- 1Department of Informatics, The University of Electro-Communications, Chofu, Japan
- 2Research Fellow of Japan Society for the Promotion of Science, Chiyoda, Japan
To enrich the virtual reality experience and improve realism, many studies have proposed embedding tactile devices into head-mounted displays (HMDs). However, although thermal and vibrotactile cues have become commonplace, presentation of the constant pressure necessary for softness expression remains relatively rare. In this study, we propose a suction-type tactile presentation method that addresses this issue. Through subjective evaluation and simulation using the finite element method, we verified that the proposed suction-type tactile presentation method is suitable for use with HMDs and that by increasing the number and density of the suction holes, a stronger tactile sensation can be created.
1 Introduction
In recent years, the demand for high-quality virtual reality (VR) experiences has increased concomitant with the decreasing cost of head-mounted displays (HMDs). In addition to the visual and auditory information provided by HMDs, VR can be enriched by presenting tactile information, and the presentation of such tactile information to the palm is particularly popular (Maisto et al., 2017). The palm is the most commonly used part of the human body for basic exploratory movements, and it is an effective site for presenting tactile sensations to improve the realism of VR environments. However, to physically present haptic information, the hand must touch a mechanical haptic device, which hinders the free movement of the hand and arm. As a solution to this problem, non-contact tactile presentation techniques using ultrasonic waves and lasers have been proposed (Hwang et al., 2017; Jun et al., 2015). However, these techniques provide only a limited range of motion and require high-precision hand shape recognition to accurately irradiate ultrasonic waves or lasers to the hand.
We previously proposed Haptopus, which enables a hands-free tactile VR experience by presenting virtual fingertip tactile information to the face in a VR environment (Kameoka et al., 2018; Kameoka and Kajimoto, 2021). Haptopus has a built-in suction-type tactile presentation device, which enables users to experience VR with tactile information by only wearing the HMD.
Previous suction-type tactile devices have predominantly been for the palm or forearm, rather than the face. However, because the face comes into contact with the HMD, it provides a convenient area for tactile presentation. In addition, the establishment of a stable tactile presentation method for the face can be applied to the other areas.
In this study, we investigated the suction-type tactile presentation method on the face necessary for the design of Haptopus. Specifically, we evaluated the performance and sensitivity of the suction tactile system and utilized the finite element method (FEM) to optimize the sensory presentation method for skin suction tactile sensation. Subsequently, we compared the subjective evaluation and FEM analysis.
2 Related Work
2.1 Hand-Tactile Information Presented to Other Parts of the Body
Numerous tactile devices have been developed with a focus on the hands or fingers and several studies have also been conducted on tactile presentation to other parts of the body. Here, we focus on studies that present hand-tactile information (i.e., tactile information related to hand–object interaction) to the other parts of the body.
The presentation of hand-tactile information to different parts of the body has predominantly been used in the development of artificial limbs (prosthetic arms) to stimulate the cut surface of the limb or its surroundings using pressure sensation (Shi et al., 2020), electrical stimulation (Schoepp et al., 2018), and skin shear (Antfolk et al., 2012). There have also been some attempts to present hand-tactile information to the other parts of the body in the VR environment. It has been presented to the sole of the feet (Okano et al., 2018), forearm (Moriyama et al., 2018), and back (Moriyama et al., 2019) to assist in handling objects in VR environments. Our approach of presenting hand-tactile information to the face via an HMD-embedded tactile device is another example.
Referred Sensation is a phenomenon in which a person who has lost a limb feels a tactile sensation of the lost limb in a different part of the body. This hand-tactile sensation is sometimes even felt on the cheeks, and it can also occur in healthy people (Ramachandran 1998). It is theorized that the phenomenon may be due to the functional localization of the brain and the proximity of the face and hand regions in the primary motor cortex (Penfield and Rasmussen, 1950). Ichinose et al. confirmed that tactile transference technology can be used as a treatment for patients suffering from phantom limb pain due to the loss of an arm (or of arm sensation), and reported that presenting vibration to the cheek was effective in their case (Ichinose et al., 2017). These facts imply that presenting hand-tactile information to the face might provide neurophysiological benefits.
2.2 Tactile Presentation Devices Embedded in HMD
Various tactile presentation methods involving the embedding of a device into HMDs have been proposed. Examples include applying heat (Peiris et al., 2017), compression by belt winding (Chang et al., 2018), skin shearing (Wang et al., 2019), vibration (Wolf et al., 2019), balloon compression (Kon et al., 2017), and ultrasonics (Shen et al., 2022). However, the primary purpose of such devices was to reproduce the sensations felt by the head in a VR environment and not tactile sensations felt by the hand. To present sensations in the hand area, especially in sensitive areas such as fingertips, it is necessary to use a method that can present tactile sensations to multiple locations, corresponding to each finger. From this viewpoint, heat is not suitable for presenting individual fingertip sensations because the spatial resolution is low. Vibration is another solution, but bone conduction might lower the spatial resolution, and long-term continuous use of vibration is not desired by users. Ultrasonic stimulation is also possible, but currently its output power is limited and success has only been had in presenting to sensation to the lips, which is a highly sensitive tactile area. Thus, we consider it is still challenging to present distributed tactile sensation by ultrasound. Air compression by balloon can present pressure, but it has the disadvantage that the HMD is pushed out and the display moves, which interferes with the experience. Other small pin-matrix type tactile presentation methods might be integrated into HMDs (Kyung et al., 2005; Kim etal., 2019), but we did not adopt them because the forehead has lower spatial resolution than fingertips. Electromagnetic devices such as solenoids can also be considered, but they have a similar issue to that of air compression.
Considering the above drawbacks of current methods, we surmised that a skin suction-type tactile presentation method may be a good solution because it can be designed as small and lightweight, and embedding it into the HMD is possible. It can also present a relatively soft tactile sensation compared with vibrotactile actuators, which would enable long-term use.
2.3 Suction-Type Tactile Devices
In air suction-type tactile devices, the tactile presentation area can be separated from the air pressure control area and connected with a thin tube, allowing the device to be made smaller. The suction type is also superior to the air-balloon type in terms of durability. The air-balloon type requires a flexible membrane that is vulnerable. By contrast, the suction type does not require any membrane because it acts directly on the skin.
In addition, a sense of pressure, not suction, is presented when it is designed with the appropriate size (Makino et al., 2004). Thus, this technique can present a continuous sense of pressure, which is important for the perception of contact while grasping a virtual object.
Two types of skin suction-type tactile devices have been proposed: devices that are affixed to the finger by suction and present a sense of friction and devices that present the suction itself as a tactile stimulus. Arai et al. achieved omnidirectional skin shear stimulus by attaching an air suction device to the surface of a hydraulic slide shaft that can move with two degrees of freedom (Arai et al., 2001). Similarly, Yamaoka et al. reproduced the sensation of touching an adhesive surface by using the adhesive force of air suction (Yamaoka et al., 2008). In addition, Hachisu et al. developed a table-top suction tactile presentation device and demonstrated that it is possible to modulate the sense of friction (Hachisu and Fukumoto, 2014).
In terms of using the skin suction itself as a tactile stimulus, Makino et al. investigated the characteristics of skin suction tactile presentation on the palm and reported that tactile sensation associated with suction is perceived as a pressure sensation (Makino et al., 2004; Makino et al., 2003). Other researchers have also presented pressure sensation by suction stimuli and created the cue for force (Ben Porquis et al., 2011), the direction of force (Porquis et al., 2012; Maemori et al., 2014), and modulated the hardness perception of objects (Ben Porquis et al., 2014; Nagano et al., 2019). Overall, suction tactile presentation is often performed on the fingertips and has not yet been applied to the face. In this study, we focused on a design for presenting tactile sensation to the face via suction.
2.4 FEM Applied to Skin
The FEM is frequently used to investigate the mechanical changes that occur in the skin and how various mechanoreceptors respond during tactile perception (Maeno et al., 1998). In particular, the activity of Merkel cells, which mainly respond to small skin deformations (Saal et al., 2017), and subjective tactile intensity correlated with the strain energy applied to tactile receptors have been investigated. The strain energy distribution has also been used to analyze suction tactile sensation (Makino et al., 2004; Ben Porquis et al., 2013). In this study, we examined the relationship between tactile intensity and tactile quality using the distribution and strength of strain energy applied to the region where Merkel cells exist by skin structure simulation.
3 Suction Stimulate System Design
3.1 Suction System
To use suction tactile sensation, we designed a suction air pressure control system comprising an air suction pump (SC3701PML, Shenzhen Skoocom Electronic Co., Ltd.), solenoid valves (SC415GF, SC0526GF, Shenzhen Skoocom Electronic Co., Ltd.), and an air pressure sensor (MIS-2503-015V) (Figure 1). The air pressure sensor and solenoid valve are controlled by a microcontroller (ESP-WROOM-32), and the air pressure value is controlled by switching the solenoid valve according to the value of the air pressure sensor. The air pressure is adjusted by switching between suction, exhaust, and stop states by switching the two solenoid valves on and off (Figure 2). Although it is possible to adjust the air pressure by changing the power output of the pump, we did not adopt this method because it requires controlling the rotation speed of the motor, which would greatly increase the response time. The air pressure was monitored constantly: if it was higher than the target pressure, it was sucked in, whereas if it was lower than the target pressure, it was exhausted. The target pressure had a buffer pressure, and when it was within the range of the target pressure ± buffer pressure, the pressure was maintained by closing the valve and sealing it. The buffer pressure was set to one hPa and the control cycle to 1 kHz (cycle time: 1 ms).
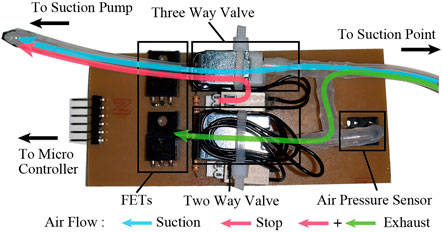
FIGURE 1. Photo of the suction control module. The air pressure sensor measures the suction air pressure and the microcontroller switches the three-way solenoid valve and two-way solenoid valve with FETs. These are controlled by a microcontroller on the motherboard.
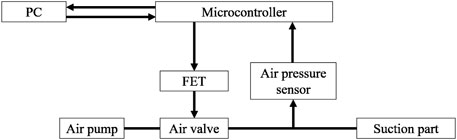
FIGURE 2. Block diagram of the suction system. The PC sends the target air pressure value to the microcontroller. The microcontroller continuously compares the air pressure sensor value with the target air pressure value and controls suction by opening and closing valves using FETs.
The maximum suction pressure used in this device was in the range of −500 to −600 hPa. Negative pressure to the skin is used in a medical treatment called cupping, in which a pressure of approximately −800 hPa is applied for 10 min or more. This leaves scars that disappear after a few weeks (Kim and Lee, 2014). However, in this study, we used minimal negative pressure and prolonged suction was not required to produce such an effect.
3.2 Evaluation of the Suction System
The solenoid valve controlling the suction pressure can switch the flow path within 10 ms after receiving a signal. Figure 3 shows the change in suction pressure and the signal input to the solenoid valve. Although it took approximately 100 ms to reach the target pressure in this system, the pressure began to change almost simultaneously with the signal input. The tip of the tube was sealed during the measurement. The results of several user evaluations conducted using different participants revealed that the wearer could perceive the suction sensation at the same time as the contact in the VR environment. Thus, we theorized that the delay would not affect our future experiments. Considering this result, we hypothesized that the amount of skin deformation (i.e., differential value of deformation) was mainly perceived in the suction tactile sensation. Saito et al. also studied the perception of suction tactile sensation (Saito et al., 2019) and demonstrated that the subjective suction tactile intensity in the upper arm is correlated with the amount of skin deformation. Therefore, we concluded that the suction pressure control by our system does not cause a significant delay in the subjective perception during the tactile presentation time.
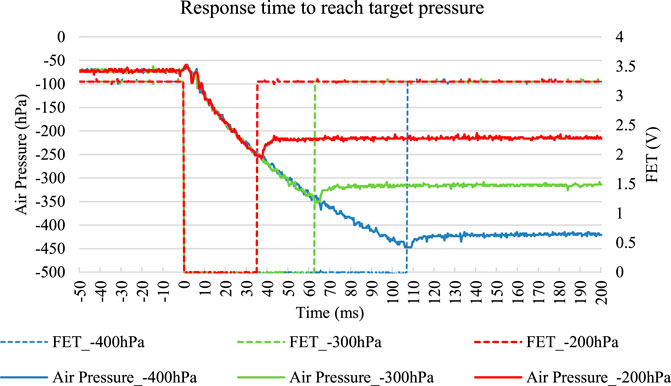
FIGURE 3. Response time to reach target pressure (−200, −300, and −400 hPa) and FET gate voltage. The suction start time was set to 0 ms.
4 Subjective Evaluation Experiment
To evaluate the proposed system, we conducted subjective evaluations to assess whether the system could provide sufficient tactile intensity to present tactile information and ascertain the kind of sensation it could provide.
4.1 Design of Suction Parts
We designed the shape of the suction part by fixing its area and varying its diameter, taking into consideration that it would be built into the HMD in the future. The suction part had a regular hexagonal contact surface circumscribed to a circle with a diameter of 25 mm, height of 7 mm, thickness of 1 mm, and a hollow interior. Makino and Shinoda (2005) and Ben Porquis et al. (2011) investigated the shape of suction holes in suction tactile sensation and empirically placed many 2 mm-diameter suction holes for tactile presentation to the fingertips. In this study, we created a new model with 2 mm (91 points), 3 mm (37 points), 4 mm (17 points), 7 mm (7 points), 10 mm (3 points), and 12 mm (1 point) suction holes in a hexagonal close-packed structure for presenting stimuli to the face, and investigated the optimal suction diameter (Figure 4). We made the suction part using an optical 3D printer (Form3, FormLabs) and used Elastic Resin (FormLabs) as the material. This material has the flexibility of silicon and adheres to the skin, preventing air leaks during skin suction.

FIGURE 4. Comparison of suction holes (from left to right): 12 mm single-point suction part, 10 mm 3-point suction part, 7 mm 7-point suction part, 4 mm 19-point suction part, 3 mm 37-point suction part, and 2 mm 91-point suction part.
4.2 Procedure
To establish a suitable sucker shape for the haptic experience, for each sucker diameter, we first investigated the minimum suction pressure at which suction could be perceived and the maximum pressure at which experientially inappropriate discomfort occurred. First, the participant placed the suction part on their cheek with their hand (Figure 5). Then, the experimenter adjusted the suction pressure, and the subject responded instantly when they began feeling the touch or any discomfort. The pressures at these times were set as the minimum and maximum. Each sucker diameter was experimented with once. The maximum suction pressure was set to −500 hPa owing to system limitations. The air pressure in the obtained suction range was divided into six equal parts for suction stimulus presentation. For example, if the maximum and minimum suction pressures were −400 hPa and −50 hPa, respectively, the system was divided into six conditions: −50, −120, −190, −260, −330, and −400 hPa. The participants were asked to rate the type of tactile sensation (perceived as suction or pressure) and suction intensity at each pressure value based on the Likert scale, with the integer values based on the following parameter values: suction or pressure (−3: suction, +3: pressure perception) and intensity of sensation (1: very weak, 7: very strong). As mentioned in Section 2.3, the suction-type tactile device was known to be perceived as pressure, not suction. The questionnaire on tactile sensation was meant to verify this effect. This study was approved by the Ethics Committee of the University of Electro-Communications.
4.3 Results
We evaluated the system in our laboratory using 10 male participants, aged 22–26 years. The experimental results are presented in Figure 6, Figure 7, and Figure 8. The data presented are the averages for all participants. Figure 6 shows that the minimum suction pressure remained almost constant irrespective of the suction diameter, but the maximum pressure was −500 hPa at a single 12 mm suction point, which was the maximum output of the device. Because no participant experienced discomfort at this value, the maximum allowable suction pressure for a single 12 mm suction site was considered to be more than −500 hPa.
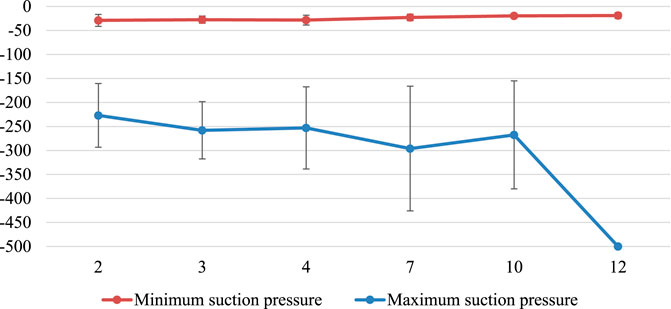
FIGURE 6. Maximum and minimum suction pressure values for different suction diameters. Error bars indicate standard deviation.
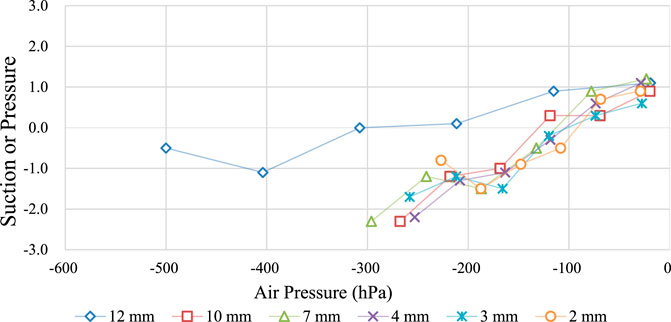
FIGURE 7. Perceptions of suction and pressure at different suction diameters and pressures. The score is −3 for suction and +3 for pressure perception.
Figure 7 shows the type of tactile sensation (suction or pressure) for each pressure at each suction diameter. It demonstrates that for all suction diameters, the stronger the suction pressure, the clearer the sensation of suction. In other words, the condition that caused the most significant pressure sensation was the minimum suction pressure for all suction systems (the minimum suction pressure is the weakest suction pressure at which a slight tactile sensation is felt). The user was more likely to feel the pressure sensation from the suction system in the case of the 12 mm suction diameter than the other suction diameters.
Figure 8 demonstrates that the tactile intensity increased with suction pressure. However, when a single 12 mm sucker was used (blue diamond in the figure), the maximum tactile strength was 3.1, which was weaker than that reported for other settings. This may be because the maximum suction pressure that the device could display was −500 hPa; thus, sufficient tactile intensity was not achieved. However, suction has some disadvantages, such as the possibility of leaving marks on the skin when the suction is increased to produce a stronger tactile sensation. The comparison of the results between the other shapes with multiple holes showed no significant differences.
Based on the results of Figure 7 and Figure 8, the relationship between the tactile sensation and tactile intensity is shown in Figure 9. The results show that low-intensity suction is likely to be perceived as pressure, whereas higher intensity is perceived as suction, irrespective of the shape of the suction unit.
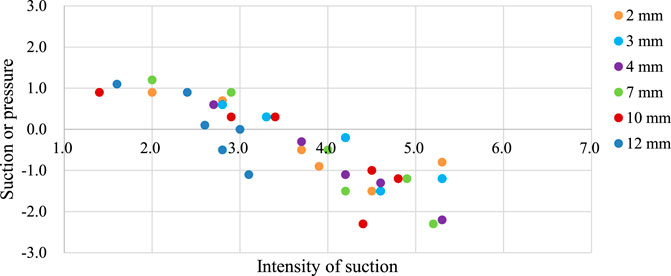
FIGURE 9. Correlation between tactile sensation (−3: suction, +3: pressure perception) and subjective intensity.
To analyze the results in Figure 7 and Figure 8, we used the Aligned Rank Transform (ART) ANOVA. A consequent one-way ANOVA of the suction diameter and tactile intensity, with Bonferroni correction, showed that 12 mm was significantly different from all other suction diameters, i.e., the tactile intensity was significantly weaker (12–2 mm: p < 0.00, 12–3 mm: p < 0.00, 12–4 mm: p < 0.00, 12–10 mm: p < 0.00). For Figure 7 (suction or pressure sensation), only the simple main effect was confirmed for suction pressure (η^2 = 0.68). For Figure 8 (tactile intensity), simple main effects and interactions (η^2 = 0.20) were observed for suction diameter size (η^2 = 0.51) and suction pressure (η^2 = 0.89). In combination with the weak correlation between tactile intensity and sensation in Figure 9, it can be considered that both suction diameter and suction pressure are related to the perception of pressure, but the pressure value has a stronger influence. Considering this, it is important to change the suction shape according to the air pressure control system used because the range of air pressure values suitable for tactile presentation varies depending on the size of the suction diameter.
5 FEM of the Suction Skin
The previous experiment showed that the tactile intensity increased with suction pressure, whereas the 12 mm single hole case produced a different trend. In this experiment, we used the FEM to observe the distribution of mechanical energy in the skin and compared the results with the subjective evaluation.
5.1 Simulation Procedure
ANSYS 2020 R2 Mechanical (ANSYS Inc.) was used to simulate the cheek skin presenting suction tactile sensation in Haptopus. The cheek structure is based on previously reported human skin data (Chopra et al., 2015). The thicknesses of the epidermis and dermis were set to 45.73 and 1,040.46 μm, respectively. The thickness of the subcutaneous tissue was assumed to be 5,000 μm, and the contact surface with the bone was assumed to be fixed (Figure 10). The physical parameters of the skin were taken from a study by Saito et al. (2019). The density was
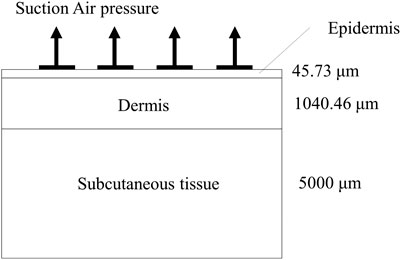
FIGURE 10. Schematic of the skin structure model. The thicknesses of the epidermis, dermis, and subcutaneous tissue are shown. Each tissue is defined as being connected to the other. Suction air pressure was applied to the epidermis in the suction direction based on the shape of the suction area.
5.2 Results
Figure 11 shows the results of the simulations for each suction shape. As the Merkel cells, which play a major role in pressure sensation, are located in the dermis of the skin, only the dermis model is shown.
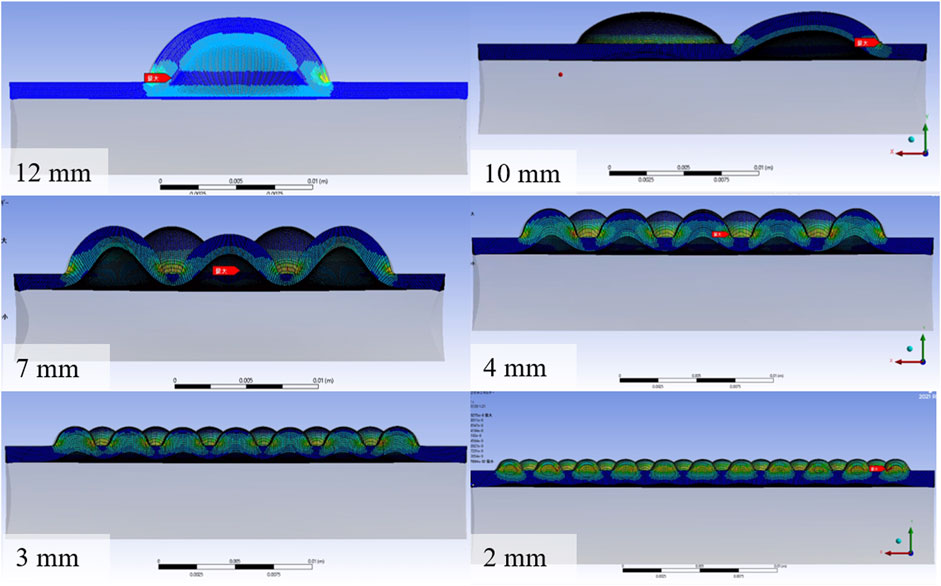
FIGURE 11. Cross-sectional view of the strain energy simulation results for each suction diameter. A pressure of −600 hPa was applied to the suction point on the skin surface. Only the dermis part is shown.
Figure 12 shows the results of the maximum strain energy at the dermis observed for each suction shape. The results show that, in general, the larger the diameter of the suction hole, the stronger the strain energy at the same suction pressure. However, for a suction diameter of 12 mm, the maximum strain energy is less than that of 10 mm.
6 Discussion
Figure 9 shows that weak negative pressure induces the sensation of pressure, whereas strong negative pressure induces the sensation of suction, regardless of the diameter of the suction hole. This creates a significant limitation: a pressure sensation created by suction cannot be strong.
Figure 12 shows that the strain energy applied to the Merkel cell region (dermis) increases with the suction diameter in the range up to 10 mm.
According to Figure 8, there is no clear relationship between the diameter of the holes and tactile intensity except when the diameter is 12 mm. Therefore, the maximum strain energy does not seem to explain the subjective tactile intensity. We theorized that the distribution (spatial sum) of strain energy, not the maximum strain energy, might affect the tactile intensity. A sucker with small suction holes has a greater overall surface area of contact with the skin, due to the number of holes. For example, a sucker with 2 mm-diameter holes has 91 holes, whereas that with 10 mm-diameter holes has only three holes. The total sum of circumferences in the case of 2 mm holes is 571 mm (2.0 × 3.14×91), whereas that of 10 mm holes is 94.2 mm (10.0 × 3.14 × 3). Therefore, although the maximum strain energy was three to four times larger in the case of 10 mm holes, the subjective intensity was similar.
This also explains why the 12 mm hole had a much smaller subjective intensity in Figure 8. In this case, there is only one suction hole, which gives a much shorter circumference. Figure 12 also shows that the maximum strain energy in the case of 12 mm became smaller than that of 10 mm. We consider that the adjacent suction holes increased the deformation of the skin and thus the strain energy (Figure 13B), whereas, in the case of 12 mm, there was only one suction hole, so the deformation was smaller (Figure 13A).

FIGURE 13. Model of skin deformation. In (A), there is only one hole and the deformation at the edge of the suction hole is small. In (B), two suction holes are adjacent to each other, and the skin deformation is greater.
In this study, we experimented with various suction diameters for skin suction tactile sensation on the face. We demonstrated that by using a suction pressure adjusted for each participant with multiple suction holes, one can control the subjective tactile intensity. Furthermore, by comparing the results with FEM simulation results, we observed that a stronger tactile sensation is generated by the multi-point suction holes than a single hole, possibly because of the strong strain between the neighboring suction holes. This means that the distance between the circumferences of the neighboring suction holes is one important design parameter, which needs further investigation. Furthermore, although the maximum strain energy is small when the diameter of the holes is small, strong sensation intensity is still obtained, presumably because of the greater total circumference of multiple holes. This is especially important for preserving subjective intensity without damaging the skin.
7 Conclusion
In this study, we investigated the design parameters of a suction-type tactile device for the face, which is intended to be embedded in an HMD. Previous methods for creating tactile sensations with suction used palms and forearms; however, suitable suction stimuli for thin skin such as the face were not clarified.
We developed a suction pressure control system and investigated the intensity and sensation of the suction tactile sensation while varying the hole diameter and suction pressure to establish optimal design parameters for use on the face. Subsequently, we found that the amount of skin deformation could be increased by increasing the density of suction holes, and stronger tactile intensity could be presented, even at the same suction pressure. The FEM simulation showed that the strain energy was concentrated at the edges of the suction holes, which provided information on how to arrange the suction holes in the suction shape design.
We also found that the pressure illusion as presented by suction diminishes when the suction is too strong. The weak pressure was similar to a light tapping sensation. Currently, it is not suitable for strong pressure sensations, such as grasping, pushing, or lifting. Further investigation is required on how to achieve a strong pressure-like sensation by suction.
There are several design parameters that we did not pursue, including the distance between the holes, different hole diameters in a single suction part, and the shape of the holes. We will further investigate these parameters to develop an efficient tactile device for the face.
Data Availability Statement
The raw data supporting the conclusions of this article will be made available by the authors, without undue reservation.
Ethics Statement
The studies involving human participants were reviewed and approved by the Ethics Review Committee of the University of Electro-Communications. The patients/participants provided their written informed consent to participate in this study.
Author Contributions
TK and HK contributed to the conception and design of the study. TK organized the experiment and performed the statistical analysis. TK wrote the first draft of the manuscript. All authors contributed to manuscript revision, read, and approved the submitted version.
Funding
This research was supported by JSPS KAKENHI, Grant Numbers JP20K20627 and JP20J23626.
Conflict of Interest
The authors declare that the research was conducted in the absence of any commercial or financial relationships that could be construed as a potential conflict of interest.
Publisher’s Note
All claims expressed in this article are solely those of the authors and do not necessarily represent those of their affiliated organizations, or those of the publisher, the editors and the reviewers. Any product that may be evaluated in this article, or claim that may be made by its manufacturer, is not guaranteed or endorsed by the publisher.
References
Antfolk, C., Björkman, A., Frank, S., Sebelius, F., Lundborg, G., Rosen, B., et al. (2012). Sensory Feedback from a Prosthetic Hand Based on Air-Mediated Pressure from the Hand to the Forearm Skin. J. Rehabil. Med. 44, 702–707. doi:10.2340/16501977-1001
Arai, F., Morita, H., Kwon, G., Fukuda, T., and Matsuura, H. (2001). “Tactile Display Which Presents Shear Deformation on Human Finger,” in Proceedings 2001 ICRA. IEEE International Conference on Robotics and Automation (Cat. No. 01CH37164), 2486–2491.3
Ben Porquis, L., Konyo, M., and Tadokoro, S. (2011). Enhancement of Human Force Perception by Multi-point Tactile Stimulation. IEEE Int. Conf. Intell. Robots Syst., 3488–3493. doi:10.1109/iros.2011.6094762
Ben Porquis, L., Maemori, D., Nagaya, N., Konyo, M., and Tadokoro, S. (2013). “Haptic Cue of Forces on Tools: Investigation of Multi-point Cutaneous Activity on Skin Using Suction Pressure Stimuli,” in 2013 IEEE/RSJ International Conference on Intelligent Robots and Systems, 2023–2029.
Ben Porquis, L., Maemori, D., Nagaya, N., Konyo, M., and Tadokoro, S. (2014). “Presenting Virtual Stiffness by Modulating the Perceived Force Profile with Suction Pressure,” in IEEE Haptics Symposium, 289–294. HAPTICS. doi:10.1109/haptics.2014.6775469
Chang, H. Y., Tseng, W. J., Tsai, C. E., Chen, H. Y., Peiris, R. L., and Chan, L. (2018). “Facepush: Introducing Normal Force on Face with Head-Mounted Displays,” in Proceedings of the 31st Annual ACM Symposium on User Interface Software and Technology, 927–935.
Chopra, K., Calva, D., Sosin, M., Tadisina, K. K., Banda, A., De La Cruz, C., et al. (2015). A Comprehensive Examination of Topographic Thickness of Skin in the Human Face. Aesthet. Surg. J. 35, 1007–1013. doi:10.1093/asj/sjv079
Hachisu, T., and Fukumoto, M. (2014). “VacuumTouch: Attractive Force Feedback Interface for Haptic Interactive Surface Using Air Suction,” in Proceedings of the Conference on Human Factors in Computing Systems, 411–420.
Hwang, I., Son, H., and Kim, J. R. (20172017). AirPiano: Enhancing Music Playing Experience in Virtual Reality with Mid-air Haptic Feedback. IEEE World Haptics Conf. (WHC), 213–218. doi:10.1109/whc.2017.7989903
Ichinose, A., Sano, Y., Osumi, M., Sumitani, M., Kumagaya, S. I., and Kuniyoshi, Y. (2017). Somatosensory Feedback to the Cheek during Virtual Visual Feedback Therapy Enhances Pain Alleviation for Phantom Arms. Neurorehabil. Neural Repair 31 (717–725), 717–725. doi:10.1177/1545968317718268
Jun, J. H., Park, J. R., Kim, S. P., Min Bae, Y., Park, J. Y., Kim, H. S., et al. (2015). Laser-induced Thermoelastic Effects Can Evoke Tactile Sensations. Sci. Rep. 5, 11016–16. doi:10.1038/srep11016
Kameoka, T., and Kajimoto, H. (2021). “Tactile Transfer of Finger Information through Suction Tactile Sensation in HMDs,” in IEEE World Haptics Conference (WHC 2021), 949–954. doi:10.1109/whc49131.2021.9517176
Kameoka, T., Kon, Y., Nakamura, T., and Kajimoto, H. (2018). “Haptopus,” in Proceedings of the Symposium on Spatial User Interaction, 11–15. doi:10.1145/3267782.3267789
Kim, S.-B., and Lee, Y.-H. (2014). Numerical Analysis of the Change in Skin Color Due to Ecchymosis and Petechiae Generated by Cupping: A Pilot Study. J. Acupunct. Meridian Stud. 7, 306–317. doi:10.1016/j.jams.2013.09.004
Kim, S. Y., Kim, Y. J., Choi, D. S., and Shin, B. S. (2019). Frequency Based Tactile Rendering Method for Pin-Array Tactile Devices. J. Ambient Intell. Humaniz. Comput., 1–8. doi:10.1007/s12652-019-01408-w
Kon, Y., Nakamura, T., and Kajimoto, H. (2017). HangerOVER: HMD-Embedded Haptics Display with Hanger Reflex. In ACM SIGGRAPH 2017 Emerging Technologies, SIGGRAPH. 2017, 1–2.
Kyung, K. U., Ahn, M., Kwon, D. S., and Srinivasan, M. A. (2005). “Perceptual and Biomechanical Frequency Response of Human Skin: Implication for Design of Tactile Displays,” in First Joint Eurohaptics Conference and Symposium on Haptic Interfaces for Virtual Environment and Teleoperator Systems. World Haptics Conference, 96–101.
Maemori, D., Porquis, L. B., Konyo, M., and Tadokoro, S. (2014). A Multi-DoF Haptic Representation Using Suction Pressure Stimuli on Finger Pads. Lect. Notes Comput. Sci. Incl. Subser. Lect. Notes Artif. Intell. Lect. Notes Bioinforma. 8619, 285–294. doi:10.1007/978-3-662-44196-1_35
Maeno, T., Kobayashi, K., and Yamazaki, N. (1998). Relationship between the Structure of Human Finger Tissue and the Location of Tactile Receptors. JSME Int. J. Ser. C 41, 94–100. doi:10.1299/jsmec.41.94
Maisto, M., Pacchierotti, C., Chinello, F., Salvietti, G., De Luca, A., Prattichizzo, D., et al. (2017). Evaluation of Wearable Haptic Systems for the Fingers in Augmented Reality Applications. IEEE Trans. Haptics 10, 511–522. doi:10.1109/toh.2017.2691328
Makino, Y., Asamura, N., and Shinoda, H. (2003). “A Cutaneous Feeling Display Using Suction Pressure,” in SICE 2003 Annual Conference, 2931–2934.2
Makino, Y., Asamura, N., and Shinoda, H. (2004). “Multi Primitive Tactile Display Based on Suction Pressure Control,” in 12th International Symposium on Haptic Interfaces for Virtual Environment and Teleoperator Systems 2004, 90–96. HAPTICS. (’04). Proceedings. doi:10.1109/haptic.2004.1287182
Makino, Y., and Shinoda, H. (2005). Suction Pressure Tactile Display Using Dual Temporal Stimulation Modes. Proc. SICE Annu. Conf., 1285–1288.Available at: https://www.sice.or.jp/org/sice2005.
Moriyama, T., Asazu, H., Takahashi, A., and Kajimoto, H. (2019). “Simple Is Vest: High-Density Tactile Vest that Realizes Tactile Transfer of Fingers,” in SIGGRAPH Asia 2019 Emerging Technologies (New York, NY: Association for Computing Machinery), 42–43. doi:10.1145/3355049.3360532
Moriyama, T., Nishi, A., Nakamura, T., Yem, V., and Kajimoto, H. (2018). “Hap-Link: Wearable Haptic Device on the Forearm that Presents Haptics Sensations Corresponding to the Fingers,” in SIGGRAPH Asia 2018 Emerging Technologies, SIGGRAPH Asia.
Nagano, H., Sase, K., Konyo, M., and Tadokoro, S. (2019). “Wearable Suction Haptic Display with Spatiotemporal Stimulus Distribution on a Finger Pad,” in IEEE World Haptics Conference (WHC 2019), 389–394. doi:10.1109/whc.2019.8816156
Okano, T., Hiki, K., Hirota, K., Nojima, T., Kitazaki, M., and Ikei, Y. (2018). Development of a Sole Pressure Display. Lect. Notes Electr. Eng. 432, 175–180. doi:10.1007/978-981-10-4157-0_30
Peiris, R. L., Peng, W., Chen, Z., Chan, L., and Minamizawa, K. (2017). “ThermoVR: Exploring Integrated Thermal Haptic Feedback with Head Mounted Displays,” in Proceedings of the Conference on Human Factors in Computing Systems, 2017.
Penfield, W., and Rasmussen, T. (1950). The Cerebral Cortex of Man: A Clinical Study of Localization of Function. J. Am. Med. Assoc. 144, 1412.
Porquis, L. B. C., Konyo, M., and Tadokoro, S. (2012). “Tactile-based Torque Illusion Controlled by Strain Distributions on Multi-Finger Contact,” in Proceedings Haptics Symposium 2012, 393–398. HAPTICS. doi:10.1109/haptic.2012.6183820
Ramachandran, V. (1998). The Perception of Phantom Limbs. The D. O. Hebb Lecture. D. O. Hebb Lect. Brain. 121, 1603–1630. doi:10.1093/brain/121.9.1603
Saal, H. P., Delhaye, B. P., Rayhaun, B. C., and Bensmaia, S. J. (2017). Simulating Tactile Signals from the Whole Hand with Millisecond Precision. Proc. Natl. Acad. Sci. U. S. A. 114, E5693–E5702. doi:10.1073/pnas.1704856114
Saito, K., Konyo, M., Nagano, H., Sakaguchi, S., and Arakawa, N. (2019). “Simultaneous Measurement of Skin Deformation and Perceptual Sensitivity Using Suction Pressure,” in IEEE World Haptics Conference (WHC) 2019. doi:10.1109/whc.2019.8816161
Schoepp, K. R., Dawson, M. R., Schofield, J. S., Carey, J. P., and Hebert, J. S. (2018). Design and Integration of an Inexpensive Wearable Mechanotactile Feedback System for Myoelectric Prostheses. IEEE J. Transl. Eng. Health Med. 6, 2100711. doi:10.1109/JTEHM.2018.2866105
Shen, V., Shultz, C., and Harrison, C. (2022). “Mouth Haptics in VR Using a Headset Ultrasound Phased Array,” in CHI Conference on Human Factors in Computing Systems (CHI '22) (New York, NY, USA: Association for Computing Machinery), 1–14. doi:10.1145/3491102.3501960275
Shi, G., Palombi, A., Lim, Z., Astolfi, A., Burani, A., Campagnini, S., et al. (2020). Fluidic Haptic Interface for Mechano-Tactile Feedback. IEEE Trans. Haptics 13 (1), 204–210. doi:10.1109/toh.2020.2970056
Wang, C., Huang, D. Y., Hsu, S. W., Hou, C. E., Chiu, Y. L., Chang, R. C., et al. (2019). “Masque: Exploring Lateral Skin Stretch Feedback on the Face with Head-Mounted Displays,” in Proceedings of the 32nd Annual ACM Symposium on User Interface Software and Technology, 439–451.
Wolf, D., Rietzler, M., Hnatek, L., and Rukzio, E. (2019). Face/on: Multi-Modal Haptic Feedback for Head-Mounted Displays in Virtual Reality. IEEE Trans. Vis. Comput. Graph. 25, 3169–3177. doi:10.1109/tvcg.2019.2932215
Keywords: air pressure, FEM, HMD, suction haptics, virtual reality
Citation: Kameoka T and Kajimoto H (2022) Design of Suction-Type Tactile Presentation Mechanism to Be Embedded in HMD. Front. Virtual Real. 3:894873. doi: 10.3389/frvir.2022.894873
Received: 12 March 2022; Accepted: 25 May 2022;
Published: 17 June 2022.
Edited by:
Jin Ryong Kim, The University of Texas at Dallas, United StatesReviewed by:
Jaeyoung Park, Hongik University, South KoreaSang-Youn Kim, Korea University of Technology and Education, South Korea
Copyright © 2022 Kameoka and Kajimoto. This is an open-access article distributed under the terms of the Creative Commons Attribution License (CC BY). The use, distribution or reproduction in other forums is permitted, provided the original author(s) and the copyright owner(s) are credited and that the original publication in this journal is cited, in accordance with accepted academic practice. No use, distribution or reproduction is permitted which does not comply with these terms.
*Correspondence: Takayuki Kameoka, a2FtZW9rYUBrYWppLWxhYi5qcA==