Comparing Biorefinery Processes at the Early Design Stage Using Large Block Analysis
- 1Product and Process Design Laboratory, Department of Chemical Engineering, Polytechnique Montréal, Montréal, QC, Canada
- 2Myers Consulting LLC, Sabula, IA, United States
The transformation of pulp and paper mills through the integration of biorefineries is increasingly considered essential to the future of many existing sites. However, evaluating the risk and return of different biorefinery process alternatives at the early design stage is challenging. There are many strategies and technologies that must be considered, each of which is typically accompanied by its unique risks, including high levels of uncertainty in capital and operating cost estimates often obtained from technology providers. The novel methodology presented in this study, called Large Block Analysis (LBA), comprises a systematic approach for addressing these important challenges at the early design stage. LBA is used to obtain relative cost estimates for six process/product combinations incorporating different Technology Readiness Levels (TRLs), for adding value to a hemicellulose stream extracted from hardwood chips. In this case study, it was found that the fixed capital costs obtained using the LBA method differed from the original costs by between 121 and −19%, and operating cost estimates differed by between 117 and −17% from the original. The results show that the most economically-viable options for the hemicellulose stream having reasonable technology risk included the production of (1) animal feed additives, (2) xylitol using a variant of the classical chemical process, and (3) furfural.
Introduction
Integrating a biorefinery to an existing pulp and paper plant is an increasingly attractive strategy being considered by forest product companies to diversify their products and markets, as the sector struggles to adjust to decreasing demand in certain segments including printing and writing papers. If designed and implemented well, biorefinery integration can change the competitiveness of sites for the long-term. Building from existing assets, biorefinery feed streams can be made available including for example hemicellulose and/or lignin extracted from the wood feedstock, which can in turn be used to produce biofuels, biochemicals, and/or biomaterials.
At the early stage of design decision-making related to biorefinery strategy development, where the goal is to eliminate less-preferred process options based on their relative risk and economics, it is challenging to compare new technologies. This is cause by many reasons, including the difficulty to obtain cost estimates on a comparable basis considering scope of cost estimate, estimate completeness, implicit, and explicit assumption, as well as the level of technology readiness and resulting uncertainty due to, but not limited to, optimism bias, reference data quality, technology risks, experience level of the estimator, cost estimation technique (Hollmann, 2014; Christensen et al., 2019).
When evaluating and comparing the economic performance of different biorefinery process options at the early design stage capital costs, operating costs and revenues must be estimated. Critical information related to costs is typically provided by technology developers. Depending especially on the Technology Readiness Level (TRL) of the constituent technologies comprising the biorefinery process, as well as other factors, the uncertainty of information can be highly uncertain such as integrated process performance and scale-up, optimism bias, and the degree to which engineering has been detailed. To assemble costs for well-proven technologies, various established cost estimation methods can be used (Peters et al., 2003; ASTM International, 2019). And in some cases these have been adapted for early-stage cost estimating (Ereev and Patel, 2012; Claypool and Raman, 2013; Benali, 2015; Cortes-Peña et al., 2020; Tsagkari et al., 2020).
Systematic methods for cost estimation in the early design stages for biorefinery projects are critical, to obtain relative costs and make comparisons for process options triage. The Large Block Analysis (LBA) method has been defined by Trottier (2021), which aims to reduce uncertainty and develop comparable costs suitable for triage decision-making. The LBA method compares distinct process alternatives by identifying the most reliable cost estimate amongst the process options, and uses this to improve the initial capital and/or operating cost estimate for all technologies and process options. The LBA method was demonstrated for the case of two pulp and paper engineering projects, in which technologies well-proven at commercial scale were considered. Despite the high level of technology development and the associated reliable cost estimates, the Large Block Analysis method resulted in modified costs as good as or superior to conventional estimation techniques at the Pre-Feasibility design stage compared to the Definition Engineering design stage (Trottier, 2021). The application of LBA to biorefinery projects with technology at lower and varying TRLs is expected to be even more effective, as the level of uncertainty of emerging and innovative technologies is much higher.
Dissolving pulp mills are particularly promising for biorefinery integration since they employ a pre-hydrolysis step to extract most of hemicelluloses prior to cooking. This step is used for the dissolving pulp process because of the need for a high cellulose content in the final pulp (>90%) (Hemanathan and Lew, 2017). An emerging pre-hydrolysis technology for removing hemicelluloses is hot water extraction (HWE). HWE has the advantages of limiting undesirable conversions, and minimizing environmental impact since it does not employ pulping chemicals or catalysts, and it enhances cellulose accessibility for the subsequent pulping process (Cheng and Wang, 2013; Wu, 2016; Hemanathan and Lew, 2017). The resulting pre-hydrolysis liquor (PHL) is composed of hexose and pentose sugars in oligomeric and monomeric forms, acetic acid, lignin, furfural, and ash (Li et al., 2010; Saeed et al., 2012). In the classical dissolving pulp process, the PHL is typically burned with the black liquor in the recovery boiler, or sent to the wastewater treatment plant. However, the water-extracted PHL stream can potentially be recovered and used as a raw material for several biorefinery processes to produce added-value products (Wu, 2016). This is due to the high sugar content of the PHL and the absence of residual pulping chemicals when water is the extraction medium. An example of the use of HWE is by American Process Inc. for extracting hemicelluloses from hardwoods (Retsina and Pylkkanen, 2014), which has been commercialized and implemented by Cascades in their mill located in Cabano Québec (Lane, 2015).
The use of PHL as a raw material and its various possibilities for valorization are well-described in the literature (Tao and Aden, 2009; Menon and Rao, 2012; Cheng and Wang, 2013; E4tech et al., 2015; Cavani et al., 2016). Several product-process options exist and their evaluation is notably complicated by different levels of technological maturity as well as variable levels of market risk depending on the targeted products.
In this article the LBA method will be applied considering the PHL from hot water extracted hardwood, and process options for its valorization.
Process/Product Options Considered for the Valorization of Water-Extracted Hemicellulose Stream
Xylitol, a sweeter that can be produced from a hardwood hemicellulose stream, is a promising alternative to regular sugar for various reasons including especially lower caloric intake than sucrose (because of how it is metabolized) with comparable sweetness, and also, beneficial oral health effects by decreasing dental care requirements, and potential to be certified organic (zuChem, 2013). It has applications in chewing gum, confectionery, food, personal care, pharmaceuticals, and nutraceuticals (Wasilenkoff, 2018). The market is growing at a compound annual growth rate (CAGR) of over 7%, driven by health-related concerns such as childhood obesity and Type II diabetes (Wasilenkoff, 2018; Motor Intelligence, 2019). The market price for xylitol was between 3,500 and 4,500 USD/t in 2018 (Wasilenkoff, 2018). The market is quite fragmented. While significant production is attributable to various small producers, Danisco and Futaste Pharmaceutical have large market share. Geographically, the largest market is in North America, followed by Europe and Russia, and finally a small market demand is growing in South America, Africa, and Asia (Motor Intelligence, 2019).
Xylitol can be produced from PHL chemically (this route has been commercialized) or via fermentation. A post-hydrolysis step is needed in both pathways to make monomeric sugars in the PHL stream available, which contains oligomers after the HWE. The pre-hydrolysis can be done by acid or enzymatic hydrolysis. The enzymatic hydrolysis has the advantage of employing milder operating conditions, and fewer inhibitors are likely to be produced (Ur-Rehman et al., 2015). Seventy to ninety percent of the xylan hemicellulose is converted to xylose using this technique (Gerbrandt, 2014).
For the classic chemical process, a purification step is required to obtain a pure xylose (>99%). This can be achieved by multiple techniques including filtration, simulated moving bed (SMB) chromatography, activated carbon columns, ion-exchange columns, and xylose crystallization. The xylose solution is hydrogenated to xylitol at high pressure (4–7 MPa) and moderate temperatures (80–140°C) with hydrogen gas and a metal catalysis e.g., Raney-Nickel (Rafiqul and Sakinah, 2013; Gerbrandt, 2014; Delgado Arcaño et al., 2018). The xylitol solution is crystallized and the mother liquor containing the remaining contaminants is separated from the xylitol crystals, which are dried before packaging (Hou-Rui, 2012; Rafiqul and Sakinah, 2013).
An interesting variant of the classic chemical pathway involves hydrogenizing a solution of mixed sugars instead of the pure xylose solution. A purification step is necessary to remove contaminants such as lignin, remaining oligomers, acetic acid, and non-organic components. All the sugars are converted to their respective alditols (90–99% xylose to xylitol conversion) by hydrogenation at high pressure (4–14 MPa) and temperature (120–140°C) with hydrogen gas and a metal catalyst (Bailey, 2017; Allen et al., 2019). After the conversion, purification by SMB chromatography is used to separate the xylitol from the other alditols and improve the recovery (Rafiqul and Sakinah, 2013; Bailey, 2017; Wasilenkoff, 2018; Allen et al., 2019).
Bioprocesses involving enzymatic fermentation can be used to produce xylitol, although the technology is to our knowledge only developed at the pilot scale (Rafiqul and Sakinah, 2013; zuChem, 2013). The bioprocess does not require a purified xylose solution because the sugar conversion to xylitol is more selective (Hou-Rui, 2012). After the PHL post-hydrolysis, the hydrolyzate is detoxified to remove inhibitors such as phenolic compounds, furfural, HMF, organic acids, and non-organic components (Mpabanga et al., 2012). The mixed sugar solution is then fermented by yeast or directly converted by enzymes to xylitol. Fermentation takes place at 28–30°C for 48–96 h, and about 81% of the xylose is converted to xylitol (Rafiqul and Sakinah, 2013; Gerbrandt, 2014). A purification step is needed to recover the xylitol from the solution that includes unconverted sugars (arabinose and galactose), this is done by SMB chromatography (Hou-Rui, 2012; Rafiqul and Sakinah, 2013).
Furfural is another attractive valorization option for the water-extracted hemicellulose stream. Furfural is used directly as a solvent as well as in some agrochemical applications such as insecticide and fungicide. It is also an important renewable chemical building block; furfural can be converted to added-value chemicals like furfuryl alcohol and tetrahydrofurfuryl alcohol, and chemical intermediates with many industrial applications (E4tech et al., 2015). The majority of the world's furfural production (60–80%) is converted to furfuryl alcohol (Iroegbu and Hlangothi, 2019; Rosales-Calderon and Arantes, 2019). Most of the global production (80–90%) of furfuryl alcohol is used to make foundry resins (furan) (Krishna et al., 2018; Rosales-Calderon and Arantes, 2019). The market price for furfural is between 800 and 1,600 USD/t while the market price of furfuryl alcohol is ~1,300 USD/t (E4tech et al., 2015; Krishna et al., 2018; Rosales-Calderon and Arantes, 2019; Mazar et al., 2020). Fossil-based product alternatives are limiting the growth of the furfural and furfuryl alcohol markets. More specifically, phenolic resins from crude oil are cheaper than using furan resins produced with furfuryl alcohol (Krishna et al., 2018; Rosales-Calderon and Arantes, 2019).
A CAGR of 4.5% between 2019 and 2024 is expected for furfural, mainly driven by the Asia-Pacific region, while furfural production and consumption is largest in China (Markets and Markets, 2019). No significant near-term market growth is expected in the United States for furfural (Markets and Markets, 2019; Rosales-Calderon and Arantes, 2019). A potential opportunity that could drive demand would be the production of diesel and aviation fuel blends, or the pharmaceutical grade of furfural (Gilani, 2014; Rosales-Calderon and Arantes, 2019).
Furfural from the HWE stream is produced in one or two steps to hydrolyze the pentosans and convert the pentoses into furfural by dehydration (Brownlee and Miner, 1948; Dashtban et al., 2012). The classical industrial processes have not been improved in recent years and have various disadvantages including long residence times, significant steam requirements, and a low yield (~50%) due to many side reactions (Cai et al., 2014; Rosales-Calderon and Arantes, 2019). Furfural production plants in the United States and Europe have almost all ceased operations, and 90% of production is now in China, South Africa, and the Dominican Republic, with the former alone responsible for 70% of the world production (Cai et al., 2014; Rosales-Calderon and Arantes, 2019). In order to improve the efficiency of the process, Mazar et al. (2020) proposed adding acid to the reactor only when the optimal temperature is reached and/or, depending on the configuration, to recover the furfural from the liquid phase as soon as it is formed and vaporizing it to limit the formation of other components. Considering industrial feasibility and integration with paper mills, the preferred configuration considered in this study to minimize capital cost and energy demand starts with a concentration step followed by an acidification step to precipitate the lignin to avoid plugging problems and during the conversion, furfural is directly condensed then recovered and purified by distillation. A cumulative yield of 56% is obtained at 170°C with this configuration (Mazar et al., 2020).
The hemicelluloses contained in PHL can also be concentrated and sold as animal feed additives in the same way as beet sugar and cane sugar molasses. Feed additives are a commodity and highly-volatile global market. The price for hemicellulose as animal feed is estimated to be between 80 and 117 USD/t, but this depends on the sugar concentration of the hemicellulose solution and the outcome of price negotiations between producers and off-takers (Gilani, 2014).
PHL can be concentrated with a multi-effect evaporator to obtain a solid content of 55% and as high as 70%, which allows it to be used in the formulation of animal feed since this sugar concentration is sufficient to meet caloric needs (Gilani, 2014). The concentration of carbohydrates should be between 55 and 84% to qualify as feed additive (Code of Federal Regulations, 2020).
The production of biogas from PHL with anaerobic treatment is possible, where the produced biogas would be used by the pulp and paper mill as a substitute for natural gas. First, the PHL is conditioned to meet the target pH and nutrients concentration for anaerobic treatment. Then, in an anaerobic reactor the PHL is degraded and converted into biogas by anaerobic bacteria and microorganisms. The biogas produced is sent to a scrubber to remove hydrogen sulfide, and then used in the mill steam boilers (Gavrilescu, 2002; Gilani, 2014). The methane content of biogas is typically between 50 and 75%, carbon dioxide between 25–45% and other elements being <2% including nitrogen, hydrogen sulfide, hydrogen, oxygen, and ammonia (Pigeon et al., 2012).
Materials and Methods
In order to compare different biorefinery options for the HWE stream processing, cost estimates for six process options were developed based on a wide range of information sources. Then the LBA method was applied to render the estimates to be on a comparative basis, as well as to identify their critical uncertainties. Figure 1 summarizes the Large Block Analysis steps.
First, the project objectives and the design basis of the case study were defined. The product-process combinations were determined based on their potential for PHL recovery from hardwoods and the interests of the industrial partner.
Reference and cost data were gathered from several sources, including for example supplier technical and commercial proposals, discussion with experts, literature, and other public information. The different process pathways were analyzed at the block flow diagram level, and processes were divided into functional areas so that they could be compared on a relative basis. For each functional area, the major equipment items were defined and order-of-magnitude mass and energy balances completed. The cost estimates for each process option were analyzed by comparing the scope of supply to identify missing cost(s) and compare the cost basis for the different estimates. The initial cost estimates were standardized so that unit costs were on the same basis, and adapted to the design basis e.g., capacity and year indexation. In some cases, it was necessary to add missing cost(s). This is necessary because the cost structure used by each supplier is specific to internal practices, appreciation of the design process, and differs from one supplier to another. Because of this, certain costs such as those for auxiliary equipment (pumps, tanks, etc.) or for certain civil works or electrical requirements, are not always included in the estimates. A cost structure considering the different functional areas, and assumptions were made so that the cost estimates were systematically reflected in the cost structure.
Next the Large Block Analysis (LBA) was conducted. Among the different options, the most thorough cost estimate was selected as a “cost estimate base case.” The “best” cost estimate may be determined based on, but not limited to, the following factors:
- The scope of the estimate provided by the supplier;
- The level of engineering accuracy of the estimate provided by the vendor;
- The supplier's industrial implementation experience at commercial scale; and
- The completeness of the estimate provided by the supplier.
The cost estimate for this base case was used to independently estimate the other process option capital and operating costs. The main differences between the initial cost estimates and LBA cost estimates were identified and examined more closely to arrive at an appropriate representation.
In conjunction with the LBA cost analysis, much was learned about each process and a risk assessment could be conducted to identify key market and technology risks. These cost and risk assessments were then used to compare the different pathways and identify the most preferred option(s) that should be retained for further analysis.
Results and Discussion
Design Basis
The dissolving pulp mill in the case study sought to valorize the PHL obtained from a hot water extraction step, and consider producing xylitol using an innovative chemical process. Aware that there are several other products and technologies that could be implemented having different risks and returns, they wished to compare the production of xylitol by the innovative chemical process with other possibilities.
The mill kraft dissolving pulp process consumes 790 bone-dry metric tons per day (bdt/d) of hardwood chips. A pre-hydrolysis step done with hot water extraction (HWE) had recently been implemented at the mill to extract hemicelluloses, and burned in the boiler along with the black liquor. If the HWE stream was sent to a biorefinery process, 95 bdt/d of pre-hydrolysis liquor or PHL (1,900 m3/h at 5% DS) would be available to be converted into added-value products. The liquor was composed of 56.5% oligomers (43% xylan), 12.7% monomers, 16.6% lignin, 11.1% acetic acid, 0.1% furfural and HMF, and 3% ash.
The fixed capital investment (FCI) was estimated for transforming the PHL into xylitol using the innovative chemical process, including the equipment costs to purify, convert, and recover the product, as well as the installation and balance of plant requirements, indirect costs, and a contingency fee.
The total production costs (TPC) were estimated including raw materials, utilities, labor including supervision, maintenance, supplies and laboratory charge, fixed charges (property taxes and insurance), and general expenses (application and sales). Certain cost elements were excluded in this study since they were deemed not relevant for early design stage triage, including for example administration, plant overhead, rent, and research and development. The raw materials cost and utilities cost were based on preliminary mass and energy balances (see additional information for the unit prices assumed). The labor cost was estimated based on the number of operators required for each process considering an hourly rate (including indirect costs) of 65 $/h for operators, and supervision was considered to represent 15% of the total labor cost.
Further assumptions for the cost estimates include the following:
• The hot water extraction (HWE) step is already implemented and so the capital and operating costs for this process have not been considered.
• No cost was assumed for the PHL stream, however the cost to concentrate the PHL is included.
• The capacity of the existing mill utilities including waste treatment and steam was deemed sufficient for the biorefinery needs.
• The process will operate 345 operating days per year.
• Costs related to the hydrogenation catalyst, chromatography resin, and yeast cells have been neglected.
• Patent and royalty costs were not considered.
• Accelerated depreciation, 6% discount rate (weighted average cost of capital or WACC), and a 26.6% tax rate were considered.
Six product-process combinations were compared in the study:
1. Xylitol production via the classical chemical process with acetic acid co-product.
2. Xylitol production via the fermentation process with acetic acid co-product.
3. Xylitol production via a variant of the chemical process (the innovative chemical process considered by the mill) with acetic acid co-product.
4. Furfural with acetic acid co-product.
5. Additive for animal feed with acetic acid co-product.
6. Biogas production.
Data Gathering and Process Analysis
Cost data used for the initial estimates are based on many information sources including from the literature (Gerbrandt, 2014; Gilani, 2014; Mazar et al., 2020; NREL report), other public sources (Wasilenkoff, 2018), as well as partner information and vendor quotations.
Figure 2 shows a simplified process diagram of the different process options considered. The similarities between the processes are highlighted by the boxes in bold. In terms of major equipment items, an initial concentration step is similar for most processes, and multiple similarities are noticeable between the xylitol processes. However, the furfural and biogas processes have relatively less in common with the xylitol processes in terms of major equipment.
A first concentration step by multiple effect falling film evaporator is necessary for the first four processes. For the production of xylitol and furfural, this step is done mainly to reduce the stream volume to be treated subsequently, thus reducing the investment cost. As for the production of animal feed additive, the PHL must be concentrated in order to meet the market expectation for calorific requirement, and to reduce transportation costs.
A conditioning step is considered for all xylitol processes involving enzymatic hydrolysis, filtration and softening, and an SMB chromatography unit. Filtration is required to avoid suspended solids accumulation in the resin beds and prevent plugging of the SMB columns. Solid contaminants can be removed by a basket centrifuge which removes most of the solids, and by a membrane filtration unit to remove the fine residual solids. An ion exchange softening unit removes the calcium and magnesium ions that hinder process performance. In order to obtain a better separation, the liquor must be concentrated before being purified using SMB chromatography. The fermentation process does not require further purification before conversion, as the bioconversion is more selective and the tolerance of microorganisms to inhibitors allows the use of a less purified solution. However, depending on the level of purification needed by the two chemical processes, further purification steps are necessary. For the classical xylitol route, a second concentrator and SMB chromatography system are necessary to further separate the xylose from the oligomers and other monomers. The next step, which is necessary in both the conventional and the variant chemical routes, includes ion exchange columns, activated carbon columns for color removal, and concentration. To obtain a pure xylose solution, the classical process requires a final conditioning step including xylose crystallization and separation of the other monomers still present. For all xylitol processes, the reaction is carried out in one or more reactors, however, the operating conditions differ (see additional information for more detail).
Once the xylitol is produced, the variant chemical process and the fermentation process require a purification step to separate the xylitol from other polyols or unconverted sugars. Finally, all xylitol processes involve a xylitol crystallization and a separation step.
Structure Definition and Scope of Estimate Comparison
In order to understand the basis of the cost estimates, a comparison of the scope of supply was reviewed for each of the estimates. Then, the most detailed cost estimate was used as the starting point for structuring the costs, and additional relevant cost categories were added. The first column of Table 1 shows the cost structure used for the study while the other columns show how each of the direct costs of the estimates were made on the basis of the initial cost estimate. In the commercial proposals, some costs were included (explicitly included) while others were defined as being outside the scope of supply (explicitly not included). In some cases, it was ambiguous whether certain costs were included in the estimate (unspecified). This is particularly the case for less precise estimates that do not have a well-defined scope. These ambiguities make it difficult to compare estimates, and the technology provider was contacted to clarify whether these costs were included or not.
Adjustments to the Base Case Cost Estimate
Once the cost basis has been defined for each option, the initial estimates were adjusted to the case study specifics.
Some adaptations were necessary to make the estimates obtained consistent with the design basis of the case study, for example:
• The addition of a concentration step after the HWE for the three xylitol processes was necessary, as the resulting PHL is more dilute than the one that was considered in the technology developer estimates. The cost of an evaporator was estimated and added (2.9 M$).
• The initial estimate for the classical chemical xylitol process was missing certain process steps:
• The cost of the conversion step was added based on the installed cost of the hydrogenation step of a process having the same capacity (7.2 M$), provided by one of our partners.
• The xylitol crystallization equipment cost (1.4 M$) was added to the estimate based on data from literature.
• The initial estimate for the animal feed additive production required the addition of an evaporator (the equipment had been considered relocated in a previous study that the estimate was based on). The cost of an evaporator (4.3 M$) was added.
• A desulphurization step was added to the estimate received for the biogas process, to utilize the biogas produced internally by the mill. The cost of a venturi scrubber and blower (0.1 $) was added.
• Adjustment for the case study capacity (using scale factors between 0.5 and 0.7).
• Certain additional costs had to be added for missing equipment items:
• A factor of 15% of equipment cost (2.5 M$) was added to the xylitol variant chemical process to account for foundation, site work and waste treatment modification.
• 6, 15, and 10% of FCI were added to the biogas estimate in consideration of service facilities (0.9 M$), missing indirect costs (2.3 M$), and contingency (1.6 M$), respectively.
Cost Structure Refining
The cost components for each process option were placed into the same cost structure for comparison purposes, where the cost structure considered the highest level of detail possible based on the data received from different sources. Then depending on the level of detail for different process options, the detailed cost data are assembled into common aggregated areas. Table 2 shows the initial cost estimates aggregated into their functional areas i.e., conditioning, conversion, and product recovery.
Base Case Selection
A “most reliable cost” base case estimate was selected among the six considered, and used to estimate all other process options. Table 3 presents a qualitative comparison of the different cost estimates according to assessment criteria.
In summary, the xylitol classic chemical process estimate was considered the most reliable cost for the following reasons:
• It is the most accurate and complete estimate.
• Although the initial estimate of this process included several information sources, most of the costs are based on a single feasibility level estimate (±20%).
• It is one of the most mature processes considered, and it is the one for which the most information is available.
Cost Differences Identification
To estimate the other process options from the base case cost estimate, the differences in costs were identified and a basis for adjustment was determined. For the purposes of early stage design cost comparisons, some costs could be considered to be the same as the base case, while others needed adjustment according to flow rate, operating conditions, or equipment differences, and some costs were added when the process or an area was not comparable to the base case. While some elements are considered not applicable (NA) when they are not required by the process compared to the base case. For the hemicellulose conditioning as an example, Table 4 summarizes the cost differences considered, and Table 5 shows the LBA adjustment made.
Tables 4, 5 address adjustments made relative to major equipment items. Other costs including installation and support disciplines and indirect costs were evaluated as a percentage of the purchased equipment cost, the direct costs, or the FCI. The percentage used in the base case (xylitol classic chemical) was adjusted based on process analytics and Good Engineering Judgement. Table 6 overviews the adjustment basis considered for each cost element.
To illustrate this approach in the case of the fermentation process, the following adjustments were considered:
• The installation percentage related to the conversion was increased compared to the most reliable cost estimate, since the reactors are significantly larger.
• The cost of services was reduced for the fermentation process since it did not use hydrogen gas.
• The start-up and commissioning percentage was reduced since there is lower process complexity (number of major equipment items).
Table 7 summarizes the specific percentages established for each process option to estimate the installation, balance of plant, and indirect costs considering the most reliable base case.
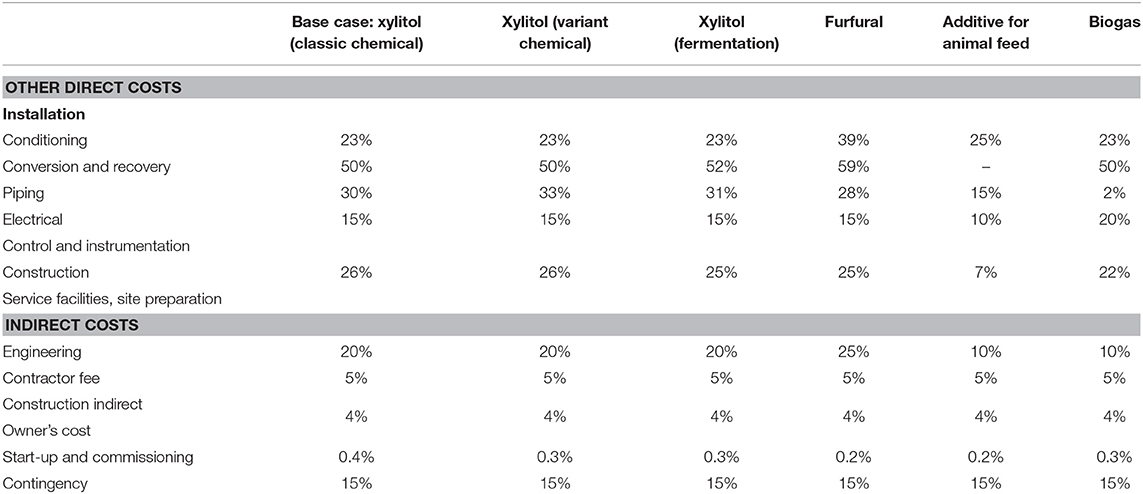
Table 7. Major equipment installation and indirect costs: Large Block Analysis adjustments using basis expressed in Table 6.
Large Block Analysis Cost Estimates
On the basis of the above systematic methodology, it is possible to obtain a relative estimate (Table 8) based on the most reliable base case for all other process options.
Capital Cost Estimates Comparison With Large Block Analysis Estimates
The initial estimates from engineers and technology developers were compared to those obtained using LBA, and the differences quantified for discussion with those who completed the initial estimates. This step is critical, to understand if the justification for the differences between the initial and relative estimates are appropriate, and make final adjustments accordingly. Table 9 compares the initial estimate for the xylitol fermentation process with the LBA estimate.
In this example, a significant difference between the xylitol fermentation process estimates is noticeable for the cost of equipment related to the conditioning of the extracted hemicelluloses. The initial estimate was based on academic work using the ICARUS cost estimation module within Aspen. On the other hand, the LBA-based relative estimate is based on more precise data derived largely from demonstration scale operation results extrapolated to the industrial scale. Following a discussion with experts and the developer of the initial cost estimate, it was accepted that the relative cost obtained with LBA was more realistic. Also significantly, the reactor material and fabrication costs were expected to be higher than for the classic chemical process. Other major differences are related to installation and support discipline and indirect cost. As per common practice in early stage design work, the contingency has been standardized between the different processes compared.
Based on discussions with providers of the LBA-based estimates, few changes were made to the information in Table 8. It was found that the classical chemical xylitol process required the greatest adjustment. Amongst other things, this could be attributed to a lack of industrial scale experience and a high level of optimism implicit in the initial estimates. The largest difference between the estimates for the animal feed additive comes from the estimate of indirect costs. This could be explained, for example, by the use of a general factor that had underestimated these costs. As a final example, the difference between the initial estimate of the biogas process (mature technology) and the LBA-based estimate comes from changes in the assumptions of certain costs resulted in a relatively smaller adjustment.
Operating Cost Estimates
In a similar manner, the LBA method was applied to the operating cost estimates. Operating costs depend to a greater degree on certain assumptions including those related to process integration with the pulping process. The approach is otherwise quite analogous to that of capital cost estimation, and leads to similar adjustments. The LBA results are presented in Table 10.
For the xylitol classic chemical, xylitol fermentation process, and the xylitol variant chemical, a significant change was related to labor cost. The initial cost assumed 39 $/h in the lowest estimate which was not representative of the case study cost of labor including wages and payroll taxes (for example employer contributions to government plans and vacation pay). The biggest difference between the initial estimate and the LBA-based estimate for the furfural process was also due to labor cost, which was initially estimated as a percentage of the production cost, whereas it was systematically estimated by evaluating the number of operators/unit operations in the LBA-based estimate.
Market and Technology Risk Assessment
Based on literature, purchased studies, as well as discussion with suppliers and other experts, market and technology risks were identified as summarized in Table 11.
We note that many market and (especially) technology risks became evident as a consequence of conducting Large Block Analysis through exchanges with the technology developers and experts consulted to resolve cost differences. Certainly during early-stage design, a classification into three classes (high/medium/low) or at most five classes is adequate for triage decision-making.
While a systematic assessment of risks was conducted for the six product-process options, we focus on the findings of xylitol in this discussion as an example.
Xylitol: Market Risks
The market risk for xylitol in the first three process options was assessed as “medium” relative to all product-process options.
The pharmaceutical segment for xylitol is currently small, while the food market is growing quickly in North America. It is expected that there may be a drop in prices for xylitol, currently considered a specialty sweetener. However it is for now a supply-driven market, and eventually the price could drop if it becomes a commodity with increased supply from extracted hemicellulose as raw material. Swings in Chinese production could also significantly impact market price and this was considered a significant concern, although it was felt that a consistent quality and reliable source of xylitol would address this concern to a large extent. For certain xylitol applications, a long accreditation time could delay access to the food or (especially) the pharmaceutical markets. For example, accreditation for pharmaceutical grade xylitol can take as much as 5 years, and any changes to the production process requires re-validation.
Xylitol: Technology Risks
At its current level of development, the production of xylitol by enzymatic hydrolysis is uncertain in terms of the amount of enzyme required, as well as the enzyme cost and conversion rate. For the classical chemical process, xylose separation, and purification are more complex, requiring an additional crystallization step and the associated complexity/risk. Depending on the yield, an additional step may be necessary to recover some of the xylose lost during the centrifugation of the xylose crystals. For the variant of the chemical process and the fermentation process, an additional step of purification is necessary to separate for the first one the xylitol from the other alditols. Discussions with experts highlighted the risk associated with obtaining a low conversion yield for the chemical variant process and, the yield predicted by the technology developer for hydrogenation of a sugar solution may be optimistic compared to that obtained industrially for a pure xylose solution. As for the fermentation process, the conversion of xylose to xylitol by fermentation implies a certain risk due to the uncertainty of the performance of the microorganisms, which depends on their tolerance to inhibitors. This step is also challenging, and implies a complex management between batches including a sanitization step imperative to avoid the growth of undesirable bacteria and considerable downtime. This is especially a concern if the process is not designed to avoid areas where material can accumulate due to the presence of porosity, edges, or poor design of pipes and reactors.
Profitability Assessment and Implication of Results
The six process options were evaluated using the LBA method and risk assessment approach described. Figure 3 summarizes the results obtained for the internal rate of return (IRR) and the risk associated with each option. The risk shown is the greater of market risk or technology risk for each of the options presented in Table 11. Figure 4 summarizes the net present value (NPV).
According to these results, the production of xylitol by the classic chemical process, by the fermentation process and as well as the production of biogas to replace part of the natural gas consumed by the plant are not interesting alternatives considering the (nominal) minimum acceptable return. The production of xylitol by variant of the chemical process and the production of furfural offer interesting returns and should continue to be examined, however strategies (and costs) to mitigate their risks should be elaborated. For example, for the xylitol process, a phased implementation could help to reduce the technological risk. As for furfural, the market risk can be reduced should long-term contracts with partners be possible.
The feed additive process option offers an interesting return at lower risk, however this low capital cost option does not offer a significantly increased cash flow as shown by the low NPV in Figure 4. From a net present value perspective, xylitol produced by the variant of the chemical process offers the greatest gain due to a high yield and the selling price of the xylitol, but it also implies a higher capital investment.
In light of the results obtained, the production of xylitol through variant of the chemical process, the production of furfural as well as the production of animal additive might be retained for further analysis and engineering.
Conclusions
Choosing between process and product options at the early design stage is difficult, especially when technologies and their cost data are accompanied by high levels of uncertainty and risk. The Large Block Analysis (LBA) method has been identified as having the potential to facilitate such comparisons (Trottier, 2021). In this paper, the LBA method is systematically explained and used to assess the production of xylitol by a variant of the conventional chemical process with other biorefinery options. LBA can be broadly applied using this systematic methodology, and many of the process and engineering considerations underlined, in order to manage uncertainty in the early design stages and for triaging process options.
Through the LBA analysis of uncertain cost data provided by engineers and technology developers, and a systematic market and technology risk analysis, it was found that although the production of xylitol by the variant of the classical chemical process remains interesting, the capital investment was likely under-estimated by over 100% in initial assessments. A higher level of technology risk was identified in the course of the LBA, notably due to a potentially over-estimated conversion efficiency. Future trials should be conducted with the PHL of the mill to validate yield.
Furfural has been identified as an attractive alternative, associated with a high market risk. Identification of off-takers ahead of project implementation would limit this risk. Animal feed additive production is an option with less risk and significantly less capital investment, but also less profit.
It has been found that application of the Large Block Analysis significantly clarified the relative costs and risks for the process options considered at the early design stage, underlining the importance of:
• Understanding the physical and construction aspects of the processes considered to be able to identify how they differ;
• Having experience in cost estimation techniques to be able to quantify the differences between the processes in approximate and relative monetary terms;
• Having good communication with technology developers, engineers, and experts in order to make a fair comparison of the process options, including an understanding how initial costs were estimated.
The decision to progress with the three preferred process options at the early design stage was clarified, and in this case, three process options distinct in character and having different engineering emphases going forward to determine whether they would be the preferred option for implementation.
Data Availability Statement
The raw data supporting the conclusions of this article will be made available by the authors, without undue reservation.
Author Contributions
ÉT and PS: methodology. ÉT: written document and original draft. PS and CM: review. All authors contributed to the article and approved the submitted version.
Conflict of Interest
CM is the owner of Myers Consulting LLC.
The remaining authors declare that the research was conducted in the absence of any commercial or financial relationships that could be construed as a potential conflict of interest.
Publisher's Note
All claims expressed in this article are solely those of the authors and do not necessarily represent those of their affiliated organizations, or those of the publisher, the editors and the reviewers. Any product that may be evaluated in this article, or claim that may be made by its manufacturer, is not guaranteed or endorsed by the publisher.
Supplementary Material
The Supplementary Material for this article can be found online at: https://www.frontiersin.org/articles/10.3389/frsus.2021.759191/full#supplementary-material
References
Allen, L., Arato, C., Brix, T., Clarke, P. A., Davies, J., Gene, B., et al. (2019). Processes to Create Multiple Value Streams from Biomass Sources. U.S. Patent No. PCT/US2017/018260. U.S. Patent and Trademark Office.
ASTM International (2019). “Standard classification for cost estimate classification system,” in Designation: E2516 – 11 , (West Conshohocken, PA).
Benali, M. (2015). I-BIOREF Software – Modeling and Analysis for Technical, Economic, and Environmental Assessment of Biorefinery Processes. Retrieved from: https://www.nrcan.gc.ca/sites/www.nrcan.gc.ca/files/canmetenergy/files/pubs/I-BIOREF-brochure_EN.pdf (accessed June 23, 2021).
Brownlee, H. J., and Miner, C. S. (1948). Industrial development of furfural. Industr. Eng. Chem. 40, 201–204. doi: 10.1021/ie50458a005
Cai, C. M., Zhang, T., Kumar, R., and Wyman, C. E. (2014). Integrated furfural production as a renewable fuel and chemical platform from lignocellulosic biomass. J. Chem. Technol. Biotechnol. 89, 2–10. doi: 10.1002/jctb.4168
Cavani, F., Albonetti, S., Basile, F., and Gandini, A. (2016). Chemicals and Fuels from Bio-Based Building Blocks. Berlin: John Wiley & Sons, Incorporated. doi: 10.1002/9783527698202
Cheng, H., and Wang, L. (2013). “Lignocelluloses feedstock biorefinery as petrorefinery substitutes,” in Biomass Now – Sustainable Growth and Use, ed M. D. Matovic (Rijeka: INTECH). doi: 10.5772/51491
Christensen, P., Dysert, L. R., Bates, J., Borowicz, J. J., Bredehoeft, P. R. J., Brown, R. B., et al. (2019). “AACE international recommended practice no. 18R-97 cost estimate classification system – as applied in engineering, procurement, and construction for the process industries,” TCM Framework: 7.3 – Cost Estimating and Budgeting (Fairmont, WV: AACE International).
Claypool, J. T., and Raman, D. R. (2013). Development and validation of a technoeconomic analysis tool for early-stage evaluation of bio-based chemical production processes. Bioresour. Technol. 150, 486–495. doi: 10.1016/j.biortech.2013.08.094
Code of Federal Regulations (2020). “Sec. 573.520 hemicellulose extract,” in Title 21–Food And Drugs, Vol. 6. U.S: U.S. Food and Drug Administration (Silver Spring, MD).
Cortes-Peña, Y., Kumar, D., Singh, V., and Guest, J. S. (2020). BioSTEAM: a fast and flexible platform for the design, simulation, and techno-economic analysis of biorefineries under uncertainty. ACS Sustain. Chem. Eng. 8, 3302–3310. doi: 10.1021/acssuschemeng.9b07040
Dashtban, M., Gilbert, A., and Fatehi, P. (2012). Production of furfural: overview and challenges. J. Sci. Technol. For. Products Proc. 2, 44–53.
Delgado Arcaño, Y., Valmaña García, O. D., Mandelli, D., Carvalho, W. A., and Magalhães Pontes, L. A. (2018). Xylitol: a review on the progress and challenges of its production by chemical route. Catal. Today 344, 2–14. doi: 10.1016/j.cattod.2018.07.060
E4tech RE-CORD WUR. (2015). From the Sugar Platform to Biofuels and Biochemicals: Final Report for the European Commission Directorate-General Energy. Retrieved from: https://ec.europa.eu/energy/content/sugar-platform-biofuels-and-biochemicals_en?redir=1 (accessed June 23, 2021).
Ereev, S. Y., and Patel, M. K. (2012). Practitioner's section Standardized cost estimation for new technologies (SCENT) - methodology and tool. J. Bus. Chem. 9, 31–48.
Gavrilescu, M. (2002). Engineering concerns and new developments in anaerobic waste-water treatment. Clean Technol. Environ. Policy 3, 346–362. doi: 10.1007/s10098-001-0123-x
Gerbrandt, K. (2014). The impacts of xylitol production from hemicellulose residues: process design, life cycle, and techno-economic assessment (thesis). University of Toronto, Toronto, CA, Canada.
Gilani, B. (2014). Sustainability assessment of the hot water extraction biorefinery process using a phased implementation approach (Master). École Polytechnique de Montréal Montréal, Montréal, QC, Canada.
Hemanathan, K., and Lew, P. C. (2017). Recent trends and developments in dissolving pulp production and application. Cellulose 24, 2347–2365. doi: 10.1007/s10570-017-1285-y
Hollmann, J. K. (2014). Improve your contingency estimates for more realistic project budgets: reliable risk-analysis and contingency-estimation practices help to better manage costs in CPI projects of all sizes. Chem. Eng. 121, 36–44.
Hou-Rui, Z. (2012). “Key drivers influencing the large scale production of xylitol,” in D-Xylitol, eds S. S. da Silva and A. K. Chandel (Berlin; Heidelberg: Springer), 267–289. doi: 10.1007/978-3-642-31887-0_12
Iroegbu, A. O., and Hlangothi, S. P. (2019). Furfuryl alcohol a versatile, eco-sustainable compound in perspective. Chem. Afr. 2, 223–239. doi: 10.1007/s42250-018-00036-9
Krishna, S. H., Huang, K. F., Barnett, K. J., He, J. Y., Maravelias, C. T., Dumesic, J. A., et al. (2018). Oxygenated commodity chemicals from chemo-catalytic conversion of biomass derived heterocycles. AIChE J. 64, 1910–1922. doi: 10.1002/aic.16172
Lane, J. (2015). API Announces First Commercial Implementation of GreenBox+ Technology. Retrieved from: https://www.biofuelsdigest.com/bdigest/2015/06/22/api-announces-first-commercial-implementation-of-greenbox-technology/ (accessed May 27, 2021).
Li, H., Saeed, A., Jahan, M. S., Ni, Y., and van Heiningen, A. (2010). Hemicellulose removal from hardwood chips in the pre-hydrolysis step of the kraft-based dissolving pulp production process. J. Wood Chem. Technol. 30, 48–60. doi: 10.1080/02773810903419227
Markets Markets (2019). Furfural Market by Raw Material (Sugarcane Bagasse, Corncob, Rice Husk and Others), Application (Derivatives (Furfural Alcohol and Other Derivatives), Solvent) and Region (Asia-Pacific, Americas, Europe,Middle East and Africa) - Global Forecast to 2024. Retrieved from: https://www.marketsandmarkets.com/Market-Reports/furfural-market-101056456.html (accessed May 11, 2021).
Mazar, A., Ajao, O., Benali, M., Jemaa, N., Wafa Al-Dajani, W., and Paleologou, M. (2020). Integrated multiproduct biorefinery for furfural production with acetic acid and lignin recovery: design, scale-up evaluation, and technoeconomic analysis. ACS Sustain. Chem. Eng. 8, 17345–17358. doi: 10.1021/acssuschemeng.0c04871
Menon, V., and Rao, M. (2012). Trends in bioconversion of lignocellulose: biofuels, platform chemicals & biorefinery concept. Progr. Energy Combust. Sci. 38, 522–550. doi: 10.1016/j.pecs.2012.02.002
Motor Intelligence (2019). Xylitol Market. Retrieved from: https://www.mordorintelligence.com/industry-reports/xylitol-market (accessed May 27, 2021).
Mpabanga, T. P., Chandel, A. K., da Silva, S. S., and Singh, O. V. (2012). “Detoxification strategies applied to lignocellulosic hydrolysates for improved xylitol production,” in D-Xylitol, eds S. S. da Silva and A. K. Chandel (Berlin; Heidelberg: Springer-Verlag), 63–82. doi: 10.1007/978-3-642-31887-0_3
Peters, M. S., Timmerhaus, K. D., and West, R. E. (2003). Plant Design and Economics for Chemical Engineers, 5th Edn. New York, NY: McGraw-Hill.
Pigeon, S., Fortier, C., Coderre, F., and Drolet, J.-Y. (2012). Biométhanisation Fiche détaillée. Retrieved from: https://transitionenergetique.gouv.qc.ca/fileadmin/medias/pdf/agroalimentaire_agricole/1-Biométhanisation.pdf (accessed June 28, 2021).
Rafiqul, I. S. M., and Sakinah, A. M. M. (2013). Processes for the production of xylitol—a review. Food Rev. Int. 29, 127–156. doi: 10.1080/87559129.2012.714434
Retsina, T., and Pylkkanen, V. (2014). Process for Producing Fermentable Sugars and Low-Ahs Biomass for Combustion or Pellets. Alexandria, VA: U.S. Patent and Trademark Office. U. S. Patent No. US8685685B2.
Rosales-Calderon, O., and Arantes, V. (2019). A review on commercial-scale high-value products that can be produced alongside cellulosic ethanol. Biotechnol. Biofuels 12:240. doi: 10.1186/s13068-019-1529-1
Saeed, A., Jahan, M. S., Li, H., Liu, Z., Ni, Y., and van Heiningen, A. (2012). Mass balances of components dissolved in the pre-hydrolysis liquor of kraft-based dissolving pulp production process from Canadian hardwoods. Biomass Bioenergy 39, 14–19. doi: 10.1016/j.biombioe.2010.08.039
Tao, L., and Aden, A. (2009). The economics of current and future biofuels. In Vitro Cell. Dev. Biol. Plant 45, 199–217. doi: 10.1007/s11627-009-9216-8
Trottier, É. (2021). Évaluation économique de technologies émergentes par la méthode Large Block Analysis (MEng Thesis). Polytechnique Montréal, Montréal, QC, Canada.
Tsagkari, M., Kokossis, A., and Dubois, J. L. (2020). A method for quick capital cost estimation of biorefineries beyond the state of the art. Biofuels Bioproducts Bioref. 14, 1061–1088. doi: 10.1002/bbb.2114
Ur-Rehman, S., Mushtaq, Z., Zahoor, T., Jamil, A., and Murtaza, M. A. (2015). Xylitol: A review on bioproduction, application, health benefits, and related safety issues. Critical Reviews in Food Science and Nutrition, 55, 1514–1528. doi: 10.1080/10408398.2012.702288
Wasilenkoff, C. (2018). Fortress Advanced Bioproducts. Available online: https://www.fortressge.com/wp-content/uploads/2018/03/Fortress-Advanced-Bioproducts-Presentation-March-19-2018.pdf (accessed June 22, 2021).
Wu, C. (2016). The potential of pre-hydrolysis liquor from the dissolving pulp process as recovery source of xylooligosaccharide-a mini-review. Bio Resour. 11, 7917–7927. doi: 10.15376/biores.11.3.Wu
zuChem (2013). Xylitol Production Process Partnering Opportunity. Retrieved from: https://www.zuchem.com/wp-content/uploads/2013/05/Xylitol-Process-Opportunity-05222013.pdf (accessed June 22, 2021).
Keywords: cost estimate, CAPEX—capital expenses, process economics, techno-economic, biorefinery and bioeconomy
Citation: Trottier É, Myers C and Stuart P (2022) Comparing Biorefinery Processes at the Early Design Stage Using Large Block Analysis. Front. Sustain. 2:759191. doi: 10.3389/frsus.2021.759191
Received: 16 August 2021; Accepted: 15 October 2021;
Published: 12 September 2022.
Edited by:
Irene Mei Leng Chew, Monash University Malaysia, MalaysiaReviewed by:
Viknesh Andiappan, Heriot-Watt University Malaysia, MalaysiaJully Tan, Monash University Malaysia, Malaysia
Copyright © 2022 Trottier, Myers and Stuart. This is an open-access article distributed under the terms of the Creative Commons Attribution License (CC BY). The use, distribution or reproduction in other forums is permitted, provided the original author(s) and the copyright owner(s) are credited and that the original publication in this journal is cited, in accordance with accepted academic practice. No use, distribution or reproduction is permitted which does not comply with these terms.
*Correspondence: Paul Stuart, paul.stuart@polymtl.ca