then heated to 55°C–65°C in a storage drum to facilitate subsequent pumping. The pumping process was regulated by means of a user interface Raspberry Pi 3 controller, which sent signals to the pumps and valves through a set of relays to transfer the fluids. Methanol, which had been pre-mixed in a prescribed ratio with sodium hydroxide (NaOH), was heated to 55°C to form a sodium methoxide solution. Both the methoxide and the WVO were mixed in the reaction tank and continuously circulated through an ultrasonic mixer and the in-line heater. This process was intended to mix the reactants thoroughly, so that the transesterification could be completed within the shortest time possible. The heater was adjusted to maintain a reaction temperature of approximately 55°C. Within 25 min of initiating the production process the mixture showed a deep color separation, which indicated the reaction/transformation was taking place. Recirculation of the reactants was maintained for a maximum of 70 min. The reacted mixture was then pumped to the separation tanks. Figure 2 illustrates a flowchart for the sequence of operations. For a given volume of oil (either virgin canola oil or WVO obtained from a cafeteria facility) used in a given test, approximately 1 L of methanol was utilized. This yielded prescribed methanol/oil volume and molar ratios for the test regimen. In every instance the reaction temperatures were carefully controlled. As demonstrated by Guerrero Fajardo et al. (2010); Li et al. (2023), this was done to enhance the reaction rates, and to ensure that significant methanol evaporation did not occur, due to the resulting safety concerns. Likewise, the test durations were limited, based on observations reported in Hasan et al. (2017); Degfie et al. (2019).
In this research NaOH (sodium hydroxide or basic lye) was used as a catalyst for the transesterification process required for biodiesel production. Prior to initiating the reaction, titration was performed to calculate the amount of free fatty acids present in an oil sample. This facilitated the determination of the optimum amount of catalyst to be employed; refer to Ityokumbul Igbax et al. (2022) which provides a thorough description of the experimental apparatus and procedures utilized in the present investigation. Waste vegetable oil feedstock was pumped from the oil storage drum to the reaction tank of the biodiesel apparatus using a DC oil pump operating at 12 V and 4,500 rpm. Under those conditions, the calibrated pump was capable of inducing a flow of 10.5 gpm of WVO. Likewise, the methoxide flow from the methoxide tank to the reaction tank was generated by means of a brushless 12 VDC pump that yielded a calibrated flow rate of 3 gpm. The known calibration for each pump permitted precise control of the mixing ratio of WVO and methoxide. For example, if a mixture ratio of 4:1 was desired, the reaction tank would receive 4 gallons of oil and 1 gallon of methoxide. In that case, the oil pump supplied 4 gallons of oil to the reaction tank in approximately 23 s. Subsequently, the methoxide pump was operated for 20 s to produce the required mixing ratio, as determined by the reaction predictions. The methoxide pump was brushless, and thus supplied the flow at a relatively slow speed to avoid any hazardous effects potentially caused by the corrosive and volatile nature of the fluid. When both liquids were in the reaction chamber, the in-line thermostatically controlled heater temperature was set to maintain the desired temperature over the range of 50°C–70°C; this aspect of the apparatus was required to overcome any heat loss to the environment through the shell of the reaction tank and plumbing. The circulation process which carried the mixed oil and methoxide through the apparatus was executed using a Singflow FL-40 ProPump diaphragm pump operating at 4.5 gpm and 40 psi. The ultrasonic mixing device had a maximum power of 500 W, which was varied in duration, as well as by the chosen amplitude percentage (adjustable from 20% to 100%) as displayed on a potentiometer. The circulation process was the most critical stage of operation since certain parameters such as temperature, the intensity of mixing, and the sonochemistry condition was varied to seek an optimum set of conditions to maximize production. The circulation process through the heater and ultrasonic mixer was continued for periods ranging from 30 to 90 min. During this process, there was constant agitation imparted to the fluid by virtue of the gross fluid motion induced by the pump, small-scale motion generated using ultrasound, and the impact of heat which gave rise to the collision of molecules and the induced stresses involving all the components of the reaction. These activities served to help mix the immiscible reactant liquids, thus increasing the area of contact on a microscopic basis, thereby enhancing the reaction rate.
In the present investigation mechanical mixing was achieved by combined ultrasound and agitation induced by pump impellers, which in turn influenced the reaction rate. As the fluid was being pumped through the reaction apparatus, mechanical action and increased temperature enabled/facilitated the biodiesel reaction. Ultrasonic mixers have power ratings and frequencies of operations that significantly contributes to the speed/rate of reaction. This affects both the cohesive force and the molecular mass in a way to improve production yields and reduce the required time. Ultrasound is known for producing cavitation which occurs due to the formation and subsequent collapse of microbubbles that are generated by virtue of the local pressure falling below the vapor pressure. The act of using ultrasound and mechanical mixing creates some emulsion, due to the fine dispersion of minute droplets of one liquid in another in which it is not soluble or miscible; refer to Cucheval and Chow (2008). An emulsion is a mixture of two or more liquids that are normally immiscible owing to liquid-liquid phase separation. Emulsification can be caused by biodiesel that has not been fully reacted. This is results in monoglycerides and diglycerides being present in the fuel, due to incomplete reaction. In fact, mono and diglycerides tend to be the major culprits that form/constitute an emulsifier because of their nature toward dissolution. Therefore, in the present investigation the need for enhanced mixing and the use of the correct amount of catalyst was deemed to be imperative when high yields and optimum processing time were to be achieved. Other methods including mechanical action by stirring, circulation, and ultrasonic mixing have likewise been proven to enhance the biodiesel production process; refer to (Ho et al., 2016; Sivaramakrishnan and Incharoensakdi, 2018b; Malani et al., 2019). Both the addition of catalyst and ultrasound energy to the mixture should be quantified based on the calculated parameters, or else the solution becomes emulsified, forms soap, and presents difficulty in separation.
In general, the choice of incorporating ultrasonic mixing in biodiesel production must consider such factors as the capacity of the device, the nature of the fluid, the frequency and amplitude of the operation, and the overall power rating. Ultrasonic mixers are rated based on their input power and frequency, which can range from 200 W to 1500 W and 20 kHz–100 kHz, respectively. Previous research has suggested that the lower the frequency the greater the tendency to cause emulsification. Therefore to account for some of these challenges posed by forming sludges of the viscous mixtures, different sonotrodes may utilize a unique frontal area tailored to suit specific operations. The resulting operation time of a sonotrode is determined by the mechanical amplitude (50%–100%), and the chemical and physical properties (e.g., pressure and temperature) of the liquid to be sonicated. The ultrasound device used for this study was a Hielscher BS4d40 sonotrode coupled with a B4-1.8 booster. The booster had a frontal area of 12.5 cm2. With that configuration, at full-scale the sonotrode produced sound waves at a frequency of 20 kHz with an amplitude of 31 µm. The ultrasonic mixer was capable of imparting energy to the reactants with an intensity of 40 W/cm2, i.e., it had a full-scale power rating of 500 W. To control the input power a potentiometer allowed for adjustment of the amplitude. Where sonication was employed the amplitude was adjusted to 75% of its peak value. Typically, this investigation employed 20 min of ultrasonic mixing, where sonication was applied with either pulse-modulation or continuous operation. For pulse sonication, the ultrasonic mixer was operated at 75% of full power for the first 10 min of the production run. This was followed by a 10-min period where no sonication was utilized. Thereafter the ultrasonic mixer was again run at 75% of full power for 10 additional minutes, such that a total of 450 kJ of energy were imparted to the reactants over the entire course of testing. For continuous sonication, the ultrasonic mixer was operated at 75% of full power for varying time periods, without any intervening idle period. In certain instances, no sonication was employed, so as to provide a baseline for comparison. Figure 3 shows the outcome of applying excessive ultrasound to biodiesel processing.
A simplified procedure termed the Warnquist 27/3 test was adopted in the present research to ascertain whether the biodiesel passed the quality test; refer to John et al. (2017). The 27/3 test was performed by pouring 27 mL of methanol and 3 mL of the produced biodiesel maintained at 24°C into a test tube. The mixture was then vigorously shaken for approximately 1 min. After allowing the products to settle by gravity for 15 min, the quality was determined by visual inspection of the mixed solution. If the solution had colloidal solids or particulates floating inside (refer to Figure 4), the biodiesel was deemed to have low quality, and thus did not pass the test. This meant the reactants had not fully reacted, and that some of the available triglycerides still needed to be further reacted with methanol. If the solution was transparent and had no appearance of colloidal solids floating in it, then the biodiesel quality was regarded as being satisfactory. All samples were checked by this method to establish the efficacy of the production procedures. The 27/3 test identifies traces of triglycerides in the finished biodiesel. The practicality of the 27/3 test deals with the ability to dissolve biodiesel in methanol, with a clear solution indicating that the sample is acceptable. Its use helps small-scale and remote producers to determine the success of every batch of biodiesel produced.
Biodiesel separation from its by-product glycerin can be achieved via different methods. Gravitational and electrostatic separation were utilized in the present research program. The ratio/fraction of the separated fluid (i.e., the “pure” “biodiesel”) was compared to the total volume and multiplied by 100 to give the yield percentage of the product on a volume basis per the equation below:
4 Experimental results
Previously (Ityokumbul Igbax et al., 2022) investigated the use of virgin canola oil and waste vegetable oil to produce biodiesel resulting from base-catalyzed transesterification processes. The goal of the study was to explore the improvement of biodiesel production to achieve high yields. For a given volume of oil (either virgin canola oil or WVO obtained from a cafeteria facility), approximately 1 L of methanol was utilized. This yielded prescribed methanol/oil volume and molar ratios for the test regimen. In every instance the reaction temperatures were carefully controlled. As demonstrated by Guerrero Fajardo et al. (2010); Verduzco (2013), this was done to enhance the reaction rates, and to ensure that significant methanol evaporation did not occur, due to the resulting safety concerns. Likewise, the test durations were limited, based on observations reported in (Hasan et al., 2017; Degfie et al., 2019). From that test program it was not clear how the sonication schedule influenced biodiesel yield. For example, the virgin canola oil tests were performed using a combination of no sonication, continuous sonication for either five or 10 min, or pulse sonication for 20 min (at 75% full power). In contrast the WVO tests reported in (Ityokumbul Igbax et al., 2022) were all conducted using 20 min of pulse sonication at 75% full power. Likewise, it was not fully elucidated how the sonication intensity/energy added over the entire production run influenced biodiesel yield. Regardless of the sonication schedule, virgin canola oil tests and WVO tests were all conducted using sonication at 75% full power. To partly address those concerns, the matrix of test conditions in Table 1 through IV were performed in this investigation. All tests utilized an oil to methanol volume ratio of 6:1. To establish whether the energy that must be added to the transesterification process by sonication scales with the reactant volume, when the volume of reactants was doubled the sonication duration was likewise doubled for select cases. Titrations were performed to determine the FFA percentage and the optimal amount of catalyst to be used. Biodiesel viscosity was measured at the reaction temperature using a temperature-controlled water bath. In every instance the separation of biodiesel and glycerin was performed using gravimetric settling, and the required time to achieve the final yield was recorded refer to: (Ityokumbul Igbax et al., 2022). Any production runs that failed to pass the 27/3 test were clearly noted. This aspect of the investigation was intended to ascertain the effectiveness of the application of ultrasound under different application intensities and durations, to establish the benefits of ultrasound with virgin/waste vegetable oils during the processing of biodiesel.
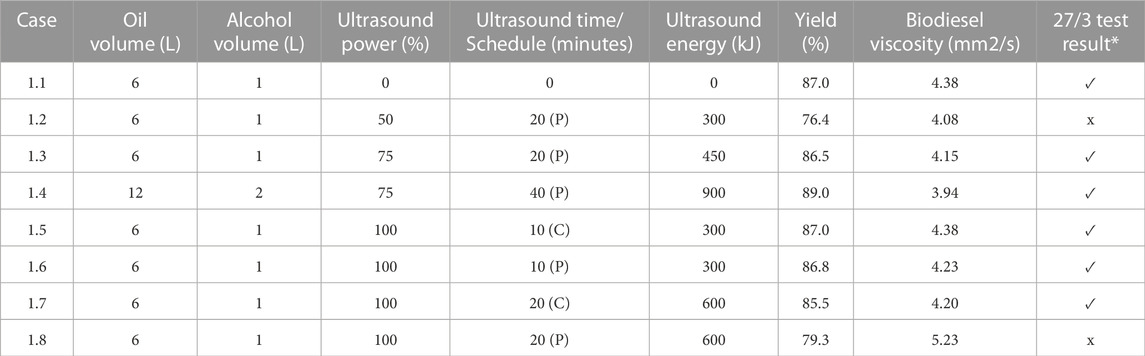
TABLE 1. Influence of Sonication Schedule on Virgin Canola Oil - FFA = 4.25%. The symbol ✓denotes that the sample passed the 27/3 test; the symbol x indicates that sample failed the 27/3 test. P denotes Pulse and C denotes Continuous.
In Table 1 through 4, test data for four different vegetable oils samples were considered. They were denoted as follows: (i) virgin canola oil, (ii) canola oil mix, (iii) WVO, and (iv) WVO1. The samples designated as “WVO1” were obtained from a batch of waste vegetable oil that had been stored in an open drum for over 1 year, whereas the samples designated as “WVO” were obtained from a cafeteria facility just prior to testing. The “canola oil mix” samples were created by mixing virgin canola oil with a prescribed portion of the WVO samples to obtain the desired FFA content. These four different oils had FFA percentages of 4.25, 5.20, 5.83, and 7.61%, respectively. The amount of catalyst used for these cases corresponded to 6.5, 7.5, 8.0, and 9.0 g of sodium hydroxide, respectively. Figure 5 provides a photograph of the respective oils. In every instance the test procedures to produce biodiesel from each sample conformed to those described previously. The sonication schedule and energy added by sonication were recorded in each instance. The data from the production runs in Table 1 through 4 were presented for each oil sample in terms of yield, biodiesel viscosity, and passage/failure of the 27/3 test for complete reaction/quality. The tests were intended to establish if ultrasound is beneficial or detrimental to the production of biodiesel from a vegetable oils exhibiting a range of FFA percentages.
A graphical summary of the test results reported Table 1 for virgin canola oil is depicted in Figure 6. The label “C” implies continuous sonication, whereas the designation “P” denotes pulse sonication. The tests conducted using 6 L of oil with 1 L of methanol implied that the use of ultrasound on virgin canola oil was not necessarily beneficial, since it did not improve the result. For those cases, increasing the energy added by sonication to the reactant mixture tended to reduce the yield slightly. For example, case 1.1 employing no ultrasound resulted in a yield of 87.0%. This yield was the highest yield for the smallest reactant volumes. In contrast case 1.4, where 12 L of oil were reacted with 2 L of methanol, exhibited the greatest yield of 89.0% for production runs that utilized virgin canola oil. In that case 40 min of pulse sonication was employed at 75% power. It is noted that the yield measurement accuracy was limited by the scale readability of the graduated cylinder, and a 2% difference in yield measurements was likely within the margin of error for such measurements. Hence it was inconclusive as to whether applying sonication energy on virgin vegetable oil to enhance mixing with methanol was beneficial in terms of increased yield.
Figure 7 summarizes results as reported in Table 2, where the experiments were conducted on virgin canola oil mixed with less degraded waste vegetable oil. The FFA percentage of canola oil was intentionally higher than that for virgin canola oil. This indicated that the mixed oil had some impurities derived from the waste vegetable oil, which had been used to fry food in a cafeteria facility. These changes impacted the chemical structure of the oil, which presumably affected biodiesel production. The cases that passed the 27/3 tests utilized 6 L of oil and 1 L of methanol. In these instances, the highest yield of 83.7% was again obtained when no sonication was employed; refer to case 2.1. However, for progressively higher sonication energy a distinct pattern was observed, where the maximum yield was obtained when 20 min of pulse sonication was employed at 75% power, such that 450 kJ of sonication energy was added to the reactants. These results suggest that an optimum amount of sonication energy may be discerned as a function of increased FFA percentage. By comparison to the results obtained for virgin canola oil, case 2.2 considered the case where 12 L of oil reacted with 2 L of methanol using 40 min of pulse sonication at 75% power. However, that test condition did not pass the 27/3 test. For the data presented in Table 2, no clear pattern was evident in the data regarding whether pulse or continuous sonication at the same total energy level was most beneficial in terms of final yield.
Figure 8 recapitulates the data reported in Table 3 for those cases that passed the 27/3 test. In those instances, the experiments were performed using relatively fresh (i.e., less degraded) waste vegetable oil. Case 3.3 used 20 min of pulse sonication at 75% full power, resulting in a total energy input of 450 kJ, and had the highest yield of 81.8%. In that instance 6 L of oil and 1 L of methanol were employed. By contrast, case 3.4 considered 12 L of oil and 2 L of methanol to retain the same 6:1 volume ratio. In that occasion 900 kJ of sonication energy derived from 40 min of pulse sonication at 75% power were utilized to achieve a yield of 79.0%. The lowest overall yield of 76.1% was associated with case 3.2, where 300 kJ of sonication energy was added throughout the production process. Case 3.1 did not utilize sonication, and failed the 27/3 test. This suggests that for higher FFA content, sonication enhanced biodiesel yield. In general, the yields obtained using WVO were lower when compared to the results attained from virgin canola oil, indicating that the greater the FFA content the lower the yield, if all other experimental parameters remained the same.
Figure 9 portrays biodiesel yield data for experiments obtained from testing performed on waste vegetable oil that had been degraded, as presented in Table 4. Only trials that passed the 27/3 tests are depicted. Cases that utilized 6 L of oil and 1 L of methanol are shown. The maximum yield of 83.6% was achieved for case 4.3, where 20 min of pulse sonication at 75% full power was employed for 20 min for a total sonication energy input of 450 kJ. Case 4.1 did not utilize sonication and failed the 27/3 test, once again signifying that for elevated WVO FFA percentages the use of sonication to enhance mixing is beneficial in promoting the successful production of biodiesel. It was noted that case 4.3, where the process employed 12 L of oil and 2 L of methanol to attain a 6:1 volume ratio, did not pass the 27/3 test, despite utilizing 900 kJ of energy derived from pulse sonication at 75% of full power for 40 min.
Collectively the principal outcomes from the data presented in Table 1 through IV are illustrated in Figure 110. For each oil sample considered in the present investigation (as indicated by the FFA%), the total sonication energy that resulted in the maximum biodiesel yield for each experiment while simultaneously passing the 27/3 test are shown. In every instance these results pertain to the cases where 6 L of oil were reacted with 1 L of methanol. Although not shown in Figure 10, it was observed from this test program that the maximum yield for virgin canola oil or mixed canola oil was obtained for no sonication, indicating that the use of sonication to enhance mixing for those oils was not warranted. Where sonication was employed, generally the maximum yield for the four oil samples was achieved using 450 kJ of pulsed sonication energy being applied for 20 min. For the lower FFA percentage samples (i.e., for virgin canola oil or mixed canola oil), the data implied that the application of sonication energy in a pulsed mode resulted in higher yields than those obtained by continuous sonication for the same overall energy input. However, the matrix of test cases presented in I through IV was insufficient to clearly establish whether application of sonication in a pulsed mode was superior to the results obtained by means of continuous sonication under those circumstances. Likewise, at the higher FFA percentages associated with WVO, the data suggested that there was relatively little difference in measured yield when applying 600 kJ of sonication energy either in a pulsed or continuous mode throughout the production run.
5 Summary and conclusion
This work provided a demonstration of improved small-scale biodiesel production techniques. The present study evaluated the application of ultrasonic mixing (sonication) and heating on four different vegetable oil samples having different FFA values and presented the resulting yields as a function of the energy applied. The study was focused on reducing the processing time and increasing the production rate of biodiesel to achieve high yields. Different waste oil streams were used as the raw materials. These oils had different fatty acid contents resulting from previous environmental or processing conditions. This research utilized a transesterification process for the mixture of vegetable oil and alcohol in the molar ratio of 6:1 at an average temperature of 55°C over a period of 60 min. An original contribution of this investigation is that it provided extensive details regarding the magnitude of the sonication energy added to the reactant mixture during the biodiesel production process to enhance mixing of the immiscible oils and methanol. The resulting biodiesel yield is thought to constitute a significant indicator of the profitability of the production.
The optimum amount of ultrasound energy was 450 kJ for the particular sets of test conditions that were considered. An original contribution of this investigation was that it provided extensive details regarding the magnitude of the sonication energy added to the reactant mixture during the biodiesel production process. A complete description of the sonication mixing schedules and the oil-to-alcohol volume ratios that were employed was presented. Varying amounts of sonication energy were employed in the biodiesel production runs performed in this investigation. This was implemented to enhance the mixing of the oil samples with the methanol. This was deemed to be necessary to ensure that the resulting biodiesel passed the 27/3 quality check and was within acceptable limits of viscosity; refer to Ityokumbul Igbax et al. (2022). The free fatty acid content had a profound impact on the yield. It was observed that when the ultrasonic energy supplied to the solution was increased for mixtures with high FFA, there was an increased tendency for emulsification to occur which decreased the yield. The amount of energy added to reactants by sonication was limited in the present investigation. Presumably, for larger batch volumes of methanol/oil, more sonication would be beneficial to overcome the resistance to mixing of the oil and methanol associated with their viscosity, inherent immiscibility, FFA%, and the presence of contaminants. The variable sonication periods employed with biodiesel production from pure canola oil led to difficulty in directly comparing the measured yields to those resulting obtained from WVO, where a consistent sonication schedule was employed. It is recommended that any future testing utilizing pure canola oil should use the same sonication procedures used for the WVO tests to facilitate comparable yield assessments. The energy added by sonication to the reactants throughout the transesterification process for all tests was restricted, due to the observation that excessive sonication yielded soap formation, such that the biodiesel produced failed to pass the 27/3 test. The influence of sonication frequency was not considered in the present research, and this warrants further investigation. Although (Manickam et al., 2014; Oliveira et al., 2018), presented that higher frequency such as 50 kHz provided higher biodiesel yield when compared to 20 kHz. Further investigation is therefore suggested. This research did not directly measure the energy needed to operate the pumps and in-line heater. Similarly, a bomb calorimeter to measure the energy content of the biodiesel that was produced was unavailable.
The experimental results reported in the present study were largely based on qualitative observations of the nature of the product. Regarding an assessment of the overall accuracy associated with the yield, it was estimated that such measurements achieved an accuracy of ±3%, based simply on the readability of the scale mounted to the separation tank; refer to Ityokumbul Igbax et al. (2022). This contention was bolstered by noting that the final yield values obtained either by gravitation settling or electrostatic coagulation resided within ±3% of each other when the experiments were performed under identical circumstances. It was deemed likely that measurements of the frequency of sonication and the ultrasonic energy imparted to the reacting mixture was accomplished with an uncertainty exceeding ±1%. This was based on prior calibration information provided by the sonotrode manufacturer, as well as the associated scale readability of the meters used in the measurements. Every effort was made to eliminate bias (systematic) errors in the measurements by performing careful calibrations of the instrumentation prior to conducting the measurements. An insufficient number of tests were performed to unambiguously assess a confidence level associated with precision (random) errors, thus precluding their quantification based on a statistical analysis.
In general, it was demonstrated that to achieve improved yields, the presence of greater FFA content required more added ultrasound energy to enhance mixing, up to a certain maximum amount. The optimum ultrasound energy depended on the WVO composition, as influenced by the FFA content. The use of ultrasound on biodiesel produced from virgin canola oil was deemed to be unnecessary, since its use did not necessarily improve quality or provide any significant yield increase. As shown in Table 1 and Figure 6, modest yield decreases were observed in most instances where sonication was employed with virgin canola oil. Likewise, there were two occasions (e.g., cases 1.2 and 1.8) where the utilization of sonication with virgin canola oil resulted in biodiesel samples that failed to pass the 27/3 tests. However, in many instances, it was noted that the application of ultrasound in conjunction with WVO improved the mixture reaction and increased the yield, although as noted the use of too much sonication was detrimental. It was found that there was a favorable impact on the yield of biodiesel when ultrasound was used with WVO of different FFA values. The present investigation demonstrated that adding too much ultrasonic energy reduced the biodiesel yield obtained from canola oil. For example, excessive sonication was observed to cause difficulty in achieving biodiesel/glycerin separation when the product formed emulsified, colloidal solutions. This also led to the formation of semi-solid glycerin product which had the potential to block the pipes in the reactor, thereby incurring additional maintenance requirements and additional production cost. Presumably, for larger batch volumes of methanol/oil, more sonication would be beneficial to overcome the resistance to mixing of the oil and methanol associated with their viscosity, inherent immiscibility, FFA%, and the presence of contaminants. The variable sonication periods employed with biodiesel production from pure canola oil led to difficulty in directly comparing the measured yields to those resulting obtained from WVO, where a consistent sonication schedule was employed. However, it was implied that the use of ultrasound on virgin canola oil was not necessarily beneficial, since it did not improve the resulting yield. The results suggest that an optimum amount of sonication energy may be discerned as a function of increased FFA percentage. For higher FFA content, sonication generally enhanced biodiesel yield, up to a certain point. Exceeding that value of added sonication energy often led to soap formation and emulsification, resulting in biodiesel that did not pass the 27/3 test. If such instrumentation is available, Igbax et al. (2022) recommended the use of the following equipment/methods to determine the exact composition of both virgin and waste vegetable oil: (i) mass spectrometer, (ii) gas chromatography, (iii) electron microscopy, (iv) thermal oxidation testing, (v) Fourier transform infrared spectrometry, and (vi) liquid processor/simulators. This paper focused on the impact of FFA values associated with virgin canola oil, or canola oil mixed with various amounts of WVO obtained from a cafeteria facility, and likewise considered how the application of ultrasound influenced the yield. It is recommended that additional studies be performed on other vegetable oil samples; these may potentially include soya, neem, coconut, corn, and groundnut oils. A comprehensive energy balance could also be considered.
Data availability statement
The original contributions presented in the study are included in the article/Supplementary Material, further inquiries can be directed to the corresponding author.
Author contributions
SIg: Conceptualization, Data curation, Formal Analysis, Investigation, Methodology, Project administration, Resources, Software, Supervision, Validation, Writing–original draft, Writing–review and editing. DS: Supervision, Writing–review and editing. AE: Supervision, Writing–review and editing. SId: Supervision, Writing–review and editing.
Funding
The author(s) declare that no financial support was received for the research, authorship, and/or publication of this article.
Conflict of interest
The authors declare that the research was conducted in the absence of any commercial or financial relationships that could be construed as a potential conflict of interest.
Publisher’s note
All claims expressed in this article are solely those of the authors and do not necessarily represent those of their affiliated organizations, or those of the publisher, the editors and the reviewers. Any product that may be evaluated in this article, or claim that may be made by its manufacturer, is not guaranteed or endorsed by the publisher.
References
Agee, B. M., Mullins, G., and Swartling, D. J. (2014). Use of solar energy for biodiesel production and use of biodiesel waste as a green reaction solvent. Sustain. Chem. Process. 2 (1), 21–10. doi:10.1186/s40508-014-0021-2
Almasi, S., Ghobadian, B., Najafi, G., and Soufi, M. D. (2021). A novel approach for bio-lubricant production from rapeseed oil-based biodiesel using ultrasound irradiation: multi-objective optimization. Sustain. Energy Technol. Assessments 43, 100960. doi:10.1016/j.seta.2020.100960
Anastopoulos, G., Zannikou, Y., Stournas, S., and Kalligeros, S. (2015). Transesterification of vegetable oils with ethanol and characterization of the key fuel properties of ethyl esters. Energies 2 (2), 362–376. doi:10.3390/en20200362
Bucham, J. O., Igbax, S. I., and Aliyu, A. B. (2022). Hybrid aluminium alloy (aa6061) composite mechanical properties investigation. United Int. J. Res. Technol. 3, 44–48.
Chen, G., Shan, R., Shi, J., and Yan, B. (2014). Ultrasonic-assisted production of biodiesel from transesterification of palm oil over ostrich eggshell-derived cao catalysts. Bioresour. Technol. 171, 428–432. doi:10.1016/j.biortech.2014.08.102
Chen, L., He, L., Zheng, B., Wei, G., Li, H., Zhang, H., et al. (2023). Bifunctional acid-activated montmorillonite catalyzed biodiesel production from non-food oil: characterization, optimization, kinetic and thermodynamic studies. Fuel Process. Technol. 250, 107903. doi:10.1016/j.fuproc.2023.107903
Cravotto, G., Boffa, L., Mantegna, S., Perego, P., Avogadro, M., and Cintas, P. (2008). Improved extraction of vegetable oils under high-intensity ultrasound and/or microwaves. Ultrason. sonochemistry 15 (5), 898–902. doi:10.1016/j.ultsonch.2007.10.009
Cucheval, A., and Chow, R. (2008). A study on the emulsification of oil by power ultrasound. Ultrason. sonochemistry 15 (5), 916–920. doi:10.1016/j.ultsonch.2008.02.004
Degfie, T. A., Mamo, T. T., and Mekonnen, Y. S. (2019). Optimized biodiesel production from waste cooking oil (wco) using calcium oxide (cao) nano-catalyst. Sci. Rep. 9 (1), 18982. doi:10.1038/s41598-019-55403-4
Fadhil, A. B., Dheyab, M. M., Ahmed, K. M., and Yahya, M. H. (2012). Biodiesel production from spent fish frying oil through acidbase catalyzed transesterification. Pak. J. Anal. Environ. Chem. 13 (1), 7.
Fayyazi, E., Ghobadian, B., Najafi, G., Hosseinzadeh, B., Mamat, R., and Hosseinzadeh, J. (2015). An ultrasound-assisted system for the optimization of biodiesel production from chicken fat oil using a genetic algorithm and response surface methodology. Ultrason. sonochemistry 26, 312–320. doi:10.1016/j.ultsonch.2015.03.007
Freedman, B., Pryde, E., and Mounts, T. (1984). Variables affecting the yields of fatty esters from transesterified vegetable oils. J. Am. Oil Chem. Soc. 61, 1638–1643. doi:10.1007/bf02541649
Gao, Z., Zhou, Z., Wang, M., Shang, N., Gao, W., Cheng, X., et al. (2023). Highly dispersed pd anchored on heteropolyacid modified zro2 for high efficient hydrodeoxygenation of lignin-derivatives. Fuel 334, 126768. doi:10.1016/j.fuel.2022.126768
Gashaw, A., and Teshita, A. (2014). Production of biodiesel from waste cooking oil and factors affecting its formation: a review. Int. J. Renew. Sustain. energy 3 (5), 92–98.
Gebremariam, S., and Marchetti, J. (2017). Biodiesel production technologies: review. aims energy 5 (3), 425–457. doi:10.3934/energy.2017.3.425
Gröschl, M. (1998). Ultrasonic separation of suspended particles-part ii: design and operation of separation devices. Acta Acustica united Acustica 84 (4), 632–642.
Guerrero Fajardo, C. A., Osorio León, I. D., and Sierra Vargas, F. E. (2010). Evaluating the effect of temperature on biodiesel production from castor oil. Ing. Investig. 30 (2), 52–61. doi:10.15446/ing.investig.v30n2.15733
Hanh, H. D., Dong, N. T., Okitsu, K., Nishimura, R., and Maeda, Y. (2009). Biodiesel production through transesterification of triolein with various alcohols in an ultrasonic field. Renew. Energy 34 (3), 766–768. doi:10.1016/j.renene.2008.04.007
Hasan, a. A.-K. M., Mashkour, M. A., and Mohammed, A. A. (2017). Impact of mixing speed & reaction time on the biodiesel production from sunflower oil. Assoc. Arab Univ. J. Eng. Sci. 24 (3), 101–134.
Ho, W. W. S., Ng, H. K., and Gan, S. (2016). Advances in ultrasound-assisted transesterification for biodiesel production. Appl. Therm. Eng. 100, 553–563. doi:10.1016/j.applthermaleng.2016.02.058
Huang, J., Wang, J., Huang, Z., Liu, T., and Li, H. (2023). Photothermal technique-enabled ambient production of microalgae biodiesel: mechanism and life cycle assessment. Bioresour. Technol. 369, 128390. doi:10.1016/j.biortech.2022.128390
Ityokumbul Igbax, S., Swartling, D., ElSawy, A., and Idem, S. (2022). “Improving the yield of biodiesel production using waste vegetable oil considering the free fatty acid content,” in ASME international mechanical engineering congress and exposition (American Society of Mechanical Engineers), 86687, V006T08A028.
Jagadale, S., Jugulkar, L., and Intensity, M. (2012). Review of various reaction parameters and other factors affecting on production of chicken fat based biodiesel. Int. J. Mod. Eng. Res. 2 (2), 407–411.
Jambrak, A. R., Mason, T. J., Lelas, V., Herceg, Z., and Herceg, I. L. (2008). Effect of ultrasound treatment on solubility and foaming properties of whey protein suspensions. J. food Eng. 86 (2), 281–287. doi:10.1016/j.jfoodeng.2007.10.004
John, J. J., Kuhn, S., Braeken, L., and Van Gerven, T. (2017). Ultrasound assisted liquid–liquid extraction with a novel interval-contact reactor. Chem. Eng. Process. Process Intensif. 113, 35–41. doi:10.1016/j.cep.2016.09.008
Khan, O., Khan, M. E., Yadav, A. K., and Sharma, D. (2017). The ultrasonic-assisted optimization of biodiesel production from eucalyptus oil. Energy Sources, Part A Recovery, Util. Environ. Eff. 39 (13), 1323–1331. doi:10.1080/15567036.2017.1328001
Koc, A. B., Abdullah, M., and Fereidouni, M. (2011). Soybeans processing for biodiesel production. Soybean-application Technol. 19, 32.
Koc, A. B., and McKenzie, E. H. (2010). Effects of ultrasonication on glycerin separation during transesterification of soybean oil. Fuel Process. Technol. 91 (7), 743–748. doi:10.1016/j.fuproc.2010.01.020
Lam, M. K., Lee, K. T., and Mohamed, A. R. (2010). Homogeneous, heterogeneous and enzymatic catalysis for transesterification of high free fatty acid oil (waste cooking oil) to biodiesel: a review. Biotechnol. Adv. 28 (4), 500–518. doi:10.1016/j.biotechadv.2010.03.002
Li, Y., Zhu, K., Jiang, Y., Chen, L., Zhang, H., Li, H., et al. (2023). Biomass-derived hydrophobic metal-organic frameworks solid acid for green efficient catalytic esterification of oleic acid at low temperatures. Fuel Process. Technol. 239, 107558. doi:10.1016/j.fuproc.2022.107558
Mahamuni, N. N., and Adewuyi, Y. G. (2009). Optimization of the synthesis of biodiesel via ultrasound-enhanced base-catalyzed transesterification of soybean oil using a multifrequency ultrasonic reactor. Energy & fuels 23 (5), 2757–2766. doi:10.1021/ef900047j
Mahmoodi, N. M., Taghizadeh, A., Taghizadeh, M., and Baglou, M. A. S. (2019). Surface modified montmorillonite with cationic surfactants: preparation, characterization, and dye adsorption from aqueous solution. J. Environ. Chem. Eng. 7 (4), 103243. doi:10.1016/j.jece.2019.103243
Malani, R. S., Shinde, V., Ayachit, S., Goyal, A., and Moholkar, V. S. (2019). Ultrasound–assisted biodiesel production using heterogeneous base catalyst and mixed non–edible oils. Ultrason. sonochemistry 52, 232–243. doi:10.1016/j.ultsonch.2018.11.021
Manickam, S., Arigela, V. N. D., and Gogate, P. R. (2014). Intensification of synthesis of biodiesel from palm oil using multiple frequency ultrasonic flow cell. Fuel Process. Technol. 128, 388–393. doi:10.1016/j.fuproc.2014.08.002
Mason, T. J., Chemat, F., and Ashokkumar, M. (2015). “Power ultrasonics for food processing,” in Power ultrasonics (Elsevier), 815–843.
Mittelbach, M., and Remschmidt, C. (2004). Biodiesel: the comprehensive handbook. Martin Mittelbach.
Mousavi, S. R., Asghari, M., and Mahmoodi, N. M. (2020). Chitosan-wrapped multiwalled carbon nanotube as filler within peba thin film nanocomposite (tfn) membrane to improve dye removal. Carbohydr. Polym. 237, 116128. doi:10.1016/j.carbpol.2020.116128
Naveena, B., Armshaw, P., and Tony Pembroke, J. (2015). Ultrasonic intensification as a tool for enhanced microbial biofuel yields. Biotechnol. Biofuels 8 (1), 140. doi:10.1186/s13068-015-0321-0
Oliveira, P. A., Baesso, R. M., Moraes, G. C., Alvarenga, A. V., and Costa-Félix, R. P. B. (2018). “Ultrasound methods for biodiesel production and analysis,” in Biofuels-State of development. Editor K. Biernat (Intechopen), 121–148.
Sáez-Bastante, J., Pinzi, S., Arzamendi, G., De Castro, M. L., Priego-Capote, F., and Dorado, M. (2014). Influence of vegetable oil fatty acid composition on ultrasound-assisted synthesis of biodiesel. Fuel 125, 183–191. doi:10.1016/j.fuel.2014.02.015
Sanli, H., and Canakci, M. (2008). Effects of different alcohol and catalyst usage on biodiesel production from different vegetable oils. Energy & Fuels 22 (4), 2713–2719. doi:10.1021/ef700720w
Santos, N. D. S. A., Roso, V. R., Malaquias, A. C. T., and Baeta, J. G. C. (2021). Internal combustion engines and biofuels: examining why this robust combination should not be ignored for future sustainable transportation. Renew. Sustain. Energy Rev. 148, 111292. doi:10.1016/j.rser.2021.111292
Shinde, K., and Kaliaguine, S. (2019). A comparative study of ultrasound biodiesel production using different homogeneous catalysts. ChemEngineering 3 (1), 18. doi:10.3390/chemengineering3010018
Sivaramakrishnan, R., and Incharoensakdi, A. (2018a). Microalgae as feedstock for biodiesel production under ultrasound treatment–a review. Bioresour. Technol. 250, 877–887. doi:10.1016/j.biortech.2017.11.095
Sivaramakrishnan, R., and Incharoensakdi, A. (2018b). Utilization of microalgae feedstock for concomitant production of bioethanol and biodiesel. Fuel 217, 458–466. doi:10.1016/j.fuel.2017.12.119
Stavarache, C., Vinatoru, M., Maeda, Y., and Bandow, H. (2007). Ultrasonically driven continuous process for vegetable oil transesterification. Ultrason. sonochemistry 14 (4), 413–417. doi:10.1016/j.ultsonch.2006.09.014
Stavarache, C., Vinatoru, M., Nishimura, R., and Maeda, Y. (2005). Fatty acids methyl esters from vegetable oil by means of ultrasonic energy. Ultrason. sonochemistry 12 (5), 367–372. doi:10.1016/j.ultsonch.2004.04.001
Suslick, K. S., Didenko, Y., Fang, M. M., Hyeon, T., Kolbeck, K. J., McNamara, W. B., et al. (1999). Acoustic cavitation and its chemical consequences. Philosophical Trans. R. Soc. Lond. Ser. A Math. Phys. Eng. Sci. 357 (1751), 335–353. doi:10.1098/rsta.1999.0330
Teixeira, C. B., Junior, J. V. M., and Macedo, G. A. (2014). Biocatalysis combined with physical technologies for development of a green biodiesel process. Renew. Sustain. Energy Rev. 33, 333–343. doi:10.1016/j.rser.2014.01.072
Thanh, L. T., Okitsu, K., Sadanaga, Y., Takenaka, N., Maeda, Y., and Bandow, H. (2010). Ultrasound-assisted production of biodiesel fuel from vegetable oils in a small scale circulation process. Bioresour. Technol. 101 (2), 639–645. doi:10.1016/j.biortech.2009.08.050
Thirumarimurugan, M., Sivakumar, V., Xavier, A. M., Prabhakaran, D., and Kannadasan, T. (2012). Preparation of biodiesel from sunflower oil by transesterification. Int. J. Biosci. Biochem. Bioinforma. 2 (6), 441–444. doi:10.7763/ijbbb.2012.v2.151
Towerton, G. (2007). “The use of ultrasonic reactors in a small scale continuous biodiesel process,” in Proceedings of the international congress on acoustics Madrid, Spain.
Verduzco, L. F. R. (2013). Density and viscosity of biodiesel as a function of temperature: empirical models. Renew. Sustain. Energy Rev. 19, 652–665. doi:10.1016/j.rser.2012.11.022
Wang, S., Xiao, P., Yang, J., Carabineiro, S. A., Wiśniewski, M., Zhu, J., et al. (2023). Catalytic combustion of volatile organic compounds using perovskite oxides catalysts—A review. Front. Chem. Sci. Eng., 1–28. doi:10.1007/s11705-023-2324-x
Zhang, Q., Hu, M., Wang, J., Lei, Y., Wu, Y., Liu, Q., et al. (2022). Synthesis of silicotungstic acid/ni-zr-o composite nanoparticle by using bimetallic ni-zr mof for fatty acid esterification. Catalysts 13 (1), 40. doi:10.3390/catal130-10040
Keywords: ultrasound, free fatty acid, biodiesel, optimization, yield
Citation: Igbax SI, Swartling D, ElSawy A and Idem S (2023) Impact of ultrasonic mixing on virgin and waste vegetable oils for biodiesel production. Front. Energy Res. 11:1268172. doi: 10.3389/fenrg.2023.1268172
Received: 27 July 2023; Accepted: 07 August 2023;
Published: 21 August 2023.
Edited by:
Hu Li, Guizhou University, ChinaCopyright © 2023 Igbax, Swartling, ElSawy and Idem. This is an open-access article distributed under the terms of the Creative Commons Attribution License (CC BY). The use, distribution or reproduction in other forums is permitted, provided the original author(s) and the copyright owner(s) are credited and that the original publication in this journal is cited, in accordance with accepted academic practice. No use, distribution or reproduction is permitted which does not comply with these terms.
*Correspondence: Saanyol Ityokumbul Igbax, saanyol@hotmail.com