Aging of Polyphenylene Sulfide-Glass Composite and Polysulfone in Highly Oxidative and Strong Alkaline Environments
- 1Faculty of Materials Science and Engineering, Delft University of Technology, Delft, Netherlands
- 2Faculty of Industrial Design Engineering, Delft University of Technology, Delft, Netherlands
- 3Zero Emission Fuels B.V., Delft, Netherlands
Alkaline water electrolysis becomes increasingly important for the supply of renewable energy, and of raw material for the chemical industry. An attractive choice for the encapsulation of the electrolyte cell is an (advanced) engineering polymer. The objective of this paper is to find a suitable one that can withstand for many years: 30 wt% KOH solution and pure oxygen at a high pressure of 50 bar and at an elevated temperature of 90°C. Using CES EduPack, 12 possible thermoplastic polymers were selected, of which polyphenylene sulfide (PPS) and polysulfone (PSU) were further investigated using accelerated testing. The polymers have been exposed to three KOH concentrations (15, 30 and 45 wt%), two oxygen pressures (pure O2 at 5 bar and air with pO2 = 20%), and three temperatures (90°C, 120°C, and 170°C). Extensive characterization of the exposed samples has been carried out using various techniques, including weight, tensile, DMA, and creep-recovery measurements, as well as DSC, FTIR, XRD and SEM. After 12 weeks of aging, glass fiber reinforced PPS failed in a strong alkaline solution at high temperatures, due to the dissolution of the glass fibers. The PPS matrix itself and PSU turned out to be resistant to thermo-oxidative and chemical degradation under the conditions tested. Only marginal changes in mechanical, visco-elastic and thermal behavior were observed, which can be ascribed to physical rather than chemical aging. In view of the brittle nature of PPS, it could be concluded that PSU is the most promising candidate for the long-term application in alkaline electrolysis. Extrapolating the data using time-temperature superposition, it is predicted that PSU will retain its integrity and mechanical properties for a period of 20 years of operation.
1. Introduction
The use of hydrogen will become increasingly important. Hydrogen is an energy carrier, but also an important constituent for the production of carbon based fuels. Currently, the cheapest and most common way of producing hydrogen is via steam reforming of natural gas (Smolinka, 2014). This process requires fossil fuels and emits carbon dioxide, which is harmful for the environment. Therefore, cleaner methods of extracting hydrogen gas are being pursued such as different approaches to water electrolysis.
Hydrogen production by electrolytic water splitting is well known. Already, by 1902 more than 400 electrolyzers were in operation, and by 1948, the first pressurized industrial electrolyzer was built (Kreuter and Hofmann, 1998). Yet, in 2014, only 1% of the global hydrogen production was produced by water electrolysis (Smolinka, 2014). It is therefore important to study methods that make water electrolysis more cost effective (Schmidt et al., 2017). Small scale alkaline electrolysis units powered by solar energy can operate fully off grid and may provide a sustainable solution for local hydrogen production. For the economic success of such mini-factories the durability and ease of manufacturing are of prime importance.
The material choice of the container of an alkaline electrolyzer has been discussed rarely in the literature. The composition of the electrodes or the hydrophilic membrane are much more dealt with, since these affect the efficiency of the electrolyzer. However, the encapsulation of the electrolyzer is important for the design of a large hydrogen production system. The capital cost of alkaline electrolysis rather than the efficiency or the price of the electricity puts a major limitation on widespread hydrogen production (Marini et al., 2012).
So far, the materials chosen most for the housing of advanced water electrolysis cells are monel and polyether ether ketone (PEEK). Monel is used in cells working under extreme conditions up to 400°C and 90 bar (Ganley, 2009). Ju et al. (2018) designed an alkaline electrolyzer operating at 30 bar and 80°C. For that electrolyzer, a single cell with monopolar configuration, PEEK is applied, since it is chemically stable against alkaline solutions, shows excellent mechanical resistance to high temperature and high pressure and is an electrical insulator. Allebrod et al. (2013) developed an electrolyzer with a polytetrafluoroethylene (PTFE) liner and an inconel autoclave, which can withstand high temperatures (up to 250°C), pressures (up to 42 bar) and a hostile caustic environment. However, monel, inconel and PEEK are expensive.
Zero Emissions Fuel (Netherlands), a contributor to this investigation, ventures on the development of solar powered hydrogen production using stacks of polymeric mini-cells for alkaline water electrolysis. Figure 1A shows a 3D-view of the design of these mini-cells, which can be cheaply mass produced. The cells can be easily stacked together to form a mini-plant for off the grid H2 production, see Figure 1B.
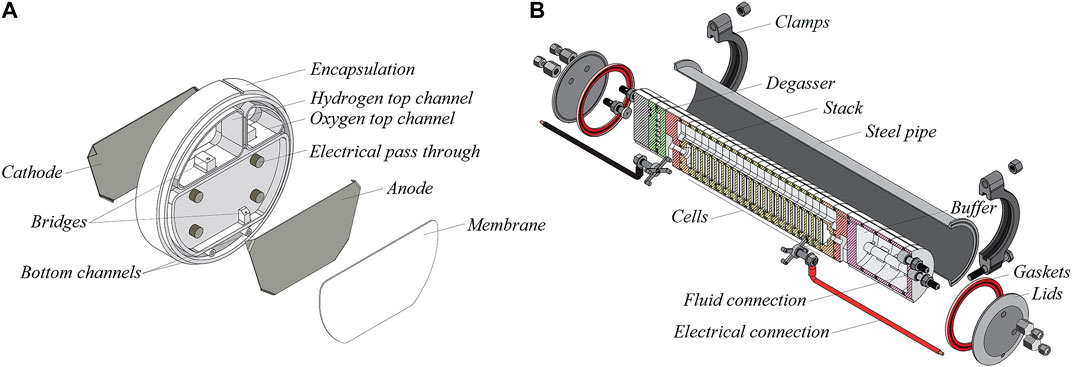
FIGURE 1. (A) Exploded view of mini-cell for bipolar zero gap alkaline electrolysis. Apart from the electrodes and the Zirfon-Perl membrane, it will be made of an injection moulded polymer that will withstand the harsh conditions of 50 bar O2 and 30 wt% KOH at a temperature of 90°C. The polymer encapsulation functions not only as housing, but also contains two compartments, where the H2 and O2 gases are collected (courtesy ZEF, Netherlands). (B) Module of 18 photo-voltaic powered mini-cells, which embody a solar powered mini-plant for H2 production (courtesy, ZEF, Netherlands). It will be integrated with a methanol synthesis reactor. The 50 bar pressure in the mini-cells eliminates the need of a compressor. This makes the system more efficient. The overall efficiency is raised further by the elevated temperature of 90°C in the cells.
The diffusion of electrolytes through a polymer drives the degradation and therefore plays an important role in its lifetime (Zaikov et al. (1988), Iordanskii et al. (1979), Moiseev et al. (1976)). For more background on the degradation and failure analysis of polymers, we refer to Brown and Greenwood (2002), Celina (2013), Hamid (2000), Lampman et al. (2003), Reich and Stivala (1971), Verdu (2012), Wright (2001), while for more information on the alkaline electrolysis of water, we refer to Ursua et al. (2011), Guillet and Millet (2015), Schalenbach et al. (2018), David et al. (2019).
The main aim of this paper is to assess the use of rather cheap polymers for the durable housing of an alkaline electrolyzer. A material selection procedure, outlined in Section 2, was carried out, from which two high-tech polymers were chosen for an appraisal. The accelerated aging methods are described in Section 3, followed by the results and discussion in Sections 4 and 5, respectively.
2. Material Selection
The material for the encapsulation has to meet certain criteria, such as being non-conductive, having a lifetime in the order of that of an electrolyzer which is 6–10 years (Schmidt et al., 2017), and being suitable for cost-effective mass production using injection molding. Furthermore, the polymer should resist strong alkalis (pH > 10) and endure a high pressure of 50 bar and an operation temperature of at least 90°C for an optimal performance of the electrolyzer (Kovač et al., 2019; Phillips et al., 2017).
Using these criteria and the CES EduPack material database, about 12 potentially suitable polymers were singled out (Granta Design, 2018). From this selection two promising high performance thermoplastics, both much cheaper than PEEK (85 €/kg), were chosen, which are polyphenylene sulphide (PPS, 7.50 €/kg) and polysulfone (PSU, a.k.a. PSF, 10.40 €/kg). Their chemical structures are depicted in Table 1. These high strength aromatic polymers seem in particular attractive, because of their long-term use in Zirfon-Perl membranes (Afga, Belgium) for alkaline electrolysis. This indicates that both polymers remain stable in an alkaline environment. The question remains, whether PPS and PSU will withstand the highly alkaline conditions in the mini-cells for many years at 90°C under an oxygen pressure of 50 bar. PPS as such is too brittle for this load bearing application, it has to be reinforced with strong fibers, so we opted for PPS-40%gf (5.60 €/kg). Other salient properties of PPS and PSU are recapped in Sections 2.1 and 2.2.
For more details about the composition of the porous Zirfon-Perl membranes we refer to: Afga data sheet (2020), Vermeiren et al. (2009), Xu et al. (2014), Guillet and Millet (2015); Lee et al. (2020). The stability against KOH of general purpose PPS and PSU membranes is, in spite of their large surface area, also pointed out by Wang et al. (2017).
2.1. Polyphenylene Sulfide Reinforced With 40% Glass Fibers (PPS-40%gf)
Polyphenylene sulphide is a sulphur-containing aromatic polymer with a good thermal stability up to 200°C. It is dimensionally stable, so that complex parts can be moulded to within tight tolerances. Due to its chemical stability, it is not prone to a wide range of solvents and corrosive media even at elevated temperatures. Moreover, its aromatic rings make the polymer resistant against high temperatures and give it excellent hydrolytic stability (Kemmish, 2011; McKeen, 2016).
PPS is seldom used in its pure form. For high strength purposes, it is always mixed with fibers, such as glass or carbon fibers, or minerals and fillers in order to overcome its inherent brittleness (McKeen, 2016). The most general type of PPS is reinforced with 40% glass fibers. Admittedly, it is known that glass performs poorly in highly caustic environments. This may affect the durability of glass-reinforced PPS in an alkaline electrolyzer. Nonetheless, since both CES EduPack/Materials Selector and the manufacturer state that PPS-40%gf is resistant against alkaline solutions (Granta Design, 2018; Ticona, 1999), the PPS-40%gf has been included in the study. The more so, because Ellis and Smith (2012) also claim in their polymers database that PPS-40%gf is resistant to strong alkalis.
A typical application of PPS under extreme conditions is as filters in coal-fired power-plants, for which, growing interest has been shown in China leading to different PPS degradation studies (Cai and Hu, 2015; Wang et al., 2011). When heated in oxygen or air to temperatures above 250°C, PPS will undergo oxidative cross-linking (Lee et al., 2013; McKeen, 2016; Yamashita et al., 1993a). This leads to thermoset-like properties, but also to a more brittle behavior. The oxidation of PPS involves the creation of sulfuryl groups (−SO2−), because the low bond energy of the C-S bond causes easy oxidation (Cai and Hu, 2015; Xing et al., 2018).
2.2. Polysulfone
Polysulfone is a rigid, amorphous high temperature thermoplastic. It has a high thermal stability, good ductility, high toughness and strength and is chemically stable, making it useful for demanding engineering applications. It also withstands electrolytic solutions with a pH from 2 to 13, and oxidizing agents (McKeen, 2016). The polymer is transparent in its natural state by virtue of its fully amorphous nature.
PSU is often used for membranes in the food industry or as a reverse osmosis membrane, because of its excellent resistance to hydrolysis by hot water/steam and its excellent resistance to acids and bases. It is also used as gas separation membrane for oxygen enrichment (Chong et al., 2016), which implies good stability against oxidation.
Gesner and Kelleher (1968) found that PSU is essentially inert to both air and oxygen up to 140°C. After 8,000 h of aging at 125°C, the infrared spectrum did not differ from that of the original polymer and the weight loss was less than 0.2% (Gesner and Kelleher, 1968). When aged for 6 months at 110°C, the tensile break strength merely drops less than 10% and the elongation by less than 5% (Gesner and Kelleher, 1968). Yamashita et al. (1993b) found that below the glass temperature of PSU, which is between 186°C and 192°C, main chain scission and cross-linking occur simultaneously, whereas cross-linking predominates above the Tg during photo-degradation. Cross-linking in PSU arises due to similar mechanisms as mentioned above for PPS (Yamashita et al., 1993b).
3. Methods
The aim is to gain a better understanding of the evolution of the (mechanical and thermal) properties of PPS-40%gf and PSU when exposed to a highly oxidizing atmosphere or a strong alkaline solution at elevated temperatures. From the experimental data, extrapolations will be made from which the potential lifetime of the polymer can be estimated.
3.1. Sample Shapes and Materials
For PPS a commercially available 40% glass-reinforced grade (Fortron 1140L4) was used, while for PSU Udel P-1700 BK 937 was chosen. The aging experiments were performed on injection moulded dog-bone shaped samples, see Figure 2.
3.2. Aging Conditions
Table 2 gives an overview of the aging conditions. The aging experiments were conducted over a period of 4–12 weeks. At five or six instances, samples were removed from the set-up, cooled, and characterized with different techniques.
3.3. Aging Equipment
The samples exposed to air were aged in open beakers at 90°C, 120°C or 170°C in an air circulating oven. The KOH samples were contained in HDPE screw lid containers to prevent the evaporation of liquid and were also stored in the oven. The KOH solution was regularly refreshed to maintain a consistent KOH concentration.
The density of PSU is lower than that of a KOH-solution for 30 and 45 wt% KOH. This means that the PSU samples tend to float in these solutions. The containers were therefore chosen small enough for all samples to be packed vertically. So they were fully immersed, except for the upper few millimetres.
3.3.1. High Pressure Oxygen Aging Set-up
No high pressure facilities were available at our laboratory. The maximum O2 pressure was therefore limited to 5 bar for safety reasons. Since the kinetics of chemical degradation is ruled by the pressure and the temperature, we could in part compensate for the necessity of a lower pressure by exposing the samples to temperatures well above 90°C. The self-made set-up is shown in Figure 3.
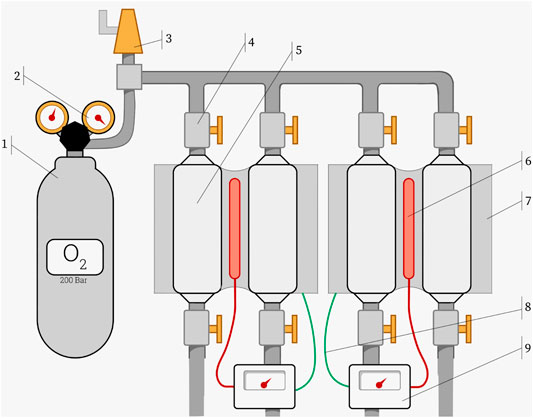
FIGURE 3. Schematic of the oxygen set-up containing the following parts: 1) 5L 200 bar pure oxygen flask, 2) pressure regulator, 3) pressure relief valve set at 8 bar, 4) oxygen certified Swagelok needle valve, 5) 18 mm Swagelok tube containing the samples, 6) heating element, 7) aluminum block for heating the tubes, 8) thermocouple, and 9) SB1 PID temperature regulator from RKC INSTRUMENT Inc. Heating paste has been applied between the heating element and aluminum block and between the 18 mm tubes and the aluminum block.
3.4. Equipment and Measurement Procedures
Mechanical tests were done on a Zwick Z010 tensile tester with a 500 N load-cell and 0.5 mm/min test speed. The ultimate tensile strengths (UTS) and the rupture strain are taken as the stress and strain values just before rupture. The Young’s modulus follows from the slope between 0.2 and 0.6% strain, and the toughness from the integral of the stress-strain curve until rupture.
A TA-Instruments DMA Q800 was used to measure the dynamic mechanical properties in tensile mode at frequencies of 1, 3.2, 10, 31.6 and 60 Hz during a temperature scan from RT to 290°C at 2°C/min (displacement amplitude 15 μm). The same instrument was employed for the creep-recovery experiments. The basics of these measurements is outlined in Figure 4. They were performed at 90°C, 110°C, 130°C, and 150°C with a creep stress of 5 MPa. From the short-term data acquired at these four temperatures, the long-term creep will be estimated in Section 5.4. The 1 h creep tests were preceded by 15 min equilibration time in order to erase possible previous stresses.
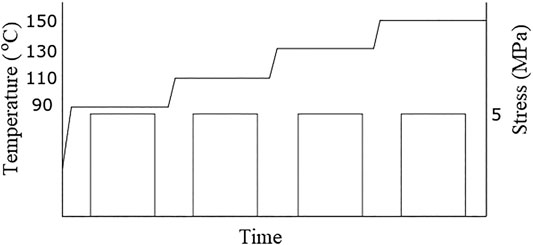
FIGURE 4. Sequence of loadings and unloadings in the creep-recovery test. The schedule starts with a hold at 90°C for 15 min., a creep measurement at 5 MPa for 60 min., followed by a temperature increase, equilibration and recovery of 15 min., then again a creep test at 5 MPa for 60 min and so on.
In addition, DSC experiments were performed on the Perkin Elmer DSC 7 from RT to 400°C at 10°C/min. ATR-FTIR measurements were carried out on the ThermoFisher Nicolet iS50, 16 scans were recorded at an optical resolution of 4 cm−1. A Bruker D8 Advance diffractometer with Bragg-Brentano geometry and a Lynxeye position sensitive detector were used for the XRD measurements. Finally, SEM was performed on a Jeol JSM-IT100.
4. Results
4.1. Polyphenylene Sulfide-40%gf Exposed to Oxygen and to KOH
Aging of PPS-40%gf at 90°C in air or oxygen did not alter its mechanical properties significantly for aging times up to 12 weeks (84 days), see Figure 5A. The strain to rupture varies, but the trend is not fully consistent. DMA measurements showed that air and oxygen aging above the Tg of 95°C, at 120°C, resulted in a 10–15°C increase in the glass transition, indicating a mild form of oxidative cross-linking.
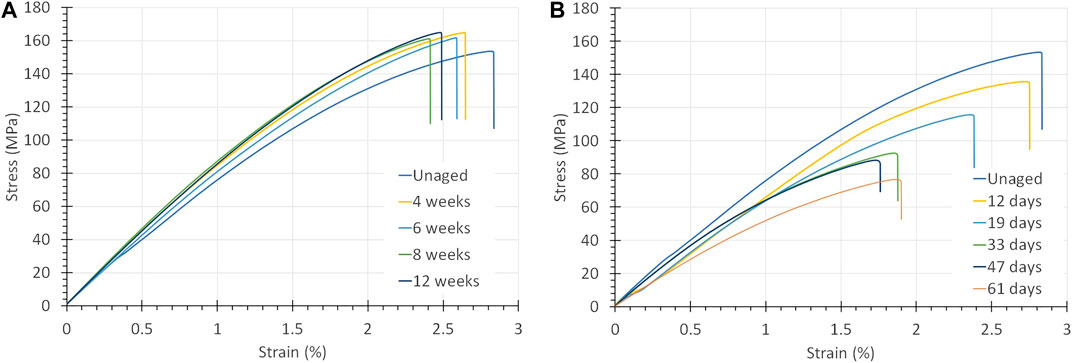
FIGURE 5. (A) Stress-strain curves of PPS-40%gf exposed to O2 at 5 bar and 90°C. It is mainly the strain to rupture that changes. (B) Stress-strain curves of PPS-40%gf exposed to a 30 wt% KOH solution at 90°C. The mechanical properties are seen to deteriorate dramatically.
PPS-40%gf exposed to alkaline solutions behaves, however, completely differently. Figure 5B shows the stress-strain curves obtained from PPS-40%gf aged in a 30 wt% KOH solution at 90°C exposed for different periods. The graph displays a large decrease in the UTS from 153.5 down to 79.6 MPa. Furthermore, the strain at rupture, the Young’s modulus and the toughness can be seen to drop significantly: from 2.7 to 1.9 for the strain to rupture from 7.5 to 5.9 GPa for the modulus and from 2.6 down to 1.3 MPa, for the toughness. Similar vast drops in mechanical properties were found for PPS-40%gf exposed to 15 and 45 wt% KOH.
The strong decrease in mechanical properties of PPS-40%gf when exposed to KOH is substantiated by the DMA results. As shown in Figure 6B the storage modulus decreased from about 12 to below 8 GPa after 61 days of exposure. Both the storage modulus of the glass and the rubbery region decreased by about a third, similar to the lowering found in the Young’s modulus. By contrast, the position of the peaks of the loss modulus, which correspond to the glass transition, did not change much.
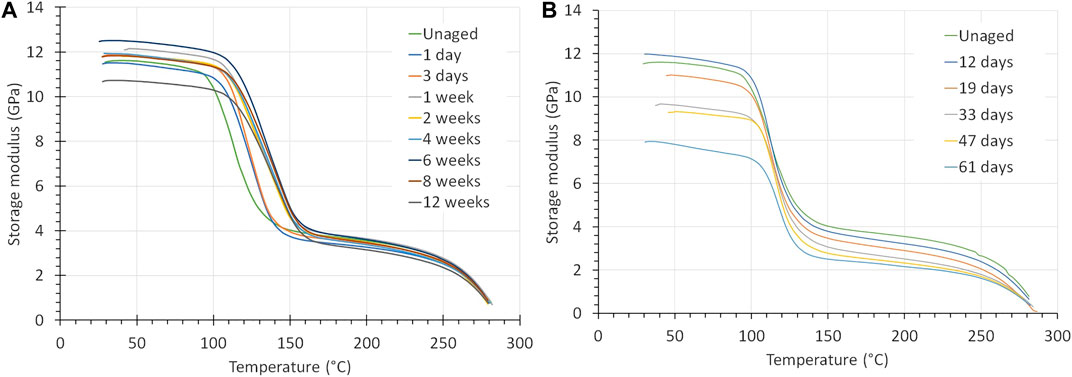
FIGURE 6. The 1 Hz modulus curves of PPS-40%gf exposed to (A) 5 bar O2 at 120°C and (B) a 30 wt% KOH solution at 90°C, which exhibits a big drop in the modulus below Tg.
SEM images taken of the fracture surfaces after tensile testing, are given in Figure 7. The left image presents the unaged sample, and that at the right after 61 days in a 30 wt% KOH solution at 90°C. The images reveal a drastic increase in damage to the glass fibers. After 61 days, most of the fibers near the surface are dissolved and replaced by precipitates containing potassium, as was confirmed by energy-dispersive X-ray (EDS) analysis and XRD.
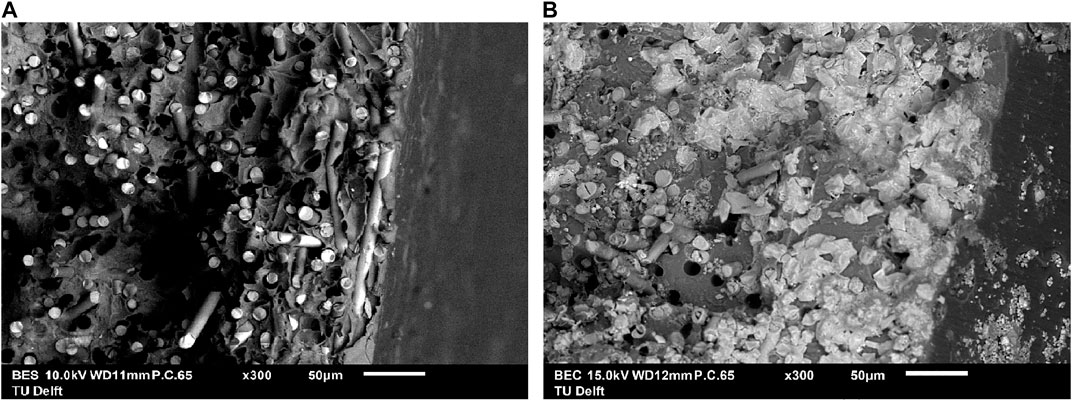
FIGURE 7. SEM images at ×300 magnification of the fracture surface of (A) unaged PPS-40%gf, and (B) PPS-40%gf exposed to 30 wt% KOH at 90°C for 61 days. The glass fibers suffered severely.
The results of the degradation tests for PPS-40%gf are summarized in Table 3. From the mechanical tests and SEM images it is bore out that the dissolution of the glass fibers is responsible for the rapid failure of PPS-40%gf when exposed to a hot alkaline environment.
4.2. Polysulfone Exposed to Oxygen
The results for PSU are summed up in Table 4. Figure 8 show the stress-strain curves of PSU exposed O2 at 90°C and to air at 170°C, from which the effects on the Young’s modulus, UTS, strain at UTS and toughness become evident. PSU is clearly more ductile than PPS-40%gf. It has a higher strain at UTS (5.5% compared to 2.7% for PPS-40%gf) and does not break in a brittle way. Instead PSU deforms plastically through necking. The tensile test has been stopped just before necking started. As illustrated in Figure 8B, the UTS of PSU increased from 62 to above 80 MPa when aged in air near its Tg, at 170°C. This increase, in combination with a decrease in toughness may be interpreted as an oxidative cross-linking effect. Although, this may also be due to physical aging, which leads to a lower molecular mobility, and which proceeds rapidly, close to Tg.
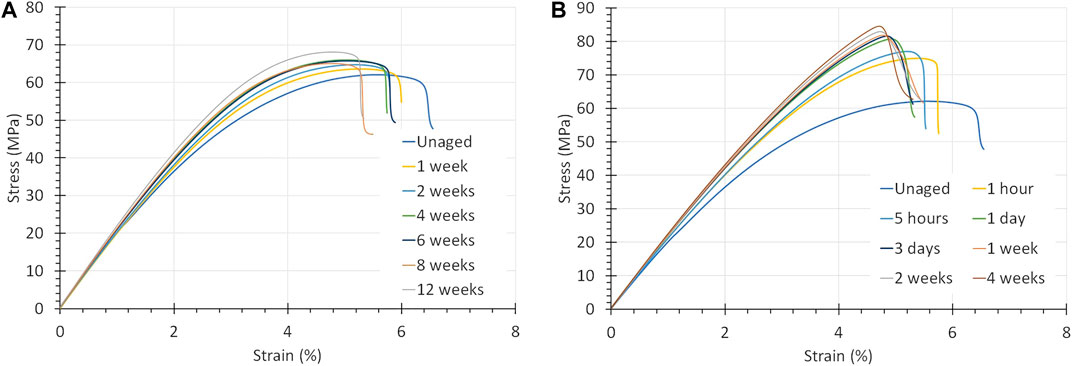
FIGURE 8. (A) Stress-strain curves of PSU exposed to pure O2 at 5 bar and 90°C. The strain to rupture is lowered to a new level, while the strength and E-modulus are enhanced. (B) Stress-strain curves of PSU exposed to air at 170°C, which is close to its Tg of 185°C. The strain to rupture becomes less, whereas the strength and E-modulus increase.
Figure 10A shows the creep compliance of unaged PSU compared to PSU aged in pure oxygen at 5 bar and 120°C for 2 weeks and for 12 weeks. The compliance reduces as a function of exposure time, meaning that the polymer becomes stiffer.
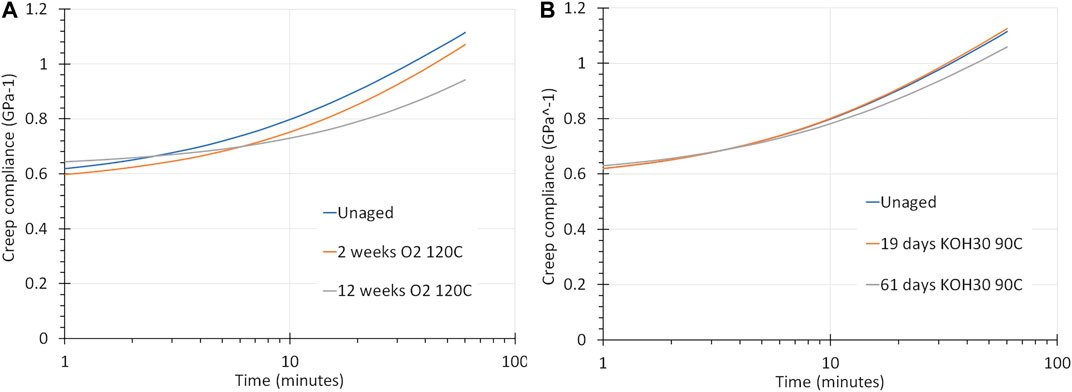
FIGURE 10. (A) Creep compliance of PSU and PSU aged in oxygen at 5 bar and 120°C for 2 and 12 weeks. The curves are given for a creep-recovery measurement at 150°C at a stress of 5 MPa, for 1 h. PSU becomes to some degree less compliant. (B) Creep of PSU and PSU aged in a 30 wt% KOH solution at 90°C for 19 and 61 days, measured by creep-recovery at 150°C at a stress of 5 MPa for 1 h. The compliance is less affected than after an O2 exposure.
Figure 9 shows the SEM-results. The image of PSU exposed to O2 5 bar at 120°C for 8 weeks in B) looks very much like that of unaged PSU in A).
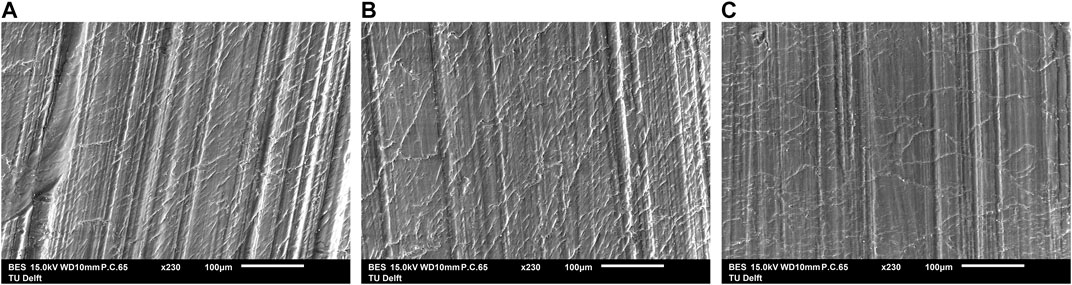
FIGURE 9. SEM images of the surface of PSU: (A) unaged, (B) exposed to O2 5 bar 120°C for 8 weeks and (C) exposed to 30 wt% KOH at 90°C for 61 days. The images look very much alike.
The FTIR results (see Supplementary Data Sheet) show no difference between untreated and treated samples, which suggest that it is unlikely that oxygen has reacted with the PSU chains, since this would be visible in changes in the relative height or appearance of new peaks in the FTIR spectra.
XRD and weight measurements also did not indicate any changes.
4.3. Polysulfone Exposed to KOH
Figure 11 shows the stress-strain curve of PSU exposed to 30 wt% KOH at 90°C. The stress-strain curves look totally different from the PPS-40%gf curves. Instead of poorer mechanical properties, PSU acquired a higher ultimate tensile strength over time (from 62 to 67 MPa), along with a decrease in strain at UTS (from 5.5 to 4.7) and a decrease in toughness (from 2.3 to 2 MPa). Within the error bounds, no distinct change in the Young’s modulus was observed.
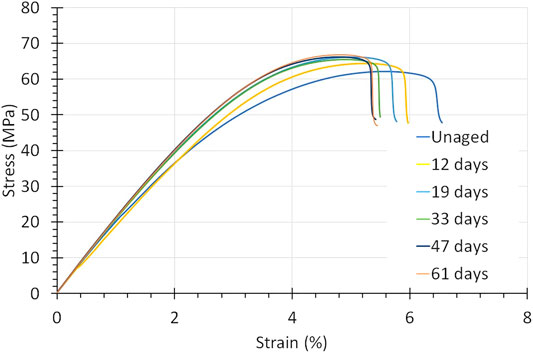
FIGURE 11. Stress-strain curves of PSU exposed to 45 wt% KOH at 90°C. In particular, the strain to rupture shrinks, but this levels off with aging time.
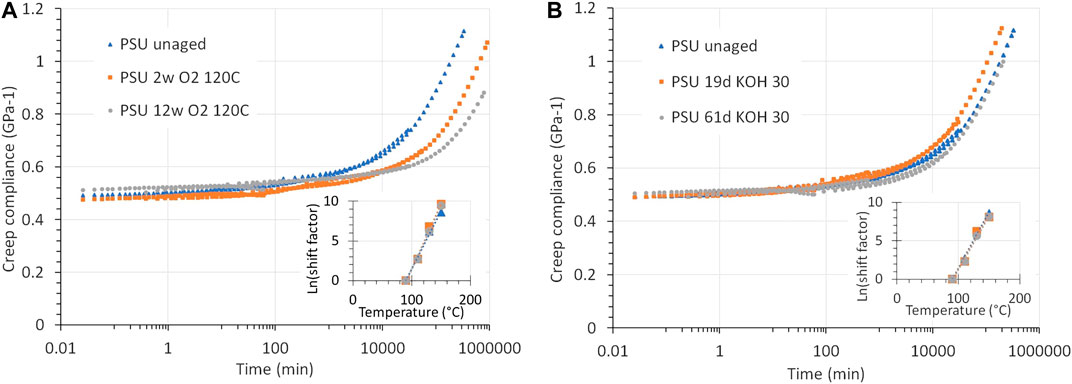
FIGURE 12. Predicted long-term creep for PSU aged in (A) O2 (5 bar, 120°C) and (B) KOH (30 wt%, 90°C). The insets show the corresponding Arrhenius shift plots. The prediction was achieved by composing master curves with time-temperature superposition. Exposure to O2 reduces the creep, while for KOH the predicted creep closely matches that of unaged PSU.
The effect of aging in KOH on the creep compliance is presented in Figure 10B. It turns out to be marginal.
There is in Figure 9C no distinction, except for the presence of KOH particles, between the SEM image of PSU exposed to a 30 wt% KOH solution at 90°C for 61 days and pristine PSU in a).
5. Discussion and Extrapolation of Results
5.1. Polyphenylene Sulfide-40%gf Exposed to Oxygen and to KOH
The outcome of PPS-40%gf exposed to KOH implies that PPS-40%gf is unfit for use in an alkaline electrolyzer. All the testing and the SEM images show that the glass fibers degraded too strongly.
5.2. Polysulfone Exposed to Oxygen
The UTS and Young’s modulus increase regardless of oxygen partial pressure, they seem to depend primarily on the aging temperature, as Figure 8 demonstrated. This complies with the effects expected for oxygen induced cross-linking. Although, the increases level off after some time. Actually, the latter is more in line with physical aging, whereby the free volume declines less and less, which forces the kinetics to slow down.
The results of Figures 10B, 11 elucidate that PSU has not undergone any serious degradation or hydrolysis due to the presence of water and KOH. The changes in properties are relatively small. The polymer becomes slightly stronger and stiffer. This can be attributed to physical aging caused by ongoing structural rearrangements that lower the free volume and thus the molecular mobility. Since the samples have been exposed to 90°C, which is well below its Tg only minor effects on the relaxation behavior are observed. They are similar to those of PSU exposed to air or pure oxygen at 90°C.
The aging experiments validate that PSU is a very stable polymer. This is due to its very high Tg of around 185°C, meaning that the polymer chains will show very low mobility at an operating temperature of 90°C. This immobility will block the ingress of other molecules.
5.3. Predicting the Creep Compliance Over 20 years (Polysulfone)
Visco-elastic effects like creep and stress relaxation in polymers are caused by the slow sliding of the long molecular chains under loading. At elevated temperatures these effects are speeded up, which led early researchers to formulate time-temperature superposition: all visco-elastic properties can be mapped on to a single curve (the master curve) when scaled to a reduced time scale:
In the short term creep-recovery measurement, data were collected at four temperatures: 90°C, 110°C, 130°C and 150°C. These can be lined up into one master curve at 90°C, which extends to much longer times. The horizontal shifting of the higher temperature curves to longer times has been performed for unaged and aged PSU. This resulted in the master curves and shift plots of Figure 10. The reference temperature of the master curves was taken as 90°C, since this is equal to the operation temperature of the electrolyzer.
The shift-factor is a kinetic property which can be used to calculate the activation energy of the mechanical relaxation. Since the reference temperature is well below the Tg of PSU, the Arrhenius model can be used to describe
where
In order to extrapolate the compliance to longer timescales, the creep master curve data can also be fitted to the empirical Kohlrausch-Williams-Watts function. The KWW function, or stretched exponential, is widely used to describe relaxation phenomena. For long-term tensile creep, the following KWW model can be used:
where
Fitting the KWW function to the master curve with four variables
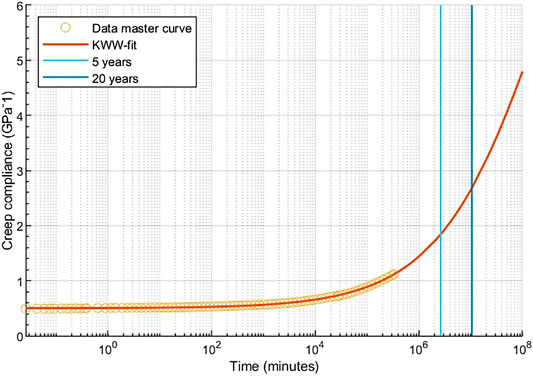
FIGURE 13. Long-term creep compliance master curve of unaged PSU with a KWW fit on a log scale. The blue lines represent the time after 5 and 20 years.
The KWW fit of the extrapolated master curve can be used to predict the creep compliance after a certain time, if the material is hold at a constant pressure and temperature of 90°C. Although, speculative, our results suggest that after 20 years of continuous use at 90°C the creep compliance would be equal to about 2.7 GPa−1, which leads to a strain of about 1.4%.
5.4. Extrapolation of the Mechanical Results (Polysulfone)
Time-temperature superposition can also be applied to other properties than the creep compliance (Gillen and Clough, 1989). The strain data from PSU aged in oxygen and air at 90°C, 120°C, and 170°C have been shifted along the time axis to get an estimate of the impact of aging at 90°C over a long period. The results are presented in Figure 14. After 20 years, it is expected that the strain at break will go down to about 80% of the initial value. It follows from the creep extrapolation, that 20 years at 90°C will lead to a strain of 1.4%. This is well below the 4.5% strain before necking, meaning the polymer will most likely not fail after 20 years at 90°C.
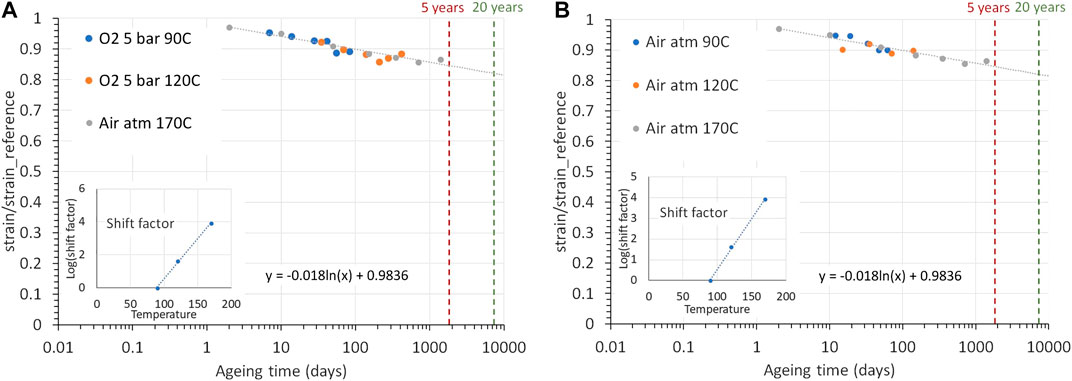
FIGURE 14. Time-temperature superposition of strain at UTS results of PSU (A) aged in oxygen and (B) in air. The red and green lines represent the time after 5 and 20 years.
6. Conclusion
A broad appraisal was made of the behavior of PPS-40%gf and PSU after exposure to the hostile conditions to which the encapsulation of alkaline electrolyzer is subjected. Most attention was paid to the mechanical results, because they are of major importance for the reliability of the encapsulation.
The Following Conclusions can be Drawn
(1) PPS-40%gf is not suited for the housing of an alkaline electrolyzer due to the dissolution of the glass fibers by the KOH solution. This result can be expected for any type of glass-reinforced polymer. The claim by CES EduPack and Ellis and Smith (2012) that PSU-30%gf is resistant to strong alkaline solutions seems therefore wrong.
(2) PSU turns out to resist both oxygen and KOH solution at elevated temperatures. Only small changes in mechanical, visco-elastic and thermal behavior are observed, which can be linked to molecular immobilization induced by physical aging. PSU does not degrade irreversibly by thermo-oxidative cross-linking and hydrolysis under the aging conditions tested.
(3) By extrapolating the experimental data it is found that when PSU is subjected to a pressure of 5 MPa for 20 years, the creep compliance increases from 0.5 GPa−1 to 2.7 GPa−1, which results in a strain of 1.4%. It is further evident that PSU will retain 80% of its strain at UTS after 20 years in a pure oxygen environment at 90°C. PSU will therefore most probably preserve its integrity and internal structure after 20 years of continuous exposure to air, as well as O2 and KOH, at the required 90°C.
(4) PPS, without reinforcement is brittle, which is undesirable. Hence, PSU which has a higher toughness and a longer durability is by far a much better candidate for the long-term application in alkaline electrolysis.
Based on this outcome, PSU will be used in a pilot plant for the encapsulation of modular solar powered mini-electrolyzers.
Data Availability Statement
The raw data supporting the conclusions of this article will be made available by the authors, without undue reservation.
Author Contributions
XZ: Conceptualization, Methodology, Formal analysis, Investigation, Writing-Original Draft, Visualization AB: Conceptualization, Supervision, Writing-Review and Editing KJ: Methodology, Software, Formal analysis, Resources, Writing-Review and Editing, Supervision JT: Methodology, Formal analysis, Writing-Review and Editing, Supervision JK: Methodology, Resources, Funding acquisition.
Conflict of Interest
The authors declare that the research was conducted in the absence of any commercial or financial relationships that could be construed as a potential conflict of interest.
Acknowledgments
We wish to thank ZEF (Zero Emission Fuels) BV for making this research possible. We further like to thank M. van den Brink, S. Garcia, V. Montano, S. Ghodrat, N. Geerlofs, R.W.A. Hendrikx and S. van Asperen for their assistance with the characterization.
Supplementary Material
The Supplementary Material for this article can be found online at: https://www.frontiersin.org/articles/10.3389/fmats.2020.610440/full#supplementary-material.
References
Afga data sheet (2020). Zirfon Perl UTP 500+, separator membrane for alkaline electrolysis consisting of an open mesh PPS fabric that is symmetrically coated with a mixture of a polymer and ZrO2. (remark of present authors: PSU is used as polymer). Afga claims an expected operational life that extends to over 10 years. [Dataset].
Allebrod, F., Chatzichristodoulou, C., and Mogensen, M. B. (2013). Alkaline electrolysis cell at high temperature and pressure of 250°C and 42 bar. J. Power Sources 229, 22–31. doi:10.1016/j.jpowsour.2012.11.105
Brown, R. P., and Greenwood, J. H. (2002). Practical guide to the assessment of the useful life of plastics. United Kingdom: Smithers Rapra Publishing.
Cai, W., and Hu, G. (2015). Oxidation degradation of polyphenylene sulfide needle felt at different sulfuric acid dew point temperatures. High Perform Polym 27, 94–99. doi:10.1177/0954008314540311
Celina, M. C. (2013). Review of polymer oxidation and its relationship with materials performance and lifetime prediction. Polym. Degrad. Stabil. 98, 2419–2429. doi:10.1016/j.polymdegradstab.2013.06.024
Chong, K., Lai, S., Thiam, H., Teoh, H., and Heng, S. (2016). Recent progress of oxygen/nitrogen separation using membrane technology. J. Eng. Sci. Technol. 11, 1016–1030.
David, M., Ocampo-Martínez, C., and Sánchez-Peña, R. (2019). Advances in alkaline water electrolyzers: a review. Journal of Energy Storage 23, 392–403. doi:10.1016/j.est.2019.03.001
Ganley, J. C. (2009). High temperature and pressure alkaline electrolysis. Int. J. Hydrogen Energy 34, 3604–3611. doi:10.1016/j.ijhydene.2009.02.083
Gesner, B., and Kelleher, P. (1968). Thermal and photo-oxidation of polysulfone. J. Appl. Polym. Sci. 12, 1199–1208. doi:10.1002/app.1968.070120518
Gillen, K. T., and Clough, R. L. (1989). Time-temperature-dose rate superposition: a methodology for extrapolating accelerated radiation aging data to low dose rate conditions. Polym. Degrad. Stabil. 24, 137–168. doi:10.1016/0141-3910(89)90108-0
Granta Design (2018). CES EduPack materials selector (version 18.1.1) [Software]. Note includes CAMPUSPlastics database [Dataset].
Guillet, N., and Millet, P. (2015). “Alkaline water electrolysis,” In Hydrogen Production by Electrolysis. Editors G-J Agata (Weinheim, Germany: Wiley-VCH Verlag GmbH & Co. KGaA), 117–166.
Iordanskii, A. L., Shterenzon, A., Moiseev, Y. V., and Zaikov, G. E. (1979). Diffusion of electrolytes in polymers. Russ. Chem. Rev. 48, 781–797.
Ju, W., Heinz, M. V. F., Pusterla, L., Hofer, M., Fumey, B., Castiglioni, R., et al. (2018). Lab-scale alkaline water electrolyzer for bridging material fundamentals with realistic operation. ACS Sustain. Chem. Eng. 6, 4829–4837. doi:10.1021/acssuschemeng.7b04173
Kemmish, D. J. (2011). Practical guide to high performance engineering plastics. United Kingdom: Smithers Rapra Publishing.
Kovač, A., Marciuš, D., and Budin, L. (2019). Solar hydrogen production via alkaline water electrolysis. Int. J. Hydrogen Energy 44, 9841–9848. doi:10.1016/j.ijhydene.2018.11.007
Kreuter, W., and Hofmann, H. (1998). Electrolysis: the important energy transformer in a world of sustainable energy. Int. J. Hydrogen Energy 23, 661–666. doi:10.1016/S0360-3199(97)00109-2
Lampman, S. (2003). Characterization and failure analysis of plastics. Cleveland, OH: ASM International.
Lee, H., Dung, D. T., Kim, J., Pak, J. H., Kim, S. k., Cho, H. S., et al. (2020). The synthesis of a zirfon-type porous separator with reduced gas crossover for alkaline electrolyzer. Intern. J. Energy Res. 44, 1875–1885. doi:10.1002/er.5038
Lee, S., Kim, D.-H., Park, J.-H., Park, M., Joh, H.-I., and Ku, B.-C. (2013). Effect of curing poly (p-phenylene sulfide) on thermal properties and crystalline morphologies. Adv. Chem. Eng. Sci. 3, 145–149. doi:10.4236/aces.2013.32017
Marini, S., Salvi, P., Nelli, P., Pesenti, R., Villa, M., Berrettoni, M., et al. (2012). Advanced alkaline water electrolysis. Electrochim. Acta 82, 384–391. doi:10.1016/j.electacta.2012.05.011
McKeen, L. W. (2016). Permeability properties of plastics and elastomers. Norwich, NY: William Andrew.
Moiseev, Y. V., Markin, V. S., and Zaikov, G. E. (1976). Chemical degradation of polymers in corrosive liquid media. Russ. Chem. Rev. 45, 246–266. doi:10.1070/RC1976v045n03ABEH002632
Phillips, R., Edwards, A., Rome, B., Jones, D. R., and Dunnill, C. W. (2017). Minimising the ohmic resistance of an alkaline electrolysis cell through effective cell design. Int. J. Hydrogen Energy 42, 23986–23994. doi:10.1016/j.ijhydene.2017.07.184
Reich, L., and Stivala, S. (1971). Elements of polymer degradation. Pennsylvania Plaza, NY: McGraw-Hill.
Schalenbach, M., Zeradjanin, A. R., Kasian, O., Cherevko, S., and Mayrhofer, K. J. (2018). A perspective on low-temperature water electrolysis–challenges in alkaline and acidic technology. Int. J. Electrochem. Sci 13, 1173–1226. doi:10.20964/2018.02.26
Schmidt, O., Gambhir, A., Staffell, I., Hawkes, A., Nelson, J., and Few, S. (2017). Future cost and performance of water electrolysis: an expert elicitation study. Int. J. Hydrogen Energy 42, 30470–30492. doi:10.1016/j.ijhydene.2017.10.045
Smolinka, T. (2014). Water electrolysis: status and potential for development. Freiburg, Germany: Fraunhofer Institute for Solar Energy Systems ISE.
Ticona, (1999). Design with Fortron PPS.pdf. Available at: http://www.hipolymers.com.ar/pdfs/fortron/diseno/Designing%20with%20Fortron%20PPS.PDF (Accessed July 12, 2019). [Dataset].
Ursua, A., Gandia, L. M., and Sanchis, P. (2011). Hydrogen production from water electrolysis: current status and future trends. Proc. IEEE 100, 410–426. doi:10.1109/JPROC.2011.2156750
Vermeiren, P., Moreels, J., Claes, A., and Beckers, H. (2009). Electrode diaphragm electrode assembly for alkaline water electrolysers. Int. J. Hydrogen Energy 34, 9305–9315. doi:10.1016/j.ijhydene.2009.09.023
Wang, H. C., Jiang, D. H., and Liu, Y. (2011). Life problem analysis on PPS filter application of bag dedusters in coal-fired power plants. Adv. Mat. Res. 236-238, 2464–2470. doi:10.4028/www.scientific.net/AMR.236-238.2464
Wang, X., Li, Z., Zhang, M., Fan, T., and Cheng, B. (2017). Preparation of a polyphenylene sulfide membrane from a ternary polymer/solvent/non-solvent system by thermally induced phase separation. RSC advances 7, 10503–10516. doi:10.1039/C6RA28762J
Wright, D. (2001). Failure of plastics and rubber products: causes, effects and case studies involving degradation. United Kingdom: Smithers Rapra Publishing.
Xing, J., Xu, Z., and Deng, B. (2018). Enhanced oxidation resistance of polyphenylene sulfide composites based on montmorillonite modified by benzimidazolium salt. Polymers (MDPI) 10, 1–15. doi:10.3390/polym10010083
Xu, L., Yu, Y., Li, W., You, Y., Xu, W., and Zhang, S. (2014). The influence of manufacturing parameters and adding support layer on the properties of zirfon® separators. Front. Chem. Sci. Eng. 8, 295–305. doi:10.1007/s11705-014-1433-y
Yamashita, T., Kudo, T., Horie, K., Maeda, S., and Nagata, K. (1993a). Degradation of sulfur-containing aromatic polymers (II): change in fluorescence spectra of polyphenylenesulfide (PPS) during annealing. Polym. Degrad. and Stab. 39, 279–284. doi:10.1016/0141-3910(93)90002-Z
Yamashita, T., Tomitaka, H., Kudo, T., Horie, K., and Mita, I. (1993b). Degradation of sulfur-containing aromatic polymers: photodegradation of polyethersulfone and polysulfone. Polym. Degrad. Stabil. 39, 47–54. doi:10.1016/0141-3910(93)90124-2
Keywords: polymers, polyphenylene sulfide, polysulfone, accelerated aging, pure oxygen, lifetime prediction, long-term creep, modular alkaline electrolysis
Citation: Zheng XX, Böttger AJ, Jansen KMB, van Turnhout J and van Kranendonk J (2020) Aging of Polyphenylene Sulfide-Glass Composite and Polysulfone in Highly Oxidative and Strong Alkaline Environments. Front. Mater. 7:610440. doi: 10.3389/fmats.2020.610440
Received: 25 September 2020; Accepted: 19 November 2020;
Published: 22 December 2020.
Edited by:
Pingan Song, University of Southern Queensland, AustraliaReviewed by:
Yongan Niu, Shenyang University of Chemical Technology, ChinaDavid Aili, Technical University of Denmark, Denmark
Copyright © 2020 Zheng, Böttger, Jansen, van Turnhout and van Kranendonk. This is an open-access article distributed under the terms of the Creative Commons Attribution License (CC BY). The use, distribution or reproduction in other forums is permitted, provided the original author(s) and the copyright owner(s) are credited and that the original publication in this journal is cited, in accordance with accepted academic practice. No use, distribution or reproduction is permitted which does not comply with these terms.
*Correspondence: X. X. Zheng, xiao_xu@live.nl