- Laboratory of Catalysis and Catalytic Processes, Dipartimento di Energia, Politecnico di Milano, Milano, Italy
Structured catalysts are strong candidates for the intensification of non-adiabatic gas-solid catalytic processes thanks to their superior heat and mass transfer properties combined with low pressure drops. In the past two decades, different types of substrates have been proposed, including honeycomb monoliths, open-cell foams and, more recently, periodic open cellular structures produced by additive manufacturing methods. Among others, thermally conductive metallic cellular substrates have been extensively tested in heat-transfer limited exo- or endo-thermic processes in tubular reactors, demonstrating significant potential for process intensification. The catalytic activation of these geometries is critical: on one hand, these structures can be washcoated with a thin layer of catalytic active phase, but the resulting catalyst inventory is limited. More recently, an alternative approach has been proposed, which relies on packing the cavities of the metallic matrix with catalyst pellets. In this paper, an up-to-date overview of the aforementioned topics will be provided. After a brief introduction concerning the concept of structured catalysts based on highly conductive supports, specific attention will be devoted to the most recent advances in their manufacturing and in their catalytic activation. Finally, the application to the methane steam reforming process will be presented as a relevant case study of process intensification. The results from a comparison of three different reactor layouts (i.e. conventional packed bed, washcoated copper foams and packed copper foams) will highlight the benefits for the overall reformer performance resulting from the adoption of highly conductive structured internals.
1 Introduction
The continuous increase in environmental sustainability awareness demands for an urgent and radical change in the approach to chemical processes. In this view, process intensification has been widely recognized as the most valuable solution to improve the overall efficiency of energy intensive chemical processes, as well as the most promising route for the scale-down of processes for the distributed production of chemicals and energy vectors, including e.g. H2 production. However, the approach is not trivial and requires the design of innovative catalytic reactor concepts. In this work, a detailed and up-to-date review of these topics is proposed. After a preliminary focus on the recent advances of the production processes of geometric structured supports based on metallic materials, an overview on their activation procedures will be presented. Finally, a practical application of all the reported concepts and findings will be provided by discussing the most recent approaches to the intensification of the methane steam reforming (MSR) process.
2 Metallic Substrates for Process Intensification
2.1 Monolithic Three-Dimensional Geometric Supports
In this paragraph, a review of the state of the art of monolithic three-dimensional geometric supports for catalytic applications is reported. We focus on metallic supports in form of honeycomb monoliths, open cell foams and periodic open cellular structures (POCS), and devote special attention to the case of highly conductive materials (e.g. copper and aluminum).
2.1.1 Honeycomb Monoliths
Honeycomb monoliths supports are mechanically and thermally continuous structures consisting of thin-walled, narrow and parallel channels where reactants can flow; the channels have usually a square cross section for ceramic honeycombs with openings in the range of 0.5 up to few millimiters; other shapes as triangles, hexagons and more complex geometries are also available (Baharudin and Watson, 2018). When dealing with metallic supports, sinusoidal channels are produced via the rolling of shaped metallic foils; resulting support show channels with 0.5–5 mm diameters. In various applications, due to low Reynolds numbers, the flow is laminar inside the channels and this results in limited pressure drops, which are typically one or two orders of magnitude smaller compared to packed bed configurations operated under the same conditions. Since in these structures each channel is segregated, no radial mixing occurs.
For the considered channel shape, it is possible to fully characterize the monoliths by two key parameters, namely the “CPSI”, i.e. the number of channels per square inch, and the open-frontal area (OFA), that is the ratio between the area available for gas flow and the whole cross section of the monolith (Hosseini et al., 2020). Typically, CPSI varies between 100 and 1,200, while the void fraction ranges from 0.5 to 0.9. Monoliths offer a high specific geometric surface area in the range of 1,000–5,000 m−1 that enhances both mass and heat transfer rates, thus enabling the design of compact reactors (Baharudin et al., 2020).
Honeycomb monoliths have represented for decades the State of the Art of heterogeneous supported catalysts, finding extensive applications in several processes for environmental protection such as exhaust gas treatment, selective catalytic reduction (SCR) of NOx, catalytic combustion and abatement of volatile organic compounds (Avila et al., 2005; Govender and Friedrich, 2017). Very large surface area and the peculiar geometry of honeycombs is also interesting in the case of GTL applications where, as an example, a small film of liquid flows on the surface of the reactor and the gas diffuses in the liquid film (Cybulski and Moulijn, 2006). Materials and production processes of metallic monoliths are industrially well consolidated and restricted to a limited number of technologies, i.e. extrusion or rolling of flat and corrugated foils (see Figure 1). The corrugation method has been widely studied and it allows creating a variety of complex geometries. Because of the production process, however, those supports display a worse effective radial thermal conductivity, if compared to extruded metallic monoliths, due to the lack of material continuity in the radial direction as documented by Amalraj et al. (Amalraj et al., 2019). On the other hand, extruded metallic monolith show excellent thermal conductivity if manufactured in conductive metals (i.e. copper, aluminum), as demonstrated by studies conducted in our group in the last decades (Tronconi et al., 2004; Visconti et al., 2009) with thermal conductivities in excess of 20 W/m/K. Nevertheless, the extrusion route for the production of metallic monoliths is complex and discourages the adoption at industrial scale.
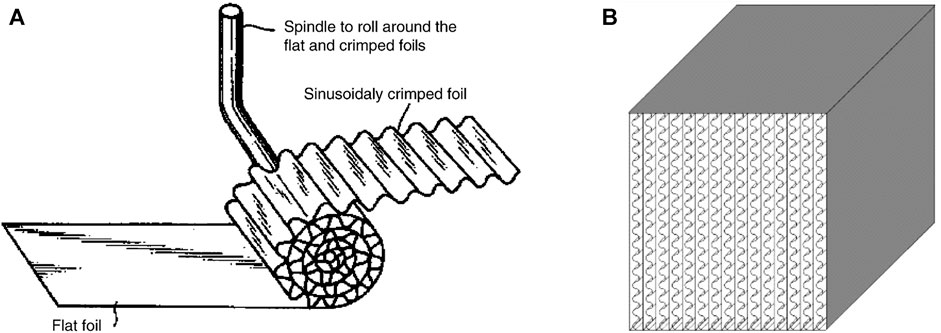
FIGURE 1. Example of monolith construction by rolling around a spindle (A) and piling up alternates flat and crimped foils (B) (adapted from (Avila et al., 2005)).
Despite the consolidated scenario of monoliths manufacturing, the recent development of 3D-printing techniques has paved the way to new routes for the manufacturing of a large variety of structured supports. This represents an opportunity for enabling a new production approach for honeycomb monoliths. As an example, Davó-Quiñonero et al. proposed a honeycomb-like structure fabricated using a template prepared by 3D printing, characterized by the presence of asymmetrical channels, with the channels section decreasing along the monolith axis (Davó-Quiñonero et al., 2019). Given the relative novelty of the topic, only a limited number of studies are available in literature concerning metallic supports. In this sense, Agueniou et al. successfully produced stainless-steel honeycomb monoliths that were tested in the dry reforming of methane, showing competitive performance with respect to traditional cordierite supports (Agueniou et al., 2021).
2.1.2 Open Cell Foams
Open-cell solid foams are objects consisting of interconnected ligaments (i.e. struts), which form a complex network of void polyhedrons, defined as cells (Figure 2A). The repetition of randomly oriented unit cells in the space provides self-standing mechanical properties to the structure, while the presence of pores, namely the communication windows between two cells, allows fluid flow throughout the material in the three directions of space. While open cell foams are commercially classified based on the number of pores per linear inch (PPI), other parameters are crucial to precisely characterize the properties of these supports. Cell size and pore size, strut diameter and structure porosity (ε) are widely considered the specifications of interest to characterize the geometrical properties of open cell foams. Whereas the latter is an average diameter taken over a representative elementary volume (REV), typically a cube with at least a size equal to three cell sizes, cells and pores are average values subject to a distribution. Based on these parameters, several models are available in literature to determine the geometric surface area (Sv, m−1) and other properties of interest (Inayat et al., 2011a). Porosity and surface area can be also quantified performing detailed µ-CT scans of the samples to provide a 3D reconstruction of the foam geometry. Generally, for commercial foams, cell sizes in the range [0.5–5 mm], porosities in the range of [0.75–0.9] for ceramic substrates [0.85–0.96] for metallic substrates and surface to volume ratios in the range [300–5,000 m−1] have been reported. As already reported for honeycombs, a high surface area of the support promotes gas/solid heat and mass transport, at the expenses of pressure drops (Das et al., 2018).
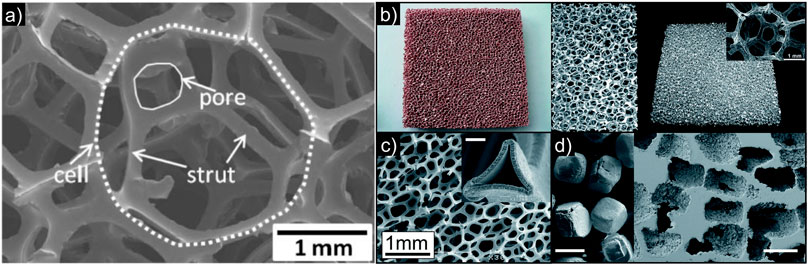
FIGURE 2. High-magnification detail of the cell structure of an open cell foam (A) (Zhang et al., 2012)). Examples of open cell foams: Duocel® copper and aluminum based foams (B), Incofoam® nickel foam prepared by replication technique (C) and titanium open porous material prepared with the space holder approach (D) (Kränzlin and Niederberger, 2015).
Metallic open cell foams are considered lightweight but stiff structures, with excellent thermal, mechanical and acoustic properties (Lu et al., 1998). Based on these features, these materials are valuable candidates to be implemented in several industrial applications (e.g. heat exchangers, thermal energy absorbers, vaporizers, and etc.). In view of their high porosity and high surface to volume ratio, open cell foams have gained popularity as innovative internals in fiof heterogeneousxed bed catalytic reactors (Bianchi et al., 2013), enabling high activity per unit volume (Giani et al., 2005; Bracconi et al., 2018b). Moreover, due to the complex support geometry that promotes interaction with the fluid flow, external (fluid-solid) mass transfer resistances are limited (Richardson et al., 2000) and, at the same time, radial heat transfer is high thanks to the conductive and continuous structure (Bianchi et al., 2012). Foams exhibit effective thermal conductivities up to 10 W/m/K if Aluminum is employed and up to 20 W/m/K for copper materials (Aghaei et al., 2017; Bracconi et al., 2018a). This determines an improvement in gas/solid heat and/or mass-transfer rates with respect to honeycombs, and a boost in the effective heat transfer rates for non-adiabatic processes that require heat exchange with reactor walls, with a minimal increase in pressure drops. Thus, this results in limited temperature gradients and reduced hot/cold spots in highly exo/endothermic processes (Giani et al., 2005). For the case of mass transfer limited applications, open cell foams, for the same surface areas, grant higher gas/solid mass transfer rates at the expense of higher pressure drops. Nevertheless, by comparing samples with a dimensionless index, open cell foams with high porosityexhibit similar performances providing additional advantages in the design of compact devices. Applications of foams also for GTL processes have been reported by Busser et al. (Busser et al., 2020).
Open cell foams are typically produced in the form of monolithic pieces which can be manufactured by different production processes (Banhart, 2001; García-Moreno, 2016). Among others, the use of a template structure is one of the most popular manufacturing approach. The template is usually made of polymeric materials and is used either for the preparation of a castable mold (e.g. replication by investment casting) or for the deposition of the metal directly onto the polymeric sponge, followed by the removal of the polymeric backbone (Goodall and Mortensen, 2014; Kränzlin and Niederberger, 2015). In the casting process, at first polymeric foam voids are filled with a ceramic compound; then, after polymer removal, the ceramic structure is used as a mold, and is infiltrated by the melted metal. When the ceramic material is removed, a perfect metal copy of the starting polymeric foam is thus obtained. On the contrary, straight metal deposition onto the polymer surface is usually performed in two steps: first, the polymeric foams is coated by using physical vapor deposition (PVD), in order to make it conductive; then, a thick metallic layer is formed by electroplating and, finally, the polymer is removed by heating (Paserin et al., 2004). In the latter case, hollow struts are typically obtained (Figure 2C).
More recently, an alternative approach has been proposed, which consists in the combination of sponge replication and freezing techniques using PU templates for the production of porous open-cell copper foams using an aqueous copper dispersion (Sutygina et al., 2021). Foams were effectively produced, and the relevance of processing conditions (temperature and atmosphere) on final structure properties was thoroughly discussed. A simplified method was also proposed by Sutygina et al., who reported the production of aluminum open cell foams by the replica process using an aqueous aluminum-based slurry (Sutygina et al., 2019) and assisted by vacuum (Sutygina et al., 2020b).
Another method for open-cell foams production is based on the use of space holders (Figure 2D). The latter are individual particles of different shapes and materials (sodium chloride, carbonates, sugar, or metals); they must provide a percolating network throughout the body in order to be efficiently removed, thus creating the strut pores. By using this technique, macroscopic bodies with a controllable average cell size can be produced (Kränzlin and Niederberger, 2015).
Some of the manufacturing methods reported so far (i.e. investment casting and space holder techniques) have been reviewed and compared to the sponge replica process, for the production of aluminum and copper open cell foams (Sutygina et al., 2020a). Recently, Liu et al. proposed an alternative approach for the production of copper-based internals for the manufacturing of methanol steam reforming micro-reactors (Liu et al., 2019). It consisted in a laser processing method to fabricate the copper foams with hole arrays, determining an improvement of the radial distribution uniformity and an increase of the axial flow rates of the reactants under reaction conditions.
The recent advances in additive manufacturing and in computational capability allowed a change in the paradigm of the investigation of the fundamental properties of open cell foams. Accordingly, numerical methods for the generation of virtual foam structures have been proven to reproduce the geometrical properties of real foams samples, starting from a few pieces of geometrical information, e.g. the cell diameter and the void fraction (Bracconi et al., 2017). Thus, such models were effectively 3d-printed and tested in a comprehensive investigation of pressure drops, using a combined numerical (CFD)/experimental approach. A very good agreement between the simulations and experimental data was demonstrated, revealing the individual effects of the geometrical properties such as cell size, porosity and strut shape on the pressure drop, which can be hardly isolated in experimental studies of physical foam samples (Bracconi et al., 2019).
2.1.3 Additive Manufacturing of Geometric Supports
The recent advances in additive manufacturing technologies paved the way as well to a new generation of structured supports, namely periodic open cellular structures (POCS) (Lawson et al., 2021). The building block of the structure consists in a unit cell with well-defined three-dimensional geometry (Figure 3A), which is periodically repeated in space to form a self-standing ordered object. Examples of additively manufactured POCS are shown in Figure 3B. At the present time, the use of additive manufacturing for the production of geometric supports with tailored properties is a hot research topic, which is stimulating a strong research activity in the field. Detailed reviews are available, providing general information on the stages of the 3D printing process, 3D printing methods, and applications in the field of heterogeneous catalysis (Hurt et al., 2017; Soliman et al., 2020; Laguna et al., 2021; Lawson et al., 2021; Mooraj et al., 2021).
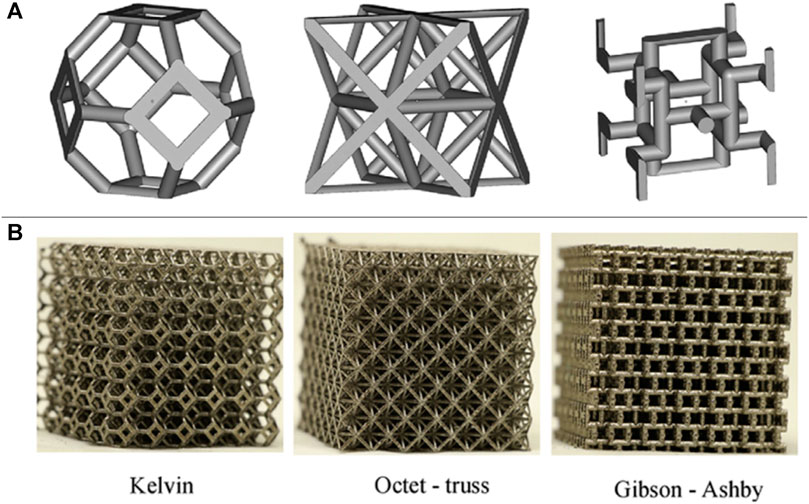
FIGURE 3. Examples of different unit cells (A) and steel-based 3D printed (B) POCS based on the same unit cells (adapted from (Al-Ketan et al., 2018))
This innovative production approach enables a remarkable freedom to operate in terms of management of the support properties, which allows tuning cell shape, orientation and size, as well as porosity, strut size, and overall dimension with high accuracy (Inayat et al., 2011b; Bianchi et al., 2016). In comparison to open cell foams, the design flexibility and the accuracy in morphology control represent one of the major advantages of POCS (Laguna et al., 2021). This enables the possibility to tune the topology of the object aiming at solving some of the most crucial issues of catalyst supports, namely mass transfer and, thanks to the high thermal conductivity of the bulk material, heat transfer (Busse et al., 2018; Papetti et al., 2018; Bracconi et al., 2020; Ferroni et al., 2021). These structures can be also used for GTL processes, as recently demonstrated by Littwin and co-workers (Littwin et al., 2021).
Among the large variety of geometries, triply periodic minimal surfaces (TPMS) represent the latest advances in additive manufacturing for the production of tailored geometric supports (Al-Ketan et al., 2018). A TPMS can be defined as a single, continuous, smooth and periodic arrangement of surfaces. The architecture construction takes place from a single surface that is replicated in the three-dimensional space until forming a sample of the desired overall dimensions; due to the generation approach, space is thus divided into two interwoven domains (Pelanconi and Ortona, 2021). The mathematically-generated and dimensionless TPMS is then converted into a proper lattice, by means of either a strut-based or a sheet-based approach (Kapfer et al., 2011). In the first case one domain is filled with solid, while the other is left empty. In the second case, the surface is thickened, thus determining the formation of two separate empty domains (Pelanconi and Ortona, 2021). Such supports have been proposed at first in ceramic form for catalytic applications (Al-Ketan et al., 2019), but evidence of their production in steel was reported by different research groups (Zhao et al., 2018; Feng et al., 2019). Among others, Baena-Moreno et al. demonstrated the effectiveness of TPMS in the highly exothermic CO2 methanation process (Baena-Moreno et al., 2021). In comparison to additively manufactured monoliths with parallel channels, TPMS demonstrated enhanced catalyst performance regarding CO2 conversion and selectivity, thanks to the higher turbulence and the improved heat transfer conductivities. Additionally, Zhou at el. (Zhou et al., 2020) designed a functionally graded scaffold based on TPMS, with programmable pore size distribution features. These structures were effectively modelled and additively manufactured using a titanium alloy.
In view of the large variety of available geometries, many different additive manufacturing techniques have been successfully tested for 3D printing metallic structures (Zhang et al., 2018), such as selective electron beam melting (SEBM) (Körner, 2016), selective laser melting (SLM), investment casting (Anglani and Pacella, 2018), binder jetting, robocasting (Danaci et al., 2016; Danaci et al., 2018), and combined 3D printing-replica.
SEBM and SLM techniques enable the production of metallic structures using a high-energy laser beam; the laser is pointed to a powder bed and metallic particles are melted/sintered into a solid structure (Zhou and Liu, 2017; Parra-Cabrera et al., 2018). Various materials have been successfully tested, such as stainless steel (Lefevere et al., 2013), FeCrAlY (Rombouts et al., 2006; Stiegler et al., 2019), titanium (Klumpp et al., 2014), copper (Guschlbauer et al., 2018), and aluminum (Bastos Rebelo et al., 2018; Aboulkhair et al., 2019; Lind et al., 2020). In particular, Klummp et al. produced Ti-6Al-V4 cubic cell POCS by SEBM (Klumpp et al., 2014); structures of different porosities were effectively produced, and the influence of cell sizes, porosities and tilt angle on pressure drops was assessed. In a similar way, Knorr et al. used the same process for the preparation of POCS structures, which were tested for the catalytic hydrogenation of ethane (Knorr et al., 2012). Steel alloy structures produced by SEBM were also tested for the investigation of heat transfer in liquid flow (Hutter et al., 2011), as well as of mass transfer in gas/liquid applications (Cai et al., 2016; Lämmermann et al., 2016). While the SEBM/SLM techniques have been demonstrated to be industrially ready for many materials (i.e. aluminum and titanium alloys, stainless steel), some limitations are still present in the case of highly conductive metals (e.g. copper), with constraints in terms of printable details and geometries.
The high intensity energy issues related to SEBM/SLM techniques are typically overcome by the binder jetting process, which applies the paradigms of the traditional 2D printing to the development of three-dimensional objects. In this process, the final object is obtained by a layer-by-layer selective deposition of a liquid binder onto a powder beds of precursors materials, such as ceramics (Lv et al., 2019), stainless steel (Mirzababaei and Pasebani, 2019; Lecis et al., 2021) and copper (Bai and Williams, 2015). Thanks to the powder-liquid interaction, the cross section of the object is produced; after the removal of excess powder, the final structure is obtained by thermal treatment, to remove the binder components and to sinter the metal framework (Ziaee and Crane, 2019).
The aforementioned powder-based printing methods use a layer-by-layer methodology that is characterized by critical issues, namely the presence of large amounts of powder, which imply safety issues fort materials handling, and the transition through a molten metal phase. In the first case, post-build powder removal from the empty volumes of the structures may be complex, due to powder agglomeration and to the ductility of the metal. Moreover, the presence of small sized metal particles calls for special handling and storage procedure, due to the high sensitivity to oxidation which may also determine the release of remarkable quantities of energy in relatively short time (i.e. explosive dust aerosols) (Tran et al., 2019). As far as metal melting is concerned, critical issues may arise, especially when highly conductive metals are used. High local thermal gradients may be present due the high thermal conductivity, and this may determine the generation of local defects, such as layer curling and delamination (El-Wardany et al., 2018). Moreover, a significant shrinkage may occur in the sintering process, since powder grains need to melt to form a continuous matrix; in this regards, the design of the sample is subject to a careful preliminary study of the potential shrinkage in the three directions.
Investment casting is an alternative manufacturing approach to overcome such technological limits. In literature, 3D structures with struts diameters ranging from 0.4 to 1 mm were effectively produced, with porosities up to 93% (Anglani and Pacella, 2018). Due to the use of molten metals, investment casting allows decreasing the residual roughness of printed object, which is usually in the same range of metal particle size for powder-based techniques. Despite the overall good printing performance, the maximum object dimensions and minimum printable strut size represent the most remarkable constraints of this technique.
Robocasting is another powder-free approach to 3D-printing of metallic structures, which is based on the extrusion of a metal/metal oxide paste through a nozzle. The thus obtained self-standing structure is thermally treated to remove solvents and binders, and to promote the sintering of metal powders. Copper and stainless steel structures were successfully printed by robocasting (Danaci et al., 2018); nevertheless, the methodology provides clear limitations in the geometry of the samples that can be printed, as well as in the resolution of details.
An alternative approach that allows overcoming many of these limitations consists in the combination of 3D printing and replica techniques in a two-steps approach. First, additive manufacturing, namely stereolithography (SLA), is used to produce high resolution resin structures, with details up to 25 µm and fibers in the range 200–500 µm (Bracconi et al., 2019). Then, the replica process is used: the polymeric structure is coated with a powder slurry of the final desired material and, subsequently, the polymeric template is removed by thermal treatment. This approach represents a good compromise between cost, time and effectiveness, especially when the production of small batches is required. Recently, this procedure has been investigated successfully for the production of copper POCS with controlled geometry, demonstrating the possibility to produce almost defect-free materials with a strut size of 500 μm (Balzarotti et al., 2020b).
Despite the interesting possibilities enabled by 3D printing towards optimization of the catalyst supports, still limited applications are found in the literature. This may be due partly to the lack of confidence of major industrial players towards these technologies and to the still limited possibilities in terms of size that can be allowed by 3D printing. Instead, for small scale systems, 3D printing is starting to offer interesting potential as an enabling technology, as recently presented by Grande and coworkers (Grande and Didriksen, 2021).
2.2 Strategies for the Catalytic Activation of Structured Supports
All the structured supports reported so far are typically not catalytically active. Thus, activation strategies are required to disperse effectively the catalytic active phase on the surface of the supports. Among others, electrochemical deposition, spray-based techniques, chemical vapor deposition (CVD) and slurry coating have been extensively studied and reported in recent reviews (Mehla et al., 2019; Palma et al., 2019).
Electrochemical-based deposition processes allow depositing a metallic coating on a substrate by using an ionic solution under electric current. This method was found to be particularly effective for the functionalization of high porosity open cell foams (Ho et al., 2019). In chemical vapor deposition (CVD), the support is coated by chemical reaction with a gas-phase precursor of the material to be deposited and the process is typically run at low pressure and high temperature (Serp et al., 2002). More in general, spraying-based methods employ dispersion liquids containing the catalytic medium in form of nanoparticles, which are deposited by spraying onto different supports to obtain catalytically active structured catalysts. Spraying the liquid with active nanoparticles onto different supports is a relatively facile method, but the preparation of the “active” liquid based on catalyst nanoparticles is complicated and expensive (Wang Z. et al., 2019).
In all the methodologies reported so far, the complexity of the process induces some limitations to large-scale production. In this view, activation procedures based on slurry coating are widely considered the best compromise in terms of versatility, scalability, cost-effectiveness, and flexibility. In this procedure, the catalytic material is first dispersed in a liquid medium, aiming at obtaining a stable catalytic slurry. Then, the slurry is deposited onto the surface of the structured support. Dip coating is typically used in this stage, resulting in a consolidated methodology for flat surfaces. As far as porous supports are concerned, liquid entrainment into the pores of the material may be a detrimental issue, which may lead to a non-optimal control of washcoat thickness and, in the most severe cases, to clogging. Several procedures have been reported in literature to overcome these issues, such as e.g. gas blowing. In this case, the coating thickness depends on the balance between viscous forces and shear stresses induced by air flow throughout the structure (Cristiani et al., 2012). Spin coating represents a valid alternative to blowing. While this technique is well consolidated in the field of flat surfaces functionalization (Sahu et al., 2009), only in recent years has it been technologically transferred to complex geometry supports (Zhang et al., 2012), with promising results reported both for honeycomb monoliths (Balzarotti et al., 2019b), open cell foams (Ambrosetti et al., 2018) and POCS (Balzarotti et al., 2021). Finally, slurry-based processes require a series of thermal treatment stages after wet coating deposition, in order to complete the washcoating process and to obtain the morphological and mechanical resistance properties of the final catalytic washcoat (Meille, 2006; Montebelli et al., 2014).
More recently, a radically different “activation” approach was reported in literature to overcome the heat/mass transfer limitations of traditional packed bed configurations, while still taking advantage of the presence of an interconnected metallic matrix (Visconti et al., 2016; Fratalocchi et al., 2018). In this view, the concept of packed foams was introduced, which consists in filling the empty cavities of structured cellular supports with catalytic pellets (Vervloet et al., 2013; Visconti et al., 2016). This new reactor layout has several advantages with respect to washcoated catalysts, such as higher catalyst inventory and higher productivity per reactor volume, moreover preventing the issues related to the complexity of the washcoating process. The packed foam concept was further investigated by a combined experimental and numerical approach, which demonstrated the dependency of the packing efficiency on the pore to pellet size ratio. In these configurations, pressure drops are similar to the ones displayed by packed bed reactors and can be estimated by an Ergun-like correlation, accounting for the total porosity and the total wetted area of the system (pellet and foam) (Ambrosetti et al., 2020b).
Aluminum open cell foams were effectively packed and tested in a lab-scale tubular reactor; the highly-exothermic and strongly temperature-dependent Fischer-Tropsch synthesis (FTS) was operated in the new configuration, and compared with a traditional packed bed reactor layout under the same industrial process conditions, using an active Pt-promoted Co/Al2O3 catalyst (Fratalocchi et al., 2018). Results validated the superior performance of the new reactor layout over the packed bed system, opening a new perspective for the intensification of the FTS process. The concept resulted in enhanced heat transfer performances without any detrimental effect on catalyst inventory and pressure drops. Using a similar approach, the concept of “packed-POCS” was numerically investigated (Ambrosetti et al., 2020c), and experimentally validated in the same FTS fixed-bed reactor, evidencing further improvements in terms of overall process performance and heat transfer rates (Fratalocchi et al., 2020). An additional experimental campaign performed by the same research group highlighted the relevant contribution of near-wall heat transfer resistances, which were significantly reduced by packed POCS additively manufactured with a continuous outer metallic skin (Fratalocchi et al., 2022).
Towards the industrial application of the concept, attention should be devoted to packing and unpacking procedures. Based on our experience, when the“window/pellet” diameter ratio is larger than 1.5/2 it is possible to easily pack the system applying conventional approaches already used for the loading of packed beds. Moreover, the possibility of using structured supports that have a limited size in length and diameter also in the case of very large/long tubes forces to work with cartridges positioned one atop the other. Is then possible to pack these supports externally from the reactor tubes and then load the samples one by one. Unloading the catalyst supports may be necessary if the catalyst lifetime is shorter than the plant lifetime. It is possible to depack the system with vibrations or by removing the ensemble catalyst/catalyst support and then re-load the system.
3 Towards the Intensification of Methane Steam Reforming Process
3.1 Perspectives for a Multiscale Reforming Process
Hydrogen is one of the most important chemicals, which is directly involved in many production processes of key chemical products, such as ammonia, methanol, as well as in refining processes. Accordingly, chemical and petrochemical applications account for more than 95% of pure hydrogen and 70% of the total hydrogen demand (Hydrogen - Fuels and Technologies - IEA, 2021). These processes are characterized by an economy of scale and require large and centralized reactor units (Zohuri, 2019). At the industrial scale, hydrogen is mainly produced by steam reforming of methane (MSR) and other light hydrocarbons (Baharudin and Watson, 2017), using multi-tubular packed bed reactors. In the process, two main reactions occur, namely the endothermic methane steam reforming (Eq. 1) and the water gas shift reaction (Eq. 2).
Due to the strong endothermicity of the reforming reaction, heat is provided by external burners, where a fraction of the hydrocarbon feed is burnt in a radiant furnace (Figure 4) (Dybkjaer, 1995). At the industrial scale, high flow velocities are used in the reformer tubes to maximize the convective heat transfer from the tube walls to the catalyst and the tubes/burners layout is optimized to manage the heat flux along the tubes (Sanz et al., 2016).
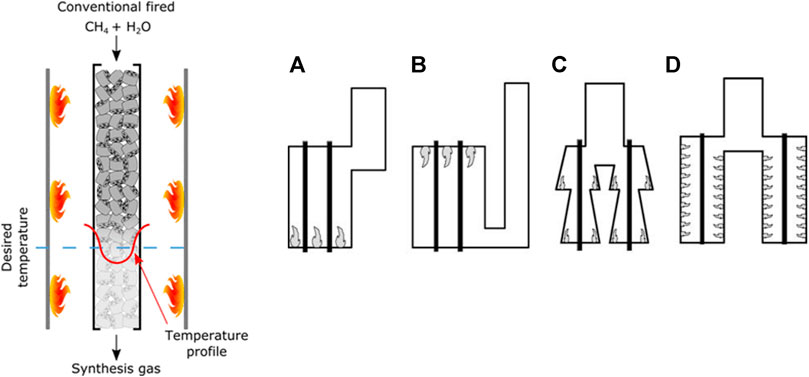
FIGURE 4. Schematic representation of a traditional reformer tube (left (Mortensen et al., 2017)) and tubes/burners arrangements in fire radiant furnaces (A–D) (Ferreira-Aparicio et al., 2005).
In addition to the consolidated and constantly growing production for industrial applications, hydrogen is gaining more and more consideration for promoting the sustainable development of society worldwide (Falcone et al., 2021). Among the many properties, it is a potentially sustainable energy vector, which could play one of the main roles in the fulfillment of the requirements of many of the United Nations’ Sustainable Development Goals. This perspective determines an increasing demand for low cost, small-scale devices for distributed hydrogen production. This target could be reached by the assessment of clean, sustainable and cost-competitive production processes (Kolb, 2013; Specchia, 2014; Ambrosetti et al., 2020a), as well as by the effective management of a new kind of hydrogen demand, characterized by the strong fluctuations of fuel and energy markets (Ahmed and Krumpelt, 2001). While long term, sustainable and fossil-free solutions are set to be designed for a sustainable future, in the short-term MSR is still the best compromise between cost, effectiveness, and process know-how. Moreover, the existing methane supply chain could be exploited for a distributed hydrogen production, which could benefit from the available expertise in the industrial applications of the process (Ambrosetti et al., 2020a).
Nevertheless, the downscale of large industrial reactor layout is not feasible immediately, and strong R&D efforts are still needed to run efficiently the MSR process at the small scale. At these conditions, the reduction in reactants feed would induce heat transfer limitations, which are detrimental for the overall process efficiency, if the traditional packed bed configuration of industrial reformers would be used (Gascon et al., 2015). According to this scenario, innovative approaches to intensify the process are in fact required (Ryu et al., 2007). Several approaches have been followed in order to effectively run the reforming process at small scale, thus enabling a distributed and distributed hydrogen production (Kapteijn and Moulijn, 2022); the latter can be summarized in 1) the use of PGM-based catalysts, 2) the improvement of heat and mass transfer by using structured catalysts and reactors, and 3) the electrification of the reforming process. In the following, a resume of the state of the art of each of these strategies will be reported.
3.2 PGM-Based Catalysts for MSR Intensification
Typical methane reforming catalysts consist of transition metal nanoparticles dispersed on a high surface area ceramic support, such as high surface area alumina (Simakov et al., 2015). Due to its low price and good catalytic activity in a broad temperature range, nickel has been selected as the metal of choice for MSR at the industrial scale. A recent review reports the most recent advances in Ni based catalysts for MSR, with special attention devoted to their use in structured catalysts (Meloni et al., 2020). Nevertheless, several aspects strongly limit the adoption of nickel-based active phases, such as coking at low steam-to-carbon ratios and insufficient activity at low temperature. Another relevant problem of Ni-based catalysts is the high risk associated with pyrophoric nature of the catalysts that reduces the possibility of safely operating the reactor at small scale. Moreover, from the process intensification point of view, miniaturization and improvement of heat transfer rates is not sufficient to achieve optimal overall performance. Accordingly, “catalyst-intensification” is also needed to prevent hot spots and guarantee optimal catalytic performance in small sized devices (Stefanidis and Vlachos, 2010).
When dealing with kinetic investigations, structured catalysts provide an additional option reducing risks of mass transport limitations and temperature gradients in the system—and also reducing pressure drops with respect to powdered bed catalysts. Either when dealing with washcoated systems (Palma et al., 2015) or packed foam systems (Ambrosetti et al., 2021b), structured catalysts allow to perform kinetic investigations in concentrated conditions and high conversions with respect to other approaches present in the literature (diluted beds, annular reactors). Testing the catalyst in more controlled conditions allows also to reduce the risk of coking as demonstrated by Palma et al. (Palma et al., 2015).
The adoption of noble metals to improve catalyst effectiveness is widely established in the literature and was reviewed by Farrauto et al.(Farrauto, 2014) as a valuable approach to improve the activity of small scale reformes. The use of PGM elements as catalytic active phase allows a significant enhancement of the reactions kinetics, which results in a reduction of the overall catalyst inventory. PGMs such as Ru, Rh, Ir, Pt, and Pd have been extensively investigated for reforming applications and their role has been fully addressed in literature reviews (Amjad et al., 2013; Angeli et al., 2014; Chen et al., 2020), also including bimetallic catalysts based on nickel and promoted with a noble metal (Simakov et al., 2015). In addition to the use of PGM, catalyst intensification can be obtained also by modification of the ceramic support (Palma et al., 2020), aiming at reducing coking and sintering.
3.3 Improvement of Heat and Mass Transfer Rates
The improvement of heat and mass transport phenomena in chemical processes is a hot research topic for catalysis, which is at the basis of a variety of process intensification strategies. Among others, the use of microchannel reactors has been extensively investigated as a possible solution to run strongly non-adiabatic processes (such as MSR) at the small scale (See Figure 5). In microchannel reactors, the reactants feed flows in small diameter channels (typically in the 50–5,000 μm range), which enhances both heat and mass interphase transfer rates. In this view, a multi-flow layout was proposed coupling the endothermic MSR with exothermic reactions, which were run in segregated adjacent channels (Chen et al., 2018). More recent applications of the same reactor concept have been reported in (Ashraf et al., 2021), where also the dynamic behavior of the system has been considered. FeCrAl was used as bulk material for the reactor (Kolb et al., 2006; Avci et al., 2010), while different active phase were evaluated for the catalytic media (Farrauto et al., 2007).
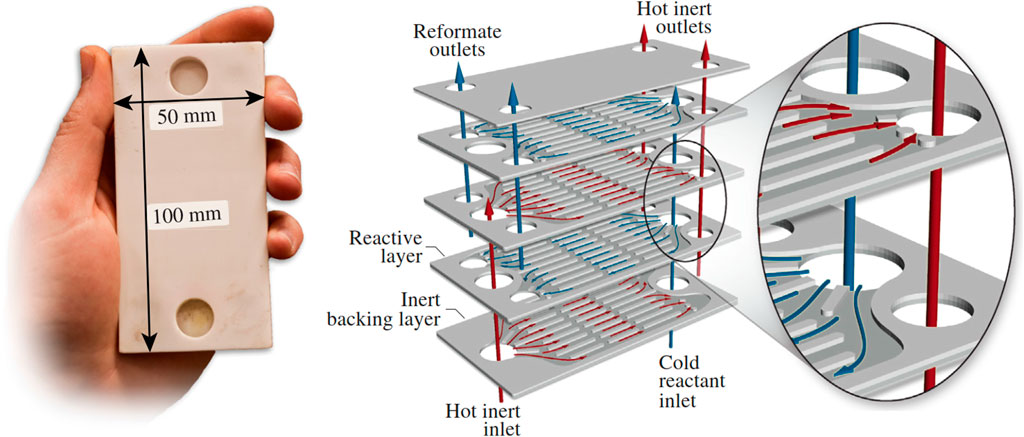
FIGURE 5. Schematic representation of the layout and size of microchannel reactors (Murphy et al., 2013).
The presence of thin washcoated catalytic layers allows good thermal regulation and control of chemical processes, which are further enhanced by the use of conductive metallic materials (e.g. aluminum, copper, and stainless steel), according to the requirements of the specific application. Furthermore, microchannel reactors offer the possibility to develop modular systems, as the total reactor volume can be achieved by adding many small reactors with the same dimension. All the properties reported so far enable many degrees of freedom in terms of reactor design.
The design of structured catalyst based on conductive internals is another valuable approach to boost the heat and mass transfer performance of many processes. Many efforts have been spent for the investigation of the beneficial effects associated with the introduction of thermally conductive internals (Tronconi et al., 2014; Baharudin and Watson, 2018). As reported in the previous section, the metallic structures are catalytically activated either by depositing a thin washcoat layer of catalytic material onto the geometric surface of the support (Montebelli et al., 2014) or by filling the porosity of the supports with catalytic pellets. Steel-based materials have been extensively investigated as bulk material constituent of cellular matrices in view of their chemical inertness and resistance at high temperature. Among others, Yu et al. proposed steel-based supports in the methanol reforming, which were activated using copper-based catalysts (Yu et al., 2007), while other works report similar materials for the dry reforming of methane, using Ni and Ru-based catalysts (Sang et al., 2012). A similar approach was used for the performance optimization of biogas reforming reaction, with a detailed experimental investigation of catalyst formulation and washcoat process optimization (Roy et al., 2014; Roy et al., 2015). Despite the large use and availability of steel-based supports, significant limitations are present due to the low thermal conductivity of this material. While aluminum has a significantly higher thermal conductivity, its low melting point (approx. 660°C) limits the application to milder processes (i.e. water gas shift (Palma et al., 2016) and methanol steam reforming (Echave et al., 2013)). Some research groups investigated nickel and nickel-alloys as bulk materials for open cell foams (Park et al., 2013; Park et al., 2014). The higher thermal conductivity with respect to steel-based structures was found to be beneficial for the process performance in the CO2 steam reforming of CH4, as improved radial heat transfer rates were observed with respect to catalytic alumina pellets.
Copper represents the best compromise in term of thermal conductivity and resistance at relatively high temperature (up to 900°C). Nevertheless, this material has not found extensive application for the production of supported catalysts in the reforming processes. Structured copper catalysts have been applied in the solar reforming of methane for supporting Ni-based Mg/Al oxides catalysts (Jang et al., 2014; Qi et al., 2015), and some other works have been reported dealing with the methanol reforming process (Shen et al., 2013; Zhou et al., 2017). In all cases, the beneficial role of the highly conductive internal matrix on the heat transfer properties was evidenced, resulting in milder cold spots across the catalytic bed.
One of the most recent works based on copper internals focuses on a synergetic approach to MSR process intensification (Balzarotti et al., 2019a), as the strategy included both the adoption of a highly active Rh/Al2O3 catalyst and the use of highly conductive copper foams. 40 PPI copper foams (Figure 6A) were catalytically activated by washcoating a thin layer of Rh/Al2O3 catalyst onto the support surface (Figure 6B). A packed bed configuration was also tested as a benchmark of the traditional process layout, using home-made egg-shell pellets based on the same catalyst composition.
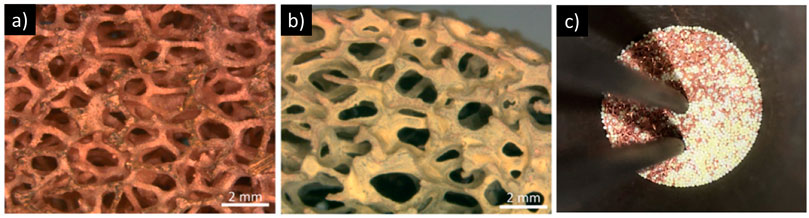
FIGURE 6. Optical microscopy analysis of the bare copper foam (A), Rh/Al2O3 washcoated samples (B) and copper foam packed with Rh/Al2O3 pellets loaded in the tubular reactor (C) (adapted from ref. (Balzarotti et al., 2019a) and (Balzarotti et al., 2020a)).
The authors compared the different reactor layouts in the 600–800°C range, at atmospheric pressure, using two different space velocities, namely 5,000 and 10,000 h−1. The results of the experimental campaign demonstrated smoother temperature profiles across the catalytic bed, with significantly reduced radial temperature gradients, in the case of the washcoated Cu-foam configuration, thus confirming the beneficial role of the solid conductive matrix in the radial heat transfer. Based on the reported results, washcoated copper foams are valuable candidates for the enhancement of the performance in methane reformers. For the same oven temperature, the improved temperature profile and heat transfer determined better results in terms of methane conversion with respect to the packed bed benchmark layout both in the equilibrium-limited and in the kinetic controlled regime, thanks to a higher and more evenly distributed temperature across the reactor. The same copper substrates were also tested in the packed foam configuration (Figure 6C (Balzarotti et al., 2020a)), using a similar approach to that previously reported for the FTS synthesis (Fratalocchi et al., 2018). In particular, different metallic supports were tested, namely 12 PPI FeCrAl foams, and copper foams with 10 and 40 PPI. While the low-conductive FeCrAl internals did not bring any improvement in process performance, remarkable enhancements of the heat transfer performance were reported using highly conductive internals (Cu foams). The latter allowed a reduction of the maximum radial temperature difference across the catalytic bed and, thus, higher methane conversions were obtained. Furthermore, the authors proposed a model for the estimation of the global heat transfer coefficient of the system, reporting good accordance with the experimental results. The model elucidates the effect of the foam morphology (porosity, cell size) on the heat transfer properties, which have a strong impact on process performances. In addition to the promising developments at the industrial/production scale, the enhancement of heat transfer in strongly non-adiabatic system opens new experimental approaches also from the research point of view. The use of copper packed foams layout allowed in fact the investigation of previously untested highly concentrated reactant feeds in the MSR process, enabling a kinetic study with minimized temperature gradients (Ambrosetti et al., 2021b). Based on this approach, a more robust kinetic model could be developed under concentrated conditions which are more representative of industrial large-scale applications.
3.4 Decarbonization of MSR by Electrification
Towards the reduction of CO2 footprint, the use of a larger amount of energy from non fossil fuel feedstock is one of the main trends observed worldwide. In the process industry this may lead to the use of electric energy for pre-heating purposes or to run the process compressors. The transition scenarios to the low-carbon energy in chemical industries are commonly based on the so-called power-to-X concept, which consists in the use of renewable electricity to run chemical processes (Stankiewicz and Nigar, 2020) with the use of hydrogen typically produced by H2O electrolysis. Another approach is represented by switching the heat supply to endothermic reactors from combustion heat to electric heating, with a positive effect induced by the replacement of fossil fuels with low-carbon electricity (Madeddu et al., 2020). In a chemical reactor, the conversion of electricity into heat to sustain endothermic processes can be performed either directly or indirectly. While the first case is mainly covered by the Joule heating process, the latter case offers more options, such as microwaves and induction heating (Stankiewicz and Nigar, 2020). In the first case, the challenge is represented by the inclusion of electrically heated elements in the reactor or by the heating of the reactor shell, whereas in the other cases the challenges are related to the presence of materials that can be inductively heated/irradiated by microwaves, the design of reactor walls where induction/microwaves can be transmitted through. This relatively new approach to reactor design calls for a comprehensive re-consideration of the traditional reactor layouts in order to take into account the new energy supply methods. Also in this case, the presence of a structured catalyst facilitates the electrification with micro-wave and induction heating, whereas it is also possible to exploit the structured reactor for Joule-heating as reported by Badakhsh and co-authors (Badakhsh et al., 2021).
Based on this scenario, several research groups have proposed different solutions. The investigation reported by Rieks et al. is one of the first examples of the application of direct Joule heating to the methane reforming process. In particular, the high thermal duty of the dry reforming process was fulfilled by directly washcoating heating elements consisting of a FeCrAl alloy with a LaNi0.95Ru0.05O3 catalyst, at different washcoat thicknesses (Rieks et al., 2015). Wismann et al. applied the same approach in a more disruptive way by integrating an electrically heated catalytic structure directly into a methane steam reforming reactor (Wismann et al., 2019a). Current flow was forced in the walls of a 50 cm long and thin FeCrAl tube, whose inner walls were made catalytically active by depositing a catalytic washcoat layer (Wismann et al., 2019b). The proposed reactor layout is represented in Figure 7. Results demonstrated how the direct contact between heat source and catalyst changes the heat transfer dynamics, thus reducing the temperature gradients with respect to fired reformers. The flexibility of electrically heated systems was further validated by a combination of CFD modelling and lab scale reactor tests (Wismann et al., 2021). In a similar way, Renda et al. tested direct Joule heating by using commercial silicon carbide heating elements (Renda et al., 2020), demonstrating the feasibility of heating up the system to high temperature (i.e. 800°C) and to sustain the reaction, with methane conversions as high as 85%, in the case of both steam and dry reforming. In a recent paper Ambrosetti et al. performed a mathematical model analysis addressing the potential of SiC foams with the dual role of resistive elements and catalyst substrates in methane steam reforming (Ambrosetti et al., 2021a). The simulation results showed that very high efficiencies and specific H2 productivities can be achieved.
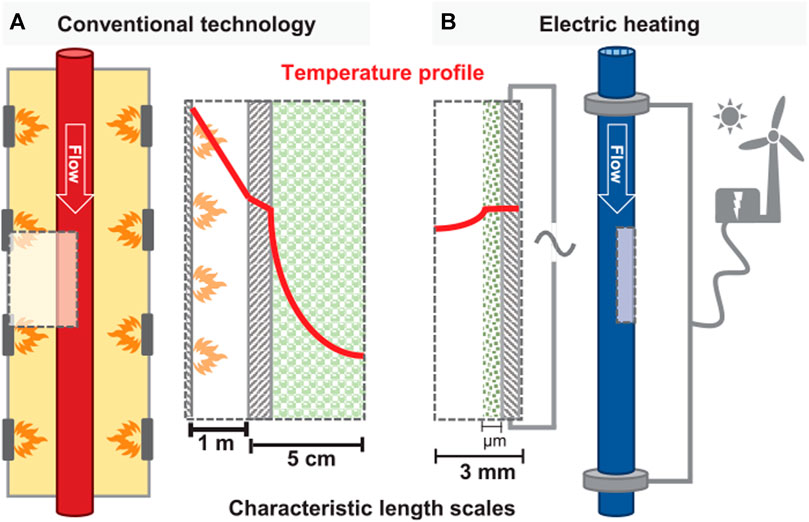
FIGURE 7. Schematic representation of reactor scale and temperature profiles in conventional reformers (A) and in the electrified reformer (B) (Wismann et al., 2019a).
In addition to the reported studies of the reforming process, similar approaches have been effectively applied to other energy demanding processes, such as methanol production (Delikonstantis et al., 2021), ammonia cracking for hydrogen production (Badakhsh et al., 2021) and CO2 methanation (Dou et al., 2020).
As far as indirect heating is concerned, microwave-assisted catalysis is gaining relevance in view of finding new routes for modular and environmentally friendly energy supply in energy intensive processes. Accordingly, Meloni et al. attempted to overcome the heat transfer limitations of the methane steam reforming reaction by microwave heating (Meloni et al., 2021). Ni-based catalysts were prepared and tested, showing promising methane conversions at gas hourly space velocities (GHSV) of about 5,000 h−1. Similarly, Marin et al. demonstrated the same heat supply approach for the dry reforming of methane, using a Mn doped lanthanum strontium cobaltite (LSC) material, which was used as both microwave absorber and catalyst (Marin et al., 2021). Promising single-pass conversions in the 80–90% range were obtained, with stable operation for over 10 h. Together with hot spots, catalyst stability is one of the main constraints of microwave-heated processes, especially under increased catalyst inventory. In order to try and overcome these limitations, Chen et al. engineered a new reactor layout consisting of a packed monolith configuration, in which the monolith acted as microwave absorbing material while monolith channels were filled with catalytic pellets (Chen et al., 2021). The proposed system was tested for the dry reforming of methane over a commercial Rh/Al2O3 catalyst, achieving stable methane conversions in the range of 90% at high temperature.
In the context of indirect heating, induction heating represents a valuable alternative to microwave assisted heating (Wang W. et al., 2019). One of the first experimental investigations was published by Pérez-Camacho et al., who reported an induction heating system for performing the conversion of biogas to synthesis gas using renewable energy (Pérez-Camacho et al., 2015). Vinum et al. proposed binary and ternary alloy nanoparticles to be used both as susceptors (for induction heating) and as catalytic active phase for the steam reforming of methane (Vinum et al., 2018). CoNi and CuCoNi-based materials were tested, showing that the overall performance is limited by chemical reactivity, in opposition to the traditional externally heated reformers, which are limited by heat transport. Materials based on the same composition were tested by other authors (Varsano et al., 2019; Almind et al., 2020; Scarfiello et al., 2021), paving the way to further process optimization that would enable the technology to be competitive with other electricity driven routes to hydrogen production.
4 Conclusion
This literature survey of the state of the art of new materials and approaches for process intensification has highlighted the most recent trends in this research field. While apparently many different approaches have been proposed for meeting the target of efficient management of non-adiabatic catalytic processes, a common guideline can be identified, which calls for a continuous improvement of the knowledge regarding the management of heat and mass transfer in heterogeneous catalytic systems. With vastly superior ranges of degrees of freedom for their design, spatially structured catalysts and reactors clearly emerge as the protagonists of such new developments.
In this view, the recent advances in additive manufacturing technologies promise to provide new effective tools to overcome many structural constraints of past and current reactor layouts, thus enabling to debottleneck key heat-transfer limited industrial processes, as urgently needed for the upcoming Energy Transition. The enhanced heat transfer properties of thermally conductive open-cell foams and POCS are of paramount importance in this perspective.
Finally, disruptive synergies can be expected in the near future from the direct or indirect electrification of endothermic catalytic processes, including not only the steam and dry reforming of methane, but in perspective also other H2-related reactions like the Reverse Water Gas Shift, the ammonia and methanol decomposition, and other dehydrogenation reactions.
Author Contributions
RB: Conceptualization, Methodology, Investigation, Writing Original Draft MA: Conceptualization, Writing Review and Editing AB: Conceptualization, Writing Review and Editing GG: Conceptualization, Writing Review and Editing ET: Conceptualization, Writing Review and Editing, Funding acquisition.
Funding
The research leading to these results has received funding from the European Research Council under the European Union’s Horizon 2020 Research and Innovation Program (Grant Agreement no. 694910/INTENT: “Structured Reactors with Intensified Energy Transfer for Breakthrough Catalytic Technologies”).
Conflict of Interest
The authors declare that the research was conducted in the absence of any commercial or financial relationships that could be construed as a potential conflict of interest.
Publisher’s Note
All claims expressed in this article are solely those of the authors and do not necessarily represent those of their affiliated organizations, or those of the publisher, the editors and the reviewers. Any product that may be evaluated in this article, or claim that may be made by its manufacturer, is not guaranteed or endorsed by the publisher.
References
Aboulkhair, N. T., Simonelli, M., Parry, L., Ashcroft, I., Tuck, C., and Hague, R. (2019). 3D Printing of Aluminium Alloys: Additive Manufacturing of Aluminium Alloys Using Selective Laser Melting. Prog. Mater. Sci. 106, 100578. doi:10.1016/J.PMATSCI.2019.100578
Aghaei, P., Visconti, C. G., Groppi, G., and Tronconi, E. (2017). Development of a Heat Transport Model for Open-Cell Metal Foams with High Cell Densities. Chem. Eng. J. 321, 432–446. doi:10.1016/J.CEJ.2017.03.112
Agueniou, F., Vidal, H., de Dios López, J., Hernández-Garrido, J. C., Cauqui, M. A., Botana, F. J., et al. (2021). 3D-printing of Metallic Honeycomb Monoliths as a Doorway to a New Generation of Catalytic Devices: the Ni-Based Catalysts in Methane Dry Reforming Showcase. Catal. Commun. 148, 106181. doi:10.1016/J.CATCOM.2020.106181
Ahmed, S., and Krumpelt, M. (2001). Hydrogen from Hydrocarbon Fuels for Fuel Cells. Int. J. Hydrogen Energ. 26, 291–301. doi:10.1016/S0360-3199(00)00097-5
Al‐Ketan, O., Pelanconi, M., Ortona, A., and Abu Al‐Rub, R. K. (2019). Additive Manufacturing of Architected Catalytic Ceramic Substrates Based on Triply Periodic Minimal Surfaces. J. Am. Ceram. Soc. 102, 6176–6193. doi:10.1111/jace.16474
Al-Ketan, O., Rowshan, R., and Abu Al-Rub, R. K. (2018). Topology-mechanical Property Relationship of 3D Printed Strut, Skeletal, and Sheet Based Periodic Metallic Cellular Materials. Additive Manufacturing 19, 167–183. doi:10.1016/J.ADDMA.2017.12.006
Almind, M. R., Vendelbo, S. B., Hansen, M. F., Vinum, M. G., Frandsen, C., Mortensen, P. M., et al. (2020). Improving Performance of Induction-Heated Steam Methane Reforming. Catal. Today 342, 13–20. doi:10.1016/J.CATTOD.2019.05.005
Amalraj, P. B. C. A., Ebner, A. D., and Ritter, J. A. (2019). Effective Radial Thermal Conductivity of a Parallel Channel Corrugated Metal Structured Adsorbent. Ind. Eng. Chem. Res. 58, 16922–16933. doi:10.1021/acs.iecr.9b03057
Ambrosetti, M., Balzarotti, R., Cristiani, C., Groppi, G., and Tronconi, E. (2018). The Influence of the Washcoat Deposition Process on High Pore Density Open Cell Foams Activation for CO Catalytic Combustion. Catalysts 8, 510. doi:10.3390/catal8110510
Ambrosetti, M., Balzarotti, R., Fratalocchi, L., Bracconi, M., Groppi, G., and Tronconi, E. (2020a). “CHAPTER 11. Structured Catalysts and Non-conventional Reactor Designs for Energy Applications,” in Heterogeneous Catalysis for Energy Applications (The Royal Society of Chemistry), 361–396. doi:10.1039/9781788019576-00361
Ambrosetti, M., Beretta, A., Groppi, G., and Tronconi, E. (2021a). A Numerical Investigation of Electrically-Heated Methane Steam Reforming over Structured Catalysts. Front. Chem. Eng. 3, 1–17. doi:10.3389/fceng.2021.747636
Ambrosetti, M., Bonincontro, D., Balzarotti, R., Beretta, A., Groppi, G., and Tronconi, E. (2021b). H2 Production by Methane Steam Reforming over Rh/Al2O3 Catalyst Packed in Cu Foams: A Strategy for the Kinetic Investigation in Concentrated Conditions. Catal. Today. doi:10.1016/J.CATTOD.2021.06.003
Ambrosetti, M., Bracconi, M., Maestri, M., Groppi, G., and Tronconi, E. (2020b). Packed Foams for the Intensification of Catalytic Processes: Assessment of Packing Efficiency and Pressure Drop Using a Combined Experimental and Numerical Approach. Chem. Eng. J. 382, 122801. doi:10.1016/J.CEJ.2019.122801
Ambrosetti, M., Groppi, G., Schwieger, W., Tronconi, E., and Freund, H. (2020c). Packed Periodic Open Cellular Structures - an Option for the Intensification of Non-adiabatic Catalytic Processes. Chem. Eng. Process. - Process Intensification 155, 108057. doi:10.1016/J.CEP.2020.108057
Amjad, U.-E. -S., Vita, A., Galletti, C., Pino, L., and Specchia, S. (2013). Comparative Study on Steam and Oxidative Steam Reforming of Methane with Noble Metal Catalysts. Ind. Eng. Chem. Res. 52, 15428–15436. doi:10.1021/ie400679h
Angeli, S. D., Monteleone, G., Giaconia, A., and Lemonidou, A. A. (2014). State-of-the-art Catalysts for CH4 Steam Reforming at Low Temperature. Int. J. Hydrogen Energ. 39, 1979–1997. doi:10.1016/J.IJHYDENE.2013.12.001
Anglani, A., and Pacella, M. (2018). Logistic Regression and Response Surface Design for Statistical Modeling of Investment Casting Process in Metal Foam Production. Proced. CIRP 67, 504–509. doi:10.1016/j.procir.2017.12.252
Ashraf, M. A., Tacchino, S., Peela, N. R., Ercolino, G., Gill, K. K., Vlachos, D. G., et al. (2021). Experimental Insights into the Coupling of Methane Combustion and Steam Reforming in a Catalytic Plate Reactor in Transient Mode. Ind. Eng. Chem. Res. 60, 196–209. doi:10.1021/acs.iecr.0c04837
Avci, A. K., Trimm, D. L., and Karakaya, M. (2010). Microreactor Catalytic Combustion for Chemicals Processing. Catal. Today 155, 66–74. doi:10.1016/J.CATTOD.2009.01.046
Avila, P., Montes, M., and Miró, E. E. (2005). Monolithic Reactors for Environmental Applications. Chem. Eng. J. 109, 11–36. doi:10.1016/j.cej.2005.02.025
Badakhsh, A., Kwak, Y., Lee, Y.-J., Jeong, H., Kim, Y., Sohn, H., et al. (2021). A Compact Catalytic Foam Reactor for Decomposition of Ammonia by the Joule-Heating Mechanism. Chem. Eng. J. 426, 130802. doi:10.1016/J.CEJ.2021.130802
Baena-Moreno, F. M., González-Castaño, M., Navarro de Miguel, J. C., Miah, K. U. M., Ossenbrink, R., Odriozola, J. A., et al. (2021). Stepping toward Efficient Microreactors for CO2 Methanation: 3D-Printed Gyroid Geometry. ACS Sust. Chem. Eng. 9, 8198–8206. doi:10.1021/acssuschemeng.1c01980
Baharudin, L., and James Watson, M. (2017). Hydrogen Applications and Research Activities in its Production Routes through Catalytic Hydrocarbon Conversion. Rev. Chem. Eng. 34, 43–72. doi:10.1515/revce-2016-0040
Baharudin, L., and Watson, M. J. (2018). Monolithic Substrate Support Catalyst Design Considerations for Steam Methane Reforming Operation. Rev. Chem. Eng. 34, 481–501. doi:10.1515/revce-2016-0048
Baharudin, L., Yip, A. C.-K., Golovko, V., and Watson, M. J. (2020). Potential of Metal Monoliths with Grown Carbon Nanomaterials as Catalyst Support in Intensified Steam Reformer: a Perspective. Rev. Chem. Eng. 36, 459–491. doi:10.1515/revce-2018-0007
Bai, Y., and Williams, C. B. (2015). An Exploration of Binder Jetting of Copper. Rapid Prototyp. J. 21, 177–185. doi:10.1108/RPJ-12-2014-0180
Balzarotti, R., Ambrosetti, M., Arnesano, M., Anglani, A., Groppi, G., and Tronconi, E. (2021). Periodic Open Cellular Structures (POCS) as Enhanced Catalyst Supports: Optimization of the Coating Procedure and Analysis of Mass Transport. Appl. Catal. B: Environ. 283, 119651. doi:10.1016/j.apcatb.2020.119651
Balzarotti, R., Ambrosetti, M., Beretta, A., Groppi, G., and Tronconi, E. (2020a). Investigation of Packed Conductive Foams as a Novel Reactor Configuration for Methane Steam Reforming. Chem. Eng. J. 391, 123494. doi:10.1016/J.CEJ.2019.123494
Balzarotti, R., Beretta, A., Groppi, G., and Tronconi, E. (2019a). A Comparison between Washcoated and Packed Copper Foams for the Intensification of Methane Steam Reforming. React. Chem. Eng. 4, 1387–1392. doi:10.1039/c9re00125e
Balzarotti, R., Bisaccia, A., Tripi, M. C., Ambrosetti, M., Groppi, G., and Tronconi, E. (2020b). Production and Characterization of Copper Periodic Open Cellular Structures Made by 3D Printing‐replica Technique. Jnl Adv. Manuf Process. 2, e10068. doi:10.1002/amp2.10068
Balzarotti, R., Cristiani, C., and Francis, L. F. (2019b). Combined Dip-Coating/spin-Coating Depositions on Ceramic Honeycomb Monoliths for Structured Catalysts Preparation. Catal. Today 334, 90–95. doi:10.1016/j.cattod.2019.01.037
Banhart, J. (2001). Manufacture, Characterisation and Application of Cellular Metals and Metal Foams. Prog. Mater. Sci. 46, 559–632. doi:10.1016/S0079-6425(00)00002-5
Bastos Rebelo, N. F., Andreassen, K. A., Suarez Ríos, L. I., Piquero Camblor, J. C., Zander, H.-J., and Grande, C. A. (2018). Pressure Drop and Heat Transfer Properties of Cubic Iso-Reticular Foams. Chem. Eng. Process. - Process Intensification 127, 36–42. doi:10.1016/J.CEP.2018.03.008
Bianchi, E., Heidig, T., Visconti, C. G., Groppi, G., Freund, H., and Tronconi, E. (2012). An Appraisal of the Heat Transfer Properties of Metallic Open-Cell Foams for Strongly Exo-/endo-Thermic Catalytic Processes in Tubular Reactors. Chem. Eng. J. 198-199, 512–528. doi:10.1016/j.cej.2012.05.045
Bianchi, E., Heidig, T., Visconti, C. G., Groppi, G., Freund, H., and Tronconi, E. (2013). Heat Transfer Properties of Metal Foam Supports for Structured Catalysts: Wall Heat Transfer Coefficient. Catal. Today 216, 121–134. doi:10.1016/J.CATTOD.2013.06.019
Bianchi, E., Schwieger, W., and Freund, H. (2016). Assessment of Periodic Open Cellular Structures for Enhanced Heat Conduction in Catalytic Fixed-Bed Reactors. Adv. Eng. Mater. 18, 608–614. doi:10.1002/adem.201500356
Bracconi, M., Ambrosetti, M., Maestri, M., Groppi, G., and Tronconi, E. (2018a). A Fundamental Analysis of the Influence of the Geometrical Properties on the Effective thermal Conductivity of Open-Cell Foams. Chem. Eng. Process. - Process Intensification 129, 181–189. doi:10.1016/J.CEP.2018.04.018
Bracconi, M., Ambrosetti, M., Maestri, M., Groppi, G., and Tronconi, E. (2018b). A Fundamental Investigation of Gas/solid Mass Transfer in Open-Cell Foams Using a Combined Experimental and CFD Approach. Chem. Eng. J. 352, 558–571. doi:10.1016/j.cej.2018.07.023
Bracconi, M., Ambrosetti, M., Maestri, M., Groppi, G., and Tronconi, E. (2017). A Systematic Procedure for the Virtual Reconstruction of Open-Cell Foams. Chem. Eng. J. 315, 608–620. doi:10.1016/j.cej.2017.01.069
Bracconi, M., Ambrosetti, M., Maestri, M., Groppi, G., and Tronconi, E. (2020). Analysis of the Effective thermal Conductivity of Isotropic and Anisotropic Periodic Open Cellular Structures for the Intensification of Catalytic Processes. Chem. Eng. Process. - Process Intensification 158, 108169. doi:10.1016/J.CEP.2020.108169
Bracconi, M., Ambrosetti, M., Okafor, O., Sans, V., Zhang, X., Ou, X., et al. (2019). Investigation of Pressure Drop in 3D Replicated Open-Cell Foams: Coupling CFD with Experimental Data on Additively Manufactured Foams. Chem. Eng. J. 377, 120123. doi:10.1016/j.cej.2018.10.060
Busse, C., Freund, H., and Schwieger, W. (2018). Intensification of Heat Transfer in Catalytic Reactors by Additively Manufactured Periodic Open Cellular Structures (POCS). Chem. Eng. Process. - Process Intensification 124, 199–214. doi:10.1016/j.cep.2018.01.023
Busser, T., Serres, M., Philippe, R., and Vidal, V. (2020). Hydrodynamics of Gas-Liquid Co-current Flow through a Thin Sheet of Highly Porous Open Cell Solid Foam. Chem. Eng. Sci. 226, 115811. doi:10.1016/j.ces.2020.115811
Cai, X., Wörner, M., Marschall, H., and Deutschmann, O. (2016). Numerical Study on the Wettability Dependent Interaction of a Rising Bubble with a Periodic Open Cellular Structure. Catal. Today 273, 151–160. doi:10.1016/j.cattod.2016.03.053
Chen, J., Liu, B., Gao, X., and Xu, D. (2018). Production of Hydrogen by Methane Steam Reforming Coupled with Catalytic Combustion in Integrated Microchannel Reactors. Energies 11, 2045. doi:10.3390/en11082045
Chen, L., Qi, Z., Zhang, S., Su, J., and Somorjai, G. A. (2020). Catalytic Hydrogen Production from Methane: A Review on Recent Progress and Prospect. Catalysts 10, 858. doi:10.3390/catal10080858
Chen, W., Malhotra, A., Yu, K., Zheng, W., Plaza-Gonzalez, P. J., Catala-Civera, J. M., et al. (2021). Intensified Microwave-Assisted Heterogeneous Catalytic Reactors for Sustainable Chemical Manufacturing. Chem. Eng. J. 420, 130476. doi:10.1016/J.CEJ.2021.130476
Cristiani, C., Finocchio, E., Latorrata, S., Visconti, C. G., Bianchi, E., Tronconi, E., et al. (2012). Activation of Metallic Open-Cell Foams via Washcoat Deposition of Ni/MgAl2O4 Catalysts for Steam Reforming Reaction. Catal. Today 197, 256–264. doi:10.1016/j.cattod.2012.09.003
Cybulski, A., and Moulijn, J. A. (2006). “Monolithic Catalysts for Three Phases Processes Chapter,” in Structured Catalysts and Reactors (CRC Press), 355–391.
Danaci, S., Protasova, L., Lefevere, J., Bedel, L., Guilet, R., and Marty, P. (2016). Efficient CO 2 Methanation over Ni/Al 2 O 3 Coated Structured Catalysts. Catal. Today 273, 234–243. doi:10.1016/j.cattod.2016.04.019
Danaci, S., Protasova, L., Snijkers, F., Bouwen, W., Bengaouer, A., and Marty, P. (2018). Innovative 3D-Manufacture of Structured Copper Supports post-coated with Catalytic Material for CO 2 Methanation. Chem. Eng. Process. - Process Intensification 127, 168–177. doi:10.1016/j.cep.2018.03.023
Das, S., Sneijders, S., Deen, N. G., and Kuipers, J. A. M. (2018). Drag and Heat Transfer Closures for Realistic Numerically Generated Random Open-Cell Solid Foams Using an Immersed Boundary Method. Chem. Eng. Sci. 183, 260–274. doi:10.1016/J.CES.2018.03.022
Davó-Quiñonero, A., Sorolla-Rosario, D., Bailón-García, E., Lozano-Castelló, D., and Bueno-López, A. (2019). Improved Asymmetrical Honeycomb Monolith Catalyst Prepared Using a 3D Printed Template. J. Hazard. Mater. 368, 638–643. doi:10.1016/J.JHAZMAT.2019.01.092
Delikonstantis, E., Igos, E., Theofanidis, S.-A., Benetto, E., Marin, G. B., Van Geem, K., et al. (2021). An Assessment of Electrified Methanol Production from an Environmental Perspective. Green. Chem. 23, 7243–7258. doi:10.1039/D1GC01730F
Dou, L., Yan, C., Zhong, L., Zhang, D., Zhang, J., Li, X., et al. (2020). Enhancing CO2 Methanation over a Metal Foam Structured Catalyst by Electric Internal Heating. Chem. Commun. 56, 205–208. doi:10.1039/C9CC07525A
Dybkjaer, I. (1995). Tubular Reforming and Autothermal Reforming of Natural Gas - an Overview of Available Processes. Fuel Process. TechnologyTechnol 42, 85–107. doi:10.1016/0378-3820(94)00099-F
Echave, F. J., Sanz, O., Velasco, I., Odriozola, J. A., and Montes, M. (2013). Effect of the alloy on Micro-structured Reactors for Methanol Steam Reforming. Catal. Today 213, 145–154. doi:10.1016/J.CATTOD.2013.02.027
El-Wardany, T. I., She, Y., Jagdale, V. N., Garofano, J. K., Liou, J. J., and Schmidt, W. R. (2018). Challenges in Three-Dimensional Printing of High-Conductivity Copper. J. Electron. Packag. Trans. ASME 140, 020907. doi:10.1115/1.4039974
Falcone, P. M., Hiete, M., and Sapio, A. (2021). Hydrogen Economy and Sustainable Development Goals: Review and Policy Insights. Curr. Opin. Green Sust. Chem. 31, 100506. doi:10.1016/J.COGSC.2021.100506
Farrauto, R. J., Liu, Y., Ruettinger, W., Ilinich, O., Shore, L., and Giroux, T. (2007). Precious Metal Catalysts Supported on Ceramic and Metal Monolithic Structures for the Hydrogen Economy. Catal. Rev. 49, 141–196. doi:10.1080/01614940701220496
Farrauto, R. J. (2014). New Catalysts and Reactor Designs for the Hydrogen Economy. Chem. Eng. J. 238, 172–177. doi:10.1016/J.CEJ.2013.07.004
Feng, J., Fu, J., Lin, Z., Shang, C., and Niu, X. (2019). Layered Infill Area Generation from Triply Periodic Minimal Surfaces for Additive Manufacturing. Computer-Aided Des. 107, 50–63. doi:10.1016/J.CAD.2018.09.005
Ferreira‐Aparicio, P., Benito, M. J., and Sanz, J. L. (2005). New Trends in Reforming Technologies: from Hydrogen Industrial Plants to Multifuel Microreformers. Catal. Rev. 47, 491–588. doi:10.1080/01614940500364958
Ferroni, C., Bracconi, M., Ambrosetti, M., Maestri, M., Groppi, G., and Tronconi, E. (2021). A Fundamental Investigation of Gas/Solid Heat and Mass Transfer in Structured Catalysts Based on Periodic Open Cellular Structures (POCS). Ind. Eng. Chem. Res. 60, 10522–10538. doi:10.1021/acs.iecr.1c00215
Fratalocchi, L., Groppi, G., Visconti, C. G., Lietti, L., and Tronconi, E. (2020). Adoption of 3D Printed Highly Conductive Periodic Open Cellular Structures as an Effective Solution to Enhance the Heat Transfer Performances of Compact Fischer-Tropsch Fixed-Bed Reactors. Chem. Eng. J. 386, 123988. doi:10.1016/J.CEJ.2019.123988
Fratalocchi, L., Groppi, G., Visconti, C. G., Lietti, L., and Tronconi, E. (2022). Packed-POCS with Skin: A Novel Concept for the Intensification of Non-adiabatic Catalytic Processes Demonstrated in the Case of the Fischer-Tropsch Synthesis. Catal. Today 383, 15–20. doi:10.1016/J.CATTOD.2020.12.031
Fratalocchi, L., Visconti, C. G., Groppi, G., Lietti, L., and Tronconi, E. (2018). Intensifying Heat Transfer in Fischer-Tropsch Tubular Reactors through the Adoption of Conductive Packed Foams. Chem. Eng. J. 349, 829–837. doi:10.1016/J.CEJ.2018.05.108
García-Moreno, F. (2016). Commercial Applications of Metal Foams: Their Properties and Production. Materials 9, 85. doi:10.3390/ma9020085
Gascon, J., van Ommen, J. R., Moulijn, J. A., and Kapteijn, F. (2015). Structuring Catalyst and Reactor - an Inviting Avenue to Process Intensification. Catal. Sci. Technol. 5, 807–817. doi:10.1039/C4CY01406E
Giani, L., Groppi, G., and Tronconi, E. (2005). Mass-transfer Characterization of Metallic Foams as Supports for Structured Catalysts. Ind. Eng. Chem. Res. 44, 4993–5002. doi:10.1021/ie0490886
Goodall, R., and Mortensen, A. (2014). Porous Metals. Phys. Metall. Fifth 1, 2399–2595. doi:10.1016/B978-0-444-53770-6.00024-1 Ed.
Govender, S., and Friedrich, H. (2017). Monoliths: A Review of the Basics, Preparation Methods and Their Relevance to Oxidation. Catalysts 7, 62. doi:10.3390/catal7020062
Grande, C. A., and Didriksen, T. (2021). Production of Customized Reactors by 3D Printing for Corrosive and Exothermic Reactions. Ind. Eng. Chem. Res. 60, 16720–16727. doi:10.1021/acs.iecr.1c02791
Guschlbauer, R., Momeni, S., Osmanlic, F., and Körner, C. (2018). Process Development of 99.95% Pure Copper Processed via Selective Electron Beam Melting and its Mechanical and Physical Properties. Mater. Charact. 143, 163–170. doi:10.1016/J.MATCHAR.2018.04.009
Ho, P. H., Ambrosetti, M., Groppi, G., Tronconi, E., Fornasari, G., Vaccari, A., et al. (2019). Electrodeposition of CeO2 and Pd-CeO2 on Small Pore Size Metallic Foams: Selection of Deposition Parameters. Catal. Today 334, 37–47. doi:10.1016/J.CATTOD.2019.02.005
Hosseini, S., Moghaddas, H., Masoudi Soltani, S., and Kheawhom, S. (2020). Technological Applications of Honeycomb Monoliths in Environmental Processes: A Review. Process Saf. Environ. Prot. 133, 286–300. doi:10.1016/J.PSEP.2019.11.020
Hurt, C., Brandt, M., Priya, S. S., Bhatelia, T., Patel, J., Selvakannan, P., et al. (2017). Combining Additive Manufacturing and Catalysis: a Review. Catal. Sci. Technol. 7, 3421–3439. doi:10.1039/C7CY00615B
Hutter, C., Büchi, D., Zuber, V., and Rudolf von Rohr, P. (2011). Heat Transfer in Metal Foams and Designed Porous media. Chem. Eng. Sci. 66, 3806–3814. doi:10.1016/j.ces.2011.05.005
Hydrogen - Fuels and Technologies - IEA (2021) Hydrogen - Fuels and Technologies - IEA. Available at: https://www.iea.org/fuels-and-technologies/hydrogen.
Inayat, A., Freund, H., Schwab, A., Zeiser, T., and Schwieger, W. (2011a). Predicting the Specific Surface Area and Pressure Drop of Reticulated Ceramic Foams Used as Catalyst Support. Adv. Eng. Mater. 13, 990–995. doi:10.1002/adem.201100038
Inayat, A., Schwerdtfeger, J., Freund, H., Körner, C., Singer, R. F., and Schwieger, W. (2011b). Periodic Open-Cell Foams: Pressure Drop Measurements and Modeling of an Ideal Tetrakaidecahedra Packing. Chem. Eng. Sci. 66, 2758–2763. doi:10.1016/j.ces.2011.03.031
Jang, J. T., Yoon, K. J., and Han, G. Y. (2014). Methane Reforming and Water Splitting Using Zirconia-Supported Cerium Oxide in a Volumetric Receiver-Reactor with Different Types of Foam Devices. Solar Energy 101, 29–39. doi:10.1016/j.solener.2013.12.019
Kapfer, S. C., Hyde, S. T., Mecke, K., Arns, C. H., and Schröder-Turk, G. E. (2011). Minimal Surface Scaffold Designs for Tissue Engineering. Biomaterials 32, 6875–6882. doi:10.1016/J.BIOMATERIALS.2011.06.012
Kapteijn, F., and Moulijn, J. A. (2022). Structured Catalysts and Reactors - Perspectives for Demanding Applications. Catal. Today 383, 5–14. doi:10.1016/J.CATTOD.2020.09.026
Klumpp, M., Inayat, a., Schwerdtfeger, J., Körner, C., Singer, R. F., Freund, H., et al. (2014). Periodic Open Cellular Structures with Ideal Cubic Cell Geometry: Effect of Porosity and Cell Orientation on Pressure Drop Behavior. Chem. Eng. J. 242, 364–378. doi:10.1016/j.cej.2013.12.060
Knorr, T., Heinl, P., Schwerdtfeger, J., Körner, C., Singer, R. F., and Etzold, B. J. M. (2012). Process Specific Catalyst Supports-Selective Electron Beam Melted Cellular Metal Structures Coated with Microporous Carbon. Chem. Eng. J. 181-182, 725–733. doi:10.1016/j.cej.2011.10.009
Kolb, G., Hessel, V., Cominos, V., Pennemann, H., Schürer, J., Zapf, R., et al. (2006). Microstructured Fuel Processors for Fuel-Cell Applications. J. Mater. Eng. Perform. 15, 389–393. doi:10.1361/105994906X117161
Kolb, G. (2013). Review: Microstructured Reactors for Distributed and Renewable Production of Fuels and Electrical Energy. Chem. Eng. Process. Process Intensification 65, 1–44. doi:10.1016/J.CEP.2012.10.015
Körner, C. (2016). Additive Manufacturing of Metallic Components by Selective Electron Beam Melting - A Review. Int. Mater. Rev. 61, 361–377. doi:10.1080/09506608.2016.1176289
Kränzlin, N., and Niederberger, M. (2015). Controlled Fabrication of Porous Metals from the Nanometer to the Macroscopic Scale. Mater. Horiz. 2, 359–377. doi:10.1039/C4MH00244J
Laguna, O. H., Lietor, P. F., Godino, F. J. I., and Corpas-Iglesias, F. A. (2021). A Review on Additive Manufacturing and Materials for Catalytic Applications: Milestones, Key Concepts, Advances and Perspectives. Mater. Des. 208, 109927. doi:10.1016/J.MATDES.2021.109927
Lämmermann, M., Schwieger, W., and Freund, H. (2016). Experimental Investigation of Gas-Liquid Distribution in Periodic Open Cellular Structures as Potential Catalyst Supports. Catal. Today 273, 161–171. doi:10.1016/j.cattod.2016.02.049
Lawson, S., Li, X., Thakkar, H., Rownaghi, A. A., and Rezaei, F. (2021). Recent Advances in 3D Printing of Structured Materials for Adsorption and Catalysis Applications. Chem. Rev. 121, 6246–6291. doi:10.1021/acs.chemrev.1c00060
Lecis, N., Mariani, M., Beltrami, R., Emanuelli, L., Casati, R., Vedani, M., et al. (2021). Effects of Process Parameters, Debinding and Sintering on the Microstructure of 316L Stainless Steel Produced by Binder Jetting. Mater. Sci. Eng. A 828, 142108. doi:10.1016/J.MSEA.2021.142108
Lefevere, J., Gysen, M., Mullens, S., Meynen, V., and Van Noyen, J. (2013). The Benefit of Design of Support Architectures for Zeolite Coated Structured Catalysts for Methanol-To-Olefin Conversion. Catal. Today 216, 18–23. doi:10.1016/J.CATTOD.2013.05.020
Lind, A., Vistad, Ø., Sunding, M. F., Andreassen, K. A., Cavka, J. H., and Grande, C. A. (2020). Multi-purpose Structured Catalysts Designed and Manufactured by 3D Printing. Mater. Des. 187, 108377–108378. doi:10.1016/j.matdes.2019.108377
Littwin, G., von Beyer, M., and Freund, H. (2021). Detailed Investigation of Liquid Distribution and Holdup in Periodic Open Cellular Structures Using Computed Tomography. Chem. Eng. Process. - Process Intensification 168, 108579. doi:10.1016/j.cep.2021.108579
Liu, Y., Zhou, W., Lin, Y., Chen, L., Chu, X., Zheng, T., et al. (2019). Novel Copper Foam with Ordered Hole Arrays as Catalyst Support for Methanol Steam Reforming Microreactor. Appl. Energ. 246, 24–37. doi:10.1016/J.APENERGY.2019.03.199
Lu, T. J., Stone, H. a., and Ashby, M. F. (1998). Heat Transfer in Open-Cell Metal Foams. Acta Materialia 46, 3619–3635. doi:10.1016/S1359-6454(98)00031-7
Lv, X., Ye, F., Cheng, L., Fan, S., and Liu, Y. (2019). Binder Jetting of Ceramics: Powders, Binders, Printing Parameters, Equipment, and post-treatment. Ceramics Int. 45, 12609–12624. doi:10.1016/J.CERAMINT.2019.04.012
Madeddu, S., Ueckerdt, F., Pehl, M., Peterseim, J., Lord, M., Kumar, K. A., et al. (2020). The CO2 Reduction Potential for the European Industry via Direct Electrification of Heat Supply (Power-to-heat). Environ. Res. Lett. 15, 124004. doi:10.1088/1748-9326/abbd02
Marin, C. M., Popczun, E. J., Nguyen-Phan, T.-D., Tafen, D. N., Alfonso, D., Waluyo, I., et al. (2021). Designing Perovskite Catalysts for Controlled Active-Site Exsolution in the Microwave Dry Reforming of Methane. Appl. Catal. B: Environ. 284, 119711. doi:10.1016/J.APCATB.2020.119711
Mehla, S., Das, J., Jampaiah, D., Periasamy, S., Nafady, A., and Bhargava, S. K. (2019). Recent Advances in Preparation Methods for Catalytic Thin Films and Coatings. Catal. Sci. Technol. 9, 3582–3602. doi:10.1039/C9CY00518H
Meille, V. (2006). Review on Methods to deposit Catalysts on Structured Surfaces. Appl. Catal. A: Gen. 315, 1–17. doi:10.1016/j.apcata.2006.08.031
Meloni, E., Martino, M., and Palma, V. (2020). A Short Review on Ni Based Catalysts and Related Engineering Issues for Methane Steam Reforming. Catalysts 10, 352. doi:10.3390/catal10030352
Meloni, E., Martino, M., Ricca, A., and Palma, V. (2021). Ultracompact Methane Steam Reforming Reactor Based on Microwaves Susceptible Structured Catalysts for Distributed Hydrogen Production. Int. J. Hydrogen Energ. 46, 13729–13747. doi:10.1016/J.IJHYDENE.2020.06.299
Mirzababaei, S., and Pasebani, S. (2019). A Review on Binder Jet Additive Manufacturing of 316L Stainless Steel. Jmmp 3, 82. doi:10.3390/jmmp3030082
Montebelli, A., Visconti, C. G., Groppi, G., Tronconi, E., Cristiani, C., Ferreira, C., et al. (2014). Methods for the Catalytic Activation of Metallic Structured Substrates. Catal. Sci. Technol. 4, 2846–2870. doi:10.1039/c4cy00179f
Mooraj, S., Qi, Z., Zhu, C., Ren, J., Peng, S., Liu, L., et al. (2021). 3D Printing of Metal-Based Materials for Renewable Energy Applications. Nano Res. 14, 2105–2132. doi:10.1007/s12274-020-3230-x
Mortensen, P. M., Engbæk, J. S., Vendelbo, S. B., Hansen, M. F., and Østberg, M. (2017). Direct Hysteresis Heating of Catalytically Active Ni-Co Nanoparticles as Steam Reforming Catalyst. Ind. Eng. Chem. Res. 56, 14006–14013. doi:10.1021/acs.iecr.7b02331
Murphy, D. M., Manerbino, A., Parker, M., Blasi, J., Kee, R. J., and Sullivan, N. P. (2013). Methane Steam Reforming in a Novel Ceramic Microchannel Reactor. Int. J. Hydrogen Energ. 38, 8741–8750. doi:10.1016/j.ijhydene.2013.05.014
Palma, V., Meloni, E., Renda, S., and Martino, M. (2020). Catalysts for Methane Steam Reforming Reaction: Evaluation of CeO2 Addition to Alumina-Based Washcoat Slurry Formulation. C. J. Carbon Res. 6, 52. doi:10.3390/c6030052
Palma, V., Pisano, D., Martino, M., and Ciambelli, P. (2016). Structured Catalysts with High Thermoconductive Properties for the Intensification of Water Gas Shift Process. Chem. Eng. J. 304, 544–551. doi:10.1016/J.CEJ.2016.06.117
Palma, V., Ruocco, C., Castaldo, F., Ricca, A., and Boettge, D. (2015). Ethanol Steam Reforming over Bimetallic Coated Ceramic Foams: Effect of Reactor Configuration and Catalytic Support. Int. J. Hydrogen Energ. 40, 12650–12662. doi:10.1016/j.ijhydene.2015.07.138
Palma, V., Ruocco, C., Cortese, M., and Martino, M. (2019). Recent Advances in Structured Catalysts Preparation and Use in Water-Gas Shift Reaction. Catalysts 9, 991. doi:10.3390/catal9120991
Papetti, V., Dimopoulos Eggenschwiler, P., Della Torre, A., Lucci, F., Ortona, A., and Montenegro, G. (2018). Additive Manufactured Open Cell Polyhedral Structures as Substrates for Automotive Catalysts. Int. J. Heat Mass Transfer 126, 1035–1047. doi:10.1016/j.ijheatmasstransfer.2018.06.061
Park, D., Moon, D. J., and Kim, T. (2014). Preparation and Evaluation of a Metallic Foam Catalyst for steam-CO2 Reforming of Methane in GTL-FPSO Process. Fuel Process. Tech. 124, 97–103. doi:10.1016/J.FUPROC.2014.02.021
Park, D., Moon, D. J., and Kim, T. (2013). Steam-CO2 Reforming of Methane on Ni/γ-Al2O3-Deposited Metallic Foam Catalyst for GTL-FPSO Process. Fuel Process. Tech. 112, 28–34. doi:10.1016/J.FUPROC.2013.02.016
Parra-Cabrera, C., Achille, C., Kuhn, S., and Ameloot, R. (2018). 3D Printing in Chemical Engineering and Catalytic Technology: Structured Catalysts, Mixers and Reactors. Chem. Soc. Rev. 47, 209–230. doi:10.1039/c7cs00631d
Paserin, V., Marcuson, S., Shu, J., and Wilkinson, D. S. (2004). CVD Technique for Inco Nickel Foam Production. Adv. Eng. Mater. 6, 454–459. doi:10.1002/adem.200405142
Pelanconi, M., and Ortona, A. (2021), “Review on the Design Approaches of Cellular Architectures Produced by Additive Manufacturing,” in Review on the Design Approaches of Cellular Architectures Produced by Additive Manufacturing BT - Industrializing Additive Manufacturing. eds. M. Meboldt, and C. Klahn (Cham: Springer International Publishing), 52–64.doi:10.1007/978-3-030-54334-1_5
Pérez-Camacho, M. N., Abu-Dahrieh, J., Rooney, D., and Sun, K. (2015). Biogas Reforming Using Renewable Wind Energy and Induction Heating. Catal. Today 242, 129–138. doi:10.1016/J.CATTOD.2014.06.010
Qi, J., Sun, Y., Xie, Z., Collins, M., Du, H., and Xiong, T. (2015). Development of Cu Foam-Based Ni Catalyst for Solar thermal Reforming of Methane with Carbon Dioxide. J. Energ. Chem. 24, 786–793. doi:10.1016/j.jechem.2015.10.001
Renda, S., Cortese, M., Iervolino, G., Martino, M., Meloni, E., and Palma, V. (2022). Electrically Driven SiC-Based Structured Catalysts for Intensified Reforming Processes. Catal. Today 383, 31–43. doi:10.1016/J.CATTOD.2020.11.020
Richardson, J. T., Peng, Y., and Remue, D. (2000). Properties of Ceramic Foam Catalyst Supports: Pressure Drop. Appl. Catal. A: Gen. 204, 19–32. doi:10.1016/S0926-860X(00)00508-1
Rieks, M., Bellinghausen, R., Kockmann, N., and Mleczko, L. (2015). Experimental Study of Methane Dry Reforming in an Electrically Heated Reactor. Int. J. Hydrogen Energ. 40, 15940–15951. doi:10.1016/J.IJHYDENE.2015.09.113
Rombouts, M., Kruth, J. P., Froyen, L., and Mercelis, P. (2006). Fundamentals of Selective Laser Melting of Alloyed Steel Powders. CIRP Ann. 55, 187–192. doi:10.1016/S0007-8506(07)60395-3
Roy, P. S., Park, N.-K., and Kim, K. (2014). Metal Foam-Supported Pd-Rh Catalyst for Steam Methane Reforming and its Application to SOFC Fuel Processing. Int. J. Hydrogen Energ. 39, 4299–4310. doi:10.1016/J.IJHYDENE.2014.01.004
Roy, P. S., Raju, A. S. K., and Kim, K. (2015). Influence of S/C Ratio and Temperature on Steam Reforming of Model Biogas over a Metal-Foam-Coated Pd–Rh/(CeZrO 2 –Al 2 O 3 ) Catalyst. Fuel 139, 314–320. doi:10.1016/J.FUEL.2014.08.062
Ryu, J.-H., Lee, K.-Y., La, H., Kim, H.-J., Yang, J.-I., and Jung, H. (2007). Ni Catalyst Wash-Coated on Metal Monolith with Enhanced Heat-Transfer Capability for Steam Reforming. J. Power Sourc. 171, 499–505. doi:10.1016/J.JPOWSOUR.2007.05.107
Sahu, N., Parija, B., and Panigrahi, S. (2009). Fundamental Understanding and Modeling of Spin Coating Process: A Review. Indian J. Phys. 83, 493–502. doi:10.1007/s12648-009-0009-z
Sang, L., Sun, B., Tan, H., Du, C., Wu, Y., and Ma, C. (2012). Catalytic Reforming of Methane with CO2 over Metal Foam Based Monolithic Catalysts. Int. J. Hydrogen Energ. 37, 13037–13043. doi:10.1016/j.ijhydene.2012.05.056
Sanz, O., Velasco, I., Reyero, I., Legorburu, I., Arzamendi, G., Gandía, L. M., et al. (2016). Effect of the thermal Conductivity of Metallic Monoliths on Methanol Steam Reforming. Catal. Today 273, 131–139. doi:10.1016/J.CATTOD.2016.03.008
Scarfiello, C., Bellusci, M., Pilloni, L., Pietrogiacomi, D., La Barbera, A., and Varsano, F. (2021). Supported Catalysts for Induction-Heated Steam Reforming of Methane. Int. J. Hydrogen Energ. 46, 134–145. doi:10.1016/J.IJHYDENE.2020.09.262
Serp, P., Kalck, P., and Feurer, R. (2002). Chemical Vapor Deposition Methods for the Controlled Preparation of Supported Catalytic Materials. Chem. Rev. 102, 3085–3128. doi:10.1021/cr9903508
Shen, C.-C., Jian, T.-Y., and Wang, Y.-T. (2013). Steam Reforming of Methanol in a Compact Copper Microchannel Foam Reactor. Fuel Cells 13, 965–970. doi:10.1002/fuce.201300169
Simakov, D. S. A., Wright, M. M., Ahmed, S., Mokheimer, E. M. A., Román-Leshkov, Y., and Romn-Leshkov, Y. (2015). Solar thermal Catalytic Reforming of Natural Gas: A Review on Chemistry, Catalysis and System Design. Catal. Sci. Technol. 5, 1991–2016. doi:10.1039/C4CY01333F
Soliman, A., AlAmoodi, N., Karanikolos, G. N., Doumanidis, C. C., and Polychronopoulou, K. (2020). A Review on New 3-D Printed Materials' Geometries for Catalysis and Adsorption: Paradigms from Reforming Reactions and CO2 Capture. Nanomaterials 10, 2198. doi:10.3390/nano10112198
Specchia, S. (2014). Fuel Processing Activities at European Level: A Panoramic Overview. Int. J. Hydrogen Energ. 39, 17953–17968. doi:10.1016/J.IJHYDENE.2014.04.040
Stankiewicz, A. I., and Nigar, H. (2020). Beyond Electrolysis: Old Challenges and New Concepts of Electricity-Driven Chemical Reactors. React. Chem. Eng. 5, 1005–1016. doi:10.1039/D0RE00116C
Stefanidis, G. D., and Vlachos, D. G. (2010). Intensification of Steam Reforming of Natural Gas: Choosing Combustible Fuel and Reforming Catalyst. Chem. Eng. Sci. 65, 398–404. doi:10.1016/j.ces.2009.06.007
Stiegler, T., Meltzer, K., Tremel, A., Baldauf, M., Wasserscheid, P., and Albert, J. (2019). Development of a Structured Reactor System for CO 2 Methanation under Dynamic Operating Conditions. Energy Technol. 7, 1900047–1900112. doi:10.1002/ente.201900047
Sutygina, A., Betke, U., Hasemann, G., and Scheffler, M. (2020a). Manufacturing of Open-Cell Metal Foams by the Sponge Replication Technique. IOP Conf. Ser. Mater. Sci. Eng. 882, 012022. doi:10.1088/1757-899x/882/1/012022
Sutygina, A., Betke, U., and Scheffler, M. (2021). Hierarchical‐Porous Copper Foams by a Combination of Sponge Replication and Freezing Techniques. Adv. Eng. Mater., 2001516. doi:10.1002/adem.202001516
Sutygina, A., Betke, U., and Scheffler, M. (2019). Open-Cell Aluminum Foams by the Sponge Replication Technique. Materials 12, 3840. doi:10.3390/ma12233840
Sutygina, A., Betke, U., and Scheffler, M. (2020b). Open‐Cell Aluminum Foams by the Sponge Replication Technique: A Starting Powder Particle Study. Adv. Eng. Mater. 22, 1901194. doi:10.1002/adem.201901194
Tran, T. Q., Chinnappan, A., Lee, J. K. Y., Loc, N. H., Tran, L. T., Wang, G., et al. (2019). 3D Printing of Highly Pure Copper. Metals 9, 756. doi:10.3390/met9070756
Tronconi, E., Groppi, G., Boger, T., and Heibel, A. (2004). Monolithic Catalysts with 'high Conductivity' Honeycomb Supports for Gas/solid Exothermic Reactions: Characterization of the Heat-Transfer Properties. Chem. Eng. Sci. 59, 4941–4949. doi:10.1016/J.CES.2004.07.018
Tronconi, E., Groppi, G., and Visconti, C. G. (2014). Structured Catalysts for Non-adiabatic Applications. Curr. Opin. Chem. Eng. 5, 55–67. doi:10.1016/j.coche.2014.04.003
Varsano, F., Bellusci, M., La Barbera, A., Petrecca, M., Albino, M., and Sangregorio, C. (2019). Dry Reforming of Methane Powered by Magnetic Induction. Int. J. Hydrogen Energ. 44, 21037–21044. doi:10.1016/J.IJHYDENE.2019.02.055
Vervloet, D., Kapteijn, F., Nijenhuis, J., and van Ommen, J. R. (2013). Process Intensification of Tubular Reactors: Considerations on Catalyst Hold-Up of Structured Packings. Catal. Today 216, 111–116. doi:10.1016/j.cattod.2013.05.019
Vinum, M. G., Almind, M. R., Engbæk, J. S., Vendelbo, S. B., Hansen, M. F., Frandsen, C., et al. (2018). Dual‐Function Cobalt-Nickel Nanoparticles Tailored for High‐Temperature Induction‐Heated Steam Methane Reforming. Angew. Chem. Int. Ed. 57, 10569–10573. doi:10.1002/anie.201804832
Visconti, C. G., Groppi, G., and Tronconi, E. (2016). Highly Conductive "packed Foams": A New Concept for the Intensification of Strongly Endo- and Exo-Thermic Catalytic Processes in Compact Tubular Reactors. Catal. Today 273, 178–186. doi:10.1016/j.cattod.2016.02.060
Visconti, C. G., Tronconi, E., Lietti, L., Groppi, G., Forzatti, P., Cristiani, C., et al. (2009). An Experimental Investigation of Fischer-Tropsch Synthesis over Washcoated Metallic Structured Supports. Appl. Catal. A: Gen. 370, 93–101. doi:10.1016/j.apcata.2009.09.023
Wang, W., Tuci, G., Duong-Viet, C., Liu, Y., Rossin, A., Luconi, L., et al. (2019a). Induction Heating: An Enabling Technology for the Heat Management in Catalytic Processes. ACS Catal. 9, 7921–7935. doi:10.1021/acscatal.9b02471
Wang, Z., Zhao, K., Xiao, B., Gao, P., He, D., Cai, T., et al. (2019b). Fabrication of Monolithic Catalysts: Comparison of the Traditional and the Novel Green Methods. Catalysts 9, 981. doi:10.3390/catal9120981
Wismann, S. T., Engbæk, J. S., Vendelbo, S. B., Bendixen, F. B., Eriksen, W. L., Aasberg-Petersen, K., et al. (2019a). Electrified Methane Reforming: A Compact Approach to Greener Industrial Hydrogen Production. Science 364, 756–759. doi:10.1126/science.aaw8775
Wismann, S. T., Engbæk, J. S., Vendelbo, S. B., Eriksen, W. L., Frandsen, C., Mortensen, P. M., et al. (2021). Electrified Methane Reforming: Elucidating Transient Phenomena. Chem. Eng. J. 425, 131509. doi:10.1016/J.CEJ.2021.131509
Wismann, S. T., Engbæk, J. S., Vendelbo, S. B., Eriksen, W. L., Frandsen, C., Mortensen, P. M., et al. (2019b). Electrified Methane Reforming: Understanding the Dynamic Interplay. Ind. Eng. Chem. Res. 58, 23380–23388. doi:10.1021/acs.iecr.9b04182
Yu, H., Chen, H., Pan, M., Tang, Y., Zeng, K., Peng, F., et al. (2007). Effect of the Metal Foam Materials on the Performance of Methanol Steam Micro-reformer for Fuel Cells. Appl. Catal. A: Gen. 327, 106–113. doi:10.1016/j.apcata.2007.05.003
Zhang, H., Suszynski, W. J., Agrawal, K. V., Tsapatsis, M., Al Hashimi, S., and Francis, L. F. (2012). Coating of Open Cell Foams. Ind. Eng. Chem. Res. 51, 9250–9259. doi:10.1021/ie300266p
Zhang, Y., Wu, L., Guo, X., Kane, S., Deng, Y., Jung, Y.-G., et al. (2018). Additive Manufacturing of Metallic Materials: A Review. J. Materi Eng. Perform. 27, 1–13. doi:10.1007/s11665-017-2747-y
Zhao, M., Liu, F., Fu, G., Zhang, D., Zhang, T., and Zhou, H. (2018). Improved Mechanical Properties and Energy Absorption of BCC Lattice Structures with Triply Periodic Minimal Surfaces Fabricated by SLM. Materials 11, 2411. doi:10.3390/ma11122411
Zhou, W., Ke, Y., Wang, Q., Wan, S., Lin, J., Zhang, J., et al. (2017). Development of Cylindrical Laminated Methanol Steam Reforming Microreactor with Cascading Metal Foams as Catalyst Support. Fuel 191, 46–53. doi:10.1016/j.fuel.2016.11.058
Zhou, X., Jin, Y., and Du, J. (2020). Functionally Graded Scaffolds with Programmable Pore Size Distribution Based on Triply Periodic Minimal Surface Fabricated by Selective Laser Melting. Materials 13, 5046. doi:10.3390/ma13215046
Zhou, X., and Liu, C.-J. (2017). Three-dimensional Printing for Catalytic Applications: Current Status and Perspectives. Adv. Funct. Mater. 27, 1701134. doi:10.1002/adfm.201701134
Ziaee, M., and Crane, N. B. (2019). Binder Jetting: A Review of Process, Materials, and Methods. Additive Manufacturing 28, 781–801. doi:10.1016/J.ADDMA.2019.05.031
Keywords: process intensification, additive manufacturing, steam reforming, structured catalysts, hydrogen production
Citation: Balzarotti R, Ambrosetti M, Beretta A, Groppi G and Tronconi E (2022) Recent Advances in the Development of Highly Conductive Structured Supports for the Intensification of Non-adiabatic Gas-Solid Catalytic Processes: The Methane Steam Reforming Case Study. Front. Chem. Eng. 3:811439. doi: 10.3389/fceng.2021.811439
Received: 09 November 2021; Accepted: 20 December 2021;
Published: 17 January 2022.
Edited by:
Sébastien Thomas, l'Environnement et la Santé (ICPEES), FranceReviewed by:
Stefania Specchia, Politecnico di Torino, ItalyConcetta Ruocco, University of Salerno, Italy
Regis Philippe, CP2M (UMR 5128 CNRS/CPE Lyon/UCBL), France
Frederik Kapteijn, Delft University of Technology, Netherlands
Copyright © 2022 Balzarotti, Ambrosetti, Beretta, Groppi and Tronconi. This is an open-access article distributed under the terms of the Creative Commons Attribution License (CC BY). The use, distribution or reproduction in other forums is permitted, provided the original author(s) and the copyright owner(s) are credited and that the original publication in this journal is cited, in accordance with accepted academic practice. No use, distribution or reproduction is permitted which does not comply with these terms.
*Correspondence: Enrico Tronconi, ZW5yaWNvLnRyb25jb25pQHBvbGltaS5pdA==