Mineralogy and geotechnical properties of alkaline-activated kaolin with zeolitic tuff and cement kiln dust as landfill liners
- Department of Geology-Applied Geology and Environment, The University of Jordan, Amman, Jordan
Mixtures of variable proportions of kaolin, quartz sand, zeolitic tuff, and cement kiln dust were blended while adding an 8 M sodium hydroxide (NaOH) solution to allow alkali-activation of kaolin and achieve the optimum strength. This study investigated the mineralogy, microstructure, and geotechnical properties of the prepared mixtures. The aim was to produce a sustainable, environmentally friendly landfill liner. The samples were compacted in stainless steel molds to a maximum dry density and optimum moisture content, extruded from the molds, and left to cure in an oven at varying temperatures from 40°C to 80°C for 24 h. The investigations included XRD, SEM, unconfined compressive strength, and hydraulic conductivity tests. Test results showed the development of a hydroxysodalite binder due to the alkali reaction of kaolin, which caused an increase in strength ranging from 20 to 25 MPa depending on the curing temperature. Alkaline activation was effective even at temperatures as low as 40°C. A mixture of 100 units of kaolin, 45 units of sand, 45 units of zeolitic tuff, and 10% by weight cement kiln dust (CKD) with an 8 M sodium hydroxide activator was found to best achieve the required strength and hydraulic conductivity of 10−9 m/s for the landfill liner. The zeolitic tuff with high cation exchange capacity, available in the mixture, absorbs contaminants in the leachate and prevents pollution of the groundwater. The use of cement kiln dust contributes to enhancing strength and solving an acute environmental problem.
1 Introduction
1.1 Alkali activation
Alkali activation of aluminosilicates is a term used to describe the synthesis of alkali-activated binders at low curing temperatures. Intensive research has been ongoing on the use of alkali-activated materials as an alternative to Portland cement (Davidovits, 1991; Provis and Bernal, 2014; Shaqour et al., 2017). This process involves the reaction of a solid aluminum-silicate under alkaline conditions, producing a hardened binder based on a combination of hydrous alkali-aluminum-silicate or alkali-alkali earth-aluminum-silicate phases (Provis, 2018).
Recently, extensive research has been conducted on the application of geopolymers as soil stabilizers, where geopolymers improve the microstructure of the soil and hence its mechanical properties and stability. Kaolinite reacts with sodium hydroxide at low temperatures to form hydroxysodalite, which is a stable and hard material (Shaqour et al., 2017), as illustrated by Eq. 1.
Alshaaer et al. (2007) used chemical polymerization reactions of kaolinite to produce mineral polymers that are suitable for use as construction materials. The reaction mechanism of alkali activation involves three steps: (1) dissolution of aluminosilicate material in a high-pH solution; (2) reorientation of the mobile monomeric species to attain a more thermodynamically stable state; and (3) polycondensation or precipitation of new hydrated aluminosilicate phases (Pacheco-Torgal et al., 2008; Burciaga-Díaz and Escalante-García, 2013).
Kaolinite clay Al2Si2O5 (OH) 4 consists of alternating sheets of SiO4-tetrahedra and Al-octahedra joined by apical oxygen atoms. It forms a major constituent of kaolin deposits that are rich in aluminosilicate, which makes them good precursors for the production of alkali-activated binders. Kaolin deposits are widely available in Jordan and enable the production of alkali-activated cement binders at a reasonable cost, a key consideration for a developing country with limited resources.
1.2 Landfill liners
The purpose of landfill liners is to prevent leakage and subsurface contamination from landfill leachate into groundwater. Landfill liners should satisfy certain criteria to serve their purpose of long-term prevention of contaminants in the leachate from passing through the aquifer. These criteria are as follows:
1) Low hydraulic conductivity, typically less than or equal to 10−9 m/s.
2) Adequate bearing capacity, as the liner material should be sufficiently strong to sustain the stress exerted by the overlying body of waste.
3) Low shrinkage and cracking. The liner should have low shrink-swell and cracking potential. The investigated mixture with the hard alkali-activated binder would reduce the shrink–swell cracking of the landfill liner.
4) High cation exchange capacity (CEC) to absorb contaminants from landfill leachate.
The durability of alkali-activated cement binders is an important parameter that reflects the resistance of materials to short- and long-term performance under weathering action, chemical attack, and abrasion while maintaining their desired properties (Detwiler and Taylor, 2005). In general, the chemical resistance of alkali-activated binder cements (e.g., in acidic or sulfate environments) is generally high; however, further research on the limitations of standardized testing methods when applied to alkali-activated cements is needed (Provis, 2018).
Leachate released from traditional landfills may contain toxic and hazardous materials (Adeolu et al., 2011). The main function of the liner system is to prevent landfill materials and leachate from entering groundwater. Landfill base liner systems usually consist of several components including protective layers, liquid accumulation and separation mechanisms, resistive surface sheets, and absorption amplification layers. A variety of processes, including absorption, resistance, capacitance, and sometimes adsorption and reaction, are commonly used (US. Council N. R., 2007).
Sand/bentonite mixtures are good landfill liners because of their low hydraulic conductivity and linear relationship between the void ratio and hydraulic conductivity (Stewart, 1996). Fly ash-based materials can act as good landfill liners to prevent pollutant migration. Lime fly ash, fly ash, bentonite fly ash, and polymer lime fly ash have been tested (Hettiaratchi et al., 1999).
The hydraulic conductivity of a landfill can increase with the increasing size of the coarser portion, depending on the type of clay material used. The amount of clay can be the controlling factor when it exceeds the holding capacity of the voids in the coarser portions (Sivapullaiah et al., 2000). A bentonite mixture of 20% red earth stabilized with 1% lime or cement can work as a linear material (Sivapullaiah et al., 2003).
Compacted clay that contains red mud (an industrial waste produced by the aluminum industry commonly used to generate alumina from bauxite) was found to have good compression strength and a lower hydraulic conductivity and swelling rate that suit landfill liners (Kalkan, 2006).
Roberts and Shimaoka (2008) studied the use of bentonite-coated gravel as a landfill liner material. The results revealed that low hydraulic conductivities are achievable through proper compaction.
Umar et al. (2015) studied the hydraulic conductivity of compacted lateritic soil partially replaced with metakaolin (MK) for use as a landfill liner. They recorded an improvement in the UCS of the soil with 20% MK, as well as a decrease in the hydraulic conductivity to the order of 6.3 × 10−10 m/s, which satisfies the landfill requirement.
However, traditional bentonite clay liners require thick layers of this material to meet the landfill criteria of high strength, low hydraulic conductivity, and minimum shrinkage. The present study investigated the possibility of producing an alkali-activated binder from mixtures of natural raw materials such as kaolin, quartz sand, zeolitic tuff, and cement dust to act as low-cost, thin landfill liners, meeting the liner criteria with substantial cost reduction. Alkaline-activated kaolin and CKD will contribute to the long-term strengthening of the in-situ bottom liner. The high cation exchange capacity (CEC) of the zeolitic tuff allows it to absorb contaminants from the leachate. The combination of alkali-activated kaolin, zeolitic tuff, and CKD results in the formation of a sustainable, low-cost, strong landfill liner with low hydraulic conductivity and high pollutant absorbance capacity.
2 Materials
2.1 Kaolin
Kaolin deposits are available in Jordan. Khoury and El-Sakka (1986) provided detailed descriptions of their geology, mineralogy, and availability. These deposits are rich in kaolinite, formed by 1:1 stacking of tetrahedral silica sheets and octahedral alumina/gibbsite sheets. The silica sheet in kaolinite is composed of Si4+ at the center and O2− at the vertices. In comparison, the gibbsite sheet has Al3+ ion at the center with OH− at the vertices (Das and Bharat, 2021). Table 1 presents the chemical composition of the raw materials used in the current investigation.

Table 1. Chemical composition of kaolin, zeolitic tuff (ZT), and cement kiln dust (CKD) used in the study.
2.2 Zeolitic tuff
Natural zeolitic tuff is widely available in Jordan and generally contains phillipsite, chabazite, and faujasite as the most abundant zeolite minerals. The zeolite content in these tuffs varies from 20% to 65%. Using simple mineral processing methods, zeolite concentrates of up to 90% can be achieved (Yasin, 1997). Zeolites are an extremely useful group of minerals characterized by a microporous structure and aluminosilicate minerals with high cation exchange capacity (CEC). Natural zeolites have higher CEC values than clay bentonite (normally used as landfill liner bases), with values between 200 and 400 meq/100 g because of their open aluminum-silicate framework structure; thus, they can adsorb contaminants in landfill leachate (Ibrahim and Ingethorpe, 1996). Cations of sodium (Na), potassium (K), calcium (Ca) and magnesium (Mg) held in their structures can be exchanged with contaminants in solution and therefore used for the purification of water and municipal sewage effluent. Zeolitic tuffs can remove harmful cations such as Cu+2, Cr+3, Ni+2, Pb+2, and Zn+2 from industrial wastewater. These materials are used in agriculture as slow water releasers, animal waste treatment agents, and air purification media to reduce the odor intensity and ammonia gas concentration, which reduce the energy required for air ventilation (Dwairi, 1998). Mixtures of zeolitic tuff with small amounts of bentonite have strong bonds that support the microstructure, with the pores filled by the swelling bentonite. A bentonite-embedded zeolite was tested, and the results showed that a bentonite/zeolite ratio of 0.1 satisfied the requirements for a landfill liner (Shaqour et al., 2011).
2.3 Cement kiln dust
Cement kiln dust (CKD) is a fine, highly alkaline industrial waste material generated from the production of cement clinker during the manufacturing of Portland cement, portions of which contain some reactive calcium oxide (Detwiler et al., 1996). Portland cement production generates enormous quantities of CKD, usually left as stockpiles or disposed of in landfills, causing environmental pollution. CKD is an effective stabilizing material, comprising clinker particles with unreacted and partially calcined raw materials. Previous research (Baghdadi et al., 1995; Solanki et al., 2009; Sharma, 2017; Ismeik et al., 2021; Sharo et al., 2021) has shown that the addition of CKD to soil improves its strength and decreases its swelling potential. CKD production is estimated to constitute approximately 15%–20% of clinker production (Kunal and Rajor, 2012), causing an acute environmental problem. It is a source of quicklime (CaO) that interacts with soil in the same manner as Portland cement and calcium hydroxide Ca(OH)2 (Sharo et al., 2021). Some of the potential landfill liner mixtures include CKD to increase mixture strength, reduce shrinkage potential, and make the mixture sustainable and environmentally friendly.
3 Methodology
The current investigation followed the steps below:
1) Collection of samples of the raw materials from geological outcrops identified in El-Hiswa, South Jordan, and Aritain, Northeast Jordan, for kaolin and zeolitic tuff, respectively. CKD was obtained from a local cement factory in Jordan. A mass of 50 kg of kaolin and 50 kg of zeolitic tuff were prepared, crushed, mixed thoroughly, and sieved on sieve No. 10. The part-passing sieve No. 10 was used to prepare the mixtures.
2) Designing and executing a sample preparation program. Raw materials of kaolin, quartz sand, zeolitic tuff, and CKD were used to prepare four mixtures in addition to a control mixture. The main component was kaolin, fixed at 100 units; other additives were set to reasonable, balanced percentages that served the purpose. Mix 1 included 100 units of kaolin and 100 units of quartz sand blended with 10% CKD. The constituents were thoroughly mixed together using an IKA digital dual-range mixer (model IKA-RW20) in a 300 rpm blender for 10 min while adding sodium hydroxide solution. Mix 2 with 100 units of kaolin, 50 units of quartz sand, and 50 units of ZT thoroughly mixed while adding NaOH solution as described for Mix 1. Mix 3 was similar to Mix 2 but included the addition of 10% CKD. Mix 4 consisted of 100 kaolin and 100 ZT with a NaOH solution. Mix 5 constituted 100 units of kaolin with a NaOH solution, which was used as a control mixture. Samples of the mixtures were compacted in stainless steel molds to MDD and OMC and then oven-cured at variable temperatures ranging from 30 to 80°C. The five mixtures and their constituents are given in Table 2.
3) Designing a testing program for representative samples of the different mixtures.
4) Running XRD, SEM, UCS, and hydraulic conductivity tests on selected samples.
Tests were conducted on kaolin collected from the El-Hiswa deposit, located in southern Jordan. The kaolin clay was crushed and homogenized using a cone crusher (TRIO model TC36) equipped with micro filters to obtain a particle size of mostly <20 μm. The plastic limit was determined to be 28% according to ASTM standard D4318-10 (2017). Pure and clean quartz sand (free from impurities), was obtained from a local supplier to be used as an inert filler material to reduce cracking and enhance mixing workability. Zeolitic tuff was used as a contaminant absorbent due to its high CEC. The Si/Al molar ratios for the kaolin-clay and zeolitic tuff-clay mixtures used in this study were 2.8 and 2.6, respectively, which are the same as those calculated by Shaqour et al. (2017). The alkaline reactants of analytical grade and NaOH (≥98.0%) were obtained from Merck (Darmstadt, Germany). The alkaline activating solutions were prepared using deionized Millipore water and used immediately.
Different mixtures were prepared by mixing a fixed percentage of kaolin set to 100 units as a reference for the other constituents. A sodium hydroxide solution was added to each of the mixtures, after which they were set to cure in an oven for 24 h at varying temperatures of 40–80°C for alkali activation. The constituents of the five mixtures are given in Table 2. Some selected samples were oven cured for 3 and 5 days to determine the effect of longer oven curing.
Mineralogical (XRD and SEM) testing was conducted on prepared specimens chipped from the cylindrical samples (25 mm dimeter, 50 mm height) of the mixtures following the standard procedure of each test, as explained in Section 4. Strength and hydraulic conductivity tests were subsequently conducted on full-size cured samples to determine the best mixture for use as a landfill liner (Figure 1).
One mixture was oven-cured at various temperatures (30, 40, 60, and 80°C) to determine the effect of the curing temperature on the developed strength and other geotechnical properties. Tests were also conducted on the cured samples for mineralogical composition, strength, and hydraulic conductivity.
4 Experimental program
In the proposed research, representative samples of mixtures of alkali-activated kaolin, zeolitic tuff, and CKD were tested. XRD, SEM, unconfined compression strength tests, hydraulic conductivity, and other geotechnical property calculations were also conducted on the four mixtures to assess their potential use as sustainable, low-cost, environmentally friendly landfill liners. A fifth mixture of kaolinite and sodium hydroxide alkali solution was prepared and tested as a reference for the other mixtures.
The investigation included determining the chemical and mineral composition as well as the morphology and microstructure of the raw materials and mixtures using X-ray fluorescence (XRF), X-ray diffraction (XRD), scanning electron microscopy (SEM), unconfined compression strength (UCS), and hydraulic conductivity.
4.1 XRD testing
A Rigaku Miniflex automated X-ray diffractometer at the University of Missouri, Kansas City, (UMKC), United States, was used for testing representative samples of the mixtures during the author’s visit as a Fulbright Scholar. Small specimens of each mixture were ground and pulverized in an agate mortar and then dusted onto a silicon wafer zero background plate coated with a thin layer of petroleum jelly. The excess sample powder was then removed by inverting and tapping the mount, leaving a thin layer of powder for analysis. The scans were run at 30 kV and 15 mA using Cu Kα radiation (λ = 1.5418 Å) at a 0.05° step size and 3 s/step (essentially 1° 2θ/minute) from 0.0 to 60° 2θ. The patterns were interpreted using MDI Jade V.8 and Crystal Impact’s Match V.3.15 software.
4.2 SEM testing
The morphology of the alkali-activated materials was investigated by means of a Tescan Vega 3 LMU tungsten filament SEM instrument equipped with a Bruker Quantax EDS (Energy-dispersive spectroscopy) system using Esprit2 software. The SEM images were collected at 6.10–4 Pa with a 20 kV accelerating voltage in back-scattered electron imaging mode. SEM imaging was conducted on platinum-coated specimens using a Quorum-Emitech K550X sputter coater. Tests were carried out at the laboratories of the Earth and Environmental Sciences at UMKC.
4.3 Unconfined compressive strength testing
Unconfined compressive strength tests were conducted to evaluate the developed strength of the various NaOH-based, alkali-activated mixtures. The strength test was performed using a universal unconfined compression testing machine in the Materials Engineering Laboratory at the Department of Geology, The University of Jordan, with a strain rate of 1 mm/min.
4.4 Hydraulic conductivity testing
DigiFlow-K is an automated hydraulic conductivity testing system designed specifically for geotechnical testing. The DigiFlow-K system, manufactured by GEOTAC’s TestNet system, provides automation through data acquisition and control. A TestNet system is a series of interconnected modules that are connected to a computer via a serial (COM) port. TestNet employs Distributed Data Acquisition and Control (DDAC), which offers significant advantages over conventional methods used for data collection and test control. A typical data acquisition system consists of a centrally located data logger/controller.
Selected samples of the mixtures were tested for hydraulic conductivity at the Department of Civil Engineering (UMKC, USA) using a triaxial cell unit that was connected to water pumps that applied suitable cell pressures. Special sample holders were designed and fabricated to suit small samples with a 25-mm diameter and 50-mm height. The tested sample was inserted into a rubber membrane and installed in the tri-axial cell after being fixed to the holders with O-rings. The sample was then saturated before the hydraulic conductivity test started. The sample information and test data were input into the software, after which the test commenced to determine the hydraulic conductivity automatically. The tests took a few days to complete.
5 Results and discussion
5.1 XRD mineralogical test results
X-ray diffraction (XRD) was used to determine the mineral content of the raw materials and various mixtures and to identify any developed binding material because of the alkali reaction during oven curing. X-ray diffraction results showed that new mineral phases developed during alkaline activation reactions that caused bonding and cementation.
Figure 2 shows the XRD diffractogram of the kaolin deposit in Jordan. The major constituents are kaolinite, quartz, and muscovite. Kaolinite is the source of aluminum oxide, which is the precursor for alkali activation with sodium hydroxide. The kaolin diffractogram shows other constituents, i.e., quartz, gypsum, and illite. The fact that the quartz peak appears higher and more distinctive than the kaolinite peak reflects the crystallinity rather than the quantity.
The zeolitic tuff contains chabazite (zeolite mineral) as the main constituent, together with hematite, in addition to augite and chlorite, which are common in volcanic tuff (Figure 3).
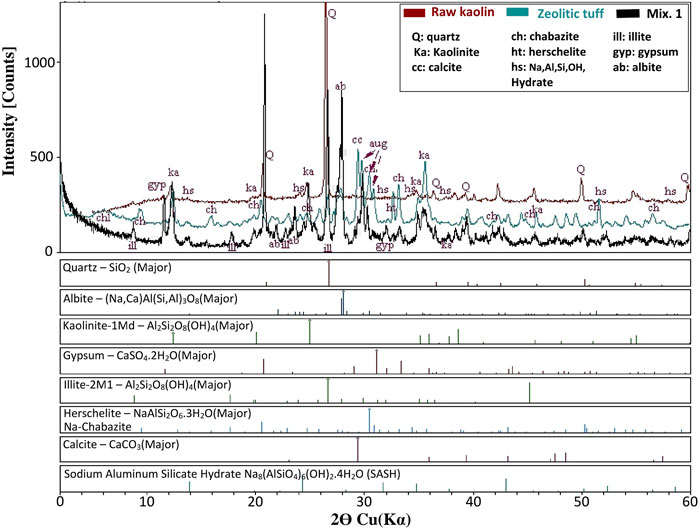
Figure 3. XRD diffractogram with raw kaolin and zeolitic tuff compared to Mix1 oven cured at 80°C. Na-Al-Si-OH Hydrate is Sodium Aluminum Silicate Hydroxide Hydrate.
Figure 4 shows the XRD diffractograms of mixtures 1 to 5, showing that the mineral kaolinite, is least in Mix 5, because most of it was transferred to the sodium-aluminom-silicate hydrate (the binder) that is evident in Mix 5. Mix 1 at 80°C contains kaolinite, but it has a lower intensity than that of the raw kaolin due to the consumption of kaolinite by the reaction to form the binder sodium aluminum silicate hydrate (SASH), which is evident in the XRD diffractograms of all the mixtures.
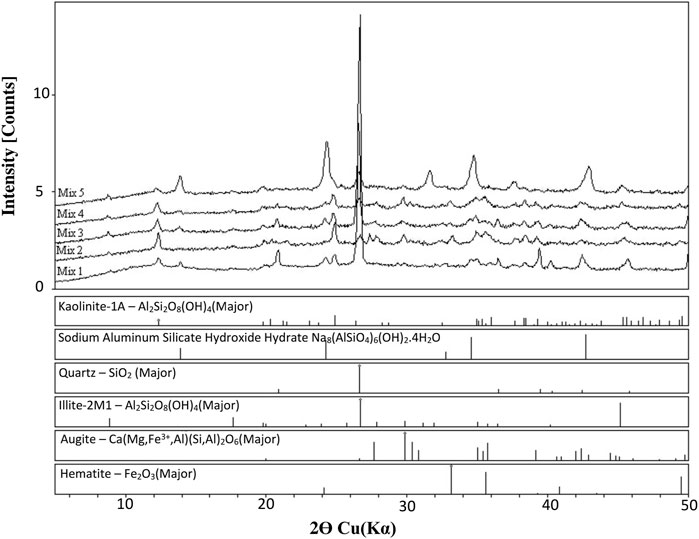
Figure 4. XRD diffractograms of mixes 1 to 5 cured at 80°C showing development of binding material sodium-aluminum-silicate-hydrate.
Quartz is available in all the mixture 1 to 4, but not in Mix 5, where there was no quartz sand. Similar peak heights of sodium-aluminum-silicate hydrate are observed in Mixes 1, 3, and 4; more evident in Mix 2 and most evident for Mix 5. This could be explained by the initial contents of the mixtures and the influence of such constituent interference on the alkali reaction with kaolinite to produce the binder.
Mix samples were left at room temperature for 1, 7, and 28 days after oven curing to check for any strength changes. The XRD patterns of these samples are presented in Figure 5. No difference in mineral composition was observed; however, strength changes were detected, as discussed in the UCS section.
5.2 Scanning electronic microscopy (SEM) tests and results
Specimens of representative samples were prepared and mounted in an SEM instrument in order to study the microstructure after alkali activation. Figure 6 shows a photomicrograph of Mix 1 (sand, kaolin, and sodium hydroxide), which shows slightly etched kaolinite crystals and the binding material sodium-aluminum silicate hydrate (SASH). Figure 7 illustrates the development of the binding material (SASH) in Mix 2. Etched kaolinite particles and the binding material SASH are evident in Mix 3, as illustrated in the photomicrograph given in Figure 8. Mapping via SEM showed that aluminum, silicon, oxygen, sodium, calcium, potassium, magnesium, and iron were the main elements detected in Mix 3, which reflected the original composition of the mixture and the newly developed binding material.
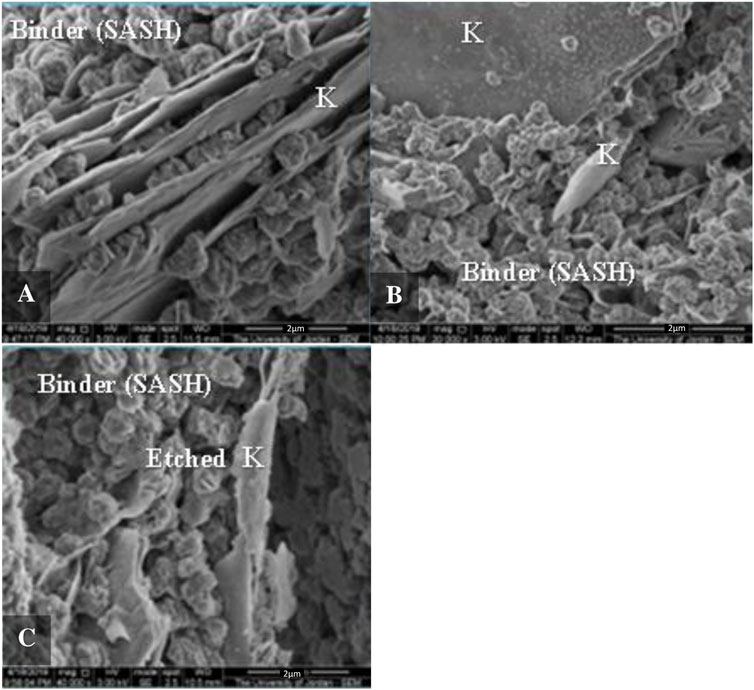
Figure 7. SEM Photomicrograghs for mix 2, prepared by oven drying at 80 C, showing reaction product binding material (SASH), and etched kaolinite (A–C). K: kaolinite, SASH: sodium aluminum silicate hydrate.
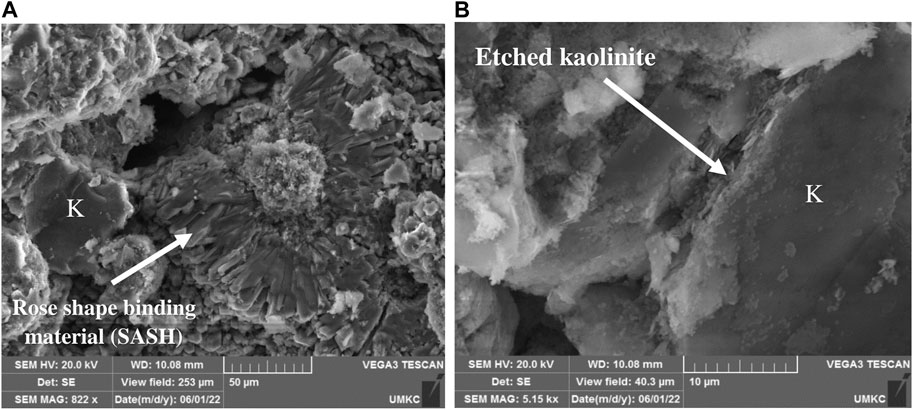
Figure 8. SEM Photomicrograghs for mix 3, prepared by oven drying at 80 C, showing reaction product of binding material (SASH), and etched kaolinite (K), K: Kaolinite, SASH: Sodium-Aluminum- Silicate- Hydrate.
5.3 Unconfined compression strength testing and results
Cylindrical representative samples of Mixes 1 to 5 were prepared by compacting the calculated mass of each mixture, in a stainless steel mold 25 mm in diameter and 50 mm in height. After compacting the sample in the stainless steel mold to the required density, it was then extruded carefully and subjected to curing in an oven for a period of 24 h. Alkali activation occurs through the reaction between aluminum oxides in kaolinite minerals and sodium hydroxide, which results in the formation of the binding material sodium-aluminum silicate hydrate (SASH).
Figure 9 shows the UCS test results for samples from Mixes 1, 2, 3, and 4. Mix 1 had the highest strength (23.6 MPa), followed by Mix 3 (22.6 MPa) and Mix 2 (21.5 MPa), while Mix 4 had the lowest strength (10.1 MPa). Mixes 1 and 3 have quartz sand that is characterized by high density and hardness, which contributes to the high strength, in addition to cement dust (CKD), which promotes cementation. Mix 3 has slightly less strength than Mix 1 because of the presence of zeolitic tuff, which is less dense than quartz sand. However, Mix 3 is more suitable for use as a landfill liner than Mix 1 because it contains zeolitic tuff, which can absorb pollutants.
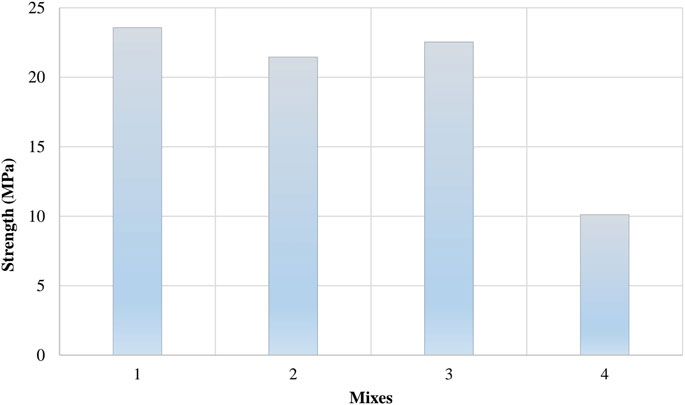
Figure 9. Unconfined compressive strength test results on the 4 mixes at 1 day room temp (RT) curing after the oven curing.
Figure 10 shows the UCS test results for samples of Mixes 1, 2, and 3 after 1, 7, and 28 days, respectively at room temperature (RT) curing after the oven curing. The results show a general decrease in strength with increasing RT curing time, which indicates that the standards for testing Portland cement concrete do not apply to alkali-activated concrete and that additional investigations are needed to establish specific standards for testing alkali-activated concrete or morters. This confirms the conclusion of Provis (2018). It may be a good idea if the samples are kept in an alkaline solution at room temperature, for a certain period of time, such that the alkali reaction goes through all stages and comes to an end. However, such a decrease in strength due to room temperature curing should not affect the strength of the mixture when applied to landfill liners because the mixture is under load and, in fact, is expected to be under hot conditions, which will allow further alkali reactions that will cause the mixture to develop additional strength.
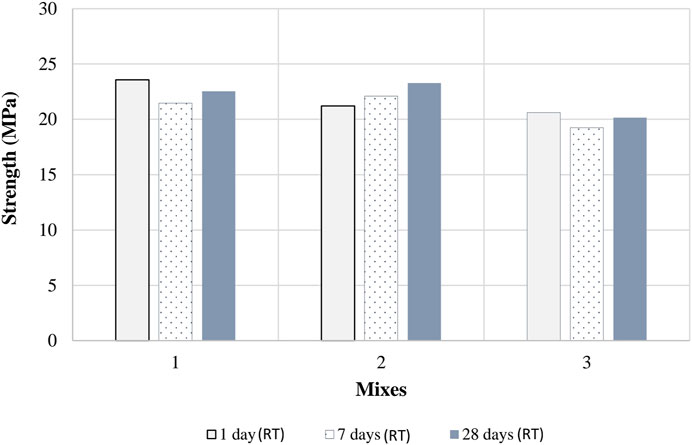
Figure 10. Unconfined compressive test results on samples of mixes 1, 2, and 3 after 1, 7, 28 days at room temperature (RT).
5.4 Hydraulic conductivity tests and results
Initially, prepared alkaline-activated cylindrical samples of Mixes 2, 3, and 4 were first set to saturation in the triaxial cell-permeability device for approximately 1 week. After saturation, the system was programmed by inputting sample information, including diameter, height, and other identification parameters. The system was then set to run the hydraulic conductivity test. Each test took approximately 2 weeks from saturation to permeation.
Mixes 2 and 3 were short-listed as good candidates for use as landfill liners. Hydraulic conductivity tests were also conducted on representative samples of these mixtures.
Figures 11, 12 show hydraulic conductivities of 1.0 × 10−6.3 cm/s (1.0 × 10−8.3 m/s) and 1.0 × 10−6.5 cm/s (1.0 × 10−8.5 m/s) for representative samples of mixtures 2 and 4, respectively.
A representative sample of Mix 3 had a hydraulic conductivity of 1.0 × 10−7 cm/s (1.0 × 10−9 m/s) when tested after 1 day of room temperature (RT) curing after oven curing, which satisfies the requirements for landfill liners (Figure 13).
As a result of unconfined compressive strength tests and hydraulic conductivity tests together with the constituent materials, Mix 3 was found to be the most suitable mixture for satisfying the requirements of sustainable, cost-effective landfill liners. The addition of cement kiln dust to Mix 3 contributes to its low hydraulic conductivity and high strength, which increase its durability and sustainability.
6 Conclusion and recommendations
1. Test results show that Mixes 1, 2, and 3 meet the requirements for landfill liners; however, Mix 3 (with 100 units of kaolin, 45 units of quartz sand, 45 units of zeolitic tuff, and 10% by weight CKD) is the most suitable low-cost, sustainable, and environmentally friendly mixture for use as landfill liners.
2. Tests showed that new phases developed during alkaline activation reactions, causing bonding and cementation to develop strengths ranging from 20 to approximately 25 MPa, depending on the curing temperature.
3. Alkali-activated kaolin is an excellent, environmentally friendly product that achieves a hydraulic conductivity as low as 10−9 m/s, which is required for landfill liners.
4. Alkaline activation is effective even at temperatures as low as 40°C for producing mixtures with reasonably high strength and low hydraulic conductivity that are required for use as landfill liners. The overlying dump material on top of the bottom liner can increase the temperature to more than 40°C. This allows continuation of the alkali activation process during the lifetime of the landfill, leading to an increase in strength and a decrease in hydraulic conductivity of the proposed liner. This makes the proposed landfill liner an excellent choice.
5. The use of cement kiln dust contributes to strengthening and reducing the hydraulic conductivity of the mixture. This approach also contributes to solving the acute environmental problems that cement dust causes, thereby reducing management and disposal costs for owners.
Further research should be conducted on these materials, the possibility of running a pilot test should be explored, and the applicability and performance of the proposed mixture should be tested by monitoring the leachate composition and adsorption capability of the zeolitic tuff component in the mixture.
Scope statement
The main objective of this study was to identify a suitable mixture of alkali-activated kaolin, sand, zeolitic tuff (ZT), and cement kiln dust (CKD) that works as a sustainable, environmentally friendly landfill liner. Test samples of variable mixtures were prepared to the maximum dry density (MDD) and optimum moisture content (OMC) in stainless steel molds and left to cure in an oven at varying temperatures ranging from 40°C to 80°C. Tests examined mineralogy, morphology, micro-texture, strength, and hydraulic conductivity through running X-ray diffraction (XRD), scanning electron microscopy (SEM), unconfined compressive strength (UCS), and hydraulic conductivity tests. Tests indicated the development of new mineralogical phases that caused bonding and cementation, leading to an increase in strength and a decrease in the hydraulic conductivity of the landfill liner. The load of the overlying dump material on top of the proposed lining layer can reach such a temperature to allow alkali activation to achieve the strength and low hydraulic conductivity required for use as a long-term sustainable landfill liner. This approach fits with the structural material section of the “Frontiers in Materials” journal.
Data availability statement
The original contributions presented in the study are included in the article/Supplementary material, further inquiries can be directed to the corresponding author.
Author contributions
FS: Conceptualization, Data curation, Formal Analysis, Funding acquisition, Investigation, Methodology, Project administration, Resources, Supervision, Validation, Visualization, Writing–original draft, Writing–review and editing.
Funding
The author(s) declare that financial support was received for the research, authorship, and/or publication of this article by the University of Jordan.
Acknowledgments
The author wishes to thank the Deanship of Scientific Research at the University of Jordan for funding the research project and facilitating tests at the Department of Geology. We thank the University of Jordan for granting the author sabbatical leave to complete this research project at UMKC and the Fulbright Mission-Jordan for their grant to the author to work at the University of Missouri, Kansas City, United States, for 9 months to complete the testing program. Thanks are given to Dr. Mohannad Ismeik for reviewing the manuscript. The author thanks Professor James Murowchick for his help in running the XRD and SEM tests at the Department of Earth and Environmental Sciences at UMKC. Thanks to Professor John Kevern for his help during the author’s stay at UMKC. Thanks also to Dr. Megan Hart for her help in facilitating the running of the hydraulic conductivity tests at the Department of Civil Engineering, UMKC.
Conflict of interest
The author declares that the research was conducted in the absence of any commercial or financial relationships that could be construed as a potential conflict of interest.
Publisher’s note
All claims expressed in this article are solely those of the authors and do not necessarily represent those of their affiliated organizations, or those of the publisher, the editors and the reviewers. Any product that may be evaluated in this article, or claim that may be made by its manufacturer, is not guaranteed or endorsed by the publisher.
References
Adeolu, A. O., Ada, O. V., Gbenga, A. A., and Adebayo, O. A. (2011). Assessment of groundwater contamination by leachate near a municipal solid waste landfill. Afr. J. Environ. Sci. Technol. 5 (11), 933–940. doi:10.5897/AJEST11.272
Alshaaer, M., Esaifan, M., Khoury, H., Wastiels, J., and Cuypers, H. (2007). “Chemical stabilization of local materials in Jordan for construction purposes,” in Proceedings of the 8th International Conference on Concrete, Hammamat–Tunisia, November, 2007.
ASTM D4318 (2017). Standard test methods for liquid limit, plastic limit, and plasticity index of soils. ASTM D 4318. West Conshohocken, PA, USA: ASTM International.
Baghdadi, Z. A., Fatani, M. N., and Sabban, N. A. (1995). Soil modification by cement kiln dust. J. Mater. Civ. Eng. 7, 218–222. doi:10.1061/(ASCE).0899-1561(1995)7:4(218)
Burciaga-Diaz & Escalante-Garcia (2013). Structure, mechanisms of reaction, and strength of an alkali-activated blast furnace slag. J. Am. Ceram. Soc. 96 (12), 3677–3948. doi:10.1111/jace.12620
Das, P., and Bharat, T. V. (2021). Kaolin based protective barrier in municipal landfills against adverse chemo-mechanical loadings. Sci. Rep. 11, 10354. doi:10.1038/s41598-021-89787-z
Davidovits, J. (1991). Geopolymers: inorganic polymeric new materials. J. Therm. Analysis 37, 1633–1656. doi:10.1007/BF01912193
Detwiler, R. J., Bhatty, J. I., and Bhattacharja, S. (1996). Supplementary cementing materials for use in blended cements. Res. Dev. Bull. RD112T, Portland Cem. Assoc. Skokie, Ill.,
Detwiler, R.J., and Taylor, P.C. (2005). Portland Specifier's Guide to Durable Concrete, Global Cement and concrete Association gcca, Skokie, Illinois, USA.
Dwairi, M. (1998). Evaluation of Jordanian zeolite tuff as A controlled slow-release fertilizer for NH+4. Environ. Geol. 34, 1–4. doi:10.1007/s002540050251
Hettiaratchi, J. P. A., Achari, G., Joshi, R. C., and Okoli, R. E. (1999). Feasibility of using fly ash admixtures in landfill bottom liners or vertical barriers at contaminated sites. J. Environ. Sci. Health - Part A Toxic/Hazardous Subst. Environ. Eng. 34 (10), 1897–1917. doi:10.1080/10934529909376938
Ibrahim, K., and Ingethorpe, S. D. J. (1996). Mineral processing characteristics of natural zeolites from the aritayn formation of Northeast Jordan. Miner. Deposita 31 (6), 589–596. doi:10.1007/bf00196140
Ismeik, M., Shaqour, F., and Hasan, S. (2021). Geotechnical evaluation of clayey soils amended with cement kiln dust during freeze‒thaw cycling. Arabian J. Geosciences 14 (19), 2023. doi:10.1007/s12517-021-08144-6
Kalkan, E. (2006). Utilization of red mud as a stabilization material for the preparation of clay liners. Eng. Geol. 87 (3–4), 220–229. doi:10.1016/j.enggeo.2006.07.002
Khoury, H. N., and El-Sakka, W. (1986). Mineralogical and industrial characterization of the Batn El-Ghoul clay deposits, southern Jordan. Appl. Clay Sci. 1 (4), 321–351. doi:10.1016/0169-1317(86)90009-8
Kunal, S. R., and Rajor, A. (2012). Use of cement kiln dust in cement concrete and its leachate characteristics. Resour. Conservation Recycl. 61, 59–68. doi:10.1016/j.resconrec.2012.01.006
Pacheco-Torgal, F., Castro-Gomes, J., and Jalali, S. (2008). Alkali-activated binders: a review Part 1. Historical background, terminology, reaction mechanisms and hydration products. Constr. Build. Mater. 22, 1305–1314 1309.
Provis, J. (2018). Alkali-activated materials. Cem. Concr. Res. 114, 40–48. doi:10.1016/j.cemconres.2017.02.009
ProvisBernal, J. L. S. A. (2014). Geopolymers and related alkali-activated materials. Annu. Rev. Mater. Res. 44, 299–327. doi:10.1146/annurev-matsci-070813-113515
Roberts, A. A., and Shimaoka, T. (2008). Analytical study on the suitability of using bentonite-coated gravel as a landfill liner material. Waste Manag. 28 (12), 2635–2644. doi:10.1016/j.wasman.2008.01.020
Shaqour, F., Ismeik, M., and Esaifan, M. (2017). Alkali activation of natural clay using a Ca(OH)2/Na2CO3 alkaline mixture. Clay Min. 52, 485–496. doi:10.1180/claymin.2017.052.4.06
Shaqour, F., White, S., and Webb, J. (2011). Geotechnical characterization of geomaterial blends with zeolitic tuffs for use as landfill liners. Bull. Eng. Geol. Environ. 70 (4), 691–697. doi:10.1007/s10064-011-0375-6
Sharma, R. K. (2017). Laboratory study on stabilization of clayey soil with cement kiln dust and fiber. Geotech. Geol. Eng. 35, 2291–2302. doi:10.1007/s10706-017-0245-5
Sharo, A., Shaqour, F., and Ayyad, J. (2021). Maximizing strength of CKD–stabilized expansive clayey soil using natural zeolite. KSCE J. Civ. Eng. 25, 1204–1213. doi:10.1007/s12205-021-0786-2
Sivapullaiah, P. V., Lakshmi Kantha, H., and Madhu Kiran, K. (2003). Geotechnical properties of stabilised Indian red earth. Geotechnical Geol. Eng. 21 (4), 399–413. doi:10.1023/B:GEGE.0000006051.02215.a6
Sivapullaiah, P. V., Sridharan, A., and Stalin, V. K. (2000). Hydraulic conductivity of bentonite-sand mixtures. Can. Geotechnical J. 37 (2), 406–413. doi:10.1139/t99-120
Solanki, P., Khoury, N., and Zaman, M. (2009). Engineering properties and moisture susceptibility of silty clay stabilized with lime, class C fly ash, and cement kiln dust. J. Mater. Civ. Eng. 21 (12), 749–757. doi:10.1061/(ASCE)0899-1561(2009)21:12(749)
Stewart, M., Stewart, D. I., and Cousens, T. W. (1996). Predicting the properties of bentonite-sand mixtures. Clay Miner. 31 (2), 243–252. doi:10.1180/claymin.1996.031.2.10
Umar, S. Y., Elinwa, A. U., and Matawal, D. S. (2015). Hydraulic conductivity of compacted lateritic soil partially replaced with metakaolin. J. Environ. Earth Sci. 5 (4), 53–65.
US. Council N. R. (2007). Assessment of the performance of engineered waste containment barriers. Washington, D.C., United States: National Academies Press.
Keywords: kaolin, alkaline activation, zeolitic tuff, cement kiln dust (CKD), landfill liners, unconfined compressive strength (UCS), hydraulic conductivity
Citation: Shaqour F (2024) Mineralogy and geotechnical properties of alkaline-activated kaolin with zeolitic tuff and cement kiln dust as landfill liners. Front. Mater. 11:1368618. doi: 10.3389/fmats.2024.1368618
Received: 10 January 2024; Accepted: 10 April 2024;
Published: 26 April 2024.
Edited by:
Muhannad T. Suleiman, Lehigh University, United StatesReviewed by:
Susan White, La Trobe University, AustraliaReyad Al Dwairi, Tafila Technical University, Jordan
Copyright © 2024 Shaqour. This is an open-access article distributed under the terms of the Creative Commons Attribution License (CC BY). The use, distribution or reproduction in other forums is permitted, provided the original author(s) and the copyright owner(s) are credited and that the original publication in this journal is cited, in accordance with accepted academic practice. No use, distribution or reproduction is permitted which does not comply with these terms.
*Correspondence: Fathi Shaqour, f.shaqour@ju.edu.jo