Adhesive Characteristic and Mechanism of Ballastless Track Sealant in Hydrolysis Condition
- 1School of Highway, Chang’an University, Xi’an, China
- 2School of Transportation Science & Engineering, Harbin Institute of Technology, Harbin, China
The current evaluation method cannot predict accurately the hydrolysis resistance of sealants applied in ballastless slab track. And the degradation mechanism of sealant in hydrolysis condition has not been researched systemically. In this paper, the hydrolysis resistance of different sealants was researched with the aid of the self-developed direct tensile test method. The atomic force microscope was employed to analyze the micro-adhesion force on the surface of sealants, and thereby the correlation between macro-behavior and the micro-mechanism of sealants during hydrolysis was established. Results showed that the characteristics of the interface between sealants and substrates are reduced after hydrolysis, and that sealants with higher soft-segment content have good resistance to hydrolysis. Reduction of the bonding area after hydrolysis is also an important factor in the reduction of the characteristics of the adhesive interface. The micro-adhesion force of soft segments shows a fluctuating reduction tendency, and that of hard segments reduces more significantly during hydrolysis. The micro-adhesion force has good correlation with the maximum tensile force, but a poor correlation with failure displacement. The maximum tensile force is proved to be an optimal evaluation index in determining the hydrolysis resistance of sealants.
Introduction
The quality of sealant installation in the supporting layer joint of the ballastless track is a key factor in the determination of its service life (Lin and Yan, 2014). Given their proper installation, sealants can protect the rebar and edges of the supporting-layer concrete from atmospheric precipitation. The most widely used sealant material in ballastless track is polyurethane, because its properties can be adjusted across a wide range, and it is moderately priced (Esveld, 2003). Safety considerations obliged discussion of the critical requirements of ballastless track maintenance, most notably the fact that the polyurethane sealant used should serve without failing for no less than 10 years. It was emphasized that this is a big challenge to sealant durability. Especially for sealants installed in cold areas, erosion by water will reduce their adhesion properties with joint wall of supporting layer concrete, and cause their loss of efficiency (Xu, 2013).
The current evaluation method of the hydrolysis resistance of sealants was imported from the tension performance test method at maintained extension in GB/T 13477.10 (GB/T 13477.10, 2017), but the evaluation index and testing parameters correlated poorly with service conditions. In addition, not enough attention was given on the correlation of the mechanism and the adhesive property of the sealant under hydrolysis conditions (Ghosh et al., 2018), with the result that there was a lack of theoretical support for improving the hydrolysis-resistant properties of the targeted sealants. Because little work has been done on the mechanism and evaluation method of ballastless track sealants in hydrolysis condition, experience from related field has to be referenced.
Mitchell developed a crack sealant adhesion test, based on the direct tensile test, to measure maximum load and energy for separation (Al-Qadi and Fini, 2011). Dannenberg (1961) tested the adhesive performance between coating materials and metal plate by injecting alcohol into the interface. Fini modified this test method to assess the bonding properties of pavement sealants (Fini and Al-Qadi, 2011). Also, Fini (2008) conducted a sessile drop test to examine the compatibility of sealants and specific aggregates by testing the contact angles. Shephard employed the 180° peel test to assess the adhesion of sealants to various substrates (Shephard and Wightman, 1996). Shuang tested the rheological behavior of sealants at different temperatures (Shuang et al., 2016). This technique can be used to calculate surface energy. The boiling water test is commonly used to research the adherence of aggregate and asphalt in the asphalt binder field (Pasandín and Pérez, 2014). To summarize the foregoing research experience: A direct-tensile test can simulate closely the crack expansion caused by thermal loading (Al-Qadi et al., 2008).
Additionally, the hydrolysis mechanism of polyurethane sealants has been researched. Most sealants installed in the ballastless track are polyether polyurethane, which has a strong resistance capacity to hydrolysis, due to the weak-polar of the ether group (Zain, 2015). The polyurethane sealants’ erosion by moisture is bi-directional: 1) Water molecules can enter the sealant-microdefect through the open porosity of its surfaces, which leads to the expansion of its volume, followed by shrinkage as the air dries. This repetitive cycle accumulates stress in the sealant body, and this results in the degradation of sealant properties. 2) Water molecules affect the hydrogen bond in the hard phase of the polyurethane, which causes irreversible damage to the sealant (Kau et al., 2010). Various microcosmic examination methods were also introduced to characterize the micro-properties of sealants. Schön mapped the elastic moduli distribution of polyurethane quantitatively, using the atomic force microscope (AFM) (Schön et al., 2011). Jiang characterized the polyurethane modified by acrylate/nano-ZnO (for the dyeing of cotton fabrics) as scanning electron microscope (Jiang et al., 2018). Nabulsi employed infrared radiation to research isocyanate formation during the assembly of rigid polyurethane foam (Nabulsi et al., 2018). Related research experience shows that the AFM method could indicate micro-structure and surface-adhesion quantitatively, which would correlate with the developing rules of the adhesive behaviors of sealants.
This paper aims to report the developing rules of the adhesive behaviors of sealants under hydrolysis conditions. The self-developed method of evaluation of the adhesive properties of sealants is installed in the ballastless slab track. Also, AFM is employed to quantitatively analyze micro-structure and surface adhesion at various degrees of hydrolysis. Last, the correlation of microscopic properties and macro-bonding behaviors of ballastless sealants will be discussed to represent the hydrolysis resistance mechanism.
Materials and Methods
Adhesive Property Test Method
At low temperatures, the sealant adhesive property test is conducted with the self-developed low temperature tensile tester. The low temperature tensile tester could apply a direct tensile load on specimen (seen in Figure 1A) by pulling one end piece (seen in Figure 1B) along with the sliding rail, and the detailed testing procedure can be seen in Xue et al. (2020). The maximum traveling distance is 100 mm, the maximum stretch force is 2 kN, the environmental temperature range is −35 to 60°C, and the loading rate varies from 3 to 200 mm/h. It was proved that the test can meet the evaluation requirements of sealants precisely.
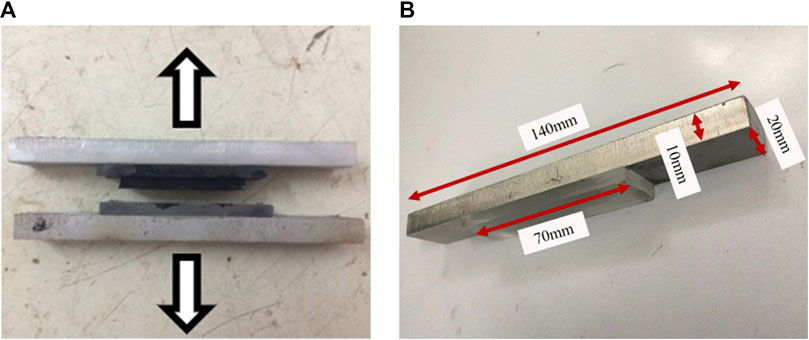
FIGURE 1. Adhesive test specimen of polyurethane sealant and its failure mode: (A) failed specimen; (B) end piece.
Regarding the climatic conditions in the service area of sealants: The selected test temperature is −25°C. It is unrealistic to simulate the real cracking rate in a laboratory test because the joint movement rate of cement concrete slabs (due to temperature drops) is about 5 × 10−5∼8 × 10−5 mm/min. Based on previous research experience, 100 mm/h was the selected standard loading rate (Xue, 2018).
Polyurethane Sealant Hydrolysis
Because the low intensity of the current hydrolysis test method, it is difficult to meet the evaluation requirement of the 10-year service life of the polyurethane sealant. According to the actual working conditions of sealants, the highest surface temperature of the supporting layer can be as high as 60°C in summer. In addition, according to the water immersion test method recommended in the GB/T 1690-2010 “Test Method for Resistance to Liquid of Vulcanized Rubber or Thermoplastic Rubber,” it is reasonable to determine the soaking time to be the integral multiple of 7 days. Therefore, the specimens were soaked at 60°C for 7, 14, 21, 28, and 35 days, respectively.
Adhesion Force
As a polymer material, the relative molecular weight of polyurethane can be as large as 106 (Xue et al., 2020). In addition, molecular chains of polyurethane contain a large number of polar groups, such as the NH and –NCO groups (Jang et al., 2002). Therefore, a Van der Waals interaction force has an important impact on the adhesion properties of polyurethane sealant (Bräuer et al., 2002; Zheng et al., 2006). With the advance in material characterization methods, the Bruker Company (United States) developed a new Peakforce model for the AFM in 2009, and the probe periodically taps the sample and the pN-level interaction force is measured directly by the deflection of the cantilever in Peakforce model. Therefore, the mechanical parameters of the sealant surface, among which adhesion force is an important evaluation index to characterize the Van der Waals force of materials (Tan et al., 2020), was scanned based on the Peakforce mode of AMF after various soaking-time lengths, and the micro-mechanism of polyurethane sealant hydrolysis was studied. The Peakforce mode scanning parameters are shown in Table 1. The AFM specimen can be seen in Figure 2.
Results and Discussion
Four different polyurethane sealants (SE, NI, WQ, SY) commonly used in cold regions of China were selected for the adhesive test, and the sealant properties can be seen in Table 2. The properties of the tested materials meet the requirements of the current specifications (the Provisional Technical Specification for sealant in the Ballastless Track of the High-Speed Railway) for sealants installed in the ballastless slab track. To study the developing rules of sealant adhesive properties under hydrolysis condition, the specimens were hydrolyzed at 60°C for various time lengths, and maximum tensile forces and failure displacements were analyzed and compared.
Maximum Tensile Force
The maximum tensile force is defined as “the peak value of the tensile force measured in the adhesive test.” It is used to characterize the adhesion strength of sealants to substrate. The development of the maximum tensile force of four kinds of sealant, after various hydrolysis time lengths, was as shown in Figure 3.
As shown in Figure 3, the ranking from high to low of the maximum tensile forces for the unhydrolyzed-sealants is NI > SE > WQ > SY. Compared with the R value of sealants, the maximum tensile force has a positive correlation with the R value. This is because sealants with a higher R value have more hard segments and polar groups, which leads to the higher adhesive strength of sealants. The adhesive strength of the four sealants decreased significantly after hydrolysis.
After 35 days of hydrolysis, the residual rate of the maximum tensile force (the ratio of maximum tensile force before and after hydrolysis) of the four sealants (SE, NI, WQ, and SY) was 56.6, 52.8, 63.9, and 63.4%, respectively. Compared with the R value of sealants, the residual rate of the maximum tensile force correlates negatively with the R value, on the whole. It can be concluded that the residual rate of the maximum tensile force of sealants with higher R value is smaller after hydrolysis, although the WQ residual rate of the maximum tensile force is slightly higher than that of SY. But the overall trend is clear. This is because the tested sealant was polyether polyurethane. That is currently the most widely used material. The polarity of the C–O–C group in soft segment is weak (Li et al., 2020), so its hydrolysis-resistance ability is strong. In contrast, the content of polar groups in hard segment is relatively high, so degradation will take place preferentially under hydrolysis.
Comparing the failure interface of the adhesive specimen before and after hydrolysis (seen in Figure 4), it becomes evident that the smaller adhesion area of the polyurethane after hydrolysis is an important reason for the reduction of bonding strength. It can be concluded that the effect of water on polyurethane not only degrades the hard segments, but also enters the interior of sealants along surface defects and connecting voids. This results in sealant expansion (Schollenberger and Stewart, 1971). After hydrolysis, the adhesive properties of sealants reduce under the synergistic effect of hard-segment decrease and material shrinkage.
Failure Displacement
“Failure displacement” is defined as “the displacement where the maximum tensile force occurs.” Micro-crack within the sealant body appears once the load-displacement curve reaches its peak point. That eventually develops to macro-damage. The development of the failure displacement of the four materials under hydrolysis is shown in Figure 5.
As shown in Figure 5, the failure displacements of the tested sealants before hydrolysis are SY, WQ, SE, NI, from high to low. Unlike the maximum tensile index, failure displacement has a positive correlation with the R values of sealants. This is due to the higher content of soft segment in sealants with a smaller R value, which determines the macro-flexibility and deformation propensity of polyurethane (Janardhan et al., 1994). After hydrolysis, the failure displacement of the four sealants decreased significantly. The residual rate of failure displacement (the ratio of failure displacement after a 35-day hydrolysis to initial failure displacement) of NI was the smallest (22.4%) of all. As already noted, the maximum tensile force results indicated that hydrolysis has the severest effect on the adhesive force of sealants with the largest R value. In the light of the failure displacement results, it can be concluded that hydrolysis acts mainly on the hard segment of polyether polyurethane.
In addition, the average coefficients of variation of the maximum tensile force and failure displacement measured during the hydrolysis of the four sealants are 12.5 and 19.6%, respectively. It can be said that the stability of the maximum tensile force index is better than that of the failure displacement. This is because the micro-defects within the sealant body result in stress concentration if sealants are applied as an exterior load. The random spatial distribution characteristics of micro-defects in sealants may cause the poor stability of the failure displacement index (Brünig et al., 2014; Qiang et al., 2018).
Micro Adhesion Force
According to the AFM scanning results, the microphase separation characteristics of polyurethane lead to the various micro-elevations on the surface of sealants. The elevation of the soft segment is lower, and that of the hard segment is higher (2,930). To analyze quantitatively the development characteristics of the adhesion forces of the soft and hard segments during hydrolysis, the AFM scanning results were analyzed mathematically. The elevation of each scanning point was analyzed independently, and recorded as soft segment in the range 0–20% of the total elevation, and as hard segment in the range 80–100%. As the developmental rules of average adhesion force, the soft and hard segment adhesion force of sealant (after various hydrolysis times) were observed by PeakForce mode based on the AFM, as shown in Figure 6.

FIGURE 6. The developmental rules of adhesion force in various domains during hydrolysis: (A) average adhesion force; (B) adhesion force of soft segment; (C) adhesion force of hard segment.
As shown in Figure 6A, the overall micro-adhesion force on the surface of polyurethane tends to decrease, indicating the Van der Waals force decrease during hydrolysis. Figures 6B,C shows that the adhesion force of soft segments has a trend of fluctuating decrease during hydrolysis, and that the hard segments decrease more significantly. It can be concluded that hydrolysis affects mainly the hard segments. In addition, it can be seen in Figure 6B that for the four sealants tested in this study, the adhesion force of all the soft segment increases after 14-days of hydrolysis. Consistently with the failure displacement test results shown in Figure 5 (which was affected mainly by soft segment) the trend of NI and SY to decrease slowed down when hydrolyzed for 14 days. The soft segments of polyether polyurethane have strong hydrolysis resistance. Short-term hydrolysis may improve the crosslinking level of polyurethane, but degradation plays a dominant role after long-term hydrolysis. Under the effect of this competitive mechanism, the developing rules of soft segment fluctuate.
Correlation Between Macro-Micro Properties of Sealants
To research the relationship between the macro- and micro-properties of sealants, a correlation analysis of the residual rate of the average adhesion force in AFM scanning results, and that of maximum tensile force/failure displacement in direct tensile test during hydrolysis, is as shown in Figure 7.
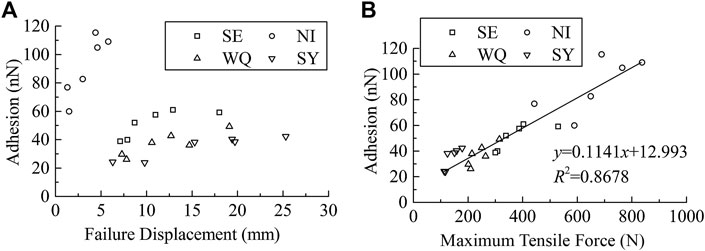
FIGURE 7. Correlation analysis between the macro- and micro-properties of sealants in hydrolysis condition: (A) maximum tensile force—adhesion; (B) failure displacement—adhesion.
It can be seen in Figure 7 that the adhesion force measured by AFM has a good correlation with the maximum tensile force index (of which R2 could be as large as 0.8678 in fitting analysis) but a poor correlation with the failure displacement index. In addition, it can be concluded that intermolecular force is an important micro-mechanism affecting the macro-adhesive properties of the polyurethane sealant. And the maximum tensile force was proved to be an optimal index in evaluating the developing rules of sealants’ adhesive interface during hydrolysis.
Conclusion
The adhesive properties of sealants applied in ballastless slab track were researched using the direct tensile test after hydrolysis. Maximum tensile force and failure displacement were analyzed as the evaluation indices. In addition, the micro-adhesion force on the surface of sealants was tested on the PeakForce mode of the AFM after hydrolyzation. Regression analysis was employed to correlate the macro-bonding behavior and the micro-adhesive mechanism. The main conclusions can be summarized as follows:
(1) For the unhydrolyzed-sealants, the R value has a positive correlation with adhesion strength, and a negative correlation with failure displacement. The adhesive characteristics of sealants reduced after hydrolysis. Hydrolysis acts mainly on the hard segment of polyether polyurethane. Reduction after hydrolysis of the adhesion area between sealants and substrates is also an important cause of the decrease in bonding strength. The stability of maximum tensile force is better than that of failure displacement.
(2) The overall adhesion force, tested by AFM, on the surface of sealants tends to decrease. This indicates that the Van der Waals force decreases during hydrolysis. The adhesion force of soft segments shows a trend of fluctuating decrease during hydrolysis, and that of hard segments, a significant decrease. Short-term hydrolysis may improve the crosslinking level of sealants, because it strengthens the bonding interface between sealants and substrates. But degradation plays the dominant role after long-term hydrolysis.
(3) The adhesion force tested on the AFM has a good correlation with the maximum tensile force, but a poor correlation with failure displacement. Intermolecular force is an important micro-mechanism affecting the macro-adhesive properties of the polyurethane sealant. The maximum tensile force is proved to be an optimal evaluation index when determining the hydrolysis resistance of sealants in the direct tensile test.
Data Availability Statement
All datasets generated for this study are included in the article.
Author Contributions
HX: Methodology. YT and AS: Supervisor.
Funding
This study was supported by National Natural Science Foundation of China (Grant No. 51908055) and Fundamental Research Funds for the Central Universities (Grant No. 300102219103).
Conflict of Interest
The authors declare that the research was conducted in the absence of any commercial or financial relationships that could be construed as a potential conflict of interest.
References
Al-Qadi, I. L., and Fini, E. (2011). Development of a Crack Sealant Adhesion Test (CSADT) specification for hot-poured bituminous sealants. J. Test. Eval. 39 (2), 184–190. doi:10.1520/jte103108
Al-Qadi, I. L., Yang, S. H., Masson, J. F., and McGhee, K. K. (2008). Characterization of low temperature mechanical properties of crack sealants utilizing direct tension test. Rantoul, IL: Illinois Center for Transportation, Publication No. ICT-08-028.
Bräuer, M., Hupfer, B., Nagel, J., and Lehmann, D. (2002). Chemical modification of polyurethane for two-component injection molding. Polym. Eng. Sci. 42 (4), 859–869. doi:10.1002/pen.10997
Brünig, M., Gerke, S., and Hagenbrock, V. (2014). Stress-state-dependence of damage strain rate tensors caused by growth and coalescence of micro-defects. Int. J. Plast. 63 (9), 49–63. doi:10.1016/j.ijplas.2014.04.007
Dannenberg, H. (1961). Measurement of adhesion by a blister method. J. Appl. Polym. Sci. 5 (14), 125–134. doi:10.1002/app.1961.070051401
Fini, E. H. (2008). Adhesion mechanism of bituminous crack sealant to aggregate and laboratory test development. PhD Dissertation. Urbana-Champaign (IL): University of Illinois at Urbana-Champaign.
Fini, E. H., and Al-Qadi, I. L. (2011). Development of a pressurized blister test for interface characterization of aggregate highly polymerized bituminous materials. J. Mater. Civ. Eng. 23 (5), 656–663. doi:10.1061/(asce)mt.1943-5533.0000222
Ghosh, D., Turos, M., Johnson, E., and Marasteanu, M. (2018). Rheological characterization of asphalt binders treated with bio sealants for pavement preservation. Can. J. Civ. Eng. 45 (5), 407–412. doi:10.1139/cjce-2017-0058
Janardhan, R., Ramamurthy, K., and Anand, J. S. (1994). Solution properties of polyurethane. Polym. Test. 13 (5), 397–404. doi:10.1016/0142-9418(94)90049-3
Jang, J. Y., Jhon, Y. K., Cheong, I. W., and Kim, J. H. (2002). Effect of process variables on molecular weight and mechanical properties of water-based polyurethane dispersion. Colloids Surf. A Physicochem. Eng. Asp. 196 (2), 135–143. doi:10.1016/S0927-7757(01)00857-3
Jiang, H., Wang, Y., Quan, H., and Li, W. (2018). Synthesis and characterization of waterborne polyurethane modified by acrylate/nano-ZnO for dyeing of cotton fabrics. Fibers Polym. 19 (4), 703–710. doi:10.1007/s12221-018-7985-6
Kau, C., Huber, L., Hiltner, A., and Baer, E. (2010). Damage evolution in flexible polyurethane foams. J. Appl. Polym. Sci. 44 (12), 2069–2079. doi:10.1002/app.1992.070441202
Li, C., Zheng, J., Zhang, Z., Sha, A., and Li, J. (2020). Morphology-based indices and recommended sampling sizes for using image-based methods to quantify degradations of compacted aggregate materials. Constr. Build. Mater. 230, 116970. doi:10.1016/j.conbuildmat.2019.116970
Lin, H. S., and Yan, H. (2014). “Study on the measures to improve the durability of Chinese CRTSⅠSlab track,” in Transportation research record: journal of the transportation research board. Washington, D.C.: Transportation Research Board of the National Academies.
Nabulsi, A. A., Cozzula, D., Hagen, T., Leitner, W., and Müller, T. E. (2018). Isocyanurate formation during rigid polyurethane foam assembly: a mechanistic study based on in situ IR and NMR spectroscopy. Polym. Chem. 9, 4891–4899.
Pasandín, A. R., and Pérez, A. R. (2014). Effects of the asphalt penetration grade and the mineralogical composition on the asphalt-aggregate bond. Petrol. Sci. Technol. 32 (22), 2730–2737.
Qiang, T., Yan, G., Bai, L., Li, X., Zou, L., Rosta, L., et al. (2018). Phase mixing and separation in polyester polyurethane studied by small-angle scattering: a polydisperse hard sphere model analysis. Polymer 147, 1–7. doi:10.1016/j.polymer.2018.05.069
Schollenberger, C. S., and Stewart, F. D. (1971). Thermoplastic polyurethane hydrolysis stability. J. Elastomers Plast. 3 (1), 28–56. doi:10.1177/009524437100300103
Schön, P., Bagdi, K., Molnár, K., Markus, P., Pukánszky, B., and Julius Vancso, G. (2011). Quantitative mapping of elastic moduli at the nanoscale in phase separated polyurethanes by AFM. Eur. Polym. J. 47 (4), 692–698. doi:10.1016/j.eurpolymj.2010.09.029
Shephard, N. E., and Wightman, J. P. (1996). “An analysis of the 180° peel test for measuring sealant adhesion.” in Science and technology of building seals. Sealants, glazing and weatherproofing: fifth volume, ASTM STP 1271. Editor M. A. Lacasse (West Conshohocken, PA: American Society for Testing and Materials).
Shuang, L., Mo, L., Kai, W., Xie, Y., and Woldekidan, M. F. (2016). Preparation, microstructure and rheological properties of asphalt sealants for bridge expansion joints. Construct. Build. Mater. 105, 1–13. doi:10.1016/j.conbuildmat.2015.12.017
Tan, X., Zhang, J., Guo, D., Sun, G., Zhou, Y., and Zhang, W. (2020). Preparation and repeated repairability evaluation of sunflower oil-type microencapsulated filling materials, J. Nanosci. Nanotechnol. 20 (3), 1554–1566. doi:10.1166/jnn.2020.17338
Xu, J. J. (2013). Optimum design for expansion joint anti-seepage slab ballastless track on subgrade of frigid district high-speed Railway. Railway Standard Design 7, 19–21 [in Chinese, with English summary]
Xue, H. X. (2018). Decaying rules and mechanism of the adhesive properties of ballastless slab track sealants at low temperature considering environmental factors. PhD dissertation. Harbin (China): Harbin Institute of Technology [in Chinese, with English summary].
Xue, H., Tan, Y., and Sha, A. (2020). Test method on adhesive property of joint sealant in supporting layer of ballastless slab track. J. Mater. Civ. Eng. 32 (10). doi:10.1061/(ASCE)MT.1943-5533.0003163.
Zain, N. M. (2015). Durability of green polyurethane adhesive bonded aluminum alloy in dry and hydrothermal ageing conditions. J. Appl. Polym. Sci. 131 (23). doi:10.1002/app.41151
Keywords: ballastless track sealant, hydrolysis resistance, microscopic characteristic, direct tensile test, multi-scale analysis
Citation: Xue H, Tan Y and Sha A (2020) Adhesive Characteristic and Mechanism of Ballastless Track Sealant in Hydrolysis Condition. Front. Mater. 7:535483. doi:10.3389/fmats.2020.535483
Received: 04 March 2020; Accepted: 31 August 2020;
Published: 25 September 2020.
Edited by:
Hazizan Md. Akil, University of Science Malaysia, MalaysiaReviewed by:
Rafael Guntzel Arenhart, Federal University of Santa Catarina, BrazilPengfei Liu, RWTH Aachen University, Germany
Copyright © 2020 Xue, Tan and Sha. This is an open-access article distributed under the terms of the Creative Commons Attribution License (CC BY). The use, distribution or reproduction in other forums is permitted, provided the original author(s) and the copyright owner(s) are credited and that the original publication in this journal is cited, in accordance with accepted academic practice. No use, distribution or reproduction is permitted which does not comply with these terms.
*Correspondence: Yiqiu Tan, yiqiutan@163.com