- Insititute of Metal Forming, TU Bergakademie Freiberg, Freiberg, Germany
In this study the influence of varying twin-roll casting (TRC) conditions on the microstructure, texture and mechanical properties of a Mg-6.8Y-2.5Zn-0.4Zr alloy (WZ73) was investigated. In particular the twin-roll cast speed and rolling gap were varied. Post twin-roll casting, the microstructure exhibits non-uniformity across the strip thickness and consists of a network-like arrangement of the long period stacking ordered (LPSO) phases and the α-Mg matrix. The α-Mg matrix is characterized by dobulites (flake-like structures). Various defects typical for twin-roll cast strips were observed, along with a notable impact of casting conditions on the precipitation, morphology, and phase composition of the LPSO phases. The twin-roll casting speed significantly influences the resultant microstructural features. Higher casting speeds reduce the average equivalent deformation degree, leading to an increase in the phase fraction of LPSO structures but a reduction in thickness. Additionally, higher TRC speeds result in decreased solidification times, promoting inhomogeneity and segregation defects. These changes also impact the distribution of precipitates and strip temperature at the roll gap exit, delaying solidification and influencing centerline segregation thickness. Kink bands and yttrium-rich precipitates were present in all samples, with LPSO phases precipitating along grain boundaries. No dynamic recrystallization was observed. Texture analysis revealed basal and non-basal slip activation, with lower intensities at higher TRC speeds. The yield strength (YTS) and tensile strength (UTS) behaved similar whilst the elongation remained unchanged by the TRC conditions.
1 Introduction
The utilization of Twin-roll Casting (TRC) has brought about a significant advancement in the manufacturing techniques for magnesium alloys, positioning itself as a crucial approach in the production of light metal sheets. This method is particularly beneficial as it merges casting and rolling into a unified and efficient process. Traditional methods for creating magnesium alloy sheets involve several steps: continuous casting, surface pretreatment, homogenization, pre-rolling through multiple passes, hot rolling, and various heat treatments (Wang et al., 2010; Asqardoust et al., 2017; Li et al., 2019). In contrast, TRC allows for the direct production of thin strips, typically ranging from 3 to 7 mm in thickness, directly from the molten state. This method delivers notable economic and energy advantages by generating semi-finished products with near-net-shape in a single operation. At present, TRC is mainly utilized for magnesium wrought alloys like from the AZ-series, the AM-series or the WE-series (Bohlen et al., 2015; Bae et al., 2009; Chang et al., 2012; Neh et al., 2016; Kittner et al., 2019).
Likewise, there was an increasing interest in magnesium alloys containing rare earth elements, which stems from their superior tensile strength of up to 610 MPa in nanocrystalline Mg-RE alloys produced via powder metallurgy and subsequent extrusion (Kawamura et al., 2001). In other research tensile strength above 400 MPa and elongations up to 12% could be achieved through rolling, extrusion or heat treatments (Itoi et al., 2008; Lu et al., 2015; Zhu et al., 2017). These mechanical properties are attributed to the presence of long period stacking ordered (LPSO) phases forming in alloys combining a rare earth element like Y, Gd, Nd or Dy and a transition atom like Zn, Ni or Cu (Saal and Wolverton, 2012). These LPSO structures, characterized by an extended stacking sequence along the c-axis, enhance both the strength and ductility of the alloys. The stacking sequence usually enhances 10-, 14-, 18- or 24-times and within this sequence, atomic layers are enriched with Y and Zn atoms. The enriched layers are arranged alternately with several α-Mg atomic layers. The unit cells are usually hexagonal (H) or rhombohedral (R) (Zhu et al., 2010; Abe et al., 2011). The formation of LPSO phases has been observed in ternary systems like Mg-Y-Zn and under various conditions, including conventional casting, heat treatments, and hot deformation processes (Kim et al., 2008; Li et al., 2009; Hagihara et al., 2010a; Wang et al., 2010; Liu et al., 2013). For example, in a cast Mg-Zn-Y alloy the 18R LPSO phase is most common. Notably, the LPSO phases differ in the stacking sequence of the unit cell, with the 18R and 14H types being the most common in Mg-Y-Zn alloys. However, differentiation between these ordering types based solely on chemical composition is not possible (Nie et al., 2014; Yang and Kim, 2019). Furthermore, the LPSO phases provide a special deformation mechanism the so-called kinking or formation of kink bands. Kink bands are described as areas between two approximately parallel walls formed by edge dislocations with opposite signs, originating in areas with increased local stress levels (Frank and Stroh, 1952). The kink bands have been observed before in other hot rolled, extruded or compressed magnesium alloys containing LPSO phases and display kink angles between 30° and 60° (Hagihara et al., 2010b; Kim et al., 2015; Egusa et al., 2021; Zheng et al., 2021).
Available literature on Y-containing Mg-wrought alloys with LPSO phase typically uses casting to produce ingots or billets and extrusion as the deformation process. However, twin-roll casting offers a much more effective production process for wrought alloys and is rarely investigated for LPSO-containing Mg alloys. Twin-roll casting of Mg-Y-Zn alloys has only been reported in a few studies. For instance, Suzawa et al. (2019) investigated the superplastic behavior of a TRC-prepared Mg-Zn-Y master alloy sheet, though they provided no details of the TRC process itself (Suzawa et al., 2019). Kim et al. (2008) studied the mechanical properties and microstructure of a Mg-Zn-Y alloy after TRC but found only icosahedral phases (I-phase), not LPSO phases, in this alloy (Kim et al., 2008). Additionally Kittner et al. (2020) investigated twin-roll casting of an WZ73 alloy before but they focused on hot rolling or the deformation behavior of one TRC state in particular (Kittner et al., 2020; Ullmann et al., 2021).
In this work, therefore, twin-roll casting of a Mg-Y-Zn alloy (WZ73) was applied to obtain thin sheets with a fine dendritic microstructure of α-Mg and LPSO phases. This paper investigates the influence of various twin-roll casting parameters, particularly the rolling gap and twin-roll casting speed, on the microstructure, texture and mechanical properties of the magnesium alloy WZ73.
2 Materials and methods
The present investigation involved the implementation of the horizontal TRC process on a pilot-plant scale, utilizing a TRC plant at an industrial scale located at the Institute of Metal Forming (IMF, TU Bergakademie Freiberg, Germany) made by hpl-Neugnadenfelder Maschinenfabrik GmbH (Kittner et al., 2020). Throughout the melting of the Mg-6.8Y-2.5Zn-0.4Zr (wt%) (WZ73) magnesium alloy ingots, a protective gas atmosphere (SF6) was meticulously maintained. Detailed information regarding the chemical composition of the WZ73 alloy can be found in Table 1. The melting of the WZ73 alloy ingots took place in a melting furnace using a steel crucible set at a temperature of 730°C, also under the SF6 protective gas atmosphere. Furthermore, the melting furnace was linked to a preheated launder and an adjacent nozzle through a riser. A pump was employed to ensure the continuous supply of molten magnesium, which was then introduced into the roll gap (4.5 mm, 4.42 mm, 4.38 mm) via the casting nozzle. The rolls utilized in the process had a diameter of 840 mm and were equipped with a water-cooling system. The interaction between the molten metal and the top and bottom rolls facilitated heat transfer at the contact interfaces. As a result, a meniscus-shaped solidification zone was formed, leading to a delayed solidification process in the central portion of the strip. Through the application of this technique, the production of a magnesium strip with a width of 710 mm and an average thickness ranging between 5.3 mm and 5.5 mm was achievable. The TRC speed was adjusted to fall within the range of 1.5 and 2.1 m/min.
For the purpose of performing the applied average equivalent deformation degree in twin-roll casting, the solidification model developed by Weiner et al. (2022) was implemented. Alloy-specific material parameters were used to calculate this model (Liu et al., 2018; Kittner et al., 2022). This particular model, which is rooted in the Freiberg Layer Model developed by Weiner et al. (2022), has the capability to replicate the average deformation degree
Samples for microstructure analysis were prepared through conventional grinding and polishing techniques. Two different types of acids were utilized for the etching process. Initially, a solution comprising distilled water, glacial acetic acid (C2H4O2 by Fisher Scientific GmbH), ethanol, and picric acid (C6H3N3O7 moistened with 33% of H2O by ITW Reagents) was employed, followed by the use of 3% nitric acid (Schmitz-Metallographie GmbH) in a subsequent step. The microstructure examination was carried out using optical microscope the Keyence VHX 6000 at the IMF in Freiberg, Germany, focusing on longitudinal measurements of the specimens. Additionally, a scanning electron microscope assessment including energy dispersive X-ray spectroscopy (EDS) was performed utilizing a ZEISS GeminiSEM 450 at the same facility. X-ray diffraction analysis was executed using a Seifert-FPM RD 7 device at the Institute of Materials Science at the TU Bergakademie Freiberg, employing CuKα radiation (λ = 1.540598 Å) for phase identification. The diffraction patterns were captured within a 2θ-range of 20°–150°, with a step size of 0.02° and a step time of 25 s. Moreover, texture analysis was conducted through electron backscattering diffraction (EBSD) analysis using a ZEISS GeminiSEM 450 instrument at the IMF. EBSD was conducted at 15 kV and a step size of 2.5 μm. Subsequently, the EBSD data was examined, and the pole figures were computed utilizing the MTex MATLAB Toolbox (version 5.9.0, MTex, Ralf Hielscher, TU Bergakademie Freiberg, Germany) (Bachmann et al., 2010).
Tensile tests were performed following the DIN EN ISO 6892–1 standard to evaluate the mechanical properties at ambient temperature using a universal testing machine (AG-50, Shimadzu Deutschland GmbH, Duisburg, Germany). The specimens conformed to the DIN 50125 shape H geometry with a gauge length of 80 mm and were prepared in parallel (0°) orientation relative to the twin-roll casting direction from the strip mid width. The gauge thickness corresponded to the strip thickness. To ensure statistical reliability, five specimens were tested under identical conditions. The testing was conducted at a constant crosshead speed of 2.0 mm/min.
3 Results and discussion
3.1 Simulations utilizing Freiberg Layer Model
For a more thorough evaluation of the various microstructures, the Freiberg Layer Model, as devised by Weiner et al. (2022), was utilized to compute the average equivalent deformation degree
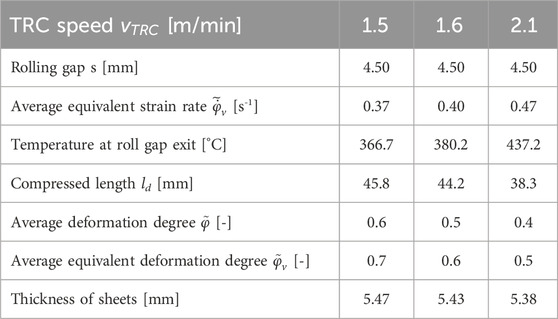
Table 2. Resulting average deformation degree, average equivalent deformation degree and average equivalent strain rate based on twin-roll casting parameters calculated by using the Freiberg layer model by Weiner et al. (2022) for a varying twin-roll casting speed.
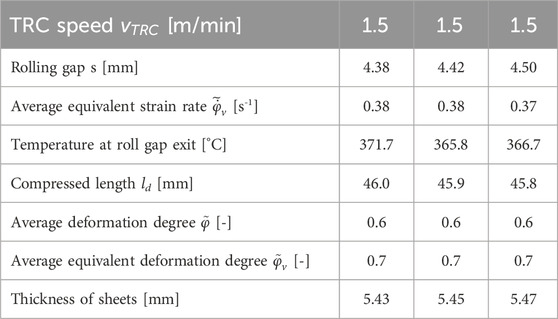
Table 3. Resulting average deformation degree, average equivalent deformation degree and average equivalent strain rate based on twin-roll casting parameters calculated by using the Freiberg layer model by Weiner et al. (2022) for a varying rolling gap.
During further analysis it was found that it is difficult to visualize the dependency on just one parameter as they are mutual dependent and all change as soon as one is changed. Additionally, all parameters shown in Table 2 have an influence on the microstructure, texture and mechanical properties of the twin-roll cast WZ73 alloy. For example, increasing the TRC speed reduces the average equivalent deformation degree but increases the strip temperature at roll gap exit, which in turn affects solidification kinetics and segregation behavior. Similarly, adjusting the rolling gap alters the compressed length and indirectly influences the phase fraction of LPSO phases.
3.2 Twin-roll cast defects
During the microstructural analysis, typical twin-roll cast defects such as surface bleeds, centerline segregations, cracks, and inhomogeneous microstructures could be detected within all investigated samples (Figure 1). The observed defects include surface bleeds, centerline segregations, an inhomogeneous microstructure, and the presence of cracks. These defects have been previously documented in twin-roll cast WZ73 alloy and other similar materials (Gras et al., 2005; Hadadzadeh and Wells, 2015; Li et al., 2020; Kittner et al., 2022). The most prominent among these defects are the centerline segregations, which exhibit an increase in thickness with an increase in TRC speed (see Figure 2) and an increase of the rolling gap. This formation of centerline segregation is attributed to the interplay of higher deformation levels, increased TRC speed, and elevated strip temperatures, as discussed in earlier studies (Gras et al., 2005; Hadadzadeh and Wells, 2015). The elevated TRC speed and associated factors result in a larger volume of liquid being compressed towards the center of the strip. This is due to the delayed solidification caused by the rapid movement and shorter contact time with the rolls, leading to a lower heat transfer rate. Furthermore, a bigger rolling gap also leads to a larger volume of liquid between the water-cooled rolls. Therefore the heat transfer takes more time and the material solidifies later giving more time to the segregation process (Gras et al., 2005; Wells and Hadadzadeh, 2014). The segregations depicted, e.g., in Figure 2 can be classified as deformation segregations. As described by Lockyer et al. (1996) they appear due to rapid deformation. The simultaneous deformation of the molten and solid materials generates small liquid pockets between the solid grains (Lockyer et al., 1996; Yun et al., 2000). Centerline segregations, on the other hand, primarily arise from the swift cooling of material in contact with the water-cooled rolls. This rapid cooling causes the solidification front to shift towards the strip’s center, leaving behind a residual melt enriched in alloying elements (Hadadzadeh and Wells, 2015; Kittner et al., 2019). The formation of cracks was found regardless of the TRC conditions (see Figure 1a) and has multiple reasons. For example, an uneven solidification can be the reason as well as the inhomogeneous microstructure (see Figure 1b). Due to the formation of large grains, which is caused by varying solidification conditions and the rather great freezing range of 30 K of the WZ73 alloy, intergranular cracking is promoted (Lockyer et al., 1996; Gras et al., 2002; Kittner et al., 2022). This freezing range can also promote the formation of surface bleeds, which were observed in all the samples and are visible in Figure 1c. As described by Barekar and Dhindaw (2014) the casting speed influences the development of surface bleeds as well (Barekar and Dhindaw, 2014). In this study it was observed that the thickness and connectivity of the surface bleeds decreases with an increased TRC speed and increased rolling gap. This development results from less contact time with and less pressure during rolling. Therefore, less melt is squeezed from the strip middle towards the surface where it then solidifies (Gras et al., 2002; Essadiqi et al., 2012; Barekar and Dhindaw, 2014).
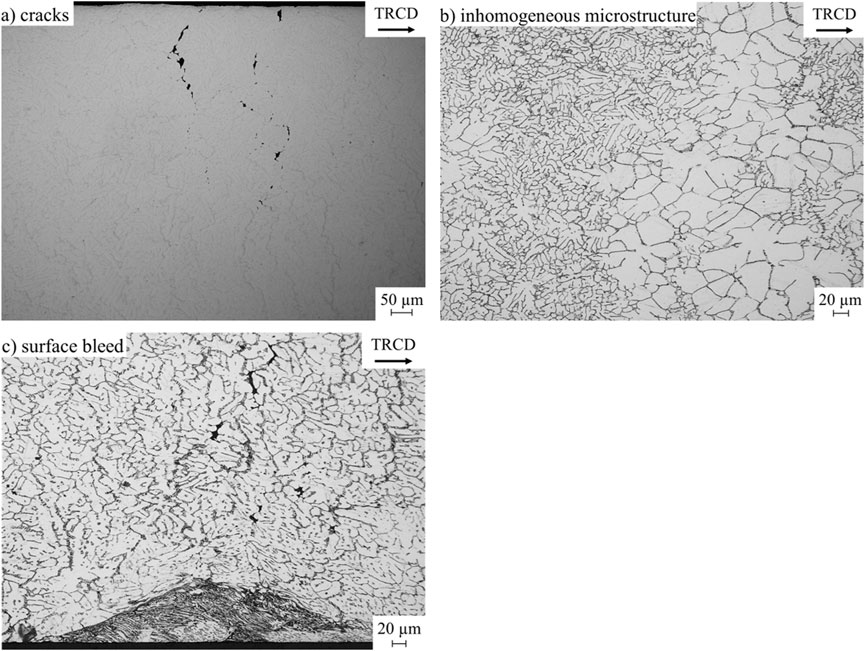
Figure 1. Optical images of twin-roll cast defects observed in the WZ73 alloy (a) cracks; (b) inhomogeneous microstructure; (c) surface bleed.
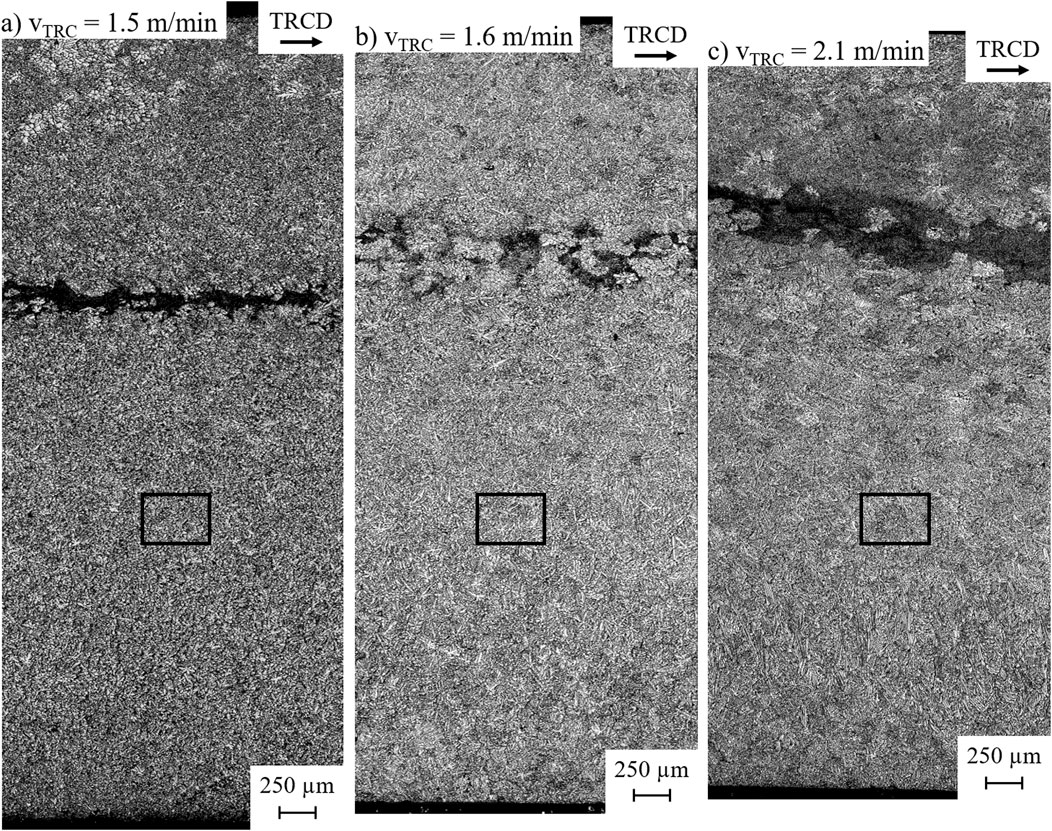
Figure 2. Optical images showing the entire strip thickness of the twin-roll cast WZ73 alloy depending on the twin-roll casting speed (a) vTRC = 1.5 m/min; (b) vTRC = 1.6 m/min; (c) vTRC = 2.1 m/min including markings for Figure 3.
3.3 Microstructure
The chemical composition of the WZ73 alloy (Table 1) shows higher measured values for Y (7.7 wt%), Zn (4.1 wt%), and Zr (0.5 wt%) compared to the nominal composition (6.8Y-2.5Zn-0.4Zr). This deviation may arise from analytical uncertainties inherent to EDS measurements, such as matrix effects or limited detection limits for light elements. Additionally, minor impurities or inhomogeneities in the alloy during melting could contribute to this variation. The slight excess of Y and Zn aligns with prior studies on Mg-Y-Zn alloys, where compositional fluctuations are common due to the volatility of Zn during melting and the tendency of Y to segregate during solidification (e.g. (Zhu et al., 2010)).
The microstructures depending on the different applied TRC speeds are presented in Figure 2 showing the whole strip thickness. The centerline segregations are clearly visible and are becoming thicker when the average equivalent deformation degree is decreasing. Additionally, an inhomogeneous microstructure can be observed. Both phenomena have been described in the previous chapter. Figure 3 shows the microstructure in detail below mid thickness. The microstructure widely consists of flake-like structures (marked with red circles), so called dobulites which have been reported for a twin-roll cast WZ73 alloy before (Kittner et al., 2020). It can also be observed that the microstructure consists of two parts: a light part referring to the α-Mg matrix and darker, network-like shapes which were identified as LPSO phases. In general, the microstructure lacks large dendrites which are typically formed from the surface to the middle of the strip. This is a distinguishing feature compared to twin-roll cast microstructures observed in AZ31 or ZAX210 alloys (Hadadzadeh and Wells, 2015; Kittner et al., 2019). Also small grains cannot be identified, indicating that no dynamic recrystallisation took place during TRC. This is consistent with observations made by Ullmann et al. (2021). They found that the recrystallization characteristics of the WZ73 alloy during hot rolling are predominantly influenced by the equivalent strain rate as opposed to the average equivalent deformation degree. It is observed that the average equivalent strain rate applied during twin-roll casting is relatively low, possibly contributing to the absence of dynamic recrystallization sites. A similar columnar microstructure was observed by Barekar and Dhindaw (2014) for a twin-roll cast aluminum alloy. Accordingly this type of microstructure is based on the deformation and the faster cooling during the TRC process (Barekar and Dhindaw, 2014). In addition to the dobulites some grains can be observed but grain boundaries are not detectable. This suggests that the secondary phase (LPSO phase) distributes along the grain boundaries. A proof for this will be presented in later in Figure 9. The precipitation along the grain boundaries was discussed before by Chen et al. (2010) for the microstructure of cast Mg-Y-Zn alloys. They identified the network-like structure as the X-phase (Mg12YZn) which can be associated with the LPSO phase. The observed type of precipitation indicates the 18R stacking sequence (Chen et al., 2010; Chen et al., 2012; Chiu and Huang, 2018). In this study the EDS measurements (see Figures 3b,d,f) performed also suggest that the precipitates marked with number 2 and 4 belong to yttrium and zinc rich phases like the Mg12YZn phase. As mentioned before this phase is often associated with LPSO structures, though a direct stoichiometric equivalence is not always confirmed due to variations in stacking sequences (e.g., 18R vs 14H). The precipitation along grain boundaries further supports the 18R type identification, as this morphology is characteristic of the 18R LPSO phase in WZ73 alloys (Nie et al., 2014; Yang and Kim, 2019; Krbetschek et al., 2022). Additionally Zr-rich precipitates marked with A3, B3 and C3 were identified and usually located at the center of a flake-like structure. The precise chemical composition could not be identified as they are too small and therefore exceeding the detection limit of the EDS measurement. Zirconium was not found in either the matrix or the network-like structures.
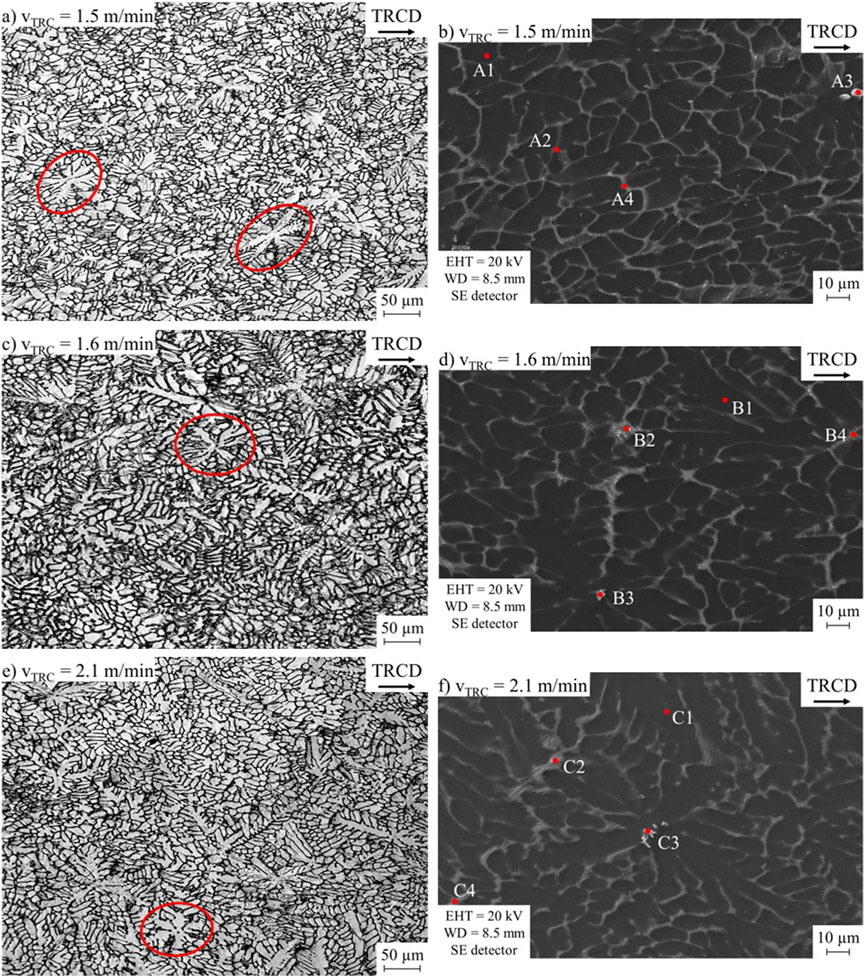
Figure 3. Detailed optical images (a,c,e) and SEM images (b,d,f) of the twin-roll cast WZ73 alloy taken below mid-thickness including points of EDS analysis (point 1: magnesium matrix, points 2 to 4 precipitates) (a,b) vTRC = 1.5 m/min; (c,d) vTRC = 1.6 m/min; (e,f) vTRC = 2.1 m/min (red circles showing dobulites).
The Table 4 and Figure 4 show the development of the thickness and phase fraction of the LPSO phases depending on the TRC speed. Whereas the phase fraction increases with an increased TRC speed, the thickness slightly decreases. This is a result of the TRC speed which leads to a lower average equivalent deformation degree when increased. Resulting from a higher TRC speed the contact time between the melt and rolls decreases. Therefore, the heat transfer is lower, resulting in a higher strip temperature. As the precipitation is based on diffusion, which is dependent on time and temperature, the higher strip temperature gives more time for the alloying elements dissolve into the matrix and the formation of LPSO phase. This can also be seen by the lower Mg contents of the matrix in Table 5.
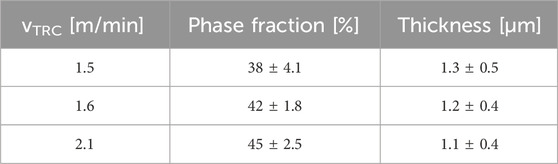
Table 4. Phase fraction and thickness of the LPSO phase depending on the twin-roll casting speed vTRC.
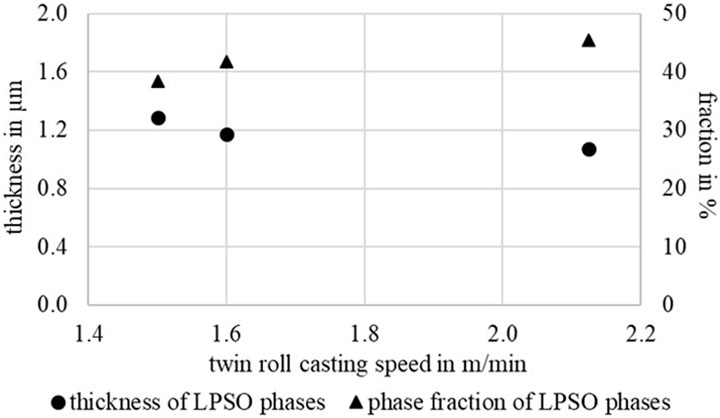
Figure 4. Evolution of the phase fraction and thickness of the LPSO phase depending on the twin-roll casting speed vTRC.
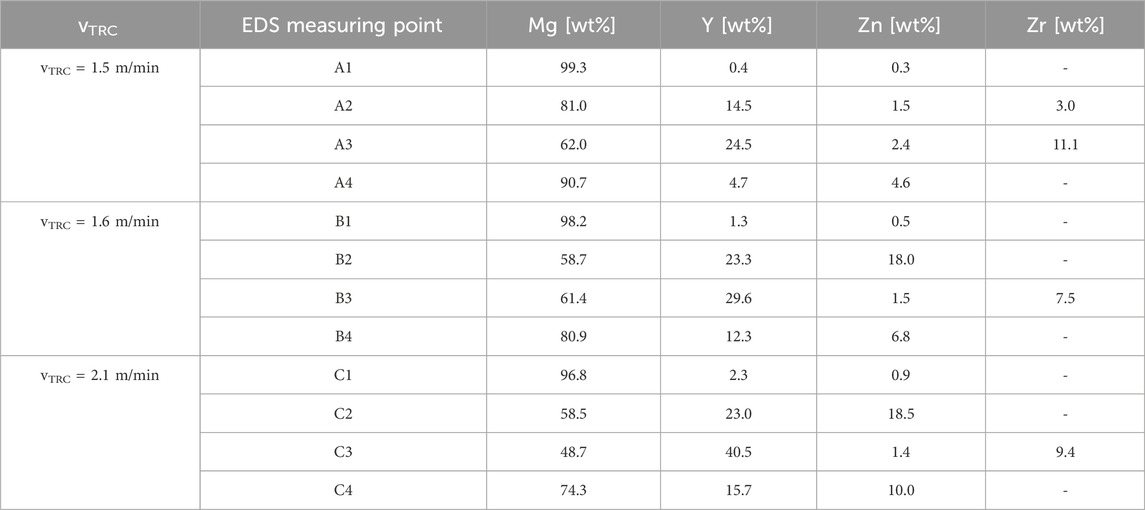
Table 5. Chemical composition of structural constituents according to marking in SEM images Figures 3b,d,f determined via EDS analysis (energy dispersive X-ray spectroscopy) of the twin-roll cast WZ73 alloy.
The results of the X-ray diffraction (XRD) analysis presented graphically in Figure 5. In addition to the α-Mg phase, the Mg12YZn phase and the Mg3Y2Zn3 phase were detected. The Mg12YZn, which was detected, has been assigned as the stoichiometry of the LPSO phases (Zhu et al., 2010; Lu et al., 2012; Yang and Kim, 2019). But this does not line up with the from literature identified peaks for the LPSO phases (Hadadzadeh and Wells, 2015; Saadati et al., 2017; Kittner et al., 2019; Yang and Kim, 2019). A reason can be different chemical composition of the alloys and the fact that a clear identification of the specific stacking sequence of the LPSO phase and therefore clarification whether it is 14H or 18R is not possible via XRD. The identified Mg3Y2Zn3 phase is assigned to the W-phase in WZ73 and has been detected in twin-roll cast Mg-Y-Zn alloys before (Kim et al., 2008; Yang and Kim, 2019).
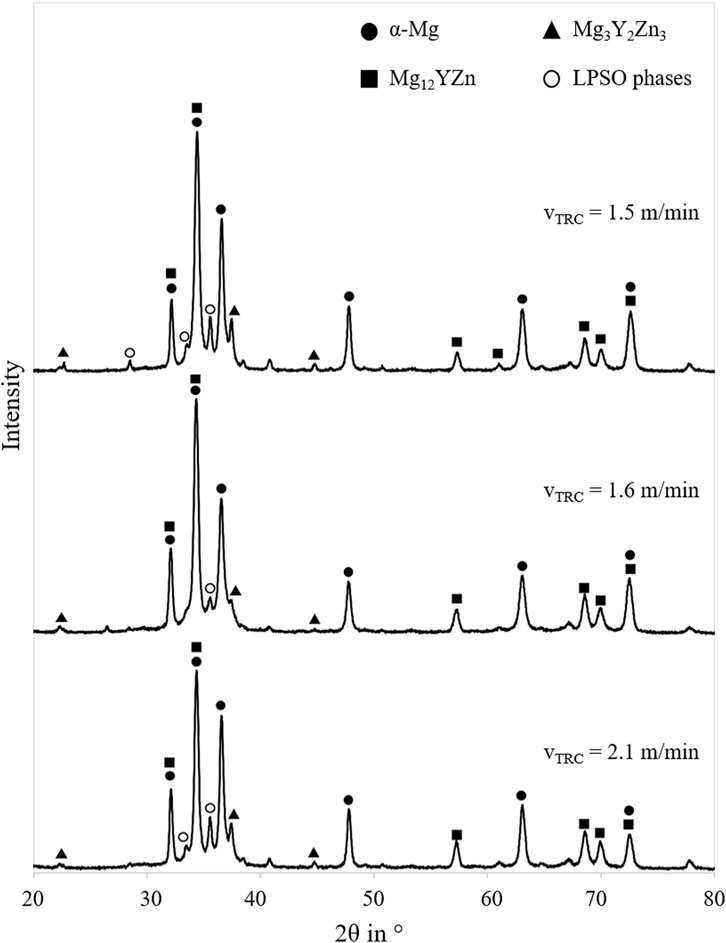
Figure 5. Results of the XRD analysis of the twin-roll cast WZ73 alloy measured along the cross section.
As for the influence of the rolling gap the microstructures are shown in Figure 6. It can be seen that there no significant centerline segregations above the strip middle regardless of the rolling gap (see Figures 6a–c). The detailed images in Figures 6d–f show that the microstructure consists of two parts as well, the α-Mg matrix and the LPSO phase. The matrix can be seen as the light, flake-like structure (marked with red circles) and the LPSO phase as dark, network-like structure (Kurz et al., 2015; Kittner et al., 2020). Both structural parts show a similar composition as described before in Table 5. But grain boundaries can be hardly detected yet again. Fine grains indicating dynamic recrystallization were not observed in any of the samples. Regarding the investigation of Ullmann et al. (2021) which suggests a propagation of dynamic recrystallisation with higher equivalent strain rates, it can be proposed that an average equivalent strain rate of 0.4 s-1 (compare Table 2) is too low for this mechanism to appear.
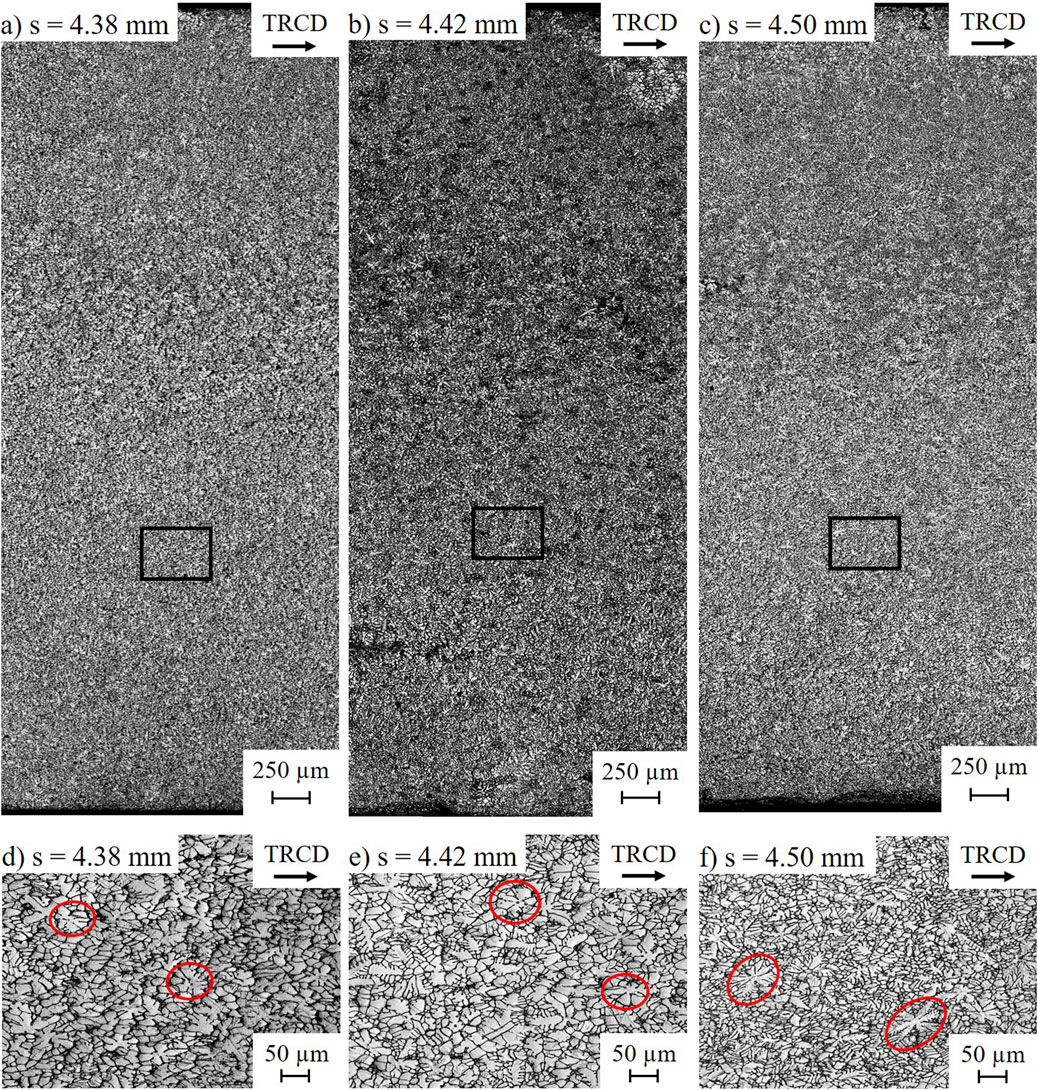
Figure 6. Optical images showing (a–c) the entire strip thickness of the twin-roll cast WZ73 alloy including markings for the (d–f) detailed images depending on the rolling gap (a,d) s = 4.38 mm; (b,e) s = 4.42 mm; (c,f) s = 4.50 mm (red circles showing dobulites).
The evaluation of the phase fraction and thickness of the LPSO phase depending on the rolling gap is presented in Table 6 and Figure 7. It is visible that the phase fraction increases slightly with an increased rolling gap whereas the thickness of the phases decreases. This can be explained by the reduced contact of the melt and the rolls. Because of that the heat transfer and cooling rate of the strip is reduced favoring the precipitation of the LPSO phases as the strip temperature is higher and there is more time to precipitate (Gras et al., 2005; Wells and Hadadzadeh, 2014; Javaid et al., 2016). At the same time the alloying elements dissolute more in the matrix or precipitate within the centerline segregation. This leads to the reduced thickness of the LPSO phase.
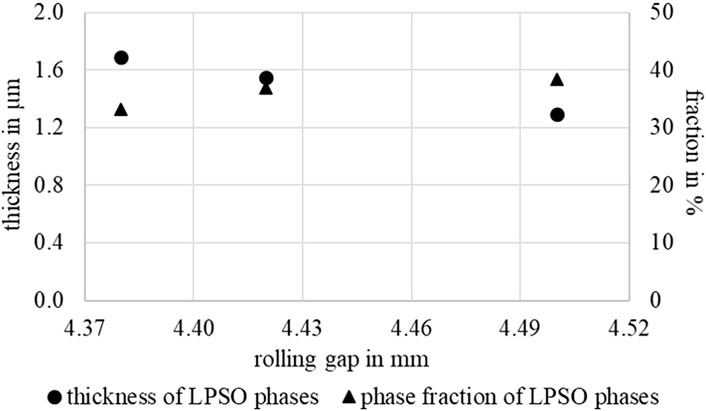
Figure 7. Evolution of the thickness and the phase fraction of the LPSO phases depending on the rolling gap.
In all investigated variations of TRC speed and rolling gap kink bands could be observed within the 18R LPSO phase as shown in Figure 8 (marked with green arrows). They were usually detected in the strip middle. The morphology has been reported before for kinked 18R phase, for example, after the ECAP process (Liu et al., 2017; Sun et al., 2024). It was reported by Zheng et al. (2021) that kinking within the 18R phase usually tends to occur if the angle between the basal planes and the direction of force impact is big. This is the case if the basal planes are orientated perpendicular to the direction of the force. Kinking then progresses by a lattice rotation due to the generation and slip of dislocation pairs of opposite signs on basal planes (Zheng et al., 2021). It is also believed that kinking becomes more dominant when the basal slip is hindered during the deformation process (Hagihara et al., 2010b; Liu et al., 2017). Therefore it is suggested that during the TRC process the 18R phases kink because the basal planes are orientated favorably to the compression direction during rolling (compare (0001) pole figures in Figure 10) and the basal slip is hindered due to the solidification and strip cooling. If the deformation process would go on the 18R phase would start zigzagging and finally break into smaller precipitates as it was observed by Liu et al. during severe deformation (Liu et al., 2017).
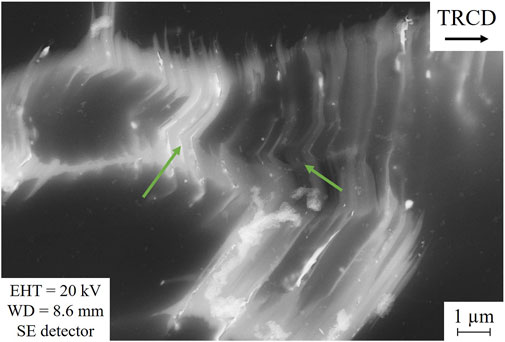
Figure 8. Detailed SEM image of kinked 18R LPSO phase in the twin-roll cast WZ73 alloy (green arrows mark kink bands).
Figure 9 shows an overlap of an optical image and an EBSD map of the same spot of a twin-roll cast WZ73 sample. The different colors mark the different orientations of the dobulites. It is visible that the LPSO phases (black, network like structures) precipitated within of these flake-like structures and along the boundaries. The precipitation along the boundaries is marked by the circled areas. This image clearly states why the boundaries are not properly visible during the optical investigations as they are overlapped by the network-like structure of the LPSO phase.
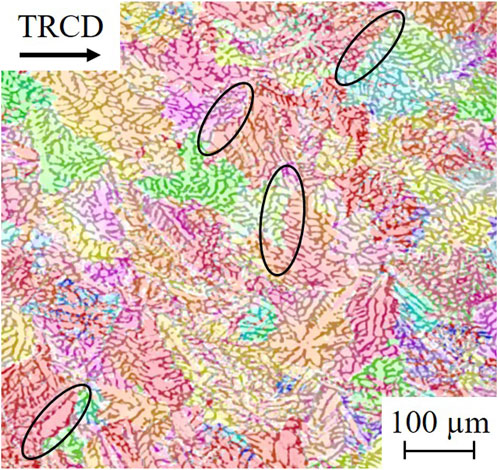
Figure 9. Overlapping of an optical image and EBSD map at the same position of the twin-roll cast WZ73 alloy with markings for overlapping LPSO phases and grain boundaries.
3.4 Texture
The (0001) and
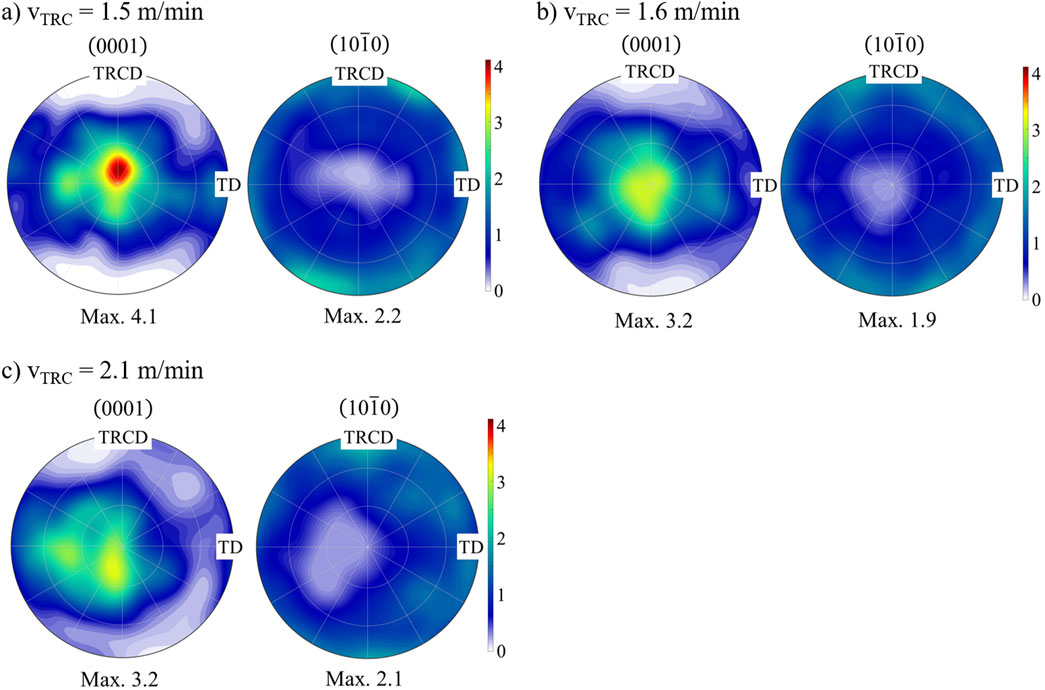
Figure 10. (0001) and
3.5 Mechanical properties
The results of the tensile tests performed at room temperature for the twin-roll cast WZ73 alloy are presented in Table 7. Figure 11 displays stress-strain curves of the twin-roll cast material shown exemplarily on one of the five tested samples. The material shows a brittle behavior with a small elongation at fracture. This is due to the inhomogeneous microstructure caused by the varying solidification kinetics and was presented before for other magnesium alloys (Lee et al., 2005; Kim et al., 2008; Neh et al., 2014; Kittner et al., 2019). Additionally the network-like distribution of the LPSO phases influences the mechanical properties (Ullmann et al., 2021).

Table 7. Mechanical properties of the twin-roll cast WZ73 alloy depending on the twin-roll casting speed vTRC, average value of five samples.
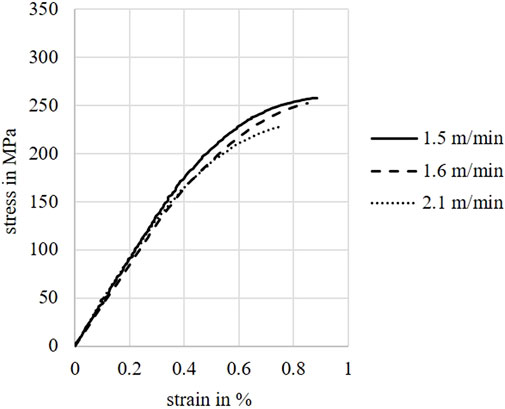
Figure 11. Stress-strain curves of the twin-roll cast WZ73 alloy at room temperature (shown exemplarily on one of five tested samples).
The influence of twin-roll casting parameters demonstrates that an increased TRC speed leads to a reduction in both yield strength (YTS) and ultimate tensile strength (UTS), while elongation remains unchanged. This decline in YTS and UTS can be attributed to the microstructural evolution observed at higher twin roll casting speeds. The mechanical properties are also closely linked to microstructural features and defects observed in TRC WZ73 alloys. Centerline segregations, which increase in thickness with rising TRC speed, act as crack initiation sites during tensile testing, contributing to the observed decrease in YTS and UTS. Simultaneously, the network-like LPSO phases at grain boundaries enhance strength through kink band formation and improved load transfer but may reduce ductility due to their inhomogeneous distribution. The absence of dynamic recrystallization, likely caused by low strain rates, further contributes to the brittle behavior (Kim et al., 2008; Qian et al., 2022).
The mechanical properties are also closely linked to the microstructural features of the LPSO phases. As shown in Figures 4, 7, the phase fraction of LPSO structures increases with higher TRC speeds and rolling gaps, while their thickness decreases. This trend is attributed to the interplay between solidification kinetics and alloying element diffusion. Higher TRC speeds reduce the average equivalent deformation degree (Table 3), leading to prolonged solidification times and increased phase fraction. However, the thinner LPSO phases at higher TRC speeds may limit their ability to act as effective barriers to dislocation motion, potentially reducing their strengthening contribution (Kim et al., 2008). The network-like distribution of LPSO phases at grain boundaries enhances strength through kink band formation and improved load transfer (Zheng et al., 2021). However, their inhomogeneous distribution, particularly in regions with thick centerline segregations, may promote crack initiation and reduce ductility. The observed decrease in YTS and UTS with increasing TRC speed (Table 7) aligns with the increased thickness of centerline segregations, which act as stress concentrators (Qian et al., 2022).
The interplay between twin-roll casting parameters, microstructure, texture, and mechanical properties is evident in this study. Higher TRC speeds reduce the average equivalent deformation degree, leading to increased LPSO phase fractions and thicker centerline segregations. These microstructural features correlate with the observed decrease in yield and ultimate tensile strengths, as segregations act as crack initiation sites. The texture evolution, characterized by basal pole elongation and pyramidal slip activation, further supports the role of non-basal slip in accommodating deformation.
While the as-cast material exhibits limited ductility, previous research has demonstrated that post-TRC processing can significantly improve mechanical properties. For example, heat treatment at 500°C for 2 h increases elongation to 4% (UTS = 195 ± 3 MPa; YTS = 136 ± 2 MPa), and hot rolling with an equivalent strain of 0.6 and strain rate of 62 s-1 further enhances ductility to 12% (UTS = 270 ± 4 MPa; YTS = 191 ± 4 MPa) (Ullmann et al., 2021).
4 Conclusion
The present work shows the influence of twin-roll casting parameters (twin-roll cast speed and rolling gap) on the microstructure and texture evolution as well as mechanical properties based on the average equivalent deformation degree and average equivalent strain rate of the twin-roll cast state. The results can be summarized as follows:
1. Various speeds of TRC ranging from 1.5 m/min to 2.1 m/min were subjected to testing. The solidification model was employed to determine the average equivalent deformation degree and compressed length. It was observed that, across all the TRC speeds examined, the average equivalent strain rate remained consistent, whereas the average equivalent deformation degree decreased as the TRC speed increased. The rolling gap does not significantly influence the average equivalent deformation degree and average equivalent strain rate.
2. Common twin-roll casting defects like cracks, an inhomogeneous microstructure, centerline segregations and surface bleeds could be detected.
3. The microstructure is composed of an α-Mg matrix and network-like LPSO phases that are present at the grain boundaries. The proportion of LPSO phases increases as the twin-roll casting speed increases. The identification of the Mg12YZn phase as part of the LPSO phase was confirmed through XRD measurements. The specific ordering within the phases was not definitively determined, although the presence of the 18R LPSO phase was indicated by precipitation along the grain boundaries. Additionally, small yttrium and zirconium rich precipitates were observed but their chemical composition could not be clearly identified due to their size.
4. The texture is characterized by an elongated basal pole in the twin-roll cast direction with low intensity decreasing with an increased twin-roll casting speed. The activation of pyramidal slip systems is suggested by the observed sixfold symmetry in the
5. The YTS and UTS are decreasing with an increasing twin-roll casting speed whilst the elongation remains unchanged.
Data availability statement
The raw data supporting the conclusions of this article will be made available by the authors, without undue reservation.
Author contributions
FU: Formal analysis, Visualization, Methodology, Conceptualization, Writing – review and editing, Writing – original draft, Investigations. MU: Validation, Conceptualization, Writing – review and editing. UP: Supervision, Writing – review and editing.
Funding
The author(s) declare that financial support was received for the research and/or publication of this article. This research was funded by the Deutsche Forschungsgemeinschaft (DFG, German Research Foundation) – Project number 497456843.
Acknowledgments
The authors acknowledge the support of Max Weiner for providing the initial code for the simulations and guidance regarding its usage and the work of Dr. Schimpf from the Institute of Materials Science at TU Bergakademie Freiberg as he provided the XRD-measurements.
Conflict of interest
The authors declare that the research was conducted in the absence of any commercial or financial relationships that could be construed as a potential conflict of interest.
Generative AI statement
The author(s) declare that no Generative AI was used in the creation of this manuscript.
Publisher’s note
All claims expressed in this article are solely those of the authors and do not necessarily represent those of their affiliated organizations, or those of the publisher, the editors and the reviewers. Any product that may be evaluated in this article, or claim that may be made by its manufacturer, is not guaranteed or endorsed by the publisher.
References
Abe, E., Ono, A., Itoi, T., Yamasaki, M., and Kawamura, Y. (2011). Polytypes of long-period stacking structures synchronized with chemical order in a dilute Mg–Zn–Y alloy. Philos. Mag. Lett. 91 (10), 690–696. doi:10.1080/09500839.2011.609149
Asqardoust, S., Zarei-Hanzaki, A., Abedi, H. R., Krajnak, T., and Minárik, P. (2017). Enhancing the strength and ductility in accumulative back extruded WE43 magnesium alloy through achieving bimodal grain size distribution and texture weakening. Mater. Sci. Eng. A 698, 218–229. doi:10.1016/j.msea.2017.04.098
Azzeddine, H., and Bradai, D. (2011). Texture and microstructure of WE54 alloy after hot rolling and annealing. Mater. Sci. Forum 702-703, 453–456. doi:10.4028/www.scientific.net/MSF.702-703.453
Bachmann, F., Hielscher, R., and Schaeben, H. (2010). Texture analysis with MTEX – free and open source software Toolbox. Semi-Solid Process. Alloys Compos. X (160), 63–68. doi:10.4028/www.scientific.net/SSP.160.63
Bae, G. T., Bae, J. H., Kang, D. H., Lee, H., and Kim, N. J. (2009). Effect of Ca addition on microstructure of twin-roll cast AZ31 Mg alloy. Metals Mater. Int. 15 (1), 1–5. doi:10.1007/s12540-009-0001-3
Barekar, N. S., and Dhindaw, B. K. (2014). Twin-roll casting of aluminum alloys – an overview. Mater. Manuf. Process. 29 (6), 651–661. doi:10.1080/10426914.2014.912307
Bohlen, J., Yi, S., Victoria-Hernández, J., Schell, N., Schwebke, B., Brokmeier, H.-G., et al. (2015). The microstructure and texture development during twin roll casting and rolling of magnesium alloy AZ31. 471–476. doi:10.1002/9781119093428.ch87
Chang, L. L., Cho, J. H., and Kang, S. K. (2012). Microstructure and mechanical properties of twin roll cast AM31 magnesium alloy sheet processed by differential speed rolling. Mater. & Des. 34, 746–752. doi:10.1016/j.matdes.2011.06.060
Chen, B., Lin, D., Zeng, X., and Lu, C. (2010). Effects of yttrium and zinc addition on the microstructure and mechanical properties of Mg–Y–Zn alloys. J. Mater. Sci. 45 (9), 2510–2517. doi:10.1007/s10853-010-4223-z
Chen, B., Lu, C., Lin, D., and Zeng, X. (2012). Effect of zirconium addition on microstructure and mechanical properties of Mg97Y2Zn1 alloy. Trans. Nonferrous Metals Soc. China 22 (4), 773–778. doi:10.1016/S1003-6326(11)61244-2
Chiu, C., and Huang, H.-M. (2018). Microstructure and properties of Mg-Zn-Y alloy powder compacted by equal channel angular pressing. Mater. (Basel, Switz.) 11 (9), 1678. doi:10.3390/ma11091678
Egusa, D., Inoue, K., Nagai, Y., and Abe, E. (2021). Recovery features of kink boundaries upon post-annealing of a hot-extruded Mg-Zn-Y alloy. Mater. Charact. 177, 111153. doi:10.1016/j.matchar.2021.111153
Essadiqi, E., Jung, I.-H., and Wells, M. A. (2012). “Twin roll casting of magnesium,” in Advances in Wrought Magnesium Alloys//Advances in wrought magnesium alloys: fundamentals of processing, properties and applications. Editors C. Bettles, and M. R. Barnett (Cambridge: Elsevier; Woodhead Publ), 272–303.
Frank, F. C., and Stroh, A. N. (1952). On the theory of kinking. Proc. Phys. Soc. Sect. B 65 (10), 811–821. doi:10.1088/0370-1301/65/10/311
Gras, C., Meredith, M., Gatenby, K., and Hunt, J. D. (2002). Defect Formation in twin roll-cast AA 3xxx and 5xxx series aluminium alloys. Mater. Sci. Forum 396-402, 89–94. doi:10.4028/www.scientific.net/MSF.396-402.89
Gras, C., Meredith, M., and Hunt, J. D. (2005). Microdefects formation during the twin-roll casting of Al–Mg–Mn aluminium alloys. J. Mater. Process. Technol. 167 (1), 62–72. doi:10.1016/j.jmatprotec.2004.09.084
Hadadzadeh, A., and Wells, M. A. (2015). Inverse and centreline segregation formation in twin roll cast AZ31 magnesium alloy. Mater. Sci. Technol. 31 (14), 1715–1726. doi:10.1179/1743284714Y.0000000750
Hagihara, K., Kinoshita, A., Sugino, Y., Yamasaki, M., Kawamura, Y., Yasuda, H. Y., et al. (2010a). Effect of long-period stacking ordered phase on mechanical properties of Mg97Zn1Y2 extruded alloy. Acta Mater. 58 (19), 6282–6293. doi:10.1016/j.actamat.2010.07.050
Hagihara, K., Yokotani, N., and Umakoshi, Y. (2010b). Plastic deformation behavior of Mg12YZn with 18R long-period stacking ordered structure. Intermetallics 18 (2), 267–276. doi:10.1016/j.intermet.2009.07.014
Itoi, T., Takahashi, K., Moriyama, H., and Hirohashi, M. (2008). A high-strength Mg–Ni–Y alloy sheet with a long-period ordered phase prepared by hot-rolling. Scr. Mater. 59 (10), 1155–1158. doi:10.1016/j.scriptamat.2008.08.001
Javaid, A., Hanke, J., Simha, C. H., and Kozdras, M. S. (2016). “Twin roll casting of magnesium strip at canmet materials — modeling and experiments,” in Magnesium Technology 2015. Editors M. V. Manuel, A. Singh, M. Alderman, and N. R. Neelameggham (Cham: Springer), 461–464.
Kawamura, Y., Hayashi, K., Inoue, A., and Masumoto, T. (2001). Rapidly solidified powder metallurgy Mg97Zn1Y2Alloys with excellent tensile yield strength above 600 MPa. Mater. Trans. 42 (7), 1172–1176. doi:10.2320/matertrans.42.1172
Kim, J.-K., Sandlöbes, S., and Raabe, D. (2015). On the room temperature deformation mechanisms of a Mg–Y–Zn alloy with long-period-stacking-ordered structures. Acta Mater. 82, 414–423. doi:10.1016/j.actamat.2014.09.036
Kim, K.-H., Suh, B.-C., Bae, J. H., Shim, M.-S., Kim, S., and Kim, N. J. (2010). Microstructure and texture evolution of Mg alloys during twin-roll casting and subsequent hot rolling. Scr. Mater. 63 (7), 716–720. doi:10.1016/j.scriptamat.2009.12.010
Kim, K.-H., Lee, J. G., Bae, G. T., Bae, J. H., and Kim, N. J. (2008). Mechanical properties and microstructure of twin-roll cast Mg-Zn-Y alloy. Mater. Trans. 49 (5), 980–985. doi:10.2320/matertrans.MC200752
Kittner, K., Ullmann, M., Arndt, F., Berndorf, S., Henseler, T., and Prahl, U. (2022). Analysis of defects in a twin roll cast Mg-Y-Zn magnesium alloy. Eng. Rep. 4 (7-8). doi:10.1002/eng2.12394
Kittner, K., Ullmann, M., Arndt, F., Kawalla, R., and Prahl, U. (2020). Microstructure and texture evolution during twin-roll casting and annealing of a Mg–6.8Y2.5Zn–0.4Zr alloy (WZ73). Crystals 10 (6), 513. doi:10.3390/cryst10060513
Kittner, K., Ullmann, M., Henseler, T., Kawalla, R., and Prahl, U. (2019). Microstructure and hot deformation behavior of twin roll cast Mg-2Zn-1Al-0.3Ca alloy. Mater. (Basel, Switz.) 12 (7), 1020. doi:10.3390/ma12071020
Krbetschek, C., Trân, R., Wemme, H., Ullmann, M., Prahl, U., and Rafaja, D. (2022). Hot crack susceptibility of cast Mg97Y2Zn1. Eng. Rep. 4 (7-8). doi:10.1002/eng2.12380
Kurz, G., Wendt, J., Bohlen, J., and Letzig, D. Microstructure evolution of different magnesium alloys during twin roll casting, (2015). 465–470. doi:10.1002/9781119093428.ch86
Lee, J. Y., Kim, D. H., and Lim, H. K. (2005). Effects of Zn/Y ratio on microstructure and mechanical properties of Mg-Zn-Y alloys. Mater. Lett. 59 (29-30), 3801–3805. doi:10.1016/j.matlet.2005.06.052
Li, B., Teng, B., and Wang, E. (2019). Effects of accumulative rolling reduction on the microstructure characteristic and mechanical properties of Mg-Gd-Y-Zn-Zr sheets processed by hot rolling. Mater. Sci. Eng. A 765, 138317. doi:10.1016/j.msea.2019.138317
Li, R. G., Fang, D. Q., An, J., Lu, Y., Cao, Z. Y., and Liu, Y. B. (2009). Comparative studies on the microstructure evolution and fracture behavior between hot-rolled and as-cast Mg96ZnY3 alloys. 8th STERMAT Stereology Image Analysis Mater. Sci. 60 (6), 470–475. doi:10.1016/j.matchar.2008.11.015
Li, Y., He, C., Li, J., Wang, Z., Wu, Di, and Xu, G. (2020). A novel approach to improve the microstructure and mechanical properties of Al-Mg-Si aluminum alloys during twin-roll casting. Mater. (Basel, Switz.) 13 (7), 1713. doi:10.3390/ma13071713
Liu, H., Ju, J., Yang, X., Yan, J., Song, D., Jiang, J., et al. (2017). A two-step dynamic recrystallization induced by LPSO phases and its impact on mechanical property of severe plastic deformation processed Mg97Y2Zn1 alloy. J. Alloys Compd. 704, 509–517. doi:10.1016/j.jallcom.2017.02.107
Liu, H., Xue, F., Bai, J., and Sun, Y. (2013). Effect of heat treatments on the microstructure and mechanical properties of an extruded Mg95.5Y3Zn1.5 alloy. Mater. Sci. Eng. a 585 (0), 261–267. doi:10.1016/j.msea.2013.07.025
Liu, X., Wu, Y., Liu, Z., Lu, C., Xie, H., and Li, J. (2018). Thermal and electrical conductivity of as-cast Mg-4Y-xZn alloys. Mater. Res. Express 5 (6), 066532. doi:10.1088/2053-1591/aac99b
Lockyer, S. A., Yun, M., Hunt, J. D., and Edmonds, D. V. (1996). Micro- and macrodefects in thin sheet twin-roll cast aluminum alloys. Mater. Charact. 37 (5), 301–310. doi:10.1016/S1044-5803(97)80019-8
Lu, F., Ma, A., Jiang, J., Yang, D., and Zhou, Q. (2012). Review on long-period stacking-ordered structures in Mg-Zn-RE alloys. Rare Met. 31 (3), 303–310. doi:10.1007/s12598-012-0510-y
Lu, R., Wang, J., Chen, Y., Qin, D., Yang, W., and Wu, Z. (2015). Effects of heat treatment on the morphology of long-period stacking ordered phase, the corresponding damping capacities and mechanical properties of Mg–Zn–Y alloys. J. Alloys Compd. 639, 541–546. doi:10.1016/j.jallcom.2015.03.208
Neh, K., Ullmann, M., and Kawalla, R. (2014). Twin-roll-casting and hot rolling of magnesium alloy WE43. Procedia Eng. 81 (81), 1553–1558. doi:10.1016/j.proeng.2014.10.189
Neh, K., Ullmann, M., and Kawalla, R. (2016). Substitution of rare earth elements in hot rolled magnesium alloys with improved mechanical properties. Mater. Sci. Forum 854, 57–64. doi:10.4028/www.scientific.net/MSF.854.57
Nie, J. F., Zhu, Y. M., and Morton, A. J. (2014). On the structure, transformation and deformation of long-period stacking ordered phases in Mg-Y-Zn alloys. Metallurgical Mater. Trans. a 45 (8), 3338–3348. doi:10.1007/s11661-014-2301-6
Qian, X., Dong, Z., Jiang, B., Lei, B., Yang, H., He, C., et al. (2022). Influence of alloying element segregation at grain boundary on the microstructure and mechanical properties of Mg-Zn alloy. Mater. & Des. 224, 111322. doi:10.1016/j.matdes.2022.111322
Saadati, M., Khosroshahi, R. A., Ebrahimi, G., and Jahazi, M. (2017). Formation of precipitates in parallel arrays on LPSO structures during hot deformation of GZ41K magnesium alloy. Mater. Charact. 131, 234–243. doi:10.1016/j.matchar.2017.07.007
Saal, J. E., and Wolverton, C. (2012). Thermodynamic stability of Mg–Y–Zn long-period stacking ordered structures. Scr. Mater. 67 (10), 798–801. doi:10.1016/j.scriptamat.2012.07.013
Sun, C., Liu, H., Xu, Z., Wu, Y., Yan, K., Ju, J., et al. (2024). Refining 18R-LPSO phase into sub-micron range by pre-kinking design and its prominent strengthening effect on Mg97Y2Zn1 alloy. J. Mater. Sci. & Technol. 176, 13–24. doi:10.1016/j.jmst.2023.07.051
Suzawa, K., Inoue, S., Nishimoto, S., Fuchigami, S., Yamasaki, M., Kawamura, Y., et al. (2019). High-strain-rate superplasticity and tensile behavior of fine-grained Mg97Zn1Y2 alloys fabricated by chip/ribbon-consolidation. Mater. Sci. Eng. A 764, 138179. doi:10.1016/j.msea.2019.138179
Ullmann, M., Kittner, K., Henseler, T., Krbetschek, C., Rafaja, D., Kawalla, R., et al. (2020). Dynamic recrystallization and texture evolution of Mg-6.8Y-2.5Zn-0.3Zr alloy during hot rolling. Procedia Manuf. 50, 809–816. doi:10.1016/j.promfg.2020.08.146
Ullmann, M., Kittner, K., and Prahl, U. (2021). Hot rolling of the twin-roll cast and homogenized Mg-6.8Y-2.5Zn (WZ73) magnesium alloy containing LPSO structures. Metals 11 (11), 1771. doi:10.3390/met11111771
Wang, B. S., Xiong, S., and Liu, Y. (2010). Tensile fracture of as-cast and hot rolled Mg-Zn-Y alloy with long-period stacking phase. Trans. Nonferrous Metals Soc. China 20 (Suppl. 2), s488–s492. doi:10.1016/S1003-6326(10)60524-9
Weiner, M., Schmidtchen, M., and Prahl, U. (2022). Extension of the Freiberg layer model by means of solidification for roll casting. Adv. Eng. Mater. 24 (8). doi:10.1002/adem.202101546
Wells, M. A., and Hadadzadeh, A. (2014). Twin roll casting (TRC) of magnesium alloys – opportunities and challenges. Mater. Sci. Forum 783-786, 527–533. doi:10.4028/www.scientific.net/MSF.783-786.527
Yang, J. Y., and Kim, W. J. (2019). Effect of I(Mg3YZn6)-W(Mg3Y2Zn3)- and LPSO(Mg12ZnY)-phases on tensile work-hardening and fracture behaviors of rolled Mg–Y–Zn alloys. J. Mater. Res. Technol. 8 (2), 2316–2325. doi:10.1016/j.jmrt.2019.04.016
Yun, M., Lokyer, S., and Hunt, J. D. (2000). Twin roll casting of aluminium alloys. Mater. Sci. Eng. A 280 (1), 116–123. doi:10.1016/S0921-5093(99)00676-0
Zheng, C., Chen, S.-F., Wang, R.-X., Zhang, S.-H., and Cheng, M. (2021). Effect of hydrostatic pressure on LPSO kinking and microstructure evolution of Mg–11Gd–4Y–2Zn–0.5Zr alloy. Acta Metall. Sin. Engl. Lett. 34 (2), 248–264. doi:10.1007/s40195-020-01120-1
Zhu, J., Chen, X. H., Wang, L., Wang, W. Y., Liu, Z. K., Liu, J. X., et al. (2017). High strength Mg-Zn-Y alloys reinforced synergistically by Mg12ZnY phase and Mg3Zn3Y2 particle. J. Alloys Compd. 703, 508–516. doi:10.1016/j.jallcom.2017.02.012
Keywords: twin-roll casting (TRC), magnesium alloy, LPSO phases, microstructure, texture
Citation: Ueberschär F, Ullmann M and Prahl U (2025) Influence of varying twin-roll casting conditions on the microstructure and texture development and mechanical properties of a Mg-6.8Y-2.5Zn-0.4Zr alloy. Front. Met. Alloy. 4:1635322. doi: 10.3389/ftmal.2025.1635322
Received: 26 May 2025; Accepted: 20 June 2025;
Published: 04 July 2025.
Edited by:
Andrea Tridello, Polytechnic University of Turin, ItalyReviewed by:
Petra Maier, University of Applied Sciences Stralsund, GermanyXiaojie Zhou, Changsha University of Science and Technology, China
Copyright © 2025 Ueberschär, Ullmann and Prahl. This is an open-access article distributed under the terms of the Creative Commons Attribution License (CC BY). The use, distribution or reproduction in other forums is permitted, provided the original author(s) and the copyright owner(s) are credited and that the original publication in this journal is cited, in accordance with accepted academic practice. No use, distribution or reproduction is permitted which does not comply with these terms.
*Correspondence: Franziska Ueberschär, ZnJhbnppc2thLnVlYmVyc2NoYWVyQGltZi50dS1mcmVpYmVyZy5kZQ==