- Shenzhen Key Laboratory of Cross-scale Manufacturing Mechanics, SUSTech Institute for Manufacturing Innovation, Department of Mechanics and Aerospace Engineering, Southern University of Science and Technology, Shenzhen, Guangdong, China
Precision glass molding (PGM) enables high-accuracy, efficient production of complex optical components, yet interfacial adhesion between mold and glass surfaces remains a significant barrier, impacting both quality and mold durability. This review comprehensively examines the factors influencing adhesion behavior, including the roles of material selection, surface wettability, process parameters, and thermodynamic principles in defining interfacial performance. Through a detailed analysis of anti-adhesion materials and optimized process strategies, such as controlled temperature, pressure, and atmospheric conditions, this work elucidates mechanisms that mitigate adhesion and extend mold life. Thermodynamic modeling, including work of adhesion calculations, provides a quantitative foundation for predicting interfacial behavior, offering guidance for material and process optimization in PGM applications. The findings provide a multi-dimensional framework for addressing adhesion challenges in PGM, setting the stage for enhanced efficiency and quality in precision optics manufacturing.
1 Introduction
Glass lenses are essential components in advanced optical systems, commonly shaped into aspheres, freeform surfaces, and microstructured arrays, and are widely applied in optical imaging, illumination systems, and fiber-optic communications (Yin et al., 2017; Tan et al., 2021; Hamed et al., 2023; Kim and Choi, 2021). They are indispensable in consumer products such as cameras, projectors, and telescopes, as well as in industrial applications like LiDAR, night vision, and optical metrology equipment. With the rising demand for high-precision optical lenses, the development of scalable production methods has become critical (Chernomyrdin et al., 2017; Cao et al., 2019; Xu et al., 2016). For example, in the semiconductor industry, key optical components require nanometer or sub-nanometer accuracy, maintaining flatness within 10 nm and profile accuracy within 100 nm across diameters of 150–300 mm (Senellart et al., 2017; Capasso, 2018; Li et al., 2014). Although conventional milling, grinding, and polishing methods can achieve spherical lenses at scale, they are limited for aspheric and irregular lenses, which require iterative dimensional and shape adjustments (Ghosh et al., 2018; Shimizu et al., 2021; Peng et al., 2021). This makes high-precision, large-size optical component production costly, complex, and highly dependent on operators’ skill. Further, the stringent accuracy requirements necessitate slow feed rates in mechanical processing, resulting in low throughput. For certain soft or brittle materials, these techniques may not be suitable, as they risk material deformation or fracture (Yuan et al., 2018; Chen et al., 2018; Lee et al., 2014; Vu et al., 2021). Ultra-precision equipment, essential for achieving the desired accuracy, is expensive and specialized, and tools used in ultra-precision grinding and turning suffer wear, requiring frequent replacement (Wang S. et al., 2023; Fei et al., 2020; Wang G. et al., 2024). These challenges make traditional machining a less suitable option for mass-producing small-aperture, high-repeatability, and low-cost optical components.
The emergence of precision glass molding has revolutionized glass processing by facilitating the production of complex surface structures and is now the leading technology for high-precision, small-aperture aspheric optics at low cost and high efficiency (Ming et al., 2020; Zhang and Liu, 2017; Zhou, et al., 2017; Shu et al., 2023; Asgar et al., 2021). As a rapid replication technology, PGM significantly reduces individual component cycle times to approximately 120 s once process parameters are defined (Kadono and Kitamura, 2022; Vieira, 2022). Using the principle of hot pressing, PGM exploits the behavior of glass in the supercooled liquid region, above its glass transition temperature (Tg), where softened glass is molded within a closed cavity to replicate the mold geometry precisely (Zhang L. et al., 2020; Zhang X. et al., 2019; Zhang et al., 2018). Figure 1 compares conventional and precision glass molding processes: PGM is a four-stage process, involving heating, pressing, cooling, and demolding, yielding a finished lens without additional processing, while conventional methods require multiple machining steps such as diamond turning, grinding, polishing, and final cleaning. PGM circumvents the need for further polishing or machining, enabling substantial reductions in both production time and costs.
However, the quality of molded lenses in PGM relies on numerous factors, such as the choice of mold and glass materials, mold quality, thermal deformation properties of the glass, and control of process parameters like temperature and pressure (Liu et al., 2021; Symmons et al., 2016). Even minor imperfections in each step of the PGM process can directly impact the surface quality and optical performance of the final product. The process involves complex thermodynamic deformations, with the glass viscosity changing in response to temperature, interacting with the stability of the mold coating, making process optimization challenging (Liu et al., 2022; Liu et al., 2023; Liu G. et al., 2017). Presently, this technology faces numerous scientific challenges, including the development of mold and coating materials, modeling glass behavior, optimizing process conditions, and achieving high-precision molding equipment (Xie et al., 2017; Huang, et al., 2020b). Among these, interfacial adhesion remains particularly challenging (Liu and Zhang, 2017; Huang et al., 2023; Kim et al., 2019). Adhesion can lead to surface scratches or residues during demolding, lowering optical transmission and imaging quality, while accelerating mold coating wear and reducing mold lifespan (Wang et al., 2019; Chizhik et al., 2020). Frequent mold replacement and downtime reduce production efficiency and increase maintenance costs, adding complexity to manufacturing. For high-precision optical components, even minor interfacial adhesion can significantly affect product yield, making it a critical bottleneck in PGM.
In response to the challenges posed by mold-glass interfacial adhesion, this review examines the development of adhesion-related issues, focusing on advances in mold, glass, and coating materials, process optimization, and the fundamental mechanisms of adhesion. Current challenges and limitations in adhesion control are discussed, with a further analysis of anti-adhesion mechanisms in PGM. Finally, this review explores the future outlook for PGM development.
2 Adhesion challenges
2.1 Mold and glass materials
The interaction between mold and glass materials fundamentally determines interfacial performance in PGM processes. The physical and chemical compatibility of these materials is crucial for controlling interfacial adhesion; thus, selecting appropriate materials for both mold and glass is an essential preliminary step in PGM (Sun F. et al., 2022; Vu et al., 2019; Bobba and Morgan, 2022; Vu et al., 2020). Mold materials must withstand numerous cycles of molding without degradation, resisting deformation, wear, and adhesion over thousands of molding cycles. Consequently, mold materials must meet stringent requirements. They need to have low reactivity with other elements, high machinability, excellent thermal conductivity, high hardness and robust fracture toughness. Moreover, mold materials must have a coefficient of thermal expansion (CTE) similar to that of the glass material or show minimal differences to minimize form deviation. These properties collectively ensure that mold materials exhibit low chemical reactivity and mechanical deformation under high temperatures, minimizing physical or chemical interactions with glass. This stability preserves the mold’s surface structure and geometry, extending its operational lifespan.
Common mold materials, such as NiP, Si, Si3N4, SiC, WC, Zr–Si–N, and microcrystalline aluminum, are selected based on factors like machinability, operational temperature, and surface structural requirements (Friedrichs et al., 2019). Hard materials like WC and SiC offer excellent high-temperature performance and wear resistance, making them widely used in the mass production of precision glass optics. However, their high hardness also poses challenges for machining fine microstructural features. In contrast, Ni-P alloys—despite limitations such as lower hot hardness and reduced thermal stability—are often chosen for applications where detailed surface features and good tribological compatibility with certain glasses are required (Prater et al., 2016; Zhou et al., 2018a; Lee et al., 2018).
Given the necessity for anti-adhesion properties, protective coatings are often applied to extend mold life, becoming a standard practice in glass molding. Commonly used coatings include ceramic coatings (CrN, AlCrN, AlTiN), precious metal coatings (Pt/Ir, Re/Ir, Mo/Ru), and diamond-like carbon (DLC) (Saksena et al., 2021; Xie et al., 2021; Chen et al., 2020). Ceramic coatings provide high hardness and wear resistance but are prone to surface cracking after repeated high-temperature cycles, reducing their adhesion resistance over time. Precious metal coatings, with their chemical inertness and oxidation resistance, effectively mitigate chemical adhesion at high temperatures. However, these coatings are prone to wear under high loads, limiting their stability in prolonged applications. In contrast, DLC coatings exhibit an ultra-low friction coefficient (as low as 0.06) and excellent anti-adhesion and wear resistance, maintaining surface integrity in high-temperature, high-friction environments (Griffiths et al., 2016; Kim and Kim, 2022; Wang Z. F. et al., 2023). Therefore, selecting mold materials demands a balanced consideration of application requirements to minimize adhesion.
The properties of low-Tg glass used in PGM are also essential for interfacial adhesion behavior. Optical glass must transition to a plastic state below approximately 600 °C to meet molding requirements while remaining chemically inert to prevent irreversible reactions with the mold at high temperatures. Low-Tg and ‘short’ glasses are advantageous for glass molding because the molding temperature can be chosen at relatively low, as the process is commonly conducted near the softening temperature where viscosity is sufficiently low (Liu J. H. et al., 2017; Shu et al., 2022; Pallicity et al., 2017). Adhesion during molding not only causes scratches and residue on the glass surface but also damages mold coatings, shortening mold lifespan. This adhesion behavior results from the amorphous structure of glass, as illustrated in Figure 2A, where glass undergoes a continuous transition from a supercooled liquid to an amorphous solid upon cooling. In the Tg–Ts range, the glass exhibits viscoelastic behavior characterized by elastic deformation and viscous flow. This unique behavior, shown in Figure 2B, defines the forming temperature window for PGM, typically lies between Tg and the softening point Ts (∼106.6 Pa·s viscosity). Leading optical glass manufacturers, such as CDGM, HOYA, OHARA, SUMITA, and SCHOTT, produce glass tailored for PGM applications.
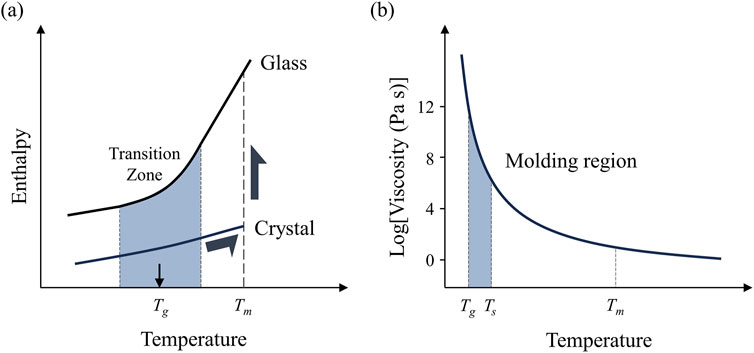
Figure 2. Glass property: (a) the glass enthalpy dependence on temperature, (b) typical viscosity-temperature curve.
Following material selection, high-precision lens production in PGM requires careful preparation of both mold and glass. Mold surfaces must achieve optical-grade roughness and dimensional accuracy through precision machining, while glass materials are prepared as preforms for molding. Since PGM forms the final shape in a single pressing step without subsequent polishing, the mold material must have a coefficient of thermal expansion closely matched to that of the glass to minimize form deviation. Additionally, the glass preforms are required to meet stringent specifications regarding cleanliness, surface roughness and bulk optical integrity—including homogeneity, absence of inclusions, and minimal residual stress—to meet requirements of the final optical components. The prepared mold and glass preform are then assembled in PGM equipment to produce the optical component.
2.2 Demolding process in PGM
The PGM process involves a series of well-defined thermal and mechanical stages designed to shape glass into optical components. As illustrated in Figure 3, the entire process comprises five consecutive steps: initial heating, soaking, pressing, controlled cooling and final demolding. In the first stage, the glass preform and mold are firstly heated to the required molding temperature, followed by a second phase of heat retention to ensure uniform temperature distribution. During the third stage, a defined pressure is applied, maintaining close contact between glass and mold surfaces for a specified period, enabling the glass to conform to the mold geometry. Subsequently, the glass is gradually cooled to approximately Tg, then rapidly cooled and demolded. The first cooling phase solidifies the glass, enabling a faster second cooling phase, which increases production efficiency.
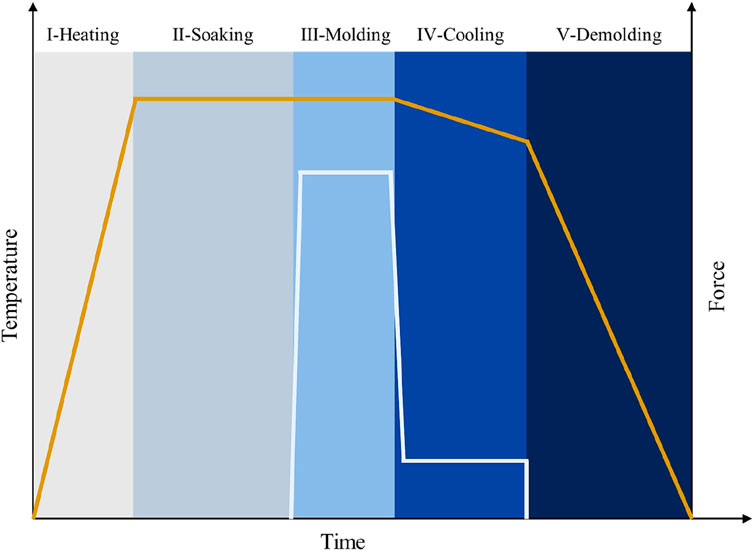
Figure 3. A typical molding cycle of PGM (Reproduced form (Zhang and Liu, 2017).
Interfacial adhesion manifests during demolding, leading to surface scratches, glass breakage, or mold coating damage. During demolding, glass undergoes a transition from a viscoelastic to a solid state in the Tg–Ts range, retaining some flowability. This characteristic means that if adhesion between the glass and mold is excessive during cooling and demolding, glass surface defects or mold damage can occur. However, demolding adhesion reflects the cumulative effects of each preceding process phase: heating and retention, pressing, and cooling. Specifically, during heating and retention, glass is brought to a viscoelastic state and adheres tightly to the mold. During pressing, excessive pressure or prolonged contact time increases the contact area, raising friction and intensifying adhesion. Any instability in the coating may trigger chemical reactions at high temperatures, exacerbating adhesion forces. During the cooling stage, demolding adhesion is primarily influenced by the cooling rate and interfacial compatibility between the mold and glass. A slower cooling rate extends the period during which the glass remains partially fluid, thereby enhancing the potential for physical or chemical bonding at the interface. Moreover, incompatible material properties, such as high wettability, can further facilitate adhesion. Hence, controlling adhesion during demolding requires precise regulation of process parameters, including the heating rate, retention time, molding temperature, applied pressure, cooling rate, final cooling temperature, demolding temperature, and rate.
2.3 Contact forces at the interface
During demolding in PGM, glass tends to adhere to the mold surface, primarily due to its viscoelastic properties, which cause increased molecular mobility and adhesion at high temperatures. When glass and mold surfaces are in close contact, molecular attraction creates adhesion-prone regions where material transfer is more likely, leading to physical adhesion at the interface. This tendency means that sections of the glass may remain attached to the mold surface, particularly under high interfacial contact forces. Three primary forces — adhesive force, frictional force, and thermal contraction stress — act on the interface (Pallicity et al., 2017; Li et al., 2022; Liu et al., 2021; Vu et al., 2024; Luo et al., 2022), each influencing demolding difficulty in distinct ways (Figure 4).
Adhesive force is the principal interfacial force between glass and mold, driven by molecular interactions at high temperatures. In the viscoelastic state, adhesive force increases with contact area, intensifying during cooling as glass transitions from a viscous to a solid state. Repeated molding and demolding operations gradually exert stress on the mold surface, potentially causing wear and delamination, especially if the mold is inadequately protected, allowing chemical reactions that accelerate surface damage (Guo et al., 2007). Frictional force, acting tangentially during demolding, impedes separation as the glass slides across the mold surface. This force is primarily influenced by mold surface roughness and coating friction coefficient. When glass cools and hardens, frictional force further resists tangential separation, particularly if microstructures on the mold surface intensify friction. Repeated friction exacerbates adhesion and may cause localized wear, especially with higher-friction materials. Thermal contraction stress arises from the differential thermal expansion between glass and mold materials, causing tensile or compressive stress at the interface during cooling. When cooling rates are uneven or thermal expansion differences are substantial, stress concentration at the glass-mold interface can become significant. Thermal contraction stress causes tighter adhesion at the interface, increasing adhesion and friction resistance. In micro-structured molds and arrayed lenses, edge or corner areas experience localized stress concentration, accelerating mold failure. These three forces collectively exacerbate demolding adhesion through distinct physical mechanisms, underscoring the need for a comprehensive approach to interfacial adhesion control.
3 Adhesion behaviors
3.1 Glass surface defects and mechanisms of formation
From an application perspective, adhesion-induced surface defects on molds and glass pose significant challenges to maintaining quality. On glass surfaces, these defects typically appear as micro-voids, scratches, waviness, and micro-bubbles. Under such conditions, gas can be trapped between glass and mold, leading to localized micro-void formation. As molding temperatures rise, trapped gases expand, increasing the number and size of these voids significantly. This defect issue becomes even more pronounced in ultra-thin glass molding, particularly with curved glass surfaces. For instance, studies on curved, ultra-thin glass have shown that higher forming temperatures facilitate glass flow and mold replication but also exacerbate adhesion, resulting in increased surface defects like micro-bubbles (Zhang et al., 2021). Although increased forming pressure can reduce bubble density, it simultaneously tightens the mold-glass contact, leading to defects such as waviness.
Defect formation mechanisms are actively explored to better understand the impact of adhesion on defect evolution. Studies on chalcogenide glasses show that adhesion strengthens at elevated temperatures, particularly when the mold surface exhibits significant roughness and the temperature distribution is uneven (Zhou, et al., 2017). Research on the formation and growth of micro-cavities at varying temperatures has identified several pathways, as depicted in Figure 5. The process is analyzed in three stages: (1) Transition from interfacial fracture to cohesive deformation: As the molding temperature rises, adhesion shifts from an interfacial fracture mode to cohesive deformation within the glass. At lower temperatures, adhesion occurs primarily at the glass-mold interface, creating shallow, disk-shaped micro-cavities. With increasing temperatures, however, the viscoelasticity of glass intensifies, causing adhesion to promote internal deformation, leading to deeper cavities. This transition indicates a shift in cavity formation, from interface crack propagation to local deformation within the glass. (2) Gas entrapment effects: Gas trapped at the glass-mold interface or within the glass expands during separation, leading to localized stress release, which promotes micro-cavity growth into larger, deeper defects. This suggests that the rate and manner of stress release during adhesion directly influence gas entrapment and cavity expansion. (3) Cavity growth and coalescence: Adhesion-induced cohesive deformation within the glass can create numerous small cavities that may coalesce over time, forming larger cavities as temperature and time progress. Under high-temperature conditions, enhanced viscoelasticity promotes stress concentration and material flow, which facilitates cavity expansion.
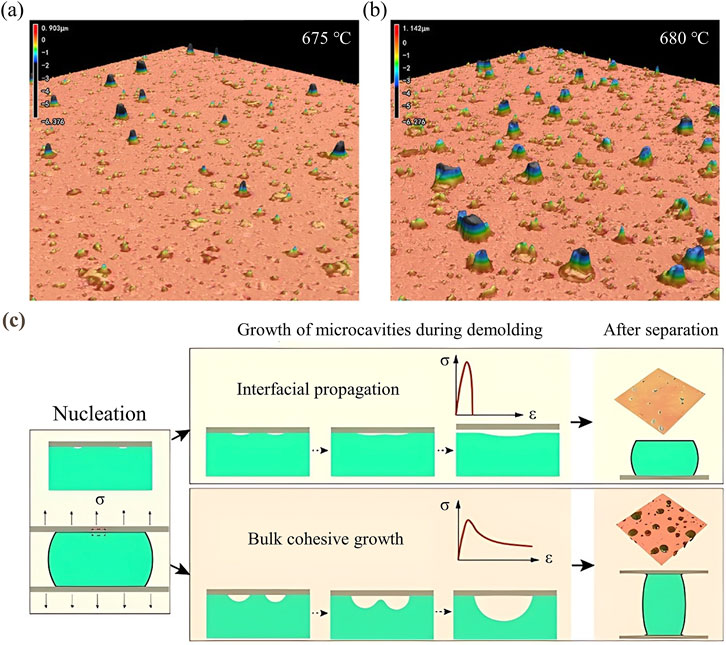
Figure 5. The 3D isometric back-view contours of microcavities for cohesive cases (a) 675°C, (b) 680°C, and (c) illustrative diagram showing bifurcation in microcavity growth (Reproduced from (Zhou et al., 2022)).
Adhesion-related surface defects have a multiscale impact on the optical and mechanical performance of molded glass components. At the microscale (less than 1 µm), adhesion creates nano-defects like micro-bubbles and micro-cavities that increase surface roughness, decreasing light transmittance and propagation efficiency. Increased surface roughness also amplifies light scattering, adversely affecting reflection and refraction properties, particularly in high-precision optics where imaging quality is critical. At the mesoscale (1–100 µm), adhesion-induced waviness, micro-cracks, and surface irregularities cause non-uniform refraction and scattering, leading to substantial optical distortion. These mesoscale defects prevent accurate focusing, reducing resolution and image clarity, which compromises imaging accuracy in optical devices. At the macroscale (greater than 100 µm), extensive deformation, cracking, or fracture due to adhesion compromises the structural integrity of the glass component (Youn et al., 2006). Such defects not only impair optical performance but also increase the likelihood of component failure in use, shortening product lifespan.
3.2 Mold adhesion patterns and damage mechanisms
Beyond affecting glass surface quality, adhesion in PGM processes poses critical risks to mold integrity. Adhesion patterns on mold surfaces exhibit varied morphology depending on material type and processing conditions (Zhu et al., 2015; Huang, et al., 2020a; Youn et al., 2006; Kim et al., 2020). The glass–mold interfacial adhesion on microgrooved surfaces is shown in Figure 6a, while Figures 6b,c demonstrate that the adhesion of ChG glass on Ni–P molds involves both physical and chemical interactions (Zhou et al., 2017a; Zhu et al., 2023). For PtIr-Ni coatings, the degradation process follows six stages, including sequential oxidation and gas evolution, leading to funnel-shaped ruptures, delamination due to adhesion loss, deep substrate corrosion, and glass crystallite accumulation on oxidized areas (Klocke et al., 2016). Open craters were observed in the PtIr-Ni layer, where significant amounts of tungsten and cobalt were detected. After the coating was compromised, its anti-adhesion performance declined, resulting in an increased friction coefficient and stronger glass adhesion to the coating surface. After 500 press cycles, the WC-Co molds exhibited adhesion characteristics with island oxides, randomly distributed on the surface at the micrometer scale (Chen and Wang, 2014). For the Cr28Si17N55 coating, after 100 thermal cycles, the adhesive regions observed under a light microscope had a diameter of 500 μm (Chen et al., 2020). Further SEM analysis revealed that when the coating adhered to the glass, it exposed the underlying hard metal substrate, resulting in coating failure. Additionally, WC molds pressed with D-FK95 flat glass displayed four distinct residual glass patterns between 450 °C and 535 °C: uniformly dispersed dots, island-like clusters, streaks, and layered coverage (Zhao et al., 2023). High temperatures enhance glass flowability, aligning residual glass distribution with flow direction, highlighting the influence of glass flow on adhesion patterns. B270® glass from Schott AG deposits as distinct dots on PtIr mold surfaces, while chalcogenide glass produces more mottled patterns (Friedrichs et al., 2020). In extreme cases, adhesion causes irregular damage to the coating layer, exposing the underlying mold substrate.
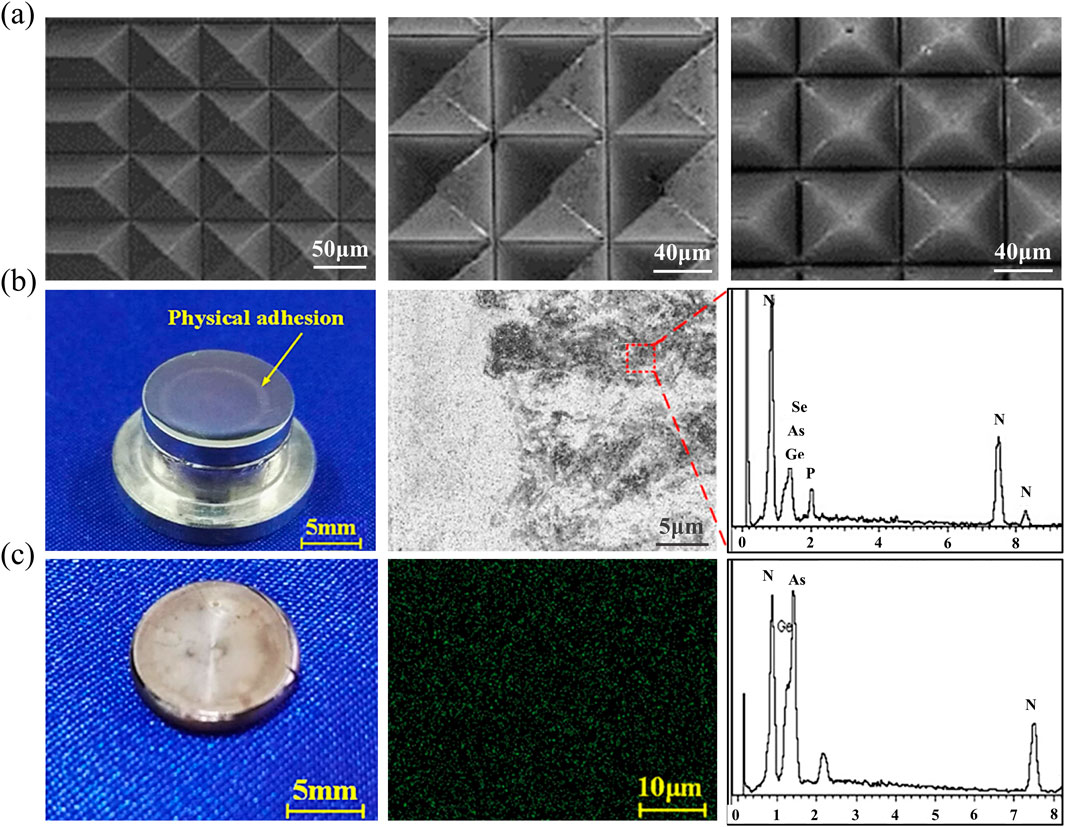
Figure 6. Adhesion morphologies and mechanisms of glass on different mold surfaces. (a) SEM images of micropyramidal structures, showing the mold surface before molding, after molding, and the corresponding molded glass from left to right, (b) characterization of the mold after compression, including optical image, microscopic observation, and EDS analysis revealing physical adhesion, (c) analysis of ChG glass after compression, including surface morphology, EDS mapping of Ni distribution, and elemental composition indicating chemical adhesion (Adapted with permission from Zhu et al. Study of interfacial adhesion and Re–Ir alloy coating in chalcogenide glass molding. Langmuir 2023, 39, 9924-9931. Copyright 2023 American Chemical Society.).
Different adhesion patterns contribute to mold damage through mechanisms such as stress concentration, oxidation reactions, and increased surface roughness. Stress concentration is a primary damage mechanism in mold edges and high-curvature regions, where adhesion tends to occur. For instance, thermal cycling tests with chalcogenide glass reveal that residual glass thickness correlates closely with mold surface stress concentration, increasing from 5 nm to 20 nm at high-stress regions (Zhou et al., 2018b). With repeated thermal cycles, adhesion exacerbates micro-crack growth and causes localized deformation and material degradation. Accumulated adhesion residue in high-stress areas intensifies damage, ultimately leading to localized mold failure.
Oxidation also plays a key role in mold damage. Oxidation alters surface chemistry, accelerating interactions between mold and glass, which expands the distribution and thickness of adhesion residue. Studies on Zr-Si-N coatings show that oxidation significantly increases adhesion coverage, particularly during repeated high-temperature cycles. On a Zr-Si-N coating with 20% Si content, glass residue thickness is approximately 5 nm, while uncoated molds exhibit up to 20 nm of residue (Chang et al., 2018). This difference primarily stems from the coating’s chemical inertness, which reduces oxidation reactions and adhesion. However, oxidation inevitably degrades the coating’s stability over time, increasing glass residue and mold surface damage.
Increased surface roughness also significantly contributes to mold damage. Rougher mold surfaces promote adhesion by increasing contact area and residue thickness. For instance, studies show that PtIr-coated molds with initial roughness of 10 nm undergo multiple thermal cycles at high temperatures (350°C–800°C), increasing surface roughness to over 100 nm, which amplifies residue coverage and thickness (Friedrichs et al., 2020). Under combined oxidative and mechanical stress, coatings gradually delaminate, concentrating adhesion residue in the delaminated areas. By reducing roughness (from Ra = 70 nm–30 nm), glass residue thickness decreases by over 50%, underscoring roughness control as a key factor in minimizing adhesion and extending mold life. Different materials exhibit unique adhesion-induced roughness progression; for example, Al2O3 coatings maintain roughness below Ra = 5 nm after 100 cycles, while uncoated molds reach Ra = 50 nm (Chien et al., 2012). Zr-Si-N coatings effectively prevent adhesion after 450 thermal cycles, maintaining residue thickness at just 5 nm, demonstrating strong anti-adhesion performance at high temperatures (Chen et al., 2020). The DLC-coated molds demonstrated superior surface stability compared to other coatings (Chen et al., 2023). Despite a gradual increase in surface roughness with repeated molding cycles, the roughness remained below 5 nm after 500 cycles (Figure 7a). Nonetheless, microscopic deposits were observed, mainly caused by glass adhesion and residual glass component streaks (Figure 7b).
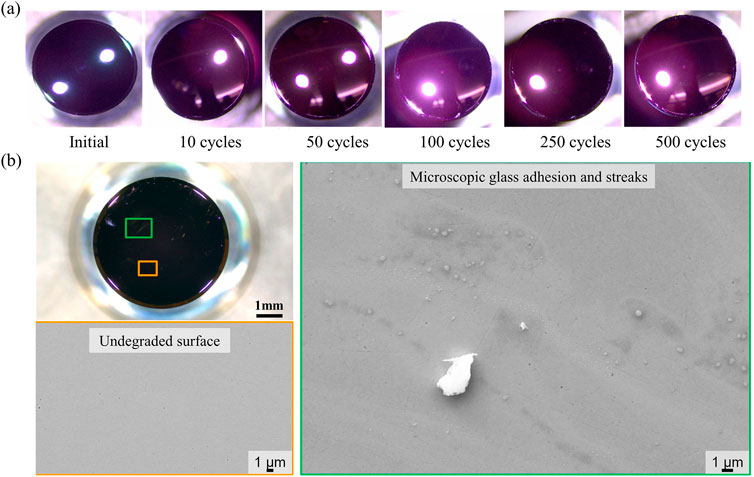
Figure 7. DLC-coated mold after cyclic testing. (a) Surface roughening observed on the mold surface and (b) SEM image showing degradation of the DLC coating after 500 molding cycles.
3.3 Adhesive forces and influencing factors
In PGM, adhesive force refers to the interfacial forces between glass and mold, primarily arising from molecular interactions, electrostatic forces, and possible chemical bonding. Unlike simple physical contact, the forming process subjects glass and mold to both chemical and mechanical forces, resulting in distinctive adhesion behavior. Adhesive force is commonly measured to characterize interfacial adhesion strength, with methods like pull-off and shear tests quantifying the force needed to separate glass and mold under controlled temperature, pressure, and interfacial conditions. Custom equipment is typically required, integrating load sensors to record adhesive force throughout the demolding process. Recently, new measurement techniques have emerged for adhesion research. For example, atomic force microscopy (AFM) enables micro-scale adhesion force analysis, allowing real-time data collection at the interface and providing insights into adhesion force dynamics at a finer scale (Han et al., 2009). Adhesive force quantification enables a better understanding of these interfacial interactions, aiding in adhesion mitigation strategies for production.
For planar glass-mold contact molding, adhesive force is defined as the counterforce detected at the glass-mold interface during demolding. Adhesion force profiles usually display an upward trend until they reach a maximum value, after which there is a sharp decline to zero, as observed in the region enclosed by the dashed-line circle in Figure 8a (Zhou et al., 2020). This initial rise corresponds to the interfacial adhesion stage, while the subsequent drop to zero indicates the complete separation of the interfaces. Moreover, the work done during the adhesion process can be computed by measuring the area beneath the force-displacement curves, as is evident from Figure 8b.
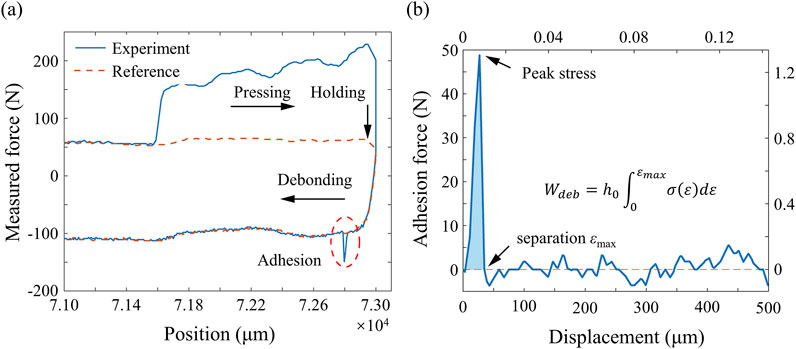
Figure 8. Adhesion force assessment: (a) The measured force plotted as a function of the bottom mold’s position, with a molding temperature of 655°C and a debonding velocity of 10 μm/s, (b) the adhesion force-displacement curve and the corresponding nominal stress-strain relationship.
Adhesive force magnitude is influenced by multiple factors, including temperature, pressure, mold material, surface roughness, and forming environment. Investigation into the effects of molding and demolding temperatures, as well as coating materials, remains a key focus (Zhang Y. et al., 2019; Ikeda et al., 2016). The measured demolding force for K-PSK200 glass increased from 0.5 MPa to 0.74 MPa at temperatures of 420 °C and 430°C, while for the enforced demolding condition with GC molds, it rose from 0.52 MPa to 0.58 MPa. For L-BAL42 glass at 560 °C, the adhesion force was 0.4 MPa. Typically, the adhesive force increases with higher molding temperatures, which leads to more uniform adhesion layers on the mold surface. For D-FK95 glass, the adhesive force remains low (below 1 N) at molding temperatures below 505 °C (Zhao et al., 2023). However, at 535 °C, it increases significantly to approximately 48.4 N, corresponding to an adhesion stress of 0.8 MPa. Pressure also plays a role; at 515 °C, increasing applied pressure from 100 N to 250 N markedly raises adhesive force, adhesion stress, and contact area, expanding from 2.23 to 6.17 μm2. The choice of coating material further influences surface affinity, improving adhesion resistance. For example, uncoated WC molds exhibit adhesive stress of 0.17 MPa at 515 °C, whereas Ta–C coatings reduce it to 0.03 MPa, though AlCrN coatings exhibit higher adhesive stress, at 0.92 MPa. The varying adhesion conditions during demolding lead to distinct surface morphology evolutions in the molded optical glass. Figure 9 compares the microscopic images of the upper and lower interfaces of the molded glass (Li et al., 2022). The formation and morphology of bubble defects were notably affected by the demolding process, which was in turn influenced by differences in the molding temperature. Overall, adhesive force measurement serves as a direct indicator of demolding effectiveness, guiding further process optimization.
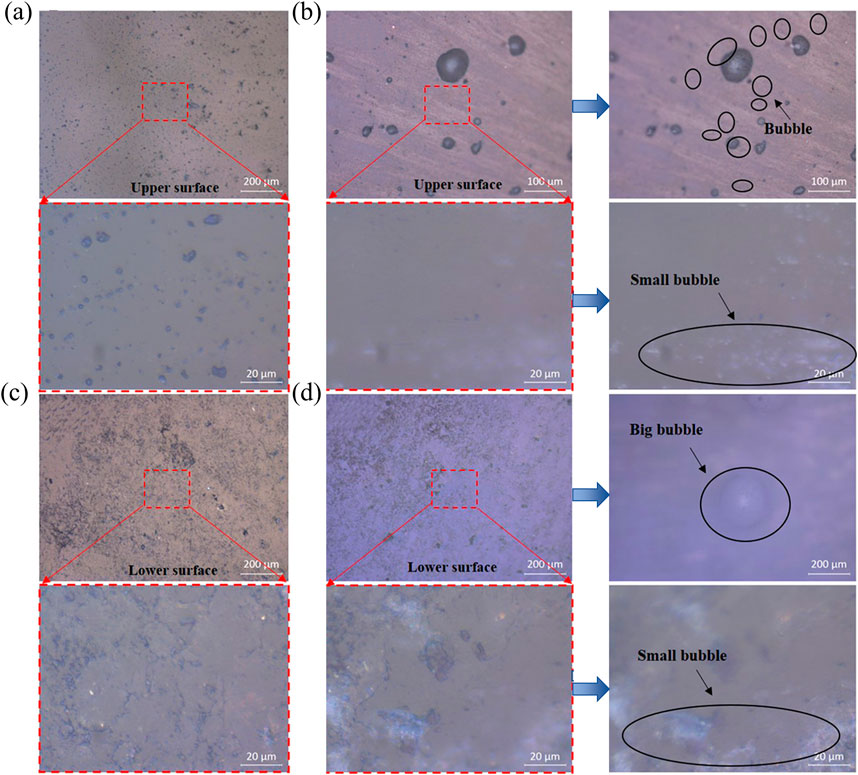
Figure 9. Comparison of the upper and lower interfaces of the molded glass under different demolding conditions. (a) The upper surface at a molding temperature of 490 °C, (b) the upper surface at 510 °C, (c) the lower surface at 490 °C and (d) the lower surface at 510 °C.
4 Advances in adhesion control
4.1 Molds and coatings development
To effectively control adhesion and extend mold lifespan, current research focuses on developing advanced mold materials and coatings, as well as optimizing processing parameters. The development of high-performance molds and coatings is essential for reducing adhesion, as the direct, repeated contact between molds and glass under high temperature and pressure conditions leads to mold wear, oxidation, and surface degradation over time, compromising the molding quality. Table 1 summarizes the key properties of common mold materials used in glass molding (Asgar et al., 2021; Kudělka et al., 2020; Garion, 2014; Yu et al., 2021). The materials exhibit significant differences in hardness, Young’s modulus, thermal conductivity, and thermal expansion coefficient, which directly influence their performance under high-temperature molding conditions. Protective coatings are needed for WC, Si, SiC and SiO2 molds, whereas GC and Ni-P molds often do not. Among them, WC has become one of the most widely applied in industrial mass production. Specifically, cobalt-free, nano-grain WC demonstrates significant resistance to adhesion in glass forming processes, maintaining stability under high hardness and high-temperature conditions. Glassy carbon (GC) is also gaining attention for its excellent thermal conductivity and ability to endure ultra-high glass transition temperatures without a coating (Grunwald et al., 2019). In micro-nano optical glass molding, GC molds withstand temperatures up to 1,360 °C, making them suitable for high-temperature glass processing, despite their relatively high fabrication cost (Li K. S. et al., 2021). Si is another common mold material, frequently used in micro-nano structures due to established microfabrication techniques such as photolithography and dry etching. Silicon’s low thermal expansion coefficient and excellent thermal conductivity make it ideal for precision molding. Additionally, Ni-P molds, fabricated through electroforming and micro-machining techniques, achieve the fine micro-groove structures required for high-surface-quality optical applications (Yu et al., 2021).
Protective coatings have become indispensable in PGM to further enhance mold resistance against adhesion. Common coatings include precious metals (e.g., Pt-Ir, Re-Ir), ceramic coatings (e.g., CrAlN, AlTiN, α-Al2O3), and diamond-like carbon (DLC) (Saha et al., 2010; Akhtar et al., 2024). Pt-Ir coatings maintain stability at temperatures up to 700 °C, while ceramic coatings like Al2O3 offer a cost-effective alternative for high-temperature molding. For Ni-P molds, the coated surface shows a high level of uniformity and low roughness of 9.29 nm (Figures 10a,b), contributing to superior form accuracy in the resulting glass structures (Figure 10c). DLC coatings are valued for their ultra-low friction, but their thermal stability deteriorates at lower temperatures due to graphite (Akhtar et al., 2022; Gharam et al., 2010). Recent progress, however, has extended their applicability to higher-temperature environments (>600 °C) (Friedrichs et al., 2022; Shu et al., 2024). Each coating type offers unique advantages in practical applications, with many anti-adhesion coatings achieving consistent and stable results. For instance, nano-graphite-coated Si molds enable clean molding at 370 °C, potentially replacing traditional coatings for optical glass molding (Zhang L. and Yan J. W., 2022). α-Al2O3 coatings show excellent anti-adhesion performance when forming den se barium crown glass (D-ZK3) and chalcogenide glass (IRG206), with notably lower surface stress in high-temperature environments compared to traditional Ta-based coatings, making it ideal for high-precision optical applications (Zhang Y. et al., 2020).
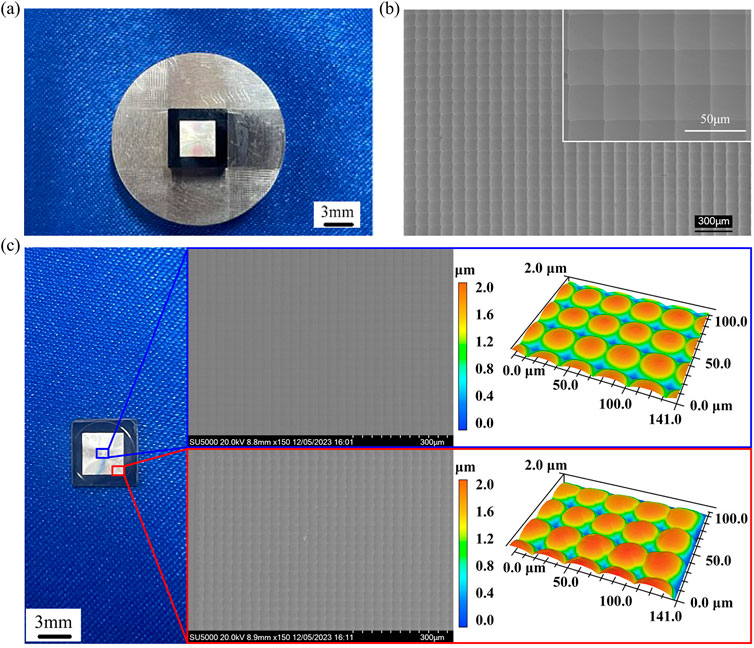
Figure 10. Evaluation of molding performance using Ni–P molds. (a) Photograph of the mold, (b) surface topography of the microlens arrays, (c) structural morphology of the molded glass components (Adapted with permission from Wang et al. (2024). Copyright 2024 American Chemical Society.).
Research into new coating materials is actively exploring high-temperature stability and multifunctionality (Zhang, et al., 2024a; Bernhardt et al., 2013; Wang L. et al., 2024; Dukwen et al., 2016). Nano-graphite carbon coatings, applied through chemical vapor deposition (CVD), offer hydrophobicity and low surface energy, making them ideal for anti-adhesion (Brüssel et al., 2024). In micro-optics molding, nano-graphite carbon coatings exhibit low friction and high replication accuracy, with experiments indicating that these coatings maintain low adhesion and surface quality even above 500 °C, showing promising potential for mass production of micro-structured optical components. This development broadens the application of Si molds in complex optical patterns, positioning them as viable alternatives to WC molds. Emerging coating research also focuses on composite multi-layer structures to enhance oxidation resistance and mechanical performance (Shu et al., 2024). For example, multi-layer coatings of α-Al2O3 with Ta or DLC provide a combined advantage of oxidation resistance and anti-adhesion in high-temperature environments, demonstrating excellent performance in both infrared and visible optical glass molding. Advances in coatings and molds for PGM have been summarized in Table 2.
4.2 Process optimization
In addition to material advancements, process optimization is crucial for minimizing interfacial adhesion. Effective temperature, pressure, and cooling rate control, as well as the introduction of external fields, have been shown to reduce glass-mold adhesion. Key process parameters, such as temperature and pressure control, ultrasonic assistance, and vacuum/inert gas environments, significantly impact mold adhesion behavior (Vu et al., 2024; Li K. et al., 2020; Zhou, et al., 2017).
Temperature control is particularly important in glass molding, as the molding temperature directly influences glass flow and adhesion behavior (Zhang Z. et al., 2024; Mosaddegh and Ziegert, 2013; Shu et al., 2022; Zhou et al., 2010; Sarhadi et al., 2014). In the molding process of ChG for aspherical lens, the area ratios of the microdimples on the formed ChG pillars exhibit an approximately logarithmic growth with the elevation of the molding temperature (Zhou, et al., 2018a). The optimal range of the increased molding temperature is deduced to be between 380 - 382 °C. This temperature range helps to minimize defects caused by adhesion. Regarding shape accuracy, a higher molding temperature results in a better fit between the mold and the glass surface, yet it also leads to a larger roughness of the molded lens. Moreover, the shrinkage phenomenon becomes more pronounced as the molding temperature rises. Consequently, a lower molding temperature of 382 °C is more favorably recommended to prevent surface adhesion and shape deviation. For Corning®Gorilla®Glass Victus™ glass, when the molding temperature is raised from 800 °C to 806 °C, the average proportion of crack area drops from 24.72% to 2.15% (Yang et al., 2022). Generally, the surface roughness of 3D ultra-thin glass increases with an increase in the molding temperature. The final surface roughness value of the bending region reaches 8.13 μm at a molding temperature of 810 °C. This occurs because the intensity of thermal movement within the ultra-thin glass intensifies with the increase in temperature, enhancing the fluidity of the glass surface and thus increasing the surface roughness. In conclusion, the appropriate selection of molding temperatures can comprehensively optimize the molding quality. Additionally, segmented temperature control allows for optimized temperature distribution by setting different zones within the mold at varied temperatures, preventing localized overheating and further suppressing adhesion (Hopmann et al., 2024).
Pressure control is another critical optimization strategy. The adhesion force increases with increased applied force and compression hold time, but more detailed research is required (Zhang et al., 2021; Huang et al., 2013). The molding force was reported to have a coefficient of 21.39 in linear relationship with adhesion force with confidence of 68.6% (Fischbach et al., 2010). A too high molding force can result in structure rupture but a too small pressure cannot make an adequate shape transfer from mold surfaces (Cheng et al., 2021). While a smaller holding force was maintained during cooling to ensure shape accuracy, the adhesion force relationship with it was not studied due to the expected very limited influence during cooling.
External field assistance, particularly ultrasonic assistance, shows potential in reducing adhesion. This technique is particularly suitable for high-precision optical component manufacturing, as it improves the problem of adhesion without altering temperature or pressure parameters. As shown in Figure 11, the simulated deformation behavior of glass reveals that ultrasonic assistance molding (UGMP) significantly decreases the contact angles and markedly enhances the cavity filling rate, as demonstrated by quantitative comparison (Yu et al., 2019). The enhancement in molding performance is mainly attributed to three ultrasound-induced effects: thermal softening, friction reduction and stress superposition (Nguyen et al., 2015; Yu et al., 2020). Specifically, ultrasonic vibration applied to the mold shortens the actual contact time between the mold and the glass in each vibration cycle (Zhou, et al., 2017). This intermittent contact weakens adhesion at the interface and contributes to more efficient demolding. Furthermore, the superimposed vibration can effectively weaken adhesion resistance, even when unpolished and uncoated molds are used, potentially enabling desirable demolding performance for molded glass arrays (Luo et al., 2020). In addition, ultrasonic thermal effects help distribute stress more uniformly, particularly in regions prone to stress concentration, thereby reducing the risk of localized adhesion. However, overly large vibration amplitudes should be avoided, as they may introduce excessive interfacial gaps, leading to unwanted adhesion or even glass fracture (Yu et al., 2019).
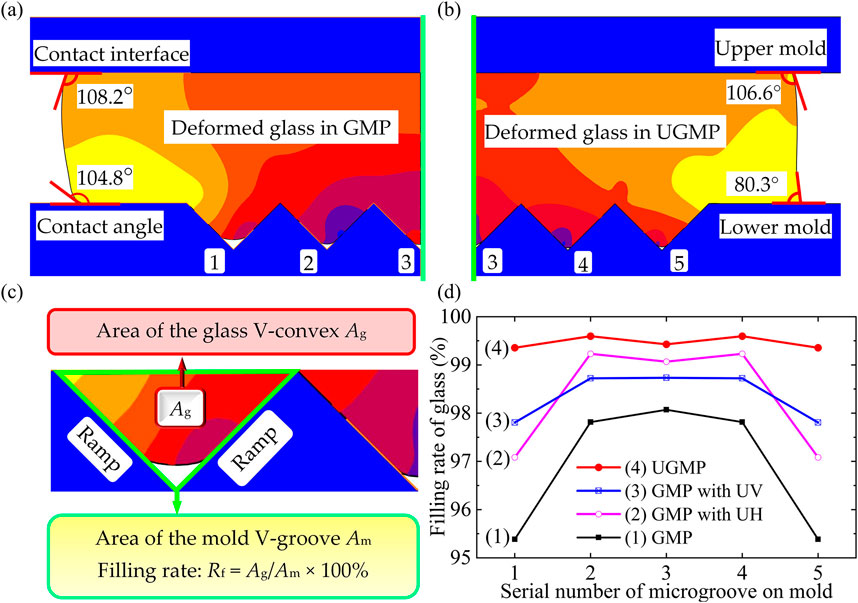
Figure 11. Effects of ultrasonic-assisted molding on the surface quality of molded lenses. (a) Simulated contact interface under GMP, (b) simulated contact interface under UGMP, (c) illustration of filling rate calculation, and (d) comparison of filling rate for four different molding processes.
Finally, using vacuum or inert gas environments during molding effectively reduces oxidation and adhesion. High temperatures increase the likelihood of oxidation between glass and mold surfaces, causing glass residue on the mold surface and increasing demolding resistance. Glass lenses manufactured by PGM in a vacuum environment usually have high forming quality. However, the industrial scalability of this approach is limited due to the lengthy vacuum chamber cycling process, including the time-consuming evacuation and repressurization steps. Alternatively, nitrogen—owing to its chemical inertness—can be introduced as a high-temperature cooling medium for both molds and lenses, enabling faster cooling rates and enhancing overall molding efficiency (Zhou et al., 2019; Zhou et al., 2023).
In summary, process optimization techniques—including precise temperature and pressure control, ultrasonic field assistance, and controlled molding environments—reduce adhesion forces between mold and glass, enhancing mold longevity and product quality. The combined application of these methods supports improved anti-adhesion performance in PGM, providing a strong foundation for high-precision optical component mass production.
5 Thermodynamics of adhesion
Adhesion in PGM involves multiple complex thermodynamic factors, such as interfacial work of adhesion, material wettability, and atomic interactions. Together, these factors govern the interfacial behavior between glass and mold materials, impacting molding quality and mold longevity. Understanding adhesion thermodynamics is key not only for elucidating the mechanisms of adhesion but also for developing more effective anti-adhesion coatings and optimizing the molding process. This section explores three core aspects of adhesion thermodynamics. First, the interfacial work of adhesion quantifies the energy required to separate the glass from the mold, serving as a primary measure of adhesion strength. Second, wettability characterizes the spreading behavior of molten glass on the mold surface and is closely associated with contact angle at the interface, which can be controlled through material or coating selection. Finally, atomic interactions, including physical forces and chemical bonding, explain the fundamental nature of adhesion at the molecular level.
5.1 Interface adhesion work
In PGM, interfacial adhesion arises from frictional forces and chemical reactions at the glass-mold interface. The work of adhesion (Wad) represents the energy required to separate two materials and is expressed using the concept of surface free energy (Monfared et al., 2017; Fernandez-Toledano et al., 2017). This measure is critical for evaluating the durability of mold surfaces and ensuring a smooth molding process. Defined as the energy required to separate two adhering surfaces, the work of adhesion can be calculated with Dupré equation as follows (Tadmor et al., 2017):
where the γmold and γglass are the surface free energy (SFE) of the mold surface and optical glass, respectively; γinter is the interfacial interaction energy. Equation 1 illustrates that higher surface free energies or lower interfacial energy lead to stronger adhesion. By selecting materials with appropriate surface energies, interfacial adhesion can be effectively controlled during the molding process. The surface energy calculations can be further refined to account for crystal structure and atomic configuration. The macroscopic atom (MA) model is frequently used to estimate the work of adhesion, accommodating both crystalline and amorphous materials by incorporating parameters such as atomic concentration, surface enthalpy, and atomic degrees of freedom in a vacuum environment. Take a compound AmBn and CxDy as an example:
where
This model is valuable for selecting mold and coating materials, as it predicts adhesion behaviors across material combinations, helping to avoid mold wear and surface defects on glass. For instance, high-temperature softening glass materials with lower surface energies are favorable for reducing adhesion, whereas mold materials with similar thermal expansion coefficients and high chemical inertness, such as tungsten and tungsten carbide, mitigate interfacial reactions during high-temperature molding. Studies demonstrate significant variations in work of adhesion across mold-glass combinations: low-surface-energy materials like PTFE (18.5 mJ/m2) and sapphire (638 mJ/m2) effectively suppress adhesion in thermoplastic forming, whereas high-surface-energy materials like Ni-P (1,093 mJ/m2) and Si (1,250 mJ/m2) tend to exhibit stronger interfacial adhesion, increasing the likelihood of bonding with glasses. (Monfared et al., 2017). The corresponding adhesion work with La-based metallic glass is 1774, 1,395, 1932 for Ni-P, sapphire and Si, respectively. Additionally, coatings like DLC (684 mJ/m2), Si (1,250 mJ/m2), and SiC (905 mJ/m2) on molds have shown excellent anti-adhesion properties, preserving surface quality with lower work of adhesion values (Zhao et al., 2023).
5.2 Wettability
Wettability is a critical thermodynamic factor in PGM, particularly at high temperatures where glass is in a semi-fluid state. It determines the spreading and adhesion behavior of glass on the mold surface, directly impacting glass distribution, flowability, and ease of demolding (Pastewka and Robbins, 2014). Understanding the fundamentals of wettability, including its concepts and measurement methods, is essential for analyzing adhesion thermodynamics. Wettability reflects the ability of a liquid to spread over a solid surface and is typically measured by the contact angle. A smaller contact angle indicates better spreading and stronger wettability, whereas a larger angle reflects poor wettability.
In PGM, wettability at high temperatures is crucial. Measuring high-temperature contact angles involves placing a small glass piece (either a chip or cylindrical glass) on the mold coating, heating it above the glass transition temperature (Tg) to reach a flowing or semi-flowing state, and recording the contact angle between the molten glass and the mold coating using high-speed cameras to capture dynamic changes. Different coating materials exhibit distinct wettability and anti-adhesion characteristics at elevated temperatures. High wettability on a mold surface promotes glass adhesion, whereas low wettability reduces interfacial adhesion (Zhang L. and Yan J., 2022). The measured high-temperature contact angles between molten D-K59 glass and three materials—crystallized Zr55Cu30Ni5Al10 metallic glass, WC, and Si—were approximately 153.8°, 145.3°, and 122.7°, respectively. These results indicate that the crystallized metallic glass demonstrates superior resistance to glass adhesion compared to WC (Sun S. D. et al., 2022). For enhanced mold longevity and minimal glass residue, coatings with larger high-temperature contact angles, such as α-Al2O3 and DLC, are preferred due to their low wettability and reduced glass adhesion (Zhang, et al., 2020b). The contact angles of Ta and α-Al2O3 coatings were close as 136.1° and 132.2°, respectively, whereas the DLC coating exhibited a slightly higher value of 151.8°. With rising temperature, α-Al2O3 coating displayed a significant reduction in contact angle, dropping to 108.1° at 690 °C. Notably, α-Al2O3 still maintains a large contact angle below 700 °C, exhibiting excellent anti-adhesion properties. Similarly, by optimizing the structure of Re/Ir coatings on WC-based molds, superior anti-sticking performance can be achieved at high temperatures, reducing glass adhesion (Wei et al., 2019).
The wettability between specific mold and glass materials varies, influencing adhesion behavior accordingly. PGM glasses, such as visible-transparent D-ZK3 and IR-optimized IRG206, differ in properties like molding temperature and thermal sensitivity. α-Al2O3 coatings show low wettability with both D-ZK3 and IRG206, making them suitable for forming these glass types, whereas DLC coatings are more appropriate for molding lower-temperature IR glass (Zhang L. et al., 2020). By comparing wettability data across coating-glass pairs, mold coatings can be tailored to match specific glass types, facilitating more efficient molding processes.
5.3 Atomic interactions
Considering demolding adhesion mechanisms, physical and chemical adhesion are the two predominant contributors. In physical adhesion, van der Waals forces and electrostatic interactions play key roles. Surface topography—such as microscopic asperities and indentations—on the mold can influence the real contact area with the glass, thereby affecting the magnitude of van der Waals interactions. In terms of chemical adhesion, the high-temperature and high-pressure environment during molding facilitates interfacial atomic or molecular diffusion, potentially triggering chemical reactions and the formation of interfacial bonds. Studies have revealed that the adhesion between glass and protective coatings such as Pt, PtIr, and Ir strongly correlates with changes in surface composition. Specifically, Pt-containing coatings can form Pt–O–Si bonds at the interface upon contact with glass. As the Pt content increases, the surface concentration of Si, Na, and K also rises, leading to an increase in adhesion strength (Saksena et al., 2021). Additionally, surfaces of mold materials such as WC and various alloys are prone to oxidation at elevated temperatures, which can lead to the formation of oxide layers. These oxide layers may chemically interact with the glass or enhance interfacial bonding, thereby resulting in increased adhesion forces during demolding (Li K. S. et al., 2020; Akhtar et al., 2024).
In the field of simulation and modeling, molecular dynamics (MD) simulations offer atomic-scale insights into the interfacial mechanisms between glass and mold materials. By constructing accurate atomic models, MD simulations can directly observe the interactions between atoms, as well as the formation and breakage of chemical bonds in real time. For example, in the Cu/amorphous SiO2 system, the adhesion strength significantly increases when the copper layer is fully oxidized (Figure 12). This enhancement is attributed to the formation of stronger chemical bonds between the oxidized copper and silicon atoms in SiO2, which shifts the fracture interface from the Cu/SiO2 interface to the oxidized layer/crystalline Cu interface (Urata et al., 2018). Moreover, during the demolding stage after glass molding, a fraction of silicon atoms can remain on the mold surface—an atomic-scale adhesion behavior that can be captured through MD simulations (Huang et al., 2022). Regarding the van der Waals and electrostatic interactions at the demolding interface, it has been found that for a given contact area, the non-bonded interaction energies show minimal variation across different nanostructure shapes, suggesting that such interactions are primarily governed by the interfacial contact area (Yang et al., 2019). Collectively, these studies indicate that demolding adhesion results from a combination of physical interactions, chemical bonding, and interfacial structural evolution. Both experimental and simulation approaches are effective in elucidating the adhesion mechanisms across different material systems. However, current research on adhesion formation at glass molding interfaces remains limited in both scope and depth, warranting further investigation in future work.
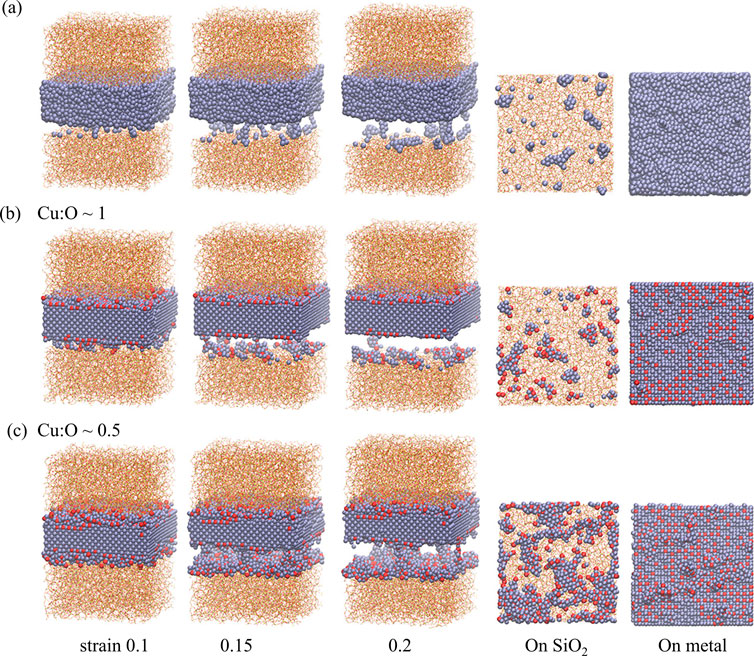
Figure 12. Interface separation images for different Cu/oxidized Cu–SiO2 contacts and corresponding fracture surface morphologies on the SiO2 and Cu sides. (a) A crystalline Cu model, (b) an oxidized Cu model with Cu:O ≈ 1, and (c) an oxidized Cu model with Cu:O ≈ 0.5. (Adapted with permission from Urata et al. (2018). Copyright 2018 American Chemical Society.).
6 Summary and perspectives
Significant progress has been made in elucidating the interfacial mechanisms underpinning mold-glass adhesion in precision glass molding, alongside the development of various mitigation strategies. Nevertheless, critical challenges remain in optimizing interfacial adhesion to ensure mold durability and enable scalable manufacturing of advanced optical components. Protective coatings—such as DLC, Pt-Ir, and Re-Ir—have demonstrated promising anti-adhesion properties due to their low friction, chemical inertness, and thermal compatibility. Yet, their long-term performance is compromised by cyclic thermal stresses, leading to delamination and degradation. A deeper understanding of coating-glass interactions under dynamic conditions is urgently needed to inform the rational design of robust, anti-sticking surfaces.
Process parameters such as molding temperature, compression force, and hold time are key determinants of adhesion strength, yet their synergistic effects remain insufficiently understood. Developing predictive models that couple these parameters with interfacial stress evolution and defect formation—such as elemental interdiffusion, coating degradation, and microcracking—will be essential. Future studies should integrate thermal cycling experiments with advanced characterization techniques (e.g., SEM, XPS) to uncover the mechanistic pathways by which specific parameter combinations modulate adhesion.
Importantly, the demolding process involves complex interfacial separation dynamics influenced by high-temperature wetting behavior, thermal shrinkage, and residual stresses. Adhesion is not merely a reversible contact phenomenon but is governed by localized stress states, cooling uniformity and surface condition heterogeneities. Investigating the early-stage interface formation—prior to the full application of molding pressure—and modeling separation dynamics via fracture mechanics frameworks may yield more accurate predictions of release conditions and critical energy thresholds.
At the atomic scale, interfacial adhesion arises from a complex interplay of van der Waals forces, electrostatic interactions, and in some cases, stronger ionic or covalent bonding. However, for the multicomponent glasses used in molding, accurate interatomic potentials remain limited. There is a growing need to identify how atomic-scale features—such as local coordination environments, surface terminations and defect states—influence adhesion behavior under processing-relevant conditions. A mechanistic understanding of these interactions will open avenues for tailoring interfacial chemistry and structure, ultimately enabling the design of surfaces that resist adhesion by design.
Together, these insights lay the groundwork for a new generation of materials and strategies aimed at mastering interfacial adhesion in precision glass molding—transforming current limitations into opportunities for high-throughput, high-fidelity production of next-generation optical systems.
Author contributions
HZ: Formal Analysis, Methodology, Validation, Visualization, Writing – original draft, Writing – review and editing. LZ: Conceptualization, Funding acquisition, Project administration, Resources, Supervision, Writing – review and editing.
Funding
The author(s) declare that financial support was received for the research and/or publication of this article. This work was supported by the National Natural Science Foundation of China (No. 52293401), the Shenzhen Key Laboratory of Cross Scale Manufacturing Mechanics Project (No. ZDSYS20200810171201007), and the High-level special funds (G03034K003) from Southern University of Science and Technology, Shenzhen, China.
Acknowledgments
The authors acknowledge the assistance of SUSTech Core Research Facilities for the SEM observation.
Conflict of interest
The authors declare that the research was conducted in the absence of any commercial or financial relationships that could be construed as a potential conflict of interest.
Generative AI statement
The author(s) declare that no Generative AI was used in the creation of this manuscript.
Publisher’s note
All claims expressed in this article are solely those of the authors and do not necessarily represent those of their affiliated organizations, or those of the publisher, the editors and the reviewers. Any product that may be evaluated in this article, or claim that may be made by its manufacturer, is not guaranteed or endorsed by the publisher.
References
Akhtar, A., and Ruan, H. (2022). Review on thin film coatings for precision glass molding. Surfaces Interfaces 30, 101903. doi:10.1016/j.surfin.2022.101903
Akhtar, A., Wang, J. B., He, R. Z., Yi Chun Wong, E., Hung, K. R., and Ruan, H. (2022). Microstructural evaluation of sputtered Ru-Pt multilayer anti-stick coatings for glass molding. Mater. and Des. 220, 110898. doi:10.1016/j.matdes.2022.110898
Akhtar, A., Wang, W., and Ruan, H. (2024). A study of Ru–Cr protective coatings for precision glass molding. Appl. Surf. Sci. 645, 158878. doi:10.1016/j.apsusc.2023.158878
Asgar, M. A., Kim, J., Haq, M. R., Kim, T., and Kim, S. M. (2021). A comprehensive review of micro/nano precision glass molding molds and their fabrication methods. Micromachines 12 (7), 812. doi:10.3390/mi12070812
Bennett, I. J., Kranenburg, J. M., and Sloof, W. G. (2005). Modeling the influence of reactive elements on the work of adhesion between oxides and metal alloys. J. Am. Ceram. Soc. 88 (8), 2209–2216. doi:10.1111/j.1551-2916.2005.00408.x
Bernhardt, F., Georgiadis, K., Dolle, L., Dambon, O., and Klocke, F. (2013). Development of a ta-C diamond-like carbon (DLC) coating by magnetron sputtering for use in precision glass molding. Mater. Werkst. 44 (8), 661–666. doi:10.1002/mawe.201300171
Bobba, D., and Morgan, C. (2022). “Reduction of cycle time during press molding of glass lenses,” in Proceeding of SPIE optical engineering + applications conference. doi:10.1117/12.2633380
Brüssel, F., Huang, W., and Yan, J. (2024). Investigation of failure modes and material structural responses of nanographite coatings on single-crystal silicon by nanoscratching. Tribol. Int. 193, 109349. doi:10.1016/j.triboint.2024.109349
Cao, G., Lin, H., Fraser, S., Zheng, X., Del Rosal, B., Gan, Z., et al. (2019). Resilient graphene ultrathin flat lens in aerospace, chemical, and biological harsh environments. ACS Appl. Mater Interfaces 11 (22), 20298–20303. doi:10.1021/acsami.9b05109
Capasso, F. (2018). The future and promise of flat optics: a personal perspective. Nanophotonics 7 (6), 953–957. doi:10.1515/nanoph-2018-0004
Chang, L. C., Zheng, Y. Z., Chen, Y. I., Chang, S. C., and Liu, B. W. (2018). Bonding characteristics and chemical inertness of Zr-Si-N coatings with a high Si content in glass molding. Coatings 8 (5), 181. doi:10.3390/coatings8050181
Chen, C., Friedrichs, M., Jiang, C., Wang, L., Dang, M., Grunwald, T., et al. (2023). Studies on protective coatings for molding tools applied in a precision glass molding process for a high abbe number glass S-FPM3. Coatings 13 (8), 1438. doi:10.3390/coatings13081438
Chen, X., Liu, W., Dong, B., Lee, J., Ware, H. O. T., Zhang, H. F., et al. (2018). High-speed 3D printing of millimeter-size customized aspheric imaging lenses with sub 7 nm surface roughness. Adv. Mater. 30 (18), e1705683. doi:10.1002/adma.201705683
Chen, Y. I., Ke, Y. E., Sung, M. C., and Chang, L. C. (2020). Rapid thermal annealing of Cr-Si-N, Ta-Si-N, and Zr-Si-N coatings in glass molding atmospheres. Surf. Coatings Technol. 389, 125662. doi:10.1016/j.surfcoat.2020.125662
Chen, Y. I., and Wang, H. H. (2014). Oxidation resistance and mechanical properties of Cr-Ta-Si-N coatings in glass molding processes. Surf. Coatings Technol. 260, 118–125. doi:10.1016/j.surfcoat.2014.08.085
Cheng, K. C., Huang, C. Y., Hung, J. C., Wang, A. C., and Lin, Y. C. (2021). Study of the transcription effects of pressing dies with ultrasonic polishing on glass molding. Processes 9 (11), 2083. doi:10.3390/pr9112083
Chernomyrdin, N. V., Frolov, M. E., Lebedev, S. P., Reshetov, I. V., Spektor, I. E., Tolstoguzov, V. L., et al. (2017). Wide-aperture aspherical lens for high-resolution terahertz imaging. Rev. Sci. Instrum. 88 (1), 014703. doi:10.1063/1.4973764
Chien, H., Kuo, C., and Huang, S. (2012). Molding of Al2O3-coated chalcogenide glass lenses. Opt. Eng. 51 (3), 033401. doi:10.1117/1.Oe.51.3.033401
Chizhik, P., Friedrichs, M., Dietzel, D., and Schirmeisen, A. (2020). Tribological analysis of contacts between glass and tungsten carbide near the glass transition temperature. Tribol. Lett. 68 (4), 127. doi:10.1007/s11249-020-01363-0
Dukwen, J., Friedrichs, M., Liu, G., Tang, M. J., Dambon, O., and Klocke, F. (2016). Tribological wear analysis and numerical lifetime prediction of glassy carbon tools in fused silica molding. Wear 364-365, 144–153. doi:10.1016/j.wear.2016.07.011
Fei, F., Xi, X., Qiao, X., Jian, W., Bo, Z., Ruiqing, X., et al. (2020). Progress on ultra precision manufacturing technology of large-aperture high-power laser optics. Opto-Electronic Eng. 47 (8), 200135–200135-13. doi:10.12086/oee.2020.200135
Fernandez-Toledano, J. C., Blake, T. D., Lambert, P., and De Coninck, J. (2017). On the cohesion of fluids and their adhesion to solids: young's equation at the atomic scale. Adv. Colloid Interface Sci. 245, 102–107. doi:10.1016/j.cis.2017.03.006
Fischbach, K. D., Georgiadis, K., Wang, F., Dambon, O., Klocke, F., Chen, Y., et al. (2010). Investigation of the effects of process parameters on the glass-to-mold sticking force during precision glass molding. Surf. Coatings Technol. 205 (2), 312–319. doi:10.1016/j.surfcoat.2010.06.049
Friedrichs, M., Grunwald, T., and Bergs, T. (2019). “Evaluation of mold materials for precision glass molding,” in Proceeding of sixth European seminar on precision optics manufacturing conference. doi:10.1117/12.2526769
Friedrichs, M., Grunwald, T., and Bergs, T. (2022). Mold protective coatings for precision glass molding. Polym. Opt. Molded Glass Opt. Des. Fabr. Mater. 2022, 2. doi:10.1117/12.2633076
Friedrichs, M., Peng, Z. R., Grunwald, T., Rohwerder, M., Gault, B., and Bergs, T. (2020). PtIr protective coating system for precision glass molding tools: design, evaluation and mechanism of degradation. Surf. Coatings Technol. 385, 125378. doi:10.1016/j.surfcoat.2020.125378
Garion, C. (2014). Mechanical properties for reliability analysis of structures in glassy carbon. World J. Mech. 04 (03), 79–89. doi:10.4236/wjm.2014.43009
Gharam, A., Lukitsch, M., Balogh, M., and Alpas, A. T. (2010). High temperature tribological behaviour of carbon based (B4C and DLC) coatings in sliding contact with aluminum. Thin Solid Films 519 (5), 1611–1617. doi:10.1016/j.tsf.2010.07.074
Ghosh, G., Sidpara, A., and Bandyopadhyay, P. P. (2018). Review of several precision finishing processes for optics manufacturing. J. Micromanufacturing 1 (2), 170–188. doi:10.1177/2516598418777315
Griffiths, C. A., Rees, A., Kerton, R. M., and Fonseca, O. V. (2016). Temperature effects on DLC coated micro moulds. Surf. Coatings Technol. 307, 28–37. doi:10.1016/j.surfcoat.2016.08.034
Grunwald, T., Wilhelm, D. P., Dambon, O., and Bergs, T. (2019). Influence of glassy carbon surface finishing on its wear behavior during precision glass moulding of fused silica. Mater. (Basel) 12 (5), 692. doi:10.3390/ma12050692
Guo, Y. H., Liu, G., Xiong, Y., and Tian, Y. C. (2007). Study of the demolding process - implications for thermal stress, adhesion and friction control. J. Micromech Microeng 17 (1), 9–19. doi:10.1088/0960-1317/17/1/002
Hamed, H., Eldiasty, M., Seyedi-Sahebari, S. M., and Abou-Ziki, J. D. (2023). Applications, materials, and fabrication of micro glass parts and devices: an overview. Mater. Today 66, 194–220. doi:10.1016/j.mattod.2023.03.005
Han, J. H., Lee, S. W., Choi, G. J., Lee, S. Y., Hwang, C. S., Dussarrat, C., et al. (2009). Chemical vapor deposition of Ru thin films with an enhanced morphology, thermal stability, and electrical properties using a RuO4 precursor. Chem. Mater 21 (2), 207–209. doi:10.1021/cm802485r
Hopmann, C., Kahve, C. E., Fritsche, D. C., and Fellerhoff, J. (2024). Evaluation of a self-optimizing local mold temperature control for inline warpage reduction of injection molded parts. Mater. Werkst. 55 (1), 21–32. doi:10.1002/mawe.202300142
Huang, C. Y., Chen, C. C., Chou, H. Y., and Chou, C. P. (2013). Fabrication of fresnel lens by glass molding technique. Opt. Rev. 20 (2), 202–204. doi:10.1007/s10043-013-0035-0
Huang, H., Yang, W., Ming, W. Y., Zhang, G. J., Xu, Y. J., and Zhang, Z. (2022). Mechanism of springback behavior in ultra-thin glass molding process: a molecular dynamics study. J. Non-Crystalline Solids 596, 121841. doi:10.1016/j.jnoncrysol.2022.121841
Huang, S. Z., Jiang, C. W., Tian, Z. W., Ren, B. W., Tang, Y. Z., Xie, F. L., et al. (2023). Optimization of precision molding process parameters of viscoelastic materials based on BP neural network improved by genetic algorithm. Mater. Today Commun. 35, 106149. doi:10.1016/j.mtcomm.2023.106149
Huang, X. F., Xie, Z. W., Li, K. S., Chen, Q., Chen, Y. J., and Gong, F. (2020a). Thermal stability of CrWN glass molding coatings after vacuum annealing. Coatings 10 (3), 198. doi:10.3390/coatings10030198
Huang, X. F., Xie, Z. W., Li, K. S., Chen, Q., Gong, F., Chen, Y. J., et al. (2020b). Microstructure, wear and oxidation resistance of CrWN glass molding coatings synthesized by plasma enhanced magnetron sputtering. Vacuum 174, 109206. doi:10.1016/j.vacuum.2020.109206
Ikeda, H., Kasa, H., and Nishii, J. (2016). Effect of mold stiffness on surface flatness of mold-pressed glass. Microsyst. Technol. 22 (8), 2087–2091. doi:10.1007/s00542-015-2521-8
Kadono, K., and Kitamura, N. (2022). Recent progress in chalcogenide glasses applicable to infrared optical elements manufactured by molding technology. J. Ceram. Soc. Jpn. 130 (8), 584–589. doi:10.2109/jcersj2.22079
Kao, W. H., Su, Y. L., Horng, J. H., and Wu, C. M. (2021). Structure, mechanical properties and thermal stability of nitrogen-doped TaNbSiZrCr high entropy alloy coatings and their application to glass moulding and micro-drills. Surf. Coatings Technol. 405, 126539. doi:10.1016/j.surfcoat.2020.126539
Kim, D., and Choi, Y. (2021). Applications of smart glasses in applied sciences: a systematic review. Appl. Sci. 11 (11), 4956. doi:10.3390/app11114956
Kim, J. W., and Kim, T. G. (2022). Release characteristics of a high-hardness DLC coating on an aspherical glass lens mold. Mod. Phys. Lett. B 36 (17), 2242024. doi:10.1142/S0217984922420246
Kim, K. H., Hwang, K. J., Lee, H., Jeong, S. M., Lee, M. H., and Bae, S. Y. (2020). Improvement of adhesion properties of glass prepared using SiC-deposited graphite mold via low-temperature chemical vapor deposition. J. Korean Ceram. Soc. 57 (1), 112–118. doi:10.1007/s43207-019-00010-2
Kim, Y. K., Haq, M. R., and Kim, S. M. (2019). Glass molding of all glass Fresnel lens with vitreous carbon micromold. Opt. Express 27 (2), 1553–1562. doi:10.1364/OE.27.001553
Klocke, F., Dambon, O., Rohwerder, M., Bernhardt, F., Friedrichs, M., and Merzlikin, S. V. (2016). Model of coating wear degradation in precision glass molding. Int. J. Adv. Manuf. Technol. 87 (1-4), 43–49. doi:10.1007/s00170-015-8005-2
Kudělka, R., Václavek, L., Tomáštík, J., Malecová, S., and Čtvrtlík, R. (2020). Laser-induced surface acoustic waves for thin film characterization. Acta Polytech. CTU Proc. 27, 57–61. doi:10.14311/app.2020.27.0057
Lee, S. H., Ko, I. H., and Kim, T. Y. (2018). Surface failure analysis of AlCrN coating on WC substrate subjected to high-temperature oxidation in glass-molding machine. Appl. Surf. Sci. 452, 210–216. doi:10.1016/j.apsusc.2018.05.031
Lee, W. M., Upadhya, A., Reece, P. J., and Phan, T. G. (2014). Fabricating low cost and high performance elastomer lenses using hanging droplets. Biomed. Opt. Express 5 (5), 1626–1635. doi:10.1364/BOE.5.001626
Li, J. F., Luo, H. Y., He, Y. L., Liu, Y., Zhang, L., Zhou, K. M., et al. (2014). Semiconductor saturable absorber mirror passively Q-switched 2.97μm fluoride fiber laser. Laser Phys. Lett. 11 (6), 065102. doi:10.1088/1612-2011/11/6/065102
Li, K., Xu, G., Liu, X., and Gong, F. (2020a). Deformation behavior of glass nanostructures in hot embossing. ACS Appl. Mater Interfaces 12 (32), 36311–36319. doi:10.1021/acsami.0c08435
Li, K. S., Wang, Z. L., and Gong, F. (2022). The evolution and generation of nanosurfaces and their microcontact mechanism in glass-embossing process. J. Am. Ceram. Soc. 105 (7), 4655–4668. doi:10.1111/jace.18462
Li, K. S., Xu, G., Huang, X. F., Chen, Q., Xie, Z. W., and Gong, F. (2020b). Surface evolution analysis of CrxWyNz coatings on WC mold in glass molding process. Surf. Coatings Technol. 393, 125839. doi:10.1016/j.surfcoat.2020.125839
Li, K. S., Xu, G., Wen, X. B., Zhou, J., and Gong, F. (2021a). High-temperature friction behavior of amorphous carbon coating in glass molding process. Friction 9 (6), 1648–1659. doi:10.1007/s40544-020-0452-6
Li, M., Chen, Y., Luo, W., and Cheng, X. (2021b). Interfacial interactions during demolding in nanoimprint lithography. Micromachines 12 (4), 349. doi:10.3390/mi12040349
Liu, G., Vu, A.-T., Dambon, O., and Klocke, F. (2017a). Glass material modeling and its molding behavior. MRS Adv. 2 (16), 875–885. doi:10.1557/adv.2017.64
Liu, J. H., Chen, X. D., Lin, Z. Q., and Diao, S. P. (2017b). Multiobjective optimization of injection molding process parameters for the precision manufacturing of plastic optical lens. Math. Problems Eng. 2017 (1), 2834013. doi:10.1155/2017/2834013
Liu, W., and Zhang, L. (2017). Numerical optimization platform for precision glass molding by the simplex algorithm. Appl. Opt. 56 (12), 3245–3250. doi:10.1364/AO.56.003245
Liu, Y., Xing, Y., Fu, H., Li, C., Yang, C., Cao, B., et al. (2021). Deformation analysis of the glass preform in the progress of precision glass molding for fabricating chalcogenide glass diffractive optics with the finite element method. Micromachines 12 (12), 1543. doi:10.3390/mi12121543
Liu, Y., Xue, C., Sun, G., and Zhang, G. (2023). Analysis on the instability of the surface profiles of precision molding chalcogenide glass aspherical lenses in mass production. Opt. Express 31 (19), 31158–31176. doi:10.1364/OE.501104
Liu, Y., Xue, C., Xing, Y., Li, C., and Yang, C. (2022). “Optimization on the general molds design method for precision glass molding,” in Preceedings of seventh asia pacific conference on optics manufacture and 2021 international forum of Young scientists on advanced optical manufacturing conference. doi:10.1117/12.2606086
Luo, H., Yu, J., Lou, H., Huang, K., Hu, J., and Xu, B. (2020). Thermal/tribological effects of superimposed ultrasonic vibration on viscoelastic responses and mold-filling capacity of optical glass: a comparative study. Ultrasonics 108, 106234. doi:10.1016/j.ultras.2020.106234
Luo, H., Yu, J. W., Hu, J. Z., Tang, K., Xu, B. C., and Wang, F. (2022). Effects of uniform/nonuniform interface friction on mold-filling behavior of glass microarray: a numerical-experimental study. Tribol. Lett. 70 (1), 20. doi:10.1007/s11249-022-01563-w
Ming, W. Y., Chen, Z. J., Du, J. G., Zhang, Z., Zhang, G. J., He, W. B., et al. (2020). A comprehensive review of theory and technology of glass molding process. Int. J. Adv. Manuf. Technol. 107 (5-6), 2671–2706. doi:10.1007/s00170-020-05051-0
Monfared, A., Liu, W. D., and Zhang, L. C. (2017). On the adhesion between metallic glass and dies during thermoplastic forming. J. Alloys Compd. 711, 235–242. doi:10.1016/j.jallcom.2017.04.005
Mosaddegh, P., and Ziegert, J. (2013). The effect of temperature on the stick-slip friction behavior of optical glasses in precision glass molding. Appl. Mech. Mater. 307, 381–386. doi:10.4028/www.scientific.net/AMM.307.381
Nguyen, L. P., Hao, K. C., Su, Y. H., and Hung, C. H. (2015). Modeling the embossing stage of the ultrasonic-vibration-assisted hot glass embossing process. Int. J. Appl. Glass Sci. 6 (2), 172–181. doi:10.1111/ijag.12090
Pallicity, T. D., Vu, A. T., Ramesh, K., Mahajan, P., Liu, G., and Dambon, O. (2017). Birefringence measurement for validation of simulation of precision glass molding process. J. Am. Ceram. Soc. 100 (10), 4680–4698. doi:10.1111/jace.15010
Pastewka, L., and Robbins, M. O. (2014). Contact between rough surfaces and a criterion for macroscopic adhesion. Proc. Natl. Acad. Sci. 111 (9), 3298–3303. doi:10.1073/pnas.1320846111
Peng, Y. F., Shen, B. Y., Wang, Z. Z., Yang, P., Yang, W., and Bi, G. (2021). Review on polishing technology of small-scale aspheric optics. Int. J. Adv. Manuf. Technol. 115 (4), 965–987. doi:10.1007/s00170-021-07202-3
Prater, K., Dukwen, J., Scharf, T., Herzig, H. P., Plöger, S., and Hermerschmidt, A. (2016). Micro-structuring of glassy carbon for precision glass molding of binary diffractive optical elements. Opt. Mater Express 6 (11), 3407–3416. doi:10.1364/Ome.6.003407
Saha, B., Liu, E., Tor, S. B., Hardt, D. E., Chun, J. H., and Khun, N. W. (2010). Improvement in lifetime and replication quality of Si micromold using N:DLC:Ni coatings for microfluidic devices. Sensors Actuators B Chem. 150 (1), 174–182. doi:10.1016/j.snb.2010.07.019
Saksena, A., Prünte, S., Holzapfel, D. M., Patterer, L., and Schneider, J. M. (2021). Influence of glass contact induced changes in surface composition of Pt, PtIr and Ir protective coatings on glass adhesion. Appl. Surf. Sci. 548, 149282. doi:10.1016/j.apsusc.2021.149282
Sarhadi, A., Hattel, J. H., and Hansen, H. N. (2014). Evaluation of the viscoelastic behaviour and glass/mould interface friction coefficient in the wafer based precision glass moulding. J. Mater. Process. Technol. 214 (7), 1427–1435. doi:10.1016/j.jmatprotec.2014.02.008
Senellart, P., Solomon, G., and White, A. (2017). High-performance semiconductor quantum-dot single-photon sources. Nat. Nanotechnol. 12 (11), 1026–1039. doi:10.1038/nnano.2017.218
Shimizu, Y., Chen, L. C., Kim, D. W., Chen, X. G., Li, X. H., and Matsukuma, H. (2021). An insight into optical metrology in manufacturing. Meas. Sci. Technol. 32 (4), 042003. doi:10.1088/1361-6501/abc578
Shu, C., Yin, S., and Huang, S. (2024). Preparation and performance of Ti/Ti-DLC composite coatings for precision glass molding. Ceram. Int. 50 (3), 5210–5223. doi:10.1016/j.ceramint.2023.11.267
Shu, C. S., Guo, X. P., Yin, S. H., Huang, S., and Mao, Z. Z. (2023). Fabrication of curved aspheric compound eye microlens array with high surface quality by precision glass molding. Precis. Eng. 82, 129–139. doi:10.1016/j.precisioneng.2023.03.009
Shu, C. S., Yin, S. H., Li, Y. Q., Mao, Z. Z., Guo, X. P., and Huang, S. (2022). High-precision molding simulation prediction of glass lens profile for a new lanthanide optical glass. Ceram. Int. 48 (11), 15800–15810. doi:10.1016/j.ceramint.2022.02.118
Sun, F., Yang, J., Fu, J., Wang, B., Ma, J., and Shen, J. (2022a). Hierarchical macro to nano press molding of optical glasses by using metallic glasses. J. Non-Crystalline Solids 594, 121821. doi:10.1016/j.jnoncrysol.2022.121821
Sun, S. D., Li, K. S., Chu, W. Y., and Gong, F. (2022b). Tungsten carbide molds for precision glass molding process: mechanism of high-temperature degradation. Int. J. Refract. Metals Hard Mater. 105, 105841. doi:10.1016/j.ijrmhm.2022.105841
Symmons, A., Huddleston, J., and Knowles, D. (2016). “Design for manufacturability and optical performance trade-offs using precision glass molded aspheric lenses,” in The proceedings of polymer optics and molded glass optics: design, fabrication, and materials conference. doi:10.1117/12.2238111
Tadmor, R., Das, R., Gulec, S., Liu, J., E N’guessan, H., Shah, M., et al. (2017). Solid-liquid work of adhesion. Langmuir 33 (15), 3594–3600. doi:10.1021/acs.langmuir.6b04437
Tan, N. Y. J., Zhang, X. Q., Neo, D. W. K., Huang, R., Liu, K., and Senthil Kumar, A. (2021). A review of recent advances in fabrication of optical Fresnel lenses. J. Manuf. Process. 71, 113–133. doi:10.1016/j.jmapro.2021.09.021
Urata, S., Yoshino, H., Ono, M., Miyasaka, S., Ando, R., and Hayashi, Y. (2018). Adhesion between copper and amorphous silica: a reactive molecular dynamics study. J. Phys. Chem. C 122 (49), 28204–28214. doi:10.1021/acs.jpcc.8b09990
Vieira, L. d. S. (2022). A review on the use of glassy carbon in advanced technological applications. Carbon 186, 282–302. doi:10.1016/j.carbon.2021.10.022
Vu, A. T., Grunwald, T., and Bergs, T. (2024). Friction in glass forming: tribological behaviors of optical glasses and uncoated steel near glass transition temperature. J. Non-Crystalline Solids 642, 123160. doi:10.1016/j.jnoncrysol.2024.123160
Vu, A. T., Vu, A. N., Grunwald, T., and Bergs, T. (2020). Modeling of thermo-viscoelastic material behavior of glass over a wide temperature range in glass compression molding. J. Am. Ceram. Soc. 103 (4), 2791–2807. doi:10.1111/jace.16963
Vu, A. T., Vu, A. N., Liu, G., Grunwald, T., Dambon, O., Klocke, F., et al. (2019). Experimental investigation of contact heat transfer coefficients in nonisothermal glass molding by infrared thermography. J. Am. Ceram. Soc. 102 (4), 2116–2134. doi:10.1111/jace.16029
Vu, V. T., Ui Hasan, S. A., Youn, H., Park, Y., and Lee, H. (2021). Imaging performance of an ultra-precision machining-based Fresnel lens in ophthalmic devices. Opt. Express 29 (20), 32068–32080. doi:10.1364/OE.438531
Wang, G., Zhou, T. F., Guo, W. J., Yao, X. Q., and Yu, Q. (2024a). Surface modification of nickel-phosphorus plating by Ti ion implantation for chalcogenide glass lens molding. Surfaces Interfaces 48, 104375. doi:10.1016/j.surfin.2024.104375
Wang, L., Hu, Y., Zhang, Z., Liu, Y., and Xue, C. (2024b). Rapid manufacturing technology for aspheric optical elements. Opto-Electronic Eng. 51 (1), 230171–1. doi:10.12086/oee.2024.230171
Wang, S., Kong, L., Wang, C., and Cheung, C. (2023a). Ultra-precision manufacturing of microlens arrays using an optimum machining process chain. Opt. Express 31 (2), 2234–2247. doi:10.1364/OE.479696
Wang, Z., Jiao, M., Zhang, Y., Zhang, F., and Wang, Z. (2019). “Selection of coating for low Tg glass precision glass molding,” in Preceedings of 9th international symposium on advanced optical manufacturing and testing technologies: advanced optical manufacturing technologies conference. doi:10.1117/12.2514699
Wang, Z. F., Zhou, T. F., Yu, Q., Yao, X. Q., Liu, P., and Wang, X. B. (2023b). Thermomechanical performance enhancement of nickel-phosphorus mold by Ti-DLC coating. Mater. Today Commun. 35, 106025. doi:10.1016/j.mtcomm.2023.106025
Wang, G., Zhou, T. F., and Sun, X. (2024). Study on deformation behavior of glass in high-temperature molding for massive unit microlens arrays. ACS Appl. Mater. Interfaces 16 (32), 43038–43048. doi:10.1021/acsami.4c10406
Wei, J. J., Zhu, X. Y., Chen, L. X., Liu, J. L., and Li, C. M. (2019). High quality anti-sticking coating based on multilayer structure. Surf. Coatings Technol. 362, 72–77. doi:10.1016/j.surfcoat.2019.01.067
Xie, J., Zhou, T., Ruan, B., Du, Y., and Wang, X. (2017). Effects of interface thermal resistance on surface morphology evolution in precision glass molding for microlens array. Appl. Opt. 56 (23), 6622–6630. doi:10.1364/AO.56.006622
Xie, J. Q., Zhou, T. F., Zhu, Z. C., Gao, P., Chen, J., Wang, X. B., et al. (2021). Research on rhenium-iridium alloy coating on microgroove molds in precision glass molding. Appl. Nanosci. 11 (3), 797–806. doi:10.1007/s13204-019-01097-z
Xu, Y., Chen, Q., Zhang, C., Wang, R., Wu, H., Zhang, X., et al. (2016). Two-Photon-pumped perovskite semiconductor nanocrystal lasers. J. Am. Chem. Soc. 138 (11), 3761–3768. doi:10.1021/jacs.5b12662
Yang, J., Weng, C., Lai, J., Ding, T., and Wang, H. (2019). Molecular dynamics simulation on the influences of nanostructure shape, interfacial adhesion energy, and mold insert material on the demolding process of micro-injection molding. Polym. (Basel) 11 (10), 1573. doi:10.3390/polym11101573
Yang, W., Zhang, Z., Ming, W. Y., Yin, L., and Zhang, G. J. (2022). Study on shape deviation and crack of ultra-thin glass molding process for curved surface. Ceram. Int. 48 (5), 6767–6779. doi:10.1016/j.ceramint.2021.11.228
Yin, S. H., Jia, H. P., Zhang, G. H., Chen, F. J., and Zhu, K. J. (2017). Review of small aspheric glass lens molding technologies. Front. Mech. Eng. 12 (1), 66–76. doi:10.1007/s11465-017-0417-2
Youn, S. W., Takahashi, M., Goto, H., and Maeda, R. (2006). Microstructuring of glassy carbon mold for glass embossing - comparison of focused ion beam, nano/femtosecond-pulsed laser and mechanical machining. Microelectron. Eng. 83 (11-12), 2482–2492. doi:10.1016/j.mee.2006.05.007
Yu, J., Luo, H., Nguyen, T. V., Huang, L., Liu, B., and Zhang, Y. (2020). Eigenfrequency characterization and tuning of Ti-6Al-4V ultrasonic horn at high temperatures for glass molding. Ultrasonics 101, 106002. doi:10.1016/j.ultras.2019.106002
Yu, J. W., Luo, H., Nguyen, T. V., Lu, Y. T., Huang, L., and Zhang, Y. Y. (2019). Mechanism study on microformability of optical glass in ultrasonic-assisted molding process. Int. J. Appl. Glass Sci. 10 (1), 103–114. doi:10.1111/ijag.12365
Yu, Q., Zhou, T. F., He, Y. P., Liu, P., Wang, X. B., Jiang, Y. G., et al. (2021). Annealed high-phosphorus electroless Ni-P coatings for producing molds for precision glass molding. Mater. Chem. Phys. 262, 124297. doi:10.1016/j.matchemphys.2021.124297
Yuan, W., Li, L. H., Lee, W. B., and Chan, C. Y. (2018). Fabrication of microlens array and its application: a review. Chin. J. Mech. Eng. 31 (1), 16–19. doi:10.1186/s10033-018-0204-y
Zhang, L., and Yan, J. (2022a). Amorphous carbon coated silicon wafer as mold insert for precision glass molding. Procedia CIRP 108, 525–530. doi:10.1016/j.procir.2022.03.082
Zhang, L., and Yan, J. W. (2022b). Study on nano-graphitic carbon coating on Si mold insert for precision glass molding. Surf. Coatings Technol. 448, 128893. doi:10.1016/j.surfcoat.2022.128893
Zhang, L., and Yi, A. Y. (2021). Investigation of mid-infrared rapid heating of a carbide-bonded graphene coating and its applications in precision optical molding. Opt. Express 29 (19), 30761–30771. doi:10.1364/OE.405603
Zhang, L., Zhou, L. Y., Zhou, W. C., Zhang, S. Q., and Yi, A. Y. (2020a). Design, fabrication and testing of a compact large-field-of-view infrared compound eye imaging system by precision glass molding. Precis. Eng. 66, 87–98. doi:10.1016/j.precisioneng.2020.06.017
Zhang, L., Zhou, W., and Yi, A. Y. (2018). Investigation of thermoforming mechanism and optical properties' change of chalcogenide glass in precision glass molding. Appl. Opt. 57 (22), 6358–6368. doi:10.1364/AO.57.006358
Zhang, L. C., and Liu, W. D. (2017). Precision glass molding: toward an optimal fabrication of optical lenses. Front. Mech. Eng. 12 (1), 3–17. doi:10.1007/s11465-017-0408-3
Zhang, W., Yang, D., Gong, F., Chen, Y., Chen, T., Xie, Z., et al. (2024a). Understanding the role of Pt addition on structure and thermal stability of CrWN glass molding coating in nitrogen molding atmosphere. Vacuum 220, 112815. doi:10.1016/j.vacuum.2023.112815
Zhang, X., Wang, Z. X., Li, H. T., Hou, C. Y., Kong, X. Y., Zhang, Y. S., et al. (2019a). Modeling and experimental investigation of polymer micropart demolding from a Zr-based bulk metallic glass mold. Polym. Eng. and Sci. 59 (11), 2202–2210. doi:10.1002/pen.25223
Zhang, Y., Yan, G., Li, Z., and Fang, F. (2019b). Quality improvement of collimating lens produced by precision glass molding according to performance evaluation. Opt. Express 27 (4), 5033–5047. doi:10.1364/OE.27.005033
Zhang, Y., Yan, G. P., You, K. Y., and Fang, F. Z. (2020b). Study on α-Al2O3 anti-adhesion coating for molds in precision glass molding. Surf. Coatings Technol. 391, 125720. doi:10.1016/j.surfcoat.2020.125720
Zhang, Z., Liu, Y., Li, C., Ding, Y., Yang, C., Zhao, Y., et al. (2024b). Precision glass molding technology for XY polynomial freeform optical elements with simulations and experiments. Opt. Express 32 (13), 22905–22927. doi:10.1364/OE.525414
Zhang, Z., Yang, W., Ming, W., Yin, L., Liao, D., and Zhang, G. (2021). Surface integrity analysis of ultra-thin glass molding process. Ceram. Int. 47 (21), 30584–30597. doi:10.1016/j.ceramint.2021.07.236
Zhao, H. H., Gain, A. K., Li, Z., and Zhang, L. C. (2023). Wear of mold surfaces: interfacial adhesion in precision glass molding. Wear 524-525, 204847. doi:10.1016/j.wear.2023.204847
Zhou, J., Li, L. H., Ng, M. C., and Lee, W. B. (2019). Effect of molding machine's stiffness on the thickness of molded glass rings. Int. J. Appl. Glass Sci. 10 (4), 584–597. doi:10.1111/ijag.13535
Zhou, J., Xu, H. K., Zhu, C. Y., Li, L. H., Ng, M. C., and Liu, K. (2022). Characterization and growth mechanisms of adhesion-induced microcavities during debonding of softened glass. Int. J. Appl. Glass Sci. 13 (4), 629–644. doi:10.1111/ijag.16596
Zhou, J., Zhu, C., Li, L., Ng, M. C., and Liu, K. (2020). Temperature and rate dependent debonding behaviors of precision glass molding interface. J. Am. Ceram. Soc. 104 (1), 243–255. doi:10.1111/jace.17478
Zhou, T., Liu, X., Liang, Z., Liu, Y., Xie, J., and Wang, X. (2017a). Recent advancements in optical microstructure fabrication through glass molding process. Front. Mech. Eng. 12 (1), 46–65. doi:10.1007/s11465-017-0425-2
Zhou, T., Xie, J., Yan, J., Tsunemoto, K., and Wang, X. (2017b). Improvement of glass formability in ultrasonic vibration assisted molding process. Int. J. Precis. Eng. Manuf. 18 (1), 57–62. doi:10.1007/s12541-017-0007-6
Zhou, T., Xu, R., Ruan, B., Liang, Z., and Wang, X. (2018b). Fabrication of microlens array on 6H-SiC mold by an integrated microcutting-etching process. Precis. Eng. 54, 314–320. doi:10.1016/j.precisioneng.2018.06.008
Zhou, T., Yan, J., Yoshihara, N., and Kuriyagawa, T. (2010). Study on nonisothermal glass molding press for aspherical lens. J. Adv. Mech. Des. Syst. Manuf. 4 (5), 806–815. doi:10.1299/jamdsm.4.806
Zhou, T., Zeng, Z. H., Yu, Q., Zhou, J., Liu, P., and Wang, X. (2023). Study on gas trapping during precision glass molding of microlens array in a nitrogen atmosphere. Int. J. Appl. Glass Sci. 14 (3), 435–444. doi:10.1111/ijag.16624
Zhou, T., Zhou, Q., Xie, J., Liu, X., Wang, X., and Ruan, H. (2017). Surface defect analysis on formed chalcogenide glass Ge_22Se_58As_20 lenses after the molding process. Appl. Opt. 56 (30), 8394–8402. doi:10.1364/AO.56.008394
Zhou, T., Zhu, Z., Liu, X., Liang, Z., and Wang, X. (2018a). A review of the precision glass molding of chalcogenide glass (chg) for infrared optics. Micromachines 9 (7), 337. doi:10.3390/mi9070337
Zhu, X., Wei, J., Chen, L., Liu, J., Hei, L., Li, C., et al. (2015). Anti-sticking Re-Ir coating for glass molding process. Thin Solid Films 584, 305–309. doi:10.1016/j.tsf.2015.01.002
Keywords: precision glass molding, adhesion mechanism, optical components, process optimization, mold quality
Citation: Zhao H and Zhang L (2025) Mold-glass interface adhesion mechanisms in precision glass molding. Adv. Opt. Technol. 14:1588934. doi: 10.3389/aot.2025.1588934
Received: 06 March 2025; Accepted: 01 May 2025;
Published: 14 July 2025.
Edited by:
Allen Yi, The Ohio State University, United StatesReviewed by:
Jian Zhou, Hefei University of Technology, Hefei, ChinaAnh Tuan Vu, Fraunhofer Institute for Production Technology (FHG), Germany
Copyright © 2025 Zhao and Zhang. This is an open-access article distributed under the terms of the Creative Commons Attribution License (CC BY). The use, distribution or reproduction in other forums is permitted, provided the original author(s) and the copyright owner(s) are credited and that the original publication in this journal is cited, in accordance with accepted academic practice. No use, distribution or reproduction is permitted which does not comply with these terms.
*Correspondence: Liangchi Zhang, emhhbmdsY0BzdXN0ZWNoLmVkdS5jbg==