- Ultra-High Precision Manufacturing Laboratory, Department of Mechatronics Engineering, Faculty of Engineering, the Built Environment and Technology, Nelson, Nelson Mandela University, Port Elizabeth, South Africa
Single-point diamond turning (SPDT) is the state-of-the-art technology for ultra-precision manufacturing of optical products with optical surface roughness down to 1 nm. The SPDT technology has an important role in advanced manufacturing of critical components in different fields of industry. In a SPDT process, different cutting mechanisms affect the optical surface generation and reduce the quality of the turned product. Different efforts have been undertaken to improve the machining conditions as well as optical surface generation mechanisms. Recently, the application of magnetic field assistance in non-conventional SPDT platforms has shown promising results in terms of improving the cutting stability as well as the quality of surface finish. The application of magnetic field assistance becomes more important in SPDT of hard-to-cut materials including titanium alloy. In this study, magnetic field assistance is used in SPDT of Ti-6Al-4V alloy. The machining results show that using this technique could significantly improve the machining conditions and the quality of optical surface generation. The magnetic field assisted SPDT with air coolant could successfully improve the quality of surface finish by 62.5% when compared to non-magnetic purely mechanical SPDT process in dry cutting conditions. Magnetic field assistance is a passive machining technique, environmentally friendly, and it can promote green manufacturing and clean production in ultra-precision SPDT applications.
1 Introduction
In advanced manufacturing technologies, single-point diamond turning (SPDT) is the state-of-the-art technology for manufacturing optical components with optical surface roughness down to 1 nm. In a SPDT process, there are different factors that could negatively influence the optical surface generation mechanisms and decrease the quality of optical surface finish. The effects of harming factors are induced in diamond turning of brittle- and hard-to-cut materials. Tool wear, cutting temperature, tool life, and optical surface roughness are important factors in ultra-precision manufacturing which are significantly affected in diamond turning of hard-to-cut materials including titanium alloys and stainless steel (Zhang et al., 2015; Hatefi and Abou-El-Hossein, 2020b; Goel et al., 2021). Analytical models and non-conventional machining technologies are solutions that have been employed during SPDT of hard-to-cut materials to improve the cutting conditions and the outcome of the machining process in terms of surface roughness. Surfacy topography and transition edge width of the diamond turned products are critical factors in advanced manufacturing of engineering materials. The unconventional methods have been recently proposed to predict and evaluate the 3D surface roughness and surface texture in advanced manufacturing of hard-to-cut materials. By development of analytical surface topography models, the influence of different machining factors/conditions on the quality of the machined workpiece could be determined (Chabot et al., 2022; Karmiris-Obratański et al., 2022; Molnar and Szabo, 2022). Also, different non-conventional technologies have been developed and used in ultra-precision SPDT, including active vibration, hot machining, ion implantation, gas shielding, and magnetic manipulation techniques (Hatefi and Abou-El-Hossein, 2020a).
Active vibration systems and hot machining techniques are effective solutions that have shown positive impacts on the outcome of the SPDT process. The application of active vibration and hot machining solutions during advanced manufacturing of different materials is well-established (Singh and Khamba, 2006; Kumar, 2013; Venkatesan et al., 2014; Hatefi and Abou-El-Hossein, 2020a). Although active vibration and hot machining solutions are effective, they have negative effects on the machining conditions and the quality of optical surface generation. Active vibration techniques, including ultrasonic assisted SPDT, induce surface damage and passive vibrations. Hot machining solutions, including laser assisted SPDT, increase the cutting temperature during the diamond cutting process. Increasing the cutting temperature negatively affects the material swelling and tool wear while affecting the quality of surface finish. Nitrogen cold plasma jet and magnetic field assistance are recently developed techniques that could assist the SPDT process and improve the quality of optical surface generation mechanisms without negatively affecting the diamond cutting process (Xu et al., 2012; Xu et al., 2014; Yuan et al., 2017; Zhu et al., 2018; Hatefi and Abou-El-Hossein, 2020a).
Among the above-mentioned non-conventional assistive techniques, the application of magnetic field assistance during SPDT has shown promising results in terms of improving the machining conditions as well as the quality of surface finish. This technique is passive, contactless, and low-cost. In this technique, two strong neodymium permanent magnets are used to create a magnetic field with controlled magnetic flux density around the diamond cutting zone. This technique could positively influence different machining parameters and cutting mechanisms, without negatively affecting the optical surface generation mechanisms (Peruri and Chaganti, 2019; Hatefi and Abou-El-Hossein, 2022). As illustrated in Figure 1, the application of magnetic field assistance can positively impact different surface generation mechanisms and machining parameters. Applying a magnetic field generates damping effects and reduces the passive vibrations while improving uncut and overcut chip formation. It can enhance the workpiece material properties and improve the thermal conductivity of the workpiece material which can improve cutting conditions.
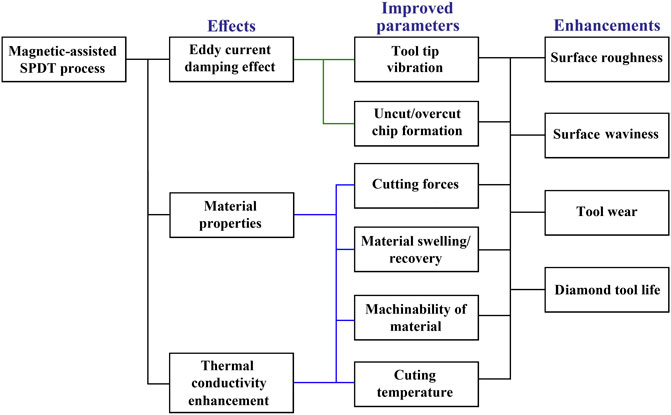
FIGURE 1. The influence of magnetic field assistance on surface generation mechanisms and machining parameters in ultra-precision SPDT applications (Hatefi and Abou-El-Hossein, 2022)
Ti-6Al-4V is one of the most commonly used titanium alloys with element components presented in Table 1. Ti-6Al-4V has high tensile strength, corrosion resistance, and fabricability. It has a wide range of applications in different industry sectors. This lightweight and strong alloy saves weight in highly loaded structures and is hence extremely suitable for jet engines, gas turbines, and airframe components. The low density, high strength, high corrosion resistance, and biocompatibility are attractive characteristics of Ti-6Al-4V for applications such as bridges, implants, and reconstruction plates. Its applications have also been extended to the marine and chemical industries due to its high corrosion resistance to most corrosive acids and alkalis. However, titanium alloys have low thermal conductivity and ultra-precision SPDT of titanium alloys is associated with poor machinability and relatively low-quality surface finish. High cutting temperatures and wear are associated with ultra-precision manufacturing of titanium alloys. High diamond tool wear, short diamond tool life, and low surface quality are major drawbacks in ultra-precision diamond turning of Ti-6Al-4V. Titanium alloys have high sustainability of work hardening due to low thermal conductivity and increased cutting temperature when diamond turned (Arrazola et al., 2009; Zhang et al., 2013; Hatefi and Abou-El-Hossein, 2022). Titanium has weak magnetic properties compared to ferromagnetic materials, however, the reaction of particles to a magnetic field could be seen in the material. The susceptibility of titanium is 14.6 ppm, which means the material has a positive paramagnetic behavior, which means that during the magnetic field assisted SPDT of titanium, the magnetic moments of the titanium workpiece tend to react and align towards the externally applied magnetic field.
In purely mechanical ultra-precision SPDT of Ti-6Al-4V, an average surface roughness above 30 nm is usually achieved, which is relatively high (Lou and Wu, 2022). The application of magnetic field assistance in ultra-precision SPDT is a relatively new topic in advanced manufacturing technologies. Recently, a few experimental studies have been performed to evaluate the effects of using magnetic field assistance with a magnetic flux density of 0.01 and 0.02 T during ultra-precision SPDT of Ti-6Al-4V (Yip and To, 2019a; Yip and To, 2019b). The results of experimental investigations show that increasing the strength of the magnetic field could positively impact the machining conditions. The best quality surface finish machined on the Ti-6Al-4V using a magnetic field assisted SPDT platform is reported by (Khalil et al., 2022), where an average surface roughness of 13.3 nm was generated using a magnetic field assisted SPDT platform with magnetic strength of 0.02 T. The results of performed experimental studies showed that applying a magnetic field during the diamond cutting process could reduce the passive vibrations, cutting temperature, un-cut/over-cut chip formation, material swelling, and surface roughness. Improving the mentioned mechanisms result in reduced diamond tool wear and extension of the diamond tool life (Yip and To, 2017a; Yip and To, 2017b). However, the optimum cutting conditions and machining factors need to be determined to achieve an ideal magnetic field assisted SPDT platform for cutting Ti-6Al-4V. In general, more experimental investigations need to be performed on magnetic field assisted SPDT of different hard-to-cut materials to investigate the correlation between the magnetic flux density and the outcome of the diamond cutting process. The optimum cutting conditions need to be determined to achieve the best possible outcome in terms of the quality of surface finish.
The propose of this study is to investigate the effects of applying a magnetic field, with an average magnetic flux density of 0.045 T at the cutting zone, on the quality of surface finish in ultra-precision SPDT of Ti-6Al-4V alloy. In this study, a mechanical structure was developed to enable applying a strong magnetic field around the cutting zone, with an average magnetic flux density of 0.045 T at the cutting zone. Subsequently, a series of experiment performed and the Ti-6Al-4V alloy workpiece was cut under different machining conditions (dry and wet) while using different cutting parameters. The machining results of the magnetic field assisted diamond turned samples, including the surface roughness of the finished surface, have been compared to the results of purely mechanical diamond turned samples. The optimum cutting conditions have been determined to achieve the best possible quality of surface finish with minimum surface roughness. In the following sections, the details of the experimental study are presented and the obtained results are analyzed and discussed. Finally, conclusions are drawn and opportunities for the future work are suggested.
2 Methods and materials
2.1 Theory and principles
To enable a non-conventional magnetic field assisted SPDT platform, a strong magnetic field with controlled magnetic flux density, concentrated at the tool-workpiece interaction zone, should be created. For this purpose, two strong magnets should be fixed at the desired positions at the sides of the machine spindle. In this structure, each magnet creates a magnetic field in the environment. The magnetic flux density created by the magnets will be more intense as much as the magnets get closer to each other. The magnetic flux density created by a magnet could be calculated using theoretical equations. Moreover, on-machine measurement techniques could be performed for measuring the average magnetic flux density at the cutting zone. In the proposed magnetic field assisted SPDT platform, two magnets are used. Figure 2 illustrates the average magnetic flux density between two magnets with opposite poles. However, there will be a falloff in the average flux density between the magnets and the flux density throughout the region between the magnet faces will not be uniform. However, the magnetic field along its central axis is easy to predict, calculate and measure. The magnetic flux density created by each magnet at position x between the magnets, presented in Figure 2, could be calculated using Eq. 1 (2021, Hatefi, 2021):
Where, B is the magnetic flux density created at distance X, X is the distance from the magnet, and Br is the magnetic remanence of the magnet. L, D, and W are the dimensions of the magnets. As illustrated in Figure 2, when the opposite poles of two magnets are facing each other, the magnetic flux density created between them equals the sum of magnetic flux densities created by each magnet at the desired point.
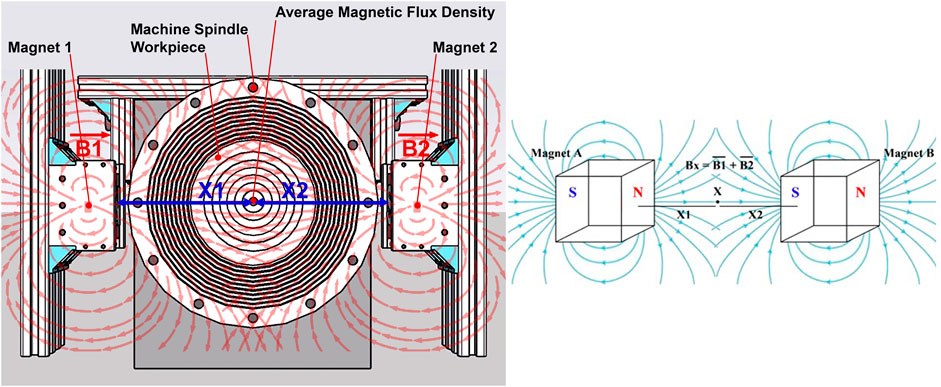
FIGURE 2. Illustration of the magnetic flux density generated between two magnets at the cutting zone.
Applying a magnetic field could have two major effects on the diamond cutting mechanisms. The first effect is the generation of an eddy current inside the workpiece material. The generated eddy current creates a magnetic field opposite the direction of the existing magnetic field. The interaction between the magnetic fields causes the generation of a resistive force against the change in the current state of the magnetic fields. The Lorentz force acts as a viscous damper system and creates a damping force that could suppress the unwanted passive vibrations while dissipating the kinetic energy of vibration into heat (Sodano and Bae, 2004). This effect could improve the diamond cutting stability during the SPDT process while reducing the amplitude of the passive vibrations of the turning system. The Gauss law is one of Maxwell’s equations that can describe the magnetic field existed. Eq. 2 presents the differential form of the Gauss law (Hatefi and Abou-El-Hossein, 2022):
where, ∇ is the differential vector operator, E is the electric field vector, ρ is the charge per unit volume (volume charge density), and ε0 is the electric permittivity of free space.
According to the Lorentz law, presented in Eq. 2, when a conductive material is moving/rotating in a magnetic field, an eddy current is generated inside the workpiece due to the variation of a static magnetic field. The eddy current would generate a magnetic field in the direction against the applied magnetic field. Consequently, the interaction between these two magnetic fields creates a repulsive force against the change in the existing flux, called the Lorentz force (Sodano and Bae, 2004; Ebrahimi et al., 2010). The Amper’s force law describes the generated Lorentz force, as given in Eq. 3 (Hatefi and Abou-El-Hossein, 2022):
where, F is the Lorentz force, E is the electric field, q is the electric charge, and Ve is the velocity of the conductor (workpiece) which is moving/rotating, and B is the magnetic field vector. In this condition, the kinetic energy of the passive vibrations is damped while dissipating energy from the eddy current damping effect. In this condition, the generated damping effect could be calculated from Eq. 4 (Hatefi and Abou-El-Hossein, 2022):
where, Fdamping is the generated damping force, and Ceddy and Ctt are the damping coefficients of the eddy current damper.
Thermal conductivity enhancement of the workpiece material is the second effect that could significantly improve the outcome of the SPDT process. Improving the thermal conductivity of the material could decrease the cutting temperature and improve the quality of surface finish. When a magnetic field is applied during SPDT of ferromagnetic and paramagnetic materials, which have positive paramagnetic behavior, it could positively affect the interaction between the particles in the material. In a purely mechanical SPDT process, because of the van der Waals forces, as well as dipole-dipole interactions, the paramagnetic particles in the workpiece material would attach to each other and reduce the thermal conductivity of the workpiece material. The susceptibility of titanium alloy is 14.6 ppm and the material properties of titanium alloys could be positively influenced by a magnetic field. In the presence of the external magnetic field, these paramagnetic particles, called dipole momentums, tend to be aligned with the direction of an externally applied magnetic field, and this would significantly reduce the dipole-dipole interactions (Lajvardi et al., 2010; Nkurikiyimfura et al., 2013). Eq. 5 presents the energy between the paramagnetic particles inside the workpiece material (Hatefi and Abou-El-Hossein, 2022):
where, Ud is the energy between particles i and j, r is the distance between paramagnetic particles i and j, and mp is the mass of particles i and j. Moreover, the coupled constant between the particles i and j could be calculated by using Eq. 6 (Hatefi and Abou-El-Hossein, 2022):
where, Lp is the couple constant of particles i and j, KB is the Brownian constant, and Tp is the temperature. The paramagnetic particles are oriented in the workpiece material randomly while following the Brownian motion as L < 1, where, by applying a magnetic field the amount of L is increased. When the workpiece material is in the presence of the applied magnetic field, the dipole-dipole interactions are decreased enough and the paramagnetic particles can get aligned to the externally applied magnetic field. Therefore, the number of linear structures of the particles (linear chains) is increased, and consequently, the thermal conductivity of the workpiece material is increased. Thermal conductivity enhancement could decrease the cutting temperature and improve the quality of surface finish (Hatefi and Abou-El-Hossein, 2022).
2.2 Development of the magnetic field assisted SPDT platform
In the experimental study, a Precitech Nanoform 250 Ultragrind machine tool was used for ultra-precision SPDT experiments. A rigid adjustable mechanical structure was developed from aluminum material. The developed structure enables precisely setting and securing the position of magnets, as well as the strength of the magnetic field at the cutting zone, during the diamond turning process. In the magnetic field assisted series of the experimental study, the developed mechanism was installed on the machine tool to enable the magnetic field assisted SPDT platform. In the developed mechanism, two neodymium MRERE673 rare Earth rectangular bar magnets with dimensions of 50*50*25 mm, were installed on the mechanical structure. The distance between the magnets was set to achieve an average magnetic flux density of 0.045 T around the cutting zone. Figure 3 presents the developed adjustable mechanical structure installed on the SPDT machine tool. By using this mechanism, a non-conventional magnetic field assisted SPDT platform was enabled that could apply a magnetic field with the strength of 0.045 T around the cutting zone.
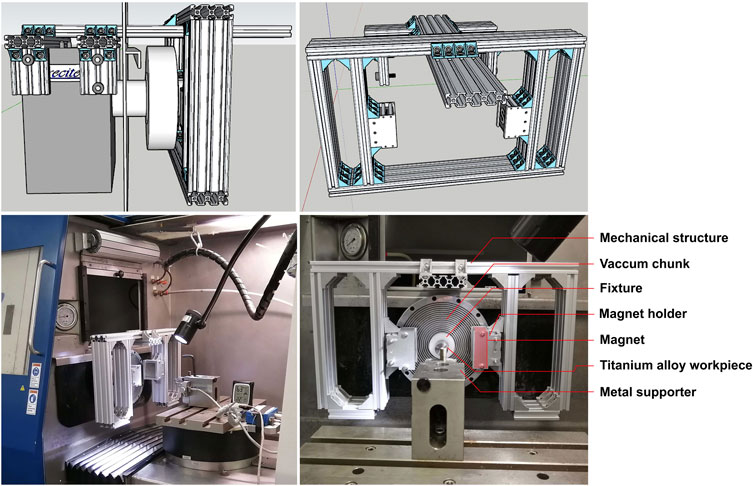
FIGURE 3. 3D model of the mechanical structure of the magnetic field assistance technique and the experimental setup of the mechanical structure installed on the Precitech Nanoform 250 Ultragrind machine tool.
2.3 Experimental study
In the experimental study, a cylindrical Ti-6Al-4V workpiece, with a diameter of 25 mm and a length of 50 mm was used. The Precitech Nanoform 250 Ultragrind machine tool was configured, the machining parameters were set, and a diamond tool was installed. An on-machine microscope was used to set the position of the diamond tool and the cutting edge of the diamond tool. In the experiments, a diamond tool, No. 50mNGi, with a rake angle of 0°, was used. The geometric parameters of the diamond tool and the components of the Ti-6Al-4V workpiece are presented in Table 1. The test samples for diamond turning were Ti-6Al-4V bars with a diameter of 25 mm and a height of 50 mm. The installation of the diamond tool on the machine tool and the on-machine setting of the rake angle of the diamond tool is illustrated in Figure 4. During the experiment, different machining conditions were used to compare the results of machining samples including the surface roughness generated, and to discover the effects of applying a strong magnetic field of 0.045 T on the quality of surface finish. Figure 5 illustrates the experimental stands of the non-magnetic purely mechanical and magnetic field assisted SPDT platforms used in the experiments.
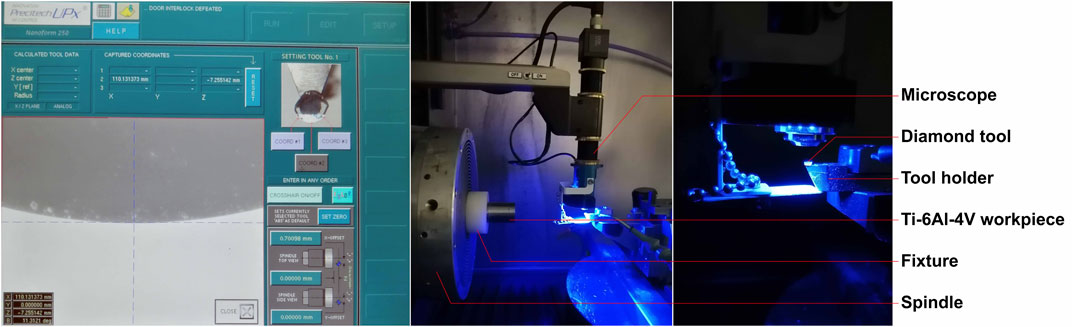
FIGURE 4. Installation of the diamond tool on the machine tool and on-machine setting of the rake angle.
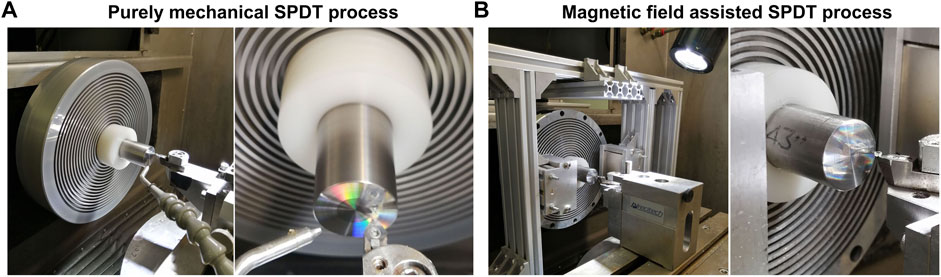
FIGURE 5. Experimental stand of the machining tests: (A) Purely mechanical SPDT platform; (B) Magnetic field assisted SPDT platform.
Moreover, the cutting parameters including cutting speed and feed rate were varied during the experimental investigation to evaluate the effects of magnetic field assistance on the optical surface finish in different machining conditions. A depth-of-cut of 4 µm remained constant through the cutting processes to avoid the size effect as well as high cutting temperature. The results of previous studies revealed that a feed rate of 4–8 mm/min and a depth-of-cut of 4 µm are optimum values for achieving the best possible quality of surface finish (Gopal and Rao, 2003; Sardinas et al., 2006; Yanda et al., 2010; Yip and To, 2018; Yip and To, 2019c). After determining the optimum cutting speed, the effect of increasing the feed rate on the surface roughness at the optimum cutting speed was evaluated. For this purpose, in all test groups, the machining test with optimum cutting speed was repeated while a feed rate of 8 mm/min was used at the optimum cutting speed.
The machining experiments were divided into four groups, as presented in Table 2. In the first machining series (S.1), the workpiece was cut in a non-magnetic dry cutting condition with air coolant. In the second series of the experiment (S.2), the workpiece was cut in a non-magnetic wet cutting condition with Kerosene. Subsequently, the mechanical structure and the magnets were installed on the machine tool for performing the magnetic field assisted machining series (S.3) and (S.4). In the third machining series (S.3), the workpiece was cut using the magnetic field assisted SPDT platform in dry cutting conditions with air coolant. In the last machining series (S.4), the workpiece was cut using magnetic field assisted SPDT platform in wet cutting conditions with Kerosene. Each series of machining tests were repeated two times. After each machining process, a direct measurement technique using a Form Talysurf PGI Dimension Machine by Taylor Hobson profilometer was employed to measure the mean deviation of the surface height from the mean profile line giving average roughness Ra values. This optical profilometer is a surface profiler that gives the 3D form a precise measurement in hollow and lofty aspherical lenses as well as modules, with a 50 nm repeatability and a form measurement capability of better than 0.1 µm. For the surface measurement, four particular locations were selected on the surface of the diamond turned samples for measuring the average surface roughness. The measurement was conducted three times on the locations. The average surface roughness measured in each machining test is presented in Table 2.
3 Results
The cutting conditions and the average surface roughness generated in the machining experiments are presented in Table 2. In the experiments, a feed rate of 4 mm/min and a depth-of-cut of 4 µm remained constant while varying the cutting speed from 750 to 3000 rpm. The results revealed that a cutting speed of 1500 (rpm) is the optimum cutting speed for SPDT of Ti-6Al-4V alloy. Figure 6 illustrates the graph generated using the obtained results to illustrate the effects of magnetic field assistance, coolant, and cutting speed on the quality of surface finish. It can be seen that in all machining conditions, the minimum surface roughness was generated at a cutting speed of 1500 rpm. Subsequently, a feed rate of 8 mm/min was set to examine the effect of feed rate on the quality of surface finish at the optimum cutting speed of 1500 rpm. Figure 7 illustrates the effect of feed rate on the quality of surface finish at a cutting speed of 1500 rpm.
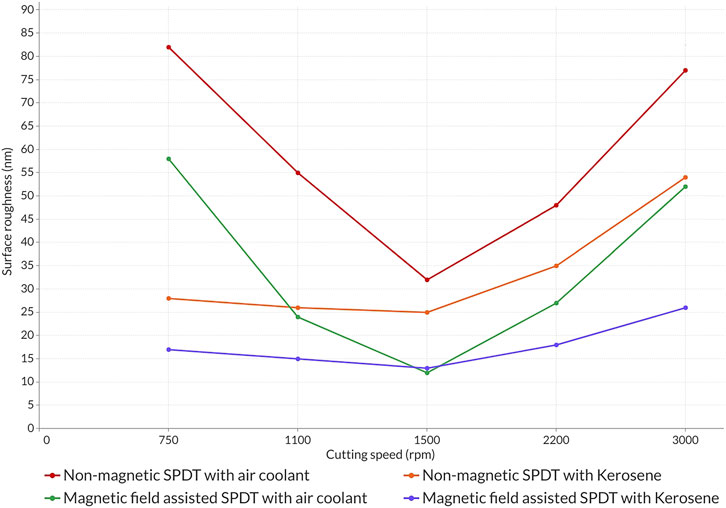
FIGURE 6. The average surface roughness generated in all machining series, with a feed rate of 4 mm/min and a depth-of-cut of 4 μm, at different cutting speeds.
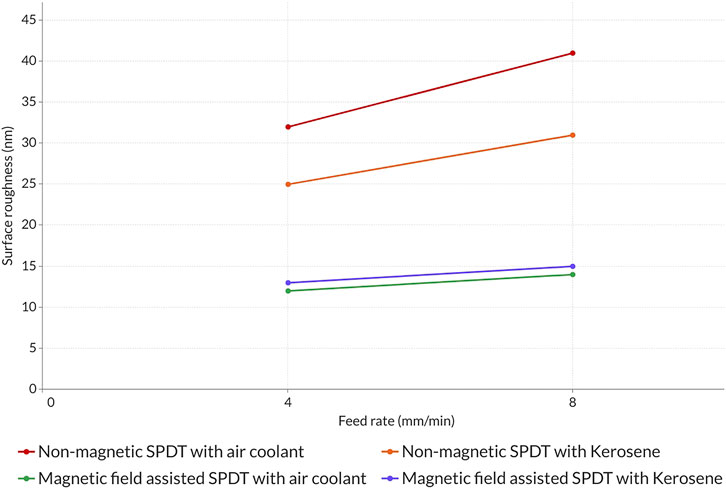
FIGURE 7. The effect of feed rate on the quality of surface finish with a depth-of-cut of 4 μm at a cutting speed of 1500 (rpm).
In general, it can be deduced from the obtained results that cutting parameters and coolant have direct effects on the quality of the surface finish. Moreover, in all machining conditions, the application of magnetic field assistance during the SPDT process could significantly improve the quality of the surface finish and minimize the surface roughness generated.
3.1 The effect of machining conditions and cutting parameters on surface roughness
Machining conditions, coolant, and cutting parameters have direct impacts on the quality of surface finish. To achieve the best possible quality of the surface finish, the optimum machining parameters and cutting conditions need to be determined and used. It is well-established that in ultra-precision machining, cutting parameters, including the cutting speed, feed rate, and depth-of-cut, have a direct influence on the quality of surface finish. These factors have a direct influence on different surface generation mechanisms, including passive vibration and the cutting temperature, and can induce diamond tool wear. By using suitable machining factors, cutting conditions could be improved and the quality of the surface finish could be enhanced (Hatefi and Abou-El-Hossein, 2020b; Goel et al., 2021). During the SPDT process, the relatively low and high cutting speeds cause high impact force from the workpiece applied to the diamond tool. Experimental studies revealed that a cutting speed of 1500 is proper to be used during the diamond cutting process (Yip and To, 2018). This effect can be seen in the results obtained in this experimental study where, in all machining series, the minimum surface roughness was generated at a cutting speed of 1500 rpm.
The effect of feed rate on the quality of surface finish at the optimum cutting speed of 1500 rpm was evaluated in each machining series. It can be seen in Figure 7 that in all machining conditions, increasing the feed rate could negatively affect the quality of the surface finish and increase the average surface roughness generated. A feed rate of 4 mm/min is the optimum rate compared to higher feeds.
In the S1 machining series, a purely mechanical SPDT platform with air coolant was used to machine Ti-6Al-4V alloy. It can be seen that a cutting speed of around 1500 rpm is optimum cutting speed with the best quality of surface finish generated. Lower/higher cutting speeds result in increasing the surface roughness. Moreover, increasing the cutting speed cause an increase in the cutting temperature which affects the quality of surface finish. In the S2 machining series, a purely mechanical SPDT with Kerosene was used to cut Ti-6Al-4V alloy in wet machining conditions. It can be seen that Kerosene could significantly reduce the generated surface roughness by decreasing the cutting temperature, when compared to the results of the S1 series of the experiment. However, the effect of increasing/decreasing the cutting speed on the quality of surface finish is still clear in the obtained results in S.2. In general, wet machining could reduce the cutting temperature and improve the machining conditions which results in improving the quality of surface finish. The effect of using Kerosene during diamond cutting can be seen in the results obtained in all machining tests in S.1 and S.2. It can be seen in S.1.3 and S.2.3 that in a non-magnetic SPDT of Ti-6Al-4V at the optimum cutting speed of 1500 rpm, using Kerosene could improve the quality of surface finish for 22.3%.
3.2 The effect of magnetic field assistance on the quality of surface finish
In this section, the results obtained in non-magnetic machining series S.1 and S.2 series are compared to the results obtained in magnetic field assisted machining series S.3 and S.4. Subsequently, the effect of wed machining conditions in magnetic field assisted SPDT of Ti-6Al-4V are assessed so that the optimum machining conditions and cutting parameters could be determined. Figure 8 illustrates the effect of magnetic field assistance on the quality of surface finish in all machining series presented in Table 2.
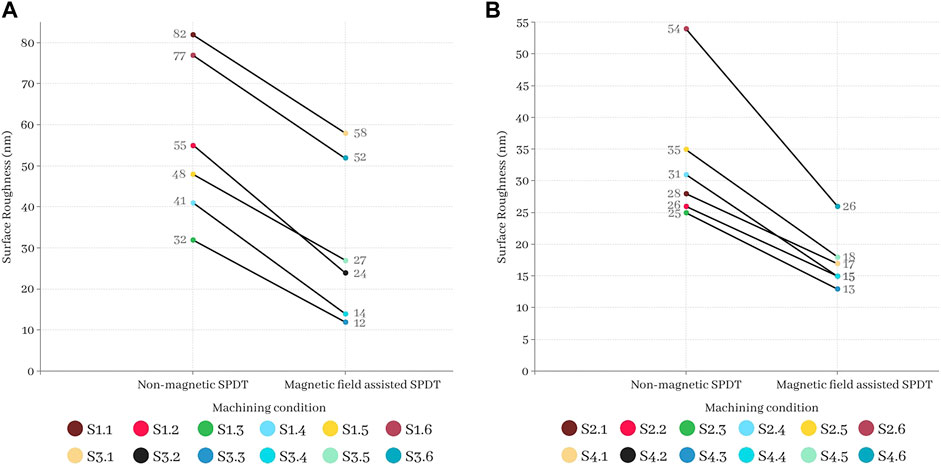
FIGURE 8. The effect of magnetic field assistance on the quality of surface finish in all machining series in Table 2: (A) Dry cutting conditions with air coolant; (B) Wet cutting conditions with Kerosene.
It can be seen in Figure 8 that in all machining conditions in S.1 and S.3 machining series with dry cutting conditions, applying a magnetic field could decrease the surface roughness generated. Same conclusion applies when comparing the results of S.2 and S.4 machining series in wet machining conditions, where significant improvement on the quality of surface finish can be seen in magnetic field assisted SPDT series. It can be seen that in S.1 machining series, S1.3 could obtain the best quality of surface finish, with an average surface roughness of 32.3 nm. In same machining conditions (S3.3), the application of magnetic field assistance could improve the quality of surface finish for 62.5% in dry machining conditions where, an average surface roughness of 12.1 nm was generated. In addition, it can be seen that in S.2 machining series, S2.3 could obtain the best quality of surface finish, with an average surface roughness of 25.1 nm. In same machining conditions (S4.3), that the application of magnetic field assistance could improve the quality of surface finish for 47% in wet machining conditions where, an average surface roughness of 13.3 nm was generated.
It can be seen that applying a magnetic field could significantly improve the quality of surface finish in both S.3 and S.4 machining series, when compared to non-magnetic machining series S.1 and S.2. Moreover, it can be seen in the results obtained in S.3 and S.4 that applying Kerosene during a magnetic field assisted SPDT could improve the surface roughness by decreasing the cutting temperature. However, at the optimum cutting speed of 1500 rpm, the application of magnetic field assistance in decreasing the cutting temperature can eliminate the need of wet machining using Kerosene. The results show that by using optimum cutting parameters in a magnetic field assisted SPDT, the minimum surface roughness in dry cutting conditions was achieved.
3.2.1 Optimum cutting conditions for magnetic field assisted SPDT of Ti-6Al-4V
Using optimum cutting parameters plays and important role in obtaining the minimum surface roughness by decreasing the cutting temperature. Although the application of coolant is important for decreasing the cutting temperature and improving the surface quality, the application of wet machining could potentially induce tool-tip-related and tool-workpiece passive vibrations during diamond cutting which induces surface roughness (Hatefi and Abou-El-Hossein, 2022). During the machining process, using optimum cutting conditions as well as magnetic field assistance can eliminate the need of wet machining using Kerosene. The application of magnetic field assistance in SPDT could improve the machining conditions and eliminate the need of using Kerosene by improving the cutting stability and enhancing the thermal conductivity of the workpiece material which results in reducing the cutting temperature.
Figure 9 presents the effect of applying a magnetic field of 0.045 T on the quality of surface finish at a cutting speed of 1500 (rpm) in dry and wet machining conditions using a feed rate of 4 and 8 mm/min. The application of magnetic field assistance could improve the quality of surface finish by 62.5% in S3.3, 64.9% in S3.4, 47% in S4.3, and 51.5% in S4.4. The minimum surface finish was achieved in S3.3 where the Ti-6Al-4V alloy was cut under dry cutting conditions at a cutting speed of 1500 rpm with a feed rate of 4 mm/min. The results of the experimental tests revealed that by using optimum machining parameters in test series S3.3, dry ultra-precision SPDT of Ti-6Al-4V with minimum surface roughness, down to 12 nm, could be achieved. It can be seen in Figure 9 that the best quality surface was machined in S3.3 with an average surface roughness of 12.1 nm.
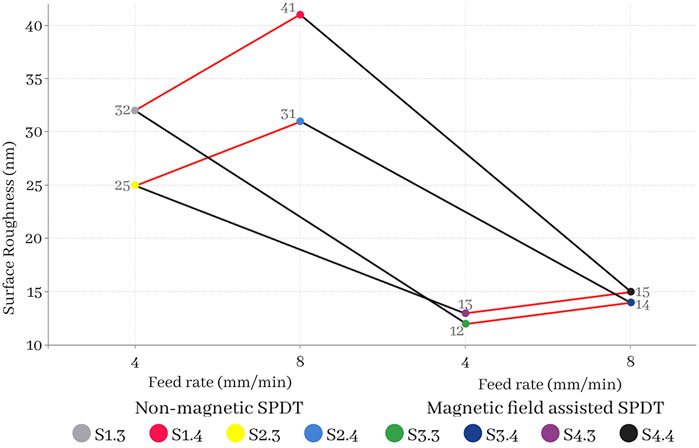
FIGURE 9. The effect of magnetic field assistance on optical surface finish in SPDT of Ti-6Al-4V alloy at a cutting speed of 1500 (rpm) in dry and wet machining conditions as presented in Table 2.
4 Discussion
Ultra-precision SPDT of Ti-6Al-4V is associated with poor machinability with relatively low-quality surface finish, especially in dry machining conditions. Titanium alloys are difficult-to-cut materials with low machinability using SPDT technology. It is difficult to achieve a high-quality surface, with relatively low surface roughness, when ultra-precision SPDT technology is used to machine titanium alloys. High tool wear and low surface quality, with a surface roughness of around 20–30 nm are expected in ultra-precision SPDT of Ti-6Al-4V (Khalil et al., 2022; Lou and Wu, 2022). Titanium alloys have low thermal conductivity and the generated cutting heat during the diamond cutting of titanium alloy is trapped at the cutting zone due to low dissipation of the heat outside the cutting zone. This effect increases the cutting temperature and negatively affects the quality of the surface finish (Bordin et al., 2015). The cutting temperature is expected to increase with increasing the cutting speed while decreasing the optical surface quality (Khalil et al., 2022). This effect can be seen in the obtained results of the experimental tests.
Recently different non-conventional techniques have been used during the machining of Ti-6Al-4V to improve the quality of the surface finish and machining conditions. Unconventional liquids and fluids, including propylene glycol, alkaline soap water, and sodium nitrite, are a category of solutions used in the advanced manufacturing of Ti-6Al-4V alloy (Mukhopadhyay et al., 2018; Mukhopadhyay and Kundu, 2019; Mukhopadhyay and Kundu, 2021). Non-conventional machining techniques, including hot machining, magnetic field assistance, and nitrogen cold plasma jet, are another category of machining techniques, used during the machining of titanium alloys to enhance the machining conditions and the outcome of the process in terms of surface finish (Bordin et al., 2017; Hatefi and Abou-El-Hossein, 2020a; Agrawal et al., 2021). Among the recent solutions used during the advanced manufacturing of titanium alloys, the application of magnetic field assistance proved to be a suitable solution for sustainable manufacturing of titanium alloys.
The results of previously performed experimental studies show that applying a magnetic field around the cutting zone could reduce the machine tool and cutting tool related passive vibrations and decrease the cutting temperature by reducing the material conductivity of the workpiece material (Yip, 2018; Yip and To, 2018; Yip and To, 2019b). By improving these two factors, cutting conditions and the surface generation mechanisms could be improved. This would result in significant improvement in terms of generated surface roughness. In the previously performed studies, magnetic field assisted SPDT platform has been used for ultra-precision manufacturing of titanium alloys. In the performed experimental studies, strong magnetic fields, with magnetic flux density of 0.01 T and 0.02 T, were used. The results of performed studies revealed that applying a magnetic field around the cutting zone could significantly improve the optical surface finish. Moreover, the results of experimental tests show a correlation between the intensity of the applied magnetic field and the optical surface finish quality. It has been revealed that increasing the intensity of the applied magnetic field can positively improve the cutting conditions and improve the optical surface generation quality. The average surface roughness generated in magnetic field assisted SPDT of Ti-6Al-4V alloy is between 10 and 20 nm. The results of the performed experimental studies on the ultra-precision SPDT of titanium alloys using magnetic field assistance are presented in Table 3. Figure 10 compares the results of ultra-precision SPDT of Ti-6Al-4V with average surface roughness generated.
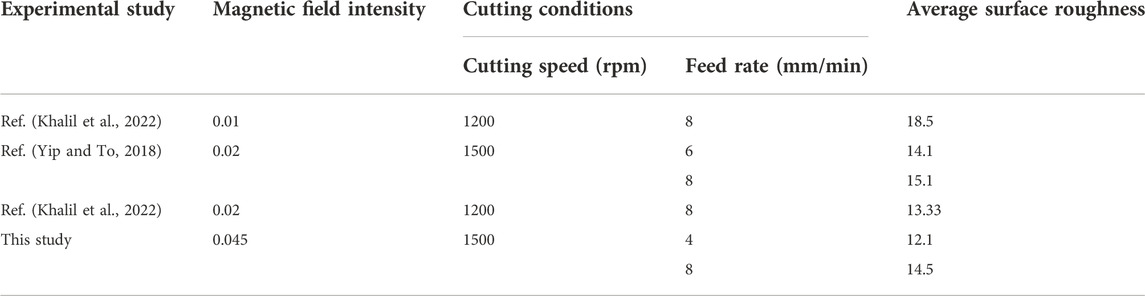
TABLE 3. Evaluation of the effect of applying a magnetic field on the quality of surface finish: The results of experimental studies and improvement of the generated surface roughness compared to turned samples without magnetic field assistance in dry cutting conditions.

FIGURE 10. Comparing the results of the ultra-precision SPDT of Ti-6Al-4V with minimum surface roughness: The magnetic field intensity and the average of generated surface roughness.
In this experimental study, by using a stronger magnetic field, with an average magnetic flux density of 0.045 T at the cutting zone, the quality of the optical surface finish has been improved. The results of this experimental investigation show that in the presence of a magnetic field of 0.045 T, the quality of the optical surface finish and machining conditions could be improved. It can be seen in S.3.3 and S3.4 machining series that in similar cutting conditions, by using a feed rate of 8 mm/min an average surface roughness of 14.5 nm, and by using a feed rate of 4 mm/min an average surface roughness of 12.1 nm could be generated. The results of the experimental study show that using optimum cutting conditions and a magnetic field of 0.045 T result in improving the quality of the finished surface in dry machining conditions.
5 Conclusion
The application of non-conventional machining techniques during ultra-precision SPDT technologies has been emerging. These techniques have shown positive impacts on the optical surface generation mechanisms while improving the quality of the optical surface finish. Magnetic field assistance is a low-cost and contactless solution with passive elements. This technique has shown promising results in terms of improving the machining conditions and optical surface generation mechanisms. This technique could reduce the cutting temperature and improve the diamond cutting stability by damping passive vibrations. Applying a magnetic field has shown no destructive effect on the optical surface generation mechanisms. Magnetic field assistance can significantly improve the machinability of titanium alloys without requiring advanced equipment and extra energy resources. The results of this experimental study show that the application of magnetic field assistance could improve the quality of surface finish up to 62.5% in a dry cutting condition. Therefore, using this technique could eliminate the need for coolant/lubrication solutions and reduce the environmental issues of using cutting fluid/lubricants in the SPDT process. The application of magnetic field assistance could promote the sustainability of ultra-precision SPDT of titanium alloys.
In the future studies, the magnetic assistance could be used as one of the assisting techniques in hybrid SPDT platforms. This technique could compensate for the negative effects caused by active vibration and hot machining techniques, thus an ideal solution to be used in future hybrid SPDT technologies. Also, more research needs to be performed to fully understand the correlation between the intensity of the applied magnetic field, cutting conditions, and surface generation mechanisms. Supermagnete, 2021.
Data availability statement
The original contributions presented in the study are included in the article/supplementary material, further inquiries can be directed to the corresponding author.
Author contributions
Conceptualization, SH; methodology, SH, and KA-E-H; fabrication of mechanism, SH; data generation and analysis, SH, and KA-E-H; writing original draft, SH; final review and editing, SH and KA-E-H; All authors have read and agreed to the published version of the manuscript.
Acknowledgments
The authors would like to thank Research Development of Nelson Mandela University for their support of this research.
Conflict of interest
The authors declare that the research was conducted in the absence of any commercial or financial relationships that could be construed as a potential conflict of interest.
Publisher’s note
All claims expressed in this article are solely those of the authors and do not necessarily represent those of their affiliated organizations, or those of the publisher, the editors and the reviewers. Any product that may be evaluated in this article, or claim that may be made by its manufacturer, is not guaranteed or endorsed by the publisher.
References
Agrawal, C., Wadhwa, J., Pitroda, A., Pruncu, C. I., Sarikaya, M., and Khanna, N. (2021). Comprehensive analysis of tool wear, tool life, surface roughness, costing and carbon emissions in turning Ti–6Al–4V titanium alloy: Cryogenic versus wet machining. Tribol. Int. 153, 106597. doi:10.1016/j.triboint.2020.106597
Arrazola, P.-J., Garay, A., Iriarte, L.-M., Armendia, M., Marya, S., and Le Maitre, F. (2009). Machinability of titanium alloys (Ti6Al4V and Ti555. 3). J. Mater. Process. Technol. 209, 2223–2230. doi:10.1016/j.jmatprotec.2008.06.020
Bordin, A., Bruschi, S., Ghiotti, A., and Bariani, P. (2015). Analysis of tool wear in cryogenic machining of additive manufactured Ti6Al4V alloy. Wear 328, 89–99. doi:10.1016/j.wear.2015.01.030
Bordin, A., Sartori, S., Bruschi, S., and Ghiotti, A. (2017). Experimental investigation on the feasibility of dry and cryogenic machining as sustainable strategies when turning Ti6Al4V produced by Additive Manufacturing. J. Clean. Prod. 142, 4142–4151. doi:10.1016/j.jclepro.2016.09.209
Chabot, T., Brousseau, D., Auger, H., and Thibault, S. (2022). Surface topography in single-point diamond turning of image slicers. Opt. Eng. 61, 035104. doi:10.1117/1.oe.61.3.035104
Ebrahimi, B., Khamesee, M. B., and Golnaraghi, F. (2010). Permanent magnet configuration in design of an eddy current damper. Microsyst. Technol. 16, 19–24. doi:10.1007/s00542-008-0731-z
Goel, B., Singh, S., Sarepaka, R. V., Mishra, V., Khatri, N., Aggarwal, V., et al. (2021). Diamond turning of optical materials: A review. Int. J. Mach. Mach. Mater. 23, 160–190. doi:10.1504/ijmmm.2021.114016
Gopal, A. V., and Rao, P. V. (2003). Selection of optimum conditions for maximum material removal rate with surface finish and damage as constraints in SiC grinding. Int. J. Mach. Tools Manuf. 43, 1327–1336. doi:10.1016/s0890-6955(03)00165-2
Hatefi, S., and Abou-El-Hossein, K. (2022). Review of magnetic-assisted single-point diamond turning for ultra-high-precision optical component manufacturing. Int. J. Adv. Manuf. Technol. 120, 1591–1607. doi:10.1007/s00170-022-08791-3
Hatefi, S., and Abou-El-Hossein, K. (2020a). Review of non-conventional technologies for assisting ultra-precision single-point diamond turning. Int. J. Adv. Manuf. Technol. 111, 2667–2685. doi:10.1007/s00170-020-06240-7
Hatefi, S., and Abou-El-Hossein, K. (2020b). Review of single-point diamond turning process in terms of ultra-precision optical surface roughness. Int. J. Adv. Manuf. Technol. 106, 2167–2187. doi:10.1007/s00170-019-04700-3
Hatefi, S. (2021). Hybrid single-point diamond turning process for ultra-high-precision of titanium alloy. Port Elizabeth, South Africa: Nelson Mandela University.
Karmiris-Obratański, P., Karkalos, N. E., Kudelski, R., and Markopoulos, A. P. (2022). Experimental study on the effect of the cooling method on surface topography and workpiece integrity during trochoidal end milling of Incoloy 800. Tribol. Int. 176, 107899. doi:10.1016/j.triboint.2022.107899
Khalil, A. K., Yip, W. S., and To, S. (2022). Theoretical and experimental investigations of magnetic field assisted ultra-precision machining of titanium alloys. J. Mater. Process. Technol. 300, 117429. doi:10.1016/j.jmatprotec.2021.117429
Kumar, J. (2013). Ultrasonic machining—A comprehensive review. Mach. Sci. Technol. 17, 325–379. doi:10.1080/10910344.2013.806093
Lajvardi, M., Moghimi-Rad, J., Hadi, I., Gavili, A., Isfahani, T. D., Zabihi, F., et al. (2010). Experimental investigation for enhanced ferrofluid heat transfer under magnetic field effect. J. Magnetism Magnetic Mater. 322, 3508–3513. doi:10.1016/j.jmmm.2010.06.054
Lou, Y., and Wu, H. (2022). Effect of parameters on surface roughness during the ultra-precision polishing of titanium alloy. PloS one 17, e0272387. doi:10.1371/journal.pone.0272387
Molnar, V., and Szabo, G. (2022). Designation of minimum measurement area for the evaluation of 3D surface texture. J. Manuf. Process. 83, 40–48. doi:10.1016/j.jmapro.2022.08.042
Mukhopadhyay, M., Kundu, P. K., and Das, S. (2018). Experimental investigation on enhancing grindability using alkaline-based fluid for grinding Ti-6Al-4V. Mater. Manuf. Process. 33, 1775–1781. doi:10.1080/10426914.2018.1476759
Mukhopadhyay, M., and Kundu, P. K. (2021). Ecological and economical processing of Ti-6Al-4V with an augmentation in grindability. Sādhanā 46, 196–210. doi:10.1007/s12046-021-01732-y
Mukhopadhyay, M., and Kundu, P. K. (2019). Evaluating application potentiality of unconventional fluids for grinding Ti-6Al-4V using alumina wheel. Mater. Manuf. Process. 34, 1151–1159. doi:10.1080/10426914.2019.1615086
Nkurikiyimfura, I., Wang, Y., and Pan, Z. (2013). Heat transfer enhancement by magnetic nanofluids—A review. Renew. Sustain. Energy Rev. 21, 548–561. doi:10.1016/j.rser.2012.12.039
Peruri, S. R., and Chaganti, P. K. (2019). A review of magnetic-assisted machining processes. J. Braz. Soc. Mech. Sci. Eng. 41, 450. doi:10.1007/s40430-019-1944-z
Sardinas, R. Q., Santana, M. R., and Brindis, E. A. (2006). Genetic algorithm-based multi-objective optimization of cutting parameters in turning processes. Eng. Appl. Artif. Intell. 19, 127–133. doi:10.1016/j.engappai.2005.06.007
Singh, R., and Khamba, J. (2006). Ultrasonic machining of titanium and its alloys: A review. J. Mater. Process. Technol. 173, 125–135. doi:10.1016/j.jmatprotec.2005.10.027
Sodano, H. A., and Bae, J.-S. (2004). Eddy current damping in structures. Shock Vib. Dig. 36, 469–478. doi:10.1177/0583102404048517
Supermagnete (2021). How do you calculate the magnetic flux density. Available: https://www.supermagnete.de/eng/faq/How-do-you-calculate-the-magnetic-flux-density#formula-for-block-magnet-flux-density (Accessed.
Venkatesan, K., Ramanujam, R., and Kuppan, P. (2014). Laser assisted machining of difficult to cut materials: Research opportunities and future directions-a comprehensive review. Procedia Eng. 97, 1626–1636. doi:10.1016/j.proeng.2014.12.313
Xu, W., Huang, S., Chen, F., Song, J., and Liu, X. (2014). Diamond wear properties in cold plasma jet. Diam. Relat. Mater. 48, 96–103. doi:10.1016/j.diamond.2014.07.008
Xu, W., Liu, X., Song, J., Wu, L., and Sun, J. (2012). Friction and wear properties of Ti6Al4V/WC-Co in cold atmospheric plasma jet. Appl. Surf. Sci. 259, 616–623. doi:10.1016/j.apsusc.2012.07.086
Yanda, H., Ghani, J., Rodzi, M., Othman, K., and Haron, C. (2010). Optimization of material removal rate, surface roughness and tool life on conventional dry turning of FCD700. Int. J. Mech. Mater. Eng. 5, 182–190.
Yip, W. S. (2018). Magnetic field assisted ultra-precision machining for improving machinability of titanium alloys.
Yip, W., and To, S. (2019a). Effects of magnetic field on microstructures and mechanical properties of titanium alloys in ultra-precision diamond turning. Mat. Res. Express 6, 056553. doi:10.1088/2053-1591/ab069e
Yip, W., and To, S. (2017a). Reduction of material swelling and recovery of titanium alloys in diamond cutting by magnetic field assistance. J. Alloys Compd. 722, 525–531. doi:10.1016/j.jallcom.2017.06.167
Yip, W., and To, S. (2019b). Reduction of tool tip vibration in single-point diamond turning using an eddy current damping effect. Int. J. Adv. Manuf. Technol. 103, 1799–1809. doi:10.1007/s00170-019-03457-z
Yip, W., and To, S. (2018). Sustainable manufacturing of ultra-precision machining of titanium alloys using a magnetic field and its sustainability assessment. Sustain. Mater. Technol. 16, 38–46. doi:10.1016/j.susmat.2018.04.002
Yip, W., and To, S. (2019c). Sustainable ultra-precision machining of titanium alloy using intermittent cutting. Int. J. Precis. Eng. Manuf. -Green. Tech. 7, 361–373. doi:10.1007/s40684-019-00078-5
Yip, W., and To, S. (2017b). Tool life enhancement in dry diamond turning of titanium alloys using an eddy current damping and a magnetic field for sustainable manufacturing. J. Clean. Prod. 168, 929–939. doi:10.1016/j.jclepro.2017.09.100
Yuan, J., Lyu, B., Hang, W., and Deng, Q. (2017). Review on the progress of ultra-precision machining technologies. Front. Mech. Eng. 12, 158–180. doi:10.1007/s11465-017-0455-9
Zhang, S., To, S., Wang, S., and Zhu, Z. (2015). A review of surface roughness generation in ultra-precision machining. Int. J. Mach. Tools Manuf. 91, 76–95. doi:10.1016/j.ijmachtools.2015.02.001
Zhang, Y., Zhou, Z., Wang, J., and Li, X. (2013). Diamond tool wear in precision turning of titanium alloy. Mater. Manuf. Process. 28, 1061–1064. doi:10.1080/10426914.2013.773018
Keywords: ultra-precision machining, magnetic field assisted machining, non-conventional machining, sustainable manufacturing, advanced manufacturing
Citation: Hatefi S and Abou-El-Hossein K (2022) Experimental investigation on the effects of magnetic field assistance on the quality of surface finish for sustainable manufacturing of ultra-precision single-point diamond turning of titanium alloys. Front. Mech. Eng 8:1037372. doi: 10.3389/fmech.2022.1037372
Received: 05 September 2022; Accepted: 07 November 2022;
Published: 17 November 2022.
Edited by:
Nicola Ivan Giannoccaro, University of Salento, ItalyReviewed by:
Manish Mukhopadhyay, Meghnad Saha Institute of Technology, IndiaPanagiotis Karmiris-Obratański, AGH University of Science and Technology, Poland
Copyright © 2022 Hatefi and Abou-El-Hossein. This is an open-access article distributed under the terms of the Creative Commons Attribution License (CC BY). The use, distribution or reproduction in other forums is permitted, provided the original author(s) and the copyright owner(s) are credited and that the original publication in this journal is cited, in accordance with accepted academic practice. No use, distribution or reproduction is permitted which does not comply with these terms.
*Correspondence: Shahrokh Hatefi, c2hhaHJva2guaGF0ZWZpQG1hbmRlbGEuYWMuemE=