Thermal and solutal energy transport analysis in entropy generation of hybrid nanofluid flow over a vertically rotating cylinder
- 1Department of Mathematics, Quaid-I-Azam University, Islamabad, Pakistan
- 2Department of Mathematics, Faculty of Science, University of Tabuk, Tabuk, Saudi Arabia
- 3Faculty of Engineering and Technology, Future University in Egypt, New Cairo, Egypt
- 4Department of Mathematics, College of Science, Taif University, Taif, Saudi Arabia
- 5Mechanical Engineering Department, College of Engineering and Islamic Architecture, Umm Al-Qura University, Makkah, Saudi Arabia
- 6Mechanical Engineering Department, College of Engineering, Prince Sattam Bin Abdulaziz University, Wadi Addawaser, Saudi Arabia
- 7Production Engineering and Mechanical Design Department, Faculty of Engineering, Mansoura University, Mansoura, Egypt
An investigation of an axisymmetric mixed convective boundary layer flow of silver-titanium dioxide/water (
1 Introduction
Nanofluids exhibit superior heat transport features to those of regular fluids. The effectiveness of heat exchange and the compactness of lower thermal conductivity fluid are delayed in the process, but many techniques are used to develop heat transport phenomena. One innovative trick is used to improve the heat transport/thermal conductivity of a fluid through the suspension of nanoparticles in the base liquids. Nanofluid thermal conductivity mainly depends upon the volume fraction of nanoparticles. The thermal conductivity of nanoparticles is expected to be greater than that of usual fluids. These nanoparticles are very small, not more than 100 mm. The term nanofluids was first used to refer to the fluids along suspended nanoparticles by Choi [1]. Some experimental outcomes have been obtained by Eastman et al. [2] with respect to the development of thermal conductivity with the suspension of
In the modern era, entropy generation is the most valuable subject for the researcher, in which irreversible processes of mass and heat transport occur. The Second Law of Thermodynamics entirely revolves around entropy. The design of the system that depends upon heat transport has a valuable application in the real life of the entropy generation. Entropy minimized energy losses in the system. Heat and mass transport processes occur in heat exchange, heat engines, fluid flow, heat pumps, refrigerators, air conditioners, power plants, anelastic deformation, and substance mixing and expansion, among other sites. Significant work has been done on entropy with application to various fields by Adrian Bejan [21–24]. Mahian et al. [25] elaborated convective heat transport augmentation with the use of nanofluid flow and entropy generation impacts to develop high heat flux cooling devices. Siavashi et al. [26] scrutinized the heat transport and entropy generation characteristics of nanofluid flow across an annular pipe in a two-phase combination model. Rashid et al. [27] observed entropy generation on ferromagnetic fluid flows along the slip and nonlinear radiation impact across a stretching sheet. Khan et al. [28] reviewed the modeling and computational study of hybrid nanofluids subject to entropy generation. Muhammad et al. [29] examined the Darcy–Forchheimer boundary layer flow influenced by activation energy and entropy generation across a curved surface. Recent studies related to the investigation of entropy generation are given in Refs. [30–33].
Heat transportation occurs due to temperature gradients. There are three modes of heat transfer conduction, radiation, and convection. Heat transportation phenomena have many important industrial and engineering applications, such as heat exchange, power generation, nuclear power, refrigeration, petroleum production, and so on. Fourier [34] first developed the law of heat conduction to analyze the rate of heat transport in a system. Ellahi et al. [35] scrutinized the heat transfer rate of a mixed convective boundary layer fluid flow across a vertical permeable slender cylinder. The heat and mass transportation of a non-Newtonian fluid flow influenced by transverse magnetic field and suction/injection effect towards permeable stretching sheet was developed by Sandeep et al. [36]. The heat transfer scrutiny of MHD micropolar fluid flows subject to joule heating and chemical reactions across a stretching sheet were explored by Dawar et al. [37]. Ramadan et al. [38] analyzed that flow and heat transport in a microchannel influenced by gas cooling conditions and thermal creep. Finally, other studies of heat transfer are presented in Refs. [39–48].
The aim of this examination is to study the 3D axisymmetric MHD flow of a viscous nanofluid with nanoparticles generated by vertically rotating a stretching cylinder. The main concern of this existing inquiry is to identify entropy generation evaluation of mixed convective hybrid nanofluid flow with modified Fourier’s and Fick’s law across a rotating and stretching surface. Moreover, convective boundary conditions are also considered to identify a flow regime. The formulated fluid model is converted into a pair of ODEs by adopting appropriate similarity variables. The coupled ODEs are numerically manipulated with the aid of BVP4C MATLAB built-in technique [49–53]. A graphical inquiry into the evolving parameters with respect to temperature distribution, concentration distribution, and velocity profile is established and discussed. The comparison of current outcomes with previous investigation is presented, and a good harmony is shown between them.
2 Flow modelling
Here, we observe a steady, incompressible, axisymmetric laminar, and mixed convective boundary layer flow of
The related surface and ambient conditions are stated as follows:
In the above Eqs. 1–6,
2.1 Hybrid nanofluid model
The experimental relationship for an Ag-TiO/water hybrid nanofluid is given as follows [14],
2.1.1 Hybrid nanofluid dynamic viscosity
2.1.2 Hybrid nanofluid density
2.1.3 Hybrid nanofluid specific heat capacity
2.1.4 Hybrid nanofluid thermal conductivity
2.1.4 Thermal and solutal volumetric coefficient
Here, s1 and s2 specify the silver (Ag) and titanium dioxide (TiO2) nanoparticles, respectively. Further, the solid volume fraction of Ag is represented by
Table 1 presents the thermo-physical features of convectional fluid and hybrid nanofluid, as follows:
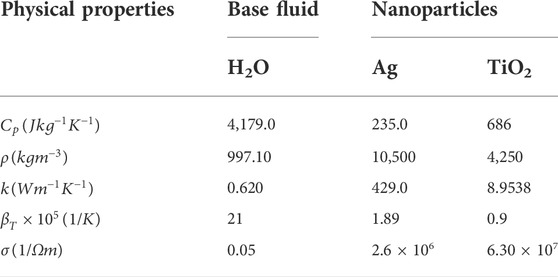
TABLE 1. Thermophysical characteristics of base liquid and nanoparticles [14].
2.2 Similarity variables
The applicable similarity variables are signified as in [50]:
Using Eq. 12, Eqs. 2–10 take the following form:
The convenient conditions are as follows:
The parameters involved are given as Reynold number
The above equations hold only for the positive Reynold number, and the solution convergence criteria are very slow for the lower Reynolds numbers. To improve solution convergence, we use the transformation
The convenient conditions at the boundary are as follows:
2.3 Entropy generation
To include irreversibility sources, for present article, entropy generation consists of the heat transport, mass transport, and joule heating impact. The equation of entropy generation is stated as follows:
Entropy generation
Now, using the transformation
In the above equation, the parameter of the temperature difference is
2.4 Skin friction
The quantities of interest, such as skin friction, are very precious for the engineering point of view. No transport of heat and mass rate were observed in the current investigation. The mathematical form of skin fraction is as follows:
In Eq. 29,
Equation (30) in its dimensionalized form is as follows:
3 Graphical discussion
The numerical algorithm BVP4C in MATLAB is used to solve Eqs. 20–23 along with the boundary conditions (Eqs. 24, 25). The Bvp4c technique is only applicable to first-order ordinary differential equations. Thus, we first transform the third and second-order equations into a first-order differential equation with the use of a new variable. References [32–35] are recommended to readers because this system is well-known. Table 2 displays an assessment of the present outcomes in comparison with previously published data. From the table, it can be concluded that the current outcomes show good harmony with the results produced by Fang and Yao [31]. Table 3 presents the tabulated values for skin friction for different emerging parameters. It can be observed from the table that due to enhancement of the estimation of the Reynold number and magnetic parameters, the numerical value of skin friction is enhanced, while it falls due to the enhancement of the value of mixed convection and buoyancy ratio parameters it is reduced. For several growing parameters, graphical results are achieved covering axial and swirl velocity, temperature, and concentration field. Figures 2A,B illustrate the influence of the magnetic parameters on swirl and axial velocity. The figure shows that both fluid velocities diminish with a higher estimation of the magnetic parameter. When the magnetic parameter value is increased, Lorentz force appears, which enhances resistive force in the fluid flow, and as a result, the fluid velocity is reduced. The upshot of the influence of the buoyancy ratio parameter on swirl and axial velocity is discussed in Figures 2C,D. The figure shows that axial velocity improves while swirl velocity declines with growing estimation of the buoyancy ratio parameter, and the same result is found for the mixed convection parameter portrayed in Figures 2E,F. Physically, both buoyancy movement forces and forced convection progress in the same direction, boosting the values of the buoyancy ratio parameter. Thus, because the buoyancy effect produces resistive force to the rotation of fluid particles, the axial velocity of liquid flow grows, while the swirl velocity decreases. A relationship between the temperature and concentration distribution via thermal and solutal stratification is observed in Figures 3A,B. The fluid temperature and concentration are both diminished with thermal and solutal relaxation parameter effects. Physically, the mass and heat transport in the fluid flow are reduced with the dimensionless thermal and solutal relaxation parameter; as a result, both the profiles diminish. Figures 4A,B explore the upshot of thermal and solutal Biot number on temperature and concentration field. Greater convection is caused by an increment in the thermal Biot number, resulting in higher temperature and correlated thickness of boundary layer. The same behavior is seen for the solutal Biot number that is depicted in Figure 4B. The response of the Eckert number on temperature and Schmidt number on concentration profile is observed in Figures 5A,B, respectively. If the Eckert number is strong, the fluid components are more energetic due to energy storage. As a result, there is an upsurge in fluid temperature (see in Figure 5A). Figure 5B discloses the influence of the Schmidt number on concentration distribution. It is seen that by boosting the values of
4 Concluding remarks
In the present analysis, the mixed convection hybrid nanofluid flow is discussed using a modified Fourier and Ficks law. Entropy generation is calculated. Further, the influences of heat generation/absorption, chemical reaction, Joule heating, and the thermal and solutal Biot number are discussed. This analysis presents the thermal characteristics of hybrid nanofluid, which presents many novel applications in the thermal engineering, such as nuclear reactions, heat exchangers, cooling and heating devices, fission and fusion chemical reactions, coolant in machining and manufacturing, thermal extrusion processes, and much more. The bvp4c approach is utilized to solve the problem numerically. The key findings of the present results are as follows:
➢ Axial and swirl velocities are reduced due to Lorentz forces produced by higher magnetic parameters.
➢ The axial velocity of fluid flow is enhanced and the swirl velocity is decreased with the buoyancy ratio parameter, as the buoyancy effect generates resistive force to the rotation of fluid particles.
➢ The temperature field is a growing function of thermal Biot number and the Eckert number but presents a diminishing function of thermal relaxation parameter.
➢ For larger values of the Schmidt number and solutal relaxation, the parameter concentration field is reduced, but for larger solutal Biot numbers, it is enhanced.
➢ Entropy generation is boosted with increased Reynolds number and reduced with falling parameter of temperature difference.
Data availability statement
The original contributions presented in the study are included in the article/supplementary material, and further inquiries can be directed to the corresponding author.
Author contributions
SA: conceptualization, methodology, software, formal analysis, writing-original draft preparation. NA: Software, Resources, Writing - review and editing. MK: writing original draft preparation, data curation, investigation, visualization, validation. EA: Funding acquisition, Writing - review and editing, Investigation. ET-E: Funding acquisition, Writing - review and editing, Visualization. KGe: Writing - review and editing, validation. KGu: Methodology, Writing - review and editing. AG: Methodology, Writing - review and editing, Resources.
Acknowledgments
The authors thank the Taif University Researcher for supporting project number TURSP-2020/16, Taif University, Taif, Saudi Arabia. The authors would like to thank the Deanship of Scientific Research at Umm Al-Qura University for supporting this work by Grant Code: 22UQU4331317DSR49.
Conflict of interest
The authors declare that the research was conducted in the absence of any commercial or financial relationships that could be construed as a potential conflict of interest.
Publisher’s note
All claims expressed in this article are solely those of the authors and do not necessarily represent those of their affiliated organizations, or those of the publisher, the editors and the reviewers. Any product that may be evaluated in this article, or claim that may be made by its manufacturer, is not guaranteed or endorsed by the publisher.
References
1. Choi SU, Eastman JA. Enhancing thermal conductivity of fluids with nanoparticles (No. ANL/MSD/CP-84938. IL (United States): Argonne National Lab. (1995). CONF-951135-29).
2. Eastman JA, Choi US, Li S, Thompson LJ, Lee. S. Enhanced thermal conductivity through the development of nanofluids. MRS Proc (1996) 457:3. doi:10.1557/proc-457-3
3. Ur Rehman F, Nadeem S. Heat transfer analysis for three-dimensional stagnation-point flow of water-based nanofluid over an exponentially stretching surface. J Heat Transfer (2018) 140(5). doi:10.1115/1.4038359
4. Sheikholeslami M. Numerical investigation for CuO-H2O nanofluid flow in a porous channel with magnetic field using mesoscopic method. J Mol Liquids (2018) 249:739–46. doi:10.1016/j.molliq.2017.11.069
5. Bilal M, Sagheer M, Hussain S. Numerical study of magnetohydrodynamics and thermal radiation on Williamson nanofluid flow over a stretching cylinder with variable thermal conductivity. Alexandria Eng J (2018) 57(4):3281–9. doi:10.1016/j.aej.2017.12.006
6. Maskeen MM, Zeeshan A, Mehmood OU, Hassan M. Heat transfer enhancement in hydromagnetic alumina–copper/water hybrid nanofluid flow over a stretching cylinder. J Therm Anal Calorim (2019) 138(2):1127–36. doi:10.1007/s10973-019-08304-7
7. Reddy SRR, Bala Anki Reddy P, Rashad AM. Activation energy impact on chemically reacting Eyring–Powell nanofluid flow over a stretching cylinder. Arab J Sci Eng (2020) 45:5227–42. doi:10.1007/s13369-020-04379-9
8. Ullah I, Ullah R, Alqarni MS, Xia WF, Muhammad T. Combined heat source and zero mass flux features on magnetized nanofluid flow by radial disk with the applications of Coriolis force and activation energy. Int Commun Heat Mass Transfer (2021) 126:105416. doi:10.1016/j.icheatmasstransfer.2021.105416
9. Khan MN, Nadeem S. A comparative study between linear and exponential stretching sheet with double stratification of a rotating Maxwell nanofluid flow. Surf Inter (2021) 22:100886. doi:10.1016/j.surfin.2020.100886
10. Dawar A., Shah Z., Tassaddiq A., Kumam P., Islam S., Khan W. A convective flow of Williamson nanofluid through cone and wedge with non-isothermal and non-isosolutal conditions: A revised buongiorno model. Case Studies in Thermal Engineering (2021) 24:100869. doi:10.1016/j.csite.2021.100869
11. Dawar A., Saeed A., Kumam P. Magneto-hydrothermal analysis of copper and copper oxide nanoparticles between two parallel plates with Brownian motion and thermophoresis effects. International Communications in Heat and Mass Transfer (2022) 133:105982. doi:10.1016/j.icheatmasstransfer.2022.105982
12. Dawar A., Wakif A., Thumma T., Shah N. A. Towards a new MHD non-homogeneous convective nanofluid flow model for simulating a rotating inclined thin layer of sodium alginate-based Iron oxide exposed to incident solar energy. International Communications in Heat and Mass Transfer (2022) 130:105800. doi:10.1016/j.icheatmasstransfer.2021.105800
13. Waini I., Ishak A., Pop I. Hybrid nanofluid flow past a permeable moving thin needle. Mathematics (2020) 8(4):612. doi:10.3390/math8040612
14. Kumar R.N., Gowda R.P., Abusorrah A.M., Mahrous Y.M., Abu-Hamdeh N.H., Issakhov A., Rahimi-Gorji M., Prasannakumara B.C. Impact of magnetic dipole on ferromagnetic hybrid nanofluid flow over a stretching cylinder. Phys Scr (2021) 96(4):045215. doi:10.1088/1402-4896/abe324
15. Bakar SA, Arifin NM, Bachok N, Ali FM. Effect of thermal radiation and MHD on hybrid Ag–TiO2/H2O nanofluid past a permeable porous medium with heat generation. Case Stud Therm Eng (2021) 28:101681. doi:10.1016/j.csite.2021.101681
16. Salahuddin T, Siddique N, Khan M, Chu YM. A hybrid nanofluid flow near a highly magnetized heated wavy cylinder. Alexandria Eng J (2022) 61(2):1297–308. doi:10.1016/j.aej.2021.06.014
17. Dawar A, Bonyah E, Islam S, Alshehri A, Shah Z. Theoretical analysis of Cu-H2O, Al2O3-H2O, and TiO2-H2O nanofluid flow past a rotating disk with velocity slip and convective conditions. J Nanomater (2021) 1–10. doi:10.1155/2021/5471813
18. Dawar A, Islam S, Shah Z. A comparative analysis of the performance of magnetised copper–copper oxide/water and copper–copper oxide/kerosene oil hybrid nanofluids flowing through an extending surface with velocity slips and thermal convective conditions. Int J Ambient Energ (2022) 1–19. doi:10.1080/01430750.2022.2063387
19. Ramzan M, Dawar A, Saeed A, Kumam P, Watthayu W, Kumam W. Heat transfer analysis of the mixed convective flow of magnetohydrodynamic hybrid nanofluid past a stretching sheet with velocity and thermal slip conditions. Plos one (2021) 16(12):e0260854. doi:10.1371/journal.pone.0260854
20. Gao J, Liu J, Yue H, Zhao Y, Tlili I, Karimipour A. Effects of various temperature and pressure initial conditions to predict the thermal conductivity and phase alteration duration of water based carbon hybrid nanofluids via MD approach. J Mol Liquids (2022) 351:118654. doi:10.1016/j.molliq.2022.118654
22. Bejan A, Second-law analysis in heat transfer and thermal design. Adv Heat transfer (1982). p. 1–58.
23. Bejan A. Entropy generation minimization: The new thermodynamics of finite‐size devices and finite‐time processes. J Appl Phys (1996) 79(3):1191–218. doi:10.1063/1.362674
24. Bejan A. Entropy generation minimization: The method of thermodynamic optimization of finite-size systems and finite-time processes. Boca Raton, FL: CRC Press (1996).
25. Mahian O, Kianifar A, Kleinstreuer C, Moh’d A AN, Pop I, Sahin AZ, et al. A review of entropy generation in nanofluid flow. Int J Heat Mass Transfer (2013) 65:514–32. doi:10.1016/j.ijheatmasstransfer.2013.06.010
26. Siavashi M, Bahrami HRT, Saffari H. Numerical investigation of flow characteristics, heat transfer and entropy generation of nanofluid flow inside an annular pipe partially or completely filled with porous media using two-phase mixture model. Energy (2015) 93:2451–66. doi:10.1016/j.energy.2015.10.100
27. Rashid M, Khan MI, Hayat T, Khan MI, Alsaedi A. Entropy generation in flow of ferromagnetic liquid with nonlinear radiation and slip condition. J Mol Liquids (2019) 276:441–52. doi:10.1016/j.molliq.2018.11.148
28. Khan MI, Alsaedi A, Hayat T, Khan NB. Modeling and computational analysis of hybrid class nanomaterials subject to entropy generation. Comput Methods Programs Biomed (2019) 179:104973. doi:10.1016/j.cmpb.2019.07.001
29. Muhammad R, Khan MI, Jameel M, Khan NB. Fully developed Darcy-Forchheimer mixed convective flow over a curved surface with activation energy and entropy generation. Comput Methods Programs Biomed (2020) 188:105298. doi:10.1016/j.cmpb.2019.105298
30. Riaz A, Bobescu E, Ramesh K, Ellahi R. Entropy analysis for cilia-generated motion of Cu-blood flow of nanofluid in an annulus. Symmetry (2021) 13(12):2358. doi:10.3390/sym13122358
31. Riaz A, Abbas T, Zeeshan A, Doranehgard MH. Entropy generation and MHD analysis of a nanofluid with peristaltic three-dimensional cylindrical enclosures. Int J Numer Methods Heat Fluid Flow (2021) 31:2698–714. doi:10.1108/hff-11-2020-0704
32. Siddiqui BK, Batool S, mahmood ul Hassan Q, Malik MY. Repercussions of homogeneous and heterogeneous reactions of 3D flow of Cu-water and AL2O3-water nanofluid and entropy generation estimation along stretching cylinder. Ain Shams Eng J (2022) 13(1):101493. doi:10.1016/j.asej.2021.05.007
33. Salahuddin T, Imtiaz I, Khan M. Analysis of entropy generation in AA7072-methanol and AA7072+ AA7075-methanol flow near a parabolic surface. Appl Maths Comput (2022) 413:126616. doi:10.1016/j.amc.2021.126616
35. Ellahi R, Riaz A, Abbasbandy S, Hayat T, Vafai K. A study on the mixed convection boundary layer flow and heat transfer over a vertical slender cylinder. Therm Sci (2014) 18(4):1247–58. doi:10.2298/tsci110923097e
36. Sandeep N, Kumar BR, Kumar MJ. A comparative study of convective heat and mass transfer in non-Newtonian nanofluid flow past a permeable stretching sheet. J Mol Liquids (2015) 212:585–91. doi:10.1016/j.molliq.2015.10.010
37. Dawar A, Shah Z, Tassaddiq A, Islam S, Kumam P. Joule heating in magnetohydrodynamic micropolar boundary layer flow past a stretching sheet with chemical reaction and microstructural slip. Case Stud Therm Eng (2021) 25:100870. doi:10.1016/j.csite.2021.100870
38. Ramadan KM, Qisieh O, Tlili I. Thermal creep effects on fluid flow and heat transfer in a microchannel gas cooling. Proc Inst Mech Eng C: J Mech Eng Sci (2022) 236(9):5033–47. doi:10.1177/09544062211057039
39. Zaydan M, Hamad NH, Wakif A, Dawar A, Sehaqui R. Generalized differential quadrature analysis of electro‐magneto‐hydrodynamic dissipative flows over a heated riga plate in the presence of a space‐dependent heat source: The case for strong suction effect. Heat Trans (2022) 51(2):2063–78. doi:10.1002/htj.22388
40. Sohail M, Nazir U, EssamEl-Zahar R, Alrabaiah H, Kumam P, Mousa AAA, et al. A study of triple-mass diffusion species and energy transfer in Carreau–Yasuda material influenced by activation energy and heat source. Sci Rep (2022) 12(1):10219–7. doi:10.1038/s41598-022-13890-y
41. Nazir U, Sohail M, Kumam P, Sitthithakerngkiet K, Mousa AAA, Khan MJ, et al. A dynamic assessment of various non-Newtonian models for ternary hybrid nanomaterial involving partially ionized mechanism. Sci Rep (2022) 12(1):10306–15. doi:10.1038/s41598-022-14312-9
42. Sohail M, El-Zahar ER, Mousa AAA, Nazir U, Althobaiti S, Althobaiti A, et al. Finite element analysis for ternary hybrid nanoparticles on thermal enhancement in pseudo-plastic liquid through porous stretching sheet. Sci Rep (2022) 12(1):9219–3. doi:10.1038/s41598-022-12857-3
43. Hou E, Wang F, Nazir U, Sohail M, Jabbar N, Thounthong P. Dynamics of tri-hybrid nanoparticles in the rheology of pseudo-plastic liquid with dufour and soret effects. Micromachines (2022) 13(2):201. doi:10.3390/mi13020201
44. Tlili I, Sajadi SM, Baleanu D, Ghaemi F. Flat sheet direct contact membrane distillation study to decrease the energy demand for solar desalination purposes. Sustainable Energ Tech Assessments (2022) 52:102100. doi:10.1016/j.seta.2022.102100
45. Zhang J, Sajadi SM, Chen Y, Tlili I, Fagiry MA. Effects of Al2O3 and TiO2 nanoparticles in order to reduce the energy demand in the conventional buildings by integrating the solar collectors and phase change materials. Sustain Energ Tech Assessments (2022) 52:102114. doi:10.1016/j.seta.2022.102114
46. Tlili I, Alharbi T. Investigation into the effect of changing the size of the air quality and stream to the trombe wall for two different arrangements of rectangular blocks of phase change material in this wall. J Building Eng (2022) 52:104328. doi:10.1016/j.jobe.2022.104328
47. Qi X, Sidi MO, Tlili I, Ibrahim TK, Elkotb MA, El-Shorbagy MA, et al. Optimization and sensitivity analysis of extended surfaces during melting and freezing of phase changing materials in cylindrical Lithium-ion battery cooling. J Energ Storage (2022) 51:104545. doi:10.1016/j.est.2022.104545
48. Alzahrani J, Vaidya H, Prasad KV, Rajashekhar C, Mahendra DL, Tlili I. Micro-polar fluid flow over a unique form of vertical stretching sheet: Special emphasis to temperature-dependent properties. Case Stud Therm Eng (2022) 34:102037. doi:10.1016/j.csite.2022.102037
49. Fang T, Yao S. Viscous swirling flow over a stretching cylinder. Chin Phys Lett (2011) 28(11):114702. doi:10.1088/0256-307x/28/11/114702
50. Ahmed A, Khan M, Ahmed J. Mixed convective flow of Maxwell nanofluid induced by vertically rotating cylinder. Appl Nanosci (2020) 10(12):5179–90. doi:10.1007/s13204-020-01320-2
51. Nayak MK, Mabood F, Dogonchi AS, Ramadan KM, Tlili I, Khan WA. Waves in random and complex media (2022). p. 1–22.Entropy optimized assisting and opposing non-linear radiative flow of hybrid nanofluid
52. Qin L, Ahmad S, Khan MN, Ahammad NA, Gamaoun F, Galal AM. Thermal and solutal transport analysis of Blasius–Rayleigh–Stokes flow of hybrid nanofluid with convective boundary conditions. Waves in Random and Complex Media (2022) 1–19. doi:10.1080/17455030.2022.2072018
Keywords: Ag-TiO2/H2O hybrid nanofluid, Cattaneo-Christov double diffusion theory, convective boundary conditions, joule heating, vertical rotating cylinder, entropy generation
Citation: Ahmad S, Ahammad NA, Khan MN, Algehyne EA, Tag-Eldin E, Gepreel KA, Guedri K and Galal AM (2022) Thermal and solutal energy transport analysis in entropy generation of hybrid nanofluid flow over a vertically rotating cylinder. Front. Phys. 10:988407. doi: 10.3389/fphy.2022.988407
Received: 07 July 2022; Accepted: 25 July 2022;
Published: 26 September 2022.
Edited by:
Arshad Riaz, University of Education Lahore, PakistanReviewed by:
Muhammad Sohail, Khwaja Fareed University of Engineering and Information Technology (KFUEIT), PakistanIskander Tlili, National Engineering School of Monastir, Tunisia
Copyright © 2022 Ahmad, Ahammad, Khan, Algehyne, Tag-Eldin, Gepreel, Guedri and Galal. This is an open-access article distributed under the terms of the Creative Commons Attribution License (CC BY). The use, distribution or reproduction in other forums is permitted, provided the original author(s) and the copyright owner(s) are credited and that the original publication in this journal is cited, in accordance with accepted academic practice. No use, distribution or reproduction is permitted which does not comply with these terms.
*Correspondence: Shafiq Ahmad, ashafiq@math.qau.edu.pk