Design of solvent-assisted plastics recycling: Integrated economics and environmental impacts analysis
- 1Department of Chemical Engineering, Rowan University, Glassboro, NJ, United States
- 2Assessment Group, Energy Systems and Infrastructure Analysis, Argonne National Laboratory, Lemont, IL, United States
In 2018, the United States generated over 35. 7 million tons of plastic waste, with only 8.4% being recycled and the other 91.6% incinerated or disposed of in a landfill. The continued growth of the polymer market has raised concerns over the end of life of plastics. Currently, the waste management system is faced with issues of inefficient sorting methods and low-efficiency recycling methods when it comes to plastics recycling. Mechanical recycling is the commonest recycling method but presents a lower-valued recycled material due to the material incompatibilities introduced via the inefficient sorting methods. Chemical recycling offers a promising alternative as it potentially allows for plastics to maintain their original properties. To that end, there is the need to investigate feasible chemical recycling methods to help mitigate the challenging problem posed by plastics at the end-of-life stage. This work proposes a conceptual solvent-assisted plastics recycling framework based on a superstructure optimization approach. This framework is evaluated using a representative case study to recover Polyethylene Terephthalate (PET). In this case study, it is found that polymer recovery is both economically and environmentally favorable when compared to traditional methods of disposal such as incineration.
Introduction
In 2019, ~368 million metric tons of plastic were produced globally and by the year 2050, plastic production is expected to triple (Tiseo, 2020). From the beginning of large-scale production of plastics in 1950–2019, ~7,300 million metric tons of plastics have been produced globally (Geyer et al., 2017). As shown in Figure 1, the general trend for yearly global plastic production has been growing exponentially for the past 70 years. With the continued growth of the polymer industry, it is estimated that between 850 and 950 metric tons of plastic waste will be generated per year (Degnan and Shinde, 2019).
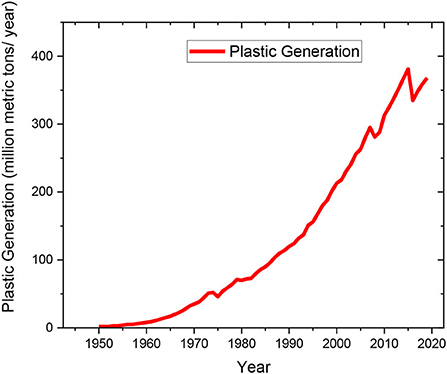
Figure 1. Plastic waste generation from 1950 to 2019 (Values used for plotting adapted from Geyer et al., 2017).
Plastic waste generation has become increasingly concerning as 79% of all waste plastics end up in landfills, 12% are incinerated, and only 9% are recycled (Geyer et al., 2017). The current management infrastructure lacks an effective sorting method for plastic waste; hence portions of the plastics sent to material recovery facilities are rejected. As the rate of plastic waste generation grows, continuing to landfill the majority of waste plastics will become ineffective as the surface area of the earth is finite. Furthermore, waste plastics make up 80% of marine debris as these materials are illegally dumped into the ocean or are carried from the land by natural phenomena (UN General Assembly, 2018). This accumulation of plastics in the ocean affects both the marine ecosystem and human health. Waste plastic in the ocean gradually begins to fragment into smaller particles known as microplastics (< 5 mm). As a result, plastics has been detected in water samples from oceans and are present in common foods such as table salt. Several chemicals used in the production of plastics are known to be carcinogens and endocrine inhibitors, leading to developmental, reproductive, neurological, and immune disorders (Li et al., 2018). It is estimated that the average American eats, drinks, and inhales 74,000–113,000 microplastic particles annually, with the exposure risks to humans being uncertain (Cox et al., 2019, 2020). Thus, better mitigation plans are needed to address the plastic waste issue.
Inefficient sorting techniques and low-efficiency recycling methods are important factors limiting waste plastic recycling (Schwarz et al., 2021). Commonly used plastics typically made of Polyethylene Terephthalate (PET) and Low-Density Polyethylene (LDPE) end up in Municipal Solid Waste (MSW) streams. The MSW streams can vary widely in composition, physical and chemical properties, and overall recycling potential. These streams often contain other materials like cardboard and metal that need first to be separated out at a Material Recovery Facility (MRF) (Schwarz et al., 2021). This separation is typically achieved based on polymer type using near-infrared (NIR) technologies. The materials are further separated into clear and colored streams using optical sensors (Schyns and Shaver, 2021). The separation of multilayered plastics such as water bottles with plastic sleeves is expensive and often contains polyamides or ethylene vinyl alcohols that can affect the chemical, physical, and mechanical properties of the recyclate (Mehta, 2020).
Plastic recycling can be divided into four main types of processes: primary, secondary, tertiary, and quaternary recycling (Kumar, 2021). Primary recycling involves the recovery and reprocessing of pure polymer streams. Secondary recycling requires sorting the polymer waste stream, size reduction, and reprocessing where the material is downcycled (Sahajwalla and Gaikwad, 2018). Tertiary recycling is the depolymerization of polymers and is used for polymers when primary and secondary methods are not applicable (Kumar, 2021). Quaternary recycling is when the polymer is used for energy recovery via pyrolysis (Schyns and Shaver, 2021). More than 90% of the recycled plastics fall into this secondary recycling category. These materials are subjected to mechanical recycling methods. Extrusion is the most widely used mechanical recycling method as it is a cheap, large-scale, and solvent-free recovery method (Schyns and Shaver, 2021). However, the mechanical properties of the polymer is affected by this method, which leads to the performance downgrade of the polymer material. Another barrier to mechanical recycling is the recyclability of the material. The polymer blends present in the waste stream can compromise the mechanical integrity of the recycled product due to the incompatibility in the physical properties of the different polymers. Furthermore, these polymers often have additives present in them to enhance their physical and chemical properties, which cannot be addressed by mechanical recycling techniques (Solis and Silveira, 2020). As plastic waste generation continues to grow, it is imperative to simultaneously address the inefficiencies in the MSW sorting system and explore alternative primary recycling methods that are more widely applicable.
While chemical recycling methods are traditionally reserved for tertiary and quaternary recycling, there has been recent work done to suggest it could have applications for primary recycling (Tullo, 2019). The fundamental mechanisms behind chemical recycling methods are different from mechanical recycling as it deals primarily with the breakdown of the chemical structure of the material. As a result, chemical recycling is more tolerant of contaminants and yield material equivalent to the original, reducing the amount of downcycling (Tullo, 2019). Chemical recycling further allows reprocessing the material into petrochemicals that can be used as fuel or into new plastics (Al-Salem et al., 2009). Tertiary recycling methods, typically chemical-based techniques, can cleave polymer chains and include processes such as hydrolysis, methanolysis, and glycolysis (Thomas et al., 2019). In addition, tertiary recycling methods can recover individual monomers and separate the additives. These monomers can then be used to create new polymers. Quaternary recycling methods can also convert the polymer into smaller fuel-grade hydrocarbons using processes such as pyrolysis, gasification, and hydrocracking (Kunwar et al., 2016). However, quaternary recycling methods result in greenhouse gas emissions as the material is combusted. Nevertheless, using these plastics-to-fuel processes to produce hydrocarbon fuels has been shown to produce less emissions than traditional fuel production processes (Benavides et al., 2017).
Recent work conducted shows that a dissolution process can be used as a primary recycling method (Sherwood, 2020). The dissolution process requires an appropriate solvent to dissolve the solute and can be used to recover the polymer or monomer so that it can be converted into new plastics. However, this method requires large amounts of solvent as that is often the agent in excess in the reaction driving up the operational cost. In addition, these processes lead to large amounts of solvent waste, which can be challenging to manage because of the emissions associated with its disposal. As a result, the chemical recycling industry is dominated by quaternary recycling processes as they are more economically favorable. To make primary chemical recycling methods economically competitive, strategies to reduce operational costs need to be implemented.
Chemical recycling methods can be economically viable and environmentally friendly if designed using systems thinking approach to optimize performance. The systems thinking approach can provide solutions to complex and challenging problems that have to meet multiple criteria. Thus, holistic solutions can be obtained to relatively new and unexplored processes. As solvent-assisted recycling of plastics is a relatively new area that needs to be explored further, the systems thinking approach is employed in this work. Also, solvents are the predominant materials used in the chemical recycling of plastics, hence, it presents a good opportunity to recover the waste solvents for reuse to help reduce the recycling cost and improve the greenness of the overall process. Furthermore, quantification of the environmental impacts associated with the integration of solvent recovery for reuse has been relatively explored. In this work, we leverage a methodology from previous work by Chea et al. (2020) to evaluate plastic recovery methodologies. This work utilizes an optimization approach to simultaneously analyze multiple possible recovery pathways and reports the most economically favorable option. Incorporating this solvent recovery framework in the design of plastic-to-plastic processes could benefit chemical recycling technologies and provide more opportunities to recover waste plastic that overwise end up in the environment. A superstructure-based approach to process synthesis is implemented as a one-by-one analysis of all the possible recycling pathways is often infeasible within the design frame (Diwekar, 2010; Tseng et al., 2013; Mukherjee et al., 2015). The work proposed in this study examines the techno-economics of chemical recycling using a solvent. We further present an environmental assessment of the optimized pathway using the Greenhouse gas, Regulated Emissions, and Energy use in Technologies (GREET) model. This study provides an optimization framework to address the economic challenges of implementing large-scale plastic recycling in the current waste management infrastructure and the environmental impacts.
This paper is divided into four sections. Section 1 discusses the previous work done in the literature and the motivation for this study. In section Material and methods, we focus on the methodology, where we describe the data preparation, superstructure generation, the general optimization framework, and the environmental impact assessment used in this study. In section 3, we describe a representative PET case study to evaluate the framework and present results from the cost optimization as well as the environmental impact assessment from the GREET method. We then present some concluding thoughts in section Conclusion.
Materials and methods
In this section, we discuss data preparation, economic model building, and its optimization. We then present the general approach for the optimization framework evaluation. We finally discuss the environmental impact assessment of the recycling process using the GREET method.
Data preparation
The first step to developing the framework for the optimization of the recovery processes is data collection, where we gathered all the parameters needed for the problem. These parameters are associated with solvents, plastics, and the technologies used in the framework. Physical and chemical properties for common solvents and polymers were collected and compiled into a chemical database. We further investigated separation technologies and made the selection on a case-specific basis. The applicability of the technologies was evaluated based on factors such as driving force and component interactions. The separation technologies used in this work where, we considered the recycling of PET as a representative case study were modeled using mathematical equations typically found in engineering textbooks (Biegler, 1997; Richardson et al., 2002; Towler and Sinnott, 2012; de Haan, 2013; Gorak and Sorensen, 2014; Tarleton, 2014; Basile et al., 2015; Nagy, 2019). We use the SuperPro Designer™ software to acquire data for standard capacity and cost, standard labor-hour, and technology utility requirement cost for each process technology. The Greenhouse gas, Regulated Emissions, and Energy use in Technologies (GREET) model (Argonne National Laboratory, 2021) was used to quantify the Life Cycle Inventories (LCI) for the optimal pathway after the optimization, and hence the environmental impact assessment. Furthermore, an incineration model was created to compare economic and environmental impact to the proposed framework recovery.
Superstructure development and economic model building
After data preparation, the next step is to develop a superstructure comprising all possible technologies with their stream flows and build mathematical models to help estimate the cost for each technology.
A superstructure is an approach to process synthesis that encompasses all technology alternatives, streams, mixers, and splitters for all possible flow combinations (Yenkie et al., 2017; Chea et al., 2020). The separation steps are divided into four stages based on the type of separation required: solid removal, recovery, purification, and refinement. Typically, plastic wastes are accompanied by other solid waste. It is therefore important to remove these accompanied solids to help in the downstream processes. Thus, the primary stage in this polymer recovery system is solid removal, consisting of the following technologies: sedimentation (SDM), filtration (FLT), adsorption (ADS1), precipitation (PRC), and centrifugation (CNF). This stage in the recovery process also aims to remove remaining solid additives from the polymer recycling process. Sedimentation, centrifugation, and filtration are similar as the separation through these methods depend on the settling velocity of the solid impurities and additives being removed. After the removal of the solid contaminants and additives, the effluent stream continues into the recovery stage of the framework.
The second stage contains four possible technologies for removing liquid impurities: distillation (DST), pervaporation (PVP1), adsorption (ADS2), and microfiltration (MF). Distillation is an “energy-intensive” unit that utilizes differences in boiling points to separate components. In the pervaporation unit, a membrane selectively permeates components from the feed through the membrane and vaporizes them during this passing. A vacuum is used to collect the vapor product and to create a large pressure gradient to drive the separation of the mixture. Microfiltration is another process unit that utilizes a membrane for separation from the remaining components in the stream. Unlike pervaporation, the product remains a liquid in the permeate stream. Additionally, the pressure gradient driving the separation is caused by a difference in partial pressure rather than a vacuum.
To reach the specified polymer purity, a purification stage is implemented. This third stage includes microfiltration (MF2), ultrafiltration (UF1), and pervaporation (PVP2) as the purification process units. The pervaporation and microfiltration in this stage are designed using the same principles of separation described for the same technologies in stage two above. Ultrafiltration is another membrane process that is semi-permeable allowing the desired solvent to be separated from the mixture through a pressure driving force. The ultrafiltration unit has a more selective membrane and operates at higher pressures than the microfiltration unit. At the end of the purification stage, the polymer recovery stream could contain impurities above their allowable constraints. A refinement stage with Ultrafiltration (UF2), Nanofiltration (NF), and Pervaporation (PVP3) is then implemented to satisfy the purity specifications. We provided bypasses that allow a stage to be skipped if not needed to reach the desired purity (Wu et al., 2017; Yenkie et al., 2017). Incineration was also considered a possible pathway despite the absence of an incineration path in the superstructure. Figure 2 illustrates the proposed superstructure for this work where we use PET as a case study. This superstructure comprises 480 possible pathways. It further contains 50 streams, 4 bypasses, and 15 individual separation units for determining a recovery process with a minimized cost objective. We provide further details of the PET recovery process in the Results and Discussion section.
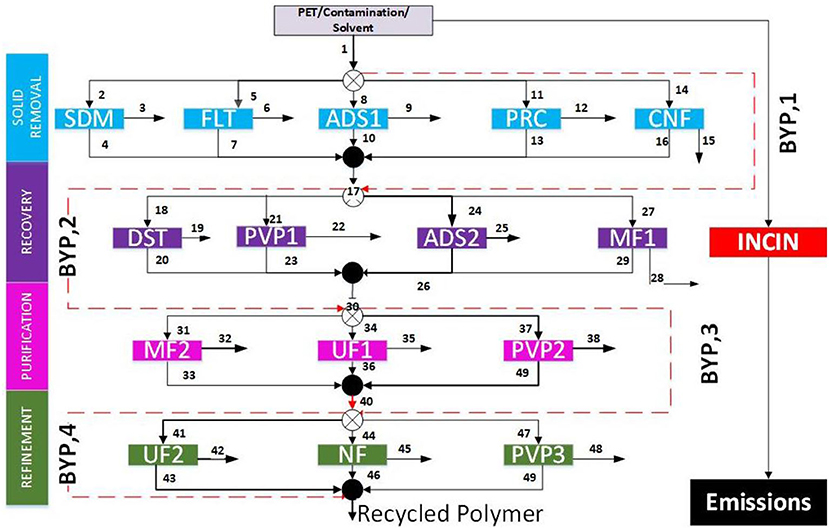
Figure 2. Generic superstructure for polymer recycling (SDM, Sedimentation; FLT, Filtration; ADS, Adsorption; PRC, Precipitation; CNF, Centrifugation; DST, Distillation; PVP, Pervaporation; MF, Microfiltration; UF, Ultrafiltration; NF, Nanofiltration; BYP, Bypass).
For each technology in the superstructure, mathematical models based on mass/energy balances, design equations, and constraints were formulated to help estimate the technology cost, and hence the overall recovery pathway cost. There were six major categories within this cost analysis: capital, labor, utilities, consumables, overhead, and materials cost, if applicable for the specific case. Technologies were sized using a cost-to-capacity methodology shown in Equation 1.
The capital cost was based on the capacity of the separation unit and evaluated with a bare module cost (BMC) multiplier of 5.4 and a capital recovery factor (CRF) of 0.11, calculated using Equation 2 below:
where, i in the equation represents the real pretax marginal rate, which was assumed to be 10 percent, and n is the plant life of 25 years. The utility cost was calculated based on the energy, steam, and cooling water requirements for each unit. The raw material cost accounts for the purchase of components added to the recovery process. The labor cost was calculated for 330 working days per year at $30/h for each operator required. Consumables refer to materials within the separation units that are depleted over time, such as membranes and adsorbents. The consumables cost considers the amount associated with replacing these materials a set amount of times per operational year. The “other” cost encompasses the overhead costs associated with administrative and management hiring. These individual costs are calculated and summed to find the total cost of the recovery process.
Optimization strategy
In this section, we highlight the overall problem formulation as a mixed-integer non-linear optimization (MINLP) and the framework for evaluation.
MINLP formulation
Individual separation technologies were modeled as Non-linear Programming (NLP) in the General Algebraic Modeling Systems (GAMS). The selection of technology at each stage of the optimization problem is achieved with the introduction of binary variables. The NLP aspect of the model presented us with continuous variables whiles the implementation of binary variables for the selection of the technologies presented us with a Mixed Integer Programming (MIP) problem. The consideration of both continuous and binary variables transformed the model into an MINLP optimization problem. MINLP problems are encountered when a “yes” or “no” (1–0) decision has to be made. In this work, technologies selected are assigned a value of “1” indicating the unit operation is active, while inactive units are assigned a value of “0.” The sum of all binary variables at a stage is equal to 1 to ensure only one technology is selected at the stage. We implemented the Branch-And-Reduce Optimization Navigator (BARON) solver in GAMS to determine the optimal recovery pathway.
Framework for evaluation
Below are the evaluation steps implemented for the recovery process:
Step#1: Polymer classification
Step#2: Polymer waste input and output specification
Step#3: Optimization problem formulation as an MINLP
Step#4: Determination of optimal recovery pathway based on cost minimization using GAMS
Step#5: Environmental Impact Assessment using the GREET model
Figure 3 shows the general strategy for the analysis summarizing the key steps in the problem formulation and solution reporting.
Environmental impact assessment using the GREET model
As stated earlier, the environmental impact assessment was conducted for the optimal recovery pathway for the PET case study. The environmental impact of this work was based on greenhouse gas (GHG) emissions. As mentioned previously the GREET model (Argonne National Laboratory, 2021) and life cycle impact data quantify the environmental impact. Life cycle inventories (LCIs) were developed for each step in the PET recycling process. Each of these inputs was divided by the kilogram of PET recovered, which served as the functional unit. The first step, swelling and dye removal, requires the input of ethyl benzoate and heat. The production of ethyl benzoate requires reacting benzoic acid with ethanol. The production process for ethanol and PET are models that can be found in the GREET database; hence we focused on building a model for benzoic acid production and subsequently, ethyl benzoate. The production of benzoic acid is based on the partial oxidation of toluene with water being a byproduct. The model created for benzoic acid helps in quantifying the LCI data for the recovery process. In terms of energy requirements, we considered electricity and natural gas used in steam generation for the production processes of each component. The upstream emissions for the energy requirement models are already in-built processes within the GREET database. The final life cycle assessment for the recovery framework entails the summation of LCI data for the ethyl benzoate (ethanol + benzoic acid processes), electricity and natural gas requirements, and PET for the entire recycling process. GREET reports various types of emissions from CO to PM10, each of these emissions categories are normalized over their respective global warming potentials and the final values are reported in units of kg CO2 equivalent emissions per kg of PET recovered. We describe the PET case study in the Results and Discussion section.
Results and discussion
In this section, we present a description of the PET recovery case study. We then discuss the results associated with applying our framework to this case study and some sensitivity analysis.
PET recovery process description
Polyethylene terephthalate (PET) is a polyester derived from crude oil. This material is used for packaging food and beverages because of its inert properties, recyclability, and durability. Sherwood (2020) have developed and patented a two-stage closed-loop recycling process that uses an organic solvent such as ethyl benzoate (EB) to recycle post-consumer PET waste (Sherwood, 2020). The proposed process consists of two steps: (1) dye removal and (2) polymer recovery as shown in Figure 4.
PET waste is firstly subjected to a dye removal step by dissolution using a solvent such as an ethyl benzoate at 120°C. The solvent at this temperature swells the polymer and dissolves traces of the dye. The second step of the process uses ethyl benzoate at 180°C to dissolve the swelled PET fully. Any material remaining in the solid phase is removed as contamination in a filtration step. The resulting product stream from this process consists of recycled PET, ethyl benzoate, acetaldehyde produced from PET degradation at high temperatures, and remaining polymer additives. Solvent recovery is a necessary step to increase the economic viability of the plastic recovery process because of the large volume of solvent required for the successful dissolution of the plastic. Unlike other processes that have stringent solvent purity requirements, Sherwood et al. proposed that the solvent recovered can be reused within the same process for the recycling of polymer through chemical means (Sherwood, 2020).
An inlet flow of 100 kg/h was chosen for PET entering the dissolution stage. A solvent-to-plastic ratio of 22.78 g ethyl benzoate: 1 g PET was used to calculate the 2278 kg/h solvent entering flow. The feed rates for the polymer additives (ADD) and acetaldehyde (ACT) were set to 0.5 kg/h based on standard PET formulation and the PET thermal degradation curve (Das and Tiwari, 2019). Most of the polymer additives are removed with dyes in the initial swelling phase of plastic recycling. Therefore, the presence of additives in the initial stream is minimal. The plastic recycling process reaches temperatures above the PET glass transition temperature, but below the decomposition temperature thus, minimal acetaldehyde byproduct was likely produced in the process. Acetaldehyde and the additives had an outlet specification of 95% removal. The polymer recovery optimization process was specified for a PET purity of 95% and a recovery of 95%. We applied our developed superstructure to this case study.
Technoeconomic analysis
Table 1 displays the optimization results from GAMS, which contains the annual operating costs and the price per kg processed compared for the optimal pathway and incineration. There are 480 possible recovery pathways. The polymer recycling stream optimization model consists of 780 equations, 562 variables, and 19 discrete variables. BARON, which is the solver used, converged to a solution within 5.26 s with an optimality gap of 1E-05. The optimal polymer recovery pathway to recover PET from a stream containing 94% EB, 4% PET, and 0.5% ACT and ADD required the use of adsorption, pervaporation, and ultrafiltration. Figure 5 shows the optimal path highlighted in the superstructure.
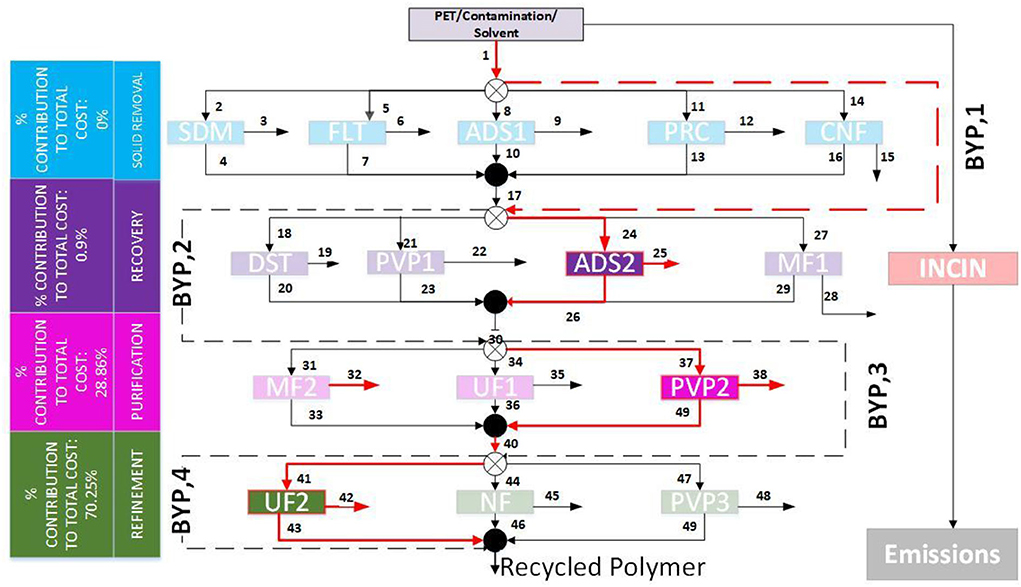
Figure 5. Optimal path for PET Recovery with the respective stage-wise cost contribution. The technologies selected are Adsorption (ADS) in the recovery stage, Pervaporation (PVP) in the purification stage, and Ultrafiltration (UF) in the refinement stage. The solid removal stage was bypassed.
This process has an annual operation cost of $77,000/yr over a 25-year period with an annual recovery rate of 768.48 metric tons/yr of PET at a purity of 99%. The incineration of PET has an annual operation cost of $3.01 million/yr, which is greater by a factor of nearly 39 than the annual operation cost of polymer recovery. Comparing recovery to incineration there is a 97% reduction in cost when recovering the material. Figure 6 displays the total contribution of each cost category for the feasible pathway.
The annualized capital cost contributes to much of the total cost followed by the overhead (other) cost and consumables cost. The small utility cost contribution is due to the relatively low energy requirements for the technologies in this process. All three of the selected technologies require additional components/materials for separation and therefore contribute to the overall consumables cost. The annualized capital cost is directly related to the capacity of the unit operations selected. The breakdown of the stagewise contribution to the total cost of the process is shown in Figure 7. There is no cost associated with the solid removal stage since the optimal pathway bypasses that stage. The refinement stage contributes the most to the overall cost followed by the purification and recovery stages. As with the overall cost distribution, the main contributing factor in the refinement stage is annualized capital cost.
The large capacity ultrafiltration unit selected in the refinement stage is responsible for the significant stage and overall annualized capital cost contribution. The membranes for the pervaporation and ultrafiltration units make up the majority of the contribution to the consumables cost compared to the adsorbent from the adsorption unit.
Sustainability analysis
The emission components considered for this work include VOC, CO, NOx, PM10, PM2.5, SOx, BC, OC, CH4, N2O, and CO2. The total GHG for the recovery process is 7.7 gCO2-eq/kg PET while that of incineration is 339.3 gCO2-eq/kg PET. Recycling PET waste results in a 98% reduction in GHG emissions. Figure 8 shows the component distribution for polymer recovery and incineration. The highest emissions are associated with CO2 for both the recycling and incineration processes.
Figure 9 shows the percentage contribution of each subprocess for PET recycling. The ethyl benzoate process dominated this distribution. This high EB value is primarily due to the ethanol production process, which contributed to 94% of the emissions, while the remaining 6% was for benzoic acid production. The solvent accounted for the highest emissions while the energy inputs had a lesser contribution. Therefore, recovering the solvent (EB) for reuse in this process can be beneficial in further reducing the carbon footprint of the recycling process.
Sensitivity analysis
From the economic analysis, it can be seen that the two largest factors driving the cost are capital cost and consumable cost. The capital cost of the units is based on the capacity which is a function of flowrate. The consumable costs are based on the cost of the membrane and the replacement time. Sensitivity analysis was performed at varying flowrate and replacement times. This analysis was carried by varying one of the parameters while holding the other constant. First, the flowrate was varied from 1500 kg/h to 5000 kg/h by increments of 500 kg/h. The trend in unit price as flowrate is increases can be seen in Figure 10.
As the flowrate is increased the unit cost reduces. This is because the capacity of the unit scales linearly with flowrate, while the capital cost of the unit scales exponentially with a power of two-thirds.
It can again be seen the unit price trends down as the replacement time is increased in Figure 11. This is because membrane replacement time and number of membranes required for a year have an inverse relationship.
Conclusion
We have developed a superstructure based chemical plastic recycling framework that incorporates solvent recovery and considers a stage-wise analysis of multiple technologies. The viability of this framework was evaluated with the recovery of PET using ethyl benzoate solvent. Common polymer and solvent properties, separation technologies, and municipal solid waste handling information were necessary to obtain the information for solving the chemical plastic recycling related problem. Multiple polymer recovery pathways were analyzed simultaneously to obtain the optimal recovery pathway. This case has demonstrated that chemical recycling is both economically favorable, with a 97% reduction in cost, and greener, with a 98% reduction in net GHG emissions. Further investigation into solvent production processes is required to reduce both the emissions and cost of these processes, as the solvent requirement is the driving factor for both metrics. Additional work is being done to develop models for mechanical and thermal recycling technologies to be incorporated into the superstructure for further comparison. With these additional models, we will conduct more case studies for different plastic types. These analyses will expand the existing framework to become an all-inclusive polymer recovery framework that can be applied to any industry that generates large amounts of plastic waste.
Data availability statement
The original contributions presented in the study are included in the article/supplementary material, further inquiries can be directed to the corresponding author.
Author contributions
AL, KH, JC, and JS: Preliminary data collection. AL: Visualization. AL and KH: Writing-original draft. AL and EA: Writing-review and editing and formal analysis. PB and KY: Conceptualization, writing-review, and editing. All authors contributed to the article and approved the submitted version.
Funding
U.S. Department of Energy (DoE) Science Undergraduate Laboratory Internship (SULI) program supported one of the authors' (i.e., AL) internship during the summer of 2021 at Argonne National Laboratory's Energy Systems and Infrastructure Analysis. Argonne National Laboratory's work was supported by the U.S. Department of Energy, Office of Energy Efficiency and Renewable Energy (EERE)—Bioenergy Technologies Office (BETO) under contract DE-AC02-06CH11357. This work was supported by the United States Environmental Protection Agency's Pollution Prevention (P2) Program: NP-96259218.
Acknowledgments
The authors would like to thank the Department of Chemical Engineering at Rowan University for its resources and support.
Conflict of interest
The authors declare that the research was conducted in the absence of any commercial or financial relationships that could be construed as a potential conflict of interest.
Publisher's note
All claims expressed in this article are solely those of the authors and do not necessarily represent those of their affiliated organizations, or those of the publisher, the editors and the reviewers. Any product that may be evaluated in this article, or claim that may be made by its manufacturer, is not guaranteed or endorsed by the publisher.
Supplementary material
The Supplementary Material for this article can be found online at: https://www.frontiersin.org/articles/10.3389/frsus.2022.989720/full#supplementary-material
References
Al-Salem, S. M., Lettieri, P., and Baeyens, J. (2009). Recycling and recovery routes of plastic solid waste (PSW): a review. Waste Manage. 29, 2625–2643. doi: 10.1016/j.wasman.2009.06.004
Argonne National Laboratory (2021). GREET: Greenhouse Gases, Regulated Emissions, and Energy use in Transportation [WWW Document]. Available online at: https://greet.es.anl.gov/ (accessed 19 October, 2021).
Basile, A., Figoli, A., and Khayet, M. (2015). Pervaporation, Vapour Permeation and Membrane Distillation: Principles and Applications. Cambridge: Elsevier Science and Technology.
Benavides, P. T., Sun, P., Han, J., Dunn, J. B., and Wang, M. (2017). Life-cycle analysis of fuels from post-use non-recycled plastics. Fuel 203, 11–22. doi: 10.1016/j.fuel.2017.04.070
Biegler, L. (1997). Systematic Methods of Chemical Process Design, 1st Edn. Upper Saddle River, NJ: Prentice Hall PTR.
Chea, J., Lehr, A., Stengel, J., Savelski, M. J., Slater, C. S., and Yenkie, K. (2020). Evaluation of solvent recovery options for economic feasibility through a superstructure-based optimization framework. Ind. Eng. Chem. Res. 59, 5931–5944. doi: 10.1021/acs.iecr.9b06725
Cox, K. D., Covernton, G. A., Davies, H. L., Dower, J. F., Juanes, F., and Dudas, S. E. (2019). Human consumption of microplastics. Environ. Sci. Technol. 53, 7068–7074. doi: 10.1021/acs.est.9b01517
Cox, K. D., Covernton, G. A., Davies, H. L., Dower, J. F., Juanes, F., and Dudas, S. E. (2020). Correction to human consumption of microplastics. Environ. Sci. Technol. 54, 10974–10974. doi: 10.1021/acs.est.0c04032
Das, P., and Tiwari, P. (2019). Thermal degradation study of waste polyethylene terephthalate (PET) under inert and oxidative environments. Thermochim. Acta 679:178340. doi: 10.1016/j.tca.2019.178340
de Haan, A. B. (2013). Industrial Separation Processes: Fundamentals, De Gruyter Textbook. Berlin: De Gruyter . doi: 10.1515/9783110306729
Degnan, T., and Shinde, S. L. (2019). Waste-plastic processing provides global challenges and opportunities. MRS Bull. 44, 436–437. doi: 10.1557/mrs.2019.133
Geyer, R., Jambeck, J. R., and Law, K. L. (2017). Production, use, and fate of all plastics ever made. Sci. Adv. 3:e1700782. doi: 10.1126/sciadv.1700782
Gorak, A., and Sorensen, E. (2014). Distillation: Fundamentals and Principles. San Diego, CA: Elsevier Science and Technology. doi: 10.1016/B978-0-12-386547-2.05002-X
Kumar, R. (2021). Tertiary and quaternary recycling of thermoplastics by additive manufacturing approach for thermal sustainability. Mater. Today Proc. Int. Conf. Newer Trends Innov. Mech. Eng. Mater. Sci. 37, 2382–2386. doi: 10.1016/j.matpr.2020.08.183
Kunwar, B., Cheng, H. N., Chandrashekaran, S. R., and Sharma, B. K. (2016). Plastics to fuel: a review. Renew. Sustain. Energy Rev. 54, 421–428. doi: 10.1016/j.rser.2015.10.015
Li, J., Liu, H., and Paul Chen, J. (2018). Microplastics in freshwater systems: a review on occurrence, environmental effects, and methods for microplastics detection. Water Res. 137, 362–374. doi: 10.1016/j.watres.2017.12.056
Mehta, A. (2020). “The plastic sorting challenge,” in Chemistry World [WWW Document]. Available online at: https://www.chemistryworld.com/features/the-plastic-sorting-challenge/4011434.article (accessed 31 May, 2021).
Mukherjee, R., Sengupta, D., and Sikdar, S. K. (2015). Sustainability in the context of process engineering. Clean Technol. Environ. Policy 17, 833–840. doi: 10.1007/s10098-015-0952-7
Nagy, E. (2019). Nanofiltration, in: Basic Equations of Mass Transport Through a Membrane Layer. Waltham, MA: Elsevier, 417–428. doi: 10.1016/B978-0-12-813722-2.00015-7
Richardson, J. F., Harker, J. H., and Backhurst, J. R. (2002). Coulson and Rochardson's Chemical Engineering Volume 2 Technology and Separation Processes, 5th Edn. Burlington, MA: Butterworth-Heinemann.
Sahajwalla, V., and Gaikwad, V. (2018). The present and future of e-waste plastics recycling. Curr. Opin. Green Sustain. Chem. Reuse Recycling 13, 102–107. doi: 10.1016/j.cogsc.2018.06.006
Schwarz, A., Ligthart, T., Bizarro, D., Wild, P., Vreugdenhil, B., and Harmelen, T. (2021). Plastic recycling in a circular economy; determining environmental performance through an LCA matrix model approach. Waste Manage. 121, 331–342. doi: 10.1016/j.wasman.2020.12.020
Schyns, Z. O. G., and Shaver, M. P. (2021). Mechanical recycling of packaging plastics: a review. Macromol. Rapid Commun. 42:2000415. doi: 10.1002/marc.202000415
Sherwood, J. (2020). Closed-loop recycling of polymers using solvents : remaking plastics for a circular economy. Johnson Matthey Technol. Rev. 64, 4–15. doi: 10.1595/205651319X15574756736831
Solis, M., and Silveira, S. (2020). Technologies for chemical recycling of household plastics—A technical review and TRL assessment. Waste Manage. 105, 128–138. doi: 10.1016/j.wasman.2020.01.038
Tarleton, E. S. (2014). Progress in Filtration and Separation. San Diego, CA: Elsevier Science and Technology.
Thomas S. Kanny K. Thomas M. Rane A. and Abitha V. K. (2019). Recycling of Polyethylene Terephthalate Bottles. Cambridge, MA: Elsevier.
Tiseo, I. (2020). “Topic: Global plastic waste,” in Statista [WWW Document]. Available online at: https://www.statista.com/topics/5401/global-plastic-waste/ (accessed 19 December, 2020).
Tseng, M.-L., (Anthony) Shun Fung, C., Tan, R. R., and Siriban-Manalang, A. B. (2013). Sustainable consumption and production for Asia: sustainability through green design and practice. J. Clean. Prod. 40, 1–5. doi: 10.1016/j.jclepro.2012.07.015
Tullo, A. (2019). “Plastic has a problem; is chemical recycling the solution?” in Chemical and Engineering News [WWW Document]. Available online at: https://cen.acs.org/environment/recycling/Plastic-problem-chemical-recycling-solution/97/i39 (accessed 31 May, 2021).
UN General Assembly. (2018). Making the United Nations Relevant to All People. Plastics | General Assembly of the United Nations. Available online at: https://www.un.org/pga/73/plastics/ (accessed May 31, 2021).
Wu, W., Yenkie, K., and Maravelias, C. T. (2017). A superstructure-based framework for bio-separation network synthesis. Comput. Chem. Eng. 96, 1–17. doi: 10.1016/j.compchemeng.2016.10.007
Keywords: optimization, recycling, economics, environmental impacts, plastics
Citation: Lehr AL, Heider KL, Aboagye EA, Chea JD, Stengel JP, Benavides PT and Yenkie KM (2022) Design of solvent-assisted plastics recycling: Integrated economics and environmental impacts analysis. Front. Sustain. 3:989720. doi: 10.3389/frsus.2022.989720
Received: 08 July 2022; Accepted: 30 August 2022;
Published: 21 September 2022.
Edited by:
Debalina Sengupta, Texas A&M University, United StatesReviewed by:
José María Ponce-Ortega, Michoacana University of San Nicolás de Hidalgo, MexicoJecksin Ooi, Heriot-Watt University Malaysia, Malaysia
Copyright © 2022 Lehr, Heider, Aboagye, Chea, Stengel, Benavides and Yenkie. This is an open-access article distributed under the terms of the Creative Commons Attribution License (CC BY). The use, distribution or reproduction in other forums is permitted, provided the original author(s) and the copyright owner(s) are credited and that the original publication in this journal is cited, in accordance with accepted academic practice. No use, distribution or reproduction is permitted which does not comply with these terms.
*Correspondence: Kirti M. Yenkie, yenkie@rowan.edu