- 1Department of Plant and Environmental Sciences, Faculty of Science, University of Copenhagen, Taastrup, Denmark
- 2Futonics Laser GmbH, Katlenburg-Lindau, Germany
Weed control is necessary to ensure a high crop yield with good quality. Herbicide application and mechanical weeding are the most common methods worldwide. The use of herbicides has led to the increasing occurrence of herbicide-resistant weeds and unwanted contamination of the environment. Mechanical weed control harms beneficial organisms, increases the degradation of organic matter, may dry out the soil, and stimulate new cohorts of weed seeds to germinate. Therefore, there is a need to develop more sustainable weed control means. We suggest using small autonomous vehicles equipped with lasers as a sustainable alternative method. Laser beams are based on electricity, which can be produced from non-fossil fuels. Deep learning methods can be used to locate and identify weed and crop plants for targeting and delivery of laser energy with robotic actuators. Given the targeted nature of laser beams, the area exposed for weed control can be reduced substantially compared to commonly used weed control methods. Therefore, the risk of affecting non-target organisms is minimized, and the soil will be kept untouched in the field, avoiding triggering weed seeds to germinate. Small autonomous vehicles may have limited weeding capacity, and precautions need to be taken as reflections from the laser beam can be harmful to humans and animals. In this paper, we discuss the pros and cons of replacing or supplementing common used weed control methods with laser weeding. The ability to use laser weeding technology is relatively new and not yet widely practiced or commercially available. Therefore, we do not discuss and compare the costs of the various methods at this early stage of the development of the technology.
Introduction
Worldwide, weed infestations constitute one of the most devastating constraints for crop production and make it challenging to increase yields and supply food for a growing population (FAO, 2021). Effective and affordable weed control is essential to achieve high yields, but often it affects the environment negatively (Kudsk and Streibig, 2003). Indiscriminate application of herbicides increases the risk of environmental contamination, given weeds typically constitute only a small proportion of the target area, with most herbicide applied hitting non-target material or lost to spray drift (Kudsk and Streibig, 2003; Harrison, 2011). Problems with herbicide-resistant weeds are increasing worldwide (Heap, 2021), and new herbicide modes of action have not been found since the 1980s (Duke, 2011). The negative side-effects of pesticide use have resulted in stricter regulation and political initiatives to reduce pesticide use (Andreasen and Streibig, 2011; European Commission, 2021).
Mechanical weed control harms beneficial organisms like predatory beetles and spiders on the soil surface and earthworms in the soil (Tamburini et al., 2016; Sharma et al., 2017). It also increases the risk of soil erosion and leaching of plant nutrients, promotes unnecessary mineralization of soil organic matter, and dries out soils with limited moisture content (Cloutier and Leblanc, 2001). Flame weeding requires a large amount of gas (Sivesind et al., 2009), and it may not be considered environmentally sustainable in the long term due to the CO2 derived production.
Therefore, there is a need for developing new techniques supplementing or replacing present weed control methods (Andreasen et al., 2018; Bitarafan and Andreasen, 2020).
Laser beams can deliver high-density energy on selected spots. A laser beam can be directed toward a weed plant and warm up the plant tissue harming or killing the plant (Heisel et al., 2001, 2002). Identification of the target is essential to limit energy consumption. Recognition tools based on artificial intelligence make it possible to distinguish weeds from crop plants in agricultural environments in real-time (Wang et al., 2019; Rakhmatulin et al., 2021). The meristem can be detection by using high resolution cameras, while the positioning can be guided by precise laser scanners. Therefore, research in laser weeding technologies has increased, and some field robots are now arriving on the marketplace (e.g., https://carbonrobotics.com/).
This paper explains what a laser is and discusses the advantages and disadvantages of using lasers for weed control. No products are widely used. Therefore, we do not compare the costs of laser weeding with other weed control methods. If or when mass production of laser robots for weed control will take place, prices will surely decrease, and laser weeding may become economically competitive to other weed control methods and perhaps necessary to replace or supplement commonly used weed control means.
What is Laser?
Laser is an acronym for “light amplification by stimulated emission of radiation.” A laser is a device that emits light through optical amplification based on the stimulated emission of electromagnetic radiation. The laser has unique properties such as coherence, monochromaticity, directionality, and high intensity during the irradiation of different substances (Bityurin, 2005; Dlugunovich et al., 2006; Ferraz et al., 2007). Collimated laser beams executes high levels of energy in the form of a narrow and non-spreading beam. A laser differs from other light sources in that it emits coherent light. Two wave sources are coherent if their frequency and waveform are identical. Laser beams can be focused on extremely small spots, achieving a very high irradiance, or having very low divergence to concentrate their power at a great distance (Chu, 2011). Lasers are characterized by their wavelength in a vacuum. A benefit of laser is that beam divergence and shape can be adjusted with optics for more precise delivery of energy for weed control.
Lasers have been used in various industrial applications to measure, cut, bore holes, etch, weld, and remove paints. For example, laser irradiation enables precise surface modification of polymers with little surface damage depending of the wavelength used (Fabbri and Messori, 2017). Carbon-dioxide lasers, typically operating at 10,600 nm, are used to burn tissues because the infrared beams are strongly absorbed by the water of biological cells (Gates et al., 1965; Wieliczka et al., 1989). One micrometer of laser wavelengths can penetrate the eye removing tissue from the cornea, reshaping the transparent outer layer of the eye with intense ultraviolet pulses. Less-intense laser pulses can destroy abnormal blood vessels that spread across the retina in patients who have diabetes, delaying the blindness associated with the disease (Kolikov and Koshlan, 2020).
The different types of lasers use different active (laser) media and emit at different wavelengths. The active medium of a diode laser is a semiconductor, which is excited via an electrical current. The emission wavelengths of diode lasers vary between ultraviolet to infrared radiation, whereas typical wavelengths are 940 and 980 nm, with laser power from mW to several kW. A fiber laser is a type of solid-state laser which active medium is a doped glass fiber. Solid-state and fiber lasers are excited via optical radiation. Emission wavelengths of fiber lasers are typically in the visible and the near infrared light spectrum. The output powers of fiber laser systems can reach up to many kW (Hitz et al., 2012). The diode laser and fiber laser used by Kaierle et al. (2013) operated with a wavelength of 1,908 and 532 nm, respectively. The active medium of a CO2 laser is a gas mixture of nitrogen (N2), helium (He) and carbon dioxide (CO2) that is excited via an electric gas discharge. The typical emission wavelengths of CO2 lasers are in the far infrared light spectrum. Mostly the three wavelength bands at 9.3 μm, 10.2 μm and at 10.6 μm are used (Witteman, 1987).
A very important parameter for laser applications especially for weeding is the beam quality, as it defines the achievable maximum power density. Compared to conventional light, laser beams have in principle very low divergence and allow propagation over long distances without noticeable spreading of the beam. The better the beam quality the lower the divergence of the laser beam. A constant quantity for laser-beam propagation in an optical train is the beam parameter product BPP, given by multiplication of far field divergence and beam waist radius. For a fiber laser, the BPP is 0.34 to 1.8 mm x mrad, for a CO2 laser 6 mm x mrad and a high-power diode laser > 100 mm x mrad (Bachmann et al., 2007). In comparison, the beam propagation of the CO2 laser and the diode laser are worse than that of the fiber laser systems. For transmission of high-power laser radiation from the laser source to the focusing optics two different alternatives are used in applications: beam guiding by glass fibers and beam guiding through the air by mirror systems. The first alternative is not really feasible for CO2 laser radiation because of a lack of suitable materials with high transparency to transmit the laser radiation over a certain length without noticeable power loss. But in the case of NIR lasers like diode or fiber lasers, glass fibers are a common way for transmission of laser radiation, sometimes used in combination with mirror systems. The advantage of glass fibers vs. mirror systems is easier adjustment and maintenance of laser processing systems. Changing components like the laser source, focusing units and the glass fiber itself needs less optical adjustment effort than for mirror systems, especially in use of multi-axis beam-delivery systems (Klein, 2012). Recently, laser beam has been used as a non-chemical weed control method.
Lasers For Weed Control
Three laser types have been used for weed control experiments: The carbon dioxide laser (CO2 laser) (e.g., Heisel et al., 2001, 2002), the diode laser (e.g., Wöltjen et al., 2008), and the fiber laser (e.g., Kaierle et al., 2013; Coleman et al., 2021).
For both CO2 and fiber laser types, the light energy is strongly absorbed in the plant (Gates et al., 1965) leading to lethal damage. As the energy from the CO2 laser is directly absorbed on the surface of the plant, it provides the highest density of energy deposition. The energy from the 2 μm fiber laser is mainly absorbed by the water inside the plant, therefore a larger area of the plant is heated (Wieliczka et al., 1989). For weed control, a thulium-doped fiber laser emitting at 2 μm wavelength is more beneficial because the radiation penetrates through the epidermis and is therefore not solely absorbed on the surface of the plant (Wieliczka et al., 1989).
Several initiatives have been taken combining recognitions tools for plant species identification with laser equipment placed on small autonomous vehicles creating a new way to control weeds (e.g., https://welaser-project.eu/; https://weedbot.eu/; https://carbonrobotics.com/). This combination is a prerequisite for using laser for weed control because treating the whole area with laser beams would not be sustainable due to the required energy consumption.
Energy
Laser is based on electricity, which can be produced sustainably by windmill, hydropower, solar panel and other non-fossil resources. Importantly for field robots, electrical energy can be stored in batteries. Laser wavelengths have been found to strongly influence the thermal coupling and the minimum lethal doses for plants (Kaierle et al., 2013). The thermal coupling in the plant tissue mainly depends on the spectral absorption value at the specific wavelength. Kaierle et al. (2013) studied the dose- and wavelength-dependent lethal effect of laser treatment on the weed species Amaranthus retroflexus L. at the early growth stages. They found, that the overall energy demand was smallest (125 J per weed), when a wavelength of 10,600 nm was used (CO2 laser). When a wavelength of 1,908, 940, and 532 nm (fiber, diode and solid-state laser) were used, a dose of 230, 237 and 1400 J per weed, respectively, were required to kill the weed.
Marx et al. (2012) used a CO2 laser (10,600 nm) to irradiate the grass weed Echinochloa crus-galli, (L.) Beauv., and found that laser energy of at least 54 J per plant was necessary for lethally damaging each treated plant at a probability level of 95%. Lethal damages depend on weed species, laser spot position, growth size, laser spot area, and applied laser energy (J) (Heisel et al., 2001, 2002; Mathiassen et al., 2006; Marx et al., 2012; Rakhmatulin and Andreasen, 2020).
Only plants that threaten the crop yield or quality should be exposed, harmed or killed by the laser beams to avoid unnecessary energy consumption. Small weeds are more sensitive to lasers and require less energy than large plants. The best weeding result is obtained if the meristem of the target plant is exposed on the cotyledon stage or the two permanent leaf stage, at these stages, only the apical meristem is developed for most weed species (Mathiassen et al., 2006; Marx et al., 2012; Rakhmatulin and Andreasen, 2020). The larger the plants are, the more meristems are developed, and the ability to reestablish by sprouting from lateral meristems after the laser treatment increases (Figure 1).
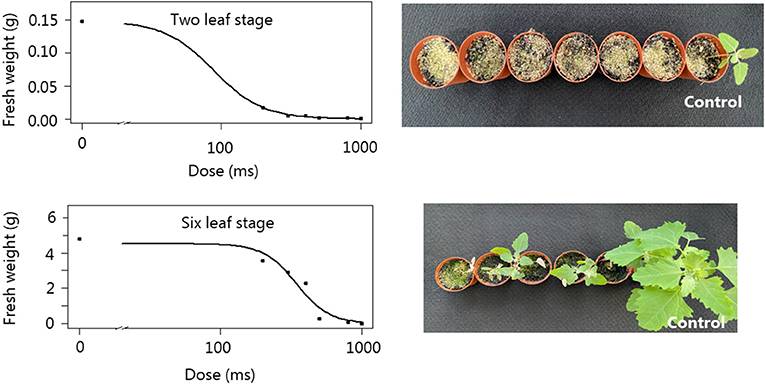
Figure 1. Dose-response experiment with a 50 W fiber laser. Chenopodium album L. plants were exposed at the two and six leaf stage to various pulse lengths (n = 3) (modified from Andreasen et al., 2021).
In contrast to mechanical weeding, the laser can hit weed plants very close to the crop plants without damaging leaves and roots due to the small laser diameter and ability to move the beam with advanced optics, as long as the meristem of the weed plant does not cover the crop plant.
Treated Area
Advances in AI and field robotics makes it possible to precisely locate and identify weed and crop plants (Gikunda and Jouandeau, 2019; Rakhmatulin et al., 2021) and direct the laser beam toward the meristems of the weed seedlings for real-time laser control. Assuming single spot applications is used and there is limited heat movement beyond the irradiate spot, only a small proportion of the area in the field will be exposed to the treatment. As a rough estimate, if the laser beam has a diameter of 2 mm and there are 100 weed plants m−2, the direct exposed area is equal to 12 × 22/7 mm2 × 100 = 314 mm2 = 0.31% of the total area. Only the target plant and not the soil will be exposed directly to the ray in many cases. Compared with herbicide application, mechanical weeding, and flame weeding, where the total area or a large part of the area is exposed to the treatment, laser weeding can reduce the environmental impact of weed control to a minimum.
The smaller the diameter of the laser beam is, the more efficiently does the laser harm the weed plant because all the energy are focused on a small spot (Figure 2). However, if the diameter is too small it may not affect enough cells to kill the plant (Marx et al., 2012), and the smaller the diameter, the more difficult it becomes to hit the meristem precisely in field scenarios with rough terrain.
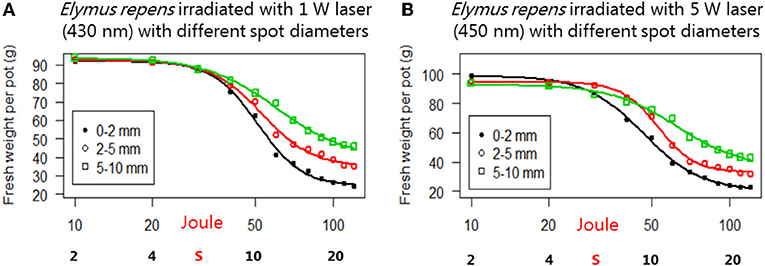
Figure 2. Dose-response curves. (A) Elymus repens (L.) Desv. ex Nevski. plants were exposed to a 1 W laser (435 nm) beam and (B) to a 5 W laser (450 nm) beam. Three diameters (+/− 0.05 mm) of the internal spot of the laser beams were used. The plants were harvest 40 days after laser exposure (modified from Rakhmatulin and Andreasen, 2020).
Biodiversity
With the very small treated area and highly targeted nature of laser weed control, there are likely substantial benefits in reducing off-target impact. If some non-crop plants do not affect the crop negatively, a recognition system can be used to identify the plant species, and define them as non-targets. Such plants could be rare and endangered species, plant species with a positive allelopathic effect on the crop, species supporting pollinators during the growing seasons (e.g., Veronica sp.), plant species creating hiding and nesting places for beneficial insects or plant species providing other ecosystem services.
Although the laser beam heats the spot it hits, the exposure time is short (less than a second) (Andreasen et al., 2021), and the temperature increase around the place is limited. Therefore, the temperature increase may only affect the surrounding environment insignificantly (Figure 3).
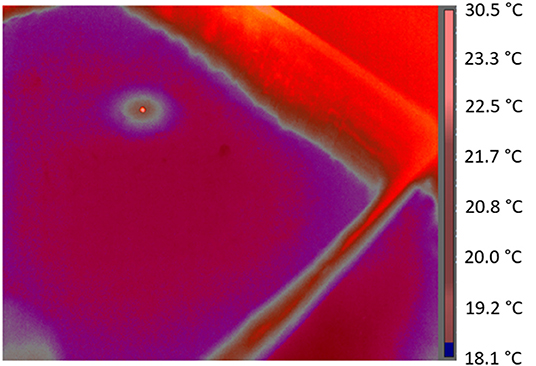
Figure 3. Laboratory experiment with a fiber laser (50 W, 2 mm diameter) exposing the soil in a tray. The soil surface temperature was measured with an infrared camera. The temperature is only significantly increasing close to the spot (modified from Andreasen et al., 2021).
As a weed/crop recognition system is essential, laser weeding combined with weed control thresholds (Ali et al., 2013, 2014) could further reduce energy consumption and support biodiversity. This would especially be relevant in cereals, where a small weed density often has no significant impact on the yield or the quality of the harvested product.
With respect to vehicle movement and obstacle avoidance, recognition systems can identify farmland bird nests and other non-target organisms that the vehicle should avoid. In organic production, biodiversity has high priority, and here, laser weeding can replace manual weeding, which is hard work, time-consuming, often low paid and not attractive (Ramahi and Fathallah, 2006; Tiwari et al., 2021). Farmers of organic farms often struggle finding work power for hand weeding in Europe and elsewhere (Fennimore, 2014). Robotic laser weeding may solve this problem and release work power to other jobs.
Impact on the Soil
Soil compaction is becoming an increasing problem mainly caused by using larger and heavier tractors and field implements (Batey, 2009). Wheel-traffic studies on a silty clay loam have showed that tractor wheel traffic of normal farming operations can compact the soil to a 45 cm depth. Penetrometer resistance was a more sensitive indicator of soil compaction than was bulk density (Voorhees et al., 1978). A penetrometer is a device forced into the soil to measure resistance to vertical penetration (Davidson, 1965). Wheel traffic increased soil bulk density by 20% or less, whereas penetrometer resistance was increased by 400% (Voorhees et al., 1978). Smith and Dickson (1990) investigated the effects of vehicle weight and ground pressure on soil compaction. The compaction resulting from conventional vehicles, and from vehicles which were purpose-built to minimize soil compaction carrying low and high payloads, exemplified the importance of reducing vehicle weight as a means of minimizing soil compaction.
Presently, small, relatively light autonomous vehicles are developed to conduct laser weeding (see, e.g., https://welaser-project.eu/; https://weedbot.eu/; https://carbonrobotics.com/) (Figure 4). Light vehicles do not compress the soil and influence the soil texture like heavy tractors transporting thousands of liters of spraying liquids or heavy implements for mechanical weed control.
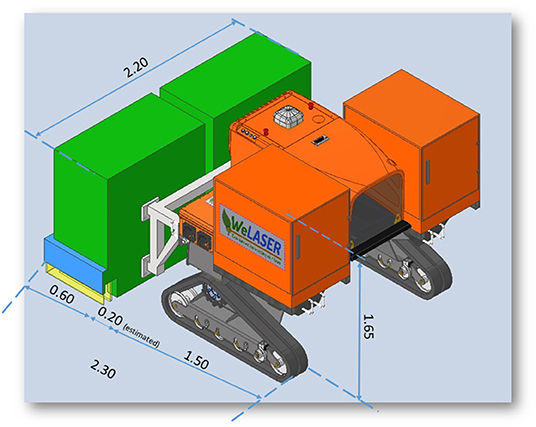
Figure 4. Dimensions of a prototype of an autonomous vehicle for laser weeding (from https://welaser-project.eu/).
Mechanical weed control has a significantly negative effect on beneficial organisms living on the soil surface like predatory ground beetles and spiders (Symondson et al., 2002; Michalko et al., 2019). It also affects earthworms and other organisms in the soil, contributing to the sustenance of a fertile soil (Doran and Zeiss, 2011). It is highly likely that laser weeding interferes much less with the soil environment given the very small treated areas and the heat movement and limited movement of the heat beyond the target. Mechanical weed control may also promote unnecessary mineralization of organic matter by aerating the soil and redistributing microorganisms, which may results in the leaching of plant nutrients (Doran and Zeiss, 2011). It also triggers a new cohort of dormant weed seeds to germinate by exposing the small weed seeds to red light and scratching the seed coat, making water uptake by the seeds easier (Cloutier and Leblanc, 2001).
Laser weeding only interacts with a small part of the soil surface by heating the spot and the near surrounding when hitting the ground (Figure 3). Therefore, the method does not trigger weed seeds to germinate on the whole area, making it necessary to control weeds several times in the season. However, weed species have different temperature requirements for seed germination. Therefore, it is likely that if seeds from weed species with higher temperature requirements (e.g., Solanum nigrum L. and Urtica urens L.) are in the soil seed bank, they may escape an early laser treatment and emergence later in the season (e.g., in sugar beets, maize, vegetables), resulting in a need for one or several extra treatments. It is also likely that the heating of the spot would trigger dormant seeds of these weed species to germinate in this tiny area.
While laser weeding just exposes a tiny area of the field for a very short time (milliseconds), herbicides are usually spread on the total field area. Therefore, there is a risk of affecting all kinds of organisms it hits. In contrast to laser weeding, herbicides stay in the environment for a while and potentially affect organisms on and in the soil for a longer period and may pose a risk of leaching to surface and groundwater. While herbicides potentially affect natural microorganisms on the whole soil surface, laser weeding only affects microorganisms by increasing the temperature where the ray hits the ground and close to the treated spot (Figure 3). Therefore, recolonization of microorganisms in the spot rapidly can take place (Khan et al., 2020).
Weeding Capacity
Presently, small autonomous vehicles are designed to conduct laser weeding (hereafter called laser weeders). Small vehicles with a working width of, e.g., 2.2 m (Figure 4) have a limited capacity to treat a large area compared to a big sprayer with a 24–36 m width sprayer boom. Laser weeders have to locate and identify crop and weed plants and direct the laser toward the target plants in real-time. This is a complicated task, which may limit the weeding process to a driving speed of 4–6 km h−1. Suppose there are many weed plants (>100 m2), the driving speed may need to be reduced. The higher the laser power (W), the less time (ms) is necessary to control the weeds, and the driving speed can be increased. However, the speed of the detection and targeting system for the laser may be a limiting factor for increasing the operating speed.
Depending on weather and driving conditions, herbicide applications with sprayers may take place with a speed between 6 and 12 km h−1 (Wolf, 2009) and up to 20 km h−1 in countries such as Australia and United States (Womac et al., 2001).
Mechanical weed control can be conducted with many different implements having different working widths, but often they are wider than 2.2 m and usually the driving speed of common harrows varies between 4 and 12 km h−1 (4 km h−1 for sensitive crops or crop stages, with 8 km h−1 being the more commonly used speed (Cloutier et al., 2007). Autonomous vehicles can potentially drive day and night, which would reduce the capacity problem.
In general, the best effect of weed control is achieved when the weed plants are small. This counts for laser weeding (Kaierle et al., 2013; Rakhmatulin and Andreasen, 2020), herbicide application (Streibig, 1988), mechanical weeding (Rasmussen et al., 2010), flame weeding (Ascard, 1995), and weeding with ultraviolet radiation (Andreasen et al., 1999). The result also depends on several other factors, especially the weather conditions and developmental stage of the crops and weeds (Rasmussen et al., 2010; Varanasi et al., 2016). There is limited research on the influence of environment conditions on laser performance, however, it is likely that because lasers rely on heating for control, lower temperatures and wet plants may reduce efficacy.
One way to overcome capacity challenges could be to have a fleet of laser weeders working in the same field (Sørensen and Bochtis, 2010; Gonzalez-de-Santos et al., 2017). Laser weeding can also be used in combination with other methods, although that would reduce the benefits. For example, mechanical weed control could occur between the rows in row crops like vegetables, beets and maize, and then the laser weeder could shoot down weeds close to the crop plants in the rows where mechanical weeding may harm the roots or leaves of the crop. The smaller the focus area, the faster the small laser weeders should drive. In principal, this concept would also be helpful in the minor crop where no herbicides are approved and in herbicide sensitive crops. In principle, chemical treatment could be applied between rows protecting the crops with screens while laser weeding occurs in the crop rows.
Efficacy of the Laser
A laser weeder consists of a complex system where many factors influence the precision (e.g., the recognition system, the laser guiding system, driving speed etc.) (Vitali et al., 2021). As long as the recognitions system only separates the crop from other plants, it can be done with a high precision (93%) in real-time (Rakhmatulin et al., 2021). A complex recognition and decision system, that locate and identify many different weed species and decide which one needs to be irradiated may require more processing time than a simple system resulting in a slower driving speed.
For row crops, which have no or little competitive ability against weeds in the first part of the growing season, weed control is essential, and the control rate of the laser needs to be very high. If the field is uneven with many stones, holes and tractor tracks, there is a risk that vibrations and tremors significantly reduce the efficacy, and the laser may harm the crop plants instead. Therefore, seedbed preparation must be done carefully to ensure a flat and uniform field. Alternatively slow speed reduces vibration and increases the hit rate. If the laser beam hits imprecisely, there is a risk that the beam may harm the crop (Rakhmatulin and Andreasen, 2020). If weed plants cover a crop plant, the crop plant may also be damaged. If the beam only hits a leaf, the leaf will be damaged but the plant may regrow.
Safety
With respect to the autonomous movement and navigation of the robotic platform through a field, laser weeders have the same safety issues as other autonomous vehicles. Although such vehicles are only approved driving on the roads in a few experimental places until now, some robots (e.g., lawnmowers) are widely accepted and used on private and public properties. Also, small autonomous agricultural robots are approved to drive on private and public properties (e.g., in EU and UK) as long as all safety guidelines are followed (Basu et al., 2020).
A collimated laser beam executes high levels of energy in the form of a narrow and non-spreading beam, transmitting into heat energy when it hits a surface. The heat can potentially ignite dry material in the field (e.g., straw, leaves, other organic matters, lost paper) and start a fire. While driving, various sensors (e.g., smoke sensors, cameras) can be mounted to register any sign of uncontrolled heating or fire. However, when the laser weeder has passed, a spark could be hidden and expose a danger. Many fires have been started by leaving a spark after flame weeding (Rask and Kristoffersen, 2007), and this is also a risk with laser weeding. Therefore, surveillance of the laser weeder and the treated area must be considered. Leaving the laser weeder driving without surveillance, for example, during the night, could be too risky. Dry organic matter should be avoided on the soil surface, and therefore plowing, which may not be sustainable in the long term, might be necessary to reduce fire risks in some fields.
Laser beams can be harmful to humans and animals. Infrared cameras and sensors must be mounted on the vehicle to warn and stop it when it approaches humans, animals or any other obstacles ensuring an appropriate safety distance. Depending on the laser wavelength, the laser can be more or less harmful to the eyes and skin and cause irreversible damages (e.g., blindness). Visible and near-infrared (400–1,400 nm) laser light pose a critical hazard on the retina. Since the tissue structures of the retina are unable to undergo any repair, lesions caused by the focusing of visible or near-infrared light on the retina may be permanent. The most critical area of the retina is the central portion, the macula, and the fovea.
Laser light in the ultraviolet or far-infrared spectrum can cause damage to the cornea or the lens. Far infrared (1,400 nm – 1 mm; CO2 lasers, 10,600 nm) can cause thermal damage by the heating of the tears and tissue water of the cornea. Excessive exposure to infrared radiation results in a loss of transparency of the cornea or surface irregularities (Occupational, Safety and Health Administration, 2022).
Skin damage is most commonly caused by thermal injury. Thermal damage is associated with lasers operating at exposure times >10 ms and in the wavelength region from the near-ultraviolet to the far-infrared. The thermal effects of laser exposure depend on (1) The absorption and scattering coefficients of the tissues at the laser wavelength, (2) Irradiance or radiant exposure of the laser beam, (3) Duration of the exposure and pulse repetition characteristics, where applicable, (4) Extent of the local vascular flow, and (5) Size of the area irradiated (Occupational, Safety and Health Administration, 2022).
Laser protecting glasses for the specific laser wavelength can protect the operator of the laser weeder when it is necessary to adjust, clean or work close to the laser weeder. Clothing and gloves can help protect the skin. Screens and curtains can be mounted, avoiding laser beams escaping from the target area caused by reflection from stones, sand and other reflecting items, which may spread the beam. It is important to stress that the laser beams can be invisible, and only the result of heating can be seen, for example, when it hit a target.
Conclusion
Are small autonomous vehicles equipped with lasers for weed control then friends or foes? They can be friends because laser weeding does not pose the same problems as other weed control methods and therefore constitutes a suitable alternative or supplement to, for example, herbicide application or mechanical weed control. Developments in weed recognition and field robotic mean lasers can be integrated and controlled easily with on-board computers. Yet lethal damage is dependent on weed species, laser spot position, growth size, laser spot area, and applied laser energy (J), and there is limited research on many of these features and their relationship with external environments.
Given the highly targeted nature of the laser and the potential use of spot beams it is likely, that the area directly exposed for weed control can be reduced from almost 100% to <1% dependent on the diameter of the laser beam and the number of weed plants m−2. As a result they should interfere substantially less with the biodiversity and environment in the field. Small autonomous vehicles are also considerable lighter than ordinary tractors with sprayers or implements for mechanical control and affect the soil texture and soil organisms less, ensuring a better growth substrate for the crops. Such robots can also replace hand weeding in organic farming and release human resources to more attractive work.
However, they can also turn into foes if we do not take sufficient precautions by educating people working, staying or playing on the farms or in the fields. We may not fear, what we do not see, and as the beams may be invisible, people may ignore that refection from laser beams can cause irreversible damage to the eyes and skin. Also, there is a risk of leaving a spark in the field that may start a fire, and therefore surveillance might be necessary to prevent accidents. Safety guidelines have to be followed for all weed control techniques and safety must have the highest priority.
Author Contributions
CA wrote the first draft of the manuscript with input from MS. All authors edited and accepted the final manuscript.
Funding
This work was funded by the EU–project WeLASER Sustainable Weed Management in Agriculture with Laser-Based Autonomous Tools, Grant agreement ID: 101000256, funded under H2020-EU.3.2.1.1.
Conflict of Interest
The authors declare that the research was conducted in the absence of any commercial or financial relationships that could be construed as a potential conflict of interest.
Publisher's Note
All claims expressed in this article are solely those of the authors and do not necessarily represent those of their affiliated organizations, or those of the publisher, the editors and the reviewers. Any product that may be evaluated in this article, or claim that may be made by its manufacturer, is not guaranteed or endorsed by the publisher.
Acknowledgments
We thanks our partners and stakeholders in the WeLASER project for valuable discussions and input to the manuscript.
References
Ali, A., Streibig, J. C., and Andreasen, C. (2013). Yield loss prediction models based on early estimation of weed pressure. Crop Prot. 53, 125–131. doi: 10.1016/j.cropro.2013.06.010
Ali, A., Streibig, J. C., Christensen, S., and Andreasen, C. (2014). Image based thresholds for weeds in maize fields. Weed Res. 55, 26–33. doi: 10.1111/wre.12109
Andreasen, C., Bitarafan, Z., Fenselau, J., and Glasner, C. (2018). Exploiting waste heat from combine harvesters to damage harvested weed seeds and reduce weed infestation. Agriculture 8:42. doi: 10.3390/agriculture8030042
Andreasen, C., Hansen, L., and Streibig, J. C. (1999). The effect of ultraviolet radiation on the fresh weight of some weeds and crops. Weed Tech.13, 554–560. doi: 10.1017/S0890037X00046194
Andreasen, C., Saberi, M., and Rakhmatulin, I. (2021). Weed Control With Laser Beams Using Autonomous Vehicle: Pros and Cons. Presentation at the World Ag Robotic Forum, FIRA 2021. Hybrid event, online & Toulouse, France.
Andreasen, C., and Streibig, J. C. (2011). Evaluation of changes in weed flora in arable fields of Nordic countries—Based on Danish long-term surveys. Weed Res. 51, 214–226. doi: 10.1111/j.1365-3180.2010.00836.x
Ascard, J. (1995). Effects of flame weeding on weed species at different developmental stages. Weed Res. 35, 397–411. doi: 10.1111/j.1365-3180.1995.tb01636.x
Bachmann, F., Loosen, P., and Poprawe, R. (2007). High Power Diode Lasers. Technology and Applications. Springer Nature.
Basu, S., Omotubora, A., Beeson, M., and Charles Fox, C. (2020). Legal framework for small autonomous agricultural robots. AI Soc. 35, 113–134. doi: 10.1007/s00146-018-0846-4
Batey, T. (2009). Soil compaction and soil management – a review. Soil Use Manage. 25, 335–345. doi: 10.1111/j.1475-2743.2009.00236.x
Bitarafan, Z., and Andreasen, C. (2020). Harvest Weed Seed Control: Seed production and retention of Fallopia convolvulus, Sinapis arvensis, Spergula arvensis and Stellaria media at spring oat maturity. Agron. 10:42. doi: 10.3390/agronomy10010046
Bityurin, N. (2005). 8 studies on laser ablation of polymers. Ann. Rep. Progr. Chem. 1, 216–247. doi: 10.1039/b408910n
Chu, B. (2011). Laser Light Scattering: Basic Principles and Practice (2ed edition). New York, NY: Dower Publications, Inc.
Cloutier, D. C., and Leblanc, M. L. (2001). “Mechanical weed control in agriculture” in Physical Control Methods in Plant Protection, eds C. Vincent, B. Panneton, and F. Fleurat-Lessard (Berlin/Heidelberg: Springer). doi: 10.1007/978-3-662-04584-8_13
Cloutier, D. C., van der Weide, R. Y., Peruzzi, A., and Leblanc, M. L. (2007). “Mechanical weed management” in Non-Chemical Weed Management: Principles, Concepts and Technology, eds M. K. Updahyaya and R. E. Blackshaw (CABI international). doi: 10.1079/9781845932909.0111
Coleman, G., Betters, C., Squires, C., Leon-Saval, S., and Walsh, M. (2021). Low energy laser treatments control of annual ryegrass (Lolium rigidum). Front. Agron. 2, e601542. doi: 10.3389/fagro.2020.601542
Davidson, D. (1965). “Penetrometer Measurements”. in Methods of Soil Analysis, ed. C.A. Black (New York, NY: Academic Press, Inc.).
Dlugunovich, D., Zhbankov, R., Zhadanovskii, V., Zagorskaya, S., and Firsov, S. (2006). Structural transformation of polysaccharides exposed to CO2-laser radiation. J. Appl. Spectroscopy 73, 178–188. doi: 10.1007/s10812-006-0055-7
Doran, J. W., and Zeiss, M. R. (2011). Soil health and sustainability: managing the biotic component of soil quality. Appl. Soil Ecol. 15, 3–11. doi: 10.1016/S0929-1393(00)00067-6
Duke, S. (2011). Why have no new herbicide modes of action appeared in recent years? Pest. Manage. Sci. 68, 505–512. doi: 10.1002/ps.2333
European Commission (2021). Available online at: https://ec.europa.eu/food/plants/pesticides/sustainable-use-pesticides/farm-fork-targets-progress_en (accessed January 26, 2022).
Fabbri, P., and Messori, M. (2017). “5 - Surface modification of polymers: chemical, physical, and biological routes” in Modification of Polymer Properties, eds C. F. Jasso-Gastinel and J. M. Kenny (Elsevier Inc.). doi: 10.1016/B978-0-323-44353-1.00005-1
FAO (2021). NSP–Weeds. Available online at: https://www.fao.org/agriculture/crops/thematic-sitemap/theme/biodiversity/weeds/en/ (accessed December 10, 2021).
Fennimore, S. (2014). The Role of Hand Weeding in Weed Management. UC Weed Science. Weed Control, Management, Ecology, and Minutia. Available online at: https://ucanr.edu/blogs/blogcore/postdetail.cfm?postnum=14405 (accessed June 24, 2014).
Ferraz, C., Mittal, G., Bilanski, W., and Abdullah, H. (2007). Mathematical modeling of laser based potato cutting and peeling. Biosystems 90, 602–613. doi: 10.1016/j.biosystems.2007.01.004
Gates, D. M., Keegan, H. J., Schleter, J. C., and Weidner, V. R. (1965). Spectral properties of plants. Appl. Optics 4, 11–20. doi: 10.1364/AO.4.000011
Gikunda, P., and Jouandeau, N. (2019). Modern CNNs for IoT based farms. arXiv. 1–12. doi: 10.1007/978-3-030-26630-1_7
Gonzalez-de-Santos, P., Ribeiro, A., Fernandez-Quintanilla, C., Lopez-Granados, F., Brandstoetter, M., Tomic, S., et al. (2017). Fleets of robots for environmentally-safe pest control in agriculture. Precision Agric. 18, 574–614. doi: 10.1007/s11119-016-9476-3
Harrison, J. L. (2011). Pesticide Drift and the Pursuit of Environmental Justice., Cambridge: MIT Press.
Heap, I. (2021). The International Herbicide-Resistant Weed Database. Available online at: www.weedscience.org (accessed January 14, 2022).
Heisel, T., Schou, J., Andreasen, C., and Christensen, S. (2002). Using laser to cut and measure thickness of Beta vulgaris L. and Solanum nigrum L. stems. Weed Res. 42, 242–248. doi: 10.1046/j.0043-1737.2002.00282.x
Heisel, T., Schou, J., Christensen, S., and Andreasen, C. (2001). Cutting weeds with CO2 laser. Weed Res. 41, 19–29. doi: 10.1046/j.1365-3180.2001.00212.x
Hitz, C. B., Ewing, J., and Hecht, C. (2012). Introduction to Laser Technology. 4th edition. Hoboken, NJ: IEEE Press, John Wiley & Sons, Inc. doi: 10.1002/9781118219492
Kaierle, S., Marx, C., Rath, T., and Hustedt, M. (2013). Find and irradiate — lasers used for weed control. Laser Technik J. 10, 44–47. doi: 10.1002/latj.201390038
Khan, M. J., Jurburg, S. D., He, J., Brody, G., and Gupta, D. (2020). Impact of microwave disinfestation treatments on the bacterial communities of no-till agricultural soils. Eur J Soil Sci. 71, 1006–1017. doi: 10.1111/ejss.12867
Klein, R. (2012). Laser Welding of Plastics: Materials, Processes and Industrial Applications. Weinheim: Wiley-VCH Verlag & Co.
Kolikov, T., and Koshlan, K. (2020). Laser Interaction with Heterogeneous Biological Tissue in Mathematical Modeling. Cham: Springer International Publishing A&G.
Kudsk, P., and Streibig, J. C. (2003). Herbicides a two edge-sword. Weed Res. 43, 90–102. doi: 10.1046/j.1365-3180.2003.00328.x
Marx, C., Barcikowski, S., Hustedt, M., Haferkamp, H., and Rath, T. (2012). Design and application of a weed damage model for laser-based weed control. Biosystems Eng. 113, 148–157. doi: 10.1016/j.biosystemseng.2012.07.002
Mathiassen, S. K., Bak, T., Christensen, S., and Kudsk, P. (2006). The effect of laser treatment as a weed control method. Biosyst. Eng. 95, 497–505. doi: 10.1016/j.biosystemseng.2006.08.010
Michalko, R., Pekár, S., Dul'a, M., and Entling, M. H. (2019). Global patterns in the biocontrol efficacy of spiders. A meta-analysis. Global Ecol Biogeogr. 28, 1366–1378. doi: 10.1111/geb.12927
Occupational Safety Health Administration. (2022). Laser Hazards. OSHA Technical Manual (OTM). Section III, Chapter 6. US Department of Labor. Available online at: https://www.osha.gov/otm/section-3-health-hazards/chapter-6 (accessed January 26, 2022).
Rakhmatulin, I., and Andreasen, C. (2020). A Concept of a compact and Inexpensive device for controlling weeds with laser beams. Agron. 10:1616. doi: 10.3390/agronomy10101616
Rakhmatulin, I., Kamilaris, A., and Andreasen, C. (2021). Deep neural networks to detect and classify weeds from crops in agricultural environments in real-time: A review. Remote Sens. 13:4486. doi: 10.3390/rs13214486
Ramahi, A. A., and Fathallah, F. A. (2006). Ergonomic evaluation of manual weeding practice and development of an ergonomic solution. Proc. Hum. Fact. Ergon. Soc. 2006, 1421–1425. doi: 10.1177/154193120605001335
Rask, A. M., and Kristoffersen, P. (2007). A review of non-chemical weed control on hard surfaces. Weed Res. 47, 370–380. doi: 10.1111/j.1365-3180.2007.00579.x
Rasmussen, J., Mathiasen, H., and Bibby, B. M. (2010). Timing of post-emergence weed harrowing. Weed Res. 50, 436–446. doi: 10.1111/j.1365-3180.2010.00799.x
Sharma, D. K., Tomar, S., and Chakraborty, D. (2017). Role of earthworm in improving soil structure and functioning. Curr. Sci. 113, 1064–1071. doi: 10.18520/cs/v113/i06/1064-1071
Sivesind, E., Leblanc, M., Cloutier, D., Siguin, P., and Stewart, K. (2009). Weed response to flame weeding at different development stages. Weed Res. 23, 438–443. doi: 10.1614/WT-08-155.1
Smith, D. L. O., and Dickson, J. W. (1990). Contributions of vehicle weight and ground pressure to soil compaction. J. Agri. Engineer. Res. 46, 13–29. doi: 10.1016/S0021-8634(05)80110-6
Sørensen, C. G., and Bochtis, D. D. (2010). Conceptual model of fleet management in agriculture. Biosystems Eng. 105, 41–50. doi: 10.1016/j.biosystemseng.2009.09.009
Streibig, J. C. (1988). Herbicide bioassay. Weed Res. 28, 479–484. doi: 10.1111/j.1365-3180.1988.tb00831.x
Symondson, W. O. C., Sunderland, K. D., and Greenstone, M. H. (2002). Can generalist predators be effective biocontrol agents? Ann. Rev. Entomol. 47, 561–594. doi: 10.1146/annurev.ento.47.091201.145240
Tamburini, G., Simone, S. D., Sigura, M., Boscutti, F., and Marini, L. (2016). Conservation tillage mitigates the negative effect of landscape simplification on biological control. J. Appl. Ecol. 53, 233–241. doi: 10.1111/1365-2664.12544
Tiwari, S., Sindel, B. M., Smart, N., Coleman, M. J., Fyfe, C., Lawlor, C., et al. (2021). Hand weeding tools in vegetable production systems: an agronomic, ergonomic and economic evaluation. Int. J. Agr. Sustainability. doi: 10.1080/14735903.2021.1964789. [Epub ahead of print].
Varanasi, A., Prasad, P. P. V., and Jugulam, M. (2016). Chapter three. Impact of climate change factors on weeds and herbicide efficacy. Adv. Agronomy 135, 107–146. doi: 10.1016/bs.agron.2015.09.002
Vitali, G., Francia, M., Golfarell, M., and Canavari, M. (2021). Crop management with the IoT: an interdisciplinary survey. Agron. 11:181. doi: 10.3390/agronomy11010181
Voorhees, W. B., Senst, C. G., and Nelson, W. W. (1978). Compaction and soil structure modification by wheel traffic in the Northern corn belt. Soil Sci. Soc. Amer. 42, 344–349. doi: 10.2136/sssaj1978.03615995004200020029x
Wang, A., Zhang, W., and Wei, X. (2019). A review on weed detection using ground-based machine vision and image processing techniques. Comput. Electron. Agric. 158, 226–240. doi: 10.1016/j.compag.2019.02.005
Wieliczka, D. M., Weng, S., and Querry, M. R. (1989). Wedge shaped cell for highly absorbent liquids: infrared optical constants of water. Appl. Optics 28, 1714–1719. doi: 10.1364/AO.28.001714
Witteman, W. J. (1987). The CO2 Laser. Springer Series in Optical Sciences. Berlin: Springer-Verlag.
Wolf, T. (2009). Best management practices for herbicide application technology. Prairie Soil Crop J. 2, 24–31. Available online at: https://prairiesoilsandcrops.ca/articles/volume-2-4-screen.pdf (assessed February 07, 2022).
Wöltjen, C., Haferkamp, H., Rath, T., and Herzog, D. (2008). Plant growth depression by selective irradiation with CO2 and diode laser. Biosystems Eng. 110, 316–324. doi: 10.1016/j.biosystemseng.2008.08.006
Keywords: alternative weed control, integrated weed management, non-chemical weed control, site-specific weed management, thermal weed control, weed killers
Citation: Andreasen C, Scholle K and Saberi M (2022) Laser Weeding With Small Autonomous Vehicles: Friends or Foes? Front. Agron. 4:841086. doi: 10.3389/fagro.2022.841086
Received: 21 December 2021; Accepted: 31 January 2022;
Published: 07 March 2022.
Edited by:
Ali Ahsan Bajwa, New South Wales Department of Primary Industries, AustraliaReviewed by:
Guy Coleman, The University of Sydney, AustraliaGraham Brodie, The University of Melbourne, Australia
Copyright © 2022 Andreasen, Scholle and Saberi. This is an open-access article distributed under the terms of the Creative Commons Attribution License (CC BY). The use, distribution or reproduction in other forums is permitted, provided the original author(s) and the copyright owner(s) are credited and that the original publication in this journal is cited, in accordance with accepted academic practice. No use, distribution or reproduction is permitted which does not comply with these terms.
*Correspondence: Christian Andreasen, Y2FuQHBsZW4ua3UuZGs=
†ORCID: Mahin Saberi orcid.org/0000-0003-1456-1119