- 1Department of Engineering Sciences, University of Agder, Grimstad, Norway
- 2Unicon AS, Oslo, Norway
- 3Department of Structural Engineering, Norwegian University of Science and Technology, Trondheim, Norway
This paper is a presentation of an investigation into the suitability of locally produced ultra-high-performance fiber-reinforced concrete (UHPFRC) for the rehabilitation of deteriorated concrete bridge decks in Norway. Full-scale production was conducted at a conventional ready-mix concrete plant using mostly locally available materials from silos at the plant. Material properties relevant for bridge deck rehabilitation were investigated, including compressive strength, residual flexural strength, E-modulus, shrinkage, and resistance to chloride ion penetration. These results were compared to earlier experiences at laboratory scale. The findings indicate that full-scale production of UHPFRC with locally available constituents is achievable using common facilities for ready-mixed concrete, including mixing, transportation, and pumping in quantities appropriate for industrialized bridge deck rehabilitation. The applied UHPFRC mix design was found suitable for bridge rehabilitation, considering compressive and flexural strength, shrinkage, and durability evaluated by resistance against chloride migration. Up to approximately 3 vol% of micro steel fibers (225 kg/m3) were stepwise added, achieving a castable and self-leveling UHPFRC mix. Self-leveling mixes are not suitable for applications in slopes, which are common for bridge decks. Adjustments to the mix design are necessary to achieve thixotropy. Some additional material properties remain to be evaluated, such as the bond between the old concrete substrate and the new UHPFRC layer. This is being investigated in the next stage of the project.
1 Introduction
Many countries, including Norway, are currently facing a severe backlog in the maintenance of transportation networks (RIF Engineers, 2021). Insufficient durability of reinforced concrete bridges is particularly related to rebar corrosion due to chlorides from the sea or deicing salting. Old reinforced concrete bridges often lack membranes to prevent water intrusion. Retrofitting a membrane is usually undesirable due to the increased dead-load and, thus, the potential for exceeding the capacity of the structure. Consequently, deicing salting can increase chloride content in the decks, potentially causing reinforcement corrosion. Additionally, many bridge decks cast before the 1990s are affected by alkali-silica reactions (Jensen, 2004; Kongshaug et al., 2021). This is accelerated by high humidity content in the concrete, due to the lack of membranes.
A promising repair method is the application of an Ultra-High-Performance Fiber-Reinforced Concrete (UHPFRC/UHPC) overlay, both for reinforced concrete bridges (Graybeal et al., 2020; Bertola et al., 2021b; Brühwiler, 2024) and steel-concrete composite bridges (Brühwiler, 2023a). UHPFRC is a cementitious-based material with superior mechanical properties and durability, compared to conventional concrete (Russell and Graybeal, 2013). This class of materials has been developed over the past 30 years (Brühwiler, 2020), but has not yet reached widespread application. UHPFRC is commonly composed of cement and other cementitious binders, fine aggregates, a low amount of water (water-to-binder (w/b) ratio around 0.2), chemical admixtures, and a high content of micro steel fibers (often above 150 kg/m3) (Russell and Graybeal, 2013; Graybeal et al., 2020; Brühwiler, 2024). This composition gives a material with high compressive strength (above 120 MPa), tensile strength above 5 MPa with strain-hardening properties, and low permeability (Graybeal et al., 2020; Brühwiler, 2024). The low permeability, high ductility, and the crack distributing effect of the fibers significantly reduce the ingress of moisture and chloride.
The use of an overlay of UHPFRC for restoring old bridges has been implemented in a few European countries and the U.S., both for strengthening and repairing (Sritharan et al., 2018; Graybeal et al., 2020; Bertola et al., 2021b; Fehling and Thiemicke, 2023; Vítek et al., 2025). The Czech Republic has developed UHPFRC for 15 years leading multiple bridge applications (Vítek et al., 2025). The first application of UHPFRC for strengthening purposes on a bridge in the Czech Republic was made in 2022, yielding positive results. Before the full-scale application, several experiments were conducted. These included bond tests, bending tests of slabs with conventional concrete and UHPFRC, and technical tests to verify the ability to cast slopes. In Germany, UHPFRC has been applied to new roads bridges as a thin waterproofing layer, without need for asphalt (Fehling and Thiemicke, 2023). In addition, bridge deck rehabilitation has been conducted in Austria and the Netherlands (Fehling and Thiemicke, 2023).
Due to substantial research work over 25 years, Switzerland has the highest application rate worldwide, ranging above 400 applications of UHPFRC for bridge repair between 2004 and 2024 (Brühwiler, 2024). The reason for success is primarily that UHPFRC solutions are found to be cost-effective compared to traditional methods, as well as giving reduced material consumption, shorter construction periods, and improved durability leading to lower future maintenance costs (Brühwiler, 2024). In addition, the environmental impact has been found to be lower (Hajiesmaeili et al., 2019; Bertola et al., 2021b; Brühwiler, 2024). The national Swiss UHPFRC Model Standard (Brühwiler, 2023b) has been developed for the use of UHPFRC to rehabilitate concrete structures, to facilitate further use of this material exceeding that covered by the CEN standards for ready-mixed concrete.
The U.S. has also been investigating UHPFRC technology for bridges. The main application area has been field-cast connection between prefabricated reinforced concrete elements (Graybeal et al., 2020). However, there is a growing interest in using UHPFRC as a repair material as well, and the U.S. Federal Highway Administration (FHWA) has published the report Design and Construction of UHPC-Based Bridge Preservation and Repair Solutions (Haber et al., 2022). In the US, development of a non-proprietary UHPFRC for bridge deck rehabilitation has been presented, using locally available materials and non-patented products (Alvarez et al., 2024). Full-scale application of UHPFRC overlay was performed on a two-lane road bridge (Alvarez et al., 2024). Several tests were performed for quality assurance of the mix, including slump flow, compressive strength, flexural strength and pull-off test.
Some research has focused on improving material properties of UHPFRC on laboratory scale. Research has been carried out to develop low-shrinkage UHPCs for bridge deck overlay using calcined bauxite aggregate to reduce the autogenous shrinkage (Wei et al., 2023). Others have investigated the behavior of reinforced concrete elements strengthened with UHPFRC (Kadhim et al., 2023). Additionally, research has explored the fresh properties of UHPFRC to better suit use in bridge deck overlay, e.g., investigation into thixotropic properties (Du et al., 2023).
Despite the substantial backlog on bridge rehabilitation in Norway, the potential for using UHPFRC has been insufficiently investigated so far. This paper is a report on results from the first stage of a research project aimed at contributing to this shortcoming. The focus in this paper is to evaluate the suitability of UHPFRC made from local constituents in Norway, for applications related to the rehabilitation of deteriorated concrete bridges, and the potential for using standard facilities for ready-mixed concrete (RMC) to produce, transport, and pump UHPFRC in quantities appropriate for industrialized bridge rehabilitation. The term “Full-scale production” refers in this paper to industrial production of concrete at a conventional RMC plant, in quantities sufficient for demonstrating all equipment needed for the complete process from mixing to placing. The second and final phase of the project includes a pilot on full-scale rehabilitation of a deteriorated bridge. This project could represent a significant step toward full-scale industrial application of UHPFRC in Norway.
The adoption of industrial production and use of UHPFRC faces several challenges. One is the lack of successful pilot projects. Others include the absence of established standards and the lack of expertise within the concrete industry. Up to now, most production of UHPFRC in Norway has been on a laboratory scale (Fidjestol et al., 2012; Lande and Thorstensen, 2021). The present project is aimed at addressing the shortcomings mentioned above by involving key industrial actors, thereby contributing to the broader knowledge base and facilitating the adoption of UHPFRC in bridge rehabilitation at a national scale. This is partly based on the former research project (Dr.Techn Olav Olsen, 2020).
2 Preconditions for the use of UHPFRC for bridge deck repair
UHPFRC has material properties appropriate for bridge deck rehabilitation (Haber et al., 2022): e.g., low permeability and high resistance towards degradation mechanisms, high mechanical strength, high stiffness, and high bond strength towards substrates made of ordinary concrete. The use of UHPFRC to repair bridge decks is often performed by adding a thin layer of UHPFRC on the bridge deck (Haber et al., 2022), after thorough preparation of the substrate. In some cases, the overlay is solely intended to extend the lifespan of the bridge by providing a new and protective layer against chlorides and moisture; in other cases, the UHPFRC is also used to enhance the bearing capacity of the bridge. A thickness of 20–40 mm of UHPFRC is sufficient to protect the existing structure (Bertola et al., 2021b). For strengthening of the structural capacity, ordinary reinforcement is used combined with the UHPFRC. In such cases, at least 40 mm is required to ensure adequate cover for the additional reinforcement. Damaged concrete and corroded rebars in the original structure are removed before adding the UHPFRC. The Swiss UHPFRC Model Standard (Brühwiler, 2023b) specifies that the thickness should be over 25 mm for a protective layer and above 40 mm for reinforced UHPFRC.
To ensure high strength and low permeability (and thus improved durability against degradation mechanisms), the UHPFRC mix for bridge deck repair should be specifically designed. Both high compressive strength and extended durability are achieved through a high binder content, a low water-to-binder ratio, and the use of fine aggregates (Richard and Cheyrezy, 1995). The w/b-ratio of UHPFRC is normally in the range of 0.2–0.28 (Brühwiler, 2020; Haber et al., 2022) and Dmax no larger than 1 mm (Brühwiler, 2020). Some have also used larger Dmax of 4–5 mm for real-case applications (Alvarez et al., 2024; Vítek et al., 2025). Additionally, optimizing the granular composition with closely packed particles will further contribute to these properties (Richard and Cheyrezy, 1995). Achieving high tensile strength with strain-hardening behavior is also essential, as this enhances ultimate capacity and stiffness while preventing crack formation under service loads (Brühwiler, 2020). Ensuring strain-hardening behavior provides the structure with protection against water and chloride ingress (Brühwiler, 2020). This tensile behavior is mainly obtained by high steel fiber content, but also compact matrix and low w/b ratio (Bertola et al., 2021b). Straight high-strength steel fibers with a length (lf) between 12–13 mm and a diameter (df) of around 0.2 mm are frequently used in UHPFRC (Larsen and Thorstensen, 2020). To achieve significant strain-hardening behavior and high tensile strength in the range of 8–14 MPa, steel fibers with an aspect ratio (lf divided by df) above 65 and a content of at least 3 vol% (235 kg/m3) should be used (Brühwiler, 2020). Ensuring the required workability with high fiber content requires attention to the mix design (Brühwiler, 2020). Finally, it is important for bridge deck overlay that the UHPFRC have thixotropic consistency enabling casting with the necessary slope (Haber et al., 2022; Abellán-García et al., 2024).
Typical mass proportions of UHPFRC are as follows: 37% cementitious materials (including cement, microsilica, and sometimes other supplementary cementitious materials), 50% fine aggregates, 4.5% water, 2% admixtures and 6.5% steel fibers (Haber et al., 2022). Table 1 shows an overview of material properties for UHPFRC for rehabilitation of existing concrete structures, according to Brühwiler (Brühwiler, 2020).
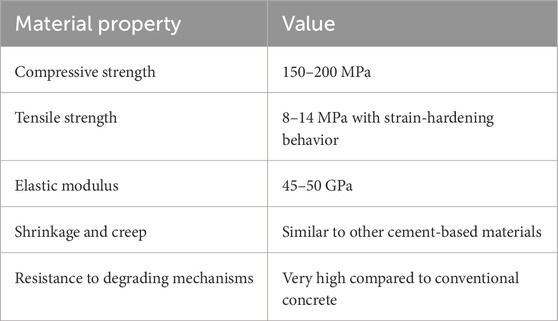
Table 1. Overview of material properties for UHPFRC for rehabilitation of existing concrete structures (Brühwiler, 2020).
For real-scale applications, quality assurance is required. The following is the argumentation for a suggested list of properties to test for quality assurance. UHPFRC is a fiber-reinforced material where fibers have a structural purpose. This is not covered by the current CEN standard for structural concrete, Eurocode 2 (European Committee for Standardization, 2004). The Norwegian Concrete Association has adopted regulations (publication number 38, NB38) for the use of fiber-reinforced concrete for structural purposes (The Norwegian Concrete Association, 2024b), acting as a national standard. The publication includes a list of tests to be performed, mostly referring to European standards (EN) for material testing. The Swiss UHPFRC Model Standard (Brühwiler, 2023b) also refers to several EN standards. However, additional test procedures for tensile properties are specifically developed for UHPFRC. This includes both a direct tensile test and a tensile bending test of 30 mm × 100 mm × 500 mm plates. NB38 utilizes the same standard for tensile properties as the fib model code (federation internationale du beton, 2013), EN 14651, measuring the flexural tensile strength of fiber-reinforced concrete. Based on the requirements for quality assurance in the Swiss UHPFRC model standard with some adjustments following NB38 and other requirements for Nordic conditions, a list on test procedures for fresh and hardened state properties is proposed (Table 2) for the use of UHPFRC in bridge rehabilitation. The table also provides relevant test standards.
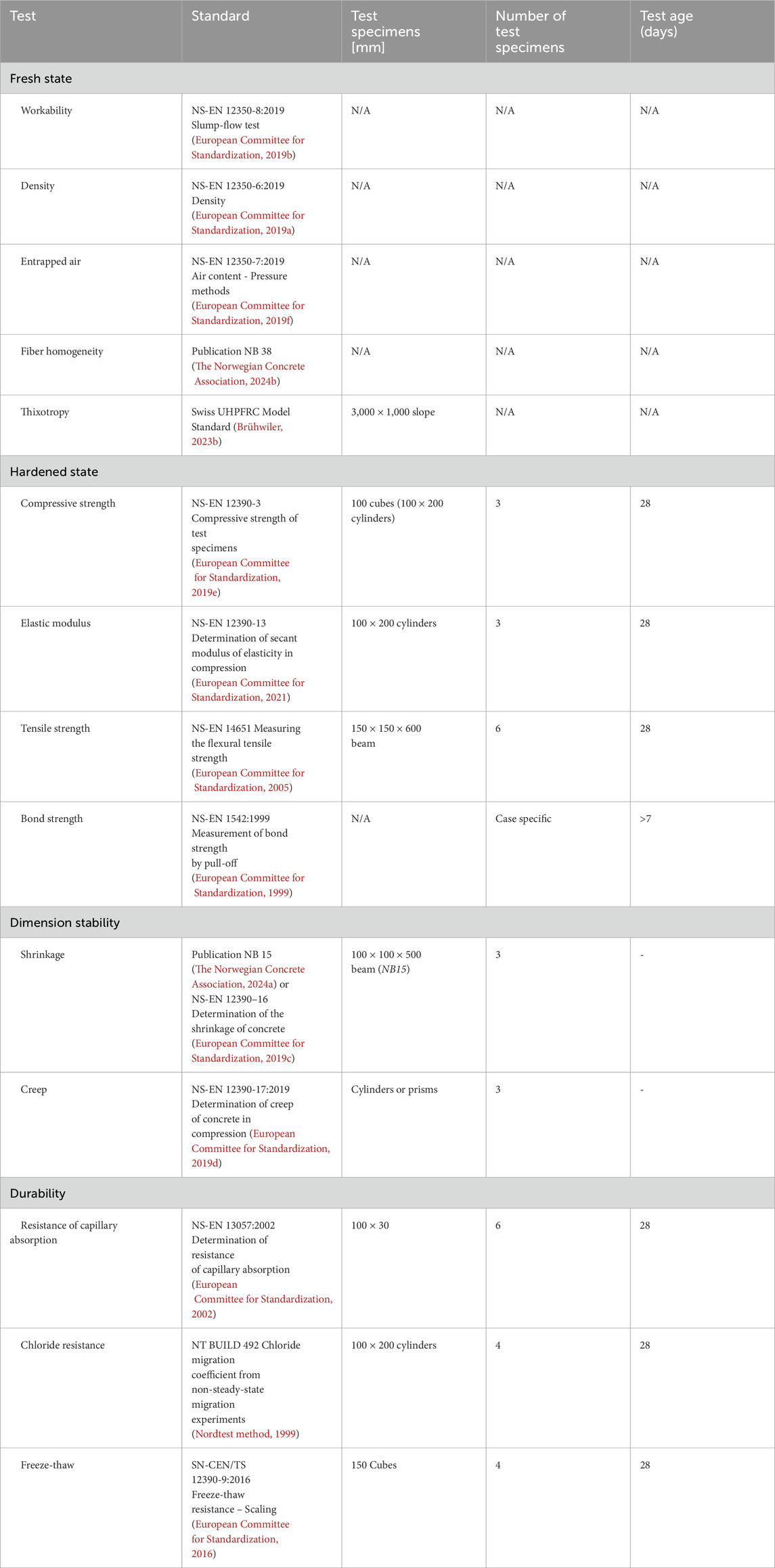
Table 2. Relevant tests for quality assurance for bridge rehabilitation with UHPFRC for Nordic conditions.
Fresh properties: The suggested list includes testing of workability, density, and entrapped air. In addition to these basic material tests, the Swiss UHPFRC Model Standard (Brühwiler, 2023b) includes a test on the suitability to be cast with a slope. This test is to cast an inclined slab with dimensions 3 m × 1 m. The suitability of the UHPFRC is verified by casting the UHPFRC similarly to the intended application, i.e., the surface should have similar roughness, and the inclination should be the same as for the intended application. This test is included in our suggested list in Table 2. Further included in the list, is a test of fiber homogeneity gathered from NB 38 (The Norwegian Concrete Association, 2024b). Three samples of 8 L fresh concrete are withdrawn from the concrete truck, one at the beginning of the pouring, one at the middle, and one at the end. The steel fibers in each sample are separated from the concrete, dried, and weighed. The fiber content in each sample must range from 0.8 to 1.2 times the intended fiber content, and the average of the three samples should be between 0.85 and 1.15 times the intended fiber content.
Hardened properties: In the hardened state, the suggested list for testing includes the basic material properties of compressive strength, elastic modulus, and tensile strength, all according to EN standards. EN 14651 is proposed as a test method for tensile strength, as this is referred to in both NB38 and the fib model code. An additional property that should be tested for bridge deck rehabilitation is bond properties between the new UHPFRC and the old conventional concrete layer. This can be done by pull-off test or direct tensile test (Vítek et al., 2025). Both tests are applied on elements made from a layer of UHPFRC cast on a substrate of conventional concrete. Failure should appear in the conventional concrete layer (Vítek et al., 2025). According to the Swiss UHPFRC Model Standard (Brühwiler, 2023b) pull-off test should be conducted following EN 1542:1999. This test is also the one included in Table 2. UHPFRC generally exhibits high resistance to degrading mechanisms compared to conventional concrete (e.g., chloride migration, carbonation, abrasion, and freeze-thaw) (Russell and Graybeal, 2013; Fehling and Thiemicke, 2023). However, the durability properties must be assessed in each individual case before the full-scale application of locally made UHPFRC. In the Swiss UHPFRC Model Standard (Brühwiler, 2023b) permeability is evaluated by capillary absorption tests performed according to EN 13057:2002. An alternative would be the NT BUILD 492 for accelerated chloride migration, as this is a dominant degrading mechanism for bridges in Norway. Freeze-thaw is also highly relevant, and the dominant test method is according to SN-CEN/TS 12390–9:2016. All three are included in the suggested list in Table 2. Norwegian version of the EN standards is given.
Some of these tests were conducted on the full-scale produced UHPFRC in this stage of the ongoing project, while more tests will be performed during the next.
3 Materials and methods
3.1 Materials
The UHPFRC used in this project was produced at an RMC plant in the Southern part of Norway. The mix design was developed for the same RMC plant in the former industrial research project New applications of UHPC (Dr.Techn Olav Olsen, 2020), now reused with some minor adjustments. All major constituents were available from the standard concrete production at the RMC plant: cement, silica fume, natural sand, shrinkage-reducing admixture (SRA), and retarder. Additionally, the following constituents were added: superplasticizer (SP) especially developed for UHPFRC, limestone filler, and micro steel fibers. UHPFRC is usually made with a maximum particle size of 1 mm (Brühwiler, 2020). Larger maximum particle size has been used in some studies (Spiesz and Hunger, 2017; Alvarez et al., 2024; Ouyang et al., 2024; Shi et al., 2024; Vítek et al., 2025). It was also successfully used for UHPC in the former industrial research project (Dr.Techn Olav Olsen, 2020), which the present project is closely related to. Information obtained from the technical data sheets for the constituents used in the production of UHPFRC is presented in Table 3.
The UHPC mix composition logged from the quality system of the full-scale production facility is shown in Table 4. The water-to-binder (w/b) ratio was 0.22, where the binders included cement and microsilica (k-value = 1). The fiber content was varied to test fresh-state consistency, using 0 vol%, approximately 2 vol% (152 kg/m3) and 3 vol% (225 kg/m3). A series of specimens were cast without steel fibers for testing accelerated chloride migration, where the presence of steel fibers would compromise measurements.
Properties measured on the specimens produced in the present project with industrial full-scale mixing were compared to values obtained in a former project where a similar UHPFRC was produced in the lab. The mix designs of the lab-scale produced UHPFRC are presented in Table 5. The results were also compared to a previous full-scale production of UHPFRC at the same RMC plant (Lande et al., 2024). The mix design from this full-scale production is also included in Table 4. The mix designs are highly comparable, though some small variations occur: Some constituents have different origins, and admixtures SRA and retarder were not applied in the lab mixing.
3.2 UHPC production
A total of 2 cubic meters were mixed in the RMC plant, using a 4 m3 twin-shaft paddle mixer. Limestone filler was added manually during mixing, which was time-consuming. Finally, the UHPC was poured into a truck for transportation. A short transportation was performed internally at the production site. A combined pumper and mixer truck (PuMi) was used to transport the UHPC, to sequentially mix the fibers in the UHPC, and finally to deliver the UHPFRC through pumping. The steel fibers were added to the mix in two steps: first about 2 vol% (152 kg/m3) before the flow spread was measured, then increased to about 3 vol% (225 kg/m3) before the flow spread was measured again.
The ambient weather was sunny with temperatures around 20°C. UHPFRC generally requires a longer mixing time than regular concrete, often quantified to a multiplication factor of 7–8 (Lande et al., 2024). Due to the manual addition of limestone filler and several sequences of adding steel fibers, the mixing time was extended further. This resulted in the temperature increase in the UHPFRC. The temperature was logged several times throughout the process, and it was noted that the fresh properties degraded towards less flowability and more stickiness.
As a last step, the UHPFRC was cast through pumping. Around 60% of the ready-mixed concrete delivered in Norway is placed by pumping (Mortensvik and Thorstensen, 2025). Hence, regarding the industrial focus of this project, it was decided to test the ability of the UHPFRC to be placed by pumping in equipment used for traditional concrete. The pump part of the PuMi was used for this purpose. Clogging of the pipeline and hoses is a frequent bottleneck when pumping concrete, which is both time- and cost-consuming (Mortensvik and Thorstensen, 2025). The skilled PuMi operator evaluated the UHPFRC as being too stiff and sticky for pumping, after the long processing time of fiber addition and measuring. More water and SP were added until an adequate consistency was obtained, as evaluated by the operator. Figure 1 shows the flow chart of the production process.
3.3 Material property testing
An overview of the tests conducted in this part of the research project is shown in Table 6, including the number of specimens tested in parallel, curing, and test age. All tests are in accordance with the suggested list for quality assurance (QA) (Table 2). However, the complete QA is not performed in this stage of the project. The remaining will be performed as part of the ongoing final stage of the project, which will include a full-scale bridge deck repair.
Fresh properties of the RMC production were tested through slump flow according to NS-EN 12350-8:2019 (European Committee for Standardization, 2019b), for each of the three levels of fiber content 0, 2, and 3 vol% (Figure 2). The slump flow was performed by filling a cone with a height of 300 mm and a diameter of 100 mm at the top and 200 mm at the base. The result is the average diameters of the largest flow spread (d1) and the flow spread perpendicular to d1 (d2).
Figure 3 shows an illustration of the strength-based properties tested. Compressive strength was measured according to NS-EN 12390-3 (European Committee for Standardization, 2019e), using 100 mm cubes and on 100 × 200 mm cylinders (Figures 3a,b). Cylinders were tested to investigate the correlation between tests performed on cubes and cylinders. This correlation is well known for standard concrete, but not correspondingly known for locally produced UHPFRC. 100 mm cubes were tested at 1, 7, 14, and 28 days after casting. Three test specimens were tested for each test age. E-modulus was tested according to NS-EN 12390-13 on 100 × 200 mm cylinders (European Committee for Standardization, 2021). Three test specimens were tested 28 days after casting, according to the recommendations in Table 2. These results from the full-scale test were also compared to results from the lab-scale tests.
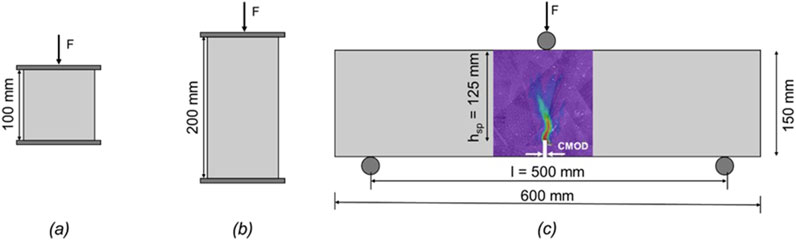
Figure 3. Strength-based properties, (a) compressive strength of cubes, (b) E-modulus and compressive strength of cylinders, and (c) residual flexural tensile strength of beams.
Flexural tensile strength was tested using NS-EN 14651 for fiber-reinforced concrete (European Committee for Standardization, 2005). Six notched UHPFRC beams with about 3 vol% of steel fibers from the RMC production and three from the lab-scale production were tested. The beams were tested in three-point bending with a span length of 500 mm (Figure 3c). The dimensions of the beams were 150 mm × 150 mm × 600 mm. A 25 mm notch was cut centrally in the lower edge of the beam, giving the height 125 mm of the beam over the notch (hsp). The specimens were rotated 90° around the longitudinal axis before the notch was cut, to obtain smooth surfaces for application of load and to prevent the effect of fiber segregation. The force was applied at a constant rate of 0.6 mm/min. The test procedure requires force and crack mouth opening displacements (CMODs) to be registered during the test. A Digital Image Correlation (DIC) system was applied to identify CMOD values. This was done through a virtual extensometer crossing the notch tip in the DIC software (Vic3D). The flexural tensile strength was calculated corresponding to CMODs of 0.05 mm, 0.5 mm, 1.5 mm, 2.5 mm, and 3.5 mm. CMOD equal to 0.05 mm was used to determine the flexural strength at the limit of proportionality (LOP) (fct,L). The remaining CMODs were used to calculate the residual tensile strengths: fR1, fR2, fR3 and fR4. The flexural strength (fRj) for the various CMODs was calculated using the formula in NS-EN 14651 (Equation 1):
where Fj is the load corresponding to the different CMODs (j = 1, 2, 3, and 4) (Newton), l is the span length (mm), b is the width, and hsp is the depth of the notched beam (mm). Flexural strength for maximum load was also calculated.
The test procedure in Annex A of Publication 15 (NB15) by the Norwegian Concrete Association (The Norwegian Concrete Association, 2024a) was used to evaluate the shrinkage. The test measures total shrinkage, i.e., the sum of drying and autogenous shrinkage. Figure 4 shows the test rig. The test specimens were 100 mm × 100 mm × 500 mm beams with cast-in-place steel pegs at both ends. The test specimens were stored in laboratory conditions (20°C and 50%–60% RH) with a minimum of 25 mm between the test beams. The procedure was to first zero a dial gauge towards a reference steel rod. After zeroing the dial gauge, the length of the UHPFRC specimens was measured, followed by a re-measurement of the steel rod to control that the measurement was valid. At least three repeated measurements were performed for each specimen before recording the average value. Measurements were first conducted after 24 h and subsequently used as the reference for corresponding measurements conducted 7 days, 14 days, 28 days, 56 days, 91, and 270 days after casting. The shrinkage was calculated in ‰ of the reference length (24 h). Average values from three beams were used to represent the shrinkage. Long-term measurements will be conducted after 360 days.
The chloride penetration resistance was evaluated using the Nordtest method NT BUILD 492 chloride migration coefficient from non-steady-state migration experiments (Nordtest method, 1999). This accelerated test method is commonly applied for UHPFRC to assess chloride resistance (Li et al., 2020). Cylindrical UHPC test specimens (d = 100 mm and t = 50 mm) without steel fibers were sawn centrically from cylindrical specimens 100 mm × 200 mm. The test utilizes electric potential to accelerate the chloride migration, using the initial current to manage the exposure time. The inclusion of electric conductive fibers in the specimen might corrupt the procedure. Following the standard, each specimen was preconditioned. Subsequently, each specimen was placed in a rubber sleeve and submerged in a catholyte (NaCl solution) in one end and an anolyte (NaOH solution) in the other (Figure 5). The theory is that chloride ions from the catholyte solution migrate into the UHPC specimen, accelerated by the applied electric potential. After exposure, each specimen was split in half to access the cross-sections. Each cross-section was sprayed with silver nitrate to detect the chloride penetration depth. This depth was measured every 10 mm along the surface (Figure 5). The non-steady-state migration coefficient (Dnssm, × 10−12 m2/s) was calculated using the following formula (Equation 2):
where T is the average of the initial and final temperature in the anolyte solution (°C), L is the thickness of the test specimen (mm), U is the applied voltage (V), t is the test duration (hours), and xd is the average penetration depth (mm). The resistance against chloride migration was compared to three classes of conventional concrete, C20/25, C30/37, and C45/55. Four samples of each concrete type were tested.
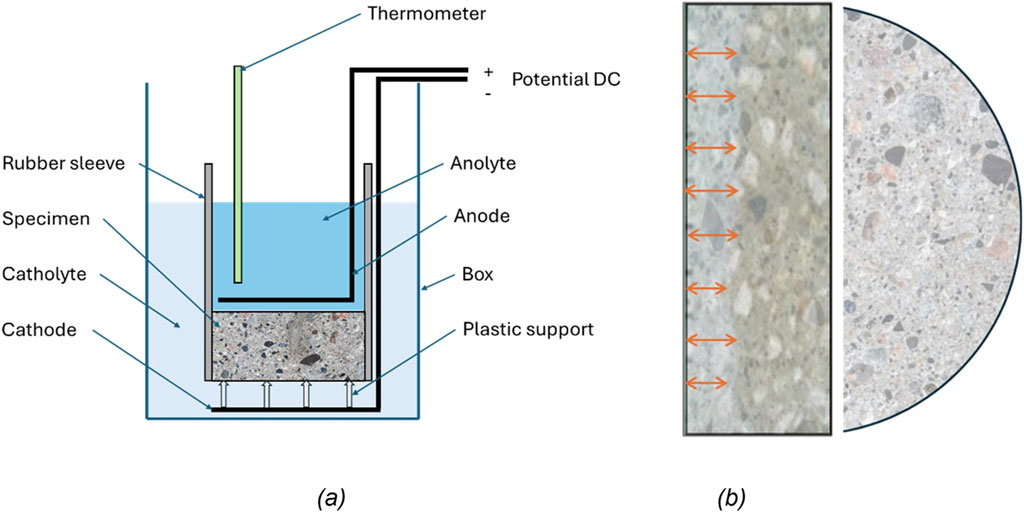
Figure 5. Chloride resistance according to NT BUILD 492, (a) arrangement of the test setup and (b) measurement of chloride penetration depth on the cross section of the split test specimen.
4 Results and discussion
4.1 Material properties
The inclusion of steel fibers effectively prevents and delays the initiation of microcracks in the concrete matrix (Zhang et al., 2023). This leads to improved crack control and crack distribution, resistance to crack growth, and enhanced ductility and strength properties. UHPFRC, however, differs in several aspects from conventional steel-fiber-reinforced concrete. This includes a denser, high-strength matrix, the use of micro steel fibers, and a higher fiber content. Considering the higher number of micro steel fibers compared to standard steel fibers at the same volume proportion, UHPFRC can give further improvements in mechanical and durability properties. In the following, the effect of steel fibers on UHPFRC for bridge deck rehabilitation is presented and discussed, comparing specimens cast during full-scale RMC production and those produced at laboratory scale.
4.1.1 Fresh properties
A large slump flow of 900 mm was achieved for the initial UHPC without steel fibers included in the mix (Figure 6). This was reduced to 740 mm with the addition of around 2 vol% (152 kg/m3) steel fibers. At approximately 3 vol% (225 kg/m3), the UHPFRC became very viscous - not applicable for pumping. Hence, the mix was adjusted with SP and water to obtain fresh properties applicable for pumping. The mix remained viscous but was considered satisfactory for pumping. An overview of the slump flow is provided in Figure 6, showing the decrease in flowability as the fiber content was increased. The decrease in flowability as a function of an increase in steel fiber content is found in several papers (Yu et al., 2014; Wu et al., 2016; Le Hoang and Fehling, 2017; Meng and Khayat, 2018; Yang et al., 2021). This trend has also been observed for other types of concrete containing micro steel fibers (Wang et al., 2025). In a review paper where (Zhou et al., 2021) refer to 184 scientific papers, three mechanisms are identified as main contributors to the loss of workability following a higher fiber content for UHPFRC. One is that the increased surface area of the elongated fiber shapes binds more water. It is commonly known that any surface physically binds a thin layer of water–often quantified to the thickness of two to three molecules. Given the micro dimensions of the fibers used for UHPFRC, the number of fibers and the accumulated surface area are consequently high. This surface area also increases the requirement for cement paste, which is given as a second explanation in the review paper. All particle surfaces should be covered with paste, and a surplus volume of paste is needed to “lift” each particle from the others to reduce the internal friction in the mix. Thus, when adding more and more fibers sequentially without compensating with more paste, the internal friction between particles increases, resulting in a reduced slump flow. A third explanation stated in the review paper is the risk of mutual fiber winding associated with the dispersion and distribution of fibers. Interlocking between fibers and aggregate particles further increases the risk of reduced workability. The elongated fibers have the potential to be packed nearly as dense as the less elongated aggregate particles. However, if stacked randomly, the fibers might interfere with aggregate particles, preventing dense packing and increasing internal friction. Balancing high fiber content with correspondingly high workability is recommended to secure dense packing. When, in this investigation, the fiber content was increased without compensating for the need for more cement paste, the above-mentioned explanatory mechanisms from the review paper act as good explanations for the loss of workability following the increase of fiber content. Wang et al. found that the workability of geopolymer concrete decreased with an increasing content of micro steel fibers (Wang et al., 2025). For this type of concrete, the reduction in workability is explained by the steel fibers having an elongated shape, poor filling ability, and increased surface area compared to the aggregates, which leads to poorer particle packing. Furthermore, increased internal friction due to interlocking between fibers and aggregate particles also contributes to reduced slump flow. Similarly (Zhang et al., 2024), observed increased viscosity for geopolymer concrete containing 2 vol% of micro steel fibers, caused by reduced packing of particles and higher friction between the steel fibers. Sun et al. studied Polyvinyl alcohol (PVA) fibers in modified cement-based materials finding that higher content of fibers reduced the slump flow and increased thixotropy of the mix (Sun et al., 2024). However, concrete with PVA fibers is affected by additional mechanisms that reduce the slump flow (Sun et al., 2024).
Relatively large aggregate particles (Dmax 8 mm) were used in this UHPFRC mix, which may have contributed to the reduced slump flow caused by the increasing fiber content. It was found that the spread flow was reduced from 900 mm to 550 mm, as the fiber content increased from 0 vol% to around 3 vol% (225 kg/m3), as shown in Figure 6. Normally, aggregates with a Dmax under 1 mm are used in UHPFRC (Brühwiler, 2020), allowing the fibers to distribute more freely. Le Hoang and Fehling used a fine-grained UHPFRC (Dmax 0.5 mm) and found that an increase in steel fiber content from 0 vol% to 1.5 vol% and 3 vol% reduced the slump flow (Le Hoang and Fehling, 2017). However, the reduction was considerably lower (17% reduction at 3 vol%) compared to the findings in this study with Dmax 8 mm (39% reduction at 3 vol%).
The final aspect of the fresh properties, according to the suggested list for QA in Table 2, regards the casting process of UHPFRC. Bridge decks are commonly cast with a surface slope. To attain this, the fresh UHPFRC must have thixotropic properties (Haber et al., 2022; Abellán-García et al., 2024). In this case, we achieved a castable and self-leveling mix when energy was added to the UHPFRC. The rheological properties can be adjusted to achieve a thixotropic behavior, e.g., with viscosity-modifying admixtures.
4.1.2 Strength-based properties
Figure 7 shows the compressive strength of the UHPFRC produced at the RMC plant, both as time series and for different test series. Cubes containing around 3 vol% (225 kg/m3) of steel fibers were tested at 1, 7, 14, and 28 days of curing in water at 20°C. A compressive strength of 42 MPa was obtained after 1 day of curing, and 147 MPa after 14 days. The 28-day reference strength was found to be 170 MPa. This is well above the advised level of 120 MPa stated by (Graybeal et al., 2020), and satisfies the requirement of 150–200 MPa advised by Brühwiler (Brühwiler, 2020), for UHPFRC to enhance existing structures (Table 1). These results demonstrate that it is possible to produce large quantities of UHPFRC using ordinary industrial equipment for conventional ready-mixed concrete, based on a common fraction of natural sand—and that the resulting material satisfies requirements for strength given by authoritative sources suitable e.g., for repair of bridges. Also, the restriction of Dmax < 1 mm normally used for UHPFRC, can be bypassed to achieve satisfactory compressive strength if the aggregate has sufficient strength. This might also both favor the economy and help reduce technical challenges like shrinkage.
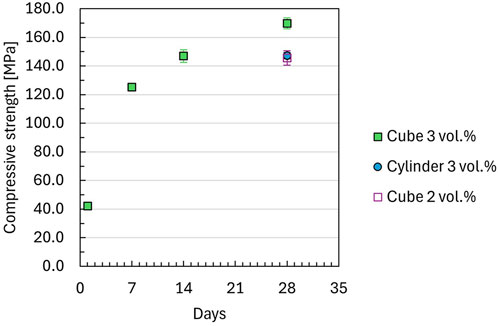
Figure 7. Average compressive strength of UHPFRC produced at RMC-plant. Error bars show standard deviation.
Another evaluation was to determine the ratio between compressive strength measured on cubes vs cylinders. The conversion factor was determined at 0.87, well corresponding to the value 0.84–0.86 that is stated in Eurocode 2 for standard high-strength concrete (C80/95 and C90/105).
A third evaluation was to investigate whether the results achieved in the full-scale production are reproducible on lab-scale. This is important knowledge, as the utilization of industrial equipment requires a stop in ordinary production—which is both expensive and disturbing to normal industrial production. Remains of UHPFRC might also require extra cleaning procedures—further increasing the negative consequences for normal production.
The results on compressive strength from the full-scale production at the RMC plant (Figure 8) are compared to those obtained at laboratory facilities with the mix design in Table 5, as well as those from a previous full-scale test made at the same RMC plant (Table 4) presented in (Lande et al., 2024). As shown in Figure 8, the results from both full-scale productions are nearly identical (for about 2 vol%). Although the mix design was not exactly the same (Tables 4 and 5), it involved the same w/b ratio, steel fiber content, Dmax of aggregate, and similar binder content. This indicates that repeatability is good even with the variations occurring in industrial production systems, e.g., in constituents stemming from natural ores. Similar results were obtained when comparing samples produced at lab facilities to those produced at the RMC plant for the same fiber content. Variations are limited to 10%. These results are consistent with previous results (Lande et al., 2024).
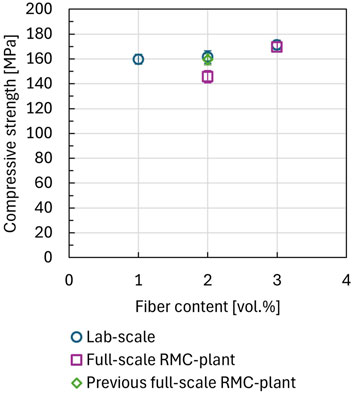
Figure 8. Average compressive strength of UHPFRC at 28 days produced at RMC-plant compared to similar mix at lab-scale and previous full-scale production of UHPFRC at RMC-plant. Error bars show standard deviation.
Fibers have been found to increase the compressive strength of different types of concrete (Sun et al., 2024; Zhang et al., 2024; Wang et al., 2025). The series made from the RMC production demonstrates an increase of 17% in compressive strength when the fiber content is increased from 2 vol% (152 kg/m3) to 3 vol% (225 kg/m3). The impact—and whether at all there is an impact—of fibers on compressive strength, is highly disputed in the literature (Larsen and Thorstensen, 2020). The impact on compressive strength from adding steel fibers varies from a considerable increase (Wu et al., 2016; Ibrahim et al., 2017) to a negligible effect (Le Hoang and Fehling, 2017). Regarding the span in fiber content from 2 to 3 vol%, the impact on compressive strength typically seems to be evaluated as lower than 10% in most papers (Meng and Khayat, 2016; Wu et al., 2016; Pourbaba et al., 2018). We consider two possible sources for the deviations between the results from the RMC production and those found in the literature: One is the limited number of test specimens. Concrete is a highly anisotropic material, known for its high span in test result values. Only three specimens were tested for RMC production, which may have included random variations, causing a higher average value than what is representative of the population. The second reason might be that the large amount of micro steel fibers was not homogeneously distributed. Evenly distribution of microfibers in the mix of fine particle materials is challenging, as discussed above in the section concerning the size of Dmax. The small portion of UHPFRC taken for the three cubes may have originated from a partition of the 2 m3 mix having a high concentration of fibers. This increases the risk that the small number of test specimens is not representative of the total population. While the impact was found to be 17% on the RMC-produced mix, it was only 6% on the lab-scale mix - where the number of parallel tests was 12. Thus, the results from the lab-scale mix might be more representative of the impact of fibers on compressive strength than those from the RMC mix. This is also in harmony with the results from a majority of the literature, as discussed above.
The observed increase in compressive strength can be explained by the ability of the steel fibers to bridge cracks delaying the formation and propagation of microcracks (Yoo et al., 2014; Ibrahim et al., 2017). Addition of steel fiber content above 3 vol% has been found not to cause a corresponding increase in compressive strength. It might even cause an adverse effect (Yoo et al., 2014; Meng and Khayat, 2018). This can be explained by fiber agglomerations causing entrapped air (Meng and Khayat, 2018; Larsen and Thorstensen, 2020) and inhomogeneous fiber distribution (Yoo et al., 2014). Yang et al. found that an increase in steel fiber content entailed large-sized pores and internal defects, which in turn negatively impacted the mechanical properties of UHPFRC (Yang et al., 2021). Fiber agglomeration has been documented when high volumes (3 vol%) of steel fibers are added (Le Hoang and Fehling, 2017; Meng and Khayat, 2018). Even in fine-grained UHPFRC mixes with 3 vol% of steel fibers, fiber agglomerations have been documented (Le Hoang and Fehling, 2017). For coarser-grained concrete types containing micro steel fibers, fiber agglomeration resulting in non-uniformed dispersion of fibers was observed for 2 vol% fiber content, causing reduced strength (Zhang et al., 2024).
Figure 9 shows the effect of steel fiber content on the elastic modulus of lab-scaled produced UHPFRC. At 3 vol% the UHPFRC produced at RMC plant is compared to specimens cast in the lab. It is indicated that the steel fiber content leads to a small increase in the E-modulus. However, the increase was negligible (limited to 2.4%). This aligns with the results by (Le Hoang and Fehling, 2017), who found only a minor effect. Some have concluded that fiber content increases elastic modulus, varying from less than 5% to around 12% (Hassan et al., 2012; Yoo et al., 2013; Yang et al., 2021).
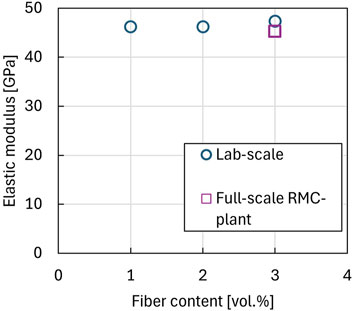
Figure 9. Average elastic modulus UHPFRC produced at RMC-plant compared to similar mix at lab-scale.
Figure 10 shows (a) the load-CMOD and (b) load-deflection curves for the three-point bending tests for six UHPFRC beams with about 3 vol% (225 kg/m3) of steel fibers, produced at the RMC plant. A similar behavior was obtained for all six beams.
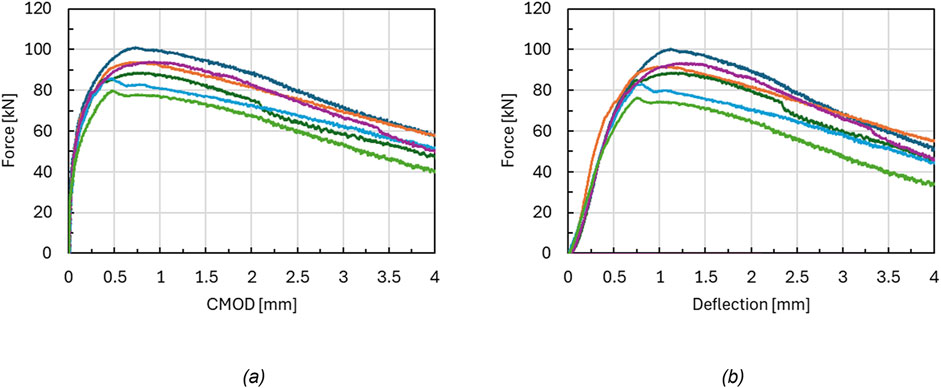
Figure 10. Three-point bending test results for UHPFRC produced at RMC-plant with 3 vol% of steel fibers, (a) load-CMOD relation, and (b) load-deflection. CMOD and deflection values are obtained from DIC analysis.
The load-deflection behavior of steel-fiber-reinforced concrete can be divided into two stages (Zhang et al., 2023): 1) a linear elastic stage and 2) an inelastic stage. In stage 1, the matrix carries most of the load, while the contribution from the steel fibers is small. In stage 2, the steel fibers become activated and carry most of the load as cracks are formed. The second stage can be divided into three phases: transition, deflection hardening, and post-peak. During the transition phase an evident drop in load is typically observed in steel fiber-reinforced concrete, indicating the transfer of the tensile stresses from concrete to the steel fibers due to the formation of a crack. This drop was less evident for UHPFRC beams (Figure 10b) due to the high content of steel fibers leading to the formation of multiple microcracks. In the deflection phase, the deflection increases with increased load until the maximum load is reached. In this phase, several tightly spaced microcracks are formed. These microcracks were observed for all UHPFRC beams using the DIC system. After the maximum load was reached, the post-peak stage began, representing the development of the microcracks into macrocracks, leading to a decrease in load-carrying capacity. This is in line with the description by (Zhang et al., 2023). In this region, the steel fibers are pulled out of the matrix. Due to the high content of steel fibers, the beams were not fully split into two parts at the end of the test.
The stages of the load-CMOD curves for fiber-reinforced concrete can be divided into three (Zhang et al., 2023): 1) linear elastic stage, 2) hardening stage, and 3) post-softening phase. During the elastic stage, the CMOD increases with the load. The strength is related to the concrete matrix. During stages 2 and 3, the strength is related to the steel fibers. Stages 2 and 3 represent the initiation and propagation of microcracks in the hardening stage and propagation of microcracks into macrocracks in the softening stage, similarly as for the load-deflection curve. The UHFPRC beams in this study undergo these three stages. The elastic stage is denoted by the limit of proportionality (LOP) in EN 14651 and is measured at a CMOD of 0.05 mm. At CMOD 0.05 mm the average load for all six beams was about 40 kN. After the elastic stage, the load and CMOD increase to a maximum load between 80 and 100 kN in the hardening stage. Following the maximum load, the load decreases in the softening stage as the cracks widen into macrocracks. The variations in maximum load and behavior are within a normal span for fiber-reinforced concrete. High scatter is common, as the strength is related to the orientation and distribution of the fibers, which again is a result of the casting and compaction process. The resulting capacity is a function of fiber orientation and distribution across the notch.
Based on the load-CMOD curves, residual flexural tensile strength values were calculated from Equation 1. This serves as a basis for structural design calculations of steel fiber-reinforced concrete, according to the fib model code and the new Eurocode 2 Annex L. In the fib model code 2020 UHPFRC is included (di Prisco, 2023). It is discussed whether this test method is suitable for UHPFRC (López et al., 2016), as the opening does not appear in this material as one single crack. Rather, several cracks emerge around the notch. The notch influences the behavior of the beam by forcing cracks to initiate and propagate at a specific point on the beam (Walraven, 2009), not at the weakest point (López et al., 2016). This might increase the results compared to un-notched beams, as it makes the deflection hardening phase due to multiple cracking less pronounced (Walraven, 2009). This behavior can also be seen in Figure 10b. The Swiss UHPFRC Model Standard (Brühwiler, 2023b) includes specified calculation methods for composite structures of standard reinforced concrete and UHPFRC. In this design code, the procedure from EN 14651 is not followed. Rather, a four-point bending test of a thin plate (500 mm × 100 mm × 30 mm) and a uniaxial tension test are required for quality assurance of the mix. However, this procedure is also argued. Using thin elements affects the orientation of the fibers (Bertola et al., 2021b). The fibers close to the formwork will be forced more parallel to the formwork, a mechanism often referred to as the wall effect (Islam et al., 2022). Thus, for thinner elements, fiber alignment is higher than at larger dimensions. However, the thinner elements might be a good representation for bridge deck repair. Uniaxial tensile testing is preferable to describe the tensile properties of fiber-reinforced concrete but is often challenging to perform in industrial cases (Walraven, 2009).
Figure 11 shows the results of the residual flexural tensile strength for the UHPFRC produced at the RMC plant compared to those made in the laboratory. Both had approximately 3 vol% of steel fibers. Similar results are obtained for both series, including corresponding standard deviations. This corresponds with previous research on comparing lab to full-scale production (Lande et al., 2024). The flexural tensile strength is mainly related to steel fibers. Hence, distribution and orientation are important factors.
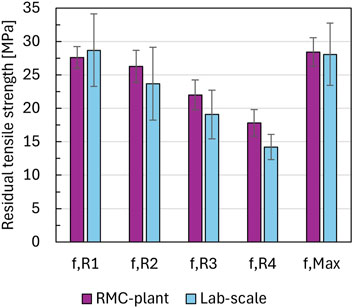
Figure 11. Residual flexural tensile strength for UHPFRC produced at RMC-plant with 3 vol% of steel fibers compared to lab-scale produced specimens. Error bars show standard deviation.
According to NB38, characteristic residual strengths fR,1k and fR,3k shall be determined. The characteristic values of fR1k and fR3k for the full-scale produced UHPFRC were determined to be 24 MPa and 18, respectively. The results for fR1k corresponded well to those obtained by Vítek et al. (2025) using the same standard and similar content of steel fibers. The characteristic residual strength fR,1k is used to determine the strength class. The highest strength class in Eurocode 2 Annex L is 8 MPa, while in the fib model code 2020, it is 14 MPa (Di Prisco, 2023). The characteristic strength of the full-scale production was determined to be 24 MPa, far above the range of both the fib model code and Eurocode 2 Annex L. The ratio fRk3/fRk1 is used to determine the ductility class (federation internationale du beton, 2013; The Norwegian Concrete Association, 2024b). For the full-scale production, the ductility class fRk3/fRk1 was determined to be 0.73. This gives class “b” (0.7 ≤ fRk3/fRk1 ≤ 0.9) (federation internationale du beton, 2013; The Norwegian Concrete Association, 2024b).
Figure 12 shows the maximum flexural strength calculated using Equation 1 and the maximum load for different fiber contents (1, 2, and 3 vol%). 3 vol% is calculated for both full-scale and laboratory-scale and shows equal results. The results show that the steel fibers have a considerable impact on the flexural strength properties, correlating flexural strength positively to fiber content. These results are in line with previous studies on the flexural strength of UHPFRC (Yoo et al., 2014; Abbas et al., 2015; Yoo et al., 2017; Meng and Khayat, 2018; Li et al., 2023). Some found an increase in flexural strength up to 4 vol% (Yoo et al., 2014) and even 6 vol% of steel fibers (Abbas et al., 2015). The increase in flexural strength is explained by the probability of more steel fibers crossing each crack, resulting in an increased bonding area between the UHPC matrix and the steel fibers (Yoo et al., 2017). Due to the higher bond area, increased forces are required to pull out the fibers (Yoo et al., 2017). Others have found an adverse effect when more than 3 vol% is added (Meng and Khayat, 2018). Others find the border when more than 4 vol% are added (Li et al., 2023). The negative effect is due to the agglomeration of fibers, resulting in uneven distribution and entrapped air. For real-scale applications are at least 3 vol% of micro steel fibers commonly applied (Bertola et al., 2021a; Bertola et al., 2021b; El Jisr et al., 2024; Vítek et al., 2025), however, even fiber content above 9 vol% have been applied using a fine-grained UHPFRC with Dmax 0.5 mm (Bertola et al., 2021b). Although the cost and environmental impact per cubic meter of UHPFRC is highly influenced by the content of steel fibers (Stengel and Schießl, 2014; Lande and Thorstensen, 2023), high contents are of high importance for performance. For bridge deck rehabilitation above 3 vol% is recommended (Brühwiler, 2020; Haber et al., 2022). The reason is to achieve strain-hardening behavior, to improve ultimate capacity and stiffness, to prevent crack formation under service loads, to protect against water and chloride ingress, and to reduce the anisotropic fiber orientation (Brühwiler, 2020).
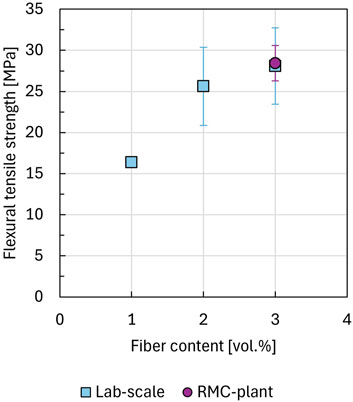
Figure 12. Average maximum flexural tensile strength for six UHPFRC produced at RMC-plant and three specimens at lab-scale for each vol% of steel fibers. Error bars show standard deviation.
4.1.3 Shrinkage
Shrinkage is an important property regarding UHPFRC for bridge deck rehabilitation. When a thin layer of fresh UHPFRC is cast on top of a substrate of old concrete, any shrinkage might cause the overlay to crack. Tensile forces due to shrinkage will lead to microcracks in the concrete (Wu et al., 2019), opening for the ingress of degrading agents like chloride, thus compromising the ability of the UHPFRC to improve the durability of the bridge. Even if the high fiber content successfully distributes cracks to a size where chloride penetration is not a problem, shrinkage might be detrimental. The shrinkage of the UHPFRC layer will cause movement relative to the substrate, thus reducing the bonding strength. This might corrupt the structural integrity of the repair.
Autogenous shrinkage in concrete is mainly caused by the volume reduction during the cement hydration while drying shrinkage is caused by external drying. Both happen in the matrix and are caused by the forces induced by the water meniscus in partly filled micropores. UHPC is known for having high autogenous shrinkage (Xie et al., 2018; Wu et al., 2019; Wei et al., 2023), explained by the high content of matrix and low w/b-ratio (Wei et al., 2023), as well as lack of the coarse aggregate which is not exposed to shrinkage. To counteract the shrinkage, an SRA admixture was applied according to the values given in Table 4. Steel fibers also contribute to decreasing autogenous and drying shrinkage (Wu et al., 2019; Zhang et al., 2023).
The total shrinkage was measured on three parallel specimens, with values presented in Figure 13. The values obtained are similar to conventional concrete (Mortensvik and Thorstensen, 2024). For this level of shrinkage, it is possible to limit the crack growth to levels that do not compromise durability. However, even this shrinkage might challenge bond strength. The potential reduction in bond strength in full-scale applications will be evaluated during the next step of this research project.
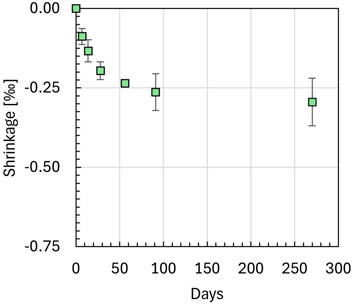
Figure 13. Total shrinkage of UHPFRC produced at RMC-plant with SRA. Average results of three prisms. Error bars show standard deviation.
4.1.4 Durability properties
Chloride-induced reinforcement corrosion is a major degrading process on bridges in Norway (Kvamstad et al., 2024), caused both by the marine environment and the use of de-icing salt during winter. UHPFRC is known from the literature for its ability to resist chloride migration.
In Figure 14, chloride ingress results from the RMC-mixed UHPC are shown in comparison to three classes of conventional concrete. The Dnssm-factor expresses the chloride ion diffusion coefficient in an accelerated test according to the NT BUILD 492. A low Dnssm-value indicates high resistance towards chloride migration, consequently indicating high durability in a chloride-rich environment. The UHPFRC in this study achieved Dnssm value of 0.3 × 10−12 m2/s. This is considerably higher resistance than the conventional concrete types C20/25, C30/37, and C45/55, which exhibited values of 17.2, 7.1 and 6.2 × 10−12 m2/s, respectively. The concrete used for the construction of bridges in Norway is close to the Eurocode 2 class C45/55 (The Norwegian Public Roads Administration, 2015). The conventional concrete types were produced according to industrial mix designs and tested at the laboratory using the same test setup. The results, shown in Figure 14, indicate that the ability of the RMC-produced UHPFRC with Dmax = 8 mm to resist chloride migration is at least 10 times that of the concrete normally used for bridges. In an earlier project (Thorstensen et al., 2016) using the simulation software Life365 and the Dnssm-factor to model the durability of concrete in chloride-rich environments, UHPFRC was evaluated to have durability of more than 300 years–making this degradation process irrelevant. According to (Li et al., 2020), the chloride ion diffusion coefficient of UHPFRC ranges from 0.2 × 10−13 to 4.1 × 10−13 m2/s. The UHPFRC in this study performs within this range (3.1 × 10−13 m2/s). The values obtained in this study were also similar to those of Lliso-Ferrando et al. (2023), using a similar test setup.
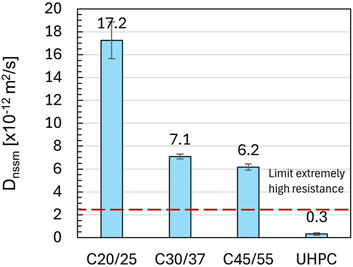
Figure 14. Dnssm (non-steady-state migration coefficient) for chloride resistance of UHPFRC produced at RMC-plant compared to three types of normal concrete. Four cylinders were used. Error bars show standard deviation.
According to Taffese and Espinosa-Leal (2022), UHPFRC can be classified in the category Extremely high resistance (Dnssm <2.5) based on the Dnssm value. Ordinary high-quality concrete classes C45/55 and C30/37 exhibit High resistance (Dnssm 5–10) and C20/25 Low resistance (Dnssm >15). Hence, the results indicate that UHPFRC has superior durability compared to conventional concrete. The high resistance towards chloride migration and other degrading mechanisms can be attributed to the dense matrix of UHPFRC (Russell and Graybeal, 2013).
Another aspect of durability that is not considered using accelerated tests such as the NT BUILD 492 method is the risk that cracking may open for the ingress of degrading agents. The steel fibers that are part of the UHPFRC prevent crack growth, improving the resistance of real structures far better than a conventional reinforced concrete layer. As found during the three-point bending tests (Section 4.1.2), the steel fibers restrain both the initiation and growth of cracks in the UHPFRC matrix. This is not only contributing to strength but also improves durability. Applying a high enough content of steel fibers results in a strain-hardening layer in structures that can resist cracking, contributing to high durability (Bertola et al., 2021b). Zhang et al. (2023) also reported that steel fibers improve the chloride resistance of concrete and that the resistance increases with steel fiber content.
4.2 Full-scale production
An important part of this project was to investigate the potential for utilizing ordinary facilities for ready-mixed concrete to produce, transport, and pour UHPFRC in quantities appropriate for industrialized bridge rehabilitation.
It has been observed that planetary mixers are generally more effective for mixing UHPFRC compared to twin-shaft mixers. However, the available equipment dictates the choice of mixer, and in this case, a twin-shaft mixer was used.
Sand and cement were weighed from the silos and dosed into the twin-shaft mixer (Figure 15a) together with water and SP. As limestone filler was not a common constituent at this RMC plant, it had to be manually transported in bags up the stairs to the top of the mixer, where it was added to the mixing procedure. Due to the narrow staircase and lack of storage space on top, the mixing procedure became long-lasting. Consequently, the temperature in the mix increased. After this procedure, the mix was loaded onto a truck and driven around the plant area for some minutes. The final step of this evaluation was whether the fresh UHPFRC might be delivered by means of ordinary pumping equipment. A combined mixer and pump truck (PuMi) was used (Figure 15b), operated by skilled staff.
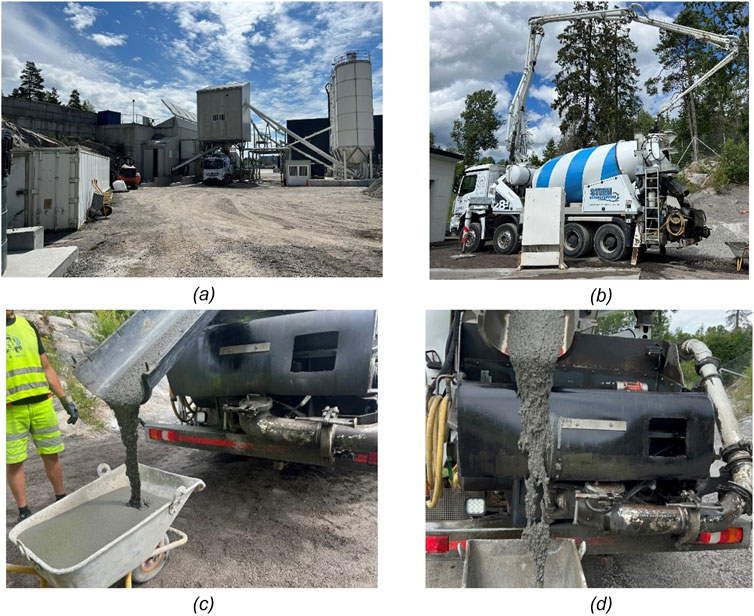
Figure 15. UHPFRC production at RMC-plant, (a) RMC-plant, (b) pumping, (c) UHPC without steel fibers, and (d) UHPC with steel fibers.
The second non-standard constituent in the UHPFRC mix was the micro steel fibers. Batches of these fibers were sequentially added and mixed in the truck, to evaluate the impact of increasing levels of fibers on the fresh properties of the UHPFRC. Adding high amounts of micro fibers directly from bags into the truck is not favorable, due to the risk of balling. Rather, a vibrating device should feed the fibers into the drum. This is also well known for larger fibers, even if the problem seems inversely proportional to the size of the fibers.
The ambient temperature was above 20°C and sunny. The procedure of adding, mixing, and sampling UHPFRC at different levels of fiber content lasted for about 3 hours. Combined with the temperature in the mix rising to a maximum of 32°C, it was believed to have caused water to evaporate from the mix. Combined with the high material temperature, the hydration process might have been accelerated and negatively influenced workability further.
The freshly made material was considered well-suitable for pumping (Figure 15c), but not after the 3-h session of adding fibers (Figure 15d). Prior to pumping, water was added to compensate for the evaporation. No scientific measurement was used in this process, except the considerations of the skilled staff—which included the certified pump operator and the technical director of the RMC producer.
Following this procedure, the pumping process turned out successful. Both bleeding in the poured material and clogging of the pumping equipment were avoided. Clogging of pipes and hoses was a major concern, due to both the risk of hose explosion and the work related to resolving the flow.
Cleansing of all equipment including the production facility and PuMi was also a concern, as fresh and hardening UHPFRC is known to be sticky and hard to handle—especially after the inclusion of fibers. However, this turned out to be not problematic.
5 Conclusion
Based on the work presented, the following conclusions are suggested:
• The literature offers an array of examples where UHPFRC has been used to renovate bridges, also being commercially successful. Most examples are from a few geographically restricted regions, utilizing proprietary UHPFRC materials. Recommendations are given on material properties in fresh and hardened states, overlay thickness, and cover in different situations. Recommendations regarding materials utilizing aggregates with Dmax limited to 1 mm are found.
• The present investigation evaluated the production of UHPFRC suitable for bridge rehabilitation based on local constituents, including natural sand with a Dmax of 8 mm. The final product was found suitable regarding tested mechanical and durability properties. Fresh properties can be altered following case-specific requirements.
• Common industrial facilities for the production, transportation, and pumping of ready-mixed concrete were found to be suitable to produce UHPFRC with aggregate with Dmax of 8 mm. Special concern needs to be taken for addition of constituents that are not common at the facilities—like limestone powder and steel fibers in this case. A vibrating device should be used for the implementation of micro steel fibers.
Data availability statement
The original contributions presented in the study are included in the article/supplementary material, further inquiries can be directed to the corresponding author.
Author contributions
IL: Writing – original draft, Writing – review and editing. RT: Writing – original draft, Writing – review and editing. BP: Writing – original draft, Writing – review and editing. TK: Writing – original draft, Writing – review and editing.
Funding
The author(s) declare that financial support was received for the research and/or publication of this article. The work presented in this paper was conducted as part of the project Repair and strengthening bridge decks with a new UHPC overlay, produced using local materials to reduce environmental impact and cost. The project is funded by the Norwegian Concrete Association through the R&D Committee’s Development Fund for 2023 (https://betong.net/nbs-utviklingsfond-tildelinger/).
Acknowledgments
The efforts of students at the University of Agder: Aram Akhte, Mikael Vermeulen, and Ørjan Ulriksen in conducting some of the laboratory experiments are greatly appreciated. The authors also gratefully acknowledge the contribution of Senior Engineer Anette Heimdal and Cecilie Ødegård for contributing to conducting the flexural strength tests. As an alternative to language editing services, ChatGPT was used during the preparation of the draft of this manuscript to improve readability and for spell-check, for some parts of the text.
Conflict of interest
Author BP was employed by Unicon AS.
The remaining authors declare that the research was conducted in the absence of any commercial or financial relationships that could be construed as a potential conflict of interest.
Generative AI statement
The author(s) declare that Gen AI was used in the creation of this manuscript. As an alternative to language editing services, ChatGPT was used during the preparation of the draft of this manuscript to improve readability and for spell-check, for some parts of the text.
Publisher’s note
All claims expressed in this article are solely those of the authors and do not necessarily represent those of their affiliated organizations, or those of the publisher, the editors and the reviewers. Any product that may be evaluated in this article, or claim that may be made by its manufacturer, is not guaranteed or endorsed by the publisher.
References
Abbas, S., Soliman, A. M., and Nehdi, M. L. (2015). Exploring mechanical and durability properties of ultra-high performance concrete incorporating various steel fiber lengths and dosages. Constr. Build. Mater. 75, 429–441. doi:10.1016/j.conbuildmat.2014.11.017
Abellán-García, J., Carvajal-Muñoz, J. S., and Ramírez-Munévar, C. (2024). Application of ultra-high-performance concrete as bridge pavement overlays: literature review and case studies. Constr. Build. Mater. 410, 134221. doi:10.1016/j.conbuildmat.2023.134221
Alvarez, A., Toledo, W. K., Weldon, B. D., and Newtson, C. M. (2024). Construction methods and lessons learned for a non-proprietary ultra-high performance concrete overlay. Constr. Mater. 4 (1), 271–291. doi:10.3390/constrmater4010015
Bertola, N., Küpfer, C., Kälin, E., and Brühwiler, E. (2021a). Assessment of the environmental impacts of bridge designs involving UHPFRC. Sustainability 13 (22), 12399. doi:10.3390/su132212399
Bertola, N., Schiltz, P., Denarié, E., and Brühwiler, E. (2021b). A review of the use of UHPFRC in bridge rehabilitation and new construction in Switzerland. Front. Built Environ. 7. doi:10.3389/fbuil.2021.769686
Brühwiler, E. (2020). UHPFRC technology to enhance the performance of existing concrete bridges. Struct. Infrastructure Eng. 16 (1), 94–105. doi:10.1080/15732479.2019.1605395
Brühwiler, E. (2023a). “Structural UHPFRC: recent applications in rehabilitation and strengthening of bridges in Switzerland” in International interactive symposium on ultra-high performance concrete (USA: Iowa State University Digital Press).
Brühwiler, E. (2023b). “Swiss UHPFRC model standard: ultra-high performance fibre reinforced cementitious composite (UHPFRC) – materials, dimensioning and execution adapted and translated version of the technical leaflet SIA 2052”.
Brühwiler, E. (2024). “UHPFRC technology for the extension of the service duration of bridges,” in Bridge maintenance, safety, management, digitalization and sustainability (London, UK: CRC Press), 158–166.
di Prisco, M. (2023). (S)FRC in EC2 and in model code 2020. Concr. Struct. 24, 36–41. doi:10.32970/cs.2023.1.6
Du, J., Guo, P., Liu, Z., and Meng, W. (2023). Highly thixotropic ultra-high-performance concrete (UHPC) as an overlay. Constr. Build. Mater. 366, 130130. doi:10.1016/j.conbuildmat.2022.130130
El Jisr, H., Moreillon, L., and Menétrey, P. (2024). Strengthening of the riddes viaduct through UHPFRC-based rehabilitation. Struct. Eng. Int. 34 (4), 577–585. doi:10.1080/10168664.2023.2194898
European Committee for Standardization (1999). “NS-EN 1542:1999 Products and systems for the protection and repair of concrete structures - test methods - measurement of bond strength by pull-off”. (Brussels).
European Committee for Standardization (2002). “NS-EN 13057:2002 Products and systems for the protection and repair of concrete structures - test methods - determination of resistance of capillary absorption”. (Brussels).
European Committee for Standardization (2004). “EN 1992-1-1:2004, Eurocode 2: design of concrete structures - Part 1-1: general rules and rules for buildings”.
European Committee for Standardization (2005). “NS-EN 14651:2005+A1:2007 Test method for metallic fibre concrete - measuring the flexural tensile strength (limit of proportionality (LOP), residual)”. (Brussels).
European Committee for Standardization (2016). “SN-CEN/TS 12390-9:2016 Testing hardened concrete - Part 9: freeze-thaw resistance with de-icing salts - scaling”. (Brussels).
European Committee for Standardization (2019a). “NS-EN 12350-6:2019 Testing fresh concrete - Part 6: density”. (Brussels).
European Committee for Standardization (2019b). “NS-EN 12350-8:2019 Testing fresh concrete - Part 8: self-compacting concrete - slump-flow test”. (Brussels).
European Committee for Standardization (2019c). “NS-EN 12390-16:2019 Testing hardened concrete - Part 16: determination of the shrinkage of concrete”. (Brussels).
European Committee for Standardization (2019d). “NS-EN 12390-17:2019 Testing hardened concrete - Part 17: determination of creep of concrete in compression”. (Brussels).
European Committee for Standardization (2019e). “NS-EN 12390-3:2019 Testing hardened concrete - Part 3: compressive strength of test specimens”. (Brussels).
European Committee for Standardization (2019f). NS-EN 12350-7: 2019 Testing fresh concrete: air content–Pressure methods. (Brussels).
European Committee for Standardization (2021). “NS-EN 12390-13:2021 Testing hardened concrete - Part 13: determination of secant modulus of elasticity in compression”. (Brussels).
federation internationale du beton, (2013). fib model code for concrete structures 2010.Lausanne, Switzerland: Fédération Internationale du Béton.
Fehling, E., and Thiemicke, J. (2023). Potential of ultra-high-performance concrete (UHPC) for refurbishment of bridges. IOP Conf. Ser. Earth Environ. Sci. 1195 (1), 012003. doi:10.1088/1755-1315/1195/1/012003
Fidjestol, P., Thorstensen, R., and Svennevig, P. (2012). “Making UHPC with local materials—the way forward,” in HiPerMat 2012, 3rd international Symposium on UHPC and Nanotechnology for high performance construction materials, 207–214.
Graybeal, B., Brühwiler, E., Kim, B.-S., Toutlemonde, F., Voo, Y. L., and Zaghi, A. (2020). International perspective on UHPC in bridge engineering. J. Bridge Eng. 25(11), 04020094. doi:10.1061/(ASCE)BE.1943-5592.0001630
Haber, Z. B., Foden, A., McDonagh, M., Ocel, J. M., Zmetra, K., and Graybeal, B. A. (2022). Design and construction of UHPC-based bridge preservation and repair solutions. United States: Federal Highway Administration. Office of Infrastructure.
Hajiesmaeili, A., Pittau, F., Denarié, E., and Habert, G. (2019). Life cycle analysis of strengthening existing RC structures with R-PE-UHPFRC. Sustain. Switz. 11 (24), 6923. doi:10.3390/su11246923
Hassan, A. M. T., Jones, S. W., and Mahmud, G. H. (2012). Experimental test methods to determine the uniaxial tensile and compressive behaviour of ultra high performance fibre reinforced concrete (UHPFRC). Constr. Build. Mater. 37, 874–882. doi:10.1016/j.conbuildmat.2012.04.030
Ibrahim, M. A., Farhat, M., Issa, M. A., and Hasse, J. A. (2017). Effect of material constituents on mechanical and fracture mechanics properties of ultra-high-performance concrete. ACI Mater. J. 114 (3), 453–465. doi:10.14359/51689717
Islam, M. M., Zhang, Q., and Jin, Q. (2022). A review of existing codes and standards on design factors for UHPC placement and fiber orientation. Constr. Build. Mater. 345, 128308. doi:10.1016/j.conbuildmat.2022.128308
Jensen, V. (2004). Alkali–silica reaction damage to Elgeseter Bridge, Trondheim, Norway: a review of construction, research and repair up to 2003. Mater. Charact. 53 (2), 155–170. doi:10.1016/j.matchar.2004.09.006
Kadhim, M. M. A., Jawdhari, A., Nadir, W., and Majdi, A. (2023). Experimental study on RC beams strengthened in flexure with CFRP-Reinforced UHPC overlays. Eng. Struct. 285, 116066. doi:10.1016/j.engstruct.2023.116066
Kongshaug, S. S., Larssen, R. M., Hendriks, M. A. N., Kanstad, T., and Markeset, G. (2021). Load effects in reinforced concrete beam bridges affected by alkali–silica reaction—constitutive modelling including expansion, cracking, creep and crushing. Eng. Struct. 245, 112945. doi:10.1016/j.engstruct.2021.112945
Kvamstad, T., Moe, H., and Lervik, I. (2024). “Norwegian coastal bridges,” in Bridge maintenance, safety, management, digitalization and sustainability (London, UK: CRC Press), 2909–2916.
Lande, I., and Thorstensen, R. T. (2021). Locally produced UHPC: the influence of type and content of steel fibres. Nordic Concr. Res. 64(1), 31–52. doi:10.2478/ncr-2021-0003
Lande, I., and Thorstensen, R. T. (2023). Comprehensive sustainability strategy for the emerging ultra-high-performance concrete (UHPC) industry. Clean. Mater. 8, 100183. doi:10.1016/j.clema.2023.100183
Lande, I., Thorstensen, R. T., Gudding Petersen, B., and Martius-Hammer, T. A. (2024). “Towards local large-scale production of UHPC in Norway,” in 6th international symposium on ultra-high performance concrete and high performance construction materials for sustainable construction (Kassel, Germany: Kassel University Press GmbH).
Larsen, I. L., and Thorstensen, R. T. (2020). The influence of steel fibres on compressive and tensile strength of ultra high performance concrete: a review. Constr. Build. Mater. 256, 119459. doi:10.1016/j.conbuildmat.2020.119459
Le Hoang, A., and Fehling, E. (2017). Influence of steel fiber content and aspect ratio on the uniaxial tensile and compressive behavior of ultra high performance concrete. Constr. Build. Mater. 153, 790–806. doi:10.1016/j.conbuildmat.2017.07.130
Li, J., Wu, Z., Shi, C., Yuan, Q., and Zhang, Z. (2020). Durability of ultra-high performance concrete – a review. Constr. Build. Mater. 255, 119296. doi:10.1016/j.conbuildmat.2020.119296
Li, Y., Zhang, W., Sun, G., Xiu, Y., Zhang, Z., Li, C., et al. (2023). A new orientational molding method for ultra-high performance concrete with high content of steel fiber and investigation on its flexure and axial tensile properties. Constr. Build. Mater. 400, 132755. doi:10.1016/j.conbuildmat.2023.132755
Lliso-Ferrando, J. R., Gandía-Romero, J. M., Soto, J., and Valcuende, M. (2023). OC, HPC, UHPC and UHPFRC corrosion performance in the marine environment. Buildings 13 (10), 2439. doi:10.3390/buildings13102439
López, J. Á., Serna, P., Navarro-Gregori, J., and Coll, H. (2016). A simplified five-point inverse analysis method to determine the tensile properties of UHPFRC from unnotched four-point bending tests. Compos. Part B Eng. 91, 189–204. doi:10.1016/j.compositesb.2016.01.026
Meng, W., and Khayat, K. H. (2016). Mechanical properties of ultra-high-performance concrete enhanced with graphite nanoplatelets and carbon nanofibers. Compos. Part B Eng. 107, 113–122. doi:10.1016/j.compositesb.2016.09.069
Meng, W., and Khayat, K. H. (2018). Effect of hybrid fibers on fresh properties, mechanical properties, and autogenous shrinkage of cost-effective UHPC. J. Mater. Civ. Eng. 30 (4), 04018030. doi:10.1061/(ASCE)MT.1943-5533.0002212
Mortensvik, Ø., and Thorstensen, R. T. (2024). “Low-carbon, shrinkage-reduced, sprayed concrete; a pilot study,” in 9th International symposium on sprayed concrete modern use of wet mix sprayed concrete for underground support. Ø. Bjøntegaard, T. Beck & C. Hagby. (Sandefjord, Norway).
Mortensvik, Ø., and Thorstensen, R. T. (2025). Sudden changes in workability during concrete pumping–an industrial approach. Nordic Concr. Res. 69 (2), 11–31. doi:10.2478/ncr-2023-0014
Nordtest method (1999). NT BUILD 492: chloride migration coefficient from non-steady-state migration experiments. Espoo, Finland: Finland.
Ouyang, X., Huang, Y., and Shi, C. (2024). Influence of fiber shapes on the compressive behaviors of ultra-high performance concrete containing coarse aggregate. J. Build. Eng. 98, 111262. doi:10.1016/j.jobe.2024.111262
Pourbaba, M., Asefi, E., Sadaghian, H., and Mirmiran, A. (2018). Effect of age on the compressive strength of ultra-high-performance fiber-reinforced concrete. Constr. Build. Mater. 175, 402–410. doi:10.1016/j.conbuildmat.2018.04.203
Richard, P., and Cheyrezy, M. (1995). Composition of reactive powder concretes. Cem. Concr. Res. 25 (7), 1501–1511. doi:10.1016/0008-8846(95)00144-2
Russell, H. G., and Graybeal, B. A. (2013). Ultra-high performance concrete: a state-of-the-art report for the bridge community (No. FHWA-HRT-13-060). USA: Federal Highway Administration.
Shi, Z., Liang, M., Su, Q., Kanstad, T., and Ferrara, L. (2024). Tensile behavior of rebar-reinforced coarse aggregate ultra-high performance concrete (R-CA-UHPC) members: experiments and restrained shrinkage creep effect. Cem. Concr. Compos. 151, 105574. doi:10.1016/j.cemconcomp.2024.105574
Spiesz, P., and Hunger, M. (2017). “Towards a more common use of Ultra-High Performance Concrete (UHPC)–development of UHPC for ready-mix and prefabrication concrete plants,” in Eleventh high performance concrete (11th HPC), 1–10. Tromsø 6-8 March 2017.
Sritharan, S., Doiron, G., Bierwagen, D., Keierleber, B., and Abu-Hawash, A. (2018). First application of UHPC bridge deck overlay in north America. Transp. Res. Rec. 2672 (26), 40–47. doi:10.1177/0361198118755665
Stengel, T., and Schießl, P. (2014). “22 - life cycle assessment (LCA) of ultra high performance concrete (UHPC) structures,” in Eco-efficient construction and building materials (Cambridge, UK: Woodhead Publishing), 528–564. F. Pacheco-Torgal, L.F. Cabeza, J. Labrincha & A. de Magalhães.
Sun, Y., Zhang, P., Guo, J., Wang, L., and Wu, J. (2024). Rheological properties and workability of PVA fiber and nano-SiO2 modified cement-based materials. Dev. Built Environ. 18, 100396. doi:10.1016/j.dibe.2024.100396
Taffese, W. Z., and Espinosa-Leal, L. (2022). Prediction of chloride resistance level of concrete using machine learning for durability and service life assessment of building structures. J. Build. Eng. 60, 105146. doi:10.1016/j.jobe.2022.105146
The Norwegian Concrete Association (2024a). NB 15 Concrete floor – floor on the ground and topping In Norwegian: NB 15 Betonggulv– gulv på grunn og påstøp.
The Norwegian Concrete Association (2024b). NB 38 Fibre reinforced concrete in load-carrying structures In Norwegian: NB 38 Fiberarmert betong i bærende konstruksjoner.
The Norwegian Public Roads Administration (2015). Handbook N400 bridge design (in Norwegian: håndbok N400 bruprosjektering). (Oslo: Vegdirektoratet).
Thorstensen, R. T., Heimdal, A., Larsen, I. L., and Hansen, H. A. (2016). LCC and carbon footprint of bridge made from locally produced UHPC, compared to standard concrete in HiPerMat 2016 4th international symposium on ultra-high performance concrete and high performance materials (Kassel, Germany: Kassel university press).
Vítek, J. L., Vráblík, L., and Coufal, R. (2025). “Strengthening of structures with UHPC–experiments and experience from application,” in Beton-und stahlbetonbau.
Walraven, J. C. (2009). High performance fiber reinforced concrete: progress in knowledge and design codes. Mater. Struct. 42 (9), 1247–1260. doi:10.1617/s11527-009-9538-3
Wang, W., Zhang, P., Dai, X., Zheng, Y., and Hu, S. (2025). Workability of self-compacting geopolymer concrete: the effect of nano-SiO2 and steel-polyvinyl alcohol hybrid fiber. Constr. Build. Mater. 460, 139849. doi:10.1016/j.conbuildmat.2024.139849
Wei, Y., Guo, W., Ma, L., Liu, Y., and Yang, B. (2023). Materials, Structure, and construction of a low-shrinkage UHPC overlay on concrete bridge deck. Constr. Build. Mater. 406, 133353. doi:10.1016/j.conbuildmat.2023.133353
Wu, Z., Shi, C., He, W., and Wu, L. (2016). Effects of steel fiber content and shape on mechanical properties of ultra high performance concrete. Constr. Build. Mater. 103, 8–14. doi:10.1016/j.conbuildmat.2015.11.028
Wu, Z., Shi, C., and Khayat, K. H. (2019). Investigation of mechanical properties and shrinkage of ultra-high performance concrete: influence of steel fiber content and shape. Compos. Part B Eng. 174, 107021. doi:10.1016/j.compositesb.2019.107021
Xie, T., Fang, C., Mohamad Ali, M. S., and Visintin, P. (2018). Characterizations of autogenous and drying shrinkage of ultra-high performance concrete (UHPC): an experimental study. Cem. Concr. Compos. 91, 156–173. doi:10.1016/j.cemconcomp.2018.05.009
Yang, J., Chen, B., and Nuti, C. (2021). Influence of steel fiber on compressive properties of ultra-high performance fiber-reinforced concrete. Constr. Build. Mater. 302, 124104. doi:10.1016/j.conbuildmat.2021.124104
Yoo, D. Y., Kim, S., Park, G. J., Park, J. J., and Kim, S. W. (2017). Effects of fiber shape, aspect ratio, and volume fraction on flexural behavior of ultra-high-performance fiber-reinforced cement composites. Compos. Struct. 174, 375–388. doi:10.1016/j.compstruct.2017.04.069
Yoo, D.-Y., Lee, J.-H., and Yoon, Y.-S. (2013). Effect of fiber content on mechanical and fracture properties of ultra high performance fiber reinforced cementitious composites. Compos. Struct. 106, 742–753. doi:10.1016/j.compstruct.2013.07.033
Yoo, D.-Y., Shin, H.-O., Yang, J.-M., and Yoon, Y.-S. (2014). Material and bond properties of ultra high performance fiber reinforced concrete with micro steel fibers. Compos. Part B Eng. 58, 122–133. doi:10.1016/j.compositesb.2013.10.081
Yu, R., Spiesz, P., and Brouwers, H. J. H. (2014). Mix design and properties assessment of ultra-high performance fibre reinforced concrete (UHPFRC). Cem. Concr. Res. 56, 29–39. doi:10.1016/j.cemconres.2013.11.002
Zhang, P., Feng, Z., Guo, J., Zheng, Y., and Yuan, P. (2024). Mechanical behavior and microscopic damage mechanism of hybrid fiber-reinforced geopolymer concrete at elevated temperature. Ceram. Int. 50 (24, Part B), 53851–53866. doi:10.1016/j.ceramint.2024.10.238
Zhang, P., Wang, C., Gao, Z., and Wang, F. (2023). A review on fracture properties of steel fiber reinforced concrete. J. Build. Eng. 67, 105975. doi:10.1016/j.jobe.2023.105975
Keywords: bridge rehabilitation, UHPFRC, UHPC, local materials, full-scale production, material properties
Citation: Lande I, Thorstensen RT, Petersen BG and Kanstad T (2025) Full-scale production and material properties of ultra-high-performance fiber-reinforced concrete (UHPFRC) for rehabilitation of bridge decks in Norway. Front. Built Environ. 11:1570920. doi: 10.3389/fbuil.2025.1570920
Received: 04 February 2025; Accepted: 28 April 2025;
Published: 20 May 2025.
Edited by:
Pablo Pujadas, Universitat Politecnica de Catalunya, SpainReviewed by:
Amir Ali Shahmansouri, Washington State University, United StatesPeng Zhang, Zhengzhou University, China
Copyright © 2025 Lande, Thorstensen, Petersen and Kanstad. This is an open-access article distributed under the terms of the Creative Commons Attribution License (CC BY). The use, distribution or reproduction in other forums is permitted, provided the original author(s) and the copyright owner(s) are credited and that the original publication in this journal is cited, in accordance with accepted academic practice. No use, distribution or reproduction is permitted which does not comply with these terms.
*Correspondence: Ingrid Lande, aW5ncmlkLmxhbmRlQHVpYS5ubw==