- 1School of Engineering, University of Birmingham, Edgbaston, United Kingdom
- 2Nippon Koei Ltd., Tokyo, Japan
Introduction
Railway sleepers (also called “railroad ties” in North America) are safety-critical components of ballasted railway tracks and the embedded type of ballastless tracks (Australian Standard: AS1085.14, 2003; Griffin et al., 2014). In addition, other types of sleepers that are used in other special locations are often termed differently to acknowledge the special conditions. For example, railway bearers are used to define the crossties used in railway turnouts (or switches and crossings). Railway transom or bridge beams are terms often used to refer to the flexural members used over the railway bridges (without a ballast top). Despite the fact that the support and boundary conditions are different, the critical duties of railway sleepers, bearers and transoms are identical: (i) to redistribute dynamic loads from the rail foot to the underlying ballast bed; and (ii) to maintain the rail gauge for safe passages of trains (Neilsen, 1991; Cai, 1992; Grassie, 1995; Kaewunruen and Remennikov, 2006). These functions demonstrate the criticality for safety of rail operations. If they are sufficiently damaged, trains can derail.
In recent years, composite materials have gained momentum in the railway industry. However, there is not much of a track record on their performance. This is probably because there are so many types of composite materials: some perform well but many do not (Kaewunruen, 2014; Kaewunruen et al., 2017; Silva et al., 2017). For example, “fiber-reinforced foamed urethane (FFU)” composites have been used as turnout bearers and embedded sleepers in Australia, Japan, UK, Germany and other places around the world for just over 40 years (Sengsri et al., 2020a). In contrast, “CarbonLoc composite” (with steel reinforcement) has been used as bridge transoms in Australia for a few years. With these in mind, there has been an effort to develop a brand-new ISO standard (ISO 12856) for standard test specifications of polymeric composite sleepers (with the scope to cover sleepers, bearers, and transoms). The draft standard has now been made available for a technical review.
The aim of this paper is to highlight the test criteria with respect to the design and actual in situ behaviors of composite sleepers in track systems. As a case study, full-scale experiments to investigate the test load behaviors of full-scale “fiber-reinforced foamed urethane (FFU)” sleepers have been adopted from very recent investigations. Influences of the standardized support conditions are highlighted in this paper. Comparative studies with in situ behaviors of composite sleepers in a ballasted railway are illustrated in order to improve the insight into the benchmarking of the ISO standard's test specification criteria.
Finite Element Analyses
It is commonly known that the two-dimensional Timoshenko beam model is the most suitable option for 2D modeling of concrete sleepers (Neilsen, 1991; Cai, 1992; Grassie, 1995; Griffin et al., 2014). Using a general-purpose finite element package STRAND7 (G+D Computing, 2001), the numerical model includes the beam elements, taking into account shear and flexural deformations, for modeling the composite sleeper. An industry-standard rectangular cross-section of 0.16 × 0.26 m is assigned to the composite sleeper elements. In this investigation, the finite element model of a composite sleeper has been previously developed and calibrated against both experimental static and dynamic results. The previous experimental results of full-scale composite sleepers (Sato et al., 2007; Sengsri et al., 2020a,b) show that the composite sleeper is likely to have a brittle failure mode with large deformation before failure. Under dynamic loading conditions, the first bending mode in a vertical plane of a composite sleeper clearly dominates the first resonant mode of vibration under a free-free condition (Sengsri et al., 2020b). Also, the dynamic modal parameters of the composite sleeper are reduced when damages occur. As a result, they reduce with damage severity (Sengsri et al., 2020b). The linear static solver is thus used in this study. The elastic modulus of the composite is set as 8.1 GPa with the density of 740 kg/m3. In this model, the full length of the sleeper is 2.5 m. The length between two rigid supports (Lc) is 1.5 m.
Since the ISO standard (ISO 12856) has been drafted without sufficient clarification for test methods for center-section under negative load test, this study compares the ISO test arrangement with an existing test method complied with the Australian Standard: AS1085.14 (2003). It is noted that the Australian Standard: AS1085.14 (2003) has prescribed the test method for evaluating the bending moments for both railway sleepers and bearers. Although the most critical loading conditions on the track systems are related to wheel impacts, the current design procedure takes the dynamic effects into account by using a dynamic load factor and treats the wheel burden as a quasi-static load (Remennikov and Kaewunruen, 2007). In practice, the wheel load generally imparts the positive bending moment at the railseat whilst providing the negative bending moment at mid span of the railway sleepers. To obtain comparable insights into a test method for the center section under a negative load test, this study considers four different load arrangements in accordance with (i) draft ISO standard provision, (ii) Australian standard provision, (iii) simulated ballast support as a uniform distributed load, and (iv) freshly tamped ballast condition simulated by a partial distributed load (illustrated in Table 1). It should be noted that the negative reference test load (FC, N) at the center section of the sleeper is chosen to be 100 kN for benchmarking purposes. This could imply that a rail seat force is 50 kN.
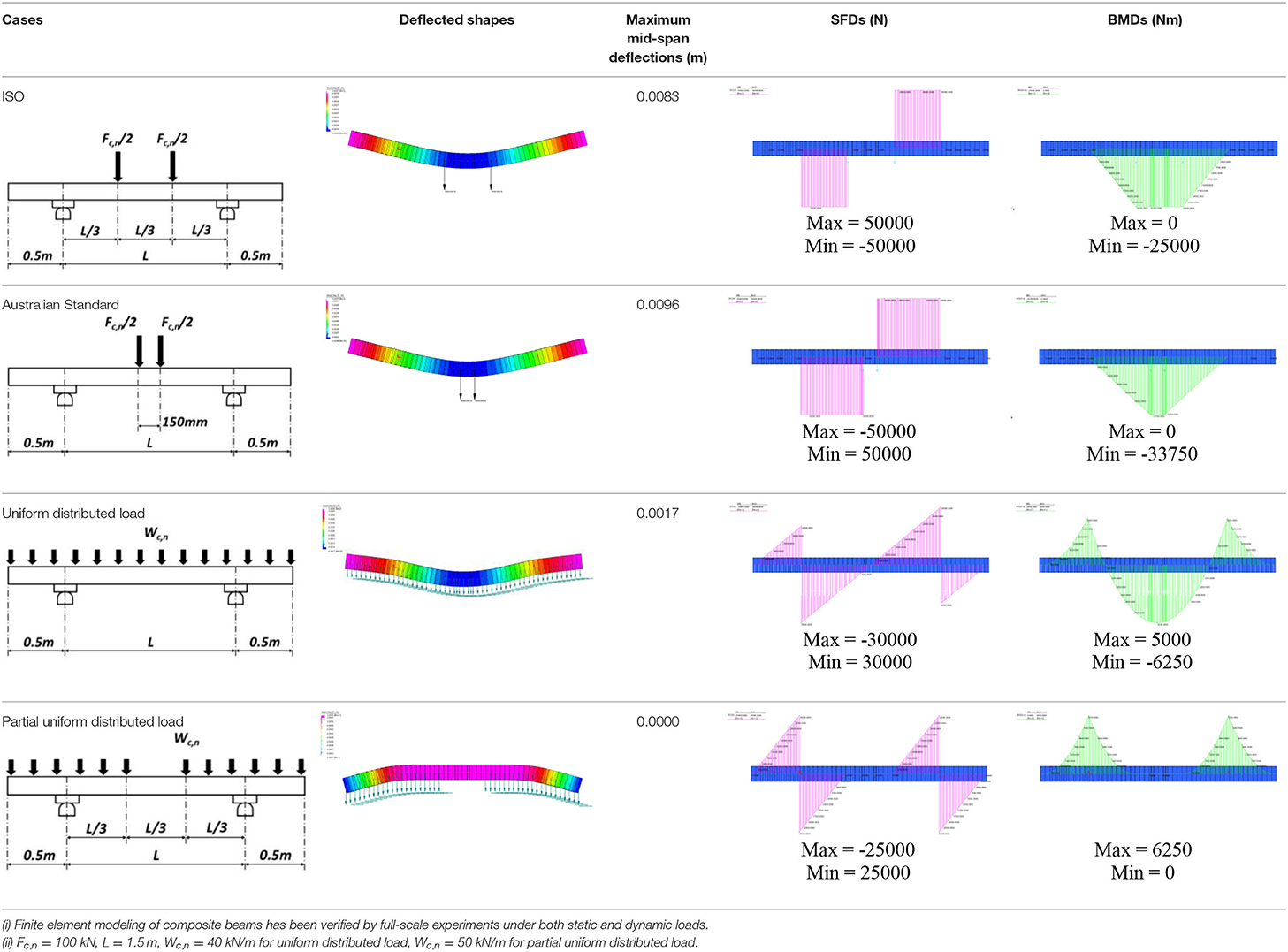
Table 1. Comparisons of test methods and resultant responses (deflection, shear force, and bending moment).
Firstly, according to the ISO standard provision, two-point loads (50 kN each) are applied with the distance of Lc/3 (500 mm in this case) in between the two-point loads. Secondly, the distance between two-point loads are reduced to 150 mm to comply with the Australian Standard. Thirdly, the uniform distributed load of 40 kN/m (equivalent to a total of 100 kN point load) is applied to reflect the full redistribution condition of ballast support (this condition represents poor track maintenance). However, in the railway industry, a proper ballast tamping and packing enable the partial support condition in practice. These activities can affect the flexural response of railway sleepers subjected to a spectrum of ballast stiffnesses including the asymmetrical ballast condition (Kaewunruen and Remennikov, 2007a,b, 2009; Shokrieh and Rahmat, 2007; Kaewunruen et al., 2016) and thus the uniform distributed load at mid-span is removed by the length of Lc/3 in the last case to reflect this condition (as recommended by AS1085.14). The comparative results presented in Table 1 include deflected shape, maximum deflection at mid span, Shear Force Diagram (SFD) and Bending Moment Diagram (BMD).
Discussion
The finite element analyses exhibit critical static effects stemmed from a variety of boundary conditions (representing test methods and ballast conditions). The effects of support conditions together with ballast conditions on the static flexural behaviors of composite sleepers are highlighted for comparison. Under the conditions specified by standards (ISO 12856 and AS1085.14), the results clearly show that the bending moment resultants are affected by the spacing between load arms (Fc, n/2). The ISO standard test method tends to yield a lesser bending moment by 35%, implying that component testing by AS1085.14 method is more efficient. In addition, there was a myth that the standard test methods could offer a situation close to in situ ballasted conditions. When considering the deflected shapes, it is evident that none of standardized test methods can completely mimic in situ behaviors. This new finding is aligned well with other studies (Reiff et al., 2007; McHenry et al., 2008; Davis et al., 2009; Tangtragulwong et al., 2011; Kaewunruen et al., 2018; McHenry and Gao, 2018; Qian et al., 2019). When considering the purpose of performance benchmarking, it is apparent that the Australian test setup condition (AS1085.14) can better represent the hogging deformations at the mid span than the test provision of ISO standard (ISO 12856). The insight into the bending moment resultants is very critical for track engineers and test engineers, who should be aware that the results obtained from standard test methods should be interpreted with cautions.
Composite materials have recently gained significant attention for applications in railway industry. In recent practice, composite sleepers and bearers have been used for bespoke replacements of aged timber components in critical areas such as switches and crossings, bridge transom sleepers, and special locations with either stiffness or clearance constraints. A new ISO standard has been drafted to accommodate the need to carry out standardized tests to benchmark the performance of polymeric composite sleepers and bearers. This study highlights the test specifications in order to illustrate the profound insight into the test methods for polymeric composite sleepers in comparison with in situ conditions in real life situations. This study explores the effectiveness of the provision in the current design code for bending test methods under various support conditions. The results clearly demonstrate that the test methods cannot fully represent in situ track conditions.
Author Contributions
SK, CN, and PS developed the concept and validated the work. MI advised on ISO standard matter. All authors contributed to the article and approved the submitted version.
Conflict of Interest
MI is the convenor of ISO standard committee for composite sleepers and is working with Nippon Koei Ltd.
The remaining authors declare that the research was conducted in the absence of any commercial or financial relationships that could be construed as a potential conflict of interest.
Acknowledgments
The first author is sincerely grateful to the Australian Academy of Science and the Japan Society for the Promotion of Sciences for his Invitation Research Fellowship (Long-term), Grant No. JSPS-L15701 at the Railway Technical Research Institute and the University of Tokyo, Japan. The authors also wish to thank to the European Commission for the financial sponsorship of the H2020-RISE Project No. 691135 RISEN: Rail Infrastructure Systems Engineering Network, which enables a global research network that tackles the grand challenge of railway infrastructure resilience and advanced sensing in extreme environments (www.risen2rail.eu). The APC is kindly sponsored by Frontiers' Authors Assistance Scheme.
References
Australian Standard: AS1085.14 (2003). Railway Track Material - Part 14: Prestressed Concrete Sleepers. Sydney, NSW: Standards Australia.
Cai, Z. (1992). Modelling of Rail Track Dynamics and Wheel/Rail Interaction (Ph.D. thesis). Department of Civil Engineering, Queen's University, Kingston, Canada.
Davis, D. D., LoPresti, J., Li, D., Otter, D. E., and Maal, L. (2009). “Evaluation of improved track components under heavy axle loads,” in Proceedings - 9th International Heavy Haul Conference: “Heavy Haul and Innovation Development” (Shanghai), 258–266.
G+D Computing (2001). Using Strand7: Introduction to the Strand7 Finite Element Analysis System. Sydney: G+D Computing.
Grassie, S. L. (1995). Dynamic modelling of concrete railway sleepers. J. Sound Vibrat. 187, 799–813. doi: 10.1006/jsvi.1995.0564
Griffin, D. W. P., Mirza, O., Kwok, K., and Kaewunruen, S. (2014). Composite slabs for railway construction and maintenance: a mechanistic review. IES J. Part A Civil Struct. Eng. 7, 243–262. doi: 10.1080/19373260.2014.947909
Kaewunruen, S. (2014). Monitoring in-service performance of fibre-reinforced foamed urethane material as timber-replacement sleepers/bearers in railway urban turnout systems. Struct. Monit. Maint. 1, 131–157. doi: 10.12989/smm.2014.1.1.131
Kaewunruen, S., Ishida, T., and Remennikov, A. M. (2016). Impact analyses for negative flexural responses (hogging) in railway prestressed concrete sleepers. J. Phys. Conf. Ser. 744:012101. doi: 10.1088/1742-6596/744/1/012101
Kaewunruen, S., Ngamkhanong, C., Papaelias, M., and Roberts, C. (2018). Wet/dry influence on behaviors of closed-cell polymeric cross-linked foams under static, dynamic and impact loads. Construct. Buil. Mater. 187, 1092–1102. doi: 10.1016/j.conbuildmat.2018.08.052
Kaewunruen, S., and Remennikov, A. M. (2006). Sensitivity analysis of free vibration characteristics of an in-situ railway concrete sleeper to variations of rail pad parameters. J. Sound Vibrat. 298, 453–461. doi: 10.1016/j.jsv.2006.05.034
Kaewunruen, S., and Remennikov, A. M. (2007a). Effect of improper ballast packing/tamping on dynamic behaviours of on-track railway concrete sleeper. Int. J. Struct. Stabil. Dyn. 7, 167–177. doi: 10.1142/S0219455407002174
Kaewunruen, S., and Remennikov, A. M. (2007b). Investigation of free vibrations of voided concrete sleepers in railway track system. J. Rail Rapid Transit 221, 495–508. doi: 10.1243/09544097JRRT141
Kaewunruen, S., and Remennikov, A. M. (2009). Influence of ballast conditions on flexural responses of railway concrete sleepers. Conc. Aust. J. Conc. Inst. Aust. 35, 57–62. Available online at: https://works.bepress.com/sakdirat_kaewunruen/51/
Kaewunruen, S., You, R., and Ishida, M. (2017). Composites for timber-replacement bearers in railway switches and crossings. Infrastructures 2:13. doi: 10.3390/infrastructures2040013
McHenry, M., and Gao, Y. (2018). “AAR and FRA research on polymer composite tie design and testing recommendations,” in UIUC Tie and Fastener Symposium. Available online at: https://railtec.web.illinois.edu/wp/wp-content/uploads/pdf-archive/5.1_McHenry.pdf (accessed August 23, 2020).
McHenry, M., Gao, Y., and Baillargeon, J. P. (2008). “Implementing improved composite tie design and testing guidelines into the AREMA Manual for railway engineering,” in AREMA 2018 Annual Conference and Exposition. Available online at: https://railtec.illinois.edu/wp/wp-content/uploads/Implementing-Improved-Composite-Tie-Design-and-Testing-Guidelines.pdf (accessed August 23, 2020).
Neilsen, J. C. O. (1991). Eigenfrequencies and eigenmodes of beam structures on an elastic foundation. J. Sound Vibrat. 145, 479–487. doi: 10.1016/0022-460X(91)90115-Z
Qian, Y., Dersch, M., Gao, Z., and Edwards, J. R. (2019). Railroad infrastructure 4.0: Development and application of an automatic ballast support condition assessment system. Transport. Geotech. 19, 19–34. doi: 10.1016/j.trgeo.2019.01.002
Reiff, R., Joy, R., and Sullivan, H. (2007). Non-destructive testing of plastic and composite ties. Railway Track Struct. 103, 20–22.
Remennikov, A. M., and Kaewunruen, S. (2007). A review on loading conditions for railway track structures due to wheel and rail vertical interactions. Struct. Control Health Monit. 15, 207–234. doi: 10.1002/stc.227
Sato, M., Kanie, S., and Mikami, T. (2007). Structural modeling of beams on elastic foundations with elasticity couplings. Mech. Res. Commun. 34, 451–459. doi: 10.1016/j.mechrescom.2007.04.001
Sengsri, P., Ngamkhanong, C., de Melo, A. L. O., and Kaewunruen, S. (2020b). Experimental and numerical investigations into dynamic modal parameters of fiber-reinforced foamed urethane composite beams in railway switches and crossings. Vibration 3, 174–188. doi: 10.3390/vibration3030014
Sengsri, P., Ngamkhanong, C., Melo, A. L. O., Papaelias, M., and Kaewunruen, S. (2020a). Damage detection in fiber-reinforced foamed urethane composite railway bearers using acoustic emissions. Infrastructures 5:50. doi: 10.3390/infrastructures5060050
Shokrieh, M. M., and Rahmat, M. (2007). Effects of Young's modulus on response of railway sleeper. Appl. Math. Model. 31, 700–711. doi: 10.1016/j.apm.2005.12.004
Silva, E. A., Pokropski, D., You, R., and Kaewunruen, S. (2017). Comparison of structural design methods for railway composites and plastic sleepers and bearers. Aust. J. Struct. Eng. 18, 160–177. doi: 10.1080/13287982.2017.1382045
Keywords: railway composite sleeper, bearers, transoms, bending test methods, ISO standard, Australian Standard
Citation: Kaewunruen S, Ngamkhanong C, Sengsri P and Ishida M (2020) On Hogging Bending Test Specifications of Railway Composite Sleepers and Bearers. Front. Built Environ. 6:592014. doi: 10.3389/fbuil.2020.592014
Received: 06 August 2020; Accepted: 22 September 2020;
Published: 11 November 2020.
Edited by:
Sanjay Shrawan Nimbalkar, University of Technology Sydney, AustraliaReviewed by:
Ruilin You, China Academy of Railway Sciences, ChinaTing Li, Southwest Jiaotong University, China
John Riley Edwards, University of Illinois at Urbana-Champaign, United States
Copyright © 2020 Kaewunruen, Ngamkhanong, Sengsri and Ishida. This is an open-access article distributed under the terms of the Creative Commons Attribution License (CC BY). The use, distribution or reproduction in other forums is permitted, provided the original author(s) and the copyright owner(s) are credited and that the original publication in this journal is cited, in accordance with accepted academic practice. No use, distribution or reproduction is permitted which does not comply with these terms.
*Correspondence: Sakdirat Kaewunruen, cy5rYWV3dW5ydWVuQGJoYW0uYWMudWs=; Makoto Ishida, aXNoaWRhLW1rQG4ta29laS5qcA==