- Laboratory of Industrial Chemistry and Reaction Engineering, Johan Gadolin Process Chemistry Center (PCC), Åbo Akademi, Turku, Finland
Throughout the decades, the solid–fluid processes have been modeled with the hypothesis of ideal, non-porous particles. Numerous relevant industrial reactions with reactive solids do not involve ideal slabs, spheres, or cylinders, but instead the particles have rough surfaces comparable of the Moon with cracks and craters. The theory of non-ideal solid particles is briefly reviewed and the effect of the non-ideality is illustrated for batch processes. In general, surface roughness results in the increase of the apparent reaction order with respect to the solid reactant.
Background: Classical Ideal Models for Reactive Surfaces
A few years ago, as the 2nd Edition of the textbook Chemical Reaction Engineering and Reactor Technology (2019) was prepared, the existing chapter devoted to reactive solids was revised and extended. To get inspiration, one of the authors (Salmi) of this article had a look at the newest edition of the monumental treatise of Pierre Trambouze and Jean-Paul Euzen, Les Réacteurs Chimiques, de la Conception à la Mise en Oeuvre (Trambouze and Euzen, 2002). However, the second edition of this excellent book did not anymore contain the chapter devoted to reactive solid materials. In the preface of the second edition, the authors explained that this particular chapter had been removed due to its low industrial importance for refineries and petrochemistry. It might be true.
However, reactive solids appear in numerous chemical processes—not only in the pure chemical industry, but in process industry in general. Let us think about the reactions which are applied in fine chemical and pharmaceutical industries in one corner, and reactions with minerals, leaching of ores, and combustion processes on the other side. The key issue is that the solid material undergoes dramatic changes during the progress of the process—not only chemically, but physically as well. Reactants are changed chemically to products, but structural changes of the solid particles take place simultaneously, which makes this sector of chemical reaction engineering particularly challenging, probably the most demanding field in contemporary reaction engineering.
The author's first contact to the field of reactive solids was in the marvelous reaction engineering course for undergraduates given at Åbo Akademi University by professors Leif Hummelstedt and Lars-Eric Lindfors—Kemisk reaktionsteknik (Hummelstedt and Lindfors, 1978). This elementary course for 3rd year undergraduates was mainly focused on ideal reactors and homogeneous systems. At the very end of the well-written course compendium, professor Hummelstedt had added a short chapter about reactive solids, a chapter which became for one of the current authors as a source of frustration at the first glance, because it is difficult to mechanically learn something which is not fully understood. Departing from the main line of the excellent lecture material, the authors had only put the final model equations concerning reactive solid materials, evidently to limit the volume of the compendium and to adapt to the very strict lecturing schedule. Famous equations relating the reaction time to the radius of a spherical solid particle and the overall conversion of the solid material were presented. The cases described were shrinking particles and particles with porous product layers (or ash layer as called in 1960's and 70's). The concept is illustrated by Figure 1.
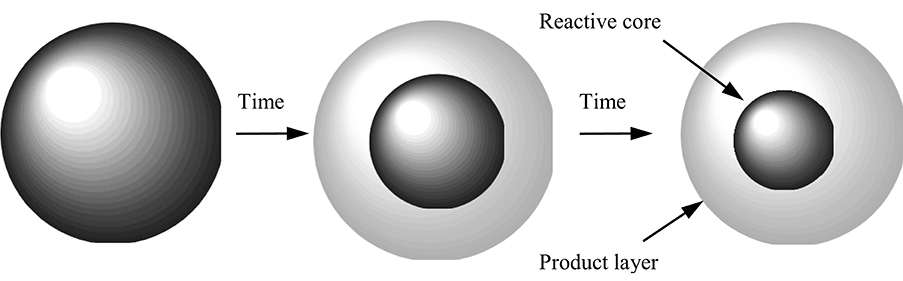
Figure 1. Product layer model. The shrinking particle model is obtained by removing the product layer from the figure.
The equations landed on the pages of the compendium without any derivation, but luckily, a good study circle of undergraduates provided a way out. We were often spending time in the undergraduate library of our university, in a beautiful historic Reuter's building. After screening the shelves in the library, some textbooks became a source of great inspiration. The first one was the classical, very condensed treatment of K.G. Denbigh and J.C.R. Turner: Chemical Reactor Theory (Denbigh and Turner, 1965). These scientists at the Universites of London and Cambridge presented the essentials of chemical reaction engineering in a condensed structure comprising around 200 pages. A special section was devoted to reactive solids, for shrinking particles and for particles with product layers (ash layers). Reading this book, one of the authors of this text got a feeling that everything was very clear, or at least understandable. The fundamentals of solid reactivity were presented so clearly by Denbigh and Turner that it was easy to understand the final equations in the domestic course compendium, which related the solid particle radius and conversion to the reaction time.
Later on, one of the authors of this article got contact to the classical textbook written by Octave Levenspiel—Chemical Reaction Engineering, the first edition of which appeared in 1962 by John Wiley & Sons. The theory of reactive solids was treated in a very precise and rigorous manner by Levenspiel, based on the product (ash) layer model of Yagi and Kunii (1955). The results are compressed to a generalized diagram presented in the book of Levenspiel (1999). The diagram can be used to judge, which one of the steps in a fluid–solid process—surface reaction, film diffusion or diffusion through the product layer—is rate determining. The experimental results can be put inside of the plot and verified before any extensive and advanced numerical calculations are undertaken.
The model equations which are the basis of the tests are collected in Table 1. It should be kept in mind that the equations listed in Table 1 are valid for conditions, where the fluid-phase component is in excess and its concentration in the bulk surrounding the solid phase is constant. Such circumstances prevail for instance in semibatch reactors with an excess of the liquid-phase reactant and in test reactors, where the solid particles are exposed to a high gas flow (i.e., in thermogravimetric equipment).
The classical theory of Yagi and Kunii (1955) and further developed by Levenspiel (1999) can rather easily be extended to cases, where all the three steps—film diffusion, product layer diffusion and surface reaction contribute to the overall rate of the process.
The generalized model equations are presented [e.g., by Salmi et al. (2019)]. For first-order kinetics with respect to the fluid-phase component, analytical solutions can be obtained which relate the particle radius and the reaction time. They are summarized in Table 2. By considering some limiting cases—chemical reaction or diffusion control—the equations presented in Table 1 can be acquired from the equations listed in Table 2.
For the general case that no one of steps alone is the rate limiting one, Equations (T6), (T7) can be used to get information about the rate controlling steps. The parameters Φ′, Φ″ and BiM can be conveniently estimated with non-linear regression analysis by using experimentally recorded t/τ vs. r/R data and the fit of models (T6) and (T7) can be compared.
The models discussed above were restricted to a unimodal particle size distribution, to one particle size, but particle size distributions can be incorporated in a rather straightforward way: each particle is assumed to have a similar behavior, and the particle size distribution is shifted downwards during the progress of the reaction. The treatment of particle size distributions in batch reactors is described for instance by Grénman et al. (2011).
Dilemmas to Be Surmounted: Toward Non-Ideal Models
Is there anything still to be developed further? The issues which have been discussed in this text so far, are based on the idea of completely ideal particles, spheres, long cylinders, and slabs. For instance, if we have a cylindrical particle like a very long pencil, then we need to calculate the lateral surface, but the ends of the cylinder can be neglected because they are so tiny in the proportion—or on the other hand, the reactive particles might be perfect non-porous spheres, as presented in classical texts. It is of course intuitively understood that this theory is a simplification, but the reality is sometimes different. Sohn and Szekely (1972) and Szekely et al. (1976) invented the theory of the grain model, with a structure of solids resembling raspberries or cloudberries, consisting of clusters of small particles which are in mutual contact through diffusion. This is the core of their theory, and a multitude of equations was developed based on the grain model. The theory has however not made any global breakthrough, even though it is a non-ideal model assuming different diffusion coefficients between the grains and inside the grains. Real reactive solid particles do not always fit to this kind of grain structures.
How do the real solid particles applied in industrial processes look? Microscopy provides the answer; there has been a tremendous leap in the technology of microscopy in the last decades. Particularly useful in this sense is Scanning Electron Microscopy (SEM), which provides a helicopter view of solid particle surfaces down to few micrometer resolution. What has been assumed to be an ideal particle with shape factors one, two, and three, for slab, cylinder, and sphere, is not the reality, but instead, it might resemble the moon landscape. It brings our memory to the landing of Apollo 11 on the moon surface in July 1969. The surface of our satellite has a lot of defects, such as cracks and craters. This implies that the actual surface area-to-volume ratio can be much higher than that predicted by ideal geometry as indicated by the samples displayed in Figure 2 (left 1–2: particles of mineral wool, right: particles in zinc leaching).
Another very useful experimental technique to be kept in mind is physisorption (i.e., the measurement of the solid surface area by nitrogen adsorption—a very well-established tool in the field of heterogeneous catalysis for the measurement of relatively large specific surface areas). Nowadays it is possible with the most modern gas adsorption technique to determine the surface areas of particles with a very low porosity, possessing specific surface areas of only a few square meters per gram. These materials could be characterized as non-porous or semi-porous. They have a low surface area and a very low amount of nitrogen adsorption, but modern equipment can still handle the small surface areas. In fact, solid particles of this kind deviate strongly from ideal geometry (Figure 1). The challenging issue with a non-ideal solid-phase is discussed in the newest edition of the authors' textbook (Salmi et al., 2019).
Classical chemical kinetics is a strong tool in the determination of the mechanisms of solid–fluid processes. In experimental devices, where a high degree of turbulence prevails around the solid particles, the resistance of film diffusion is suppressed, and if no product layer is formed since the product is dissolved or cracked away from the reactive surface, then the rate controlling step is the chemical process itself.
When we derive the rate equations for ideal solid geometries with respect to the amount of substance, or the concentration of the solid material measured in moles per liter, the reaction order is 1/2 for a long cylinder and 2/3 for a sphere. Reaction orders <1 imply that a complete conversion of the solid reactant is achieved within a finite reaction time (if the reaction order is zero with respect to the fluid component; Salmi et al., 2019), whereas for reaction orders equal to one and exceeding one, and from a theoretical point of view, an infinitely long reaction time is needed to attain a complete conversion.
A former experimental project in the authors' laboratory brought the dilemma of ideal particles in daylight, as the leaching of zinc was measured, and it was observed that the reaction order was completely different from 2/3 predicted by ideal spherical particles (Salmi et al., 2010). The particles were evidently neither perfectly non-porous nor perfect spheres. Furthermore, the reaction did not proceed to complete conversion. The young experimentalist of the project was interrogated about why the leaching kinetics remained pending and did not go to completion? Was there any problems with the analytical procedures? The experimental scientist believed in her results, so we decided to find an explanation. Some facts supported the experimental results: because of the surface defects, the ideal shape factor could not be successfully applied and the second fact was that a full conversion of the solid reactant was not obtained. Therefore, the reaction order was evidently higher than 2/3 for the solid reactant.
How to obtain a simple but realistic model for non-ideal solids so that the experimental observations could be described by a molecular-based but still simple mathematical model? The equations for the new approach were written down on a napkin: the basic idea was simply that the integer values for the shape factor in the reactivity equations were replaced with non-integer values. A non-integer shape factor can be related to the experimentally measured surface area of a solid particle. This model had the potential to explain many of our previously obtained experimental results. The first article combining the experimental facts and the theoretical approach was published (Salmi et al., 2011), taking also into account the formation of product layer and the shrinking particle, and consequently, new as well as old data were treated and updated with this model. Additionally, the model could take into account the particle size distribution. Later on, a fruitful collaboration with mathematicians of our university enabled us to publish a model for the shifting of the particle size distribution of the non-ideal particles, and the model was validated with industrially relevant cases (Grénman et al., 2011).
The basic concepts of the theory of non-ideal surfaces is summarized below. For the sake of illustration, a well-stirred batch reactor with equal particle sized solids in the liquid phase is presumed. For fluid–solid processes, the overall rate is assumed to be proportional to the accessible surface area (A). For a dissolved component (i) in a perfectly mixed, batchwise operated tank reactor, the balance equation can thus be written as
The specific rates (Rik) are expressed as mol/(m2s). The totally accessible surface area (A) is related to the number of particles (nP) and the specific surface area (σ), which can be measured with nitrogen adsorption.
The total area of accessible surface are of solid particles in the reactor is A,
while the volume of an individual particle is
where M and n denote the molar mass and the total amount of the solid substance, respectively. The number of particles can be obtained from the initial state (0) (i.e., at the start of the process),
from which the number of particles can be solved and inserted in Equation (2), which becomes
The area-to-volume ratio A0P/V0P is expressed by the shape factor (a) and the initial characteristic dimension of the particle (R0), a = (A0P/V0P)R0, which gives
The ratio AP/A0P obtains the following values for the ideal geometries: (R/R0)2 for a sphere, (R/R0)1 for an infinitely long cylinder, and (R/R0)0 for a slab. After expressing these ratios with the particle volumes we obtain (VP/V0P)2/3, (VP/V0P)1/2, and (VP/V0P)0 for the ideal geometries. The relation can be generalized to (VP/V0P)(a−1)/a for an arbitrary geometry. Consequently, the following relation between the area and the volume is obtained,
For a constant number of particles, the particle volumes and amounts of substance are related by
which is inserted in Equation (6):
The ratio a/R0 is
which is expressed with the original specific surface area (σ) of the particle
We have now
which is inserted in the expression of A, Equation (10):
If the mole fraction of the solid material is constant (x0j), the amounts of substance are n0j = x0jn0 (t = 0) and nj = x0jn (t > 0). After denoting 1/a = x and inserting these expressions in Equation (14), the total accessible area in the system becomes
For a long cylinder, x = 1/2 and for a perfect non-porous sphere, x = 1/3. Thus, the reaction orders (=1–x) 1/2 and 2/3 are predicted for these particles. For a slab, x = 1 and the observed reaction order approaches zero.
However, as the real particles deviate from the ideal ones, the accessible surface area for the chemical reactions easily become higher. Parameter x has in general the value x = 1/a, in which a >> 3 in cases that surface defects appear on the particle. This implies that effective reaction orders 2/31 < – x < 1 can be observed in practice. For porous particles, x is very small and first order kinetics with respect to the solid material is observed experimentally. This is evident when looking at the numerical values presented in Table 3.
Two observations are important: the effective reaction order (1 – x) increases with the particle size and with the specific surface area and quite quickly, it approaches one with respect to the solid component, which explains that sometimes the kinetics remains “pending” (i.e., a complete conversion of the reactant is not achieved).
Example: Single Fluid–Solid Reaction in a Batch Reactor
A simplified case with a single chemical reaction and chemical reaction control is considered here, as well as the reaction order (n) with respect to the fluid phase component (i). The reaction rate expression is
For a well-stirred batch reactor, the mass balance of a solid component (j) can be written in the form (Salmi et al., 2019),
For a liquid-phase component (i) is obtained,
Very often the component concentrations are used in the treatment of the mass balances.
For the liquid-phase components, the use of concentrations is evident. The amount of substance (ni) is divided by the fluid volume (VL). Formally a similar definition of the concentration can be applied to the solid component, too. If the volume of the fluid phase is virtually constant, the balance equations become after division by the fluid volume,
The term is constant throughout the reaction, while the concentration cj varies. The experimentally observed reaction order thus depends on the particle geometry (x = 1/a).
After inserting the rate expression (16) in the mass balances (19) and (20) and introducing a dimensionless Damköhler number (Da),
the balance equations obtain the forms displayed below,
where λ = νi/νj. The dimensionless concentrations (y) can be easily simulated numerically in the Damköhler space. Moreover, for the simplified case that λ = 1 and equimolar initial amounts of the components are used, yi = yj = y leads to the simple differential equation,
The differential equation is solved by separation of variables and integration. The initial condition y = 1 at Da = 0 is valid. The solution becomes,
for n ≠ x and,
for n = x.
Two special cases are of particular interest: the reaction is of zero order or first order with respect to the fluid-phase component. After inserting the values n = 0 and n = 1 and recalling that x = 1/a, the corresponding solutions for zero and first order kinetics are obtained as follows.
For n = 0:
For n = 1:
a ≠ 1
a = 1 It is very interesting to consider the limit behavior of the model for highly non-ideal particles, for which parameter a, the shape factor can obtain high values because of the surface defects.
For n = 0, the function in Equation (26) approaches the exponential function for high values for a → ∞,
which de facto implies that first order kinetics is observed. On the other hand, for n = 1 and a → ∞, the limit case of Equation (27a) becomes
which corresponds to second order kinetics.
Numerical simulations of model Equations (26), (27) are provided in Figure 3, which reveals the very strong effect of the shape factor on the kinetics. The simulations displayed in the figure illustrate, why the reaction orders based on ideal geometries such as slab (a = 1), cylinder (a = 2), and ideal spheres (a = 3) do not describe the behavior of non-ideal particles, because non-linear particles regularly show a higher reaction order with respect to the solid component than the ideal ones. This implies that a complete conversion of the solid reactant is typically not achieved in real experiments with non-ideal solid particles.
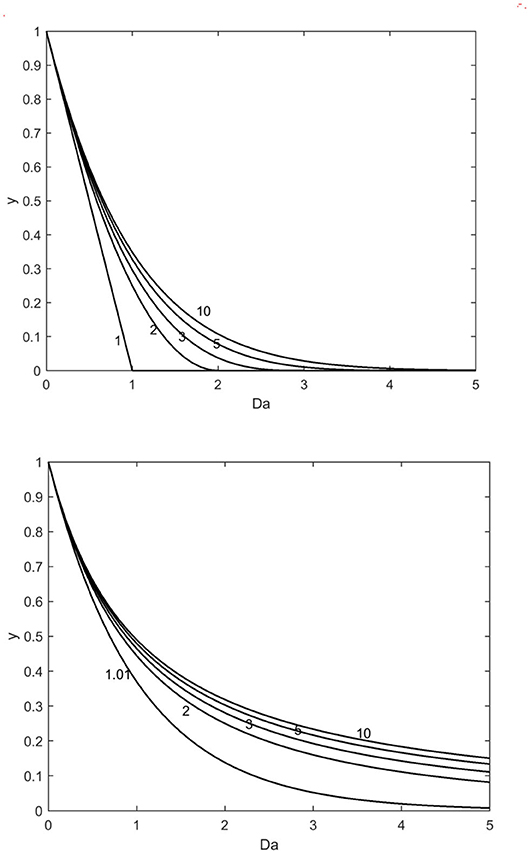
Figure 3. Numerical simulations of models (26) (upper) and (27) (lower) in Damköhler space (Da); simulation parameter: shape factor (a = 1, 2, 3, 5, and 10 in the figures).
Conclusions and Future Perspectives
The approach presented in this article enables to describe the kinetics of non-ideal solids with surface defects and, in the ultimate case, the model approaches the model for completely porous particles. The main benefit is that the reaction kinetics close to first order with respect to the solid material can be predicted by the model. Only one parameter, the shape factor is needed to take into account the non-ideality. Furthermore, the value of the shape factor can be obtained from measurable quantities (particle density, surface area, and characteristic thickness) as summarized in Table 3. For processes, where the specific surface area changes during the progress of the reaction, the shape factor can be updated as a function of time, but that requires experimental, time-dependent data on the specific surface area. The main benefit of including non-ideality is to get better kinetic models which do not have systematic deviations from the experimental data. The improved modeling approach presented by us might be beneficial in process scale-up.
New perspectives should be discussed—where shall we go in future? A multitude of fluid-solid processes are conducted not only in batch reactors, but they appear in continuous reactors, where particles enter the system, they react and leave the reactor vessel. There, we approach the theories of crystallization, but in a reversed manner. We do not only have a stagnant particle size distribution, but the population balances will be included, because particles which exceed a specific size, or go below it, are not only created by the solid-liquid or solid-gas reaction, but they are also influenced by the inflow and outflow. Theories of non-ideal particles, particle size distributions in dynamic forms, population balances, and flow models are needed in future. The dream is to have kinetic models, particle size distributions, and population balances coupled to the most modern approach to computational fluid dynamics. With such a sophisticated multiscale approach, the behavior of sophisticated gas-liquid-solid processes could be predicted and optimized, from the treatment of minerals to fine chemistry.
The main benefit of including non-ideality is to get better kinetic models which do not have systematic deviations from the experimental data. The improved modeling approach presented by us might be beneficial in process scale-up.
Data Availability Statement
The raw data supporting the conclusions of this article will be made available by the authors, without undue reservation.
Author Contributions
TS and PT wrote the 1st version of the manuscript. JW made the computations. All authors took part in the final editing of the manuscript.
Funding
This work is part of the activities financed by Academy of Finland, the Academy Professor Grants 319002 (TS) and 320115 (PT).
Conflict of Interest
The authors declare that the research was conducted in the absence of any commercial or financial relationships that could be construed as a potential conflict of interest.
Acknowledgments
The economic support is gratefully acknowledged.
References
Denbigh, K. G., and Turner, J. C. R. (1965). Chemical Reactor Theory, 1st Edn 1965, 2nd Edn 1971. Cambridge: Cambridge University Press.
Grénman, H., Ingves, M., Wärnå, J., Corander, J., Murzin, D., and Salmi, T. (2011). Common potholes in modeling solid–liquid reactions—methods for avoiding them. Chem. Eng. Sci. 66, 4459–4467. doi: 10.1016/j.ces.2011.04.022
Levenspiel, O. (1999). Chemical Reaction Engineering, 1st Edn 1962, 2nd Edn 1972, 3rd Edn 1999. New York, NY: John Wiley and Sons.
Salmi, T., Grénman, H., Bernas, H., Wärnå, J., and Murzin, D. (2010) Mechanistic modelling of kinetics mass transfer for a solid–liquid system: leaching of zinc with ferric iron. Chem. Eng. Sci. 65, 4460–4471. doi: 10.1016/j.ces.2010.04.004
Salmi, T., Grénman, H., Wärnå, J., and Murzin, D. (2011). Revisiting shrinking particle and product layer for fluid-solid reactions—from ideal surfaces to real surfaces. Chem. Eng. Process. Process Intensif. 50, 1076–1094. doi: 10.1016/j.cep.2011.05.015
Salmi, T. O., Mikkola, J.-P., and Wärnå, J. P. (2019). Chemical Reaction Engineering and Reactor Technology, 1st Edn (2011), 2nd Edn (2019). Boca Raton, FL: CRC Press Taylor & Francis Group. doi: 10.1201/9781315200118-1
Sohn, H. Y., and Szekely, J. (1972). A structural model for gas–solid reactions with a moving boundary—III: a general dimensionless representation of the irreversible reaction between a porous solid and a reactant gas. Chem. Eng. Sci. 27, 763–778. doi: 10.1016/0009-2509(72)85011-5
Szekely, J., Evans, J. W., and Sohn, H. Y. (1976). Gas–Solid Reactions. New York, NY: Academic Press.
Trambouze, P., and Euzen, J.-P. (2002). Les Réacteurs Chimiques, de la Conception à la Mise en Oeuvre.
Yagi, S., and Kunii, D. (1955). Studies on fluidized-solids reactors for particles with decreasing diameters. Chem. Eng. Jpn. 19:500. doi: 10.1252/kakoronbunshu1953.19.500
Notation
Keywords: fluid-solid, kinetics, morphology, non-ideality, modeling
Citation: Salmi T, Wärnå J and Tolvanen P (2020) Understanding of Solid-Fluid Kinetics and Mass Transfer: From Ideal to Non-ideal Models, From Perfect Spheres to Moon Landscape. Front. Chem. Eng. 2:6. doi: 10.3389/fceng.2020.00006
Received: 23 April 2020; Accepted: 06 July 2020;
Published: 14 August 2020.
Edited by:
Jorge Norberto Beltramini, Queensland University of Technology, AustraliaReviewed by:
Arne Reinsdorf, Evonik Industries, GermanyHeather Trajano, University of British Columbia, Canada
Copyright © 2020 Salmi, Wärnå and Tolvanen. This is an open-access article distributed under the terms of the Creative Commons Attribution License (CC BY). The use, distribution or reproduction in other forums is permitted, provided the original author(s) and the copyright owner(s) are credited and that the original publication in this journal is cited, in accordance with accepted academic practice. No use, distribution or reproduction is permitted which does not comply with these terms.
*Correspondence: Tapio Salmi, dGFwaW8uc2FsbWlAYWJvLmZp