- 1Ordos Coal to Liquid Branch, China Shenhua Coal to Liquid and Chemical Co., Ltd., Ordos, China
- 2College of Energy and Transportation Engineering, Inner Mongolia Agricultural University, Hohhot, China
- 3Erdos Lutai Highway Engineering Co., Ltd., Ordos, China
Direct coal liquefaction residue (DCLR), a byproduct of the coal-to-oil process, poses a significant challenge for resource recycling and high-value utilization. Research has found that DCLR performs well in high temperature performance, but its shortcomings in low temperature performance remain a key issue limiting its widespread application. This research employs a composite modification approach, using DCLR as the primary material and incorporating SBS, rubber powder, aromatics oil, plasticizers, and stabilizers to prepare DCLR high-viscosity modified bitumen. The optimal formula was determined as 6% Styrene-Butadiene Styrene block copolymer (SBS) + 5% DCLR + 3% Dibutyl phthalate (DBP) + 10% rubber powder + 4% aromatics oil + 0.15% stabilizer. Performance tests showed that the rutting factor of the DCLR high-viscosity asphalt was 59.8% higher than that of the LT high-viscosity asphalt, and the G*/sinδ value after Rolling Thin Film Oven Test (RTFOT) aging had the smallest increase, confirming its excellent high-temperature rut resistance and resistance to short-term aging. The zero-shear viscosity (ZSV) values obtained by fitting the Carreau model indicated that within the temperature range of 46°C–64°C, the ZSV values of the DCLR modified asphalt were 1-2 orders of magnitude higher than those of the control samples, and the asphalt still maintained stable viscoelasticity at high temperatures (64°C), demonstrating its outstanding interfacial bonding performance. The bending beam rheometer (BBR) test results showed that the creep stiffness modulus of the three asphalts decreased while the creep rate increased, and the creep stiffness and creep rate had an approximate exponential relationship with temperature. Under the same temperature conditions, the stiffness modulus and creep rate of the DCLR high-viscosity asphalt were not significantly different from those of the Lutai (LT) high-viscosity asphalt, indicating its relatively good low-temperature crack resistance. Fluorescence microscopy results revealed that the DCLR system formed a stable three dimensional colloidal skeleton structure between the modifier molecules and the asphaltenes, which is the fundamental reason for its superior performance and low-temperature properties compared to the LT high-viscosity asphalt.
1 Introduction
Under the background of implementing the “Transportation Power” strategy, China’s high-grade highway construction is facing the dual challenges of a large proportion of heavy-duty traffic and a significant increase in traffic volume. The demand for high-viscosity asphalt with excellent temperature stability in road engineering construction is growing. However, traditional modified asphalt faces a contradiction between performance improvement and cost control, and this technological predicament forms a strategic coupling point with the problem of coal chemical solid waste disposal: direct coal liquefaction residue (DCLR), as a typical coal-based solid waste, has significant synergistic potential with the upgrade of road asphalt materials in terms of its solid waste disposal needs.
The solid-liquid separation process of direct coal liquefaction technology generates substantial by-products, accounting for approximately 30% of the original coal mass, which are referred to as DCLR (Sun et al., 2017). Conventional disposal methods pose significant environmental risks: open-pit storage can result in the migration of polycyclic aromatic hydrocarbons and heavy metals via leaching, while incineration treatment generates persistent pollutants such as dioxins. With the increasing global demand for clean energy and sustainable materials, DCLR has garnered significant attention due to its high carbon content and modification potential (Ji et al., 2023a; Zhang et al., 2016). DCLR exhibits a high content of asphaltenes and resins, coupled with a low content of saturated and aromatic components, enabling it to effectively enhance the high-temperature performance of asphalt. Furthermore, it can increase the viscosity of modified asphalt to a degree that meets the requirements for high-viscosity asphalt preparation. Remarkably, the nitrogen- and sulfur-containing (N/S) polar functional groups in DCLR significantly enhance the interfacial bonding strength between asphalt and silicate aggregates. This dual attribute of “solid waste-resources” represents an innovative breakthrough in addressing both the performance limitations of road materials and the challenge of coal-based solid waste disposal, and has emerged as a prominent research focus in the field of asphalt pavement materials.
DCLR can significantly enhance the high-temperature rutting resistance of asphalt mixtures through physical or chemical modification. Numerical simulations and dynamic creep tests reveal that DCLR modified asphalt mixtures exhibit markedly reduced rut depth compared to conventional mixtures, indicating superior deformation resistance (Ji et al., 2021a). Furthermore, composite modification techniques (e.g., synergistic use of SBS and aromatic oil) substantially improve the high-temperature rheological properties of DCLR modified asphalt, with an optimal composition of 9% DCLR + 4% SBS + 2% aromatic oil delivering the best rutting resistance (Li et al., 2022). The high-temperature deformation characteristics of DCLR-modified asphalt were successfully simulated and experimentally validated using a second-order corrected Burgers rheological model, with prediction deviations confined to less than 5% (Ji et al., 2021b).
Studies also demonstrate that fly ash and DCLR increase the viscosity, rutting resistance, elasticity, and permanent deformation resistance of asphalt mastic while reducing its temperature sensitivity (Jianming et al., 2020). However, these additives may adversely affect the low-temperature and fatigue performance of the mastic (Zhechao et al., 2024). Incorporating modifiers such as benzaldehyde and DOP during compounding can elevate the asphalt’s solubility parameter, thereby minimizing the solubility parameter difference between asphalt and the DCLR system. This enhances their compatibility and improves the overall performance of DCLR modified asphalt (Ji et al., 2023b). Additionally, DCLR improves the bonding capacity of asphalt mastic when used as a fine aggregate, strengthening load transfer. In asphalt mixtures, DCLR functions dually as both a skeleton and a filler (Jie et al., 2021). Thermal loading dominates over mechanical stress in governing rutting resistance, while DCLR-modified asphalt demonstrates negligible sensitivity to both temperature fluctuations and loading variations, highlighting its superior thermomechanical stability (Ji et al., 2024b).
Although DCLR excels in high-temperature performance, its shortcomings in low-temperature performance remain a key issue limiting its widespread application. Studies have found that increasing the DCLR content can lead to an increase in the low-temperature creep compliance of asphalt and a decrease in crack resistance (Li et al., 2022). Researchers have attempted to enhance low-temperature performance through composite modification. For instance, adding 3% dioctyl maleate or a combination of 2% SBS and 15% rubber powder can approximately double the low-temperature ductility of DCLR modified asphalt. It meets the technical requirements of SBS modified asphalt (Ji et al., 2019). Furthermore, physical hardening effect analysis reveals that under low-temperature conditions, the number and morphology of the “beehive structure” of DCLR modified asphalt decrease. However, silane coupling agents and other expansion agents can effectively inhibit the deterioration of the microstructure (Ji et al., 2021c). Molecular dynamics simulations further demonstrate that expansion agents can significantly enhance the compatibility between asphalt components and DCLR by reducing the solubility parameter difference between the two. Among these, the synergistic effect of benzyl alcohol (BA) and DOP proves to be the most effective (Ji et al., 2024a). Beyond traditional asphalt mixtures, the application potential of DCLR in recycled materials and innovative pavement systems has gradually emerged. For example, when DCLR replaces mineral powder or serves as a geopolymer filler, it can enhance the dynamic stability and shear resistance of emulsified asphalt mixtures (Yang et al., 2024).
Building on previous research findings, a systematic investigation of the performance optimization paths of DCLR modified asphalt at multiple scales is required, with a focus on addressing its low-temperature performance deficiencies and insufficient adaptability to complex environments. While research on the application of DCLR in high-viscosity modified bitumen is relatively limited, this study aims to fill this gap. By leveraging the high-viscosity characteristics of DCLR, this research employs a composite modification approach, using DCLR as the primary material and incorporating SBS, rubber powder, aromatics oil, plasticizers, and stabilizers to prepare DCLR high-viscosity modified bitumen. Through comprehensive basic performance tests, the optimal formulation was identified. Furthermore, advanced testing techniques such as dynamic shear rheometry (DSR), BBR and fluorescence microscopy were utilized to evaluate the high- and low-temperature rheological properties, as well as the microstructural characteristics of the DCLR high-viscosity bitumen. These findings provide valuable theoretical support for enhancing the resource utilization of coal-based solid waste and advancing the green transformation of road engineering.
2 Materials and methods
2.1 Materials
2.1.1 DCLR
The chemical composition of DCLR comprises 34%∼37% heavy oil, 17%∼22% asphaltenes, and a combined fraction of 43%∼46% pre-asphaltenes and tetrahydrofuran insoluble (THFI), with corresponding thermomechanical performance parameters quantitatively summarized in Table 1.
2.1.2 Other additives
During the preparation process of DCLR high-viscosity asphalt, a star-shaped SBS modifier (YH-602T) produced by Sinopec Baling Petrochemical Company was adopted, which conforms to the specifications of “Thermoplastic elastomer styrene butadiene block copolymer (SBS)” (SH/T 1610). SBS technical indicators are shown in Table 2. Furthermore, 40-mesh rubber powder has been chosen to enhance the high-temperature performance, elastic recovery, and aging resistance of modified asphalt. The primary technical specifications are outlined in Table 3. The critical physicochemical parameters of 4# Aromatic Oil are systematically detailed in Table 4. This specific aromatic oil promotes the development of stable colloidal microstructures, ultimately enhancing the low-temperature flexibility of asphalt binders. Plasticizers do not chemically react with polymers and can improve the flexibility and tensile strength of modified asphalt without altering its fundamental chemical properties. This study did not employ benzaldehyde or DOP additives utilized in prior research due to their high costs and adverse environmental impacts. Instead, a more stable, cost-effective, and eco-friendly material combination of dibutyl phthalate (DBP) and aromatic oil was adopted. DBP, a plasticizer with its key physicochemical properties summarized in Table 5, was employed to tailor the rheological behavior of the asphalt binder. In the preparation of high viscosity modified asphalt, benzaldehyde is usually added to improve the compatibility between the modifier and the asphalt, and to enhance the low-temperature performance of high viscosity modified asphalt. In addition, stabilizers (provided by Fuhua Chemical Co., Ltd.) were used to improve the storage stability of DCLR modified asphalt.
2.1.3 Control group matrix asphalt and LT high-viscosity asphalt
Haiyun 90# matrix asphalt and Lutai (LT) high-viscosity asphalt (produced by Erdos Lutai highway engineering Co., Ltd. and its main components include matrix asphalt, viscosity-enhancing additives, plasticizers, rubber powder, etc.) were used as control groups for performance evaluation. LT high-viscosity asphalt was selected as the control material because it represents the industry benchmark for drainage pavement applications. Its balanced performance in high-temperature stability and low-temperature crack resistance provides a critical reference for evaluating whether DCLR-modified asphalt meets practical engineering requirements. Furthermore, LT asphalt’s commercial availability and standardized formulation ensure data comparability, unlike lab-blended or region-specific high-viscosity alternatives. Their basic technical parameters are shown in Table 6.
2.2 Preparation of DCLR high-viscosity asphalt
The DCLR high-viscosity modified asphalt was fabricated following the optimized synthesis procedure depicted in Figure 1, involving controlled thermal conditioning and high-shear mixing to ensure homogeneous dispersion of coal liquefaction residue within the asphalt matrix.
2.3 Test methods
2.3.1 DSR test
The high-temperature rheological characteristics of DCLR high-viscosity asphalt were characterized through DSR measurements performed on a Discovery HR-1 rotational rheometer (TA Instruments, New Castle, DE) equipped with 25-mm parallel-plate geometry. A standardized testing configuration was maintained with a plate gap distance of 1 mm throughout the experimental protocol, consistent with ASTM specifications for asphalt material analysis. The temperature range was set from 46°C to 100°C, with intervals of 6°C, and the loading frequency was varied from 0.1 to 100 rad/s. The rutting factor (G*/sinδ) was used as an evaluation index for the high-temperature performance of the asphalt; the temperature at which G*/sinδ reaches or exceeds 1 kPa was defined as the critical temperature.
Asphalt viscosity exhibits stabilization at extreme shear rates. Zero shear viscosity (ZSV) describes the steady-state viscosity value of a material at extremely low shear rates (shear rates approaching zero). It reflects the flow characteristics of materials in a static or near static state, and is a key parameter for characterizing the entanglement of long-term relaxation behavior of polymer fluids. For asphalt polymer materials, a higher ZSV value indicates a more stable material structure. Research indicates that an elevation in the ZSV value is associated with an improvement in rutting resistance (Lihan et al., 2010). Among rheological models, the Carreau-derived ZSV demonstrates optimal correlation with field performance, establishing it as a reliable evaluation metric (Meng et al., 2008). This study employed a simplified Carreau equation (Equation 1) to quantify ZSV across asphalt formulations. Additionally, the ZSV was utilized to characterize the high-temperature rheological behavior of DCLR high-viscosity asphalt.
In the equation,
2.3.2 BBR test
The SYD-0627 asphalt bending beam rheometer was used to conduct the tests at temperatures of −12°C, −18°C, and −24°C. The creep stiffness modulus S was obtained to evaluate the ability of DCLR high-viscosity asphalt to resist permanent deformation, while the creep rate m was used to assess its stress relaxation properties. Additionally, the control criteria recommended by the SHRP program, which are a creep stiffness S ≤ 300 MPa and a creep rate m ≥ 0.3, were applied as evaluation standards.
2.3.3 Fluorescence microscopy
A Nexcope NE910-FL fluorescent microscope was used to analyze the micro-morphological characteristics of DCLR high-viscosity asphalt, focusing on the uniformity of the high-viscosity modifier distribution and the phase separation state.
3 Results and discussion
3.1 Development of high-viscosity asphalt formula utilizing DCLR
Based on a large number of preliminary basic experimental research, the additions of SBS modifier, DCLR modifier, and plasticizer DBP (all as a percentage of asphalt mass) were determined. The dosage of SBS, DBP plasticizer, and other plasticizers was fixed, while the optimization of aromatic oil and stabilizers required fine-tuning on the established main framework. This approach avoids the coupling effects of multiple variables and ensures comparability with the control group. Considering the low-temperature performance and storage stability of high-viscosity asphalt, different amounts of aromatic oil and stabilizer were incorporated into the formulation, resulting in the development of four formulations, as illustrated in Figure 2. Furthermore, optimization was achieved through basic asphalt performance tests, 60°C dynamic viscosity measurements, and storage stability assessments, ultimately establishing the optimal DCLR high-viscosity asphalt formulation. The experimental results are summarized in Table 7.
Through comparative analysis of key parameters, it was found that the F3 group modified asphalt met the specification limits in core indicators, including 60°C dynamic viscosity (107,824 Pa·s), penetration (46.20 mm), and softening point (95.3°C). The group achieved a peak ductility of 31.0 cm, with a softening point difference of 1.6°C, significantly lower than the standard threshold of ≤2.5°C. Experimental data indicate that the modifier-asphalt system of this formulation exhibits good compatibility, characterized by a stable blend phase and outstanding anti-segregation performance (Yang et al., 2022). Based on these performance advantages, the optimal formulation for DCLR high-viscosity asphalt was finalized as: SBS 6%, DCLR 5%, DBP 3%, rubber powder 10%, aromatic oil 4%, and stabilizer 0.15% (by mass).
3.2 DCLR high-viscosity asphalt DSR test results
3.2.1 Rutting factor (G*/Sinδ)
Figure 3 illustrates the temperature-dependent rutting resistance (G*/sinδ) of asphalt samples before and after aging. The data reveal a rapid decrease in rutting factor at low temperatures (<50°C), followed by a pronounced decline above 60°C, eventually stabilizing at elevated temperatures. This behavior stems from thermally weakened intermolecular interactions in asphalt, where increased viscous component dominance reduces elastic modulus, culminating in a viscoelastic flow state. Notably, DCLR modified high-viscosity asphalt consistently exhibited the highest rutting resistance, with a 42.6% average enhancement in G*/sinδ over matrix asphalt, highlighting its superior high-temperature performance retention after aging.
Using 46°C as a representative evaluation temperature, all asphalt samples exhibited a marked enhancement in rutting resistance (G*/sinδ) after RTFOT aging, with an average increase of 66.7%. This hardening behavior correlates with the compositional evolution occurring during aging: light components (saturates and aromatics) progressively transform into heavy fractions (resins and asphaltenes), thereby restructuring the viscoelastic network. Significantly, although aging modified the absolute G*/sinδ values, the characteristic exponential thermal decay behavior maintained structural congruence with pristine counterparts, thereby validating the retention of intrinsic temperature-rheological coupling mechanisms. Compared with the corresponding original asphalt, the G*/sinδ of LT high-viscosity asphalt and DCLR high-viscosity asphalt increased by 104.5% and 62.6% respectively after Pressure Aging Vessel (PAV, according to AASHTO R 28) aging. DCLR high-viscosity asphalt exhibits superior aging resistance compared to LT high-viscosity asphalt, attributed to the enhanced anti-aging performance derived from DCLR’s high aromaticity and colloidal stability.
3.2.2 Zero shear viscosity (ZSV)
Frequency sweep analyses were performed on matrix asphalt, DCLR modified high-viscosity asphalt, and LT-modified asphalt to quantify their viscoelastic responses. Nonlinear regression using the simplified Carreau model (Equation 1) enabled determination of zero shear viscosity (η0) and model fidelity (R2) across temperature regimes. The derived rheological parameters, systematically compared in Table 8, reveal distinct temperature-dependent viscous behaviors among the formulations.
As evidenced by Table 8, matrix asphalt exhibits marked thermal thinning of ZSV with rising temperatures. A critical viscosity collapse occurs beyond 82 °C (R2 < 0.95), signaling transition to Newtonian flow dominance. In contrast, both DCLR- and LT-modified high-viscosity asphalts maintain robust temperature ZSV correlations (R2 > 0.99) across the 46°C–100°C spectrum, demonstrating superior thermo-rheological stability despite progressive viscosity reduction.
The ZSV-temperature profiles (Figure 4) demonstrate distinct rheological hierarchies among asphalt formulations. DCLR modified high-viscosity asphalt displays the highest ZSV at low temperatures (<52°C), correlating with superior rutting resistance. While all systems exhibit viscosity reduction with rising temperature, matrix asphalt shows minimal thermal sensitivity compared to modified counterparts. This thermally driven softening arises from molecular chain mobilization and weakened intermolecular forces, as described by the Arrhenius-type flow activation mechanism. Notably, when temperature exceeds a critical transition temperature (approximately 70°C), the ZSV values of the three asphalts stabilize, indicating that the asphalt enters a Newtonian fluid state. In this state, viscosity is primarily governed by the free volume theory, and the temperature’s effect on viscosity diminishes, explaining the slowing down of viscosity changes in the high-temperature region. The ZSV value of DCLR modified asphalt is significantly higher than that of the control group, which may be related to the multi-level ordered structure formed by the stacking of polycyclic aromatic hydrocarbons, polar group bonding, and entanglement of polymer chains in DCLR high viscosity modified asphalt. Its essence is the synergistic enhancement effect of molecular scale interactions.
3.3 DCLR high-viscosity asphalt BBR test results
The trends of S and m values for various asphalts at different temperatures are presented in Figure 5. Based on the low-temperature rheological performance analysis, there exists a significant correlation between the stiffness modulus S and the creep rate m of the three asphalts under temperature changes: as temperature decreases, the S value shows a monotonically increasing trend, while the m value decreases. The base asphalt demonstrated non-compliant creep stiffness (S = 378 MPa) at −18°C, exceeding the Strategic Highway Research Program performance grading (PG) threshold (S ≤ 300 MPa) and exhibiting brittle fracture at −24°C, which demonstrates its failure to satisfy the dual SHRP PG specifications (AASHTO M 320) requiring concurrent fulfillment of S ≤ 300 MPa and m ≥ 0.3. In contrast, LT high viscosity asphalt meets PG requirements (S = 275 MPa, m = 0.3339) at −24°C, and its low-temperature performance is superior to DCLR modified asphalt. But the DCLR modified asphalt also meets the relevant requirements at this temperature.
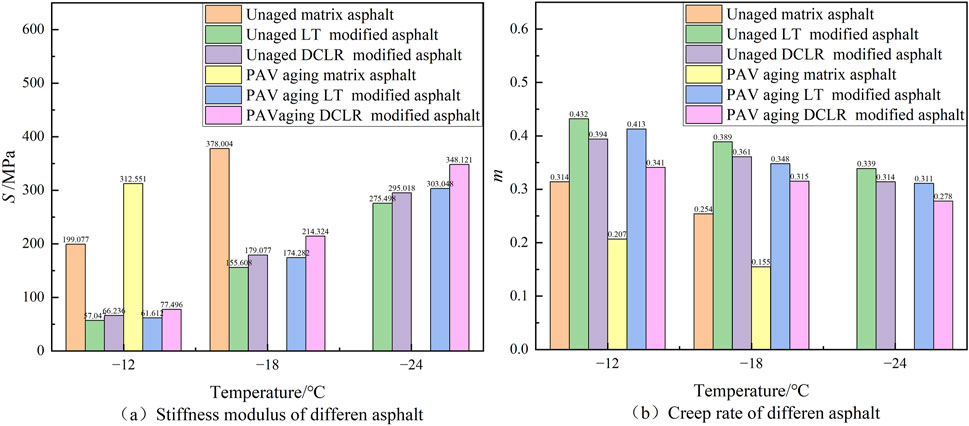
Figure 5. Low-temperature rheological parameters of different asphalt. (a) Stiffness modulus of differen asphalt (b) Creep rate of differen asphalt.
It can be observed that the low-temperature performance of DCLR high viscosity asphalt before and after PAV aging is slightly lower than that of LT high viscosity asphalt. Taking the stiffness modulus at −18°C as an example, after PAV aging, the values for LT and DCLR high-viscosity asphalts increased by 18.4% and 13.5%, respectively, compared to the unaged original asphalt. Although DCLR high-viscosity asphalt exhibits lower initial low-temperature performance than LT high-viscosity asphalts, its performance degradation after PAV aging is less pronounced. This divergence stems primarily from two factors: (1) the aromatic oil modifier stabilizes the colloidal structure via high-speed shear dispersion, ensuring homogeneous DCLR distribution within the asphalt matrix; (2) such treatment enhances asphalt’s stress relaxation capability, notably reducing storage modulus. Meanwhile, SBS modifier forms a three-dimensional network structure by absorbing soft components, which interacts with rubber powder particles at the interface. This interaction creates a sub-homogeneous composite system, with SBS serving as the dispersed phase and DCLR as the continuous phase. The interface strengthening effect between the DCLR modifier and the matrix material asphalt results in the DCLR high-viscosity asphalt enhencing low-temperature and high-temperature performance.
Although the low-temperature performance of DCLR-modified asphalt is slightly lower than that of LT asphalt, its significant unit cost advantage and better social benefits. This triple advantage of “low-cost-high-performance-environmental-friendly” makes DCLR have stronger market competitiveness in the application of high-viscosity asphalt. DCLR high-viscosity asphalt incorporates DCLR and rubber powder, with both raw materials for the modifier being solid waste. Specifically, DCLR represents the unreacted mixture produced during the direct coal liquefaction process, featuring a relatively low recycling cost. By utilizing these two types of solid waste materials concurrently, DCLR high-viscosity asphalt not only mitigates environmental pollution but also facilitates resource reuse, thereby possessing considerable social and economic value.
3.4 DCLR high-viscosity asphalt fluorescence microscope test results
To further investigate modifier distribution characteristics and interfacial effects, the microstructural evolution of asphalt before and after aging was characterized using fluorescence microscopy (×800 magnification), as shown in Figure 6. The results indicate that the original matrix asphalt exhibits a significant heterogeneous distribution pattern in the unaged state, with clear phase separation between fluorescent regions and dark areas (Figure 6A). After short-term aging, the matrix asphalt system undergoes significant phase recombination, characterized by an expanded fluorescent region, an increased number and size of black particles, while maintaining a discrete distribution pattern overall (Figure 6B). DCLR high-viscosity asphalt demonstrates a unique structural advantage in its original state: its micrograph reveals a network cementation structure, forming a colloidal system dominated by a continuous phase, as seen in Figure 6C. Notably, although short-term aging leads to a particle coarsening phenomenon similar to that in the matrix asphalt, the network skeleton of the DCLR system remains structurally intact, as shown in Figure 6D. Compared to DCLR modified asphalt and matrix asphalt, the original LT high-viscosity asphalt has fewer fluorescent regions, which are more evenly distributed and exhibit relatively better compatibility (Figure 6E). However, after short-term aging, the LT high-viscosity asphalt shows an increase in fluorescent regions, presenting an overall even distribution, but with poor structural integrity and worse compatibility than DCLR modified asphalt.
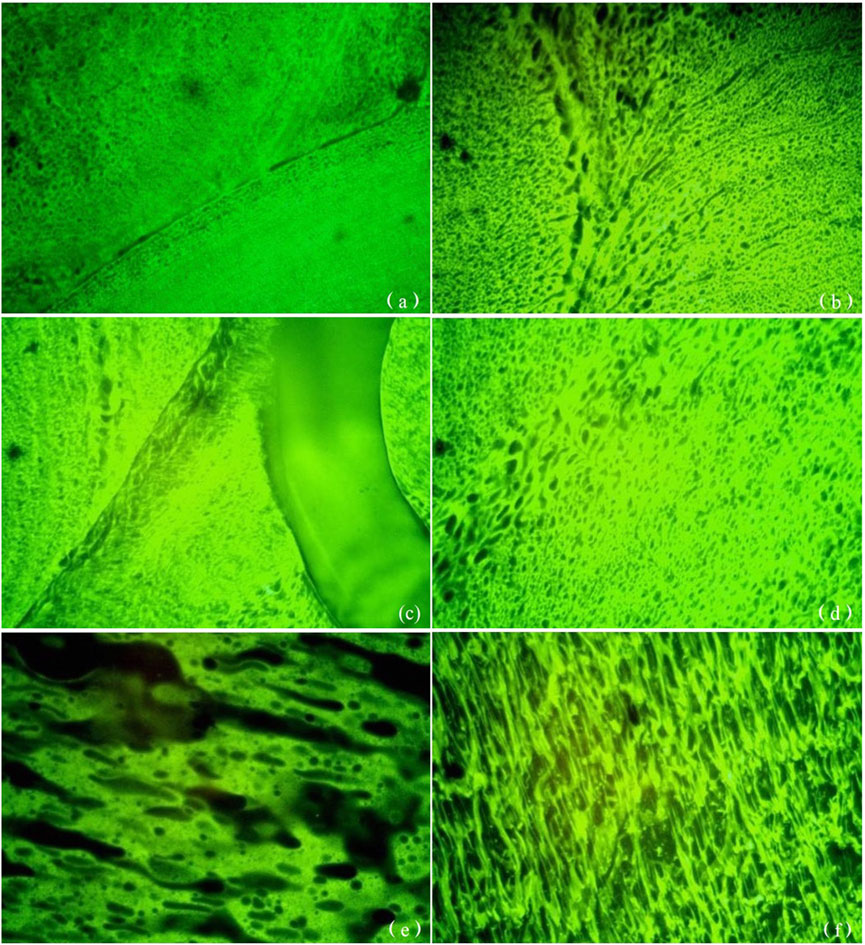
Figure 6. Fluorescence microscope test results for different asphalt. (A) Original matrix asphalt. (B) Matrix asphalt after short-term aging. (C) DCLR high viscosity asphalt in its original state. (D) DCLR high viscosity asphalt after short-term aging. (E) the original LT high-viscosity asphalt. (F) LT high viscosity asphalt after short-term aging.
Through comparison of the microstructural morphologies of the three asphalt types, it is observed that both DCLR high-viscosity asphalt and LT high-viscosity asphalt exhibit uniform distribution and good compatibility. Additionally, the DCLR high-viscosity asphalt can form a partial colloidal network structure, demonstrating superior viscoelastic properties compared to LT high-viscosity asphalt. This three-dimensional network structure effectively inhibits the formation of microcrack defects, corresponding to the reduction of “beehive structures” under low-temperature conditions as described in the Introduction. However, short-term aging affects the solubility of modifiers, leading to compromised compatibility.
4 Conclusion
(1) Through comprehensive analysis of basic asphalt properties, 60°C dynamic viscosity, and segregation test results, the optimal formulation of DCLR high-viscosity asphalt has been determined as follows: 6% SBS, 5% DCLL, 3% DBP, 10% rubber powder, 4% aromatic oil, and 0.15% stabilizer.
(2) Dynamic shear rheological tests on the three asphalt types results demonstrate that DCLR high-viscosity asphalt exhibits the highest rutting factor (G*/sinδ), indicating superior high-temperature rutting resistance. After RTFOT aging, the mean G*/sinδ values for matrix asphalt, LT high-viscosity asphalt, and DCLR high-viscosity asphalt increased significantly by 117.6%, 57.6%, and 52.2%, respectively. These results confirm that the conversion of light components to heavy components enhances high-temperature stability and also highlight that DCLR high-viscosity asphalt demonstrates good resistance to short-term aging. Within the temperature range of 46°C–100°C, both DCLR high-viscosity asphalt and LT high-viscosity asphalt display better high-temperature stability, with DCLR high-viscosity asphalt achieving the highest ZSV value, which reflects its superior high-temperature performance.
(3) With decreasing temperature, the low-temperature creep stiffness of asphalt decreases while the creep rate increases, showing an approximate exponential relationship between creep stiffness, creep rate, and temperature. The various modifiers in DCLR high-viscosity asphalt play different roles, effectively enhancing the elasticity and plasticity of DCLR high-viscosity asphalt, thereby significantly improving its low-temperature performance to reach a level comparable to that of LT high-viscosity asphalt.
(4) Both DCLR and LT high-viscosity asphalt exhibit outstanding component uniformity. The DCLR system, particularly, establishes a three-dimensional colloidal network skeleton structure through interactions between modifier molecules and asphaltene, which fundamentally accounts for its superior viscoelastic properties and low-temperature performance compared to LT high-viscosity asphalt. Furthermore, under short-term aging, the modified asphalt systems experience component migration and recombination. The DCLR sample demonstrates superior modifier compatibility, as evidenced by the minimal increase in rutting factor after aging.
Data availability statement
The original contributions presented in the study are included in the article/supplementary material, further inquiries can be directed to the corresponding author.
Author contributions
LuY: Methodology, Writing – original draft. WY: Writing – original draft, Conceptualization. RY: Methodology, Data curation, Writing – original draft. LYa: Data curation, Writing – original draft, Software. LYo: Project administration, Visualization, Writing – review and editing, Validation. GZ: Writing – review and editing, Investigation.
Funding
The author(s) declare that financial support was received for the research and/or publication of this article. The work in the paper was supported by the project: “Research and Application Technology of Coal Liquefied Oil Residue Modified Asphalt by Inner Mongolia Transportation Group Mengtong Maintenance Co., Ltd”.
Conflict of interest
Authors LuY and WY were employed by China Shenhua Coal to Liquid and Chemical Co., Ltd. Author GZ was employed by Erdos Lutai Highway Engineering Co., Ltd.
The remaining authors declare that the research was conducted in the absence of any commercial or financial relationships that could be construed as a potential conflict of interest.
The authors declare that this study received funding from Inner Mongolia Transportation Group Mengtong Maintenance Co., Ltd. The funder was not involved in the study design, collection, analysis, interpretation of data, the writing of this article, or the decision to submit it for publication.
Generative AI statement
The author(s) declare that no Generative AI was used in the creation of this manuscript.
Publisher’s note
All claims expressed in this article are solely those of the authors and do not necessarily represent those of their affiliated organizations, or those of the publisher, the editors and the reviewers. Any product that may be evaluated in this article, or claim that may be made by its manufacturer, is not guaranteed or endorsed by the publisher.
References
Ji, J., Chen, M., Suo, Z., Wei, J., Wang, J., and Chen, L. (2021b). Rutting prediction model of asphalt mixture based on the triaxial repeated load test. Adv. Civ. Eng. 2021 (2), 1–9. doi:10.1155/2021/5238680
Ji, J., Huang, C., Ma, T., Xu, X., Zhang, J., Han, B., et al. (2023b). Evaluation of compatibilizers for improving compatibility between direct coal liquefaction residue and asphalt. China J. Highw. Transp. 36 (06), 1–13. doi:10.19721/j.cnki.1001-7372.2023.06.001
Ji, J., Liu, H., Yao, H., and You, Z. (2024a). Influence of compatibilization methods on the compatibility between asphalt and DCLR components with molecular dynamics (MD) method. Constr. Build. Mater. 431, 136474. doi:10.1016/j.conbuildmat.2024.136474
Ji, J., Liu, H., Yao, H., and You, Z. (2024b). Influence of direct coal liquefaction residue (DCLR) on the rutting behavior of asphalt mixture with the discrete element method. Constr. Build. Mater. 453, 139028. doi:10.1016/j.conbuildmat.2024.139028
Ji, J., Suo, Z., Ran, Z., Li, H., Han, B., Wang, J., et al. (2021c). Effect of physical hardening on low temperature performance of DCLR modified asphalt. Constr. Build. Mater. 295, 123545. doi:10.1016/j.conbuildmat.2021.123545
Ji, J., Wang, Z., Li, P., Zheng, W., Xu, X., Wang, Z., et al. (2023a). A review on direct coal liquefaction residue applied in asphalt pavements. J. Clean. Prod., 395. doi:10.1016/j.trgeo.2025.101606
Ji, J., Wang, Z., Yao, H., Wang, D., Zhang, R., Diab, A., et al. (2021a). A numerical study on rutting behaviour of direct coal liquefaction residue modified asphalt mixture. Road Mater. Pavement Des. 22 (6), 1454–1468. doi:10.1080/14680629.2019.1690029
Ji, J., Yuan, Z., Wei, J., Suo, Z., Xu, Y., Li, H., et al. (2019). Improvements of low-temperature properties of direct coal liquefaction residue modified asphalt. J. China Univ. Petroleum Nat. Sci. Ed. 43 (4), 166–173. In Chinese. doi:10.3969/j.issn.1673-5005.2019.04.020
Jianming, W., Zhang, S., Ying, S., Gong, X., Chen, C., and Jow, J. (2020). Super hard asphalt (SHA) from direct coal liquefaction process as pavement material. J. Clean. Prod. 274 (9), 123815. doi:10.1016/j.jclepro.2020.123815
Jie, J., Qiang, X. X., Ying, X., Wang, Z., and Wang, J. n. (2021). Research on performance of direct coal liquefaction residue modified asphalt mortar. J. Fuel Chem. Technol. 49 (8), 1095–1101. doi:10.1016/s1872-5813(21)60081-6
Li, Y., Kang, X., Gao, Q., and Jia, Y. (2022). Rheological properties of composite modified asphalt with direct coal liquefaction residues. Lecture notes in Civil engineering. 235, 59–74. doi:10.1007/978-981-99-1748-8_5
Lihan, L., Han, G., and Sun, Y. (2010). Evaluation method and indicator for viscosity of high-viscosity asphalt. J. Build. Mater. 13 (03), 352–356+362. In Chinese. doi:10.3969/j.issn.1007-9629.2010.03.016
Meng, Y., Zhang, X., and Jia, J. (2008). Research on zero shear viscosity of asphalt based on different loading modes. J. Traffic Transp. Eng. (04), 35–39. In Chinese. Available online at: https://transport.chd.edu.cn/en/article/id/200804008.
Sun, M., Zhang, D., Huang, M., Chen, J., Tang, X., He, C., et al. (2017). Properties and carbonization behavior of asphalt modified with the THF-soluble fraction of a coal liquefaction residue. Petroleum Sci. Technol. 35 (7), 674–680. doi:10.1080/10916466.2016.1271811
Yang, G., Xiao, Z., Jiang, Z., Ding, W., Miao, D., and Qiao, Q. (2024). Utilization of direct coal liquefaction residue (DCLR) in recycled emulsified asphalt mixtures: a solution as geopolymer binder and filler materials. Constr. & Build. Mater. 438, 137278. doi:10.1016/j.conbuildmat.2024.137278
Yang, Z., Wang, L., Xu, B., Cao, D., Li, J., and Zhao, K. (2022). Performance of SBS modifier-crumb rubber composite modified asphalt used as an anti-wear layer of perpetual pavement. Int. J. Pavement Eng. 23 (12), 4097–4111. doi:10.1080/10298436.2021.1932882
Zhang, D., Luo, R., Chen, Y., Zhang, S., and Sheng, Y. (2016). Performance analysis of DCLR modified asphalt based on surface free energy. China J. Highw. Transp. 29 (01), 22–28. Available online at: https://www.researchgate.net/publication/299392181_Performance_analysis_of_DCLR-modified_asphalt_based_on_surface_free_energy.
Keywords: DCLR high-viscosity asphalt, optimal formula, rutting factor, zero-shear viscosity, fluorescence microscopy
Citation: Yong L, Yong W, Yanyan R, Yandan L, Yongxiang L and Zhong G (2025) Rheological properties study of high-viscosity asphalt based on direct coal liquefaction residue. Front. Built Environ. 11:1619524. doi: 10.3389/fbuil.2025.1619524
Received: 28 April 2025; Accepted: 09 June 2025;
Published: 09 July 2025.
Edited by:
Bowei Sun, Civil Aviation University of China, ChinaReviewed by:
Tengfei Nian, Lanzhou University of Technology, ChinaYongdan Wang, Northwest A & F University Hospital, China
Zhiagang Li, Xi’an University of Science and Technology, China
Xiaojin Lu, Southeast University, China
Copyright © 2025 Yong, Yong, Yanyan, Yandan, Yongxiang and Zhong. This is an open-access article distributed under the terms of the Creative Commons Attribution License (CC BY). The use, distribution or reproduction in other forums is permitted, provided the original author(s) and the copyright owner(s) are credited and that the original publication in this journal is cited, in accordance with accepted academic practice. No use, distribution or reproduction is permitted which does not comply with these terms.
*Correspondence: Li Yongxiang, bHl4aWFuZ0BpbWF1LmVkdS5jbg==