Pultrusion of Bendable Continuous Fibers Reinforced Composites With Reactive Acrylic Thermoplastic ELIUM® Resin
- Arkema GRL, Lacq, France
Continuous fiber reinforced composites were made using in-situ polymerization of a new liquid thermoplastic resin. Depending on the temperature profile in the die and the initiators used, it was shown that PREDICI software enables the simulation of the radical polymerization reaction. By using an appropriate sizing for the fibers, the properties of the pultruded part are comparable to standard thermoset resins. Moreover, the specific thermoplastic behavior of the matrix provides the unique advantage of being post-formable or shapeable as desired while maintaining mechanical performances.
Introduction
Nowadays, continuous fiber-reinforced composites (CFRC) are widely used in various industrial sectors as aircraft, automotive, building and construction or transportation applications. When compared to metallic parts, the lighter weight but equivalent mechanical properties of the CFRC materials makes them attractive in reducing their environmental footprint and fuel consumption. Manufacturing CFRC has been based on thermoset composite technology, but due to new environmental issues and especially a growing need for recyclability, thermoplastic matrix composites offer some advantages. Thermoplastic-based composites are commonly processed by hot-processing of pre-impregnated reinforcing yarns or tows but thermoplastic matrices usually exhibit high viscosity in the molten state that could impair the fiber impregnation. To overcome this problem, more reliable and cost-effective processing strategies were developed in which the in-situ polymerization (van Rijswijk and Bersee, 2007) of a new acrylic liquid thermoplastic resin is accomplished after fiber impregnation. The polymerization can take place in a mold or die that are already being used for common thermoset applications. In this study, an acrylic liquid thermoplastic resin ELIUM® was investigated in a pultrusion process. Pultrusion is an automatic and continuous process for manufacturing continuously fiber-reinforced thermoplastic composites (Ma and Chen, 1991a,b, 1992a,b). One of the major advantages of the process is its continuous nature, which in principle may enable a high degree of automation. The objective of this paper is to present the use of an acrylic thermoplastic resin with a suitable viscosity, which polymerizes in the pultrusion die. It provides a new concept for in-situ thermoplastic pultrusion on existing tooling and an opportunity for developing an entirely new era of pultruded composite profiles and structures. This paper discusses the prediction of the radical polymerization of the acrylic resin in the die, the interfacial properties, the mechanical properties of pultruded glass fiber, the dynamic mechanical properties and the post-formability. Indeed, unlike thermoset resins, pultruded thermoplastic composites can be locally heated and post-formed under pressure into a complex 3D shape in order to fulfill specific design needs (Becker et al., 2016).
Materials and Methods
Table 1 summarizes the materials used in this study, which include methyl methacrylate monomer, ELIUM® C595 E acrylic resin, peroxide initiators, and glass fiber.
Apparatus and Methods
The pultrusion machine used was designed by ROMEO Engineering Inc. and consisted of a pultrusion die with multiple heating zones and dimensions of 0.2 × 10 × 100 cm (thickness × width × length), as shown in Figure 1. The surfaces of the stainless steel die have been treated by chrome plating. A universal material testing machine was used for the mechanical property tests, an Instron 1175 with a 100 kN S/N UK1280 cell (Instron Co.). Optical microscopy was done using Zeiss Axioplan2 (Zeiss Co.). The SEM (Scanning Electron Microscope) used was a GeminiSEM 500 (Zeiss Co.) and fracture surfaces of the specimen were coated with a gold film by sputtering process, making them conductive for SEM analyses. The RDS (Rheometric dynamic spectrometer) utilized was a Rheometric Scientific RDA II (Rheometrics Inc.). Gas chromatography used was the Series II 5890 apparatus (Hewlett Packard Co.).
Tensile strength and tensile modulus were measured following the specification of ISO 527 with the use of strain extensometer. The sample dimensions were 0.2 × 2.5 × 25 cm (thickness × width × length) and the crosshead speed was 5 mm/min and a strain rate of 3 × 10−4 s−1. Flexural strength and flexural modulus were measured following ISO 14129 in both machine direction (i.e., fibers direction) and transverse direction. The sample dimensions were 0.2 × 1.5 × 8 cm, the span was 4 cm and the crosshead speed was 2 mm/min. Compressive strength and compressive modulus were measured following ISO 14126 and the Celanese method with the use of strain gauges. The sample dimensions were 0.2 × 1 × 12 cm and the crosshead speed was 21 mm/min. All mechanical analysis were performed on three samples.
The glass transition temperature was measured based on the DMA curves at the maximum of tangent delta and the remaining residual monomer level from the pultruded thermoplastic composite part was measured by gas chromatography, following an internal standard.
Results and Discussion
ELIUM® Polymerization in Pultrusion
Pultrusion is a continuous process that produces parts with a constant cross-section, such as I-beams, channels, solid rods and rails. The process utilizes fibers (glass, carbon), resin, filler, peroxides, pigments, and release agent. The fiber reinforcement is fed from spools into a resin bath where the fiber substrate is thoroughly impregnated with the resin mixture. An alternative process would be the impregnation in an injection box (I-box). The wet fibrous material then proceeds through forming guides where excess resin is removed from the fiber. The fiber/resin matrix solidifies into the exact shape of the cavity of the heated die being used. Grippers or caterpillar pads then pull the cured material to a cut off station where it is cut to the desired length. Pultrusion can produce very high strength parts with fiber content as high as 80 wt%.
As with many processes, there is more than one method for pultrusion (see Figure 2). With practice and experience, the method can be modified to fit the application or specific requirement.
Generally, the resin used for the in-situ pultrusion process should possess the following characteristics: (1) high reactivity (complete polymerization in <2 min), (2) long pot life in the impregnation bath (more than 8 h at ambient temperature or one shift of successive production), and (3) good wettability of the fiber.
The conditions for ELIUM® polymerization in pultrusion utilize temperatures between 100 and 140°C depending on the desired line speed and peroxide cocktail that is used. A typical formulation is shown in Table 2 (Gerard et al., 2018).
Simulation of Kinetics With the Modeling Software PREDICI
The following section will present the results of a computational model for the simulation of the polymerization of methyl methacrylate based on the formulation and initiator system described in section ELIUM® Polymerization in Pultrusion. The simulation was carried out by using the software PREDICI. Zoller et al. (2015, 2016) described the different model parts and the robustness of the simulation in previous publications. The different reaction steps, such as decomposition of the peroxide, initiating of the peroxide radical with the first monomer, propagation and termination, for the simulation of the polymerization of ELIUM® resin are shown in Figure 3.
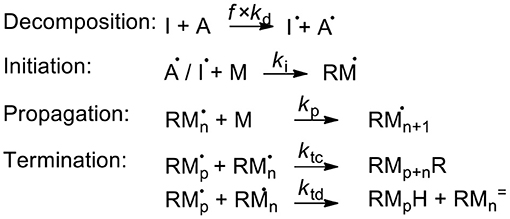
Figure 3. Main reactions taken into account for PREDICI simulation of ELIUM® resin with initiators (A, I), polymer end-group (R) and monomer (M).
The initiating step is described by the thermal decomposition of the peroxides based on the Arrhenius equations given by the supplier (see Table 3) (Nouryon, 2019) in combination with a model based on the free volume describing the solvent cage-effect (Achilias et al., 1988; Achilias and Kipasissides, 1992). The cage-effect describes a solvent surrounding the reacting species. The species needs to get out of this solvent cage in order to react with other molecules (Guillaneuf et al., 2008). As the efficiency determines how many radicals are actually able to initiate the polymerization, it is a very important factor and needs to be calculated throughout the whole conversion range. It was reported in literature that the efficiency decreases strongly at high conversions, between 70 and 80% depending on the polymerization conditions (Balke and Hamielec, 1973; Russell et al., 1988). The efficiency drop is generally explained with the increasing viscosity resulting in a decrease in diffusivity of the radicals. The higher viscosity can be envisioned like a more cohesive cage, where it becomes less probable for the radicals to escape.
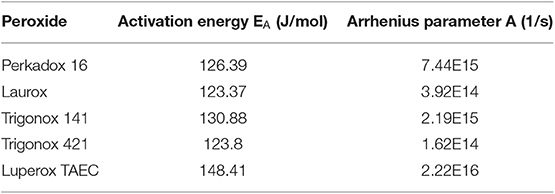
Table 3. Overview on the Arrhenius parameters of the different peroxides used (Nouryon, 2019).
The propagation step has a great influence on the polymerization time as well as the chain length of the polymers. The propagation rate coefficient at low conversion kp,0 of a large number of acrylic (Beuermann et al., 1997, 2007; Kattner et al., 2015) and methacrylic monomers (Beuermann et al., 1996, 2000; Hutchinson et al., 1998; Yin et al., 2003; Achilias and Sideridou, 2004; Haehnel et al., 2014) is well-investigated by several research groups and the IUPAC working party “Modeling of kinetics and processes of polymerization.” The propagation rate coefficient kp is constant over a large range of conversion and drops rapidly at the glass transition of the polymer due to diffusion limitations similar to the cage effect as shown in Figure 4. For the simulation, the diffusion-controlled propagation model from Achilias et al. was chosen (Achilias et al., 1988; Achilias and Kipasissides, 1992).
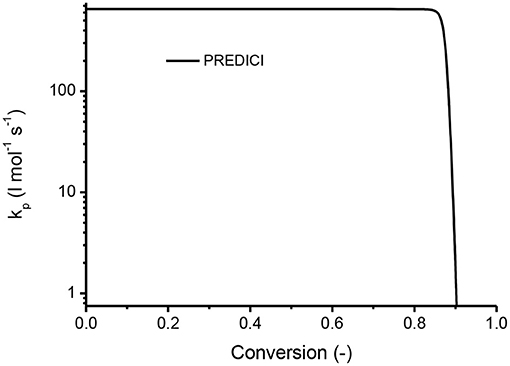
Figure 4. Propagation rate coefficient kp as developed in PREDICI with the Achilias diffusion model (Haehnel et al., 2014; Zoller et al., 2015, 2016).
The main difficulty in the description of a bulk polymerization of methyl methacrylate (MMA) is the termination step. In this case, an empirical model of Ballard (Ballard et al., 1984; Russell et al., 1988) was used for the simulation of the conversion of MMA.
The polymerization of MMA is initiated by three different peroxides; Bis(tert-butylcyclohexyl) peroxydicarbonate (Perkadox 16), Dilauroyl peroxide (Laurox), and 2,5-Dimethyl-2,5-di(2-ethylhexanoylperoxy)hexane (Trigonox 141). The conversion profiles of the different peroxides as well as the conversion of the monomer MMA are shown in isothermal simulation conditions in Figure 5 without presence of the glass fibers. A possible influence of the glass fibers would be mainly a decrease in the exotherm as the fibers would act as a heat sink for the resin. These assumptions are not taken into account in the model as it does not take into account the exotherm of the polymerization reaction. As shown in Figures 5, 6, the conversion of the peroxides are simulated. In both cases there is a “starter peroxide” (Perkadox 16), a “follow-up peroxide” (Laurox or Trigonox 421) and a “finisher peroxide” (Trigonox 141 or TAEC). All of them have a particular role in the polymerization process as the different names indicate. The starter allows a quick conversion at the beginning of the polymerization accompanied by a quick increase of viscosity (Trommsdorff effect or gel effect). The follow-up peroxide has the role to pursue the polymerization and might be largely consumed (>70% conversion) at the end of the polymerization. Therefore, a finisher is added to the formulation to ensure the conversion of the last percentages of monomer. Considering a typical pultrusion die of 1 m, the speed would be 0.5 m/min. It can be easily shown that for a speed of 1 m/min, the residence time in the die would be 60 s and the gelation of MMA would be outside of the die (after 60 s). The fact that the curing would happen outside of the die leads to incomplete conversion and a high residual monomer content that heavily impairs the material properties.
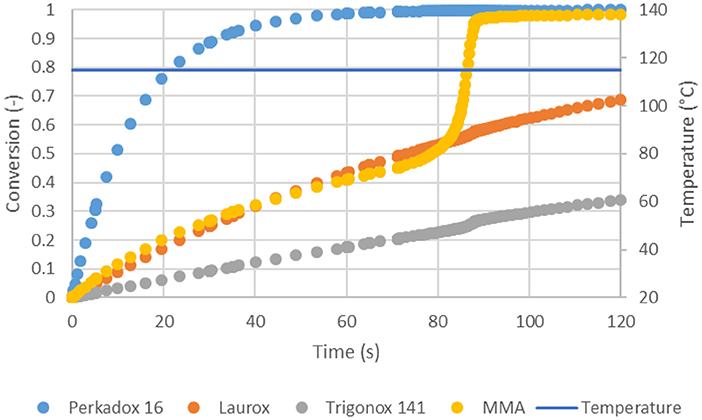
Figure 5. Typical PREDICI simulation of the conversion of the initiators Perkadox 16 (blue points), Laurox (orange points), Trigonox 141 (gray points), the monomer methyl methacrylate (MMA) (yellow points), and the temperature (isothermal 110°C) (blue line).
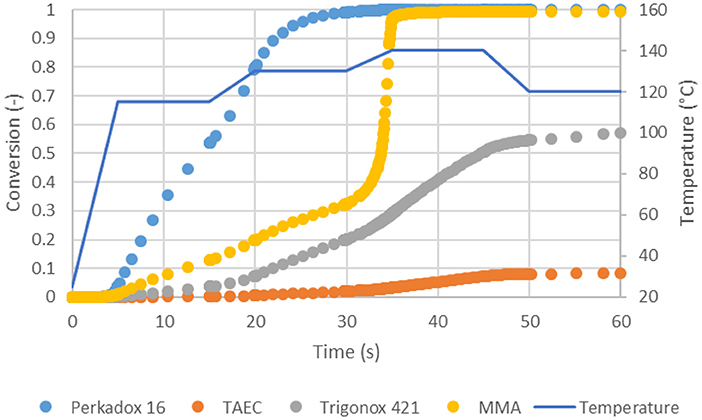
Figure 6. Alternative PREDICI simulation of the conversion of the initiators Perkadox 16 (blue points), Luperox TAEC (orange points), Trigonox 421 (gray points), the monomer methyl methacrylate (MMA) (yellow points), and the temperature (zone 1: 115°C, zone 2: 130°C, zone 3: 140°C, zone 4: 120°C) (blue line).
The advantage of the simulation software is the optimization of the process parameters. An example is given below in Figure 6 with the parameters of four heating zones each with a different temperature. The heating zones were optimized in a way that the conversion of the peroxides has a similar profile as the isothermal one at 110°C, which was experimentally shown to give good results. In that case, the gelation can be predicted in the die with a faster conversion. The case below in Figure 6 is using a die length of 1 m and a speed of 1 m/min, which results in a residence time of 60 s. Here it is shown that the methyl methacrylate (MMA) is able to convert completely using the given conditions. A further improvement of the simulation would be the use of the experimental temperature curve for more accurate predictions.
Mechanical Characterization of Pultruded Profiles
The obtained unidirectional (UD) pultruded profiles, produced at 110°C based on the formulation given in Table 2, were (thermo)-mechanically and chemically analyzed as shown in Table 4. The resulting properties are comparable to vinyl ester or epoxy thermoset profiles (Tensile strength 0°:900 MPa, Tensile Modulus 0°: 42 GPa) (Exel Composites, 2019). It is shown that the properties in fiber (0°) direction are extremely high with flexural, tensile and compression strength values above 1,000 MPa, especially the compression strength.
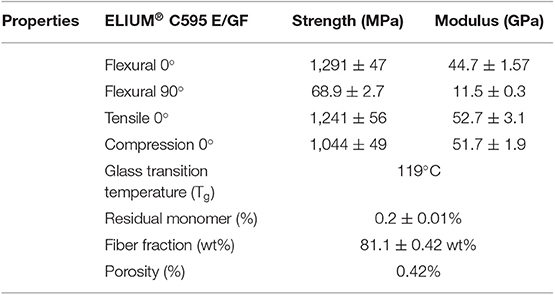
Table 4. Mechanical and thermomechanical properties (flexural 0° and 90° strength, flexural modulus 0° and 90°, tensile strength 0°, tensile modulus 0°, compression strength 0°, compression modulus 0°, glass transition temperature (Tg), residual monomer content, fiber fraction and porosity) of pultruded UD glass profiles with ELIUM® C595 E.
The values of the transverse strength in UD profiles can be easily improved by adding some non-woven fabric mats, webs or fabrics during the pultrusion process.
The Choice of the Proper Sizing for ELIUM® Resins
The cross-section and longitudinal fracture surfaces of pultruded glass fiber reinforced acrylic thermoplastic composites were investigated by scanning electron microscope as shown in Figure 7.
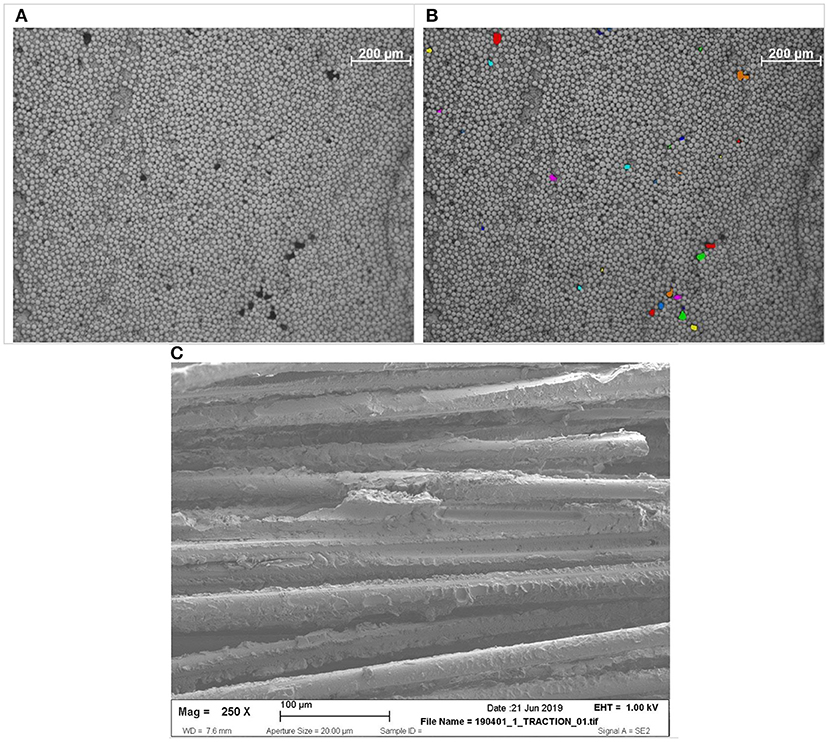
Figure 7. Microscope of cross-section sample with ELIUM C595 E. (A) Original photo. (B) Photo with indicated porosity used for calculations. (C) MEB picture of sample with broken surface after tensile testing.
The fractographic study of the fracture surfaces of the thermoplastic pultruded part was used as a complementary tool for the composites mechanical characterization, providing an important contribution for the processing optimization of the materials (Barbosa et al., 2019).
From Figure 7, one can observe that the fiber bundles are evenly distributed in the acrylic thermoplastic matrix and only a few areas of porosity are noticed. The calculated porosity based on Figure 7B is 0.42%. Figure 7C shows that the wet-out of fibers by acrylic resin is complete. The strong interfacial adhesion observed along the fibers leads to a cohesive failure. Damage of the matrix near the fibers may be related to the surface treatment or sizing of the fibers as a suitable sizing favors the matrix anchorage to the fibers. This type of failure occurs directly at the fiber/matrix interface and its main morphological feature is the presence of a thin layer of resin around the fibers. In composite materials, it is known that in order to achieve better mechanical properties, a strong fiber/matrix interfacial adhesion is required for improved stress transfer between the resin and the fiber. In the case of this study, a glass fiber with a suitable sizing was chosen. The sizing is a vinyl group with the ability to react chemically during the in-situ polymerization of the acrylic resin in the pultrusion die leading to improved mechanical properties.
Conditions for Thermoforming
The dynamic shear storage modulus (G′) of fully polymerized acrylic resin and pultruded composites counterpart are illustrated in Figure 8.
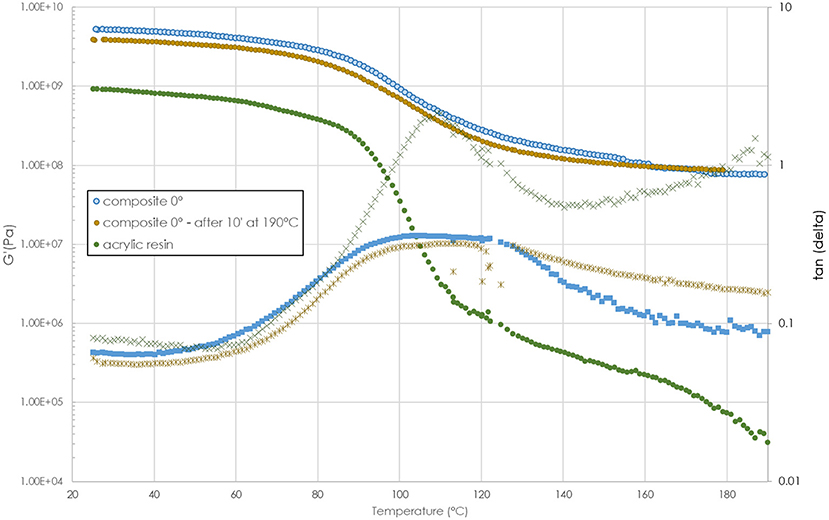
Figure 8. Dynamic shear storage modulus (G′) and tan(delta) measured by DMA of pure resin ELIUM C595 E (green dots) and pultruded profile with ELIUM C595 E in 0° glass fiber direction (blue dots) and 0° glass fiber direction after a post-treatment simulating the thermoforming process at 190°C for 10 min (blue dots).
One can observe that the dynamic shear storage modulus (G′) of the neat resin is lower than those of pultruded glass fiber reinforced acrylic thermoplastic composites. At low temperature, the dynamic shear storage modulus of the resin is 109 Pa and >5 × 109 Pa for the pultruded composites (typical glassy state). When the temperature is near the glass transition temperature Tg (100–120°C), the G′ decreases sharply and finally levels off at 107-108 Pa for the composite and 104 Pa at 190°C for the acrylic resin (typical rubbery state), which demonstrates that the thermoplastic matrix could flow easily during thermoforming unlike thermoset resins.
Since the acrylic resin is an amorphous polymer, the glass transition temperature of pultruded acrylic thermoplastic composites increased only slightly (Table 5).
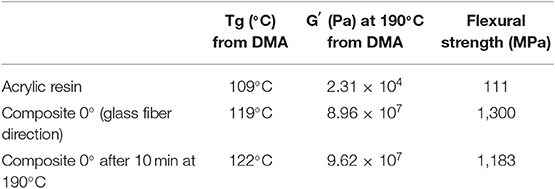
Table 5. Dynamic Mechanical properties (Glass transition temperature, storage modulus at 190°C and flexural strength) of neat resin, pultruded composite part and pultruded composite part after post-treatment (10′ at 190°C).
Glass fiber reinforced acrylic thermoplastic pultruded strips were cut into suitable length and placed in a heated mold for thermoforming (at 190°C, 10 bars) for 10 min, and then was cooled. Properties of post-formed product are shown in Table 5. One can observe that the mechanical and thermal properties of post-formed pultruded parts are the same as those without post-treatment. This demonstrates that the acrylic thermoplastic pultruded products can be post-formed or reshaped by using heat and pressure without degrading the properties. This is one of the major advantages of thermoplastic pultruded profiles as illustrated in Figures 9A,B from a study carried out by the University of Siegen. The acrylic thermoplastic composites pultruded strips of this study have been heated above the glass transition temperature of the polymer so that the material has been formed to a three-dimensional V shape in a mold. Upon cooling, the composite retains this shape without delamination of the composite material.
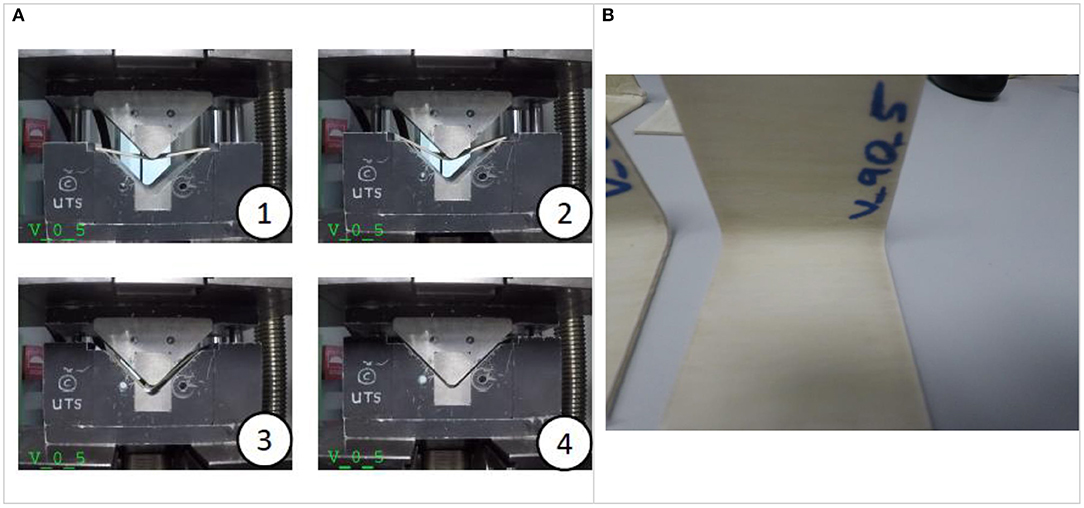
Figure 9. (A) Experimental set-up of thermoforming trials and (B) Thermoformed pultruded ELIUM® UD profile (Univ. Siegen).
This thermoplastic property can also be used to provide specific surface texturing effect or patterns by using embossing/stamping treatment right after the pultrusion die (Figure 10). The surface roughness of the pultruded composite end products can be used to enhance the interfacial properties by promoting mechanical adhesion/strength of the host matrices (i.e., structural adhesives in case of post-bonding, thermoplastic polymers for over or insert molding processes, or concrete for CFRC reinforcement of concrete structures).
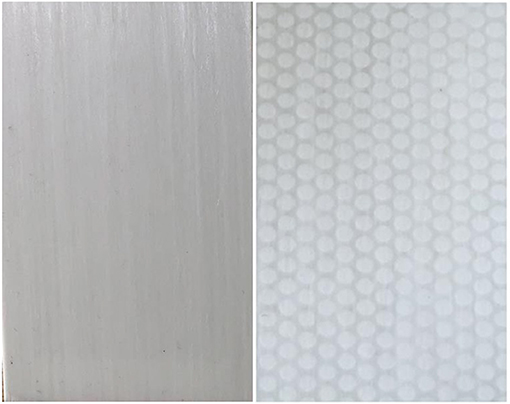
Figure 10. Pultruded ELIUM® sample before (left) and after (right) embossing treatment by calendaring on the pultrusion line after the die.
Conclusions
A novel acrylic liquid thermoplastic resin system was developed for the pultrusion process. Radical in-situ polymerization of the acrylic liquid resin, simulated with the PREDICI software, can take place in the pultrusion die in the presence of continuous fibers at moderate temperature: The pultrusion line does not require any adaption from existing machines and processing cycle time can be adjusted by a careful choice of peroxide initiators, depending on specifications. A further advantage of the pultrusion process is that the reactive nature of the resin gives a better fiber to matrix bond, which significantly improves the end-used mechanical properties.
The status is that the mechanical properties of such a new system are similar or better than standard continuous fiber reinforced thermoset resins and yet thermoplastic matrix composites could offer important advantages in end-used properties, such as fatigue and corrosion resistance, in assembly by welding, post-formability for more complex shapes and recyclability. Indeed, acrylic liquid thermoplastic resin lends itself to recycling. Four recycling techniques could be considered (Cousins et al., 2018), including mechanical grinding, thermoforming, dissolution and chemical depolymerization by pyrolysis under conditions such that monomers can be recovered. Composite parts made from this new resin can be indeed easily ground and then compounded with other thermoplastic resins whose properties can be enhanced by the recycled material. The acrylic thermoplastic resin can also be depolymerized into recycled monomer that can be reused in the production of recycled resin for the manufacturing of new composite parts with exactly the same properties and thus meets the criteria for circular economy.
The recent focus of both polymer chemists and composite engineers on reactive processing of thermoplastic composites not only demonstrates the interest in expanding the application field of thermoplastic composites but also provides the necessary means to accomplish this.
Data Availability Statement
All datasets generated for this study are included in the article/supplementary material.
Author Contributions
AZ, PE, and PG have conceived, designed, performed the experiments along with analyzing the data, and wrote the paper.
Conflict of Interest
The authors declare that the research was conducted in the absence of any commercial or financial relationships that could be construed as a potential conflict of interest.
Acknowledgments
Authors would like to acknowledge the Elium® team, the Institute of Technological Research (IRT-M2P, Metz) for having allowed to carry out pultrusion trials and Dr. Jan Boecking from University of Siegen for conducting the thermoforming trials on pultruded thermoplastic composite profiles.
References
Achilias, D., Kiparissides, C., and Reactions, F. P. (1988). Modeling of diffusion-controlled free-radical polymerization reactions. J. Appl. Polym. Sci. 35, 1303–1323. doi: 10.1002/app.1988.070350516
Achilias, D. S., and Kipasissides, C. (1992). Development of a general mathematical framework for modeling diffusion-controlled free-radical polymerization reactions. Macromolecules 25, 3739–3750. doi: 10.1021/ma00040a021
Achilias, D. S., and Sideridou, I. D. (2004). Kinetics of the benzoyl peroxide/amine initiated free-radical polymerization of dental dimethacrylate monomers: experimental studies and mathematical modeling for TEGDMA and bis-EMA. Macromolecules 37, 4254–4265. doi: 10.1021/ma049803n
Balke, S. T., and Hamielec, A. E. (1973). Bulk polymerization of methyl methacrylate. J. Appl. Polym. Sci. 17, 905–949. doi: 10.1002/app.1973.070170320
Ballard, M. J., Napper, D. H., and Gilbert, R. G. (1984). Kinetics of emulsion polymerization of methyl methacrylate. J. Polym. Sci. Polym. Chem. Ed. 22, 3225–3253. doi: 10.1002/pol.1984.170221141
Barbosa, L. C. M., Bortuluzzi, D. B., and Ancelotti, A. C. (2019). Analysis of fracture toughness in mode II and fractographic study of composites based on Elium® 150 thermoplastic matrix. Compos. B Eng. 175:107082. doi: 10.1016/j.compositesb.2019.107082
Becker, D., François, G., Bozsak, V., and Mitschang, P. (2016). Combining the best of two polymer worlds: thermoformable acrylic resin systems for large-scale production. Kunststoffe 12, 49–51. Available online at: https://www.kunststoffe.de/en/journal/archive/article/thermoformable-acrylic-resin-systems-for-large-scale-production–2028874.html
Beuermann, S., Buback, M., Davis, T. P., Gilbert, R. G., Hutchinson, R. A., Kajiwara, A., et al. (2000). Critically evaluated rate coefficients for free-radical polymerization, 3. Propagation rate coefficients for alkyl methacrylates. Macromol. Chem. Phys. 201, 1355–1364. doi: 10.1002/1521-3935(20000801)201:12<1355::AID-MACP1355>3.0.CO;2-Q
Beuermann, S., Buback, M., Davis, T. P., Gilbert, R. G., Hutchinson, R. A., Olaj, O. F., et al. (1997). Critically evaluated rate coefficients for free-radical polymerization, 2. Propagation rate coefficients for methyl methacrylate. Macromol. Chem. Phys. 198, 1545–1560. doi: 10.1002/macp.1997.021980518
Beuermann, S., Buback, M., Hesse, P., Kuchta, F.-D. D., Lacík, I., and van Herk, A. M. (2007). Critically evaluated rate coefficients for free-radical polymerization part 6: propagation rate coefficient of methacrylic acid in aqueous solution (IUPAC Technical Report). Pure Appl. Chem. 79, 1463–1469. doi: 10.1351/pac200779081463
Beuermann, S., Paquet, D. A., McMinn, J. H., and Hutchinson, R. A. (1996). Determination of free-radical propagation rate coefficients of butyl, 2-ethylhexyl, and dodecyl acrylates by pulsed-laser polymerization. Macromolecules 29, 4206–4215. doi: 10.1021/ma960081c
Cousins, D., Suzuki, Y., Murray, R. E., Samaniuk, J. R., and Stebner, A. P. (2018). Recycling glass fiber thermoplastic composites from wind turbine blades. J. Clean. Prod. 209, 1252–1263. doi: 10.1016/j.jclepro.2018.10.286
Exel Composites (2019). Exel Laminates–Reinforcing Structures LowRes. Available online at: https://www.exelcomposites.com/en-us/english/products/laminates.aspx (accessed June 20, 2019).
Gerard, P., Escale, P., and Zoller, A. (2018). Liquid Composition Comprising Two Initiators, Ist Process of Polymerization, Use and Material of Composition Obtained Following Polymerization of Composition. Patent WO2018/115342.
Guillaneuf, Y., Couturier, J. L., Gigmes, D., Marque, S. R. A., Tordo, P., and Bertin, D. (2008). Synthesis of highly labile SG1-based alkoxyamines under photochemical conditions. J. Org. Chem. 73, 4728–4731. doi: 10.1021/jo800422a
Haehnel, A. P., Stach, M., Chovancová, A., Rueb, J. M., Delaittre, G., Misske, A. M., et al. (2014). (Meth) acrylic monomers with heteroatom-containing ester side chains: a systematic PLP-SEC and polymerization study. Polym. Chem. 5, 862–873. doi: 10.1039/C3PY00948C
Hutchinson, R. A., Beuermann, S., Paquet, D. A., McMinn, J. H., and Jackson, C. (1998). Determination of free-radical propagation rate coefficients for cycloalkyl and functional methacrylates by pulsed-laser polymerization. Macromolecules 31, 1542–1547. doi: 10.1021/ma971307u
Kattner, H., Drawe, P., and Buback, M. (2015). Novel access to propagation rate coefficients of radical polymerization by the SP–PLP–EPR method. Macromol. Chem. Phys. 216, 1737–1745. doi: 10.1002/macp.201500191
Ma, C. C., and Chen, C. H. (1991a). Pultruded fiber reinforced thermoplastic poly(methyl methacrylate) composites. Part I. Correlation of processing parameters for optimizing the process. Polym. Eng. Sci. 31, 1086–1093. doi: 10.1002/pen.760311503
Ma, C. C., and Chen, C. H. (1991b). Pultruded fiber reinforced thermoplastic poly(methyl methacrylate) composites. Part II. Mechanical and thermal properties. Polym. Eng. Sci. 31, 1094–1100. doi: 10.1002/pen.760311504
Ma, C. C., and Chen, C. H. (1992a). Pultruded fiber-reinforced poly(methyl methacrylate) composites. I. Effect of processing parameters on mechanical properties. J. Appl. Poly. Sci. 44, 807–817. doi: 10.1002/app.1992.070440508
Ma, C. C., and Chen, C. H. (1992b). Pultruded fiber-reinforced poly(methyl methacrylate) composites. II. Static and dynamic mechanical properties, environmental effect, and postformability. J. Appl. Poly. Sci. 44, 819–827. doi: 10.1002/app.1992.070440509
Nouryon (2019). Product Search. Available online at: https://polymerchemistry.nouryon.com/products-applications/product-search/ (accessed June 17, 2019).
Russell, G. T., Napper, D. H., and Gilbert, R. G. (1988). Initiator efficiencies in high-conversion bulk polymerizations. Macromolecules 21, 2141–2148. doi: 10.1021/ma00185a045
van Rijswijk, K., and Bersee, H. E. N. (2007). Reactive processing of textile fiber-reinforced thermoplastic composites–an overview. Compos. A Appl. Sci. Manuf. 38, 666–681. doi: 10.1016/j.compositesa.2006.05.007
Yin, M., Davis, T. P., Heuts, J. P. A., and Barner-Kowollik, C. (2003). Propagation and termination rate coefficients in N-vinylcarbazole free radical polymerization obtained via 440 nm pulsed laser and online 1H NMR kinetic experiments. Macromol. Rapid Commun. 24, 408–412. doi: 10.1002/marc.200390066
Zoller, A., Gigmes, D., and Guillaneuf, Y. (2015). Simulation of radical polymerization of methyl mathacrylate at room tempearture using a tertiary amine/BPO initiating system. Polym. Chem. 6, 5719–5727. doi: 10.1039/C5PY00229J
Keywords: CFRC, thermoplastic composite, ELIUM®, pultrusion, acrylic resin, modeling, PREDICI, thermoforming
Citation: Zoller A, Escalé P and Gérard P (2019) Pultrusion of Bendable Continuous Fibers Reinforced Composites With Reactive Acrylic Thermoplastic ELIUM® Resin. Front. Mater. 6:290. doi: 10.3389/fmats.2019.00290
Received: 03 July 2019; Accepted: 30 October 2019;
Published: 03 December 2019.
Edited by:
Alfonso Maffezzoli, University of Salento, ItalyReviewed by:
Luigi Sorrentino, Italian National Research Council, ItalyMylène Lagardère, IMT Lille Douai, France
Copyright © 2019 Zoller, Escalé and Gérard. This is an open-access article distributed under the terms of the Creative Commons Attribution License (CC BY). The use, distribution or reproduction in other forums is permitted, provided the original author(s) and the copyright owner(s) are credited and that the original publication in this journal is cited, in accordance with accepted academic practice. No use, distribution or reproduction is permitted which does not comply with these terms.
*Correspondence: Pierre Gérard, pierre.gerard@arkema.com