- 1National Institute of Standards & Technology, Gaithersburg, MD, United States
- 2Department of Physics, Georgetown University, Washington, DC, United States
The development of secondary sources as industrial feedstocks is important to creating resilient supply chains that contribute towards diverting resources away from landfills, mitigating deleterious environmental impacts, and minimizing market volatility. A major challenge to develop secondary feedstocks is the coordination and digitalization of the large quantities of generated information at each phase of a product’s life cycle. This paper builds upon earlier work that illustrates a top-level model of the activities and information needs to integrate product manufacturing with circular practices. This paper extends the initial work to explore the cyclical nature of Circular Economy (CE) information flows specifically related to product End-of-life. Using the Integrated Definition 0, IDEF0, modeling technique this paper examines the End-of-life function envisioned under a CE manufacturing model [ISO, 2012]. This function is decomposed into subsequent child functions and is analyzed relative to other product life cycle phases. The paper reviews the current global product EoL practices and in the context of the developed IDEF0 model. The proposed framework contributes a detailed description and presentation of information flows and the drivers of change (i.e., feedback loops) that are essential for creating secondary material streams based on the critically analyzing the reviewed literature. The novelty of this study includes the identification of standards and metrics gaps to facilitate quantitative assessment and evaluation in a CE. The study further elucidates the discussion around CE in terms of resource regeneration by ‘designing out waste’ and decoupling economic growth from resource depletion.
1 Introduction
The Circular Economy (CE) is an economic model that promotes efficient resource consumption patterns via waste mitigation strategies, long-term value retention, reduction of society’s reliance on virgin resources, and closed-loop resource flows for products, components, and materials (Morseletto, 2020; Hofmann, 2019). The CE paradigm has gained tremendous momentum in the past decade and has been positioned as a means of decoupling virgin resource consumption and the associated environmental impacts from economic growth (Velenturf and Purnell, 2021). This can contribute towards the creation of new business opportunities and jobs, address material price volatility and secure supply chains (Kalmykova et al., 2018; Mathews and Tan, 2016). One way of achieving tangible benefits via CE practices is through the development of secondary sources of industrial feedstock. Recovered material feedstocks are critical to closing material flow loops. Besides technological and regulatory barriers, another barrier to the implementation of effective End-of-Life (EoL) treatment practices to close material flow loops is that CE-specific standards remain nascent even though the CE paradigm is not new. Thus, strengthening measurement science (a science-driven system of metrics, methods, and indicators) to support the development of standards remains vital.
This paper contributes towards our understanding of the current waste crisis, from a global as well as U.S. perspective, and identifies standards’ needs and associated barriers to integrate the recovery of materials into existing manufacturing practices. Opportunities in terms of digital technologies that could aid in overcoming the identified barriers have been discussed. The aforementioned objectives of the paper are addressed via the following sub-tasks:
1) The representation of the product recovery process for a generic product by, through the decomposition of the EoL product life cycle phase in the context of a CE (Reslan et al., 2022).
2) The subsequent identification of potential measurement science opportunities relative to waste reporting, inconsistencies in waste terminology and classification, and the lacunae in data requirements from the proposed activity model.
The paper is structured as follows: Section 2 reviews the literature to provide the readers with an in-depth understanding of the current global waste crisis, existing waste management practices, and barriers impacting recoverability (particularly from the point of view of the technical standards). Section 3 proposes an activity model for EoL product treatment and management. The model proposed in this paper characterizes processes that facilitate material recovery from used products and provides a basis to develop relevant standards and further measurement science for the effective evaluation of environmental performance. The activity model representation of the EoL phase of a product is described in Section 4, followed by an analysis in Section 5, wherein specific standards gaps in the EoL phase are identified along with the broad areas where implementing standards would contribute towards closing material flow loops and a CE. Our findings are compared with the current CE related standards landscape in Section 6, followed by a summary and conclusions section.
2 Background: The current waste crisis
In a circular economy, waste is viewed as a resource with value (Schmitt et al., 2021). The world generates more and more waste each year, but little is known about the compositions of many waste streams, who is producing the waste, and where it is ending up (Singh and Ordoñez, 2016). With high-quality, traceable data up and down waste streams, we can identify what is being produced and how to best make that “waste” into a resource reducing reliance on landfills. This section covers the current global and US waste landscape, the barriers, and opportunities to better manage the current crisis and needs for data and standards.
2.1 The global solid waste management landscape
Solid waste threatens human quality of life and the environment, and waste streams are expected to increase around the world. Waste production and management between high- and low-income countries differ greatly (See Supplementary Appendix A1 for country classification according to income). High-income countries like the United States, those in Western Europe, Japan, and Saudi Arabia generate much waste (34% of the world’s waste as of 2016) and generally have high collection, treatment, recovery, and disposal rates (Kaza et al., 2018). Low-income countries, on the other hand, have the opposite relationship with waste, generating very little (5% of the world’s waste as of 2016) and collecting relatively little (about 39%) (Kaza et al., 2018), although the informal waste management sector tends to be robust in these countries—an estimated 15 million people were estimated to make a living from informal recycling in 2007 (Aparcana, 2017; Medina, 2008). The United States, European Union, Japan, and other countries take a decentralized approach in which local governments dictate much of the solid waste management (SWM) practices. While the US Environmental Protection Agency (EPA) has regulatory authority over hazardous waste and can make recommendations for how to best manage and divert waste, state, tribal, and local governments regulate non-hazardous waste [US EPA, 2021c]. Similarly, in Japan, SWM is governed by municipalities and in the EU, the EU defines policies around SWM, but each member state defines and implements policies locally (Gusmão Gomes de Andrade Lima et al., 2016).
Waste generation is increasing in low-, medium-, and high-income countries (Figure 1A, refer to Supplementary Appendix A1). While high-income countries are currently responsible for most global waste generation now, the World Bank predicts that the amount of waste that low-income countries generate will increase threefold by 2050 (Kaza et al., 2018). Figure 1B provides waste generation projections regionally and it is observed that waste generation is growing the fastest in Sub-Saharan Africa, South Asia, and the Middle East North Africa region. Middle- and high-income countries are also predicted to increase the amount of waste they generate in the years to come (Figure 1B, refer to Supplementary Appendix A1). This is in part because waste generation increases with income and with urbanization. In addition, as a country gets more prosperous, it manages its waste more sustainably (Ferronato and Torretta, 2019; Kaza et al., 2018), as less sustainable practices like open dumping cause heavy health and environmental damage (dos Muchangos et al., 2015; Modak et al., 2015; Sanneh et al., 2011; Torretta et al., 2017). This trend will be influenced by other factors including policy and technology that also play a role in how sustainably waste is managed (Okot-Okumu and Nyenje, 2011; Han and Zhang, 2017). Sustainable management practices can be less impactful in terms of environmental degradation and human health but can also incur prohibitively expensive up-front costs. SWM in low-income countries may be less expensive than it is in medium- and high-income countries, but account for a higher percentage of residential income and municipal budget (Matheson, 2022). The World Bank found that SWM in urban areas can account for 20% of a municipality’s budget in low-income countries (although it can be as high as 80–90%) (Hoornweg and Bhada-Tata, 2012; Srivastava et al., 2015), but only 10% and 4% in medium- and high-income countries, respectively (Kaza et al., 2018). Having an established systems for collecting waste is a good first step toward 1) describing that waste and 2) implementing strategies to decrease and divert waste.
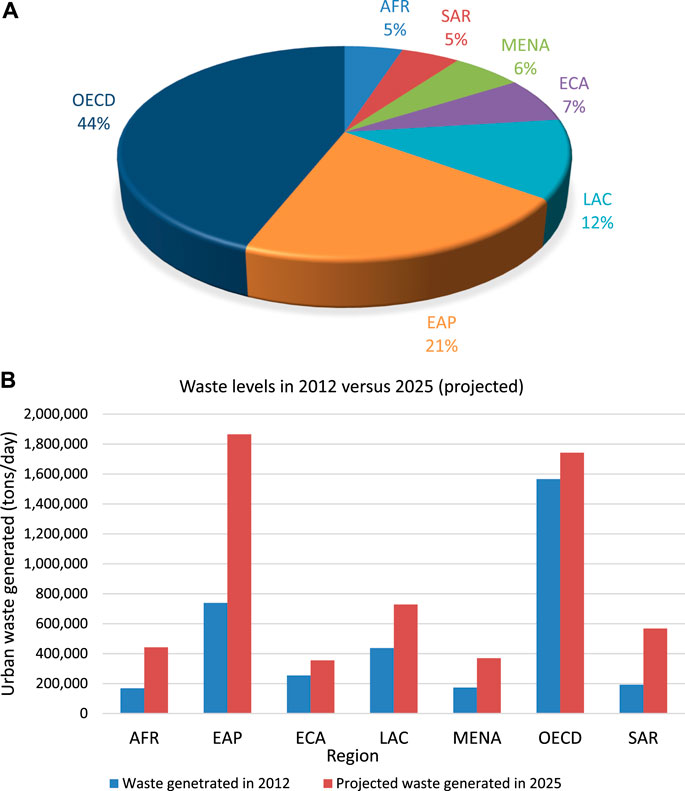
FIGURE 1. (A) Share of waste generation by region * [based on the findings of Hoornweg and Bhada-Tata, 2012. (B) Waste generation by region* for 2012 and 2025 (projected) [based on the findings of Hoornweg and Bhada-Tata, 2012.*(AFR: Africa; EAP: East Asia & Pacific;ECA: Eastern & Central Asia; LCA: Latin America & the Caribbean; MENA: Middle East & North Africa; OECD: Organization for Economic Cooperation & Development; SAR: South Asia).
See Supplementary Appendices A1, A2 for a more detailed breakdown on country classification according to regions and income levels.
2.2 Challenges in measuring and categorizing waste
Solid waste is generated by industry, households, and governments. Characterizing this waste is a necessary pre-cursor to measuring it. Waste can broadly be defined as three types of solid waste categories. First, pre-consumer waste is waste that “has never reached the end-user” [UL, 2020] (e.g., industrial scrap and food waste that never reached a consumer) whereas post-consumer waste did reach the end user (e.g., municipal curbside waste). Second, waste can also be categorized into hazardous—which the US EPA defines as “a waste with properties that make it dangerous or capable of having a harmful effect on human health or the environment” (US Environmental Protection Agency, 2021a) and non-hazardous. As mentioned before, the US EPA regulates hazardous solid waste, but not non-hazardous solid waste. Furthermore, we categorize waste streams based on which sector is generating it: industrial waste (so called ICI, or industrial, commercial, and institutional waste), construction and demolition waste (C&D) and municipal solid waste (MSW, or waste generated by households and businesses that use management systems like curbside pickup). Further, an ASTM International publication, provides more detailed categories for characterizing discards from manufacturing facilities.
Accurately measuring waste streams is difficult, both locally and globally (Martínez et al., 2022; United Nations Environment Programme, 2015). As a result, the amount of industrial waste generated and its management globally are underestimated (Ferronato and Torretta, 2019). One reason is a lack of standard methods for countries to define different waste streams (Chen et al., 2020; United Nations Environment Programme, 2015). The general trend is that countries do not separate ICI, C&D, and MSW in their reporting. For example, the EU reportedly generated 2.337 million tons of waste in 2018 across all economic activities and households (Eurostat, 2021), but it does not report MSW, ICI, or C&D separately, instead letting countries create their own definitions (Woodard, 2020). Singapore, too, does not separate manufacturing waste from MSW (Kerdlap et al., 2019). Japan, however, does distinguish between MSW and industrial waste Government of Japan Ministry of Environment, 2018; for more, see Table 1 in Woodard, 2020]. In the US, states, tribes, and local governments may collect data on non-hazardous solid waste, but they are not required to report it to federal agencies (US Environmental Protection Agency, 2022).
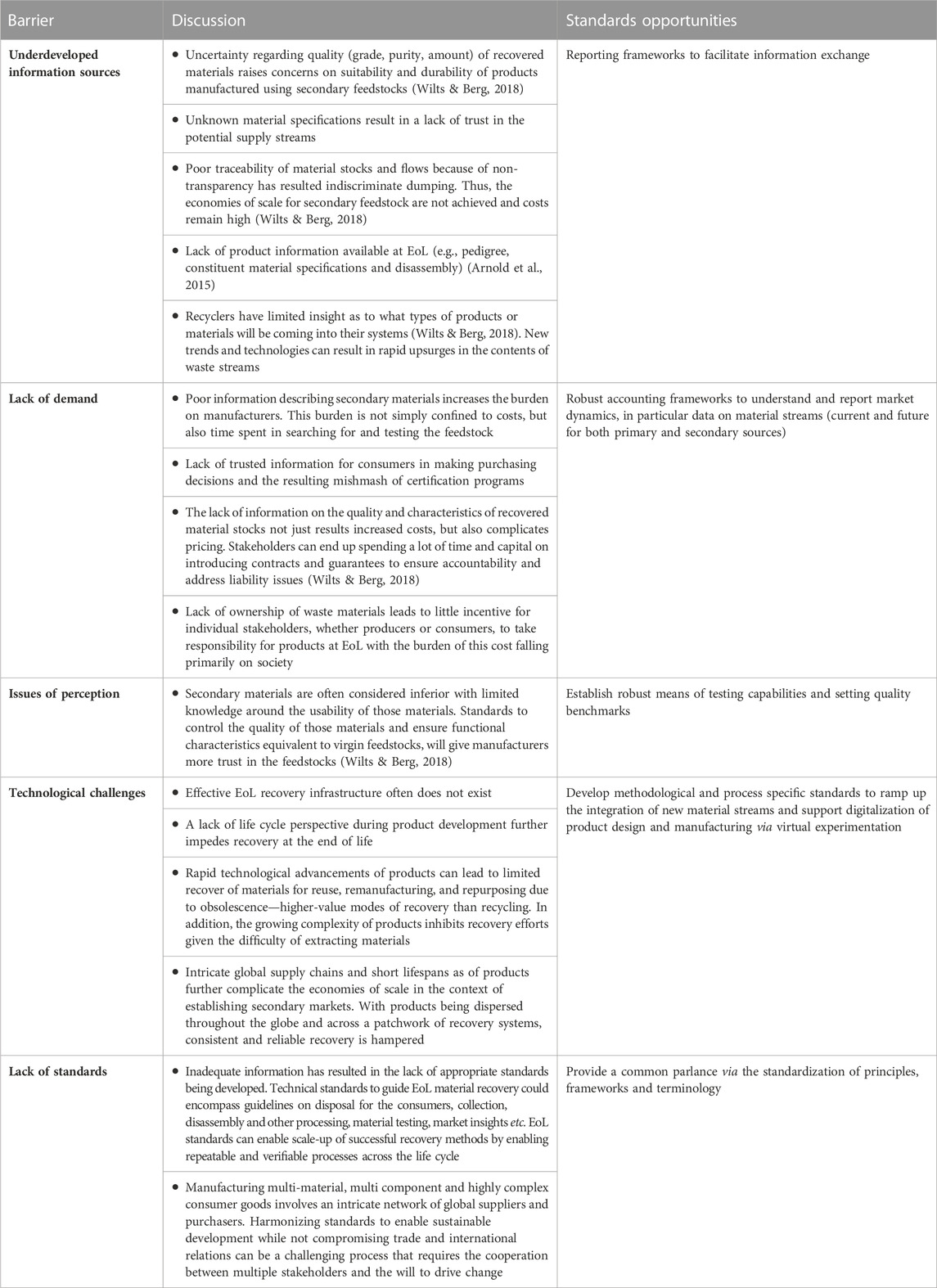
TABLE 1. Barriers to EoL material recovery (Arnold et al., 2015; Wilts & Berg, 2018).
Another problem is with terminology in what exactly constitutes ICI waste. The World Bank reported that the waste that is created from industrial processes globally (e.g., manufacturing, agriculture) is almost 18 times greater than MSW (Kaza et al., 2018). The Ellen MacArthur Foundation reported that factories in Europe produced 46 million more tons of waste than households [Ellen MacArthur Foundation, 2022]. However, in the US, at least, this comparison is not as simple as it seems because (Krones, 2016). The absence of clarity around exactly what the compositions of various waste categories is and how much is generated is another barrier to collecting trustworthy, traceable data.
2.3 Magnitude of industrial waste in the United States
The US does not have a good understanding of its material flows, especially when it comes to waste generated by the manufacturing sector. As a high-income country, the U.S. generates a disproportionate amount of waste relative to many other countries in the world. In 2018, it generated 292 million US short tons of MSW according to the US EPA (The EPA collects information on MSW and hazardous waste, but not ICI or C&D (US Environmental Protection Agency, 2020).) The MSW infrastructure consists of five components: 1) landfills, 2) incinerators, 3) transfer stations, 4) material recovery facilities (MRFs), and 5) mechanical and chemical recycling facilities (US Environmental Protection Agency, 2021a). The EPA reported that the country generated 292 million tons of MSW in 2018, 32.1% of which was recycled or composted. Reporting on waste generated by manufacturers (ICI waste), however, is decentralized and not aggregated (Krones, 2016).
In the National Recycling Strategy (US Environmental Protection Agency, 2021a) the EPA identified improving collection and materials management infrastructure as one of its objectives to achieving a 50% recycling rate by 2030. This includes mapping out the infrastructure and identifying and filling gaps. A better understanding of the US’s solid waste infrastructure may be used to address ICI and C&D waste streams.
Unfortunately, the problem of waste segregation, categorization and tracking is compounded by large-scale production of increasingly complex multi-material, multi-component products very efficiently. The electronics sector represents one such example and the growing electronics waste (e-waste) problem is exacerbated by society’s inability to collect, segregate, and treat EoL electronics (Schumacher and Green, 2021). Although in the US e-waste is meant to be treated separately under the category of Waste Electrical and Electronics Equipment (WEEE), inevitably some e-waste ends up in the MSW stream especially with growth in the number of household goods that embed electronics. The plastics sector represents yet another example of haphazard EoL treatment and difficult segregation (Beers et al., 2022). Other sectors see similar problems and, in future, clean energy technologies—such as electric vehicles (EVs), wind turbines and solar panels—pose a similar problem if an adequate practices for addressing the resulting waste streams are not developed (Mathur et al., 2020; Maani et al., 2021; Schumacher and Forster, 2022; NIST, 2022).
Solutions for better waste management practices are needed across a number of dimensions including technological advances, better engineering and manufacturing practices, and policies and regulations. Solutions will need capabilities for tracking and quantifying waste streams, segregating waste streams to prevent cross contamination, and technologies that can address the complex nature of these products including effective material extraction. Currently, the US has no clear path to deal with the impending clean energy technology waste that will ensue in the near future. Developing a robust system to manage EoL post-consumer goods is especially important to facilitate recovery and preserve resources, and also to support the reuse of those materials by fostering new streams of material of known quality and reliable quantities.
2.4 Industrial waste and post-consumer products recovery infrastructure in the US
One main reason that it is important to understand and quantify industrial and post-consumer waste is that this waste can be valuable. Market pressures are pivotal to the recycling industry where recycled content competes with virgin feedstock. Industries are not strongly incentivized to reduce or divert waste. Many of their decisions to use virgin or recycled material is based on price, and markets for diverted waste are not strong (Le Moigne, 2021). For years, China bought and processed nearly half of the world’s recyclables, but in 2018 the country implemented an import ban on recyclables; India, Malaysia, Thailand, and Vietnam followed suit shortly afterward (Kerdlap et al., 2019; Solid Waste Association of North America, 2021). Since then, the market for secondary materials has been unstable and subject to great fluctuations. It is often cheaper to buy virgin materials than recycled ones, especially plastics, and incinerate or landfill waste than recycle it (Solid Waste Association of North America, 2021). A stronger, more regulated market for waste streams, policy changes such as tax and other incentives, and/or pressure from consumers could address this problem (Solly et al., 2019).
The federal government has little authority in the management and control over non-hazardous industrial waste. It is classified under Subtitle D of the Resource Conservation and Recovery Act (RCRA), which bans it from being disposed of in open dumps and sets minimum federal guidelines for landfills. States themselves can set stricter rules on the disposal of industrial waste (US Environmental Protection Agency, 2021b). This results not only in a patchwork of recycling policies that vary regionally, it also means that no organization is able to account for the content, magnitude, and flow of waste streams. Better insight into the flow of goods would support recyclers in better preparing for their management, as well as prepare potential processors and consumers of the waste streams.
One way to divert dumping and increase value recovery from discarded materials and products is via Industrial Symbiosis. Industrial symbiosis, a branch of industrial ecology, is a relationship in which different industries share or sell resources with one another. When done effectively, this relationship can yield huge environmental, economic, and social benefits [for review, see Neves et al., 2020]. The most famous example of industrial symbiosis is the eco-industrial park in Kalundborg, Denmark, in which a variety of industries–e.g., oil refinery, pharmaceutical plant, and gypsum board facility–and the city share water and electricity and exchange outputs from their processes to be used as feedstock for other processes. For example, two pharmaceutical companies that are in the partnership produce biomass as an output, but instead of disposing of that biomass, the companies sell it to another member of the eco-industrial park, a bioenergy company, that uses the biomass as feedstock to create natural gas.
Some companies in the US also use industrial symbiosis to increase profit and decrease waste. Industrial symbiosis facilitates open-loop recovery, i.e., the use of recovered materials to manufacture different products (Mathur et al., 2020). Closed-loop recovery on the other hand reintroduces recovered materials to manufacture the same product (Mathur et al., 2020). A collaboration between a waste management company and a manufacturer called the Casella-Hypertherm Recycling Partnership (CHRP) expanded into a larger recovery ecosystem in the northeastern US that made recycling easier and more cost-effective than it had been before the relationship (Krones, 2017). There are other instances of manufacturers creating value for secondary resources using industrial symbiosis and research in this area examines several potential opportunities as well (Light House Society, 2019; Mathur et al., 2019; 2020; 2022). A report to the Washington State Department of Commerce suggested that industrial symbiosis operates best when it is supported by “dedicated facilitation,” such as the government (Light House Society, 2019). The report also suggests that governments could act as investors and convenors to facilitate such collaborative ecosystems. Washington State recently passed new legislation to facilitate these relationships [Establishing a Statewide Industrial Waste Coordination Program, 2021].
2.5 Measurement science barriers to effective waste recovery
The literature reviewed highlights the scale of waste generated. It also highlights the fact that current measures to address this waste are lacking. This is evident by the quantities of waste being produced and under conventional disposal practices, subsequently ending up in landfills owing to the lack of requisite material recovery infrastructure and, also high labor costs, particularly in developed countries (Darby and Obara, 2005; Nnorom and Osibanjo, 2008; Akram et al., 2019). Industrial waste is of particular concern since many manufacturing sectors consume high-quality and therefore, high-value industrial feedstock. Processing industrial feedstock to the required specifications can be extremely resource intensive in terms of energy, water, and other resources. Furthermore, each processing phase results in the generation of byproducts. Often these are hazardous and must be disposed in special landfills (Ilankoon et al., 2018; Mathur et al., 2020; Ahirwar and Tripathi, 2021).
Increasing populations and consumer demands also means the acquisition and creation of industrial feedstocks as a consequence of complex processes for use in products with lifetimes that are getting shorter with each generation (e.g., consumer electronics, single-use and other plastic products) (Richter et al., 2019; Faraca and Astrup, 2019; Heller et al., 2020). Society’s ability to exploit the economies of scale of manufactured, complex, multi-component and multi-material products has resulted in indiscriminate consumption and disposal by a growing global population. This linear economy is unsustainable and has resulted in environmental degradation and the depletion of resources. Simply landfilling used products results in the loss of valuable resources. Wilts and Berg identified four challenges to recovering discarded materials and used products (Wilts & Berg, 2018). Based on our literature review, we expand on those challenges and highlight a fifth challenge—standards (See Table 1). Standards will be needed across many dimensions to create recovery systems that work in unison with production, material acquisition, and disposal mechanisms and to scale these solutions globally. Table 1 summarizes the barriers to material recovery and identifies broad areas for potential standards development. Table 2 in Section 4 further elaborates upon the standards requirements derived from the EoL IDEF0 model.
2.6 Opportunities for better measurement: The Circular Economy and digital technologies amalgamation
The CE vision addresses society’s current limitations by closing material flow loops and reducing reliance on virgin resources. It is especially important as estimates are that global material consumption and waste generation will double by 2050 (Franzo et al., 2021). While CE is a promising paradigm for decoupling economic growth from resource consumption and environmental degradation, other emerging digital technologies (DT) such as internet of things (IoT), big data analytics (BDA), artificial intelligence (AI) and additive manufacturing, have the potential to change the way society manufactures and delivers products (Korhonen et al., 2018; Pieroni et al., 2019; World Economic Forum, 2016; Lasi et al., 2014). Interest in exploring the potential of DT in the realm of CE-driven manufacturing is growing (Awan et al., 2021; Liu et al., 2021). Although various studies have been undertaken to investigate linked DT and CE strategies, the overall understanding where DT can be used to implement CE practices remains underdeveloped (Ingemarsdotter et al., 2019; Kristoffersen et al., 2020; Rosa et al., 2020; Cagno et al., 2021; Liu et al., 2021). Although Liu et al. provide a thorough analysis of how DT can be used in the context of reverse supply chains, extending product lifespans, remanufacturing, and fostering industrial symbiosis, they highlight the importance of multi-dimensional and multi-actor data requirements, safe and secure data exchange platforms and advancing empirical research (Liu et al., 2021).
Addressing these gaps will require research and development to advance measurement science that, in turn, will facilitate the development of appropriate CE-driven technical standards. Standards are instrumental in regularizing technological innovations, enabling trade between nations and establishing trust within markets, and quantifying performance. EoL product recovery is an area that requires particular attention. Closing material flow loops will require the seamless transfer of information between multiple stakeholders to facilitate effective disposal, collection, and recovery mechanisms; novel processing methods; material testing methods; and creation of an infrastructure that promotes secondary material markets. Furthermore, critical information loops can feedback information to other product life cycle phases, creating the potential to drive CE strategies earlier in the life cycle, such as, through the implementation of Design for Environment (DfE). Identifying these information loops is vital to bridge DT with a CE framework for manufacturing.
3 Activity-based representation of CE to strengthen sustainability and measurement science for the development of standards
Strengthening measurement science for manufacturing and around emerging sustainable manufacturing activities will build repeatability in best practices, enable quicker scale up of sustainability approaches, and create trust in industrial practices and systems. Developing and standardizing sustainability evaluation methods and tools will contribute towards eliminating inaccuracy and ambiguity in claims and enable manufacturers to compare processes and their impacts consistently. Sustainable manufacturing is a function of many parameters, including material use, energy use, waste, and equipment. Early work on sustainable manufacturing was often focused on improving the efficiency of manufacturing processes and production systems in order to reduce resource consumption. The work discussed herein builds out from that foundation to look at the broader set of needs for creating fully circular material loops.
Early NIST work used the IDEF0 technique to define the Systems Integration for Manufacturing Application (SIMA) reference architecture to model the design to production phase of the product development (Barkmeyer et al., 1987; Christopher et al., 1996). Subsequent work extended this model with sustainability considerations which provided a framework for standards development [Valivullah et al., 2014]. Mani et al. proposed an activity model for sustainable manufacturing (Mani et al., 2013). More recently Reslan et al. extended the model by introducing activities that address CE practices across a full product life cycle incorporating including practices that address the flow of material back into the manufacturing system. (Reslan et al., 2022). The model integrates sustainable manufacturing and CE practices for manufacturing of a generic product. This paper decomposes the product EoL phase of that life cycle model and delves deeper to highlight opportunities for enabling CE in the context of closing material flow loops.
3.1 Life cycle thinking for sustainable manufacturing
NIST work towards sustainable manufacturing resulted in standards for representing manufacturing processes and set a vision for using those standards to both reduce process impacts through data collection and continuous improvement and to subsequently build a framework for measuring the environmental impacts of manufacturing (Mani et al., 2016; Brundage et al., 2018a). Subsequent efforts made strides for building on the resulting digital standards (ASTM E3012) to generate data suitable for life cycle inventories to be used in life cycle assessments; more research is needed in this regard (ASTM International, 2016; Kulkarni et al., 2019; Bernstein et al., 2019; Brundage et al., 2018b; Komoto et al., 2020).
Life cycle thinking underpins the need to facilitate the exchange of information between various product life cycle phases with the understanding that product developers may be able to use this information to develop less environmentally impactful products. The challenge then lies in identifying what this information is and prioritizing these information exchanges to implement practices that are most beneficial. Well-defined manufacturing process taxonomies and classifications support modeling of manufacturing processes to shed further light on the sustainability performance for use in manufacturing planning (Lu et al., 2016). Information needed from manufacturing production activities to help address life cycle impacts and material recovery includes.
• physical resource, emissions, and material flows between processes, and
• resource needs and consumption patterns for particular processes (i.e., lubricants, tooling, water, and others)
• material composition and recovery guidance for output products.
To better understand the complexity of information needs for a CE, we developed a similar model of the broader product manufacturing life cycle using the IDEF0 technique. The IDEF0 modeling approach provides a framework for defining the activities and flows necessary to accomplish a complex undertaking, in terms of physical as well as information flows and at varying levels of complexity. This is a consequence of IDEF0 possessing a standardized syntax thus making the models well-defined and easy to understand. The IDEF0 models are well-structured and can provide significant via detailed model decompositions. Due to their scalability, flexibility and adaptability are used to model and analyze complex systems and enterprise operations (Waissi et al., 2015). The resulting model in this study has been developed to help guide and integrate evolving standards and needs specifically for new practices to pursue CE objectives, i.e., objectives that require systems thinking.
3.2 IDEF0
IDEF0 is a functional, or activity, modeling language used primarily to model decisions, actions, and activities within complex systems. The model comprises several basic units. Each unit is composed of five elements, namely, an activity, inputs, outputs, controls, and mechanisms (See Figure 2) [ISO, 2012; Reslan et al., 2022]. An activity represents a function that is being modeled in the IDEF0 diagram. An input is a flow that gets modified by the activity while an output is the resulting flow acted upon by the activity. Mechanisms are the means to complete the given activity and controls define the conditions required to ensure that the corrected output gets generated.
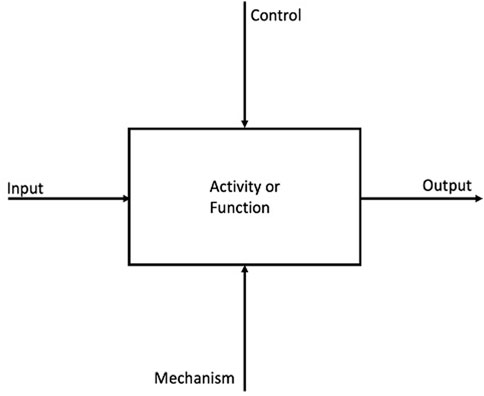
FIGURE 2. The IDEF0 schematic [adapted from Reslan et al., 2022].
These model units can be further decomposed into more detailed units and represent the hierarchy of activities within a system. The decomposed diagrams, referred to as child diagrams, are labeled as A nx where n is the label of the parent and x is a sequential numbering at the child level of decomposition. Thus, in summary the IDEF0 standard enables modeling of complex activities and provides users with a structured graphical form to analyze entire systems. This in turn can serve as a communication tool to support decision-making across an organization.
On reviewing the literature IDEF0 modeling method has been applied to and discussed in a wide variety of contexts, including sustainable manufacturing. In addition to the use of the technique as discussed above for a high-level view of the design-to-manufacturing system view, IDEF0 was used in past studies to highlight the advantages of an integrated model approach for optimizing energy and material efficiencies during manufacturing (Harun and Cheng, 2011; Smith and Ball, 2012; Meteyer et al., 2014; Harun et al., 2019). Eldessouky et al. (2009) present an IDEF0 framework for reverse engineering products to manufacture spare parts. IDEF0 has also been used specifically to analyze redistributed manufacturing for the production of shoes (Moreno et al., 2017). Zhang et al. (2011) introduced the use of IDEF0 in the context of designing a sustainable Product Service System (PSS). Wang et al. (2011) applied IDEF0 to EoL vehicle infrastructure to analyze the current recovery infrastructure and evaluate future alternatives.
In the context of product recovery, Sarigecili et al. (2013) developed an IDEF0 activity model for EoL activities for manufactured products with the intention of helping businesses integrate sustainability practices. Um et al. (2008) demonstrate the use of a product recovery management system developed in IDEF0 to model the management of byproducts and EoL material generated by a construction company. Similarly, the IDEF0 framework proposed by Errington and Childe (2013) focuses simply on the inspection activity during remanufacturing. Ziout et al. (2014) presented a top-level IDEF0 model for EoL product recovery for fuel cells and demonstrated the complexities involved in determining a product’s EoL fate while considering the collective interests of a multitude of stakeholders. Consistently, the literature reviewed highlighted the lack of standardized terminology and varying interpretations of definitions used in the context of product recovery [Um et al., 2008; Eldessouky et al., 2009; Wang et al., 2011; Sarigecili et al., 2013; Ziout et al., 2014]. Although this literature has pointed to product recovery IDEF0 models that may contribute to sustainable development, the NIST work by Reslan et al. (2022) was the only study found which specifically developed a model to address CE implications.
The study has contributed in the following ways:
1) It has addressed the identified gap in the literature by providing a detailed and systematic representation of the product recovery process for a generic product by building upon the previously developed activity model (Reslan et al., 2022), through the decomposition of the EoL product life cycle phase in the context of a CE.
2) It has identified potential measurement science opportunities with respect to mitigating inconsistencies relative to waste reporting, inconsistencies in waste terminology and classification, and the lacunae in data requirements from the proposed activity model.
The proposed model is a highly detailed depiction of the activities including their inputs, outputs, mechanisms and controls, and interactions with the other activities of the product recovery process. It provides a rich representation of business, environmental and societal concerns, and has the potential to be a basis towards building up waste mitigation frameworks and strategies.
4 Results: The extended manufacturing CE IDEF0 model for material recovery
The following section presents a reference model for material recovery within a manufacturing CE IDEF0 (Figure 3) to provide an overview of current efforts with respect to CE-promoting standards. This framework builds upon past work by Reslan et al. (2022) towards a manufacturing CE model. Sub-sections 4.1, 4.2 and 4.3 describe each of the decomposed sub-functions in greater detail.
4.1 Activities A-0 & A-n
The manufacturing CE model, Production in a CE (A0) is a framework for specifying the integration of circular business practices throughout common manufacturing practices (Figure 3). The decomposition of A0 (into child diagrams) is presented in Figure 4 (Reslan et al., 2022). Taking a product life cycle perspective, the major sub-functions, A-n of A0 are Design Product (A1), Acquire Materials (A2), Produce Product (A3), Use and Consume (A4) and Treat at EoL (A5). Product manufacturing comprises the product design (A1) phase driven essentially by prevalent market gaps or requirements. Once the product has been designed, the requisite materials are sourced (A2) and the product is produced as a result of transformative manufacturing processes (A3). The finished product is then distributed for use and consumption (A4). Traditionally, after it has fulfilled its primary functionality and reached its end of life, the product is discarded by the user, where it undergoes Treatment at EoL (A5). This later function or activity is being transformed by the movement towards a CE to bring the products and/or their constituent materials back into the economy. Figure 4 adapted from Reslan et al. (2022) illustrates the inputs and outputs from one life cycle stage to the next, in addition to mechanisms that facilitate activities at each stage given the controls.
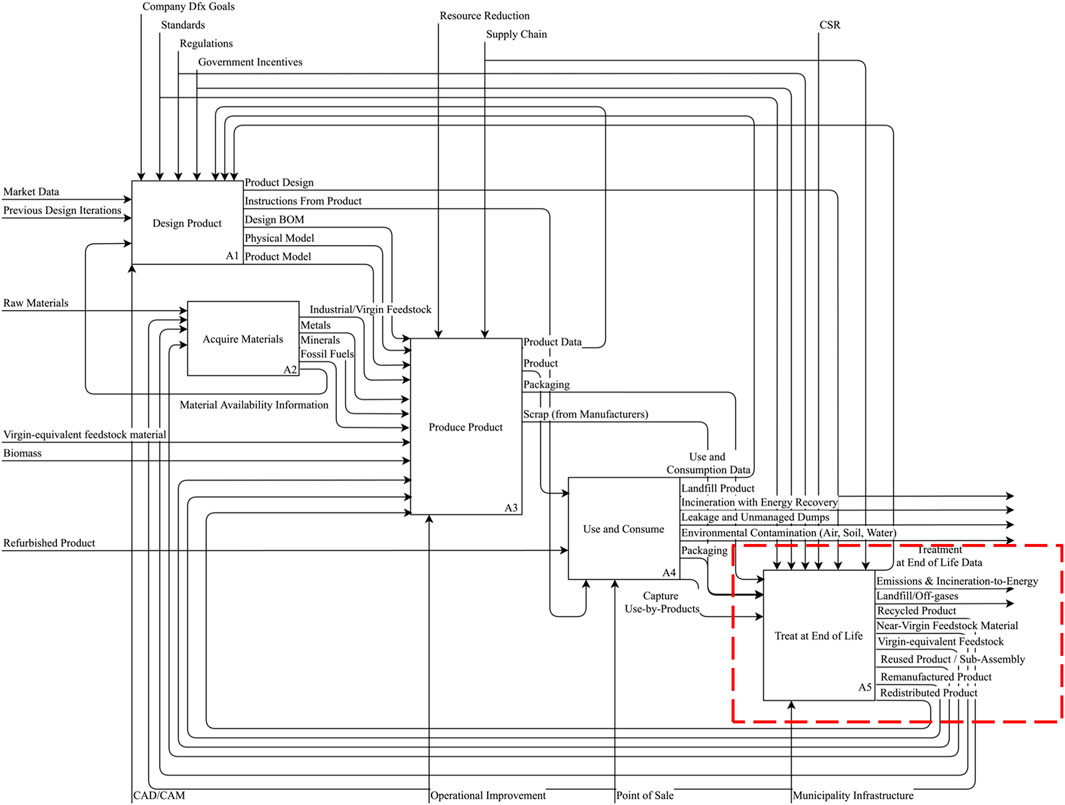
FIGURE 4. A0 manufacturing-based CE IDEF0 function comprising sub-functions A1, A2, A3, A4 & A5 (see Figure 1). The sub-function, A5 i.e., Treat at End of Life phase is highlighted.
Unlike a traditional linear economy, the CE paradigm promotes the notion of the waste hierarchy (See Figure 5) to close material flow loops and thereby aims to decouple economic growth from resource consumption (Mathur et al., 2019). The principle of the waste hierarchy is not new and prioritizes reduction, reuse and recycling over incineration and disposal in landfills. Thus, within a CE paradigm, the waste hierarchy has the potential to facilitate decision-making to minimize the EoL products and materials being discarded in landfills and enable conservation of resources through the creation of secondary material sources via reuse, remanufacture and recycling. The stratified approach that the waste hierarchy takes, can help overcome the lack of clarity by providing a holistic view of waste management practices if various terminology and indices are adequately defined (Pires & Martinho, 2019).
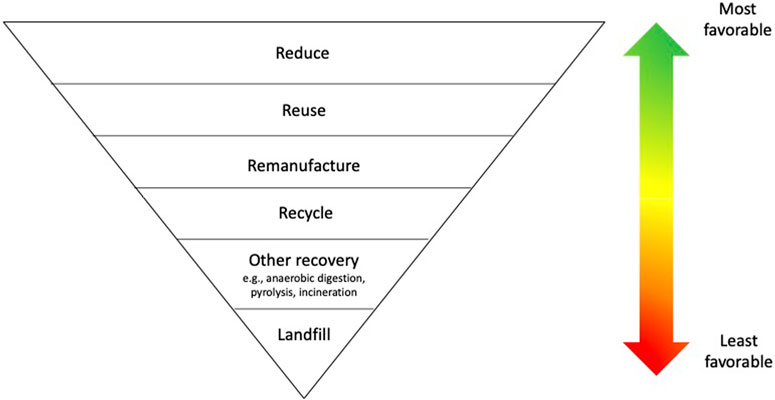
FIGURE 5. The waste hierarchy (Adapted from the EU Waste Framework Directive 2008/98/EC & Mathur et al., 2019).
The overall degree of product and material recovery is facilitated by corporate will, personnel expertise, and existing EoL recovery infrastructure. The degree of recovery and thus, of CE, is limited by the lack of effective regulations, incentives, market demand for secondary materials and unified associated standards. Another big limitation is the suitability of recovered material since procedures around quality control, contamination levels and the technical inability to process discarded material into reusable forms remains challenging. Further, the extent of product recovery often is a direct consequence of decisions taken at the early phases of product design (A1) and, therefore, information related to product treatment feasibility and options at the EoL must feed back into the product design phase for future considerations and improvements.
The proposed IDEF0 manufacturing CE framework is particularly important in creating a mechanism where early design decisions are facilitated based on accurate information flows from the other phases of a product’s life cycle (A2 through A5). Using the top-level IDEF0 function (A0) and the derived sub-functions (A-n) (Figure 4), the following subsections build upon the notion of extending CE by closing material flow loops and the waste hierarchy.
4.2 Activity A5 treat at end of life
To understand the interrelationships between activities that specifically drive material recovery, the node A5, Treatment at EoL in the child diagram in Figure 4 is decomposed further into subsequent lower-level diagrams. This decomposition is instrumental in providing a more exhaustive understanding of the inter-related elements at product EoL. Figure 6 presents the child diagram of sub-function A5, Treatment at EoL decomposed into three activities, namely, Collect end-of-life products (A51), Clean/separate/sort products (A52), and Treat end-of-life products (A53).
Once products have fulfilled their primary functions within the use phase of a product’s life cycle (A4), the resulting EoL products need to be collected, often over regions spanning vast areas and transported to central processing units for further processing. Unutilized material in the form of byproducts and scrap that are generated at the A3 Produce Product phase of a product’s life cycle also need to be addressed and, therefore, feed into A51 and A52 for recovery. The node A51 Collect EoL products, in Figure 6 represents EoL product collection and feeds into the node A52 Clean/separate/sort products. The collected and segregated material subsequently feeds into A53 Treat end-of-life products where it is treated in accordance with the principle of waste hierarchy for recovery (reuse, remanufacture, recycling and energy recovery). It should be noted that depending on the type and composition of a product and the maturity of recovery related interventions, the product may not necessarily undergo each of the recovery steps in the waste hierarchy. For instance, a product may be dismantled and some components directly reused, not undergo remanufacturing, but undergo recycling and subsequent landfilling.
Even the most common consumer products can be extremely complex in that they comprise numerous components, sub-assemblies, and assemblies. Further, often a combination of different materials is used to fabricate these products. Collected EoL products, therefore, need to be pre-treated and are dismantled, sorted, and cleaned. This is an important step in material recovery as material cross-contamination can result in unnecessary material losses as the product undergoes subsequent processing in A53 Treat end-of-life products. As a result of product complexity owing to design and materials used, A5 needs to be supported by robust infrastructure, and adequate expertise through skilled personnel. These factors have been identified as mechanisms for A51, A52 and A53. Similarly, the controls associated with A51, A52 and A53 are regulations, and the waste hierarchy classifies EoL treatment across a range of alternatives. Therefore, the A53 Treat end-of-life products activity is further decomposed in close alignment with the principles of the waste hierarchy (See Figure 7). Cleaned, separated, and sorted EoL product components and products may be directly reused (A531) in manufacturing an altogether new product if they are deemed fit upon inspection. Often however, as a consequence of use and/or mechanical disassembly methods (A532) at EoL, components and sub-assemblies may suffer some degradation or damage.
Fit products may be reintroduced into the economy through remanufacturing (A533). Remanufacturing entails repairing part of a product in combination with possibly adding new parts (often fabricated using virgin resources from A2) or repairing/maintaining existing parts to rebuild the product to its original specifications (Ijomah et al., 1999; Sundin & Bras, 2005; Sundin & Lee, 2012; Ortegon et al., 2013). Products and product components that can neither be reused nor remanufactured are processed further through recycling (A534). Unfortunately, owing to the inevitable cross-contamination and complexities associated with recycling processes, losses do occur. These losses can be in the form of material losses and/or emissions. In the case of material losses, the residues resulting from recovery processes (reuse, remanufacturing, and recycling) may be incinerated (A534) for energy and/or simply landfilled (A535). On the other hand, carbon capture and sequestration may be employed to mitigate impacts as a result of landfilling discarded materials (Brigagão et al., 2021). Careful evaluation of trade-offs for EoL treatments need to be undertaken to facilitate the most appropriate EoL pathway. Once again, the mechanisms to facilitate the functions at the A-nnn level include adequate infrastructure and expertise. The controls are regulations, standards, and governmental incentives, in further addition to initial product design.
4.3 Activity A53 Treat end of life products
Activity A53 Treat EoL products is further decomposed. The Reuse activity, A531, is the most favorable of recovery scenarios as it avoids the manufacture of an altogether new product thereby resulting in resource savings and avoided environmental impacts (Figure 8). Reuse entails collected and sorted used products simply being inspected, replaced, and reassembled, and evaluated for fitness before reentering the market. Reuse, in essence, can be considered a perfect closed loop. Products that are found to have undergone degradation and are not fit for direct reuse are subsequently disassembled into sub-assemblies and components. Unacceptable products that cannot be reused are mechanically separated, sorted, and isolated and are subsequently tested for integrity and graded. Acceptable sub-assemblies and/or components are fed back into the economy for reuse. Those deemed unacceptable for direct reuse are consequently considered for remanufacturing.
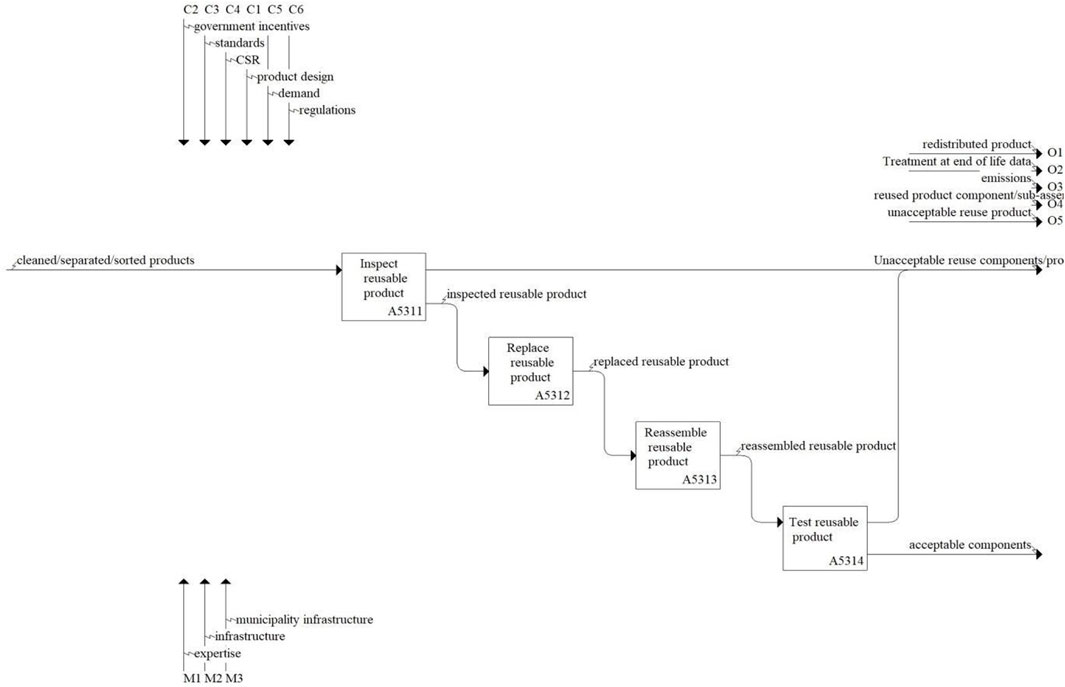
FIGURE 8. A531 Reuse phase in the context of a manufacturing CE IDEF0 model (the controls and mechanisms remain consistent across all the sub-activities under A531).
The inputs from the disassembly phase (Figure 9), i.e., disassembled product components and sub-assemblies are now inspected and depending on their level of degradation they are remanufactured (Figure 10) using virgin raw material inputs. Once tested, the acceptable parts are introduced into the economy and often marketed as refurbished products. Those found unacceptable are subsequently recycled.
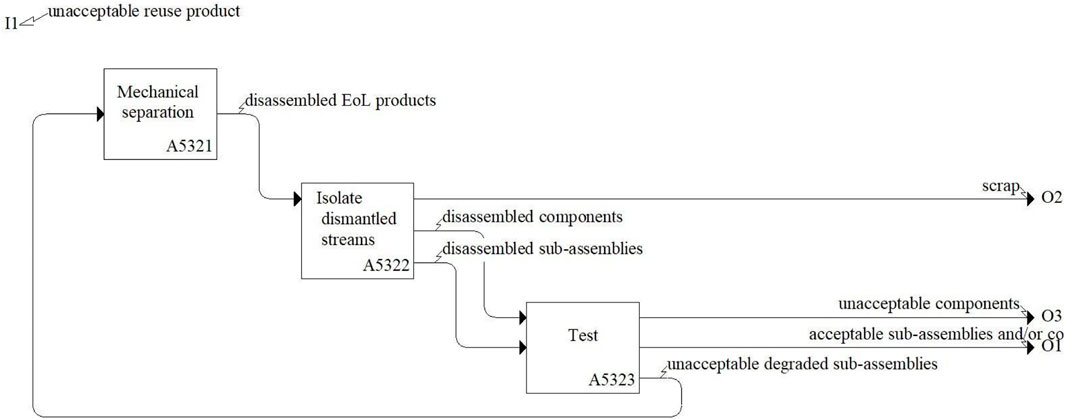
FIGURE 9. A532 Disassemble product phase in the context of a manufacturing CE IDEF0 model (the controls and mechanisms remain consistent across all the sub-activities under A532).
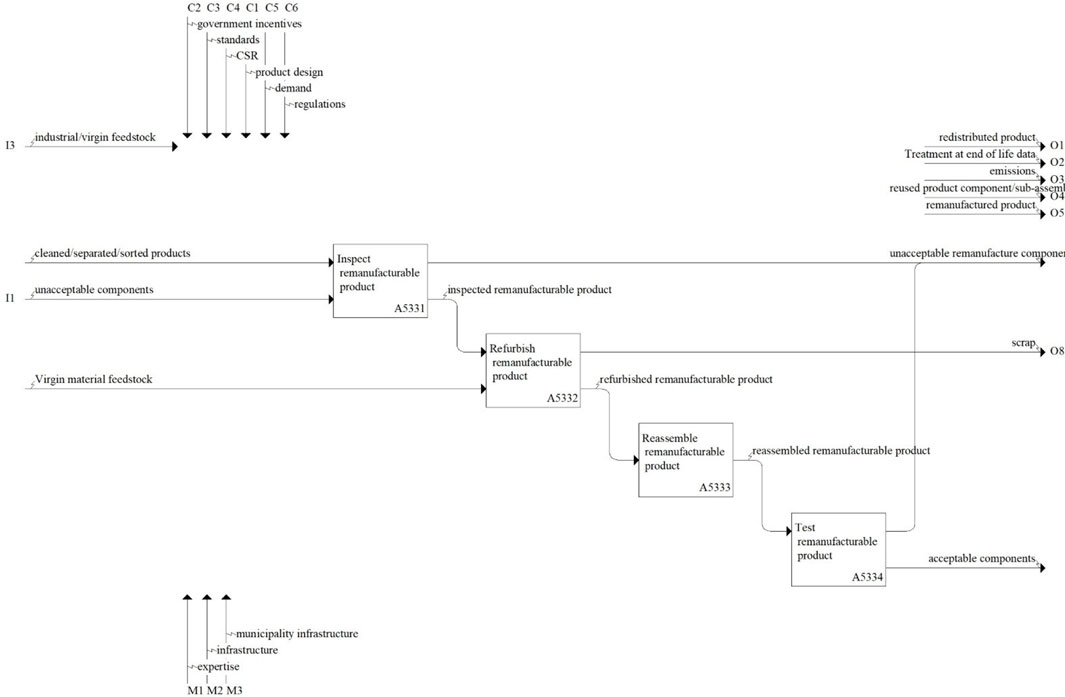
FIGURE 10. A533 Remanufacture phase in the context of a manufacturing CE IDEF0 model (the controls and mechanisms remain consistent across all the sub-activities under A533).
The Recycle node, A534 is decomposed further (See Figure 11) into Mechanical recycling (A5331) and Chemical recycling (A5332). The objective of recycling is to process recovered materials into feedstock of identical or similar material properties and quality as the virgin feedstock that can be reintroduced into the economy, thus closing material flow loops. Mechanical recycling is a less environmentally intensive process than chemical recycling as it usually comprises simply shredding or granulating the material. This is then reintroduced in the economy by combining it with virgin feedstock. Material streams can be difficult to recycle mechanically when contamination is a high concern. For instance, in the case of plastics chemical recycling may be undertaken. Unlike mechanical recycling, chemical recycling is a more resource intensive process as it does not preserve the molecular structure of the material. Chemical recycling usually comprises a series of chemical reactions and can result in the generation of byproducts that may need to be further recycled (Beers et al., 2022).
The principle of waste hierarchy enables the closing of material flow loops by providing a framework to identify the tightest loops—those which result in the least material losses—and thereby contributes towards planning for a CE. However, as mentioned earlier, product complexity and poor design leads to difficulties in isolating material streams and can contribute to EoL products being incinerated (A535) for energy recovery. Alternatively, if incineration is not feasible, disposal through landfilling (A536) is the only alternative. Both incineration and landfilling are least favorable EoL treatment alternatives but have been the most widely implemented alternatives in the past as a direct consequence of the traditional linear economy model. Incineration and landfilling can result in a loss of resources that could potentially be recovered as our recovery infrastructure matures.
5 Key takeaways from the EoL activity model and identified standards needs
The uncertainties associated with establishing product recovery and closing material loops need to be addressed in order to operationalize the proposed model. One way is via the development of effective standards. The preceding section describes the activities at the product end of life phase in the context of a manufacturing CE framework. Like the design, material acquisition and production phases, the product EoL phase can be extremely complex in the context of closing material flow loops. The EoL framework presented is aligned with the principle of waste and material management and aims to help prioritize treatment of products and materials at their EoL. Effective material recovery strategies have thus far been hindered by a lack of adequate recovery infrastructure, technological challenges, a lack of skills, and a society’s inability to respond from a systems perspective. Often policy setting practices are more reactionary in addressing immediate problems than anticipatory of emerging problems. A shift in perspective is needed to address global issues such as waste management and climate change. Sustainable development goals promote the shift from a remedial approach to a preemptive approach which will enable businesses and communities to transition in an orderly way. An incremental transition will enable adaptive and more resilient response to environmental (e.g., pollution), societal (e.g., job losses) and economic (e.g., brittle supply chains) situational disruptions. EoL material recovery has the potential of reshaping the current business ecosystem. The creation of secondary sources of industrial feedstock can reduce our dependence on virgin resources, benefit society and mitigate supply chain risks.
We analyzed the information flows in the IDEF0 model. In Table 2 we broadly identify the areas where standards will be required. First and foremost, standardization of terminology is required for clear communication. This can be achieved via a consensus-based approach by involving experts in industry, academia, government, and standard bodies. Research into developing appropriate metrics and guidelines is required. Developing standards to measure and compare key performance metrics for materials can eventually support closing material flow loops and thereby creation of secondary material flows to support a CE. Such standards will be needed for the broad range of material types. Foundational standards may help to facilitate uniformity and completeness across the more specialized standards.
The implications of establishing CE standards on material recovery can be far reaching. These implications have been summarized below and cover a few broad areas where the development of standards will be particularly helpful:
5.1 Consumer decision-making
Once a product has reached the end of use, the consumer must determine how it should be discarded. Consumers may sell or donate products that are functional, but those that do not need to be disposed of, and for many product categories (e.g., electronics, textiles) consumers remain unaware on the suitable disposal method. Regional inconsistencies in recycling infrastructure result in confusion around even more common categories, such as plastics, paper, and glass. Data to support consumer decision-making can help strengthen overall collection numbers, which in turn can drive the creation of a secondary materials marketplace. Collection and sorting data is also essential in helping waste handlers (municipal workers, recyclers, or manufacturers with take back programs) to effectively segregate material streams once EoL products are collected. Labels and markings on products is one way of handling EoL product collection and preventing cross-contamination.
5.2 Material traceability, collection, dismantling and segregation, and recovery
The collection of EoL products is a big challenge currently hindered by lack of knowledge of product compositions, poorly labeled products and components, and a lack of know-how on safe dismantling techniques both in terms of insight into the product design and technological and skill-related barriers. Data needs to be transmitted effectively to EoL practitioners to enable efficient handling, which in turn will drive more efficient segregation of material streams. This is an important step in preventing cross-contamination and unnecessary losses. Besides environmental losses, material contamination can contribute to the overall decrease in the economic value of the materials. Clear and concise data on material and product compositions, in addition to their economic values can enable better sorting.
5.3 Secondary feedstock testing and durability
EoL products need to be evaluated for fitness to determine the best method of handling. This will require the development of testing methods and criteria to facilitate product reuse and remanufacturing where possible. The intrinsic integrity of components and/or materials can be impacted by the recovery process it undergoes. Also, the degradation experienced during its use phase can impact what components are reusable versus other recovery means. Standardized specifications for recovered materials along with standard methods and tools to test them will serve to overcome barriers discussed earlier. Information flows that effectively communicate recovered product components, material compositions, and other properties are needed.
5.4 Material losses, “waste” to landfills
Residual losses are an inevitable part of the manufacturing process and information on the quantities, composition and quality of such losses can be valuable to facilitate both closed-loop and open-loop (via industrial synergies) recovery processes. Residual losses are inevitable also at the EoL product recovery phase. Informational flows characterizing these losses in terms of quantity and quality are essential to determining the effective EoL processing treatment. This information is also critical for future product design practices in terms of planning for EoL of the product. It will support design for the environment, better material and process efficiencies, and strengthen supply chains through insights into future sources of feedstocks.
5.5 Net environmental footprints
Closing EoL material flow loops is instrumental for mitigating environmental impacts by diverting EoL products away from the landfill and through material recovery practices that help conserve resources, including those that are embodied. Embodied resources represent the total resources (materials, energy, others) used to manufacture a product, at every stage of its life from material extraction processes to EoL treatment and disposal processes. Standard methods and tools enable accurate quantification of net environmental impacts for products and product systems. The benefits of measuring product footprints across different environmental impact categories can enable effective comparisons between products and materials that can fulfill similar functions. Additionally, environmental quantification tools can help in the identification of ‘hot-spots’ that may lead to changes in design, material substitutions, and most efficient processing practices. Disaggregated information flows with details on inputs and outputs during manufacturing will facilitate the measurement of environmental impacts. This information will be necessary to develop standard practices for defining overall product impacts.
6 Current standards landscape
Standards can enable the realization of CE practices and in recent years the momentum around implementing CE practices has increased. While many standards exist to support CE objectives, The British Standards Institution (BSI) was the first to introduce a standard specifically addressing CE, BS 8001, in 2017. Since then, the European commission adopted the Circular Economy Action Plan (CEAP) in 2020. More recently, the International Organization for Standardization (ISO), ASTM-International and the European Commission for Standardization (CEN) have initiative activities to address CE principles (Reslan et al., 2022).
At the EoL phase, standards play an important role in defining disposal and treatment processes, quality and contamination criteria, storage, handling, and transportation criteria. Currently, as pointed out in preceding sections these standards lack harmonized clarity on several levels. This ranges from poorly defined terminology to a lack of adequate metrics to measure and classify EoL waste streams. Further, several stakeholders are involved in facilitating closed-loop recovery and CE, thus identifying, and engaging the breadth of stakeholders is also very important.
In the context of sustainable development, three main categories of standards can be instrumental in supporting manufacturers transition to a CE (Figure 12). Shared goals such as the United Nations Sustainable Development Goals (UNSDGs) (Desa, 2016), Green House Gas (GHG) protocols (World Resources InstituteWorld Business Council for Sustainable Development, 2004), and the Sustainability Standards Accounting Board (SASB) (SASB, 2018) standards set a direction for what needs to be done. Management standards promote good practices in a manufacturing environment and are instrumental in improving overall sustainability performance. Management standards such as the ISO management standards and the CEN-CENELEC Joint Technical Committee (IEC, 2019) have contributed towards improving material and energy utilization in manufacturing firms. Measurement standards such as those from ASTM International E60.13 on Sustainable Manufacturing enable the fulfillment of other categories by specifying means for implementing processes to demonstrate progress through continuous improvement in performance of processes and practices. Many more standards in the measurement category will be needed to add clarity to things such as material quality and traceability.
Standards related specifically to CE remain nascent and will need to build on sustainability goals, management standards and measurement standards. CE takes into consideration the entire product life cycle. The ISO 323 Technical Committee on CE was established in 2019 and is responsible for developing foundational standards on CE. Figure 13 provides an overview of the ISO TC 323, its five working groups and their respective scopes.
7 Summary and conclusions
This paper provides an overview of the current global waste crisis and examines the CE paradigm in the context of the manufacturing sector. The paper highlights the various barriers associated with closing material flow loops that in turn could facilitate CE practices. The lack of standards associated with EoL products is one such barrier and limits effective tracing, collection, sorting, and segregation of EoL products, and subsequent recovery of EoL products. Furthermore, quality, contamination and material durability issues also need to be addressed via appropriate measurement standards. The authors of this paper have represented the EoL product phase using the waste hierarchy via an IDEF0 model that has been decomposed to four levels. Based on this, the main barriers to implementing CE practices at the EoL and also information and feedback flows that could drive standards development have been identified.
One shortcoming of this study is the lack of a demonstrated case study. Future work may involve the analysis of a product or product family with respect to the waste hierarchy and the identification of product-specific metrics and standards’ needs. At the same time, it should be noted that although the RMH has in the past influenced many developed countries as a guide for waste management, it does have its limitations [Dijkgraaf and Vollebergh, 2004; Van Ewijk & Stegemann, 2016]. For one thing, the application of the RMH in the context of dematerialization has not been studied conclusively. Van Ewijk and Stegemann, 2016 identified a few limitations of the waste hierarchy. For instance, the waste hierarchy fails to provide guidance regarding choosing the suitable level within the hierarchy. It lacks methods to adequately distinguish between open and closed loop recovery, and it fails to make a connection between waste management and other industry sectors. Thus, it overlooks the possibility of creating secondary markets for a diverse set of sectors. Furthermore, the waste hierarchy in its current form fails to address absolute reductions in material throughput due to a lack of rigor that could facilitate establishing clear guidelines or policies (Van Ewijk and Stegemann, 2016). Thus, future work should involve developing and integrating a value-based approach to the hierarchy. The development of standards may be one avenue by which to target more stringent measures for dematerialization within a larger resource-use framework.
This study also highlights the importance of creating reliable data sources. There is potential for future work on developing and maintaining data repositories, particularly those focused on manufacturing unit processes that consider associated uncertainties. Past work has cited the importance of information marketplaces as not just sources of reliable data but also a means of recognizing the value of collected data sets (Lawrenze et al., 2021). Product EoL information and potential recovery strategies along with secondary material properties is essential to validate and consequently facilitate the creation of secondary feedstocks. Information marketplaces can have great potential in the context of enabling a CE since they have the ability to address the information gaps and enable information exchange between the multiple stakeholders (Lawrenze et al., 2021). Also, it has been observed that information can be lost over time, especially when products change ownership, and further work needs to be carried out to accurate differentiate, collect, and maintain dynamical and static information (Kintscher et al., 2020; Lawrenze et al., 2021).
Data availability statement
The original contributions presented in the study are included in the article/Supplementary Material, further inquiries can be directed to the corresponding author.
Author contributions
Conception and design of study: NM; Acquisition of data: NM and NL; Analysis and interpretation of data: NM, NL, and KM; Drafting the manuscript: NM, NL, and KM.
Acknowledgments
The authors would like to thank the reviewers for their feedback that significantly helped improve this manuscript.
Conflict of interest
The authors declare that the research was conducted in the absence of any commercial or financial relationships that could be construed as a potential conflict of interest.
Publisher’s note
All claims expressed in this article are solely those of the authors and do not necessarily represent those of their affiliated organizations, or those of the publisher, the editors and the reviewers. Any product that may be evaluated in this article, or claim that may be made by its manufacturer, is not guaranteed or endorsed by the publisher.
Supplementary material
The Supplementary Material for this article can be found online at: https://www.frontiersin.org/articles/10.3389/fmtec.2023.988073/full#supplementary-material
References
Ahirwar, R., and Tripathi, A. K. (2021). E-Waste management: A review of recycling process, environmental and occupational health hazards, and potential solutions. Environ. Nanotechnol. Monit. Manag. 15, 100409. doi:10.1016/j.enmm.2020.100409
Akram, R., Fahad, S., Hashmi, M. Z., Wahid, A., Adnan, M., Mubeen, M., et al. (2019). Trends of electronic waste pollution and its impact on the global environment and ecosystem. Environ. Sci. Pollut. Res. 26 (17), 16923–16938. doi:10.1007/s11356-019-04998-2
Aparcana, S. (2017). Approaches to formalization of the informal waste sector into municipal solid waste management systems in low- and middle-income countries: Review of barriers and success factors. Waste Manag. 61, 593–607. doi:10.1016/j.wasman.2016.12.028
Arnold, S. M., Holland, F. A., Bednarcyk, B. A., and Pineda, E. J. (2015). Combining material and model pedigree is foundational to making ICME a reality. Integr. Mater Manuf. Innov. 4, 37–62. doi:10.1186/s40192-015-0031-2
ASTM International (2016). Standard guide for characterizing environmental aspects of manufacturing processes. Available at: https://www.astm.org/e3012-16.html.doi:10.1520/E3012-16
Awan, U., Sroufe, R., and Shahbaz, M. (2021). Industry 4.0 and the circular economy: A literature review and recommendations for future research. Bus. Strategy Environ. 30, 2038–2060. doi:10.1002/bse.2731
Barkmeyer, E., Christopher, N., Feng, S., Fowler, J., Frechette, S., Jones, A., et al. (1987). SIMA reference architecture Part I: Activity models, NIST interagency/internal report (NISTIR). Gaithersburg, MD: National Institute of Standards and Technology. [online]. Available at: https://tsapps.nist.gov/publication/get_pdf.cfm?pub_id=821013. doi:10.6028/NIST.IR.5939Accessed July 5, 2022)
Beers, K., Schumacher, K., Migler, K., Morris, K. C., and Kneifel, J. (2022). An assessment of mass balance accounting methods for polymers workshop report, 1500. Gaithersburg, MD: NIST Special Publication, 206. doi:10.6028/NIST.SP.1500-206
Bernstein, W. Z., Tamayo, C. D., Lechevalier, D., and Brundage, M. P. (2019). Incorporating unit manufacturing process models into life cycle assessment workflows. Procedia CIRP 80, 364–369. doi:10.1016/j.procir.2019.01.019
Brigagão, G. V., de Medeiros, J. L., Ofélia de Queiroz, F. A., Mikulčić, H., and Duić, N. (2021). A zero-emission sustainable landfill-gas-to-wire oxyfuel process: Bioenergy with carbon capture and sequestration. Renew. Sustain. Energy Rev. 138, 110686. doi:10.1016/j.rser.2020.110686
Brundage, M., Bernstein, W., Kliks, T., Nishi, H., Hoffenson, S., Chang, Q., and Morris, K. (2018a). Analyzing environmental sustainability methods for use earlier in the product lifecycle. J. Clean. Prod. 187, 877–892. [online]. doi:10.1016/j.jclepro.2018.03.187
Brundage, M., Lechevalier, D., and Morris, K. (2018b). Toward standards-based generation of reusable life cycle inventory data models for manufacturing processes. ASME J. Manuf. Sci. Eng. 141. doi:10.1115/1.4041947
Cagno, E., Neri, A., Negri, M., Bassani, C. A., and Lampertico, T. (2021). The role of digital technologies in operationalizing the circular economy transition: A systematic literature review. Appl. Sci. 11 (8), 3328. doi:10.3390/app11083328
Chen, D. M. C., Bodirsky, B. L., Krueger, T., Mishra, A., and Popp, A. (2020). The world’s growing municipal solid waste: Trends and impacts. Environ. Res. Lett. 15 (7), 074021. doi:10.1088/1748-9326/ab8659
Christopher, N., Feng, S. C., Fowler, J. E., Frechette, S. P., Jones, A., Jurrens, K., et al. (1996). SIMA reference architecture Part 1: Activity models. 5939, Gaithersburg, Maryland, USA: National Institute of Standards and Technology. NISTIR.
Darby, L., and Obara, L. (2005). Household recycling behaviour and attitudes towards the disposal of small electrical and electronic equipment. Resour. Conservation Recycl. 44 (1), 17–35. doi:10.1016/j.resconrec.2004.09.002
Desa, U. N. (2016). Transforming our world: The 2030 agenda for sustainable development. dos Muchangos.
Dijkgraaf, E., and Vollebergh, H. R. (2004). Burn or bury? A social cost comparison of final waste disposal methods. Ecol. Econ. 50 (3–4), 233–247.
dos Muchangos, L. S., Tokai, A., and Hanashima, A. (2015). Analyzing the structure of barriers to municipal solid waste management policy planning in Maputo city, Mozambique. Environ. Dev. 16, 76–89. doi:10.1016/j.envdev.2015.07.002
Eldessouky, H. M., El-Kilany, K. S., and Rashed, O. A. (2009). Structured analysis methodology for reverse engineering of spare parts. PEDAC.
Ellen MacArthur Foundation (2022). Circular economy. Available at: https://ellenmacarthurfoundation.org/topics/circular-economy-introduction/overview.
Errington, M., and Childe, S. J. (2013). A business process model of inspection in remanufacturing. J. Remanufacturing 3 (1), 7–22. doi:10.1186/2210-4690-3-7
Eurostat (2021). Waste statistics. Available at: https://ec.europa.eu/eurostat/statistics-explained/index.php?title=Waste_statistics#Total_waste_generation.
Faraca, G., and Astrup, T. (2019). Plastic waste from recycling centres: Characterisation and evaluation of plastic recyclability. Waste Manag. 95, 388–398. doi:10.1016/j.wasman.2019.06.038
Ferronato, N., and Torretta, V. (2019). Waste mismanagement in developing countries: A review of global issues. Int. J. Environ. Res. Public Health 16 (6), 1060. doi:10.3390/ijerph16061060
Franzo, S., Urbinati, A., Chiaroni, D., and Chiesa, V. (2021). Unravelling the design process of business models from linear to circular: An empirical investigation. Bus. Strategy Environ. 30 (6), 2758–2772. doi:10.1002/bse.2892
Government of Japan Ministry of Environment (2018). Fundamental plan for establishing a sound material-cycle society. Available at: https://www.env.go.jp/en/recycle/smcs/4th-f_Plan.pdf.
Gusmão Gomes de Andrade Lima, D., Lee Barbosa Firmo, A., Lopes Lucena, L., Odete Holanda Mariano, M., Fernando Thomé Jucá, J., and Dantas Lima, J. (2016). Solid waste management in Brazil: An analysis of public policies under European and USA laws. doi:10.13140/2.1.4970.8801
Han, H., and Zhang, Z. (2017). The impact of the policy of municipal solid waste source-separated collection on waste reduction: A case study of China. J. Mater. Cycles Waste Manag. 19, 382–393.
Harun, K., and Cheng, K. (2011). “Life Cycle Simulation (LCS) approach to the manufacturing process design for sustainable manufacturing,” in 2011 IEEE international symposium on assembly and manufacturing (ISAM), 1–8. doi:10.1109/ISAM.2011.5942370
Harun, K., Moin, I., Suffian, H., Abd Rahman, N., Ghafar, N. H., and Mohamed, F. (2019). An integrated approach towards sustainable manufacturing–A framework. Adv. Transp. Logist. Res. 2, 340–348.
Heller, M. C., Mazor, M. H., and Keoleian, G. A. (2020). Plastics in the US: Toward a material flow characterization of production, markets and end of life. Environ. Res. Lett. 15 (9), 094034. doi:10.1088/1748-9326/ab9e1e
Hofmann, F. (2019). Circular business models: Business approach as driver or obstructer of sustainability transitions? J. Clean. Prod. 224, 361–374. doi:10.1016/j.jclepro.2019.03.115
Hoornweg, D., and Bhada-Tata, P. (2012). What a waste: A global review of solid waste management. Urban development series; knowledge papers no. 15. Washington, DC: World Bank. © World Bank. Available at: https://openknowledge.worldbank.org/handle/10986/17388 License: CC BY 3.0 IGO.
IEC (2019). European standards for a circular economy | IEC. Technical Report. Available at: https://www.iec.ch/blog/.european-standards-circular-economy.
Ijomah, W. L., Bennett, J. P., and Pearce, J. (1999). “Remanufacturing: Evidence of environmentally conscious business practice in the UK,” in Proceedings first international symposium on environmentally conscious design and inverse manufacturing, 192–196. doi:10.1109/ECODIM.1999.747607
Ilankoon, I. M. S. K., Ghorbani, Y., Chong, M. N., Herath, G., Moyo, T., and Petersen, J. (2018). E-waste in the international context - a review of trade flows, regulations, hazards, waste management strategies and technologies for value recovery. Waste Manag. 82, 258–275. doi:10.1016/j.wasman.2018.10.018
Ingemarsdotter, E., Jamsin, E., Kortuem, G., and Balkenende, R. (2019). Circular strategies enabled by the internet of things—a framework and analysis of current practice. Sustainability 11 (20), 5689. doi:10.3390/su11205689
International Standards Organization (2012). I eInformation technology — modeling languages — Part 1: Syntax and semantics for IDEF0. Available at: https://www.iso.org/obp/ui/#iso:std:iso-iec-ieee:31320:-1:ed-1:v1:en.
Kalmykova, Y., Sadagopan, M., and Rosado, L. (2018). Circular economy–From review of theories and practices to development of implementation tools. Resour. conservation Recycl. 135, 190–201. doi:10.1016/j.resconrec.2017.10.034
Kaza, S., Yao, L., Bhada-Tata, P., and Van Woerden, F. (2018). What a waste 2.0: A global snapshot of solid waste management to 2050. Washington, DC. Available at: https://openknowledge.worldbank.org/handle/10986/30317.
Kerdlap, P., Low, J. S. C., and Ramakrishna, S. (2019). Zero waste manufacturing: A framework and review of technology, research, and implementation barriers for enabling a circular economy transition in Singapore. Resour. Conservation Recycl. 151, 104438. doi:10.1016/j.resconrec.2019.104438
Kintscher, L., Lawrenz, S., Poschmann, H., and Sharma, P. (2020). Recycling 4.0-digitalization as a key for the advanced circular economy. J. Commun. 15 (9), 652–660.
Komoto, H., Bernstein, W. Z., Kwon, S., and Kimura, F. (2020). Standardizing environmental performance evaluation of manufacturing systems through ISO 20140. Procedia CIRP 90, 528–533. doi:10.1016/j.procir.2020.02.043
Korhonen, J., Honkasalo, A., and Seppala, J. (2018). Circular economy: The concept and its limitations. Ecol. Econ. 143, 37–46. doi:10.1016/j.ecolecon.2017.06.041
Kristoffersen, E., Blomsma, F., Mikalef, P., and Li, J. Y. (2020). The smart circular economy: A digital-enabled circular strategies framework for manufacturing companies. J. Bus. Res. 120, 241–261. doi:10.1016/j.jbusres.2020.07.044
Krones, J. S. (2016). “Accounting for non-hazardous industrial waste in the United States [PhD],” in Materials science and engineering (Massachusetts Institute of Technology).
Krones, J. S. (2017). Industrial symbiosis in the upper valley: A study of the casella-hypertherm recycling partnership. Sustain. Switz. 9 (5), 806. doi:10.3390/su9050806
Kulkarni, A., Bernstein, W. Z., Lechevalier, D., Balasubramanian, D., Denno, P., and Karsai, G. (2019). “Towards operational use of unit manufacturing process models,” in 2019 IEEE international conference on industrial technology (ICIT), 818–823. doi:10.1109/ICIT.2019.8754963
Lasi, H., Kemper, H. G., Fettke, P., Feld, T., and Hoffmann, M. (2014). Industry 4.0. Bus. Inf. Syst. Eng. 6, 239–242. doi:10.1007/s12599-014-0334-4
Lawrenz, S., Nippraschk, M., Wallat, P., Rausch, A., Goldmann, D., and Lohrengel, A. (2021). Is it all about Information? The role of the information gap between stakeholders in the context of the circular economy. Procedia CIRP 98, 364–369. doi:10.1016/j.procir.2021.01.118
Le Moigne, R. (2021). “Waste watchers,” in Ellen MacArthur foundation. Available at: https://ellenmacarthurfoundation.org/articles/waste-watchers.
Light House Society (2019). Washington industrial waste coordination (industrial symbiosis) program recommendations. International Synergies Ltd., & Center for Sustainable Infrastructure. Available at: www.lhsbc.com.
Liu, S., Bao, J., Lu, Y., Li, J., Lu, S., and Sun, X. (2021). Digital twin modeling method based on biomimicry for machining aerospace components. J. Manuf. Syst. 58, 180–195. doi:10.1016/j.jmsy.2020.04.014
Lu, Y., Morris, K. C., and Frechette, S. (2016). Current standards landscape for smart manufacturing systems. National Institute of Standards and Technology, 39. NISTIR, 8107.
Maani, T., Mathur, N., Singh, S., Rong, C., and Sutherland, J. W. (2021). Potential for Nd and Dy Recovery from end-of-life products to meet future electric vehicle demand in the US. Procedia CIRP 98, 109–114. doi:10.1016/j.procir.2021.01.014
Mani, M., Larborn, J., Johansson, B., Lyons, K. W., and Morris, K. C. (2016). Standard representations for sustainability characterization of industrial processes. J. Manuf. Sci. Eng. 138 (10). doi:10.1115/1.4033922
Mani, M., Madan, J., Lee, J. H., Lyons, K. W., and Gupta, S. K. (2013). Review on sustainability characterization for manufacturing processes. Gaithersburg, MD: National Institute of Standards and Technology, 7913. Report No. NISTIR.
Martínez, J. H., Romero, S., Ramasco, J. J., and Estrada, E. (2022). The world-wide waste web. Nat. Commun. 13 (1), 1615. doi:10.1038/s41467-022-28810-x
Matheson, T. (2022). Disposal is not free: Fiscal instruments to internalize the environmental costs of solid waste. Int. Tax Public Finance 29, 1047–1073. doi:10.1007/s10797-022-09741-1
Mathews, J., and Tan, H. (2016). Circular economy: Lessons from China. Nature 531, 440–442. doi:10.1038/531440a
Mathur, N., Deng, S., Singh, S., Yih, Y., and Sutherland, J. W. (2019). Evaluating the environmental benefits of implementing Industrial Symbiosis to used electric vehicle batteries. Procedia CIRP 80, 661–666. doi:10.1016/j.procir.2019.01.074
Mathur, N., Singh, S., and Sutherland, J. W. (2020). Promoting a circular economy in the solar photovoltaic industry using life cycle symbiosis. Resour. Conservation Recycl. 155, 104649. doi:10.1016/j.resconrec.2019.104649
Mathur, N., Sutherland, J. W., and Singh, S. (2022). A study on end of life photovoltaics as a model for developing industrial synergistic networks. Jnl Remanufactur 12, 281–301. doi:10.1007/s13243-022-00111-y
Medina, M. (2008). The informal recycling sector in developing countries: Organizing waste pickers to enhance their impact. Gridlines; No. 44. Washington, DC: World Bank. Available at: https://openknowledge.worldbank.org/handle/10986/10586 License: CC BY 3.0 IGO.
Meteyer, S., Xu, X., Perry, N., and Zhao, Y. F. (2014). Energy and material flow analysis of binder-jetting additive manufacturing processes. Procedia Cirp 15, 19–25. doi:10.1016/j.procir.2014.06.030
Modak, P., Wilson, D. C., and Velis, C. (2015). “Waste management: Global status,” in Global waste management outlook (United Nations Environmental Programme), 51–79.
Moreno, M., Turner, C., Tiwari, A., Hutabarat, W., Charnley, F., Widjaja, D., et al. (2017). Re-Distributed manufacturing to achieve a circular economy: A case study utilizing IDEF0 modeling. Procedia CIRP 63, 686–691. doi:10.1016/j.procir.2017.03.322
Morseletto, P. (2020). Targets for a circular economy. Resour. Conservation Recycl. 153, 104553. doi:10.1016/j.resconrec.2019.104553
Neves, A., Godina, R., Azevedo, S. G., and Matias, J. C. O. (2020). “A comprehensive review of industrial symbiosis,” in Journal of cleaner production (Elsevier Ltd), 247. doi:10.1016/j.jclepro.2019.119113
NIST (2022). Fostering a circular economy and carbon sequestration for construction materials. Available at: https://www.nist.gov/news-events/events/2022/06/fostering-circular-economy-and-carbon-sequestration-construction.
Nnorom, I. C., and Osibanjo, O. (2008). Overview of electronic waste (e-waste) management practices and legislations, and their poor applications in the developing countries. Resour. conservation Recycl. 52 (6), 843–858. doi:10.1016/j.resconrec.2008.01.004
Ortegon, K., Nies, L. F., and Sutherland, J. W. (2013). Preparing for end of service life of wind turbines. J. Clean. Prod. 39, 191–199. doi:10.1016/j.jclepro.2012.08.022
Pieroni, M. P. P., McAloone, T. C., and Pigosso, D. C. A. (2019). Business model innovation for circular economy and sustainability: A review of approaches. J. Clean. Prod. 215, 198–216. doi:10.1016/j.jclepro.2019.01.036
Pires, A., and Martinho, G. (2019). Waste hierarchy index for circular economy in waste management. Waste Manag. 95, 298–305. doi:10.1016/j.wasman.2019.06.014
Reslan, M., Last, N., Mathur, N., Morris, K. C., and Ferrero, V. (2022). Circular economy: A product life cycle perspective on engineering and manufacturing practices. Procedia CIRP 105, 851–858. doi:10.1016/j.procir.2022.02.141
Richter, J. L., Tähkämö, L., and Dalhammar, C. (2019). Trade-offs with longer lifetimes? The case of LED lamps considering product development and energy contexts. J. Clean. Prod. 226, 195–209. doi:10.1016/j.jclepro.2019.03.331
Rosa, P., Sassanelli, C., Urbinati, A., Chiaroni, D., and Terzi, S. (2020). Assessing relations between circular economy and industry 4.0: A systematic literature review. Int. J. Prod. Res. 58, 1662–1687. doi:10.1080/00207543.2019.1680896
Sanneh, E. S., Hu, A. H., Chang, Y. M., and Sanyang, E. (2011). Introduction of a recycling system for sustainable municipal solid waste management: A case study on the greater banjul area of the Gambia. Environ. Dev. Sustain. 13 (6), 1065–1080. doi:10.1007/s10668-011-9305-9
Sarigecili, M. I., Baysal, M. M., Zhu, B., and Roy, U. (2013). A disassembly process model for end-of-life activities of manufactured products. Int. J. Sustain. Manuf. 3 (1), 37–56. doi:10.1504/ijsm.2013.058620
SASB, 2018. Sustainability accounting standards board. Technical Re- port. publication Title: Sustainability Accounting Standards Board. Available at: https://www.sasb.org/.
Schmitt, T., Wolf, C., Lennerfors, T. T., and Okwir, S. (2021). Beyond “Leanear” production: a multi-level approach for achieving circularity in a lean manufacturing context. J. Clean. Prod. 318, 128531. doi:10.1016/j.jclepro.2021.128531
Schumacher, K., and Forster, A. (2022). Facilitating a circular economy for textiles workshop report, 1500. NIST Special Publication, 204. doi:10.6028/NIST.SP.1500-207
Schumacher, K., and Green, M. L. (2021). Circular economy in the high-tech world workshop report, 1500. NIST Special Publication, 204. doi:10.6028/NIST.SP.1500-204
Singh, J., and Ordoñez, I. (2016). Resource recovery from post-consumer waste: Important lessons for the upcoming circular economy. J. Clean. Prod. 134, 342–353. doi:10.1016/j.jclepro.2015.12.020
Smith, L., and Ball, P. (2012). Steps towards sustainable manufacturing through modelling material, energy and waste flows. Int. J. Prod. Econ. 140 (1), 227–238.
Solid Waste Association of North America (2021). Recycling markets have strongly recovered since national sword. Available at: https://www.northjersey.
Solly, J., Poissonnier, G., Petigny, J., Menigault, C., Luisce, E., Harscoet, E., et al. (2019). Economic study of the Canadian plastic industry, markets and waste. Summ. Rep. Environ. Clim. Chang. Can. 1, 1–63.
Srivastava, V., Ismail, S. A., Singh, P., and Singh, R. P. (2015). Urban solid waste management in the developing world with emphasis on India: Challenges and opportunities. Rev. Environ. Sci. Biotechnol. 14 (2), 317–337. doi:10.1007/s11157-014-9352-4
Sundin, E., and Bras, B. (2005). Making functional sales environmentally and economically beneficial through product remanufacturing. J. Clean. Prod. 13 (9), 913–925. doi:10.1016/j.jclepro.2004.04.006
Sundin, E., and Lee, H. M. (2012). “In what way is remanufacturing good for the environment?,” in Design for innovative value towards a sustainable society. Editors M. Matsumoto, Y. Umeda, K. Masui, and S. Fukushige (Dordrecht: Springer). doi:10.1007/978-94-007-3010-6_106
Torretta, V., Ferronato, N., Katsoyiannis, I. A., Tolkou, A. K., and Airoldi, M. (2017). “Novel and conventional technologies for landfill leachates treatment: A review,” in Sustainability (Switzerland), 9, 9. MDPI. doi:10.3390/su9010009
Um, J., Yoon, J. S., and Suh, S. H. (2008). An architecture design with data model for product recovery management systems. Resour. conservation Recycl. 52 (10), 1175–1184. doi:10.1016/j.resconrec.2008.06.001
United Nations Environment Programme (2015). Global waste management outlook. Available at: https://www.unep.org/resources/report/global-waste-management-outlook.
US Environmental Protection Agency (2020). Advancing sustainable materials management: 2018 fact sheet assessing trends in materials generation and management in the United States. Available at: https://www.epa.gov/facts-and-figures-about-materials-waste-and-recycling/advancing-sustainable-materials-management.
US Environmental Protection Agency (2022). Inventory of U.S. Greenhouse gas emissions and sinks: 1990-2020. Available at: https://www.epa.gov/ghgemissions/draft-inventory-us-greenhouse-gas-emissions-and-sinks-1990-2020.
US Environmental Protection Agency (2021a). National recycling Strategy: Part One of a series on building a circular economy for all. Available at: https://www.epa.gov/recyclingstrategy/national-recycling-strategy-part-one-series-building-circular-economy-join-effort.
US Environmental Protection Agency (2021b). Resource conservation and recovery act (RCRA). Available at: https://www.epa.gov/rcra.
US Environmental Protection Agency (2021c). National biennial hazardous waste report. Available at: https://rcrapublic.epa.gov/rcrainfoweb/action/main-menu/view.
Van Ewijk, S., and Stegemann, J. A. (2016). Limitations of the waste hierarchy for achieving absolute reductions in material throughput. J. Clean. Prod. 132, 122–128. doi:10.1016/j.jclepro.2014.11.051
Velenturf, A. P., and Purnell, P. (2021). Principles for a sustainable circular economy. Sustain. Prod. Consum. 27, 1437–1457. doi:10.1016/j.spc.2021.02.018
Waissi, G. R., Demir, M., Humble, J. E., and Lev, B. (2015). Automation of strategy using IDEF0—a proof of concept. Operations Res. Perspect. 2, 106–113. doi:10.1016/j.orp.2015.05.001
Wang, Y., Chen, M., Gao, J. Q., and Chen, E. (2011). Modeling and analysis of end of life vehicles recovery: An enhanced IDEF0 methodology (Part I). Adv. Mater. Res. 314–316, 2539–2542. doi:10.4028/www.scientific.net/amr.314-316.2539
Wilts, H., and Berg, H. (2018). The digital circular economy: Can the digital transformation pave the way for resource-efficient materials cycles? 2017. Umwelt, Energie: Wuppertal Institut für Klima.
Woodard, R. (2020). Waste management in Small and Medium Enterprises (SMEs) – a barrier to developing circular cities. Waste Manag. 118, 369–379. doi:10.1016/j.wasman.2020.08.042
World Economic Forum, E. M. F. (2016) in Intelligent assets: Unlocking the circular economy potential. Editor R. Sheppard Available at: https://ellenmacarthurfoundation.org/intelligent-assets-unlocking-the-circular-economy-potential.
World Resources Institute, World Business Council for Sustainable Development (2004). “GHG protocol: A corporate accounting and reporting standard: Revised edition,” in Technical report. Greenhouse gas protocol organization. Available at: https://ghgprotocol.org/sites/default/files/standards/ghg- protocol- revised.pdf.
Zhang, H., Haapala, K. R., Mary, E., and Funk, K. H. (2011). Environmental impact and cost assessment of product service systems using IDEF0 modeling. Proc. NAMRI/SME 39.
Keywords: circular economy, material recovery, end-of-life, circular economy standards, sustainable development, process models, IDEF0
Citation: Mathur N, Last N and Morris KC (2023) A process model representation of the end-of-life phase of a product in a circular economy to identify standards needs. Front. Manuf. Technol. 3:988073. doi: 10.3389/fmtec.2023.988073
Received: 06 July 2022; Accepted: 21 March 2023;
Published: 18 April 2023.
Edited by:
Mélanie Despeisse, Chalmers University of Technology, SwedenReviewed by:
Anbesh Jamwal, Malaviya National Institute of Technology, Jaipur, IndiaOkechukwu Okorie, University of Exeter, United Kingdom
Peter Ball, University of York, United Kingdom
Copyright © 2023 Mathur, Last and Morris. This is an open-access article distributed under the terms of the Creative Commons Attribution License (CC BY). The use, distribution or reproduction in other forums is permitted, provided the original author(s) and the copyright owner(s) are credited and that the original publication in this journal is cited, in accordance with accepted academic practice. No use, distribution or reproduction is permitted which does not comply with these terms.
*Correspondence: Nehika Mathur, bmVoaWthLm1hdGh1ckBuaXN0Lmdvdg==