Study on sedimentation stability of silicone oil-based magnetorheological fluids with fumed silica as additive
- 1School of Mechatronic Engineering, China University of Mining and Technology, Xuzhou, China
- 2School of Intelligent Engineering, Jiangsu Vocational College of Information Technology, Wuxi, China
In order to study the sedimentation stability of silicone oil-based magnetorheological fluids with fumed silica as additive, magnetorheological fluids with different mass fractions of fumed silica, particle sizes of carbonyl iron powder and viscosities of silicone oil were prepared. The sedimentation rate of magnetorheological fluids was calculated by observation method, and the zero-field viscosity of magnetorheological fluids was measured by viscometer. The results show that the sedimentation rate and viscosity of magnetorheological fluids increase gradually with the increase of the mass fraction of fumed silica. The mass fraction of fumed silica should not be constant for magnetorheological fluids, but should be determined according to the content of silicone oil in magnetorheological fluids. With the increase of average diameter of carbonyl iron powder, the sedimentation stability of magnetorheological fluids becomes worse. With the increase of viscosity of silicone oil, the sedimentation stability of magnetorheological fluids does not increase significantly. However, the high viscosity of silicone oil will result in wall hanging phenomenon, and increase the start-up difficulty of magnetorheological device. With 2.5 wt% of fumed silica for silicone oil, the magnetorheological fluids has good sedimentation stability and suitable zero-field viscosity.
1 Introduction
Magnetorheological fluids (MRFs) are a kind of smart material with unique rheological effect. The main components of MRFs are carrier fluid, micrometer soft magnetic particles and functional additives (Roupec et al., 2021). MRFs appear as Newtonian fluid at zero magnetic field. Under the action of magnetic field, the MRFs become solid-like, and the magnetic particles form chain shape and have anti-shear ability (Khajehsaeid et al., 2022; Ghasemi et al., 2023). When the magnetic field is removed, MRFs quickly return to the Newtonian fluid state. MRFs have millisecond response time and good real-time controllability, which makes them suitable for devices controlled by external magnetic fields, such as brakes (Vezys et al., 2018; Acharya et al., 2021), clutches (Akbari et al., 2022; Bira et al., 2022), dampers (Wang et al., 2021; Nordin et al., 2022) and polishing devices (Bai et al., 2019; Milde et al., 2022). However, the density of the magnetic particles is about 7 times bigger than the carrier fluid, the magnetic particles settle in the carrier fluid (Kaide et al., 2020; Su et al., 2020; Maurya and Sarkar, 2021; Zhu et al., 2021). When the magnetorheological device stops working, the sedimentation of magnetic particles is difficult to avoid (Aruna et al., 2019; Cheng et al., 2021a; She et al., 2023). The sedimentation and agglomeration of magnetic particles will directly affect the performance of MRFs, so it is very important to study the sedimentation stability of MRFs for magnetorheological device.
At present, many scholars have studied the sedimentation stability of MRFs through particle modification, base oil mixing and additive replacement. In particle modification, the sedimentation of MRFs can be reduced by changing the size, shape and content of particles. Lee et al. (2015) obtained the sedimentation velocity formula of MRFs by using Stokes equation, which showed that smaller magnetic particles had better sedimentation stability because of their higher kinetic stability. Lee et al. (2019) compared the sedimentation stability of the MRFs prepared by spherical carbonyl iron powders (CIPs) and flake-shaped CIPs. Due to the large surface area of the flake CIPs, the sedimentation stability of the MRFs prepared by flake-shaped CIPs is better. Zhang et al. (2019) established a formula for sedimentation velocity of MRFs with different particle volumetric concentrations based on Dick model by comparing three different sedimentation velocity models (Vesilind model, Dick model and Richardson and Zaki model). In terms of base oil, the sedimentation stability of MRFs is improved mainly by mixing several kinds of oil. Jinaga et al. (2019) prepared MRFs by mixing silicone oil (25%), honey (25%) and organic oil (50%) as base oil. Sunflower oil and cottonseed oil are used in the mixed oil for comparative analysis, and it was found that cottonseed oil-based MRFs had better anti-sedimentation property. Tong et al. (2022) prepared three MRFs by three base oils (silicone oil, ionic liquid and mixture of silicone oil and ionic liquid). The MRFs prepared by mixture of silicone oil and ionic liquid has better sedimentation stability. In terms of additives, additives can be divided into surfactants, thixotropic agents and nanoparticles. Sharmili et al. (2023) compared and studied the sedimentation rates of MRFs with four additives (siloxane, lithium, oleic acid and SDBS), siloxane-MRFs exhibited high sedimentation resistance. Cvek et al. (2022) fabricated compact/mesoporous silica, the sub-micro additive prevented the CIPs from aggregation, which can significantly improve the sedimentation stability of MRFs. Xu et al. (2018) found that fumed silica (0.5–0.6 wt%) was the most promising additive proportion for proper rheological and sedimentation properties. Cheng et al. (2021b) prepared the MRFs with fumed silica (1.85 wt%), and the sedimentation rate was about 92.4%, which showed better sedimentation stability compared with commercial MRFs (87.6%). Kim and Choi, (2022) used ZnFe2O4 to fill the free space among the CIPs and improved the stability of the MRFs against rapid sedimentation of CIPs.
From the above studies, it can be found that small amount of fumed silica can greatly improve the sedimentation stability of MRFs, so fumed silica is also the main direction for more researchers to study the sedimentation stability of MRFs. From the research papers on silica, it can be seen that researchers have obtained the most appropriate mass fraction of fumed silica through a large number of tests, so as to achieve the best MRFs sedimentation stability. However, the mass fraction of fumed silica obtained after a lot of tests is only suitable for the mass fraction of special magnetic particles, and cannot be applied to MRFs with different mass fractions of magnetic particles. In this paper, the effects of the mass fraction of fumed silica, the particle size of CIPs and the viscosity of silicone oil on the sedimentation stability and zero-field viscosity of MRFs were studied. The law that the mass fraction of fumed silica should be determined according to the content of silicone oil is found, which should be useful for selecting the best content of the fumed silica for the sedimentation stability of MRFs.
2 Materials and methods
2.1 Materials
The magnetic particles are CIPs produced by TIANYI (China). CIPs are widely used as magnetic particles in MRFs because of its low coercivity, high permeability, simple chemical properties and easy magnetization. The carrier fluid is silicone oil produced by DOW CORNING (USA). The additive is hydrophobic fumed silica produced by WACKER (Germany). The thixotropic mesh formed by fumed silica can effectively prevent CIPs from settling in silicone oil, as shown in Figure 1.
2.2 Preparation method
MRFs can be prepared according to the process shown in Figure 2. The CIPs, silicone oil and fumed silica are weighed by a balance and poured into a beaker (Zhang et al., 2021). MRFs are stirred by a high-speed agitator for 1 h to uniformly disperse the CIPs and fumed silica into the silicone oil.
2.3 Test methods
Due to the obvious density difference between CIPs and silicone oil, the CIPs with higher density can settle easily in the silicone oil. The sedimentation rate of MRFs is measured by observation method. When the total volume of MRFs is a and the volume of the precipitated layer is b, the sedimentation rate is the ratio of b to a, as shown in Figure 3. The sedimentation rate x(t) of the MRFs can be derived from Eq. 1.
The zero-field viscosity of MRFs is measured by NDJ-1 rotational viscometer (China). The zero-field viscosity of MRFs is affected by thixotropic effect of fumed silica. So the zero-field viscosity of MRFs is measured immediately after the preparation of MRFs. Since the speed has great influence on the viscosity, the speed is adjusted to 30 r/min. And the temperature has a big impact on viscosity, a water bath is used to control the measured temperature at 25°C, as shown in Figure 4.
2.4 Experimental methods
Since sedimentation predominantly occurs within the first 2 days, the sedimentation rate is recorded every 6 h within the first 2 days. After 2 days, the sedimentation rate is recorded once a day. In order to investigate the effect of the mass fraction of fumed silica on the sedimentation stability of MRFs, the six kinds of MRFs with fumed silica (1 wt%), silicone oil (100 cst), and CIPs (30 wt%, 40 wt%, 50 wt%, 60 wt%, 70 wt%, 80 wt%) with average particle size of 5.5 μm were prepared. The specific components are shown in Table 1.
In order to study the effects of mass fraction of fumed silica and silicone oil on the sedimentation rate of MRFs, the 30 kinds of MRFs with different mass fractions of fumed silica (0 wt%, 0.5 wt%, 1 wt%, 1.5 wt%, 2 wt%, 2.5 wt%, 3 wt%) and silicone oil (70 wt%, 60 wt%, 50 wt%, 40 wt%, 30 wt%) were prepared. The average particle size of CIPs is 5.5 μm, and the viscosity of silicone oil is 100 cst in experiments. It should be emphasized that the mass fraction of fumed silica refers to the proportion of fumed silica to silicone oil, while the mass fraction of silicon oil refers to the proportion of silicone oil to entire MRFs. The specific components of 30 kinds of MRFs are shown in Table 2.
In order to study the effect of CIPs diameter on the sedimentation rate of MRFs, three kinds of MRFs were prepared by using different particle diameters of CIPs (2 μm, 3.5 μm, 5.5 μm) as magnetic particles, as shown in Table 3. The particle size distribution of CIPs with different particle sizes measured by GSL-1010 laser particle size measurement (China) is shown in Figure 5. In this experiment, 60 wt% of CIPs, 39 wt% of silicone oil (100 cst) and 1 wt% of fumed silica are adopted.
In order to study the influence of the viscosity of the silicone oil on the sedimentation rate of the MRFs, three kinds of MRFs were prepared by using different viscosities of silicone oil (50 cst, 100 cst, 350 cst) as the carrier fluid, as shown in Table 4. In this experiment, 60 wt% of CIPs (5.5 μm), 39 wt% of silicone oil and 1 wt% of fumed silica are adopted.
3 Results and discussion
3.1 Mass fraction of fumed silica
Figure 6A shows the sedimentation rates of MRFs with different mass fractions of CIPs (30 wt%, 40 wt%, 50 wt%, 60 wt%, 70 wt%) when fumed silica is 1wt%. The sedimentation rate of MRFs-1 stabilizes after only 5 days, and the sedimentation rate remains at 38%. The sedimentation rate of MRFs-5 keeps stable after 14 days and reaches at 77%. With the mass fraction of CIPs increasing, the sedimentation rate of MRFs decreases and the sedimentation stability time also becomes longer. Figure 6B shows the MRFs-6 prepared by fumed silica (1 wt%) and CIPs (80 wt%). This MRFs does not have fluidity, and it is difficult to stir with glass rods. The results show that fumed silica with fixed mass fraction is not suitable for MRFs with different mass fractions of CIPs. As the mass fraction of CIPs increases, the mass fraction of silicone oil decreases. In the case of constant mass fraction of fumed silica, as the mass fraction of silicone oil decreases, the thixotropic mesh will become stronger. Then the sedimentation stability of MRFs will be improved. Since the thixotropic reaction of fumed silica occurs in silicone oil, it is assumed that the reasonable amount of fumed silica used should be determined by the mass fraction of silicone oil.
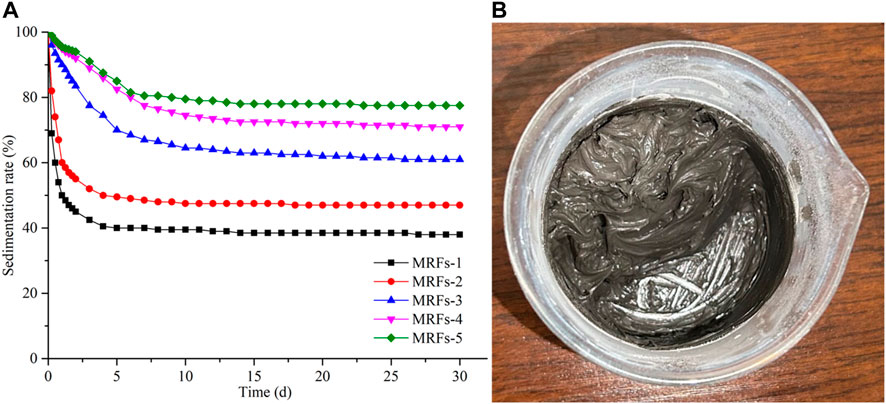
Figure 6. Sedimentation stability of MRFs with different mass fractions of CIPs: (A) sedimentation rate of MRFs-1, MRFs-2, MRFs-3, MRFs-4 and MRFs-5, (B) MRFs-6.
Figures 7A–G show the MRFs sedimentation curves for the different mass fractions of fumed silica (0 wt%, 0.5 wt%, 1 wt%, 1.5 wt%, 2 wt%, 2.5 wt%, 3 wt%) for silicone oil, respectively. The sedimentation rates of MRFs-7 and MRFs-12 are 12.5% and 21%, as shown in Figures 7A, B. The fumed silica (0.5 wt%) in the silicone oil can increase the sedimentation rate of MRFs, but the effect is not obvious. The main reason for the small difference in sedimentation rates is the weak thixotropic mesh formed by the fumed silica (0.5 wt%) in the silicone oil. The sedimentation rates of MRFs-12 and MRFs-16 are 21% and 52%, as shown in Figure 7B. With the increase of mass fraction of CIPs, the thixotropic mesh is not enough to support a large number of CIPs, so the difference in sedimentation rates between MRFs-12 and MRFs-16 is large. As shown in Figure 6, there is 33% difference in sedimentation rate between MRFs-7 and MRFs-11, 31% between MRFs-12 and MRFs-16, 24% between MRFs-17 and MRFs-21, 19% between MRFs-22 and MRFs-26, 12.5% between MRFs-27 and MRFs-31, 3.5% between MRFs-32 and MRFs-36% and 3.5% between MRFs-37 and MRFs-41. With the increasing of the mass fraction of fumed silica for silicone oil, the influence of the mass fraction of CIPs on the sedimentation rate of MRFs becomes less and less. When the mass fraction of fumed silica reaches more than 2.5wt% for silicone oil, the influence of the mass fraction of CIPs on the sedimentation rate of MRFs is almost negligible.
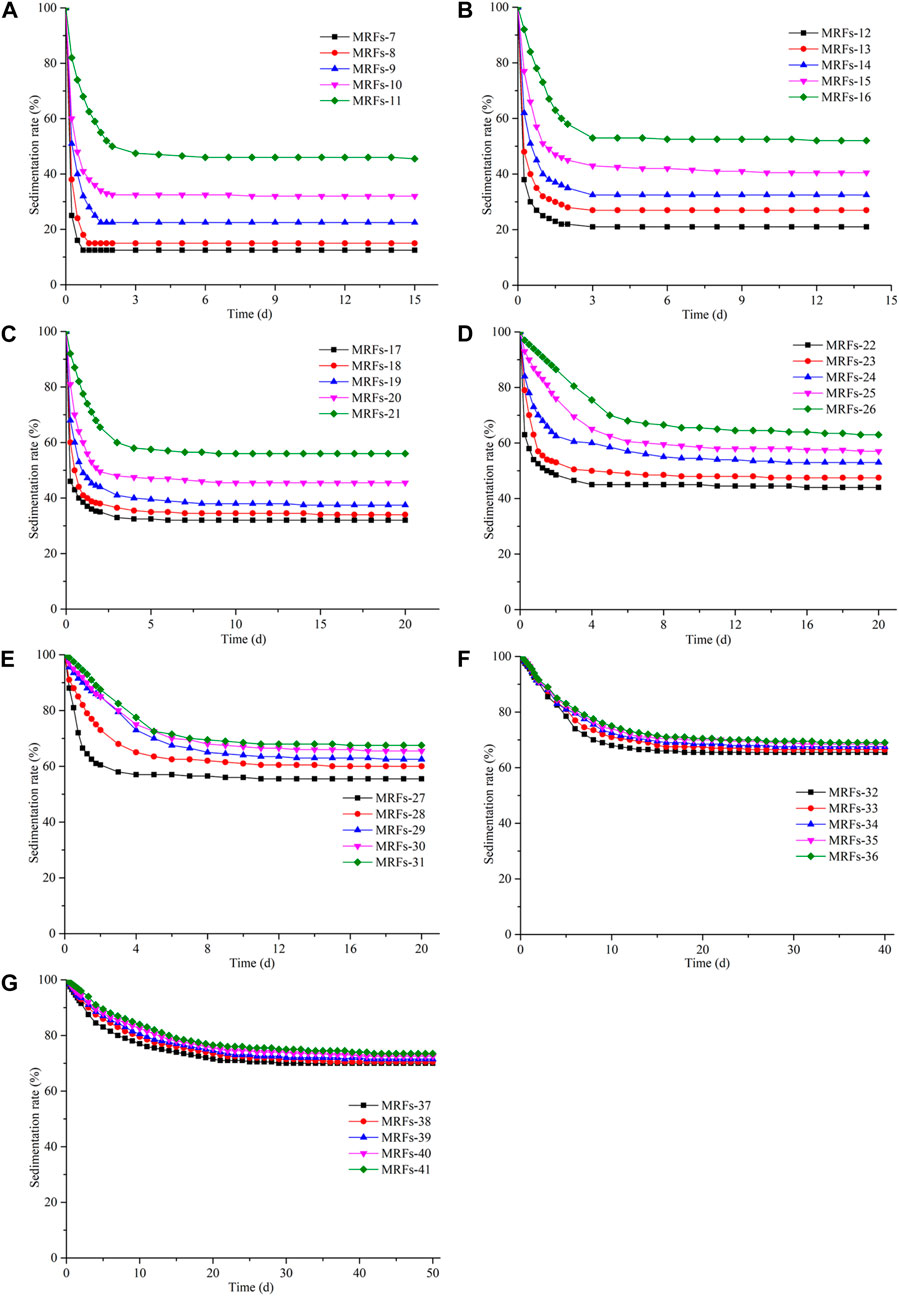
Figure 7. Sedimentation rate of MRFs with different mass fractions of fumed silica: (A) 0 wt% (B) 0.5 wt% (C) 1 wt% (D) 1.5 wt% (E) 2 wt% (F) 2.5 wt% (G) 3 wt%.
In addition, the mass fraction of fumed silica for silicone oil has great influence on the sedimentation stability time of MRFs. The sedimentation stability durations of MRFs-11, MRFs-16, MRFs-21, MRFs-26, MRFs-31, MRFs-36 and MRFs-41 with same 30 wt% of silicone oil are 3 days, 3 days, 7 days, 12 days, 16 days, 22 days and 33 days, respectively. The MRFs with other mass fractions of silicone oil also have similar regularity, the higher the mass fraction of fumed silica, the longer the sedimentation stability time. As the mass fraction of fumed silica continues to increase, the thixotropic mesh in silicone oil is gradually denser. Therefore, CIPs needs to spend more time finding the appropriate balance point in the thixotropic mesh.
Figure 8 shows the viscosity curves of MRFs with different mass fractions of silicone oil and fumed silica. When the mass fraction of fumed silica is the same, the viscosity of MRFs decreases with the increase of the mass fraction of silicone oil. The increase of the mass fraction of silicone oil leads to the decrease of the mass fraction of CIPs, which will lead to the decrease of the overall viscosity of the MRFs. When the mass fraction of silicone oil is the same, the viscosity of MRFs increases obviously with the increase of the mass fraction of fumed silica. Both the mass fraction of silicone oil and fumed silica have influence on the viscosity of MRFs, but the mass fraction of fumed silica plays a much larger role on the viscosity of MRFs. When the mass fraction of fumed silica is from 2.5 wt% to 3 wt%, the viscosity of MRFs suddenly increases greatly. The high viscosity of MRFs will increase the start-up difficulty of magnetorheological device. Due to the small difference in sedimentation rates between MRFs with 2.5 wt% and 3 wt% of fumed silica, it is more appropriate to choose 2.5 wt% of fumed silica.
3.2 Particle size of CIPs
Figure 9 shows the sedimentation curves of three kinds of MRFs prepared by CIPs with different average particle sizes (2 μm, 3.5 μm, 5.5 μm). On account of the average particle size of CIPs increases, the gravity of a single CIP increases. With the increase of CIPs particle size, the sedimentation rate of MRFs decreases gradually. Similarly, large particle size CIPs will also make the sedimentation velocity of MRFs faster. Since MRFs-42, MRFs-43, and MRFs-4 have the same mass fraction of fumed silica and silicone oil, so the three kinds of MRFs have the same thixotropic mesh. The thixotropic mesh has poor supporting effect on CIPs with large particle size, which leads to poor sedimentation stability of MRFs prepared by CIPs with large particle size.
3.3 Viscosity of silicone oil
Figure 10 shows the sedimentation curves of three kinds of MRFs prepared by different viscosities of silicone oil (50 cst, 100 cst, 350 cst). With the increase of viscosity of silicone oil, the sedimentation rate of MRFs increases gradually. Because the high viscosity of silicone oil will hinder the movement of CIPs, the high viscosity of silicone oil not only increases the sedimentation rate of MRFs, but also slows down the sedimentation velocity of MRFs. However, MRFs-45 prepared by higher viscosity of silicone oil appear wall hanging phenomenon above the test tube, as shown in Figure 10. Moreover, the difference in sedimentation rates between MRFs-44 and MRFs-4 is 3%, and the difference in sedimentation rates between MRFs-4 and MRFs-45 is only 1%. Although the viscosity of silicone oil can improve the sedimentation stability of MRFs, it is not obvious to increase the sedimentation rate of MRFs by increasing the viscosity of silicone oil.
4 Conclusion
In this study, the effects of the mass fraction of fumed silica, particle size of CIPs and viscosity of silicone oil on the sedimentation stability of MRFs were investigated. Since fumed silica forms thixotropic mesh in the silicone oil, it prevents CIPs from settling. Therefore, the content of fumed silica should be mainly determined by the content of silicone oil. When the mass fraction of fumed silica for silicone oil reaches more than 2.5 wt%, the sedimentation rate of MRFs prepared by different mass fractions of silicone oil is basically consistent. However, when the mass fraction of silica to silicone oil reaches 3 wt%, the viscosity of MRFs becomes higher. The high viscosity of MRFs increases the start-up difficulty of magnetorheological device. With the increase of particle size of CIPs, the sedimentation stability of MRFs will become worse. With the increase of the viscosity of silicone oil, the sedimentation stability of MRFs will be improved. But the effect of increasing the viscosity of silicone oil to improve the sedimentation rate of MRFs is not obvious. In short, when fumed silica is 2.5 wt% for silicone oil, the MRFs with different mass fractions of silicone oil have good sedimentation stability and suitable zero-field viscosity.
Data availability statement
The original contributions presented in the study are included in the article/Supplementary material, further inquiries can be directed to the corresponding author.
Author contributions
LY: Data curation, Formal Analysis, Writing–original draft. FC: Conceptualization, Funding acquisition, Writing–review and editing. HL: Methodology, Writing–review and editing.
Funding
The author(s) declare financial support was received for the research, authorship, and/or publication of this article. This work was supported by the National Natural Science Foundation of China (52074272, 52305078).
Conflict of interest
The authors declare that the research was conducted in the absence of any commercial or financial relationships that could be construed as a potential conflict of interest.
Publisher’s note
All claims expressed in this article are solely those of the authors and do not necessarily represent those of their affiliated organizations, or those of the publisher, the editors and the reviewers. Any product that may be evaluated in this article, or claim that may be made by its manufacturer, is not guaranteed or endorsed by the publisher.
References
Acharya, S., Saini, T. R. S., Sundaram, V., and Kumar, H. (2021). Selection of optimal composition of MR fluid for a brake designed using MOGA optimization coupled with magnetic FEA analysis. J. Intel. Mat. Syst. Str. 32, 1831–1854. doi:10.1177/1045389x20977905
Akbari, E., Khajehsaeid, H., and Asiaban, R. (2022). On the design of cylindrical magnetorheological clutches. Int. J. Appl. Mech. 14, 2250049. doi:10.1142/s1758825122500491
Aruna, M. N., Rahman, M. R., Joladarashi, S., and Kumar, H. (2019). Influence of additives on the synthesis of carbonyl iron suspension on rheological and sedimentation properties of magnetorheological (MR) fluids. Mat. Res. Express. 6, 086105. doi:10.1088/2053-1591/ab1e03
Bai, Y., Xue, D. L., and Zhang, X. J. (2019). Polishing performance of magnetorheological finishing with flocculated and deflocculated aqueous polishing fluid. Opt. Eng. 58, 025104. doi:10.1117/1.OE.58.2.025104
Bira, N., Dhagat, P., and Davidson, J. R. (2022). A low-power magnetorheological fluid clutch utilizing electropermanent magnet arrays. Front. Mat. 9, 1039004. doi:10.3389/fmats.2022.1039004
Cheng, J. Z., Liu, K., Zhang, Z. C., Wei, Z. Q., Ma, Y. H., and Lu, S. R. (2021a). Effect of compound surfactants modified carbonyl iron on magnetorheological fluids. J. Supercond. Nov. Magn. 34, 1177–1183. doi:10.1007/s10948-021-05813-1
Cheng, J. Z., Liu, K., Zhang, Z. C., Wei, Z. Q., Ma, Y. H., and Lu, S. R. (2021b). Effect of compound surfactants modified carbonyl iron on magnetorheological fluids. J. Supercond. Nov. Magn. 34, 1177–1183. doi:10.1007/s10948-021-05813-1
Cvek, M., Jamatia, T., Suly, P., Urbanek, M., and Torres-Mendieta, R. (2022). Stable magnetorheological fluids containing bidisperse fillers with compact/mesoporous silica coatings. Int. J. Mol. Sci. 23, 11044. doi:10.3390/ijms231911044
Ghasemi, S. S., Ebrahimi, N. G., and Hajalilou, A. (2023). Simultaneous effect of magnetic nanoparticles additive and noble metal coating on carbonyl iron-based magnetorheological fluid. J. Alloy. Compd. 961, 171012. doi:10.1016/j.jallcom.2023.171012
Jinaga, R., Jagadeesha, T., Kolekar, S., and Choi, S. B. (2019). The synthesis of organic oils blended magnetorheological fluids with the field-dependent material characterization. Int. J. Mol. Sci. 20, 5766. doi:10.3390/ijms20225766
Kaide, A., Kanda, M., Tochigi, H., and Saeki, T. (2020). Rheology and stability of magnetorheological fluids prepared with three types of stabilizers. J. Chem. Eng. Jpn. 53, 438–445. doi:10.1252/jcej.19we119
Khajehsaeid, H., Alaghehband, N., and Bavil, P. K. (2022). On the yield stress of magnetorheological fluids. Chem. Eng. Sci. 256, 117699. doi:10.1016/j.ces.2022.117699
Kim, H. M., and Choi, H. J. (2022). Enhanced magnetorheological response of carbonyl iron suspension with added ZnFe2O4 particles. Ieee. Trans. Magn. 58, 4600205. doi:10.1109/TMAG.2021.3086863
Lee, J. Y., Kwon, S. H., and Choi, H. J. (2019). Magnetorheological characteristics of carbonyl iron microparticles with different shapes. Korea-Aust. Rheol. J. 31, 41–47. doi:10.1007/s13367-019-0005-6
Lee, S., Shin, K. Y., and Jang, J. (2015). Enhanced magnetorheological performance of highly uniform magnetic carbon nanoparticles. Nanoscale 7, 9646–9654. doi:10.1039/c4nr07168a
Maurya, C. S., and Sarkar, C. (2021). Synthesis and characterization of novel flake-shaped carbonyl iron and water-based magnetorheological fluids using laponite and oleic acid with enhanced sedimentation stability. J. Intel. Mat. Syst. Str. 32, 1624–1639. doi:10.1177/1045389x20987001
Milde, R., Moucka, R., Sedlacik, M., and Pata, V. (2022). Iron-sepiolite high-performance magnetorheological polishing fluid with reduced sedimentation. Int. J. Mol. Sci. 23, 12187. doi:10.3390/ijms232012187
Nordin, N. H. D., Muthalif, A. G. A., Razali, M. K. M., Ali, A., and Salem, A. M. (2022). Development and implementation of energy-efficient magnetorheological fluid bypass damper for prosthetics limbs using a fuzzy-logic controller. Ieee. Access. 10, 18978–18987. doi:10.1109/access.2022.3149893
Roupec, J., Michal, L., Strecker, Z., Kubík, M., Machácek, O., and Choi, H. J. (2021). Influence of clay-based additive on sedimentation stability of magnetorheological fluid. Mat. Struct. 30, 027001. doi:10.1088/1361-665x/abd345
Sharmili, P., Rajesh, S., Mahendran, M., Saravanakumar, S., Abirami, G., Sivakami, A., et al. (2023). Rheometric and stability analysis of additive infused magnetorheological fluids: a comparative study. Soft. Matter 46, 6. doi:10.1140/epje/s10189-023-00262-1
She, N., Chen, B. S., Lu, M. R., Xu, Y. C., Peng, X. D., and Hung, S. C. (2023). A multi-particle sedimentation stability investigation of magnetorheological fluid using the DEM. Korea-Aust. Rheol. J. 36, 1–14. doi:10.1007/s13367-023-00080-z
Su, Z. B., Luo, Y. P., Ying, W., Jiao, L., and Ji, D. S. (2020). Study on sedimentation stability of magnetorheological fluids based on different lubricant formulations. Mat. Res. Express. 7, 085702. doi:10.1088/2053-1591/abb055
Tong, Y., Zhao, P. H., Li, X. G., Ma, N., Dong, X. F., Niu, C. G., et al. (2022). Properties and mechanism of ionic liquid/silicone oil based magnetorheological fluids. Int. J. Smart. Nano. Mat. 13, 263–272. doi:10.1080/19475411.2022.2069876
Vezys, J., Mazeika, D., Kandrotaite-Janutiene, R., Dragasius, E., Kilikevicius, A., and Korobko, E. V. (2018). Sedimentation influence on magnetorheological brake torque moment. Strength. Mater+ 50, 357–367. doi:10.1007/s11223-018-9979-4
Wang, N., Pang, S., Ye, C. L., Fan, T. T., and Choi, S. B. (2021). The friction and wear mechanism of O-rings in magnetorheological damper: numerical and experimental study. Tribol. Int. 157, 106898. doi:10.1016/j.triboint.2021.106898
Xu, J. H., Li, J. Y., and Cao, J. G. (2018). Effects of fumed silica weight fraction on rheological properties of magnetorheological polishing fluids. Colloid. Polym. Sci. 296, 1145–1156. doi:10.1007/s00396-018-4332-9
Zhang, Y. A., Jiang, J. L., Ouyang, C. K., Meng, Y. G., Jia, W. P., Ma, L. R., et al. (2021). Effect of base oil lubrication properties on magnetorheological fluids. Mat. Struct. 30, 095011. doi:10.1088/1361-665x/ac15a0
Zhang, Y. J., Li, D. C., and Zhang, Z. L. (2019). The study of magnetorheological fluids sedimentation behaviors based on volume fraction of magnetic particles and the mass fraction of surfactants. Mat. Res. Express. 6, 126127. doi:10.1088/2053-1591/ab5ed8
Keywords: magnetorheological fluids, silicone oil, fumed silica, sedimentation stability, viscosity
Citation: Yu L, Chen F and Li H (2024) Study on sedimentation stability of silicone oil-based magnetorheological fluids with fumed silica as additive. Front. Mater. 11:1395507. doi: 10.3389/fmats.2024.1395507
Received: 04 March 2024; Accepted: 28 March 2024;
Published: 11 April 2024.
Edited by:
Yang Yu, University of New South Wales, AustraliaReviewed by:
Shaoqi Li, Nanjing Tech University, ChinaXufeng Dong, Dalian University of Technology, China
Copyright © 2024 Yu, Chen and Li. This is an open-access article distributed under the terms of the Creative Commons Attribution License (CC BY). The use, distribution or reproduction in other forums is permitted, provided the original author(s) and the copyright owner(s) are credited and that the original publication in this journal is cited, in accordance with accepted academic practice. No use, distribution or reproduction is permitted which does not comply with these terms.
*Correspondence: Fei Chen, cfcumtxz@126.com