- Center for Corrosion and Biofouling Control, Florida Institute of Technology, Melbourne, FL, United States
The application of a proactive grooming program to manage the fouling control coatings applied to ship hulls provides an opportunity to address the climate crisis, invasive species and the discharge of biocides into the marine environment. A large percentage of the total power required to propel a ship is to overcome the viscous drag created between the hull and the water. The powering penalty due to increases in coating roughness and the development of biofouling are well documented. In addition, poorly maintained fouling control coatings may lead to the transportation of invasive species. In-water hull cleaning is therefore an important part of ship operations; however, this is typically implemented as a reactive measure when fouling reaches a critical level and requires powerful machinery which damages the coatings, creates unwanted discharge and in many locations the discharge will require capture and disposal. Ship hull grooming is being developed as a proactive method to manage fouling control coatings that will ensure that they are maintained in a smooth and fouling free condition, there is no transport of invasive species or excessive discharge of material that occurs during cleaning. This manuscript will summarize the findings of many years of research and development.
Introduction
The shipping industry is vital to trade, defense, and the world economy; however, it is under increasing pressure to reduce its environmental footprint in terms of CO2 emissions, as a point source for biocides used for the control of biofouling, and the transportation of invasive species (International Maritime Organization, IMO). Our findings from several years of research investigating the proactive underwater maintenance of fouling control coatings (grooming), has demonstrated that such an approach offers the potential to ensure that the major areas of a ship hull can be kept in a smooth and fouling free condition for the lifetime of the coating. This in turn will reduce the environmental footprint of a ship and costs in terms of fuel and wear on machinery.
There are many factors that determine how and when a ship hull is cleaned (Figure 1). These include:
• Vessel Specifics: the type of vessel, its schedule, utilization and speed
• Fouling Control Coatings: the type, condition and age of fouling control coating
• Environmental Conditions: physical and chemical properties of seawater and ecology.
In-water hull cleaning is routinely performed on ships in ports and harbors around the world, however, up until recently this has only been done using powerful devices as a reactive measure once fouling has reached significant levels (US Navy, 2006; United States Environmental Protection Agency [US EPA], 2011; McClay et al., 2015; Morrisey and Woods, 2015; Zabin et al., 2016; Song and Cui, 2020). This results in excessive discharges of paint and biofouling to the environment which may then require capture, treatment and disposal. It also damages the coating (Bohlander, 2009; Earley et al., 2014; Scianni and Georgiages, 2019; Oliveira and Granhag, 2020; Tamburri et al., 2020; BIMCO/ICS, 2021; Jones, 2021; Scianni et al., 2021). Ship hull grooming has been defined as “the gentle, habitual and frequent mechanical maintenance of submerged ships’ hulls in order that they remain free from extraneous matter such as fouling organisms and particulate debris, with minimal impact to the coating” (Tribou and Swain, 2010). The purpose of this paper is to review our findings and to place them in context with the requirements to reduce environmental impacts and improve the operational efficiency of ships.
Fouling control coatings are known to foul when a ship is subjected to prolonged periods of inactivity. In 2003 SeaRobotics submitted a proposal to the Office of Naval Research “The HullBUG, A miniature Underwater Vehicle for Cleaning Ship Hulls” (Holappa et al., 2013). In 2005, the Office of Naval Research funded a ship hull grooming program. The concept was to develop fully autonomous vehicles that would proactively maintain fouling control coatings free of fouling (Figure 2).
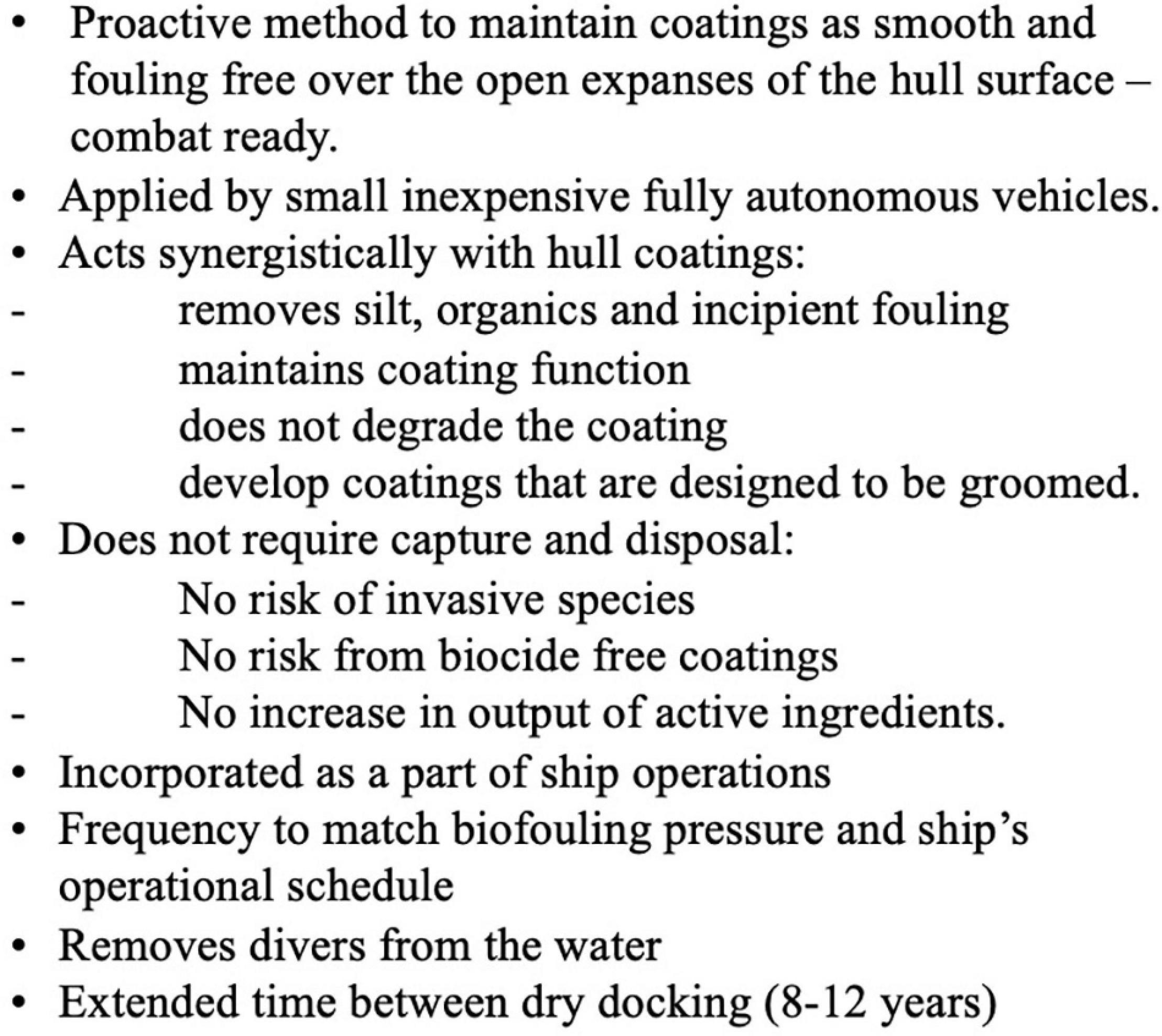
Figure 2. Concepts for the development of a fully autonomous ship hull grooming vehicle (Swain et al., 2020).
Early research on small sized test panels demonstrated that proactive in water grooming may provide an effective method to prevent fouling (Tribou and Swain, 2010). This led to the construction of a large-scale test facility at Port Canaveral, Florida to develop and demonstrate the technology. It also found that the requirements for the grooming method were different for the biocide and biocide free systems (Figure 3). The performance of biocide-based systems is enhanced by a grooming method that maintains the active ingredient at a level that prevents fouling without causing excessive discharge into the environment (Swain and Tribou, 2014; Tribou and Swain, 2017). The performance of the fouling release coatings is enhanced by a grooming method that provides sufficient force to remove the fouling without damaging the surface.
Background
This research focused on the coating types and operational schedule of US Navy ships. About 96% of the US Navy ships are coated with copper ablative antifouling (AF) paint and the rest with copper free coatings including some fouling release systems. The majority of ships spend 40–60% of their time pier-side and this makes them vulnerable to fouling (Martin and Ingle, 2012). According to Chapter 081 of the Naval Ships’ Technical Manual (Supplementary Table 1) a full hull clean for ablative and self-polishing paints will be required when a fouling rating of FR-40 or greater exists over 20 percent of the hull, exclusive of docking block areas and appendages. The fouling release coatings are treated differently and when a fouling rating of FR-50 or greater is observed over 10 percent of a hull NAVSEA Code 00C are contacted for cleaning advice. The challenges of waiting until the ship becomes covered by calcareous fouling before cleaning are that the ship is already operating with a drag penalty, that cleaning will require fairly high forces that may damage the coating and that the calcareous shells may become entrapped by the cleaning device causing further damage. Schultz et al. (2011) concluded that savings as high as $12 million/ship over a 15-year period could be achieved for the US Navy fleet of DDG-51 destroyers if the hull condition was maintained at a fouling rating of 10. Our research has demonstrated that regular grooming of BRA640 and IS1100 is able to maintain these coatings at a Navy Ship Technical Manual fouling rating of 0.
The findings from this study may also be used to help better manage the fouling control coatings of commercial shipping. Seaborne trade and the number of ships that are operating in the marine environment has increased dramatically in the last 50 years. According to the United Nations Conference on Trade and Development (2020) e-Handbook of Statistics the international seaborne trade grew from 2,605 million tons loaded in 1970 to 11,083 million tons in 2019. In 2019 there were 52,961 commercial ships with flags of registration of 1,000 GT and above. The environmental impacts from this number of vessels and the associated ports and harbors are enormous and the industry is now facing increased regulations to reduce harm to the environment. One option to lessen these impacts is by the improved selection and management of fouling control coatings (Swain, 2017). The condition and treatment of these surfaces have a significant impact on the power required to move a vessel (CO2 emissions), the release of active ingredients to control fouling (biocides) and the transfer of marine organisms to new locations (invasive species).
Large Scale Test Facility
A large-scale seawater test facility was constructed in 2012 at Port Canaveral to evaluate the technology, provide a scientific understanding of the grooming process and to enable the development of grooming tools (Figure 4). The Port is subtropical and has year-round biofouling (Figure 5). The test surfaces were constructed from three 2.4 m × 4.57 m × 6.35 mm thick steel plates that were welded to 0.76 m diameter steel pipe for floatation. These were bolted together to form a continuous length of 13.7 m. The structures were coated with Intergard 264 epoxy anticorrosive paint and a topcoat of either Interspeed BRA 640 (BRA640) copper polishing or Intersleek 1100SR (IS1100) fouling release coating from Akzo Nobel. The steel pipes provided floatation and the panels were suspended vertically representing the vertical sides of a ship. A 10.4 m Mainship trawler acted as a control center for the grooming vehicle and was moored adjacent to the pipe. The fouling control surfaces were groomed on a weekly basis and ungroomed areas acted as controls. The panels were inspected by divers and periodically, the panels were rotated to the horizontal position to enable visual inspection, dry film thickness and roughness measurements.
Grooming Method
There are several different categories of cleaning devices available to remove biofouling from underwater surfaces (Akinfiev et al., 2007; Curran et al., 2016; Song and Cui, 2020). The concept for grooming required the design and fabrication of specialized tools that were engineered to apply the minimum force required to remove incipient fouling and biofilms without damaging the surface. Because the concept is to eventually develop fully autonomous vehicles the grooming tool was also designed to minimize power demands. Prior research guided our choice to favor small diameter (about 102 mm) vertically rotating brushes rotating at between 300 to 600 rpm (Wathen, 1994; Schumacher, 1996; Harper, 2014). The brush rotation creates a low pressure in the entrapped water which causes suction forces and holds the brush to the surface. The vertical forces applied to the coating are controlled by the arrangement of the brush elements and the speed of rotation (Harper, 2014; Tribou, 2015; Erdogan, 2016). The variables included in grooming tool design are many and include: brush element material and size, element arrangement and mode of operation. For the grooming trials presented in this paper we used a 102 mm diameter hub populated with an outer and inner row of 24 tufts of nylon bristles. The grooming tool consisted of five brushes arranged with a slight overlap to give a swath of 560 mm and propelled by a remotely operated vehicle (SeaBotix vLBV). The vehicle was driven at about 0.25 m/s in a lawn mower pattern and a 50% overlap was visually maintained on reciprocal runs. Under these conditions an area of about 250 m2 can be groomed each hour and it would therefor take about 12 h to groom an Arleigh Burke class destroyer (DDG-51) with a wetted surface area of ∼3000 m2.
Long-Term Grooming Performance
To demonstrate the effectiveness of a grooming program the results from two long-term grooming studies and one cleaning study applied to Interspeed BRA640 and Intersleek 1100SR are presented (Swain et al., 2020). They follow the changes in biofouling, coating condition, dry film thickness (Elcometer digital coating thickness gauge) and roughness (TQC Hull Roughness Analyzer) for the duration of the deployment. Other results from grooming research have been published by Tribou and Swain (2010, 2015, 2017) and Hearin et al. (2015, 2016).
Interspeed BRA640
The BRA640 coating was subjected to weekly grooming for a period of 54 months (Figure 6). The groomed surfaces were maintained free of fouling, however, the ungroomed surfaces became fouled. The fouling included: biofilms, encrusting bryozoans, arborescent bryozoans, barnacles, tubeworms and colonial tunicates. The ungroomed surfaces were cleaned by divers using scrapers and brushes when the fouling rating reached FR-40 or greater over 20 percent of the surface (at 8, 14, 23, 30, 36, 47, and 54 months) and three times during dry dockings due to hurricane evacuations from the port.
The panels were inspected in the horizontal position at 12, 24, 33, 35, and 48 months immersion. Average dry film thickness measurements (DFT) showed a steady reduction which was similar for both the groomed and ungroomed surfaces (Figure 7). The change in DFT was used to calculate average copper output using the mass balance method presented in ISO 10890 (2010): Paints and varnishes – Modeling of biocide release rate from antifouling paints by mass-balance calculation (Table 1). The technical data for the BRA640 applied to the panel was as follows: % mass content of cuprous oxide 41.79; mass fraction of biocide in biocidal ingredient 0.86; density of paint 2.26 g/cm3; volume solids content of paint 58.03. The average copper release rate was calculated to be 11μg/cm2/day.
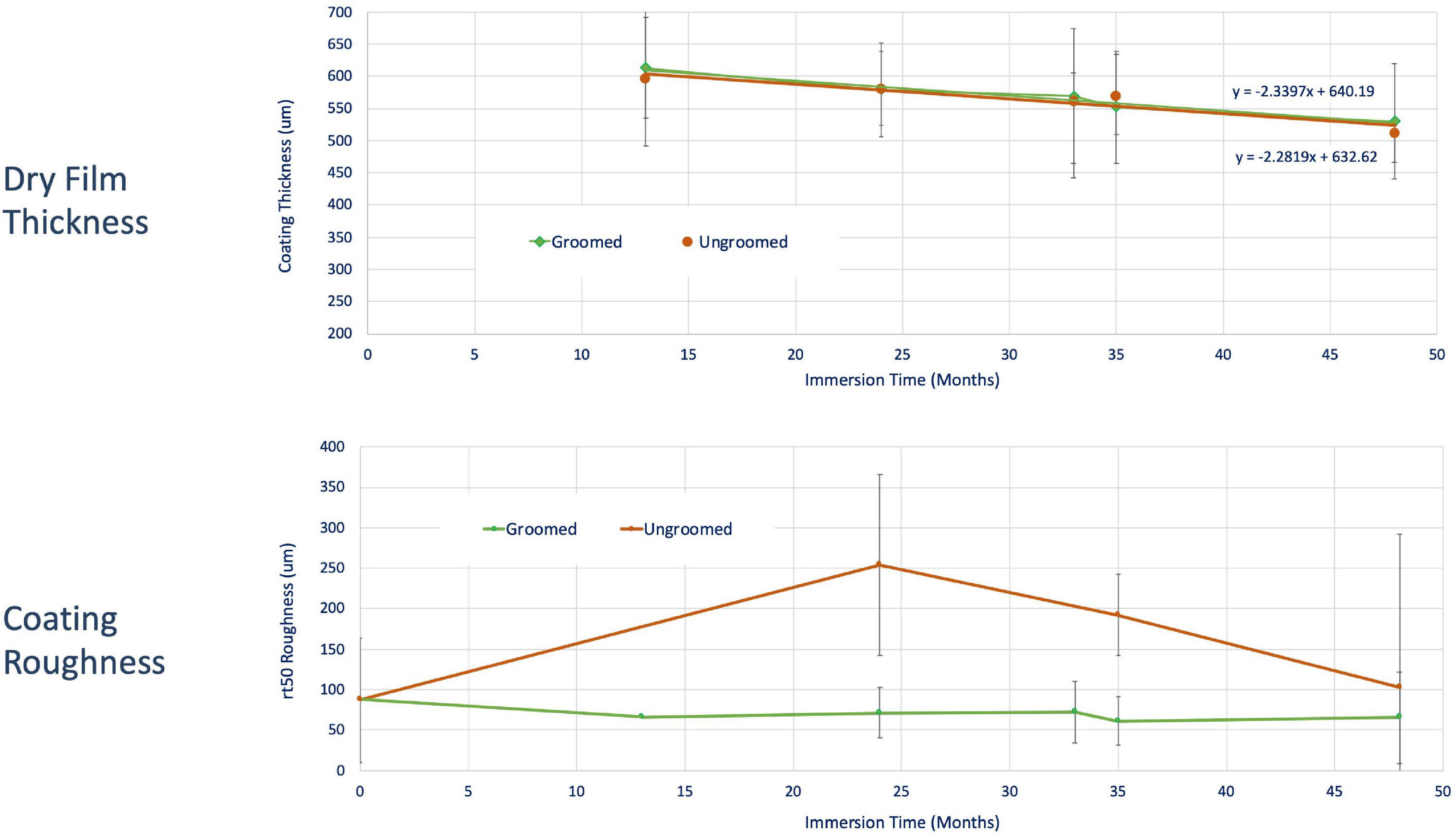
Figure 7. Change in dry film thickness and coating roughness for BRA640 during a 54 months deployment.
Coating roughness measurements using the hull roughness analyzer demonstrated that the groomed surfaces became smoother (average roughness decreased from about 90 to 70 microns). The ungroomed coatings increased in roughness due damage to the coating caused by cleaning and remains of fouling that was not totally removed.
Intersleek 1100SR
The IS1100 was groomed weekly for a period of 33 months (Figure 8). The groomed panel remained free of fouling except for occasional patches of tenacious biofilm and encrusting bryozoans that were removed during subsequent grooming sessions. The prevention of these types of fouling has been solved by modifying the brush design to better interact with the fouling release coatings. The ungroomed panel became fouled and required diver cleaning after 18 and 30 months. Another cleaning occurred during dry docking in October 2016 due to a hurricane. The fouling included: biofilms, encrusting bryozoans and tubeworms.
The panels were inspected in the horizontal position after 12, 24, 33, and 35 months immersion (Figure 9). Average dry film thickness values showed no significant difference during the immersion period. There was no significant change in coating roughness, however, the presence of small nicks in the coating caused by fish feeding on the fouling caused an increase in the standard deviation after 24 months. This was greater on the ungroomed surface and was attributed to fish feeding on the more abundant fouling.
Cleaning
BRA640 and IS1100 coated steel panels were left to foul over a one-year period and then subjected to diver cleaning. The BRA640 was heavily encrusted with barnacles, tubeworms and encrusting bryozoans and had a fouling rating of 90% FR100 and 10% FR30 (Figure 10). The IS1100 was not as heavily fouled including mainly biofilms, encrusting bryozoans and a few tubeworms with a fouling rating of 40% FR100 and 60% FR30.
The BRA640 was initially cleaned with a rotating polypropylene brush, but this was unable to remove the barnacle base plates and so a wire brush was applied. This removed most of the antifouling coating which had a DFT of about 150 microns. The removal of 150 microns DFT BRA640 would release 0.2 kg copper/m2 into the water.
The IS1100 was cleaned using the polypropylene brush. This removed most of the fouling, however, a small amount of biofilm remained, and some damage occurred to the coating where the brush filaments were allowed to dig into the coating and where calcareous fouling became entrapped in the brush causing damage to the coating before being ejected.
Whilst both these coatings were fouled at a much greater level than would normally be allowed, the damage to both the BRA640 and the IS1100 coatings caused by the brush forces required to remove established biofouling demonstrated the negative impacts of a reactive ship hull cleaning program. The force required to remove a fouling organism is a function of the adhesion strength and the base area (Swain et al., 1994, 2007; Swain, 1996; Zargiel et al., 2011; Zargiel and Swain, 2014). A comparison of the typical force required to remove barnacles of increasing base diameter from a silicone fouling release surface, copper base antifouling, epoxy and cathodically protected bronze are presented in Figure 11. It not only demonstrates how different surfaces require different cleaning forces but also the exponential relationship between increasing barnacle diameter and the force required for removal. This emphasizes the importance of removing barnacles at an early stage which requires less force and prevents damage to the coating.
Grooming and Commercial Fouling Control Coatings
Whilst most of our research has focused on two US Navy qualified fouling control coatings (BRA640 and IS1100) we ran a one-year deployment of several commercial fouling control coatings (Figure 12). These were 150 × 300 mm panels of which one set were groomed once a week and the other set left to foul. All the groomed panels were kept free of fouling and only the copper free coating, which was very soft, showed signs of accelerated depletion due to grooming.
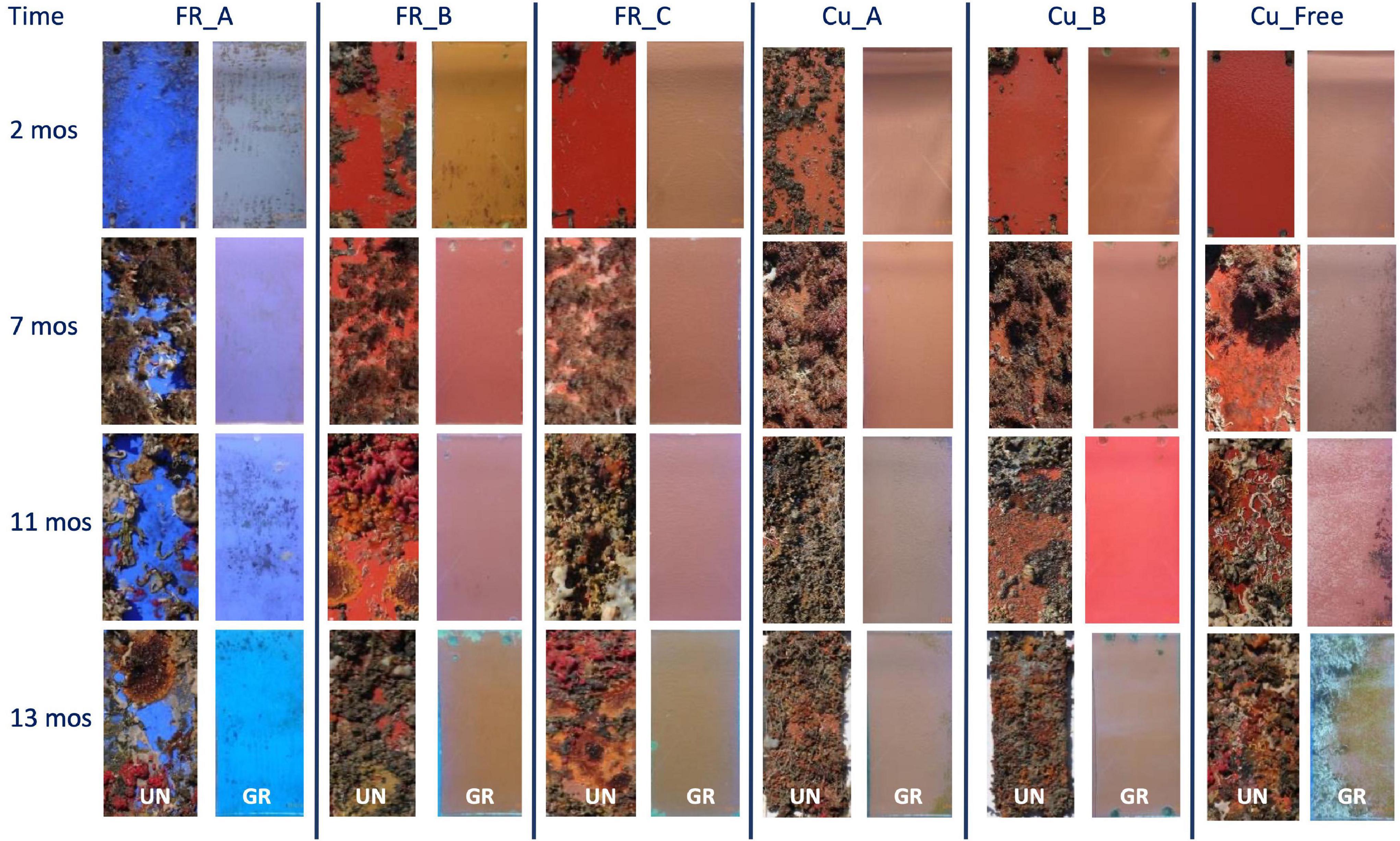
Figure 12. The progression of fouling on three fouling release coatings and three biocide-based coatings subjected to static immersion: ungroomed vs. groomed once a week.
Discussion
Long-term deployment of both biocide and fouling release coatings under static immersion in a location with high fouling pressure has demonstrated that a well-managed grooming program will maintain the coatings clear of fouling without damage or roughening of the surface. The adoption of a proactive inwater cleaning program has the ability to reduce greenhouse gas emissions, prolong the service life of fouling control coatings, reduce the point source discharge and the need for capture created by costly reactive cleaning programs and prevent the transport of invasive species.
Greenhouse Gas Emissions
The International Maritime Organization (2020a) Fourth Greenhouse Gas Study estimates that international shipping contributed about 2.89% of global greenhouse gas emissions or 1,076 million tons in 2018. The power to move a ship must overcome residuary resistance (which includes wave making resistance, form resistance, eddy resistance, and frictional form resistance) and frictional resistance. The frictional resistance may contribute between 40–90% of the power to move a ship. The contribution of frictional resistance for high-speed ships (cruise liners, passenger ships and navy vessels) will be less than for low-speed vessels (bulk carriers and tankers) (MAN B&W, 2004). The friction drag is a function of the seawater viscosity, the velocity gradients that develop in the boundary layer and the surface roughness. Surface imperfections in the form of coating roughness, weld beads, hull plate corrosion and biofouling all increase turbulence and mixing in the boundary layer which increases drag (Redfield and Hutchins, 1952; Townsin et al., 1981; Schultz, 2004, 2007; Swain, 2010). The absolute penalties incurred by hull roughness and biofouling are difficult to predict due to differences in hull form, hull speed and the heterogeneous nature of the hull condition and biofouling. However, assuming uniform roughness or biofouling Schultz (2007) developed a table that relates the hull condition to equivalent sand roughness height and maximum peak to trough height over a 50 mm sample length and applied them to the powering penalties for a 136 m long Oliver Hazard Perry class frigate (FFG-7) (Supplementary Table 1). These may be used to estimate the percent increase in viscous drag due to the hull condition. The data clearly demonstrates the importance of paying attention to everything from coating roughness (as applied 2% increase in resistance) the development of a biofilm or slime layer (11–21% resistance) and heavy calcareous fouling (86% resistance). According to the US Navy Technical Manual for Waterborne Underwater Cleaning of Navy Ships (2006) the decision to initiate a hull cleaning operation is based on the results of precleaning hull inspections. If a fouling rating of FR-50 or higher (over 10 percent of the hull) is observed for non-ablative paints or FR-40 (over 20 percent of the hull) higher for ablative and self-polishing paints (exclusive of docking block areas and appendages) is observed then a full hull cleaning is required. According to Schultz et al. (2011) this hull condition would increase the resistance of an Arleigh Burke-class destroyer (DDG-51) by 29 and 19% at speeds of 7.7 and 15.4 m s–1, respectively, compared to the hydraulically smooth condition.
There are very few publications that provide information on the outer hull condition of the worlds fleet as most data are privy to the ship owners and paint industry. Munk et al., 2009 estimated that 1/3rd all vessels were in good condition, <20% added resistance; 1/2 all vessels in reasonable condition, 20–40% added resistance and the remainder in poor condition, >50% added resistance. More recently the Safinah Group published their findings for drydock inspections of nearly 270 ships where they found that 40% of ships had more than 20% hard fouling on the flats and that 10% of ships had more than 40% of their underwater area covered by hard fouling (Mihaylova, 2020). Clearly a significant reduction in fuel consumption and CO2 emissions can be gained by improving the maintenance of fouling control coatings.
From a global perspective, if the underwater portion of all the worlds shipping could be maintained in a smooth and fouling free condition, then the reduction in CO2 and other exhaust gasses would be significant. Taking the estimates for CO2 emissions from ships as 1,056 million tons/year (International Maritime Organization, 2020a) and assuming the average contribution of power from frictional resistance to move a ship is 70%, then using the estimated hull condition from Munk et al., 2009, we can estimate the reduction in CO2 emissions if all vessels were maintained in a smooth and fouling free condition: 1,056 million tons/year × 0.7 friction resistance × [(33% ships with a 10% penalty) + (50% ships with 30% penalty) + (17% ships with 50% penalty)] = 198 million tons of CO2 or 19% reduction of ship emissions.
Such calculations cannot be viewed as absolute but are presented as a demonstration of the importance of proactively managing the ship hull condition.
Point Source Discharge
Most fouling control surfaces use active ingredients to prevent biofouling. For most coatings this is the form of biocides which are incorporated into the paint and designed to be continually released at the minimum rate to prevent marine growth (Swain, 1999; Martins et al., 2020). These may reach concentrations in the water column or accumulate in sediments at levels that have a negative impact on marine life. This was a major setback for the biocide tributyltin which in the 1970s was being used as a very successful ingredient in antifouling paints (Champ, 2003; Dafforn et al., 2011). However, by the 1980s it was found to be negatively impacting non-target species at levels of less than 0.05 μg L–1 (Laughlin and Linden, 1987) and ultimately the IMO introduced international regulations that prohibited its use (International Maritime Organization, 2008).
Copper has been successfully used in antifouling paints since the middle 1800s (Laidlaw, 1952) and today about 96% of the US Navy’s fleet and 90% of the worlds ships use copper-based systems (Blossom, 2018). Copper is a naturally occurring element and required in trace amounts as a micronutrient. However, copper input from antifouling paints in areas of high boating activity may cause copper concentrations to reach undesirable levels (Srinivasan and Swain, 2007) and the National Recommended Water Criteria (USA) lists copper as a priority pollutant with recommended dissolved copper concentrations in the marine environment not to exceed 4.8 μg/l or an instantaneous concentration of 30 μg/l (Valkirs et al., 1994; United States Environmental Protection Agency [US EPA], 2016). The challenge to the chemist is to formulate the paint so that it releases the active ingredients at the minimum rate to prevent fouling under all service conditions of the ship. The minimum release rates for copper to prevent fouling has been quoted as between 10 to 20 μg/cm2/day (Barnes, 1948) and 16 to 22 μg/cm2/day (de la Court, 1988, 1989) to prevent barnacle and algal fouling, respectively (Swain, 2010). Actual release rates are highly variable (Seligman and Zirino, 1998; Haslbeck and Ellor, 2005; Haslbeck and Holm, 2005; Finnie, 2006) due to factors such as the type and age of paint, the ship activity and environmental conditions. Blossom (2002) estimated the annual copper input from all antifouling paints to be about 15x106kg/yr. Our estimate for 120,000 active commercial ships (including those < 100 gross tons) in the world fleet with an approximate wetted surface area of 325 × 106 m2 (Moser et al., 2016) and assuming an average copper leaching rate of 10 μg Cu cm–2 day–1 is:
10 μg Cu/cm2/day × 325 × 106 m2 × 0.9 × 365 days/year × 10,000 cm2/m2 × 10–9 kg/μg = 10.7×106 kg copper/year.
One of the challenges to managing a biocide-based coating is if the release rates drop below the threshold to prevent fouling, and the coatings become fouled. According to the US Navy Ship Technical Manual, the decision to clean ablative and self-polishing coatings is made when a fouling rating of 40 (Supplementary Table 1) or greater, is observed over 20 percent of the hull, exclusive of docking block areas and appendages. This will be done with the least aggressive method, however, experience has shown that the forces required to remove fouling, especially barnacle base plates, from a biocide based coating require vigorous cleaning that leads to coating loss and damage (United States Environmental Protection Agency [US EPA], 2011; Morrisey et al., 2013; Earley et al., 2014; Scianni and Georgiages, 2019; Tamburri et al., 2020). According to Morrisey et al. (2013) light cleaning may remove up to 650 μg Cu cm–2 and aggressive cleaning up to 3,290 μg Cu cm–2. This is a lot less than our observations for cleaning the BRA640 using a wire brush where up to 150 microns DFT coating were removed. This would be equivalent to 21,000 μg Cu cm–2. Using these numbers then the aggressive cleaning of a very large ship with an underwater surface area of 10,000 m2 (a 300+m cruise or container ship) may theoretically release between 329 to 2,100 kg of copper.
Whilst the environmental effects of copper are well understood, most copper-based paints also contain co-biocides to improve their performance. These may include: copper pyrithione, copper thiocyanate, cybutryne, dichlorooctylisothiazolinone, dichlorofluanid, medetomidine, tolylfluanid, tralopyril, zinc pyrithione, and zineb (Martins et al., 2020). The long-term environmental effects of these additives are less well understood. For example the co-biocide cybutryne (Irgarol-1051) may be added to paint at a weight percent of 2.3%. This may give a release rate of 2 μg cybutryne/cm2/day (Netherlands, 2014) and environmental monitoring has shown it to be persistent in the environment and reach levels that are harmful to corals and other organisms (Owen et al., 2002; Sheikh et al., 2016). This has caused the IMO to a draft amendment to prohibit anti-fouling systems containing cybutryne (also known under its industry name Irgarol-1051) to apply to ships from January 1, 2023 (International Maritime Organization, 2020b).
Invasive Species
The translocation of species to new areas by biofouling on ships has long been recognized as a problem (Lewis, 2020) and this is recognized as one of the primary vectors of non-indigenous species (Hewitt and Campbell, 2010). It has been estimated that 60% California’s non-indigenous species and 80% of those present in New Zealand were transported by ship hull fouling (Kospartov et al., 2008; Ruiz et al., 2011; Miller et al., 2018; Scianni and Georgiages, 2019). One of the benefits of grooming is that a clean hull will not transport invasive species (Hunsucker et al., 2018a,b,c). They used the BRA640 and IS1100 associated with the long-term grooming study to record the presence and abundance of the non-indigenous organisms on the groomed versus ungroomed coatings. They found that non-indigenous species such as the Asian green mussel (Perna viridis), the striped acorn barnacle (Balanus amphitrite), arborescent bryozoan (Bugula neritina), calcareous tubeworm (Hydroides elegans), encrusting bryozoan (Watersipora subtorquata complex), and a filamentous bryozoan (Zoo-botryon verticillatum) recruited to the ungroomed coatings. None were present on the groomed surfaces. This demonstrates the benefits of a biofouling management strategy that incudes grooming.
The benefits of grooming or proactive cleaning to prevent the spread of invasive species is obvious, however, it must be remembered that robotic underwater cleaning of a ship hull is at present only applicable to the large open areas of a hulls’ surface. This leaves small portions of the hull and niche areas that will still need intervention by divers to remove fouling.
Summary
Large scale testing of an ROV equipped with a grooming tool has demonstrated that grooming (proactive, frequent light cleaning) can maintain fouling control coatings in a smooth and fouling free condition for extended periods without causing increases in the discharge of active ingredient into the environment. The practical and economic application of a successful grooming program for ships will require investment in new technology, hardware and a better understanding of the biofouling sequence in terms of ship operational schedules and fouling control coatings. It will require the development of inexpensive and reliable remotely operated or autonomous vehicles to move the grooming tool over the ship hull. Grooming tools will need to be designed to match the forces required to remove the fouling without causing excessive wear or damage to the coating. The hardness and durability of the major types of coatings must be matched to the grooming method. A guide to geographical and seasonal biofouling pressures and composition needs to be developed so that a digital twin may be linked to a ships’ schedule and coating system to predict how and when grooming should occur. The development of such systems is now being considerd by several research teams and commercial companies. These include: Greensea (Kinnaman, 2019, 2020; Kyritsis and Arapkoules, 2021); Jotun SeaSkater (Oftedahl and Skarbø, 2021); International Paint Intertrac®HullCare and SeaRobotics. As these systems mature, so the costs and availability to the shipping community should provide commercially viable methods to apply proactive in water hull maintenance. This will reduce the environmental footprint and financial costs of shipping.
Author Contributions
GS: principal investigator. HG and JH: research engineer. KH, ER, AS, and MT: research scientist. CE, LF, MH, JTH, KL, MN, BW, and AW: grad student.
Conflict of Interest
The authors declare that the research was conducted in the absence of any commercial or financial relationships that could be construed as a potential conflict of interest.
Publisher’s Note
All claims expressed in this article are solely those of the authors and do not necessarily represent those of their affiliated organizations, or those of the publisher, the editors and the reviewers. Any product that may be evaluated in this article, or claim that may be made by its manufacturer, is not guaranteed or endorsed by the publisher.
Acknowledgments
We would like to acknowledge the support from the Office of Naval Research (N00014-10-1-0919, N00014-16-1-3050, and N6833518C01471) and the program managers, Stephen McElvany and Paul Armistead. Also, the many people who have been directly involved or contributed to the work. Don Darling, Ken Hollopa, Ben Lovelace (SeaRobotics); Ben Kinnaman, Karl Lander, and James Truman (Greensea); Liz Haslbeck, Bill Hertel, Eric Holm, Matt Naiman, (NSWC) Tom McCue (NAVSEA), and the staff at Cape Marina.
Supplementary Material
The Supplementary Material for this article can be found online at: https://www.frontiersin.org/articles/10.3389/fmars.2021.808549/full#supplementary-material
Supplementary Table 1 | Combing the fouling rating (RT) as given in the US Naval Ships’ Technical Manual with the equivalent sand grain roughness height (ks) and average coating roughness RT50 from Schultz (2007).
References
Akinfiev, T., Alexander, J., and Lavendelis, E. (2007). A brief survey of ship hull cleaning devices. Trans. Eng 7, 2007–2024.
Barnes, H. (1948). Studies on anti-fouling compositions. Part IV. The relationship between leaching rate, copper loss, and anti-fouling performance, under raft and service conditions. J. Iron. Steel Inst. 159, 175–185.
BIMCO/ICS (2021). Industry Standard on in-Water Cleaning With Capture. V1.01. Available online at: www.bimco.org/-/media/bimco/ships-ports-andvoyage-planning/environmentprotection/biofouling/2021-industry-standard-inwater-cleaningfinal.ashx?rev=7e4ea382b7864d59951bf53f6595e4b2
Blossom, N. (2002). 11th International Congress on Marine Corrosion and Fouling. Session: Copper for Biofouling Control. July 22–26 July 2002. San Diego, CA.
Blossom, N. (2018). Use of copper-based antifouling paint: A U.S. regulatory update. CoatingsTech 15:3.
Bohlander, J. (2009). Review of Options for In-water Cleaning of Ships. MAF Biosecurity New Zealand Technical Paper No. 2009/42. New Zealand: Border Standards Directorate Operations Standards and Facilities Group MAF Biosecurity, 34.
Champ, M. A. (2003). Economic and environmental impacts on port and harbors from the convention to ban harmful marine anti- fouling systems. Mar. Pollut. Bull. 46, 935–940. doi: 10.1016/S0025-326X(03)00106-1
Curran, A., O’Connor, B., Lowe, C., and King, E. (2016). Analyzing the Current Market of Hull Cleaning Robots. Washington, DC: United States Coast Guard, Project Center.
Dafforn, K., Lewis, J., and Johnston, E. (2011). Antifouling strategies: history and regulation, ecological impacts and mitigation. Mar. Pollut. Bull. 62, 453–465. doi: 10.1016/j.marpolbul.2011.01.012
de la Court, F. H. (1988). “The minimum leaching rate of some toxins from antifouling paints required to prevent settlement of fouling organisms,” in Biodeterioration 7, eds D. R. Houghton, R. N. Smith, and H. O. W. Eggins (London: Elsevier Applied Science), 305–308. doi: 10.1007/978-94-009-1363-9_40
de la Court, F. H. (1989). “Appendix 4.G. – Fouling and anti-fouling,” in Ship Painting Manual, ed. A. M. Berendsen (London: Graham & Trotman), 160–166.
Earley, P., Brandon, L., Barbeau, S. K., Bundy, R., McDonald, J. A., and Rivera-Duarte, I. (2014). Life cycle contributions of copper from vessel painting and maintenance activities. Biofouling 30, 51–68. doi: 10.1080/08927014.2013.841891
Erdogan, C. (2016). The Design of an Articulating Five-Headed In-water Grooming Tool to Maintain Ships Free of Fouling. Masters thesis. Melbourne, FL: Ocean Engineering. Florida Institute of Technology.
Finnie, A. (2006). Improved estimates of environmental copper release rates from antifouling products. Biofouling 22, 279–291. doi: 10.1080/08927010600898862
Harper, M. (2014). Optimized Brush Design for Grooming and Vehicle Attachment. Masters thesis. Melbourne, FL: Ocean Engineering. Florida Institute of Technology.
Haslbeck, E., and Ellor, J. A. (2005). Investigating tests for antifoulants: variation between laboratory and in situ methods for determining copper release rates from navy-approved coatings. J. Protect. Coat. Linings 2005, 34–44.
Haslbeck, E., and Holm, E. R. (2005). Standard methods: tests on leaching rates from antifouling coatings reveal high level of variation in results among laboratories. Eur. Coat. J. 2005, 26–31.
Hearin, J., Hunsucker, K., Swain, G., Gardner, H., Stephens, A., and Lieberman, K. (2016). Analysis of mechanical grooming at various frequencies on a large-scale test panel coated with a fouling-release coating. Biofouling 32, 561–569. doi: 10.1080/08927014.2016.1167880
Hearin, J., Hunsucker, K., Swain, G., Gardner, H., Stephens, A., Lieberman, K., et al. (2015). Analysis of long-term mechanical grooming on large-scale test panels coated with an antifouling and a fouling-release coating. Biofouling 3, 625–638. doi: 10.1080/08927014.2015.1081687
Hewitt, C., and Campbell, M. (2010). The relative contribution of vectors to the introduction and translocation of marine invasive species, Report commissioned by The Australian Department of Agriculture. Fisher. For. 10:42.
Holappa, K. W., Darling, D. T., and Hertel, W. M. III (2013). Robotic Submersible Cleaning System. U.S. Patent No. 8506719. Washington, DC: U.S. Patent and Trademark Office, 4–5.
Hunsucker, K. Z., Ralston, E., and Swain, G. (2018a). “Specialized grooming as a mechanical method to prevent marine invasive species recruitment and transport on ship hulls,” in Coasts in Crisis: Invasive Species Impacts That Degrade Coastal Environments. Coastal Education and Research Foundation, eds C. Finkl and C. Makowski (Berlin: Springer). doi: 10.1007/978-3-319-91382-7_7
Hunsucker, K., Braga, C., Erdogan, C., Gardner, H., Hearin, J., Ralston, E., et al. (2018b). The Advantages of Proactive in Water Hull Grooming From a Biologists Perspective. Redworth: HullPIC.
Hunsucker, K., Vora, G., Travis Hunsucker, J., Gardner, H., Leary, D., Kim, S., et al. (2018c). Biofilm community structure and the associated drag penalties of a groomed fouling release ship hull coating. Biofouling 34, 162–172. doi: 10.1080/08927014.2017.1417395
International Maritime Organization (2008). International Convention on the Control of Harmful Anti-fouling Systems on Ships International Maritime Organization 4 Albert Embankment. London: International Maritime Organization.
International Maritime Organization (2020a). Fourth Greenhouse Gas Study. London: International Maritime Organization.
International Maritime Organization (2020b). Marine Environment Protection Committee (MEPC). November. The Control of Harmful Anti-Fouling Systems on Ships (AFS Convention), to Include Controls on the Biocide Cybutryne, Vol. 75. London: International Maritime Organization, 16–20.
ISO 10890 (2010). Paints and Varnishes —Modelling of Biocide Release Rate From Antifouling Paints by Mass-Balance Calculation. Geneva: ISO.
Jones, E. (2021). Summary – Testing of Reactive In-water Cleaning Systems for Removal of Vessel Biofouling. Biosecurity New Zealand Technical Paper No: 2021/11. New Zealand: Biosecurity.
Kinnaman, B. (2019). The Future of Autonomous Robotic Hull Grooming, Maritime Reporter and Engineering News, March.
Kinnaman, B. (2020). Greensea’s New Ship Hull Crawler Tech Launches With VideoRay Defender, Marine Technology News, April.
Kospartov, M., Inglis, G., Seaward, K., Van den brink, A., D’ Archino, R., and Ahyong, S. (2008). Nonindigenous and Cryptogenic Marine Species in New Zealand – Current State of Knowledge: Interim Report. NIWA Research Report Prepared for MAF-BNZ Project BNZ10740. Wellington: NIWA.
Kyritsis, D. A., and Arapkoules, N. (2021). “RAGS – robotic applications for grooming and (In-water) survey,” in Proceedings of the 2nd Port In-Water Cleaning Conference PortPIC’21, Pontignano.
Laidlaw, F. B. (1952). “History of the prevention of fouling,” in Marine Fouling and Its Prevention Ch 11 Contribution No. 580 Woods Hole Oceanographic Institute, (Massachusetts: Woods Hole).
Laughlin, R. B., and Linden, O. (1987). Tributyltin – Contemporary and environmental issues. Ambio 16, 252–256.
Lewis, J. (2020). “Invasive species,” in Environmental Impact of Ships (Cambridge: Cambridge University Press). doi: 10.1017/9781108381598.008
Martin, F., and Ingle, M. (2012). Shipboard Coatings Developments and Emerging Surface Technologies. Sustainable Surface Engineering for Aerospace and Defense Workshop. Aug 31-Sept 3, 2009. Westminster, CO.
Martins, S. E., Oliveira, I., Langford, K., and Thomas, K. (2020). “Biocides from marine coatings,” in Environmental Impact of Ships. Cambridge: Cambridge University Press. doi: 10.1017/9781108381598.007
McClay, T., Zabin, C., Davidson, I., Young, R., and Elam, D. (2015). Vessel Biofouling Prevention and Management Options Report, Report No. CG-D-15-15. Washington, DC: U.S. Department of Homeland Security.
Mihaylova, R. (2020). Biofouling in Commercial Shipping: The Importance of Ship-Specific Functional Specifications. Data Insights Paper Safinah Group.
Miller, A., Whitman, I. C., Davidson, M. S., Steves, M. B., Moser, C. S., Drake, L. A., et al. (2018). Evaluation of wetted surface area of commercial ships as biofouling habitat flux to the United States. Biol. Invasions 20, 1977–1990. doi: 10.1007/s10530-018-1672-9
Morrisey, D., and Woods, C. (2015). In-water Cleaning Technologies: Review of Information. Prepared for Ministry for Primary Industries, New Zealand. MPI Technical Paper No: 2015/38. ISBN No: 978-1-77665-128-3. New Zealand: Biosecurity.
Morrisey, D., Gadd, J., Page, M., Lewis, J., Bell, A., and Georgiades, E. (2013). In-water Cleaning of Vessels: Biosecurity and Chemical Contamination Risks, MPI Technical Paper. MPI Technical Paper, 2013/11, Wellington, New Zealand. New Zealand: Biosecurity, 267.
Moser, C. S., Wier, T. P., Grant, J. F., First, M. R., Tamburri, M. N., Ruiz, G. M., et al. (2016). Quantifying the total wetted surface area of the world fleet: a first step in determining the potential extent of ships’ biofouling. Biol. Invasions 18, 265–277. doi: 10.1007/s10530-015-1007-z
Munk, T., Kane, D., and Yebra, D. M. (2009). “The effects of corrosion and fouling on the performance of ocean going vessels,” in Advances in Marine Antifouling Coatings and Technologies. Cambridge: Woodhead Publishing Series. doi: 10.1533/9781845696313.1.148
Netherlands (2014). Regulation (EU) no528/2012 Concerning the Making Available on the Market and Use of Biocidal products. Cybutryne Product type PT 21 (Antifouling). Cambridge: Woodhead Publishing Series.
Oftedahl, G. A., and Skarbø, R. A. (2021). The Need for an International l Standard for Proactive Hull Cleaning and the Clean Hull Initiative (CHI). 2nd Port In-Water Cleaning Conference. PortPIC’2. Pontignano, Italy.
Oliveira, D., and Granhag, L. (2020). Ship hull in-water cleaning and its effects on fouling-control coatings. Biofouling 2, 332–350. doi: 10.1080/08927014.2020.1762079
Owen, R., Knap, A., Toaspern, M., and Carbery, K. (2002). Inhibition of coral photosynthesis by the antifouling herbicide Irgarol 105. Mar. Pollut. Bull. 44, 623–632. doi: 10.1016/S0025-326X(01)00303-4
Redfield, A. C., and Hutchins, L. W. (1952). “The effects of fouling,” in Marine Fouling and Its Prevention Ch 1 Contribution No. 580 (Woods Hole, MA: Woods Hole Oceanographic Institute).
Ruiz, G. M., Fofonoff, P. W., Steves, B., Foss, S. F., and Shiba, S. N. (2011). Marine invasion history and vector analysis of California: a hotspot for western North America. Divers. Distrib. 17, 362–373. doi: 10.1111/j.1472-4642.2011.00742.x
Schultz, M., Bendick, J., Holm, E., and Hertel, W. (2011). Economic impact of biofouling on a naval surface ship. Biofouling 27, 87–98. doi: 10.1080/08927014.2010.542809
Schultz, M. P. (2004). Frictional resistance of antifouling coating systems. ASME J. Fluids Eng. 126, 1039–1047. doi: 10.1115/1.1845552
Schultz, M. P. (2007). Effects of coating roughness and biofouling on ship resistance and powering. Biofouling 23, 331–341. doi: 10.1080/08927010701461974
Schumacher, K. (1996). An Instrumented Rotating Brush Device to Evaluate the Removal of Biofouling From Non-toxic Antifouling Coatings. M.S. thesis. Melbourne, FL: Florida Institute of Technology, Melbourne.
Scianni, C., and Georgiages, E. (2019). Vessel in-water cleaning or treatment: identification of environmental risks and science needs for evidence-based decision making. Front. Mar. Sci. 6:467. doi: 10.3389/fmars.2019.00467
Scianni, C., Lubarsky, K., Ceballos-Osuna, L., and Bates, T. (2021). Yes, we CANZ: initial compliance and lessons learned from regulating vessel biofouling management in California and New Zealand. Manag. Biol. Invas. 12, 727–746. doi: 10.3391/mbi.2021.12.3.14
Seligman, P. F., and Zirino, A. (eds.). (1998). Chemistry, Toxicity, and Bioavailability of Copper and its Relationship to Regulation in the Marine Environment. San Diego, CA: Space and Naval Warfare Systems Center.
Sheikh, A. M., Juma, F. S., KarstenDahl, P., Rashid, R. J., Mohammed, M. S., Hassan, A. M., et al. (2016). Occurrence and distribution of antifouling biocide Irgarol-1051 in coral reef ecosystems. Zanzibar Mar. Pollut. Bull. 109:15. doi: 10.1016/j.marpolbul.2016.05.035
Song, C., and Cui, W. (2020). Review of underwater ship hull cleaning technologies. J. Marine. Sci. Appl. 19, 415–429. doi: 10.1007/s11804-020-00157-z
Srinivasan, M., and Swain, G. (2007). Managing the use of copper- based antifouling paints. J. Environ. Manage 39, 423–441. doi: 10.1007/s00267-005-0030-8
Swain, G. W., and Schultz, M. P. (1996). The testing and evaluation of non-toxic antifouling coatings. Biofouling 187–197. doi: 10.1080/08927019609386279
Swain, G. (2010). The Importance of Ship Hull Coatings and Maintenance as Drivers for Environmental Sustainability, RINA Conf. Ship Design and Operation for Environmental Sustainability, London. doi: 10.3940/rina.es.2010.17
Swain, G. (2017). A guide to developing a biofouling management plan. Mar. Technol. Soc. J. 51, 105–110. doi: 10.4031/MTSJ.51.2.6
Swain, G. W., Schultz, M. P., and Vincent, H. L. (1994). “Shear Force measurements of barnacle adhesion for field evaluation of nontoxic foul-release surfaces,” in Recent Developments in Biofouling Control, eds M.-F. Thompson, R. Nagabhushanam, R. Sarajini, and M. Fibngerman. New Delhi: Oxford and IBH Publishing Co.
Swain, G., Kovach, B., Touzot, A., Casse, F., and Kavanagh, C. J. (2007). Measuring the performance of today’s antifouling coatings. J. Ship Product. 23, 164–171. doi: 10.5957/jsp.2007.23.3.164
Swain, G., Tribou, M., Gardner, H., and Hunsucker, K. (2020). “In-water grooming of fouling control coatings: from research to reality,” in Proceedings of the PortPIC. Hamburg/Germany, 14-15 September 2020, Hamburg.
Tamburri, M. N., Davidson, I. C., First, M. R., Scianni, C., Newcomer, K. A., Inglis, G. J., et al. (2020). In-water cleaning and capture to remove ship biofouling: an initial evaluation of efficacy and environmental safety. Front. Mar. Sci. 7:437. doi: 10.3389/fmars.2020.00437
Townsin, R. L., Byrne, D., Svensen, T. E., and Milne, A. (1981). Estimating the technical and economic penalties of hull and propeller roughness. Trans. SNAME 89, 295–318.
Tribou, M. (2015). Brush Development for Underwater Ship Hull Coating Maintenance. Ph.D. thesis. Melbourne, FL: Ocean Engineering, Florida Institute of Technology. doi: 10.5957/WMTC-2015-205
Tribou, M., and Swain, G. (2010). The use of proactive in-water grooming to improve the performance of ship hull antifouling coatings. Biofouling 2, 47–56. doi: 10.1080/08927010903290973
Tribou, M., and Swain, G. (2015). Grooming using rotating brushes as a proactive method to control fouling. Biofouling 3, 309–319. doi: 10.1080/08927014.2015.1041021
Tribou, M., and Swain, G. (2017). The effects of grooming on a copper ablative coating: a six year study. Biofouling 3, 494–504. doi: 10.1080/08927014.2017.1328596
United Nations Conference on Trade and Development (2020). Available online at: https://stats.unctad.org/handbook/index.html (accessed November, 2021).
United States Environmental Protection Agency [US EPA] (2011). Underwater Ship Husbandry Discharges. EPA 800-R-11-004. November 29011. Washington, DC: United States Environmental Protection Agency.
United States Environmental Protection Agency [US EPA] (2016). Draft Aquatic Life Ambient Estuarine/Marine Water Quality Criteria for Copper. CAS Registry Number 7440-50-8.
US Navy (2006). Naval Ships’ Technical Manual Ch.081 – Waterborne underwater hull cleaning of Navy ships, Publication # S9086-CQ-STM-010/CH-081 Revision 5. Washington, DC: Naval Sea Systems Command.
Valkirs, A. O., Davidson, B. M., Kear, L. L., Fransham, R. L., Zirino, A. R., and Grovhoug, J. G. (1994). Environmental Effects From In-Water Cleaning of Ablative Copper Antifouling Coatings. San Diego, CA: Naval Command, Control and Ocean Surveillance Center.
Wathen, T. (1994). The Design of Brush Technology for the Evaluation of Non-toxic Foul Release Coatings. M.S. thesis. Melbourne, FL: Florida Institute of Technology, Melbourne.
Zabin, C., Davidson, I., and Ruiz, G. (2016). In-water Vessel Cleaning: Current and Emerging Technologies, Associated Risks, and Management Options for Hawaii. Hawaii: Hawaii State Department of Land and Natural Resources, Division of Aquatic Resources.
Zargiel, K. A., and Swain, G. (2014). Static versus dynamic settlement and adhesion of diatoms to ship hull coatings. Biofouling 30, 115–129. doi: 10.1080/08927014.2013.847927
Keywords: biofouling, fouling control coatings, grooming, ships, green house gas emissions, biocides, invasive species
Citation: Swain G, Erdogan C, Foy L, Gardner H, Harper M, Hearin J, Hunsucker KZ, Hunsucker JT, Lieberman K, Nanney M, Ralston E, Stephens A, Tribou M, Walker B and Wassick A (2022) Proactive In-Water Ship Hull Grooming as a Method to Reduce the Environmental Footprint of Ships. Front. Mar. Sci. 8:808549. doi: 10.3389/fmars.2021.808549
Received: 03 November 2021; Accepted: 14 December 2021;
Published: 18 February 2022.
Edited by:
Satya Panigrahi, Indira Gandhi Centre for Atomic Research (IGCAR), IndiaReviewed by:
Sriyutha Murthy, Bhabha Atomic Research Centre, IndiaXikun Song, Xiamen University, China
Copyright © 2022 Swain, Erdogan, Foy, Gardner, Harper, Hearin, Hunsucker, Hunsucker, Lieberman, Nanney, Ralston, Stephens, Tribou, Walker and Wassick. This is an open-access article distributed under the terms of the Creative Commons Attribution License (CC BY). The use, distribution or reproduction in other forums is permitted, provided the original author(s) and the copyright owner(s) are credited and that the original publication in this journal is cited, in accordance with accepted academic practice. No use, distribution or reproduction is permitted which does not comply with these terms.
*Correspondence: Geoffrey Swain, c3dhaW5AZml0LmVkdQ==