- Matelys - Research Lab, Vaulx-en-Velin, France
Understanding and predicting the vibro-acoustic behavior of acoustical porous materials (like foams, synthetic or natural fibers, metamaterials...) requires to determine the parameters of their solid and their fluid phases. This work presents an non-exhaustive overview of the methods commonly used to assess the visco-elastic and acoustic parameters of such acoustic porous media. A first part is dedicated to identify the parameters related to the dissipation in the fluid phase while a second part focuses on the identification of the parameters related to the solid phase (also called the skeleton). The perspectives related to the characterization of acoustical porous media are also depicted, particularly in the context of recent and ongoing standardization developments.
1 Introduction
Traditionally, 2 types of characterization are considered for an acoustical porous material: the acoustic one related to its fluid phase and the elastic (or more rigorously viscoelastic) one related to its solid phase (also called the skeleton of the porous medium). These 2 characterizations can be considered as independent in some cases, while in general they are not, since the fluid phase can influence the solid behavior and vice versa. The seminal work by M. A. Biot is often used to account for the coupling between these 2 phases (Biot, 1956a; Biot, 1956b, Biot, 1962; Allard and Atalla, 2009; Jaouen, 2025a).
The acoustic parameters of the fluid phase, for an isotropic material, are those required to compute its dynamic mass density
1. The open porosity
2. The static air-flow resistivity
3. The high frequency limit of the dynamic tortuosity
4. The viscous characteristic length
5. The thermal characteristic length
6. The static thermal permeability
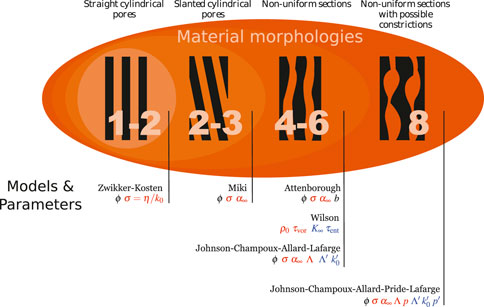
Figure 1. Schematic representation of profiles of pore networks and models that can be used to describe these morphologies. The more complicated the morphology, the more parameters are required. In blue: parameters related to the visco-inertial dissipation effects and in red: the parameters of the thermal dissipation effects.
The elastic parameters of the solid phase are, again for an isotropic material, its mass density
The model involving the 6 JCAL parameters discussed for the fluid phase above and the 4 elastic parameters above for the solid phase, i.e., 10 parameters in total, is referred to as the Biot-JCAL model.
Some models for the fluid phase require less than 6 parameters depending on the morphology assumption of the pore structure or the physical phenomena involved. As examples the Delany-Bazley-Miki (DBM) model (Delany and Bazley, 1970; Miki, 1990) only requires
Similarly, some models for the solid phase are derived from Biot equations with some simplifications. The limp model for a light material with a Young’s modulus close to 0 (like a cotton candy) requires only the mass density
Hence, other examples of models to describe the behavior of acoustical porous materials are: the limp-DBM or the rigid-body-JCA.
In the next sections of this document, we will focus on (i) the hypotheses used regarding the materials to be characterized, (ii) the characterization of the acoustic parameters of the fluid phase, (iii) the characterization of the elastic parameters of the solid phase, (iv) some general considerations regarding the characterization of acoustical porous media. This document cannot be exhaustive and does not aim to provide a complete review of the characterization methods but rather to give some guidelines.
2 Hypotheses
To characterize acoustical porous media, assuming they are composed of only 2 phases: a fluid and a solid, the following hypotheses apply.
• Both the fluid and solid phases are assumed to be continuous (so that the theory of continuous media can be applied to both phases)
• The pore size within the material is small compared to the wavelengths of the waves involved, ensuring that the material can be descibed by an Representative Elementary Volume (REV) and behaves as a homogeneous medium at the macroscopic level (Bensoussan et al., 1978; Auriault et al., 2010). Note that while
• A no-slip condition as well as a thermodynamic equilibrium at the interface between the fluid and the solid phases are commonly assumed in most models. While this hypothesis is not mandatory, it reduces the number of parameters to be evaluated.
3 Characterization of the acoustic parameters
In this section, we focus on the characterization of the parameters related to the fluid phase and in particular to the parameters of the Johnson-Champoux-Allard-Lafarge (JCAL) model. Other models and parameters exist (see, e.g., Wilson (1993), Horoshenkov et al. (2019), but they can be expressed as those of the JCAL one (Jaouen, 2025b).
Note that the titles of some references mention the characterization of “acoustic and non-acoustic” parameters, following the request of some reviewers, in previous articles published by, e.g., Doutres et al. (2010), who argued that porosity, for example, is not a parameter used only in acoustics and therefore cannot be labeled as an acoustic parameter.
The techniques are divided into two distinct categories: direct measurements are those for which an analog or numerical signal can be directly correlated to the value of the parameter while indirect estimations are all other methods.
Only some of the acoustical parameters used to describe the visco-inertial and thermal behviors of acoustical porous materials are directly measurable. The open porosity, the static air flow resistivity and the high frequency limit of the dynamic tortuosity can be directly measured. The devices used in these cases are borrowed from science fields related to other porous materials (such as rocks) or are adapted from these other porous materials to acoustical ones (which have usually very large permeability and porosity compared to rocks).
The remaining part of the acoustical parameters
3.1 Direct measurements
Direct measurements were the first to be developed and are still commonly used today to double check the results of indirect estimations.
3.1.1 Static air-flow resistivity
The first parameter to be directly measured is the static air-flow resistivity
3.1.2 Open porosity
The second parameter to be directly measured is the open porosity
A first method, for acoustical porous materials with porosity close to 1, was introduced by Beranek (1942) and was later improved or adapted [see, e.g., Champoux et al. (1991), Leclaire et al. (2003)]. The principle is to reduce the volume of an enclosure containing a material sample. Doing so, the pressure will increase in the enclosure compared to the atmospheric pressure. This increase in pressure depends on the volume of the enclosure and the volume accessible to the air inside the porous medium. By measuring the pressure increase it is possible to determine the open porosity of the material. This method is close to the one used for geomaterials called gas picnometer, detailed in various standards, which is based on the injection of a gas under pressure in the volume enclosure. One keypoint is that the larger the samples the more accurate will be the results.
An alternative technique is based on Archimedes’ principle (Panneton and Gros, 2005; Salissou and Panneton, 2007): the porosity is measured by weighing a sample of known volume and then saturating it with a fluid of known density. Again, accurate measurements are obtained with large samples.
3.1.3 High-frequency limit of the tortuosity
Brown (1980), then Johnson et al. (1982) published methods for measuring the high frequency limit of the tortuosity from the determination of the electrical resistance at the extremities of a porous sample for which an electrically charged liquid has saturated the fluid phase.
One difficulty with these methods is saturating the sample, which can be difficult for materials with small pore sizes of a few microns or tens of micron, while these materials typically exhibit the highest tortuosity values. These methods, which are no longer in use, also require the skeleton of the tested material to be an electrical insulator and prior knowledge of the open porosity.
3.2 Indirect estimations
Indirect estimations are based on the measurement of one or more physical quantities in combination with a model (sometimes only its physical asymptotic limits).
Inverse methods are a large part of indirect estimations. There are two types of inversions: numerical and analytical. Numerical inversions are based on minimization techniques between a numerical simulation and at least one indicator such as the sound absorption coefficient, the surface impedance, the characteristic wavenumber... The estimation of more than two parameters usually relies on a multiple indicators to avoid local minima during the minimization step.
Analytical inversions rely on analytical expressions to identify the parameters.
3.2.1 Ultrasound frequencies approach
The tortuosity
One keypoint of this method is that it is a quick method which was then used to mapped heterogeneity of material samples. One limit is however that at ultrasound frequencies, the multiple scattering phenomenon can appear in porous media with a characteristic pore size of hundreds of microns. This multiple scattering is not accounted for in classical visco-thermal dissipation models and require additional developments [see, e.g., Tournat et al., (2004)]. While trying to estimate more parameters (
Later, based on the work of Panneton and Only in the audible frequencies range, Groby et al. (2010) have proposed a method to extract
Currently, high-frequency methods are being developed to estimate the parameters
3.2.2 Audible frequency approach
3.2.2.1 Whole frequency range
The first attempts to characterize the visco-inertial and thermal dissipation effects of porous media over audible frequency ranges were made by minimization techniques, in diffuse sound field, or more commonly in impedance tubes (with more controlled excitation, at plane waves and normal incidence) (International Organization for Standardization ISO, 2023). Then, analytical techniques were developed to assess the dynamic bulk properties
The impedance tube gained in popularity in the late 1990s when the process to extract
Note that the 3-microphone technique is currently in the process of being standardized via ISO 10534-3 International Organization for Standardization (ISO) (proposition submitted).
A drawback of impedance tube methods is that the boundary conditions can influence the overall behaviors of
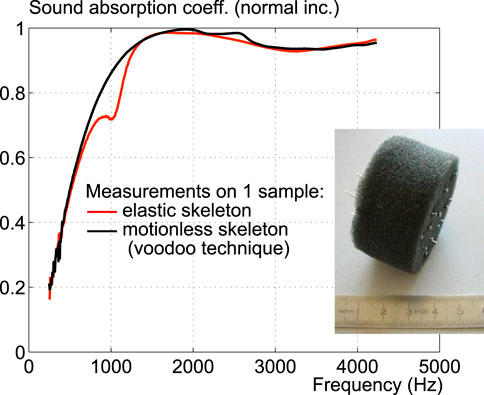
Figure 2. The “Voodoo” technique relies on adding nails to the material sample as described in Iwase et al. (1998) to reduce or shift the frequencies of the skeleton resonances.
3.2.2.2 Asymptotic limits
The low-frequency limit of the imaginary part
The open-porosity can also be estimated from high and low frequency asymptotes. As an example, Jaouen et al. (2020) estimate the open porosity from the low and high frequency limits of the real part
The drawback of these methods being the possible difficulty in identifying the asymptotes due to the limited spacing between the microphones at low frequencies, the diameter of the tube at high frequencies and possible vibrations of the skeleton of the porous sample.
3.2.3 Time domain methods
In the early 2000s, theoretical and experimental developments were also made in the time domain.
Fellah et al. (2003) presented a method for estimating the porosity and the tortuosity of a porous material sample from the reflected impulse waves. This method is limited to highly absorbing samples as it approximates the reflected waves as coming only from the first interface with air.
Two additional methods were developed a few years later to estimate the static air-flow resistivity from the reflected waves Sebaa et al. (2005) or the transmitted waves Fellah et al. (2006) depending on the resistance of the sample. Numerical inversions (i.e., minimization techniques) were used to extract the value of the air-flow resistivity with the prior knowledge of the porosity.
Measurements in the time domain and analysis in both the time and the frequency domains were used, for transmitted waves, to estimate
While the time domain approach is in a sparse state of development, it offers perspectives for complementary robust characterization methods.
3.2.4 Pore size distribution and microtomography
Less common methods for estimating the parameters of the fluid phase include measuring the material’s Pore Size Distribution (PSD) or extracting its microstructure (at the Representative Elementary Volume) from 3D microtomography scans (Horoshenkov et al., 2016, Horoshenkov et al., 2019; Perrot et al., 2012; Chevillotte et al., 2013).
The pore size distribution is usually obtained by typical methods such as mercury intrusion into the pore network. 3D microtomography acquisitions being expensive, 2D images are usually preferred with the added difficulty of capturing the third dimension which can result in inaccurate microstructure dimensions or large uncertainties about these dimensions, and hence inaccurate or uncertain material parameters.
From the microstructural information extracted by one or the other method, the parameters of a Johnson-Champoux-Allard-Lafarge model or even a Johnson-Champoux-Allard-Pride-Lafarge model (Pride et al., 1993) with 2 additional low-frequency parameters usually denoted as
3.3 A note about thin porous media
The acoustic characterization of facing screens or perforated plates, typically with a thickness of a few millimeters or less, has been less addressed. Like Maa between the 1970s and the 1990s (Maa, 1975; Maa, 1998; Atalla and Sgard, 2007), in 2007, used the models developed for thicker porous media (Atalla and Sgard benefited from an update of the models to the JCA and JCAL ones compared to Maa) while adding a correction to account for the flow distortion around the pores or perforations (see Figure 3). The associated length correction Jaouen and Chevillotte (2018) introduces additional viscous dissipation that is not negligible compared to the viscous dissipation occurring within the pores or perforations themselves.
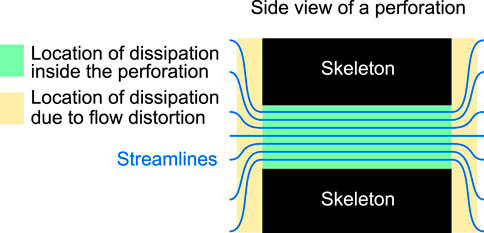
Figure 3. Length correction due to flow distortion for thin porous media. The smaller the perforation rate (i.e., the porosity), the larger the added dissipation.
Based on Atalla and Sgard model (Jaouen and Bécot, 2011), developed an inverse analytical method to estimate the independent parameters required from the measurements of the thin porous material backed by a cavity in an impedance tube.
3.4 Work in progress and perspectives
The methods presented in the previous sections still require attention, as some subtleties remain. For example, at ultrasonic frequencies, it is not always easy to determine whether scattering effects are involved. In the impedance tube, dealing with the limp, rigid body or, more generally, the motion or vibration of the skeleton can also be challenging.
Some work is still in progress to characterize the materials in different environments or conditions (and the references given up to the next section do not all refer to characterization, but sometimes to models, as no characterization is yet known to the authors). For example, at high temperature (for muffler or thermo-acoustic applications) (Debray, 2000; Di Giulio et al., 2024), at high pressure (Aurégan and Pachebat, 1999; Temiz et al., 2016; Chevillotte et al., 2017), with a fluid phase partially or totally saturated with water (for building and underwater applications) Chabriac et al., 2016; Gourlay et al., 2017), with flow (for aviation or appliance applications), in-situ (for end-of-chain applications).
On a different note, while the main dissipation phenomena are the same for all materials (including, for example, materials with inner quarter-wavelength or Helmholtz resonators): visco-inertial, thermal and structural damping in the skeleton, some techniques are being developed to handle the specificities of multiple dynamics, aka “metamaterials”. Examples of materials for which developments are in progress include: activated carbon exhibiting a sorption phenomenon (making it impossible to measure porosity directly) (Castillo, 2011; Bechwati et al., 2012; Shen and Jiang, 2014; Venegas and Umnova, 2016) natural fibers which typically exhibit multiple scales of porosity (as were the materials manufactured using the first 3D printing technologies but this tendency is decreasing as printing precision improves), as well as materials with fractal microstructures (Jaouen and Olny, 2005; Fellah et al., 2021); nanomaterials for which it can be difficult to manufacture prototype samples with a number of cells large enough to have dimensions suitable for testing using impedance tubes or ultrasound techniques.
As reported above, standardization methods are trying to adapt to these new methods and new materials at a faster pace than ever before (International Organization for Standardization, 2025). They also provide a more critical and informative approach to some techniques, as in the case of ASTM E2611-2019 (ASTM International, 2019) and a possible future ISO 10534-4 International Organization for Standardization (ISO) (proposition to be submitted) (4 microphones), by explaining the fundamental differences between diffuse field transmission measurement on large samples and impedance tube transmission measurement on small samples (International Organization for Standardization, 2024).
4 Characterization of the elastic parameters
Most of the experimental methods used to characterize visco-elastic parameters (Young’s moduli, loss factors and Poisson’s ratios) are adaptations of techniques used for polymers or metal (Gibson and Ashby, 1997; Corsaro and Sperling, 1990; Hilyard and Cunningham, 1994) (note that the terms elastic and visco-elastic parameters are used interchangeably to refer to the parameters of the solid phase). Modifications of existing devices are usually made to account for the interaction between the two phases of an acoustical porous material or to account for specific ranges of values for these acoustical porous materials. Young’s moduli and loss factors of acoustical materials range from approximately
A wide variety of methods exist to characterize the visco-elastic parameters of the solid phase of porous materials. They are typically divided into different categories according to their frequency regime: static/quasistatic or dynamic and their vibration nature: uniaxial compression, torsion, bending…
An almost exhaustive list was given in Jaouen et al. (2008) and is still relevant today. Interlaboratory tests have followed [see, e.g., Bonfiglio et al. (2018), Chevillotte et al. (2020)]. Thus this work will not enumerate all the methods, but will emphasize several key features.
From interlaboratory tests, large deviations were observed between the values of the elastic parameters obtained by different methods. The main deviations were coming from the frequency range and the initial condition (imposed load or imposed strain).
The uni-axial compression [in the quasistatic regime Langlois et al. (2001) or in the dynamic one as described in, e.g., (International Organization for Standardization ISO, 1989; Bonfiglio and Pompoli, 2015)], on cubic or short cylindrical samples, is probably the most common method used (due to its apparent simplicity). By examining the difficulties of such methods, it is possible to highlight the critical aspects of viscoelastic characterization of porous materials.
Apart from the issues of cutting and positioning the material sample in the test bench, the uni-axial compression methods is influenced by factors such as.
1. The possible anisotropy of the material,
2. The environment conditions and in particular the temperature and the frequency (as these factors can significantly influence the elastic moduli and their loss factors),
3. The static strain or stress dependence of the material,
4. The coupling with the fluid phase (as air enters and leaves the sample during the compression test)
Point 1, the anisotropy, is particularly important for fibrous materials as the elastic parameters in the direction of the fibers can differ significantly from those in perpendicular directions. Successive uni-axial compression tests on 3 different axes (assuming they are the principal axes of the materials) only provide estimations of the elastic parameters.
Point 2, the temperature and frequency dependence is illustrated in Figure 4. Visco-elastic materials (compared to elastic materials) exhibit strain and energy dissipations that are time-dependent. This time dependence implies a frequency dependence as well as a temperature dependence according to the Time-Temperature Superposition (TTS). This point is particularly important for a material with a polymer skeleton, since its glass transition temperature (or frequency) is usually (designed to be) between −20 and 20°C (or a few Hz to a few thousand Hz). While visco-elastic models evolve with mathematical tools such as fractional derivatives, commonly involving between 5 and 7 parameters (Dinzart and Lipiński, 2010; Gourdon et al., 2015), it can be observed that there are still few characterizations made at different temperatures and frequencies.
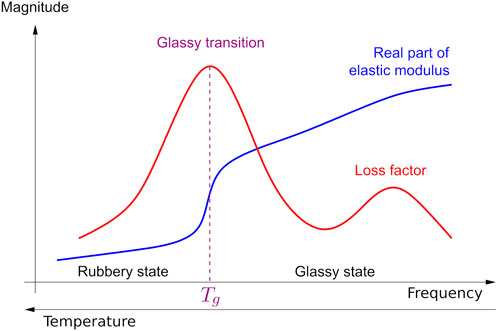
Figure 4. Schematic representation of the evolution of a complex modulus with time and frequency as per the Time-Temperature Superposition (TTS) principle or more rigoursly here its frequency representation.
Point 3, the static strain or stress dependence is illustrated in Figure 5. Estimation of the visco-elastic parameters requires, or at least is much easier, to be in region 1 of Figure 5, where the linear visco-elastic theory can be applied. It is worth noting that only a few studies on the hysteresis effect in porous materials have been carried out (Guyer et al., 1997; Gusev and Aleshin, 2002) and this field of research is still wide open. Point 3 highlights the fact that it is necessary for the rigorous experimenter to perform a strain-stress measurement before the actual visco-elastic characterization. It is noteworthy that there is no linear range for fibers, due to their microstructures, which reinforces the fact that the static strain or stress used during the tests should be reported and adapted to the application in which the material will be used. An additional difficulty with the dynamic uni-axial compression method (based on the resonance of a mass-spring system, the porous sample playing the role of a heavy spring) is that the frequency range and the static stress and strain are not independent.
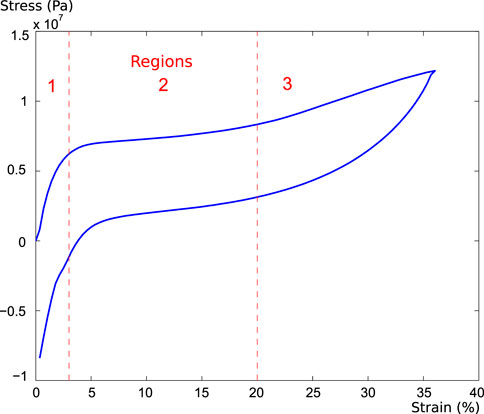
Figure 5. Strain vs stress measurement of a foam showing a hysteresis behavior. Region 1 is a linear bending region, region 2 is the buckling region, region 3 is the densification region where the foam behaves as a solid material after the cells have collapsed.
Point 4, the coupling with the fluid phase, has been studied by a few authors including Kraak (1959) [and discussed further in Schmelzer et al. (2021)] and Danilov et al. (2004). In his work, W. Kraak has proposed a correction to the measurement of the elastic properties of the material sample based on the transverse resistivity of the material (i.e., in a direction perpendicular to the axis of compression). This correction is currently considered to be included in an ongoing revision of ISO 9052-1 (International Organization for Standardization ISO, 1989). Danilov et al. on the other hand have pointed out the importance of staying at low frequencies (below 50–100 Hz) to avoid a significant influence of the fluid phase on the results of the elastic characterization.
Once these first 4 points have been addressed, it remains to estimate the complex Young’s modulus and possibly the Poisson’s ratio, assuming an isotropic material. Indeed, the test result for the uni-axial compression test on a material is the complex stiffness of the material sample (a function of its complex Young’s modulus, Poisson’s ratio and dimensions). Some authors refer to the “apparent Young’s modulus”, another quantity derived from the stiffness. The apparent Young’s modulus is equal to the Young’s modulus only when the Poisson’s ratio is 0 [i.e., for fibrous materials without specific surface or bulk treatment Tarnow, 2005; Berthelot, 1999]. In all the other cases, a difficult direct measurement of the Poisson’s ratio from a transverse displacement is required, or alternatively and most commonly, 2 samples with different shape factors must be tested to determine the Young’s modulus and the Poisson’s ratio using a pre-computed abacus (Sim and Kim, 1990; International Organization for Standardization ISO, 2011).
For materials with higher Young’s moduli and lower porosity, the cantilever beam as described in ASTM E756 (ASTM International, 2005) and ISO 6721-3 (International Organization for Standardization ISO, 2021) (homogeneous, damped on one side, i.e., the Oberst’s beam, damped on both sides, i.e., the modified Oberst’s beam, or the sandwich beam) is a more suitable technique. Again, the estimation of the Young’s modulus (in the axis of the beam) and its associated loss factor can be a difficult task depending on the studied frequency range, the thickness of the porous material and thus the required hypotheses regarding the shear and the compression in the deflection direction for the porous material.
While tentatives were made to characterize the elastic parameters from impedance tube measurements, the results were not always reliable due to the lack of control over the boundary conditions. Even for thin materials, backed by an air-gap, where a clamped boundary condition can be guaranteed at the periphery with the tube, the difficulty is to identify the bending modes before estimating the elastic parameters. In addition, there is a difference in stresses between an impedance tube and common elastic characterization techniques. A sound pressure of 80 dB is a weak excitation causing a low stress for the specimen under test, a stress often smaller than the one required to be in the linear stress-strain zone when exciting only the skeleton of the material during, e.g., an uni-axial compression (the stress being only sufficient for a surface stimulation of the “hairs” of the sample).
Methods based on guided wave measurements (Allard et al., 2005; Boeckx et al., 2005b; Boeckx et al., 2005a; Glorieux et al., 2014) on specimens with dimensions of 1 square meter or more have also been studied. The size of the samples together with the numerical and experimental works needed to extract the elastic parameters were the main limitations of these methods, which have not seen any new developments for a decade.
5 General considerations
This section presents some general considerations that apply to both the acoustic and elastic characterizations.
• Uncertainties in measurements and characterizations are now regularly reported, improving the reliability of the results (see e.g., Horoshenkov et al. (2007), Pompoli et al. (2017), Gaborit et al. (2020).
• Anisotropy remains a slowly growing area of research (Melon et al., 1998; Göransson et al., 2009; Guastavino, 2008; Cuenca and Göransson, 2012; Van der Kelen and Göransson, 2013) despite its importance for some materials (in particular fibrous) and for some conditions like mechanical excitations (Tran-Van, 2004) (in French) (Parra Martinez et al., 2016). The primary challenge lies in the increased number of parameters required compared to isotropic materials (
• Statistical approaches (in particular Bayesian methods) and Machine Learning algorithms are more and more used to identify and correct errors in measurement data (Chazot et al., 2012; Roncen et al., 2018; Stender et al., 2021; Gaborit and Jaouen, 2023; Chevillotte, 2024). The commercial availability of material databases has significantly improved the efficiency and applicability of these algorithms, allowing for more accurate predictions in the characterizations of materials.
6 Conclusion
Both acoustic and elastic characterizations of porous media remain active fields of research with adaptations of methods to new challenges such as materials with multiple dynamics, more complex environment conditions with high temperature or flow…
While numerous methods are available, certain points still require attention.
• On the acoustic side, the low-frequency parameters
• On the elastic side, broadband frequency characterization remains the exception rather than the rule while polymers exhibit noticeable frequency-dependent behaviors.
• On both sides, the research on anisotropy is notably sparse while fibrous materials, that exhibit noticeable anisotropy (such as natural or recycled synthetic fibers) are becoming more common.
Standardization is evolving faster than ever to keep up with recent developments. Newly published standards try to be more critical and informative about the methods and try to remain open to the development of new methods to meet the challenges of new materials and applications.
Finally, it is important to keep in mind that no method can be considered perfect. A combination of complementary methods often provides the most robust and comprehensive results and the words of Tamas Pritz provide an insightful reminder of the importance of simplicity in methodological development: “Some works suggest that the curiosity of the methods is more important than the results... In my opinion, the simpler the method, the better to have reliable results.”
Author contributions
LJ: Writing – original draft. F-XB: Writing – review and editing. FC: Writing – review and editing.
Funding
The author(s) declare that no financial support was received for the research and/or publication of this article.
Conflict of interest
The authors declare that the research was conducted in the absence of any commercial or financial relationships that could be construed as a potential conflict of interest.
Generative AI statement
The author(s) declare that no Generative AI was used in the creation of this manuscript.
Publisher’s note
All claims expressed in this article are solely those of the authors and do not necessarily represent those of their affiliated organizations, or those of the publisher, the editors and the reviewers. Any product that may be evaluated in this article, or claim that may be made by its manufacturer, is not guaranteed or endorsed by the publisher.
References
Allard, J.-F., and Atalla, N. (2009). Propagation of sound in porous media: modelling sound absorbing materials. Chichester, West Sussex, United Kingdom: Wiley.
Allard, J.-F., Castagnede, B., Henry, M., and Lauriks, W. (1994). Evaluation of tortuosity in acoustic porous materials saturated by air. Rev. Sci. Instrum. 65, 754–755. doi:10.1063/1.1145097
Allard, J. F., Henry, M., Boeckx, L., Leclaire, P., and Lauriks, W. (2005). Acoustical measurement of the shear modulus for thin porous layers. J. Acoust. Soc. Am. 117, 1737–1743. doi:10.1121/1.1868392
ASTM International (2005). E756: standard test method for measuring vibration-damping properties of materials
ASTM International (2019). E2611: standard test method for normal incidence determination of porous material acoustical properties based on the transfer matrix method
Atalla, N., and Sgard, F. (2007). Modeling of perforated plates and screens using rigid frame porous models. J. Sound. Vib. 303, 195–208. doi:10.1016/j.jsv.2007.01.012
Aurégan, Y., and Pachebat, M. (1999). Measurement of the nonlinear behavior of acoustical rigid porous materials. Phys. fluids 11, 1342–1345. doi:10.1063/1.869999
Auriault, J.-L., Boutin, C., and Geindreau, C. (2010). Homogenization of coupled phenomena in heterogenous media, 149. John Wiley and Sons. doi:10.1002/9780470612033
Bechwati, F., Avis, M., Bull, D. J., Cox, T. J., Hargreaves, J. A., Moser, D., et al. (2012). Low frequency sound propagation in activated carbon. J. Acoust. Soc. Am. 132, 239–248. doi:10.1121/1.4725761
Bécot, F.-X., and Sgard, F. (2006). On the use of poroelastic materials for the control of the sound radiated by a cavity backed plate. J. Acoust. Soc. Am. 120, 2055–2066. doi:10.1121/1.2214134
Bensoussan, A., Lions, J.-L., and Papanicolaou, G. (1978). Asymptotic analysis for periodic structures, 374. American Mathematical Soc.).
Beranek, L. L. (1942). Acoustic impedance of porous materials. J. Acoust. Soc. Am. 13, 248–260. doi:10.1121/1.1916172
Berthelot, J.-M. (1999). Composite materials: mechanical behavior and structural analysis. New York: Springer. doi:10.1007/978-1-4612-0527-2
Biot, M. A. (1956a). Theory of propagation of elastic waves in a fluid-saturated porous solid. i. low-frequency range. J. Acoust. Soc. Am. 28, 168–178. doi:10.1121/1.1908239
Biot, M. A. (1956b). Theory of propagation of elastic waves in a fluid-saturated porous solid. ii. higher frequency range. J. Acoust. Soc. Am. 28, 179–191. doi:10.1121/1.1908241
Biot, M. A. (1962). Mechanics of deformation and acoustic propagation in porous media. J. Appl. Phy. 33, 1482–1498. doi:10.1063/1.1728759
Boeckx, L., Leclaire, P., Khurana, P., Glorieux, C., Lauriks, W., and Allard, J.-F. (2005a). Guided elastic waves in porous materials saturated by air under lamb conditions. J. Appl. Phys. 97. doi:10.1063/1.1886885
Boeckx, L., Leclaire, P., Khurana, P., Glorieux, C., Lauriks, W., and Allard, J.-F. (2005b). Investigation of the phase velocities of guided acoustic waves in soft porous layers. J. Acoust. Soc. Am. 117, 545–554. doi:10.1121/1.1847848
Bonfiglio, P., and Pompoli, F. (2015). Determination of the dynamic complex modulus of viscoelastic materials using a time domain approach. Polym. Test. 48, 89–96. doi:10.1016/j.polymertesting.2015.09.016
Bonfiglio, P., Pompoli, F., Horoshenkov, K. V., Rahim, M. I. B. S. A., Jaouen, L., Rodenas, J., et al. (2018). How reproducible are methods to measure the dynamic viscoelastic properties of poroelastic media? J. Sound Vib. 428, 26–43. doi:10.1016/j.jsv.2018.05.006
Brown, R. J. S. (1980). Connection between formation factor for electrical resistivity and fluid-solid coupling factor in biot’s equations for acoustic waves in fluid-filled porous media. Geophysics 45, 1269–1275. doi:10.1190/1.1441123
Castillo, R. G. V. (2011). Microstructure influence on acoustical properties of multi-scale porous materials. (PhD thesis). University of Salford, Salford, United Kingdom.
Chabriac, P.-A., Gourdon, E., Gle, P., Fabbri, A., and Lenormand, H. (2016). Agricultural by-products for building insulation: acoustical characterization and modeling to predict micro-structural parameters. Constr. Build. Mater. 112, 158–167. doi:10.1016/j.conbuildmat.2016.02.162
Champoux, Y., and Allard, J.-F. (1991). Dynamic tortuosity and bulk modulus in air-saturated porous media. J. Appl. Phys. 70, 1975–1979. doi:10.1063/1.349482
Champoux, Y., Stinson, M. R., and Daigle, G. A. (1991). Air-based system for the measurement of porosity. J. Acoust. Soc. Am. 89, 910–916. doi:10.1121/1.1894653
Chazot, J.-D., Zhang, E., and Antoni, J. (2012). Acoustical and mechanical characterization of poroelastic materials using a Bayesian approach. J. Acoust. Soc. Am. 131, 4584–4595. doi:10.1121/1.3699236
Chevillotte, F. (2024). Porous material characterization with bayesian and machine learning method. INTER-NOISE NOISE-CON Congr. Conf. Proc. Inst. Noise Control Eng. 270, 9590–9597. doi:10.3397/in_2024_4269
Chevillotte, F., Marchner, P., Martinez, M., Roncen, R., and Simon, F. (2017). “Analysis of the non-linear behavior of micro-perforated plates using lattice Boltzmann method,” in Proc. Of symposium on the acoustics of poro-elastic materials (SAPEM) 2017.
Chevillotte, F., Perrot, C., and Guillon, E. (2013). A direct link between microstructure and acoustical macro-behavior of real double porosity foams. J. Acoust. Soc. Am. 134, 4681–4690. doi:10.1121/1.4824842
Chevillotte, F., Ronzio, F., Bertolini, C., Hoang, M. T., Dejaeger, L., Duval, A., et al. (2020). Inter-laboratory characterization of biot parameters of poro-elastic materials for automotive applications. Tech. Rep. doi:10.4271/2020-01-1523
Corsaro, R. D., and Sperling, L. H. e. (1990). Sound and vibration damping with polymers. Washington, DC: American Chemical Society. doi:10.1021/bk-1990-0424
Cuenca, J., and Göransson, P. (2012). Inverse estimation of the elastic and anelastic properties of the porous frame of anisotropic open-cell foams. J. Acoust. Soc. Am. 132, 621–629. doi:10.1121/1.4731222
Cummings, A. (1991). Impedance tube measurements on porous media: the effects of air-gaps around the sample. J. Sound. Vib. 151, 63–75. doi:10.1016/0022-460X(91)90652-Z
Danilov, O., Sgard, F., and Olny, X. (2004). On the limits of an “in vacuum” model to determine the mechanical parameters of isotropic poroelastic materials. J. Sound. Vib. 276 (3-5), 729–754. doi:10.1016/j.jsv.2003.08.036
Debray, A. (2000). Contribution to the study of dissipative silencers: effect of structural vibrations, effect of flow. Ph.D. thesis, Université du Maine, Le Mans. France.
Delany, M. E., and Bazley, E. N. (1970). Acoustical properties of fibrous absorbent materials. Appl. Acoust. 3, 105–116. doi:10.1016/0003-682X(70)90031-9
Di Giulio, E., Perrot, C., and Dragonetti, R. (2024). Experimental characterization of thermal and viscous powers in porous media under oscillating flow. Therm. Sci. Eng. Prog. 103057doi, 103057. doi:10.1016/j.tsep.2024.103057
Dinzart, F., and Lipiński, P. (2010). Self-consistent approach of the constitutive law of a two-phase visco-elastic material described by fractional derivative models. Archives Mech. 62, 135–156.
Doutres, O., Salissou, Y., Atalla, N., and Panneton, R. (2010). Evaluation of the acoustic and non-acoustic properties of sound absorbing materials using a three-microphone impedance tube. Appl. Acoust. 71, 506–509. doi:10.1016/j.apacoust.2010.01.007
Fellah, Z. E. A., Berger, S., Lauriks, W., Depollier, C., Aristegui, C., and Chapelon, J.-Y. (2003). Measuring the porosity and the tortuosity of porous materials via reflected waves at oblique incidence. J. Acoust. Soc. Am. 113, 2424–2433. doi:10.1121/1.1567275
Fellah, Z. E. A., Fellah, M., Ongwen, N. O., Ogam, E., and Depollier, C. (2021). Acoustics of fractal porous material and fractional calculus. Mathematics 9, 1774. doi:10.3390/math9151774
Fellah, Z. E. A., Fellah, M., Sebaa, N., Lauriks, W., and Depollier, C. (2006). Measuring flow resistivity of porous materials at low frequencies range via acoustic transmitted waves. J. Acoust. Soc. Am. 119, 1926–1928. doi:10.1121/1.2179749
Gaborit, M., Dazel, O., Göransson, P., and Jaouen, L. (2020). Generation of uncertainty envelopes for thin acoustic screens with uncertain parameters. Acta Acust. 4, 8. doi:10.1051/aacus/2020007
Gaborit, M., and Jaouen, L. (2023). Using data-driven techniques to provide feedback during material characterisation. INTER-NOISE NOISE-CON Congr. Conf. Proc. Inst. Noise Control Eng. 265, 2305–2309. doi:10.3397/in_2022_0330
Gibson, L. J., and Ashby, M. F. (1997). Cellular solids: structure and properties. Cambridge University Press. doi:10.1017/CBO9781139878326
Glorieux, C., Descheemaeker, J., Vandenbroeck, J., Groby, J.-P., Boeckx, L., Khurana, P., et al. (2014). Temperature and frequency dependence of the visco-elasticity of a poro-elastic layer. Appl. Acoust. 83, 123–126. doi:10.1016/j.apacoust.2014.03.010
Göransson, P., Guastavino, R., and Hörlin, N.-E. (2009). Measurement and inverse estimation of 3d anisotropic flow resistivity for porous materials. J. Sound. Vib. 327, 354–367. doi:10.1016/j.jsv.2009.06.028
Gourdon, E., Sauzeat, C., Di Benedetto, H., and Bilodeau, K. (2015). Seven-parameter linear viscoelastic model applied to acoustical damping materials. J. Vib. Acoust. 137, 061003. doi:10.1115/1.4030719
Gourlay, E., Glé, P., Marceau, S., Foy, C., and Moscardelli, S. (2017). Effect of water content on the acoustical and thermal properties of hemp concretes. Constr. Build. Mater. 139, 513–523. doi:10.1016/j.conbuildmat.2016.11.018
Groby, J.-P., Mallejac, M., Merkel, A., Romero-García, V., Tournat, V., Torrent, D., et al. (2021). Analytical modeling of one-dimensional resonant asymmetric and reciprocal acoustic structures as willis materials. New J. Phys. 23, 053020. doi:10.1088/1367-2630/abfab0
Groby, J.-P., Ogam, E., De Ryck, L., Sebaa, N., and Lauriks, W. (2010). Analytical method for the ultrasonic characterization of homogeneous rigid porous materials from transmitted and reflected coefficients. J. Acoust. Soc. Am. 127, 764–772. doi:10.1121/1.3283043
Guastavino, R. (2008). Elastic and acoustic characterisation of anisotropic porous materials. Sweden: KTH Royal Institute of Technology. Ph.D. thesis.
Gusev, V., and Aleshin, V. (2002). Strain wave evolution equation for nonlinear propagation in materials with mesoscopic mechanical elements. J. Acoust. Soc. Am. 112, 2666–2679. doi:10.1121/1.1517252
Guyer, R., McCall, K., Boitnott, G., Hilbert Jr, L., and Plona, T. (1997). Quantitative implementation of preisach-mayergoyz space to find static and dynamic elastic moduli in rock. J. Geophys. Res. Solid Earth 102, 5281–5293. doi:10.1029/96JB03740
Hilyard, N. C., and Cunningham, A. e. (1994). “Physical behaviour of polymeric foams – an overview,” in Low density cellular plastics: physical basis of behaviour. doi:10.1007/978-94-011-1256-7
Horoshenkov, K. V., Groby, J.-P., and Dazel, O. (2016). Asymptotic limits of some models for sound propagation in porous media and the assignment of the pore characteristic lengths. J. Acoust. Soc. Am. 139, 2463–2474. doi:10.1121/1.4947540
Horoshenkov, K. V., Hurrell, A., and Groby, J.-P. (2019). A three-parameter analytical model for the acoustical properties of porous media. J. Acoust. Soc. Am. 145, 2512–2517. doi:10.1121/1.5098778
Horoshenkov, K. V., Khan, A., Bécot, F.-X., Jaouen, L., Sgard, F., Renault, A., et al. (2007). Reproducibility experiments on measuring acoustical properties of rigid-frame porous media (round-robin tests). J. Acoust. Soc. Am. 122, 345–353. doi:10.1121/1.2739806
International Organization for Standardization (ISO) (1989). 9052-1, Acoustics – determination of dynamic stiffness – Part 1: materials used under floating floors in dwellings Currently in revision
International Organization for Standardization (ISO) (2011). 18437-5, Mechanical vibration and shock – characterization of the dynamic mechanical properties of visco-elastic materials – Part 5: Poisson ratio based on comparison between measurements and finite element analysis
International Organization for Standardization (ISO) (2018). 9053-1, Acoustics – materials for acoustical applications – determination of airflow resistance – Part 1: static airflow method
International Organization for Standardization (ISO) (2021). 6721-3, Plastics – determination of dynamic mechanical properties – Part 3: flexural vibration – resonance-curve method
International Organization for Standardization (ISO) (2023). 10534-2, acoustics – determination of acoustic properties in impedance tubes –Part 2: transfer-function method for normal sound absorption coefficient and normal surface impedance
International Organization for Standardization (ISO) (proposition submitted) (2025). 10534-3, acoustics – determination of acoustic properties in impedance tubes –Part 3: 3-microphone technique for bulk properties
International Organization for Standardization (ISO) (proposition to be submitted) (2024). 10534-4, acoustics – determination of acoustic properties in impedance tubes –Part 4: 4-microphone technique for bulk properties and transmission performances
Iwase, T., and Izumi, Y. (1996). A new sound tube measuring method for propagation constant in porous material-method without any air space at the back of test material (in Japanese). J. Acoust. Soc. Jpn. 52, 411–419.
Iwase, T., Izumi, Y., and Kawabata, R. (1998). “A new measuring method for sound propagation constant by using sound tube without any air spaces back of a test material,” in Proceedings of inter.noise, 98. Christchurch, New Zealand.
Jaouen, L. (2025a). Biot’s theory of poroelasticity. Acoust. Porous Mater. Available online at: https://apmr.matelys.com.
Jaouen, L. (2025b). Propagation models assuming a motionless skeleton. Acoust. Porous Mater. Available online at: https://apmr.matelys.com.
Jaouen, L., and Bécot, F.-X. (2011). Acoustical characterization of perforated facings. J. Acoust. Soc. Am. 129, 1400–1406. doi:10.1121/1.3552887
Jaouen, L., and Chevillotte, F. (2018). Length correction of 2d discontinuities or perforations at large wavelengths and for linear acoustics. Acta Acustica united Acustica 104, 243–250. doi:10.3813/AAA.919166
Jaouen, L., Gourdon, E., and Glé, P. (2020). Estimation of all six parameters of johnson-champoux-allard-lafarge model for acoustical porous materials from impedance tube measurements. J. Acoust. Soc. Am. 148, 1998–2005. doi:10.1121/10.0002162
Jaouen, L., and Olny, X. (2005). “Indirect acoustical characterization of a foam with two scales of porosity,” in Proc. Of symposium on the acoustics of poro-elastic materials (SAPEM) 2005.
Jaouen, L., Renault, A., and Deverge, M. (2008). Elastic and damping characterizations of acoustical porous materials: available experimental methods and applications to a melamine foam. Appl. Acoust. 69, 1129–1140. doi:10.1016/j.apacoust.2007.11.008
Johnson, D. L., Koplik, J., and Dashen, R. (1987). Theory of dynamic permeability and tortuosity in fluid-saturated porous media. J. Fluid Mech. 176, 379–402. doi:10.1017/s0022112087000727
Johnson, D. L., Plona, T. J., Scala, C., Pasierb, F., and Kojima, H. (1982). Tortuosity and acoustic slow waves. Phys. Rev. Lett. 49, 1840–1844. doi:10.1103/PhysRevLett.49.1840
Kraak, W. (1959). Der einfluss des strömungsstandwertes bei der bestimmung der dynamischen steifigkeit poröser dämm-materialien. Hochfrequenztech. Elektroakust. 67, 111–113.
Lafarge, D., Lemarinier, P., Allard, J.-F., and Tarnow, V. (1997). Dynamic compressibility of air in porous structures at audible frequencies. J. Acoust. Soc. Am. 102, 1995–2006. doi:10.1121/1.419690
Lafarge, D., and Nemati, N. (2013). Nonlocal maxwellian theory of sound propagation in fluid-saturated rigid-framed porous media. Wave Motion 50, 1016–1035. doi:10.1016/j.wavemoti.2013.04.007
Langlois, C., Panneton, R., and Atalla, N. (2001). Polynomial relations for quasi-static mechanical characterization of isotropic poroelastic materials. J. Acoust. Soc. Am. 110, 3032–3040. doi:10.1121/1.1419091
Leclaire, P., Kelders, L., Lauriks, W., Glorieux, C., and Thoen, J. (1996a). Determination of the viscous characteristic length in air-filled porous materials by ultrasonic attenuation measurements. J. Acoust. Soc. Am. 99, 1944–1948. doi:10.1121/1.415378
Leclaire, P., Kelders, L., Lauriks, W., Melon, M., Brown, N., and Castagnede, B. (1996b). Determination of the viscous and thermal characteristic lengths of plastic foams by ultrasonic measurements in helium and air. J. Appl. Phys. 80, 2009–2012. doi:10.1063/1.363817
Leclaire, P., Umnova, O., Horoshenkov, K., and Maillet, L. (2003). Porosity measurement by comparison of air volumes. Rev. Sci. Instrum. 74, 1366–1370. doi:10.1063/1.1542666
Maa, D.-Y. (1975). Theory and design of microperforated panel sound-absorbing constructions. Sci. Sin. XVIII, 55–71.
Maa, D.-Y. (1998). Potential of microperforated panel absorber. J. Acoust. Soc. Am. 104, 2861–2866. doi:10.1121/1.423870
Melon, M., Mariez, E., Ayrault, C., and Sahraoui, S. (1998). Acoustical and mechanical characterization of anisotropic open-cell foams. J. Acoust. Soc. Am. 104, 2622–2627. doi:10.1121/1.423897
Miki, Y. (1990). Acoustical properties of porous materials - modifications of delany-bazley models. J. Acoust. Soc. Jpn. 11, 19–24. doi:10.1250/ast.11.19
Olny, X., and Boutin, C. (2003). Acoustic wave propagation in double porosity media. J. Acoust. Soc. Am. 114, 73–89. doi:10.1121/1.1534607
Olny, X., and Panneton, R. (2008). Acoustical determination of the parameters governing thermal dissipation in porous media. J. Acoust. Soc. Am. 123, 814–824. doi:10.1121/1.2828066
Panneton, R. (2007). Comments on the limp frame equivalent fluid model for porous media. J. Acoust. Soc. Am. 122, EL217–EL222. doi:10.1121/1.2800895
Panneton, R., and Gros, E. (2005). A missing mass method to measure the open porosity of porous solids. Acustica Acustica united Acustica 91, 342–348.
Panneton, R., and Olny, X. (2006). Acoustical determination of the parameters governing viscous dissipation in porous media. J. Acoust. Soc. Am. 119, 2027–2040. doi:10.1121/1.2169923
Parra Martinez, J. P., Dazel, O., Göransson, P., and Cuenca, J. (2016). Acoustic analysis of anisotropic poroelastic multilayered systems. J. Appl. Phys. 119. doi:10.1063/1.4942443
Perrot, C., Chevillotte, F., and Panneton, R. (2008). Bottom-up approach for microstructure optimization of sound absorbing materials. J. Acoust. Soc. Am. 124, 940–948. doi:10.1121/1.2945115
Perrot, C., Chevillotte, F., Tan Hoang, M., Bonnet, G., Bécot, F.-X., Gautron, L., et al. (2012). Microstructure, transport, and acoustic properties of open-cell foam samples: experiments and three-dimensional numerical simulations. J. Appl. Phys. 111. doi:10.1063/1.3673523
Pilon, D., Panneton, R., and Sgard, F. (2004). Behavioral criterion quantifying the effects of circumferential air gaps on porous materials in the standing wave tube. J. Acoust. Soc. Am. 116, 344–356. doi:10.1121/1.1756611
Pompoli, F., Bonfiglio, P., Horoshenkov, K. V., Khan, A., Jaouen, L., Bécot, F.-X., et al. (2017). How reproducible is the acoustical characterization of porous media? J. Acoust. Soc. Am. 141, 945–955. doi:10.1121/1.4976087
Pride, S., Morgan, F., and Gangi, A. (1993). Drag forces of porous-medium acoustics. Phys. Rev. B 47, 4964–4978. doi:10.1103/PhysRevB.47.4964
Roncen, R., Fellah, Z. E., Lafarge, D., Piot, E., Simon, F., Ogam, E., et al. (2018). Acoustical modeling and bayesian inference for rigid porous media in the low-mid frequency regime. J. Acoust. Soc. Am. 144, 3084–3101. doi:10.1121/1.5080561
Roncen, R., Fellah, Z. E. A., Piot, E., Simon, F., Ogam, E., Fellah, M., et al. (2019). Inverse identification of a higher order viscous parameter of rigid porous media in the high frequency domain. J. Acoust. Soc. Am. 145, 1629–1639. doi:10.1121/1.5095403
Sadouki, M., Fellah, Z., Berbiche, A., Fellah, M., Mitri, F., Ogam, E., et al. (2014). Measuring static viscous permeability of porous absorbing materials. J. Acoust. Soc. Am. 135, 3163–3171. doi:10.1121/1.4874600
Salissou, Y., and Panneton, R. (2007). Pressure/mass method to measure open porosity of porous solids. J. Appl. Phys. 101, 124913. doi:10.1063/1.2749486
Salissou, Y., and Panneton, R. (2010). Wideband characterization of the complex wave number and characteristic impedance of sound absorbers. J. Acoust. Soc. Am. 128, 2868–2876. doi:10.1121/1.3488307
Schmelzer, M., Wittstock, V., Bietz, H., and Brezas, S. (2021). On the influence of the air flow resistivity on the measurement of the dynamic stiffness of underlays for floating floors. Acta Acust. 5, 13. doi:10.1051/aacus/2021004
Sebaa, N., Fellah, Z., Fellah, M., Lauriks, W., and Depollier, C. (2005). Measuring flow resistivity of porous material via acoustic reflected waves. J. Appl. Phys. 98. doi:10.1063/1.2099510
Shen, Y., and Jiang, G. (2014). Sound absorption properties of composite structure with activated carbon fiber felts. J. Text. Inst. 105, 1100–1107. doi:10.1080/00405000.2014.899080
Sim, S., and Kim, K.-J. (1990). A method to determine the complex modulus and Poisson’s ratio of viscoelastic materials for fem applications. J. Sound Vib. 141, 71–82. doi:10.1016/0022-460X(90)90513-Y
Smith, C. D., and Parrott, T. L. (1983). Comparison of three methods for measuring acoustic properties of bulk materials. J. Acoust. Soc. Am. 74, 1577–1582. doi:10.1121/1.390119
Stender, M., Adams, C., Wedler, M., Grebel, A., and Hoffmann, N. (2021). Explainable machine learning determines effects on the sound absorption coefficient measured in the impedance tube. J. Acoust. Soc. Am. 149, 1932–1945. doi:10.1121/10.0003755
Tarnow, V. (2005). Dynamic measurements of the elastic constants of glass wool. J. Acoust. Soc. Am. 118, 3672–3678. doi:10.1121/1.2118267
Temiz, M. A., Tournadre, J., Lopez Arteaga, I., and Hirschberg, A. (2016). Non-linear acoustic transfer impedance of micro-perforated plates with circular orifices. J. Sound. Vib. 366, 418–428. doi:10.1016/j.jsv.2015.12.022
Tournat, V., Lafarge, D., Pagneux, V., and Jaouen, L. (2004). Multiple scattering in porous media. Phys. Rev. E 70, 26609. doi:10.1103/PhysRevE.70.026609
Tran-Van, J. (2004). Etude de l’influence de l’isotropie transverse des laines minérales sur la transmission acoustique des parois multicouches. France: Université de Poitiers. Ph.D. thesis.
Utsuno, H., Tanaka, T., Fujikawa, T., and Seybert, A. (1989). Transfer function method for measuring characteristic impedance and propagation constant of porous materials. J. Acoust. Soc. Am. 86, 637–643. doi:10.1121/1.398241
Van der Kelen, C., and Göransson, P. (2013). Identification of the full anisotropic flow resistivity tensor for multiple glass wool and melamine foam samples. J. Acoust. Soc. Am. 134, 4659–4669. doi:10.1121/1.4824841
Venegas, R., and Umnova, O. (2016). Influence of sorption on sound propagation in granular activated carbon. J. Acoust. Soc. Am. 140, 755–766. doi:10.1121/1.4959006
Verdière, K., Panneton, R., Elkoun, S., Dupont, T., and Leclaire, P. (2013). Transfer matrix method applied to the parallel assembly of sound absorbing materials. J. Acoust. Soc. Am. 134, 4648–4658. doi:10.1121/1.4824839
Willis, J. R. (1981). Variational principles for dynamic problems for inhomogeneous elastic media. Wave Motion 3, 1–11. doi:10.1016/0165-2125(81)90008-1
Keywords: characterization, porous media, acoustic, visco-elastic, parameters
Citation: Jaouen L, Bécot F-X and Chevillotte F (2025) Characterizations of acoustical porous media: standardized methods, current trends and challenges. Front. Acoust. 3:1543456. doi: 10.3389/facou.2025.1543456
Received: 11 December 2024; Accepted: 16 April 2025;
Published: 08 May 2025.
Edited by:
Minghui Lu, Nanjing University, ChinaReviewed by:
Erick Ogam, UPR7051 Laboratoire de mécanique et d’acoustique (LMA), FranceFrank Simon, Office National d’Études et de Recherches Aérospatiale, France
Copyright © 2025 Jaouen, Bécot and Chevillotte. This is an open-access article distributed under the terms of the Creative Commons Attribution License (CC BY). The use, distribution or reproduction in other forums is permitted, provided the original author(s) and the copyright owner(s) are credited and that the original publication in this journal is cited, in accordance with accepted academic practice. No use, distribution or reproduction is permitted which does not comply with these terms.
*Correspondence: Luc Jaouen, bHVjLmphb3VlbkBtYXRlbHlzLmNvbQ==
†ORCID: Fabien Chevillotte, orcid.org/0000-0003-2290-6105