Accelerated Carbonation of Steel Slags Using CO2 Diluted Sources: CO2 Uptakes and Energy Requirements
- 1Department of Civil Engineering and Computer Science Engineering, University of Rome “Tor Vergata”, Rome, Italy
- 2Department of Civil and Environmental Engineering, University of Rome “La Sapienza”, Rome, Italy
This work presents the results of carbonation experiments performed on Basic Oxygen Furnace (BOF) steel slag samples employing gas mixtures containing 40 and 10% CO2 vol. simulating the gaseous effluents of gasification and combustion processes respectively, as well as 100% CO2 for comparison purposes. Two routes were tested, the slurry-phase (L/S = 5 l/kg, T = 100°C and Ptot = 10 bar) and the thin-film (L/S = 0.3–0.4 l kg, T = 50°C and Ptot = 7–10 bar) routes. For each one, the CO2 uptake achieved as a function of the reaction time was analyzed and on this basis, the energy requirements associated with each carbonation route and gas mixture composition were estimated considering to store the CO2 emissions of a medium size natural gas fired power plant (20 MW). For the slurry-phase route, maximum CO2 uptakes ranged from around 8% at 10% CO2, to 21.1% (BOF-a) and 29.2% (BOF-b) at 40% CO2 and 32.5% (BOF-a) and 40.3% (BOF-b) at 100% CO2. For the thin-film route, maximum uptakes of 13% (BOF-c) and 19.5% (BOF-d) at 40% CO2, and 17.8% (BOF-c) and 20.2% (BOF-d) at 100% were attained. The energy requirements of the two analyzed process routes appeared to depend chiefly on the CO2 uptake of the slag. For both process route, the minimum overall energy requirements were found for the tests with 40% CO2 flows (i.e., for the slurry-phase and for the thin-film route).
Introduction
Accelerated carbonation of alkaline earth metal silicate ores has been proposed as a method for ex situ carbon dioxide storage in the early 90s (Seifritz, 1990; Lackner et al., 1995). Since then, many studies have extensively investigated at laboratory scale the applicability of this treatment to Ca and Mg bearing silicates, such as serpentine, olivine and wollastonite, in view of their high carbon sequestration potential and widespread availability (especially for the first two types of minerals). Different types of process routes, i.e., gas-solid or aqueous, each performed in direct or indirect mode, have been tested (see e.g., Sipilä et al., 2008; Baciocchi et al., 2014). The most applied route is the direct aqueous one, by which the alkaline feedstock is mixed with water to obtain a Liquid to Solid (L/S) ratio above 2 l/kg, and the resulting slurry is contacted with pressurized CO2 so that Ca or Mg dissolution and carbonate precipitation take place in the same reactor. It should be noted that the operating conditions that have proven effective to promote the carbonation kinetics of the tested minerals, and hence obtain high reaction yields in technically feasible operating times (<2 h), are energy intensive; for example, direct carbonation of minerals is found to be effective at a temperature of 100−200°C and pressures of 10−100 bar (O’Connor et al., 2005; Sipilä et al., 2008). In addition, regardless of the reaction route employed, to achieve a significant CO2 uptake in short timeframes, the surface of the minerals needs to be activated by physical pretreatments, including size reduction, magnetic separation, and even thermal or steam treatment to eliminate chemically bound water for minerals like serpentine (Baciocchi et al., 2014). Hence, the energy intensive operating conditions typically required for accelerated mineral carbonation still hinder the industrial application of this technology (Zingaretti et al., 2014).
In parallel to the investigations carried out on minerals, the reactivity with CO2 of alkaline industrial residues characterized by high calcium or magnesium (hydr)oxide or silicate contents has also been extensively examined, as reported in several reviews (Costa et al., 2007; Bobicki et al., 2012; Pan et al., 2012; Baciocchi et al., 2014). Although significantly less abundant in comparison to minerals, these materials have proven to be more reactive at mild operating conditions (Huijgen et al., 2006a). Furthermore, carbonation has shown to affect some of the properties of the tested materials (i.e., main mineralogy, porosity, and mobility of specific elements) improving their long-term technical performance and/or environmental behavior (Bobicki et al., 2012; Pan et al., 2012). Thus, the application of this treatment to alkaline industrial residues may be indeed considered as a CO2 storage and utilization option, since accelerated carbonation may be also employed as a valorization technique for widening the reuse options of these materials and also to achieve other environmental benefits (Baciocchi et al., 2014). Steel manufacturing plants are the typical examples of industrial sites in which relevant flows of both CO2 and alkaline industrial residues are generated and therefore represent one of the potentially most interesting contexts for the application of accelerated carbonation. Several studies have shown that a number of different types of steel slag present a significant reactivity with CO2, allowing to achieve, for specific process routes and operating conditions, relevant CO2 uptakes (Huijgen et al., 2005; Baciocchi et al., 2010, 2015; Uibu et al., 2011; Chang et al., 2012; Santos et al., 2013a,b). Furthermore, several types of residues generated in steel manufacturing plants, such as Basic Oxygen Furnace (BOF), Electric Arc Furnace (EAF), and argon oxygen decarburization (AOD) slag, are typically not valorized and generally landfilled, or employed only for low-end applications, owing for their significant content of free calcium and magnesium (hydr)oxides that may result in poor volumetric stability and hence in a low technical performance in construction applications (Morone et al., 2014). Therefore, accelerated carbonation of these types of materials may also represent a treatment strategy to improve their properties in view of valorization.
Despite all the potential assets mentioned above, industrial-scale applications of accelerated carbonation of residues such as steel slag are also currently still missing owing to uncertainties on the feasibility of this process, especially as far as material and energy requirements are concerned. Specifically, with regard to the latter, significant CO2 uptakes in reasonable timeframes were achieved via the slurry-phase route using residues with a fine particle size (typically below 100 μm), obtained either by milling or simple sieving of the material, and operating the carbonation reactor at enhanced temperature and CO2 pressure (Huijgen et al., 2005; Chang et al., 2012; Santos et al., 2013a,b; Baciocchi et al., 2015). It should be noted, however, that in a recent study, milder operating conditions were shown to be effective employing a proper lixiviant (ammonium chloride) to enhance calcium dissolution (Mattila et al., 2014). Besides, promising results in terms of CO2 uptake (even if lower than those attained through the former route) have been achieved also via the thin-film (or wet) route (Baciocchi et al., 2011, 2015; Santos et al., 2013b; Morone et al., 2014), which is operated at lower temperature and CO2 pressure and also presents the advantage of not generating a liquid by-product that necessitates suitable management and treatment.
In the last years, several studies have assessed the energy requirements associated to direct carbonation of minerals and industrial residues adopting the slurry-phase route (e.g., Huijgen et al., 2006b; Kelly et al., 2011; Kirchofer et al., 2012), while to our knowledge this evaluation for the thin-film route was performed only by Zingaretti et al., 2014. In the latter study, based on the results of lab-scale tests carried out on different types of industrial residues using pure CO2, a comparison of the energy requirements associated with both reaction routes was performed. The authors estimated that the energy requirement for CO2 storage only was around 1300–2750 MJ/tCO2 for the slurry-phase process and between for the thin-film one depending on the type of residues and operating conditions applied (Zingaretti et al., 2014). Besides, the feasibility of the thin-film carbonation route was somehow linked to the possibility of using diluted CO2 sources, thus lumping capture and storage in a single step.
This work is aimed at further assessing the feasibility of performing accelerated carbonation using diluted CO2 sources, extending the evaluation also to the slurry-phase route. To this aim, batch carbonation tests via both the slurry-phase and thin-film routes were performed on different types of BOF steel slags, using diluted CO2 sources (i.e., containing 40 and 10% vol. CO2) and a 100% CO2 source as a reference case. Then, based on the CO2 uptakes achieved in these experiments, the energy requirements for storing the CO2 emissions of a medium size natural gas fired power plant (20 MW) were assessed and discussed in terms of the type of BOF slag treated, the carbonation reaction time (from 0.5 to 24 h), and the gas composition considered (10, 40, or 100% vol.).
Materials and Methods
The slag samples tested in this work were collected from a steel plant employing the integrated steelmaking process both directly at the outlet of the BOF unit (BOF-a and BOF-c) after grinding (to d < 1 mm) and at the storage site after grinding (to d < 1 mm) for metals recovery (BOF-b and BOF-d). The slag samples were then oven-dried at 60°C and ball-milled to a final particle size of <150 μm in the case of samples a and b used for the slurry-phase route tests, or only sieved to a particle size below 125 μm, in the case of samples c and d employed in the thin-film tests. The slight differences in the preparation and final particle size of the samples tested in the two types of carbonations tests was due to the fact that the two routes were investigated in two distinct laboratories, equipped with different milling and sieving devices. Anyhow, this difference is not expected to significantly affect the obtained results, since the composition and mineralogy as well as CO2 reactivity of the same type of slag milled <150 μm or sieved <125 μm showed to be quite similar (as indicated by the results of thin-film route experiments performed on BOF samples milled at 150 μm, Baciocchi et al., 2015).
The elemental composition of the four BOF slag samples is reported in Table 1. With regard to the main elements of interest for the carbonation process, the following concentration ranges were detected for the investigated materials: Ca 21.3 − 28.9% dry wt., Mg 3.3 − 6.9%, Fe 13.9 − 19.6%, Mn 2.4 − 3.8%. Such elements were present at comparable levels in the four slag samples investigated, although BOF-c and BOF-d exhibited slightly higher Ca and Mg concentrations and somewhat lower Fe contents. Based on the evidence provided by XRD analysis and other chemical characterization methods, we estimated the amounts of the main mineralogical phases of each sample (see Table 2). Making reference to Ca and Mg-bearing phases, the samples collected directly at the outlet of the BOF unit (a and c) were characterized by a higher content of silicates, as larnite (Ca2SiO4) and hatrurite (Ca3SiO5) and oxides (MgO), while those collected from the storage site (b and d) presented basically only larnite as a Ca-silicate phase and a higher content of hydroxide phases, i.e., portlandite [Ca(OH)2] and brucite [Mg(OH)2], besides more calcite (CaCO3), an indication of natural weathering.
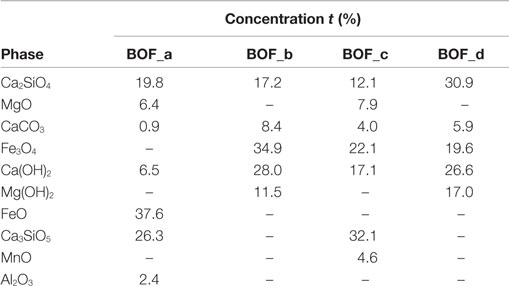
Table 2. Mineralogical composition assumed for the BOF slags on the basis of the results of XRD and other chemical analysis.
Slurry-phase accelerated carbonation tests were performed on BOF-a and BOF-b slag samples in a pressurized stainless steel reactor equipped with an external magnetic stirring device and a heating jacket. Based on the results of previous investigations (Baciocchi et al., 2011, 2015), a liquid to solid ratio (L/S) of 5 l/kg, operating temperature of 100°C and total pressure of 10 bar were selected. The thin-film route carbonation tests were carried out on BOF slag samples c and d in a pressurized stainless steel reactor placed in a water bath for temperature control. The operating conditions selected for this route based on previous investigations (Baciocchi et al., 2011, 2015; Morone et al., 2014) were a L/S of 0.3 l/kg, a temperature of 50°C, and a total pressure of 7–10 bar. For both types of routes, different reaction times (ranging from 0.5 to 24 h) and CO2 concentrations in the gas flow were tested. In particular, the slurry-phase tests were performed with 100, 40, or 10% vol. CO2 flows to simulate not only a pure CO2 flow deriving from a preliminary capture step but also diluted CO2 flows from gasification or combustion processes. In the thin-film route only 100 and 40% vol. CO2 flows were employed, since previous results obtained for steel slag adopting this configuration indicated that the CO2 uptakes achievable using a gas composition similar to fluegas were significantly lower than those attained with higher CO2 concentrations of the treated gas flow (Zingaretti et al., 2014). At the end of the slurry-phase carbonation tests, the reactor was immediately degassed and then rapidly cooled down to ambient temperature through immersion in a water bath. Then liquid/solid separation was subsequently accomplished through centrifuging at 4000 rpm followed by 0.45 μm filtration. The solid samples obtained from both types of routes were oven-dried at 105°C and analyzed to determine their carbonate content through inorganic carbon (IC) measurement employing a Shimadzu TOC analyzer equipped with a solids module. The CO2 uptake, defined as the ratio between the mass (in grams) of CO2 sequestered and the mass (in grams) of as-received dry material and expressed as a percentage, was calculated through Eq. 1 (see Supplementary Material) from the IC contents of the carbonated (CO2final) and untreated (CO2initial) samples reported as CO2 weight percent contents. The IC contents of the untreated slag samples were: 0.11% (BOF-a), 1.01% (BOF-b), 0.48% (BOF-c), and 0.71% (BOF-d).
The evaluation of the energy requirements for the carbonation process was carried out adopting the approach developed in our previous work (Zingaretti et al., 2014). Based on the mass flow rate of CO2 to store, i.e., 1 kg/s, which corresponds to the typical emission value of a 20 MW natural gas fired power plant, the amount of residues required in the process for each carbonation condition was determined. Hence, the energy requirements associated to each route were calculated summing those necessary for all the unit operations foreseen for each configuration (expressed as MJ/tCO2 stored), on the basis of the experimental data obtained for the type of investigated BOF slag (i.e., chemical composition, mineralogy, and CO2 uptake). Figure 1 reports the process layout adopted for the slurry-phase and thin-film configurations.
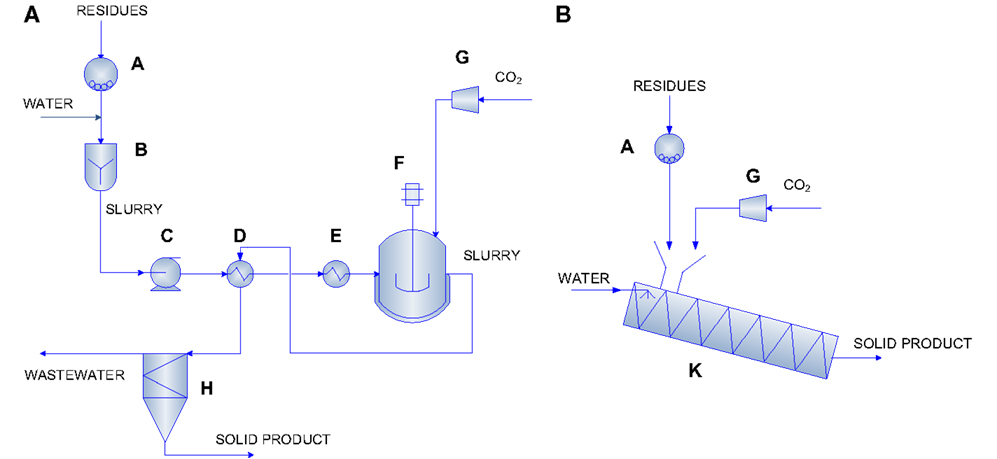
Figure 1. Carbonation process layout for the slurry-phase (A) and the thin-film (B) routes [reprinted with permission from Zingaretti et al. (2014)]. Copyright (2014) American Chemical Society. A = mill; B = rapid mixing unit; C = pump; D, E = heat exchangers; F, K = carbonation reactors; G = compressor; H = settling tank.
The process layout considered for the slurry-phase route is similar to the ones proposed by O’Connor et al. (2005) and Huijgen et al. (2006b). Namely, as can be seen in Figure 1A, in this route, the BOF slags are firstly ground to the desired particle size (unit A) and then mixed with water at a specific liquid to solid ratio (unit B). Then, the slurry is pumped (unit C) to a heat exchanger (unit D) where it is heated to 30°C below the reaction temperature. Before entering the carbonation reactor (unit F), the slurry is heated by a further heater (unit E) where it reaches the desired temperature. In the carbonation reactor, the slurry is contacted with carbon dioxide, already pressurized in a multi-stage compressor (unit G) to the desired pressure, and the carbonation reaction takes place. The slurry leaving the reactor passes through unit D to heat recovery and finally is separated (unit H) producing a solid product and a liquid stream. In the thin-film route (see Figure 1B), the BOF slags are fed to the carbonation reactor (unit K) after being ground to the specific particle size in unit A. In unit K, the material is humidified to the desired L/S ratio, heated, and contacted with CO2 already pressurized in a multi-stage compressor (unit G) to the desired pressure. The carbonation reactor in this route is envisioned as a rotary drum and the associated energy requirements are due to the material heating and the rotation of the drum. Table 3 reports the equations used to estimate the energy requirements associated to each unit operation considered in the two carbonation routes. It should be noted that, for unit D in the slurry-phase route, the overall energy requirement associated with the heating of the slurry was estimated considering the energy required to achieve the final carbonation temperature, the energy recovered in the heat exchanger by cooling the outlet stream from the carbonation reactor, the heat of reaction of the carbonation process, and the heat loss from the carbonation reactor. In the thin-film route, instead, reaction heat recovery was not taken into account since it was considered to be unpractical due to the fact that in this case there is no liquid solution. For both process routes, when a concentrated CO2 flow was assumed to be used (i.e. 100% CO2), the energy demand associated to the preliminary capture step was also accounted for, and overall quantified as 4000 kJ/kg CO2 captured [Intergovernmental Panel on Climate Change (IPCC), 2005].
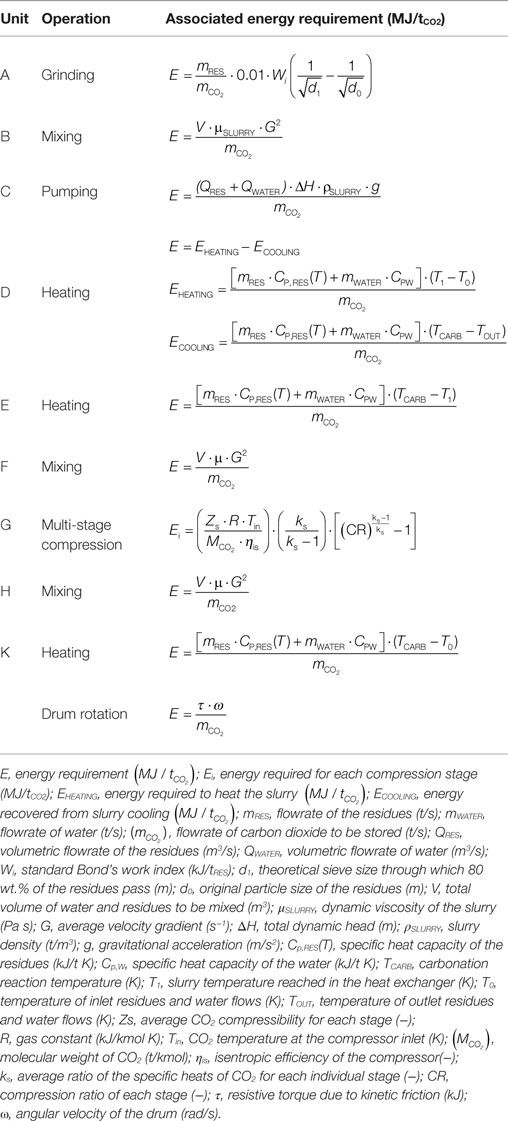
Table 3. Equations used to assess the energy requirement associated to each unit considered for the two carbonation routes.
Results and Discussion
Carbonation Performance
The CO2 sequestration yield attained from the experiments as a function of the reaction time for the two process routes and the four slag samples investigated is reported in Figure 2. Since the aim of the present paper is to provide an assessment of the energetic profile of CO2 sequestration through mineral carbonation of steel manufacturing residues applying both the slurry-phase and the thin-film route, the energy demand of the various process units as affected by the operating conditions and the intrinsic reactivity of the material toward CO2 was estimated. Thus, CO2 uptake yields are provided in the following paragraphs and discussed in light of their expected influence on the whole energetic profile of the mineral carbonation process. For an in-depth discussion of the physical phenomena, chemical reactions and mineralogical changes occurring during the process, the reader is referred to previous publications (Baciocchi et al., 2009, 2010, 2011, 2015). A review of the carbonation performance of steel slag materials from different literature studies and of its dependence on the slag characteristics and process conditions can also be found in Baciocchi et al. (2015).
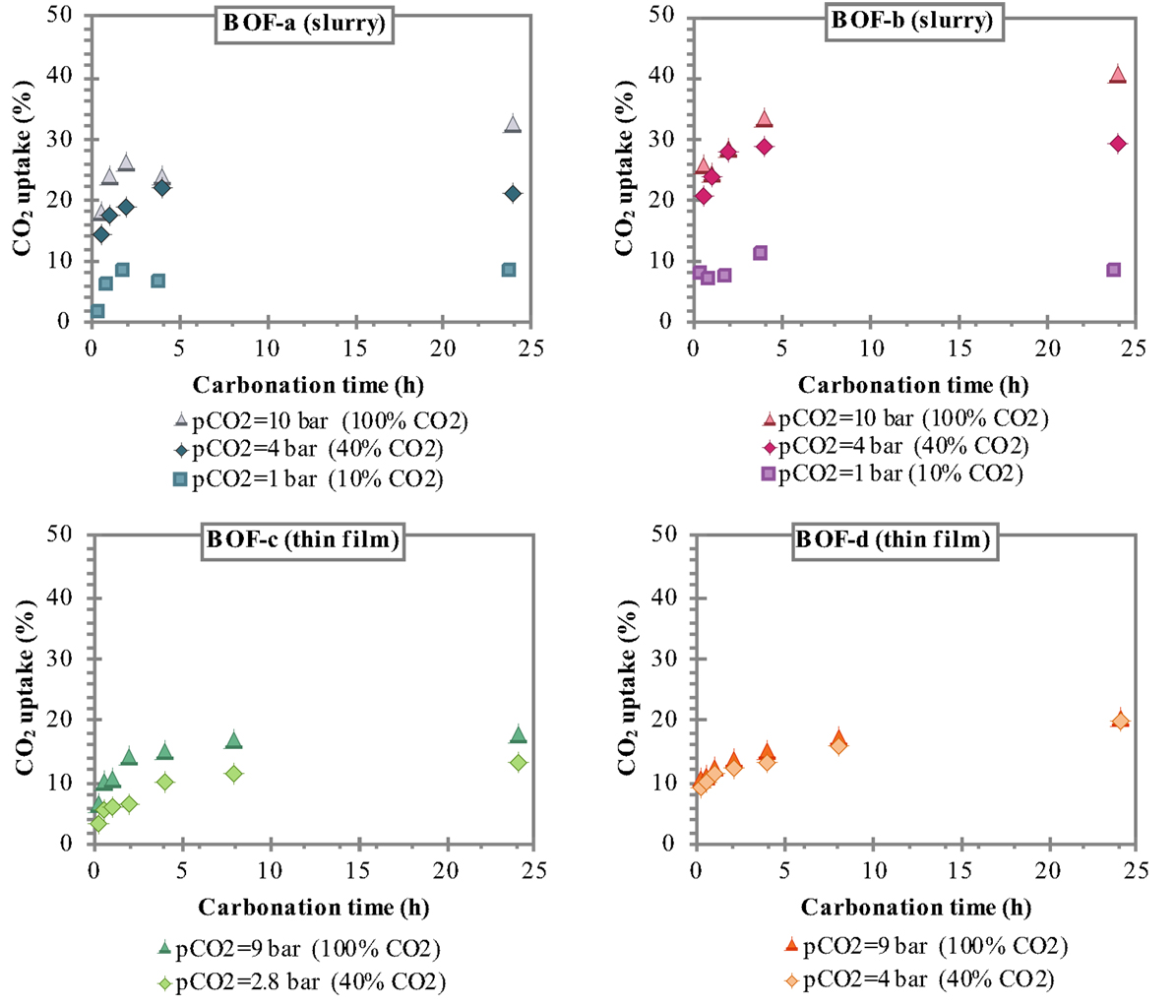
Figure 2. CO2 uptake attained for the slurry-phase route with BOF-a and BOF-b samples (T = 100°C) and the thin-film route with BOF-c samples and BOF-d samples (T = 50°C).
The CO2 uptakes measured after 24 h carbonation applying the slurry-phase route were: ≈8% at 10% CO2 for both types of slag, 21.1% (BOF-a) and 29.2% (BOF-b) at 40% CO2, and 32.5% (BOF-a) and 40.3% (BOF-b) at 100% CO2; the corresponding values resulting for the thin-film route were: 12.9% (BOF-c) and 19.5% (BOF-d) at 40% CO2, and 17.8% (BOF-c) and 20.2% (BOF-d) at 100% CO2. These results indicate the generally better performance of the BOF-b and BOF-d slag compared to BOF-a and BOF-c samples that can be related to the differences in the mineralogy of the slag; samples b and d being richer in readily reactive hydroxide phases such as portlandite and brucite compared to a and c that presented a higher content of silicates (see Table 2). It is interesting to note that, particularly for the thin-film carbonation route and for short reaction times for the slurry-phase process, the use of a 40% CO2 flow instead of a pure one did not appear to significantly affect the CO2 uptake of the slag (especially BOF-b and BOF-d). Instead, for a 10% CO2 flow the uptake resulted below 10% and appeared not to be appreciably affected by the reaction time.
Although the direct comparison of the two process routes should be made with care owing to the slight differences in composition of the slag samples investigated (see Tables 1 and 2), the observed trends certainly highlight the higher carbonation yields of the slurry-phase process as opposed to the thin-film route, confirming the findings of our previous study (Baciocchi et al., 2015). Compared to the thin-film process, the slurry-phase conditions are believed to promote the dissolution of reactive metals from the solid phase (assuming that the dissolution/precipitation reactions approach thermodynamic equilibrium conditions during the process), as well as to prevent the coating effect exerted by the precipitated carbonate product onto the unreacted core of the slag particles (Santos et al., 2013a).
Energy Requirements Assessment
The specific energy requirements of each unit operation for the slurry-phase route are reported in Figure 3 making reference to the experimental results achieved for the BOF-a and BOF-b slags. It may be noted that the various process units contributed in quite different extents to the overall energy demand. For improved clarity, the relative contributions of the process units to the total energy consumption are reported in Figure 4.
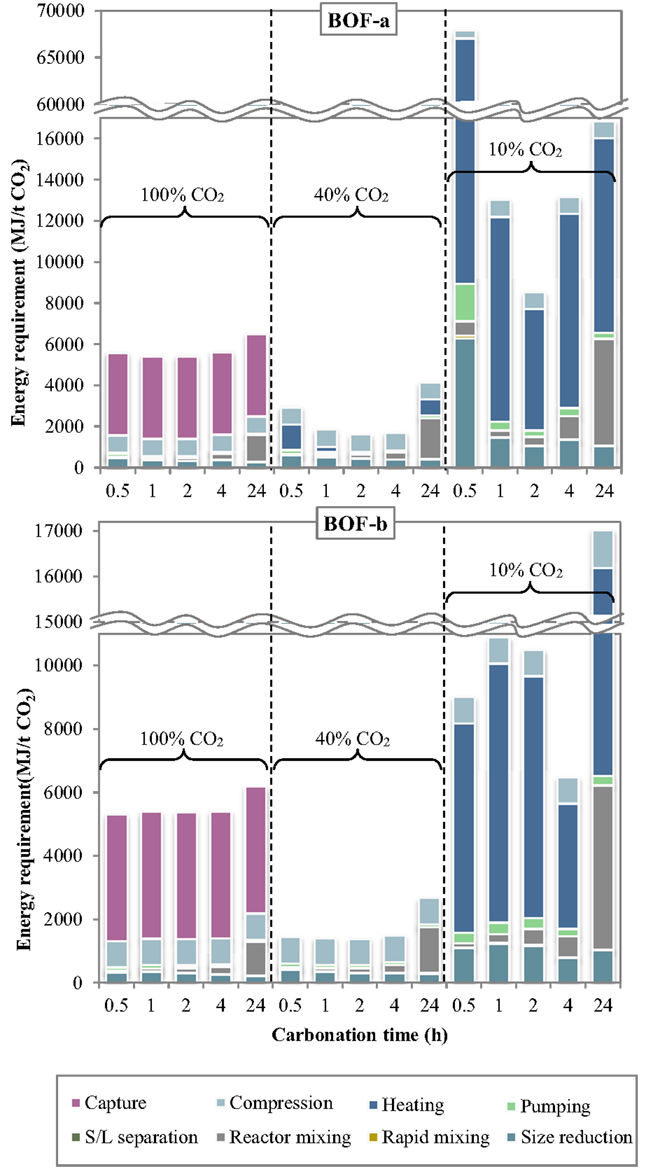
Figure 3. Energy requirement of each unit operation as a function of the carbonation conditions (slurry-phase route).
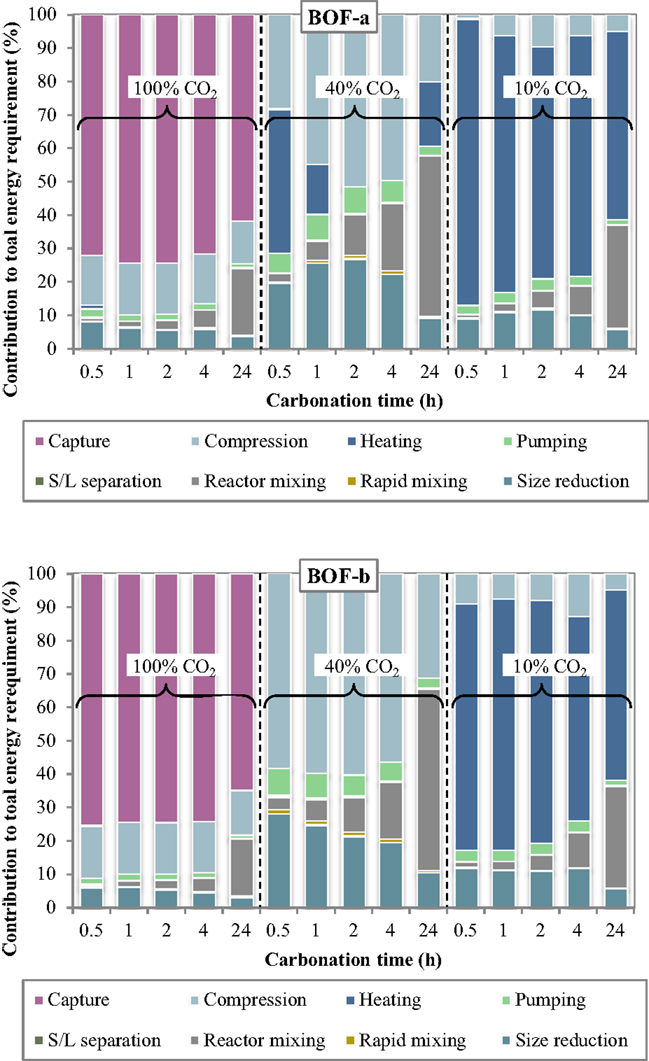
Figure 4. Relative contribution of each unit operation to the total energy consumption as a function of the carbonation conditions (slurry-phase route).
Several interesting features may be derived from the inspection of Figures 3 and 4. Specifically, the carbonation yield attained obviously turned out to play a relevant role on the energy requirements per unit mass of CO2 sequestered. For a CO2 concentration in the gaseous phase of 10% (simulating the typical content of combustion flue gases) the notably lower CO2 sequestration performances achieved implied the use of larger amounts of slag and water for storing the target amount of CO2 and therefore higher associated energy demands for almost all process units, in particular slurry heating and mixing. Comparing the energy requirements of the slurry-phase process using a combustion effluent or a concentrated CO2 flow (CO2 concentration = 100%), it is found that in the latter case the higher energy consumption associated to the preliminary capture stage is counterbalanced by the notably lower consumption of the other process operations. As a consequence, for very diluted gaseous flows a carbonation process including a pre-treatment stage aimed at concentrating CO2 in the gaseous phase is deemed economically more viable compared to the option without CO2 capture. On the other hand, for intermediate CO2 concentrations in the gas phase (CO2 = 40% vol., representing the typical CO2 level in the gaseous effluent from gasification processes), the significant CO2 uptake potential displayed by the slag, with sequestration yields comparable to those achieved using the concentrated stream, made the carbonation process energetically more competitive since in this case the duties related to the capture step were not considered.
The relative contribution of the individual unit operations to the total energy consumption was also found to vary with the specific process condition adopted. In particular, at a CO2 concentration of 10% the most energy-demanding stage was the heating phase, with energy consumptions for BOF-a ranging from for 2-h and 0.5-h carbonation (corresponding to 69 and 86% of the total energy demand) and for BOF-b ranging from for 4-h and 24-h carbonation (61 and 57% of the total energy demand). For long carbonation durations (24 h), the relative incidence of the energy consumption associated to slurry mixing inside the reactor became appreciable, with a contribution of for both slag samples (~30% of total consumption). On the other hand, for BOF-a and a short carbonation time (0.5 h), for which the CO2 uptake was of only 1.3%, the high amount of solid material to be used in the process implied a significant energy consumption (; 12% of total consumption) for slag milling.
Compared to the results described above, the addition of a preliminary capture stage to the carbonation process layout (i.e., the use of a 100% CO2 gas flow) resulted in a significant decrease in the energy requirement of all process stages (with the exception of the compression unit), and particularly of the heating stage, which was of several orders of magnitude lower than that observed when working with a gas flow containing 10% CO2. The overall energy requirement was reduced by 1.2–2.8 times for BOF-b and 1.6–12.2 times for BOF-a compared to the use of a 10%-CO2 effluent. In absolute terms, the calculated ranges for the total energy consumption were for BOF-a and BOF-b, respectively, with the highest values being in both cases associated to a carbonation time of 24 h. Using the concentrated gaseous effluent, the most relevant contribution to the overall energy demand was provided by the CO2 capture stage, which accounted for 62–74% and 65–75% of the total requirements for BOF-a and BOF-b; the gas compression stage had also an appreciable energy duty (), contributing by 12–15% and 13–16% of the overall demand for the two slag samples. The other terms were notably less relevant, except for the contribution of slurry mixing in the carbonation reactor for the longest residence time (24 h), which was of for BOF-a and BOF-b, corresponding to 20 and 17% of the total duty.
When employing a 40% CO2 concentration in the gas phase, the total energy requirement of the process was found to be considerably lower than that estimated for the two cases discussed above. As mentioned earlier, the improved energetic performance of the process using a 40% CO2 effluent was due to the fact that, while the reactivity of the slag upon carbonation was comparable to that achieved with pure CO2, the absence of the capture stage in the process layout allowed to save a significant share of energy. In this case, the overall energy requirements of the CO2 sequestration process for the BOF-a and BOF-b slags lay within the ranges . Relevant contributions to the energy penalties of the process were provided by the gas compression and size reduction units, while the duty of slurry mixing was only relevant for prolonged contact times; for the BOF-a slag the energy requirement of the heating operation was also appreciable for 0.5-h and 24-h carbonation. In absolute terms, the BOF-a slag had the following associated main energy requirements: for gas compression, for size reduction, for slurry mixing and for heating. The corresponding values calculated for the BOF-b sample were as follows: for gas compression, for size reduction, for slurry mixing, while heating theoretically required no net energy input thanks to the heat recovered from the exhaust slurry recycled to the first heater (see Figure 1).
The specific energy requirements of each unit operation for the thin-film route are reported in Figure 5 making reference to the experimental results achieved for the BOF-c and BOF-d slags. The relative contributions of the process units to the total energy consumption are reported in Figure 6. As can be observed, for the case in which carbonation was assumed to be applied on a CO2 pure stream obtained after capture, the total energy requirement as well as the contributions of the different unit operations for the two BOF slag samples analyzed appeared to be very similar. In particular, for BOF-c slag the overall energy requirements ranged from (at 0.5 h), while for sample BOF-d they varied from (at 0.5 h). It should be noted that in this case, differently from the slurry-phase route, due to the increase in the CO2 uptake of the slag for longer reaction times, the energy requirements showed to decrease progressively. This may be related to the fact that in this case the heating requirements resulted significantly lower compared to the slurry-phase route even though heat recovery was not taken into account for the thin-film route (Zingaretti et al., 2014). However, it should be acknowledged with reference to both the slurry-phase and thin-film route that for an industrial-scale application of carbonation as a CCS technique, the adoption of long reaction times (i.e., above 1–2 h) would be unfeasible. As shown in Figure 6, the main contributions to the energy requirements were: CO2 capture (~50–70%), milling and heating of the residues (~10–20%) and CO2 compression (~13%).
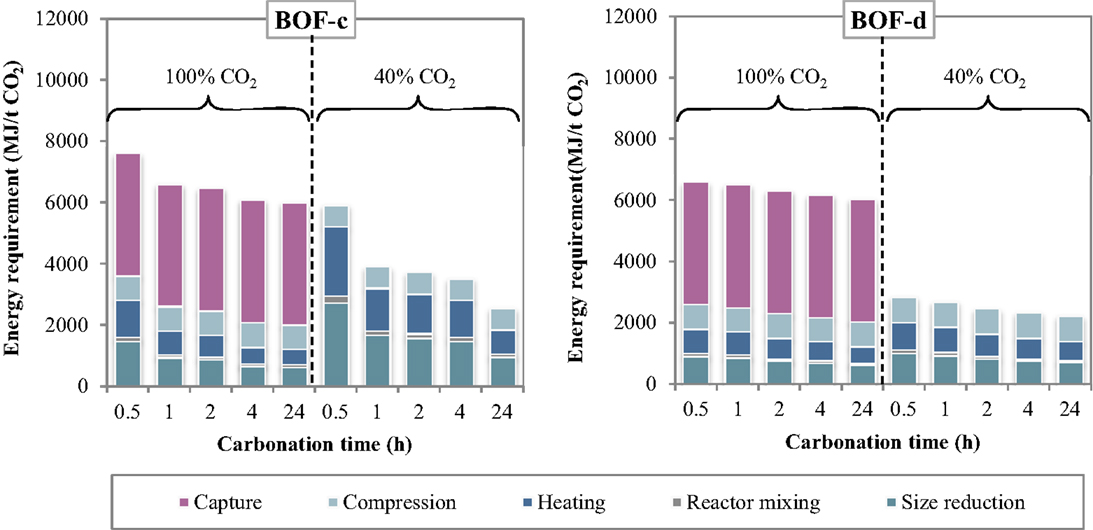
Figure 5. Energy requirement of each unit operation as a function of the carbonation conditions (thin-film route).
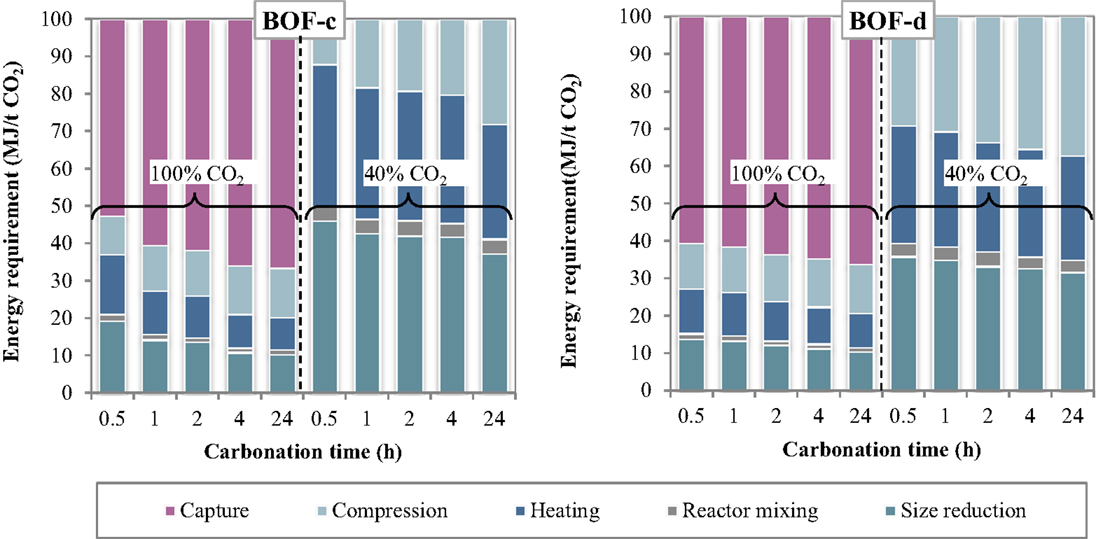
Figure 6. Relative contribution of each unit operation to the total energy consumption as a function of the carbonation conditions (thin-film route).
As for the tests carried out with 40% CO2 gas flows, similarly to what reported for the slurry-phase route, owing to the fact that capture was not assumed to be applied in this case, a notable reduction in the total energy requirements was achieved. In particular, the overall requirement ranged from for sample BOF-c and from for BOF-d, increasing also in this case progressively with reaction time. The higher requirements resulting for the first type of slag especially for short durations may be related to the lower CO2 uptakes obtained which in turn may be ascribed to the differences in the mineralogy of the two slags (type c being mainly made up by silicate phases presenting a slower reaction kinetics compared to hydroxides). It should, however, be noted that for this type of slag the tests with 40% CO2 were carried out applying a total pressure of 7 bar. As for the contributions of the single unit processes, the most relevant for BOF-c appeared to be milling (40–50%), followed by heating (25–35%) and CO2 compression (15–30%), whereas for BOF-d the three above mentioned processes appeared to exert a similar weight (30–40%) on the total energy demand.
In order to derive some considerations of wider applicability concerning the dependence of the total energy requirement of slurry-phase and thin-film carbonation from the CO2 uptake of the treated residues, the total energy requirements (excluding CO2 capture) obtained for the four types of tested slags, the two routes and different gas compositions and reaction times tested were all reported together in the same graph as a function of the CO2 uptake (see Figure 7). The trend of the data points showed to be adequately described by the following theoretical correlation function (see Eq. 2) that for a null CO2 uptake tends to infinity and remains quite constant for CO2 uptakes close to the maximum achievable ones that depend on the chemical and mineralogical composition of the material:
with and . This trend highlights the key role of the CO2 uptake in determining the overall energy requirements related to the carbonation process in particular for low reaction yields (<10% wt.). It is interesting to note that for the BOF slag samples analyzed in this study, regardless of the type of process route applied and operating conditions selected, an estimation of the total energy requirement of the process can be directly made on the basis of the CO2 uptake of the residues.
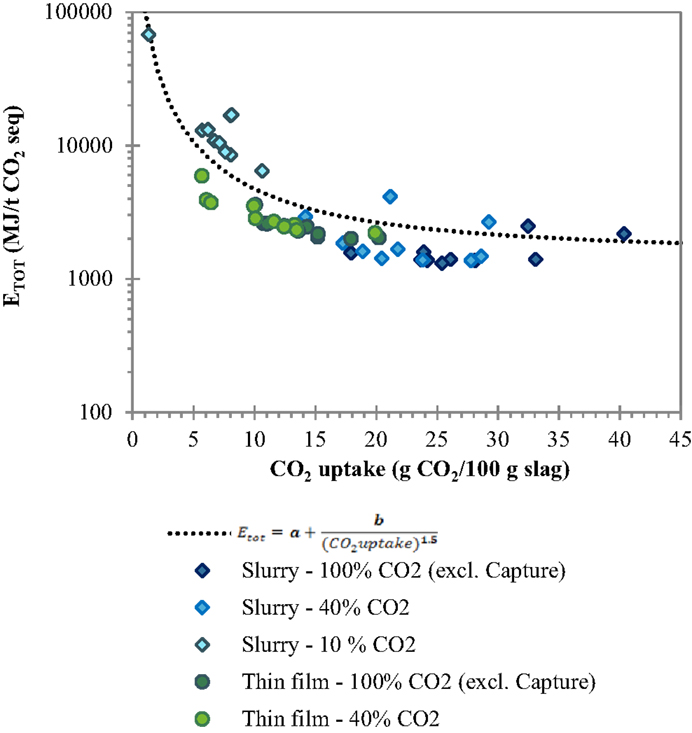
Figure 7. Trend of total energy requirement ETOT of the slurry-phase and thin-film routes as a function of the carbonation yield.
Conclusion
In this study, the possibility of directly storing the CO2 contained in diluted gas flows so to skip the energy intensive capture step was assessed by accelerated carbonation of BOF steelmaking slags both via slurry-phase and thin-film route batch scale experiments. For the slurry-phase route, maximum CO2 uptakes ranged from around 8% at 10% CO2 to 21.1% (BOF-a) and 29.2% (BOF-b) at 40% CO2 and 32.5% (BOF-a) and 40.3% (BOF-b) at 100% CO2. For the thin-film route, maximum uptakes of 13% (BOF-c) and 19.5% (BOF-d) at 40% CO2, and 17.8% (BOF-c) and 20.2% (BOF-d) at 100% were attained. The slurry-phase route hence showed to yield significantly higher uptakes than the thin-film route. However, it should be noted that this second process operates at lower temperature and makes use of significantly less water than the former one. Hence, the overall performance of these two routes was assessed also in terms of their total energy requirements on the basis of the energy demand of each their unit operations. The results of this evaluation indicated that working with a 40%-CO2 effluent turned out to be the most energy efficient carbonation strategy for BOF steelmaking slag, at least under the experimental conditions tested, applying either the slurry-phase or the thin-film route. For the slurry-phase process the most suitable conditions in terms of specific energy requirements were found for both slag samples tested at a carbonation time of 2 h, and implied a total energy duty of for BOF-a and BOF-b slag samples, respectively. For the thin-film route, the lowest energy requirements were obtained for the highest reaction times tested ( after 24 h for BOF-c and BOF-d slag samples, respectively), although especially for BOF-d slags these values were not far from the ones estimated even for lower reaction times. In this respect it should be considered that for an industrial-scale application of carbonation, regardless of the type of process route selected, the reaction time should be limited to 1–2 h. Another interesting finding of this work was that the total energy requirement for both types of routes regardless of the specific properties of the residues and the operating conditions tested showed to be directly related to the CO2 uptake of the slag. Hence, in conclusion the results of this study suggest that accelerated carbonation of BOF steel slag may be applied as a process to directly store the CO2 content of diluted gas flows such as syngas or biogas. The most promising reaction route (from an energy requirement perspective) appeared to be the slurry-phase one. However, an overall assessment of the carbonation process should also take into account that the higher CO2 sequestration performance attained by the slurry-phase route may be counterbalanced by an increased process complexity and the production of a final liquid effluent that needs further treatment prior to discharge. For this reason, prior to the selection of a specific reaction route, additional evaluations that take into consideration the potential environmental impacts of the process through a life cycle approach, as well as technical and economic aspects, are required.
Author Contributions
RB contributed to the paper starting from the conception and design of the study to the analysis and interpretation of the results. In addition he carried out the critical revision of the final manuscript. GC contributed to the paper starting from the conception and design of the study to the carrying out of the wet route carbonation experiments and interpretation and analysis of the results. AP and RP contributed to the paper starting from the conception and design of the study to the analysis and interpretation of the results. In addition they prepared the draft manuscript. AS carried out the slurry-phase experiments and contributed in the analysis and interpretation of the data. DZ contributed to the paper starting from the conception and design of the study to the analysis of the energy requirements and interpretation of the results.
Conflict of Interest Statement
The authors declare that the research was conducted in the absence of any commercial or financial relationships that could be construed as a potential conflict of interest.
Supplementary Material
The Supplementary Material for this article can be found online at https://www.frontiersin.org/article/10.3389/fenrg.2015.00056/full
References
Baciocchi, R., Costa, G., Di Bartolomeo, E., Polettini, A., and Pomi, R. (2010). Carbonation of stainless steel slag as a process for CO2 storage and slag valorization. Waste Biomass Valor. 1, 467–477. doi: 10.1007/s12649-010-9047-1
Baciocchi, R., Costa, G., Di Bartolomeo, E., Polettini, A., and Pomi, R. (2011). Wet versus slurry carbonation of EAF steel slag. Greenhouse Gases Sci. Technol. 1, 312–319. doi:10.1002/ghg.38
Baciocchi, R., Costa, G., Di Gianfilippo, M., Polettini, A., Pomi, R., and Stramazzo, A. (2015). Thin-film versus slurry-phase carbonation of steel slag: CO2 uptake and effects on mineralogy. J. Hazard. Mater. 283, 302–313. doi:10.1016/j.jhazmat.2014.09.016
Baciocchi, R., Costa, G., Polettini, A., and Pomi, R. (2009). Influence of particle size on the carbonation of stainless steel slag for CO2 storage. Energy Procedia 1, 4859–4866. doi:10.1016/j.egypro.2009.02.314
Baciocchi, R., Costa, G., and Zingaretti, D. (2014). “Accelerated carbonation processes for carbon dioxide capture, storage and utilization,” in Transformation and Utilization of Carbon Dioxide, Green Chemistry and Sustainable Technology, eds B. M. Bhanage and M. Arai (Berlin: Springer-Verlag). p. 263–299.
Bobicki, E. R., Liu, Q., Xu, Z., and Zeng, H. (2012). Carbon capture and storage using alkaline industrial wastes. Prog. Energy Combust. Sci. 38, 302–320. doi:10.1016/j.pecs.2011.11.002
Chang, E. E., Pan, S. Y., Chen, Y. H., Tan, C. S., and Chiang, P. C. (2012). Accelerated carbonation of steelmaking slags in a high-gravity rotating packed bed. J. Hazard. Mater. 22, 97–106. doi:10.1016/j.jhazmat.2012.05.021
Costa, G., Baciocchi, R., Polettini, A., Pomi, R., Hills, C. D., and Carey, P. J. (2007). Current status and perspectives of accelerated carbonation processes on municipal waste combustion residues. Environ. Monit. Assess. 135, 55–75. doi:10.1007/s10661-007-9704-4
Huijgen, W. J. J., Witkamp, G. J., and Comans, R. N. J. (2005). Mineral CO2 sequestration by steel slag carbonation. Environ. Sci. Technol. 39, 9676–9682. doi:10.1021/es050795f
Huijgen, W. W. J., Witkamp, G. J., and Comans, R. N. J. (2006a). Mechanisms of aqueous wollastonite carbonation as a possible CO2 sequestration process. Chem. Eng. Sci. 61, 4242–4251. doi:10.1016/j.ces.2006.01.048
Huijgen, W. J. J., Ruijg, G. J., Comans, R. N. J., and Witkamp, G. J. (2006b). Energy consumption and net CO2 sequestration of aqueous mineral carbonation. Ind. Eng. Chem. Res. 45, 9184–9194. doi:10.1021/ie060636k
Intergovernmental Panel on Climate Change (IPCC). (2005). IPCC Special Report on Carbon Dioxide Capture and Storage. Cambridge, UK: Cambridge University Press.
Kelly, K. E., Silcox, G. D., Sarofim, A. F., and Pershing, D. W. (2011). An evaluation of ex situ, industrial-scale, aqueous CO2 mineralization. Int. J. Greenhouse Gas Control 5, 1587–1595. doi:10.1016/j.ijggc.2011.09.005
Kirchofer, A., Brandt, A., Krevor, S., Prigiobbe, V., and Wilcox, J. (2012). Impact of alkalinity sources on the life-cycle energy efficiency of mineral carbonation technologies. Energy Environ. Sci. 5, 8631–8641. doi:10.1039/C2EE22180B
Lackner, K. S., Wendt, C. H., Butt, D., Joyce, E. L. Jr., and Sharp, D. H. (1995). Carbon dioxide disposal in carbonate minerals. Energy 20, 1153–1170. doi:10.1016/0360-5442(95)00071-N
Mattila, H. P., Wyrsta, M. D., and Zevenhoven, R. (2014). Reduced limestone consumption in steel manufacturing using a pseudo-catalytic calcium lixiviant. Energy Fuels 28, 4068–4074. doi:10.1021/ef5007758
Morone, M., Costa, G., Polettini, A., Pomi, R., and Baciocchi, R. (2014). Valorization of steel slag by a combined carbonation and granulation treatment. Miner. Eng. 59, 82–90. doi:10.1016/j.mineng.2013.08.009
O’Connor, W. K., Dahlin, D. C., Rush, G. E., Gerdemann, S. J., Penner, L. R., and Nilsen, D. N. (2005). Aqueous Mineral Carbonation: Mineral Availability, Pretreatment, Reaction Parametrics, and Process Studies. Report DOE/ARC-TR-04−002. Albany, OR: Albany Research Center.
Pan, S. Y., Chang, E. E., and Chiang, P. C. (2012). CO2 capture by accelerated carbonation of alkaline wastes: a review on its principles and applications. Aerosol Air Qual. Res. 12, 770–791. doi:10.4209/aaqr.2012.06.0149
Santos, R. M., François, D., Mertens, G., Elsen, J., and Van Gerven, T. (2013a). Ultrasound-intensified mineral carbonation. Appl. Therm. Eng. 57, 154–163. doi:10.1016/j.applthermaleng.2012.03.035
Santos, R. M., Van Bouwel, J., Vandevelde, E., Mertens, G., Elsen, J., and Van Gerven, T. (2013b). Accelerated mineral carbonation of stainless steel slags for CO2storage and waste valorization: effect of process parameters on geochemical properties. Int. J. Greenhouse Gas Control 17, 32–45. doi:10.1016/j.ijggc.2013.04.004
Sipilä, S., Teir, S., and Zevenhoven, R. (2008). Sequestration by Mineral Carbonation, Literature Review Update 2005-2007. Report VT 2008-1. Turku: Åbo Akademi University Faculty of Technology Heat Engineering Laboratory.
Uibu, M., Kuusik, R., Andreas, L., and Kirsimäe, K. (2011). The CO2-binding by Ca-Mg silicates by direct aqueous carbonation of oil shale ash and steel slag. Energy Procedia 4, 925–932. doi:10.1016/j.egypro.2011.01.138
Keywords: CO2 capture and storage, mineral carbonation, steel slags, energy requirements, fluegas
Citation: Baciocchi R, Costa G, Polettini A, Pomi R, Stramazzo A and Zingaretti D (2016) Accelerated Carbonation of Steel Slags Using CO2 Diluted Sources: CO2 Uptakes and Energy Requirements. Front. Energy Res. 3:56. doi: 10.3389/fenrg.2015.00056
Received: 19 October 2015; Accepted: 17 December 2015;
Published: 18 January 2016
Edited by:
Jennifer Wilcox, Stanford University, USAReviewed by:
Anozie Ebigbo, Imperial College London, UKHannu-Petteri Mattila, Åbo Akademi University, Finland
Copyright: © 2016 Baciocchi, Costa, Polettini, Pomi, Stramazzo and Zingaretti. This is an open-access article distributed under the terms of the Creative Commons Attribution License (CC BY). The use, distribution or reproduction in other forums is permitted, provided the original author(s) or licensor are credited and that the original publication in this journal is cited, in accordance with accepted academic practice. No use, distribution or reproduction is permitted which does not comply with these terms.
*Correspondence: Renato Baciocchi, baciocchi@ing.uniroma2.it