The milling parameters of mechanical parts are optimized by NC machining technology
- Anhui Vocational College of Grain Engineering, Hefei, Anhui, China
In the field of mechanical manufacturing, CNC machining technology plays an important role in improving the precision and efficiency of part processing. However, how to further improve the effect of NC machining by optimizing milling parameters is still a key problem. The aim of this study is to optimize CNC milling parameters through systematic research and experiments to improve the machining efficiency and quality of mechanical parts. By adjusting key parameters such as tool speed, feed speed, and removal rate cutting depth, the influence of these parameters on the milling process was systematically studied using advanced CNC machining equipment. Through the collection and analysis of experimental data, the mathematical model is established, and the optimization algorithm is applied to find the best combination of milling parameters. The experimental results show that under the optimal combination of parameters, the surface quality of parts can be significantly improved, the machining time can be reduced, and the tool wear can be reduced. This research successfully realizes the optimization of milling parameters of mechanical parts by CNC machining technology and provides an effective solution for improving machining efficiency and reducing costs. This not only has guiding significance for the application of CNC machining technology but also has important promotion value in actual production.
1 Introduction
CNC machining technology plays a crucial role in modern machinery manufacturing, and its high-precision and high-efficiency characteristics have significant advantages in improving the processing quality of parts and production efficiency (Chen and Feng, 2022; Yang and He, 2023; Zhang, 2023). However, in order to fully realize the potential of CNC machining, it is particularly important to optimize milling parameters in a scientific and rational way. In the international academic circle, many scholars have conducted in-depth research on CNC machining technology and put forward a series of valuable conclusions.
Researchers worldwide have achieved remarkable results through the optimization of CNC milling parameters. For example, Sakthivel’s research pointed out that with the support of a genetic algorithm, machining parameters such as cutting speed, feed rate, and axial cutting depth were optimized, and the cutting force effect of the CNC end milling cutter was tested by empirical methods before and after optimization, and it was found that optimizing machining parameters could improve the cutting force of CNC milling cutters (Sakthivel, 2019). Vardhan et al. (2018) used an artificial neural network to predict the material removal rate and surface roughness during CNC milling of P20 steel. The final result showed that the predicted value was very close to the experimental value, which meant that the constructed model could be used for actual prediction. The material removal rate and surface roughness of P20 steel can be predicted more accurately. At the same time, domestic scholars are also actively exploring the field of CNC machining technology to adapt to the rapid development of China’s manufacturing industry. Liu et al. (2022) proved through experiments that a reasonable adjustment of cutting depth can effectively control the surface roughness of parts and improve their surface quality. In addition, Yang (2023) proposed a method suitable for the optimization of machining process parameters in the field of numerical control machining, tested the feasibility of the method through experiments, and found that the optimization method based on a genetic algorithm can improve the machining quality and efficiency of numerical control machine tools. In 2021, in order to solve the difficult problem of thread milling, Li Aifei and others introduced Mastercam technology to achieve automatic programming processing of the target through this technology (Li and Ren, 2021). The results show that the introduction of this technology can realize the machining work of different types of threads, meet the needs of actual equipment machining, and modify the parameters, thus providing the flexibility of thread machining and boosting the application of CNC machining technology in thread machining. In 2022, Chen Xiaosheng et al. completed the milling of a new material (duralumin bronze alloy) with the help of PowerMLL technology, giving a relatively mature CNC machining system, providing a certain reference and ideas for the subsequent processing of new materials, and promoting the development of CNC machining technology. In the same year, Zhang Lingling used the Master CAM2017 software in a CNC milling processing project, which helped realize a multi-dimensional control of parts, with multi-dimensional model and high-precision control to regulate the trajectory and accuracy of parts, thus improving the processing quality and efficiency of the parts themselves (Zhang, 2022).
This paper aims to further extend the research on the optimization of CNC milling parameters. Through experimentation and data analysis, the influence of different parameters on the machining effect was discussed, a mathematical model was established and an optimization algorithm was used to obtain the best combination of milling parameters. Through the present research, we expect to provide a more scientific and reasonable parameter optimization method for the application of CNC machining technology, so as to promote the development of China’s machinery manufacturing industry and improve its competitiveness in the global manufacturing industry.
2 Mechanical parts processing technology
The machining process of mechanical parts is a crucial part of the modern manufacturing industry and is directly related to the accuracy, surface quality, and overall performance of parts. In this process, CNC machining technology has become the mainstay of the manufacturing industry, and the movement of tools is precisely controlled by computer programs to achieve high-precision machining of parts (Li, 2023). First, the design drawing of the part is converted into a numerical control program, which defines the key parameters such as the tool path, motion speed, and feed material removal rate. Then, the selection of these parameters will directly affect the machining effect of the parts.
In the actual machining process, the first preparation is made before cutting, including clamping the workpiece, selecting the appropriate tool, determining the initial tool position, etc. Then, the CNC machine tool starts to automatically run according to the preset program, cutting, milling, and executing other operations. As the operation progresses, it is necessary to constantly adjust the motion parameters of the tool according to the specific situation to ensure the accuracy and efficiency of the machining process.
The refinement and automation of the machining process of mechanical parts not only improves production efficiency and reduces production costs, but also provides higher quality parts for various industries. In today’s manufacturing industry, which is increasingly moving in the direction of digitalization and intelligence, processing technology will continue to play a key role in providing solid technical support for the manufacture of various products.
In this paper, the milling parameters of small impellers have been proven to be optimized by NC machining technology. In fact, there are many factors affecting the cutting parameters, so it is difficult to determine the optimal cutting parameters. It is necessary to consider the influence of tool stiffness, cutting speed, wear resistance, and other factors on the roughing parameters. The margin in the finishing stage is small, and the influence on the quality of the machined surface is mainly considered. Since the main purpose of this study is to improve the machining surface quality of mechanical parts, the focus will be on the investigation of small impeller CNC milling processes on the surface quality of the process parameters, such as cutting speed
The cutting parameters change with each machining process, so it is necessary to optimize the cutting parameters. When machining the important parts of the small impeller, the method of increasing the speed of the main shaft and reducing the feed rate is generally used to ensure machining accuracy and surface quality. In addition, the selection of specific parameters should also be combined with the Practical Machine Tool Design Manual and the Cutting Manual to determine.
3 Optimization of Process Parameters through an Algorithmic Model
3.1 General principles of algorithmic model optimization of process parameters
Optimization of process parameters by an algorithmic model is of great importance in the field of mechanical part machining (Wang et al., 2022). It makes the machining process more efficient through the application of mathematical modeling and optimization algorithms. In NC machining, the selection of process parameters directly affects the machining quality and efficiency of parts, so the implementation of an algorithmic model becomes an effective way to improve the overall machining performance.
First of all, the establishment of a mathematical model is the basis of algorithm optimization. A comprehensive and accurate mathematical model can be established by considering all the parameters involved in the machining process. This includes the mathematical relationships between key parameters such as tool speed, feed material removal rate, and depth of cut, in addition to the effects of these parameters on machining results. Through mathematical modeling, a model framework can be formed to provide specific reference and basis for the subsequent optimization algorithm.
Second, optimization algorithms can be used to adjust the process parameters. Commonly used optimization algorithms include genetic algorithms, simulated annealing algorithms, particle swarm optimization algorithms, etc. (Gao et al., 2023; Zhou, 2023). These algorithms find the optimal solution by iteratively adjusting the combination of process parameters to achieve the best balance between machining efficiency and part quality. In practical applications, through the selection of algorithms and the adjustment of parameters, the best combination of process parameters can be found more accurately and the processing efficiency can be improved.
In summary, the optimization of process parameters by an algorithmic model brings new ideas and methods to the machining of mechanical parts. Through the organic combination of mathematical modeling and optimization algorithms, intelligent control of the processing process is realized, which strongly supports the improvement of accuracy and efficiency in the manufacturing industry. The continuous development of this field will promote the further improvement of CNC machining technology in the future. The algorithm used here is a genetic algorithm, which has five characteristics: First, the genetic algorithm starts with a series of string sets of the problem, and has wide coverage, which is conducive to global optimization. Second, simultaneous search can be performed on multiple individuals in the population, that is, multiple solution sets can be processed within the population range, so that the algorithm can be realized and evolved, and the possibility of local optimal solutions can be reduced in the population. Third, the search direction generally does not choose the rule of certainty, but chooses the transition rule of genetic probability to guide the population. Fourth, during the evolution of the algorithm, the genetic algorithm will search itself to screen out the best individuals. Fifth, search and calculation can be started from n initial points, which is suitable for large-scale group optimization, and it is difficult to fall into the local optimal solution.
3.2 Optimization of process parameters
3.2.1 Optimization method
The idea of optimization has been vigorously promoted in the field of modern machinery. With the increasing maturity of current computer technology, optimization methods, and theories have been developed by colleges and universities. Mathematical optimization is an optimization scheme obtained through accurate calculation and comparison. When using this method, the cutting quantity should be converted into a mathematical model, and the target constraint function should be constructed to find out the constraints during processing, so that the optimal solution can be calculated with the help of a computer.
Generally speaking, the implementation of a mathematical model mainly involves three aspects: first, the design variable
3.2.2 Selection of optimized design variables
In the mathematical model, the selection of optimization variables is the key point of the whole model, which has an important impact on the final result of the optimization goal. Optimization variables are controllable factors. Generally, the more variables are selected, the easier the optimization results will be to achieve the expected effect. Cutting speed
3.2.3 Construction of objective function
Generally, objective function refers to the functional relationship between the optimized target quantity and the optimized variable. By solving for the minimum or maximum value of the objective function, the optimal solution of the optimized variable can be obtained. This study takes surface roughness and residual stress as optimization objectives, constructs multiple objective functions, and then determines constraint conditions. Although there are more constraints, it is not necessary to carry out appropriate restrictions, and reasonable constraints should be selected for the work and environment in the actual processing. According to the characteristics of NC milling of the small impeller, five constraint functions were established in the optimization process, including spindle speed constraint, feed material removal rate, axial cutting depth constraint, and radial cutting depth constraint. The corresponding function expressions are shown below:
The above formula is the spindle speed constraint function;
The above formula is the feed speed constraint function;
The above formula is the constraint function of the axial depth of the tangent;
The above formula is the constraint function of the radial depth of cut;
3.2.4 Optimization of process parameters based on a genetic algorithm
Population size, as the operational object of a genetic algorithm, should be determined first and should not be too small, otherwise, it would be prone to the occurrence of morbid genes among modern relatives, causing the competitiveness of the population to be lower and lower, with the algorithm stagnating and being unable to continue to operate. The size of the population should not be too large either, otherwise, the calculation results will not converge and the temperature of the population will be reduced. After careful consideration, it was decided to set the population range to 10–200.
In the genetic algorithm, the number of populations must be determined before subsequent operations can be carried out. During the period, the number of populations should not be too small, otherwise it is easy to have pathological gene problems, which will reduce the competitiveness of the population and make it impossible to continue operations. So a reasonable range was set for the population evolution algebra, that is, 50–500.
During evolution, new populations are produced by crossing, and if the probability of crossing is too low, the rate of population renewal and search will be reduced. If the crossover probability is too high, the existing size of the population will be destroyed and the optimal population solution will be lost. Therefore, after consideration, the crossover probability range was set to 0.4–0.99.
Variation can enrich the diversity of the population and expand the size of the population. If the probability of mutation in the population is too low, the effective gene in the population will be lost; if the probability of mutation in the population is too high, the probability of population destruction will be increased.
For ease of calculation, the population range was consequently set to 200, the population evolution algebra was set to 300, the crossover probability range was set to 0.9, and the mutation probability was set to 0.15. Part of the program obtained is as follows:
Genetic algorithm parameter initialization
Maxgen = 150; % evolutionary algebra
Sizepop = 100; % Population size
Pcross = [0.2]; % cross probability, 0–1
Pmutation = [0.1]; % probability of variation, 0–1
The optimal solution was obtained with the help of MATLAB software, with
4 Experimental results and discussion
Based on the above theoretical research and parameter selection, it was decided to effectively explore the effect of small impeller optimization by empirical means, clarifying the role of the CNC machining experiment in workpiece processing, as shown below.
4.1 Selection of experimental equipment
In order to test the effect of the optimization of the impeller’s technological parameters, the numerical control machining experiment om the impeller was carried out by using the optimized technological parameter values to test whether the experimental optimization of the technological parameters could improve the surface quality of the impeller. The processing equipment is JDGR200A10SH five-axis linkage processing machine. Machining tool selection T1,D4, 0° ball end milling cutter; T2, D1.5,3° ball end milling cutter; T3/T4,D1,2° ball end milling cutter, the material of the four processing tools are cemented carbide.
4.2 Experimental process
The experimental process was mainly carried out through the following 5 steps: First, the blank and the tool were installed. The turntable A axis was turned back to 0°, with the turntable kept in a horizontal position; the selected machining tool was then placed in the tool library. Second, the workpiece clamping was prepared. The blank material chosen was a cylindrical aluminum alloy bar, and its stability must be ensured when clamping. In order to reduce the influence of the moment of inertia on the processing of the small impeller, the blank was fixed with a three-jaw chuck to reduce the installation time as much as possible and improve the clamping efficiency and accuracy. Third, the knife point and the knife were changed. Before machining, the cutter point was set to the reference point of the small impeller. The reference point of the machine tool was set as the tool change point to avoid interference and collisions between the tool and the machine tool. Fourth, the machine was corrected. Because the selected blank of the small impeller was a cylindrical bar, and the initial machining position of the impeller blade was difficult to determine, it was necessary to ensure that the workpiece was in the coordinate system on the five-axis CNC machine tool, to then help the workpiece to be quickly located on the machine tool. Fifth, the simulation code was imported, using the input function on the machine tool; the optimized process parameters and post-processing tool path code program were directly stored in the CNC machine tool system. The machine tool was then started, and the milling process was initiated, with the processing site shown in Figure 1.
4.3 Experimental detection
After NC machining of the small impeller with the help of the five-axis motor, the small impeller obtained is shown in Figure 2.
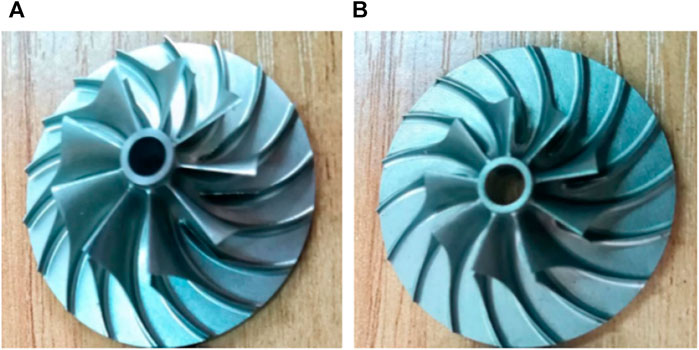
FIGURE 2. (A) Small impeller machined by process parameters before optimization (B) The small impeller obtained by optimizing the process parameters.
The process parameters before and after optimization were compared, as shown in Table 1.
It can be seen that the axial cutting depth and radial cutting depth are close to the minimum value, and the spindle speed and feed per tooth are larger. The experiment mainly tested the machining surface quality of the impeller, so it was necessary to test the surface roughness and residual stress of the impeller. Among them, in the surface roughness detection link, the surface roughness meter was used, and its principle is as follows: When the stylus on the instrument was swept vertically across the surface of the blade, the stylus is sensitive and rapid vertical rotation because of the uneven contact with the surface of the blade. At this point, under the action of the roughness measuring instrument, the motion signal is transformed into an electrical signal. After amplification and filtering processing, the electrical signal is transformed into the required digital signal. Finally, the surface roughness of the blade was directly displayed on the main screen of the measuring instrument. In addition, the surface accuracy, size, and quality of the blade will directly affect the overall mechanical performance of the small impeller, so the machining of the blade needs to be strictly carried out according to the requirements, such as a surface roughness requirement of
It can be seen that the surface roughness of the small impeller was reduced by 28.04% when the optimized process parameters were used for milling, and at the same time the processing technology requirements for the surface roughness were met, which further proves that the machining surface quality of the small impeller obtained under the optimized processing parameters is up to standard and of good quality.
Residual stress detection used the X-350A X-ray stress meter, which is part of the X-ray diffraction analyzer; it was able to measure the residual stress at any point and in any direction on the workpiece surface within a short time without damage. The algebraic sum of residual stress and load stress, i.e., the actual stress, was measured when the structure was load-bearing. The technical parameters of the X3350A X-ray stress meter are shown in Table 3.
Three random points on the blade of the small impeller were measured by means of a measuring instrument, and the residual stress
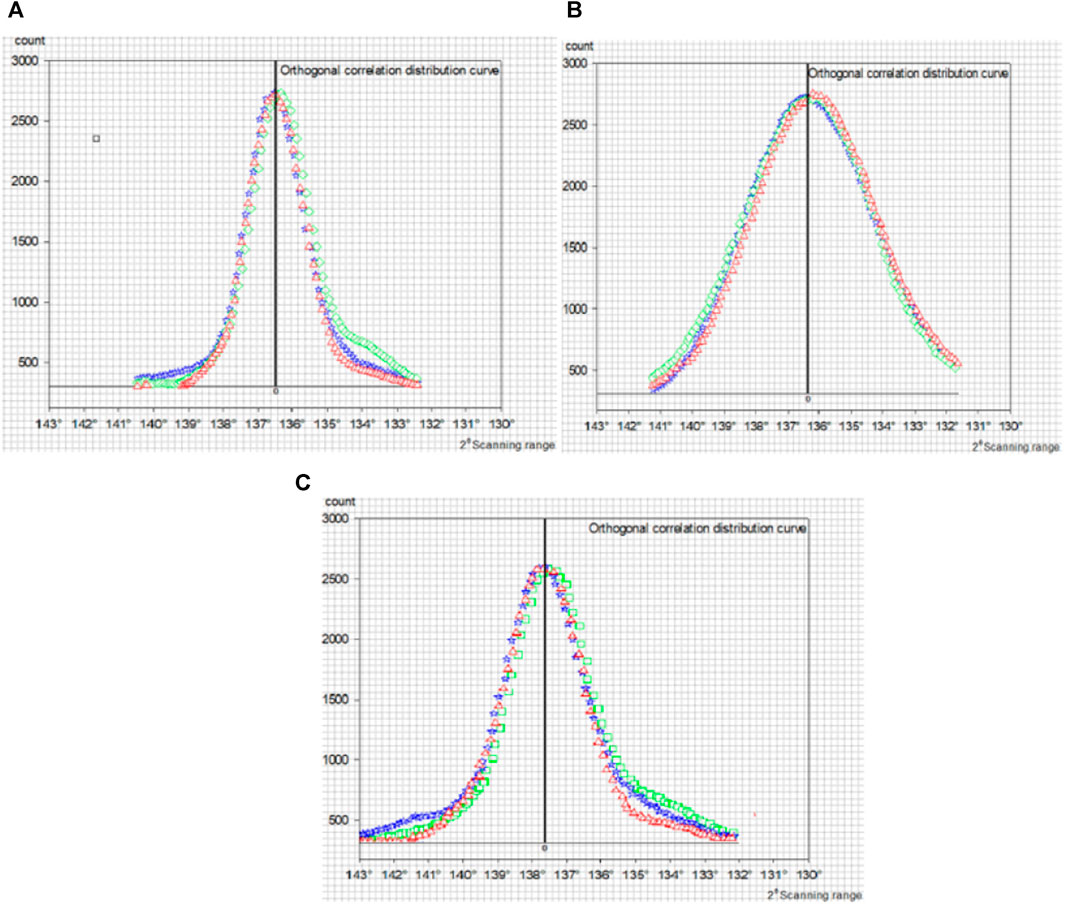
FIGURE 3. Orthogonal correlation function distribution curve. (A) random point A orthogonal correlation function distribution curve, (B) random point B orthogonal correlation function distribution curve, (C) random point C orthogonal correlation function distribution curve.
From the average measurement results of the three random points, it can be seen that the residual stress value
5 Conclusion
Based on the above research content, the milling parameters of mechanical parts were optimized by CNC machining technology, and a series of remarkable results were obtained in this study. First of all, by citing the conclusions of international and domestic scholars, we gained an in-depth understanding of the importance of CNC machining technology in improving the efficiency and quality of part manufacturing. Drawing on the experience of our colleagues, we have studied the optimization of CNC milling parameters more systematically in order to further improve machining efficiency and part quality. Second, through detailed research methods, we used advanced CNC machining equipment to clarify the impact of key parameters such as tool speed, feed speed, rate cutting depth on the milling process. By establishing a mathematical model and applying an optimization algorithm, the optimal combination of NC milling parameters was successfully determined. Finally, through the analysis of the experimental results, we verified the significant advantages of the optimized NC milling parameters in different working conditions, such as using the optimized process parameters to mill the small impeller. The surface roughness was reduced by 28.04%. It could be seen from the average measurement results of the three random points that the residual stress value after optimization,
Data availability statement
The original contributions presented in the study are included in the article/supplementary material, further inquiries can be directed to the corresponding author.
Author contributions
ZW: Conceptualization, Data curation, Formal Analysis, Funding acquisition, Investigation, Methodology, Project administration, Resources, Software, Supervision, Validation, Visualization, Writing–original draft, Writing–review and editing.
Funding
The author declares that no financial support was received for the research, authorship, and/or publication of this article.
Conflict of interest
The author declares that the research was conducted in the absence of any commercial or financial relationships that could be construed as a potential conflict of interest.
Publisher’s note
All claims expressed in this article are solely those of the authors and do not necessarily represent those of their affiliated organizations, or those of the publisher, the editors and the reviewers. Any product that may be evaluated in this article, or claim that may be made by its manufacturer, is not guaranteed or endorsed by the publisher.
References
Chen, X. S., and Feng, K. (2022). Research on NC milling technology of duralumin bronze alloy based on PowerMILL. Mold. Manuf. 22 (04), 74–76.
Gao, H. C., Xue, S., Xiao, M. X., Meng, Z. X., Hu, W., and He, Q. Q. (2023). Optimization of injection molding process parameters of air purifier Shell based on orthogonal test and BP Neural network-Genetic algorithm. Precis. Form. Eng. 15 (08), 204–210.
Li, A. H., and Ren, F. (2021). Thread nc machining based on Mastercam automatic programming study. J. coal mine Mach. 42 (03), 199–201. doi:10.13436/j.mKJX.202103062
Li, S. (2023). Research on application of CNC technology in machining of automobile parts. Automob Parts (13), 63–65.
Liu, X. X., Li, M., Wan, J., and Gao, L. Y. (2022). Large titanium alloy casting CNC processing technology research and application. J. Int. Combust. Engine Access 2022 (04), 48–50. doi:10.19475/j.carolcarrollnki.Issn1674-957-x.2022.04.016
Sakthivel, V. S. K. S. (2019). Optimization of machining parameters in CNC end milling of al7068 using genetic algorithm. J. Balk. Tribol. Assoc. 25 (2).
Vardhan, M. V., Sankaraiah, G., and Yohan, M. (2018). Optimization of cutting parameters and prediction of Ra and MRR for machining of P20 steel on CNC milling using artificial neural networks. Mater. Today 5 (13), 27058–27064. doi:10.1016/j.matpr.2018.09.010
Wang, H. J., Wang, X. Q., Zhu, Q. P., and Wang, P. G. (2022). Multi-objective optimization of ultrasonic rolling extrusion process Parameters based on Simulated annealing. J. Plast. Eng. 29 (04), 14–22.
Yang, P. Q., and He, X. J. (2023). Research on optimization of machining parameters in CNC milling. China Equip. Eng. (09), 8–11.
Yang, W. Z. (2023). CNC machine tool processing parameter optimization and test. Agric. Mach. Use Maint. 10, 56–59. doi:10.14031/j.carolcarrollnki.NJWX.2023.10.014
Zhang, L. L. (2022). Analysis on the application of Master CAM2017 in CNC milling. China Equip. Eng. (02), 15–16.
Zhang, W. X. (2023). Research on machining parameter optimization of NC milling based on deep reinforcement learning. China High-Tech (11), 40–42. doi:10.13535/j.cnki.10-1507/n.2023.11.09
Keywords: cnc machining, mechanical parts, milling parameters, optimize, automation
Citation: Wang Z (2024) The milling parameters of mechanical parts are optimized by NC machining technology. Front. Mech. Eng 10:1367009. doi: 10.3389/fmech.2024.1367009
Received: 08 January 2024; Accepted: 12 February 2024;
Published: 05 March 2024.
Edited by:
Michal Puskar, Technical University of Košice, SlovakiaReviewed by:
Tadeusz Mikolajczyk, Bydgoszcz University of Science and Technology, PolandShahrokh Hatefi, Nelson Mandela University, South Africa
Copyright © 2024 Wang. This is an open-access article distributed under the terms of the Creative Commons Attribution License (CC BY). The use, distribution or reproduction in other forums is permitted, provided the original author(s) and the copyright owner(s) are credited and that the original publication in this journal is cited, in accordance with accepted academic practice. No use, distribution or reproduction is permitted which does not comply with these terms.
*Correspondence: Zairu Wang, wzairu@hotmail.com