Marine Pollution Mitigation by Waste Oils Recycling Onboard Ships: Technical Feasibility and Need for New Policy and Regulations
- 1Department of Civil, Chemical and Environmental Engineering (DICCA), University of Genova, Genoa, Italy
- 2Department of Industrial Engineering (DII), University of Naples “Federico II”, Naples, Italy
- 3Department of Electrical, Electronic, Telecommunications Engineering and Naval Architecture (DITEN), University of Genova, Genoa, Italy
About 80% of the total pollution from ships is caused by operational oil discharges into the sea, often made deliberately and in violation of international rules; the main reasons can be due to cost savings or lack of adequate facilities in ports to receive waste oils. Therefore, reducing waste oil discharges is crucial for a proper protection of the marine environment. In this regard, the paper presents the preliminary feasibility of a particular waste recycling technology, aimed at obtaining marine fuel oil from sludge, through a pyrolysis process to be carried out in a small reactor onboard. The originality of the research consists in the adaptation of pyrolysis to oily waste produced by ships, since this technology is traditionally applied to solid waste and biomass. Furthermore, the plant has to be designed for operation on board the ship, therefore under very different constraints compared to traditional land plants. Although the preliminary lab tests and simulation results in the chemical process are promising enough, there are still some technical criticalities due to the energy optimization of the reactor for an efficient use onboard of the whole system. In addition, the possibility of recycling waste, directly onboard ships, is not yet covered by mandatory regulations, which is why shipowners generally still feel unmotivated to invest in such technologies.
Introduction
International shipping covers over 80% of global trade (IMO, 2020), thus proving to be an essential component of any program for future sustainable economic growth. Currently, the world relies on a safe, sustainable, and efficient international shipping industry, as guaranteed by the regulatory framework developed by the International Maritime Organization (IMO)—the United Nations specialized agency with responsibility for the safety and security of shipping, including the prevention of marine and atmospheric pollution from ships.
Despite IMO rules, marine pollution from ships is still a reality, as it accounts for around 20% of the total sea pollution, and it can be caused both by accidents and ships daily activities. About 80% of the total pollution from ships is estimated to be originated from operational discharges (such as discharges of waste oils or tank cleaning operations), made deliberately and in violation of international rules due to several reasons, including: lack of adequate facilities in ports to receive ships’ wastes, cost-savings (the costs for delivery to shore may be prohibitive and may cause significant delays to ships), or mere convenience of the ship’s crew (European Maritime Safety Agency, 2008).
In this framework, the present work shows a preliminary feasibility analysis of a waste recycling system to produce additional fuel from sludge (mainly generated by the diesel oil treatment). Nowadays, waste oil is collected and unloaded in reception facilities provided by port authorities, but they could be transformed into marine fuel oil, leading to environmental benefits and energy savings. It can be made by a pyrolysis process, that is, a thermal decomposition of organic materials that occurs in the absence of oxygen. The chemical process produces gaseous, liquid, and solid compounds. Onboard, the oil produced from pyrolysis can be used directly as fuel, while gas could feed the boiler onboard and solids could be sent to incinerator.
The pyrolysis technology is traditionally applied to biomass and solid waste, while in the present study the investigation is focusing on oil sludge. Currently, there are very few works in the scientific literature regarding pyrolysis used for liquids; some examples concern waste cooking oil (Romero et al., 2016), waste automobile lubricating oil (Kim and Kim, 2000), and oil sludge from the petroleum industry (Chang et al., 2000; Shie et al., 2002; Punnaruttanakun et al., 2003; Wang et al., 2007; Hu et al., 2013).
As far as the authors are aware, there are no studies concerning the use of this technology in the case of oil sludge from ships. Therefore, the innovation in the present research mainly consists in the new field of application of pyrolysis, trying to develop an onboard system that is simple to operate and as efficient as possible, compatibly with the ship requirements. To this end, the main challenge is to design a space-saving pyrolysis reactor that can possibly be powered by the free energy resources available onboard. This option would provide a double advantage: an immediate availability of free fuel for the ship and a shorter chain of waste disposal, with consequent reduction in costs and risk of pollution. A similar idea has been recently proposed by Eslam (2019), which describes a special coastal vessel, capable of receiving and recycling onboard sludge from other ships in transit in the Suez Canal, using a catalytic distillation plant.
Both solutions require appropriate legislation to encourage shipowners to use these new waste recycling technologies. In fact, current regulations provide for compliance with limits on air emissions and onboard waste management procedures, excluding waste recycling. In this light, the possibility of obtaining new fuel from sludge does not entail a real fuel reduction, which means a lower emission of pollutants. Then the technology presented in this report does not facilitate compliance with the current regulatory limits about emissions from ship’s engines, although the environmental benefits due to the recycling process are obvious. Therefore, it would be important that at least economic sustainability is demonstrated, pending desirable regulations that reward shipowners in adopting these waste recycling solutions.
Materials and Methods
The present work focuses on the feasibility to threaten onboard oil waste produced by a passenger ship. In this case, oil waste mainly consists of sludge (derived from engine fuel and oil purification) and cooking oil, while the amount of exhausted lubricating oil from the ship’s engines is negligible, and it is often stored together with oil sludge.
In this work, the waste recycling is concentrated on sludge oil because it is produced in a bigger quantity by merchant ships.
Although the pyrolysis process is mainly applied to biomass and solid waste, the choice of using this technology also for waste oils has been supported by the preliminary lab tests carried out by the authors at Genoa University (Cadenasso and Fabbri, 2017; Vigna et al., 2020). In fact, experimental results show a conversion factor into fuel around 32% (viscosity equal to 2.77 Cst), while the remaining products are water (30%), gas (17%), and solid waste (21%). In this regard, it is important to point out that these results were achieved through a thermocatalytic pyrolysis process. As an alternative, to simplify the installation onboard, in this study a pyrolysis without the use of a catalyst is investigated here.
Before undertaking new expensive experimental tests, it was decided to preliminarily analyze the efficiency of the process by numerical simulation, through the commercial software Aspen Plus (one of the leading process simulation software products in the field of chemical and process industry).
Simulation Assumptions
Aspen simulation requires defining the components involved in the process and their specifications and to choose the property methods to calculate thermodynamic properties, such as fugacity coefficient, enthalpy, entropy, Gibbs energy, and molar volume. Then it is possible to represent the process diagram regarding flows and main units (reactors, mixers, exchangers, etc.).
Regarding the property method, the Peng-Robinson model has been chosen because it is recommended for hydrocarbon processing applications such as gas processing, refinery, and petrochemical processes (AspenTech, 2010).
With respect to the composition of sludge oil produced onboard and necessary for simulation, no references were found in the literature. However, oil sludge from refinery plant (a stable emulsion of hydrocarbons compounds, water, solids and heavy metals) may be considered the most similar waste-to-oil residues on board (Hu et al., 2013).
In addition, for the present work, a chemical analysis of a sludge sample, kindly provided by GNV (an Italian Ro-Ro ferry company) has been carried out by the Renewable Energy Consortium for Research and Demonstration (RE-CORD), Florence, Italy. A comparison between RE-CORD results and the chemical composition of oil sludge from refinery plant, reported in Hu et al. (2013), is shown in Table 1.
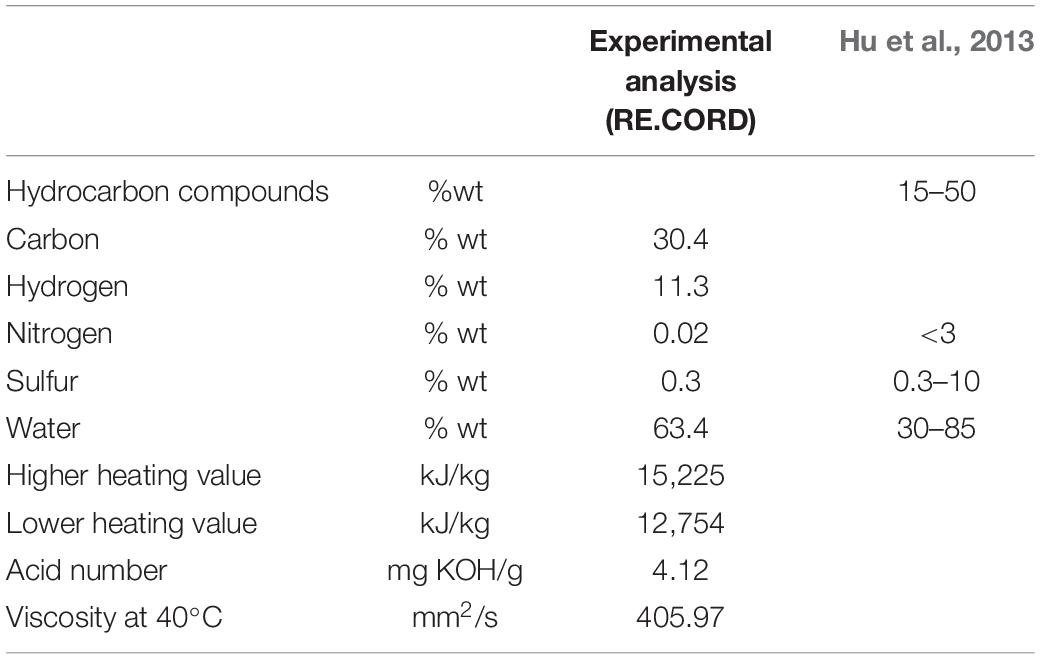
Table 1. Comparison between chemical analyses carried out by RE-CORD and Hu et al. (2013).
In summary, different sources have been considered to identify the composition of marine sludge:
• Data from the literature (Hu et al., 2013);
• Results from chemical analysis (RE-CORD);
• Typical composition of marine heavy fuel, being contained in oily sludge.
This result in the following list of elements, adopted for simulation in terms of weight percentage: Octane (0.0154%), Tridecane (0.0006%), Tetradecane (0.0009%), Pentadecane (0.0011%), Hexadecane (0.0012%), Heptadecane (0.0013%), Octadecane (0.0011%), Nonadecane (0.0012%), Eicosane (0.0011%), Heneicosane (0.0001%), Docosane (0.0009%), Tricosane (0.0008%), Tetracosane (0.0007%), Pentacosane (0.0006%), Hexacosane (0.0005%), Heptacosane (0.0004%), Octacosane (0.0005%), Nonacosane (0.0004%), Triacontane (0.0004%), Hentriacontane (0.0004%), Dotriacontane (0.0005%), 3-Ethyloctadecane (0.0218%), Dodecylcyclopentane (0.0349%), Bicyclohexyl (0.1033%), Benzene (0.0073%), 1-Pentyltetralin (0.0073%), Indene (0.0073%), 1-Methylnaphthalene (0.0109%), Acenaphthene (0.0109%), Acenaphthalene (0.0250%), Phenanthrene (0.0440%), 2-Benzyl-1-phenylheptadecane (0.0600%), Benzothiophene (0.0030%), Acridine (0.0002%), and Water (0.6340%).
For the pyrolysis reaction simulation, in Aspen Plus there are different possible types of reactors to be considered. Ward et al. (2014) suggests that the RYIELD reactor block is the most suitable for the pyrolysis process, which involves solid, liquid, and gas phases. Moreover, in this kind of process, the number of reactions involved is large and, usually, their kinetics are unknown; thus the RYIELD block is appropriate because it calculates the yield distribution of the products without the need to specify reaction stoichiometry and kinetics (Atnaw et al., 2011), unlike other reactor models contained in Aspen Plus.
To define the product yield, it was referenced to experimental results from literature (Wang et al., 2007). A fitting carried out in a MATLAB environment has been made to correlate yield (gas, solid, water, and liquid fractions) and reaction temperature. The comparison between the obtained correlation and literature data (Wang et al., 2007) is shown in Figure 1.
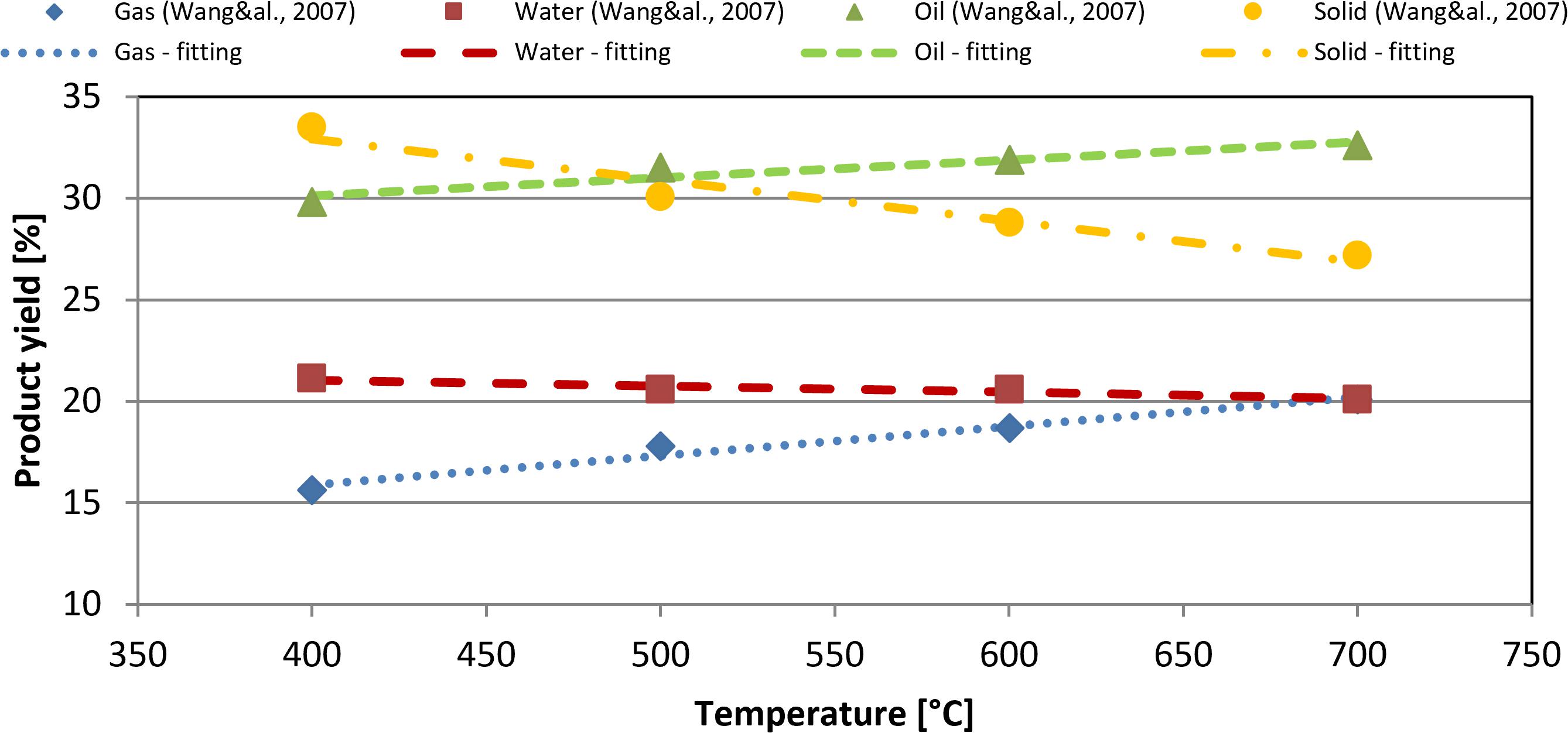
Figure 1. Comparison between simulation results and literature data (Wang et al., 2007).
Subsequently, the correlation was inserted in Aspen Plus as an embedded Excel sheet, which determines the yields of the RYIELD reactor.
Process Scheme
A process scheme of the simulated pyrolysis plant is shown in Figure 2.
In Wang et al. (2007) water is removed from sludge before the pyrolysis process, and in Hu et al. (2013), the authors report the need for dewatering of oily sludge before pyrolysis treatment. Therefore, at first, sludge was sent to a decanter (DECANTER) where almost all water (H2O) was separated. After that, heater exchanger (HEATER) was used to raise the temperature reaction and, then, sludge (HEATOIL) was sent into a jacketed and agitated reactor (REACTOR) where the feed was converted into three separate fractions: gas, liquid, and solid (GLS). The residue (SOLID) was discharged from the bottom of the reactor (SEPARSOL) and separated from liquid and gaseous products (VAP). The latter were cooled (COOLER) and sent to a condenser (CONDENS) to eliminate water (WATER) and to a flash drum (SEPAR) in order to separate the condensable compounds (OIL) from the incondensable (GAS) ones.
International Rules on Ships Pollution and Energy Efficiency
In 1973, IMO adopted the International Convention for the Prevention of Pollution from Ships, known as MARPOL, which has been amended by the Protocols of 1978 and 1997 and kept updated with relevant amendments. The MARPOL Convention addresses: pollution from ships by oil (Annex I) and by noxious liquid substances carried in bulk (Annex II), harmful substances carried by sea in packaged form (Annex III), sewage (Annex IV), garbage (Annex V), and the prevention of air pollution from ships (Annex VI). MARPOL applies to 99% of the world’s merchant tonnage.
Other treaties address anti-fouling systems used on ships (“The International Convention on the Control of Harmful Anti-fouling Systems on Ships,” 2008), the transfer of alien species by ships’ ballast water (Ballast Water Management “BWM Convention,” 2017), and the recycling of ships (“The Hong Kong International Convention for the Safe and Environmentally Sound Recycling of Ships,” the Hong Kong Convention 2009).
In MARPOL Annex VI, the Energy Efficiency Design Index (EEDI) was made mandatory for new ships since 2011 (this was the first legally binding climate change treaty to be adopted since the Kyoto Protocol). The EEDI is expressed in grams of carbon dioxide (CO2) per ship’s capacity by mile (the smaller the EEDI, the more energy efficient ship design) and is calculated by a formula based on the technical design parameters for a given ship. It is quite detailed, but the general structure can be more simply summarized as follows:
representing the energy efficiency of a vessel, expressed as the ratio between the environmental cost (CO2 emitted) and the benefit produced for society (transport work).
The EEDI requires a minimum threshold, which is tightened incrementally every 5 years to stimulate innovation and technical development toward the use of more energy efficient (less polluting) technologies, for different ship type and size segments.
In addition, IMO also suggests an approach for shipping companies to manage ship and fleet efficiency performance over time, through the Energy Efficiency Operational Indicator (EEOI) computation. It is a possible monitoring tool, defined as the ratio of mass of CO2 emitted per unit of transport work:
where Fcj is the consumption of fuel j per voyage; CFj is the conversion factor for fuel j to estimate CO2 mass (e.g., diesel oil = 3.206); mcargo is the cargo carried (tons) or work done (number of TEUs or passengers); and D is the distance in nautical miles.
Results and Discussion
Simulation Results
A 5,000-passengers ship has been examined for the case study of the pyrolysis process, given the greater quantities of waste it can produce.
Considering for the cruise ship an average sludge production of 1,175 m3/year (data available by courtesy of Costa Crociere), corresponding to about 1,000 t/year, the pyrolysis process is supposed to take 4 h a day, with a sludge flow rate of 755 kg/h. Since the water content in sludge is approximately 60%, after the initial sedimentation phase, the flow rate to the pyrolysis reactor becomes around 280 kg/h. Under this assumption, an equipment volume less than 1 m3 should be sufficient for the system arrangement onboard.
It was assumed that the reaction occurs at atmospheric pressure and 450°C temperature within the range of the study reported by Wang et al. (2007) and considered as the optimum pyrolysis temperature for oily sludge by Cheng et al. (2016).
The main results of the simulation process are reported in Table 2. The pyrolysis process allows a liquid fuel yield around 30%, similar to preliminary experimental results of Genoa University (Cadenasso and Fabbri, 2017). However, the liquid fuel obtained in wet sludge condition is only 11% because the water content in sludge is usually high, and it should be eliminated before pyrolysis (in this case, the actual feed to the pyrolysis reactor would drop to around 40% of the initial sludge quantity).
Thermal Power Sources Analysis
As previously mentioned, sludge needs to be heated to reaction temperature (450°C). Moreover, the pyrolysis reaction is endothermic; therefore, a thermal power is needed to allow the reaction proceeding. According to simulation results, the heat required is 146 kW:90 kW to preheat sludge up to 450°C and 56 kW for reaction proceeding.
The thermal power required by the pyrolysis process may be delivered by different sources, each one with pros and cons:
- by the exhaust gas from diesel engine, downstream of the turbocharger. This option would be energy-free; however, the available temperature (usually about 350°C in typical engines for passenger vessels) is lower than the reaction temperature of the pyrolysis process. Therefore, this heat source would be only suitable for a pre-heating phase.
- by the exhaust gas from the main engines, at the turbine inlet. The gas temperature is higher (around 540°C) than in the previous case; however, the engine should be appropriately modified.
- by the waste incinerator, already installed onboard passenger ships, as it could supply all the required thermal power; for instance, the power of a typical incinerator of a Costa Crociere ship is around 1,600 kW, with a combustion temperature of about 850°C (Costa Crociere Group, 2015). Furthermore, the incinerator stays on for about 11 h/day, so its heat could be used for the pyrolysis process throughout the pyrolysis process duration estimated at 4 h/day.
Therefore, the exploitation of the heat released by the incinerator seems to be the best option, although the incinerator needs some small modifications in its geometry. In fact, an integrated reactor-incinerator system could be created and the exhaust gas flow from the ship incinerator could be used for the reaction. Then, the same gases could preheat the sludge.
To move the oil sludge from the tank to the reactor, a small pump could be sufficient, given the low vertical distance between sludge tank and incinerator. Once the reaction is completed, the solid part could be directly incinerated, while the liquid product could be easily moved to the fuel tanks by gravity.
Energy Efficiency
The liquid product, about 117 ton/year, is certainly suitable as fuel for marine engines because it meets the requirements established by the ISO standard (ISO 8217:2010 RMK280); in this regard, the details of the chemical composition of the product obtained from the pyrolysis reaction by simulation are reported in Table 2.
Assuming a 50-week trip for the examined ship, the marine fuel consumption would be 40,000 ton/year; therefore, through the pyrolysis process, the saving in the fuel purchased by the shipowner is around 0.3%.
Unfortunately, this small economic advantage may not be enough for the diffusion of this technological solution; however, it is proper to consider that also the disposal sludge costs could be eliminated, or at least significantly reduced, with resulting environmental advantages.
In particular, taking into account the fuel oil price1 and also considering the elimination of the cost of oily waste disposal (an average cost of 65€/m3 can be assumed in the case of Italian port reception facilities), an annual savings of about 22% of the construction cost is estimated. The investment cost for the construction of the plant is deduced from literature data reported in Ringer et al. (2006) and Cheah et al. (2017), and it can, therefore, be recovered in about 4–5 years of operation. In addition, the sludge discharge into port often involves an important logistical organization: for example, the fuel supply is not allowed at the same time as the waste oils discharge. Therefore, the onboard oil reuse might be also convenient for ship management at the port area.
This solution would become even more practical if its undoubted environmental value would also be recognized by current legislation. In this regard, IMO rules are provided for the computation of the EEOI (Eq. 2), as previously defined. However, the sludge conversion into fuel does not allow a real CO2 emission reduction because a real fuel consumption reduction for the ship engines is not involved. In order to enhance waste recycling on board, an increase in ship cargo has been recently proposed by the authors for the EEOI computation of a passenger ferry, equipped with a possible waste oils treatment plant, adopting pyrolysis technology (Vigna et al., 2020). In the reference study, the new fuel produced from sludge is supposed as a sort of additional cargo, in order to increase the denominator of Eq. (2) and then decrease EEOI; but also in this new interpretation of IMO indicator, a significant reduction in EEOI computation is not found (less than 0.05%).
Conclusion
The present technical report deals with the important problem concerning the disposal of waste on board passenger ships, trying to transform this into an energy resource that would otherwise have to be delivered in port reception facilities, with significant costs for the shipowners and risks of pollution.
Considering only waste oils generated through the treatment of the engine fuel and lubricating oil, a small pyrolysis plant can be installed onboard to produce additional fuel from sludge. As far as the authors are aware, the present research represents the first application of a pyrolysis technology to oily waste from ships; therefore, preliminary experimental tests and simulation have been carried out. The results show a pyrolysis process conversion factor into fuel of around 30% in dry sludge condition, decreasing to about 11% in the case of wet sludge.
Although further investigations are still needed on some critical issues (e.g., design of a particular waste incinerator to be exploited to supply the necessary thermal power for the pyrolysis reaction), the transformation onboard of the waste into new fuel for the ship seems feasible.
On the other hand, the amount of economic savings cannot be considered a strong stimulus for the spread of this technology on board ships, unless new environmental policies are initiated. The current regulations on ship pollution are in fact not yet effectively applicable for a real enhancement of waste recycling on board ships.
Data Availability Statement
The original contributions presented in the study are included in the article/supplementary material, further inquiries can be directed to the corresponding author.
Author Contributions
MA, MM, BB, EA, and VV contributed to the conception and design of the study. MM organized the database and performed the simulation analysis. MA and VV performed the ship energy efficiency analysis. MA, MM, and VV wrote the first draft of the manuscript. All authors contributed to manuscript revision, read and approved the submitted version.
Funding
The research was realized under the project “Technological platform for high-efficiency energy thermoconversion of waste on board” in the framework of the cooperation Fincantieri-CNR, funded by the Italian Ministry of Infrastructures and Transports.
Conflict of Interest
The authors declare that the research was conducted in the absence of any commercial or financial relationships that could be construed as a potential conflict of interest.
Footnotes
References
AspenTech (2010). Aspen Physical Property System - Physical Property Methods. Bedford, MA: AspenTech.
Atnaw, S. M., Sulaiman, H. A., and Yusup, S. (2011). A simulation study of downdraft gasification of oil-palm fronds using ASPEN PLUS. J. Appl. Sci. 11, 1913–1920. doi: 10.3923/jas.2011.1913.1920
Cadenasso, E., and Fabbri, A. (2017). Valorizzazione Energetica a Bordo Nave di Differenti Tipologie di Rifiuti. Master’s degree thesis, Genoa, IT: University of Genoa.
Chang, C. Y., Shie, J. L., Lin, J. P., Wu, C. H., Lee, D. J., and Chang, C. F. (2000). Major products obtained from the pyrolysis of oil sludge. Energy Fuels 14, 1176–1183. doi: 10.1021/ef0000532
Cheah, K. W., Yusup, S., Singh, H. K. G., Uemura, Y., and Lam, H. L. (2017). Process simulation and techno economic analysis of renewable diesel production via catalytic decarboxylation of rubber seed oil – A case study in Malaysia. J. Environ. Manage. 203, 950–961. doi: 10.1016/j.jenvman.2017.05.053
Cheng, S., Wang, Y., Gao, N., Takahashi, F., Li, A., and Yoshikawa, K. (2016). Pyrolysis of oil sludge with oil sludge ash additive employing a stirred tank reactor. J. Anal. Appl. Pyrolysis 120, 511–520. doi: 10.1016/j.jaap.2016.06.024
Costa Crociere Group (2015). Sustainability Report. Results and Outlook. Genoa: Costa Crociere Group.
Eslam, M. M. (2019). “Recycling marine used oil using green ship conversion technique,” in Proceedings of the SPE Gas & Oil Technology Showcase and Conference, Dubai.
European Maritime Safety Agency (2008). Preventing Pollution from Ships. Lisboa: European Maritime Safety Agency.
Hu, G., Li, J., and Zeng, G. (2013). Recent development in the treatment of oily sludge from petroleum industry: a review. J. Hazard. Mater. 261, 470–490. doi: 10.1016/j.jhazmat.2013.07.069
IMO (2020). IMO Official Site. Available online at: http://www.imo.org/en/OurWork/Environment/PollutionPrevention/Pages/Default.aspx (access March 2020).
Kim, S. S., and Kim, S. H. (2000). Pyrolysis kinetics of waste automobile lubricating oil. Fuel 79, 1943–1949. doi: 10.1016/s0016-2361(00)00028-4
Punnaruttanakun, P., Meeyoo, V., Kalambaheti, C., Rangsunvigit, P., Rirksomboon, T., and Kitiyanan, B. (2003). Pyrolysis of API separator sludge. J. Anal. Appl. Pyrolysis. 6, 547–560. doi: 10.1016/s0165-2370(03)00033-0
Ringer, M., Putsche, V., and Scahill, J. (2006). Large-Scale Pyrolysis Oil Production: A Technology Assessment and Economic Analysis. Colorado: National Renewable Energy Laboratory.
Romero, M. J. A., Pizzi, A., Toscano, G., Busca, G., Bosio, B., and Arato, E. (2016). Deoxygenation of waste cooking oil and non-edible oil for the production of liquid hydrocarbon biofuels. Waste Manag. 47, 62–68. doi: 10.1016/j.wasman.2015.03.033
Shie, J. L., Chang, C. Y., Lin, J. P., Lee, D. J., and Wu, C. H. (2002). Use of inexpensive additives in pyrolysis of oil sludge. Energy and Fuels 16, 102–108. doi: 10.1021/ef0100810
Vigna, V., Altosole, M., Figari, M., and Ferrari, A. (2020). “A ship energy efficiency analysis by considering trim influence and waste recycling,” in Sustainable Development and Innovations in Marine Technologies - Proceedings of the 18th International Congress of the International Maritime Association of the Mediterranean, (Bulgaria: IMAM), 316–321. doi: 10.1201/9780367810085-41
Wang, Z., Guo, Q., Liu, X., and Cao, C. (2007). Low temperature pyrolysis characteristics of oil sludge under various heating conditions. Energy Fuels 21, 957–962. doi: 10.1021/ef060628g
Keywords: ship waste recycling, pollution, diesel oil, sludge, pyrolysis, energy efficiency, rules
Citation: Mazzoccoli M, Altosole M, Vigna V, Bosio B and Arato E (2020) Marine Pollution Mitigation by Waste Oils Recycling Onboard Ships: Technical Feasibility and Need for New Policy and Regulations. Front. Mar. Sci. 7:566363. doi: 10.3389/fmars.2020.566363
Received: 30 June 2020; Accepted: 11 November 2020;
Published: 18 December 2020.
Edited by:
Hans Uwe Dahms, Kaohsiung Medical University, TaiwanReviewed by:
Baoquan Li, Yantai Institute of Coastal Zone Research (CAS), ChinaYing Wang, Tianjin University of Commerce, China
Copyright © 2020 Mazzoccoli, Altosole, Vigna, Bosio and Arato. This is an open-access article distributed under the terms of the Creative Commons Attribution License (CC BY). The use, distribution or reproduction in other forums is permitted, provided the original author(s) and the copyright owner(s) are credited and that the original publication in this journal is cited, in accordance with accepted academic practice. No use, distribution or reproduction is permitted which does not comply with these terms.
*Correspondence: Marco Altosole, marco.altosole@unina.it