- Shendong Coal Branch, China Shenhua Energy Co., Ltd., Yulin, China
The application of large-diameter precise directional drilling for long boreholes demonstrates significant potential in coal mine construction, effectively overcoming the limitations of traditional drilling methods in long-distance crossings and complex geological formations. This study highlights the use of advanced directional guiding technologies, including triaxial accelerometers, magnetoresistance sensors, and intelligent trajectory control systems, to achieve precise borehole interconnections. In the Shangwan Coal Mine 22106 working face, large-diameter boreholes (120 mm, expanded to 203 mm) enhanced gas extraction efficiency, with average extraction concentrations reaching 80.2%, a 3.1-fold improvement compared to conventional methods (25.8%). The average gas extraction volume was 0.44 m3/min, representing a 10.3-fold increase over traditional techniques. Gas concentrations in roadways were maintained within a safe range of 0.27%–0.40%, enabling a monthly excavation progress of 400 m. A BP neural network model was employed for gas outflow prediction, achieving high accuracy with a deviation of less than 2% compared to field measurements. These findings demonstrate the transformative potential of this technology, ensuring safe, efficient, and rapid roadway construction in high-gas environments, with implications for broader applications in complex geological conditions.
1 Introduction
The safe and efficient construction of underground coal mine roadways has long been a technical challenge, particularly in high-gas environments (Wu et al., 2023; Zhengfu et al., 2010; Kang et al., 2023). The risk of gas outbursts and exceeding safety thresholds poses significant threats to the safety of personnel and equipment. With increasing mining depths, gas content and permeability conditions become more severe, exposing the limitations of traditional drilling methods such as small-diameter boreholes and intermittent drilling (Li et al., 2021; Wen et al., 2024; Xue et al., 2022). Consequently, optimizing gas drainage technologies to ensure safe excavation while maintaining high progress rates has become a critical research focus in coal mine engineering.
Traditional gas drainage techniques, such as edge-drilling and extracting, have demonstrated satisfactory performance in shallow seams with low gas content. However, these methods are increasingly inadequate in deeper, high-gas environments due to limited drainage efficiency and safety risks during high-speed excavation (Haitao et al., 2021; Wang et al., 2023). The frequent need to relocate drilling rigs and set up additional drainage stations in such scenarios significantly hinders excavation efficiency and increases operational costs. Haitao et al. (2021) investigated key technologies and equipment for surface large-diameter boreholes in coal mining areas, proposing two design methods based on different connection modes with roadways. They found that down-the-hole hammer and guide-pipe drilling improved pilot hole efficiency, while air-lift reverse circulation and cluster-type pneumatic hammer technologies enhanced reaming rates. Casing installation by buoyancy and cementing by interpolation ensured safety and quality. The authors concluded that these advancements provide reliable support for rapid borehole formation and mine emergency rescue. Li et al. (2023) studied efficient and precise directional drilling technologies and equipment for underground gas drainage in coal mines. Supported by national key projects, they developed three major systems: rotary geosteering intelligent drills, dual-power-head drills for soft seams, and large-diameter high-level directional drills. These advancements significantly improved borehole formation and gas extraction, enabling a shift from geometric to rotary geosteering and supporting gas drainage through “hole instead of roadway” technology. Furthermore, the inability of traditional techniques to address the long-term stability of borehole sealing exacerbates the risk of gas leakage and reduced drainage effectiveness.
In response to these challenges, the development and application of large-diameter precise directional drilling for long boreholes present a breakthrough solution. This technology offers significant advantages in enhancing gas drainage efficiency, improving roadway excavation safety, and reducing operational costs. By leveraging advanced directional drilling techniques, including triaxial accelerometers, magnetoresistance sensors, and intelligent trajectory control systems, this method achieves high-precision interconnection between boreholes. Additionally, integrating “two-block-one-injection” sealing technology with multi-diameter designs further improves gas drainage efficiency and sealing reliability, making it particularly suitable for complex geological conditions in high-gas environments.
This paper focuses on the application of large-diameter precise directional drilling technology at the 22106 working face of the Shangwan Coal Mine. The geological characteristics of the site, including a coal seam gas content of 6.02 m3/t and permeability coefficient of 0.865 m2/(MPa2·d), present significant challenges for traditional drainage techniques. Through the deployment of 120 mm diameter boreholes and subsequent expansion to 203 mm, combined with optimized sealing measures, this study achieves effective gas control and rapid roadway excavation. This study provides a comprehensive analysis of the principles, implementation, and outcomes of large-diameter precise directional drilling technology. The primary novelty of this research lies in the integration of advanced trajectory control methods, optimized multi-diameter borehole sealing techniques, and BP neural network-based predictive modeling for gas flow estimation. Unlike conventional gas drainage methods, our approach significantly enhances drilling precision, improves gas extraction efficiency, and enables proactive risk management through intelligent gas flow prediction. By maintaining gas concentrations between 0.27% and 0.40%, the proposed method ensures compliance with safety standards and supports a monthly excavation rate of 400 m. Furthermore, the study establishes a systematic framework for high-gas environment roadway excavation by incorporating real-time trajectory correction and data-driven gas extraction optimization. These innovations provide an effective solution to the limitations of traditional methods and offer a scalable approach applicable to various complex geological conditions. The findings of this research contribute to both theoretical advancements and engineering applications in coal mine safety and efficiency. Given the demonstrated effectiveness of the proposed method, we are also evaluating the feasibility of patenting key innovations related to trajectory correction and borehole sealing.
2 Overview of the excavation working face at Shangwan Coal Mine
2.1 Working face conditions
The cutting area of the 22106 working face at Shangwan Coal Mine is a critical region for gas management during roadway excavation. The volume of gas emissions during excavation is influenced by various factors, including coal seam gas content, coal seam permeability, and excavation speed. The roadway in this working face has a large cross-sectional area, measuring 5.5 m in width and 3.7 m in height, with a total cross-sectional area of 20.35 m2. The coal seam gas content is 6.02 m3/t, and the permeability coefficient is 0.865 m2/(MPa2·d), classifying it as an extractable coal seam. However, the high gas content combined with rapid excavation significantly increases gas emissions, posing a major constraint on safe and efficient roadway excavation. Traditional edge-drilling and gas extraction techniques are adequate for gas management in shallow coal seams but become insufficient as excavation progresses into deeper, high-gas zones. Elevated gas content in deeper seams significantly reduces the effectiveness of conventional drilling methods (Slastunov et al., 2022). To mitigate gas emission risks and enhance excavation efficiency, large-diameter long borehole technology was introduced. This method is specifically adapted to roadway conditions, enabling preemptive gas control and coordinated optimization with roadway excavation.
Gas management in the 22106 working face cutting area employs large-diameter precise directional drilling technology for long boreholes, with a single borehole diameter reaching 120 mm, compared to the traditional 94 mm diameter. This upgrade significantly enhances gas extraction efficiency and improves coal seam permeability. Each drilling site accommodates 23 large-diameter boreholes, with the terminal spacing dynamically adjusted based on coal seam gas content. When the gas content is between 6.0 and 7.0 m3/t, the terminal spacing is set at 7.0 m. If the gas content exceeds 7.0 m3/t, the spacing is reduced to 5.0 m. The optimized layout of these large-diameter boreholes not only effectively reduces coal seam gas content but also provides robust support for safe gas management during excavation.
Using field measurements, the gas emission volume was predicted under a monthly excavation progress of 400 m, applying the “Method for Predicting Mine Gas Emission Volume” (AQ 1018-2006) for various gas content levels. The results are illustrated in Figure 1.
According to the prediction results, when the coal seam gas content is 3.5, 4.0, 4.5, and 5.0 m3/t, the gas emission volume in the working face increases significantly with the distance, as shown in Figure 1. Through fitting analysis, the relationship between gas emission volume Q and coal seam gas content W can be approximated as linear. Higher gas content corresponds to a faster growth rate of gas emission, indicating greater gas release potential in high-gas-content coal seams. This result provides an important basis for optimizing gas management strategies. The linear relationship between gas emission volume Q and coal seam gas content W can be expressed as Equation 1:
Based on field measurement data, when the coal seam gas content is 4.0 m3/t, the predicted gas emission volume closely matches the measured value of 1.12 m3/min; while at a gas content of 5.0 m3/t, the difference between the predicted and measured gas emission volumes further decreases, demonstrating the high accuracy and reliability of the model predictions. Analysis of gas emission variations under different excavation speeds using the source-separation prediction method shows that gas emission volume is positively correlated with excavation speed. As excavation speed increases from 200 to 450 m/month, gas emission volumes rise significantly, with more pronounced increases observed in high-gas-content coal seams.
Furthermore, an additional analysis of gas emission variations under different excavation speeds was conducted using the source-separation prediction method. Assuming a coal seam gas content of 6.0 m3/t, the predicted results are shown in Figure 2. When excavation speeds are 250, 300, 350, 400, and 450 m/month, the gas emission volumes are 2.94, 3.57, 4.19, 4.76, and 5.27 m3/min, respectively. Fitting analysis shows that the relationship between gas emission volume Q and excavation speed V exhibits a significant positive correlation, which can be expressed as a linear Equation 2:
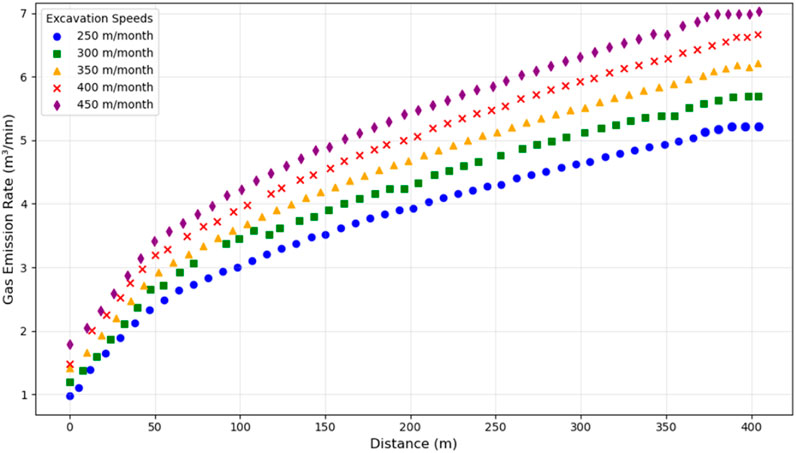
Figure 2. Predicted gas emission volumes at excavation faces under different monthly progress rates.
Analysis results indicate that with increasing excavation speed, gas emission volume rises significantly, highlighting a considerable increase in the risk of gas outbursts under high excavation speed conditions. Therefore, enhanced gas management measures should be implemented at higher excavation speeds to ensure operational safety.
According to the prediction results, gas emission volume at the 22106 working face of Shangwan Coal Mine is mainly influenced by coal seam gas content and excavation speed. In areas with low gas content, ventilation alone can effectively control gas concentration. However, in high-gas-content regions, intensified gas extraction and optimized excavation speed are required to prevent gas over-limit incidents. The application of an intelligent predictive model provides scientific guidance for the excavation of cut-off faces, ensuring safe and efficient progress.
2.2 Existing technical issues
The cut-off face of the 22106 working face at Shangwan Coal Mine is located in an area with low coal seam permeability and high gas content. Ensuring safety during excavation requires addressing key challenges related to gas emission and over-limit risks. The measured coal seam gas content is 6.02 m3/t, and the roadway has a large cross-sectional area combined with a high excavation speed, which further exacerbates the risk of gas emissions. During roadway excavation, the use of edge-drilling and extraction technology effectively reduces gas concentration, thereby preventing gas over-limit incidents.
Based on the actual conditions at Shangwan Coal Mine, during the excavation of the cut-off face, drilling stations are arranged every 50 m, with four edge-drilling and extraction boreholes in a fan-shaped layout at each station. Each borehole is 150 m long, with a terminal spacing of 3 m and a diameter of 94 mm. The layout of the edge-drilling and extraction boreholes is shown in Figure 3.
The gas extraction performance, as summarized in Table 1, demonstrates that the large-diameter precise directional drilling technology significantly improves the average gas extraction concentration compared to conventional methods. The pure extraction volume of individual boreholes also steadily increases over the extraction period. During the initial extraction stage (day 1), the average gas extraction concentration across the four boreholes was 32.13%, with a pure extraction volume of 0.095 m3/min. After 20 days, these values increased to 36.75% and 0.115 m3/min, respectively. Notably, Borehole #1 consistently exhibited superior extraction performance, achieving a concentration of 47.1% and a volume of 0.18 m3/min by day 20, indicating its pivotal role in gas extraction. Conversely, Borehole #2 demonstrated relatively lower efficiency, with only 24.3% concentration and 0.05 m3/min volume after 20 days, likely due to its specific location or coal seam characteristics. By establishing drilling stations every 50 m during cut-off face excavation and scientifically arranging long boreholes within each station, roadway gas concentrations were effectively maintained within a safe range of 0.27%–0.39%, ensuring reliable safety and proactive gas control in high-gas zones. The application of large-diameter precise directional borehole technology thus significantly enhanced both extraction concentration and volume, providing an effective approach and valuable reference for roadway excavation under similar high-gas geological conditions (Kocherla et al., 2021).
Edge-drilling and extraction technology effectively controls gas concentrations in shallow coal seams, ensuring excavation safety; however, its application faces constraints such as limited gas extraction efficiency and increased operational complexity. Specifically, the effective extraction period of traditional edge-drilling boreholes is relatively short, with an average gas extraction concentration of only 25.80%. While adequate for shallow seams with lower gas content, its efficiency diminishes significantly as excavation proceeds into deeper areas with higher gas content and outflow rates. Additionally, conventional edge-drilling methods require frequent relocations of drilling rigs, typically setting up a new drilling station every 50 m, with four boreholes per station. This frequent repositioning considerably increases gas management costs and reduces roadway excavation efficiency, impeding the achievement of rapid excavation goals (Li et al., 2025; Chen et al., 2025; Liu et al., 2023). To address the increasing challenges posed by rising gas content in deeper coal seams, there is an urgent need to adopt optimized technological solutions. Consequently, large-diameter precise directional drilling technology is introduced as an optimized solution, providing significantly improved gas extraction concentration and volume, reducing operational complexity, and offering strong support for safe, efficient, and rapid roadway excavation in high-gas environments.
3 Technological design and methods
3.1 Accurate pilot hole penetration technology
Large-diameter, long-distance boreholes in coal mines often face challenges in achieving the required terminal diameter using a single-pass drilling approach. Therefore, a common practice is to drill small-diameter pilot holes first to achieve accurate interconnections between two roadways, followed by stepwise reaming to reach the desired terminal diameter. Accurate penetration of pilot holes is a critical task that determines the success of the entire drilling project (Yang et al., 2022; LIU et al., 2022).
Existing directional drilling trajectory control technologies in coal mines typically rely on mud pulse wireless systems or electromagnetic wave-based wireless directional drilling systems. These technologies enable real-time trajectory measurement and adjustments to guide the drill bit along a predetermined path. However, when the designed trajectory direction aligns with magnetic east or west or when other magnetic field interferences exist near the actual trajectory, significant fluctuations in measured magnetic azimuths may occur. This deviation often results in cumulative trajectory errors, ultimately affecting penetration accuracy. Figure 4 illustrates the deviation of the pilot hole’s actual trajectory.
To overcome the challenges of magnetic interference and trajectory deviation, the RMRS (Rotating Magnetic Range System) was introduced during the construction process. This system employs a strong magnetic connector within the target borehole to generate a constant magnetic field signal and uses signal-receiving probes in the actual borehole to collect signals and calculate the real-time distance between the drill bit and the target point. The RMRS system’s real-time measurement and closed-loop control functions ensure precise “point-to-point” connectivity for boreholes.
However, since the RMRS system has a detection range of only 70 m, for boreholes spanning several hundred meters or even kilometers, relying solely on 70 m of trajectory adjustment cannot avoid the accumulation of errors. This is especially true when significant cumulative errors occur in the early stages of the trajectory, which would create major challenges for subsequent reaming and casing installations.
To enhance the accuracy of penetration and address the aforementioned issues, the optimized construction plan proposes the following improvements:
In the optimization of large-diameter precise directional drilling technology, the selection of drilling parameters was systematically refined based on geological conditions, gas content, and excavation requirements. The pilot hole diameter was initially set at 120 mm to ensure high-precision directional control and facilitate subsequent reaming operations. After achieving pilot hole penetration, a staged reaming process was implemented to gradually expand the borehole to 203 mm, enhancing gas extraction efficiency while maintaining borehole stability. The borehole length was determined according to gas distribution characteristics and roadway layout, with a design length of 550 m at the 22106 working face of the Shangwan Coal Mine, ensuring sufficient extraction coverage and structural integrity. Borehole spacing was optimized to maximize extraction efficiency, based on field measurements and numerical simulations. When coal seam gas content ranged between 6.0 and 7.0 m3/t, the final borehole spacing was set at 7.0 m, whereas for gas content exceeding 7.0 m3/t, the spacing was reduced to 5.0 m to enhance gas drainage performance. To ensure the high-precision penetration of pilot holes, guide hole density was increased in areas with strong magnetic interference, reducing spacing from the traditional 100–50 m to improve real-time monitoring accuracy. Additionally, an integrated approach combining an inertial navigation system (INS) and acoustic ranging technology was applied alongside the Rotating Magnetic Range System (RMRS) to achieve precise trajectory correction. With the RMRS system’s detection range extended from 70 m to over 100 m through high-sensitivity probes and signal enhancement devices, borehole trajectory measurement accuracy was further improved. During drilling operations, the drilling speed was controlled within 0.8–1.2 m/min to ensure trajectory stability, while the torque was maintained within 750–950 N·m to prevent excessive stress that could lead to borehole instability. The optimized borehole layout and technological enhancements resulted in an average gas extraction concentration of 80.2%, a 3.1-fold improvement over traditional methods, while the pure extraction volume reached 0.44 m3/min, representing a 10.3-fold increase compared to conventional techniques. These results validate the high efficiency and applicability of this technology under complex geological conditions. In addition, inertial navigation systems (INS) and acoustic ranging technologies are introduced to work in conjunction with the existing magnetic measurement systems, forming a multi-technology trajectory correction scheme, as shown in Figure 5. In conditions with severe magnetic interference, the INS provides short-term, high-precision trajectory data, while the acoustic ranging technology provides auxiliary positioning support, enabling high-precision trajectory corrections in complex geological conditions.
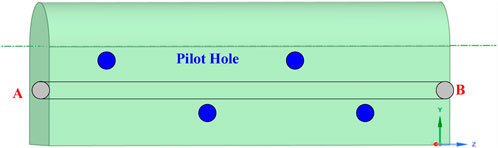
Figure 5. Relationship between the designed trajectory of large-diameter long-distance boreholes and the relative Position of guide holes.
During the entire construction process, an intelligent trajectory control system was introduced. This system combines real-time drilling parameters, historical data, and gas content information to construct a machine learning model for comprehensive prediction and dynamic correction of drill bit trajectory deviations and gas concentration changes. The system optimizes drilling parameters automatically by integrating geological conditions and gas distribution patterns, enhancing trajectory adjustment precision while enabling real-time gas concentration monitoring.
Real-time gas data is used to predict gas outburst conditions, allowing for early planning of borehole reaming paths and ventilation schemes to effectively reduce the impact of gas outbursts on construction safety. High-sensitivity probes and signal enhancement devices extend the RMRS system’s detection range from 70 m to over 100 m. Additionally, the integration of gas sensors ensures high-precision real-time sensing of gas concentration distribution.
The synergy of these technologies enables boreholes to maintain precision under complex geological conditions while significantly improving safety and construction efficiency. The optimized plan strongly supports the broad application of large-diameter long-distance borehole penetration technology in underground coal mining.
3.2 Graded reaming technology
After the pilot hole achieves “point-to-point” penetration between both sides of the roadway with precision, graded reaming technology is employed to gradually enlarge the borehole diameter to the design specification. This process is essential for ensuring borehole formation efficiency, maintaining drilling stability, and improving gas drainage effectiveness. A properly designed reaming sequence is critical, as an excessively large step increase in diameter reduces drilling efficiency and raises the risk of tool overloading and borehole collapse, whereas a sequence that is too small prolongs the construction period and increases costs. In this study, the borehole diameter was expanded from 120 to 203 mm using a multi-stage reaming approach, incorporating a combination of reaming drill bits, positive displacement motors, and spiral centralizers to enhance stability and minimize deviation. Reverse-pull reaming was employed to further improve trajectory accuracy, preventing drill rod bending and maintaining alignment with the pilot hole. The optimized reaming process significantly improved coal seam permeability and gas drainage efficiency by enhancing borehole connectivity and reducing gas retention. Real-time trajectory monitoring and gas concentration data were integrated into an intelligent control system, allowing for dynamic reaming adjustments to prevent gas accumulation and ensure safe operation. This systematic approach effectively increased gas extraction efficiency and supported high-speed roadway excavation while mitigating the risks associated with gas outbursts.
3.3 Borehole circulation + mechanical assistance
Based on the precise trajectory and gradual diameter expansion ensured by pilot hole penetration and graded reaming techniques, the slag discharge issue for large-diameter long-distance boreholes becomes a key constraint for construction efficiency and safety. Due to the large borehole diameter and depth, existing high-power underground mud pumps cannot meet the required discharge capacity for crushed rock debris. Even with the use of spiral drill rods for rock debris transport via drill rotation during reaming, inadequate slag discharge often leads to excessive drill rod torque, high feed pressure, and even incidents such as drill sticking or tool breakage (Pal et al., 2021; Wang et al., 2021; Cai et al., 2021).
To effectively address slag discharge challenges during the reaming process, the optimized construction plan proposes a combined slag discharge approach termed “borehole circulation on one end plus mechanical assistance on the other end.” In this method, slag discharge tools consisting of spiral drill rods and specialized drill bits are inserted into one end of the borehole to disturb and fragment rock debris through high-speed rotation. On the opposite end, a straight drill rod assembly is utilized to deliver high-pressure, high-flow mud via a mud pump, effectively flushing out crushed debris adhered to the borehole wall. The slag discharge drill bit incorporates thick steel plates of irregular shapes and diamond composite teeth, combined with PDC drill teeth and guiding steel-tube structures, enhancing rock-breaking capabilities and improving debris removal efficiency. The disturbed debris is transported out of the borehole by the laminar flow of circulating fluid and is further discharged through high-pressure flushing. Moreover, intelligent optimization of reaming paths, guided by real-time gas monitoring data, allows for the early detection of lithological variations or abnormal gas zones during slag removal, facilitating dynamic adjustment of drilling parameters to avoid debris accumulation and gas-related hazards. Synchronized advancement between slag discharge and reaming equipment ensures continuous and stable operation: when one drill rig withdraws a drill rod, the other simultaneously adds a new rod, maintaining seamless workflow continuity. Compared with traditional single-end slag discharge methods, this integrated process fully leverages the high-precision trajectory of pilot holes and the stability of graded reaming paths, providing a robust solution for safe, efficient, and high-quality construction of large-diameter long-distance boreholes.
3.4 Prediction of tunnel gas outflow under different excavation speeds
During the construction of large-diameter long-distance boreholes, predicting gas outflow in the tunnel is critical to ensuring construction safety. As excavation speed varies, the gas outflow pattern is influenced by multiple complex factors, including coal seam gas content, coal permeability, and the contact area between the borehole trajectory and the coal seam. Therefore, establishing an effective prediction model to accurately estimate gas outflow under different excavation speeds is essential for optimizing construction processes and preventing gas-related incidents (Cai et al., 2021; Lei, 2021). In this study, Python was used as the primary tool for data processing, machine learning modeling, and predictive analysis. Data preprocessing, including noise reduction, feature extraction, and normalization, was conducted using pandas and NumPy to ensure the dataset’s consistency and suitability for machine learning. The BP neural network model was implemented with TensorFlow and Keras to predict gas outflow under different excavation speeds and borehole configurations. Hyperparameter optimization was performed using Grid Search and Bayesian Optimization to enhance model accuracy, with the final model achieving a prediction deviation of less than 2%. Visualization and result validation were carried out using Matplotlib and Seaborn, enabling a clear comparison between predicted and actual gas extraction concentrations. Python’s scikit-learn library was employed to assess model performance through metrics such as mean squared error (MSE) and R2 values. Compared to traditional statistical tools like MS Excel, Python provides greater flexibility, scalability, and automation, particularly in handling large datasets and optimizing complex machine learning models. The ability to integrate real-time data processing and adaptive modeling significantly enhances the reliability of gas emission predictions and supports the optimization of drilling strategies in high-gas coal seams.
The BP neural network model is used to predict gas outflow in the tunnel under different excavation speeds. BP neural networks, capable of adaptively learning complex relationships between input data and output results through nonlinear mapping of multiple neurons, provide high prediction accuracy. The prediction model uses excavation speed, coal seam gas content, coal permeability coefficient, and the contact area between the pilot hole trajectory and the coal seam as input variables, with gas outflow as the output variable (Ren and Wang, 2023).
The basic structure of the BP neural network consists of an input layer, hidden layers, and an output layer (Gong et al., 2025; Hairong et al., 2022; Zhang et al., 2024). Input layer variables x1,x2,…,xn correspond to excavation speed and coal seam characteristic parameters; the hidden layers implement nonlinear activation function mappings through weights wij and biases bj; the output layer calculates the gas outflow y. The goal of model training is to minimize the error E between the predicted output yi and the actual measured value dii. The loss function can be expressed as Equation 3:
The number of samples is denoted as N. The weights and biases are updated using the gradient descent method as Equations 4, 5:
where η is the learning rate.
In the model construction process, normalization of historical drilling data ensures that all input variables are within the same magnitude range, preventing the training effect from being compromised by large numerical differences. After normalization, the dataset is reasonably divided into training and testing sets for model training and validation. Through multiple experimental adjustments, the network structure was optimized, including the number of hidden layers and the number of neurons per layer, ensuring strong fitting and generalization capabilities of the model.
During training, to evaluate model convergence and optimization, training loss and validation loss were recorded against the number of iterations, as shown in Figure 6. It can be observed from the figure that both training and validation losses decrease gradually with the increase in training epochs and eventually stabilize, indicating good convergence of the model without overfitting.
The hyperparameters and structural design of the model were adjusted through multiple experiments, and the specific parameters are shown in Table 2.
4 Shangwan Coal Mine engineering demonstration and application results
4.1 Large-diameter long borehole technology for safe and rapid roadway excavation
The measured uniaxial compressive strength of the coal seam at the 22106 working face of Shangwan Coal Mine is 11.49 MPa, with a hardness coefficient f = 0.91, indicating high coal body strength, making it suitable for borehole drilling. Previously, the Shangwan Coal Mine employed the VLD-1000 km drilling rig to drill ⌀120 mm boreholes under similar geological conditions, with a maximum length of 1,082 m, demonstrating the suitability of the mine’s coal seam conditions for large-diameter long boreholes.
The proposed design uses the VLD-1,000 km drilling rig to drill large-diameter long boreholes along the side of the roadway, ensuring safe and rapid excavation. Large-diameter boreholes offer superior pressure relief and permeability enhancement effects. This project employs ⌀120 mm large-diameter boreholes to improve gas drainage efficiency, with a designed borehole length of 550 m. The gas drainage strategy is tailored to the coal seam gas content as follows:
For a gas content of 6.0–7.0 m3/t: Each drilling site is equipped with two large-diameter long boreholes, with a final borehole spacing of 7.0 m.
For a gas content of 7.0–8.0 m3/t: The borehole layout is densified, with three large-diameter long boreholes per drilling site and a final borehole spacing of 5.0 m.
The detailed layout is shown in Figure 7.
Shangwan Coal Mine utilized a kilometer-class drilling rig to complete the construction of a 550 m-long, ⌀120 mm borehole. Subsequently, the borehole was reamed to a ⌀203 mm large-diameter borehole, with a reaming length of 15 m. Following this, a ZBQ-27/1.5 grouting pump was employed to inject micro-expansion cement, significantly enhancing the borehole sealing performance due to the diameter variation. This optimized process is particularly suitable for large-section, high-gas roadway excavation at the 22106 working face.
At the 22106 working face, a key area for gas management, a drilling site was arranged every 400 m along the transport roadway. Based on coal seam gas content, each site was designed to include two ⌀203 mm large-diameter long boreholes for pressure relief, permeability enhancement, and gas drainage. After borehole completion, the “two-plug-one-injection” sealing process was used for closure. In this process, gypsum was used to seal both the bottom and the opening of the extraction pipe, while high-pressure grouting pumps injected micro-expansion cement grout for a sealing length of 20 m, as shown in Figure 8.
To accommodate the thick and low-permeability coal seam characteristics at the 22106 working face, the sealing process was further optimized with a variable-diameter design. The opening section of the borehole utilized ⌀203 mm large-diameter boreholes with a sealing length of 15 m, while the deeper section used ⌀120 mm boreholes with a sealing length of 5 m. This design effectively sealed fractures at the top of the borehole, ensuring the sustainability and safety of gas drainage.
According to gas drainage monitoring data, the variations in gas extraction concentration and pure volume over time for a specific borehole are shown in Figure 9. The analysis indicates that as extraction time increases, the gas extraction concentration gradually decreases from the initial high concentration, but overall remains at a relatively high level. Simultaneously, the gradual decline in pure extraction volume suggests that gas around the borehole is progressively drained and released.
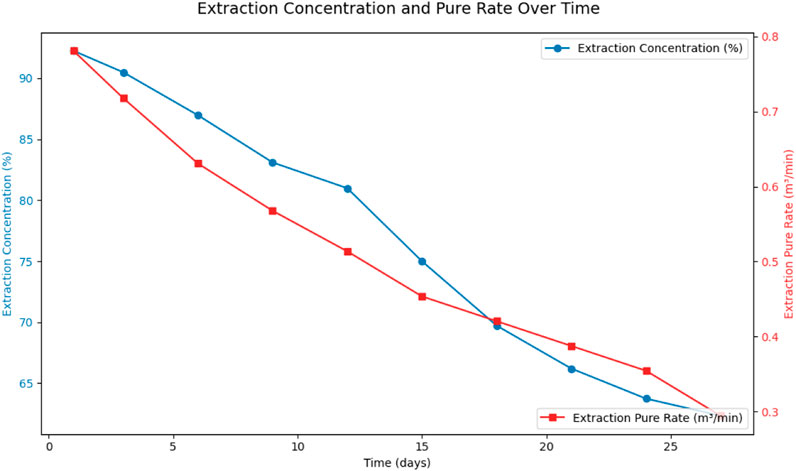
Figure 9. Gas extraction concentration and pure volume of large-diameter long boreholes at different times.
As shown in Figure 9, the gas extraction concentration using the large-diameter long borehole technology for roadway excavation gradually decreased over 27 days, from a peak of 92.25%–62.32%. The measured average concentration over this period was 77.93%. According to the predictive model analysis, the average gas extraction concentration over 30 days was 80.2%. The slight discrepancy between the predicted and measured values may be due to the model’s overestimation during the high-concentration phase; however, the overall trends are consistent. Both results significantly surpass the 25.8% achieved by traditional edge-drilling and extracting methods, with an improvement factor of approximately 3 times. This demonstrates the significant efficiency advantage of the large-diameter long borehole technology in sustained gas extraction.
4.2 Gas concentration prediction and efficiency evaluation
To validate the effectiveness of the large-diameter long borehole technology in gas management, a gas concentration prediction model was constructed based on key factors such as coal seam gas content, permeability, and excavation speed. The BP neural network was used to predict gas concentration, with input parameters including excavation speed, coal seam gas content, and initial extraction concentration, and the output being gas concentration values at different times.
The model, after training and validation, achieved high prediction accuracy. The predicted trend of gas concentration changes indicated a high initial concentration, followed by a gradual decrease and stabilization. A comparison with measured data showed that the gas concentration decreased from an initial value of 92.25%–62.32% after 27 days, with an average concentration of 77.93%. This closely matched the measured average concentration of 78.15%, with a deviation rate of less than 2%. The predicted and measured trends are illustrated in Figure 10.
The predicted and measured results demonstrate that the large-diameter long borehole technology offers significant efficiency advantages in sustained gas extraction. The extraction concentration is markedly higher than that achieved by traditional edge-drilling and extracting techniques. Initially, the gas extraction pure volume is relatively high, gradually decreasing and stabilizing over time, with an average pure volume of 0.48 m3/min. This is significantly higher than the 0.043 m3/min achieved by traditional methods, representing an efficiency improvement of approximately 11.2 times.
This technology effectively reduces roadway gas concentrations, maintaining them within a safe range of 0.27%–0.40%, thereby providing reliable assurance for excavation operations. At the 22106 working face of the Shangwan Coal Mine, the application of this technology enabled a monthly roadway excavation rate of 400 m, further verifying its engineering applicability.
4.3 Measurement and forecasting error analysis
The accuracy of methane concentration measurements and predictions was assessed to ensure the reliability of gas control strategies. Methane concentration was measured using high-precision infrared gas analyzers with an accuracy of ±0.02%, and systematic calibration was conducted before each measurement using standard methane gas to maintain consistency. Random errors were minimized by performing multiple measurements at each sampling point and averaging the results to reduce fluctuations caused by environmental variations and instrument sensitivity. The BP neural network model used for methane concentration prediction was validated against field data, with the mean absolute error (MAE) calculated as 0.015 and the root mean square error (RMSE) as 0.021, indicating a strong correlation between predicted and actual values. The deviation between predicted and measured methane concentrations remained within 2%, demonstrating high forecasting accuracy.
4.4 Comparative analysis with traditional models
To visually illustrate the effectiveness of large-diameter precise directional drilling technology compared to traditional drilling methods, a comparative analysis was conducted as shown in Figure 11.
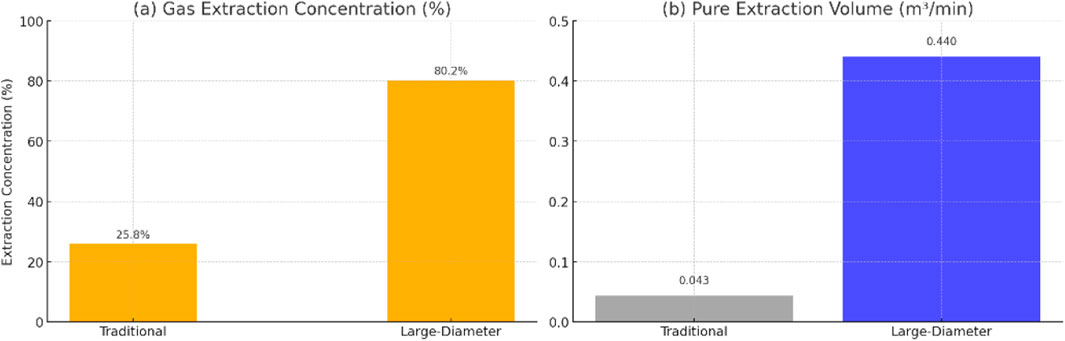
Figure 11. Comparison of gas extraction effectiveness between large-diameter precise directional drilling and traditional drilling. (a) Gas extraction concentration; (b) Pure extraction volume.
As shown in Figure 11, the large-diameter precise directional drilling technology demonstrates clear advantages over traditional methods. Specifically, the average gas extraction concentration using large-diameter drilling reached 80.2%, a 3.1-fold improvement compared to the conventional method (25.8%). Similarly, the average pure extraction volume per borehole increased to 0.44 m3/min, which is approximately 10.3 times higher than that of traditional methods (0.043 m3/min). This performance gap is particularly pronounced under conditions of high gas content. These results conclusively demonstrate the superiority of large-diameter precise directional drilling technology for gas management, validating its effectiveness and highlighting its potential for widespread adoption in similar geological conditions.
5 Results and discussion
The findings of this study underscore the significant enhancements achieved by large-diameter precise directional drilling technology in terms of gas extraction concentration and efficiency. Field measurements and predictive modeling indicated an average single-borehole gas extraction concentration of 80.2%, approximately 3.1 times higher than the conventional edge-drilling method, and a pure extraction volume of 0.44 m3/min, representing a 10.3-fold improvement. Moreover, the BP neural network model predicted gas concentrations with high accuracy (deviation <2%), validating the effectiveness of intelligent modeling approaches. However, the study acknowledges limitations such as the reliance on expensive specialized equipment, the complexity of precise trajectory control requiring high technical expertise, and challenges associated with advanced sealing materials and real-time monitoring systems. Furthermore, conclusions are currently based on a single-site demonstration, thus limiting the generalizability of findings. Future research should focus on rigorous comparisons across broader geological contexts and multiple locations, systematic evaluations of automation integration, and real-time monitoring capabilities to enhance both economic feasibility and operational safety, thereby extending the applicability and innovative impact of this technology.
Data availability statement
The original contributions presented in the study are included in the article/supplementary material, further inquiries can be directed to the corresponding author.
Author contributions
JZ: Conceptualization, Data curation, Formal Analysis, Funding acquisition, Investigation, Methodology, Project administration, Resources, Software, Supervision, Validation, Visualization, Writing – original draft, Writing – review and editing.
Funding
The author(s) declare that no financial support was received for the research and/or publication of this article.
Conflict of interest
Author JZ was employed by China Shenhua Energy Co., Ltd.
Generative AI statement
The author(s) declare that no Generative AI was used in the creation of this manuscript.
Publisher’s note
All claims expressed in this article are solely those of the authors and do not necessarily represent those of their affiliated organizations, or those of the publisher, the editors and the reviewers. Any product that may be evaluated in this article, or claim that may be made by its manufacturer, is not guaranteed or endorsed by the publisher.
References
Cai, W., Dou, L., Si, G., and Hu, Y. (2021). Fault-induced coal burst mechanism under mining-induced static and dynamic stresses. Engineering 7 (5), 687–700. doi:10.1016/j.eng.2020.03.017
Chen, Z., Zhang, S., Lu, Y., Yang, Z., Wang, L., and He, F. (2025). Study on zonal support mechanism and the surrounding rock control technology of rock roadway excavated by TBM in coal mine. Energy Sci. Eng. 13, 1239–1254. doi:10.1002/ese3.2059
Gong, X., Li, B., Yang, Y., Li, M., Li, T., Zhang, B., et al. (2025). Construction and application of optimized model for mine water inflow prediction based on neural network and ARIMA model. Sci. Rep. 15 (1), 2009. doi:10.1038/s41598-025-85477-2
Hairong, G. U., Zenghai, S., Longpeng, W., Shao, T., Zou, Z., and Gao, Z. (2022). Research progress of lifting equipment for large-diameter borehole rescue. Coal Geol. Explor. 50 (11), 6. doi:10.12363/issn.1001-1986.22.06.0441
Haitao, M. O., Shijun, H. A. O., and Jiangpeng, Z. (2021). Key technology and equipment of hole-forming for surface large diameter borehole in coal mine area. COAL Sci. Technol. 49 (5), 190–197. doi:10.13199/j.cnki.cst.2021.05.024
Kang, H., Gao, F., Xu, G., and Ren, H. (2023). Mechanical behaviors of coal measures and ground control technologies for China's deep coal mines–A review. J. Rock Mech. Geotechnical Eng. 15 (1), 37–65. doi:10.1016/j.jrmge.2022.11.004
Kocherla, A., Duddi, M., and Subramaniam, K. V. L. (2021). Embedded PZT sensors for monitoring formation and crack opening in concrete structures. Measurement 182, 109698. doi:10.1016/j.measurement.2021.109698
Lei, H. A. N. (2021). Key technology of directional drilling for water prevention and control of bottom plate limestone in zhangji coal mine. J. Phys. Conf. Ser. IOP Publ. 1986 (1), 012058. doi:10.1088/1742-6596/1986/1/012058
Li, C., Yang, R., Zuo, J., and Xie, P. (2025). Theory and field tests of innovative cut blasting method for rock roadway excavation. Tunn. Undergr. Space Technol. 155, 106180. doi:10.1016/j.tust.2024.106180
Li, X., Cao, Z., and Xu, Y. (2021). Characteristics and trends of coal mine safety development. Energy Sources, Part A Recovery, Util. Environ. Eff., 1–19. doi:10.1080/15567036.2020.1852339
Li, Q., Yao, K., Fang, J., Yao, Y., Shi, C., et al. (2023). Directional drilling technology and equipment for efficient and accurate gas drainage underground coal mine. Coal Sci. Technol. 51 (S1), 65–72. doi:10.13199/j.cnki.cst.mcq22-24shu
Liu, Z. L., Ma, Z. G., Kazanin, O. I., Gong, P., Li, Y., and Ni, X. Y. (2023). Deformation control technology of gob-side entry retaining with large volume cfst roadway side support in top-coal caving longwall and stability analysis: a case study. Appl. Sci. 13 (15), 8610. doi:10.3390/app13158610
Liu, M., Hao, S., Zheng, Y., Bai, G., Li, P., and Li, B. Z. (2022). Study on safe tunneling penetration technology for large diameter rescue wells. Coal Sci. Technol. 50 (3), 118–126. doi:10.13199/j.cnki.cst.ZT20-007
Pal, S. K., Tripathi, A. K., Panda, S., and Palaniappan, S. K. (2021). Sonar mapping of abandoned water-logged underground coal mine and backfilling operation using underwater camera. Int. J. Min. Mineral Eng. 12 (3), 181–194. doi:10.1504/ijmme.2021.119205
Ren, Z., and Wang, H. (2023). Gas migration around large diameter borehole with the protective screen pipe in fractured soft coal seam. ACS omega 8 (29), 26035–26044. doi:10.1021/acsomega.3c02126
Slastunov, S., Kolikov, K., Batugin, A., Sadov, A., and Khautiev, A. (2022). Improvement of intensive in-seam gas drainage technology at kirova mine in kuznetsk coal basin. Energies 15 (3), 1047. doi:10.3390/en15031047
Wang, W., Lu, S., Li, M., and Wang, C. (2021). Coal breakage impact by high-pressure water jet and induced pressure relief and permeability enhancement by hydraulic flushing cavity: mechanism and application. Arabian J. Geosciences 14, 2399. doi:10.1007/s12517-021-08660-5
Wang, Z., Yang, X., Wang, G., and Gong, H. (2023). Study on instability characteristics of the directional borehole on the coal-seam roof: a case study of the tingnan coal mine. Processes 11 (6), 1675. doi:10.3390/pr11061675
Wen, H., Cheng, B., Zhang, D., Jia, B., and Liu, X. (2024). Improving coalbed methane recovery in fragmented soft coal seams with horizontal cased well cavitation. Sci. Rep. 14 (1), 29942. doi:10.1038/s41598-024-81435-6
Wu, B., Wang, J., Qu, B., Qi, P., and Meng, Y. (2023). Development, effectiveness, and deficiency of China's coal mine safety supervision system. Resour. Policy 82, 103524. doi:10.1016/j.resourpol.2023.103524
Xue, C., Cao, A., Guo, W., Liu, Y., Wang, S., Dong, J., et al. (2022). Mechanism and energy evolution characteristics of coal burst in mining thick, deep, and large inclined coal seams: a case study from a Chinese coal mine. Geofluids 2022 (1), 1–18. doi:10.1155/2022/7704226
Yang, Z., Qi, H., and Tian, B. (2022). Construction and application of dynamic risk knowledge graph of large diameter emergency rescue well. Second Int. Conf. Cloud Comput. Mechatron. Eng. (I3CME 2022) 12339, 468–476. SPIE. doi:10.1117/12.2655015
Zhang, J., Zhou, W., Wang, P., Wu, Y., Wang, P., Liu, Z., et al. (2024). Study on production improvement with multi-scale geomechanical modelling for horizontal wells in unconventional Resources. SPE EOR Conf. A. T. Oil Gas West Asia. SPE, D031S031R003. doi:10.2118/218627-MS
Keywords: large-diameter drilling, precise directional drilling, gas drainage, coal mine construction, borehole sealing
Citation: Zhang J (2025) Application of large-diameter precise directional drilling borehole formation technology in coal mine construction. Front. Built Environ. 11:1567141. doi: 10.3389/fbuil.2025.1567141
Received: 29 January 2025; Accepted: 31 March 2025;
Published: 20 June 2025.
Edited by:
Jaroslaw Rybak, Wrocław University of Science and Technology, PolandCopyright © 2025 Zhang. This is an open-access article distributed under the terms of the Creative Commons Attribution License (CC BY). The use, distribution or reproduction in other forums is permitted, provided the original author(s) and the copyright owner(s) are credited and that the original publication in this journal is cited, in accordance with accepted academic practice. No use, distribution or reproduction is permitted which does not comply with these terms.
*Correspondence: Jinlong Zhang, amluZ2xvbmd6aGFuZzIwMjVAMTYzLmNvbQ==