- 1School of Marine Sciences, Darling Marine Center, University of Maine, Walpole, ME, United States
- 2Kelson Marine Co., Portland, ME, United States
- 3Department of Naval Architecture and Ocean Engineering, United States Naval Academy, Annapolis, MD, United States
- 4Aquaculture Research Institute, Darling Marine Center, University of Maine, Walpole, ME, United States
- 5Department of Civil and Environmental Engineering, University of Maine, Orono, ME, United States
- 6Conscience Bay Research, LLC New York, NY, United States
To keep global surface warming below 1.5°C by 2100, the portfolio of cost-effective CDR technologies must expand. To evaluate the potential of macroalgae CDR, we developed a kelp aquaculture bio-techno-economic model in which large quantities of kelp would be farmed at an offshore site, transported to a deep water “sink site”, and then deposited below the sequestration horizon (1,000 m). We estimated the costs and associated emissions of nursery production, permitting, farm construction, ocean cultivation, biomass transport, and Monitoring, Reporting, and Verification (MRV) for a 1,000 acre (405 ha) “baseline” project located in the Gulf of Maine, USA. The baseline kelp CDR model applies current systems of kelp cultivation to deep water (100 m) exposed sites using best available modeling methods. We calculated the levelized unit costs of CO2eq sequestration (LCOC; $ tCO2eq-1). Under baseline assumptions, LCOC was $17,048 tCO2eq-1. Despite annually sequestering 628 tCO2eq within kelp biomass at the sink site, the project was only able to net 244 C credits (tCO2eq) each year, a true sequestration “additionality” rate (AR) of 39% (i.e., the ratio of net C credits produced to gross C sequestered within kelp biomass). As a result of optimizing 18 key parameters for which we identified a range within the literature, LCOC fell to $1,257 tCO2eq-1 and AR increased to 91%, demonstrating that substantial cost reductions could be achieved through process improvement and decarbonization of production supply chains. Kelp CDR may be limited by high production costs and energy intensive operations, as well as MRV uncertainty. To resolve these challenges, R&D must (1) de-risk farm designs that maximize lease space, (2) automate the seeding and harvest processes, (3) leverage selective breeding to increase yields, (4) assess the cost-benefit of gametophyte nursery culture as both a platform for selective breeding and driver of operating cost reductions, (5) decarbonize equipment supply chains, energy usage, and ocean cultivation by sourcing electricity from renewables and employing low GHG impact materials with long lifespans, and (6) develop low-cost and accurate MRV techniques for ocean-based CDR.
Introduction
Climate change has destabilized ecosystems, global food systems, and infrastructure (Currenti et al., 2019; Mora et al., 2018; Myers et al., 2017; Pei et al., 2020; Smith et al., 2021). Atmospheric CO2 concentrations were higher in 2019 than at any point in the previous 2 million years, a result of anthropogenic greenhouse gas (GHG) emissions (IPCC, 2021). To remain below 1.5°C of warming by 2100, and avoid the worst consequences of climate change, society will have to achieve net negative GHG emissions by 2050 (IPCC, 2021). These projections dictate that emissions reductions alone will not satisfy the requirements of the Paris Agreement. Rapid decarbonization must be accompanied by large scale removal of atmospheric CO2 using best available Carbon Dioxide Removal (CDR) strategies.
CDR is defined as the intentional removal of CO2 from the atmosphere through either engineered or “nature based” approaches. Engineered solutions include direct air capture (DAC) (Marcucci et al., 2017) and point-source carbon capture and storage (CCS) (Anderson and Peters, 2016; Cruetzig, 2016). “Nature based” techniques, such as reforestation and afforestation (Edmonds et al., 2013), soil management (Smith, 2012; van Minnen et al., 2008), and ocean fertilization (Minx et al., 2018), reduce atmospheric CO2 by enhancing biological carbon pumps. The portfolio of available CDR technologies must offset emissions in the medium to near term, decarbonize infrastructure that is not readily adaptable, and remove legacy (historic) emissions (Joppa et al., 2021).
The voluntary market for carbon credits, in units of USD per ton of carbon dioxide equivalent ($ tCO2eq-1) sequestered or avoided, reached $1 billion in 2021, representing ~250 million tCO2eq emissions removed (Forest Trends’ Ecosystem Marketplace, 2021). However, credits vary widely in price and permanence of CO2 removal, a reflection of differences among project methodologies (Fuss et al., 2018). Engineered solutions, such as DAC, potentially sequester carbon on geologic time scales on the order of 1,000’s of years (NASEM, 2019). However, DAC credits can be priced > $1,000 tCO2eq-1, a result of large energy and capital requirements (Sanz-Pérez et al., 2016). Nature based solutions, such as reforestation or improved soil management, can be less energy intensive and potentially more cost effective compared to DAC (Smith, 2012). However, storing C within forest biomass or soil can lead to less permanent sequestration (i.e., 10 - 50 years) as these natural C stocks are subject to disturbance from forest fires or floods (Smith and Torn, 2013). Furthermore, terrestrial-based CDR strategies are limited in scale, as they require converting significant amounts of productive land, potentially placing stress on food systems (Kreidenweis et al., 2016). Urgent demand for verifiable, real, permanent, cost effective, and socially and ecologically sustainable carbon credits will only increase. Expanding the supply of effective CDR technologies, and reducing uncertainty regarding costs and spillover effects, will be key in realizing net zero goals (Ng et al., 2020).
Recently, research has focused on whether macroalgae can and should be included within the portfolio of available CDR solutions. Wild macroalgae represent one of the most extensive and productive vegetative biomass stocks, and export a significant portion of net primary production, nearly 44%, in the form of dissolved (DOC) and particulate (POC) organic carbon (Duarte and Cebrián, 1996). However, macroalgae primarily grow in rocky nearshore areas not conducive to localized long-term sequestration. The vast majority of this POC and DOC is therefore remineralized and eventually re-enters the atmosphere as CO2 (Krause-Jensen & Duarte, 2016; Frontier et al., 2021). Long-term sequestration (i.e., > 1,000 years) can occur when exported biomass is incorporated within deep ocean sediments (i.e., > 1,000 m), or is remineralized at depths below the permanent thermocline in areas of the ocean in which bottom waters are locked away from atmospheric exchange for extended periods (Hurd et al., 2022). First order estimates suggest that only ~11% of exported macroalgal derived C is permanently sequestered (Duarte and Cebrián, 1996). While the net contribution of macroalgae to the global C cycle is up for debate (Filbee-Dexter et al., 2022; Gallagher et al., 2022), these ecosystems potentially sequester ~0.68 GtCO2eq annually (equivalent to two-thirds of total emissions from the U.S. industrials sector (EPA, 2021). However, wild macroalgae populations have largely been ignored within blue carbon frameworks (Nellemann et al., 2009) because quantifying the annual contribution from source to sink is challenging (Barrón and Duarte, 2015).
Macroalgae aquaculture, the farming of marine or freshwater organisms, could potentially be leveraged to replicate and scale the important C sequestration contribution from wild beds and generate verifiable C credits. The farmed macroalgae industry has nearly tripled in scale since the turn of the 21st century, increasing from 10.6 million t (wet weight) harvested in 2000 to 32.4 million t (wet weight) in 2018 (FAO, 2020). Production is currently dominated by brown algae species, such as kelps, destined for the food, fertilizer, animal feed, pharmaceutical, and nutraceutical industries (Augyte et al., 2021). However, production of red algaes, such as Eucheuma and Kappaphycus spp., are not far behind and often trade for the top spot (Kim et al., 2019). Previous efforts to explore the climate change mitigation potential of macroalgae farming have included using raw materials for the production of biofuels (Michalak, 2018; Osman et al., 2020), nutrient management (Racine et al., 2021), and as a supplement within livestock feed to reduce methane emissions (Roque et al., 2021). Early-stage research is also being conducted to evaluate the potential of growing and then intentionally sinking large quantities of macroalgae in the deep ocean, locking the C incorporated within macroalgae biomass away from atmospheric exchange (DeAngelo et al., 2022; Froehlich et al., 2019; Gaines et al., 2019; NASEM, 2021; Peters, 2020).
On the spectrum of CDR technologies, the purposeful sinking of farmed macroalgae lies somewhere between an engineered and nature-based solution. The ability to control the physical and biomolecular composition of biomass through species and phenotypic selection, manipulate farm dynamics, and specify the timing and location of sinking makes farming macroalgae an attractive CDR option. With respect to larger, K-selected macroalgae species, such as Fucales and Laminariales, POC is stored in relatively refractory forms and would be more resistant to grazing after deep-sea deposition, compared to other r-selected opportunistic species, like Ulvacian or Dasyacean (Littler & Littler, 1980; Steneck & Dethier, 1994). Targeted sinking after harvest could also ensure that kelp reaches regions and depths that increase the likelihood of long-term CO2 removal, such as deep-sea canyons or abyssal plains (Harrold et al., 1998; Masson et al., 2010). These factors potentially offer higher conversion rates of “exported” biomass to sequestered carbon (Krumhansl and Scheibling, 2012). Kelp farming also requires minimal arable land and freshwater (Bricknell et al., 2020; Grebe et al., 2019; Hu et al., 2021), could be less energy intensive than other engineered solutions (such as DAC), and satisfies many of the United Nations Sustainable Development Goals (Duarte et al., 2021).
There are still considerable questions regarding the environmental, biological, geological, and, perhaps most importantly, economic feasibility of kelp aquaculture-based CDR (DeAngelo et al., 2022; Hurd et al., 2022; Troell et al., 2022). To satisfy the requirements of the IPCC, ~10 Gt of CO2eq will need to be removed each year by mid-century. Assuming a target sequestration price of $100 tCO2eq-1, the CDR sector could grow into a ~$1 trillion market (IPCC, 2021; REFINITIV, 2022). Policy makers, researchers, and investors will require accurate estimates of the economic and environmental performance, efficiency, and long-term scaling potential of available CDR technologies to make decisions regarding allocation of research and development (R&D) funding (Fuss et al., 2018). To justify further public and private financial support for kelp aquaculture CDR, it must be demonstrated that there is a pathway to cost-effectively generating kelp C credits. (Froehlich et al. (2019)) analyzed global production data and determined that the cost of producing C credits from macroalgae ranged from $71 - $27,222 tCO2eq-1. While the upper end of this range is far greater than current market prices, the ability to potentially sequester CO2 at a price point of under $100 tCO2eq-1 warrants further study. Global production models offer valuable insights into the potential of this novel concept (DeAngelo et al., 2022). However, seaweed production cost estimates can vary widely by region, species, and husbandry method (van den Burg et al., 2016). A site-specific and exploratory analysis of this low technology readiness level concept is thus required to provide insight into specific R&D needs (Thomassen et al., 2019).
The primary goal of this study was to analyze the economics of macroalgae CDR to determine a hyper-realistic baseline cost, quantify uncertainty, identify pathways for optimization and future cost reduction, and categorize research priorities. Evaluating the potential social and environmental risks associated with large-scale macroalgae farming and sinking remains a critical, yet understudied, aspect of the concept (Boyd et al., 2022; Hurd et al., 2022), but falls outside the scope of this analysis. Rather, we attempt to provide a rigorous assessment of the costs and climate potential of this emerging technology. Through an extensive literature review, expert consultations, and detailed economic and engineering analysis, we constructed a biological-techno-economic model (BTEM) of a hypothetical kelp CDR operation located within the Gulf of Maine (GOM), a region of the U.S. with an established aquaculture permitting process and an expanding kelp farming sector (Grebe et al., 2019). We quantified the effects of scale, production methods, and project emissions on the levelized costs of producing verified C credits ($ tCO2eq-1) over a 30-year horizon. The results of this work provide a replicable framework with which to guide future R&D and are relevant to both the CDR and kelp aquaculture industries generally, as the emphasis on scaling up kelp production is an active area of interest for policy makers, investors, and macroalgae farmers.
Methods
Bio-techno-economic model overview
Global models of kelp CDR approaches have been valuable tools to evaluate scalability and costs over large geographic regions (Froehlich et al., 2019; DeAngelo et al., 2022). However, due to complexities associated with choice of species, site-specific factors, and cultivation strategies, we contend that more granular regional analyses can help identify pathways for cost reductions that would not otherwise be apparent in global analyses. To create a baseline for kelp aquaculture CDR, we constrained the design space to a single kelp species (S. latissima - Phaeophyceae; sugar kelp, sea belt, or Devil’s apron; hereafter kelp), region (GOM), and available husbandry practices, defined as methods or technologies that have been demonstrated commercially (albeit at smaller scales than evaluated here).
The bio-techno-economic model (BTEM) was made up of four components: (1) an ocean cultivation submodel, (2) a kelp biological submodel, (3) a Life Cycle Assessment (LCA) submodel, and (4) a C credit verification framework (Figure 1). The ocean cultivation submodel quantifies the costs of outplanting seeded twine, installing and maintaining a cultivation structure suitable for open-ocean conditions, and harvesting/sinking kelp. The biological submodel calculates the total quantity of CO2eq sequestered each year as a function of kelp biomass yield. The LCA submodel quantifies project emissions, which must be deducted from the net C sequestration budget of the project. Lastly, the verification framework incorporates the costs, and C discounts, associated with selling C credits on open markets.
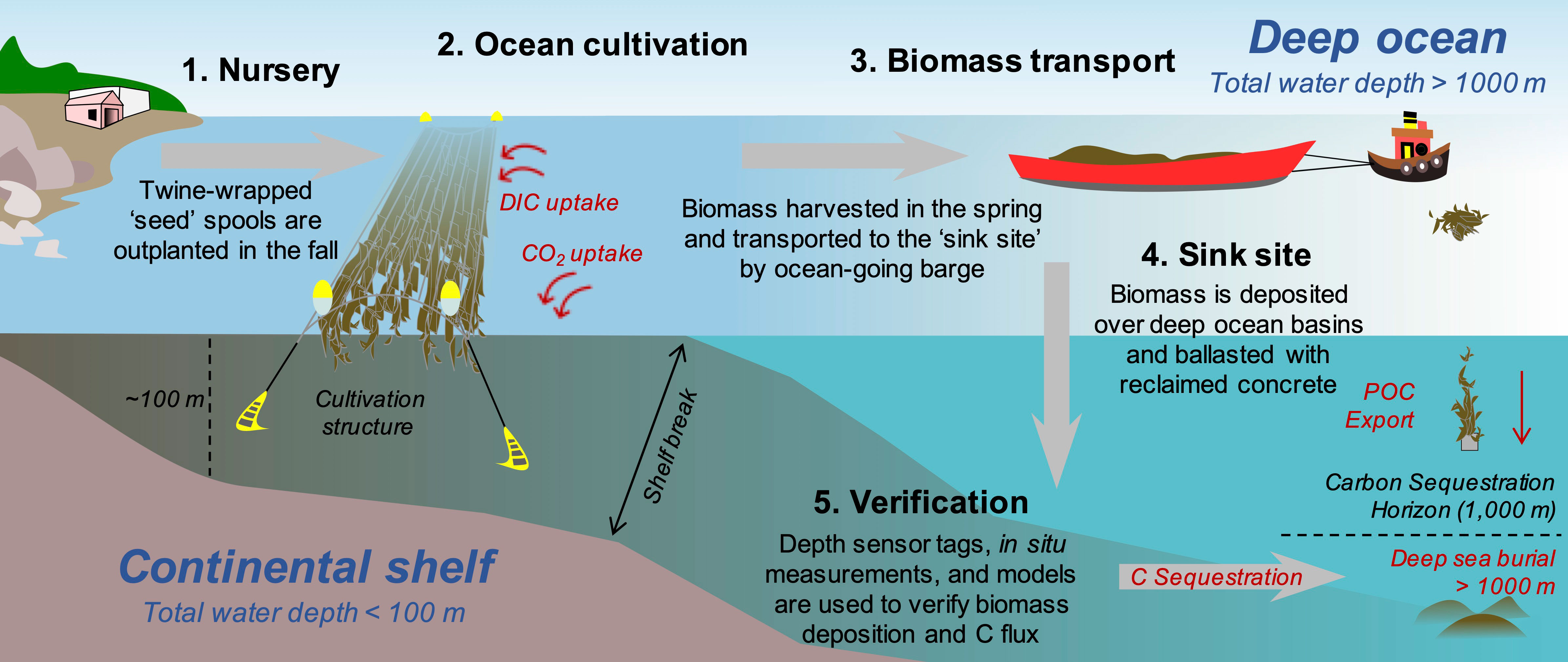
Figure 1 Conceptual diagram of offshore macroalgae cultivation in the Gulf of Maine and intentional deep-ocean sinking as a method of carbon dioxide removal (CDR). Juvenile sporophytes are grown within a land based nursery during the summer and then outplanted on twine-wrapped PVC “spools” in the fall. The cultivation site is located ~20km from the Maine coastline. As kelp uptake dissolved inorganic carbon (DIC) to build tissue, the DIC deficient seawater equilibrates with the atmosphere and draws down atmospheric CO2 into the oceanic C pool. In the spring, kelp biomass is harvested and then transported ~350 km using ocean-going barges to the deep-ocean “sink site” located at the edge of the continental shelf. Biomass is ballasted using reclaimed concrete and deposited below the Carbon Sequestration Horizon (1,000 m). Lastly, a combination of in situ measurements and modeling is used to verify the quantity of CO2eq sequestered.
The BTEM was developed with a 30-year design life, the upper end of the lifespan for agricultural infrastructure (CEN, 1990), in which costs and C credits were aggregated annually. The primary model output was the levelized cost of CO2 sequestration (LCOC; $ tCO2eq-1), which represents the unit cost of sequestering a single ton of CO2eq. LCOC was calculated by dividing the discounted sum of cash outflows over a period of time by the discounted sum of carbon credits produced during that same period of time. LCOC ($ tCO2eq-1) was calculated as:
where n was the lifespan of the operation (30 years), OC was ocean cultivation costs in year t, VC was verification costs in year t, I0 was the initial investment in year 0, CC was the number of C credits sold in year t, and r was the discount rate (6.75%) used in the analysis (January 2020 bank prime lending rate +2%). The upfront investment in capital expenditures (cap-ex), permits, and anchor installation costs (Io) was not discounted as it was paid out in the present (year 0). The following sections describe in more detail the components of submodels 1 - 4.
BTEM submodel (1): Ocean cultivation
The ocean cultivation submodel calculates an estimate of the costs required to lease, install, and operate a kelp farm in Maine state waters (0 - 3 nm from land). The U.S. lacks an established pathway to securing farming rights (i.e., a lease or equivalent legal tenure) within the federally managed Exclusive Economic Zone (EEZ) of 3 - 200 nm from shore (Otts, 2021). Maine, a state with an established aquaculture sector (DMR, 2021), was thus chosen as the study region. In Maine, no leaseholder may be in possession of a single tract that is greater than 100 acres (40.5 ha), but leaseholders may obtain multiple tracts that, in aggregate, amount to 1,000 acres (404.7 ha). We therefore designed a modular cultivation structure that occupies a footprint of 100 acres which can be replicated to fill the allotted 1,000 acres.
Relatively large prospective lease sites will likely be located in exposed ocean areas subject to wind, waves, and currents. The cultivation structure was thus designed for a representative site located SW of Monhegan Island, ME USA, ~20km from the Maine coastline. Twenty years of historical wave and current data from the site (NERACOOS, 2022) were fit to an extreme value distribution and extrapolated to compute 10-year and 50-year design values. Since kelp cultivation systems are comprised of flexible biomass components subject to nonlinear wave and current forces, neither static analysis nor typical ocean structural modeling techniques are sufficient for determining the required capacity of mooring lines, anchors, floats, etc. Therefore, we developed a time domain numerical model of the candidate structures using a Hydro-Structural Dynamic Finite Element Analysis approach (HS-DFEA). This HS-DFEA approach solves the equations of motion at each time step using a nonlinear Lagrangian method to accommodate the large displacements of structural elements, as described in the NOAA Basis-of-Design Technical Guidance for Offshore Aquaculture Installations in the Gulf of Mexico (Fredriksson and Beck-Stimpert, 2019). Forcing was based on a modified Morison equation approach (Morison et al., 1950). Similar models have been utilized for aquaculture systems consisting of nets (DeCew et al., 2010; Klebert et al., 2013; Tsukrov et al., 2003) and mussel droppers (Dewhurst, 2016; Knysh et al., 2020). These applications incorporate specific empirical hydrodynamic coefficients, and some characterize flow reduction e.g. (Patursson et al., 2010) or use a priori estimates of flow speed reduction through the structure (Dewhurst et al., 2019; Gansel et al., 2018).
Wave and current loading on buoy and line elements (including macroalgae elements) was calculated at each time step according to the relative motion between the structural elements and the surrounding fluid. The hydrodynamics of the macroalgae were incorporated using the results from (Fredriksson et al. (2020)) and included a reduction in current speed through the farm based on a spatially-averaged momentum balance approach (Rosman et al., 2010).
Three candidate farms were initially chosen. All three designs were based on a 4-point spread mooring array system with horizontal grow-lines traversing the length of the structure. Grow-lines were spaced 4 m apart and were maintained at 2 m depth with surface floats. The three designs were identical in structure and materials, but differed with respect to the ratio of farm length to width (i.e., aspect ratio), and thus the size of the “growing area” within each 100-acre plot (Figure 2). Farm design “a” had an aspect ratio of 1.6, with a grow-area length of 200 m, a grow-area width of 320 m, and 10,740 m of planted grow-line. Farm design “b” had an aspect ratio of ~2.5, with 14,742 m of planted grow-line. Farm design “c” had the largest aspect ratio (10), with a grow-area length of 1,437 m, grow-area width of 143 m, and 35,914 m of planted grow-line.
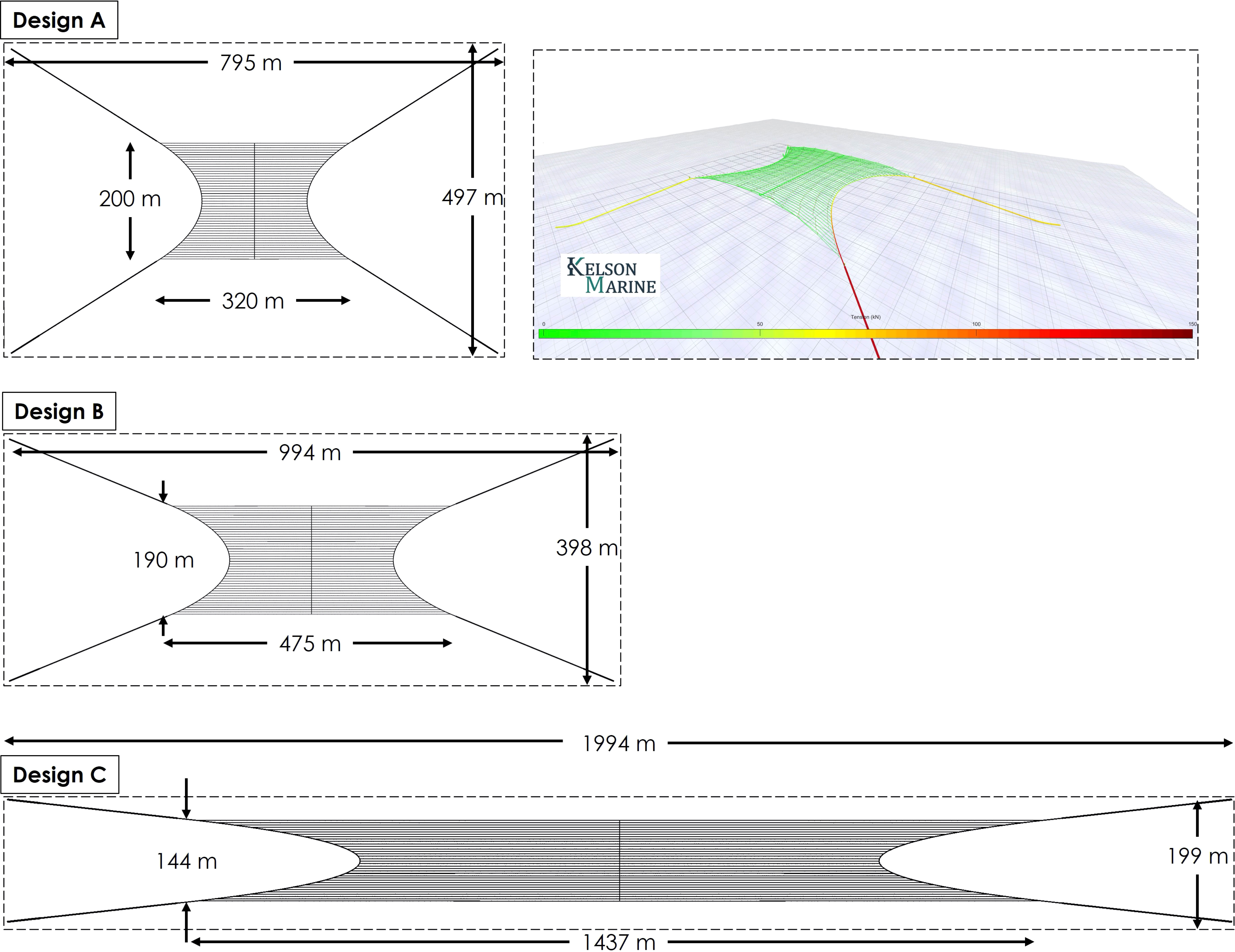
Figure 2 Overhead view of the three candidate modular cultivation structure designs. Designs differed by aspect ratio (length vs. width). Design “C”, with an aspect ratio of 10:1 was ultimately chosen as it provided the most available growing substrate within the allotted 100 acre lease footprint. Inset: Simulation of Design “A” showing tensions in structural lines in 1-year storm conditions.
For each candidate farm design, several realizations of a 50-year storm were evaluated. Both wave-dominated and current-dominated 50-year events were examined for incident wave and current headings parallel to, normal to, and at 45 degrees from the grow lines, in accordance with Norwegian finfish cage design standard NS 9415 (Standards Norway, 2009). For each one of these simulations, defined as load cases, the maximum expected tensions and forces were found by simulating the farm design using the HS-DFEA method, and deriving an extreme value distribution for the maximum loads to calculate those expected in a one-hour storm. Using the modeling techniques that incorporated the macroalgae hydrodynamic coefficients, we calculated the minimum breaking strength of the structural and mooring components required to achieve safety factors of 1.5 - 1.8 as recommended for various components of offshore structures (ABS, 2012; NAVFAC, 2012). Furthermore, the API RP 2SK (2005) recommends a reduction factor be included when high-capacity drag embedment anchors are loaded at a non-zero uplift angle (API, 2005). Each kelp cultivation structure (“a”, “b”, and “c”) was designed such that the maximum uplift angle was within the acceptable limit of 20 degrees, as per API RP 2SK. This reduction factor was included when calculating the required rated capacities of the anchors. We included an additional 15% margin on all component capacities based on preliminary uncertainty estimates in the numerical modeling approach as indicated from full-scale validation experiments.
Taking into account the required safety factors, we computed the minimum allowable capacity (e.g., breaking strength) of major structural components for each candidate design based on the results of the dynamic simulations of the system in the specified storm conditions. Breaking strength estimates were then used to identify the equipment required to anchor the farms at the proposed cultivation site. The cost of each component of the farm was then estimated based on quotes from suppliers (Table S1). The large aspect ratio of farm design “c” resulted in increased loads on the system due to the higher total biomass and the large angle between the mooring lines and the applied loads when the wind, wave, and current forces are normal to the grow lines. Despite the increased equipment expenses associated with these larger forces, the benefit of a more expansive grow-area, and thus higher kelp yields per 100-acre plot, outweighed the costs of larger anchors, buoys, etc. When expressed in terms of $ of cap-ex per kg of kelp yield, design “c”, with an aspect ratio of 10:1, outperformed the other two structures. Results were $1.95, $1.69, and $1.31 per kg of biomass for “a”, “b”, and “c”, respectively. Therefore, farm design “c” was chosen for further CDR analysis.
The primary costs within submodel (1) included the upfront investment in permits and the cultivation structure (I0) and annual farm operations (ocean cultivation costs; OC). I accrued in year 0, and was made up of cap-ex, lease application fees, permitting costs, professional engineering fees, and mooring installation costs. We assumed a 50:50 split between debt and equity to calculate cap-ex and a contingency factor of 2.5% was used for each component of the farm (Table S1). Installing drag-embedment anchors requires significant vessel capacity. Drawing on marine hydrokinetic offshore construction, we estimated that installation costs for the 1,000-acre baseline farm would be $155,266 per 11-ton anchor (Jenne et al., 2015). This covers the cost of a contracted vessel and crew, fuel, and travel to and from the site (Figure S1). Decommissioning costs were not included within our analysis as they fall outside of the “lifetime” of the project, but would likely be as expensive, if not more, than construction. Based on estimates from the offshore wind sector, we also assumed a one-time payment of $300,000 to a professional marine contractor with engineering capabilities to design the structure, select properly rated components and equipment, create site drawings and installation plans, and conduct the HS-DFEA simulations.
To secure a standard aquaculture lease >3 acres in Maine, applicants must pay a $2,000 application fee for each lease application (i.e., per 100 acre plot), also assumed in year 0. Based on consultations with the Maine Department of Marine Resources and the U.S. Army Corps of Engineers, we also included a $2,447,500 pre-leasing cost to hire consultants to help navigate the National Environmental Policy Act (NEPA) requirements, and conduct baseline environmental monitoring on fish and marine mammal aggregations within the proposed lease site through the use of in situ instrumentation, such as passive acoustic monitoring for cetaceans and geophysical-geotechnical and benthic habitat surveys (Jenne et al., 2015). While this is not currently required for leases within Maine state waters, consultations with regulators indicated that an installation of this size would likely require additional monitoring (Table 1).
The cost of annual farm operations (OC) was then further decomposed into fixed costs (FC) and operating expenses (OE) as follows:
OC = FC + OE
FC included replacement cap-ex based on the useful life of components, interest, lease fees, insurance, and regulatory fees (Table 2). The remaining portion (50%) of the initial investment in cap-ex was financed using a 30-year term loan with a 5% interest rate and annual repayment schedule, which began in year 1. Maine leaseholders must annually pay $100 acre-1 in lease rental fees (DMR, 2021). We also assumed an additional annual fee equal to 5% of annualized cap-ex (van den Burg et al., 2016) to cover insurance and any other miscellaneous fixed costs.

Table 2 Summary of costs included within Ocean Cultivation Costs (OC) in the baseline BTEM. OC was further decomposed into Fixed Costs (FC) and Operating Expenses (OE).
OE included seeded twine, labor, vessel operations, and farm maintenance (Table 2). We assumed the operation was required to construct a land-based nursery that produced twine exclusively for kelp CDR. The nursery would follow the most widely adopted kelp protocols (Coleman et al., 2022; Flavin et al., 2013; Forbord et al., 2018; Redmond et al., 2014). In the summer, juvenile sporophytes would be grown within the facility on PVC spools wrapped with 2 mm twine. The spools would then be transferred to the cultivation site in the fall when the seeded twine would be wrapped around the grow-line. We used the kelp nursery model described in (Coleman et al. (2022)) to calculate the cost of seeded twine ($ m-1). At a scale of 1,000 acres, the farm would contain 359,140 m of grow-line. Based on a conversion of seeded twine to grow-line of 1.8 (Engle et al., 2020), the operation would require 646,452 m of seeded twine each year at a cost of $0.91 m-1 (Coleman et al., 2022) (Figure S2).
Labor was decomposed into three categories: (1) seeding in the fall, (2) overwinter maintenance, (3) and harvest in the summer (Bak et al., 2018) (Table S2). Full time equivalent (FTE) person hours for seeding and maintenance were assigned to each task based on the quantity of grow-line within the farm (FTE person hours per km of grow-line). Harvest labor requirements were calculated based on final yield (FTE person hours per harvested wet ton). We assumed a labor rate of $25 hour-1. The vessels required for seeding, maintaining, and harvesting kelp within exposed offshore conditions are only needed seasonally and would likely be contracted. Based on (Hasselström et al. (2020)), we assumed a cost of $3,845 day-1 for seeding and harvest vessels, and $333 day-1 for overwinter maintenance vessels. A value of $5,000 per 100 acre plot for annual expendable and maintenance supplies was also assumed (Hoagland et al., 2003; Rubino, 2008).
Given the potential verification and regulatory challenges of measuring C flux from the release of free-floating kelp lines1), we decided to quantify the requirements of transporting the kelp biomass to a predetermined “sink” site with adequate depth. The chosen site lies at the edge of the continental shelf (depths of >1,000 m), a ~350 km trip (one-way) from the Monhegan Island case study site. Based on consultations with marine construction contractors, we assumed an hourly rate (including crew, equipment, and fuel) of $700 h-1 for the use of 2,000 hp tugboats and $62.5 hour-1 for each 2,000 t capacity ocean-going barge required to transport biomass (Hughes Marine, pers. comms., February, 2022). The tug would maintain a cruising speed of 10 km hour-1 and have a specific fuel consumption of 8.7 kg of diesel per 1,000 ton-km (Teodorović & Janić, 2017). We also included the cost ($6 ton-1) and mass (0.14 tons per ton of wet kelp) of reclaimed concrete required for sinking ballast within our transport calculations (Supplementary Materials).
BTEM submodel (2): Biological
The biological submodel determines the annual quantity of CO2eq sequestered as a function of yield (kg m-1; wet weight), a conversion from wet (WW) to dry (DW) weight and a conversion from DW to C content. The biomolecular composition and growth of S. latissima can vary by region, season, and cultivation method (Manns et al., 2017; Ometto et al., 2018). Yields as high as 24 kg m-1 (Kim et al., 2019) and as low as 0.5 kg m-1 (Bruhn et al., 2016) have been reported from sugar kelp in northern temperate farming regions. (Stekoll et al. (2021)) identified a published average of 12.5 kg m-1, which aligns well with reported yields of 12.7 kg m-1 from a location about 87 km southwest of the case study site (St-Gelais et al., 2022). These values are derived from studies on kelp produced primarily for human food applications, in which maximum biomass yield was balanced with blade quality and fouling by epibionts. For CDR applications, producers may be able to harvest later in the growing season (i.e., August or September) and maximize growth and potential CO2eq. However, we assumed a baseline (and thus likely conservative) estimate of 12.5 kg m-1. Based on a review of 14 studies, we then assumed an average +/- SD (n = 67) conversion of 13.33 +/- 3.17% of wet kelp to dry kelp, and an average +/- SD (n = 40) conversion of 28.59 +/- 4.02% of dry kelp to C (Table S3). C was converted to potential CO2eq using a stoichiometric molecular weight conversion factor of 3.67 (Duarte et al., 2017; Pendleton et al., 2012). Lastly, we assumed that 100% of potential CO2eq was delivered to a depth of >1,000 m as a result of transport to the edge of the continental shelf and sinking. There is considerable uncertainty regarding the eventual fate of kelp derived C were it to be injected below the sequestration horizon (Krumhansl & Scheibling, 2012; Smale et al., 2021). Resolving those questions, while beyond the scope of this study, will be essential in determining the potential of macroalgae CDR (NASEM, 2021).
BTEM submodel (3): Life cycle assessment
Emissions from the processes required to produce and sink each year’s “crop” of kelp must be deducted from the final quantity of CO2eq sequestered in the deep ocean to calculate the net C budget of the project. To quantify project emissions, we developed a Life Cycle Assessment (LCA) model. Environmental LCAs are useful for quantifying the sustainability of a system across the full value chain (i.e., from cradle to grave), as described in (Czyrnek-Delêtre et al. (2017)) and (Parsons et al. (2019)). The environmental impact of a product is commonly evaluated according to the guidelines of CML 2 baseline 2000 (v2.05; Institute of Environmental Sciences, Leiden University) which includes a suite of metrics, such as abiotic depletion, acidification, eutrophication, ozone layer depletion, human toxicity, freshwater aquatic ecotoxicity, marine aquatic ecotoxicity, terrestrial ecotoxicity, photochemical oxidation, and global warming potential (GWP) over 100 years (Guinee, 2002; Seghetta et al., 2016). We developed a kelp aquaculture LCA focused solely on the GWP (tCO2eq) of the farm within a typical year (Thomas et al., 2021).
The aim of the LCA was to calculate the total quantity of CO2eq emissions produced by the project that must ultimately be deducted from the quantity of sequestered CO2eq. Therefore, the functional unit of the LCA, i.e., the unit in terms of which the impacts are expressed, was tCO2eq emitted year-1. The system boundaries were set to include emissions encompassing the full baseline BTEM, from the land based nursery, to open-ocean cultivation (cradle to farm-gate), and lastly biomass transport and sinking (cradle to grave). The Life Cycle Inventory (LCI) was developed by quantifying both the energy (i.e., electricity and marine fuel) and materials (i.e., mooring lines, anchors, nursery infrastructure, and expendable supplies) consumed within each year across the full value chain of the 1,000 acre baseline kelp CDR operation. Emissions factors for all energy and materials were sourced from LCA databases, such as EcoInvent (version 3.2), and literature reviews (Thomas et al., 2021). Lastly, we conducted an “Impact Assessment” to translate the inputs and outputs of the baseline BTEM into emissions, expressed in terms of the functional unit: tCO2eq emitted year-1 (Table S4).
BTEM submodel (4): Verification framework
Selling carbon credits within compliance or voluntary markets requires third party verification to ensure the CDR project meets the IPCC criteria of ‘real’, ‘measurable’, ‘permanent’, ‘unique’ and ‘additional’ Gold Standard, 2021). Compliance markets, such as California’s cap-and-trade program, are established by regional, national, or international governing bodies (Marland et al., 2017). Voluntary markets operate outside of compliance markets, and allow corporations or individuals to offset “personal” GHG emissions (Joppa et al., 2021). Gold Standard (GS), Verified Carbon Standard (VCS), and the Clean Development Mechanism (CDM) are the most widely known verification bodies that facilitate the issuance of C credits.
We adhered to the guidelines of GS and VCS to calculate verification costs. According to these guidelines, producers must draft a project methodology. This document outlines the scientific precedent supporting the proposed project and is reviewed by experts in the associated field (Gold Standard, 2017; VCS, 2021). Drafting a methodology and navigating the review process costs $150,000. Next, project developers must submit a “Project Design” document that outlines the specifics of the proposed CDR operation (i.e., how does the proposed project follow an approved methodology)?. The GS Project Design review fee is $1,500. These costs were assumed in year 0 and, just as with the initial investment in cap-ex and regulatory fees (I0), were not discounted.
GS requires an annual third-party audit to certify the quantity of credits claimed by the producer. Two audit costs were associated with each year’s crop of kelp. First, there was a fixed “performance review” fee that ranges in price from $10,000 year-1 for simple projects, such as point source carbon capture and storage, to $100,000 year-1 for more complex projects, such as those that fall into the category of Land use and Forestry (LUF). We assumed the upper-end of the range for an annual fee of $100,000 given the complexity of verifying kelp aquaculture CDR (NASEM, 2021). Next, GS charges a $0.30 credit-1 issuance fee. CDR projects are often required to reserve a portion of credits within a “buffer pool” to account for MRV uncertainty and potentially lost C (Matzek et al., 2015; Gallagher et al., 2022). Accurately quantifying the amount of CO2eq removed not just from the oceanic C pool, but from the atmosphere, may be challenging due to the discrepancy between the timing of photosynthetic uptake of dissolved inorganic carbon (DIC) by kelp and the time required for re-equilibration of CO2 between the atmosphere and the C replete surface waters within and adjacent to the farm (Hurd et al., 2022). If the waters carrying a DIC deficit are subducted prior to the drawdown of atmospheric CO2, producers may not be able to take credit for the total amount of potential C removed by kelp. Furthermore, the artificial growth of large quantities of kelp may compete for nutrients with phytoplankton, decreasing natural NPP and thus C export and sequestration (Frieder et al., 2022). Finally, some portion of kelp derived particulate organic carbon (POC) that is deposited in the deep sea will ultimately be remineralized and, depending on deposition location, returned to the atmosphere before the 100-year mark (Siegel et al., 2021). Due to these potentially large uncertainties, we assumed 15% of credits, after all C accounting and deductions within submodels (2) and (3), respectively, would be reserved within a buffer pool.
Bio-techno-economic model analyses
We primarily focused on the levelized cost of producing C credits (LCOC; $ tCO2eq-1) to evaluate the performance of kelp CDR. First, LCOC was calculated for the 1,000-acre baseline farm. We also quantified the levelized cost of C capture by kelp (LCOK; $ t-1 kelp CO2eq) prior to sequestration and thus without transport, sinking, or verification costs. LCOK was calculated by dividing the discounted sum of expenses, less sinking and verification costs, by the discounted sum of net C credits (after all emissions and buffer pool discounts) produced over the same 30-year horizon. To assess the effects of scaling, we then adjusted the farm size from 500 - 1,500 acres in 100 acre increments and calculated a corresponding LCOC and LCOK for each farm size. All expenses were then aggregated over the 30-year design life by line-item to provide a categorical cost breakdown of LCOC for the 1,000-acre baseline farm. We then quantified the annual impact (in tCO2eq year-1; the functional unit) of the primary categories within the LCA, as well as the required buffer pool, on the net quantity of C credits produced annually. To evaluate the emissions profile of the baseline kelp BTEM in the context of macroalgae LCA literature, we also calculated the CO2eq impact of the farm from cradle to farm-gate. Excluding the emissions from biomass transport and sinking, we quantified the tCO2eq emitted per ton of dry weight kelp produced.
To assess the relative impact of key variables on LCOC, we performed a sensitivity analysis using the 1,000-acre baseline scenario. First, we increased and decreased, in 10% increments, a comprehensive set of 23 variables within the BTEM to a range of +/- 40% and calculated a corresponding LCOC after each change (Table S5; (Figure S3). Of the comprehensive list of variables selected, the 6 parameters that generated the greatest change in LCOC with changes in the baseline assumption were selected for visualization.
To develop a roadmap towards potential cost reductions and identify R&D priorities, we then conducted an “optimization” analysis. We identified a range of values from literature reviews and expert consultations for 18 key parameters within submodels (1) - (4) and iteratively changed the assumption for each parameter to the maximum or minimum value within the observed range that decreased LCOC. These changes represent potential “line of sight” improvements that exist within the current framework of kelp cultivation in emerging farming regions (i.e., North America, South America, and Europe). We performed this analysis looking at both LCOC ($ tCO2eq-1) and “additionality rate” (AR; %). Additionality is the net effect that CDR projects have on atmospheric CO2 concentrations (Barata et al., 2016). AR was thus calculated as the ratio of net C credits produced (tCO2eq after all emissions and buffer pool deductions) to the gross quantity of CO2eq sequestered each year in kelp biomass. The metric gives an estimate of the efficiency of the farm as a CDR technology. With each parameter optimization, we recorded the subsequent change in both LCOC and AR (Table S6). All changes were then combined to arrive at a parameter set that minimized LCOC and maximized AR.
To explore the future scaling potential of this emerging technology, we then evaluated the impact of top-down “learning rates’’ on the optimized LCOC. Learning rate (LR) refers to the reduction in unit production costs for technologies as a result of a doubling in scale (Faber et al., 2022). In the case of energy technologies, this would mean the % reduction in unit costs ($ kWh-1) with each doubling of total installed capacity. For kelp CDR, the LR is the unforeseen unit cost reduction ($ tCO2eq-1) that is driven by doubling the size of the farm. For the majority of energy technologies, such as natural gas and solar photovoltaics (PV), production costs have declined with increases in installed capacity due to economies of scale, R&D, and “learning by doing” (LBD) (Kavlak et al., 2018; McDonald and Schrattenholzer, 2001). Given that kelp CDR remains in concept stages (NASEM, 2021), we would be unable to accurately predict future unforeseen cost reductions as a result of empirically derived LRs from historic production data. Therefore, we calculated the effect of a range of LRs realized for other technologies on the optimized LCOC. We doubled the footprint of the 1,000-acre optimized BTEM until a levelized sequestration cost of $100 tCO2eq-1 was reached. With each doubling, we reduced LCOC by either 5%, 10%, 15%, or 20%. For comparison, the LR for PV between 1959 - 2011 was 23%, the highest for all energy technologies during that period (Rubin et al., 2015).
Results
At the scale of our baseline 1,000 acre farm, production costs (LCOC) were $17,048 tCO2eq-1. Across the range of simulated farm sizes (500 - 1,500 acres), LCOC decreased from $21,988 to $15,517 tCO2eq-1 (Figure 3). The costs of capturing and sequestering a single ton of CO2eq (i.e., sinking kelp) were consistently between $500 - $13,500 more (depending on farm scale) than those for only capturing a ton of CO2eq within kelp (excluding verification and sinking costs), reflecting the additional costs and emissions associated with biomass transport to the sink site and third-party verification of C credits (Figure 3). When examining the breakdown of LCOC, labor and fixed overhead costs made up the greatest portion of expenses at $4,299 and $3,449 tCO2eq-1, respectively (Figure 4). Fixed costs were primarily driven by the requirements of installing 40, 11-ton drag embedment anchors for a total of ~$6.2 million in year 0. Contracted vessels (not including barges and tugboats for biomass transport) and seeded twine were the next most substantial contributors to costs at $2,717 and $2,654 tCO2eq-1, respectively.
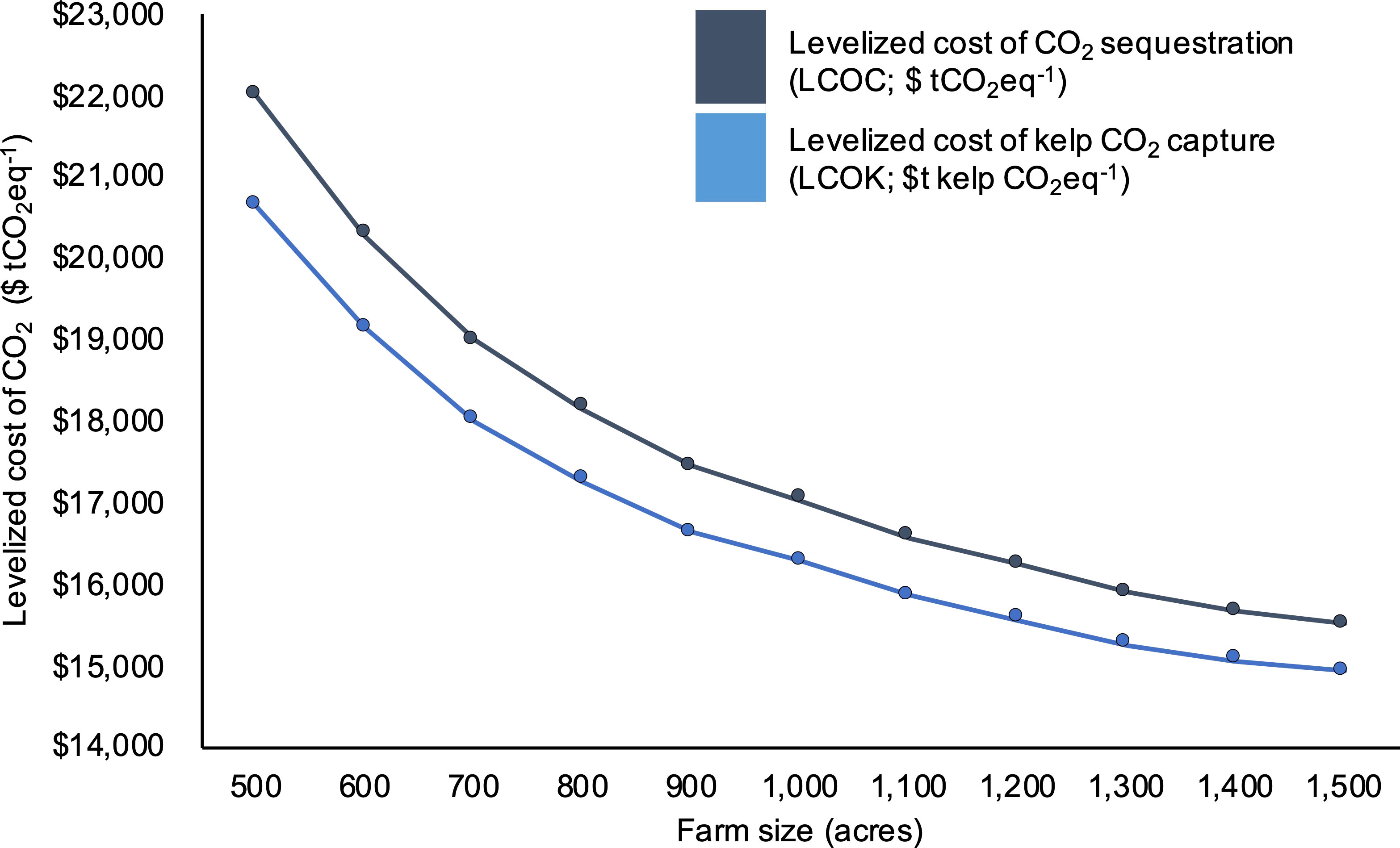
Figure 3 Levelized cost of sequestering a single ton of CO2eq ($ tCO2eq-1; LCOC; dark blue line) and levelized cost of capturing a single ton of CO2eq within kelp biomass prior to transport, verification, and permanent sequestration ($ tCO2eq-1; LCOK; light blue line) as a function of farm size (acres).
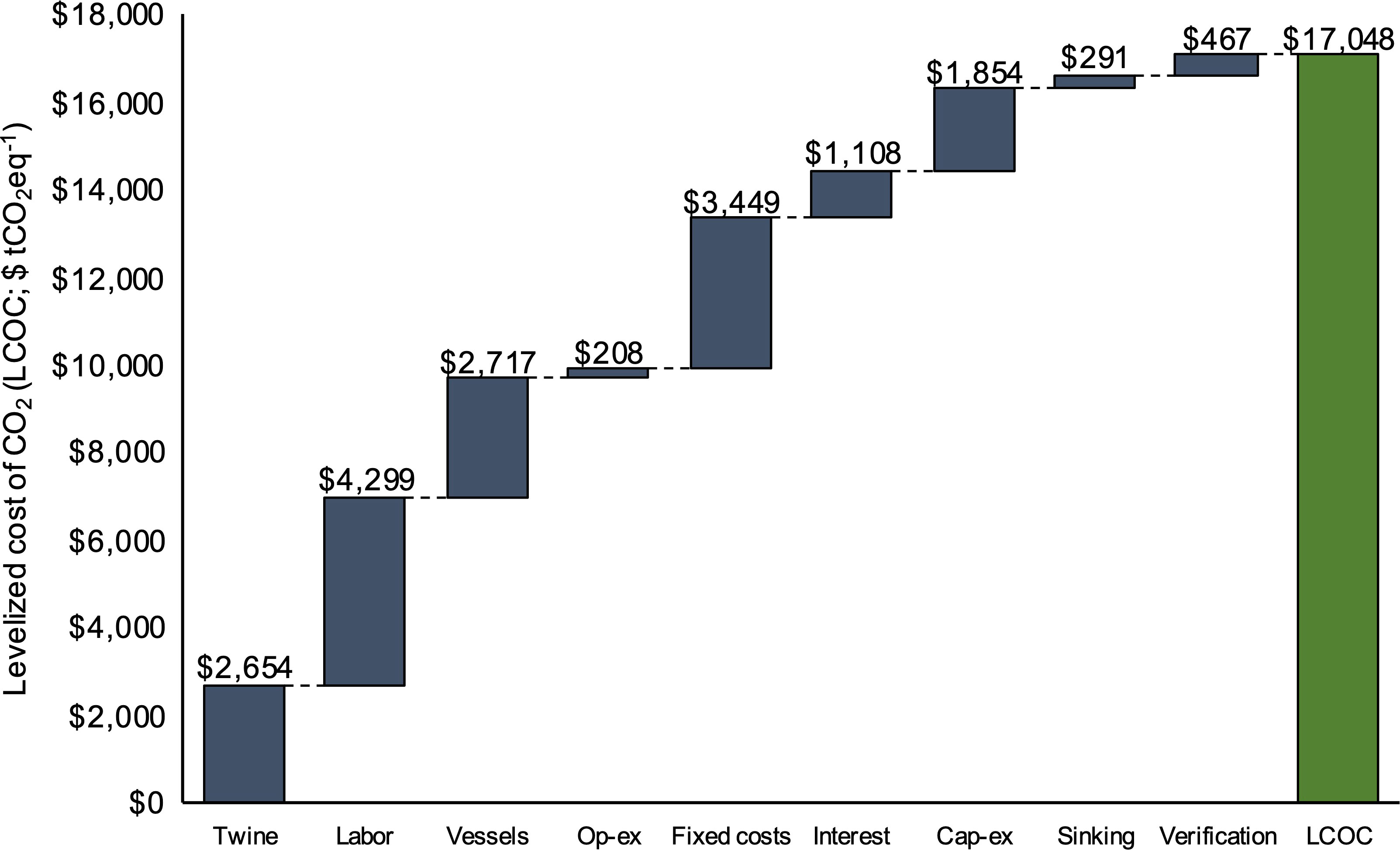
Figure 4 Breakdown of annual expenses within the baseline BTEM for LCOC ($ tCO2eq-1). The category “Vessels’’ includes only the contracted vessels required for typical farm operations. The category “Sinking” captures the cost of biomass transport to the sink site for CDR. The value above the dark blue bars represents the contribution of the specific line item, while the value above the green bar displays the total LCOC.
The baseline farm contained 359,140 m of grow-line. With yields of 12.5 kg WW m-1, 4,489 tons (WW) of kelp were produced annually. Based on the conversion factors within submodel (2), 628 tCO2eq were transported to the sink site, deposited below the sequestration horizon (>1,000 m) using reclaimed concrete, and sequestered each year. After deducting the project emissions calculated in Submodel (3), and the 15% buffer pool from Submodel (4), the baseline farm only issued 244 C credits (tCO2eq) annually, a 384 tCO2eq discount from the full potential of the operation (Figure 5). Therefore, the additionality rate (AR) of the project was 39%. In other words, 61% of the CO2eq sequestered within kelp biomass was negated by the emissions resulting from the operation. Excluding the emissions from transportation to the sink site, the baseline farm produced 0.45 tCO2eq per ton of harvested kelp biomass (DW). The operations of the nursery resulted in the largest annual deduction from the CO2eq sequestration budget, -115 tCO2eq, followed by the annualized upstream GHG impacts of the materials within the cultivation structure (-92 tCO2eq), biomass transport and sinking emissions (-70 tCO2eq), and contracted vessel fuel (-64 tCO2eq). The vast majority of nursery CO2eq emissions stemmed from electricity usage, nearly 90%, a product of sourcing energy from a standard U.S. electricity mix generated primarily from hydrocarbon-based fuels, such as natural gas. The baseline farm sequestered 7,266 tCO2eq over the 30-year lifetime of the project, an average of 0.6 tCO2eq sequestered ha-1 year-1. Therefore, to achieve Gt scale annual sequestration, the baseline farm would need to cover ~16.6 million km2.
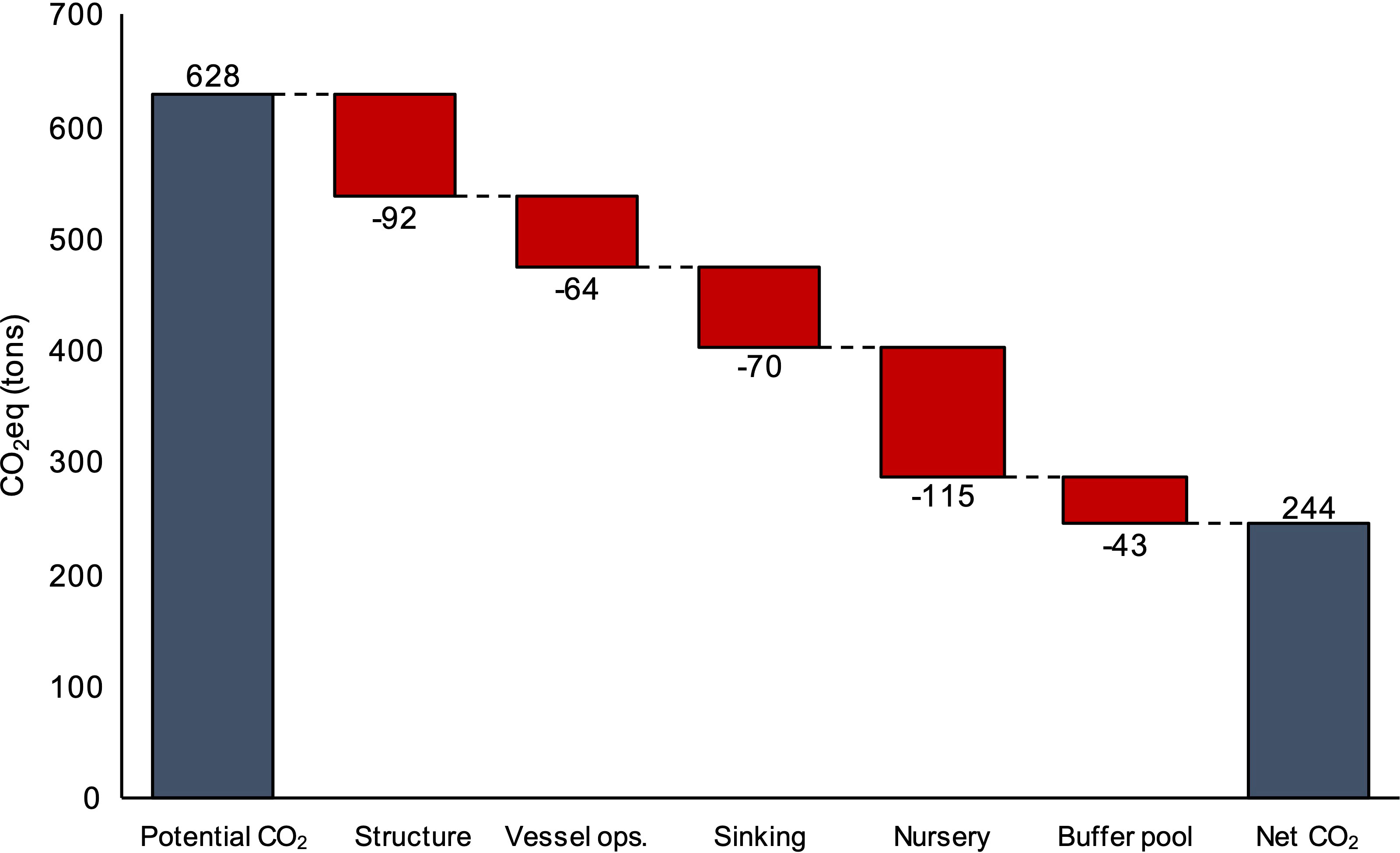
Figure 5 Deductions from the annual quantity of CO2eq sequestered each year within kelp biomass (“Potential CO2”) as a result of annual emissions from farm components (“Structure”), contracted vessel fuel consumption (“Vessel ops.”), biomass transport and sinking (“Sinking”), “Nursery equipment and energy (“Nursery”), and the 15% “Buffer pool”. The emissions represented by “Vessel ops.” do not include the fuel required to transport harvested biomass to the sink site. The category “Sinking” accounts for biomass transport emissions.
The assumptions within submodel (2) (kelp moisture content, tissue C content, and yield) were by far the most influential factors in the sensitivity analysis. A 40% decrease in either the % kelp dry weight or the C content of kelp dry matter resulted in a ~$55,000 increase in LCOC (Figure 6). The required biomass transport distance (km), the duration of the nursery grow-out period (days), and the harvest labor requirements (FTE person hours per ton of harvested biomass) were the next most sensitive parameters (Figure 6). A 40% increase or decrease in these variables resulted in 15 - 25% changes in levelized sequestration costs.
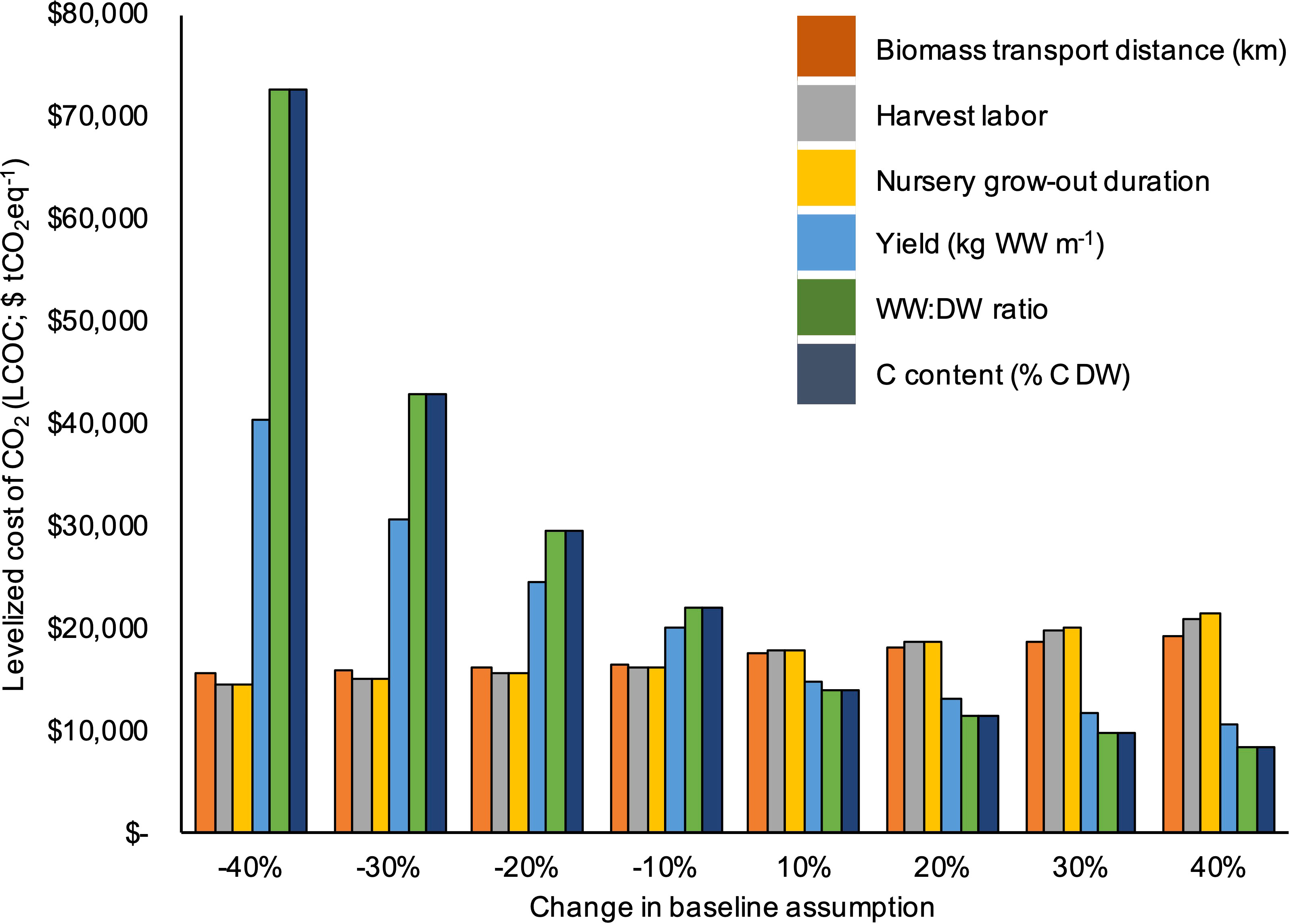
Figure 6 Results of a sensitivity analysis in which the required biomass transport distance (km), harvest labor requirements (FTE hours per ton of harvested biomass), nursery grow-out duration (days), yield (kg m-1), kelp WW : DW ratio (% WW), and kelp C content (% DW) were all changed in 10% increments to a range of +/- 40%. Parameters were changed individually while holding all others constant so as to assess the relative importance of each assumption.
The line of sight optimization pathways towards cost reduction and additionality rate (AR) increase were broken down into five categories: (1) Nursery, (2) Ocean cultivation, (3) Kelp biology, (4) Biomass transport, and (5) Verification. By combining all 18 line of sight improvements to the baseline farm, LCOC fell from $17,048 to $1,257 tCO2eq-1 (Figure 7; (Table S6), a ~14 factor reduction in levelized costs. Changing the assumptions for harvest labor requirements (FTE hours per ton of harvested kelp), the size of the spools within the nursery (m of twine per spool), and the kelp WW : DW ratio to the optimal values identified in the literature led to the largest reductions in LCOC: -$3,787, -$1,929, and -$1,904 tCO2eq-1, respectively. Reducing the nursery grow-out duration (days) and the emissions from the nursery energy supply (kg CO2eq per kWh) were the next two most impactful changes resulting in $1,823 and $1,679 reductions in LCOC, respectively (Figure 7). Only 12 of the 18 parameters impacted the AR of the baseline farm. Changing these 12 parameters to the optimum value identified in the literature increased AR from 39% to 91%, and generated a ~7 factor increase in the quantity of credits issued each year (Figure 8; (Table S6). Decreasing the buffer pool from 15% to 2% led to a 12% increase in AR, the most significant improvement. Increasing the C content of the kelp dry matter and sourcing the nursery electricity from renewables (i.e., a reduction in kg CO2eq per kWh) resulted in 8% and 7% increases in AR, respectively, the next two most impactful changes. Notably, increasing the capacity of the PVC spools within the nursery to each hold 642 m of twine (up from the baseline assumption of 132 m) led to a 5% increase in AR.
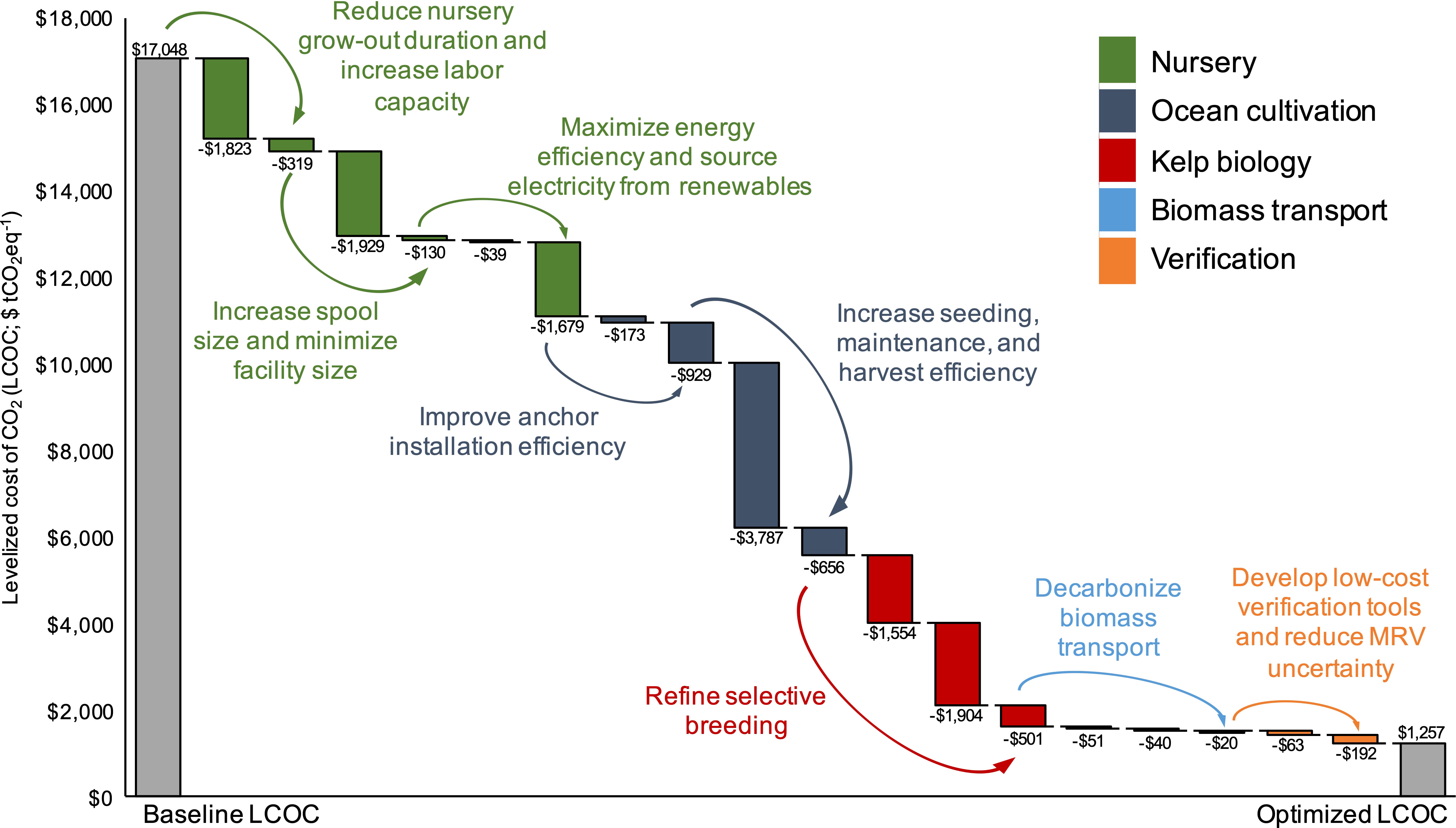
Figure 7 Optimization analysis in which the values for 18 key parameters were sequentially changed to either the minimum or maximum value identified in literature reviews that improved (lowered) levelized sequestration costs ($ tCO2eq-1). The changes were then combined to calculate an “optimized” LCOC as a result of process improvement and cost reductions (gray column). Colors correspond to the 5 areas of potential improvements: nursery production (green), ocean cultivation (dark blue), kelp biology (red), biomass transport (light blue), and verification (orange).
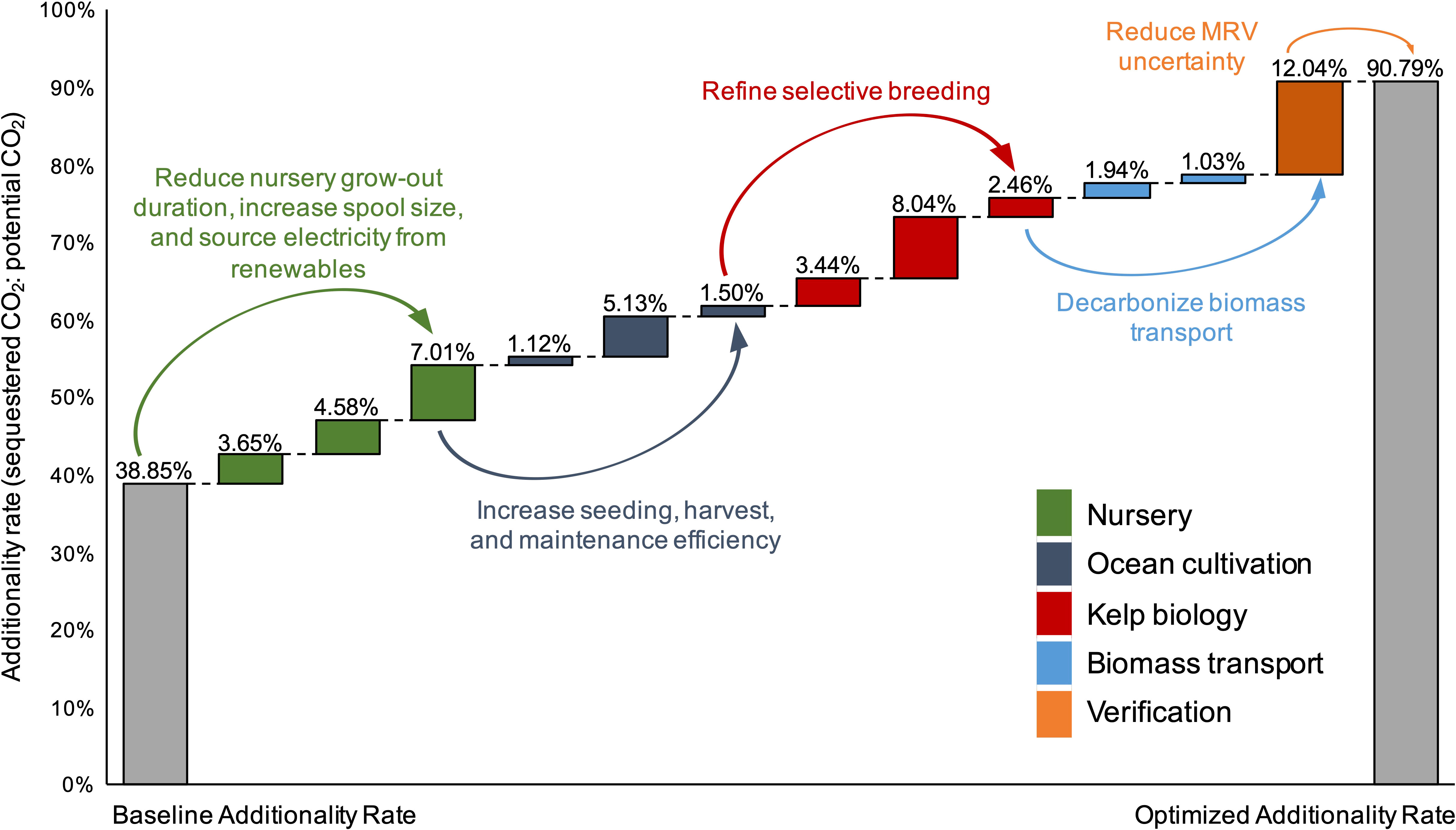
Figure 8 Optimization analysis in which the values for 12 key parameters were sequentially changed to either the minimum or maximum value identified in literature reviews that improved (increased) the additionality rate (AR) of the baseline farm (ratio of annual C credits produced: tCO2eq sequestered annually, expressed as a %). The changes were then combined to calculate an “optimized” AR as a result of process improvement (gray column). Colors correspond to the 5 areas of potential improvements: nursery production (green), ocean cultivation (dark blue), kelp biology (red), biomass transport (light blue), and verification (orange).
The learning rate (LR) analysis indicated that significant cost reductions would have to accompany increases in project scale for kelp CDR to serve as an effective climate change mitigation technology. Even when starting with the optimized LCOC of $1,257 tCO2eq-1, the magnitude of the chosen LR had a large impact on the ocean area required to achieve the cost target of <$100 CO2eq-1. For example, assuming a relatively high learning rate of 20%, the optimized farm reached a LCOC of <$100 tCO2eq-1 at a scale of 16,589 km2 (Figure 9). However, with a LR of only 5%, the optimized farm required 4.6 x 1015 km2 to reach a levelized sequestration cost of <$100 tCO2eq-1 (Figure 9). Based on the sequestration rate of the optimized farm, 410 tCO2eq km-2, the project would need ~2.4 million km2 to achieve Gt scale sequestration (1 Gt of CO2eq sequestered year-1).
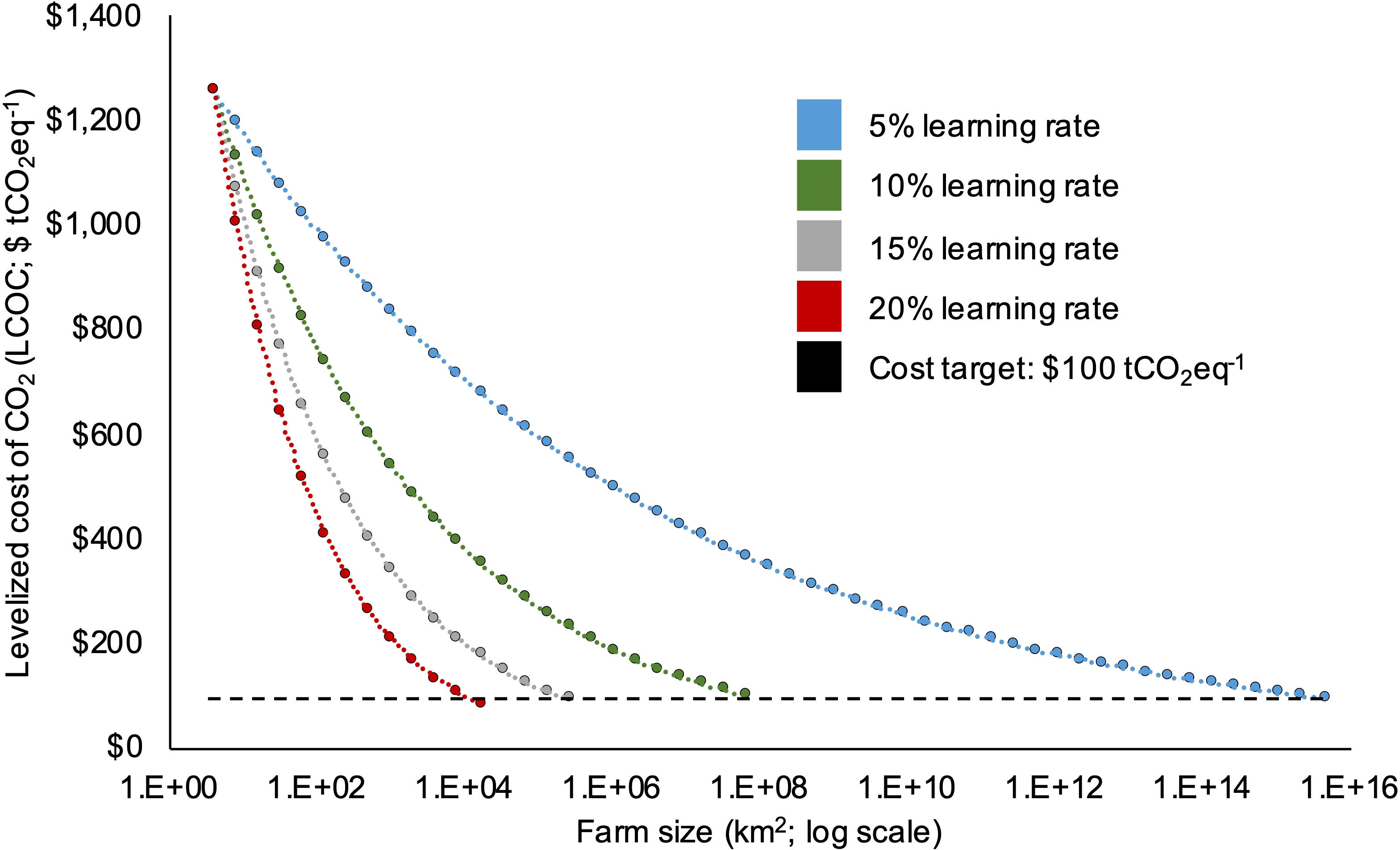
Figure 9 Levelized cost of CO2 (LCOC; $ tCO2eq-1) as a function of farm size (km2) under four learning rate (LR) scenarios: 5%, 10%, 15%, and 20% reductions in cost with each doubling of scale. The horizontal dashed line denotes a hypothetical cost target of $100 tCO2eq-1. The “optimized” bio-techno-economic model ($1,257 tCO2eq-1) was used as the starting point in this analysis.
Discussion
Significant commercial and research interest has recently flowed to the concept of growing and then sinking large quantities of kelp as a means of sequestering CO2 (Hurd et al., 2022) and supporting information therein). Kelp CDR may have potential advantages over both “nature based” and “engineered” solutions (NASEM, 2021). Given that growers can determine the timing and location of sinking, MRV of kelp CDR may eventually overcome some of the challenges facing other blue carbon approaches that simply aim to enhance standing biomass stocks, such as ecosystem restoration (Ortega et al., 2019). Furthermore, kelp aquaculture can provide numerous co-benefits to both ecosystems and coastal communities (Duarte et al., 2021; Theuerkauf et al., 2022). However, these tradeoffs remain to be resolved, and the results of our model are interpreted through a strictly techno-economic approach. It should be underscored that there are still fundamental, unanswered questions regarding potentially hazardous spillover effects, the durability of kelp C storage, relevant biogeochemical constraints and uncertainties, and overall environmental impact that ought to be explored alongside discussions of economic feasibility.
We took a hyper-realistic approach to estimating the costs and additionality of kelp aquaculture CDR and our results suggest that leveraging kelp farming as a means of selling C credits, under current assumptions, would generate production costs at the upper end of the range for CDR technologies: $17,048 tCO2eq-1. In the absence of optimization, the method would likely be cost and space prohibitive (Fuss et al., 2018). To achieve Gt-scale CO2 removal would require $1.7 x 1013 in annual investment, ~20% of global GDP2), and a farming area of ~16.6 million km2, ~1.5x the size of the U.S. exclusive economic zone (EEZ). However, we also identified optimization pathways that capture the “line of sight” improvements required to both cost effectively scale and decarbonize kelp cultivation. The combined effects of the optimization analysis led to a ~14 factor decrease in levelized costs, $1,257 vs. $17,048 CO2eq-1 (Figure 7), as well as a 7 factor increase in the annual quantity of CO2eq sequestered over the 30-year lifespan of the 1,000 acre (404.5 ha) project (Figure 8).
Our analysis highlights the challenges of not only generating verifiable kelp C credits, but also cultivating macroalgae at a large scale in deep water (>100 m) exposed sites. To reduce costs, the sector will need to de-risk alternative cultivation system designs, develop innovative seeding and harvesting methods, optimize selective breeding in conjunction with nursery production, and decarbonize kelp aquaculture at all points of the production process, i.e., from the nursery to the sink site. Ocean cultivation labor, seeded twine, vessel contracting, and mooring installation were the main drivers of expenses within the model (Figure 4). The energy required to produce seeded twine within the nursery, manufacture the materials within the cultivation structure, and transport biomass to the sink site were the largest sources of CO2eq emissions and led to substantial reductions in the annual quantity of available C credits (Figure 5). Model outputs were most sensitive to changes in yield (kg m-1), the conversion from WW to DW, and kelp C content (Figure 6). We also observed that resolving MRV uncertainty can dramatically increase the net quantity of C credits produced each year, as demonstrated by the effect that a 15% buffer pool had on the C budget within the BTEM. The extent to which kelp CDR is able to overcome these R&D, regulatory, and MRV challenges, and accelerate towards an optimized $1,257 tCO2eq-1 cost target and beyond (i.e., $100 tCO2eq-1), will ultimately determine the future potential of this emerging technology.
The “high-volume, low-value” Hasselström et al., 2020) application of kelp for CDR necessitates cultivation system designs that maximize available growing area while minimizing cap-ex and anchor installation costs. Our design process highlighted the challenges of balancing the quantity of available cultivation substrate with the aspect ratio of, and thus the loads on, the structure at large scales. The intent of the baseline model was to apply existing approaches to deep water sites in fully exposed conditions. Most farms in Maine, the study region, are sited in sheltered areas (<13 m depth) and consist of single culture lines with a mooring at each end (Flavin et al., 2013). This design was expanded and modified to be an array of multiple grow-lines with 4 m spacing, suitable for deep-water, exposed conditions. The system was specified such that the grow-lines were held in tension with a 4-point, spread mooring system connected to a header rope (Figure 2). The configuration consisted of mooring floats, anchor chain and surface floats every 12 m to maintain a nominal cultivation line grow depth of 2 m. However, even with pretensioning, the structure still required the use of 42,000 surface floats across all 1,000 acres to support the kelp as it grew (Table S1). In addition to the biomass, these floats are subjected to surface currents and winter storm waves, thereby increasing structural loads and thus cap-ex and embedded emissions.
The usable grow-area was increased by using high-efficiency drag embedment anchors to enable a minimal 3:1 mooring scope and a 10:1 ratio of structure length to width (Figure 2). However, we were still only able to fit ~89 km of grow-line within each km2 of lease area. In a recent techno-economic analysis of macroalgae CDR, (DeAngelo et al. (2022)) assumed a grow-line quantity of ~666 km per km2 of lease area, and estimated a C sequestration cost of ~$500 tCO2eq-1. The discrepancy in cost estimates is partially driven by differences in grow-line density between the two studies, and thus macroalgae biomass yields, the most sensitive parameter within our analysis (Figure 6). If farms are able to move into larger, contiguous offshore lease sites, such as the recently established U.S. Aquaculture Opportunity Areas (Morris, 2021; Riley, 2021), operators will be forced to contend with the design challenges noted here. Furthermore, the installation requirements of industrial scale anchors are a significant financial hurdle. The baseline farm required an initial construction investment (mooring installation alone) of ~$6.2 million, a value that made up nearly 12% of total levelized costs despite occurring only once (Figure 4).
These constraints suggest that the industry should continue to explore lower-cost mooring systems (including installation costs) and de-risk alternative farm and lease configurations that make more efficient use of ocean space. The latter could include reducing mooring scope, e.g. (Moscicki et al. (2022)), utilizing more vertical space in the water column, e.g. (Bak et al. (2018)) and (van Oirschot et al. (2017)), and decreasing horizontal line spacing. Expanding cultivation line diameter or using non-rope components (e.g., pipe) with larger dimensions may also increase yield for each meter of growth and address marine mammal entanglement prevention criteria. Flotation could also be incorporated with these larger cultivation components. Cost-sharing with other offshore ocean users, such as wind energy producers (Buck et al., 2010; Schupp et al., 2021) could reduce fixed permitting and siting costs, which made up 5% of the LCOC. Techniques used to calculate the dynamic loads on farm “c” and any future design iterations, including the calculations of the velocity reduction through the farm, represent an area of uncertainty, especially since the cap-ex associated with the 40 anchors is substantial. Validation efforts with in-situ measurements, additional tank tests, and other computational techniques, especially at the farm scales considered here, would provide more confidence in the load carrying requirements for the cultivation system, and could allow designers to reduce the required uncertainty factors when specifying structural components.
The next generation of kelp farm designs must also optimize labor requirements, as there will likely be tradeoffs between minimizing cap-ex and efficient seeding, maintenance, and harvest practices. Reducing the harvest labor requirements (FTE hours per ton of harvested biomass) to the lowest value identified in the literature (Correa et al., 2016) resulted in a $3,787 reduction in levelized sequestration costs (Figure 7). Furthermore, optimizing all three production steps led to a combined 7.8% increase in AR and avoided ~57 tCO2eq of annual emissions (Figure 8). The reduction in person hours necessitated fewer vessel trips to the farm site, and thus less fuel usage. Therefore, the harvest practices currently utilized by growers in emerging farming regions will pose a bottleneck, both from a cost and emissions standpoint, as farms expand into larger offshore sites. Identifying methods to automate these steps should be an immediate priority (Zhang et al., 2017). Improved cultivation systems, spray-on seeding of adult sporophytes at sea (Kerrison et al., 2018), and innovative harvest practices designed specifically to transport kelp biomass long distances may drive labor cost reductions.
The timing of harvest may be optimized specifically for kelp CDR. Producers typically remove food-grade plants from the farm site in the early spring, before the onset of fouling organisms and epibionts. However, kelp CDR operators may be able to continue the grow-out process well into the summer, thereby potentially increasing total biomass (of both kelp and fouling organisms also made of organic C) and avoiding competition with harvesting vessels contracted for other kelp uses. Utilizing kelp aquaculture infrastructure outside of the typical farming season could provide seasonal employment opportunities as well as reduce the cost of renting vessels that would otherwise be in high-demand. While the notion of an extended growing season has intriguing potential benefits, there remain large ecological unknowns regarding the epibiont, infaunal and meifaunal communities that may associate in unexpected ways with offshore kelp and farm structures at this scale. Natural analogs demonstrate that large macroalgae rafts are important habitats as well as vectors for the spread of invasive species (Avila et al., 2020; Fraser et al., 2011). At sea transportation to sinking sites and inadequate containment during sinking may promote the movement of invasive species and the dislocation and demise of many marine organisms other than kelp. Large scale farms may also serve as fish aggregating devices (FADs) or as unexpected nursery habitat for marine species, similar to the ecological function of sargassum, that would be disrupted by annual harvest and removal of biomass (Rothäusler et al., 2012). These critical ecological issues should be studied
The sensitivities within the BTEM dictate that both the biomass yield and biomolecular composition of cultivated kelp will ultimately exert the largest impact on the economic viability of macroalgae CDR. Even with innovative farm designs that maximize 3D ocean space and more efficient labor practices, producers will likely need to leverage selective breeding techniques to increase growth rates and C content, while also reducing moisture content (Augyte et al., 2020; Umanzor et al., 2021; Zhao et al., 2016). Based on the hypothetical sensitivity analysis, a 40% increase in either kelp dry matter or C content resulted in a 50% decrease in levelized sequestration costs (Figure 6). With yields of 12.5 kg WW m-1 (Stekoll et al., 2021), the farm produced ~1.5 t DW ha-1 year-1, well below the MARINER programmatic target of 25 t DW ha-1 year-1 (ARPA-E, 2017). In a common garden experiment of 100 unique parental kelp crosses in Maine USA, (Umanzor et al. (2021)) observed a 50 factor difference in yield between the fastest and slowest growing replicates. The results of their study underscore the phenotypic variation that can occur within a population derived from genetically similar sources of kelp broodstock, the heritability of these traits, and thus the relatively rapid improvements that can be achieved within only a few seasons of selection (Umanzor et al., 2021). (Froehlich et al. (2019)) estimated that, with yields of 32 t DW ha-1, the costs of kelp CDR in the North Sea would be between $1,219 - $1,924 tCO2eq-1 (Froehlich et al., 2019). When compared to our estimates of both yield (1.5 t ha-1 year-1) and cost ($17,048 tCO2eq-1), it is clear that selecting for optimal biomolecular composition and fast growth will be a powerful tool in reducing the levelized sequestration costs of kelp CDR.
In the absence of selective breeding, exogenous oceanographic factors at offshore sites may prevent economically viable kelp growth rates. Dense canopies of surface cultured kelp attenuate flow within the farm, depleting nutrients and potentially leading to decreased growth (Frieder et al., 2022). However, the greater line spacing required for open-ocean sites and the smaller fraction of the water column occupied by the biomass due to the greater water depth may result in less flow attenuation than in dense farms at protected sites. Ambient Winter surface nutrient (specifically Nitrate) conditions in offshore regions may be limiting to the extent that farmers would be unable to replicate the yields (i.e., 12 kg m-1 WW) from nearshore and coastal sites (Rebuck and Townsend, 2014; Wu et al., in review). Maximizing kelp growth is an exercise in both site selection and production optimization. Line spacing, depth, and seeding and harvest timing must all be balanced (Broch et al., 2013; Bruhn et al., 2016; Peteiro & Freire, 2013). However, if kelp aquaculture is forced to move into more oligotrophic offshore areas due to competition with other users for coastal space (van den Burg et al., 2020), in situ measurement of growth rates will be required to accurately assess the potential of large scale cultivation. The increased line spacing (4m) required by the exposed deep water baseline site may mitigate potential nutrient depletion issues, as the grow-line only occupies ~5% of the water column. Laboratory and nearshore common garden experiments must be complemented by pilot and commercial scale demonstrations to validate projected yields.
In addition to providing the necessary platform for selective breeding, improved nursery practices could have the complementary benefits of reduced operating expenses coupled with decarbonization. Optimizing the nursery assumptions within the BTEM resulted in an aggregate 35% reduction in levelized costs, as well as a 15% increase in AR (Figure 7). At a scale of 1,000 acres, the facility emitted ~112 tCO2eq year-1 from the direct consumption of electricity, and another ~2.7 tCO2eq year-1 from the upstream manufacturing of equipment (Table S4). Reducing the sporophyte grow-out duration from 44 to 33 days resulted in a 27 ton decrease in annual CO2eq emissions and a ~$1,800 decrease in levelized costs (Figure 7). Sourcing the nursery electricity exclusively from renewables led to an additional ~85 ton decrease in annual CO2eq emissions and a $1,679 reduction in LCOC (Figure 7), despite the fact that nursery electricity costs alone comprised less than 1% of total expenses (Coleman et al., 2022). Across all 18 parameters, the second largest reduction in LCOC within the optimization analysis came from maximizing the size of the PVC spools: a $1,929 decrease in LCOC and a 5% increase in AR (Figure 7). Increasing spool size or sourcing electricity strictly from renewables would be a relatively low-technology risk pathway for nursery operators in the near term. However, identifying methods to reduce the duration of the sporophyte grow-out period would require further study of optimal light, nutrient, aeration, and production strategies (Camus & Buschmann, 2017).
Improved and de-risked gametophyte culture could reduce the amount of time that kelps are held on spools within tanks (Alver, 2019), which would have knock-on effects for both the cost structure and emissions profile of land-based nursery facilities. Despite inconsistent success in the field, spools seeded with gametophytes (as opposed to spores) would only require a 14 - 21 day grow-out period in illuminated and temperature controlled tanks (Forbord et al., 2020). This timeline represents a substantial reduction from the baseline grow-out length of 44 days (Coleman et al., 2022). Furthermore, maintaining gametophyte stocks optimized for yield, C content, and moisture content would allow growers to eventually access free-floating sporophyte culture and direct seeding of grow-lines at sea (Alver et al., 2018). The process of tumble culturing free-floating kelps within large flasks has been shown to reduce space requirements by nearly 99% (Kerrison et al., 2018), and eliminate the need for PVC spools and twine entirely. It must be noted, however, that gametophyte culture would require maintaining vegetative stocks year-round, leading to potentially unforeseen energy demands or labor increases. Based on the relationships we observed between nursery emissions and costs within the BTEM, we argue that these tradeoffs should be explored within a comprehensive framework. Similarly, utilizing larger, flow-through systems might lead to a reduction in direct energy consumption if ambient light or more efficient chillers could be employed at larger scales (Greene et al., 2020; Su et al., 2017). Small-scale recirculating systems allow for redundancy and thus built-in biosecurity measures. Shifting to larger, flow-through tanks would allow nurseries to maximize space, but could also increase the risk of catastrophic product loss. Further research of the potential economic risks and benefits of these pathways is needed before such systems could be employed commercially.
As technologies mature, the application of learning rates (LRs) can help uncover the impact of unforeseen cost reductions that are typically driven by learning by doing, investment in R&D, and economies of scale. The optimized BTEM represents a best-case view of the costs of kelp CDR based on “line of sight” improvements that exist within current kelp cultivation systems. However, selective breeding, optimized gametophyte culture, improved offshore farm designs, and future technologies that lead to decarbonization of supply chains represent pathways of cost reduction with potential unforeseen consequences best captured by the application of learning rates. A “top-down” LR analysis (Faber et al., 2022), such as the one presented here (Figure 9), can allow researchers and policy makers to back into a relevant commercial scale or specific LR required to achieve financial viability for an early stage technology (Héder, 2017). As kelp CDR matures, applying empirical LRs calculated from historic production data to discrete techno-economic mechanisms would allow stakeholders to more accurately predict how reductions in e.g., per unit labor costs, cap-ex, or raw material costs may impact total levelized sequestration costs (Thomassen et al., 2020). A relevant application of this concept would be to quantify the effect that increases in farm size would have on the emissions profile of the operation (kg CO2eq emitted per unit of kelp harvested), and thus the true additionality of kelp CDR (Faber et al., 2022). The lack of historical production data for kelp farming in emerging regions (i.e., outside of the Pacific Rim), as well as the low technology readiness level of kelp farming specifically for CDR, pose a challenge to accurate cost and climate potential forecasting (Wender et al., 2014). As the kelp aquaculture industry expands in North America, Europe, and South America, the growing body of economic and lifecycle benchmarking data should be utilized to resolve these uncertainties (Engle et al., 2020; Thomas et al., 2021).
While the majority of our analysis focuses on strategies to reduce the direct costs and emissions footprint of kelp cultivation, it is clear that inaccurate Monitoring, Reporting, and Verification (MRV) will be a strong bottleneck to future scaling. There is considerable uncertainty concerning the rate at which the uptake of DIC by kelp will impact atmospheric CO2 concentrations, the fate of kelp derived POC after deep-sea deposition, and the durability of storing remineralized CO2 in the deep ocean (Bach et al., 2021). The lag in re-equilibration between the ocean and atmosphere after DIC uptake by kelps may not lead to a strict 1:1 ratio of CO2 sequestered within kelps to the quantity removed from the atmosphere (Bach et al., 2021). Using a 1:1 ratio, we demonstrated that a 17 factor reduction in costs ($1,257 vs. $17,048 tCO2eq-1) was possible if production could be optimized (Figure 7). However, if the ratio of sequestered CO2 within kelp to atmospheric CO2 removal drops to 50%, the cost (even under optimized conditions) doubles ($2,731 tCO2eq-1). Furthermore, the accuracy with which models and in situ measurements are able to track the fate of kelp POC and any remineralized C within the deep sea (Siegel et al., 2021) will determine the magnitude of the required buffer pool (Matzek et al., 2015). Under optimized assumptions, the AR of the farm was 91% (Figure 8). However, if the uncertainty factor regarding the quantity of deposited CO2 that re-enters the atmosphere before the 100 year target is 25%, then the buffer pool must be increased to 25% and the AR of the optimized farm drops from 91% to 74%. Developing accurate MRV protocols should be prioritized to the same extent as reducing the costs of kelp cultivation given the influence C accounting will have on the bottom line of future projects.
Ultimately, negative emissions technologies must be rigorously assessed based on their net benefits and risks to both society and ecosystems. While outside the scope of the present analysis, (Boyd et al. (2022)) discuss the potential impacts that large-scale kelp cultivation and subsequent deep-sea deposition could have on open-ocean ecosystems. Introducing a new species to regions of the ocean that underpin food systems, the blue economy (FAO, 2020), and global net primary productivity (Kwiatkowski et al., 2020) is inherently risky. Kelps may compete with local planktonic communities for limited nutrients, such as N and P, and light, leading to a decline in NPP and the efficiency of the biological carbon pump (Frieder et al., 2022). The increased oxygen demand at the sea floor of kelp deposition sites could also reduce sediment aerobic depth with trickle down effects on the understudied benthos (Wu et al., 2022). The space required for kelp CDR to effectively draw down atmospheric CO2 could not only pose a major bottleneck to scaling, but also displace and compete with other ocean users. Based on the optimized BTEM, ~2.4 million km2 would be needed to sequester a Gt of CO2 year-1, an area that is nearly 1,500 times greater than the current space occupied by global macroalgae aquaculture (Duarte et al., 2017). Furthermore, the biomass that would ultimately be deposited in the deep ocean could be used as a nutritious food for humans. The market for seaweed food products is established in Asia and rapidly growing in Europe, North America, and South America (Piconi et al., 2020). The ethics of this dynamic must also be discussed. Identifying a sustainable role for kelp CDR at both a climate relevant and globally responsible scale will be a challenge for regulators, policy makers, industry members, NGOs, and other ocean stakeholders moving forward. Relying on research that is transparent regarding costs, risks, and spillover effects will help guide that decision making in an effective and equitable manner.
Conclusion
We quantified the levelized costs of intentionally sinking cultivated kelp in the deep-ocean to capture and sequester atmospheric CO2. Our baseline approach sheds light on the challenges of cost effectively scaling the production of verified kelp C credits, as well as farming macroalgae at large scales in exposed offshore sites. We estimated that, according to the baseline model, the unit costs of kelp CDR would be $17,048 tCO2eq-1, with a spatial sequestration rate of 0.6 tCO2eq ha-1 year-1. Labor, mooring installation, contracted vessels, and seeded twine made up the largest portions of costs. Nursery production, the manufacturing of materials within the cultivation structure, and biomass transport to the “sink site” were the largest sources of emissions and contributed to an additionality rate (AR) of only 39%. However, we also calculated an “optimized” sequestration cost of 1,257 tCO2eq-1, with an associated AR of 91%, demonstrating that with “line of sight” process improvement and decarbonization, unit costs and emissions could be reduced by orders of magnitude. To reach this hypothetical cost floor, our analysis points towards six key R&D needs: (1) de-risk alternative farm and mooring designs that maximize space and minimize cap-ex, (2) automate the seeding and harvest process, (3) leverage selectively bred kelp strains to maximize C content and yield, (4) assess the cost tradeoffs of gametophyte culture coupled with redesigned nursery protocols, (5) decarbonize equipment supply chains, nursery production, and ocean cultivation by employing low GHG impact materials, sourcing electricity from renewable sources, and increasing labor efficiency, and (6) resolve MRV uncertainty to reduce the buffer pool and maximize net C budgets.
Data availability statement
The original contributions presented in the study are included in the article/Supplementary Material. Further inquiries can be directed to the corresponding author.
Author contributions
SC, DB, TD, DF, AS, and EL contributed to the conceptualization of the work. TD, MM, and DF conducted the cultivation structure design, engineering, and dynamic modeling. SC developed the bio-techno-economic model with input from all authors. SC, KC, TD, and MM led figure and table production. SC wrote the initial draft of the manuscript. DB, DF, AS, EL and TD provided manuscript edits and comments on model analyses. All authors contributed to the article and approved the submitted version.
Funding
This study received funding from Conscience Bay Research, LLC/Conscience Bay Company. The funder had the following involvement with the study: fundraising, conceptualization, manuscript editing. Funding was also provided by the Aquaculture Research Institute in partnership with the University of Maine and the United States Department of Agriculture Aquaculture Experimental Station.
Acknowledgments
We would like to thank Dr. J.B. Thomas of KTH Royal Institute of Technology for providing the materials for the Life Cycle Assessment model and conducting a pre-review of the manuscript. We would also like to acknowledge Matt Lappé of Conscience Bay Research for helping us refine and communicate the message of this work.
Conflict of interest
TD and MM are employed by Kelson Marine Co. DF is employed by Ocean Environmental LLC. EL is employed by Conscience Bay Research, LLC.
The remaining authors declare that the research was conducted in the absence of any commercial or financial relationships that could be construed as a potential conflict of interest
The authors declare that this study received funding from Conscience Bay Research, LLC/Conscience Bay Company. The funder had the following involvement with the study: fundraising, conceptualization, manuscript editing.
Publisher’s note
All claims expressed in this article are solely those of the authors and do not necessarily represent those of their affiliated organizations, or those of the publisher, the editors and the reviewers. Any product that may be evaluated in this article, or claim that may be made by its manufacturer, is not guaranteed or endorsed by the publisher.
Supplementary material
The Supplementary Material for this article can be found online at: https://www.frontiersin.org/articles/10.3389/fmars.2022.966304/full#supplementary-material
Footnotes
- ^ 1https://www.fastcompany.com/90548820/forget-planting-trees-this-company-is-making-carbon-offsets-by-putting-seaweed-on-the-ocean-floor
- ^ 2https://data.worldbank.org/indicator/NY.GDP.MKTP.CD
References
ABS (2012). Guidance notes on the application of fiber rope for offshore mooring [Guidance notes] (American Bureau of Shipping). Available at: https://ww2.eagle.org/content/dam/eagle/rules-and-guides/archives/offshore/90_fiberrope/fiber_rope_gn_e-feb14.pdf.
Alver M. (2019). D5.1 industrial production line for seedling:00075)(SINTEF). Available at: https://sintef.brage.unit.no/sintef-xmlui/bitstream/handle/11250/2582466/302002488-00006%2BD5.1%2BIndustrial%2Bproduction%2Bline%2Bfor%2Bseedlings.pdf?sequence=1&isAllowed=y.
Alver M., Solvang T., Dybvik H. (2018). Sate of the art (SINTEF), 17. Available at: https://sintef.brage.unit.no/sintef-xmlui/handle/11250/2478264.
Anderson K., Peters G. (2016). The trouble with negative emissions. Science 354 (6309), 182–183. doi: 10.1126/science.aah4567
API (2005). Design and analysis of stationkeeping systems for floating structures (American Petroleum Institute). Available at: https://www.api.org/~/media/Files/News/hurricane/2SK_Add.pdf.
ARPA-E (2017). Macroalgae research inspiring novel energy resources (MARINER) program overview (Department of Energy). Available at: https://arpa-e.energy.gov/sites/default/files/documents/files/MARINER_ProgramOverview_FINAL.pdf.
Augyte S., Kim J. K., Yarish C. (2021). Seaweed aquaculture–from historic trends to current innovation. J. World Aquaculture Soc. 52 (5), 1004–1008. doi: 10.1111/jwas.12854
Augyte S., Wikfors G. H., Pitchford S., Marty-Rivera M., Umanzor S., Lindell S., et al. (2020). The application of flow cytometry for kelp meiospore isolation. Algal Res. 46, 101810. doi: 10.1016/j.algal.2020.101810
Avila C., Angulo-Preckler C., Martín-Martín R. P., Figuerola B., Griffiths H. J., Waller C. L. (2020). Invasive marine species discovered on non–native kelp rafts in the warmest Antarctic island. Sci. Rep. 10 (1), 1639. doi: 10.1038/s41598-020-58561-y
Bach L. T., Tamsitt V., Gower J., Hurd C. L., Raven J. A., Boyd P. W. (2021). Testing the climate intervention potential of ocean afforestation using the great Atlantic sargassum belt. Nat. Commun. 12 (1), 2556. doi: 10.1038/s41467-021-22837-2
Bak U. G., Mols-Mortensen A., Gregersen O. (2018). Production method and cost of commercial-scale offshore cultivation of kelp in the faroe islands using multiple partial harvesting. Algal Res. 33, 36–47. doi: 10.1016/j.algal.2018.05.001
Barata P., Spors F., Kennedy P., Platanova-Oquab A., Gadde H. (2016). Carbon credits and additionality past, present, and future (World Bank), 37. Available at: https://openknowledge.worldbank.org/bitstream/handle/10986/24295/K8835.pdf?sequence=2.
Barrón C., Duarte C. M. (2015). Dissolved organic carbon pools and export from the coastal ocean: DOC EXPORT COASTAL OCEAN. Global Biogeochemical Cycles 29 (10), 1725–1738. doi: 10.1002/2014GB005056
Boyd P. W., Bach L. T., Hurd C. L., Paine E., Raven J. A., Tamsitt V. (2022). Potential negative effects of ocean afforestation on offshore ecosystems. Nat. Ecol. Evol. 6, 675–683. doi: 10.1038/s41559-022-01722-1
Bricknell I. R., Birkel S. D., Brawley S. H., Van Kirk T., Hamlin H., Capistrant-Fossa K., et al. (2020). Resilience of cold water aquaculture: A review of likely scenarios as climate changes in the gulf of Maine. Rev. Aquaculture. 13, 460–503. doi: 10.1111/raq.12483
Broch O., Ellingsen I., Forbord S., Wang X., Volent Z., Alver M., et al. (2013). Modelling the cultivation and bioremediation potential of the kelp saccharina latissima in close proximity to an exposed salmon farm in Norway. Aquaculture Environ. Interact. 4 (2), 187–206. doi: 10.3354/aei00080
Bruhn A., Tørring D., Thomsen M., Canal-Vergés P., Nielsen M., Rasmussen M., et al. (2016). Impact of environmental conditions on biomass yield, quality, and bio-mitigation capacity of saccharina latissima. Aquaculture Environ. Interact. 8, 619–636. doi: 10.3354/aei00200
Buck B. H., Ebeling M. W., Michler-Cieluch T. (2010). MUSSEL CULTIVATION AS a CO-USE IN OFFSHORE WIND FARMS: POTENTIAL AND ECONOMIC FEASIBILITY. Aquaculture Economics Manage. 14 (4), 255–281. doi: 10.1080/13657305.2010.526018
Camus C., Buschmann A. H. (2017). Macrocystis pyrifera aquafarming: Production optimization of rope-seeded juvenile sporophytes. Aquaculture 468, 107–114. doi: 10.1016/j.aquaculture.2016.10.010
CEN (1990) Eurocode–basis of structural design. European committee for standardization. Available at: https://www.phd.eng.br/wp-content/uploads/2015/12/en.1990.2002.pdf.
Coleman S., Gelais A. T., Fredriksson D. W., Dewhurst T., Brady D. C. (2022). Identifying scaling pathways and research priorities for kelp aquaculture nurseries using a techno-economic modeling approach. Front. Mar. Sci. 9. doi: 10.3389/fmars.2022.894461
Correa T., Gutiérrez A., Flores R., Buschmann A. H., Cornejo P., Bucarey C. (2016). Production and economic assessment of giant kelp macrocystis pyrifera cultivation for abalone feed in the south of Chile. Aquaculture Res. 47 (3), 698–707. doi: 10.1111/are.12529
Creutzig F. (2016). Economic and ecological views on climate change mitigation with bioenergy and negative emissions. GCB Bioenergy 8 (1), 4–10. doi: 10.1111/gcbb.12235
Currenti R., Pearce T., Salabogi T., Vuli L., Salabogi K., Doran B., et al. (2019). Adaptation to climate change in an interior pacific island village: A case study of nawairuku, Ra, Fiji. Hum. Ecol. 47 (1), 65–80. doi: 10.1007/s10745-019-0049-8
Czyrnek-Delêtre M. M., Rocca S., Agostini A., Giuntoli J., Murphy J. D. (2017). Life cycle assessment of seaweed biomethane, generated from seaweed sourced from integrated multi-trophic aquaculture in temperate oceanic climates. Appl. Energy 196, 34–50. doi: 10.1016/j.apenergy.2017.03.129
DeAngelo J., Saenz B., Arzeno-Soltero I., Frieder C., Long M., Hamman J., et al. (2022). Economic and biophysical limits to seaweed-based climate solutions. Earth Sci. doi: 10.31223/X5PG9V
DeCew J., Tsukrov I., Risso A., Swift M. R., Celikkol B. (2010). Modeling of dynamic behavior of a single-point moored submersible fish cage under currents. Aquacultural Eng. 43 (2), 38–45. doi: 10.1016/j.aquaeng.2010.05.002
Dewhurst T. (2016) DYNAMICS OF a SUBMERSIBLE MUSSEL RAFT. Available at: https://scholars.unh.edu/dissertation/1380/.
Dewhurst T., Hallowell S. T., Newell C. (2019) International Conference on Ocean, Offshore and Arctic Engineering in Dynamics of an Array of Submersible Mussel Rafts in Waves and Current, Vol. 7A, Ocean Engineering, V07AT06A045. , Glasgow, Scotland, Ocean, Offshore and Arctic Engineering Division. doi: 10.1115/OMAE2019-96388
DMR (2021). Aquaculture leases (Maine Department of Marine Resources). Available at: https://www.maine.gov/dmr/aquaculture/leases/index.html.
Duarte C. M., Bruhn A., Krause-Jensen D. (2021). A seaweed aquaculture imperative to meet global sustainability targets. Nat. Sustainability. 5, 185–193; 58. doi: 10.1038/s41893-021-00773-9
Duarte C. M., Cebrián J. (1996). The fate of marine autotrophic production. Limnology Oceanography 41 (8), 1758–1766. doi: 10.4319/lo.1996.41.8.1758
Duarte C. M., Wu J., Xiao X., Bruhn A., Krause-Jensen D. (2017). Can seaweed farming play a role in climate change mitigation and adaptation? Front. Mar. Sci. 4. doi: 10.3389/fmars.2017.00100
Edmonds J., Luckow P., Calvin K., Wise M., Dooley J., Kyle P., et al. (2013). Can radiative forcing be limited to 2.6 wm–2 without negative emissions from bioenergy AND CO2 capture and storage? Climatic Change 118 (1), 29–43. doi: 10.1007/s10584-012-0678-z
Engle C., van Senten J., Schwartz M., Brayden C., Belle S. (2020). Benchmarks for mussel, oyster, scallop, and seaweed culture in Maine [Benchmarking study] (Maine Aquaculture Association). Available at: https://maineaqua.org/benchmarking/.
EPA (2021). Inventory of U.S. greenhouse gas emissions and sinks (Environemtnal Protection Agency), 791. Available at: https://www.epa.gov/ghgemissions/inventory-us-greenhouse-gas-emissions-and-sinks-1990-2019.
Faber G., Ruttinger A., Strunge T., Langhorst T., Zimmermann A., van der Hulst M., et al. (2022). Adapting technology learning curves for prospective techno-economic and life cycle assessments of emerging carbon capture and utilization pathways. Front. Climate 4. doi: 10.3389/fclim.2022.820261
Filbee-Dexter K., Pessarrodona A., Duarte C. M., Krause-Jensen D., Hancke K., Smale D., et al. (2022). Seaweed forests are carbon sinks that can mitigate CO2 emissions (EcoEvoRxiv). doi: 10.32942/osf.io/ya7wf
Flavin K., Flavin N., Flahive B. (2013). Kelp farming manual: A guide to the processes, techniques, and equipment for farming kelp in new England waters (Ocean Approved, LLC). Available at: https://static1.squarespace.com/static/52f23e95e4b0a96c7b53ad7c/t/52f78b0de4b0374e6a0a4da8/1391954701750/OceanApproved_KelpManualLowRez.pdf.
Forbord S., Braaten Steinhovden K., Kjølbo Rød K., Handå A., Skjermo J. (2018). “Cultivation protocol for saccharina latissima,” in Protocols for macroalgae research, 1st ed, vol. Vol. 1. (CRC Press), 518. Available at: https://www.taylorfrancis.com/books/edit/10.1201/b21460/protocols-macroalgae-research-b%C3%A9n%C3%A9dicte-charrier-thomas-wichard-reddy.
Forbord S., Steinhovden K. B., Solvang T., Handå A., Skjermo J. (2020). Effect of seeding methods and hatchery periods on sea cultivation of saccharina latissima (Phaeophyceae): A Norwegian case study. J. Appl. Phycology 32 (4), 2201–2212. doi: 10.1007/s10811-019-01936-0
Forest Trends’ Ecosystem Marketplace (2021). ‘Market in motion’, state of voluntary carbon markets 2021 (Forest Trends Association). Available at: https://www.ecosystemmarketplace.com/publications/state-of-the-voluntary-carbon-markets-2021/.
Fraser C. I., Nikula R., Waters J. M. (2011). Oceanic rafting by a coastal community. Proc. R. Soc. B: Biol. Sci. 278 (1706), 649–655. doi: 10.1098/rspb.2010.1117
Fredriksson D. W., Beck-Stimpert J. (2019). Basis-of-Design technical guidance for offshore aquaculture installations in the gulf of Mexico. doi: 10.25923/R496-E668
Fredriksson D. W., Dewhurst T., Drach A., Beaver W., St. Gelais A. T., Johndrow K., et al. (2020). Hydrodynamic characteristics of a full-scale kelp model for aquaculture applications. Aquacultural Eng. 90, 102086. doi: 10.1016/j.aquaeng.2020.102086
Frieder C. A., Yan C., Chamecki M., Dauhajre D., McWilliams J. C., Infante J., et al. (2022). A macroalgal cultivation modeling system (MACMODS): Evaluating the role of physical-biological coupling on nutrients and farm yield. Front. Mar. Sci. 9. doi: 10.3389/fmars.2022.752951
Froehlich H. E., Afflerbach J. C., Frazier M., Halpern B. S. (2019). Blue growth potential to mitigate climate change through seaweed offsetting. Curr. Biol. 29 (18), 3087–3093.e3. doi: 10.1016/j.cub.2019.07.041
Frontier N., de Bettignies F., Foggo A., Davoult D. (2021). Sustained productivity and respiration of degrading kelp detritus in the shallow benthos: Detached or broken, but not dead. Mar. Environ. Res. 166, 105277. doi: 10.1016/j.marenvres.2021.105277
Fuss S., Lamb W. F., Callaghan M. W., Hilaire J., Creutzig F., Amann T., et al. (2018). Negative emissions–part 2: Costs, potentials and side effects. Environ. Res. Lett. 13 (6), 063002. doi: 10.1088/1748-9326/aabf9f
Gaines S. D., Bradley D., MacAdam-Somer I., Couture J., Racine P., Froehlich H. E., et al. (2019). The carbon offsetting potential of seaweed aquaculture (University of California Santa Barbara), 58. Available at: https://emlab-ucsb.shinyapps.io/shiny_aquaculture/.
Gallagher J. B., Shelamoff V., Layton C. (2022). Seaweed ecosystems may not mitigate CO2 emissions. ICES J. Mar. Sci. 79, fsac011. doi: 10.1093/icesjms/fsac011
Gansel L. C., Oppedal F., Birkevold J., Tuene S. A. (2018). Drag forces and deformation of aquaculture cages–full-scale towing tests in the field. Aquacultural Eng. 81, 46–56. doi: 10.1016/j.aquaeng.2018.02.001
Gold Standard (2017). Gold standard Afforestation/Reforestation (A/R) GHG emissions reduction & sequestration methodology (The Gold Standard for the Global Goals), 15. Available at: https://www.goldstandard.org/project-developers/standard-documents.
Gold Standard (2021). Carbon offsetting: What you need to know to take action against climate change (Gold Stnadard), 27. Available at: https://www.goldstandard.org/sites/default/files/documents/gold_standard_offsetting_guide.pdf.
Grebe G. S., Byron C. J., Gelais A., Kotowicz D. M., Olson T. K. (2019). An ecosystem approach to kelp aquaculture in the americas and Europe. Aquaculture Rep. 15, 100215. doi: 10.1016/j.aqrep.2019.100215
Greene J. M., Gulden J., Wood G., Huesemann M., Quinn J. C. (2020). Techno-economic analysis and global warming potential of a novel offshore macroalgae biorefinery. Algal Res. 51, 102032. doi: 10.1016/j.algal.2020.102032
Guinee J. B. (2002). Handbook on life cycle assessment operational guide to the ISO standards, Vol. 7. BF02978897, The International Journal of Life Cycle Assessment. doi: 10.1007/BF02978897
Harrold C., Light K., Lisin S. (1998). Organic enrichment of submarine-canyon and continental-shelf benthic communities bymacroalgal drift imported from nearshore kelp forests. Limnology Oceanography 43 (4), 669–678. doi: 10.4319/lo.1998.43.4.0669
Hasselström L., Thomas J.-B., Nordström J., Cervin G., Nylund G. M., Pavia H., et al. (2020). Socioeconomic prospects of a seaweed bioeconomy in Sweden. Sci. Rep. 10 (1), 1610. doi: 10.1038/s41598-020-58389-6
Héder M. (2017). From NASA to EU: The evolution of the TRL scale in public sector innovation. Innovation J. 22 (2), 1–23.
Hoagland P., Kite-Powell H. L., Jin D. (2003). Business planning handbook for the ocean aquaculture of blue mussels (Woods Hole Oceanographic Institution), 31. Available at: https://www.researchgate.net/publication/253951313_Business_planning_handbook_for_the_ocean_aquaculture_of_blue_mussels.
Hurd C. L., Law C. S., Bach L. T., Britton D., Hovenden M., Paine E., et al. (2022). Forensic carbon accounting: Assessing the role of seaweeds for carbon sequestration. J. Phycology. 58, 347–363. doi: 10.1111/jpy.13249
Hu Z., Shan T., Zhang J., Zhang Q., Critchley A. T., Choi H., et al. (2021). Kelp aquaculture in China: A retrospective and future prospects. Rev. Aquaculture 13 (3), 1324–1351. doi: 10.1111/raq.12524
IMAS (2019) Assessing the potential for restoration and permaculture of tasmania’s giant kelp forests. Available at: http://imas.utas.edu.au/kelprestoration (Accessed November 2021).
IPCC (2021) Summary for policy makers (Climate change 2021: The physical science basis. contribution of working group I to the sixth assessment report of the intergovernmental panel on climate change). Available at:https://www.ipcc.ch/report/ar6/wg1/#SPM.
Jenne D. S., Yu Y.-H., Neary V. (2015) Numerical Modeling of Flexible Structures in Offshore Environment in Levelized Cost of Energy Analysis of Marine and Hydrokinetic Reference Models. 9.
Joppa L., Luers A., Willmott E., Friedmann S. J., Hamburg S. P., Broze R. (2021). Microsoft’s million-tonne CO2-removal purchase–lessons for net zero. Nature 597 (7878), 629–632. doi: 10.1038/d41586-021-02606-3
Kavlak G., McNerney J., Trancik J. E. (2018). Evaluating the causes of cost reduction in photovoltaic modules. Energy Policy 123, 700–710. doi: 10.1016/j.enpol.2018.08.015
Kerrison P. D., Stanley M. S., Hughes A. D. (2018). Textile substrate seeding of saccharina latissima sporophytes using a binder: An effective method for the aquaculture of kelp. Algal Res. 33, 352–357. doi: 10.1016/j.algal.2018.06.005
Kim J., Stekoll M., Yarish C. (2019). Opportunities, challenges and future directions of open-water seaweed aquaculture in the united states. Phycologia 58 (5), 446–461. doi: 10.1080/00318884.2019.1625611
Klebert P., Lader P., Gansel L., Oppedal F. (2013). Hydrodynamic interactions on net panel and aquaculture fish cages: A review. Ocean Eng. 58, 260–274. doi: 10.1016/j.oceaneng.2012.11.006
Knysh A., Tsukrov I., Chambers M., Swift M. R., Sullivan C., Drach A. (2020). Numerical modeling of submerged mussel longlines with protective sleeves. Aquacultural Eng. 88, 102027. doi: 10.1016/j.aquaeng.2019.102027
Krause-Jensen D., Duarte C. M. (2016). Substantial role of macroalgae in marine carbon sequestration. Nat. Geosci. 9 (10), 737–742. doi: 10.1038/ngeo2790
Kreidenweis U., Humpenöder F., Stevanović M., Bodirsky B. L., Kriegler E., Lotze-Campen H., et al. (2016). Afforestation to mitigate climate change: Impacts on food prices under consideration of albedo effects. Environ. Res. Lett. 11 (8), 85001. doi: 10.1088/1748-9326/11/8/085001
Krumhansl K., Scheibling R. (2012). Production and fate of kelp detritus. Mar. Ecol. Prog. Ser. 467, 281–302. doi: 10.3354/meps09940
Kwiatkowski L., Torres O., Bopp L., Aumont O., Chamberlain M., Christian J. R., et al. (2020). Twenty-first century ocean warming, acidification, deoxygenation, and upper-ocean nutrient and primary production decline from CMIP6 model projections. Biogeosciences 17 (13), 3439–3470. doi: 10.5194/bg-17-3439-2020
Littler M. M., Littler D. S. (1980). The evolution of thallus form and survival strategies in benthic marine macroalgae: Field and laboratory tests of a functional form model. Am. Nat. 116 (1), 25–44. doi: 10.1086/283610
Manns D., Nielsen M. M., Bruhn A., Saake B., Meyer A. S. (2017). Compositional variations of brown seaweeds laminaria digitata and saccharina latissima in Danish waters. J. Appl. Phycology 29 (3), 1493–1506. doi: 10.1007/s10811-017-1056-z
Marcucci A., Kypreos S., Panos E. (2017). The road to achieving the long-term Paris targets: Energy transition and the role of direct air capture. Climatic Change 144 (2), 181–193. doi: 10.1007/s10584-017-2051-8
Marland E., Bates L., Domke G., Helms A., Hoyle J., Jones B., et al. (2017). Understanding and analysis: The California air resources board forest offset protocol (1st ed. 2017) (Springer International Publishing : Imprint: Springer). doi: 10.1007/978-3-319-52434-4
Masson D. G., Huvenne V. A. I., de Stigter H. C., Wolff G. A., Kiriakoulakis K., Arzola R. G., et al. (2010). Efficient burial of carbon in a submarine canyon. Geology 38 (9), 831–834. doi: 10.1130/G30895.1
Matzek V., Puleston C., Gunn J. (2015). Can carbon credits fund riparian forest restoration? Restor. Ecol. 23 (1), 7–14. doi: 10.1111/rec.12153
McDonald A., Schrattenholzer L. (2001). Learning rates for energy technologies. Energy Policy 29 (4), 255–261. doi: 10.1016/S0301-4215(00)00122-1
Michalak I. (2018). Experimental processing of seaweeds for biofuels. WIREs Energy Environ. 7 (3), 1–25. doi: 10.1002/wene.288
Minx J. C., Lamb W. F., Callaghan M. W., Fuss S., Hilaire J., Creutzig F., et al. (2018). Negative emissions–part 1: Research landscape and synthesis. Environ. Res. Lett. 13 (6), 063001. doi: 10.1088/1748-9326/aabf9b
Mora C., Spirandelli D., Franklin E. C., Lynham J., Kantar M. B., Miles W., et al. (2018). Broad threat to humanity from cumulative climate hazards intensified by greenhouse gas emissions. Nat. Climate Change 8 (12), 1062–1071. doi: 10.1038/s41558-018-0315-6
Morison J. R., Johnson J. W., Schaaf S. A. (1950). The force exerted by surface waves on piles. J. Petroleum Technol. 2 (05), 149–154. doi: 10.2118/950149-G
Morris Jr J.A. (2021). An aquaculture opportunity area atlas for the southern California bight. doi: 10.25923/TMX9-EX26
Moscicki Z., Dewhurst T., MacNicoll M., Lynn P., Sullivan C., Chambers M., et al. (2022). “Using finite element analysis for the design of a modular offshore macroalgae farm,” in The 9th Conference on Computational Methods in Marine Engineering (Marine 2021), Vol. 1. doi: 10.2218/marine2021.6855
Myers S. S., Smith M. R., Guth S., Golden C. D., Vaitla B., Mueller N. D., et al. (2017). Climate change and global food systems: Potential impacts on food security and undernutrition. Annu. Rev. Public Health 38 (1), 259–277. doi: 10.1146/annurev-publhealth-031816-044356
NASEM (2019). Negative emissions technologies and reliable sequestration: A research agenda (National Academies Press), 25259. doi: 10.17226/25259
NASEM (2021). A research strategy for ocean-based carbon dioxide removal and sequestration (National Academies Press), 26278. doi: 10.17226/26278
NAVFAC (2012). SP-2209-OCN handbook for marine geotechnical engineering (Naval Facilities Engineering Command), 457. Available at: https://apps.dtic.mil/sti/pdfs/ADA556807.pdf.
Nellemann C., Corcoran E., Duarte C., Valdés M., De Young C., Fonseca L., Grimsditch G. (Eds.) (2009). Blue carbon: The role of healthy oceans in binding carbon: a rapid response assessment (GRID-Arendal).
NERACOOS (2022). Mooring E0141: Central Maine shelf (The University of Maine Physcial Oceanography Group). Available at: http://gyre.umeoce.maine.edu/data/gomoos/buoy/html/E01.html.
Ng W. Y., Low C. X., Putra Z. A., Aviso K. B., Promentilla M. A. B., Tan R. R. (2020). Ranking negative emissions technologies under uncertainty. Heliyon 6 (12), e05730. doi: 10.1016/j.heliyon.2020.e05730
Ometto F., Steinhovden K. B., Kuci H., Lunnbäck J., Berg A., Karlsson A., et al. (2018). Seasonal variation of elements composition and biomethane in brown macroalgae. Biomass Bioenergy 109, 31–38. doi: 10.1016/j.biombioe.2017.11.006
Ortega A., Geraldi N. R., Alam I., Kamau A. A., Acinas S. G., Logares R., et al. (2019). Important contribution of macroalgae to oceanic carbon sequestration. Nat. Geosci. 12 (9), 748–754. doi: 10.1038/s41561-019-0421-8
Osman M. E. H., Abo-Shady A. M., Elshobary M. E., Abd El-Ghafar M. O., Abomohra A. E.-F. (2020). Screening of seaweeds for sustainable biofuel recovery through sequential biodiesel and bioethanol production. Environ. Sci. pollut. Res. 27 (26), 32481–32493. doi: 10.1007/s11356-020-09534-1
Otts S. (2021). Exploring options to authorize offshore aquaculture: Facilitating discussions among regulators and industry members to find common ground. Sea Grant Law Policy J. 11 (1), 1–14.
Parsons S., Allen M. J., Abeln F., McManus M., Chuck C. J. (2019). Sustainability and life cycle assessment (LCA) of macroalgae-derived single cell oils. J. Cleaner Production 232, 1272–1281. doi: 10.1016/j.jclepro.2019.05.315
Patursson Ø., Swift M. R., Tsukrov I., Simonsen K., Baldwin K., Fredriksson D. W., et al. (2010). Development of a porous media model with application to flow through and around a net panel. Ocean Eng. 37 (2–3), 314–324. doi: 10.1016/j.oceaneng.2009.10.001
Piconi P., Veidenheimer R., Chase B. (2020). Edible Seaweed Market Analysis. Available online at: https://www.islandinstitute.org/edible-seaweed-marketanalysis/
Pei Q., Zhang D. D., Fei J., Hui P. Y. (2020). Demographic crises of different climate phases in preindustrial northern hemisphere. Hum. Ecol. 48 (5), 519–527. doi: 10.1007/s10745-020-00182-0
Pendleton L., Donato D. C., Murray B. C., Crooks S., Jenkins W. A., Sifleet S., et al. (2012). Estimating global “Blue carbon” emissions from conversion and degradation of vegetated coastal ecosystems. PloS One 7 (9), e43542. doi: 10.1371/journal.pone.0043542
Peteiro C., Freire Ó. (2013). Biomass yield and morphological features of the seaweed saccharina latissima cultivated at two different sites in a coastal bay in the Atlantic coast of Spain. J. Appl. Phycology 25 (1), 205–213. doi: 10.1007/s10811-012-9854-9
Peters A. (2020). Forget planting trees: This company is making carbon offsets by putting seaweed on the ocean floor (Fast Company). Available at: https://www.fastcompany.com/90548820/forget-planting-trees-this-company-is-making-carbon-offsets-by-putting-seaweed-on-the-ocean-floor.
Racine P., Marley A., Froehlich H. E., Gaines S. D., Ladner I., MacAdam-Somer I., et al. (2021). A case for seaweed aquaculture inclusion in U.S. nutrient pollution management. Mar. Policy 129, 104506. doi: 10.1016/j.marpol.2021.104506
Rebuck N. D., Townsend D. W. (2014). A climatology and time series for dissolved nitrate in the gulf of Maine region. Deep Sea Res. Part II: Topical Stud. Oceanography 103, 223–237. doi: 10.1016/j.dsr2.2013.09.006
Redmond S., Green L., Yarish C., Kim J., Neefus C. (2014). New England seaweed culture handbook (University of Connecticut Sea Grant). Available at: http://digitalcommons.uconn.edu/seagrant_weedcult/1?utm_source=digitalcommons.uconn.edu%2Fseagrant_weedcult%2F1&utm_medium=PDF&utm_campaign=PDFCoverPages.
REFINITIV (2022). Carbon market year in revoew (REFINITIV). Available at: https://www.refinitiv.com/content/dam/marketing/en_us/documents/reports/global-carbon-market-emission-trading-system-review-2019.pdf.
Riley K. L. (2021). An aquaculture opportunity area atlas for the U.S. gulf of Mexico. doi: 10.25923/8CB3-3R66
Roque B. M., Venegas M., Kinley R. D., de Nys R., Duarte T. L., Yang X., et al. (2021). Red seaweed (Asparagopsis taxiformis) supplementation reduces enteric methane by over 80 percent in beef steers. PloS One 16 (3), e0247820. doi: 10.1371/journal.pone.0247820
Rosman J. H., Monismith S. G., Denny M. W., Koseff J. R. (2010). Currents and turbulence within a kelp forest ( macrocystis pyrifera): Insights from a dynamically scaled laboratory model. Limnology Oceanography 55 (3), 1145–1158. doi: 10.4319/lo.2010.55.3.1145
Rothäusler E., Gutow L., Thiel M. (2012). “Floating seaweeds and their communities,” in Seaweed biology (Berlin, Heidelberg: Springer), 359–380.
Rubin E. S., Azevedo I. M. L., Jaramillo P., Yeh S. (2015). A review of learning rates for electricity supply technologies. Energy Policy 86, 198–218. doi: 10.1016/j.enpol.2015.06.011
Rubino M. (2008). Offshore aquaculture in the united states: Economic considerations, implications & opportunities (U.S. Department of Commerce), 263. Available at: http://aquaculture.noaa.gov.
Sanz-Pérez E. S., Murdock C. R., Didas S. A., Jones C. W. (2016). Direct capture of CO 2 from ambient air. Chem. Rev. 116 (19), 11840–11876. doi: 10.1021/acs.chemrev.6b00173
Schupp M. F., Krause G., Onyango V., Buck B. H. (2021). Dissecting the offshore wind and mariculture multi-use discourse: A new approach using targeted SWOT analysis. Maritime Stud. 20 (2), 127–140. doi: 10.1007/s40152-021-00218-1
Seghetta M., Hou X., Bastianoni S., Bjerre A.-B., Thomsen M. (2016). Life cycle assessment of macroalgal biorefinery for the production of ethanol, proteins and fertilizers – a step towards a regenerative bioeconomy. J. Cleaner Production 137, 1158–1169. doi: 10.1016/j.jclepro.2016.07.195
Siegel D. A., DeVries T., Doney S. C., Bell T. (2021). Assessing the sequestration time scales of some ocean-based carbon dioxide reduction strategies. Environ. Res. Lett. 16 (10), 104003. doi: 10.1088/1748-9326/ac0be0
Smale D. A., Pessarrodona A., King N., Moore P. J. (2021). Examining the production, export, and immediate fate of kelp detritus on open-coast subtidal reefs in the northeast Atlantic. Limnology Oceanography. 9999, 1–14. doi: 10.1002/lno.11970
Smith P. (2012). Agricultural greenhouse gas mitigation potential globally, in Europe and in the UK: What have we learnt in the last 20 years? Global Change Biol. 18 (1), 35–43. doi: 10.1111/j.1365-2486.2011.02517.x
Smith K. E., Burrows M. T., Hobday A. J., Sen Gupta A., Moore P. J., Thomsen M., et al. (2021). Socioeconomic impacts of marine heatwaves: Global issues and opportunities. Science 374 (6566), eabj3593. doi: 10.1126/science.abj3593
Smith L. J., Torn M. S. (2013). Ecological limits to terrestrial biological carbon dioxide removal. Climatic Change 118 (1), 89–103. doi: 10.1007/s10584-012-0682-3
Standards Norway (2009) Marine fish farms requirements for site survey, risk analyses, design, dimensioning, production, installation and operation. Available at: https://www.standard.no/en/PDF/FileDownload/?redir=true&filetype=Pdf&preview=true&item=426625&category=5.
Stekoll M. S., Peeples T. N., Raymond A. E. T. (2021). Mariculture research of macrocystis pyrifera and saccharina latissima in southeast Alaska. J. World Aquaculture Soc. 52 (5), 1031–1046. doi: 10.1111/jwas.12765
Steneck R. S., Dethier M. N. (1994). A functional group approach to the structure of algal-dominated communities. Oikos 69 (3), 476. doi: 10.2307/3545860
St-Gelais A. T., Fredriksson D. W., Dewhurst T., Miller-Hope Z. S., Costa-Pierce B. A., Johndrow K. (2022). Engineering a low-cost kelp aquaculture system for community-scale seaweed farming at nearshore exposed sites via user-focused design process. Front. Sustain. Food Syst. 6. doi: 10.3389/fsufs.2022.848035
Su L., Pang S. J., Shan T. F., Li X. (2017). Large-Scale hatchery of the kelp saccharina japonica: A case study experience at lvshun in northern China. J. Appl. Phycology 29 (6), 3003–3013. doi: 10.1007/s10811-017-1154-y
Teodorović D., Janić M. (2017). “Transportation, environment, and society,” in Transportation engineering (Elsevier), 719–858. doi: 10.1016/B978-0-12-803818-5.00011-1
Theuerkauf S. J., Barrett L. T., Alleway H. K., Costa-Pierce B. A., St. Gelais A., Jones R. C. (2022). Habitat value of bivalve shellfish and seaweed aquaculture for fish and invertebrates: Pathways, synthesis and next steps. Rev. Aquaculture 14 (1), 54–72. doi: 10.1111/raq.12584
Thomassen G., Van Dael M., Van Passel S., You F. (2019). How to assess the potential of emerging green technologies? towards a prospective environmental and techno-economic assessment framework. Green Chem. 21 (18), 4868–4886. doi: 10.1039/C9GC02223F
Thomassen G., Van Passel S., Dewulf J. (2020). A review on learning effects in prospective technology assessment. Renewable Sustain. Energy Rev. 130, 109937. doi: 10.1016/j.rser.2020.109937
Thomas J.-B. E., Sodré Ribeiro M., Potting J., Cervin G., Nylund G. M., Olsson J., et al. (2021). A comparative environmental life cycle assessment of hatchery, cultivation, and preservation of the kelp saccharina latissima. ICES J. Mar. Sci. 78 (1), 451–467. doi: 10.1093/icesjms/fsaa112
Troell M., Henriksson P. J. G., Buschmann A. H., Chopin T., Quahe S. (2022). Farming the ocean – seaweeds as a quick fix for the climate? Rev. Fisheries Sci. Aquaculture, 1–11. doi: 10.1080/23308249.2022.2048792
Tsukrov I., Eroshkin O., Fredriksson D., Swift M. R., Celikkol B. (2003). Finite element modeling of net panels using a consistent net element. Ocean Eng. 30 (2), 251–270. doi: 10.1016/S0029-8018(02)00021-5
Umanzor S., Li Y., Bailey D., Augyte S., Huang M., Marty-Rivera M., et al. (2021). Comparative analysis of morphometric traits of farmed sugar kelp and skinny kelp, saccharina spp., strains from the Northwest Atlantic. J. World Aquaculture Soc. 52 (5), 1059–1068. doi: 10.1111/jwas.12783
van den Burg S., Röckmann C., Banach J. L., van Hoof L. (2020). Governing risks of multi-use: Seaweed aquaculture at offshore wind farms. Front. Mar. Sci. 7. doi: 10.3389/fmars.2020.00060
van den Burg S., van Duijn A. P., Bartelings H., van Krimpen M. M., Poelman M. (2016). The economic feasibility of seaweed production in the north Sea. Aquaculture Economics Manage. 20 (3), 235–252. doi: 10.1080/13657305.2016.1177859
van Minnen J. G., Strengers B. J., Eickhout B., Swart R. J., Leemans R. (2008). Quantifying the effectiveness of climate change mitigation through forest plantations and carbon sequestration with an integrated land-use model. Carbon Balance Manage. 3 (1), 3. doi: 10.1186/1750-0680-3-3
van Oirschot R., Thomas J.-B. E., Gröndahl F., Fortuin K. P. J., Brandenburg W., Potting J. (2017). Explorative environmental life cycle assessment for system design of seaweed cultivation and drying. Algal Res. 27, 43–54. doi: 10.1016/j.algal.2017.07.025
VCS (2021). Methodology for tidal wetland and seagrass restoration (Verra), 135. Available at: https://verra.org/wp-content/uploads/2018/03/VM0033-Methodology-for-Tidal-Wetland-and-Seagrass-Restoration-v2.0-30Sep21-1.pdf.
Wender B. A., Foley R. W., Prado-Lopez V., Ravikumar D., Eisenberg D. A., Hottle T. A., et al. (2014). Illustrating anticipatory life cycle assessment for emerging photovoltaic technologies. Environ. Sci. Technol. 48 (18), 10531–10538. doi: 10.1021/es5016923
Wu J., Keller D. P., Oschlies A.(2022). Carbon dioxide removal via macroalgae open-ocean mariculture and sinking: An earth system modeling study, Earth Syst. Dynam. doi: 10.5194/esd-2021-104
Zhang Y., Chang Z., Zheng Z., Yang J. (2017). Harvesting machine for kelp culture in floating raft. Aquacultural Eng. 78, 173–179. doi: 10.1016/j.aquaeng.2017.07.005
Zhao X. B., Pang S. J., Liu F., Shan T. F., Li J., Gao S. Q., et al. (2016). Intraspecific crossing of saccharina japonica using distantly related unialgal gametophytes benefits kelp farming by improving blade quality and productivity at sanggou bay, China. J. Appl. Phycology 28 (1), 449–455. doi: 10.1007/s10811-015-0597-2
Keywords: kelp aquaculture, levelized cost analysis, Carbon Dioxide Removal (CDR), CDR Monitoring, Reporting, and Verification (MRV), Saccharina latissima
Citation: Coleman S, Dewhurst T, Fredriksson DW, St. Gelais AT, Cole KL, MacNicoll M, Laufer E and Brady DC (2022) Quantifying baseline costs and cataloging potential optimization strategies for kelp aquaculture carbon dioxide removal. Front. Mar. Sci. 9:966304. doi: 10.3389/fmars.2022.966304
Received: 10 June 2022; Accepted: 18 July 2022;
Published: 11 August 2022.
Edited by:
Michael Phillips, WorldFish, MalaysiaReviewed by:
Leonel Pereira, University of Coimbra, PortugalPablo P. Leal, Instituto de Fomento Pesquero (IFOP), Chile
Copyright © 2022 Coleman, Dewhurst, Fredriksson, St. Gelais, Cole, MacNicoll, Laufer and Brady. This is an open-access article distributed under the terms of the Creative Commons Attribution License (CC BY). The use, distribution or reproduction in other forums is permitted, provided the original author(s) and the copyright owner(s) are credited and that the original publication in this journal is cited, in accordance with accepted academic practice. No use, distribution or reproduction is permitted which does not comply with these terms.
*Correspondence: Struan Coleman, c3RydWFuLmNvbGVtYW5AbWFpbmUuZWR1