- 1Ifremer, RDT, Plouzané, France
- 2Ifremer, ODE, Plouzané, France
- 3Mercator Ocean International, Ramonville-Saint-Agne, France
- 4Laboratoire Interdisciplinaire des Environnements Continentaux, CNRS, Université de Lorraine, Metz, France
- 5Laboratoire d’Océanographie de Villefranche, CNRS, Sorbonne Université, Villefranche-sur-Mer, France
- 6NKE Instrumentation, Hennebont, France
- 7Takuvik Joint International Laboratory, Laval University, Quebec City, QC, Canada
- 8CNRS (France), Département de Biologie et Québec-Océan, Université Laval, Quebec City, QC, Canada
- 9IUEM-UMS 3113, Université de Bretagne Occidentale, Plouzané, France
- 10CNRS, Ifremer, IRD, Laboratoire d’Océanographie Physique et Spatiale, Univ Brest, Plouzané, France
- 11Recherche et développement pour la défense Canada – Centre de recherches de l’Atlantique, Dartmouth, NS, Canada
- 12Service Hydrographique et Océanographique de la Marine, Brest, France
The international array of profiling floats known as Argo is a major component of the global ocean- and climate-observing system. In 2010, the NAOS (Novel Argo Observing System) project was selected as part of France’s Equipex “Investissement d’Avenir” program. The objectives of NAOS were to consolidate the French contribution to the Argo core mission (global temperature and salinity measurements down to 2,000 m) as well as to develop the future generation of French Argo profiling floats and prepare the next phase of the Argo program with an extension to the deep ocean (Deep-Argo), biogeochemistry (BGC-Argo) and polar seas. This paper summarizes the main technological advances and at-sea validations carried out as part of NAOS: development of a deep (4,000 m) float, a new BGC float for Research & Development (R&D) applications, and a BGC float for deployments in Arctic areas, assessment of a new density and Absolute Salinity optical sensor, improvement of the reliability of the standard Argo float, and upgraded satellite-transmission performance. French profiling floats developed in this way are now operational and among the most deployed worldwide, and the density sensor is the most promising of its kind for profiling floats applications.
Introduction
Argo is an international array of about 4,000 profiling floats that measure temperature and salinity throughout the global oceans, down to 2,000 m (Riser et al., 2016; Roemmich et al., 2019). As the first-ever global in situ ocean-observing network in the history of oceanography, it provides an essential complement to satellite systems, enabling scientists to understand the ocean’s role in the Earth’s climate and to predict evolutions of the ocean, weather and climate.
France has been playing an important role in the international Argo program since its inception in the late 90s. This country has contributed slightly less than 10% of the international effort by deploying about 65 floats per year while also making a major contribution to the Argo data-management system. Through a public/private partnership between Ifremer and the SME nke instrumentation, France is a European leader in the development of Argo instrumentation (Provor and Arvor floats).
In 2010, the 10-year NAOS (Novel Argo Observing System) project was selected as part of the French Equipex “Investissement d’Avenir” program. The objectives of NAOS were to consolidate the French contribution to the Argo core mission (global temperature and salinity measurements down to 2,000 m) as well as to develop the future generation of French Argo profiling floats and prepare the next phase of the Argo program, namely a global full-depth multidisciplinary array that includes an extension to the deep ocean (Deep-Argo), biogeochemistry (BGC-Argo), and polar seas (Roemmich et al., 2019; Claustre et al., 2020). NAOS was established through a partnership between Ifremer, UPMC, CNRS, IUEM, SHOM, nke instrumentation, and CLS.
Float-technology improvements pursued by NAOS aimed at: developing a deep (4,000 m) float, a new BGC float for R&D applications as well as a BGC float for deployments in Arctic areas; assessing a new density and Absolute Salinity optical sensor; improving the reliability of the standard Argo float; and upgrading satellite-transmission performance (Argos, Iridium). The project benefitted from and built on a European Research Council (ERC) Advanced Grant (RemOcean) awarded to LOV laboratory (Laboratoire d’Océanographie de Villefranche, UPMC/CNRS) for development of a biogeochemical component for Argo.
As part of the NAOS project, new-generation floats were deployed in the course of three scientific experiments: biogeochemical floats in the Mediterranean Sea, biogeochemical floats in the Arctic Ocean, and deep floats with oxygen sensors in the North Atlantic. These pilot areas were chosen for their particular importance for European research, namely their potential to shed light on the physical and biological functioning of the Mediterranean, on water formation and transformation in the North Atlantic, and on the coupling between physics and biology in the Arctic.
This paper reviews the technological developments carried out as part of NAOS, including in situ validation. A companion paper summarizes the contribution of NAOS to the Core-Argo array and details results from the three scientific experiments (Le Traon et al., 2020).
This paper is divided into six separated sections which detail technological developments and applications on the various components of the Argo program, respectively: (i) the Deep-Arvor; (ii) the new biogeochemical Provor CTS5; (iii) under-ice applications; (iv) the NOSS Absolute Salinity and density sensor; (v) improvements in the performance of the Arvor float; and (vi) an evaluation of satellite-communications systems on profiling floats.
Deep-Arvor Profiling Float
While the Argo program has revolutionized the monitoring of the upper ocean, the deep ocean remains largely under-sampled. Yet the deep ocean calls for scrutiny as a key component of the climate system, given its contribution to the global heat budget and sea-level rise, to the storage of heat and anthropogenic carbon, and to variations in the meridional overturning circulation. To fill this gap, the OceanObs’09 conference gathering the international ocean-observing community advocated the extension of Argo measurements below 2,000 m (Freeland et al., 2010; Garzoli et al., 2010). The Deep-Arvor float was developed to answer this need, as it allows sampling of the ocean down to 4,000 m depth, which represents 88% of the ocean’s volume (Amante and Eakins, 2009). When this development began in 2011, no other deep profiling float was designed.
Profiling-Float Conception
Hardware Design
The design of the Deep-Arvor profiling float (Figure 1, left) is very similar to that of the Arvor float deployed by the Core-Argo program (2,000 m). However, some subassemblies had to be reinforced, as detailed in Le Reste et al. (2016), which led to an instrument different from the other deep floats used today in the Deep-Argo program.
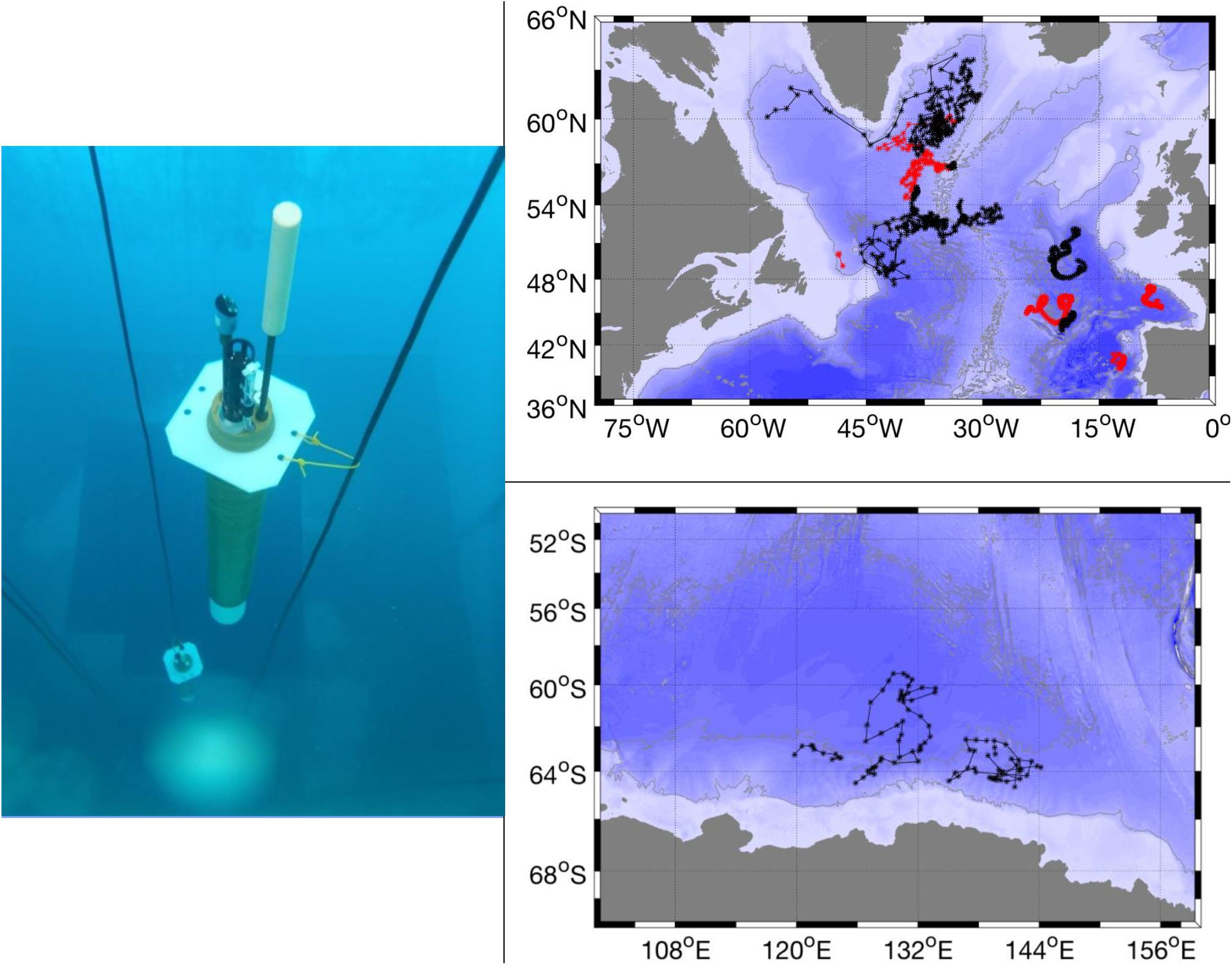
Figure 1. Left: the Deep-Arvor profiling float during tests in the seawater pool at Ifremer, in May 2019 (courtesy of Noé Poffa/Ifremer). Right: trajectories of the Deep-Arvor floats deployed in the subpolar gyre of the North-Atlantic Ocean (upper panel), and in the Southern Ocean (lower panel). Black points: NAOS floats. Red points: floats from complementary projects or prototypes.
To strike a balance between pressure resistance, compressibility and expected weight, the enclosure tube is made of filament-wound carbon fiber, and then sealed with a polyurethane layer. However, the upper and lower end caps are still made of anodized aluminum, for its high strength and low cost.
The hydraulic block is based on the same technology as the Core-Argo Arvor float, with reinforced components and control signals that have been optimized in order to minimize the float’s energy consumption.
The Deep-Arvor is supplied by a block of 32 LSH20 lithium batteries. As the amount of energy available is more than 4,200 kJ, the float can perform up to 150 cycles in continuous pumping mode, and 200 cycles in spot sampling mode.
The Deep-Arvor is currently equipped with a reinforced Seabird SBE41CP probe, which meets specifications down to 4,000 m depth. Other probes (RBR or Seabird SBE61) are currently being tested as part of the European Euro-Argo RISE project (see Section “The Deep-Arvor: A Deep Profiling Float With a High Payload Capability”).
Features
The typical profile of a Deep-Arvor remains similar to that of its predecessors, and always consists of the following phases (in order): (i) descent to a parking depth; (ii) drifting at that depth for several days; (iii) descent to the programmed profile depth; (iv) ascent to the surface; and (v) transmission of its scientific and technical data by satellite (Figure 2). The purpose of maintaining this strategy is to allow profile data to be: (i) acquired during the float’s ascent from the very bottom to the surface; and (ii) immediately transmitted to the data center, in accordance with the Argo network specifications. The Deep-Arvor is furthermore equipped with the Ice-Sensing Algorithm (ISA), which analyzes the measured temperature in real time to estimate the probability of ice at the surface. In the event of ice detection, the data of the current cycle are saved for later transmission, and the transmission phase is then skipped; in this case, the float interrupts its ascent, and directly starts the descent phase of a new cycle. The Deep-Arvor mission is fully configurable, thus permitting adjustments for elements including pressure, schedule, cycle periods, and the number and distribution of samples from a water column. In total, the Deep-Arvor allows the modification of 18 mission parameters, 37 expert parameters and 15 ISA parameters (refer to Supplementary Materials). As is the case for a Core-Argo profiling float, a Deep-Arvor can be programmed onshore before its deployment, or while the float is at sea by sending remote controls via the Iridium link.
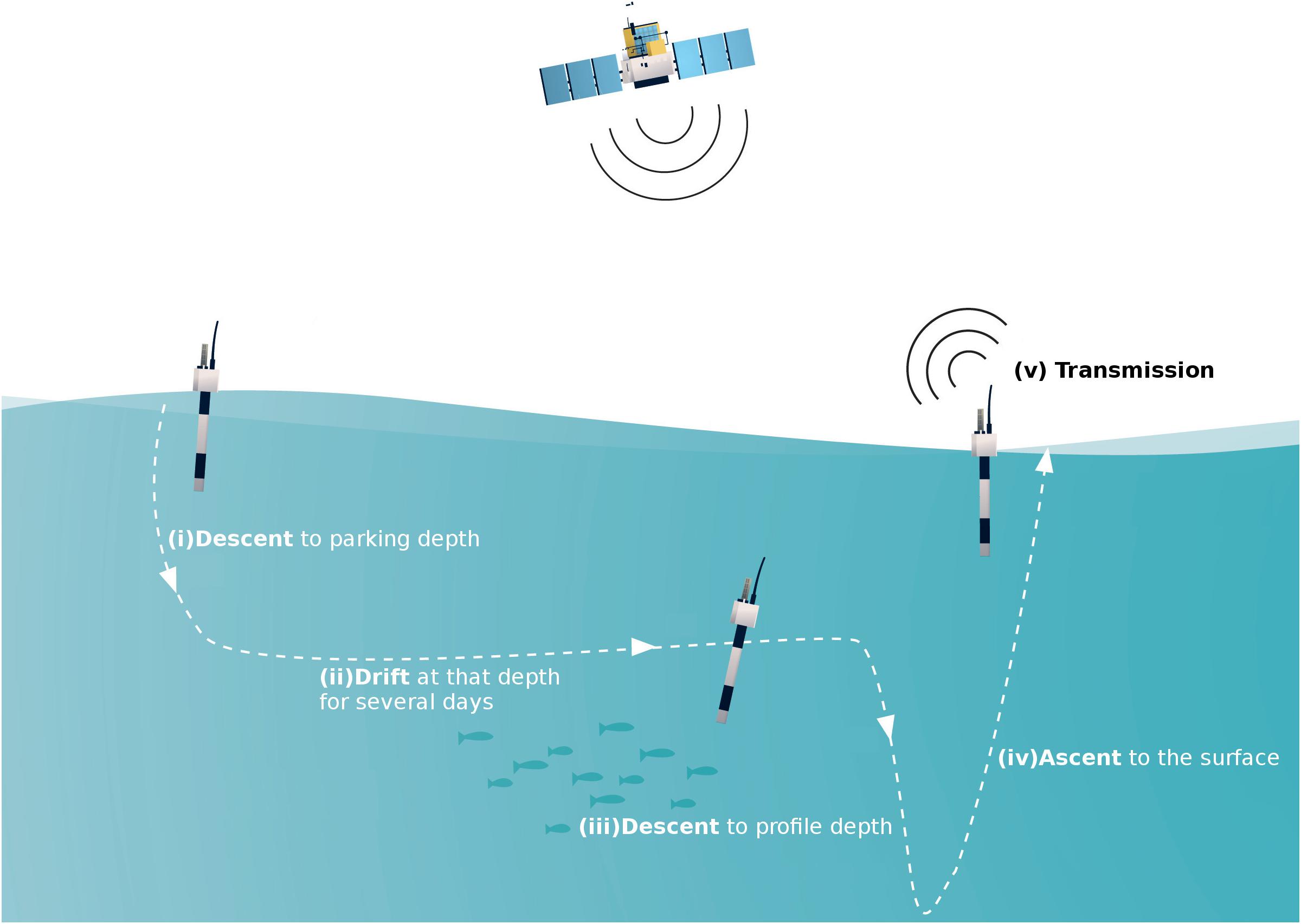
Figure 2. Typical Argo & Deep-Argo cycle (courtesy of Euro-Argo). A cycle is made of five phases: (i) the descent to the drifting depth, (ii) the drift, (iii) the descent to the profiling depth, (iv) the ascent (also named the profile), and (v) the transmission.
The hydraulic block allows precise control of the profiling float’s displacement speed in the water column. In this way, the descent rate is controlled at 30 mm/s, and the ascent rate at 90 mm/s, thereby obtaining a consistent acquisition strategy over the entire profile, and better data quality.
Two acquisition strategies are currently available. The first, called “continuous pumping,” relies on permanent renewal of the water sample over the entire profile, thanks to a pump that creates circulation within the CTD. The second, called “spot sampling,” consists of flushing the measurement cell and taking a water sample at certain predefined pressures to measure temperature and salinity. Both operating modes are available on the Deep-Arvor, allowing scientific teams to proceed according to their usual measurement method. Moreover, the Deep-Arvor allows the acquisition of 2,000 samples of pressure, temperature, salinity and dissolved oxygen (optional sensor), with the possibility of configuring the sampling characteristics differently depending on depth.
Due to its operational depth of 4,000 m, the Deep-Arvor is likely to ground more often than floats in the Core-Argo network. Its grounding strategy has therefore been strengthened, and now provides a range of solutions: (i) if the float grounds during its descent to, or while drifting at, the parking depth, it can either stay at the bottom, or shift by a pre-programmed distance and then drift for the rest of the cycle at this new depth; (ii) if the float grounds during its descent to the profile depth, it can either stay at the bottom until the programmed ascent time or start an immediate ascent. In the latter case, the profile is completed slightly earlier than expected. In all cases, the waiting mode is not recommended, as the instrument can be subject to bottom friction in the presence of currents (see next section). As the layer near the bottom is very interesting from a scientific point of view, it is heavily sampled during the first meters of the ascent.
Feedback From Deployments at Sea
Forty Deep-Arvor units were produced and deployed by the end of 2019. Sixteen of these were equipped with an oxygen optode and deployed as part of the NAOS project. Fourteen of the NAOS floats were deployed in the subpolar gyre of the North-Atlantic Ocean during the RREX and OVIDE/BOCATS surveys in 2015, 2016, 2017, and 2018 to implement a pilot array there (Figure 1, upper right). Two NAOS floats were deployed in the Southern Ocean as part of the CAPRICORN survey to contribute to a pilot array there and to evaluate Deep-Arvor float performances in ice-covered regions (Figure 1, lower right). Scientific results and sensor performances based on those deployments are presented in Le Traon et al. (2020). Six remaining NAOS floats will be deployed in the subpolar gyre of the North-Atlantic Ocean in 2020 and 2021.
Some of the first production units revealed two technical defects that have now been solved. The first was a software bug impacting grounding management, namely causing erratic management of the valve of the hydraulic system. Once corrected for this bug, the software was qualified in laboratory, then at sea. The second issue concerned the reproducibility of the performance of the hydraulic pump. This issue was addressed in two stages: (i) it was first circumvented by changing the value of the float’s internal vacuum in order to move away from pump de-priming conditions, thus allowing deployment continuity in 2018 – but getting around the problem this way was not satisfactory as a long-term solution; and (ii) it was then solved by improving the design of the hydraulic circuit, and by strengthening the hydraulic block’s production and integration procedures. The proper behavior of hydraulic pumps on 17 Deep-Arvor floats was then verified in a hyperbaric chamber in 2019.
On average, the Deep-Arvor floats affected by these two defects performed 47 cycles whereas 150 cycles were initially expected. Five NAOS Deep-Arvor floats, which were deployed in 2018 after benefitting from the internal vacuum change, are still active. Having achieved 81 cycles on average in September 2020, these floats have already exceeded the mean number of cycles realized by the previous batch.
The present-day performance of Deep-Arvor floats can be illustrated by the Deep-Arvor WMO6901757, reflecting the proper functioning of the Deep-Arvor. Its Deep-Argo cycles took place as programmed, at depths between 3,500 and 4,000 m, depending on bathymetry. The vector was controlled in a repeatable manner, with a number of hydraulic actions conforming to expectations. The 143 cycles completed by this float is close to the theoretical lifetime of 150 CTD profiles in continuous pumping mode, if we take into account the groundings that may have caused overconsumption during take-off for certain cycles (12% of the cycles), and also the performance of 16 oxygen profiles (entailing overconsumption by 15% compared to a simple CTD cycle).
In addition, several Deep-Arvor floats (for example WMO3902129, WMO6902813, and WMO6902814) have spent one or two winters under ice before reappearing in the spring, at which point the data profiles stored in the float’s internal memory were unstacked and transmitted. Their precise trajectories cannot be determined due to the lack of a positioning system under ice, but require extrapolation. The correlation between activation of the embedded ice-detection algorithm on these floats and the ice maps provided by the Copernicus Marine Environment Monitoring Service is very strong, confirming the accuracy of Deep-Arvor ice detection.
The Deep-Arvor: A Deep Profiling Float With a High Payload Capability
One advantage of the technology contained within the Deep-Arvor housing, namely a tube and not a sphere, is its capacity to embed additional sensors, in the same vein as the Provor BGC profiling floats (refer to Sections “New Biogeochemical (BGC) Float for R&D Application” and “BGC Profiling Floats for Under-Ice Application” for example). Indeed, the Deep-Arvor has demonstrated its flexibility via two specific developments where external sensors have been embedded.
The first development is the Wapiti Deep-Arvor profiling float, on which a Nortek Signature 500 kHz ADCP is embedded. The latter operates in altimetry and bottom-tracking modes in order: (i) to maintain the float at a controlled distance from the bottom (typically 80 ± 40 m) to follow deep water masses; and (ii) to measure the speed and direction of bottom scrolling, thus enabling reconstruction of the instrument’s path between two profiles. As the ADCP is particularly energy-consuming, an external battery pack was added. The ADCP and battery-pack assembly is fixed on a nacelle attached to the base of the Deep-Arvor (Figure 3, left), compensated by the addition of buoyancy foam at the head of the Deep-Arvor. Four Wapiti Deep-Arvor floats were deployed in 2017 and 2019 in the Weddell Sea, and have proven the value of their application.
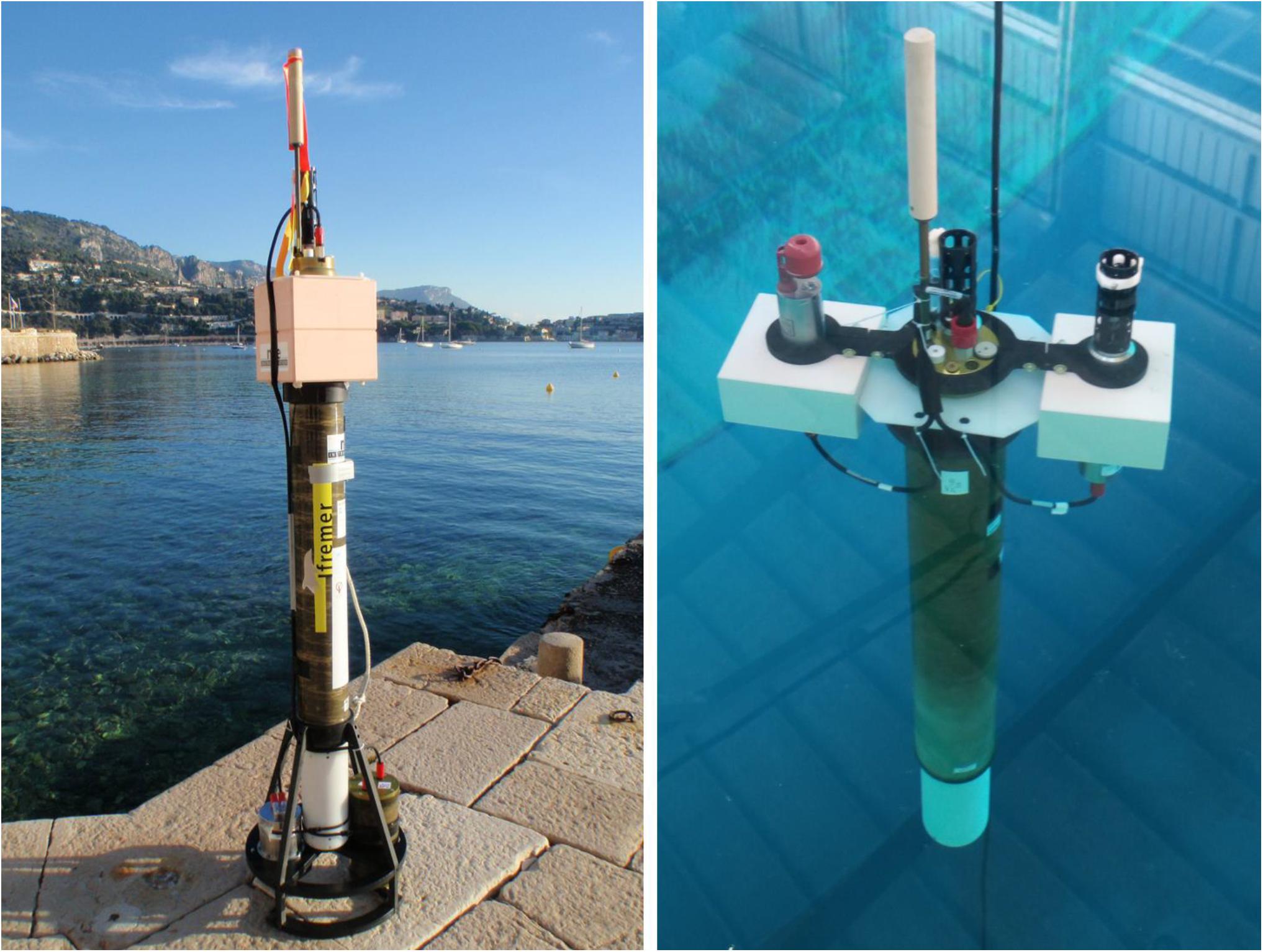
Figure 3. Left: Wapiti Deep-Arvor equipped with an ADCP operating in altimetry and bottom-tracking modes. Right: 3-headed Deep-Arvor platform designed to compare the CTD performance of SBE41CP, SBE61CP and RBRconcerto3 in situ. Courtesy of Ifremer.
The second development is the 3-headed Deep-Arvor, equipped with the reinforced SBE41CP sensor and embedded with two additional CTDs: the RBRconcerto3 and the SBE61CP (Figure 3, right). This profiling float was designed as an inter-comparison platform to evaluate the three CTDs at sea. The CTDs’ profile samples are acquired every twenty centimeters, and the sensors are synchronized on the SBE41CP. The two additional sensors are mounted alongside the profiling float. The different sensors of the three CTDs are kept in correct and controlled position with the help of specific supports. Two syntactic foam blocks are used to compensate for the extra weight of the additional CTDs and to stabilize the float. The internal electronic board manages the acquisition, synchronization, storage and transmission of the samples. The 3-headed Deep-Arvor was successfully tested at sea in the Mediterranean Sea in September 2018 and May 2019, during two cruises dedicated to technological qualifications. These deployments lasted only a few days and were limited to 2000 m depth. They confirmed the instrument’s overall functional aspects and acquisition performance, but did not provide sufficient in situ data to draw any conclusion on sensors performances. A long-term deployment is planned for December 2020.
Conclusions and Perspectives
In order to enhance knowledge on the role of the deep ocean in the climate system, Ifremer has developed a deep profiling float: the Deep-Arvor, designed as an extension of the Core-Argo profiling floats, with reinforced main subsets. Efforts focused on the Deep-Arvor’s housing – a cylinder made of high-performance composite material in order to obtain a lightweight, resistant and high-load-bearing float – and its high-pressure hydraulic system. The Deep-Arvor, now having proven its value at sea, is industrialized and commercialized by nke instrumentation.
The Deep-Argo Implementation Workshop, held in Hobart from May 13 to 15, 2019, was instrumental in defining the specifications for a Deep Argo network. The Workshop highlighted the need for a network of 1,200 deep profiling floats (Zilberman et al., 2019) to perform Argo-like cycles every 10 days for 4 years, sampling the ocean over the entire water column. The Deep-Arvor is well positioned to contribute to this challenge. First, given its design, the Deep-Arvor float is competitively priced (about twice the commercial price of a standard Argo float). This is a major asset for developing a cost-effective global Deep-Argo network based on a mix of 4,000 and 6,000 m floats. The Deep-Arvor float also offers the advantages of controllable ascent/descent displacement speed over the entire water column, and execution of the profile during the ascent, consequently allowing transmission of its data in near real time. This is essential for constraining ocean and seasonal-to-decadal climate forecasting systems (e.g., MacLachlan et al., 2015; Le Traon et al., 2019).
To increase the number of cycles achievable by the Deep-Arvor, and thus reduce the unit cost of a measurement profile, Ifremer has initiated several studies, namely to optimize the compressibility of the composite tube, to develop a low-power-consumption hydraulic system, and to explore new battery technologies. Finally, to diversify the range of sensors deployed within Argo, Ifremer is evaluating the RBRargo3 CTD| deep6k by RBR, in addition to the Seabird offer.
New Biogeochemical (BGC) Float for R&D Application
The success of the Argo physical and biogeochemical programs has demonstrated the efficiency of Argo floats in carrying various kinds of sensors for global monitoring (IOCCG, 2011; Biogeochemical-Argo Planning Group, 2016). At the same time, many sensors have evolved to smaller sizes and lower power consumption, allowing them to be installed on profiling floats. However, Argo floats, being dedicated to operational measurements, are not well suited for the purposes of laboratories exploring new applications. Consequently, a new float was developed to facilitate the testing of new sensors and onboard data processing. To our knowledge, this represents an original approach at the international level.
Technical Characteristics of the New Float
The new float, called Provor CTS5-Payload, and listed as Provor-IV in the JCOMMOPS database, is based on the same mechanics as the standard Provor floats manufactured by nke instrumentation, but additionally fitted with two new electronic boards (Figure 4). The first board, named APMT (standing for “Automate Profileur Multi-Tâches,” French for “multitasking profiling robot”), was developed by nke instrumentation to manage the float’s core functionalities, including the CTD and overall float safety. This board provides power and communicates via RS232 with a payload electronic board named Payload, developed according to LOV’s specifications and dedicated to new sensors and data processing that laboratories can implement autonomously. This dual-board architecture is ideal for float safety as well as offering flexibility to cater to new developments.
The New Provor CTS5
The new CTS5 profiling float benefits from Provor’s advantages of autoballasting, high-weight-carrying and high-energy capacity, while also offering new capabilities thanks to the APMT board. The float navigation allows for up to 10 different profiling patterns executed in a continuous loop, for which parameters can be defined according to Argo standards (parking and profile depth, time at surface, etc.). All these parameters can be modified remotely thanks to two mechanisms: (i) the standard telemetry link provided by the Iridium network; or (ii) a script file that contains the modifications to be made to the float mission at different dates. The latter function is particularly useful for modifying the mission parameters of ice floats for which it is not possible to use telemetry. The CTS5 float implements an Iridium RUDICS (Router-Based Unrestricted Digital Internetworking Connectivity Solutions) telemetry protocol that allows very high-speed satellite communication at an average of 12 kBytes/min.
Finally, through the NAOS project, the APMT board implemented a dedicated protocol to communicate with the Payload acquisition board. This protocol allows the receiving of data from and the sending of parametrization to the acquisition board. It also allows the APMT navigation board to receive basic navigation commands (called “feedback”), like “start,” “stop,” or “abort” a profile, from the acquisition board to adapt navigation to the data acquired in real time. In the NAOS project, this feedback capability was used to stop the float according to ice-avoidance algorithms implemented on the acquisition board (see Section “BGC Profiling Floats for Under-Ice Application”).
The Payload Acquisition Board
The Payload acquisition board was developed according to LOV’s specifications in the framework of the NAOS, ProVal, and remOcean projects. The board implements eight RS232 serial ports, each associated with a power switch, so that eight sensors can be controlled independently. The embedded software enables complex acquisition schemes defined with tunable XML parameter files, while onboard resources permit advanced data processing if required. Sampling can be defined independently for each sensor and at any depth for each phase of the navigation (i.e., descent, parking, ascent, and surface). The acquisition board implements several standard embedded processing methods, such as calculation by depth range of the mean, median or extreme values.
The addition of new sensors was facilitated by the software design. It mainly impacts the management of sensor power supplies and the decoding of data frames. On the other hand, standard onboard data processing up to data transmission is common to all sensors and does not need to be modified. This capacity to easily accommodate new sensors, which was the main objective of this development, has made it possible to test new applications, the main examples of which are summarized hereafter.
Test Facilities
Float safety and reliability are always matters of major concern. Following developments, these aspects require extensive testing of the new functionalities. The tests are firstly carried out in the laboratory on a simulator bench, and then at sea.
A float simulation bench, using the actual electronic boards (APMT and Payload) and therefore the actual embedded software, was provided by nke instrumentation. In this simulator, the two electronic boards are connected together as in an actual float but linked to a fake environment simulated by a computer. The CTD data, in particular pressure data, are provided by the computer that spies on the APMT board’s hydraulic actions (pump and solenoid valve) in order to supply a simulated depth based on hydrodynamic modeling of the float. The CTD profiles, and therefore the density profile, can be defined by the user to test the float’s navigation theoretically, through a density barrier for example. A real GPS is connected to the simulator while the Iridium modem, including the Iridium network, is simulated by the computer, allowing data reception or the issuing of commands to the simulated float. For the Payload acquisition board, it is possible to connect real sensors but with random data (i.e., the data measured in air by the sensor) or to connect simulated sensors with data profiles synchronized with the simulated depth.
This float simulator has been an essential element for the successful implementation of our developments. It has enabled safe and rapid identification of the vast majority of dysfunctions usually encountered in this kind of development. The simulator has also allowed us to study various safety mechanisms such as the management of grounding, as well as to validate the float’s reaction to certain failure scenarios, thus contributing to increasing the safety of prototypes.
Even after extensive simulator tests, final trials at sea are still required before a prototype can be deployed operationally. For this type of test, the LOV site offers particularly favorable conditions. Indeed, depths of more than 2,000 m, as required to test the floats at their maximum depth, are easily accessible at about 10 nautical miles from the laboratory. In addition, the Ligurian current, which runs from east to west along the coast, provides good predictability of the floats’ trajectories in anticipation of their recovery.
Examples of Uses
The CTS5-Payload float has been developed by the LOV to autonomously test new applications and sensors while benefiting from technological flexibility and budget savings. This approach has enabled, for example, the development of the Profiler for Validation (ProVal float). This float was designed to make accurate radiometric measurements to enable the validation and possibly calibration of “ocean-color” satellite sensors such as the Ocean and Land Color Imager (OLCI) onboard the satellites Sentinel-3A and 3B Copernicus. The ProVal is equipped with two arms, each carrying a double radiometer that measures downward irradiance and upwelling radiance at seven wavelengths. It is also equipped with a compass and a tilt sensor to determine the orientation of the sensors in relation to the vertical and sun position. To date, nearly 700 profiles have been acquired with this type of platform in the Mediterranean Sea and the Southern Ocean (Leymarie et al., 2018).
The CTS5-Payload has also been used to test new sensors, such as the DuraFET pH sensor (Johnson et al., 2016) or the UVP6 particle sensor (Picheral et al., 2010), both now commercially available on the Provor float. The main use of this float, however, is its polar application which will be described in Section “BGC Profiling Floats for Under-Ice Application.”
Conclusion and Perspectives
The new Provor CTS5-Payload profiling float has proven very useful for the exploration of new applications. Several applications tested on this platform, like the ProVal or the Pro-Ice floats (see Section “BGC Profiling Floats for Under-Ice Application”), but also the SeaBird DuraFET pH sensor or the UVP6 particle sensor (Hydroptic), are now sufficiently mature to be used operationally. Test phases have been precious for determining if an application or sensor is worthwhile and mature enough for wider global integration into the BGC-Argo fleet. They also offer the means to determine the optimal approach for managing a sensor in terms of data quality and power consumption. As the use of a dedicated electronic board, especially one produced by a third-party company, does not facilitate the transition from testing phase to operational use, a new acquisition board, called USEA, was developed in 2018 by nke instrumentation in partnership with LOV, to replace the Payload board. This development should greatly facilitate the industrialization of new applications. Finally, the addition of new applications on floats will also generate more data to be transmitted whereas the potential for improving telemetry capacity remains limited for the next decade (see Section “Satellite Communications”). The availability of a powerful new acquisition board will thus be an important factor in testing new embedded algorithms for onboard data processing and compression.
BGC Profiling Floats for Under-Ice Application
Polar regions are experiencing major changes due to climate change, and consequently require greater observational efforts. However, they are complex areas in which to implement technologies (Smith et al., 2019). We present here an adaptation of the Provor CTS5-Payload, described in Section “New Biogeochemical (BGC) Float for R&D Application,” to polar areas. With its large reserve of buoyancy, the Provor is particularly well suited to polar areas with a high-density gradient. The new electronics of the CTS5 are also particularly effective for under-ice navigation thanks to their data-storage capabilities and fast telemetry. These technological developments, tested in deployments carried out in Baffin Bay (Arctic Ocean, West Greenland) as part of NAOS, are discussed below. To our knowledge, there hasn’t been such types of experiments in Baffin Bay so far.
Mechanical Adaptation and Ballasting
Mechanically, the Provor CTS5-Payload “Pro-Ice” is based on the conventional Provor BGC. It allows carrying of the same types of sensors as those used for the Argo-BGC program (Bittig et al., 2019). However, the profiling float itself underwent a number of mechanical adaptations. A cylindrical cage was added around the antenna, CTD and optode to protect the upper part of the float in the event of an impact with ice. This cage, however, creates new hanging points and increases power consumption due to the additional volume required for the emergence. An upward-pointing acoustic altimeter (PS-A916, Teledyne) was also added to detect ice (see Figure 5, right). Finally, neutral buoyancy was adjusted by adding syntactic foam to achieve navigation capability through a wide range of water densities (from 1000 to 1038 kg/m3). Two series of field trials were conducted in Canada in order to verify the equipment’s behavior in polar conditions (see Supplementary Materials for details).
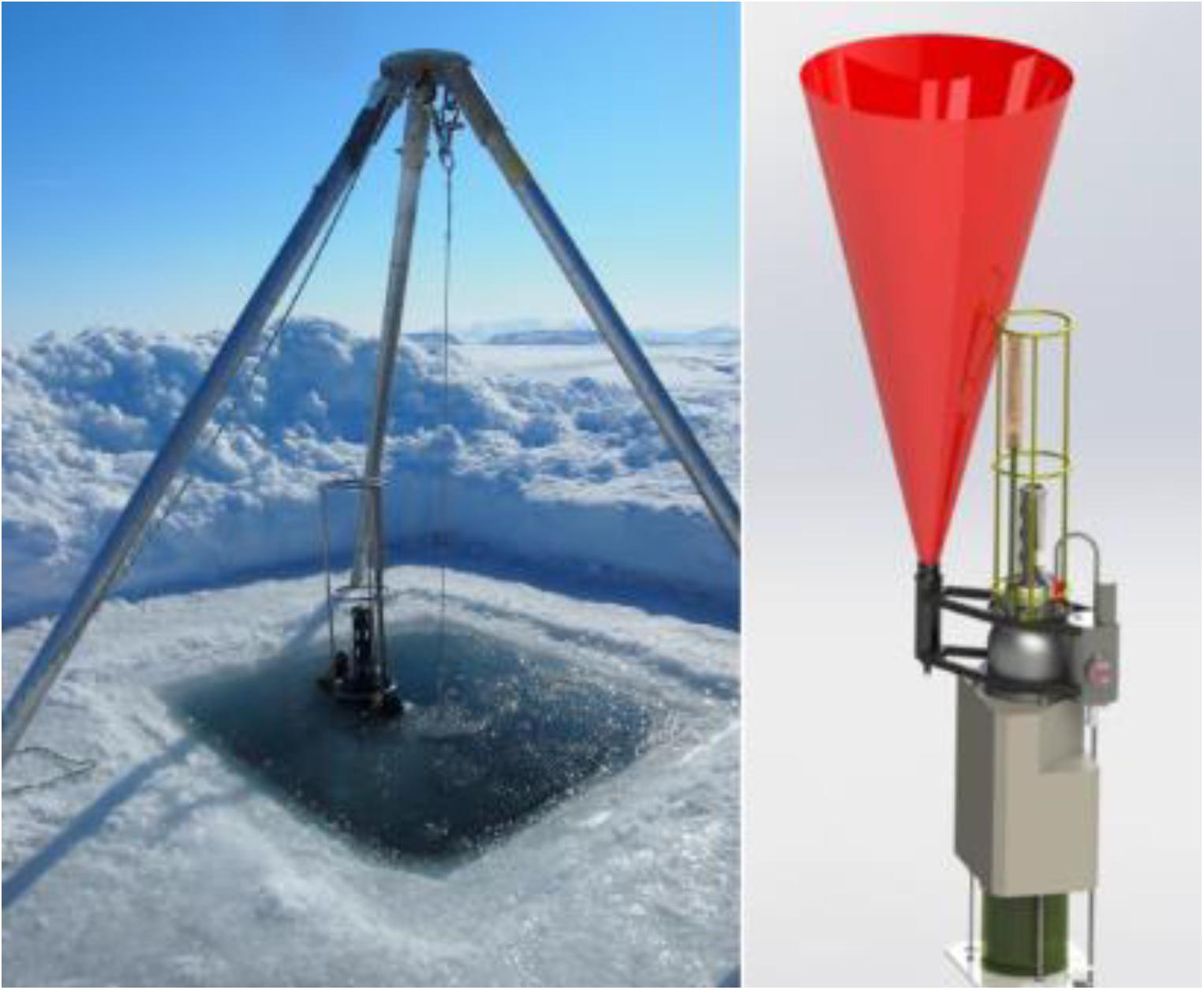
Figure 5. Left: Field trial at the Green Edge ice camp (courtesy of C. Marec). Right: Pro-Ice float design with antenna cage and upward-looking altimeter (PSA-916, acoustic beam in red).
Mission Adaptation
The main modification incorporated into the Provor CTS5-Payload float to accommodate polar conditions is the addition of different mechanisms to avoid, as much as possible, contact between the float and ice. In the event of contact, the float may remain attached to the ice, or else radically lose buoyancy in order to free itself from the ice, causing it to sink faster than tolerable. The float may also be crushed by sea ice.
As described in Section “Technical Characteristics of the New Float,” the APMT navigation board has several mechanisms that are particularly suitable for under-ice navigation. The option of script-based commands allows the parameterization of the under-ice float to be modified in the absence of communication while the protocol between boards allows the Payload acquisition board to send “stop” commands, guided by ice-detection methods (described hereafter), to the navigation board. The latter can accept the stop command or not according to a risk parameter offering 5 options ranging from no stop to the delay of surfacing by a maximum of 3, 7, 30, and 400 days. If the stop request is accepted, then the float will initiate a hydraulic braking action (see Supplementary Materials for details).
Two mechanisms have also been added to detect collisions with ice during ascent or surface snagging during descent. These mechanisms limit hydraulic transfers when the float is stuck and offer different strategies. For example, in the event of a collision with an object at the surface, detected by a lack of pressure variation despite hydraulic actions, the profiling float can start a new cycle or test a new ascent after a short descent.
Finally, it is possible to reduce the float speed in the last 100 m to facilitate braking in the event of ice detection. This option was not used during the NAOS deployments in Baffin Bay because it entails higher energy consumption for sensors and possibly greater float drift.
The flexibility of the CTS5-Payload float (see Section “New Biogeochemical (BGC) Float for R&D Application”) has made it possible to test three different ice-avoidance mechanisms, detailed below.
Ice-Sensing Algorithm and Adaptation for Baffin Bay
The ISA is currently the main technique implemented on Argo floats to avoid sea ice. First used in the Antarctic Ocean (Klatt et al., 2007), the ISA compares the median temperature near the surface with a threshold temperature. In the original algorithm, the median temperature was estimated at between 50 and 20 dbars and compared to the threshold –1.79°C corresponding to the local freezing temperature.
The water masses in Baffin Bay are nevertheless very different from those in the Antarctic with larger freshwater inlets (Curry et al., 2014). These characteristics led us to consider, from the outset, that the ISA setting should be adapted to Baffin Bay. For this analysis, 1,396 CTD profiles from Pro-Ice floats deployed in Baffin Bay were used (see section “Supplementary Materials”). These profiles were associated with a Sea Ice Concentration (SIC) estimated from the Advanced Microwave Scanning Radiometer 2 (AMSR2) with a spatial resolution of 3.125 km (Beitsch et al., 2014). For each float observation, the spatially closest SIC pixel was extracted. A secure SIC threshold of 10% was used to decide if the area was icy with a request for the ISA to be positive. For each CTD profile, the median temperature was processed for two depth ranges: the historical one between 50 and 20 dbars and a new one between 30 and 10 dbars. Then, four probabilities were determined depending on the ISA threshold: no ice (SIC < 10%) with a negative ISA, no ice with a positive ISA, ice (SIC > 10%) with a positive ISA, and finally ice with a negative ISA. These probabilities are shown on Figure 6. Optimal ISA parametrization will minimize the two wrong results: ice with a negative ISA and no ice with a positive ISA.
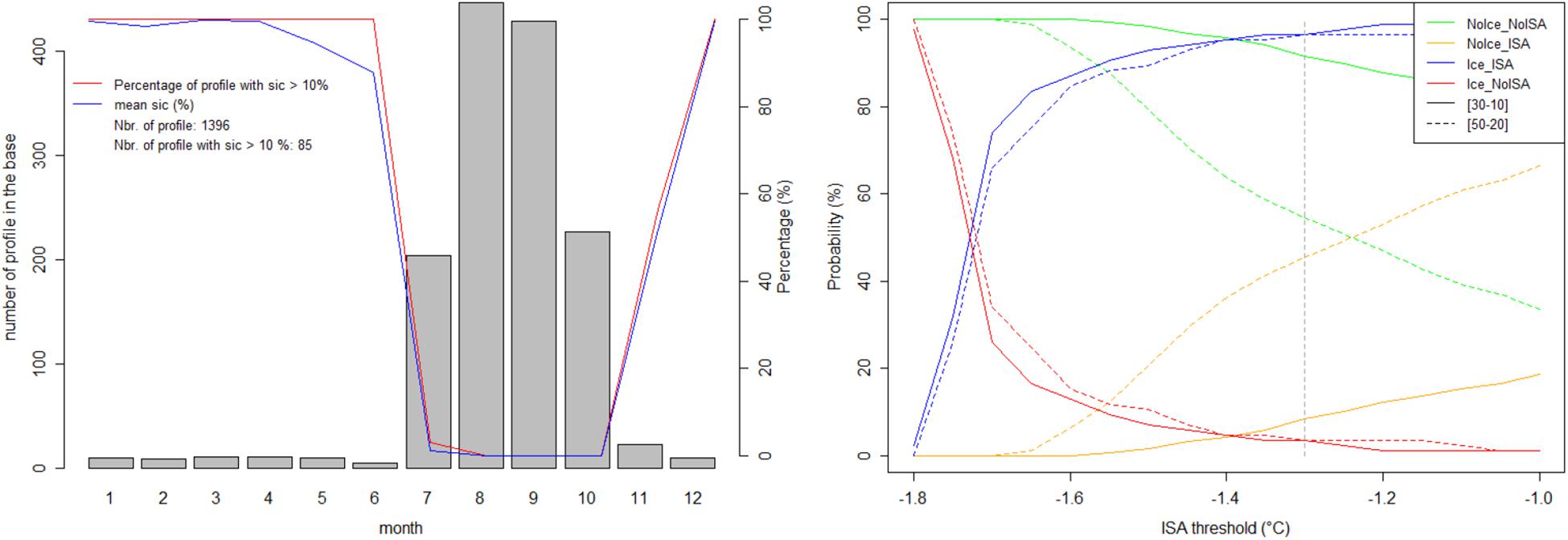
Figure 6. Left: In gray, distribution of float profiles over months included in the database. In red, percentage of profiles with Sea Ice Concentration (SIC) > 10%; in blue, mean SIC in percent. Right: NoIce_NoISA (probability to have no sea ice and negative ISA), NoIce_ISA, Ice_ISA (probability to have sea ice, and positive ISA), and Ice_NoISA statistics in function of the Ice-Sensing Algorithm (ISA) temperature threshold and for the temperature median processed between 50 and 20 dbars (dashed lines) or between 30 and 10 dbars (solid lines). Chosen threshold is –1.3°C (gray dashed line) and best depth range is 30-10 dbars.
Since July 2017, the embedded float algorithm has processed the median temperature over the depth range of 30-10 dbars and used −1.3°C as the ISA threshold. These parameters allow for probabilities of 3.5% for the most dangerous scenario – ice with a negative ISA –, and 8.4% for no ice but a positive ISA. These results are satisfactory and we do not expect them to change in the near future. Using the historical depth range (the one used in the Antarctic) for Baffin Bay, and the same threshold of −1.3°C, results in an equivalent probability of 3.5% for the first case but 45% for the second.
Upward-Looking Altimeter
The PSA-916 acoustic altimeter from Teledyne was tested to detect large objects above the float, such as icebergs as well as sea ice. This altimeter is based on a 200 kHz sonar with a range of 100 m (resolution 1 cm) and a ping rate of 5 Hz. Due to its small size and low power consumption, it is well suited for use on autonomous platforms. The digital output of the sonar is simply the distance to the obstacle estimated from the time of flight at a fixed speed of 1,500 m/s. The intensity of the return echo is not provided by the sensor.
A total of 3,236 sonar measurements (pings) were collected from 14 floats deployed in Baffin Bay and converted into measured draughts by taking float depth into account (see section “Supplementary Materials”). Onshore post-processing was used to correct the sonar output for the real sound speed estimated from the float’s CTD profile (oce R-package, described in Kelley, 2018). We propose to assess two types of corrections here. The first, noted as “corrected at ping,” takes into account the sound speed calculated at the depth of the ping. The second, noted as “corrected to surface,” uses the average speed from the ping depth to the surface. The latter is more accurate but cannot be used to interpret the result of a ping in real time. Out of all the measurements, 99% concern draughts of less than 5 meters. The distributions of these draughts are plotted in Figure 7 for draughts estimated from raw sonar distance (dotted lines) or from distance corrected for sound speed at ping depth (dashed lines) or to the surface (solid lines). The distributions are plotted in black for months where the probability of sea-ice cover is very low (August, September, and October, see Figure 6) and in red for months where the probability of sea-ice cover is very high (December to June). Draughts “corrected to surface” are, in “summer,” well centered around zero with a small standard deviation (0.38 m). Draughts “corrected at ping” are just slightly off-centered but with a comparable standard deviation. The two correction methods are a great improvement on raw sonar output. In “winter,” there is a slight increase in the mean draught (from 0.13 to 1.3 m for the best correction), which can cautiously be interpreted as a sea-ice signature. However, it should be noted that the offset of the float pressure sensor is reset for each profile upon surfacing, and given that this is not possible under ice, the depth measurement may experience greater drift in winter. Finally, these results are surprisingly good, especially the low standard deviation, considering that ±2 dbars accuracy is expected for the float pressure sensor.
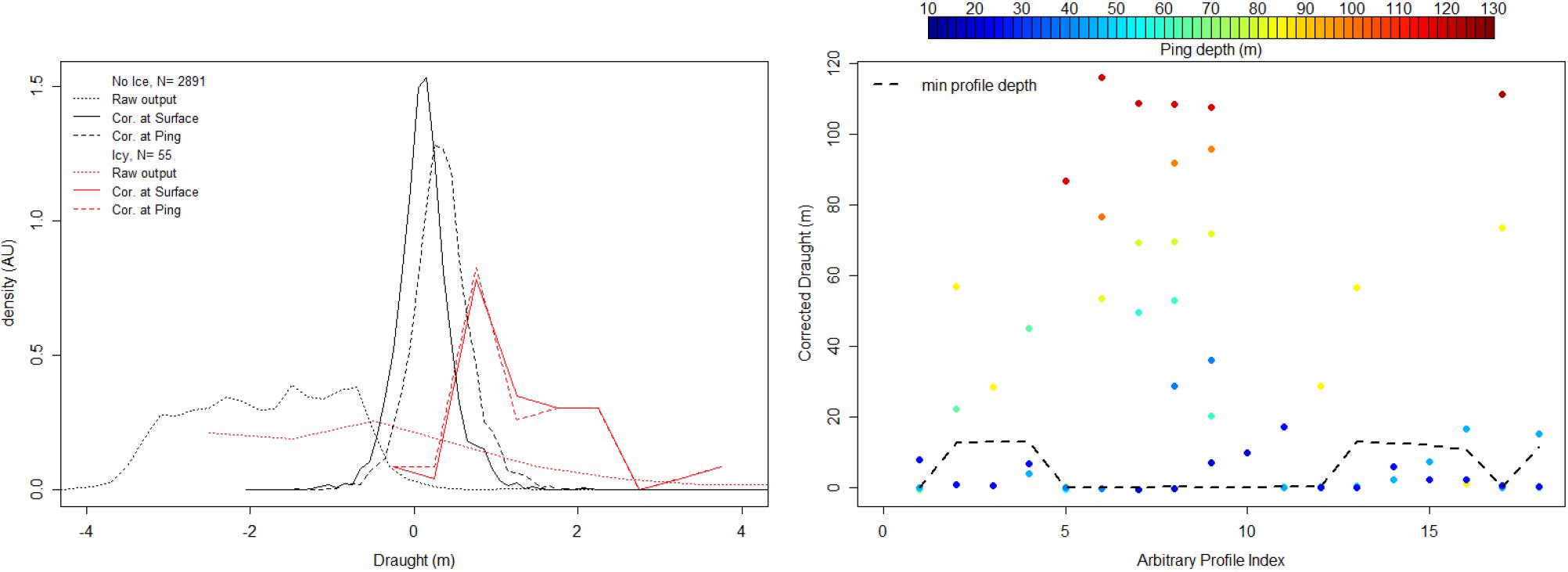
Figure 7. Left: Draught distribution, for draught <5 m, estimated from sonar raw distance (dotted line), from distance corrected for sound speed at ping depth (Cor. At Ping, dashed lines) or for mean sound speed (Cor. At Surface, solid lines). In black: profiles without ice (August, September, and October); in red: icy profiles (December to June). Right: Draught measurements for the 18 profiles with at least one draught measurement greater than 5 m. Color scale represents the measurement depth, and dashed line, the minimum depth reached for the profile.
The PSA-916 sonar was implemented with the aim of detecting large objects like icebergs or ice-ridges. On the right panel of Figure 7, we show all 18 profiles with at least one draught measurement higher than 5 m. All other draught measurements of these profiles are shown. It appears that draught is highly variable for a single profile. In addition, the minimum depth reached by the float is shown on the figure (dotted line). This minimum depth is constrained in winter to 15 m (see Systematic Winter Stop). We can see here that the echoes detected by the sonar, and their corresponding draughts, have never stopped a float, thus confirming their artifactual nature.
On the basis of our results, we think that it could be worthwhile to combine sonar measurements with a more accurate depth gauge. This could enable to have a direct detection of sea ice and even to have an estimation of its thickness which ISA does not allow. On the other hand, the detection of large objects such as icebergs does not seem to be appropriate because the risk of false detection is too high compared to the risk of encountering an iceberg.
Systematic Winter Stop and Other Ice-Detection Methods
At the beginning of the project, due to reservations about the ISA’s suitability to Baffin Bay, a systematic stop function was implemented in the Payload board. This feature allows the float to be stopped at a given depth (here, 15 dbars) for a series of given months. This was particularly useful for our deployment area where dates for the ice breakup are relatively known (typically by the end of July at the latest). Now that we have greater confidence in the ISA, the question of whether to continue using this mechanism may arise.
Other ice-detection methods were explored or partially tested during the project. For example, we integrated an internal shock detector based on acceleration measurements to a test float. The sensor selected was the SignalQuest SQ-XLD. Test trials were carried out in the Mediterranean Sea but since the sensor’s results were too difficult to interpret, we did not pursue testing. Moreover, as it is not recommended to touch ice, even briefly, to avert the risk of sticking, our focus is on detecting ice before contact.
The most promising new method tested during the NAOS project is probably the optical detector developed by Lagunas et al. (2018), based on depolarization of a laser’s reflection on ice. The method was tested, during a prototype phase, on a profiling float deployed in 2016 (WMO6902668).
Energy and Life Expectancy
Compared to the Provor CTS4 with a reported autonomy of 320 profiles (Bittig et al., 2019), the Pro-Ice offers certain advantages but above all disadvantages with regard to autonomy. On the one hand, the new APMT navigation board is more efficient and its higher communication speed (gain of at least a factor of 2, see Section “Satellite Communications”) saves energy on the Iridium transmission. On the other hand, the Pro-Ice configuration entails several drawbacks. The volume of oil pumped at the surface to emerge the additional elements such as the cage and altimeter results in an estimated overconsumption of 6 kJ per profile. The Payload board is also less energy-efficient than its equivalent on the CTS4: compared to the latter, its sensors such as the OCR and ECO operate continuously to acquire data for a longer period of time. This difference causes extra consumption of an estimated 3 kJ per profile. Taking these elements into consideration, the autonomy for a Pro-Ice float is estimated at approximately 300 cycles at 1,000 m depth – an estimate supported by the 360 cycles of unit WMO4901801, performed daily in the Labrador Sea at the beginning of the project. However, deployments in Baffin Bay have subsequently shown that the number of cycles is actually closer to 200 (Le Traon et al., 2020). This difference could be partly explained by the impact of cold temperatures on the nominal capacity of the battery (estimated loss of between 15 and 20% at 1°C), but also by an unexpected residual current between the two boards.
Conclusion
In order to extend BGC-Argo coverage to polar areas, an adapted float has been developed, requiring hardware and software evolutions as well as extensive testing in polar conditions. This float is based on the Provor CTS5-Payload, which accommodates new functionalities such as the changing of parameters without communication or the implementation of ice-detection algorithms. Fifteen Pro-Ice floats were deployed in Baffin Bay as part of NAOS. Several of them survived the Arctic winter, thus demonstrating the success of this technological development.
An in-depth assessment of these deployments and the associated scientific results are given in Le Traon et al. (2020). The technical feedback from these experiments, on components such as the Ice-Sensing Algorithm, the altimeter or the under-ice braking, will undoubtedly open the way to continued improvements in the reliability of this type of platform.
NOSS Absolute Salinity Sensor
Since the publication of the new international standard for the Thermodynamic Equation of Sea water (TEOS-10; OC SCOR and IAPSO, 2010), Absolute Salinity (SA) has become the cornerstone of the new thermodynamic equation for seawater state. However, historical databases primarily deliver Practical Salinity (SP), computed from in situ measurement of seawater pressure, conductivity and temperature. The TEOS-10 approximation to convert SP to SA relies on the measurement of some non-ionic components of seawater, such as nitrate, silicate and dissolved inorganic carbon constrained from historical measurements. It is therefore highly preferable to carry out direct and reliable measurements of SA to accurately compute the physical and thermodynamic properties of seawater. However, SA is a hard-to-define quantity considering the complexity of its biogeochemical composition and the imperfections of existing measurement techniques (Le Menn et al., 2019). Although its major inorganic components are well known, its actual composition varies in time and space, and the development of reliable methods and sensors for measuring in situ SA is an ongoing challenge.
Among the methods allowing direct in situ measurement of SA, the refractive index (RI) measurement is the one of most promising. The NOSS (nke Optical Salinity Sensor) instrument was the first and remains at the time of writing the only device to demonstrate the possibility of obtaining SA over 2,000 m depth profiles from RI measurements (Le Menn et al., 2011) on profiling floats. Prior to NAOS, initial design and qualification phases led to a first operational prototype, which was deployed several times at 2,000 m. However, these tests highlighted the need to increase the reliability of the optical component, and to miniaturize the sensor so that it could be mounted on a profiling float. Consequently, NOSS instruments equipped with smaller prisms, new reflection mirrors and systems to filtrate sunlight, were built to equip Provor floats.
Sensor Design
The NOSS sensor aims to become a new laboratory and field tool for measuring the density of seawater. This product, manufactured by nke instrumentation, has been designed to be deployed on any type of platform (e.g., floats, gliders) in a relatively compact form, sufficiently robust for in situ deployments. The principle consists in the emission of a controlled and collimated laser beam which is refracted from water to a PSD – Position Sensitive Device – to measure the RI derived from the detected micro-variations of laser beam that travel through water samples. The obtained RI, with better than 10–6 resolution combined with embedded pressure and temperature input, should allow the SA to be acquired with an uncertainty of about ±0.005 g/kg in the range of 15 to 42 g/kg, using the Millard and Seaver algorithm (Millard and Seaver, 1990). Converting laboratory methodology to a compact and deployable in situ instrumentation, the NOSS device could be called nTD, standing for RI, temperature and depth.
Lab and At-Sea Experiments
Lab Experiments
A first set of laboratory tests consisted in the calibration of the pressure sensors of two prototypes, by correcting temperature effects on the pressure values measured by these sensors. This technique boosts the accuracy of pressure measurements made by low-cost pressure sensors. The resulting expanded uncertainty on pressure measurements is ±0.6 dbar in the range of 0–2,000 dbar. In this Section, expanded uncertainty means two standard deviations.
The second batch of tests sought to obtain the linearization coefficients of the laser temperature sensor and of the external temperature sensor for each instrument, and to assess the uncertainty of these measurements. The laser temperature sensor is used to calculate the true wavelength emitted by the diode as a function of its temperature while the external temperature sensor is necessary for calculating SA from Millard and Seaver relations. As demonstrated in Liu et al. (2018), these calibrations allowed us to conclude that the Bennett relation (Bennett, 1971) shows smaller residual errors than the widely used Steinhart–Hart equation (Steinhart and Hart, 1968) implemented in the NOSS software. This has led to an expanded uncertainty of ±0.0025°C on external temperatures and ±0.02°C on laser temperatures.
Meanwhile, the following tests focused on studying the effects of temperature, the mixing speed of the calibration bath, and ambient light, on the accuracy of calibration of the RI using the position measurements made by the PSD on the two prototypes. Measurements were also made one month later to test the reproducibility of the calibration equations and the possible drift of the instruments. These calibrations led to the conclusion that the expanded uncertainty on refractive index measurements was less than 5.10–6 for the two prototypes.
Subsequent trials explored the possibility of calibrating the measured positions directly in density, using the reference densities computed from the TEOS-10 algorithm. The obtained results showed a very linear response of the two prototypes in comparison with the calibration using the RI, revealing possible inaccuracies of the Millard and Seaver (1990) equation. Nevertheless, the calibration test was made with a seawater sample with salinity of 38 instead of the usual 35, and revealed deviations between the two responses for different salinities. This suggests that direct calibration in density based on temperature variations at different salinity values is an unsuitable approach.
Further investigations were carried out to evaluate the effect of temperature on the instrument’s components. In this way, nke instrumentation built a watertight container designed to isolate the prisms of the NOSS in the calibration bath. This device allows calibrating the sensor for different salinity values obtained by diluting/evaporating Ocean Scientific International Ltd., standard seawater (bottles of linearization kits at 10, 35 or 38). It was thus possible to quantify the effect of temperature at constant salinity on the RI values obtained from the NOSS, and to achieve a new, improved calibration procedure taking into account of wavelength and temperature variations of the RI values obtained from the beam position measured from the PSD (Le Menn, 2018). The relation giving the refraction angle of the NOSS from Snell-Descartes refraction laws (Malardé et al., 2009) can then be simplified and rewritten to give the RI of the medium as a linear function of the prisms’ RI. The two coefficients of this relation can be expressed as a function of wavelength and temperature variations (Le Menn, 2018), from the wavelength and the temperature at which the calibration was made. This method reduces by a factor of 5.8 the effect of temperature and wavelength variations on the measured RI, therefore opening the way to more accurate absolute RI measurements.
At-Sea Tests
A first version of the NOSS sensor was tested at sea in 2012 in the Bay of Biscay, during a PROTEVS oceanographic campaign (Table 1). One NOSS sensor was mounted on the cage of a CTD profiler and 20 profiles in shallow and deep water (2,000 m) were obtained to validate the new design, bringing to the fore new issues to resolve (Figure 8, left).
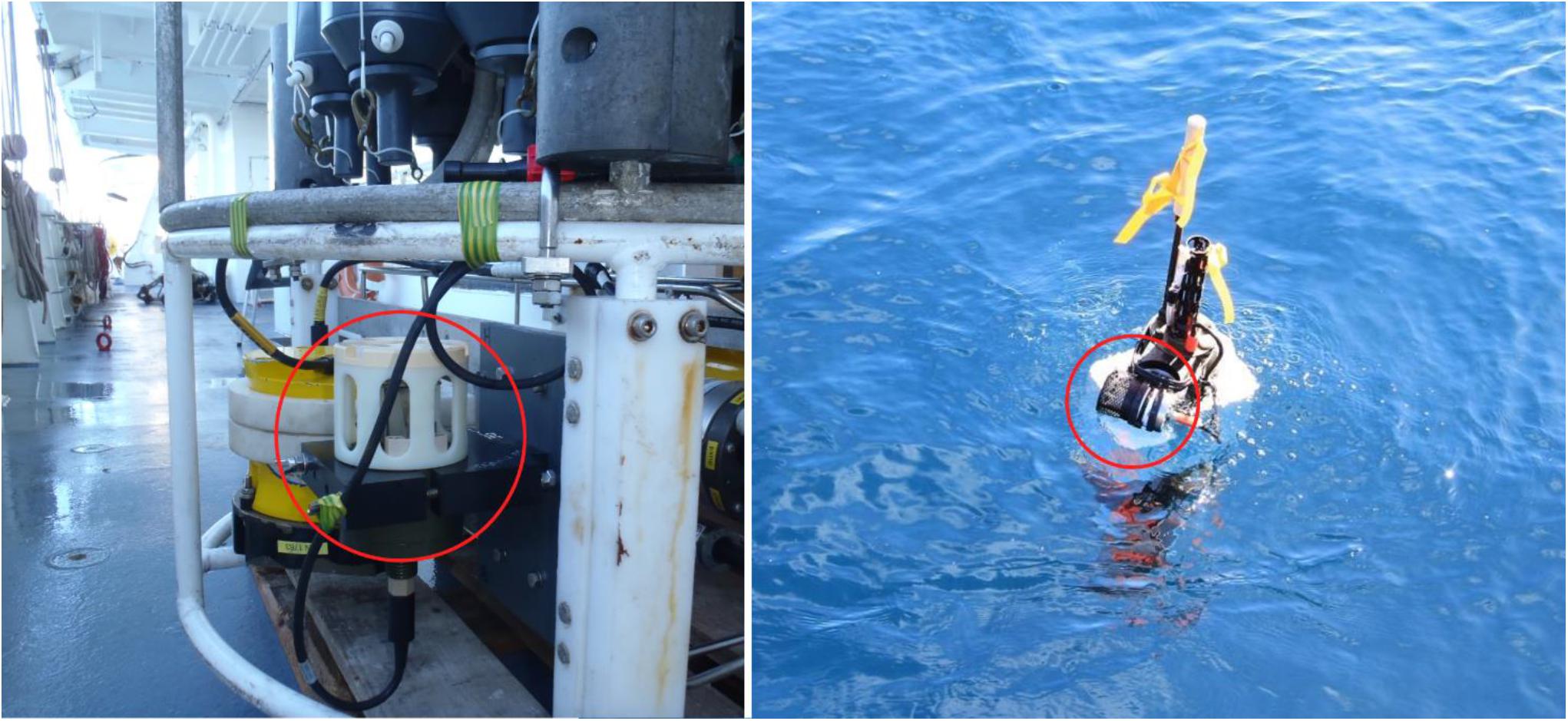
Figure 8. Left: NOSS Absolute Salinity sensor mounted on a cage during the PROTEVS oceanographic campaign in 2012 (courtesy of SHOM). Right: NOSS on a Provor float in 2015 (courtesy of LOV).
Along with tests and laboratory calibrations, two cruise campaigns were carried out as part of the NAOS project. The first cruise campaign was organized in April 2015 in the Western Mediterranean Sea at the Boussole mooring (7°54′E - 43°22′N), where floats could be recovered (Table 1). Five profiles were carried out: one at 1,000 m, a second at 1,500 m and the last three at 2,000 m. The first profile at 1,000 m showed promising results, with deviations – compared to the values computed from collocated CTD casts and TEOS-10 – inferior to ± 0.03 g/kg (Figure 9 left). However, the 1,500 and 2,000 m depth profiles showed larger non-linear discrepancies adjustable from empirical relations (Figure 9, center). These issues with NOSS SA measurements were verified during a second cruise in June 2018 (Table 1) in the eastern Mediterranean basin, where eleven NOSS casts were carried out along with CTD casts and biogeochemistry sampling for intercomparison and estimation of the minor SA component in Mediterranean deep sea (Kolodziejczyk et al., 2019).
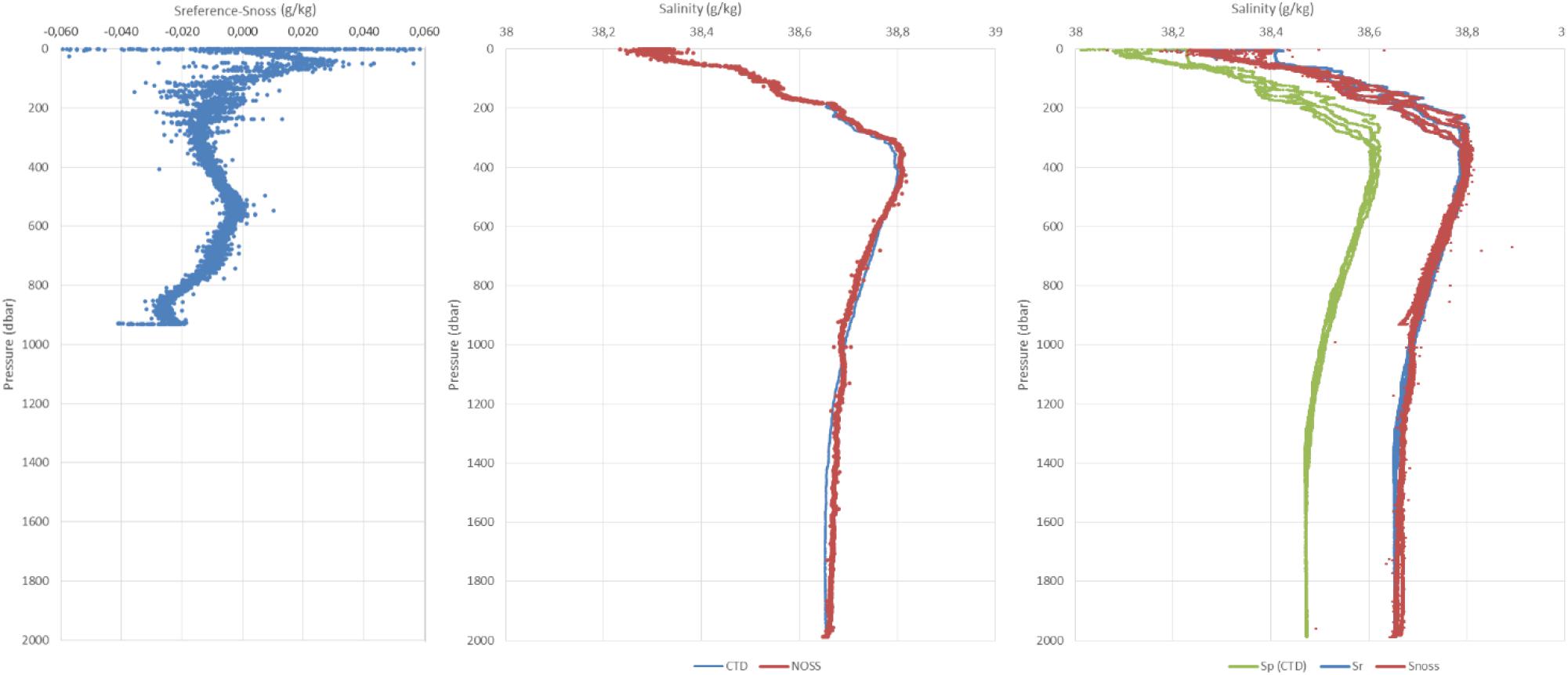
Figure 9. Left: The deviations obtained with the NOSS n° 2 between a reference Absolute Salinity calculated from the TEOS-10 and the salinity obtained with the calibrated NOSS during the first profile. Center: The response obtained during a profile at 2,000 m. Deviations at 400 m could be explained by response-time problems. Right: NOSS data post-processed after the oceanographic campaign carried out in the Mediterranean Sea in 2015, and in comparison with reference salinity (Sp, green; Snoss, red; and TEOS-10, blue).
As further work was needed to evaluate the effect of pressure at constant temperature and salinity, a pressure tank was specially built by nke instrumentation and improved by the Laboratoire National de métrologie et d’Essais (LNE-CNAM) in the framework of the METEOMET2 project1. After preliminary tests at atmospheric pressure and variable temperature, a long-duration test at 2,000 dbars revealed a flaw in the water tightness of one mirror. This flaw could explain the non-linearity errors and sensor failures observed during different tests at sea. Nke instrumentation is investigating a solution to solve this issue. In addition, nke instrumentation has worked on the development of an algorithm to compensate the effects of pressure and temperature on RI measurements (Simon et al., 2018) and to improve the measurement accuracy of the NOSS sensor, as shown in the results of post-processed data from the NOSS sensor mounted on a Provor float and acquired during a LOPS cruise in 2015 (Figure 9, right).
More recently, the NOSS sensor has undergone mechanical and optical corrections to its design in order to minimize pressure impact on the bonding of its mirrors dedicated to internal reflections, and to render it insensitive to natural-light variations in the subsurface seawater layer. Its detection window is equipped with filters that are more selective for wavelengths. A new deployment is scheduled for 2020 in the Mediterranean Sea off Villefranche-Sur-Mer. The float will be programmed with a new profile mission aiming to optimize the accuracy of measurements in Absolute Salinity.
Conclusions and Perspectives
The development of the NOSS instrument is an unprecedented advance toward a direct measurement of seawater Absolute Salinity using RI measurements obtained by a refractometry method. The NAOS project has allowed improvements of the NOSS instrument through laboratory calibration and in situ tests at sea. Although further work is needed to completely isolate the pressure effect from other effects during calibration, the improved calibration method has opened up the way for measuring in situ RI in relation to temperature, salinity and wavelength, an essential step for improving our knowledge of seawater thermodynamic and physical properties.
Further work is ongoing to achieve reliable and reproducible NOSS SA measurement beyond the NAOS project. The first publications on the NOSS sensor have stimulated research in seawater RI measurements. While various methods and sensor concepts have been published in the last few years, so far none of them has developed operational and commercial applications usable on an Argo float. Therefore, continuing improvements on the NOSS sensor are planned in the framework of a future French project, with the purchase of pressure trials at LNE-CNAM, the calibration of new prototypes at SHOM’s laboratory, the release of several Argo floats equipped with NOSS instruments, and scheduled deployment and at-sea testing during dedicated cruises.
Arvor Profiling-Float Improvements
The Arvor is a profiling float used in the Core-Argo network, which has been industrialized since 2008. After several years of deployment at sea, the NAOS project provided an opportunity to review the entire lifecycle of this product, with the aim of increasing its reliability. The resulting assessment identified various areas for improvement, further detailed in this section: (i) improvement of production methods, in order to deliver equipment with a very high reliability rate; (ii) functional improvement of the product, to achieve optimal operation at sea; and finally, (iii) improvement of the profiling float’s ergonomics during deployment operations, to boost reliability during this major phase in the product’s life. After at-sea validation of prototypes modified accordingly in 2015, serial production of the “NAOS” Arvor was launched and more than 330 floats were successfully deployed between 2016 and 2019 (Figure 10), proving the value of this work, as shown by the statistics presented at the end of this Section.
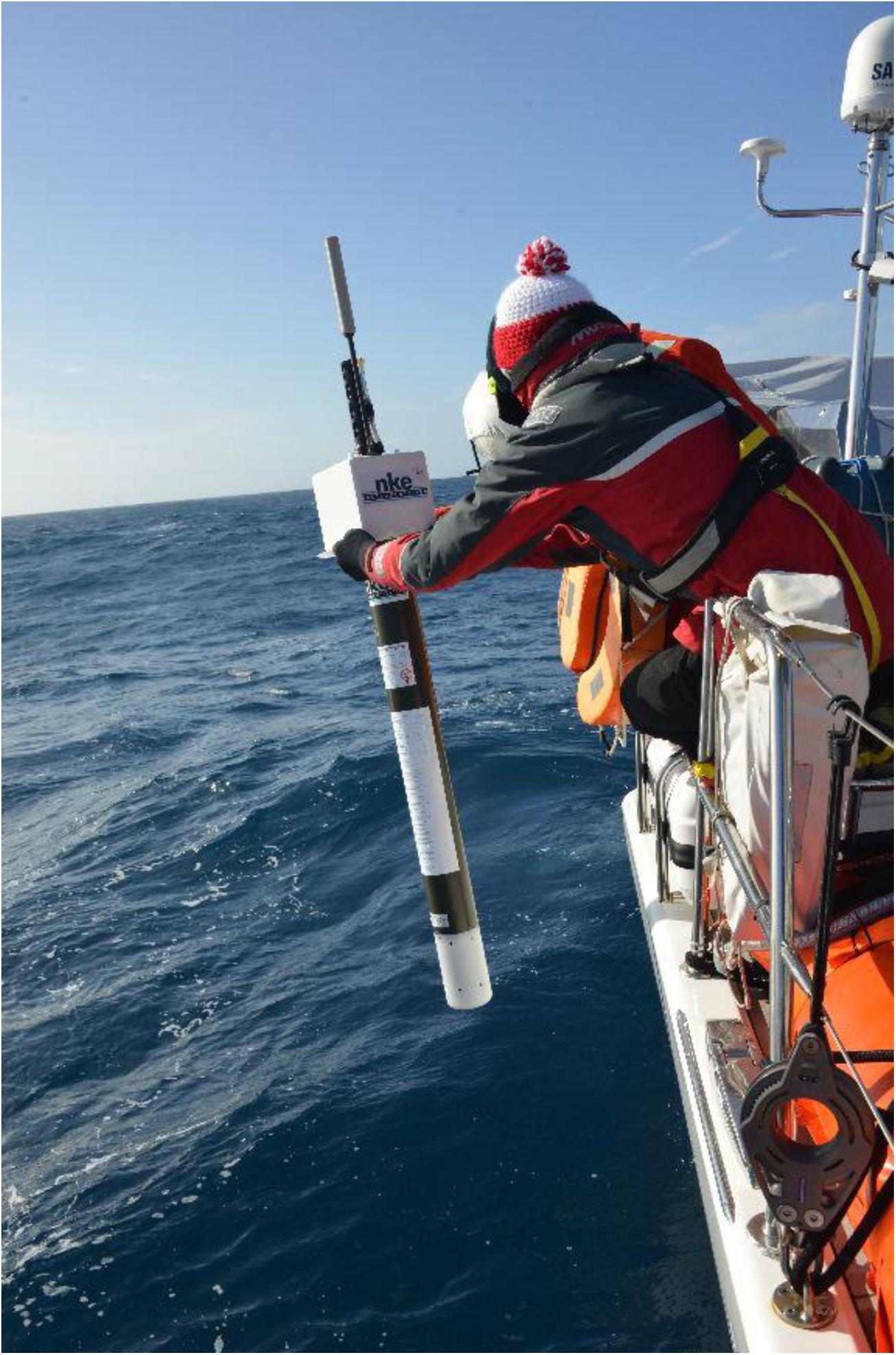
Figure 10. Deployment of an Arvor profiling float in Antarctica, 2018 (courtesy of Hanna Leniec-Koper).
Description of Improvements
Production Improvements
Improvements to the Arvor’s production methods relate to a number of areas.
The first step in this work was to make the quality of the subassemblies supplied by the various nke instrumentation subcontractors more reliable, so that more robust components could be delivered. In particular, significant work was carried out on the hydraulic system – the focal point of such an instrument. Therefore, in addition to unitary tests carried out on the pumps and solenoid valves, a test on a fully integrated hydraulic system was implemented, as well as a high-pressure running-in, with control laws similar to those used by the instrument at sea.
Another production aspect that has been improved is the in-factory handling of the CTD, which has been an ongoing source of questioning. Today, the CTDs are filled only with filtered water, stored empty and systematically cleaned with Triton, in accordance with Seabird’s Application Note 97 (Sea-Bird Scientific, 2017). During tank tests, the CTD circuit is closed to avoid soiling.
The last production step is the ballast adjustment of each float specimen. To achieve this, the weight of each float is adjusted in a freshwater basin to ensure that the float level, upon deployment at sea, is optimal on each copy of the product. A chart gives the equivalence between freshwater and seawater to allow fine-tuning of this adjustment. Yet thanks to its architecture and large hydraulic volume, the Arvor is able to operate in a vast majority of salinity conditions, without any pre-ballasting for adaptation to its deployment area. In this way, this feature facilitates the deployment schedule by offering the flexibility of floats deployable under any density conditions.
Finally, once a profiling float is integrated and tested in the laboratory, nke instrumentation performs an operational test using 8-m deep tubes, dug and filled with freshwater. At the end of production, each profiling float is therefore tested through several cycles. Operational testing allows, in addition to the factory tests, checking of the instrument’s behavior, for example hydraulic flows or acquisition timing, under conditions similar to what the float will experience at sea.
Functional Improvements
Many functional improvements have also been made on the Arvor.
First, in order to increase the reliability of embedded software development, major efforts were made to merge the various existing software versions: Arvor Argos-2, Arvor Iridium, Arvor equipped with a dissolved oxygen (DO) optode, Provor Argos-2, Provor Iridium, Provor DO, etc. This has greatly simplified the carrying of corrections or evolutions, as well as the non-regression and qualification testing phases, therefore making the product more reliable.
In addition, numerous features were implemented on the Arvor and Provor: the possibility of acquiring a high-resolution data profile (4,000 samples); the implementation of a bi-mission mode (which allows some profiling-float parameters to be changed automatically after N deployment cycles); the reinforcement of technical information sent by satellite transmissions; and the strengthening of information contained in satellite messages to improve the reliability of decoding. Moreover, to secure deployments in ice areas, the ISA was implemented. Finally, profiling floats equipped for oxygen measurement had their optode placed on a mast, in order to perform an air measurement during each cycle for self-calibration purposes.
Deployment Improvements
The last point of improvement concerns user experience, especially at the time of deployment. For this purpose, the profiling float’s self-tests, requiring no external equipment, were reinforced to offer more comprehensive automatic tests than before, including the testing of satellite transmissions, more thorough testing of the link with the CTD, and measurement of the voltage drop when the hydraulic components are activated (to check their proper connection). At the end of the self-testing, an unambiguous audible signal (powerful embedded buzzer) was set up to replace the overly discreet clicks of the solenoid valve, used previously.
Some floats were lost due to clumsiness during deployments: these include floats deployed while not activated, floats whose flotation was too low for deployment (with poor distribution of oil between the external ballast tank and the internal tank following tests, for example), or floats deployed despite an unsuccessful self-test (mainly because of its overly discreet report signal). To overcome these risks, an option was developed in the software, enabling response to these situations, and a return to a nominal operating mode immediately after launching.
Finally, a standard checklist is now provided to users, to guide them through the different steps to follow for optimal deployment. A data decoder is also available, to avoid any risk of confusion or to facilitate interpretation of the data transmitted by the equipment, including technical data. The technical fields now include the names of the Global Data Assembly Centers.
At-sea Performance Analysis
To measure the impact of this work, the lifespans of profiling floats at sea were analyzed.
For such an exercise, particular attention had to be paid to the choice of the sample. Indeed, the lifetime of a profiling float depends on many parameters, including the cycle period. An instrument which cycles every 5 days will spend about half as much time at sea as a float which follows the typical cycle of every 10 days. Therefore, only floats with a 10-day cycling period were selected.
Moreover, the Arvor product range includes floats with a lower battery capacity to cater to specific markets. The Arvor Light (referred as Arvor_L in the JCOMMOPS database) was thus not taken into account.
Figure 11 represents the lifetime of Arvor profiling floats at sea, comparing the Arvor before and after the evolutions described above. The unbroken line indicates Arvor produced and deployed after the NAOS work, i.e., between 2016 and September 2020 (depending on the serial number), representing a sample of 383 units. The dotted line curve shows Arvor produced and deployed between 2013 and 2015, representing 160 units. This figure, drawn using data from the JCOMMOPS database, illustrates the percentage of profiling floats that disappeared per 10-day period. The impact of the work carried out under NAOS on the lifetime of Arvor floats stands out clearly: 96% of Arvor produced after the NAOS evolutions are still operational at sea after 1,000 days, compared to 76% of Arvor before the NAOS work.
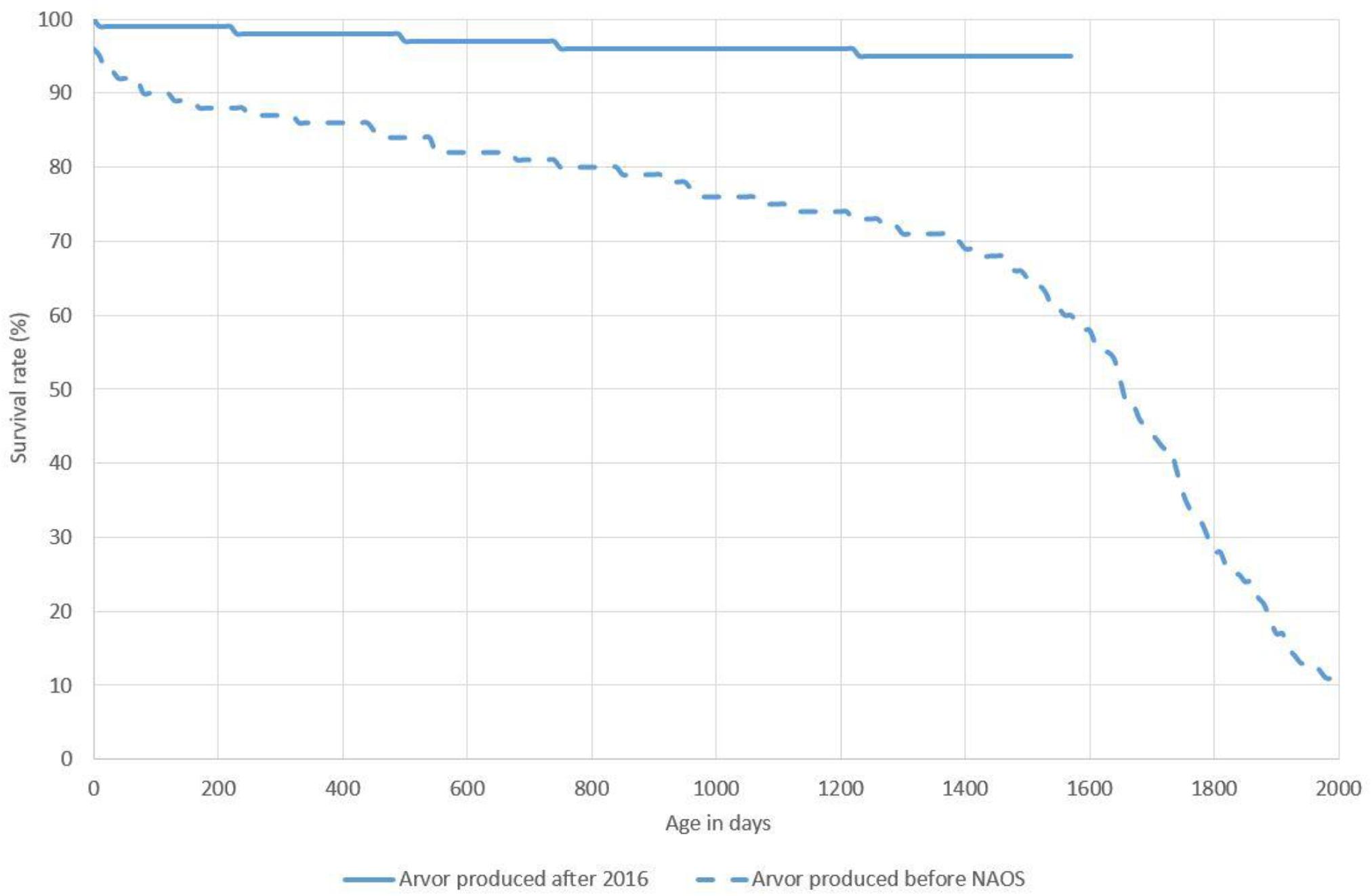
Figure 11. Survival rate of the Arvor profiling float. After 1,000 days at sea, 96% of the Arvor “after NAOS work” (i.e., produced after 2016, depending on the serial number) are still in operation, compared with 76% of the Arvor “before NAOS work” (produced and deployed from 2013 to 2016). Source: www.jcommops.org, 23 September 2020.
Meanwhile, Figure 12 compares the lifetimes of the main Argo profiling floats. Like Figure 11, it shows the benefit of the work carried out under NAOS, as the Arvor is now the second-most reliable profiling float within the Argo program.
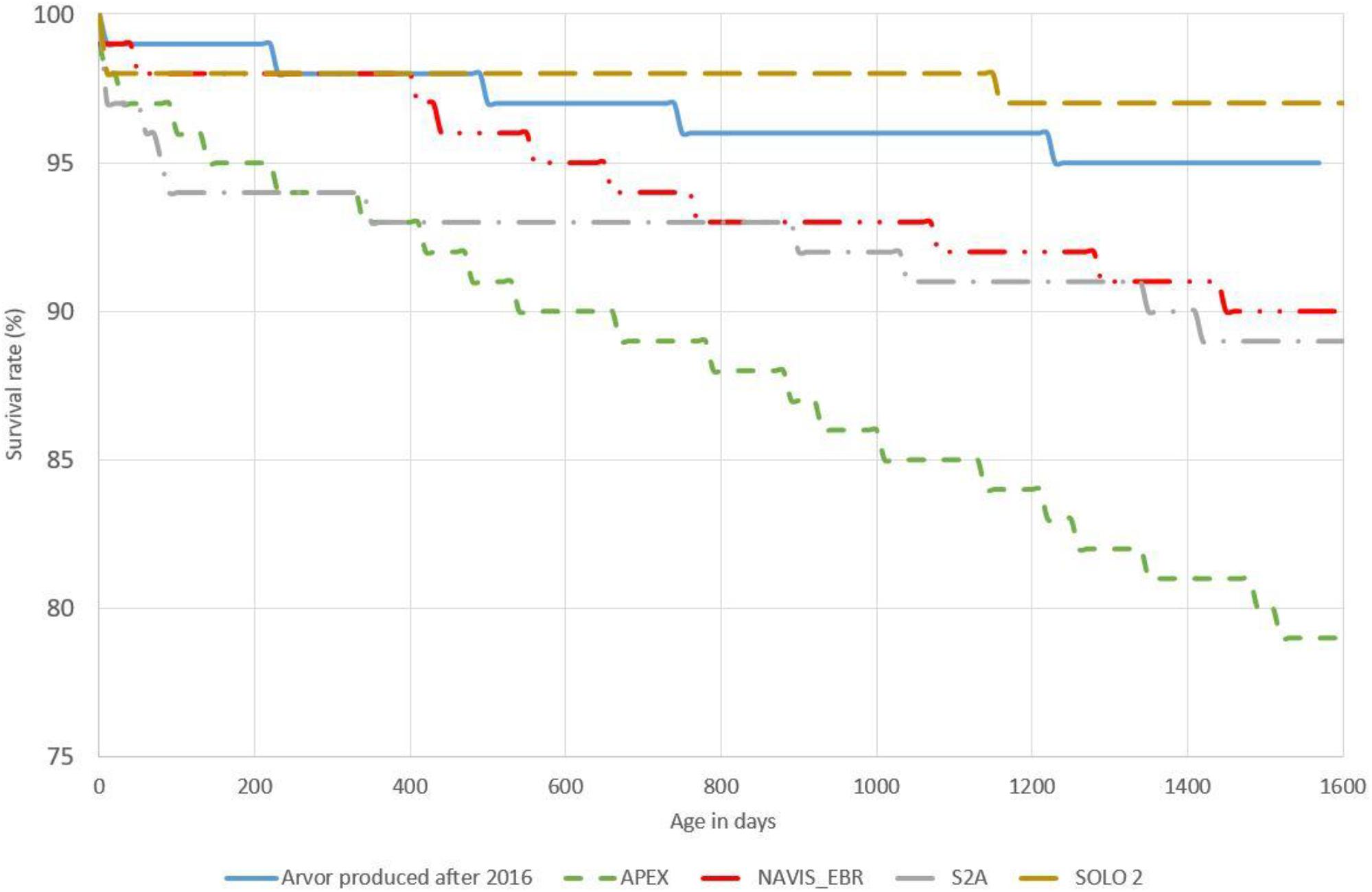
Figure 12. Survival rate of the main Argo profiling floats. After 1,000 days at sea, 98% of the SOLO 2, 96% of the Arvor, 93% of the NAVIS_EBR and S2A, and 89% of the APEX are still in operation at sea. The float-sample criteria comprised their status (active, operational, or closed), deployment date (since January 1, 2016), and cycle period (240 h or 10 days). Source: www.jcommops.org, September 23, 2020.
Conclusion
Work to improve the Arvor consisted in reviewing and improving the instrument’s production and factory test methods, adding new functionalities and offering better monitoring at sea, as well as securing the deployment method. This work is clearly fruitful, since the survival rate at sea has risen considerably since 2016: 96% of Arvor are still in operation after 1,000 days (i.e., 100 ten-day cycles) of operation at sea, making it the second-most reliable profiling float on the market. Since the end of the NAOS project, performance improvement has continued to be an ongoing goal, through the integration of new methods and processes to nke instrumentation procedures, in order to reach the highest possible level of reliability.
Satellite Communications
During their missions at sea, Argo profiling floats acquire a great number of data. These are both scientific data, such as pressure, temperature and salinity for the most common instruments, and technical data, in order to monitor a float’s behavior along its deployments.
As profiling floats are autonomous at sea, they have to transmit their data to land stations through a satellite-communication system. When the Argo network was set up, profiling floats were equipped with the Argos-2, but this communication system, would become a bottleneck limiting Argo development for several reasons. First of all, the amount of data acquired by the profiling floats increased quickly due to the will of the research community to improve the sampling resolution of the water column, and to embed additional sensors (D’Ortenzio et al., 2010). Secondly, the time allocated for Argos transmissions, typically between 6 to 12 h depending on the area of deployment, implied a drift of the profiling float at the sea surface, which created a negative impact on estimates of water-mass displacement (Sévellec et al., 2017). This time at the surface also exposed the sensors to biofouling. Finally, Argos-2 also restricted the development of specific applications, like Polar-Argo which necessitates very limited time spent at the surface to avoid sticking to ice (see Section “BGC Profiling Floats for Under-Ice Application”).
In order to avoid these limitations and to offer new perspectives to the Argo network, the Iridium system was embedded on Arvor and Provor profiling floats in 2006. Then, when the new generation of Argos, named Argos-3, was later launched, offering new functionalities compared to the previous version, the opportunity was raised to evaluate this system and to make a comparison with Iridium. In the framework of NAOS, we thus studied, implemented and evaluated the Argos-3 satellite-communication system during a pilot experiment at sea, the only one of its kind carried out at the time of writing.
This section compares the results obtained at sea on profiling floats fitted with the Argos-2 (Woodward et al., 2009), Argos-3 (André et al., 2015), Iridium SBD (Short Burst Data) (MacMahon and Rathburn, 2005), and Iridium RUDICS (Router-Based Unrestricted Digital Internetworking Connectivity Solutions) (Prior-Jones, 2008) satellite-communication modes.
These communication systems differ in two main aspects that lead to differences in their performance, as described in Table 2 (Maine et al., 1995; Velpuri et al., 2014):

Table 2. Comparison between Argos-2, Argos-3 low-data-rate, Iridium SBD and Iridium RUDICS modes, and data rates obtained on Arvor, Deep-Arvor and Provor CTS4/CTS5 profiling floats at sea.
- Argos-2 and Argos-3 are based on a network of only a few moving satellites, offering intermittent access to the network, while Iridium is made up of 66 satellites, offering permanent coverage;
- Argos-2 solely offers the possibility of transmitting uplink data (from a modem to a satellite), while Argos-3 and Iridium are bi-directional systems, guaranteeing the quality of transmissions thanks to acknowledgments.
Implementation on Profiling Floats
The satellite-communication equipment consists of a modem and an antenna (refer to Supplementary Materials). The modem is integrated in the hull of the profiling float, directly on the motherboard (Argos-2) or else deported apart (Argos-3 and Iridium). Antennas are specific designs, as they need to withstand the high pressures met during the profile at depth.
Figure 13 shows the various profiling floats exploited for this experiment: Arvor (Argos-2), Arvor A3 (Argos-3 low-data-rate mode), Deep-Arvor (Iridium SBD) and Provor CTS4 (Iridium RUDICS).
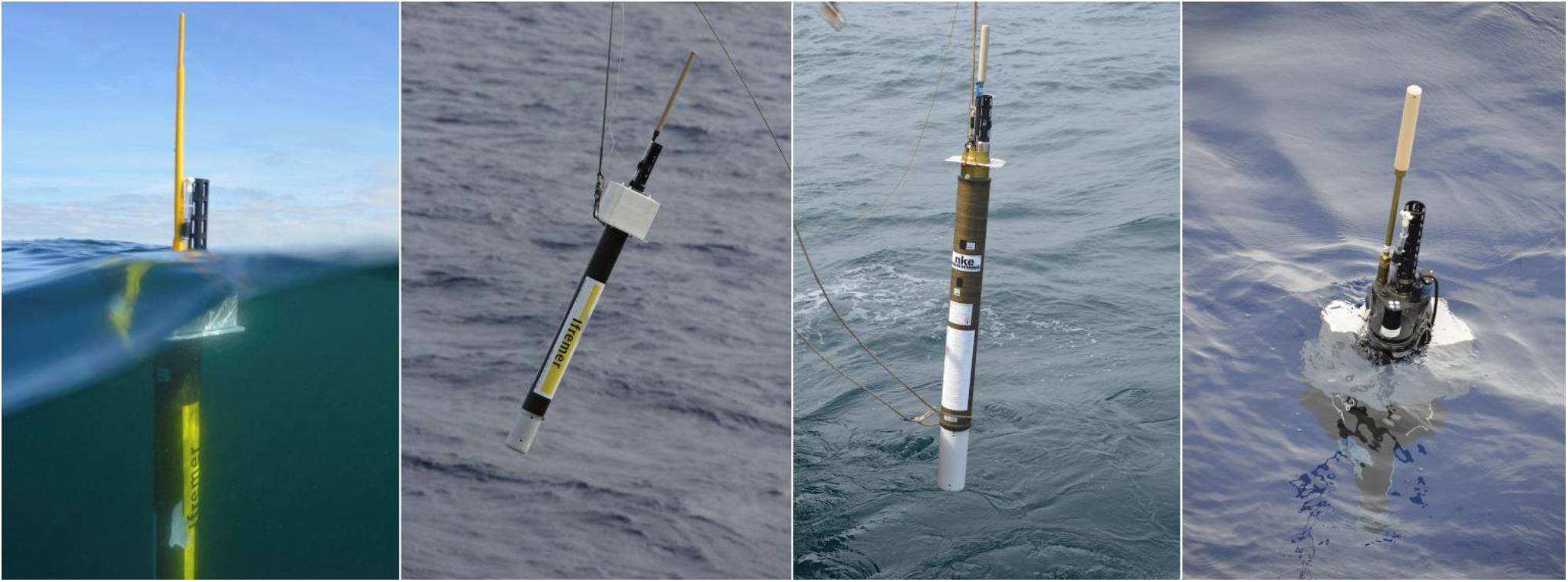
Figure 13. From left to right: Arvor Argos-2 (courtesy of Olivier Dugornay/Ifremer); Arvor Argos-3 (courtesy of Ifremer); Deep-Arvor (courtesy of Kévin Balem/LOPS); Provor CTS4 (courtesy of Giorgio Dall’Olmo/Plymouth Marine Laboratory).
Following the deployment of many such profiling floats at sea in the past years, we will now describe the performance of their satellite-transmission systems.
Results at Sea
Table 2 compares the flow rates of each transmission mode, obtained at sea. The profiling floats were chosen to cover many deployment zones, and to give results over a long period of time, to avoid regional and seasonal bias.
The data-transmission rate takes into account the time taken to get access to the network, the time taken to receive the acknowledgments and eventually to retransfer the data if necessary (if available), and in the case of Argos-2, the repetitions of blind transmissions needed to ensure a good quality of transmission.
Profiling floats equipped with Argos-2 transmitted an average profile of 500 bytes in 8 h (outside the Mediterranean Sea, where transmission was programmed to last over 12 h due to continental electromagnetic noise), i.e., an average throughput of approximately 0.001 kByte/min.
The Arvor A3 low-data-rate profiling floats are described in detail in André et al. (2015). Their statistics were computed after the launch of the Saral satellite, giving rise to better results: a profile of 500 bytes was transmitted in 3 min 10 s on average, which converts into a data-transfer rate of approximately 0.16 kByte/min. It is important to note that the results given for Argos-3 are only valid if the whole dataset can be transferred in one satellite pass. Otherwise, the floats have to wait for a new satellite pass, which can take up to a few hours, and drastically reduces the transmission rate.
The Iridium SBD performance was analyzed on 5 Deep-Arvor profiling floats, deployed from 2014 to 2018 in North and South Atlantic, for a total of 632 cycles. They transmitted a total of 8,261 SBD of 300 Bytes each, in 2,541 min in total, which leads to an average data-transfer rate of approximately 0.97 kByte/min.
The RUDICS mode was studied on two BGC platforms, the Provor CTS4 and the Provor CTS5. On these two profiling floats, the results in terms of data rates differ due to the use of two different software drivers: the Provor CTS4 operates in half duplex, while the Provor CTS5 operates in full duplex. In addition, observed data rates are also affected by the time required to access data in the platform’s internal memory, which is not dependent on the Iridium network but on the float’s coding methodology, also different on each. It is thus that on the 20 Provor CTS4 and 5 Provor CTS5 profiling floats used to compile these statistics, deployed by LOV and Takuvik, the average data rates invoiced by the access provider are 5.5 and 12 kBytes/min respectively.
Conclusion
This study allowed us to compare the at-sea performances of the Argos-2, Argos-3 low-data-rate, Iridium SBD and Iridium RUDICS satellite-communication systems on Argo profiling floats.
The Argos-2 transmission mode allows, in our context, the transmission of 1 useful byte per minute. This system is slowly disappearing as it can no longer accompany the key developments of the Argo network. Starting out as equipping 100% of Argo floats in the early 2000s, it now represents only 6.6% of the profiling floats deployed at sea (source JCOMMOPS, September 2020).
In comparison, the Argos-3 low-data-rate is more interesting, as it allows a profiling float to transmit the whole of a typical Argo CTD cycle in one satellite pass in the space of a few minutes, with a throughput of 0.16 kByte/min in our experiment. However, this approach will quickly reach its limitations, for if additional data is to be transmitted, one satellite pass will not be sufficient, and the transmission will extend to a few hours due to the need to wait for another satellite pass, drastically reducing the data rate.
Iridium allows the transmission of a great amount of data either in SBD (approximately 1 kByte/min) or RUDICS (approximately 12 kBytes/min) mode. The choice between these two modes depends on the possibility of embedding the bigger modem required for RUDICS, and the cost of transmission.
Perspectives
Even if the Iridium system is currently satisfactory, it is important to continue to evaluate potential new satellite communication systems, in order not to depend on the monopoly of a single supplier, to make it possible to transmit more and more data, and to continue to optimize Argo’s investment and operating costs.
The Argos-4 system, to be launched in 2020, can be a good candidate, as it will offer a data-transfer rate equivalent to the Iridium SBD mode: 20 kBytes transmitted in a satellite pass of 12 min, that is, approximately 1.6 kBytes/min. However, as the Argos network is intermittent, this rate slows considerably if data cannot be fully transferred in a single satellite pass. Kinéis, the new generation of Argos after 2022, nevertheless promises much better coverage, with 25 satellites, and a revisit time of less than 15 min (compared with the current time of a few hours).
In 2019, all Iridium Next satellites were launched. However, the modems dedicated to applications such as profiling floats are still under design. This network should improve the data-transfer rate by a factor of at least 10, according to the preliminary information provided.
Finally, it is important to point out that many companies intend to offer access to the internet through satellite communications, at all times and from anywhere on Earth (Randria Manotrona, 2018). This development could revolutionize an application such as Argo by opening up the possibility of transmitting a huge amount of data in a few seconds only. However, we do not yet know what modems or antennas will be used, how they can be integrated, nor at what price.
Conclusion
The 10-year NAOS project, launched in 2010, was an unprecedented effort to strengthen the French contribution to the Argo program and prepare its future challenges. The project conducted major float and sensor technological developments that are reported in this paper. Three scientific experiments preparing future extensions of the Argo core array were then carried out: deep floats equipped with dissolved oxygen optodes in the North Atlantic, BGC floats in the Mediterranean Sea, and BGC floats for under-ice applications in the Arctic Ocean. Results of these experiments are described in a companion paper (Le Traon et al., 2020). The project also contributed to strengthening the French contribution to the Core-Argo array thanks to the deployment of more than 100 standard Argo floats.
The work presented here has made it possible to federate the French Core-Argo, Deep-Argo, BGC-Argo and Polar-Argo communities around shared scientific and technological objectives, i.e., the development and qualification of new types of profiling floats (Deep-Arvor, CTS5-Payload BGC), the improvement an innovative density sensor, the implementation and qualification of new functionalities (e.g., ISA) and the improvement of the entire French profiling floats fleet (transmissions, stranding management, improvement of the lifetime of floats).
All the developments carried out thanks to the NAOS project represent a unique technological leap forward, both contributing to and benefitting from the scientific activities of the international Argo program in the broadest sense. The improved Arvor float that contributes to Core-Argo has been the most deployed profiling float worldwide in 2018 and 2019, the Deep-Arvor is the second most widely deployed profiling float that contributes to Deep-Argo (source: JCOMMOPS), and the Provor BGC profiling floats have become the platform that allows the largest number of sensors to be carried in the frame of BGC-Argo. The NOSS sensor is not operational in Argo yet, but is one of the most promising sensor for the direct measurement of seawater density. This progress highlights the role of France’s marine-research community in instrumental development activities, and its ability to innovate and propose new avenues of exploration to continually improve our understanding of the oceans.
From an organizational point of view, the next challenge for Argo is to implement and sustain its extensions, moving from regional demonstrations to long-term international and global coordination. Technology must continuously evolve to maintain state-of-the art instrumentation, improve existing capabilities, and answer new scientific challenges. Future challenges for Argo technological developments in France include:
- improving the performance of floats, and in particular extend their lifetime. This requires extensive work on the most consuming subassemblies of a profiling float, namely the hydraulic system and sensors;
- improving the performance of the sensors;
- developing a 6,000 m float capable of embarking additional sensors;
- developing and/or testing new sensors (e.g., acoustic, new BGC parameters) on BGC profiling floats;
- and further reducing costs, in order both to maintain the competitiveness of French technologies, and to enable the global Argo network to continue to develop despite increasingly expensive instruments (deep, BGC).
Data Availability Statement
The datasets presented in this study can be found in online repositories. The names of the repository/repositories and accession number(s) can be found below: http://www.coriolis.eu.org/Data-Products/Data-Delivery.
Author Contributions
P-YLT and SL supervised the technological developments of NAOS. P-YLT wrote the “Abstract” and “Introduction.” P-YLT, SL, and XA reviewed the whole manuscript content. SL, VD, CR, XA, and MA participated in the design of the “Deep-Arvor profiling float.” VTh in its exploitation, and all co-wrote the corresponding section. EL led the development of and wrote the section on the “New Biogeochemical (BGC) Float for R&D Application,” with CP who led the Payload firmware development, and FD’O, HC, AP, VTa, CS, and AD. EL led the development of and wrote the section on “BGC Profiling Floats for Under-Ice Application,” with the contribution of CP, CS, CM, JL, and MB. CM led the field trials with CP and JL and wrote the corresponding section. DM and AD led the “NOSS Absolute Salinity Sensor” development. AP, FD’O, and VTa participated in its deployment. DM, AD, and VTa in the data analysis. ML and NK in its qualification and improvement. NK, ML, and DM wrote the corresponding section. JS and SL led the “Arvor profiling-float improvements,” with the contribution of DN. XA wrote this section. BM, XA, and SL led the “Satellite communications” evaluation, written by XA. All authors read and approved the submitted version.
Conflict of Interest
Nke instrumentation is a private company, in which DM, JS, AD, DN and CS are employed. Arvor, Deep-Arvor and Provor Argo floats are industrialized and commercialized by nke instrumentation under a license agreement with Ifremer. Provor-CTS4 and Provor-CTS5 for BGC applications are commercialized by nke instrumentation under a license agreement with Ifremer and LOV.
The remaining authors declare that the research was conducted in the absence of any commercial or financial relationships that could be construed as a potential conflict of interest.
The handling editor declared a past co-authorship with one of the authors P-YLT.
Funding
The NAOS project is the result of a strong partnership between Ifremer (coordinator), UPMC (co-carrier), CNRS (INSU), UBO/IUEM (PRES UEB), SHOM and two private companies: CLS for satellite-telecommunications aspects and the SME nke instrumentation in charge of marketing the French Argo floats. The NAOS project received support from the French State under the “Investissements d’avenir” program. This support, managed by the National Research Agency (French ANR), is referred to as ANR-10-EQPX-40. The French cruises involved in the NAOS Deep-Arvor float deployment were supported by the French Oceanographic Fleet (TGIR FOF). The WAPITI project, during which the Wapiti Deep-Arvor profiling float was designed, received funding from the European Unions Horizon 2020 research and innovation program under grant agreement n°637770. The development of the new CTS5-Payload BGC float received support from the CNES (TOSCA) through the ProVal project and from the remOcean (ERC Advanced Grant N∘246777).
Acknowledgments
We would like to thank Noé POFFA and Nathanaëlle LEBRETON from the Coriolis deployment team for their assistance during the acceptance tests and deployments of profiling floats. We thank colleagues from LOPS/TOIS and ship crews of the RV Thalassa, Atalante, Pourquoi Pas?, Sarmineto del Gamboa and Investigator, who were involved in the NAOS Deep-Arvor float deployment. We also thank the UMR 7159 - Laboratoire d’Océanographie et du Climat: Expérimentations et Approches Numériques (LOCEAN), a joint research unit under the supervision of Sorbonne Université, CNRS, IRD and the Muséum National d’Histoire Naturelle, and particularly Jean-Baptiste SALLEE and Antonio LOURENCO for involving us in the WAPITI project. We also thank the DT-INSU (CNRS) and the crews of the research vessels Sagitta and Téthys II for their support during the test campaigns in the Mediterranean. Thanks to Takuvik (Maxime Benoit-Gagné and Philippe Massicote) for providing us with SIC data, and Eric Rehm for his support in the first steps of ISA investigation. Many thanks to Colline Gombault (Amundsen Science) for providing CTD data collected in Baffin Bay by the Canadian research icebreaker CCGS Amundsen and dedicated to the ISA investigation. We thank Charles Villeneuve for his help during field trials of the CTS5-Payload in cold conditions at the “Foret Montmorency,” as well as Eric Brossier for his help and advice during field tests at the Green Edge ice camp in Nunavut. We also thank the Tara teams (Nicolas Bin) for their involvement and professionalism in the recovery of a Provor NOSS float under difficult conditions in the Mediterranean Sea, and the LOV teams for their support during the test campaigns. We also thank the CLS teams for their involvement in our Argos-3 experimentation, and for providing us with all the data necessary for our analysis, in complete transparency. We are also very grateful to all the technical and administrative teams at Ifremer, LOPS, LOV, Takuvik, SHOM, and nke instrumentation for their support in the design, qualification, testing, procurement and deployments of profiling floats, and to their scientific teams for their analysis of our instruments’ behavior at sea.
Supplementary Material
The Supplementary Material for this article can be found online at: https://www.frontiersin.org/articles/10.3389/fmars.2020.577446/full#supplementary-material
Footnotes
References
Amante, C., and Eakins, B. W. (2009). ETOPO1 1 Arc-Minute Global Relief Model: Procedures, Data Sources and Analysis. NOAA Technical Memorandum NESDIS NGDC-24. Washington, DC: National Geophysical Data Center, NOAA.
André, X., Moreau, B., and Le Reste, S. (2015). Argos-3 satellite communication system: implementation on the arvor oceanographic profiling floats. J. Atmos. Ocean. Technol. 32, 1902–1914. doi: 10.1175/JTECH-D-14-00219.1
Beitsch, A., Kaleschke, L., and Kern, S. (2014). Investigating high-resolution AMSR2 sea ice concentrations during the february 2013 fracture event in the beaufort sea. Remote Sens. 6, 3841–3856. doi: 10.3390/rs6053841
Bennett, A. S. (1971). The calibration of thermistors over the range 0 - 30°C. Deep Sea Res. 19, 157–163.
Biogeochemical-Argo Planning Group (2016). The Scientific Rationale, Design and Implementation Plan for a Biogeochemical-Argo Float Array. Brest: Ifremer.
Bittig, H. C., Maurer, T. L., Plant, J. N., Schmechtig, C., Wong, A. P. S., Claustre, H., et al. (2019). A BGC-argo guide: planning, deployment, data handling and usage. Front. Mar. Sci. 6:502. doi: 10.3389/fmars.2019.00502
Claustre, H., Johnson, K. S., and Takeshita, Y. (2020). Observing the global ocean with biogeochemical-argo. Annu. Rev. Mar. Sci. 12, 23–48. doi: 10.1146/annurev-marine-010419-010956
Curry, B., Lee, C. M., Petrie, B., Moritz, R. E., and Kwok, R. (2014). Multiyear volume, liquid freshwater, and sea ice transports through davis strait, 2004-10. J. Phys. Oceanogr. 44, 1244–1266. doi: 10.1175/JPO-D-13-0177.1
D’Ortenzio, F., Thierry, V., Eldin, G., Claustre, H., Testor, P., Coatanoan, C., et al. (2010). White Book on Oceanic Autonomous Platforms for Biogeochemical Studies: Instrumentation and Measure. Available at http://www.coriolis.eu.org/content/download/3150/23513/file/2009_PABIM_white_book_version1.3.pdf (accessed September 23, 2020).
Freeland, H., Roemmich, D., Garzoli, S. L., Le Traon, P.-Y., Ravichandran, M., Riser, S., et al. (2010). “Argo—A decade of progress,” in Proceedings of OceanObs’09: Sustained Ocean Observations and Information for Society, eds J. Hall, D. E. Harrison, and D. Stammer (Paris: ESA Publ).
Garzoli, S., Boebel, O., Bryden, H., Fine, R., Fukasawa, M., Gladyshev, S., et al. (2010). “Progressing towards global sustained deep ocean observations,” in Proceedings of OceanObs’09: Sustained Ocean Observations and Information for Society, eds J. Hall, D. E. Harrison, and D. Stammer (Paris: ESA).
IOCCG (2011). “Bio-optical sensors on argo floats,” in Reports of the International Ocean-Colour Coordinating Group, No. 11, ed. H. Claustre (Dartmouth: IOCCG).
Johnson, K. S., Jannasch, H. W., Coletti, L. J., Elrod, V. A., Martz, T. R., Takeshita, Y., et al. (2016). Deep-Sea DuraFET: a pressure tolerant pH sensor designed for global sensor networks. Anal. Chem. 88, 3249–3256. doi: 10.1021/acs.analchem.5b04653
Kelley, D. E. (2018). “The oce package,” in Oceanographic Analysis with R, ed. D. E. Kelley (New York, NY: Springer), 91–101.
Klatt, O., Boebel, O., and Fahrbach, E. (2007). A profiling float’s sense of ice. J. Atmos. Ocean Technol. 24, 1301–1308. doi: 10.1175/JTECH2026.1
Kolodziejczyk, N., Taillandier, V., Malardé, D., Le Reste, S., and Le Menn, M. (2019). Résultats des essais du capteur NOSS Campagne BioArgoMed - PERLE0. LOPS-NOSS-2019–2013. Markham: PERLE.
Lagunas, J., Marec, C., Leymarie, E., Penkerc’h, C., Rehm, E., Desaulniers, P., et al. (2018). Sea-ice detection for autonomous underwater vehicles and oceanographic lagrangian platforms by continuous-wave laser polarimetry. Ocean Sens. Monit. X 10631:106310W. doi: 10.1117/12.2309571
Le Menn, M. (2018). Calibration and temperature correction of a V-block refractometer. Meas. Sci. Technol. 29:3. doi: 10.1088/1361-6501/aa9b54
Le Menn, M., Albo, P. A. G., Lago, S., Romeo, R., and Sparasci, F. (2019). The absolute salinity of seawater and its measurands. Metrologia 56:1. doi: 10.1088/1681-7575/aaea92
Le Menn, M., Bougrenet de la Tocnaye, J. L., Grosso, P., Delauney, L., Podeur, C., Brault, P., et al. (2011). Advances in measuring ocean salinity with an optical sensor. Meas. Sci. Technol. 22:8. doi: 10.1088/0957-0233/22/11/115202
Le Reste, S., Dutreuil, V., André, X., Thierry, V., Renaut, C., Le Traon, P.-Y., et al. (2016). “Deep-Arvor”: a new profiling float to extend the Argo observations down to 4000m depth. J. Atmos. Ocean. Technol. 33, 1039–1055.
Le Traon, P. Y., D’Ortenzio, F., Babin, M., Leymarie, E., Marec, C., Pouliquen, S., et al. (2020). Preparing the new phase of Argo: scientific achievements of the NAOS project. Front. Mar. Sci. 7:577408. doi: 10.3389/fmars.2020.577408
Le Traon, P.-Y., Reppucci, A., Alvarez Fanjul, E., Aouf, L., Behrens, A., Belmonte, M., et al. (2019). From observation to information and users: the copernicus marine service perspective. Front. Mar. Sci. 6:234. doi: 10.3389/fmars.2019.00234
Leymarie, E., Penkerc’h, C., Vellucci, V., Lerebourg, C., Antoine, D., Boss, E., et al. (2018). ProVal: a new autonomous profiling float for high quality radiometric measurements. Front. Mar. Sci. 5:437. doi: 10.3389/fmars.2018.00437
Liu, G., Guo, L., Liu, C., and Wu, Q. (2018). Evaluation of different calibration equations for NTC thermistor applied to high-precision temperature measurement. Measurement 120, 21–27. doi: 10.1016/j.measurement.2018.02.007
MacLachlan, C., Arribas, A., Peterson, K. A., Maidens, A., Fereday, D., Scaife, A. A., et al. (2015). Description of GloSea5: the Met Office high resolution seasonal, forecast system. Q. J. R. Met. Soc. 141, 1072–1084. doi: 10.1002/qj.2396
MacMahon, M. M., and Rathburn, R. (2005). Measuring Latency in Iridium Satellite Constellation Data Services. US Naval Academy Report no: A291464. Available online at: http://dodccrp.org/events/10th_ICCRTS/CD/papers/233.pdf (accessed September 23, 2020).
Maine, K., Devieux, C., and Swan, P. (1995). “Overview of IRIDIUM satellite network,” Proceedings of WESCON’95 (San Francisco, CA), 483. doi: 10.1109/WESCON.1995.485428
Malardé, D., Wu, Z. Y., Grosso, P., de Bougrenet de la Tocnaye, J.-L., and Le Menn, M. (2009). High-resolution and compact refractometer for salinity measurements. Meas. Sci. and Tech. 20:015204. doi: 10.1088/0957-0233/20/1/015204
Millard, R. C., and Seaver, G. (1990). An index of refraction algorithm for seawater over temperature, pressure, salinity, density and wavelength. Deep Sea Res. 37, 1909–1926. doi: 10.1016/0198-0149(90)90086-B
OC SCOR and IAPSO (2010). “The international thermodynamic equation of seawater – 2010: calculation and use of thermodynamic properties,” in Proceedinsg of the Intergovernmental Oceanographic Commission, Manuals and Guides No. 56, (Paris: UNESCO).
Picheral, M., Guidi, L., Stemmann, L., Karl, D. M., Iddaoud, G., and Gorsky, G. (2010). The underwater vision profiler 5: an advanced instrument for high spatial resolution studies of particle size spectra and zooplankton. Limnol. Oceanogr. Methods 8, 462–473. doi: 10.4319/lom.2010.8.462
Prior-Jones, M. (2008). Satellite Communications Systems Buyer’s Guide. Cambridge, MA: British Antarctic Survey.
Randria Manotrona, A. (2018). Etude De Cas : AIRBUS-ONEWEB. Stratégie de Réaction Des Firmes en Place Face À l’arrivée De Nouveaux Entrants Dans Le Secteur Spatial. MBA thesis, Toulouse Business School, Toulouse.
Roemmich, D., Alford, M. H., Claustre, H., Johnson, K., King, B., Moum, J., et al. (2019). On the future of argo: a global, full-depth, multi-disciplinary array. Front. Mar. Sci. 6:439. doi: 10.3389/fmars.2019.00439
Riser, S. C., Freeland, H. J., Roemmich, D., Wijffels, S., Troisi, A., Belbeoch, M., et al. (2016). Fifteen years of ocean observations with the global Argo array. Nat. Clim. Change 6, 145–153. doi: 10.1038/nclimate2872
Sea-Bird Scientific (2017). Best Practices for Shipping and Deploying Profiling Floats with SBE41/41CP. Application Note 97. Bellevue, WA: Sea-Bird Scientific.
Sévellec, F., Colin de Verdière, A., and Ollitrault, M. (2017). Evolution of intermediate water masses based on argo float displacements. J. Phys. Oceanogr. 47, 1569–1586.
Simon, L., Malardé, D., and David, A. (2018). NOSS Optical Sensor, Automated Computation to Improve Accuracy of Absolute Salinity Concentration Measurement in Any Type of Seawater. Piscataway, NJ: OCEANS - MTS/IEEE Kobe Techno-Ocean.
Smith, G. C., Allard, R., Babin, M., Bertino, L., Chevallier, M., Corlett, G., et al. (2019). Polar ocean observations: a critical gap in the observing system and its effect on environmental predictions from hours to a season. Front. Mar. Sci. 6:429. doi: 10.3389/fmars.2019.00429
Steinhart, J. S., and Hart, S. R. (1968). Calibration curves for thermistors. Deep Sea Res. 15, 497–503.
Velpuri, S. B., Gunda, D., and Karri, S. (2014). Analyzation of ocean information through argos. Int. J. Eng. Res. Technol. 3, 2148–2155.
Woodward, B., Ortega, C., and Guigue, M. (2009). “Sustained Ocean Observations for 30 Years Using Argos,” in Proceedings of the OceanObs’09: Sustained Ocean Observations and Information for Society (Annex), Venice.
Zilberman, N., King, B., Purkey, S., Thierry, V., and Roemmich, D. (2019). Report on the 2nd Deep Argo Implementation Workshop. Hobart, May 13-15th 2019. Available online at: https://archimer.ifremer.fr/doc/00507/61873/ (accessed September 23, 2020).
Keywords: ocean, Argo, global observing system, profiling float, deep, biogeochemistry, under-ice, float technology
Citation: André X, Le Traon P-Y, Le Reste S, Dutreuil V, Leymarie E, Malardé D, Marec C, Sagot J, Amice M, Babin M, Claustre H, David A, D’Ortenzio F, Kolodziejczyk N, Lagunas JL, Le Menn M, Moreau B, Nogré D, Penkerc’h C, Poteau A, Renaut C, Schaeffer C, Taillandier V and Thierry V (2020) Preparing the New Phase of Argo: Technological Developments on Profiling Floats in the NAOS Project. Front. Mar. Sci. 7:577446. doi: 10.3389/fmars.2020.577446
Received: 29 June 2020; Accepted: 14 October 2020;
Published: 05 November 2020.
Edited by:
Ananda Pascual, Mediterranean Institute for Advanced Studies (IMEDEA), SpainReviewed by:
Sophie E. Cravatte, Institut de Recherche pour le Développement, FranceMilena Menna, Istituto Nazionale di Oceanografia e di Geofisica Sperimentale (OGS), Italy
Philip Bresnahan, University of California, San Diego, United States
Copyright © 2020 André, Le Traon, Le Reste, Dutreuil, Leymarie, Malardé, Marec, Sagot, Amice, Babin, Claustre, David, D’Ortenzio, Kolodziejczyk, Lagunas, Le Menn, Moreau, Nogré, Penkerc’h, Poteau, Renaut, Schaeffer, Taillandier and Thierry. This is an open-access article distributed under the terms of the Creative Commons Attribution License (CC BY). The use, distribution or reproduction in other forums is permitted, provided the original author(s) and the copyright owner(s) are credited and that the original publication in this journal is cited, in accordance with accepted academic practice. No use, distribution or reproduction is permitted which does not comply with these terms.
*Correspondence: Xavier André, eGF2aWVyLmFuZHJlQGlmcmVtZXIuZnI=