- School of Materials Science and Engineering, Zhejiang University, Hangzhou, China
Due to their superior strength and oxidation resistance at high temperatures, precipitation-strengthened Ni-based superalloys are widely used in load-bearing hot components in energy generation systems, such as gas/steam engines in aircraft or power plants. However, brittleness originating from a grain boundary (GB) in a certain temperature range is one of the greatest deadlocks, which desperately restricts their thermal-mechanical processing capabilities and also industrial applications. Experimental and theoretical investigations of the origin of GB brittleness with aims to overcome it still attract many research efforts in the high-temperature material field. It is desirable to understand the GB embrittlement mechanism by dynamically investigating the entire GB cracking process in real time under stress/temperature combination, which might be hardly revealed by a traditional experiment on precipitation strength/theoretical technologies. Current advances in high-temperature mechanical testing systems, which can be operated in a transmission electron microscope (TEM), provide unique opportunities for in situ exploration of the mechanistic origins of GB brittleness of superalloys with the resolution up to an atomic scale. Here, we first briefly give an overview of the phenomenon and current understanding on GB brittleness, followed by introducing the state-of-art techniques in an in situ TEM/mechanical testing system (MTS). In the end, we will also discuss the potential application of the in situ TEM/MTS on GB brittleness and a perspective overlook.
Introduction
Containing high concentrations of as many as 10 alloying elements, precipitation-strengthened Ni-based superalloys have emerged as the materials for high-temperature operation when resistance to creep, fatigue, and environmental degradation is required, such as gas/steam engines in aircraft or power plants (Reed and Rae, 2014; Pollock, 2016; Duan et al., 2019). Although their composition is very complicated, precipitation-strengthened Ni-based superalloys have a relatively simple microstructure, especially consisting of two coherent phases. The matrix is a solid solution (γ phase) with the face-centered cubic (FCC) crystal structure, and the precipitate is an intermetallic compound Ni3Al with an ordered L12 crystal structure (γ′ phase). The unique comprehensive properties, such as mechanical properties and resistance to oxidation of the Ni3Al compound, make it extremely appropriate for high-temperature use. With Ni3Al precipitations strengthening the materials, the strength at elevated/service temperature has been significantly improved to meet the high-temperature capability of industry applications. However, brittleness originating from GB in a certain temperature range is one of the greatest deadlocks, which desperately restricts their thermal-mechanical processing capability and also industrial applications (McLean and Maradudin, 1958; Watanabe, 2001; Chu et al., 2010).
Limited ductility and lack of plastic deformation ability in precipitation-strengthened Ni-based superalloys are generally accompanied by the observation of intergranular cracks. Microstructure examination reveals that materials fracture along GBs at a very early stage of deformation, sometimes in the elastic stage during tensile testing (Watanabe, 2001). This phenomenon often refers to GB brittleness, which greatly increases the difficulty for thermomechanical forming, plastic processing, and also industrial applications of the alloys. In an extreme case for turbine blade application in aeroengine industries, huge amounts of investments and resources are poured in to develop directional solidification and single crystal growth to modify the GB structure or even completely eliminate the GB (Hirano, 1990). With the “weakest site”-GBs completely removed in single-crystal (SX) Ni-based superalloys, mechanical properties and temperature capability of modern SX blades have been greatly increased (Pollock, 2016). The innovation and development of modern SX Ni-based superalloy turbine blades are actually a history of the battle over the boundary between weakness and brittleness.
Although GB structures can be modified or even removed by directional solidification/single-crystal growth for one of the most critical applications in turbine blades, in most cases, the application of precipitation-strengthened Ni-based superalloys still utilizes their polycrystalline forms if the cost, size/complication of the part, the flexibility of fabrication processing, and equipment/technological limitations are considered. GBs are not avoidable in almost all other Ni-based superalloys. GB brittleness still remains an active research topic with the aims of mechanistically understanding its origin and further strengthening the GB through GB engineering, such as B effects on the brittleness of intermetallic Ni3Al (Liu et al., 1985; Hanna et al., 2002). Here, we first briefly describe the phenomenon of GB brittleness using a disk alloy GH4151 as an example and then provide a mini review on the understanding of GB brittleness, followed by introducing the state-of-art techniques in the in situ TEM/mechanical testing system (MTS). Later, we will discuss the perspective overlook of the future application of in situ TEM/MTS on GB brittleness of Ni-based precipitation-strengthened superalloys.
The phenomenon of grain boundary brittleness
GB brittleness commonly exists in polycrystalline Ni-based precipitation-strengthened superalloys (Pang et al., 1994; Viskari et al., 2013; Németh et al., 2017). Take the Ni-based disk alloy GH4151 as an example, which is a counterpart of the Russian alloy эκ151 (Chabina et al., 2015). The microstructure of this alloy is a typical γ′/γ two-phase structure, as shown in the inset of Figure 1A. The strengthening phase (Ni3Al, γ′) with a darker contrast is uniformly distributed in the γ matrix. During tensile tests at 923 K, polycrystalline GH4151 alloy fractures at the elastic deformation stage, and the alloy exhibits nearly zero plastic strain under tensile testing (Figure 1A). The fracture surface is extremely smooth, and the grains are almost peeled off one by one, indicating an entire intergranular fracture. In comparison, the single crystal GH4151, which is GB-free, exhibits considerable plastic deformation after yielding. Continuous work hardening is observed with a final fracture strain of about 14% (Figure 1A). Large amounts of dimples are observed on the fracture surface, indicating ductile fracture of the single crystal GH4151. Clearly, limited ductility and lack of plastic deformation before fracture of the GH4151 polycrystalline Ni-based precipitation-strengthened superalloys are indeed due to GB brittleness. Similar to the GH4151 alloy, other precipitation-strengthened Ni-based superalloys, such as Inconel 718 (Pfaendtner and McMahon, 2001), 718 plus (Viskari et al., 2013), and Udimet 720Li (Németh et al., 2017) alloys, also exhibit GB brittleness during various mechanical testing procedures. At 1023 K, the Udimet 720Li alloy fractures at a plastic strain of only 3%, and the fracture surface is also entirely intergranular (Németh et al., 2017). In addition, the Inconel 718 plus alloy exhibits GB brittleness under a fatigue experiment using a 10-Hz triangular waveform and a load ratio R = Pmin/Pmax = 0.05 at 1023 K (Viskari et al., 2013), and brittle intergranular cracking is observed for the Inconel 718 alloy at temperatures between 823 and 923 K in a single-notched four-point bending test (Pfaendtner and McMahon, 2001).
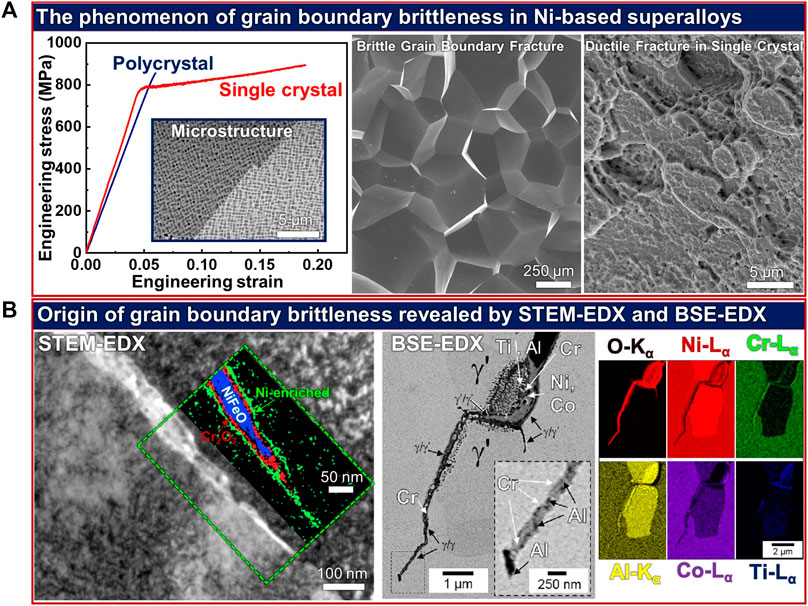
FIGURE 1. GB brittleness of precipitation-strengthened Ni-based superalloys and their origin. (A) Engineering tensile stress–strain curves of polycrystalline and single-crystal GH4151 alloys at 923 K and their corresponding fracture surfaces. Polycrystalline GH4151 fractures along GBs at the elastic deformation stage. In comparison, the single crystal GH4151 fractures with a plastic strain higher than 14%, and dimples indicate the ductile fracture mode. (B) Origin of GB brittleness is attributed to intergranular oxides. The STEM-EDX result shows that the crack tip of the 718Plus alloy tensile fractured at 923 K is filled with oxide, which consists of NiFeO (blue) wrapped in chromium oxide (red), and the outermost structure is a Ni-enriched region (green) (Viskari et al., 2013). BSE-EDX measurements of intergranular oxidation show the formation of Ni-, Co-, Cr-, Ti-, and Al-rich oxidation products at and ahead of the crack tip in U720Li after slow strain rate testing at 1123 K (Németh et al., 2017).
A brief overview on the grain boundary brittleness of Ni-based superalloys
GB brittleness appears to be a common phenomenon for precipitation-strengthened Ni-based superalloys. Many researchers exert great efforts to find the origin of GB brittleness by using various methods. Currently, it is believed that GB segregation is the most important factor, such as the brittleness of GBs induced by carbides or enrichment with oxygen or other trace elements (Pang et al., 1994; Gao et al., 1995; Fournier et al., 2001). For example, blocky primary niobium carbide precipitations are observed at the GBs of the Inconel 718 alloy, and these niobium carbide precipitations act as crack initiation sites because of the oxidation and swelling of primary niobium carbides in air under the stress/temperature combination (Fournier et al., 2001). The enrichment and segregation of niobium at GBs play an important role in creep crack growth in the Inconel 718 alloy, especially when oxygen exists in the testing environment (Pang et al., 1994; Gao et al., 1995). Under mechanical loading, the stress assists the formation of brittle niobium oxides, which act as a cracking path (Fournier et al., 2001).
Figure 1B reveals the formation of oxides at and/or ahead of cracked GB in the Inconel 718 plus alloy (Viskari et al., 2013) and the Udimet 720Li alloy (Németh et al., 2017). A scanning transmission electron microscope with energy-dispersive spectroscopy (STEM-EDX) techniques shows that oxidation takes place at or immediately ahead of an open crack tip along the GB of the Inconel 718 plus alloy, forming a closed but layered oxide structure. Near GB, the oxide is Ni-rich, an intermediate layer essentially composed of Cr2O3, and a Fe-enriched layer is found far away from the metal. It is clear that the formation of oxides is in the direction of crack growth (Figure 1B) (Viskari et al., 2013). A backscattered electron image in combination with energy-dispersive spectroscopy (BSE-EDX) analysis reveals that the oxides formed at an intergranular crack tip of the Udimet 720Li alloy consist of Ni, Co, Ti, Cr, and Al (Figure 1B) (Németh et al., 2017). Except for the oxides formed at GBs, the segregations of other trace impurities, such as sulfur, phosphorus, and hydrogen in GBs, also have detrimental effects on the brittleness of Ni-based superalloys (Dong et al., 2002; Martin et al., 2012). Segregation of impurities might reduce GB cohesion; As a result, the GB becomes the “weakest site” which causes alloy failure immaturely and loss of ductility. Theoretical studies propose that the embrittling potency of impurities can be assessed by the Rice–Wang model (Rice and Wang, 1989) using segregation energies calculated from the ab initio or semi-empirical model [molecular dynamics (MD) or Monte Carlo (MC)]. Although modeling and theoretical studies show some success in the prediction that H, S, and P act as an embrittler (Yamaguchi et al., 2005), the values of the segregation energy of a solute at GBs show large uncertainty and sometimes differ by more than one order of magnitude (Lejček et al., 2017).
For γ′-precipitation-strengthened Ni-based superalloys, the carbide that exists at GBs is often one of the origins of the crack. For the GB free of carbides, the impurity segregation at GBs or oxide formation after deformation is usually observed accompanied by the intergranular fracture. However, this is a dynamic process that ideally needs observation of the entire GB cracking development in real-time in order to understand the GB embrittlement mechanism. Under the coupling conditions of high temperature and stress, the composition distribution, defects, phase composition, and distribution of GBs are all in the change. Although some information can be obtained by traditional experimental analysis, the real-time and dynamic process of these changes cannot be obtained. In particular, for a traditional ex situ experiment, cooling the sample from high temperature to room temperature is often needed. This might make many traditional experimental analyses difficult in capturing the “real” evidence of the GB fracture process at high temperatures and stresses. It is highly desirable to understand the GB embrittlement mechanism by dynamically investigating the entire GB cracking process in real time under the stress/temperature combination using high-temperature in situ experimental techniques.
High-temperature mechanical in situ experimental techniques
In situ high-temperature mechanical testing systems (MTSs), which can be operated in a transmission electron microscope (TEM), have been rapidly developed. In situ TEM/MTS technology offers a variety of experimental platforms for exploring the microstructure-performance evolution to reveal underlying deformation mechanisms of materials under simulated service conditions. Generally, the in situ TEM/MTS includes several integrated MEMS chips with a unique biaxial tilting system that enables real-time observation of the microstructural evolution at a resolution up to the atomic scale under the combination of force and heat. Figure 2A schematically shows the atomic-resolved high-temperature MTS developed by Bestron Science and Technology (Bestron, 2019; Zhang et al., 2021). The integrated system offers high-drive force and a long displacement range with angstrom step accuracy. The precise and controllable heating stage enables the sample to reach a temperature as high as 1473 K, which has temperature accuracy, good thermal stability, and long service life.
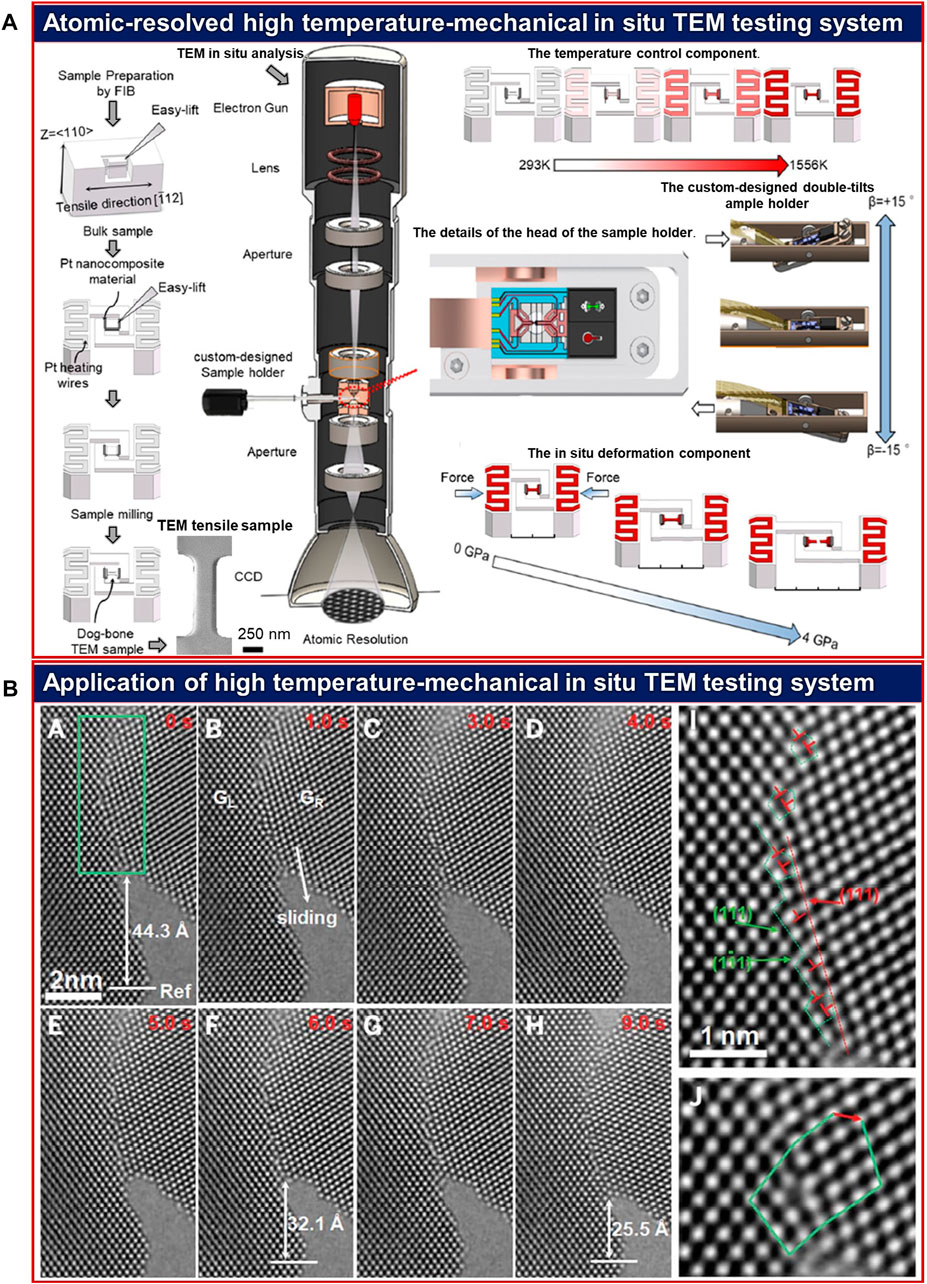
FIGURE 2. High-temperature mechanical in situ experimental techniques and application. (A) Schematic representation of the atomic-resolved high-temperature mechanical testing system (Zhang et al., 2021). (B) Snapshots of in situ TEM/MTS images showing atomic-scale sliding of an asymmetric tilt GB in a Pt bicrystal (Wang et al., 2022).
All these advantages make the in situ TEM/MTS a unique tool for tracking the sliding of GBs at the atomic scale for the first time (Wang et al., 2022). As shown in Figure 2B, using the in situ TEM/MTS , the atomic-level dynamic slip process of the GB can be observed, indicating that the GB slip at room temperature is achieved through the coordination between the direct slip between atoms at the GB and the short-range diffusion of atoms (Figure 2B). Such an observation is promising and has not been predicted in previous theories (Wang et al., 2022). In addition, with the high-temperature capability of in situ TEM/MTS , the atomistic fracture mechanism of tungsten has been reported (Zhang et al., 2021). On the atomic scale, the in situ experiment found that tungsten indeed fractures in a ductile manner at 973 K because strengthening induced multi-step body-centered cubic (BCC) to face-centered cubic (FCC) transformation. The plasticity of tungsten involves dislocation activities within the strain-induced FCC phase (Zhang et al., 2021). These research studies provide an approach for timely and atomic-resolved high-temperature mechanical investigation of materials at high temperatures. Current advances in high-temperature MTSs, which can be operated in a transmission electron microscope (TEM), might provide unique opportunities for in situ exploration of the mechanistic origins of GB brittleness of superalloys with a resolution up to the atomic scale.
The potential application on the investigation of grain boundary brittleness of precipitation-strengthened Ni-based superalloys
Over the past several years, rapid progress has been made in the in situ atomic resolution experiments, while the dynamic and atomic-scale resolution of research studies and methods on GB brittleness of Ni-based alloys are still in development. The ability to track the time-resolved, atomic-scale motion of GBs in a Pt bicrystal (Wang et al., 2022) opens opportunities for gaining deeper insight into the mechanisms of GB brittleness of precipitation-strengthened Ni-based superalloys. Revealing the atomistic mechanisms for the high-temperature mechanical behavior of GBs may answer important questions, such as when oxides were observed near the crack and whether they form before or after cracking. Theoretically, if the oxygen concentration can be measured in real-time in and just near the cracks using the in situ TEM/MTS with EDS mapping, details of cracking development related to the aforementioned questions can be answered, although such experiments still lack.
Despite these advantages, many challenges still remain, for example, the brittle fracture of GBs occurs very quickly; thus, it is hard to capture all details of the deformation microstructure characteristics in a very short time. The GBs refer to the interface of two grains with different crystal orientations. Particularly, the general type GBs in polycrystals are commonly asymmetric, which makes it difficult to realize the high resolution at the atomic level due to different Kikuchi patterns. In addition, the in situ tensile sample is merely prepared by FIB, and it is difficult to avoid gallium ion contamination or other implantation damage (Shim et al., 2009). Finally, most of the in situ mechanical sample stages are in a displacement-controlled or temperature-controlled mode, and direct force measurement is still in the development stage; therefore, it is difficult to capture the stress and quantitatively explain the deformation behavior of the material. We believe that the future development direction of high-temperature in-situ TEM/MTSs not only requires a very fine sample stage design but also needs to develop a sensitive stress detection system and high-temperature components with stable performance and high resolution under a harsh environment.
Conclusion and summary
GB brittleness significantly restricts the mechanical property of precipitation-strengthened Ni-based superalloys and limits their thermal-mechanical processing capability and industry applications. Current experimental and theoretical investigations of the origin of GB brittleness with aims to overcome it still need more effort for the high-temperature material field, especially since the detailed microscopic mechanism of GB remains ambiguous. Although current advances in high-temperature MTSs, which can be operated in a TEM, provide unique opportunities for gaining deeper insight into the mechanisms of GB brittleness of Ni-based superalloys, many challenges still remain. We believe that the future development direction of high-temperature in situ TEM/MTSs not only requires a very fine sample stage design but also needs to develop a sensitive stress detection system, high-temperature components with stable performance, and high resolution under a harsh environment.
Data availability statement
The original contributions presented in the study are included in the article/supplementary material; further inquiries can be directed to the corresponding authors.
Author contributions
QZ, QD, YZ, XW, ZZ, and HB all together finished this prospective article, including analyzing, writing, and figures.
Funding
This work was supported by the Basic Science Center Program for Multiphase Media Evolution in Hypergravity of the National Natural Science Foundation of China (No. 51988101), the Key R & D Project of Zhejiang Province (No. 2020C01002), the Natural Science Foundation of Zhejiang Province (No. LQ20E010008), the National Science and Technology Major Project of China (J2019-III-0008-0051), and the Innovation Fund of the Zhejiang Kechuang New Materials Research Institute (Nos. ZKN-20-P01 and ZKN-20-Z01).
Conflict of interest
The authors declare that the research was conducted in the absence of any commercial or financial relationships that could be construed as a potential conflict of interest.
Publisher’s note
All claims expressed in this article are solely those of the authors and do not necessarily represent those of their affiliated organizations, or those of the publisher, the editors, and the reviewers. Any product that may be evaluated in this article, or claim that may be made by its manufacturer, is not guaranteed or endorsed by the publisher.
References
Bestron (2019). Bestron science and technology. Available at: http://www.bestronst.com/.
Chabina, E. B., Lomberg, B. S., Filonova, E. V., Ovsepyan, S., and Bakradze, M. M. (2015). Change of structural and phase condition of heat resisting deformable nickel alloy at alloying tantalum and rhenium. Tr. VIAM 9, 3. doi:10.18577/2307-6046-2015-0-9-3-3
Chu, Z., Yu, J., Sun, X., Guan, H., and Hu, Z. (2010). Tensile property and deformation behavior of a directionally solidified Ni-base superalloy. Mater. Sci. Eng. A 527 (12), 3010–3014. doi:10.1016/j.msea.2010.01.051
Dong, J., Zhang, M., Xie, X., and Thompson, R. G. (2002). Interfacial segregation and cosegregation behaviour in a nickel-base alloy 718. Mater. Sci. Eng. A 328, 8–13. doi:10.1016/s0921-5093(01)01491-5
Duan, P., Zhang, P., Li, J., Li, B., Gong, X. F., Yang, G. X., et al. (2019). Intermediate temperature brittleness in a directionally solidified nickel-based superalloy M4706. Mater. Sci. Eng. A 759, 530–536. doi:10.1016/j.msea.2019.05.037
Fournier, L., Delafosse, D., and Magnin, T. (2001). Oxidation induced intergranular cracking and Portevin-Le Chatelier effect in nickel base superalloy 718. Mater. Sci. Eng. A 36, 166–173. doi:10.1016/s0921-5093(01)01224-2
Gao, M., Dwyer, D. J., and Wei, R. P. (1995). Niobium enrichment and environmental enhancement of creep crack growth in nickel-base superalloys. Scripta Metallurgica Materialia 32 (8), 1169–1174. doi:10.1016/0956-716x(95)00120-k
Hanna, B., Demura, M., Kishida, K., and Hirano, T. (2002). Fabrication of thin foils of binary Ni–Al γ/γ' two-phase alloys by cold rolling. Intermetallics 10, 255–262. doi:10.1016/s0966-9795(01)00133-9
Hirano, T. (1990). Improvement of room temperature ductility of stoichiometric Ni3Al by unidirectional solidification. Acta Metallurgica Materialia 38 (12), 2667–2671. doi:10.1016/0956-7151(90)90280-t
Lejček, P., Šob, M., and Paidar, V. (2017). Interfacial segregation and grain boundary embrittlement: An overview and critical assessment of experimental data and calculated results. Prog. Mater. Sci. 87, 83–139. doi:10.1016/j.pmatsci.2016.11.001
Liu, C. T., White, C. L., and Horton, A. J. (1985). Effect of boron on grain-boundaries in Ni 3Al. Acta Metall. 33 (2), 213–229. doi:10.1016/0001-6160(85)90139-7
Martin, M. L., Somerday, B. P., Ritchie, R. O., Sofronis, P., and Robertson, I. M. (2012). Hydrogen-induced intergranular failure in nickel revisited. Acta Mater. 60 (6-7), 2739–2745. doi:10.1016/j.actamat.2012.01.040
McLean, D., and Maradudin, A. (1958). Grain boundaries in metals. Phys. Today 11 (7), 35–36. doi:10.1063/1.3062658
Németh, A. A. N., Crudden, D. J., Armstrong, D. E. J., Collins, D. M., Li, K., Wilkinson, A. J., et al. (2017). Environmentally-assisted grain boundary attack as a mechanism of embrittlement in a nickel-based superalloy. Acta Mater. 126, 361–371. doi:10.1016/j.actamat.2016.12.039
Pang, X. J., Dwyer, D. J., Gao, M., Valerio, P., and Wei, R. P. (1994). Surface enrichment and grain boundary segregation of niobium in Inconel 718 single and poly-crystals. Scripta Metallurgica Materialia 31 (3), 345–350. doi:10.1016/0956-716x(94)90294-1
Pfaendtner, J. A., and McMahon, C. J. (2001). Oxygen-induced intergranular cracking of a Ni-base alloy at elevated temperatures—An example of dynamic embrittlement. Acta Mater. 49, 3369–3377. doi:10.1016/s1359-6454(01)00005-2
Pollock, T. M. (2016). Alloy design for aircraft engines. Nat. Mat. 15 (8), 809–815. doi:10.1038/nmat4709
Reed, R. C., and Rae, C. M. F. (2014). Physical Metallurgy of the nickel-based superalloys. Phys. Metall. 2014, 2215–2290. doi:10.1016/b978-0-444-53770-6.00022-8
Rice, J. R., and Wang, J. S. (1989). Embrittlement of interfaces by solute segregation. Mater. Sci. Eng. A 107, 23–40. doi:10.1016/0921-5093(89)90372-9
Shim, S., Bei, H., Miller, M. K., Pharr, G. M., and George, E. P. (2009). Effects of focused ion beam milling on the compressive behavior of directionally solidified micropillars and the nanoindentation response of an electropolished surface. Acta Mater. 57 (2), 503–510. doi:10.1016/j.actamat.2008.09.033
Viskari, L., Hörnqvist, M., Moore, K. L., Cao, Y., and Stiller, K. (2013). Intergranular crack tip oxidation in a Ni-base superalloy. Acta Mater. 61 (10), 3630–3639. doi:10.1016/j.actamat.2013.02.050
Wang, L., Zhang, Y., Zeng, Z., Zhou, H., He, J., Liu, P., et al. (2022). Tracking the sliding of grain boundaries at the atomic scale. Science 375 (6586), 1261–1265. doi:10.1126/science.abm2612
Watanabe, T. (2001). A general approach to the control of grain boundary fracture in brittle materials. Jpn. Soc. Mech. Eng. 01 (203), 126–133. doi:10.1299/jsmeatemapcfs.1.01.203.0_126
Yamaguchi, M., Shiga, M., and Kaburaki, H. (2005). Grain boundary decohesion by impurity segregation in a nickel-sulfur system. science 307 (5708), 393–397. doi:10.1126/science.1104624
Keywords: Ni-based superalloy, grain boundary brittleness, in situ TEM, precipitation strengthening, microstructure, intermetallic
Citation: Zhou Q, Ding Q, Zhang Y, Wei X, Zhang Z and Bei H (2022) The application of in situ TEM on the grain boundary brittleness of precipitation-strengthened Ni-based superalloys: Recent progress and perspective. Front. Met. Alloy 1:1016638. doi: 10.3389/ftmal.2022.1016638
Received: 11 August 2022; Accepted: 06 September 2022;
Published: 29 September 2022.
Edited by:
Michael Gao, National Energy Technology Laboratory (DOE), United StatesReviewed by:
Yanzhong Tian, Northeastern University, ChinaCopyright © 2022 Zhou, Ding, Zhang, Wei, Zhang and Bei. This is an open-access article distributed under the terms of the Creative Commons Attribution License (CC BY). The use, distribution or reproduction in other forums is permitted, provided the original author(s) and the copyright owner(s) are credited and that the original publication in this journal is cited, in accordance with accepted academic practice. No use, distribution or reproduction is permitted which does not comply with these terms.
*Correspondence: Qingqing Ding, cXFfZGluZ0B6anUuZWR1LmNu; Ze Zhang, emV6aGFuZ0B6anUuZWR1LmNu; Hongbin Bei, aGJlaTIwMThAemp1LmVkdS5jbg==