- 1College of Textile Science and Engineering, International Institute of Silk, Zhejiang Sci-Tech University, Hangzhou, China
- 2Zhejiang Sci-Tech University, Huzhou Research Institute Co., Ltd., Huzhou, China
The use of synthetic fibers in our daily life is growing continuously; however, the excessive dependence of these chemical fibers on petroleum-based chemicals will lead to large consumption of non-renewable resources. The scarcity of oil resources, economic and environmental problems, reliance on a few oil-rich countries, and predicted depletion of these resources. Therefore, research and development of biobased materials to reduce the use of fossil fuels have become increasingly important. Biobased synthetic fiber has a low carbon footprint in the synthesis process because its raw materials are derived from biomass. In addition, most biobased synthetic fibers have excellent biodegradability, which can be composted and degraded in natural environments or by microorganisms with or without specific conditions. However, all biobased fibers cannot be proven to be biodegradable, so the development of biodegradability is an important driving force for the progress of research on biobased fibers. In the past, biobased fiber was obtained, extracted, or synthesized from food crops, which was soon replaced by non-food crops. With environmental protection, sustainability, and resource conservation, it has become necessary to make non-food crops and food residues biobased raw materials to obtain biobased textile fibers and even to develop ideal biobased raw materials that are carbon negatives, such as moss and CO2. Besides, there is huge potential for these biobased textile fibers to be used for sustainable clothing and medical textiles due to their non-toxicity, skin friendliness, and antibacterial properties. This review paper introduces biobased synthetic textile fibers, summarizes the recent development, and clarifies key concepts in this domain.
1 Introduction
In recent years, the excessive use of crude oil has led to resource depletion and environmental pollution, which has greatly impacted our society (Zhang et al., 2021). To date, synthetic textile fibers such as polyester, nylon, spandex, and acrylic fiber mostly come from petroleum-based sources, refer to Figure 1 (Karthik and Rathinamoorthy, 2017).
The synthesis of these fibers is often accompanied by the emission of greenhouse gases such as CO2 and the rise in the price of petroleum (Asif and Muneer, 2007). As oil storage is mainly concentrated in Middle East countries, oil trade and transportation between different countries are often accompanied by risks such as oil leakage and natural disasters (Cruz and Krausmann, 2013). Besides, it is facing the dilemma of increasing depletion as it is a non-renewable resource. The energy demand is also rising with the recent scientific and technological progress and overall lifestyle development (Chand, 2020). Therefore, using new biobased materials has attracted increasing attention by reducing the dependence on fossil fuels such as petroleum-based sources and can be considered a source of positive environmental impact (Zia et al., 2016; Shekar and Ramachandra, 2018; Mann et al., 2020). Figure 2 describes some pervasive problems associated with these non-biodegradable sources.
Biobased synthetic fiber is extracted from natural renewable resources and synthesized from renewable biomass. Biomass is environmentally friendly, renewable, and biodegradable (Papageorgiou, 2018; Vinod et al., 2020). Biomass, as the only source of renewable biological carbon, can be regenerated within a decade, while fossil resources need millions of years to regenerate, so fossil resources are often called non-renewable resources (Reid et al., 2020). Moreover, the biomass industry is developing continuously and rapidly due to the enormous pressure of petrochemical products on the environment. Therefore, the research and development of synthetic polymers from renewable resources, which are then spun into biobased fibers, is a feasible solution to the problems of energy depletion and environmental pollution in the current global society (Tursi, 2019). Biobased fiber raw materials come from a wide range of sources and are often cheap and environmentally friendly. Since almost all countries have rich reserves of biomass raw material resources, thus, obtaining biobased materials would stop the dependence on a few oil-rich countries. Their raw materials are produced through fermentation using agricultural, forestry, and marine wastes or by-products as raw materials. Recent research shows that biobased polyesters and polyamides can serve as promising textile materials (Popa, 2018; Hatti-Kaul et al., 2020). Since their products are friendly to the human body and environment, appreciated by most people, and lead the global textile consumption trend. With attention paid to the comprehensive utilization of resources and the progress of synthesis and spinning technology, the development and utilization of bio-based fibers are promoted.
Traditional chemical fibers such as polyester, nylon, polypropylene, and spandex are mainly made of petroleum (Chawla, 2016); however, oil resources are facing the dilemma of increasing depletion, and such fibers are often non-biodegradable, which will pollute the environment. In synthesizing and spinning chemical fibers from petroleum extraction materials, CO2 and other greenhouse gases are usually emitted into the atmosphere, which is one of the main reasons for global warming and climate change; Thus, it negatively impacts the social environment and economy (Yoro and Daramola, 2020). As the raw material of biobased fiber is natural biomass, and all or part of the carbon atoms contained in it are derived from biomass, it can reduce greenhouse gas emissions in the process of extracting and processing into fiber (Tursi, 2019). Most biobased fibers are biodegradable, which can be degraded by respiration or chemical energy synthesis of bacteria, fungi, and other microorganisms in the environment with or without specific conditions and even in a natural composting environment, and they can be decomposed into CO2 and water (Wojnowska-Baryła et al., 2020). The CO2 emitted in this synthesis process and generated in the degradation process can be absorbed and utilized by plants through net photosynthesis in the environment to obtain new carbon-containing natural macromolecules to realize the carbon cycle in this process, as shown in Figure 3. Therefore, biobased fiber has the characteristics of overall carbon reduction or carbon-free emission. The above problems provide an effective measure for developing and producing biobased fiber and its products.
2 Biobased fiber and biodegradable fiber
In recent years, biodegradable polymers and fiber products have become very important because traditional plastic and other chemical fibers are difficult to degrade in the natural environment, which has seriously polluted the biological environment (Garrison et al., 2016; Chen and Yan, 2020; Shen et al., 2020). The pollution of textile fibers occurs in the carbon emissions in the production process and the non-degradability of its waste (Meereboer et al., 2020), so using biobased and biodegradable fibers can significantly reduce carbon emissions and improve the ecological environment. They are classified by fiber source and biodegradability, as shown in Figure 4. Biodegradable fibers can be derived not only from biobased fibers but also from petroleum-based fibers. Biobased chemical fibers are derived from renewable biomass. Although biobased and biodegradable fibers do not precisely correspond, biodegradability is an important driving force for the research progress of biobased fibers.
2.1 Biobased and biodegradable fibers
The treatment method of ordinary synthetic fiber is incineration and cremation, which causes a large number of greenhouse gases to be discharged into the air (Oberoi et al., 2021). Polylactic acid (PLA) fiber is naturally degraded by the hydrolysis of ester bonds buried in the soil. In addition, microorganisms such as actinomycete in the environment will accelerate its biodegradation (Qi et al., 2017). The CO2 produced after biodegradation enters the soil organic matter directly or is absorbed by plants, which is not discharged into the air and will not cause the greenhouse effect, which is very beneficial to the protection of the environment. Therefore, PLA fiber is currently recognized as the most significant biobased and biodegradable material and is widely used in food packaging, transportation, textiles, and electronics industries. Polyhydroxy fatty acid (PHA) is an intracellular polyester synthesized by various microorganisms. PHA is a natural macromolecular biomaterial that microorganisms can decompose in almost all environments, such as composting, soil, and seawater, and the products after decomposition are mostly water and carbon-based and do not pollute the environment (Jendrossek et al., 1996; Dilkes-Hoffman et al., 2019; Meereboer et al., 2020).
2.2 Petroleum-based biodegradable fiber
Although some chemical fiber materials mainly come from petroleum bases, their ester bonds are easily hydrolyzed and degraded by microorganisms or biological enzymes, thus showing good biodegradability. Dimethyl oxalate (DMO), an essential compound for preparing Polyglycolic acid (PGA), is prepared from coal through hydrogenation, hydrolysis, and polymerization. PGA has good biodegradability that can be completely degraded within 2–5 months (Agrawal et al., 1995). The degradation products are water and CO2, which are completely non-toxic and harmless. It is often used for absorbable surgical sutures with high biodegradability and biocompatibility (Samantaray et al., 2020; Kumar et al., 2021). Poly (butylene adipate-co-terephthalate) (PBAT) is a synthetic polymer based on traditional fossil resources. As a biodegradable plastic with the most commercial potential, the biodegradability of PBAT is related to the molecular weight of the polymer (Ferreira et al., 2019; Jian et al., 2020). In addition, it should be noted that the molecular weight can be significantly reduced when there is water. In the natural environment, it is hydrolyzed by bacteria, fungi, and algae. PBAT has ductility and flexibility comparable to low-density polyethylene, Its Young’s modulus is 20–35 MPa, and its tensile strength is 32–36 MPa (Jian et al., 2020). It is considered one of the most promising and popular sustainable materials in contemporary green material manufacturing.
Polycaprolactone (PCL) is widely used in medical textile materials and sustainable packaging as an aliphatic polyester. Bartnikowski et al. (2019) reported that the main factors of PCL degradation are non-enzymatic, random chain break, and can be carried out by acid and base-catalyzed ester hydrolysis. Al Hosni et al. (2019) buried PCL in compost at 50°C and completely degraded it by microorganisms after 91 days.
2.3 Petroleum-based non-biodegradable fiber
Traditional petroleum-based chemical fibers such as polyester, nylon, polypropylene, and spandex are petroleum-based and non-biodegradable fibers. More and more environmental pollution problems are caused by the waste of these fibers (Palamutcu, 2017; Pensupa et al., 2017; Patti et al., 2020). These petroleum-based non-biodegradable fibers have a high melting point, high crystallinity, stable molecular structure, excellent mechanical properties, and good hydrolytic and chemical corrosion resistance (Gholampour and Ozbakkaloglu, 2020; Aaliya et al., 2021). Therefore, they degrade very slowly in the natural environment. Once these materials are discarded, they will continue to exist in the environment without degradation for a very long period, causing many ecological and environmental problems.
2.4 Biobased but hardly biodegradable fibers
The biodegradability of polymer materials is a relatively complex process closely related to their chemical structure and properties (Rudnik, 2019; Zambrano et al., 2020). Although some chemical fiber materials have biological properties, their biodegradability is restricted due to their high crystallinity and excellent thermal properties, making them difficult to degrade. The binary alcohol monomer used in biological Polypropylene terephthalate fiber (PTT) is biobased 1,3-propanediol (PDO), derived from non-grain raw materials such as starch and glycerin. Biobased PTT can be prepared by direct esterification or transesterification with terephthalic acid and PDO (Shen, 2014). PTT fiber has better resilience, lower tensile modulus, and higher elongation at break than other polyester fibers (Zhang et al., 2021). However, the biobased PTT polyester fiber is close to the polyester fiber in nature and, thus, does not have biodegradability (Rahman and Bhoi, 2021). The ecological advantage of these fibers is that they can effectively reduce the carbon footprint of products, but it is difficult for products to be degraded through the natural environment after being discarded Table 1 shows the tensile strength and biodegradability of various common petroleum based fibers and bio based fibers.
3 Different generations of biobased fiber
As shown in Figure 5, biobased fibers were previously obtained, extracted, or synthesized from grain crops, which were soon replaced by nonfood crops like food waste. With environmental protection, sustainability, and resource conservation, it has become necessary to make nonfood crops and food residues biobased raw materials to obtain biobased textile fibers and even to develop ideal biobased raw materials that are carbon negatives, such as moss and CO2.
3.1 The first generation of biobased raw materials for textile fibers
At first, many biobased polymers came from agricultural products. These first-generation biobased raw materials were mainly starch extracted from crops such as corn, wheat, potato, beet, rice, and vegetable oil, and sugar obtained from raw materials such as sucrose was fermented and processed into polymers (Babu et al., 2013; Harmsen et al., 2014).
The corn starch raw material is saccharified to obtain glucose, fermented by glucose and certain strains to produce high-purity lactic acid, and then the PLA with a certain molecular weight is synthesized by the chemical synthesis method. It has excellent biodegradability, bioabsorbability, and biocompatibility. The total energy consumption during PLA production is 75. 4 MJ/kg, which has the advantages of low energy consumption and low-temperature chamber gas emission. Compared with petroleum-based traditional polymers, fossil energy consumption has decreased by 25%–55% (Rajeshkumar et al., 2021). Eerhart et al. (2012) used fructose from corn as raw material to produce bioplastics polyethylene furan dicarboxylate (PEF). They carried out energy and greenhouse gas balance research and found that compared with PET, the production of PEF can reduce non-renewable energy use by about 40%–50% and greenhouse gas emissions by about 45%–55%.
However, the first generation of biobased fiber is from crops needed in people’s daily life. For example, the production of biobased raw materials based on food crops has led to food shortages and disrupted the ratio of food to the population due to economic constraints. In addition, if the recent trend continues, it is expected that the supply of starch and sugar will be limited in the future.
3.2 Second-generation biobased raw materials for textile fibers
Currently, the selection of biobased raw materials is increasingly focused on the non-food components of plant materials (Babu et al., 2013). The second generation of biobased materials is obtained from the processing and utilization of carbohydrate polymers such as cellulose and lignin extracted from non-food crops such as bagasse, corncob, palm grove, and other food and agricultural processing wastes (Deutschmann and Dekker, 2012). As they come from non-food crops, they do not affect the food demand in people’s daily life but use the waste in food. After foody stuff is retrieved from corn, the corncobs and stalks are left. Corn stalks are generally used as feed or burned. In addition to being used as fuel, corncob can also be used to produce chemical products, such as furfural, xylose, and xylitol (Wang et al., 2010). The content of xylan is very high in corncob, and its molecular crystallinity is very low; it is easy to degrade it by microbial enzymatic hydrolysis so that corncob can be effectively used (Delgado-Arcaño et al., 2021).
Lignin is the second most abundant natural polymer in plant biomass and the main renewable source of aromatic structure on the earth, so it is considered an ideal raw material for producing biological aromatic chemicals (Raj et al., 2022). Every year, 50 million tons of lignin is produced as a by-product of the paper industry, 98% of lignin is burned and consumed, and the hidden potential of lignin due to many aromatic rings in its structure is not fully used (Mahmood et al., 2016; Souza et al., 2020). Harshvardhan et al. (2017) used natural bacterial groups instead of genetically modified microorganisms to degrade lignocellulose in bamboo chips and can produce natural vanillin without chemical treatment. Hosoya et al. (2020) produced vanillin from natural soft lignin in the presence of tetrabutylammonium ions. The aromatic ring unit of vanillin provides excellent mechanical strength, heat, and chemical resistance (Memon et al., 2020). Vanillin and its derivatives are considered promising biobased compounds among biobased aromatic compounds that could be derived from lignin. Enomoto and Iwata (2020) synthesized dipyridamole acid monomers of different side chain lengths from methyl vanillin ate and polymerized them with alkanes to obtain biphenyl-type series polyesters as shown in Figure 6, and its thermal decomposition temperature is between 340–390°C.
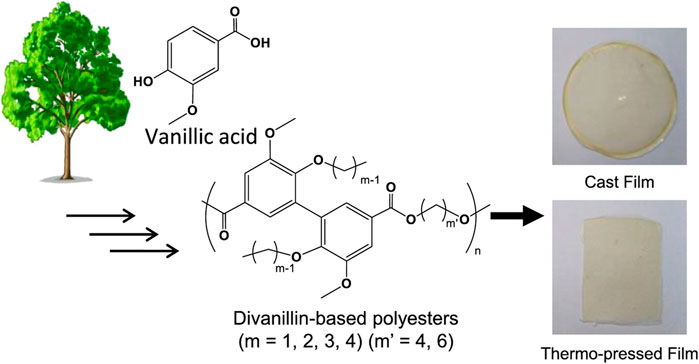
FIGURE 6. Synthesis and Film of Vanillin-based polyester (Enomoto and Iwata, 2020).
Ibrahim and Shabeer (2022) reacted isovanillin with a series of diamines under a nitrogen atmosphere to synthesize new Schiff base monomers and used p-benzoyl chloride to synthesize a series of polyesters based on isovanillin through solution polycondensation. Figure 7 shows the synthesis route. This polyester has good antibacterial properties in Escherichia coli, Vibrio parahaemolyticus, Staphylococcus aureus, Candida albicans, and Aspergillus Niger.
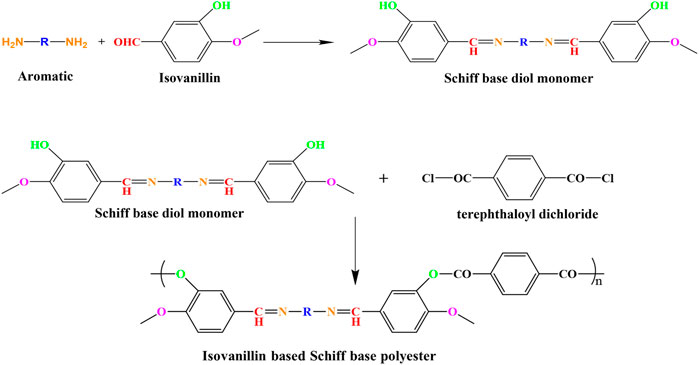
FIGURE 7. Synthesis route of Schiff base polyester (Ibrahim and Shabeer, 2022).
3.3 Third-generation biobased raw materials for textile fibers
The third generation of biobased polymer is extracted from moss, CO2, and bacterial cellulose and processed and synthesized. This kind of biomass comes from anywhere in nature. The biobased fiber produced from this kind of raw material has great potential. However, the limited technology in various aspects has not been widely developed and applied. Wi et al. (2009) studied that Ceylon moss contains high content of carbohydrates, galactose (23%), and glucose (20%). The glucose yield of the pretreated sodium chlorite sample was as high as 70%, while the contrast of the untreated sample was only 5%. Pretreatment with sodium chlorite significantly improved the efficiency of enzymatic hydrolysis. The potential of bioethanol production from sugar in Ceylon mosses is enormous.
The fibers made of CO2-based thermoplastic polyurethane (TPU) of Covestro Company adopt melt spinning technology, in which TPU is melted, pressed into very thin threads, and finally processed into endless fiber yarns. Unlike the dry spinning used to produce traditional elastic synthetic fibers, melt spinning does not require using environmentally harmful solvents (fibers, 2019). The production of elastic yarn by partially replacing raw materials from fossil resources with CO2 can become a substitute for traditional elastic yarn in the future, improving the sustainability of raw materials. Cai et al. (2021) reported a mixed chemical biochemical pathway for synthesizing starch from CO2 and hydrogen in a cell-free system. In this system, they use inorganic catalysts to reduce CO2 to methanol, convert it into three and six-carbon sugar units through enzymes, and finally convert it into polymeric starch. They could convert CO2 into starch at 22 nmol of CO2 per minute per milligram of total catalyst, which is 8.5 times higher than that of corn.
4 Application of biobased fiber
There is much attention on the sustainability of textiles in sustainable textile marketing (Chen et al., 2021; Memon et al., 2022a), textile recycling (Memon et al., 2022b), textile auxiliaries (Memon et al., 2016), and even sustainable textile heritage (Memon et al., 2022c). Biobased synthetic fiber is one of the promising approaches to impart sustainability in textiles with biosafety, biocompatibility, and biodegradability (Li et al., 2021; Baranwal et al., 2022; Xu et al., 2022). It is a renewable resource that is environmentally friendly in production and skin-friendly in products. Therefore, biobased chemical fiber as raw material has a unique use in clothing, textile materials, food packaging, biomedicine, etc. This section will introduce the application of biobased fibers in these fields.
4.1 Wearability
Biobased fiber has the advantages of good skin contact (softness, skin affinity), good wearing comfort, good moisture absorption, easy finishing, high dryness, strong humidity, and good dimensional stability (Thangavelu and Subramani, 2016). Toray Industries, Inc. has developed a 100% biobased synthetic fiber nylon 510 (N510) (Staff, 2022). It is made of sebacic acid in a castor oil plant and pentamethylene diamine in corn. It is as solid and heat-resistant as nylon 6 and has excellent dimensional stability in wet conditions (Toray, 2022). TERRYL® is Cathay that launched the biobased polyamide fiber brand in the textile field. Biobased 1,5-pentanediamine (DN5) is extracted from renewable plant materials and polymerized with various long-chain dicarboxylic acids (LCDA) to synthesize biobased polyamide can effectively reduce the use of petroleum and other fossil-based materials and reduce carbon emissions.
It can be seen from the Table 2 that the melting temperature, viscosity, and other physical properties of the Terryl™ PA56 are similar to those of the polyamide fiber (such as PA6 or PA6,6) from petroleum and other fossil-based sources. The fiber has excellent clothing properties such as low-temperature dyeing, softness, skin affinity, and wear resistance. Its inherent flame-retardant performance also brings unique application experience in some special fields.
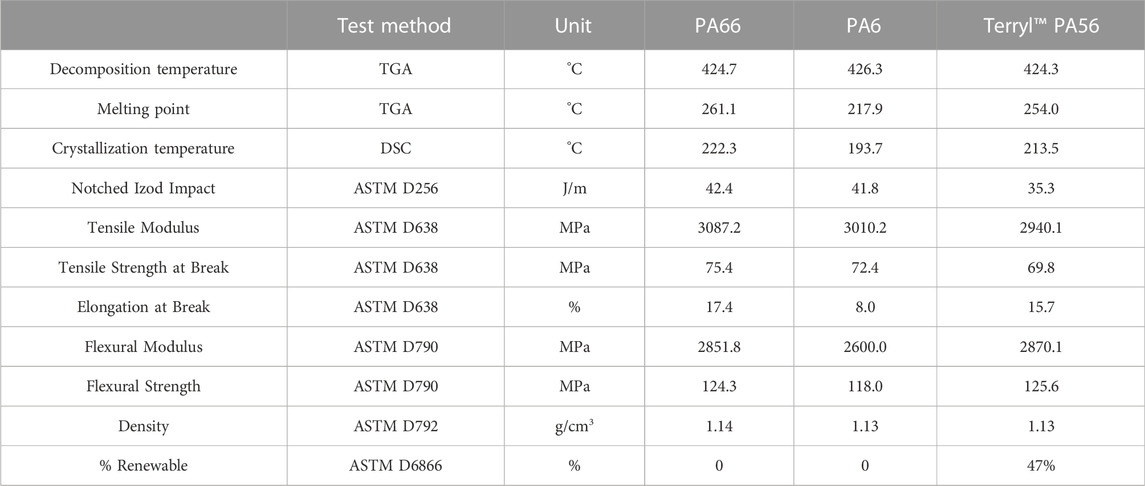
TABLE 2. Performance of PA6, PA66 and Terryl™ PA56 (biotechnology innovation organization, 2005).
Biobased raw materials can be fermented into glutamic acid through various bacteria and further transformed into glutamic acid through glutamic acid decarboxylase γ- Aminobutyric acid. Quan et al. (2022) used Polybutyrolactam (PBY) fiber as raw material, adopted the improved dry shoot wet spinning method, and used the appropriate air gap layer, sequential anhydrous ethanol solution, the coagulation bath to prepare the polymer-based polyamide fiber. PBY fiber also has good biodegradability. In the case of the prevalence of novel coronavirus, it can be used to prepare indispensable medical textiles such as masks and protective clothing after use. It can be discarded, as the natural environment can biodegrade without environmental pollution.
4.2 Antibacterial function
Textiles are stained with sweat, sebum, and other human secretions and contaminated by the environment’s dirt (Krifa et al., 2019; Broadhead et al., 2021). These pollutants are an excellent source of nutrition for various microorganisms, especially under high temperatures and humid conditions, and become a suitable environment for propagating various microorganisms (Halepoto et al., 2022). Endowing textiles with antibacterial function can not only prevent textiles from being damaged due to the corrosion of microorganisms but also cut off the way for textiles to transmit pathogenic bacteria and prevent bacteria from decomposing dirt on fabrics to produce odor, leading to dermatitis and other diseases (Memon et al., 2018). People have higher and higher requirements for quality of life and pay more attention to environmental health and self-health. Therefore, antibacterial sanitary textiles have gradually been loved by consumers.
Bioserica fiber, produced by Nanjing Bioserica ERA Antimicrobial Materials Company, is a low-carbon consumption green textile fiber exhibiting surprisingly superior antibacterial performance. Bioserica fiber is based on two biodegradable polymer resins, PLA and polyhydroxy-butyrate-co-valerate (PHBV), and is prepared by rheological modification, reactive blending, and melt spinning, which can realize natural, additive-free, green and environment-friendly antibacterial. As a promising antibacterial material, silver nanoparticles are clean, cost-effective, and harmless to the environment (Yasin et al., 2013). Many researchers use the green biological reduction method to synthesize silver nanoparticles, and these silver ions can be loaded in antibacterial agents of textile fibers to give them antibacterial properties. Yasin et al. (2013) studied a method of synthesizing silver nanoparticles using bamboo leaf extracts, which have an inhibitory effect on Escherichia coli and Staphylococcus aureus. Liu et al. (Ullah et al., 2015) exposed silver ions to the extract of Nageia nagi leaves, and the silver nanoparticles were bio-reduced rapidly under sunlight. They produce green AgNPs without an external heating source, which can show effective antibacterial performance against multi-drug resistant bacteria such as Escherichia coli and Staphylococcus aureus. Huang et al. (2017) studied the performance of PLA/PHBV filament yarns and compared them with petroleum-based (PET, PA6). They found that the PLA/PHBV filament yarn has adequate thermal and mechanical properties. In addition, in the antibacterial study of the yarn, it can inhibit 99.99%, 99.99%, and 99.31% of Staphylococcus aureus, Klebsiella pneumoniae and Candida albicans, respectively. Chiloeches et al. (2022) prepared antibacterial and compostable PLA-based fibers. They synthesized a polyitaconate containing nitrogen and N-haloamines groups, mixed it with PLA solution and electrospun them to give PLA fiber antibacterial activity as shown in Figure 8. The results showed that the PLA-based fibers prepared could effectively inactivate Gram-positive and Gram-negative bacteria.

FIGURE 8. Preparation of electrospun PLA-Based fibers of antibacterial biopolymer (Chiloeches et al., 2022).
4.3 Biomedical functions
Biobased fibers have good antibacterial, biodegradable and biocompatible properties in vivo and in vitro (Xu et al., 2022), so the application of biobased fibers in biomedical functions has a good prospect. Alginate extracted from kelp or sargassum algae of brown algae is a group of natural polysaccharides with linear anions (Gheorghita Puscaselu et al., 2020; Al Monla et al., 2022). Alginate fiber is non-toxic, with rich sources, high hygroscopicity, good biodegradability, and biocompatibility, and can be used as an excellent medical textile fiber (Aderibigbe and Buyana, 2018).
Traditional wound dressing will hinder wound regeneration. Alginate dressing can appear in hydrogel and fiber, absorb wound exudates, and then form a gel to keep the wound moist. Alginate fibers can be prepared by wet spinning or electrospinning, and because of their high conductivity in an aqueous solution, they can be blended with other polymers to prepare composite fibers. Liu et al. (Yu et al., 2016) used the wet spinning method to prepare alginate fiber combined with silver nanoparticles (AgNPs) synthesized from natural Dolcetto grape leaves and confirmed that the fiber has robust mechanical and antimicrobial properties characterized by SEM and FTIR. Wang et al. (2021) added quaternized chitosan and magnesium to the alginate spinning solution to prepare a dressing with an antibacterial function for treating diabetes wounds. Moreira Filho et al. (2020) fixing papain on alginate fiber wound dressing can endow the dressing with wound healing ability. Papain added can stimulate the production of cytokines to promote local cell proliferation, reduce scars and assist wound healing. Ullah et al. (2014) boiled the holly leaves to prepare the extract and added it into a conical flask containing AgNO3 aqueous solution. They observed the color change from colorless to yellowish-brown color, indicating that the holly leaf extract reduces silver ions into silver nanoparticles. They loaded the prepared silver nanoparticles on the cotton fiber, which showed an inhibitory effect on the growth of Escherichia coli.
AgNPs embedded in the cotton fiber had good properties due to chain hydroxyl groups in the cellulose cotton fiber, indicating that it could be used for wound dressing antibacterial finishing, and other medical textiles. Bi et al. (2020) dissolved sodium alginate (SA) and polyvinyl alcohol (PVA) in pure water to make the spinning solution, electrospun it, and collected it on aluminum foil containing PLA fiber to obtain PLA/PVA/SA composite fiber. They compared the wound healing of rats with composite fiber, PLA fiber, and commercial gauze. Figure 9 shows that the wound shrinkage rate of PLA and PLA/PVA/SA dressing treatment is higher than that of commercial gauze. On the 16th day, the wounds of PLA and PLA/PVA/SA groups are almost completely healed with few scars, showing excellent biocompatibility.
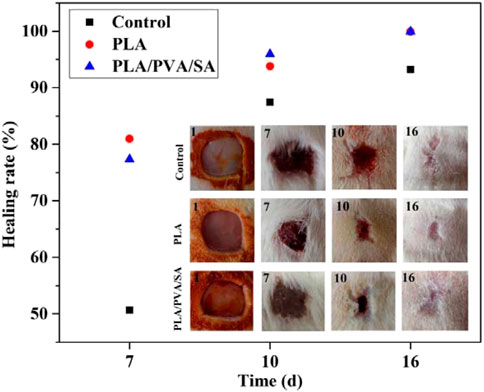
FIGURE 9. Healing rate and wound closure image of PLA fiber treatment and PLA/PVA/SA fiber treatment (Bi et al., 2020).
5 Conclusion and prospect
This paper summarizes the relationship between biobased fibers and biodegradable fibers. Most biobased fibers have the advantage of biodegradation. The use of developed biobased fibers can effectively solve the environmental pollution problems caused by abandoned non-biodegradable textiles; The development history of biobased fiber raw materials ranges from taking food crops as raw materials and its by-products as raw materials to biomass raw materials that have nothing to do with food that exists everywhere. This paper also introduces that biobased synthetic fiber has a good application in textiles and medicine due to its excellent wearability, antibacterial property, and biocompatibility.
In the future, textiles will develop towards comfort, function, intelligence, protection, ecological and environmental protection, and sustainable resources. In order to improve the awareness of environmental protection, efforts should be made to develop biobased chemical fibers that are rich in raw materials, easy to obtain, comfortable, and harmless to human health. Biobased synthetic fibers continue to develop efficiently, but they cannot replace the existing petroleum-based materials. This is mainly because the biobased conversion technology is not mature enough, the effective utilization rate of non-grain biobased materials is low, and the purification process is complex, which makes the cost of raw materials prepared too high and the quality unstable; as a result, the efficiency of the target product is low. Although all recent progress has been made in biobased and biodegradable polymers, further research is needed before completely replacing petroleum-based products. There are still some problems with the cost, technology, and equipment of biobased chemical fibers. To solve these problems, we should seek cooperation in process technology, product development, market application, and special equipment development, and develop a new production route combining various production processes. Therefore, it is necessary to build and establish raw material resources of biobased chemical fibers, develop new production technologies, systematically optimize biological fermentation, enzyme conversion, chemical synthesis, and other technologies, and achieve raw material regeneration in combination with efficient separation and purification of multi-component systems.
Author contributions
Conceptualization, KH and CZ; methodology, KH and ZS; software, KH and WT; validation, KH and CZ; formal analysis, KH and CZ; investigation, KH, XF, and CZ; resources, KH and LS; data curation, KH and MH; writing—original draft preparation, KH; writing—review and editing, WT; visualization, KH and WT; supervision, CZ; project administration, CZ; funding acquisition, CZ. All authors have read and agreed to the published version of the manuscript.
Funding
This research was funded by “Research on Preparation, Mechanical Properties and Biological Adhesion of Basalt Fibre Rein-forced Composites for Marine Pasture” of Zhejiang Sci-Tech University Huzhou Research Institute Co.
Conflict of interest
Authors WT and CZ were employed by the company Huzhou Research Institute Co., Ltd.
The remaining authors declare that the research was conducted in the absence of any commercial or financial relationships that could be construed as a potential conflict of interest.
The handling editor declared a past co-authorship with the authors CZ and TW.
Publisher’s note
All claims expressed in this article are solely those of the authors and do not necessarily represent those of their affiliated organizations, or those of the publisher, the editors and the reviewers. Any product that may be evaluated in this article, or claim that may be made by its manufacturer, is not guaranteed or endorsed by the publisher.
References
Aaliya, B., Sunooj, K. V., and Lackner, M. (2021). Biopolymer composites: A review. Int. J. Biobased Plastics 3 (1), 40–84. doi:10.1080/24759651.2021.1881214
Aderibigbe, B. A., and Buyana, B. (2018). Alginate in wound dressings. Pharmaceutics 10 (2), 42. doi:10.3390/pharmaceutics10020042
Agrawal, C. M., Niederauer, G. G., and Athanasiou, K. A. (1995). Fabrication and characterization of PLA-PGA orthopedic implants. Tissue Eng. 1 (3), 241–252. doi:10.1089/ten.1995.1.241
Al Hosni, A. S., Pittman, J. K., and Robson, G. D. (2019). Microbial degradation of four biodegradable polymers in soil and compost demonstrating polycaprolactone as an ideal compostable plastic. Waste Manag. 97, 105–114. doi:10.1016/j.wasman.2019.07.042
Al Monla, R., Dassouki, Z., Sari-Chmayssem, N., Mawlawi, H., and Gali-Muhtasib, H. (2022). Fucoidan and alginate from the Brown algae Colpomenia sinuosa and their combination with vitamin C trigger apoptosis in colon cancer. Molecules 27 (2), 358. doi:10.3390/molecules27020358
Aliotta, L., Cinelli, P., Coltelli, M. B., Righetti, M. C., Gazzano, M., and Lazzeri, A. (2017). Effect of nucleating agents on crystallinity and properties of poly (lactic acid)(PLA). Eur. Polym. J. 93, 822–832. doi:10.1016/j.eurpolymj.2017.04.041
Asif, M., and Muneer, T. (2007). Energy supply, its demand and security issues for developed and emerging economies. Renew. Sustain. energy Rev. 11 (7), 1388–1413. doi:10.1016/j.rser.2005.12.004
Babu, R. P., O'connor, K., and Seeram, R. (2013). Current progress on bio-based polymers and their future trends. Prog. Biomater. 2 (1), 8–16. doi:10.1186/2194-0517-2-8
Baranwal, J., Barse, B., Fais, A., Delogu, G. L., and Kumar, A. (2022). Biopolymer: A sustainable material for food and medical applications. Polymers 14 (5), 983. doi:10.3390/polym14050983
Bartnikowski, M., Dargaville, T. R., Ivanovski, S., and Hutmacher, D. W. (2019). Degradation mechanisms of polycaprolactone in the context of chemistry, geometry and environment. Prog. Polym. Sci. 96, 1–20. doi:10.1016/j.progpolymsci.2019.05.004
Bi, H., Feng, T., Li, B., and Han, Y. (2020). In vitro and in vivo comparison study of electrospun PLA and PLA/PVA/SA fiber membranes for wound healing. Polymers 12 (4), 839. doi:10.3390/polym12040839
biotechnology innovation organization (2005) presentation_Paul_caswell. Available from: https://www.bio.org/sites/default/files/legacy/bioorg/docs/montreal%20bioplastic%20cathay %20green %20nylon %20presentation_paul_caswell.pdf.
Boyandin, A. N., Prudnikova, S. V., Karpov, V. A., Ivonin, V. N., Dỗ, N. L., Nguyễn, T. H., et al. (2013). Microbial degradation of polyhydroxyalkanoates in tropical soils. Int. Biodeterior. Biodegrad. 83, 77–84. doi:10.1016/j.ibiod.2013.04.014
Broadhead, R., Craeye, L., and Callewaert, C. (2021). The future of functional clothing for an improved skin and textile microbiome relationship. Microorganisms 9 (6), 1192. doi:10.3390/microorganisms9061192
Cai, T., Sun, H., Qiao, J., Zhu, L., Zhang, F., Zhang, J., et al. (2021). Cell-free chemoenzymatic starch synthesis from carbon dioxide. Science 373 (6562), 1523–1527. doi:10.1126/science.abh4049
Chand, V. (2020). “Conservation of energy resources for sustainable development: A big issue and challenge for future,” in Environmental concerns and sustainable development (Berlin, Germany: Springer), 293–315.
Chen, L., Qie, K., Memon, H., and Yesuf, H. M. (2021). The empirical analysis of green innovation for fashion brands, perceived value and green purchase intention—mediating and moderating effects. Sustainability 13 (8), 4238. doi:10.3390/su13084238
Chen, X., and Yan, N. (2020). A brief overview of renewable plastics. Mater. Today Sustain. 7, 100031. doi:10.1016/j.mtsust.2019.100031
Chiloeches, A., Cuervo-Rodriguez, R., Gil-Romero, Y., Fernandez-Garcia, M., Echeverria, C., and Munoz-Bonilla, A. (2022). Electrospun polylactic acid-based fibers loaded with multifunctional antibacterial biobased polymers. ACS Appl. Polym. Mat. 4 (9), 6543–6552. doi:10.1021/acsapm.2c00928
Cinelli, P., Seggiani, M., Mallegni, N., Gigante, V., and Lazzeri, A. (2019). Processability and degradability of PHA-based composites in terrestrial environments. Int. J. Mol. Sci. 20 (2), 284. doi:10.3390/ijms20020284
Cruz, A. M., and Krausmann, E. (2013). Vulnerability of the oil and gas sector to climate change and extreme weather events. Clim. change 121 (1), 41–53. doi:10.1007/s10584-013-0891-4
de Oliveira, T. A., Oliveira Mota, I., Mousinho, F. E. P., Barbosa, R., Carvalho, L. H., and Alves, T. S. (2019). Biodegradation of mulch films from poly (butylene adipate co-terephthalate), carnauba wax, and sugarcane residue. J. Appl. Polym. Sci. 136 (47), 48240. doi:10.1002/app.48240
Delgado-Arcaño, Y., Mandelli, D., Carvalho, W. A., and Pontes, L. A. M. (2021). Valorization of corncob by hydrolysis-hydrogenation to obtain xylitol under mild conditions. Waste Biomass Valorization 12 (9), 5109–5120. doi:10.1007/s12649-021-01348-7
Deutschmann, R., and Dekker, R. F. (2012). From plant biomass to bio-based chemicals: Latest developments in xylan research. Biotechnol. Adv. 30 (6), 1627–1640. doi:10.1016/j.biotechadv.2012.07.001
Dilkes-Hoffman, L. S., Lant, P. A., Laycock, B., and Pratt, S. (2019). The rate of biodegradation of PHA bioplastics in the marine environment: A meta-study. Mar. Pollut. Bull. 142, 15–24. doi:10.1016/j.marpolbul.2019.03.020
Dwivedi, R., Pandey, R., Kumar, S., and Mehrotra, D. (2020). Poly hydroxyalkanoates (PHA): Role in bone scaffolds. J. oral Biol. craniofacial Res. 10 (1), 389–392. doi:10.1016/j.jobcr.2019.10.004
Eerhart, A., Faaij, A., and Patel, M. (2012). Replacing fossil based PET with biobased PEF; process analysis, energy and GHG balance. Energy Environ. Sci. 5 (4), 6407–6422. doi:10.1039/c2ee02480b
Enomoto, Y., and Iwata, T. (2020). Synthesis of biphenyl polyesters derived from divanillic acid, and their thermal and mechanical properties. Polymer 193, 122330. doi:10.1016/j.polymer.2020.122330
Ferreira, F. V., Cividanes, L. S., Gouveia, R. F., and Lona, L. M. (2019). An overview on properties and applications of poly (butylene adipate-co-terephthalate)–PBAT based composites. Polym. Eng. Sci. 59 (2), E7–E15. doi:10.1002/pen.24770
fibers Ucdtpmsf (2019). Available from: https://solutions.covestro.com/zh/highlights/articles/stories/2019/elastic-textiles-made-from-co2.
Garrison, T. F., Murawski, A., and Quirino, R. L. (2016). Bio-based polymers with potential for biodegradability. Polymers 8 (7), 262. doi:10.3390/polym8070262
Gheorghita Puscaselu, R., Lobiuc, A., Dimian, M., and Covasa, M. (2020). Alginate: From food industry to biomedical applications and management of metabolic disorders. Polymers 12 (10), 2417. doi:10.3390/polym12102417
Gholampour, A., and Ozbakkaloglu, T. (2020). A review of natural fiber composites: Properties, modification and processing techniques, characterization, applications. J. Mat. Sci. 55 (3), 829–892. doi:10.1007/s10853-019-03990-y
Halepoto, H., Gong, T., and Memon, H. (2022). A bibliometric analysis of antibacterial textiles. Sustainability 14 (18), 11424. doi:10.3390/su141811424
Harmsen, P. F., Hackmann, M. M., and Bos, H. L. (2014). Green building blocks for bio-based plastics. Biofuel. Bioprod. Biorefin. 8 (3), 306–324. doi:10.1002/bbb.1468
Harshvardhan, K., Suri, M., Goswami, A., and Goswami, T. (2017). Biological approach for the production of vanillin from lignocellulosic biomass (Bambusa tulda). J. Clean. Prod. 149, 485–490. doi:10.1016/j.jclepro.2017.02.125
Hatti-Kaul, R., Nilsson, L. J., Zhang, B., Rehnberg, N., and Lundmark, S. (2020). Designing biobased recyclable polymers for plastics. Trends Biotechnol. 38 (1), 50–67. doi:10.1016/j.tibtech.2019.04.011
Hosoya, T., Yamamoto, K., Miyafuji, H., and Yamada, T. (2020). Selective production of bio-based aromatics by aerobic oxidation of native soft wood lignin in tetrabutylammonium hydroxide. RSC Adv. 10 (33), 19199–19210. doi:10.1039/d0ra03420g
Huang, X., Tao, X., Zhang, Z., and Chen, P. (2017). Properties and performances of fabrics made from bio-based and degradable polylactide acid/poly (hydroxybutyrate-co-hydroxyvalerate)(PLA/PHBV) filament yarns. Text. Res. J. 87 (20), 2464–2474. doi:10.1177/0040517516671128
Ibrahim, A. M., and Shabeer, T. (2022). Antimicrobial new Schiff base polyesters: Design, thermal, and structural characterizations. Polym. Bull. Berl. 79 (2), 1119–1132. doi:10.1007/s00289-021-03548-6
Jendrossek, D., Schirmer, A., and Schlegel, H. (1996). Biodegradation of polyhydroxyalkanoic acids. Appl. Microbiol. Biotechnol. 46 (5), 451–463. doi:10.1007/s002530050844
Jian, J., Xiangbin, Z., and Xianbo, H. (2020). An overview on synthesis, properties and applications of poly (butylene-adipate-co-terephthalate)–PBAT. Adv. Industrial Eng. Polym. Res. 3 (1), 19–26. doi:10.1016/j.aiepr.2020.01.001
Karthik, T., and Rathinamoorthy, R. (2017). “Sustainable synthetic fibre production,” in Sustainable fibres and textiles (Amsterdam, Netherlands: Elsevier), 191–240.
Khalid, M. Y., and Arif, Z. U. (2022). Novel biopolymer-based sustainable composites for food packaging applications: A narrative review. Food Packag. Shelf Life 33, 100892. doi:10.1016/j.fpsl.2022.100892
Krifa, M., Rajaganesh, S., and Fahy, W. (2019). Perspectives on textile cleanliness–detecting human sebum residues on worn clothing. Text. Res. J. 89 (23-24), 5226–5237. doi:10.1177/0040517519855323
Kumar, A., Mir, S. M., Aldulijan, I., Mahajan, A., Anwar, A., Leon, C. H., et al. (2021). Load-bearing biodegradable PCL-PGA -beta TCP scaffolds for bone tissue regeneration. J. Biomed. Mat. Res. 109 (2), 193–200. doi:10.1002/jbm.b.34691
Li, J., Lai, L., Wu, L., Severtson, S. J., and Wang, W. J. (2018). Enhancement of water vapor barrier properties of biodegradable poly (butylene adipate-co-terephthalate) films with highly oriented organomontmorillonite. ACS Sustain. Chem. Eng. 6 (5), 6654–6662. doi:10.1021/acssuschemeng.8b00430
Li, Y., Zheng, X., and Chu, Q. (2021). Bio-based nanomaterials for cancer therapy. Nano Today 38, 101134. doi:10.1016/j.nantod.2021.101134
Liang, J.-Z., Duan, D. R., Tang, C. Y., Tsui, C. P., and Chen, D. Z. (2013). Tensile properties of PLLA/PCL composites filled with nanometer calcium carbonate. Polym. Test. 32 (3), 617–621. doi:10.1016/j.polymertesting.2013.02.008
Mahmood, N., Yuan, Z., Schmidt, J., and Xu, C. C. (2016). Depolymerization of lignins and their applications for the preparation of polyols and rigid polyurethane foams: A review. Renew. Sustain. Energy Rev. 60, 317–329. doi:10.1016/j.rser.2016.01.037
Mann, G. S., Singh, L. P., Kumar, P., and Singh, S. (2020). Green composites: A review of processing technologies and recent applications. J. Thermoplast. Compos. Mater. 33 (8), 1145–1171. doi:10.1177/0892705718816354
Meereboer, K. W., Misra, M., and Mohanty, A. K. (2020). Review of recent advances in the biodegradability of polyhydroxyalkanoate (PHA) bioplastics and their composites. Green Chem. 22 (17), 5519–5558. doi:10.1039/d0gc01647k
Memon, H., Ayele, H. S., Yesuf, H. M., and Sun, L. (2022). Investigation of the physical properties of yarn produced from textile waste by optimizing their proportions. Sustainability 14 (15), 9453. doi:10.3390/su14159453
Memon, H., et al. (2016). Dyeing recipe optimization for eco-friendly dyeing and mechanical property analysis of eco-friendly dyed cotton fabric: Better fixation, strength, and color yield by biodegradable salts. J. Nat. Fibers 13 (6), 749–758.
Memon, H., Jin, X., Tian, W., and Zhu, C. (2022). Sustainable textile marketing—editorial. Sustainability 14 (19), 11860. doi:10.3390/su141911860
Memon, H., Liu, H., Rashid, M. A., Chen, L., Jiang, Q., Zhang, L., et al. (2020). Vanillin-based epoxy vitrimer with high performance and closed-loop recyclability. Macromolecules 53 (2), 621–630. doi:10.1021/acs.macromol.9b02006
Memon, H., Ranathunga, G. M., Karunaratne, V. M., Wijayapala, S., and Niles, N. (2022). Sustainable textiles in the past "wisdom of the past: Inherited weaving techniques are the pillars of sustainability in the handloom textile sector of Sri Lanka. Sustainability 14 (15), 9439. doi:10.3390/su14159439
Memon, H., Wang, H., Yasin, S., and Halepoto, A. (2018). Influence of incorporating silver nanoparticles in protease treatment on fiber friction, antistatic, and antibacterial properties of wool fibers. J. Chem. 2018, 1–8. doi:10.1155/2018/4845687
Moreira Filho, R. N. F., Vasconcelos, N. F., Andrade, F. K., Rosa, M. d. F., and Vieira, R. S. (2020). Papain immobilized on alginate membrane for wound dressing application. Colloids Surfaces B Biointerfaces 194, 111222. doi:10.1016/j.colsurfb.2020.111222
Oberoi, I. S., Rajkumar, P., and Das, S. (2021). Disposal and recycling of plastics. Mater. Today Proc. 46, 7875–7880. doi:10.1016/j.matpr.2021.02.562
Palamutcu, S. (2017). “Sustainable textile technologies,” in Textiles and clothing sustainability (Berlin, Germany: Springer), 1–22.
Papageorgiou, G. Z. (2018). Thinking green: Sustainable polymers from renewable resources. Basel, Switzerland: MDPI, 952.
Patti, A., Cicala, G., and Acierno, D. (2020). Eco-sustainability of the textile production: Waste recovery and current recycling in the composites world. Polymers 13 (1), 134. doi:10.3390/polym13010134
Pensupa, N., Leu, S-Y., Hu, Y., Du, C., Liu, H., Jing, H., et al. (2017). Recent trends in sustainable textile waste recycling methods: Current situation and future prospects. Top. Curr. Chem. (Cham) 375, 76 doi:10.1007/s41061-017-0165-0
Pfau, M. R., McKinzey, K. G., Roth, A. A., and Grunlan, M. A. (2020). PCL-Based shape memory polymer semi-IPNs: The role of miscibility in tuning the degradation rate. Biomacromolecules 21 (6), 2493–2501. doi:10.1021/acs.biomac.0c00454
Popa, V. I. (2018). “Biomass for fuels and biomaterials,” in Biomass as renewable raw material to obtain bioproducts of high-tech value (Amsterdam, Netherlands: Elsevier), 1–37.
Prambauer, M., Wendeler, C., Weitzenbock, J., and Burgstaller, C. (2019). Biodegradable geotextiles–An overview of existing and potential materials. Geotext. Geomembranes 47 (1), 48–59. doi:10.1016/j.geotexmem.2018.09.006
Qi, X., Ren, Y., and Wang, X. (2017). New advances in the biodegradation of Poly (lactic) acid. Int. Biodeterior. Biodegrad. 117, 215–223. doi:10.1016/j.ibiod.2017.01.010
Quan, Q., Zhang, Y., Piao, H., Zhang, H., and Zhao, J. (2022). Polybutyrolactam (PBY) fiber: A promising biobased and biodegradable fiber fabricated by dry-jet-wet spinning. Polymer 260, 125392. doi:10.1016/j.polymer.2022.125392
Rahman, M. H., and Bhoi, P. R. (2021). An overview of non-biodegradable bioplastics. J. Clean. Prod. 294, 126218. doi:10.1016/j.jclepro.2021.126218
Raj, T., Chandrasekhar, K., Naresh Kumar, A., and Kim, S. H. (2022). Lignocellulosic biomass as renewable feedstock for biodegradable and recyclable plastics production: A sustainable approach. Renew. Sustain. Energy Rev. 158, 112130. doi:10.1016/j.rser.2022.112130
Rajeshkumar, G., Arvindh Seshadri, S., Devnani, G., Sanjay, M., Siengchin, S., Prakash Maran, J., et al. (2021). Environment friendly, renewable and sustainable poly lactic acid (PLA) based natural fiber reinforced composites–A comprehensive review. J. Clean. Prod. 310, 127483. doi:10.1016/j.jclepro.2021.127483
Reid, W. V., Ali, M. K., and Field, C. B. (2020). The future of bioenergy. Glob. change Biol. 26 (1), 274–286. doi:10.1111/gcb.14883
Samantaray, P. K., Little, A., Haddleton, D. M., McNally, T., Tan, B., Sun, Z., et al. (2020). Poly (glycolic acid)(PGA): A versatile building block expanding high performance and sustainable bioplastic applications. Green Chem. 22 (13), 4055–4081. doi:10.1039/d0gc01394c
Shekar, H. S., and Ramachandra, M. (2018). Green composites: A review. Mater. Today Proc. 5 (1), 2518–2526. doi:10.1016/j.matpr.2017.11.034
Shen, L. (2014). “Synthetic fibers from renewable resources,” in Lightweight materials from biopolymers and biofibers (Washington, United States: ACS Publications), 37–52.
Shen, M., Song, B., Zeng, G., Zhang, Y., Huang, W., Wen, X., et al. (2020). Are biodegradable plastics a promising solution to solve the global plastic pollution? Environ. Pollut. 263, 114469. doi:10.1016/j.envpol.2020.114469
Souza, R., de Souza, R. E., Brito, E. O., and Costa Lelis, R. C. (2020). A review on lignin sources and uses. J. Appl. Biotechnol. Bioeng. 7 (3), 100–105. doi:10.15406/jabb.2020.07.00222
Staff, I. E. (2022). Science and business developments. Ind. Biotechnol. 18 (1), 13–19. doi:10.1089/ind.2022.29278.rco
Supaphol, P., Dangseeyun, N., Thanomkiat, P., and Nithitanakul, M. (2004). Thermal, crystallization, mechanical, and rheological characteristics of poly (trimethylene terephthalate)/poly (ethylene terephthalate) blends. J. Polym. Sci. B. Polym. Phys. 42 (4), 676–686. doi:10.1002/polb.10767
Thangavelu, K., and Subramani, K. B. (2016). “Sustainable biopolymer fibers—production, properties and applications,” in Sustainable fibres for fashion industry (Berlin, Germany: Springer), 109–140.
Toray Toray commercializes Ecodear™ N510 (2022). Available from: https://www.toray.com/global/news/details/20220121114129.html.
Tursi, A. (2019). A review on biomass: Importance, chemistry, classification, and conversion. Biofuel Res. J. 6 (2), 962–979. doi:10.18331/brj2019.6.2.3
Ullah, N., et al. (2014). Mechanically robust and antimicrobial cotton fibers loaded with silver nanoparticles: Synthesized via Chinese holly plant leaves. Int. J. Text. Sci. 3, 1–5.
Ullah, N., et al. (2015). Photo-irradiation based biosynthesis of silver nanoparticles by using an ever green shrub and its antibacterial study. Dig. J. Nanomater. Biostruct 10, 95–105.
Urbanek, A. K., Rymowicz, W., Strzelecki, M. C., Kociuba, W., Franczak, L., and Mironczuk, A. M. (2017). Isolation and characterization of Arctic microorganisms decomposing bioplastics. Amb. Express 7 (1), 148–210. doi:10.1186/s13568-017-0448-4
Vieira, A., Vieira, J., Ferra, J., Magalhaes, F., Guedes, R., and Marques, A. (2011). Mechanical study of PLA–PCL fibers during in vitro degradation. J. Mech. Behav. Biomed. Mater. 4 (3), 451–460. doi:10.1016/j.jmbbm.2010.12.006
Vinod, A., Sanjay, M., Suchart, S., and Jyotishkumar, P. (2020). Renewable and sustainable biobased materials: An assessment on biofibers, biofilms, biopolymers and biocomposites. J. Clean. Prod. 258, 120978. doi:10.1016/j.jclepro.2020.120978
Wang, A., Wang, Y., Jiang, T., Li, L., Ma, C., and Xu, P. (2010). Production of 2, 3-butanediol from corncob molasses, a waste by-product in xylitol production. Appl. Microbiol. Biotechnol. 87 (3), 965–970. doi:10.1007/s00253-010-2557-8
Wang, H., Wei, D., Zheng, A., and Xiao, H. (2015). Soil burial biodegradation of antimicrobial biodegradable PBAT films. Polym. Degrad. Stab. 116, 14–22. doi:10.1016/j.polymdegradstab.2015.03.007
Wang, M., Yang, Y., Yuan, K., Yang, S., and Tang, T. (2021). Dual-functional hybrid quaternized chitosan/Mg/alginate dressing with antibacterial and angiogenic potential for diabetic wound healing. J. Orthop. Transl. 30, 6–15. doi:10.1016/j.jot.2021.07.006
Wi, S. G., Kim, H. J., Mahadevan, S. A., Yang, D. J., and Bae, H. J. (2009). The potential value of the seaweed Ceylon moss (Gelidium amansii) as an alternative bioenergy resource. Bioresour. Technol. 100 (24), 6658–6660. doi:10.1016/j.biortech.2009.07.017
Wojnowska-Baryła, I., Kulikowska, D., and Bernat, K. (2020). Effect of bio-based products on waste management. Sustainability 12 (5), 2088. doi:10.3390/su12052088
Xu, Z., Wu, M., Ye, Q., Chen, D., Liu, K., and Bai, H. (2022)., 14. Engineering, 100–112. doi:10.1016/j.eng.2021.06.030 Spinning from nature: Engineered preparation and application of high-performance bio-based fibersEngineering.
Yasin, S., Liu, L., and Yao, J. (2013). Biosynthesis of silver nanoparticles by bamboo leaves extract and their antimicrobial activity. J. Fiber Bioeng. Inf. 6 (6), 77–84. doi:10.3993/jfbi03201307
Yoro, K. O., and Daramola, M. O. (2020). “CO2 emission sources, greenhouse gases, and the global warming effect,” in Advances in carbon capture (Amsterdam, Netherlands: Elsevier), 3–28.
Yu, L., Memon, H., Bhavsar, P., and Yasin, S. (2016). Fabrication of alginate fibers loaded with silver nanoparticles biosynthesized via Dolcetto grape leaves (<I>Vitis vinifera cv.</I>): Morphological, antimicrobial characterization and <I>in vitro</I> release studies. Mat. focus 5 (3), 216–221. doi:10.1166/mat.2016.1317
Zambrano, M. C., Pawlak, J. J., and Venditti, R. A. (2020). Effects of chemical and morphological structure on biodegradability of fibers, fabrics, and other polymeric materials. BioResources 15 (4), 9786–9833. doi:10.15376/biores.15.4.zambrano
Zhang, Q., Song, M., Xu, Y., Wang, W., Wang, Z., and Zhang, L. (2021). Bio-based polyesters: Recent progress and future prospects. Prog. Polym. Sci. 120, 101430. doi:10.1016/j.progpolymsci.2021.101430
Keywords: biobased, biodegradable, renewable, sustainable, synthetics
Citation: Tian W, Huang K, Zhu C, Sun Z, Shao L, Hu M and Feng X (2022) Recent progress in biobased synthetic textile fibers. Front. Mater. 9:1098590. doi: 10.3389/fmats.2022.1098590
Received: 15 November 2022; Accepted: 28 November 2022;
Published: 09 December 2022.
Edited by:
Hafeezullah Memon, Zhejiang Sci-Tech University, ChinaReviewed by:
Munir Hussain, Zhejiang University, ChinaSohail Yasin, Heriot-Watt University, United Kingdom
Copyright © 2022 Tian, Huang, Zhu, Sun, Shao, Hu and Feng. This is an open-access article distributed under the terms of the Creative Commons Attribution License (CC BY). The use, distribution or reproduction in other forums is permitted, provided the original author(s) and the copyright owner(s) are credited and that the original publication in this journal is cited, in accordance with accepted academic practice. No use, distribution or reproduction is permitted which does not comply with these terms.
*Correspondence: Chengyan Zhu, Y3l6aHVAenN0dS5lZHUuY24=