- 1Department of Civil Engineering, Arak Branch, Islamic Azad University, Arak, Iran
- 2Department of Concrete Technology, Road, Housing and Urban Development Research Center (BHRC), Tehran, Iran
- 3Department of Textile Engineering, Arak Branch, Islamic Azad University, Arak, Iran
This study develops innovative hybrid fiber-reinforced Engineered Cementitious Composites (ECC) to advance sustainable construction materials. By incorporating ternary fiber systems (steel, synthetic, PVA) with supplementary cementitious materials (GGBFS, silica fume), the composites achieved significant enhancements: a 40% increase in compressive strength (94.8 MPa), 31% higher tensile strength (8.99 MPa for S10F20P2), and 20% improved flexural toughness (120 N.mm for S20F10P2), while limiting crack widths to ∼60 μm. Durability tests revealed low water penetration (3.5 mm), reduced chloride ingress (87 coulombs), and 4.4 g/m2 mass loss during freeze-thaw cycles. The integration of industrial byproducts reduced CO2 emissions by 338.2 kg/m3, demonstrating dual mechanical and environmental advantages. These results highlight the potential of ternary hybrid fiber systems for high-performance, eco-friendly concrete overlays, bridging material innovation with sustainable construction practices.
1 Introduction
Concrete is globally recognized as one of the most essential building materials and is widely used in constructing various structures and road infrastructures. However, unreinforced concrete has limitations, including low flexural and tensile strength, limited toughness, large crack widths, and brittle behavior under tensile and flexural loading. The increasing demand for advanced civil infrastructure has led to a significant rise in concrete and cement consumption, resulting in the depletion of natural resources and substantial carbon dioxide emissions. Research indicates that cement production accounts for approximately 5%–7% of global greenhouse gas emissions (Shoji et al., 2022; Ramezani and Esfahani, 2018; Modarres and Ghalehnovi, 2024; Hasani et al., 2021). While fiber-reinforced concretes (FRCs) partially address these issues, they still exhibit softening tensile behavior and limited ductility (Ravichandran et al., 2022).
Strain-hardening cementitious composites (SHCCs), also known as engineered cementitious composites (ECC), have been developed to overcome these challenges. ECCs employ a unique failure management strategy that ensures efficient fiber distribution, enhancing crack resistance and superior toughness (Soe et al., 2013). Introduced in the 1990s by Lee and his colleagues, ECCs are a specialized category of ultra-high-performance fiber-reinforced concrete (UHPFRC) based on micromechanical theory (Kafodya and Okonta, 2020; Kanda and Li, 1998; Zarei et al., 2022; Li et al., 2002). Unlike conventional concrete, ECC exhibits strain-hardening behavior after initial cracking, similar to ductile metals, with a strain capacity 300 to 500 times greater than regular concrete. Additionally, ECC demonstrates superior crack width control under loading, with microcracks propagating uniformly and stabilizing at approximately 60 μm due to its micromechanical design (Gillani et al., 2020). The exclusive use of fine sand in ECC formulations further enhances strain capacity and promotes multiple cracking (Li, 1993; Li et al., 1995; Ahmad et al., 2025). However, the absence of coarse aggregates in ECC results in higher cement consumption, often exceeding 1,000 kg/m3 in standard formulations (Asghar and Khattak, 2024). Although ECC shows promise for structural applications, its relatively lower compressive strength than other concrete materials remains a limitation (Ruan et al., 2018; Choucha et al., 2018). Enhancing compressive strength and modulus of elasticity while maintaining adequate plasticity could significantly improve its effectiveness, as these properties are critical for structural design (Liu et al., 2023).
Concrete overlays are vital in improving pavement structural performance by addressing fatigue and durability issues caused by prolonged service life. The mechanical properties of these overlays directly influence the performance of restored pavements. Engineered cementitious overlays, characterized by high strength and flexibility, offer superior performance. Investigating the properties of composite overlays with various fiber types is essential for optimizing their application in pavement repair (Hasani et al., 2021; Sobhani and Pourkhorshidi, 2021; Chompoorat et al., 2023; Buathong et al., 2023; Chompoorat et al., 2021).
The hybridization of different fiber types has been shown to enhance tensile strength and toughness in concrete (Hasani et al., 2021; Buathong et al., 2023; Chompoorat et al., 2021; Pakravan et al., 2016). Macro-synthetic fibers, for instance, improve the mechanical properties of concrete (Hasani et al., 2021), while combining polyethylene and steel fibers enhances ECC’s flexural, compressive, and tensile strength (Choi et al., 2016). Including varying-sized fibers effectively controls crack propagation and distribution in concrete (Yao et al., 2003; Chen and Liu, 2005; Cheng and Huang, 2022). Increasing the steel fiber content in concrete boosts compressive strength and tensile modulus (Kang et al., 2016). Similarly, the combination of polyethylene (PE) and steel fibers positively impacts the tensile strength of high-performance concrete (Chen and Liu, 2005). However, incorporating steel fibers alongside PVA fibers reduces the tensile strain capacity of ECC.
In contrast, the combination of PVA and basalt fibers enhances it due to the strong bonding properties of basalt fibers (Wang et al., 2019). The hybrid use of steel and polyethylene fibers in ECC improves performance under repeated loading and effectively controls crack width during flexural loading (Zhu et al., 2024). Combining steel and polyethylene fibers enhances ECC’s tensile strain capacity and resistance (Zhu et al., 2024). Studies have also demonstrated that the hybrid use of PE and PVA fibers significantly improves the mechanical properties of ECC (Shi et al., 2020). Combining steel and PVA fibers has enhanced cracking resistance and flexural performance (Soe et al., 2013).
Fibers are categorized into two categories based on size: microfibers and macrofibers. Microfibers, typically 6–20 mm in length and tens of microns in diameter, have limited impact on structural performance under large deformations. In contrast, macrofibers, ranging from 30 to 60 mm long and over 0.3 mm in diameter, provide load-bearing capacity and control visible cracks, similar to reinforcing bars, after matrix failure (Mehta, 2002).
The global concrete production exceeds 10 billion tons annually, with each ton of Portland cement production releasing approximately one ton of carbon dioxide into the atmosphere (Malhotra, 2000; Kim et al., 2007). The extensive use of riverbed sand as fine aggregate in concrete has led to environmental degradation, including riverbed erosion and increased vulnerability to floods and storms (Mehta, 2002). ECC, which eliminates the need for coarse aggregates, offers a sustainable alternative. However, its higher cement content than conventional concrete increases costs and carbon emissions (Modarres and Ghalehnovi, 2024). To reduce this issue., supplementary cementitious materials (SCMs) such as granulated blast furnace slag (GGBFS) (Sumukh et al., 2024; Qiu et al., 2016; Zhu et al., 2014) and silica fume (Zhu et al., 2014; Zhang et al., 2016; Liu et al., 2018; Wang et al., 2020) can be used as partial replacements for cement. Research has shown that incorporating GGBFS and silica fume enhances the compressive strength of ECC (Wang et al., 2020).
A key innovation of this research is the incorporation of GGBFS and silica fume to reduce cement consumption, thereby addressing environmental concerns associated with carbon dioxide emissions. This research aims to evaluate hybrid fiber’s simultaneous effects on the fresh, hardened, and durability properties of ECC containing these fibers in binary and ternary combinations by experimental tests demonstrated in Figure 1.
2 Materials
In this experimental study, industrial by-products, including silica fume (SF) and ground granulated blast furnace slag (GGBFS), were used in conjunction with ordinary Portland cement (OPC), silica sand, and micro silica to create engineered cementitious composites (ECC). Images of the raw materials are presented in Figure 2. The chemical compositions of the ordinary Portland cement, micro silica, silica fume, and ground granulated blast furnace slag are detailed in Table 1. A polycarboxylate-based superplasticizer was included to ensure the mixture’s workability. The polycarboxylate superplasticizer was specifically selected for this study due to its superior performance characteristics in fiber-reinforced ECC. Its steric hindrance mechanism provides excellent water reduction while maintaining prolonged workability, which is critical for ensuring proper fiber distribution without segregation. The anionic carboxylate groups create strong electrostatic repulsion between cement particles, significantly improving the dispersion of hybrid fibers and preventing fiber balling that a common issue in high fiber content mixes. Furthermore, three types of fibers—steel, synthetic, and polyvinyl alcohol (PVA) — were utilized in this study. Additionally, Figure 3 displays the results of the grain size analysis for the ordinary Portland cement (OPC), silica sand, micro silica, silica fume (SF), and ground granulated blast furnace slag (GGBFS), along with their corresponding curves. The microsilica byproduct (2–30 μm) from silica sand crushing effectively fills voids between cement and sand particles, reducing porosity and creating a denser ECC matrix. Images of the fibers are presented in Figure 4, and their properties are listed in Table 2. Table 3 illustrates the ECC mixtures formulated for the experimental procedures.
3 Experimental program
3.1 Mixing process
The mixing procedure was carefully designed to ensure homogeneous fiber distribution and optimal workability. A planetary mixer with a capacity of 50 L was utilized at a constant speed of 120 rpm. The dry components, including Type II Portland cement and silica sand, blended for 3 min. Approximately 80% of the mixing water containing a polycarboxylate-ether-based superplasticizer was gradually added over 2 min. The pre-mixed fibers were slowly introduced in 30-s intervals while the speed of the mixer was decreased. To 60 rpm to prevent balling. The mixture underwent final wet mixing for 3 min at 150 rpm, with periodic visual inspections confirming uniform fiber dispersion without clumping.
3.2 Casting and curing
The samples were prepared according to ASTM C31 (ASTM C31-22, 2022) and cured following ASTM C511 (ASTM C511-22, 2022) standards. Cubic and cylindrical specimens were cast in steel molds in three equal layers, with each layer receiving 25 strokes of rod compaction. Immediately after casting, all specimens were covered with damp burlap and polyethylene sheets and stored in a temperature-controlled room (25°C ± 2°C) for 24 h as specified in ASTM C31 (ASTM C511-22, 2022). Following demolding, the specimens were transferred to a lime-saturated water curing tank maintained at conditions prescribed by ASTM C511 (ASTM C511-22, 2022) (23°C ± 2°C) until testing ages 7, 28, and 90 days.
3.3 Evaluating the homogeneity of mixtures
The freshly prepared Engineered Cementitious Composite (ECC) exhibits a highly uniform and homogeneous mixture, with visual inspection confirming excellent consistency and quality throughout the sample. The surface characteristics demonstrate a well-distributed composition, free from segregation or irregularities, indicating a properly optimized mixing process. Moreover, Figures 5a–e depicts SEM photomicrographs of ECC, emphasizing the well-distribution of natural and cement matrix in the ECC mixture.
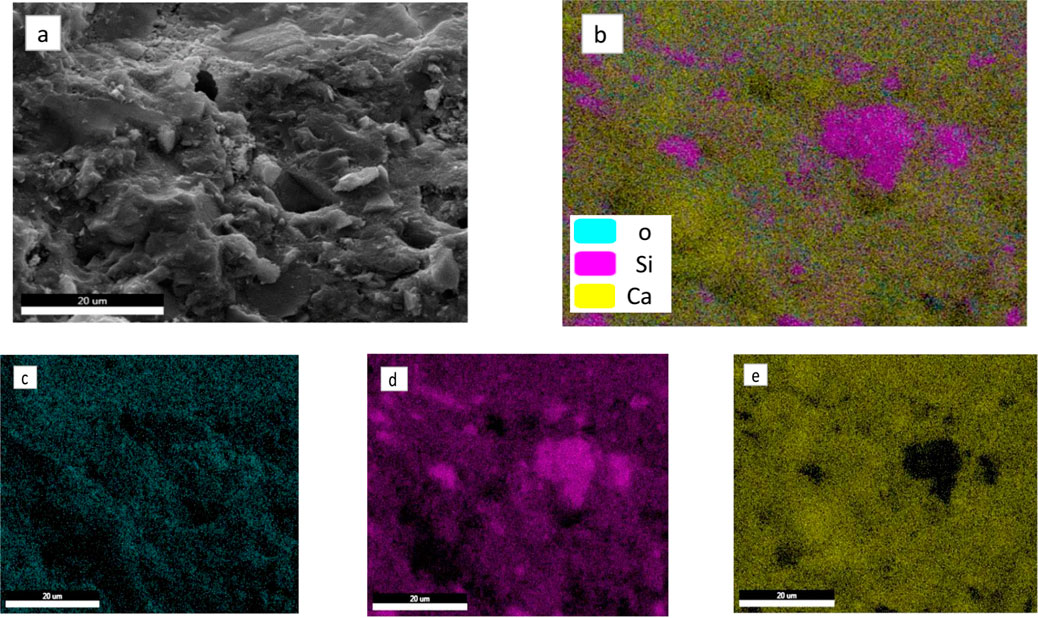
Figure 5. SEM photomicrographs of (a): Mixture, (b): Distribution of oxygen (o), Silica (Si), and Calcium (Ca) (c): Oxygen (O), (d): Silica (Si), (e): Calcium (Ca).
3.4 Test procedure
3.4.1 Properties of fresh ECC
The properties of the fresh ECC, such as specific weight, unintended air entrainment percentage, and mini-slump flow, were investigated. The research studies carried out these tests to evaluate the workability and density characteristics of the fresh ECC, which are critical for its application in construction projects. The Significance of Mini-Slump Tests in ECC Mixture: The average of two perpendicular diameters has been reported as the mini-slump value of each mix. The test to determine the air content percentage of the engineered cementitious composite will conducted by ASTM C231 (ASTM C231-22, 2022). Additionally, the specific weight measurement of the engineered cementitious composite will performed following ASTM C138 (ASTM C138-22, 2022).
3.4.2 Compressive strength test
Prepared Cubic specimens with 100 × 100 × 100 mm dimensions were for compressive strength testing. For each mixture, three samples were cast and tested at curing ages of 7, 28, and 90 days in compliance with the BS EN 12390-3 standard (BS EN 12390-3, 2019). Determined the compressive strength by applying a constant loading rate of 0.6 ± 0.2 N/mm2/s. An initial preload (approximately 30% of the anticipated failure load) is used to seat the specimen to ensure accurate measurements. Following this, the load was increased continuously and smoothly at the specified rate (±10% tolerance) to prevent any shock or sudden impact until the specimen reached its maximum load-bearing capacity. This method ensured precise and reliable evaluation of the compressive strength of the engineered cementitious composites (ECC).
3.4.3 Flexural performance test
The flexural strength of the engineered cementitious composites (ECC) was evaluated using prismatic beam specimens with dimensions of 150 × 150 × 550 mm by the ASTM C1609M-19a standard (ASTM C1609/C1609M-19a, 2019). The tests were conducted at the age of 28 days under third-point loading conditions to simulate realistic stress distribution. A controlled loading rate of 0.1 mm/min was applied to ensure a gradual and consistent increase in load, minimizing any potential impact or shock. The specimens were continuously loaded until failure, and the maximum applied load was recorded in kilonewtons (kN). Three replicate samples were tested for each mixture, and the average flexural strength was calculated and reported as the representative value.
3.4.4 Tensile (splitting) strength test
The engineered cementitious composites (ECC) tensile splitting strength was evaluated using cylindrical specimens with a diameter of 150 mm and a height of 300 mm by the ASTM C496 standard (ASTM C496/C496M, 2017). The tests were conducted at the age of 28 days to assess the tensile behavior of the material. Three replicate samples were tested for each mixture, and the average tensile splitting strength was calculated and reported as the representative value. This testing protocol ensured accurate and reliable measurement of the tensile properties of the ECC.
3.4.5 Modulus of elasticity
The mixtures’ modulus of elasticity and cylindrical specimens with dimensions of 150 × 300 mm were prepared and tested by ASTM C469 (ASTM C469, 2002). The specimens underwent axial loading, measuring stress and strain within the elastic range. The modulus of elasticity was calculated as the slope of the linear portion of the stress-strain curve. The tests were conducted under controlled temperature and constant relative humidity to ensure high accuracy and repeatability of the results.
3.4.6 Water penetration resistance
The water penetration resistance of ECC was evaluated following the EN 12390-8 standard (EN 12390-8, 2009). Specimens were tested under water pressure to measure their resistance to water ingress. Lower penetration depths indicate enhanced durability, particularly in moisture-exposed environments.
3.4.7 Water absorption
The water absorption of ECC was determined by DIN EN 1338 (DIN EN 1338, 2003). Specimens were dried, immersed in water, and weighed regularly to calculate the percentage of water absorption. Lower water absorption values indicate reduced porosity and enhanced durability, particularly in environments prone to moisture exposure.
3.4.8 Abrasion resistance test (rotating-cutter method)
DIN EN 1338 (DIN EN 1338, 2003) evaluated ECC’s abrasion resistance using the rotating-cutter method. Samples were subjected to a rotating cutter under a specified load, and the wear length was measured after a set of 28 cycles. Lower mass loss values indicate superior abrasion resistance, highlighting the material’s suitability for high-traffic surfaces and industrial applications.
3.4.9 Freeze-thaw resistance with deicing salts
The salt scaling of the ECC mixtures was determined according to EN 1338 (DIN EN 1338, 2003) with a 3% NaCI solution. At the end of freeze-thaw cycles, the mixtures were collected and weighed to determine their mass loss (ML) as a salt-scaling resistance measure.
3.4.10 Chloride ion penetration resistance
The chloride ion penetration resistance of ECC was evaluated by ASTM C1202 (ASTM C1202, 2012). The specimens were exposed to an electrical potential, and the total charge that passed through them was measured. Lower charge values indicate reduced chloride ion permeability, highlighting the material’s durability in marine environments or areas exposed to deicing salts.
3.4.11 Surface resistivity test (SR)
AASHTO T358 (AASHTO T358, 2015) measured the electrical resistivity of ECC using the four-point probe method. This test evaluates the material’s ability to resist the passage of electrical current, directly related to its permeability and durability. Higher resistivity values indicate lower permeability and enhanced durability, particularly in environments where corrosion resistance is critical.
4 Results and discussion
4.1 Fresh ECC properties
The fresh properties of the engineered cementitious composites (ECC), including density, air content, and slump flow, were evaluated to assess the workability and consistency of the mixtures. The density was measured to ensure proper compaction, and the air content was evaluated to assess the void structure in the mixture. The slump flow test was performed to assess the flowability and self-leveling traits of the ECC, which are essential for proper placement and finishing. The results of these tests are summarized in Table 4, providing a comprehensive overview of the fresh state characteristics of the developed ECC.
4.2 Compressive strength
The compressive strength of the engineered cementitious composites (ECC) was evaluated at 7, 28, and 90 days, as summarized in Table 5. Including fibers, which act as crack inhibitors, significantly enhanced the ductility of the failure mode. The fiberless ECC mixture exhibited compressive strengths of 64.2 MPa, 91.2 MPa, and 104 MPa at 7, 28, and 90 days, respectively. The observed strength improvements with silica fume and GGBFS are consistent with Liu’s (Liu et al., 2023) and Chen’s (Sumukh et al., 2024) findings.
The highest 7-day compressive strength is obtained using binary mixtures that include 10 kg/m3 of steel fibers and 1 kg/m3 of PVA fibers, achieving a strength of 88.1 MPa. In addition, ternary mixtures containing 10 kg/m3 of steel fibers, 10 kg/m3 of synthetic fibers, and 2 kg/m3 of PVA fibers also exhibit a strong compressive strength of 87.7 MPa. At 28 days, the binary mixture with 10 kg/m3 steel fibers and 2 kg/m3 PVA fibers, along with the ternary mixture of 10 kg/m3 steel fibers, 10 kg/m3 synthetic fibers, and 2 kg/m3 PVA fibers, demonstrated the highest compressive strengths of 94.8 MPa and 93.8 MPa, respectively. After 90 days, the binary mixture with 20 kg/m3 steel fibers reached 103.9 MPa, while the ternary mix with 10 kg/m3 steel fibers, 10 kg/m3 synthetic fibers, and 2 kg/m3 PVA fibers achieved 103.3 MPa, both outperforming other mixtures. Under increasing load, microcracks initiated and propagated within the matrix, activating the fiber bridging effect. This mechanism prevented large crack formation, leading to multiple microcracks near the prominent cracks.
The compressive strength generally increases with age. For instance, a mixture containing 20 kg/m3 steel fibers and 1 kg/m3 PVA fibers exhibited strengths of 80.6 MPa, 89.5 MPa, and 98.4 MPa at 7, 28, and 90 days, respectively, representing an 11% increase at 28 days and a 22% increase at 90 days. Fiber incorporation enhanced 7-day strength compared to the fiberless mixture. However, at 28 days, only the S10F0P1, S10F0P2, and S10F10P2 mixtures showed improved strength, while others displayed mixed results. By 90 days, most fiber-reinforced mixtures exhibited lower strength than fiberless.
Adding fibers to high-performance engineered cementitious composites (ECC) transforms their failure mode from brittle to ductile. While fiberless specimens (S0F0P0) failed suddenly under maximum loading, fiber-reinforced mixtures demonstrated improved cohesion and ductility due to the fibers’ bridging effect, which controls crack propagation and enhances energy absorption.
At 7 days, the S10F0P1 mixture exhibited a 40% increase in compressive strength (88.1 MPa) compared to the fiberless mix, highlighting the early-age benefits of fiber reinforcement. At 28 days, the S10F0P2 mixture achieved the highest compressive strength of 94.8 MPa, representing a 4% increase over the fiberless mixture. However, mixtures with synthetic fibers, such as S0F10P1 and S0F20P1, showed 8% and 15% reductions, respectively, indicating that synthetic fibers may negatively impact mid-term strength.
At 90 days, the S20F0P2 mixture demonstrated the highest compressive strength of 103.9 MPa, closely matching the fiberless mixture (104 MPa). However, most fiber-reinforced mixtures exhibited lower 90-day compressive strength than fiberless. For example, the S0F20P1 mixture showed a 20% reduction, while the S10F20P2 mixture experienced a 15% decrease.
The evaluation of compressive strength across 7, 28, and 90 days reveals that increasing synthetic fiber content generally reduces compressive strength. However, higher fiber content improves ductility and reduces the brittle nature of ECC, as evidenced by the cohesive failure of fiber-reinforced specimens with ternary fibers.
The 90-day compressive strength of the tested mixtures did not decrease when compared to their compressive strength at 7 and 28 days. All mixtures demonstrated increased compressive strength as the sample age progressed from 7 to 28 days–90 days.
A notable observation from the 90-day compressive strength of the mixtures studied is that adding various amounts and types of fibers decreases compressive strength compared to the mixture without fibers. This downward trend is evident when incorporating fibers into the ECC, regardless of their type or amount. The results obtained show that the compressive strength of the studied mixtures with binary and ternary fibers at the age of 90 days decreases between 2 and 20 percent compared to the mixture without fibers.
4.3 Flexural performance
Flexural beam specimens were ready and tested to evaluate their performance and energy absorption. The 28-day flexural test results are in Table 6. Fiber incorporation reduced the force needed to initiate the first crack, while the fiberless ECC mixture showed a flexural strength of 94.9 kN. These results represent an improvement over previous studies, such as Liu (Liu et al., 2023).
The highest flexural strength realized with mixtures that include 20 kg/m3 of synthetic fibers and 1 kg/m3 of PVA fibers in binary fiber combinations, as well as with 20 kg/m3 of steel fibers, 10 kg/m3 of synthetic fibers, and 2 kg/m3 of PVA fibers in ternary fiber combinations. The experimental findings highlight that using three fiber types significantly enhances flexural strength, ductility, and energy absorption while mitigating brittle behavior. The S0F20P1 design demonstrated the highest flexural strength among binary fiber mixtures, while the S20F10P2 mixture outperformed other ternary fiber mixtures.
The hybridization of fibers has a remarkable influence on the flexural behavior of engineered cementitious composites (ECC). As a baseline, the fiberless mixture (S0F0P0) achieved an impressive flexural strength of 94.9 kN. In binary fiber mixtures, polyvinyl alcohol (PVA) fibers emerged as game-changers, significantly enhancing flexural performance. A striking example is the S10F0P2 mixture, which incorporated an additional 1 kg/m3 of PVA fibers compared to the S10F0P1 mixture. This enhancement resulted in a notable increase in flexural strength, with only a minor reduction relative to the fiberless mixture. Such findings underscore the pivotal role of PVA fibers in elevating flexural properties. Figure 6 compares the load-deflection curves for the flexural beams studied, vividly illustrating their performance and mechanical behavior under bending conditions.
Combining steel, synthetic, and PVA fibers in ternary fiber mixtures enhanced flexural strength. The S20F10P2 mixture exhibited the most significant increase in flexural strength among ternary mixtures, with a 9.5% increase compared to the S10F10P1 mixture and a 5% increase compared to the S20F10P1 mixture. These results highlight the synergistic effect of hybrid fiber systems, particularly the role of PVA fibers in enhancing flexural performance.
The specimens’ failure modes provided further insights into the influence of fiber hybridization. The fiberless sample fractured abruptly after cracking, exhibiting a typical brittle failure pattern. In contrast, fiber-reinforced samples demonstrated improved ductility and crack resistance, as illustrated in Figures 7, 8. These images depict the post-failure conditions of binary and ternary fiber mixtures, respectively, showcasing fiber-reinforced specimens’ cohesive failure and multiple microcracking behaviors. The S0F10P1 mixture showed the lowest resistance to first cracking, while the S20F0P2 mixture demonstrated the highest resistance.
Flexural toughness, defined as the area under the load-displacement curve according to ASTM C1609 (ASTM C1609/C1609M-19a, 2019) and the results presented in Table 6, is a crucial parameter for evaluating the energy absorption capacity of engineered cementitious composites (ECC). The fiberless mixture (S0F0P0) showed no energy absorption after cracking, failing suddenly upon reaching its maximum flexural strength (f600 = 19,078 N) and demonstrating no residual load at L/150 deformation (f150 = 0 N). In contrast, the fiber-reinforced mixtures exhibited significant energy absorption capacity, highlighting the effectiveness of fibers in enhancing toughness and post-cracking behavior. Flexural toughness increased with higher PVA fiber content in the binary fiber mixtures. For example, the S10F0P2 mixture exhibited a 12.6% increase in toughness (T150 = 87.27 N.mm) compared to the S10F0P1 mixture (T150 = 77.52 N.mm), while the S20F0P2 and S0F10P2 mixtures showed increases of 15.2% (T150 = 108.30 N.mm) and 21.7% (T150 = 102.11 N.mm), respectively.
Among ternary fiber mixtures, the S20F10P2 mixture demonstrated the highest flexural toughness (T150 = 120.00 N.mm) and residual load at L/150 deformation (f150 = 65,986 N), representing a 20% increase in toughness compared to the fiberless mixture. The S20F10P1 and S10F20P1 mixtures also showed significant improvements, with toughness values of 114.47 N.mm and 114.59 N.mm, respectively. However, the S10F0P1 mixture experienced a 23% decline in toughness (T150 = 77.52 N.mm), indicating that certain fiber combinations may reduce energy absorption capacity.
The S0F20P1 mixture exhibited the most significant improvement in toughness, with a T150 value of 124.85 N.mm, representing a 24% increase after fiber addition.
To elaborate on the gained flexural performance, Figure 9 illustrates the flexural strength-deflection curves for various specimens. Linear and non-linear regression analyses were employed to establish the relationships characterizing these curves. The curves reveal three distinct regions, labeled R1, R2, and R3. The first region (R1) exhibits a non-linear increase, followed by the second region (R2), which demonstrates a linear decrease. The third region (R3) is also nonlinear, showcasing behavior associated with strain capacity development.
A detailed analysis of the regression coefficients in Equation 1 reveals distinct physical mechanisms governing the flexural behavior. In the initial phase (R1), coefficients a1 and b1 quantify matrix stiffness and fiber bridging effects, respectively. Higher b1 values (e.g., 2.5934 in the reference mix) indicate superior crack-control efficiency during elastic deformation. The linear phase (R2) is distinguished by its defining slope, captivating in its clarity and precision., where negative values (e.g., −11,406 in Mix B5) signify snap-back instability due to fiber pull-out, while positive values (e.g., 2,903.8 in Mix B7) reflect stable post-cracking behavior. The nonlinear phase (R3) captures ductility mechanisms through a2 and b2: pronounced negative a2 (e.g., −9.379 in Mix S20F10P2) indicates rapid energy dissipation from fiber rupture, whereas positive b2 (e.g., 1.6144 in Mix T6) suggests strain-hardening via fiber realignment. These findings align with established micromechanical theories (Chompoorat et al., 2023).
The mechanical behavior of the 14 ECC mixtures and one control mixture (without fibers) was analyzed based on their flexural stress-strain curves. Piecewise regression was employed to develop mathematical models for each of the three phases R1, R2, and R3, as described via Equation 1 and the corresponding coefficients were estimated via least square fiitong processes. The values of the coefficients obtained from Equation 1 are presented in Table 7. The quality of the fitting was evaluated using the coefficient of determination (R2). The reference mixture (S0F0P0) served as a baseline for comparing the behavior of other mixtures (B1 to T6). The results indicate that variations in the composition and structure of the composites significantly influence their flexural behavior. Mixture R exhibited a stable and predictable linear behavior with coefficients a1 = 1.1785, b1 = 2.5934, and c1 = −0.0594. The coefficient of determination (R2 = 0.9993) demonstrates the high accuracy of the model and its strong agreement with the experimental data.
Similar to mixture R, mixtures such as B1 and B2 displayed similar flexural behavior, suggesting that their compositions impart comparable mechanical properties. In contrast, mixtures such as B3 and B5, with different a1 and b1 coefficients, exhibited more nonlinear and flexible behavior. Specifically, the B3 mixture, with coefficients a1 = 1.4638 and b1 = 0.7064, demonstrated reduced stiffness and increased flexibility compared to the reference mixture.
where σ is the flexural strength, δ is the deflection and a1, b1, c1, m, c, a2, b2 and c2 are the coefficients.
Some mixtures, such as S0F20P1, S10F10P1, and S20F10P2, featured additional coefficients (a2, b2, and c2), indicating more complex and nonlinear behavior in their flexural curves. For instance, mixture S20F10P2, with coefficients a2 = −9.379, b2 = 51.437, and c2 = −61.031, exhibited significant changes in the slope of its flexural curve. This behavior may be attributed to material heterogeneity or internal structural variations within the composite, warranting further investigation in future studies. The coefficient of determination (R2) for most mixtures was notably close to 1, indicating a strong convergence between the model and the experimental data. However, mixtures S10F10P1 (R2 = 0.6814) and S10F10P2 (R2 = 0.5234) were exceptions, showing greater deviation from the proposed model. This deviation could result from experimental factors, material heterogeneity, or highly nonlinear behavior.
In analyzing the different regions of the flexural curves, the initial linear region represents the elastic behavior of the composites, where the materials exhibit stable and predictable responses. In the nonlinear region, changes in the slope of the curve reflect alterations in flexural behavior beyond the yield point. For example, in mixture, S0F10P2, the nonlinear portion of the curve, with coefficients c1 = 0.005 and c2 = −21.731, indicates gradual changes in flexural behavior. In contrast, mixture S20F10P2, with abrupt changes in the curve’s slope, exhibits more complex behavior that requires detailed analysis.
The combination of steel, synthetic, and PVA fibers in ternary fiber mixtures further enhanced flexural strength. The S20F10P2 mixture exhibited the most significant increase in flexural strength among ternary mixtures, with a 9.5% increase compared to the S10F10P1 mixture and a 5% increase compared to the S20F10P1 mixture. The S0F10P1 mixture showed the lowest resistance to first cracking, while the S20F0P2 mixture demonstrated the highest resistance.
4.4 Splitting tensile test results
The splitting tensile strength of engineered cementitious composites (ECC) was evaluated across various mixtures, as detailed in Table 8. The fiberless mixture (S0F0P0) showed a tensile strength of 6.86 MPa, serving as the baseline for comparison. Among the binary fiber mixtures, the S20F0P2 mixture exhibited the highest tensile strength at 7.93 MPa, while the S10F0P2 mixture achieved 7.32 MPa. In contrast, the S0F20P1 mixture displayed the lowest tensile strength of 5.24 MPa, indicating that excessive synthetic fiber content without steel fibers may diminish tensile performance.
The ternary fiber mixtures exhibited superior tensile strength, with the S10F20P2 mixture achieving the highest value of 8.99 MPa, closely followed by the S20F10P1 mixture (8.93 MPa) and the S10F20P1 mixture (8.87 MPa). These results underscore the effectiveness of hybrid fiber systems in enhancing the tensile performance of ECC. Combining steel, synthetic, and PVA fibers improved tensile strength and contributed to better crack resistance and ductility, making these mixtures suitable for structural applications that demand high durability.
The results of this study highlight the significant influence of fiber hybridization on the splitting tensile strength of high-performance ECC. The S10F20P2 mixture design, which incorporates a mix of steel, synthetic, and PVA fibers, achieved the highest tensile strength of 8.99 MPa. This represents a 31% increase compared to the sample without fibers, underscoring the effectiveness of hybrid fiber systems in enhancing the mechanical properties of ECC.
Among the samples with two types of fibers, the S20F0P2 mixture design exhibited the most notable improvement, showing a 15.6% increase in splitting tensile strength compared to the sample without fibers. However, the most significant enhancements were seen in samples with three types of fibers, where the tensile strength rose by 12%–31%. This suggests that combining steel, synthetic, and PVA fibers is more effective in improving tensile performance than using only two types of fibers.
4.5 Modulus of elasticity
The modulus of elasticity of the engineered cementitious composites (ECC) was evaluated across various mixtures, as detailed in Table 8. The fiberless mixture (S0F0P0) exhibited a modulus of elasticity of 44.2 GPa, serving as a baseline for comparison. Among the binary fiber mixtures, the S20F0P2 mixture demonstrated the highest modulus of elasticity of 56.4 GPa, while the S10F0P2 mixture achieved 48.1 GPa. In contrast, the S10F10P2 mixture showed the lowest modulus of elasticity of 41.27 GPa, suggesting that certain fiber combinations may reduce stiffness.
Ternary fiber mixtures exhibited superior performance, with the S10F20P1 mixture achieving the highest modulus of elasticity of 65.9 GPa, followed by the S20F10P2 mixture (58.05 GPa) and the S20F10P1 mixture (57.7 GPa). These results underscore the significant impact of hybrid fiber systems on enhancing ECC’s stiffness and structural integrity.
As summarized in Table 8, the results indicate that the modulus of elasticity ranged from 41.27 GPa to 65.9 GPa across different mixtures. The highest modulus of elasticity was observed in the S10F20P1 mixture (65.9 GPa), which contains 10 kg/m3 of steel fiber, 20 kg/m3 of synthetic fiber, and 1 kg/m3 of PVA fiber. This highlights the effectiveness of hybrid fiber systems in enhancing the stiffness of ECC. In contrast, the lowest modulus of elasticity in the S10F10P2 mixture (41.27 GPa) includes 10 kg/m3 of steel fiber, 10 kg/m3 of synthetic fiber, and 2 kg/m3 of PVA fiber.
The S20F0P2 mixture, containing 20 kg/m3 of steel fiber and 2 kg/m3 of PVA fiber, exhibited a high modulus of elasticity (56.4 GPa), emphasizing the role of steel fibers in enhancing stiffness. Likewise, the S20F10P1 mixture (57.7 GPa) and the S20F10P2 mixture (58.05 GPa) showed superior performance, further confirming the beneficial effect of steel fibers. In contrast, mixtures without steel fibers, such as S0F10P1 (54 GPa) and S0F20P1 (48.14 GPa), demonstrated lower stiffness, indicating that the absence of steel fibers may restrict the material’s capacity to resist deformation.
The modulus of elasticity tests provided critical insights into how fiber hybridization affects the stiffness of high-performance engineered cementitious composites (ECC). The results in Table 8 show a broad range of modulus values, from 41.27 GPa to 65.9 GPa, depending on the fiber composition. The S10F20P1 mixture, which includes 10 kg/m3 of steel fiber, 20 kg/m3 of synthetic fiber, and 1 kg/m3 of PVA fiber, achieved the highest modulus of elasticity at 65.9 GPa.
In contrast, the S10F10P2 mixture displayed the lowest modulus of elasticity at 41.27 GPa, likely due to an imbalance in fiber proportions that compromised the structural integrity of the matrix. Notably, mixtures with higher steel fiber content, such as S20F0P2 (56.4 GPa) and S20F10P2 (58.05 GPa), consistently demonstrated superior stiffness, further highlighting the crucial role of steel fibers in enhancing the elastic properties of ECC. Interestingly, mixtures without steel fibers, like S0F10P1 (54 GPa) and S0F20P1 (48.14 GPa), showed moderate performance.
4.6 Water penetration resistance
The water penetration resistance of the engineered cementitious composites (ECC) was evaluated by the EN 12390-8 standard (EN 12390-8, 2009). The results in Table 9 demonstrate the influence of fiber hybridization and supplementary cementitious materials (SCMs) on the material’s ability to resist water ingress. The fiberless mixture (S0F0P0) exhibited a water penetration depth of 4.5 mm, serving as the baseline for comparison.
Among the binary fiber mixtures, the S10F0P2 mixture demonstrated the lowest water penetration depth of 3.5 mm, indicating superior resistance to water ingress. In contrast, the S20F0P2 mixture showed a higher penetration depth of 5 mm, suggesting that increased steel fiber content may slightly reduce water resistance. The ternary fiber mixtures exhibited varying performance, with the S10F20P1 mixture achieving a penetration depth of 6 mm, while the S20F10P1 and S10F20P2 mixtures showed higher penetration depths of 10 mm and 7 mm, respectively.
High-performance ECC’s water penetration resistance is crucial for its durability.The S10F0P2 mixture, with 10 kg/m3 of steel fiber and 2 kg/m3 of PVA fiber, achieved the lowest water penetration depth of 3.5 mm, demonstrating excellent water resistance.
4.7 Water absorption
The water absorption of engineered cementitious composites (ECC) was assessed following DIN EN 1338:2003 (DIN EN 1338, 2003), as shown in Table 9. The baseline fiberless mixture (S0F0P0) displayed water absorption rates of 0.5% at 30 min and 1.3% at 24 h. In comparison, the S0F20P1 mixture had lower absorption rates of 0.4% at 30 min and 1.0% at 24 h, indicating better water resistance. Ternary mixtures like S10F20P2 recorded 0.4% at 30 min and 1.4% at 24 h, demonstrating the benefits of hybrid fiber systems in reducing porosity and enhancing durability.
The water absorption tests offered important insights into the porosity and durability of high-performance engineered cementitious composites (ECC). Table 9 shows that 30-min water absorption ranged from 0.3% to 0.6%, while 24-h absorption varied between 1.0% and 1.8%.
The S0F20P1 mixture, containing 20 kg/m3 of synthetic fiber and 1 kg/m3 of PVA fiber, had the lowest 24-h absorption at 1.0%, indicating excellent water resistance. In contrast, the S0F10P1 mixture exhibited the highest absorption at 1.8%, likely due to an imbalance in fiber proportions. The S10F0P2 mixture showed 24-h absorption of 1.7%, suggesting that using only steel and PVA fibers may not ensure optimal water resistance. Conversely, the S0F20P2 mixture, with 20 kg/m3 of synthetic fiber and 2 kg/m3 of PVA fiber, achieved a low 24-h absorption of 1.2%, underscoring the effectiveness of synthetic fibers in minimizing water absorption.
4.8 Abrasion resistance
The abrasion resistance of engineered cementitious composites (ECC) was assessed using DIN EN 1338:2003 (DIN EN 1338, 2003). The results in Table 10 reveal how fiber hybridization affects wear resistance. The fiberless mixture (R) exhibited a baseline abrasion width of 15 mm. Figure 10 shows the specimens’ condition after testing, highlighting wear patterns and surface degradation.

Figure 10. Surface of specimens after abrasion resistance test (a) S20F0P1, (b) S10F10P2, (c) S10F20P2.
According to DIN EN 1338:2003 (DIN EN 1338, 2003), most tested mixtures (R, B1–B8, T2–T6) have groove lengths of 17 mm or less, achieving Grade 4 for excellent abrasion resistance. The T1 mixture, with a groove length of 19 mm, is rated Grade 3 for good abrasion resistance. Figure 11 shows that adding fibers improves abrasion resistance compared to the fiberless reference mixture. These results indicate that the mixtures are suitable for heavy-duty applications, like industrial floors or abrasive environments.
Among the binary fiber mixtures, B2 and B3 demonstrated an abrasion width of 15 mm, indicating superior abrasion resistance. In contrast, mixtures B1 and B7 showed slightly higher abrasion widths of 17 mm. Mixtures B5 and B6 exhibited an abrasion width of 16 mm, suggesting moderate resistance to wear. The ternary fiber mixtures exhibited varying performance. Mixtures T4, T2, and T3 achieved an abrasion width of 17 mm, while mixtures T5 and T6 showed an abrasion width of 16 mm.
Overall, the results highlight the significant role of fiber hybridization in enhancing the abrasion resistance of ECC. Mixtures such as B2 and B3 demonstrated the best performance, while others showed moderate to slightly higher wear resistance. As shown in Table 10, the results reveal that the abrasion width varied between 15 mm and 19 mm across different mixtures. Mixture T1, which includes 10 kg/m3 of steel fiber, 10 kg/m3 of synthetic fiber, and 1 kg/m3 of PVA fiber, was previously reported to have the highest abrasion width at 19 mm. However, this value has been 17 mm in the revised data.
4.9 Freeze-thaw resistance with deicing salts
The freeze-thaw resistance of engineered cementitious composites (ECC) in the presence of deicing salts was evaluated according to DIN EN 1338:2003 (DIN EN 1338, 2003). A total of 28 freeze-thaw cycles were conducted, measuring mass loss per unit area (g/m2) to assess durability. Results are shown in Table 10 and Figure 12 illustrates several samples after testing.
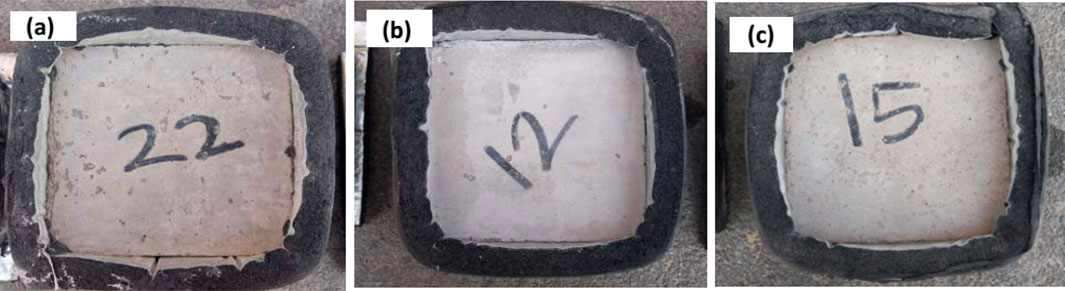
Figure 12. Specimen Appearance after freeze-thaw resistance with deicing salts test (a) T5, (b) B4, (c) T2.
The fiberless mixture (R) recorded a mass loss of 4.4 gr/m2, serving as the baseline for comparisons. Binary mixtures B1 and B2 showed a mass loss of 8.9 gr/m2, while B3 and B4 matched the fiberless mixture at 4.4 gr/m2. In contrast, mixtures B5, B6, and B8 had a higher mass loss of 17.8 gr/m2, and mixture B7 demonstrated a slightly lower loss of 13.3 gr/m2. Among the ternary mixtures, T1, T4, T5, and T6 exhibited a mass loss of 17.8 gr/m2, while T2 had the highest at 22.2 gr/m2, and T3 showed a mass loss of 13.3 gr/m2.
Freeze-thaw resistance tests with deicing salts highlighted the durability of high-performance engineered cementitious composites (ECC). Results in Table 10 indicate weight loss during freeze-thaw cycles ranged from 4.4 gr/m2 to 22.2 g/m2, with mixture R showing the lowest loss at 4.4 g/m2, indicating superior freeze-thaw resistance.
Mixture T6, containing 10 kg/m3 of steel fiber, 20 kg/m3 of synthetic fiber, and 2 kg/m3 of PVA fiber, had the highest weight loss at 17.8 gr/m2, indicating poor resistance to freeze-thaw cycles. This increased weight loss may be due to microstructural weaknesses introduced by the fibers, despite improvements in tensile strength and ductility.
Both mixtures B5 and B6 also showed a weight loss of 17.8 gr/m2, highlighting difficulties in achieving freeze-thaw resistance in fiber-reinforced composites. Conversely, mixtures B7, B8, T4, and T5 displayed effective freeze-thaw resistance, each with a low weight loss of 4.4 gr/m2, comparable to the control sample.
4.10 Rapid Chloride Permeability Test (RCPT)
The resistance of engineered cementitious composites (ECC) to chloride ion penetration was assessed using the Rapid Chloride Permeability Test (RCPT) per ASTM C1202 (ASTM C1202, 2012), with results shown in Table 10.
The fiberless mixture (R) recorded a charge of 87 coulombs, providing a reference for comparison. Based on ASTM C1202 (ASTM C1202, 2012) permeability classification, the results fall within the Very Low (100–1000 coulombs) and Negligible (<100 coulombs) ranges. As seen in Figure 13, ECC shows significantly higher resistance to chloride ion penetration than the fiberless mixture, confirming its enhanced durability in chloride-rich environments.
Among the binary fiber mixtures, the B1 mixture had the highest charge of 176 coulombs, indicating reduced resistance to chloride ion penetration. The B2, B3, and B4 mixtures had charges of 174, 169, and 173 coulombs, respectively. B5 and B6 showed charges of 165 and 180 coulombs, while B7 had a charge of 178 coulombs, suggesting better resistance.
For the ternary mixtures, T1 had a charge of 187 coulombs, T2 and T3 displayed charges of 188 and 182 coulombs, respectively. T4 had the lowest charge at 179 coulombs, while T5 and T6 showed 183 and 180 coulombs, respectively.
The Rapid Chloride Permeability Test (RCPT) provides insights into the resistance of engineered cementitious composites (ECC) to chloride ion penetration, a key factor in durability, especially in environments with deicing salts or marine exposure.
Results in Table 10 show that total charge passed, measured in coulombs, ranged from 87 to 188. According to ASTM C1202 (ASTM C1202, 2012), lower charge values indicate higher resistance: below 1000 coulombs signifies low permeability, while above 2,000 signifies high permeability.
The B1 mixture had the lowest charge at 176 coulombs, showing excellent resistance due to a dense microstructure formed by hybrid fibers that reduce porosity. The B2 mixture (174 coulombs) and R control mixture (87 coulombs) also demonstrated low permeability, underscoring the importance of a well-designed matrix for durability.
4.11 Surface resistivity test (SR)
The surface resistivity of the engineered cementitious composites (ECC) was measured using the four-point probe method in accordance with AASHTO T358 (AASHTO T358, 2015). The test results, presented in Table 10, show that the surface resistivity of the concrete ranges from 79 to 94 kΩ·cm. Figure 14 illustrates that mixtures containing fibers exhibit resistivity values of 79–94 kΩ·cm, which falls within the low corrosion rate range of 20–100 kΩ·cm. This confirms that fiber-reinforced ECC maintains its durability without increasing the risk of corrosion.
The fiberless mixture (R) had a surface resistivity of 80 kΩ·cm, serving as a reference. Among binary mixtures, B8 had the highest resistivity at 93 kΩ·cm, while B6 was lower at 79 kΩ·cm. Mixtures B5 and B7 exhibited resistivities of 84 and 82 kΩ·cm, respectively.
In ternary mixtures, T2 and T6 achieved the highest resistivity of 94 kΩ·cm, followed by T3 at 91 kΩ·cm. Mixtures T1 and T5 recorded resistivities of 92 kΩ·cm, and T4 was at 89 kΩ·cm.
According to AASHTO T 358 (AASHTO T358, 2015), higher surface resistivity values indicate lower permeability and better resistance to chloride ion ingress. This study found that all mixtures had surface resistivity values between 80 kΩ.cm and 94 kΩ.cm, indicating strong resistance to chloride ion penetration. Mixture T2, containing 20 kg/m3 of steel fiber, 10 kg/m3 of synthetic fiber, and 1 kg/m3 of PVA fiber, had the highest resistivity at 94 kΩ.cm. Similarly, mixtures T3 (91 kΩ.cm) and T1 (92 kΩ.cm) also showed high resistivity.
5 Sustainability investigation
Cement production and use are significant contributors to carbon dioxide (CO2) emissions in the construction industry. Approximately 900 kg of CO2 is released for every ton of cement produced. To address this environmental issue, this study incorporated 350 kg/m3 of ground granulated blast furnace slag (GGBFS) and 50 kg/m3 of silica fume as partial replacements for cement in high-performance engineered cementitious composites (ECC). These supplementary cementitious materials (SCMs) not only improve the mechanical properties of ECC but also considerably reduce its environmental impact.
GGBFS, a by-product of steel production, emits 58.7 kg of CO2 per ton when used as a cement substitute, compared to 780 kg of CO2 per ton if it is not repurposed. Similarly, silica fume, another industrial by-product, only emits 24 kg of CO2 per ton during production, making it a highly sustainable alternative to traditional cement.
The substitution of cement with GGBFS and silica fume resulted in a substantial decrease in CO2 emissions. As detailed in Table 11, incorporating 350 kg/m3 of GGBFS and 50 kg/m3 of silica fume reduced CO2 emissions by 338.2 kg per cubic meter of ECC. This reduction underscores the environmental advantages of using industrial by-products as cement replacements. However, the inclusion of steel fibers introduces additional ecological considerations. Overall, the environmental impact of Engineered Cementitious Composites (ECC) remains significantly lower than that of conventional concrete, primarily due to the substantial reduction in cement usage.
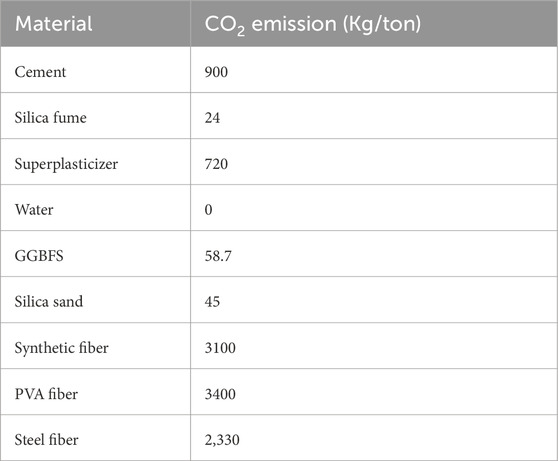
Table 11. The amount of emitted CO2 for the material (Bremner et al., 2001; Zhu et al., 2021; Lee and Park, 2005; Waqar et al., 2024).
6 Conclusion
This study assesses the mechanical and durability properties of high-performance engineered cementitious composites (ECC) reinforced with hybrid fibers. The findings are as follows:
- The S20F10P2 ternary fiber mixture showed the highest flexural strength, with a 9.5% increase over S10F10P1 and a 5% increase over S20F10P1. The failure modes of the specimens indicated enhanced ductility and multiple microcracking.
- The S20F10P2 mixture achieved the highest flexural toughness at 120.00 N.mm, with a residual load at L/150 deformation (f150 = 65,986 N), showing a 20% improvement over the control. The S0F20P1 mixture had an even greater toughness of 124.85 N.mm, highlighting the benefits of hybrid fiber systems in enhancing energy dissipation and crack resistance.
- The S10F20P2 mixture achieved the highest tensile strength at 8.99 MPa, a 31% increase over the control. Conversely, the S0F20P1 mixture had the lowest tensile strength at 5.24 MPa. This improvement is due to the combined effects of hybrid fibers—steel fibers enhance tensile capacity, while synthetic/PVA fibers aid in crack control and stress distribution.
- Water penetration tests revealed that the S10F0P2 mixture had the lowest penetration depth of 3.5 mm, indicating superior impermeability, while the S0F20P2 mixture had the highest at 10 mm.
- Water absorption tests showed that the S0F20P1 mixture had the lowest 24-h absorption at 1.0%, while the S0F10P1 mixture exhibited the highest absorption at 1.8%.
- The implications of the abrasion resistance tests are significant, as they reveal that the S0F0P0, S10F0P2, and S20F0P1 mixtures exhibit the lowest abrasion width at 15 mm, indicating superior wear resistance.
- The S0F0P0 mixture had the lowest weight loss at 4.4 g/m2, while the S10F20P2 mixture exhibited the highest weight loss at 17.78 g/m2. These findings highlight the difficulties, particularly in the presence of deicing salts, which can exacerbate scaling and surface deterioration.
- The RCPT results revealed that the S0F0P0 mixture had the lowest charge passed (87 coulombs), indicating better resistance to chloride ion penetration. In contrast, the S20F10P1 mixture had the highest charge passed (188 coulombs), suggesting that increased steel fiber content may lead to greater chloride permeability due to interconnected microcracks.
- Surface resistivity tests showed that the S20F10P1 mixture had the highest resistivity at 92 kΩ.cm, indicating excellent resistance to chloride ion penetration. The S0F0P0 mixture exhibited the lowest resistivity at 80 kΩ.cm.
- Using 350 kg/m3 GGBFS and 50 kg/m3 silica fume as cement replacements in ECC reduced CO2 emissions by 338.2 kg/m3, highlighting the environmental benefits of industrial by-products in sustainable construction.
Data availability statement
The raw data supporting the conclusions of this article will be made available by the authors, without undue reservation.
Author contributions
MK: Conceptualization, Funding acquisition, Investigation, Methodology, Resources, Validation, Visualization, Writing – original draft, Writing – review and editing. JS: Conceptualization, Investigation, Methodology, Project administration, Supervision, Writing – original draft, Writing – review and editing. SM: Conceptualization, Methodology, Supervision, Writing – review and editing. EZ: Conceptualization, Methodology, Supervision, Writing – review and editing. MB: Investigation, Methodology, Supervision, Writing – review and editing.
Funding
The author(s) declare that financial support was received for the research and/or publication of this article. The authors gratefully acknowledge the financial and laboratory support from the Road, Housing and Urban Development Research Center (BHRC) of Iran.
Conflict of interest
The authors declare that the research was conducted in the absence of any commercial or financial relationships that could be construed as a potential conflict of interest.
Generative AI statement
The author(s) declare that no Generative AI was used in the creation of this manuscript.
Publisher’s note
All claims expressed in this article are solely those of the authors and do not necessarily represent those of their affiliated organizations, or those of the publisher, the editors and the reviewers. Any product that may be evaluated in this article, or claim that may be made by its manufacturer, is not guaranteed or endorsed by the publisher.
References
AASHTO T358 (2015). Standard method of test for surface resistivity indication of concrete’s ability to resist chloride ion penetration. American Association of State Highway and Transportation Officials.
Ahmad, F., Rawat, S., Yang, R., Zhang, L., Fanna, D. J., Soe, K., et al. (2025). Effect of metakaolin and ground granulated blast furnace slag on the performance of hybrid fibre-reinforced magnesium oxychloride cement-based composites. Int. J. Civ. Eng. 23, 853–868. doi:10.1007/s40999-025-01074-4
Asghar, M. F., and Khattak, M. J. (2024). Evaluation of mixture design and tensile characteristics of polyvinyl alcohol (PVA)–fiber reinforced HMA mixtures. Int. J. Pavement Res. Technol. 17, 258–279. doi:10.1007/s42947-022-00233-3
ASTM C1202 (2012). Standard test method for electrical indication of concrete’s ability to resist chloride ion penetration. West Conshohocken, PA, USA: ASTM International.
ASTM C138-22 (2022). Standard test method for density (unit weight), yield, and air content (gravimetric) of concrete. West Conshohocken, PA: ASTM International.
ASTM C1609/C1609M-19a (2019). Standard test method for flexural performance of fiber-reinforced concrete (using beam with third-point loading). West Conshohocken, PA: ASTM International.
ASTM C231-22 (2022). Standard test method for air content of freshly mixed concrete by the pressure method. West Conshohocken, PA: ASTM International.
ASTM C31-22 (2022). Standard practice for making and curing concrete test specimens in the field. West Conshohocken, PA: ASTM International.
ASTM C469 (2002). Standard test method for static modulus of elasticity and Poisson's ratio of concrete in compression. West Conshohocken, PA, USA: ASTM International.
ASTM C496/C496M (2017). Standard test method for splitting tensile strength of cylindrical concrete specimens. West Conshohocken, PA: ASTM International.
ASTM C511-22 (2022). Standard Specification for mixing rooms, moist cabinets, moist rooms, and water storage tanks used in the testing of Hydraulic cements and concretes. West Conshohocken, PA: ASTM International.
T. W. Bremner, K. C. Hover, R. W. Poston, J. P. Broomfield, T. Joseph, R. Price, and et al. (2001). Protection of metals in concrete against corrosion ACI 222 R-01. Reported by ACI Committee 222.
BS EN 12390-3 (2019). “Standard test method for compressive strength of cement mortar,” in Standard specification for fiber-reinforced concrete. West Conshohocken, PA: ASTM International. ASTM C1116/C1116M-10a.
Buathong, P., Chompoorat, T., Jongpradist, P., Chen, X., and Jamsawang, P. (2023). Effect of palm fiber reinforcement on the unconfined compressive performance of cement-treated sand. Sustainability 15 (11), 8607. doi:10.3390/su15118607
Chen, B., and Liu, J. (2005). Contribution of hybrid fibers on the properties of the high-strength lightweight concrete having good workability. Cem. Concr. Res. 35 (5), 913–917. doi:10.1016/j.cemconres.2004.07.035
Cheng, Y., and Huang, X. (2022). Application of municipal solid waste incineration bottom ash into engineered cementitious composites. Int. J. Pavement Res. Technol. 15, 1106–1117. doi:10.1007/s42947-021-00075-5
Choi, H. K., Bae, B. I., and Choi, C. S. (2016). Lateral resistance of unreinforced masonry walls strengthened with engineered cementitious composite. Int. J. Civ. Eng. 14, 411–424. doi:10.1007/s40999-016-0026-1
Chompoorat, T., Likitlersuang, S., Buathong, P., Jongpradist, P., and Jamsawang, P. (2023). Flexural performance and microstructural characterization of cement-treated sand reinforced with palm fiber. J. Mater. Res. Technol. 25, 1570–1584. doi:10.1016/j.jmrt.2023.06.036
Chompoorat, T., Thepumong, T., Nuaklong, P., Jongvivatsakul, P., and Likitlersuang, S. (2021). Alkali-activated controlled low-strength material utilizing high-calcium fly ash and steel slag for use as pavement materials. J. Mater. Civ. Eng. 33 (8), 04021178. doi:10.1061/(ASCE)MT.1943-5533.0003798
Choucha, S., Benyahia, A., Ghrici, M., and Mansour, M. S. (2018). Effect of natural pozzolan content on the properties of engineered cementitious composites as repair material. Front. Struct. Civ. Eng. 12 (3), 261–269. doi:10.1007/s11709-017-0394-x
DIN EN 1338 (2003). Concrete paving blocks - requirements and test methods. Berlin, Germany: Deutsches Institut für Normung.
EN 12390-8 (2009). Testing hardened concrete - Part 8: depth of penetration of water under pressure. Brussels, Belgium: European Committee for Standardization.
Gillani, S. A. A., Toumi, A., and Turatsinze, A. (2020). Effect of surface preparation of substrate on bond tensile strength of thin bonded cement-based overlays. Int. J. Pavement Res. Technol. 13, 197–204. doi:10.1007/s42947-019-0101-5
Hasani, M., Moghadas Nejad, F., Sobhani, J., and Chini, M. (2021). Mechanical and durability properties of fiber reinforced concrete overlay: experimental results and numerical simulation. Constr. Build. Mater. 268, 121083. doi:10.1016/j.conbuildmat.2020.121083
Kafodya, I., and Okonta, F. (2020). Compressive and tensile strength properties of pre-compressed and soaked natural fiber reinforced lime—fly ash stabilised soil. Int. J. Pavement Res. Technol. 13, 497–509. doi:10.1007/s42947-020-0074-4
Kanda, T., and Li, V. C. (1998). Interface property and apparent strength of high-strength hydrophilic fiber in cement matrix. J. Mater. Civ. Eng. 10 (1), 5–13. doi:10.1061/(ASCE)0899-1561(1998)10:1(5)
Kang, S. T., Choi, J. I., Koh, K. T., Lee, K. S., and Lee, B. Y. (2016). Hybrid effects of steel fiber and microfiber on the tensile behavior of ultra-high performance concrete. Compos. Struct. 145, 37–42. doi:10.1016/j.compstruct.2016.02.075
Kim, J. K., Kim, J. S., Ha, G. J., and Kim, Y. Y. (2007). Tensile and fiber dispersion performance of ECC (engineered cementitious composites) produced with ground granulated blast furnace slag. Cem. Concr. Res. 37 (7), 1096–1105. doi:10.1016/j.cemconres.2007.04.006
Lee, K. M., and Park, P. J. (2005). Estimation of the environmental credit for the recycling of granulated blast furnace slag based on LCA. Resour. Conservation Recycl. 44 (2), 139–151. doi:10.1016/j.resconrec.2004.11.004
Li, V. C. (1993). From micromechanics to structural engineering: the design of cementitious composites for civil engineering applications. Dob. Gakkai Ronbunshu 471, 1–12. doi:10.2208/jscej.1993.471_1
Li, V. C., Mishra, D. K., and Wu, H. C. (1995). Matrix design for pseudo-strain-hardening fibre reinforced cementitious composites. Mater. Struct. 28, 586–595. doi:10.1007/BF02473191
Li, V. C., Wu, C., Wang, S., Ogawa, A., and Saito, T. (2002). Interface tailoring for strain-hardening polyvinyl alcohol-engineered cementitious composite (PVA-ECC). Mater. J. 99 (5), 463–472.
Liu, D., Yu, J., Qin, F., Zhang, K., and Zhang, Z. (2023). Mechanical performance of high-strength engineering cementitious composites (ECC) with hybriding PE and steel fibers. Case Stud. Constr. Mater. 18, e01961. doi:10.1016/j.cscm.2023.e01961
Liu, Y., Zhou, X., Lv, C., Yang, Y., and Liu, T. (2018). Use of silica fume and GGBS to improve frost resistance of ECC with high-volume fly ash. Adv. Civ. Eng. 2018 (1), 7987589. doi:10.1155/2018/7987589
Malhotra, V. M. (2000). Role of supplementary cementing materials in reducing greenhouse gas emissions. Concr. Technol. a Sustain. Dev. 21st Century 5, 6.
Mehta, P. K. (2002). Greening of the concrete industry for sustainable development. Concr. Int. 24 (7), 23–28. doi:10.1016/j.cemconcomp.2008.12.010
Modarres, Y., and Ghalehnovi, M. (2024). Comparison of the mechanical performance of concrete reinforced with recycled steel fibers from waste tires and hooked-end steel fibers at ambient and high temperatures. Civ. Eng. Infrastructures J. 57 (1), 61–83. doi:10.22059/ceij.2023.349788.1877
Pakravan, H. R., Jamshidi, M., and Latifi, M. (2016). Study on fiber hybridization effect of engineered cementitious composites with low-and high-modulus polymeric fibers. Constr. Build. Mater. 112, 739–746. doi:10.1016/j.conbuildmat.2016.02.112
Qiu, J., Tan, H. S., and Yang, E. H. (2016). Coupled effects of crack width, slag content, and conditioning alkalinity on autogenous healing of engineered cementitious composites. Cem. Concr. Compos. 73, 203–212. doi:10.1016/j.cemconcomp.2016.07.013
Ramezani, A. R., and Esfahani, M. R. (2018). Evaluation of hybrid fiber reinforced concrete exposed to severe environmental conditions. Civ. Eng. Infrastructures J. 51 (1), 119–130. doi:10.7508/ceij.2018.01.007
Ravichandran, D., Prem, P. R., Kaliyavaradhan, S. K., and Ambily, P. S. (2022). Influence of fibers on fresh and hardened properties of ultra-high performance concrete (UHPC)—a review. J. Build. Eng. 57, 104922. doi:10.1016/j.jobe.2022.104922
Ruan, Y., Han, B., Yu, X., Li, Z., Wang, J., Dong, S., et al. (2018). Mechanical behaviors of nano-zirconia reinforced reactive powder concrete under compression and flexure. Constr. Build. Mater. 162, 663–673. doi:10.1016/j.conbuildmat.2017.12.063
Shi, F., Pham, T. M., Hao, H., and Hao, Y. (2020). Post-cracking behaviour of basalt and macro polypropylene hybrid fibre reinforced concrete with different compressive strengths. Constr. Build. Mater. 262, 120108. doi:10.1016/j.conbuildmat.2020.120108
Shoji, D., He, Z., Zhang, D., and Li, V. C. (2022). The greening of engineered cementitious composites (ECC): a review. Constr. Build. Mater. 327 (11), 126701. doi:10.1016/j.conbuildmat.2022.126701
Sobhani, J., and Pourkhorshidi, A. R. (2021). The effects of cold-drawn crimped-end steel fibers on the mechanical and durability of concrete overlay. Civ. Eng. Infrastructures J. 54 (2), 319–330. doi:10.22059/ceij.2020.297941.1657
Soe, K. T., Zhang, Y. X., and Zhang, L. C. (2013). Impact resistance of hybrid-fiber engineered cementitious composite panels. Compos. Struct. 104, 320–330. doi:10.1016/j.compstruct.2013.01.029
Sumukh, E. P., Das, B. B., and Barbhuiya, S. (2024). Synergy of hydration and microstructural properties of sustainable cement mortar supplemented with industrial by-products. Int. J. Civ. Eng. 22 (7), 1137–1158. doi:10.1007/s40999-024-00950-9
Wang, Q., Lai, M. H., Zhang, J., Wang, Z., and Ho, J. C. M. (2020). Greener engineered cementitious composite (ECC)–The use of pozzolanic fillers and unoiled PVA fibers. Constr. Build. Mater. 247, 118211. doi:10.1016/j.conbuildmat.2020.118211
Wang, Q., Yi, Y., Ma, G., and Luo, H. (2019). Hybrid effects of steel fibers, basalt fibers and calcium sulfate on mechanical performance of PVA-ECC containing high-volume fly ash. Cem. Concr. Compos. 97, 357–368. doi:10.1016/j.cemconcomp.2019.01.009
Waqar, A., Khan, M. B., Afzal, M. T., Radu, D., Gălăţanu, T., Cazacu, C. E., et al. (2024). Investigating the synergistic effects of carbon fiber and silica fume on concrete strength and eco-efficiency. Case Stud. Constr. Mater. 20, e02967. doi:10.1016/j.cscm.2024.e02967
Yao, W., Li, J., and Wu, K. (2003). Mechanical properties of hybrid fiber-reinforced concrete at low fiber volume fraction. Cem. Concr. Res. 33 (1), 27–30. doi:10.1016/S0008-8846(02)00913-4
Zarei, A., Rooholamini, H., and Ozbakkaloglu, T. (2022). Evaluating the properties of concrete pavements containing crumb rubber and recycled steel fibers using response surface methodology. Int. J. Pavement Res. Technol. 15, 470–484. doi:10.1007/s42947-021-00049-7
Zhang, J., Wang, Q., and Wang, Z. (2016). Optimizing design of high strength cement matrix with supplementary cementitious materials. Constr. Build. Mater. 120, 123–136. doi:10.1016/j.conbuildmat.2016.05.100
Zhu, H., Zhang, D., Wang, T., McBain, M., and Li, V. C. (2021). Intrinsic self-stressing and low carbon Engineered Cementitious Composites (ECC) for improved sustainability. Cem. Concr. Res. 149, 106580. doi:10.1016/j.cemconres.2021.106580
Zhu, S., Zhang, Y. X., and Lee, C. K. (2024). An experimental study on hybrid fibre reinforced engineered cementitious composite link slabs under static and fatigue loadings. Eng. Struct. 300, 117254. doi:10.1016/j.engstruct.2023.117254
Zhu, Y., Zhang, Z., Yang, Y., and Yao, Y. (2014). Measurement and correlation of ductility and compressive strength for engineered cementitious composites (ECC) produced by binary and ternary systems of binder materials: fly ash, slag, silica fume and cement. Constr. Build. Mater. 68, 192–198. doi:10.1016/j.conbuildmat.2014.06.080
Keywords: engineered cementitious composites (ECC), mechanical response, energy absorption, pavement overlay, hybrid steel-synthetic-PVA fibers, supplementary cementitious material (SCM)
Citation: Kouhiazar Tulun M, Sobhani J, Mirhosseini SM, Zeighami E and Basiri MR (2025) Experimental study of mechanical and durability properties in hybrid binary and ternary fiber-reinforced ECC. Front. Built Environ. 11:1603359. doi: 10.3389/fbuil.2025.1603359
Received: 31 March 2025; Accepted: 12 May 2025;
Published: 15 July 2025.
Edited by:
Yucheng Zhong, Wuhan University of Technology, ChinaReviewed by:
Thanakorn Chompoorat, Civil Engineering University of Phayao, ThailandZhipeng Li, Washington State University, United States
Copyright © 2025 Kouhiazar Tulun, Sobhani, Mirhosseini, Zeighami and Basiri. This is an open-access article distributed under the terms of the Creative Commons Attribution License (CC BY). The use, distribution or reproduction in other forums is permitted, provided the original author(s) and the copyright owner(s) are credited and that the original publication in this journal is cited, in accordance with accepted academic practice. No use, distribution or reproduction is permitted which does not comply with these terms.
*Correspondence: Jafar Sobhani, MDAxMTcyOTA2NkBpYXUuYWMuaXI=