The influence of stakeholder perspectives on the end-of-life allocation in the life cycle assessment of lithium-ion batteries
- 1Chair of Sustainable Manufacturing & Life Cycle Engineering, Institute of Machine Tools and Production Technology (IWF), Technische Universität Braunschweig, Braunschweig, Germany
- 2Battery LabFactory Braunschweig (BLB), Technische Universität Braunschweig, Braunschweig, Germany
With an increasing number of electric vehicles on roads, recycling is an important topic to design circular supply chains for batteries. To stimulate such circular supply chains, the new EU battery directive includes mandatory recycled content in batteries and recovery rates of materials for lithium-ion batteries on the European market. Modeling the end-of-life of batteries as part of a life cycle assessment (LCA) is methodologically challenging as batteries are quite complex product systems. One of these challenges is the allocation of material impacts from different life cycle stages along subsequent product life cycles. We analyzed the different stakeholders in the life cycle of a lithium-ion battery and identified possible LCA questions based on their decision contexts. For each LCA question, an LCA archetype was defined, which includes the functional unit, the system boundary, and the allocation procedure. These archetypes are applied and tested in a case study. The results show a significant variance depending on the archetype used. This highlights the importance of understanding the stakeholder perspective in LCA and decision support.
1. Introduction
The transport sector is responsible for 14% of all direct and indirect GHG emissions worldwide, with road transport being by far the biggest contributor within the sector (Lamb et al., 2021). Electric vehicles are seen as a key strategy to mitigate these environmental impacts. When using zero-carbon electricity, battery electric vehicles (BEV) become three to four times less carbon-intensive per kilometer driven than internal combustion engine vehicles (International Energy Agency, 2020). Lithium-ion batteries (LIBs) comprise many metals, which have environmentally intense mining and extraction processes (Olivetti et al., 2017; Xu et al., 2020; Betz et al., 2021; Porzio and Scown, 2021). In this regard, end-of-life (EoL) strategies, particularly recycling, become increasingly relevant due to their potential to reduce the environmental impacts compared to primary materials. A manifestation of the importance of recycling is the proposal for the new EU directive (European Commission, 2020).
The draft of the EU directive proposes a wide range of measures throughout all life cycle stages of a LIB to enhance the circular economy. The draft of the new EU directive sets, among other objectives, target values for the recovery rate, the number of secondary materials to be used in batteries on the European market, and the CO2 footprint. The regulations focus on different life cycle stages and will become effective in different steps throughout the next years (see Figure 1; European Commission, 2020). It will become mandatory to give the CO2 footprint for all traction LIBs sold on the European market by 2024. By 2026, performance class labels for the CO2 footprint will be implemented, followed by the 2027 maximum thresholds. The CO2 footprint includes all life cycle stages from raw material extraction and processing to recycling and disposal. For the production of batteries, a quote regarding the secondary input of some of the main materials (lithium, nickel, cobalt, and lead) in batteries will be set. In 2025, a declaration of the secondary material quote is necessary. By 2030, a mandatory secondary material quote is implemented which is increased in 2035. For the recycling of batteries, recovery rates for some of the main materials (lithium, nickel, cobalt, copper, and lead) will be given. First mandatory recovery rates will be implemented by 2025 and then be increased by 2030 (European Commission, 2020).
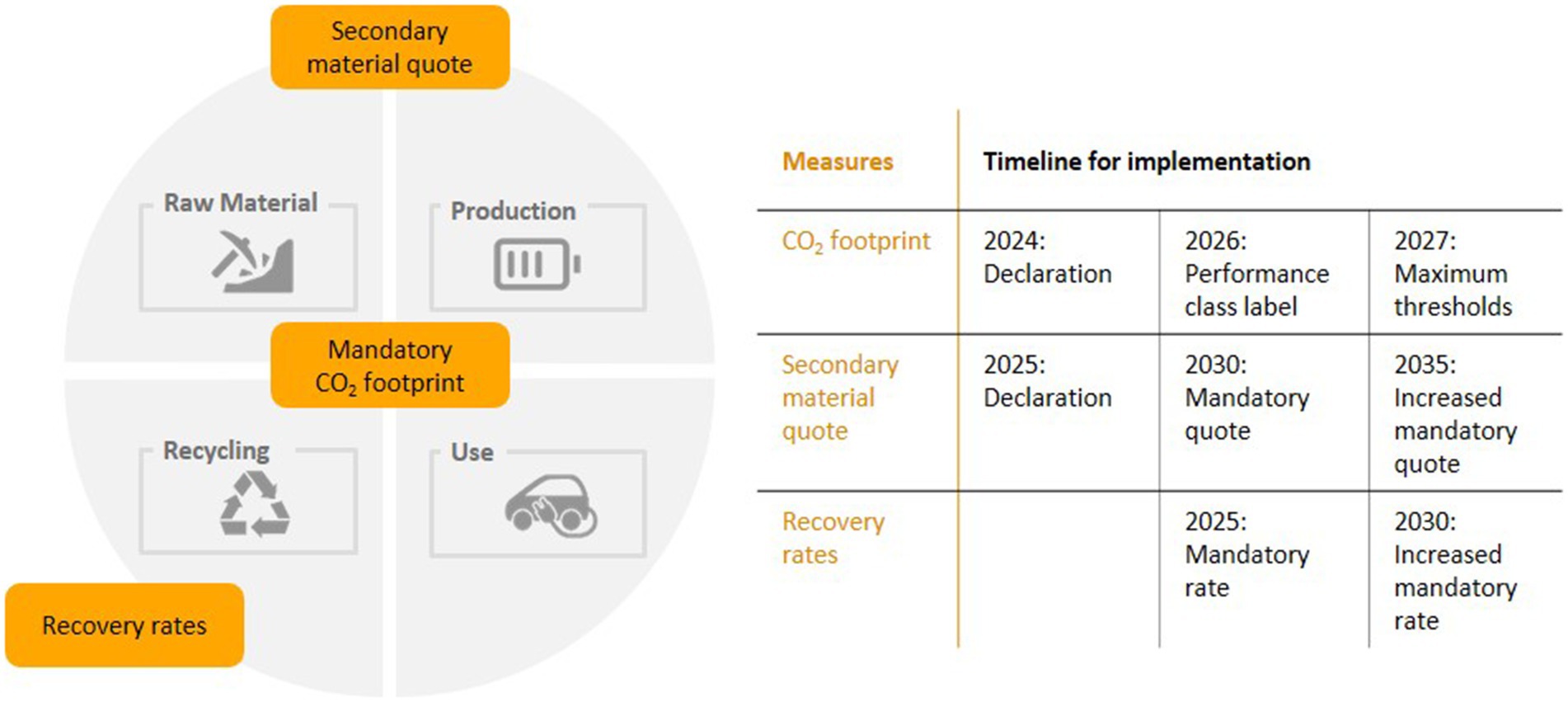
Figure 1. Measures of the EU Directive for traction LIBs related to the circularity strategies along the life cycle. On the left, the measures are linked to the life cycle stage they focus on. On the right, the timeline for the implementation of the measures is displayed. Based on European Commission (2020).
The draft of the new EU directive puts a focus on recycling to enhance the circularity of batteries. Figure 2 presents the environmental relevance of recycling scrap batteries. Understanding how circular supply chains and recycling affect the environment is essential to optimize them. The input to the recycling process (Figure 2A) is the EoL traction batteries. These contain a mix of battery materials that can be recovered in different qualities. The market of LIBs is characterized by being composed of different cell chemistries and geometries. The predominant cell types are expected to change throughout the years (International Energy Agency, 2020). The cell format as well as the module and pack design can differ (Harper et al., 2019). Without recycling, the scrap batteries would go into a non-material recovery EoL activity, i.e., landfill or incineration (Figure 2B). Recycling therefore decreases or avoids the impact coming from these EoL activities (Geyer et al., 2016).
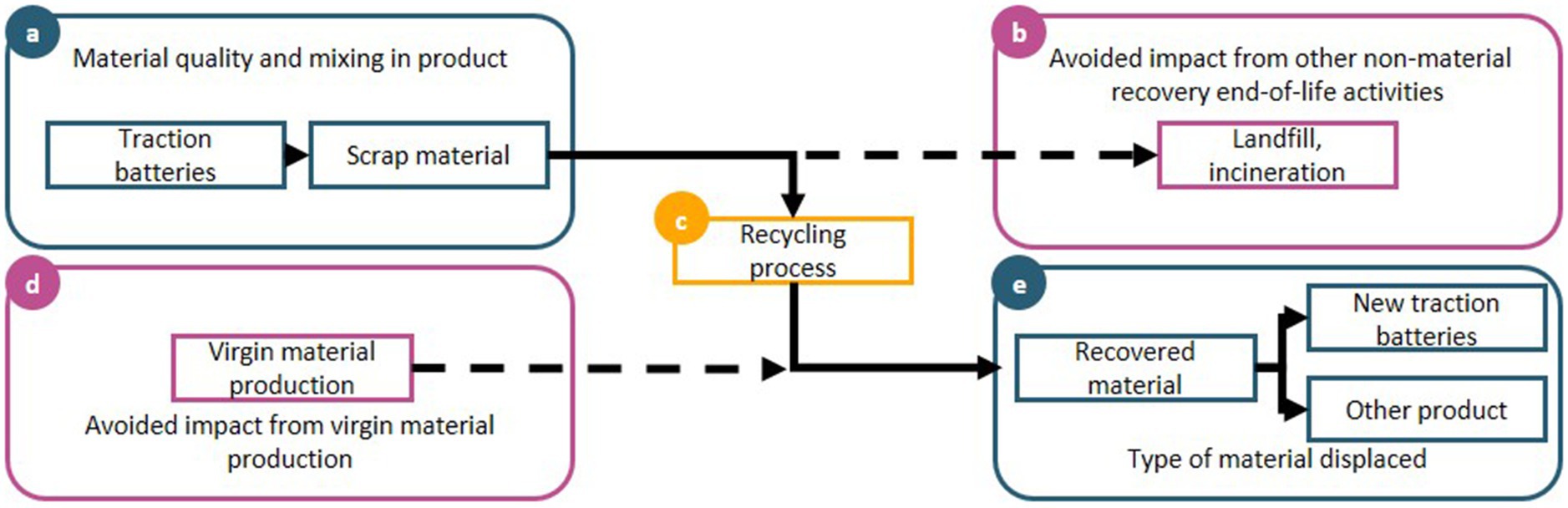
Figure 2. Environmental relevance of recycling of traction batteries based on Cerdas et al. (2018) and Geyer et al. (2016).
Various recycling processes (Figure 2C) exist that combine pyrometallurgical, hydrometallurgical, and mechanical treatment of batteries (Sommerville et al., 2021). The processes differ with regard to the kind of output materials and the qualities of the recovered materials. Further processing of the recoveries is needed to get battery-grade materials. This resulting variety leads to high complexity in the field of LIB recycling. This motivated the application of life cycle assessment (LCA) to evaluate different recycling routes and their impacts on the life cycle of the LIB (Gaines et al., 2010; Dunn et al., 2012, 2016; Ciez and Whitacre, 2019; Cusenza et al., 2019; Abdelbaky et al., 2021; Porzio and Scown, 2021).
The recovered materials allow the displacement of virgin material and therefore avoid the environmental impacts associated with primary material production (Figure 2D; Geyer et al., 2016). They can be used either in the production of new traction batteries or in other products, depending on their quality (Figure 2E). Especially for countries with no or limited access to their own battery-active material, such as Germany, recycling makes production less dependent on the international supply chains for the battery materials. This is especially beneficial, as many metals come with a geopolitical supply risk resulting from their geographic concentrations (Olivetti et al., 2017).
The environmental relevance of recycling LIBs can be quantified using LCA which is at the same time a valuable tool to support decision-making, e.g., within technology development. A key factor to this is the comparability and transparency of the studies and their results. The results are largely influenced by modeling choices—such as the allocation of environmental burdens in the multi-functional process. Recycling implies the existence of a second life cycle that shares the same materials. Therefore, the allocation of the impacts—especially of the recycling processes—between these product life cycles becomes necessary (ISO, 2006a,b). Allocation is defined as “partitioning the input or output flows of a process or a product system between the product system under study and one or more other product systems” (ISO, 2006a,b). The allocation procedures are defined as part of the scope of a study (ISO, 2006a,b). In general, it has to be differentiated between the multi-output allocation which is used to account for by-products and the EoL-allocation which is used to split impacts and benefits of processes between two or more product life cycles. In this study, the focus is on the EoL-allocation. Therefore, when referring to allocation procedures and formulas, we mean EoL-allocation.
Little attention has been given to the EoL modeling approaches in LCA studies of LIBs. Nordelöf et al. reviewed how the EoL stage is modeled in LCA studies of LIBs to investigate methodological consistency. They categorized the studies based on two archetypal modeling approaches: cutoff and avoided burden. The cutoff approach considers no material recovery but possibly secondary material input. Avoided burden does consider material recovery but only primary material inputs are assumed. In their study, a total of 25 studies were analyzed, 19 of them followed the avoided burden and six the cutoff approach. Approximately one-third of the studies deviated from the defined setups of the methods by including material recovery and secondary material input. These deviations mainly occur when applying avoided burden. As argued by the authors, the resulting hybrid approaches may have led to double counting of the recycling benefits and impacts and therefore under- or overestimating the potential environmental impacts. In this regard, one important finding of this study is that there is a general lack of methodological awareness and rigor in EoL modeling (Nordelöf et al., 2019), and therefore all modeling choices need to be well-documented and transparent.
Against this background, the influence of stakeholder perspectives on the choice of allocation procedures and therefore the environmental impacts of LIBs is analyzed. This study is structured as follows: Section 2 gives an overview and analysis of existing guidelines and frameworks for allocation. Based on several different criteria, three allocation procedures are selected, further analyzed, and adapted to complex product systems such as LIBs. In Section 3, the relevant stakeholders are identified, and LCA archetypes are developed based on the decision contexts and LCA questions of the stakeholders. The LCA archetypes include system boundary, functional unit, and allocation procedure. In the case study (Section 4), the defined archetypes are tested and applied to two exemplary battery systems. The results are presented and discussed with regard to the role of the LCA archetypes and the importance of the stakeholder perspective in the LCA and transparency in the modeling.
2. Eol allocation in LCA
2.1. Overview of existing guidelines and frameworks
The ISO 14040 standard states that the same allocation principles apply to multi-output allocation and recycling. Nevertheless, additional elaboration is required because of the differences in multi-output and EoL allocation. Recycling leads to materials and processes that are associated with more than one product system. Recycling may also influence the inherent properties of the materials in their subsequent life cycle. The norm, therefore, defined more specific allocation procedures for the EoL. It is differentiated between closed- and open-loop recycling. The closed-loop allocation applies to product systems where no changes occur in the inherent properties of the recycled material. Open-loop allocation is used for product systems where the material is recycled into another product system and potentially undergoes changes in its inherent properties.
The allocation procedures for shared unit processes are applied based on physical properties, economic value, or the number of subsequent uses of the recycled material (ISO, 2006a,b). The ISO standard only comprises general guidelines to be flexibly used in different contexts. Several more detailed and prescriptive methods and guidelines have been developed based on the ISO standards for different applications, sectors, and product groups (Allacker et al., 2017).
One such guideline is the product environmental footprint category rules (PEFCR) for high-specific energy rechargeable batteries for mobile applications (Siret et al., 2018). It gives guidance on how to conduct a PEF study to ensure they are derived, verified, and presented in a harmonized way. It also includes recommendations on allocation and the modeling of waste and recycled content. The authors propose the circular footprint formula (CFF) to model EoL products as well as recycled content (Siret et al., 2018). The CFF accounts for many aspects of the different materials in a product’s life cycle including its quality, recovery rates, and demand factors based on market conditions. Therefore, it requires specific information related to individual materials which is difficult to obtain in a complex product system such as batteries. One example is the factor for the balance between the demand and supply of individual recycled materials which is supposed to reflect market realities by giving different weights to the recycled content and the recovery rate (Ekvall et al. 2020). The PEFCR provides default values for these allocation factors, such as 0.5 for plastics and 0.2 for metals (Siret et al., 2018). These are not very detailed nor are they specific to any particular metal; therefore, it is questionable if they can reflect the demand for the battery materials which often have very fluctuating prices (U.S. Geological Survey, 2021). Additionally, the used datasets need to be compliant with the PEFCR to apply the CFF. Overall, this limits the applicability of the CFF significantly.
Ekvall et al. (2020) attempted to contribute to an international harmonization and standardization process in allocation procedures. They describe and assess different approaches to model recycling in LCA and similar environmental assessments without a specific field of application. Twelve methods are analyzed with several criteria. The main one is that a good method should create an incentive for solutions to reduce the overall environmental impact of product life cycles. This is accompanied by different sub-criteria. As a final step, they give recommendations on which allocation procedure should be used and in which context. Their recommendations are based on LCA purposes. It does not include specific allocation procedures to be used in the different contexts but is limited to describing (methodological) aspects to consider Ekvall et al., (2020).
Several frameworks have also been proposed that combine recommendations on the allocation procedure for multi-output and EoL allocation such as by Schrijvers et al. (2020) and Schrijvers et al. (2016). Based on the goal of a study, guidelines to use on the allocation procedure are provided. They describe cutoff as a specific form of partitioning as defined in ISO 14040 for multi-output allocation. This means 100% of the inventory is attributed to the life cycle under study and 0% to the co-function—the subsequent life cycle. In their opinion, it is the only appropriate allocation method for attributional LCA (ALCA) (Schrijvers et al., 2016). This contradicts other literature and guidelines (Allacker et al., 2017; Nordelöf et al., 2019; Ekvall et al., 2020).
In an updated framework, Schrijvers et al. (2016) present archetypes of goal and scope definitions to choose the appropriate allocation procedure. These archetypes represent the minimum amount of information required for this decision in the form of research questions (Schrijvers et al., 2020). They also develop an allocation procedure to be used for consequential LCA (CLCA)—the market price-based substitution which includes economic values (Schrijvers et al., 2016). The proposed formula is quite complex and not accompanied by clear documentation, which makes it difficult to use. Additionally, the required data are not readily available in the context of LIBs. This might lead to results that cannot be reproduced (Ekvall et al., 2020). The approach to combining both types of allocations leads to a framework that deviates significantly from what is described in other guidelines and from what is practiced in existing LCA studies.
2.2. Allocation procedures
Based on the following criteria, three allocation procedures were chosen:
• The formula shall have a life cycle scope, i.e., all life cycle stages are included, double counting is avoided, and the symmetry of material flows is ensured.
• The results shall be relevant to decision-makers. The allocation method is designed in a way that includes parameters that can be influenced by the decisions of the stakeholders, such as the recycled content and the recovery rate.
• The allocation procedures shall be easy to use in terms of having a low level of theoretical complexity.
• All data needed should be readily available from stakeholders or databases.
The criteria are adapted from the report of the Swedish Life Cycle Center (Ekvall et al., 2020). Applying these criteria to allocation methods described in the literature, guidelines, and publications, three methods are selected (Schrijvers et al., 2016; Allacker et al., 2017; Siret et al., 2018; Nordelöf et al., 2019; Ekvall et al., 2020): i) cutoff, ii) avoided burden, and iii) the 50/50 method. All formulas were adapted to be more reflective of a complex product system such as LIBs, in which different materials can come from primary or secondary sources and can be recycled or end up in waste treatment in the end (Table 1). Figure 3 shows the system boundaries for the three allocation methods. The extent to which the raw material extraction and processing, recycling, or waste treatment are included in the overall environmental score depends on the share of recycled content (R1) and/or the recovery rate (R2). The use phase is not considered in the formulas as it is not affected by the choice of allocation procedures.
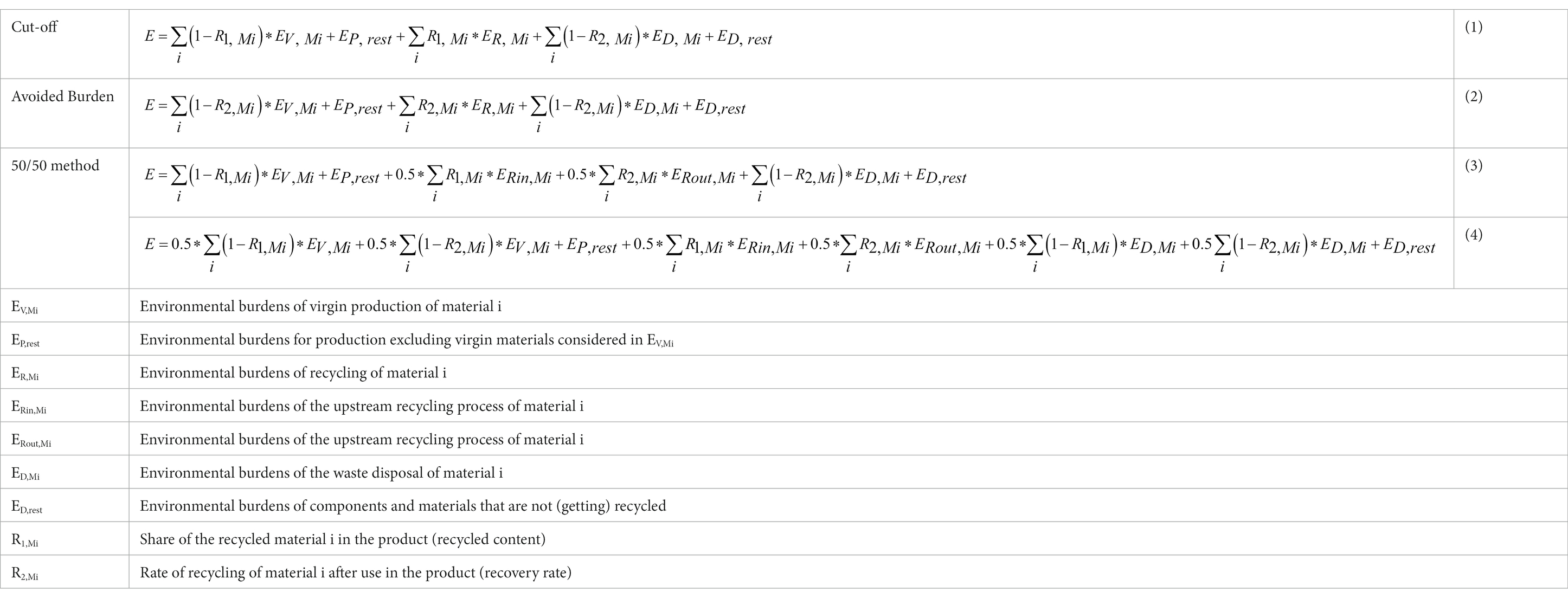
Table 1. The adapted formulas used for estimating the environmental impact based on the different allocation procedures.
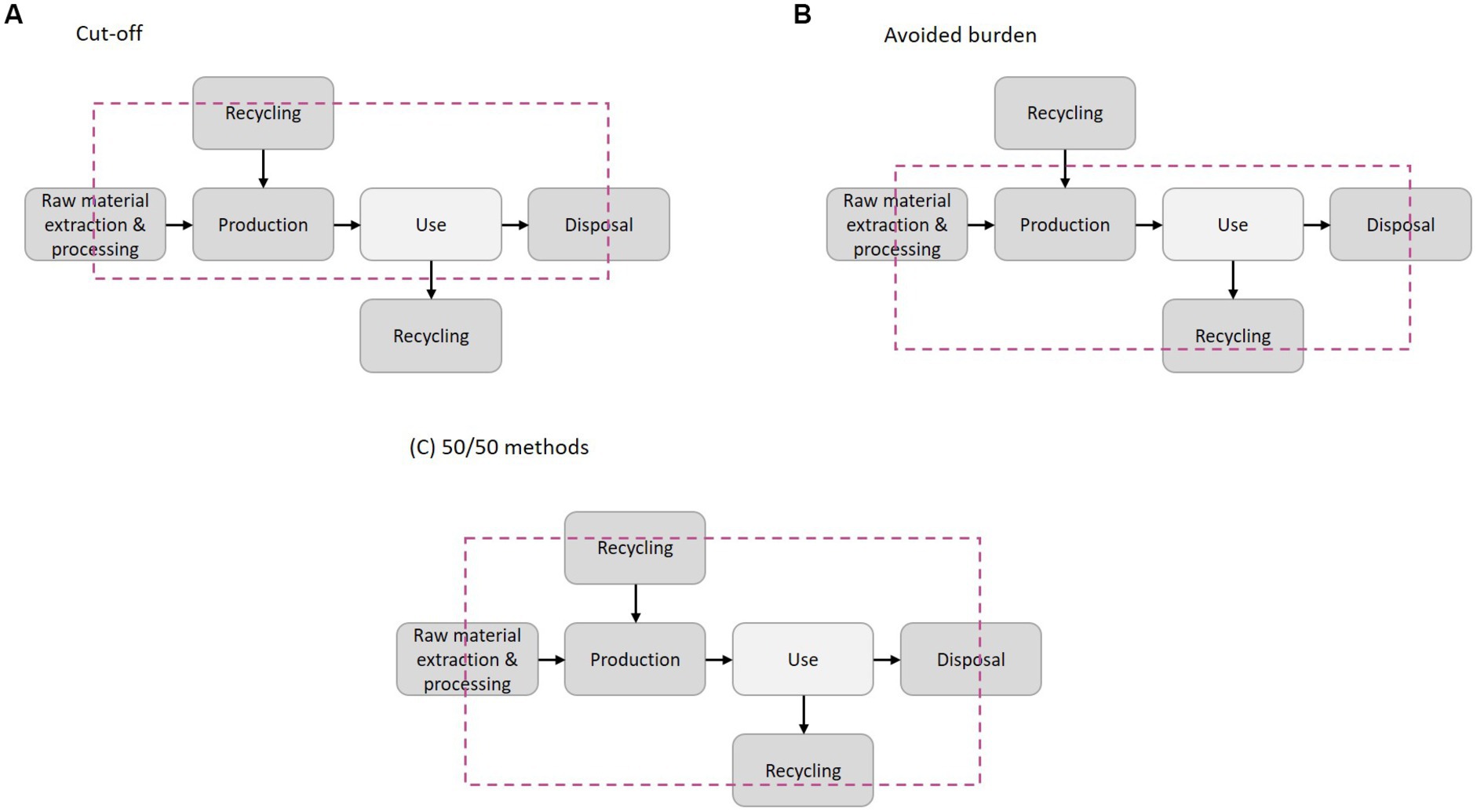
Figure 3. The system boundaries for the different allocation procedures (A) Cutoff, (B) Avoided burden, and (C) 50/50 method. The system boundaries show the extent of inclusion in the life cycle. The use phase is excluded from the system boundaries.
Cutoff is one of the two main archetypal allocation procedures used in the EoL modeling of LIBs. The system boundary (see Figure 3A) includes raw material extraction and processing for primary materials, production, recycling for the number of secondary materials used, and disposal of the materials that do not get recycled. The impacts of recycling are fully allocated to the product using the recycled material with no burdens from recycling operations attributed to the upstream product. The LCA includes no process beyond the product life cycle. Other names of this procedure are the recycled content approach or the 100:0 approach (Allacker et al., 2017; Nordelöf et al., 2019; Ekvall et al., 2020).
Avoided burden is the second main archetypal allocation procedure and is also known as allocation to material losses, 0:100 approach, closed-loop approximation, and end-of-life approach. Part of the system boundary is the extraction and processing of the raw materials that are not recycled after use, the production of the LIB, the recycling for the share of the recovery rate, as well as the waste treatment of everything that is not getting recycled (see Figure 3B). The environmental burdens of recycling are allocated upstream, while the benefits are attributed to the product that is getting recycled after use. There are also variations of the avoided burden procedure for an open-loop approach where the material might have lower quality and is used in a completely different context in the second life cycle. These interpretations fit more in the context of CLCA (Allacker et al., 2017; Nordelöf et al., 2019; Ekvall et al., 2020).
The 50/50 method is a hybrid approach for which different interpretations exist [see Formula (3) and (4)]. The environmental burdens of each recycling process are split between the product system supplying recyclable material and the product system where the recycled material is used. Some interpretations of the formula also split the environmental burdens of virgin material production and final disposal between the two product life cycles [Formula (4); see Figure 3C]. This method can also be interpreted as closed-loop, where the flow is defined as the average of the input and the output of recycled material across the boundary of the life cycle. In this sense, it is a compromise between avoided burden and allocation to virgin material use. It reflects the view that material use requires both virgin material production and final disposal. It is assumed that the supply and demand of recyclable materials are both necessary for recycling to take place (Allacker et al., 2017; Ekvall et al., 2020). In this study, we go with the first interpretation of the 50/50 method [Formula (3)].
In general, no credits are given but the impacts considered are reduced depending on the recycled content and the recovery rate. Cutoff and the 50/50 method only consider the impacts for virgin production depending on the recycled content assumed in the LIB. The primary production impacts are reduced by the amount of secondary material used. Avoided burden, in contrast to this, reduces the primary production impacts by the amount of material that is getting recycled after the use phase. In cutoff, avoided burden, and 50/50 methods, only the impact of waste treatment for materials that do not get recycled after use is considered. Cutoff considers the impact of recycling on the amount of recycled content in the battery pack. Avoided burden, in contrast to this, includes the impact of recycling on what gets recycled after use. The 50/50 method is a combination of both.
3. LCA archetypes of stakeholders based on their decision context
There is no clear definition of stakeholders in the literature. Many definitions are based on Freeman’s work on stakeholder theory which defines stakeholders as those who affect or are affected by an action or decision. The identification of relevant stakeholders can be done following different approaches—one of them being identified by experts or (other) stakeholders (Reed et al., 2009). The stakeholder definition in this publication is based on the work of the Circular Economy Directive Germany where relevant stakeholder groups in the battery life cycle are defined as suppliers and manufacturers, users, recyclers, service providers, and regulators (Acatech, Circular Economy Initiative Deutschland, & SYSTEMIQ, 2020). From this list, only stakeholders who fulfill the following criteria are considered:
• The stakeholder needs to have an influence on or active role in the whole life cycle or parts of the life cycle that are relevant for the EoL allocation and/or
• The measures of the EU battery directive related to the circular economy as presented in Figure 1 affect the stakeholder.
This leaves us with three stakeholders: regulators, battery manufacturers, and recyclers. For these stakeholders, we analyzed their interests and decision contexts from an environmental perspective, which lead to different motivations for performing this LCA and therefore LCA questions. These different questions are reflected in the system boundaries, functional units, and allocation methods. In this study, we call these an LCA archetype. In the analysis of the LCA questions, the focus lies on aspects that cover the whole life cycle of a LIB and not only gate-to-gate life cycle stages.
The regulator considers the whole life cycle and has no specific focus on one life cycle stage. With the Paris Climate Agreement and its goals, to prevent and limit climate change by reducing emissions drastically, different directives and legislations were established to achieve these. One of them is the already mentioned proposal for the new EU Directive for batteries. LCAs can be a powerful tool to assess the effectiveness of directives for reaching the Paris Climate Targets by quantifying the impact of target numbers. An LCA cannot only be used as an evaluation but also as a decision-making tool. It can help to evaluate what the target values in new directives should be or which (research) topics should be supported with public funding. The LCA is also a helpful way to implement Carbon Footprint declarations.
For the regulators, two LCA questions were identified based on their role in legislation such as the draft of the new EU directive:
• What is the environmental footprint of the products on the market?
• What effects do the target values of directives such as the EU battery directive have on the footprint of the product?
These questions lead to the same LCA archetype. To answer them, the system boundary needs to include all life cycle stages from raw material extraction and upstream recycling to waste disposal and recycling at EoL. Therefore, a battery system with potentially secondary material and recycling at EoL is analyzed as the functional unit. To be reflective of the secondary material used and the recovery rate at EoL, the 50/50 method is the most appropriate approach for the allocation.
The focus of the battery manufacturer is on the production as the life cycle stage they perform themselves. Nevertheless, they have different interests along the other life cycle stages. With the upcoming performance classes and thresholds for the CO2 footprint, one of the best achievable impacts of their product is to show that they meet self- or policy-set targets. Being transparent about the environmental impacts will become more and more important in the future—either because of arising interest and awareness in society or because the Carbon Footprint Declaration will become mandatory soon (European Commission, 2020). The LCA can also be used to evaluate different sustainability strategies: the battery manufacturer could have their focus on using secondary materials or on design for recycling. They could aim for closed- or open-loop-recycling or they could use battery chemistries that are more sustainable than LIBs. With regard to the EU Battery directive, the battery manufacturer is directly affected by several of the mentioned regulations—the CO2 footprint for batteries, the quotes for the recycled content used in their batteries, and because of the extended producer responsibility, they are also affected by the collection and recovery rates.
For the battery manufacturer, five LCA questions were identified:
• Is the product system within the given target values for the environmental footprint?
• Which sustainability strategy is more beneficial for my company?
• Which recycling technology is more beneficial for my company?
• How does the product impact change when the amount of secondary material (R1) is increased by x%?
• How does the product impact change when the recovery rate (R2) is increased by x%?
These result in quite different LCA archetypes. For the first question, it is the same as the regulators’ LCA questions. The system boundary should include all life cycle stages from raw material extraction and supply of secondary material with upstream recycling until the recycling and disposal at EoL. Again, the 50/50 method is appropriate to reflect all changes within this system boundary. The second and third questions lead to the same LCA archetype since for the question of which recycling technology is more beneficial, in the context of a whole LIB life cycle also, the sustainability strategy of the battery manufacturer is important. For these two questions, a comparative LCA with different system boundaries and battery systems is necessary to reflect the possible sustainability strategies to either focus on secondary material input or the recovery rate or on both. The first system boundary for the focus on secondary material includes the whole life cycle with raw material extraction and upstream recycling until the disposal at EoL. This system is best reflected with the cutoff as an allocation method. The second system boundary for the focus on the recovery rate covers all life cycle stages from the raw material extraction until the disposal and recycling at EoL. The appropriate allocation approach for this is the avoided burden approach. The third system boundary and allocation method are the same as described for the first LCA question of the battery manufacturer. The fourth LCA question lays focus on the secondary material input. Therefore, the system boundary includes all life cycle stages except the recycling at EoL and the cutoff approach fits best as the allocation method. For the fifth and last LCA question of the battery manufacturer, it is the opposite. The focus lies on the recovery rate which is why the upstream recycling is not included in the system boundary and the avoided burden approach is used as an allocation method.
The role of the recycler is to recover materials from the EoL batteries. With the upcoming thresholds for the CO2 footprint, the recycler might need to show to the battery manufacturers that their recycling technology has lower environmental impacts than others on the market and is in line with the requirements on recovered materials and recovery rates. Recycling technologies can have quite different focuses. The goal can be closed-loop recycling, so only recovering materials in battery grade or open-loop recycling. Looking at the draft of the new EU directive and its regulations, it is quite obvious that recycling companies are affected by the target values for recycling efficiencies and material recovery rates. They need to make sure that their process complies with these measures.
For the recycler, only one LCA question with a whole life cycle focus was identified: Is my recycling technology beneficial compared to others? This question also depends on the sustainability strategy of the battery manufacturer. Therefore, the same comparative LCA archetype as for the second and third questions of the battery manufacturer is suggested.
Based on the analysis of the interest and the decision context of the three stakeholders, some main links between them were identified in the context of circular economy targets as given by the new EU Directive for batteries. The regulators design and control the target values, which the battery manufacturers have to follow. Consequently, they need to prove their alignment with the target values. To achieve these, they choose recyclers, which technologies align with the targets as well. Throughout the stakeholders, eight LCA questions were identified. Because of the links between the stakeholders, some of the questions are identical: The regulators and the battery manufacturer both want to quantify the footprint of a product, and the recycler and the battery manufacturer both want to evaluate if a recycling technology is beneficial. Additionally, the LCA archetypes regarding the system boundary, the functional unit, and the allocation method are the same for some LCA questions. Differences will appear in the design of the rest of the goal and scope definition in the respective LCA. For example, question one of the regulators and the battery manufacturer investigate one or several products while question two of the regulators build up on this by including different scenarios which reflect a variation of the target values in regulations. In this way, the effects on different product systems can be compared. While the focus of the third question of the battery manufacturer is on the assessment of the sustainability strategies, the fourth question extends the assessment by including different possible recycling technologies. The fifth and sixth questions of the battery manufacturer look more in detail at one aspect of the comparative LCAs described in the third and fourth questions. How these LCA questions overlap and influence each other will be further highlighted in the case study in the next section.
4. Case study
In this section, we will do a case study to test the defined LCA archetypes and to identify their relevance for the interpretation of LCA studies and the decision-making based on their results. The following six LCA questions and their described archetypes will be included:
1. What is the environmental footprint of the products on the market?
2. What effects do the target values of directives have on the footprint of the product?
3. Which sustainability strategy is more beneficial?
4. Which recycling technology is more beneficial?
5. How does the product impact change when the amount of secondary material (R1) is increased by x%?
6. How does the product impact change when the recovery rate (R2) is increased by x%?
In general, the production and the use phase are excluded in this case study. We exclude the use phase since it is not the focus of the allocation approaches. The production phase is excluded because the calculated environmental impacts are not influenced by the allocation approach chosen. Building upon the LCA archetype, additional aspects will be included in the LCAs. For question one, two different recycling routes with different recovered materials will be modeled to display the different product systems. For the amount of secondary material and the recovery rate, Scenario 1 (Table 2) is used. For question two, the assessment of question one is extended with different scenarios for the recycled content and the recovery rate. Therefore, Scenarios 1 to 3 (Table 2) will be included.
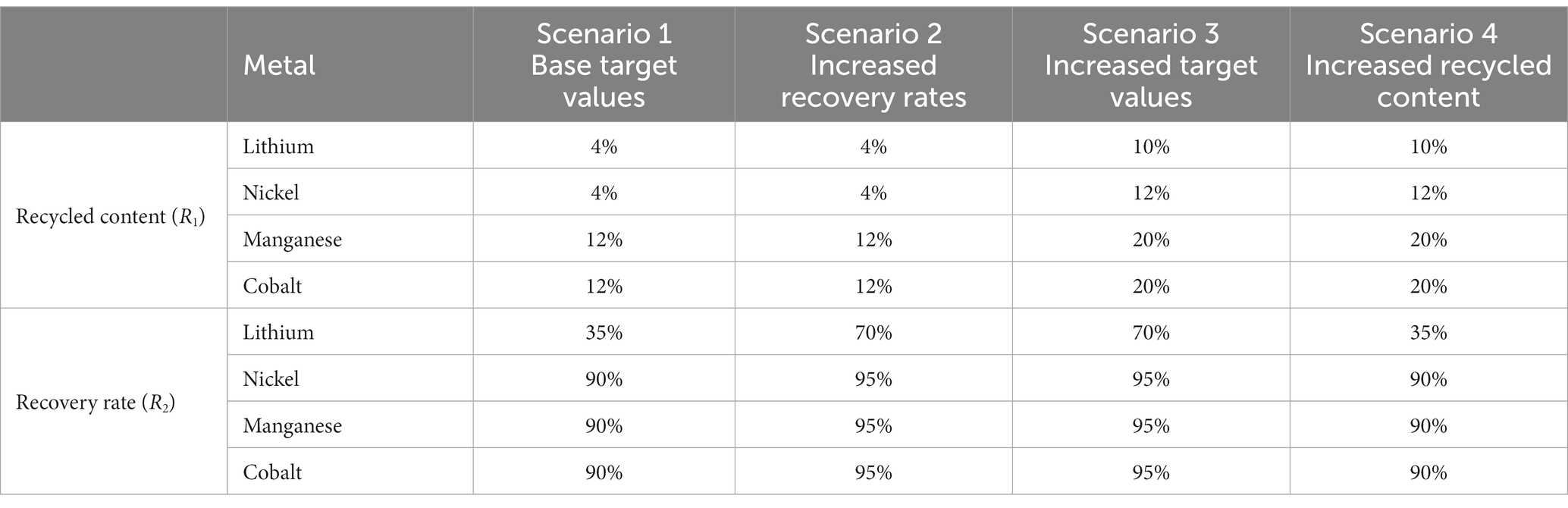
Table 2. The different scenarios considered in the study based on the proposal for the new EU Directive. For manganese, which is not addressed in the Directive, the same values as for Cobalt are assumed.
For the third question, which sustainability strategy is more beneficial, additional scenarios for the recycled content, and the recycling quote were defined. These are matched with different system boundaries. For the system boundary with upstream recycling, Scenario 4 (Table 2) is evaluated which gives the highest recycled content described in the draft of the new EU directive while the recovery rate remains at the lowest level given by the draft of the new EU directive. For the system boundary with downstream recycling, Scenario 2 (Table 2) is chosen which follows the opposite logic of Scenario 4. For the system boundary, which includes upstream and downstream recycling, Scenario 3 (Table 2) is chosen which provides the highest target values for recycled content and recovery rate. For the fourth question, these assessments are extended by comparing two different recycling routes throughout all scenarios and system boundaries.
For question five, the recycled content gets varied while the recovery rate remains the same in the assessment. Therefore, Scenarios 1 and 4 are compared. For question six, only the recovery rate changes, and the recycled content stays the same. Hence, Scenarios 1 and 2 are compared.
4.1. Impact assessment method and life cycle inventory modeling
The life cycle impact assessment was done using the ReCiPe 2016 default characterization models at the midpoint level with the Hierarchist perspective used (Huijbregts et al., 2016) because of its global applicability and environmental relevance (e.g., relevant damages are considered) (Mikosch et al., 2022). Three impact categories are chosen based on the recommendation of the PEFCR and their relevance for the stakeholders in the automotive sector: Global Warming Potential (GWP), Fossil Fuel Potential (FFP), and Metal Depletion Potential (MDP) (Siret et al., 2018; Mikosch et al., 2022).
The modeling is done using the activity browser and the ecoinvent 3.7.1 cutoff database is used for the selection of foreground and background datasets (Wernet et al., 2016; Steubing et al., 2020). The foreground system is primarily based on information available in the literature. The geographic scope of the activities modeled in the foreground and background systems are non-EU, mostly assuming production and recycling to be performed in China. If specific datasets are not found, the Rest of the World and Global data sets are used accordingly. The SI contains detailed information on the used LCI as well as the calculated LCIA.
The battery pack modeled in this study is 23.5 kWh and of NMC 622 battery chemistry. The cells have a specific energy of 0.168 kWh and the mass of each cell is 0.695 kg. The battery pack has 10 modules and each of these modules has 14 cells. The total mass of the cells is 97.24 kg and the overall mass of the battery pack is 136.96 kg (Dai et al., 2019a). The information related to the raw materials used in active material production is based on Majeau-Bettez et al. (2011). The information related to the inactive and other materials of the battery pack (such as electronics, casing, and battery management systems) is based on information available in the literature (Ellingsen et al., 2014; Dunn et al., 2016; Cerdas et al., 2018; Kelly et al., 2019; Schmidt et al., 2019; Dai et al., 2019b; Mohr et al., 2020).
The recycling routes start with a manual disassembly and dismantling step. Therefore, no environmental burdens are associated with this step. After the disassembly and dismantling, the spent batteries either go to the pyrometallurgy- or hydrometallurgy-based recycling route. The material and energy consumption of both these routes is based on the process chain provided by Dai et al. (2019a). The fractions of the battery pack that do not get recycled, get either incinerated or landfilled. The share of used batteries ending up in either is assumed to be 50%.
The first recycling route considered is the pyrometallurgy route. The spent batteries are sent to a smelter, where the plastic and electrolyte fractions are burned off to provide heat. The gasses generated in the smelter are treated in the off-gas treatment to remove any toxic substances. The carbon in the graphite and the aluminum are oxidized and act as a reductant in the smelter. After the smelting process, the cobalt, nickel, copper, and iron end up in the matte, while the rest of the components, including lithium, end up as slag. The matte is then further processed by acid leaching and solvent extraction followed by a precipitation step to recover the required metal compounds. The water generated in the above-mentioned process steps is sent to a wastewater treatment facility (Dai et al., 2019a).
The second recycling route is hydrometallurgical. The spent batteries are shredded followed by a low-temperature calcination process to remove the binder and electrolyte. The gases generated in this step are treated to remove any toxic substances and prevent their release into the atmosphere. The further steps involve several physical and chemical separation processes. The physical separation processes are used to recover the aluminum, copper, steel, and plastic components. The chemical processes such as leaching, solvent extraction, and precipitation are used to recover the cobalt, nickel, and manganese compounds. The water generated in the abovementioned process is sent to a wastewater treatment facility (Dai et al., 2019a).
The hydrometallurgical route recovers graphite, lithium, cobalt, nickel, manganese, copper, steel, aluminum, plastics, electrolyte salts, and solvents with different recycling efficiencies. The pyrometallurgical route recovers only cobalt, nickel, copper, and steel (Dai et al., 2019a). This alone would not meet the future standards of the draft of the new EU directive since Lithium is not getting recovered (European Commission, 2020). Nevertheless, it is included in this case study to have a comparison of different recycling technologies.
In the upgradation, the metal ions recovered in the recycling routes are converted to metal sulfates. The material requirements needed for the conversion processes are based on stoichiometric values and assume complete conversion. These conversion processes require water and sulfuric acid.
5. Results
In the following section, the results for each of the LCA questions described in the case studies in section 4 will be described. Figures 4–6 present the results of the case study. Figure 4 shows the GWP results for all six LCA questions, Figure 5 the FFP results, and Figure 6 the MDP results.
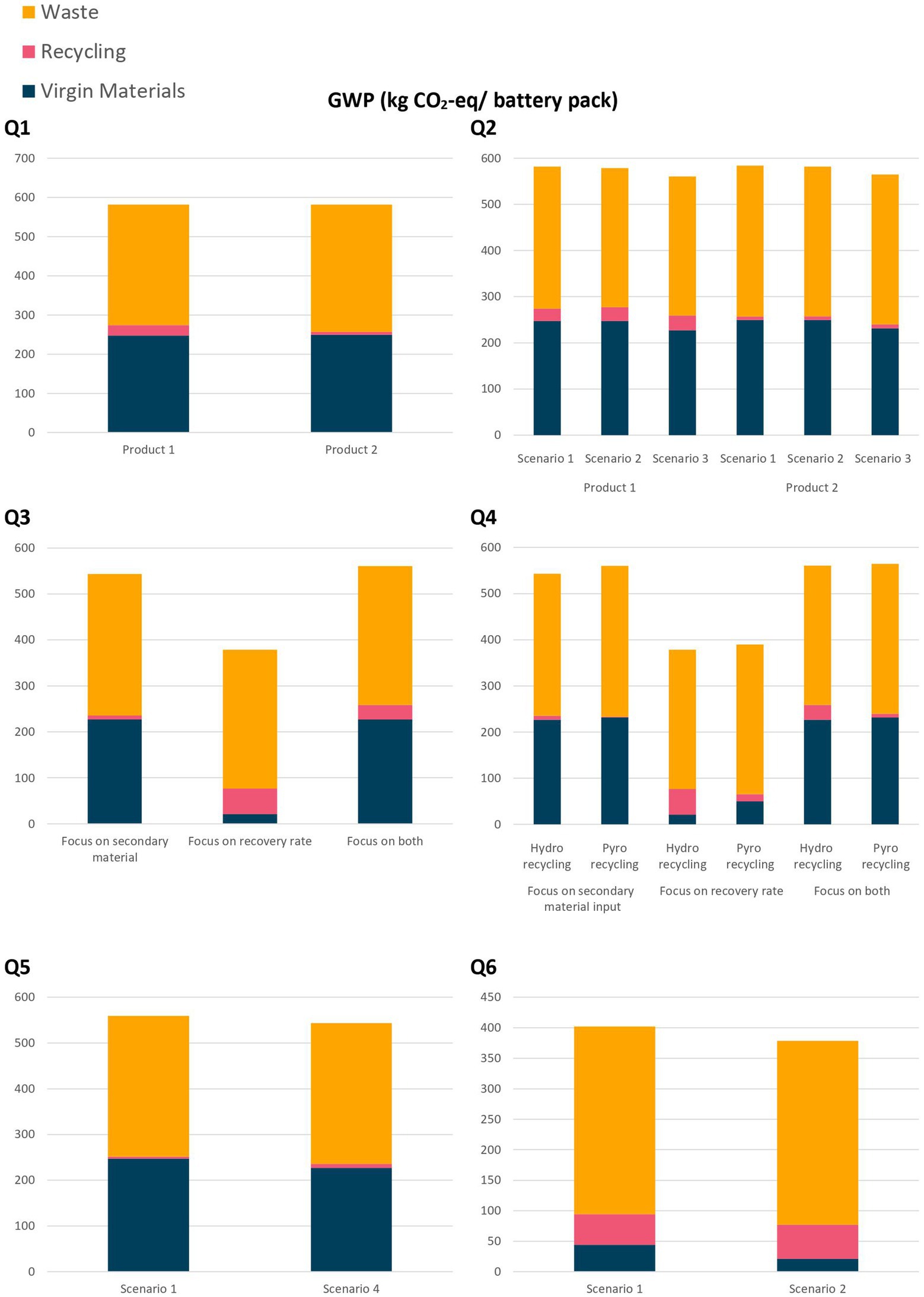
Figure 4. LCA results for GWP through all studied questions. The raw material extraction and processing are shown in blue, the recycling in pink, and the waste treatment in orange.
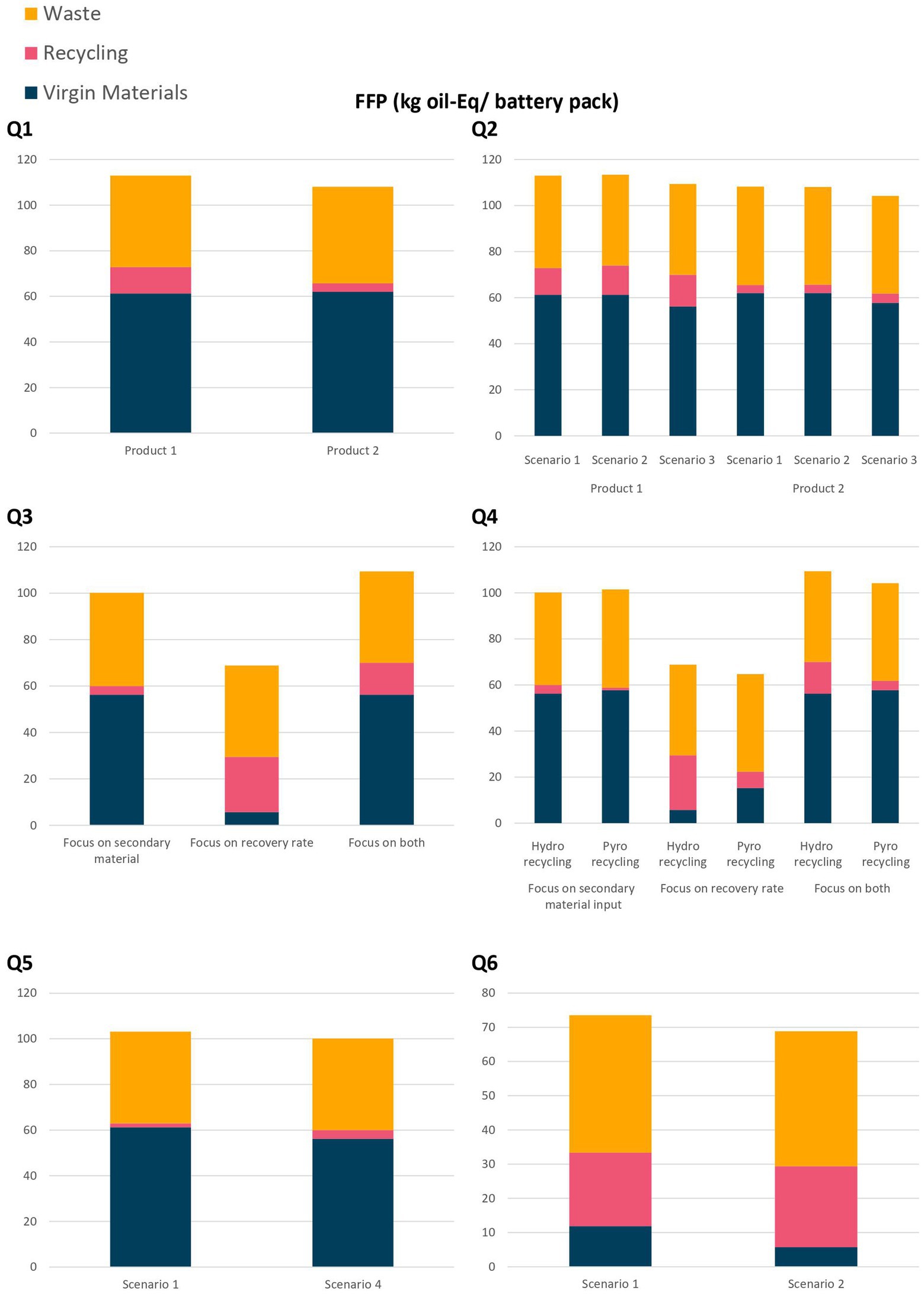
Figure 5. LCA results for FFP through all studied questions. The raw material extraction and processing are shown in blue, the recycling in pink, and the waste treatment in orange.
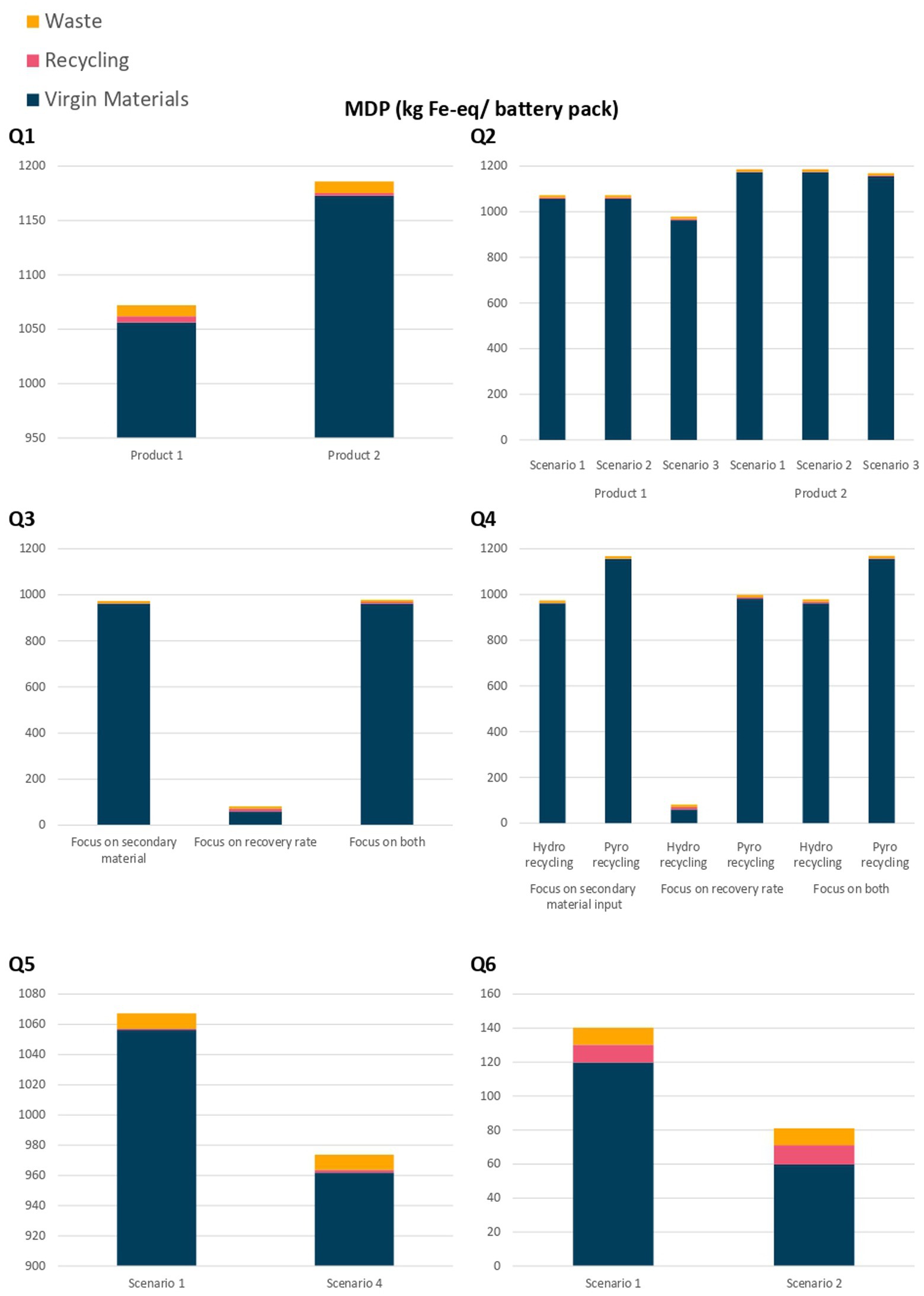
Figure 6. LCA results for MDP through all studied questions. The raw material extraction and processing are shown in blue, the recycling in pink, and the waste treatment in orange.
5.1. Q1: What is the environmental footprint of the products on the market?
For the first LCA question, we assumed that the two compared product systems are identical except for the recycling technology used. For GWP and FFP, the product system with the pyrometallurgical recycling route has lower environmental impacts. For MDP, the product system with the hydrometallurgical route has lower environmental impacts. The virgin material extraction and processing is the highest contributor to the environmental impacts for FFP and MDP. For MDP, the impacts from recycling and waste treatment only hold a very small share compared to virgin materials.
5.2. Q2: What effects do the target values of directives have on the footprint of the product?
As described in Section 4, the second LCA question extends the assessment in the first question by including variations of the recycled content and the recovery rate for both product systems. With an increase in the recovery rate (from scenario 1 to scenario 2), the impacts for the virgin material extraction and processing stay the same since the impacts from the raw materials stage depend solely on the recycled content in the 50/50 method. The recycling impacts increase with the recovery rate since more material is recycled. Consequently, the impacts of the waste treatment decrease since less material goes to waste. Overall, the impacts increase slightly in FFP and MDP with an increased recovery rate while they decrease for GWP. When more recycled content is used in the battery (from scenario 2 to scenario 3), the impacts for the raw material stage decrease. At the same time, the recycling impacts increase since more material is recycled upstream. The waste impacts do not change, since the downstream recovery rate is not varied. From scenario 1 to scenario 3, the recycled content and the recovery rate increase. As a consequence, the impacts of the extraction and processing of virgin materials decrease while the recycling impacts for upstream and downstream increase. The waste impacts decrease. Overall, the GWP, the FFP, and the MDP for both product systems decrease.
5.3. Q3: Which sustainability strategy is more beneficial?
This LCA questions deals with the topic of sustainability strategies: within the requirements of the legislation such as the draft of the new EU Directive and availability on the market—is it more beneficial for a company to focus on the use of secondary material or the recycling at the EoL. Therefore, a comparative LCA of different product systems with matching system boundaries and allocation methods was performed where each product system is reflective of another sustainability strategy. For all impact categories, the lowest impacts are calculated with a focus on recycling and the avoided burden approach. Especially, for MDP, the impacts are significantly lower than for the other two sustainability strategies. A focus on recycled content and recovery rate and therefore the 50/50 method as an allocation procedure leads to the highest impacts in all three impact categories. The benefit of the focus on recycling instead of secondary material depends on the ratio between the recycled content and the recovery rate. The draft of the new EU directive suggests a recovery rate higher than the amount of recycled content. The closer these values are together, the smaller the gap becomes between the results for cutoff and avoided burden assuming that the recycling impacts upstream and downstream are the same.
5.4. Q4: Which recycling technology is more beneficial?
The question of which recycling technology is more beneficial is an extension of the comparative LCA in question 3: Two different recycling technologies are assessed in a comparative LCA with the three different allocation procedures and their respective system boundaries. It differs whether the recycling technology or the sustainability strategy under assessment has a more significant influence on the results. For GWP, the sustainability strategy is the significant influencing factor. For FFP and MDP, it is the recycling technology. Avoided burden gives consistently among the lowest values for both recycling technologies. The focus on recycling at EoL seems to be the most beneficial sustainability strategy again for both recycling routes. Focusing on secondary material inputs and recycling often has the highest impact. Which recycling route is more beneficial depends not only on the sustainability strategy but also on the impact category. A general answer to this question is therefore difficult to find. It should be noted again that the pyrometallurgical route would not meet the requirements of the new EU battery directive since lithium is not recovered. The results for two recycling technologies in line with the directive might give clearer results.
5.5. Q5: How does the product impact change when the amount of secondary material is increased by x%?
To answer the fifth LCA question, an increase in the secondary material amount for one recycling route using the cutoff approach is evaluated. For all impact categories analyzed, the impacts for virgin material production decrease while the recycling impacts increase since more primary material is replaced by secondary material. As a consequence, more upstream recycling is included. Overall, the impacts for all impact categories decrease.
5.6. Q6: How does the product impact change when the recovery rate is increased by x%?
For the sixth LCA question, an increase in the recovery rate for one recycling route using the avoided burden approach is assessed. For all impact categories, the impacts for virgin material production decrease while the recycling impacts increase, since more material is recycled downstream. Overall, the impacts decrease in all impact categories.
6. Discussion
This study aimed to assess the influence of stakeholder perspectives on the environmental impacts of LIBs. We focus the discussion on the implications of the results for future implementation, documentation, and standardization of LCA. Stakeholder LCA archetypes, which address the typical LCA questions with appropriate system boundaries, allocation procedures, and scenarios were defined. The first question to evaluate is whether the LCA archetypes worked in the case study to answer the respective questions. In general, the results for the case study show a variation based on the specific scenarios designed which provide the answer to the question. In the six questions of the case study, the same two product systems are evaluated considering different points of view and therefore system boundaries. The difference in the product systems is solely in the recycling technology. Other technological as well as spatial or temporal variabilities are not considered. From all these questions, the results for GWP, FFP, and MDP vary significantly. This highlights why the specific goal and scope of an LCA have a significant influence on the results. Within the same LCA question, the variation overall is rather small. The compared scenarios in questions 3 and 4 show a higher variance than those of the other questions. This can be explained by the fact that in questions 3 and 4, different system boundaries and allocation methods are integrated into the assessment. Nevertheless, a variation can be seen every time. Choosing system boundaries that do not match the focus of your goal and scope would lead to results that are unable to provide the answers searched for. The results of the case study also highlight that burden shifting is a topic to be addressed. The contribution analysis shows shifts in the impacts of the life cycle stages which the overall results do not reflect in the same magnitude of order since they compensate each other partially. Additionally, the results also highlight that different impact categories should be considered to avoid burden shifting in this area.
Looking at the results of the case study, avoided burden mostly leads to the lowest environmental impacts for the product system. This is because the recovery rates demanded by the EU battery directive are higher than the share of secondary material. If this ratio would change, cutoff could be favorable in terms of the lowest environmental impacts allocated to the product system. The estimation of the recovery rates and the secondary material share is essential for the allocation procedures and brings potential uncertainty to the results. The results of questions 5 and 6 quantify the influence of changing the secondary material share or the recycling rate. In both cases, the influence on the results is less than 6%. However, we used the target values of the new EU Directive for our calculations, which limits the uncertainty since these are the minimum requirements to fulfill. Because these are already quite ambitious, it is unlikely that they will be exceeded significantly in the coming years (RECHARGE, 2021; Hoarau and Lorang, 2022). Additionally, a shift in the ratio between recycling rates and secondary material shares is very unlikely in the future since the supply of secondary material is unable to fulfill the demand in the production for most of the battery-active materials (Neidhardt et al., 2022). From a technological perspective, the use of avoided burden might be questionable. To calculate the life cycle impacts of this allocation approach, it is necessary to consider the recycling at the EoL of the battery. Since batteries have a lifetime of at least several years, it is difficult to foresee how they will be recycled at that time. Especially right now, where recycling is still a highly researched field. More effective and efficient recycling technologies would influence the allocated life cycle impacts. The cutoff method on the other hand is quite easy to implement since only upstream recycling is considered. Therefore, this information can be tracked along the value chain of the OEM.
Solely looking at the results of the case study, the 50/50 method is not attractive to be implemented since the allocated impacts are often quite high. Additionally, the 50/50 method faces the same challenges considering recycling at the EoL which were identified for the avoided burden approach. Nevertheless, the 50/50 method is quite attractive for a standardized approach from a methodological perspective since it is the only approach whose system boundaries capture the effects of secondary material share and the recovery rate. Therefore, it is linked to the most holistic sustainability strategy and also the only approach that captures all target values of the new EU Battery directive in its system boundary. Assuming the LCA approach, in general, and EoL allocation, in particular, will be standardized in future, the 50/50 method would be the best choice of the three commonly used allocation approaches, which is presented in the study since its system boundary is the broadest and matches, therefore, the different sustainability strategies.
7. Conclusion
The life cycle of a LIB was analyzed and three main stakeholders with a focus on circularity were identified: regulators, battery manufacturers, and recyclers. It was discussed what their main interests are and how they are affected by regulations such as the draft of the new EU directive. A very relevant part is giving the environmental footprint of products and processes.
In the context of a circular economy, the LCA of a LIB life cycle becomes especially challenging with regard to the allocation of impacts from the recycling phase. The state of the art on existing guidelines does not provide widely accepted standards for the field of batteries. Based on a couple of criteria, three allocation procedures were chosen and adapted to be reflective of complex products such as LIBs with different secondary material quotes and recovery rates for different materials.
Based on the stakeholder analysis and their identified interests, possible stakeholder questions for the LCA were defined. For each LCA question, the goal and scope were designed. This includes the functional unit, the system boundary, and a matching allocation procedure. These archetypes are applied and tested in a case study. The results highlight a couple of things: first of all, the archetypes achieve to answer the respective LCA questions. Second, the results show the significance of the influence of the system boundary and allocation approach.
The avoided burden approach often leads to the lowest environmental impacts. However, the application of avoided burden comes with the challenge of the big time delay between production and recycling. Therefore, it is difficult to estimate the recycling impacts of a battery at the moment it enters the market. The cutoff approach is very easy to implement. Since only upstream recycling is included in the system boundary, all data can be tracked along the value chain before the battery enters the market. The 50/50 method has the broadest system boundary. This is an advantage since it can display the effects of all sustainability strategies and target values of the EU battery directive.
In summary, the study highlighted the relevance of considering LCA archetypes in the assessment of LIBs for the proper interpretation of results and decision-making support based on two product system life cycles. This is also supported by the findings of a similar study focusing solely on the influence of EoL allocation without the stakeholder perspective (Du et al., 2022). Future work should apply the LCA archetypes to other product system life cycles to underline their significance further. Transparent documentation of the archetypes is important as long as there are no widely accepted guidelines for the LCA of LIBs with a special focus on the EoL allocation. The archetypes could also be extended with more methodological aspects. This study focused on system boundaries, functional units, and EoL allocation. However, there are more methodological aspects to consider—for example, the multi-output allocation, which is a significant topic when it comes to recycling processes. With the implementation of the measures of the EU battery directive, a standardized LCA approach becomes even more significant for comparable results in the CO2 footprint of all batteries on the European market.
Data availability statement
The original contributions presented in the study are included in the article/Supplementary material, further inquiries can be directed to the corresponding author.
Author contributions
JH and FC contributed to the conceptualization of the article. A-RA curated and organized the data. JH wrote the first draft of the manuscript and A-RA wrote sections of the manuscript. JH did the visualization. FC and CH supervised the work. All authors contributed to the article and approved the submitted version.
Funding
The project on which this publication is based was funded by the German Federal Ministry of Education and Research within the Competence Cluster Recycling & Green Battery (greenBatt) under the grant number 03XP0331A. The authors are responsible for the contents of this publication.
Conflict of interest
The authors declare that the research was conducted in the absence of any commercial or financial relationships that could be construed as a potential conflict of interest.
Publisher’s note
All claims expressed in this article are solely those of the authors and do not necessarily represent those of their affiliated organizations, or those of the publisher, the editors and the reviewers. Any product that may be evaluated in this article, or claim that may be made by its manufacturer, is not guaranteed or endorsed by the publisher.
Supplementary material
The Supplementary material for this article can be found online at: https://www.frontiersin.org/articles/10.3389/frsus.2023.1163207/full#supplementary-material
References
Abdelbaky, M., Schwich, L., Crenna, E., Peeters, J. R., Hischier, R., Friedrich, B., et al. (2021). Comparing the environmental performance of industrial recycling routes for lithium nickel-cobalt-manganese oxide 111 vehicle batteries. Procedia CIRP, 98 (The 28th CIRP conference on Life Cycle Engineering, March 10–12, 2021, Jaipur, India).
Acatech, Circular Economy Initiative Deutschland, & SYSTEMIQ. (2020). Resource-efficient battery life cycles. 1–126. Available at: https://www.circular-economy-initiative.de/publikationen
Allacker, K., Mathieux, F., Pennington, D., and Pant, R. (2017). The search for an appropriate end-of-life formula for the purpose of the European Commission environmental footprint initiative. Int. J. Life Cycle Assess. 22, 1441–1458. doi: 10.1007/s11367-016-1244-0
Betz, J., Buchert, M., Dolega, P., and Bulach, W. (2021). Resource Consumption of the Passenger Vehicle Sector in Germany Until 2035 – the Impact of Different Drive Systems. Oeko-Institut. Freiburg im Breisgau.
Cerdas, F., Andrew, S., Thiede, S., and Herrmann, C. (2018). “Environmental aspects of the recycling of Lithium-ion traction batteries” in Sustainable Production, Life Cycle Engineering and Management. eds. A. Kwade and J. Diekmann, 267–288.
Ciez, R. E., and Whitacre, J. F. (2019). Examining different recycling processes for lithium-ion batteries. Nat. Sustain. 2, 148–156. doi: 10.1038/s41893-019-0222-5
Cusenza, M. A., Bobba, S., Ardente, F., Cellura, M., and Di Persio, F. (2019). Energy and environmental assessment of a traction lithium-ion battery pack for plug-in hybrid electric vehicles. J. Clean. Prod. 215, 634–649. doi: 10.1016/j.jclepro.2019.01.056
Dai, Q., Kelly, J. C., Gaines, L., and Wang, M. (2019a). Life cycle analysis of lithium-ion batteries for automotive applications. Batteries 5:48. doi: 10.3390/batteries5020048
Dai, Q., Spangenberger, J., Ahmed, S., Gaines, L., Kelly, J. C., and Wang, M. (2019b). EverBatt: A Closed-Loop Battery Recycling Cost and Environmental Impacts Model. Argonne National Laboratory, Lemont, IL, 1–88.
Du, S., Gao, F., Nie, Z., Liu, Y., Sun, B., and Gong, X. (2022). Comparison of electric vehicle Lithium-ion battery recycling allocation methods. Environ. Sci. Technol. 56, 17977–17987. doi: 10.1021/acs.est.2c05755
Dunn, J. B., Gaines, L., Kelly, J. C., and Gallagher, K. G. (2016). Life cycle analysis summary for automotive lithiumion battery production and recycling. REWAS 2016: Towards Materials Resource Sustainability, Belgium, 73–79.
Dunn, J. B., Gaines, L., Sullivan, J., and Wang, M. Q. (2012). Impact of recycling on cradle-to-gate energy consumption and greenhouse gas emissions of automotive lithium-ion batteries. Environ. Sci. Technol. 46, 12704–12710. doi: 10.1021/es302420z
Ekvall, T., Björklund, A., Sandin, G., Jelse, K., Lagergren, J., and Rydberg, M.. (2020). Modeling Recycling in Life Cycle Assessment. IVL Swedish Environmental Institute. Stockholm.
Ellingsen, L. A. W., Majeau-Bettez, G., Singh, B., Srivastava, A. K., Valøen, L. O., and Strømman, A. H. (2014). Life cycle assessment of a Lithium-ion battery vehicle pack. J. Ind. Ecol. 18, 113–124. doi: 10.1111/jiec.12072
European Commission. (2020). Regulation of the European Parliament and of the council concerning batteries and waste batteries, repealing. Directive 2006/66/EC and amending regulation (EU) no 2019/1020. Available at: https://eur-lex.europa.eu/legal-content/EN/TXT/?uri=CELEX%3A52020PC0798
Gaines, L., Sullivan, J., Burnham, A., and Bel, B. (2010). Life-Cycle Analysis for Lithium-ion Battery Production and Recycling. Transportation Research Board 90th Annual Meeting, Washington, DC, 11, 17.
Geyer, R., Kuczenski, B., Zink, T., and Henderson, A. (2016). Common misconceptions about recycling. J. Ind. Ecol. 20, 1010–1017. doi: 10.1111/jiec.12355
Harper, G., Sommerville, R., Kendrick, E., Driscoll, L., Slater, P., Stolkin, R., et al. (2019). Recycling lithium-ion batteries from electric vehicles. Nature 575, 75–86. doi: 10.1038/s41586-019-1682-5
Hoarau, Q., and Lorang, E. (2022). An assessment of the European regulation on battery recycling for electric vehicles. Energy Policy 162:112770. doi: 10.1016/j.enpol.2021.112770
Huijbregts, M. A. J., Steinmann, Z. J. N., Elshout, P. M. F., Stam, G., Verones, F., Vieira, M., et al. (2016). ReCiPe2016: a harmonised life cycle impact assessment method at midpoint and endpoint level. Int. J. Life Cycle Assess. 22, 138–147. doi: 10.1007/S11367-016-1246-Y
ISO. (2006a). ISO - ISO 14040:2006 - environmental management — Life cycle assessment — Principles and framework.
ISO. (2006b). ISO - ISO 14044:2006 - Environmental management — Life cycle assessment — Requirements and guidelines.
Kelly, J. C., Dai, Q., and Wang, M. (2019). Globally regional life cycle analysis of automotive lithium-ion nickel manganese cobalt batteries. Mitig. Adapt. Strateg. Glob. Chang. 25, 371–396. doi: 10.1007/s11027-019-09869-2
Lamb, W. F., Wiedmann, T., Pongratz, J., Andrew, R., Crippa, M., Olivier, J. G. J., et al. (2021). A review of trends and drivers of greenhouse gas emissions by sector from 1990 to 2018. Environ. Res. Lett. 16:073005. doi: 10.1088/1748-9326/abee4e
Majeau-Bettez, G., Hawkins, T. R., and StrØmman, A. H. (2011). Life cycle environmental assessment of lithium-ion and nickel metal hydride batteries for plug-in hybrid and battery electric vehicles. Environ. Sci. Technol. 45, 4548–4554. doi: 10.1021/es103607c
Mikosch, N., Dettmer, T., Plaga, B., Gernuks, M., and Finkbeiner, M. (2022). Relevance of impact categories and applicability of life cycle impact assessment methods from an automotive industry perspective. Sustainability (Switzerland) 14:8837. doi: 10.3390/su14148837
Mohr, M., Peters, J. F., Baumann, M., and Weil, M. (2020). Toward a cell-chemistry specific life cycle assessment of lithium-ion battery recycling processes. J. Ind. Ecol. 24, 1310–1322. doi: 10.1111/jiec.13021
Neidhardt, M., Mas-Peiro, J., Schulz-Moenninghoff, M., Pou, J. O., Gonzalez-Olmos, R., Kwade, A., et al. (2022). Forecasting the global battery material flow: analyzing the break-even points at which secondary battery raw materials Can substitute primary materials in the battery production. Appl. Sci. (Switzerland) 12:4790. doi: 10.3390/app12094790
Nordelöf, A., Poulikidou, S., Chordia, M., de Oliveira, F. B., Tivander, J., and Arvidsson, R. (2019). Methodological approaches to end-of-life modelling in life cycle assessments of lithium-ion batteries. Batteries 5:51. doi: 10.3390/batteries5030051
Olivetti, E. A., Ceder, G., Gaustad, G. G., and Fu, X. (2017). Lithium-ion battery supply chain considerations: analysis of potential bottlenecks in critical metals. Joule 1, 229–243. doi: 10.1016/j.joule.2017.08.019
Porzio, J., and Scown, C. D. (2021). Life-cycle assessment considerations for batteries and battery materials. Adv. Energy Mater. 11, 2100771–2100720. doi: 10.1002/aenm.202100771
RECHARGE. (2021). Proposal for batteries regulation 2020 / 353 (COD), repealing directive 2006/66/EC and amending regulation (EU) no 2019/1020 RECHARGE statement to public consultation.
Reed, M. S., Graves, A., Dandy, N., Posthumus, H., Hubacek, K., Morris, J., et al. (2009). Who’s in and why? A typology of stakeholder analysis methods for natural resource management. J. Environ. Manag. 90, 1933–1949. doi: 10.1016/j.jenvman.2009.01.001
Schmidt, T. S., Beuse, M., Zhang, X., Steffen, B., Schneider, S. F., Pena-Bello, A., et al. (2019). Additional emissions and cost from storing Electricity in Stationary Battery Systems. Environ. Sci. Technol. 53, 3379–3390. doi: 10.1021/acs.est.8b05313
Schrijvers, D. L., Loubet, P., and Sonnemann, G. (2016). Developing a systematic framework for consistent allocation in LCA. Int. J. Life Cycle Assess. 21, 976–993. doi: 10.1007/s11367-016-1063-3
Schrijvers, D., Loubet, P., and Sonnemann, G. (2020). Consistent allocation using archetypes of LCA goal and scope definitions. Sustainability 12, 2–3. doi: 10.3390/su12145587
Siret, C., Tytgat, J., Ebert, T., Mistry, M., Thirlaway, C., Schutz, B., et al. (2018). PEFCR - product environmental footprint category rules for high specific energy rechargeable batteries for Mobile applications version: H time of validity: 31 December 2020. Available at: http://ec.europa.eu/; https://ec.europa.eu/environment/eussd/smgp/pdf/PEFCR_Batteries.pdf
Sommerville, R., Zhu, P., Rajaeifar, M. A., Heidrich, O., Goodship, V., and Kendrick, E. (2021). A qualitative assessment of lithium ion battery recycling processes. Resour. Conserv. Recycl. 165:105219. doi: 10.1016/j.resconrec.2020.105219
Steubing, B., de Koning, D., Haas, A., and Mutel, C. L. (2020). The activity browser — an open source LCA software building on top of the brightway framework. Software Impacts 3:100012. doi: 10.1016/J.SIMPA.2019.100012
Wernet, G., Bauer, C., Steubing, B., Reinhard, J., Moreno-Ruiz, E., and Weidema, B. (2016). The ecoinvent database version 3 (part I): overview and methodology. Int. J. Life Cycle Assess. 21, 1218–1230. doi: 10.1007/S11367-016-1087-8
Keywords: allocation, end-of-life, life cycle assessment, lithium-ion battery, recycling
Citation: Husmann J, Ali A-R, Cerdas F and Herrmann C (2023) The influence of stakeholder perspectives on the end-of-life allocation in the life cycle assessment of lithium-ion batteries. Front. Sustain. 4:1163207. doi: 10.3389/frsus.2023.1163207
Edited by:
Jussi I. Kantola, University of Turku, FinlandReviewed by:
Ioannis Sebos, National Technical University of Athens, GreeceAbhishek Kumar, Zhejiang University, China
Copyright © 2023 Husmann, Ali, Cerdas and Herrmann. This is an open-access article distributed under the terms of the Creative Commons Attribution License (CC BY). The use, distribution or reproduction in other forums is permitted, provided the original author(s) and the copyright owner(s) are credited and that the original publication in this journal is cited, in accordance with accepted academic practice. No use, distribution or reproduction is permitted which does not comply with these terms.
*Correspondence: Jana Husmann, j.husmann@tu-braunschweig.de