- Mechanical and Industrial Engineering, University of Illinois at Chicago, Chicago, IL, United States
Gallium-based room-temperature liquid metals possess extremely valuable properties, such as low toxicity, low vapor pressure, and high thermal and electrical conductivity enabling them to become suitable substitutes for mercury and beyond in wide range of applications. When exposed to air, a native oxide layer forms on the surface of gallium-based liquid metals which mechanically stabilizes the liquid. By removing or reconstructing the oxide skin, shape and state of liquid metal droplets and flows can be manipulated/actuated desirably. This can occur manually or in the presence/absence of a magnetic/electric field. These methods lead to numerous useful applications such as soft electronics, reconfigurable devices, and soft robots. In this mini-review, we summarize the most recent progresses achieved on liquid metal droplet generation and actuation of gallium-based liquid metals with/without an external force.
Introduction
Room-temperature gallium liquid metal alloys have drawn increasing research interests recently. These alloys not only can flow easily, but also can be shaped to some extent. They own all useful properties of other solid/molten metals such as high thermal conductivity, high electrical conductivity, inherently high density, and low vapor pressure, while being non-toxic, unlike mercury. Two important gallium-based alloys are GaInSn and EGaIn. GaInSn or galinstan is a eutectic alloy composed of 68%wt gallium, 22%wt of indium, and 10%wt of tin (Liu et al., 2012). EGaIn is a similar eutectic composition of 75.5%wt of gallium and 24.5%wt of indium (Dickey et al., 2008). Demonstrating superior performances in various aspects, gallium-based liquid metals have been explored for many novel applications, such as microfluidics devices (Khoshmanesh et al., 2017), stretchable electronics (Wang et al., 2015c; Bartlett et al., 2016), reconfigurable devices (Wang et al., 2015b), electronics cooling (Ma and Liu, 2007), vacuum pumping (Tang et al., 2015a), and painted conductive electrodes in liquid droplet actuation (Eaker et al., 2017). However, there are also some challenges in working with these liquid metals. When exposed to air, an oxide layer quickly forms on the surface of liquid metals, which is undesirable in some applications (Morley et al., 2008), since it disrupts the wetting behavior and impedes physical and electrical contacts (Giguere and Lamontagne, 1954). That said, this oxide layer is not always problematic, since it can also help stabilize the liquid mechanically. One of the leading research groups working on room-temperature liquid metals, discussed numerous emerging capabilities, and applications of gallium-based liquid metal devices enabled by the native oxide layer (Dickey, 2014, 2017). One advantage provided by oxide layer is that it facilitates manipulation of gallium-based liquid metals. In this mini-review, we highlight the most recent progress made in manipulation and actuation of gallium-based liquid metals (both in droplet and flow scale) and summarize the latest applicable techniques in this field.
Control and Manipulation of Liquid Metals
The mechanically stabilizing oxide layer on liquid metal surfaces, along with the high surface tension delivers potentials for generating, and manipulating liquid metal objects and droplets. The result can be utilized without any necessary further processing or can be considered as initial steps of intricate pattering methods which have been recently summarized by Majidi and Dickey (2015). Generated microdroplets can also be used as micropumps, microcoolers, and micromixers (Tang et al., 2016). Besides generating liquid metal objects, manipulating the motion, and shape of these metal objects is also of importance. In this approach, unique properties of liquid metals can be utilized toward applications in which flexibility and stretchability are necessary while the requirement of large pumps, wires, and direct contact with liquid metal is eliminated (Eaker and Dickey, 2016). Soft robots, reconfigurable electronics, and microelectromechanical systems (MEMS) are among these applications.
Liquid Metal Droplet Generation
Droplet generation has been studied extensively in the field of microfluidics (Xu and Attinger, 2009; Yu et al., 2011; Khoshmanesh et al., 2017; Zhu and Wang, 2017). Various existing methods are applicable to liquid metal including manual methods (Yu et al., 2014), flow focusing via microchannels (Thelen et al., 2012), molding (Mohammed et al., 2014), and inkjet printing (Li et al., 2015, 2016). The choice of method depends on specific applications and cost/complexity of the experiment. For instance, microchannel fabrication is costly and complicated. Therefore, simple cheap methods like manual droplet generation may be useful. In one attempt, liquid metal droplets were injected through a needle into another fluid with different surface tension such as sodium dodecylsulfate solution to generate microdroplets. The liquid self-breakup through jetting resulted in a large number of droplets in the scale of 50 μm (Yu et al., 2014). The downside of manual techniques lies in the low quality of the droplets; their sizes may vary and the result depends on the operator. Hence, methods such as flow focusing or molding can be beneficial. Using flow focusing, a microfluidic system was successfully developed to generate galinstan droplets in a highly viscous carrier liquid such as glycerol (Gol et al., 2015). The schematic of experiment is shown in Figure 1A. Right after the continuous generation of droplets, a T-junction on the way, including NaOH solution entering from one outlet, facilitated the transfer of galinstan droplets from glycerol to NaOH solution to prevent surface oxidation.
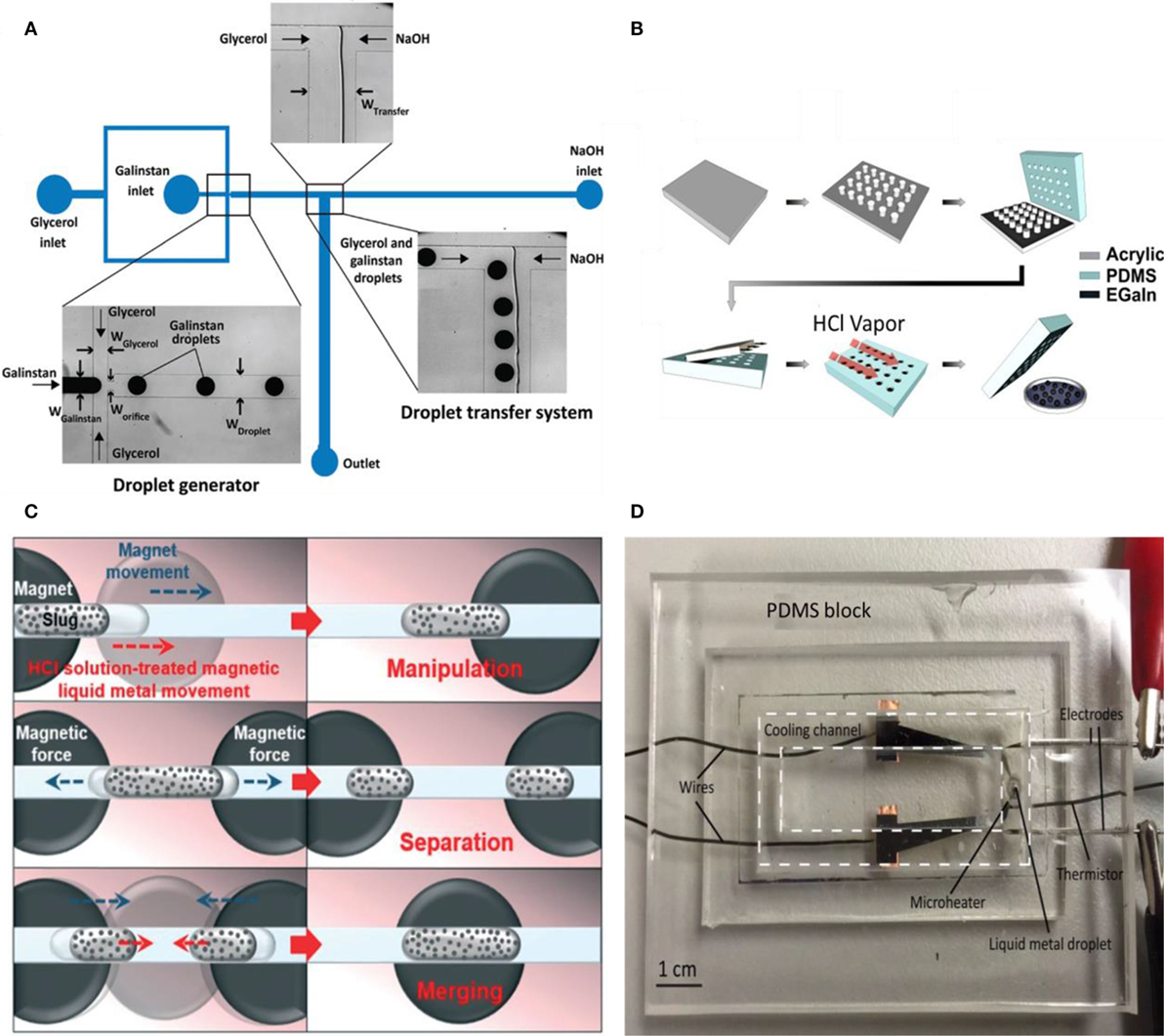
Figure 1. (A) Chip schematic for galinstan droplet generation and transition into NaOH solution (Gol et al., 2015). (B) Process of liquid metal generation and oxide layer removal with HCl vapor (Mohammed et al., 2014). (C) Schematic of liquid metal manipulation with magnetic field (Jeon et al., 2017). (D) Liquid metal cooling system (Zhu et al., 2016).
Following the same approach, Gol et al. (2016) used two inlets of NaOH after the microdroplet generation to provide the transition of galinstan droplets into two parallel streams. The benefit of these methods is in generating uniform droplets with controllable sizes on demand where the latter adds to the controllability of experiments toward reconfigurable systems. More modifications have been applied to the traditional T junctions by adding an extra branch of NaOH solution, in order to achieve smoother and more continuous droplet generation (Tian et al., 2017).
Mohammed et al. (2014) developed a method using a mold to generate gallium-based liquid metal droplets with precise sizes indicated in Figure 1B. The method does not utilize any surfactant to prevent the coalescence of generated droplets or any complicated device. In the first two steps, pillars were patterned by a laser writer on an acrylic sheet. Next, PDMS was molded with the prepared patterns and EGaIn was inserted into the reservoirs. The oxide layer formed on these liquid metals helped the located droplets on the molds to become stable. After removing the oxide layer with HCl, spheres with precise sizes were generated with respect to the shape of the mold. Atomized spraying of liquid metal is another recently explored technique by Zhang et al. (2014b) reporting liquid metal droplets in the size range of 0.7–50 μm. This spraying technique was used for tape transfer printing toward soft microfluidic electronics (Jeong et al., 2015). This method was also applied for droplet generation as the first step of pressure screen printing used in soft electronics (Wang and Liu, 2015) and liquid metal radiation shielding films (Deng and Liu, 2015).
Liquid Metal Actuation
In addition to generating liquid metal droplets with desirable size and number, the actuation and controlled motion of these objects play a significant role for various purposes, including heat dissipation (Ma and Liu, 2007), drug delivery (Sanchez et al., 2015), microfluidic pumps and mixers (Yang et al., 2016), and enhancement of heat transfer and chemical reaction (Tang et al., 2014). These findings are the results of high electrical conductivity, rapid oxidation of liquid metals, and their elastic properties displaying various interesting reactions in the presence of an external electric field (Sheng et al., 2014), magnetic field (Kim and Lee, 2015), or when two liquid metal droplets coalesce (Yuan et al., 2015a). Therefore, various actuation and manipulation methods have been investigated either in liquid metal droplets or flow.
Manipulation by External Electric/Magnetic Field
The control of gallium-based liquid metals faces obstacles, especially when their movement is necessary. They form the oxidation layer rapidly, which stick to almost every surface. Therefore, it is essential to surpass this wetting behavior when useful electronic and thermal conductivity of liquid metals are needed in motion. One process comprises coating liquid metal droplets with nano-particles, semiconductor, and insulating materials forming the so-called liquid metal marbles (Sivan et al., 2013). Depending on the coating, the application can be modified; for instance, liquid metal marbles coated with semiconductor materials can act as transistors or diodes. Furthermore, using specific micro-/nano-particles as coatings such as ferro-magnetic materials facilitated manipulations of these droplets or magnetic liquid metal marbles, by using an external magnetic field (Kim and Lee, 2015). Jeon et al. (2015) investigated the lyophobicity of liquid metal marbles coated with ferro-magnetic Fe nano-particles. Large contact and sliding angles of liquid metal marbles indicated the significant improvement in non-wetting specifications. The liquid metal marble was tested as an electrical switch that worked completely wirelessly. In a similar attempt, Fe coated liquid metals were applied to magnetically manipulate the flow and slugs in microfluidic channels with different geometries toward electrical switching (Jeon et al., 2017). In this study, Fe coated liquid metals were treated with HCl to get spherical shapes and afterward, they were collected by a syringe. The magnetic liquid metal was then injected into a PDMS-based channel filled with HCl or NaOH. As schematically shown in Figure 1C, a circular magnet was placed underneath the channel. Through moving the magnet, the magnetic liquid metal could be manipulated desirably. In the next step, two magnets were located beneath the channel and by moving them with respect to each other, merging and separating of liquid metal slugs were achieved.
Furthermore, the feasibility of coating liquid droplets with water was explored (Ding and Liu, 2016). The so-called composite liquid metal marbles were studied in different aspects such as shape, surface characteristics, and impact behaviors. In addition to preventing the oxidation, water coating on liquid metal droplets facilitates potentials for applications in 3D printing, liquid metal jet cooling, etc.
In various recent attempts, applying an external voltage has been the key to manipulate the capillary behavior of liquid metals. Synthetically chemical-electrical mechanism approach was utilized to achieve reversible deformation of liquid gallium enabling liquid metals to be used as soft robots and machines (Zhang et al., 2014a). The main idea stems from the effect of electrochemical oxidation and chemical dissolution process of gallium oxide with applying an external voltage and usage of acidic and alkali electrolytes. These processes lead to a change in liquid metal’s surface tension allowing the reversible shape transformation.
One way to affect the interfacial properties of liquid metals is electrocapillary actuation (ECA). During the classically known phenomenon, a voltage is applied via two counter electrodes to liquid metal immersed in an electrolyte. The method has been recently applied for various purposes such as producing galinstan folding patterns (Wang and Liu, 2016) and directing liquid metal through more complicated pathways. In the following summarized examples, ECA has been utilized to manipulate liquid metal.
Electrocapillary actuation can be a suitable solution to the challenging issue of removing liquid metal residue out of the pathways. To tackle the problem, electrochemical processes were applied to the surface of gallium liquid metals to remove the oxide skin (Khan et al., 2015; Morales et al., 2016). Khan et al. (2015) provided a possibility to remove liquid metals out of microchannels. This method is not hazardous like using acids and moreover, does not require complicated fabrication methods to change the structure of microchannels. The main used property is a reductive electrochemical potential which can remove the oxide layer on liquid metals’ surfaces. In the absence of oxide layer, liquid metal beads up because of its high surface tension resulting in liquid removal dominated by capillary forces. The main parts of the experimental setup included two reservoirs, one filled with electrolyte and the other with EGaIn, where these two were linked to each other and were also connected to a voltage through electrodes. The straight borosilicate capillaries between the reservoirs were prefilled with liquid metal. The applied voltage withdrew liquid metal from the microchannel with a decaying velocity versus time. The interesting phenomena is that, as soon as applying of voltage is stopped, the oxide layer reforms, preventing the liquid metal to flow, and leave the channel anymore. The useful electrical control of liquid metal flow in microchannels can provide various advantages in applications such as reconfigurable antennas and sensors, soft robots, and micropumps.
Tang et al. (2015b) also utilized electrocapillarity to direct liquid metal flow in microchannels with more than one path. With altering the polarity of voltage, two various sets of results can be achieved: the oxide layer might be removed by electrocapillarity leading to smoother liquid flow toward the desired direction, or it might reform decreasing the flow smoothness, helping to direct the flow to other outlets. The potential of this method is demonstrated for more complex channels with multiple outlets. This capability has numerous applications such as adjustable circuits and MEMS devices.
Electrowetting is another useful phenomenon recently studied on liquid metal (Diebold et al., 2017). The method was applied toward radio-frequency (RF) electronics and used acidic siloxanes to remove the oxide skin out of liquid metal surface. The advantage of siloxanes is that they are electrically insulating fluids which do not participate in the chemical reactions in the absence of water (Holcomb et al., 2016).
Manipulating the surface tension of liquid metals with an applied bias or ECA has been studied by other researchers. Gough et al. (2015) applied a low voltage or power (1–2 mW) between liquid metal and surrounding electrolyte in a reservoir connected to one or more capillary channels. The geometry of the device had a high aspect ratio (width to height) which enabled a higher ratio of surface area to volume of the liquid metal. It was also theoretically shown that ECA phenomenon is highlighted in a quasiplanar geometry as a result of increased sensitivity to surface tension changes. The process is completely reversible in a way that the oxide formation can be completely controlled with voltage acting as a switch in the middle of flow to be able to mechanically stabilize it whenever needed.
Applying a non-uniform electric field can also be useful to produce dielectrophoresis (DEP) force. For example, Tang et al. (2015c) developed a method to create galinstan 3D microstructures using DEP. After generating separate microdroplets of galinstan using ultrasonication and oxide layer, a DEP platform including chromium/gold microelectrodes was utilized to insert a DEP force to galinstan to form 3D liquid metal electrodes. In their more recent work, Tang et al. (2016) described a method combining electrocapillarity and electrochemistry for applying a sinusoidal wave signal to liquid metal stream. By altering the magnitude of voltage, the size of generated droplets changed from 85 to 185 µm.
In a different application, a droplet of galinstan was designed to cool localized hot spots (Zhu et al., 2016). As depicted in Figure 1D, a liquid metal droplet was fixed in a PDMS channel prefilled with NaOH solution while a microheater was positioned at the bottom of the channel. The droplet was actuated by a square wave DC signal induced through two electrodes. The temperature of the channel was measured by an infrared camera. Being electrically conductive, liquid metal droplet played the role of a soft pump that under actuation circulated the NaOH coolant because of Marangoni flow. Moreover, the thermal conductivity of liquid metal lead to higher heat removal rates. Eventually, a very simple system with no moving parts and adjustable flow rate was provided with the advanced properties of liquid metal applicable to electronics cooling.
As mentioned earlier, the oxide layer on liquid metal surface offers unique potentials for mechanical manipulation. One set of experiments carried out recently (Dickey et al., 2016), resulted in the highest variations in liquid metal’s surface tension ever reported in literature, highlighted by the oxide layer in addition to electrocapillarity. The method is tunable and reversible, using either oxidation or reduction in order to bead up or spread a liquid metal droplet in an electrolyte and also to do capillary injection and withdrawal of liquid metal in and out of a channel or capillary tube. This oxide layer/skin has been under more interesting studies lately, such as readily stretching liquid metal on polymeric substrates to draw liquid metal wires stabilized by the oxide layer (Lin et al., 2016) or manipulating the oxide layer of EGaIn in a reproducible way leading to a reconfigurable microfluidic device (Wang et al., 2015a). Parekh et al. (2016) utilized a 3D printing and direct writing method to fabricate complex microchannels with liquid metal as a reusable ink that can be recovered at the end by an aqueous solution using electrochemistry.
Liquid Metal Self-Actuation
Self-propelled micro- and nano-motors are among the most appealing research areas recently (Zhao and Pumera, 2013; Sanchez et al., 2015). In the past few years, attentions have been drawn to innovative applications of these motors/robots in soft matter and biological studies. These chemically powered devices can be utilized in drug delivery and duplicating the behavior of a biological organ (Majidi, 2014). Among various materials chosen for this specific purpose, liquid metal soft robotics has indicated a novel and significant impact (Xu, 2015).
All previously mentioned actuation methods require an external power supply. However, liquid metal can be manipulated easily without an electric/magnetic field as a result of its exceptional properties. Self-actuation of liquid metals can facilitate new techniques beyond soft robot applications such as self-powered machines, tunable RF, and microfluidics devices. Recently, it was indicated that liquid metal objects could be self-actuated in the presence of aluminum (Al) flakes (as fuels) resulting in a self-powered soft machine (Sheng et al., 2015; Zhang et al., 2015a,b). Figure 2A demonstrates examples of this method. The main reason behind these results is the Marangoni effect empowered by the electrochemical reaction between Al and liquid metal EGaIn coupled with the hydrogen evolution at the reaction sites. In Figure 2A (a), a droplet of EGaIn is dropped in NaOH solution, and a small sheet of Al is placed next to the liquid metal droplet. Liquid metal then breaks into the passivation layer on Al sheet, and an alloy of Al and liquid metal is made. Figure 2A (b) shows the highlighted rotation of alloyed droplet with ink. When this alloy (Al dissolved in liquid metal) is collected and injected again in NaOH solution as indicated in Figure 2A (c), a stream of small liquid metal droplets is generated, and these droplets move to different directions as running motors.
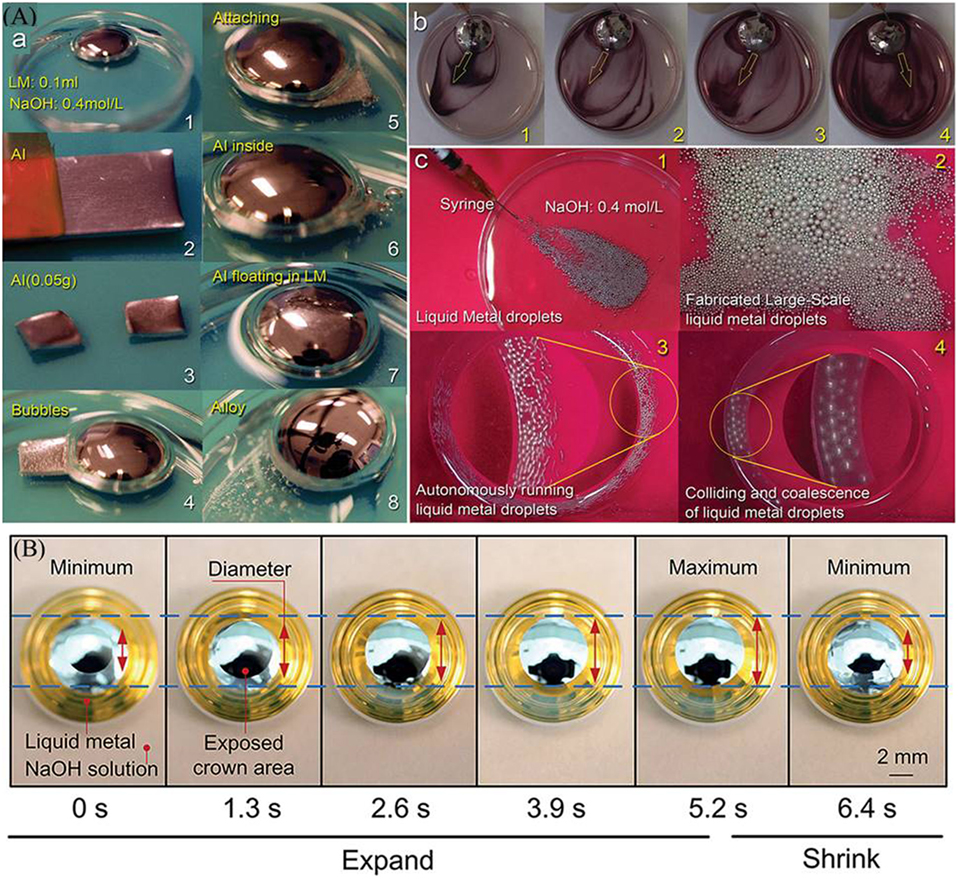
Figure 2. (A)a Preparation of aluminum (Al) liquid metal alloy. (A)b-c The automatically running droplets of liquid metal Al alloy (Sheng et al., 2015). (B) Oscillation of partially submerged GaIn droplet in NaOH solution (Yi et al., 2016).
Similarly, Yuan et al. (2015b) demonstrated a method to develop self-powered liquid metal motors with Brownian motion in an alkali electrolytes, by dissolving 1% of Al in GaIn10 (Ga 90%, In 10%). The main driving force here is also enabled by hydrogen bubbles, however with some differences compared with previous work. These tiny motors were further actuated by an electric field (20 V) to achieve much higher moving speeds (Tan et al., 2015).
Gough et al. (2016) basically developed a galvanic cell containing liquid metal as the anode, copper as the cathode, and NaOH as the electrolyte filling the channel connecting anode and cathode. The device acts very similar to a battery where the oxidation occurs in anode forming the super hydrophobic gallium oxide on liquid metal and an oxygen reduction reaction in cathode. The oxide layer growth reduces the interfacial tension in the channel and liquid metal starts to flow easily in the channel filled with electrolyte.
More fascinating potentials provided by oxide layer were lately utilized by Yi et al. (2016) and Liu et al. (2016). The former work simply used a semi-submerged liquid metal droplet in alkaline solution. Figure 2B shows the expanding and shrinking of GaIn droplet in NaOH solution. The oxide layer formed on the top exposed part of the droplet diffused along the droplet interface and the thin liquid film surrounding the droplet causing a surface tension gradient (Marangoni effect) which lead to a periodic oscillation. The self-oscillation droplet is an interesting non-hazardous model for mimicking the behavior of living organisms such as a beating heart, breathing air to produce energy. The latter work (Liu et al., 2016) explored the possibility of flowing galinstan in its own oxide layer acting as a channel with nano-meter thick walls. Galinstan was first injected through a stationary needle on a moving stage coated with PDMS. Various dog bone-shaped structures of galinstan were printed and the thin oxide layers surrounding these lines were observed. It was indicated that galinstan could be injected and withdrawn into and out of the thin oxide layer. These oxide layer channels are very flexible; in the case of fully withdrawal of liquid metal, they collapse and in case of injection, they inflate. When ruptured, these oxide layers can readily reform with the liquid metal residue. The novelty of this technique contributes to directly printed microfluidics which can collapse on its own.
Conclusion
Gallium-based liquid metal as a substitute for mercury, possesses fascinating specifications such as high surface tension, high thermal, and electrical conductivity combined with low toxicity. Moreover, the formed oxide layer on its surface, enable gallium liquid metal to be easily shaped, and desirably manipulated. Therefore, liquid metal manipulation: the generation of droplets with desired size and shape and manipulation/actuation of the generated objects and flows has been recently widely studied and investigated. In this mini-review, we focused on recent advances in these studies. The manipulation of liquid metals can occur in both liquid metal droplet and flow scale, with or without an external magnetic/electric field. The facile methods to manipulate them and their low toxicity empower gallium-based liquid metals to bring a bright future in numerous applications such as drug delivery, microfluidics, reconfigurable, and soft electronics.
Author Contributions
LM, the main author, was in charge of literature research and writing the paper. DG provided help in literature research and manuscript editing. JX, the corresponding author, reviewed the paper and provided feedback to improve the manuscript.
Conflict of Interest Statement
The authors declare that the research was conducted in the absence of any commercial or financial relationships that could be construed as a potential conflict of interest.
References
Bartlett, M. D., Fassler, A., Kazem, N., Markvicka, E. J., Mandal, P., and Majidi, C. (2016). Stretchable, high-k dielectric elastomers through liquid-metal inclusions. Adv. Mater. 28, 3726–3731. doi: 10.1002/adma.201506243
Deng, Y., and Liu, J. (2015). Liquid metal based stretchable radiation-shielding film. J. Med. Device 9, 014502. doi:10.1115/1.4029317
Dickey, M., Eaker, C., and Kahn, M. R. (2016). A method to manipulate surface tension of a liquid metal via surface oxidation and reduction. J. Vis. Exp. 107, 1–7. doi:10.3791/53567
Dickey, M. D. (2014). Emerging applications of liquid metals featuring surface oxides. ACS Appl. Mater. Interfaces 6, 18369–18379. doi:10.1021/am5043017
Dickey, M. D. (2017). Stretchable and soft electronics using liquid metals. Adv. Mater. 29, 1606425. doi:10.1002/adma.201606425
Dickey, M. D., Chiechi, R. C., Larsen, R. J., Weiss, E. A., Weitz, D. A., and Whitesides, G. M. (2008). Eutectic gallium-indium (EGaIn): a liquid metal alloy for the formation of stable structures in microchannels at room temperature. Adv. Funct. Mater. 18, 1097–1104. doi:10.1002/adfm.200701216
Diebold, A. V., Watson, A. M., Holcomb, S., Tabor, C., Mast, D., and Dickey, M. D. (2017). Electrowetting-actuated liquid metal for RF applications. J. Micromech. Microeng. 27, aa556a. doi:10.1088/1361-6439/aa556a
Ding, Y., and Liu, J. (2016). Water film coated composite liquid metal marble and its fluidic impact dynamics phenomenon. Front. Energy 10:29–36. doi:10.1007/s11708-015-0388-0
Eaker, C. B., and Dickey, M. D. (2016). Liquid metal actuation by electrical control of interfacial tension. Appl. Phys. Rev. 3, 0–12. doi:10.1063/1.4959898
Eaker, C. B., Joshipura, I. D., Maxwell, L. R., Heikenfeld, J., and Dickey, M. D. (2017). Electrowetting without external voltage using paint-on electrodes. Lab. Chip 17, 1069–1075. doi:10.1039/C6LC01500J
Giguere, P. A., and Lamontagne, D. (1954). Polarography with a dropping gallium electrode. Science 120, 390–391. doi:10.1126/science.120.3114.390
Gol, B., Kurdzinski, M. E., Tovar-Lopez, F. J., Petersen, P., Mitchell, A., and Khoshmanesh, K. (2016). Hydrodynamic directional control of liquid metal droplets within a microfluidic flow focusing system. Appl. Phys. Lett. 108, 164101. doi:10.1063/1.4947272
Gol, B., Tovar-lopez, F. J., Kurdzinski, M. E., and Tang, S. (2015). Continuous transfer of liquid metal droplets across a fluid–fluid interface within an integrated microfluidic chip. Lab. Chip 15, 2476–2485. doi:10.1039/C5LC00415B
Gough, R. C., Dang, J. H., Moorefield, M. R., Zhang, G. B., Hihara, L. H., Shiroma, W. A., et al. (2016). Self-actuation of liquid metal via redox reaction. ACS Appl. Mater. Interfaces 8, 6–10. doi:10.1021/acsami.5b09466
Gough, R. C., Morishita, A. M., Dang, J. H., Moorefield, M. R., Shiroma, W. A., and Ohta, A. T. (2015). Rapid electrocapillary deformation of liquid metal with reversible shape retention. Micro Nano Syst. Lett. 3, 4. doi:10.1186/s40486-015-0017-z
Holcomb, S., Brothers, M., Diebold, A., Thatcher, W., Mast, D., Tabor, C., et al. (2016). Oxide-free actuation of gallium liquid metal alloys enabled by novel acidified siloxane oils. Langmuir. 32, 12656–12663. doi:10.1021/acs.langmuir.6b03501
Jeon, J., Lee, J.-B., Chung, S. K., Kim, D., Wixforth, A., Strobl, C., et al. (2017). On-demand magnetic manipulation of liquid metal in microfluidic channels for electrical switching applications. Lab. Chip 379, 982–991. doi:10.1039/C6LC01255H
Jeon, J., Lee, J. J. B., Chung, S. K., and Kim, D. (2015). Magnetic liquid metal marble: wireless manipulation of liquid metal droplet for electrical switching applications. 18th International Conference on Solid-State Sensors, Actuators and Microsystems, TRANSDUCERS 2015 (Anchorage), 1834–1837.
Jeong, S. H., Hjort, K., and Wu, Z. (2015). Tape transfer atomization patterning of liquid alloys for microfluidic stretchable wireless power transfer. Sci. Rep. 5, 8419. doi:10.1038/srep08419
Khan, M. R., Trlica, C., and Dickey, M. D. (2015). Recapillarity: electrochemically controlled capillary withdrawal of a liquid metal alloy from microchannels. Adv. Funct. Mater. 25, 671–678. doi:10.1002/adfm.201403042
Khoshmanesh, K., Tang, S., Zhu, J. Y., Schaefer, S., Mitchell, A., Kalantar-zadeh, K., et al. (2017). Liquid metal enabled microfluidics. Lab. Chip 17, 2323–2329. doi:10.1039/C7LC00046D
Kim, D., and Lee, J. (2015). Magnetic-field-induced liquid metal droplet manipulation. J. Korean Phys. Soc. 66, 282–286. doi:10.3938/jkps.66.282
Li, G., Wu, X., and Lee, D.-W. (2015). Selectively plated stretchable liquid metal wires for transparent electronics. Sens. Actuators B Chem. 221, 1114–1119. doi:10.1016/j.snb.2015.07.062
Li, G., Wu, X., and Lee, D.-W. (2016). A galinstan-based inkjet printing system for highly stretchable electronics with self-healing capability. Lab. Chip 16, 1366–1373. doi:10.1039/C6LC00046K
Lin, Y., Ladd, C., Wang, S., Martin, A., Genzer, J., Khan, S. A., et al. (2016). Drawing liquid metal wires at room temperature. Extrem. Mech. Lett. 7, 55–63. doi:10.1016/j.eml.2016.03.010
Liu, S., Sun, X., Kemme, N., Damle, V. G., Schott, C., Herrmann, M., et al. (2016). Can liquid metal flow in microchannels made of its own oxide skin? Microfluid. Nanofluidics 20, 1–6. doi:10.1007/s10404-015-1665-2
Liu, T., Sen, P., and Kim, C. J. (2012). Characterization of nontoxic liquid-metal alloy galinstan for applications in microdevices. J. Microelectromech. Syst. 21, 443–450. doi:10.1109/JMEMS.2011.2174421
Ma, K., and Liu, J. (2007). Liquid metal cooling in thermal management of computer chips. Front. Energy Power Eng. China 1:384–402. doi:10.1007/s11708-007-0057-3
Majidi, C. (2014). Soft robotics: a perspective—current trends and prospects for the future. Soft Robot. 1, 5–11. doi:10.1089/soro.2013.0001
Majidi, C., and Dickey, M. D. (2015). Methods to pattern liquid metals. J. Mater. Chem. C 3, 3834–3841. doi:10.1039/C5TC00330J
Mohammed, M., Xenakis, A., and Dickey, M. (2014). Production of liquid metal spheres by molding. Metals (Basel) 4, 465–476. doi:10.3390/met4040465
Morales, D., Stoute, N. A., Yu, Z., Aspnes, D. E., and Dickey, M. D. (2016). Liquid gallium and the eutectic gallium indium (EGaIn) alloy: dielectric functions from 1.24 to 3.1 eV by electrochemical reduction of surface oxides. Appl. Phys. Lett. 109, 091905. doi:10.1063/1.4961910
Morley, N. B., Burris, J., Cadwallader, L. C., and Nornberg, M. D. (2008). GaInSn usage in the research laboratory. Rev. Sci. Instrum. 79, 56107. doi:10.1063/1.2930813
Parekh, D., Ladd, C., Panich, L., Moussa, K., and Dickey, M. (2016). 3D printing of liquid metals as fugitive inks for fabrication of 3D microfluidic channels. Lab. Chip 16, 1812–1820. doi:10.1039/C6LC00198J
Sanchez, S., Soler, L., and Katuri, J. (2015). Chemically powered micro- and nanomotors. Angew. Chem. Int. Ed. Engl. 54, 1414–1444. doi:10.1002/anie.201406096
Sheng, L., He, Z., Yao, Y., and Liu, J. (2015). Transient state machine enabled from the colliding and coalescence of a swarm of autonomously running liquid metal motors. Small 11, 5253–5261. doi:10.1002/smll.201501364
Sheng, L., Zhang, J., and Liu, J. (2014). Diverse transformations of liquid metals between different morphologies. Adv. Mater. 26, 6036–6042. doi:10.1002/adma.201400843
Sivan, V., Tang, S. Y., O’Mullane, A. P., Petersen, P., Eshtiaghi, N., Kalantar-Zadeh, K., et al. (2013). Liquid metal marbles. Adv. Funct. Mater. 23, 144–152. doi:10.1002/adfm.201200837
Tan, S., Yuan, B., and Liu, J. (2015). Electrical method to control the running direction and speed of self-powered tiny liquid metal motors. Proc. R. Soc. A. 471, 20150297. doi:10.1098/rspa.2015.0297
Tang, J., Zhou, Y., Liu, J., Wang, J., and Zhu, W. (2015a). Liquid metal actuated ejector vacuum system. Appl. Phys. Lett. 106, 31901. doi:10.1063/1.4906098
Tang, S., Lin, Y., Joshipura, I. D., Khoshmanesh, K., and Dickey, M. D. (2015b). Steering liquid metal flow in microchannels using low voltages. Lab. Chip 15, 3905–3911. doi:10.1039/C5LC00742A
Tang, S.-Y., Zhu, J., Sivan, V., Gol, B., Soffe, R., Zhang, W., et al. (2015c). Creation of liquid metal 3D microstructures using dielectrophoresis. Adv. Funct. Mater. 25, 4445–4452. doi:10.1002/adfm.201501296
Tang, S. Y., Joshipura, I. D., Lin, Y., Kalantar-Zadeh, K., Mitchell, A., Khoshmanesh, K., et al. (2016). Liquid-metal microdroplets formed dynamically with electrical control of size and rate. Adv. Mater. 28, 604–609. doi:10.1002/adma.201503875
Tang, S. Y., Sivan, V., Petersen, P., Zhang, W., Morrison, P. D., Kalantar-zadeh, K., et al. (2014). Liquid metal actuator for inducing chaotic advection. Adv. Funct. Mater. 24, 5851–5858. doi:10.1002/adfm.201400689
Thelen, J., Dickey, M. D., and Ward, T. (2012). A study of the production and reversible stability of EGaIn liquid metal microspheres using flow focusing. Lab. Chip 12, 3961–3967. doi:10.1039/c2lc40492c
Tian, L., Gao, M., and Gui, L. (2017). A microfluidic chip for liquid metal droplet generation and sorting. Micromachines 8, 39. doi:10.3390/mi8020039
Wang, J., Appusamy, K., Guruswamy, S., and Nahata, A. (2015a). Electrolytic reduction of liquid metal oxides and its application to reconfigurable structured devices. Sci. Rep. 5, 8637. doi:10.1038/srep08637
Wang, L., and Liu, J. (2015). Pressured liquid metal screen printing for rapid manufacture of high resolution electronic patterns. RSC Adv. 5, 57686– 57691. doi:10.1039/C5RA10295B
Wang, L., and Liu, J. (2016). Liquid metal folding patterns induced by electric capillary force. Appl. Phys. Lett. 108, 161602. doi:10.1063/1.4947440
Wang, M., Trlica, C., Khan, M. R., Dickey, M. D., and Adams, J. J. (2015b). A reconfigurable liquid metal antenna driven by electrochemically controlled capillarity. J. Appl. Phys. 117, 1–6. doi:10.1063/1.4919605
Wang, Q., Yu, Y., Yang, J., and Liu, J. (2015c). Fast fabrication of flexible functional circuits based on liquid metal dual-trans printing. Adv. Mater. 27, 7109–7116. doi:10.1002/adma.201502200
Xu, J. (2015). Liquid metal robotics: a new category of soft robotics on the horizon. Sci. Bull. 60, 1047–1048. doi:10.1007/s11434-015-0800-5
Xu, J., and Attinger, D. (2009). Drop on demand in a microfluidic chip. J. Micromech. Microeng. 18, 65020. doi:10.1088/0960-1317/18/6/065020
Yang, X., Tan, S., Yuan, B., and Liu, J. (2016). Alternating electric field actuated oscillating behavior of liquid metal and its application. Sci. China Technol. Sci. 59, 597–603. doi:10.1007/s11431-016-6026-1
Yi, L., Ding, Y., Yuan, B., Wang, L., Tian, L., Chen, C., et al. (2016). Breathing to harvest energy as a mechanism towards making a liquid metal beating heart. RSC Adv. 6, 94692–94698. doi:10.1039/C6RA17486H
Yu, G., Chen, X., and Xu, J. (2011). Acoustophoresis in variously shaped liquid droplets. Soft Matter 7, 10063. doi:10.1039/c1sm05871a
Yu, Y., Wang, Q., Yi, L., and Liu, J. (2014). Channelless fabrication for large-scale preparation of room temperature liquid metal droplets. Adv. Eng. Mater. 16, 255–262. doi:10.1002/adem.201300420
Yuan, B., He, Z., Fang, W., Bao, X., and Liu, J. (2015a). Liquid metal spring: oscillating coalescence and ejection of contacting liquid metal droplets. Sci. Bull. 60, 648–653. doi:10.1007/s11434-015-0751-x
Yuan, B., Tan, S., Zhou, Y., and Liu, J. (2015b). Self-powered macroscopic Brownian motion of spontaneously running liquid metal motors. Sci. Bull. 60, 1203–1210. doi:10.1007/s11434-015-0836-6
Zhang, J., Sheng, L., and Liu, J. (2014a). Synthetically chemical-electrical mechanism for controlling large scale reversible deformation of liquid metal objects. Sci. Rep. 4, 7116. doi:10.1038/srep07116
Zhang, J., Yao, Y., and Liu, J. (2015a). Autonomous convergence and divergence of the self-powered soft liquid metal vehicles. Sci. Bull. 60, 943–951. doi:10.1007/s11434-015-0786-z
Zhang, J., Yao, Y., Sheng, L., and Liu, J. (2015b). Self-fueled biomimetic liquid metal mollusk. Adv. Mater. 27, 2648–2655. doi:10.1002/adma.201405438
Zhang, Q., Gao, Y., and Liu, J. (2014b). Atomized spraying of liquid metal droplets on desired substrate surfaces as a generalized way for ubiquitous printed electronics. Appl. Phys. A Mater. Sci. Process. 116, 1091–1097. doi:10.1007/s00339-013-8191-4
Zhao, G., and Pumera, M. (2013). Magnetotactic artificial self-propelled nanojets. Langmuir 29, 7411–7415. doi:10.1021/la303762a
Zhu, J. Y., Tang, S. Y., Khoshmanesh, K., and Ghorbani, K. (2016). An integrated liquid cooling system based on galinstan liquid metal droplets. ACS Appl. Mater. Interfaces 8, 2173–2180. doi:10.1021/acsami.5b10769
Keywords: gallium-based liquid metal, liquid metal manipulation, liquid metal oxide skin, reconfigurable devices, soft electronics
Citation: Majidi L, Gritsenko D and Xu J (2017) Gallium-Based Room-Temperature Liquid Metals: Actuation and Manipulation of Droplets and Flows. Front. Mech. Eng. 3:9. doi: 10.3389/fmech.2017.00009
Received: 31 March 2017; Accepted: 07 August 2017;
Published: 30 August 2017
Edited by:
Seunghwa Ryu, KAIST, South KoreaReviewed by:
Seung Hee Jeong, École Polytechnique Fédérale de Lausanne, SwitzerlandFrancesco Dal Corso, University of Trento, Italy
Copyright: © 2017 Majidi, Gritsenko and Xu. This is an open-access article distributed under the terms of the Creative Commons Attribution License (CC BY). The use, distribution or reproduction in other forums is permitted, provided the original author(s) or licensor are credited and that the original publication in this journal is cited, in accordance with accepted academic practice. No use, distribution or reproduction is permitted which does not comply with these terms.
*Correspondence: Jie Xu, amlleHVAdWljLmVkdQ==