Performance experiment of ultra high temperature cementing slurry system
- The No. 2 Cementing Branch of PetroChina Bohai Drilling Engineering Company, Tianjin, China
Introduction: The escalating pursuit of oil and gas reserves in China has led to increasingly deep and ultra-deep well drilling, encountering extreme temperatures that challenge the heat resistance capabilities of cement slurries. This study addresses the critical need for high-performance cement slurries capable of withstanding ultra-high temperatures during drilling and completion operations.
Methods: A novel ultrahigh temperature conventional density (UHTE) cement slurry was formulated by incorporating high-temperature-resistant additives, namely DRF-1S and DRH-2L. An indoor testing framework was established to assess the slurry’s performance across various parameters: Evaluating the slurry’s ability to maintain uniform consistency over time. Measuring the amount of free water separated from the slurry under simulated downhole conditions. Assessing the slurry’s transition from fluid to solid state over time. Determining the compressive strength and other mechanical attributes after curing at elevated temperatures.
Results: The experimental findings revealed the following: An optimal silica sand dosage of 50% was found to enhance the overall performance of the UHTE cement slurry. The developed UHTE cement system, fortified with DRF-1S and DRH-2L, demonstrated effective functionality within a temperature range of 180°C to 210°C, representing a significant advancement in high-temperature resistance. The slurry maintained API water loss below 100 mL, ensuring minimal fluid loss during placement. Adjusted thickening time allowed for adequate pumping and placement without premature setting. Settlement stability was maintained below 0.04 g/cm3, indicating excellent homogeneity and stability. Incorporation of the anti-decay material DRB-3S ensured a 28-day compressive strength exceeding 50 MPa at 210°C, signifying robust structural integrity under extreme thermal conditions.
Discussion: This research provides a robust foundation for the practical application of UHTE cementing technology in ultra-high temperature environments. The successful development of the UHTE cement slurry system, characterized by its superior temperature resistance, controlled water loss, optimized thickening behavior, and exceptional mechanical properties, paves the way for field trials and further enhancements. Future work will involve testing the effectiveness of the new additive combination under actual downhole conditions and refining the formulation to develop an even more advanced UHTE cementing additive. These advancements will contribute to enhanced wellbore integrity, improved drilling efficiency, and increased safety in deep and ultra-deep oil and gas exploration endeavors in China.
1 Introduction
An important energy and strategic resource in China, oil and gas resources are the main component of the national economy and play a vital role in the economic and national strategic development (Hall, 1960; Levine et al., 2002; Tang et al., 2007). With the vigorous development of oil and gas in China, the development of major oil fields has entered the middle and late stages, and it is difficult to find new large oil and gas resources in shallow surface exploration (Gasch et al., 2005; Monteverde et al., 2008; Fahrenholtz and Hilmas, 2017; Tao et al., 2020). With the continuous improvement of drilling technology and the deepening of oilfield exploration and development, the number of high temperature deep wells and ultra deep wells with formation temperature exceeding 180°C is increasing, and higher requirements are put forward for the performance of cement slurry under high temperature and ultra-high temperature (Guillot, 1990; Velayati et al., 2015; Golla et al., 2020; Fang et al., 2021). Cementing cement slurry is a key material in cementing engineering. In order to meet the requirements of high temperature and ultra-high temperature cementing, the research and development of ultra-high temperature cementing cement slurry must be carried out (Sabins et al., 1982; Liu et al., 2006; Wuchina et al., 2007; Tao et al., 2019). The ultra-high temperature cement slurry system has also become a major difficulty in the development of the oil and gas industry, and has become a major research topic (Cheng et al., 2022; Abbas et al., 2013; Cheng et al., 2022; Gaurina-Međimurec et al., 2021).
The research of ultra-high temperature cementing slurry system mainly focuses on ultra-high temperature additives and slurry system design. Some researchers aimed at high temperature and ultra-high temperature cementing technology problems, further optimized the polymerization monomer and molecular weight distribution of retarder to develop retarders that can be used at ultra-high temperature through early research on high-temperature resistant cement slurry, to ensure the safety of cementing construction, and developed ultra-high temperature cement slurry stabilizer and anti-strength decline materials (Zhang et al., 2021; Chang et al., 2019; Son et al., 1987; Wu et al., 2001). Through additive materials and additive systems, they developed ultra-high temperature cement slurry systems that can meet the requirements of ultra-high temperature cementing, Meet the requirements of high temperature cementing. Some researchers have carried out the research on the fluid loss additive of ultra-high temperature additives, and designed the fluid loss additive products with molecular weight and molecular structure through molecular design. Different molecular design ideas will form a variety of synthetic polymer fluid loss additives, and AMPS based polymer fluid loss additive system is the main research direction of the fluid loss additive. Some researchers have carried out the research on the retarder of ultra-high temperature admixture, combined monomers with different functions through polymerization technology, and synthesized the most stable retarder products with ideal performance under the guidance of molecular design theory. The performance of AMPS based polymer products is the best (Ricky et al., 2022; Xiaofeng et al., 2019; Yan et al., 2017). Some researchers have developed the design of high temperature cement slurry. For the cementing of oil and gas wells with bottom hole static temperature higher than 120°C, 35%–40% fine sand or powder should be added to the cement slurry, so as to maintain the good strength of the cement paste and prevent the strength decline of the cement paste under high temperature conditions (Mao et al., 2015; Chang et al., 2019). Some researchers have studied the ultra-high temperature and high-density cement slurry system. The bottom of the well is in a high-pressure environment during high-temperature cementing of deep wells. In order to maintain the balance of wellbore pressure, the pressure of the liquid column in the well is always in balance with or slightly higher than the formation pressure. Therefore, high-density or ultra-high density cement slurry is required. By adding high-density weighting materials, the water cement ratio is reduced, and the bulk density of solid materials is increased the ultra-high temperature and high density cement slurry can be prepared by improving the water density of the slurry. Some researchers have studied ultra-high temperature and low-density cement slurry systems, usually adding hollow glass beads as a reducing agent to meet the requirements of reducing the density of cement slurry for well cementation, and applied it to seal high temperature and leaky formations. Some researchers have studied the ultra-high temperature anti gas channeling cement slurry system. At present, the anti gas channeling cement slurry system is mainly used for high temperature well cementing. The main anti gas channeling additives include thixotropic additives, delayed cementitious materials, and additives that enhance the gas channeling resistance of cement slurry, so as to effectively solve the problem of annular air channeling in cementing under high temperature and pressure. Some researchers have carried out different high-temperature cement slurry performance evaluations. According to the actual working conditions of oil and gas wells, they have developed flexible cement slurry, latex cement slurry, elastoplastic cement slurry, salt water cement slurry, etc. for cementing operations to meet the high-temperature cementing needs of different geological conditions. Some researchers have carried out experimental research on high temperature cement slurry for well cementation to solve the problems such as difficult adjustment of thickening time of high temperature cement slurry under high temperature conditions, large water loss of high temperature cement slurry, abnormal test thickening curve, core coating of cement slurry, strength attenuation, poor settlement stability, etc. At the same time, high temperature cement slurry will have short thickening time in the lower high temperature section, long thickening time in the upper low temperature section, and super retarding after well cementation, it has a great impact on the quality of cementing and subsequent drilling operations. Therefore, it is necessary to develop a comprehensive ultra-high temperature cementing slurry system to meet the requirements of on-site ultra-high temperature cementing operations. The working condition of ultra-high temperature cementing is complex, which puts forward higher requirements for the performance of cementing cement slurry. Cementing cement slurry should not only meet the requirements of high temperature thickening time, but also maintain a certain slurry stability and mechanical strength under high temperature conditions to improve the cementing quality. Based on the requirements of ultra-high temperature cementing operation on the performance of cement slurry, this paper configures high-temperature water loss reducer DRF-1S, high-temperature retarder DRH-2L and other supporting high-temperature cement additives to form ultra-high temperature conventional density cement slurry, and carries out indoor test research to evaluate the settlement stability, water loss performance, thickening performance and mechanical performance of ultra-high temperature cement slurry, An ultra-high temperature cement slurry system is established for oil and gas well cementing, which provides theoretical data support for ultra-high temperature cement slurry cementing technology.
2 Design idea of ultra-high temperature cement slurry system and development of supporting additives
2.1 Design ideas
The main technical difficulties of ultra-high temperature cement slurry system are to solve the problems that the thickening time of cement slurry under high temperature or ultra-high temperature can meet the requirements of construction safety, the water loss of cement slurry is strictly controlled in a lower range, and the settlement stability needs to meet the design requirements. Based on the design idea of ultra-high temperature cement slurry system, this paper has carried out a lot of experimental research, and developed fluid loss additive DRF-1S, retarder DRH-2L, stabilizer DRK-3L, anti-aging agent DRB-3S, etc. at 180°C. The additives used in this paper are mainly based on the existing high temperature additives, and the experiment is updated on the basis of the original (Figure 1).
2.2 Optimization of synthetic additives
The fluid loss additive DRF-1S is a kind of multicomponent copolymer, which is mainly made by free radical polymerization in aqueous solution. The sulfonic acid group, amide group and chain rigid group are introduced into the main chain of its molecule. The sulfonic acid group mainly plays a good role in thermal stability and salt resistance, ensuring a strong hydration capacity, and ensuring that the prepared copolymer fluid loss additive maintains a good resistance to high temperature and salt. Amide group has strong adsorption capacity and strong hydration. The chain rigid monomer makes the thermal movement of the molecular chain of the fluid loss additive slow at high temperatures, and also improves the temperature resistance of the molecular chain. The preferred retarder is an anti high temperature retarder DRH-2L, which is composed of 2-acrylamido-2-methylpropanesulfonic acid, fumaric acid and itaconic acid copolymer PAC and ethylenediamine tetramethylene phosphonate sodium. The anti high temperature retarder is a five-component copolymer prepared by the polymerization of aqueous solution free radicals. The sulfonic acid group, dicarboxylic group, chain rigid group, cationic group, etc. are introduced into the main chain of the molecule. These groups endow the molecular chain of the retarder with excellent anti high temperature and retarding properties. At the same time, the performance of the retarder is optimized by optimizing the polymerization process, molecular weight and molecular weight distribution. The temperature resistance of the retarder can reach 180 °C. When it is combined with the fluid loss reducer, the temperature resistance can reach 250°C, which has a certain dispersing effect on the cement slurry. At the same time, the increase of the dosage by 0.8%–2.0% has no effect on the compressive strength of the cement paste. When the temperature is 30°C–180°C, the dosage of the retarder should be increased according to the linear relationship. When the temperature is 140°C–180°C, its thickening time changes little, and its performance is relatively stable.
The preferred high temperature stabilizer DRK-3L is a multi copolymer prepared by aqueous solution radical polymerization. The sulfonic acid group, dicarboxylic group, amido group, cyclic rigid group, etc. are introduced into the main chain of the molecule. These groups give the high temperature stabilizer molecular chain excellent stability under high temperature conditions. At the same time, the optimal molecular weight and distribution of high temperature stabilizer molecules are obtained by optimizing the polymerization process, Therefore, the performance of the high-temperature stabilizer is optimized. The synthetic polymer high temperature stabilizer DRK-3L combined with clay mineral high temperature suspension agent DRY-S2 makes the upper and lower density difference of conventional density cement slurry at 180°C less than 0.05 g/cm3.
The preferred anti ultra-high temperature cement paste strength decline material DRB-3S is selected through a large number of tests. Silicate and phosphate materials containing aluminum, magnesium and other elements are selected and finalized through optimizing the ratio to make the anti strength decline material DRB-3S. Through the chemical action of calcium hydroxide generated by hydration reaction with cement, gel like hydration products are generated to continuously enhance its late strength, Prevent the compressive strength of cement paste from declining under ultra-high temperature.
By selecting reasonable fineness and dosage of silica sand and keeping the ratio of silica to calcium close to 1, the later strength of cement paste can be prevented from declining. When the temperature is higher than 110°C, the strength of ordinary Portland oil well cement will drop suddenly, and the permeability of cement paste will increase sharply. At the same time, in order to prevent the high-temperature strength of cement paste from declining, the high-temperature stabilizer silica sand must be added to the cement. Silica plays a variety of important roles in cementing cement, including enhancing the mechanical properties of cement, improving the high temperature resistance of cement, and improving the rheological properties of cement. Therefore, when selecting silica in cementing cement, small particles, porous shape with large specific surface area and surfactant adsorption treatment are selected. When silica is added to the cement, it absorbs Ca (OH) 2 precipitated from cement hydration, thus reducing the concentration of Ca2+ in the liquid phase, breaking the hydration balance of high calcium hydrated portland such as C2SH2 or C2SH (A), and α- C2SH reacts to produce a low silica calcium salt C5S6H and C6S6H. The strength of both monomers is above 32 MPa, so the strength and thermal stability of Portland cement under high temperature are improved. Both silica sand and quartz sand are high SiO2 containing materials. By increasing the mass ratio of silicon and calcium in the whole mixture, the mass ratio of the material is closer to 1, which is conducive to preventing the permeability of high-temperature impermeable cement slurry from decreasing, keeping the internal structure denser, continuously improving the compressive strength of the cement paste, and preventing the decline of the strength of the cement paste in the later period.
In order to maintain the stability of cement slurry and improve the density of cement paste, this paper screens the particle size and dosage of silica sand based on the principle of particle matching and close packing. Table 1 gives the optimization of the particle size combination of silica sand. Figure 2 shows the density of different silica sand particle size combinations. It can be seen from Table 1 that the particle size combination of Formula E is the most reasonable, and the permeability and viscosity are low. Therefore, it can be determined that the optimal combination of silica powder particle size is 30% 80 mesh+30% 120 mesh+37% 200 mesh+3% 70 mesh. See Table 1 for the corresponding particle size.
After determining the particle size combination of silica sand according to Table 1, strength tests were carried out for silica sand cement paste with different dosage and different curing time (Table 2). Figure 3 shows the strength of cement paste with different curing days and silica sand ratio. It can be seen from Figure 3; Table 2 that when the silica sand dosage reaches 60%, the basic strength value of cement paste is lower than 14 MPa. With the increase of silica sand dosage, the strength of cement paste decreases gradually when the curing time is short, but the strength increases when the curing time exceeds 21 days, and when the content is 40% The strength of the cement paste with 50% silica sand basically does not decline with the curing time. At the same time, the strength of the cement paste with 50% silica sand increases more. Therefore, it can be determined that the optimal amount of silica sand is 50%.
3 Performance evaluation of ultra-high temperature cement slurry for well cementation
3.1 Experimental materials and main equipment
The main materials in the cement slurry formulation include Grade G oil well cement, quartz sand, micro silicon, fluid loss additive DRF-1S, retarder DRH-2L, stabilizer DRK-3L, high-temperature suspension agent DRY-S2, dispersant DRS-1S, high-temperature reinforcement material DRB-2S, and toughening agent DRN-1S. The silica sand content is 50%. Experimental instruments include high-temperature and high-pressure water loss instrument, dual cylinder high-temperature and high-pressure thickener, high-temperature and high-pressure curing kettle, and compressive strength test equipment.
Experimental methods follow national standards, assessing the stability of cement slurry and its hydration reaction. Testing includes settling stability, free liquid test, and compressive strength test according to GB/T 19139-2012 “Oil Well Cement Test Method”. XRD comparison shows similar compositions with varying peak values, indicating resistance differences.
Experiment steps:
1.Cement samples prepared with fixed concentration and proportions.
2. High-temperature settling stability: Samples subjected to high temperature and pressure, monitored for settlement, and assessed for stability parameters.
3. Cement slurry water loss test: Prepared slurry in flow cup, recorded water loss data, analyzed the influence of admixtures on water loss.
4. Cement slurry thickening time experiment: Samples poured into thickening time tester, observed and recorded thickening time, compared the effect of retarder DRH-2L.
5. Compressive strength of cement stone: Mixed cement, water, and mortar to standard, poured into mold, vibrated to remove bubbles, cured at different temperatures, and tested for compressive strength.
Before the experiment, ensured reliable sample source and quality, prepared experiment record form and report template for documenting the process and results. XRD comparison indicated differences in resistance, ensuring stability and reliability of high-temperature sewage stone structure and mechanical properties of cement stone.
3.2 Test results
Through the infrared spectrum experiment of DRF-1S and DRH-2L, it is concluded that there are all characteristic functional groups of AMPS, AM and NX monomers in the fluid loss reducer. The characteristic peak of C=C did not appear between 1,630 cm−1 and 1,645 cm−1 in the entire IR spectrum, so the fluid loss reducer was obtained from the free radical polymerization of the three monomers. According to the peak value, all characteristic functional groups on AMPS, IA and DX monomers were found in the retarder. The characteristic peak of C=C did not appear between 1,630 cm and 1 and 1,645 cm−1 in the whole spectrum, indicating that no unreacted monomers existed in the measured molecular structure, and the reaction was relatively complete.
Through the thermogravimetric analysis of DRF-1S and DRH-2L retarding agent, it is concluded that the water loss reducer has good thermal stability of the sample in the range of 120°C–340°C, and no decomposition, sublimation and other changes that lead to the mutation of sample quality. The structure is stable in the range of 350°C, and the product has excellent temperature resistance. The retarder is reduced to polymer molecular weight fracture at 310°C–340°C, and a large number of small molecules volatilization after fracture leads to a sharp decline in quality, so the structure is stable in the 310°C range, and the product has excellent temperature resistance.
This paper evaluates the settlement stability of different cement slurry formulations at 160°C–210°C (Table 3). The cement slurry formulations are:
Formula A includes grade G cement, 25% quartz sand, 15% high-temperature reinforcement material DRB-2S, 5% micro silicon, 2% fluid loss agent DRF-1S, 6% retarder DRH-2L, 0.5% dispersant DRS-1S, 1.5% high-temperature suspension agent DRY-S2 and water. The density of cement slurry is 1.88 g/cm3.
Formula B includes grade G cement, 25% quartz sand, 15% DRB-2S, 5% micro silicon, 2% DRF-1S, 6% DRH-2L, 0.5% DRS-1S, 1.5% DRY-S2, 4% stabilizer DRK-3L and water. The density of cement slurry is 1.88 g/cm3.
It can be seen from Table 3 that under the temperature of 160°C–180°C, the cement slurry has good high-temperature stability on the whole, and the upper and lower density difference of the cement slurry is effectively controlled to be no more than 0.03 g/cm3 through high-temperature suspension stabilizer; When the temperature is 190°C–210°C, the difference between the upper and lower density of cement slurry is effectively controlled to be no more than 0.04 g/cm3 through high-temperature suspension stabilizer and high-temperature stabilizer.
Table 4; Figure 4 show the influence of different additive dosage at 160°C–210°C on water loss of cement slurry. The cement slurry formula includes Grade G cement, 25% quartz sand, 15% DRB-2S, 5% micro silicon, X% DRF-1S, 6% DRH-2L, 0.5% DRS-1S, 1.5% DRY-S2, Y% DRK-3L and water. The cement slurry density is 1.88 g/cm3.
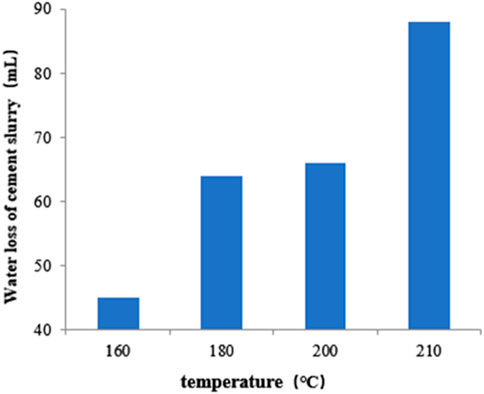
Figure 4. Water loss of cement slurry with different admixture dosages and metal oxide composites at 160°C–210°C.
It can be seen from Table 4; Figure 3 that the water loss of cement slurry gradually increases with the increase of temperature, and the increase of DRF-1S can effectively reduce the water loss of cement slurry under high temperature conditions; When DRF-1S increases by 2%, the API water loss of cement slurry within 210°C can be controlled within 100 mL, which fully shows that the fluid loss additive DRF-1S has good high temperature resistance.
Table 5 shows the thickening time changes of cement slurry with different dosage of retarder DRH-2L. The density of cement slurry is 1.88 g/cm3. The thickening time of the cement slurry can be adjusted when the temperature is 160°C–210°C. When the temperature is 210°C, the thickening time of the cement slurry can reach more than 300 min, indicating that the retarder DRH-2L has good high temperature resistance.
Under high and ultra-high temperature conditions, the long-term strength of cement paste is easy to decline. In order to improve the high temperature strength stability of the cement paste, the high temperature reinforcing material DRB-2S and the anti decay material DRB-3S should also be added to the cement paste system, so as to form crystalline phase at high temperatures and improve the high temperature stability of the cement paste. At the same time, the brittleness of the cement paste at high temperatures is obvious, and the toughening agent DRN-1S is used to improve the brittleness and toughness of the high temperature cement paste. Formula D contains formula C, 10% anti fading material DRB-3S, and its density is 1.88 g/cm3. Table 6; Figure 4 show the high-temperature mechanical properties of cement pastes with Formula C and Formula D under the curing temperature of 180°C and 210°C. It can be seen from Table 6 that the compressive strength of cement paste C after 7 days curing exceeds 30 MPa by adding high temperature reinforcing material DRB-2S, but after 28 days curing, its compressive strength has significantly decreased; The compressive strength decline rate of curing at 180°C for 28 days is 49%, and that of curing at 210.
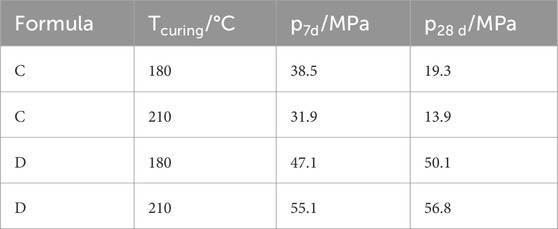
Table 6. Compressive strength of cement stone for ultra high temperature cement slurry at different curing temperatures.
°C for 28 days is 58%; For cement paste formula D, 10% anti fading material is added on the basis of formula C. Under the high temperature conditions of 180°C and 210°C, the compressive strength of cement paste cured for 7 days exceeds 45 MPa, and the compressive strength after 28 days does not show significant decline. It can also be seen from Figure 5 that the internal structure of the crushed cement paste is denser than that of the crushed cement paste with Formula C after the cement paste formula D is cured at 210°C for 28 days (Figure 6). Therefore, combining the photographs of the cement paste before and after the experiment (Figure 6), it can be seen through the experiment that the addition of high temperature reinforcing materials, anti-decay materials and toughening agents in the formula improves the density of cement stone and increases its pressure resistance at high temperatures.
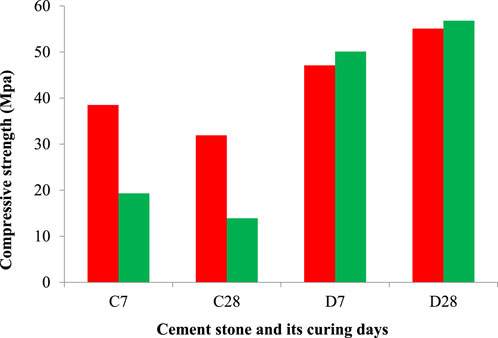
Figure 5. Compressive strength of cement paste with formula C and formula d curing temperatures of 180°C and 210°C.
4 Conclusion
(1) Based on the requirements of ultra-high temperature cementing operation on the performance of cement slurry, this paper configures high-temperature water loss reducer DRF-1S, high-temperature retarder DRH-2L and other supporting high-temperature cement additives to form ultra-high temperature conventional density cement slurry, and carries out indoor test research to evaluate the settlement stability, water loss performance, thickening performance and mechanical performance of ultra-high temperature cement slurry, An ultra-high temperature cementing slurry system is established for oil and gas well cementing. The fluid loss reducer DRF-1S, retarder DRH-2L, stabilizer DRK-3L and anti-corrosion agent DRB-3S are developed, which can ensure the performance of 210°C high temperature slurry to meet the demand.
(2) The conventional density cement slurry system with fluid loss reducer DRF-1S and retarder DRH-2L as the main agents can meet the cementing needs under the high temperature conditions of 180–210 °C, and achieve a new breakthrough in the high-temperature resistance of cement slurry. At the same time, the API water loss of cement slurry is controlled within 100 mL, the thickening time can be adjusted, and the high-temperature settlement stability is less than 0.04 g/cm3; The anti fading material DRB-3S ensures that the 28 days compressive strength of the water debris at 210 °C is higher than 50 MPa, effectively solving the problem of compressive strength degradation of the cement paste at ultra-high temperatures.
Data availability statement
The original contributions presented in the study are included in the article/Supplementary Material, further inquiries can be directed to the corresponding author.
Author contributions
QZ: Methodology, Writing–original draft, Writing–review and editing. XC: Investigation, Methodology, Writing–original draft. SZ: Formal Analysis, Investigation, Writing–original draft. DY: Investigation, Software, Writing–review and editing. LL: Investigation, Methodology, Writing–review and editing.
Funding
The author(s) declare that no financial support was received for the research, authorship, and/or publication of this article.
Acknowledgments
The authors would like to show sincere thanks to those techniques who have contributed to this research.
Conflict of interest
Authors QZ, XC, SZ, DY, and LL were employed by The No. 2 Cementing Branch of PetroChina Bohai Drilling Engineering Company.
Publisher’s note
All claims expressed in this article are solely those of the authors and do not necessarily represent those of their affiliated organizations, or those of the publisher, the editors and the reviewers. Any product that may be evaluated in this article, or claim that may be made by its manufacturer, is not guaranteed or endorsed by the publisher.
References
Abbas, G., Irawan, S., Kumar, S., and Elrayah, A. A. (2013). Improving oil well cement slurry performance using hydroxypropylmethylcellulose polymer. Adv. Mater. Res. 787, 222–227. doi:10.4028/scientific.net/amr.787.222
Chang, X., Sun, J., Xu, Z., Zhang, F., Wang, J., Lv, K., et al. (2019). A novel nano-lignin-based amphoteric copolymer as fluid-loss reducer in water-based drilling fluids. Colloids Surfaces A Physicochem. Eng. Aspects 583, 123979. doi:10.1016/j.colsurfa.2019.123979
Cheng, H., Ma, P., Dong, G., Zhang, S., Wei, J., and Qin, Q. (2022). Characteristics of carboniferous volcanic reservoirs in beisantai oilfield, junggar basin. Math. Problems Eng. 2022, 1–10. doi:10.1155/2022/7800630
Cheng, H., Wei, J., and Cheng, Z. (2022). Study on sedimentary facies and reservoir characteristics of Paleogene sandstone in Yingmaili block, Tarim basin. Geofluids 2022, 1–14. doi:10.1155/2022/1445395
Fahrenholtz, W. G., and Hilmas, G. E. (2017). Ultra-high temperature ceramics: materials for extreme environments. Scr. Mater. 129, 94–99. doi:10.1016/j.scriptamat.2016.10.018
Fang, D., Li, W., Cheng, T., Qu, Z., Chen, Y., Wang, R., et al. (2021). Review on mechanics of ultra-high-temperature materials. Acta Mech. Sin. 37, 1347–1370. doi:10.1007/s10409-021-01146-3
Gasch, M. J., Ellerby, D. T., and Johnson, S. M. (2005). “Ultra high temperature ceramic composites,” in Handbook of ceramic composites (Boston, MA: Springer), 197–224.
Gaurina-Međimurec, N., Pašić, B., Mijić, P., and Medved, I. (2021). Drilling fluid and cement slurry design for naturally fractured reservoirs. Appl. Sci. 11 (2), 767. doi:10.3390/app11020767
Golla, B. R., Mukhopadhyay, A., Basu, B., and Thimmappa, S. K. (2020). Review on ultra-high temperature boride ceramics. Prog. Mater. Sci. 111, 100651. doi:10.1016/j.pmatsci.2020.100651
Guillot, D. (1990). 4 Rheology of well cement slurries. Dev. Petroleum Sci. 28, 4–1. doi:10.1016/S0376-7361(09)70302-4
Hall, H. T. (1960). Ultra-high-pressure, high-temperature apparatus: the ``Belt''. Rev. Sci. Instrum. 31 (2), 125–131. doi:10.1063/1.1716907
Levine, S. R., Opila, E. J., Halbig, M. C., Kiser, J. D., Singh, M., and Salem, J. A. (2002). Evaluation of ultra-high temperature ceramics for aeropropulsion use. J. Eur. Ceram. Soc. 22 (14-15), 2757–2767. doi:10.1016/s0955-2219(02)00140-1
Liu, C., Shao, H., Chen, F., and Zheng, H. (2006). Rheological properties of concentrated aqueous injectable calcium phosphate cement slurry. Biomaterials 27 (29), 5003–5013. doi:10.1016/j.biomaterials.2006.05.043
Mao, H., Qiu, Z., Shen, Z., and Huang, W. (2015). Hydrophobic associated polymer based silica nanoparticles composite with core–shell structure as a filtrate reducer for drilling fluid at utra-high temperature. J. Petroleum Sci. Eng. 129, 1–14. doi:10.1016/j.petrol.2015.03.003
Monteverde, F., Bellosi, A., and Scatteia, L. (2008). Processing and properties of ultra-high temperature ceramics for space applications. Mater. Sci. Eng. A 485 (1-2), 415–421. doi:10.1016/j.msea.2007.08.054
Ricky, E., Mpelwa, M., Wang, C., Hamad, B., and Xu, X. (2022). Modified corn starch as an environmentally friendly rheology enhancer and fluid loss reducer for water-based drilling mud. SPE J. 27 (02), 1064–1080. doi:10.2118/209195-pa
Sabins, F. L., Tinsley, J. M., and Sutton, D. L. (1982). Transition time of cement slurries between the fluid and set states. Soc. Petroleum Eng. J. 22 (06), 875–882. doi:10.2118/9285-pa
Son, A. J., Ballard, T. M., and Loftin, R. E. (1987). Temperature-stable polymeric fluid-loss reducer tolerant to high electrolyte contamination. SPE Drill. Eng. 2 (03), 209–217. doi:10.2118/13160-pa
Tang, S., Deng, J., Wang, S., Liu, W., and Yang, K. (2007). Ablation behaviors of ultra-high temperature ceramic composites. Mater. Sci. Eng. A 465 (1-2), 1–7. doi:10.1016/j.msea.2007.02.040
Tao, C., Kutchko, B. G., Rosenbaum, E., and Massoudi, M. (2020). A review of rheological modeling of cement slurry in oil well applications. Energies 13 (3), 570. doi:10.3390/en13030570
Tao, C., Kutchko, B. G., Rosenbaum, E., Massoudi, M., and Massoudi, H. (2019). Steady flow of a cement slurry. Energies 12 (13), 2604. doi:10.3390/en12132604
Velayati, A., Tokhmechi, B., Soltanian, H., and Kazemzadeh, E. (2015). Cement slurry optimization and assessment of additives according to a proposed plan. J. Nat. Gas Sci. Eng. 23, 165–170. doi:10.1016/j.jngse.2015.01.037
Wu, Y. M., Zhang, B. Q., Wu, T., and Zhang, C. G. (2001). Properties of the forpolymer of N-vinylpyrrolidone with itaconic acid, acrylamide and 2-acrylamido-2-methyl-1-propane sulfonic acid as a fluid-loss reducer for drilling fluid at high temperatures. Colloid Polym. Sci. 279 (9), 836–842. doi:10.1007/s003960100494
Wuchina, E., Opila, E., Opeka, M., Fahrenholtz, B., and Talmy, I. (2007). UHTCs: ultra-high temperature ceramic materials for extreme environment applications. Electrochem. Soc. Interface 16 (4), 30–36. doi:10.1149/2.f04074if
Xiaofeng, C. H. A. N. G., Jinsheng, S. U. N., Kaihe, L. Y. U., and Fan, Z. H. A. N. G. (2019). Research and application of a novel.
Yan, S., Wang, Y., Wang, F., Yang, S., Wu, Y., and Yan, S. (2017). Synthesis and mechanism study of temperature-resistant fluid loss reducer for oil well cement. Advances in Cement Research 29 (5), 183–193.
Zhang, W., Cheng, Z., Cheng, H., Qin, Q., and Wang, M. (2021). Research of tight gas reservoir simulation technology. IOP Conference Series: Earth and Environmental Science IOP Publishing 804 (2), 022046.
Nomenclature
Keywords: ultra-high temperature, cementing, cement slurry, fluid loss reducer, high temperature resistance
Citation: Zou Q, Chen X, Zhong S, Yi D and Liu L (2024) Performance experiment of ultra high temperature cementing slurry system. Front. Mater. 11:1383286. doi: 10.3389/fmats.2024.1383286
Received: 07 February 2024; Accepted: 27 March 2024;
Published: 24 April 2024.
Edited by:
Kunal Mondal, Oak Ridge National Laboratory (DOE), United StatesReviewed by:
Arnab Bose, Boehringer Ingelheim, United StatesAsef Redwan, Idaho National Laboratory (DOE), United States
Copyright © 2024 Zou, Chen, Zhong, Yi and Liu. This is an open-access article distributed under the terms of the Creative Commons Attribution License (CC BY). The use, distribution or reproduction in other forums is permitted, provided the original author(s) and the copyright owner(s) are credited and that the original publication in this journal is cited, in accordance with accepted academic practice. No use, distribution or reproduction is permitted which does not comply with these terms.
*Correspondence: Qiang Zou, xiaodo078di@126.com