- 1Department of Mechanical Engineering, HITEC University, Taxila Cantt, Pakistan
- 2Division of Machine Learning, Luleå University of Technology, Luleå, Sweden
- 3Structural Engineering Unit, Tampere University, Tampere, Finland
In this study, the tribological properties of a green lubricant synthesized from cottonseed oil through a two-step transesterification process are investigated, with a specific focus on the maximum throughput of the second step that involves the reaction of cottonseed methyl ester with 2-ethyl-1-hexanol alcohol and a titanium isopropoxide (TIS) catalyst. The research centers on evaluating the physiochemical characteristics of this biolubricant and comparing them with those of commercial oil (5W30) and the ISO VG40 standard. Furthermore, the influence of crucial process variables, such as temperature, pressure, reaction time, and TIS catalyst concentration, is examined by analyzing variance in experimental data. Fourier transform infrared (FTIR) analysis is employed to identify functional groups, particularly emphasizing the impact of temperature and reaction time. By optimizing the second transesterification process under specific conditions (pressure = 19.42 mmHg, temperature = 175°C, catalyst concentration = 0.63%, and reaction time = 4.0 h), a cottonseed oil-based biolubricant is successfully produced, exhibiting properties comparable to those of commercial mineral lubricants. Notably, the findings reveal significant enhancements in the coefficient of friction (CoF) with a 49% reduction and wear resistance with a maximum 19% reduction. This study contributes valuable insights into optimizing biolubricant production derived from cottonseed oil through two-step transesterification, emphasizing its novel potential in improving frictional and wear characteristics.
1 Introduction
Despite having harmful ecological characteristics, fossil-based lubricants have been used for centuries. Elevated environmental concerns invite an entirely new optimization to synthesize environmentally friendly “green” machine oils not based on fossil extraction. However, to replace traditional massively used lubricants, the tribological performance of a green lubricant is critical. Friction is one of the crucial tribological characteristics because of energy losses in tribological contact. Chemically modified vegetable oils, as a class, have gained a reputation for thermo-oxidative stability with added environmental benefits. The primary challenge in their widespread use is the need for suitable lubrication performance for specific applications.
The terminology ‘biolubricant’ applies to all lubricants that are environment friendly, implying that they are biodegradable and nontoxic to the environment. Natural oils, including animal and vegetable oils (VO), are rarely used because they are highly unstable at high temperatures and harmful to equipment and machines. Synthetic oils obtained after chemical synthesis are nontoxic and biodegradable. They are obtained by various routes, mainly by obtaining straight or branched-chain monoesters, diesters, triesters, and polyol esters from vegetable oils. The conversion of triglyceride to esters can be followed or preceded by one or more transesterification reactions to improve production, such as hydrogenation and epoxidation (Cecilia et al., 2020). Different natural oils were used as raw materials to develop sustainable biodiesel and biolubricant as an alternative to fossil fuels (Panchal et al., 2017; Carlucci et al., 2019; Sharma and Sachan, 2019; Djomdi et al., 2020; Encinar et al., 2020; Gul et al., 2020; Ge et al., 2022; Rokni et al., 2022; Shahabuddin et al., 2022; Ulanova et al., 2022; Unruean et al., 2022). The conversion of triglycerides of Vegetable oil into biodiesel is through a transesterification process. This chemical reaction with Titanium dioxide, a heterogeneous catalyst, increases fatty acid methyl esters (FAME) (Carlucci et al., 2019). Adding 7.5% biolubricant to commercial lubricant showed the best wear reduction and viscosity stability results. This research implies that biolubricants derived from vegetable oils or fats can be a promising alternative to mineral lubricants due to their environmental benefits and comparable performance (Shahabuddin et al., 2022).
The tribological performance of green lubricant Karanja oil trimethylolpropane ester (KOTMPE) as an automotive lubricant was tested after blending. The transesterification process was conducted under trimethylolpropane (TMP), an acid catalyst (Sharma and Sachan, 2019). Blending TMP-based biolubricant from cottonseed up to 10% in commercial oil (SAE-40) showed the lowest friction and wear (Gul et al., 2020). Fatty acid ethyl esters (FAEEs) extracted from VO reacted with ethanol with a catalyst, producing promising bio-based chemicals. However, limited conversion and production are obtained in the conventional synthesis due to the low boiling point of ethanol. This research demonstrates the high production rate of FAEEs from palm oil, soybean, and rice bran at elevated temperatures up to 200°C, with a molar ratio of 6:1 and 1wt% catalyst (Unruean et al., 2022). Different synthesis methods were developed for green lubricant products by synthesizing sunflower oil FAME with dihydric alcohols (Ulanova et al., 2022).
Transesterification of castor seed and rapeseed methyl esters was transformed with three different alcohols and TIS as a catalyst. Temperature, catalyst concentration, and molar ratio were studied to optimize the process. The transesterification reaction with titanium isopropoxide was completed in 2 hours with 93% conversion (Encinar et al., 2020). To increase the chemical reaction of TMP triesters synthesized from camelina oil, irradiation was applied via microwave. The optimal settings for independent factors were 1.4%wt catalyst concentration, 1:3.5 M ratio, and 67.8 min reaction time (Rokni et al., 2022). Cottonseed oil has a composition of oleic (19.4%), linoleic (53.2%), linolenic (0.5%), and palmitic (23.7%) (Djomdi et al., 2020), depending upon the harvesting conditions and consequently, affects the characteristics of resulting bio lubricant after transesterification. The reactants of the transesterification reaction are ester and alcohol which occur in the presence of a catalyst. Transesterification produces a different form of esters by interchanging the alkyl group. Further analysis methods must be used to determine the complexity of produced ester (Panchal et al., 2017). The biodiesel extracted from palm oil vegetable oil (CPO) was investigated for the engine performance of the rail diesel engine operated with different blend ratios of 10%, 30%, and 50% at 750 rpm, 1500 rpm, and 2250 rpm speeds. It was found that a decrease in the cylinder peak pressure along with a reduction in emission characteristics for 10% and 30% blends by volume (Ge et al., 2022). The synthesis of waste cooking oil without a catalyst was studied with a maximum yield of 94.16% at 7.02 bar pressure and 274.8°C reaction temperature. Temperature was found to be the most critical factor for supercritical transesterification (Ahmed et al., 2023). Viscosity modifiers synthesized from cotton were used as an additive in polyalphaolefin base oil. The tribological performance of these nanocrystals, 2% by wt., reduced CoF by 30% (Li et al., 2019). The presence of fatty acid in biolubricant forms thin stable tribolayers on the metallic surfaces of sliding contact, reducing CoF and wear. Biolubricants under severe lubrication conditions are promising candidates to be blended with engine oil. A blend of palm and soybean oils with mineral oil was tested on the Phoenix Tribology/Plint TE77 test rig and found that the blend of palm oil showed a 25% improvement. In contrast, the mix of soybean showed a 27% improvement in CoF at high pressure and temperature and reciprocating.
Biolubricant extracted from cottonseed and soybean oil was synthesized with TMP-triesters and blended with a ratio of 4:1. Further, the blend was also treated with viscosity modifiers Ethylene–vinyl acetate copolymer and ethyl cellulose. The study reveals that EC was more effective in mixed and boundary lubrication. It was also mentioned that the most critical viscosity increments correspond to castor oil/EC blends (i.e., 125%, at 40°C) (Quinchia et al., 2014). Bio lubricant extracted from cottonseed and soybean oil was synthesized with TMP-triesters and further treated with extreme pressure and antiwear (EP/AW) additives at a rate of 1.5% w/w frictional properties were compared with mineral oil by employing four-ball tests. Sodium methoxide was used as a catalyst (Dodos et al., 2010). However, no one synthesized the cottonseed oil with titanium isopropoxide to produce bio lubricant and optimize the process parameters for maximum yield. Previous studies have shown that the viscosity of bio lubricant is greatly influenced by the number of carbon and branching in the alcohol chain structure (Saboya et al., 2017; Cecilia et al., 2020). 2ethyl-1hexanol alcohol was investigated for its complex chain structure for the second transesterification phase by reacting with castor FAME (Encinar et al., 2020). TIS as a catalyst was selected and studied for the yield of biolubricant because of its effectiveness. The use of titanium catalyst was also investigated in creating carbon-based and TiO2 thin film coating developed through various coating techniques. In addition, TIS can be used as a precursor of other catalysts (Mahata et al., 2015; Spiridonova et al., 2019; Encinar et al., 2020; Jedrzejczak et al., 2020). The effects of three different catalysts: TIS, titanium butoxide (TBT), and antimony trioxide (Sb2O3), on the two-step synthesis of Poly (ethylene vanillate) (PEV) through the polycondensation process were investigated. The effectiveness of all the catalysts was found, resulting in polyesters with high thermal stability. TIS during the esterification stage shows superior catalytic activity.
The prospective utilization of cottonseed-derived biolubricants as a feasible substitute for fossil-based lubricants in internal combustion engines (ICE) exhibits significant potential in mitigating urgent environmental issues. Biolubricants present a variety of benefits, such as a decrease in carbon emissions, which aligns with sustainable development goals set by the UN, SDG 13 (Climate Action). Additionally, they exhibit enhanced biodegradability in accordance with SDG15 (Life on Land). Furthermore, their usage reduces dependence on finite fossil resources, thereby supporting SDG 12 (Responsible Consumption and Production).
Numerous research investigations have been conducted to examine the application of biodegradable biolubricants (BBL) in internal combustion engines (IC), with a specific focus on their blending with mineral oil (MO) or pure vegetable oils such as palm oil (PO) and cottonseed oil (CS). According to the study conducted by (Willing, 2001), it was shown that BBL demonstrated a notably higher rate of biodegradation in comparison to MO. In their study, (Schramm, 2003), performed on-road and chassis dynamometer tests on BBL. The results indicated no statistically significant impacts on wear or exhaust gas emissions. However, a minor decrease in efficiency and an increase in NOx emissions were observed. (Bekal and Bhat, 2012) observed that friction losses were comparatively reduced in BBL mixes compared to other MO blends. Furthermore, Reddy (Reddy et al., 2014) observed comparable performance in internal combustion engines when utilizing biodiesel combined with palm oil (PO) and pure mineral oil (MO), while also observing decreased emissions in the blended fuel. In their study, Hassan (Hassan AB et al., 2006) investigated the tribological properties exhibited by blends of PO-MO. The researchers discovered several favorable qualities that contribute to the overall environmental friendliness of these blends. According to a study conducted by Ravinarayana Bhat (Das and Lingfa, 2015), it was found that the performance of Karanja oil and mineral mix oil was superior to that of MO (a reference oil) in four-stroke diesel engines. In a recent study, Gulab (Siraskar, 2018) investigated the utilization of pure cottonseed oil in compression ignition (CI) engines. The findings of this study demonstrated promising results initially. However, the author also recognized the necessity of chemical modification in order to ensure long-term effectiveness. The aforementioned experiments collectively demonstrate the possibility of BBL and different vegetable oil blends as viable replacements for lubricants in internal combustion engines. These alternatives have the advantage of being ecologically benign, as they result in lower emissions and improved tribological properties compared to traditional lubricants. Gul (Gul et al., 2020) conducted a prior investigation on a biolubricant derived from cottonseed oil. The performance of the produced lubricant was evaluated by Gul et al. via its application in an automated diesel engine, focusing on examining its tribo-behaviors. The researchers discovered that in the beginning, the pure CS oil had favorable characteristics in comparison to SAE 20W40 oil for brief periods of 96 h. However, prolonged utilization resulted in deterioration and the development of a substance resembling gum, leading to a decline in engine performance. Gulab Siraskar (Siraskar et al., 2021) carried out an in-depth investigation to evaluate the performance and emissions characteristics of cottonseed oil that has been modified with trimethylolpropane ester for use as a lubricant in compression ignition engines. The research presents an analysis of gas emissions, including hydrocarbons (HC) carbon dioxide (CO2) nitrogen oxides (NOx), and carbon monoxide (CO), in comparison to mineral lubricants. Interestingly, the study reveals that both types of lubricants show results in terms of brake efficiency (BTE) and brake-specific fuel consumption (BSFC) with recorded BSFC at 0.6 kg/kW h. Notably, the findings emphasize the environmentally friendly qualities of biobased lubricants as they significantly reduce the release of harmful gases. Specifically, the recorded HC emission is 45 ppm, NOx emission is 590 ppm, CO2 emission is 2.99 ppm, and maximum CO emission is 0.16 ppm. This research provides insights into the potential of cottonseed oil-based lubricants to reduce impact while maintaining engine efficiency.
This study explores the properties of environmentally friendly biolubricant made from cottonseed oil. The main objectives of the research are threefold: firstly, to evaluate the innovation and novelty of this biolubricant with TIS; secondly, to optimize the production processes by investigating and tuning key factors, like temperature, pressure, reaction time, and catalyst concentration to achieve maximum yield of chemical synthesis; and lastly to conduct a tribological test of biolubricant compare to synthetic motor oil. This research highlights the potential of biolubricant as both a high-performance lubricant and emphasizes the importance of a conscious approach in developing lubrication solutions within sustainable technology.
The primary objective of this experimental investigation is to evaluate the friction and wear of biolubricant extracted from native cottonseed by a double transesterification process using a TIS catalyst. This green lubricant was prepared through two-step chemical modification and a mechanical process extracting raw cottonseed oil. In the first transesterification step, the raw cottonseed oil was treated with methanol, a molar ratio of 6:1, and Potassium hydro-oxide produced FAMEs (fatty acid methyl esters). In the second step, biolubricant was produced by reacting FAMEs with isooctanol alcohol treated with 1% TIS as a catalyst, which is the novel contribution of this work. Vacuum distillation was carried out at 170°C at 26 mmHg for purification purposes, and methanol was collected as a residual. Four crucial independent factors temperature of bioreactor, vacuum pressure, catalyst concentration, and reaction time were studied to maximize the yield. Regionally available cottonseed oil is used, and no additives such as viscosity index improver, pour point depressant, or antiwear additives were added to the base oil. A comparison is made between the frictional behavior of a commercially available mineral oil (MO), SAE 5W30, engine oil, and a newly developed green lubricant.
2 Two-step transesterification process
A two-step catalyzed transesterification synthesizes the crude cottonseed oil to form biodiesel and subsequently obtain biolubricant. The process flow diagram of two-step chemical modification is presented in Figure 1. Samples of biodiesel and green lubricant were collected after each chemical synthesis along with cottonseed triglycerides, as shown in Figure 2.
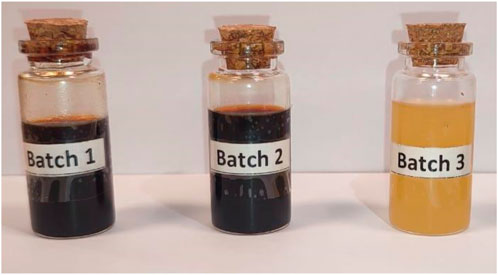
FIGURE 2. Development of biolubricant; Batch-1: Crude Cottonseed oil, Batch-2: Bio-diesel obtained after the first transesterification step, Batch-3: CS-based Green Lubricant obtained after the second transesterification.
3 Materials and testing methodology
3.1 Chemicals and computation methods
Ten liters of extracted native cottonseed oil were procured from the central Punjab market, Pakistan. The catalyst used was 1% wt/wt potassium hydroxide (KOH). Isooctly alcohol (C8H18O) of the DAE JUNG brand was used in the second chemical modification step. The second catalyst, Titanium IV) isopropoxide (TIS) of Sigma Aldrich brand with 97% purity, was used by 1.5% wt.
3.2 Chemical modification process
3.2.1 Synthesis of cottonseed FAME
In the first step, triglycerides of cottonseed oil react with methanol in a molar ratio of 6, and KOH is added 1% by weight. This results in a cottonseed methyl ester (CME) and glycerol. Process parameters for this step are shown in Figure 1. The purification process was conducted, which included washing with distilled water and drying at 100°C; this process was done five times to ensure the complete removal of glycerol and impurities. The following chemical reaction equation represents the first transesterification step.

The top layer is of CS methyl ester, also known as FAME, which is collected after draining the glycerol using a separatory funnel. The yield of this step was measured through the following equation:
3.2.2 Synthesis of green lubricant from CS FAME
The second transesterification process involves the methyl-ester reacted with iso-octyl alcohol (C8H18O) in a molar ratio of 3:1 at 170°C temperature, and titanium isopropoxide was used as a catalyst (1.5% by weight). The chemical modification process was followed by vacuum distillation for batch production of green lubricant. The purification process involves vacuum distillation at 20 mmHg. Methanol was collected as residual and recycled back to be used in 1st step. The following chemical equation represents the second transesterification step.

The chemical modification process followed by vacuum distillation for batch production of green lubricant is shown in Figure 3.
3.3 Design of experiments
To study the influence of critical factors on the yield of green lubricant, a design of experiment (DoE) was conducted.
Optimizing cotton biolubricant synthesis to achieve maximum green-lubricant yield with minimal soap formation was conducted using Minitab software with a central composite design (CCD) that included six center points. The DoE focused on four independent input factors: reaction time, catalyst concentration, pressure, and temperature.
The output/response of these four numeric factors will influence the yield of cottonseed-based green lubricant. The DoE involved selecting five levels of four input factors outlined in Table 1—a list of independent variables and their levels for DOE. The CME to iso-octyl alcohol molar ratio and stirring speed remained constant at 3:1 and 800 rpm, respectively, while TIS was used as the catalyst. The CCD recommended 30 experiments, with six experimental runs of a central point to evaluate the experimental error, 16 factorial experimental runs, and eight axial experimental runs, as shown in Table 2. The values of experimentally observed production of biolubricant are also listed in Table 2. Experimental runs with observed values of CS-based green lubricant. Experiments were performed randomly to minimize the bias.
3.4 Response surface methodology and analysis of variance (ANOVA)
Experimentally observed values were analyzed by response surface methodology. Regression analysis determined a statistical second-order polynomial equation fitted through observed values [(Angela Dean and Draguljić, 2017). Coefficients were determined through MINITAB software [(Minitab, 2018). The response yield is predicted and represented by a second-order polynomial equation by using the following relation:
where Y is the yield of green lubricant. While
The correlation value, R2, was used to determine the quality of model fitting through observed values. The higher correlation value represents the better model fitted to experimental data, while the lower value shows an insignificant model fit. ANOVA is a statistical technique determining the significance level of CCD-independent factors of different treatments. This test analyzes the variation and their causes and helps to identify the factors that significantly affect the output response. The p-value of the experimental test indicates significance, and the F-value indicates whether the term in the statistical equation is associated with the response.
3.5 Characterization of green lubricant
3.5.1 Green lubricant physicochemical characterization
Kinematic viscosities of biodiesel and green lubricant at 40°C and 100°C and density at 15°C were measured by rheometer Anton Paar MCR 302. The flash point was measured by Cleveland open cup flash apparatus, LOFP-A11, whereas Koehler measured cloud and pour points and K46001 test equipment as per ASTM D97 and D2500, respectively.
3.5.2 FTIR spectra
Two FTIR spectra were performed. One for the biodiesel was obtained after the first step of transesterification, and the second was after the second step. 2 mL of the sample was extracted containing FAME and 2 mL after setting optimal factors level determined after applying optimization techniques.
3.5.3 Pin-on-disk (PoD) tribo test
In order to evaluate the tribological performance of CS-based green lubricant, experiments were performed on a pin-on-disc tribometer based on ASTM G99. All tests were conducted at a constant load of 50 N, the sliding speed was 0.21 m/s, and the lubricant flow rate was 1.2 g/min on the Koehler PoD tribometer (K93500), USA, shown in Figure 4.
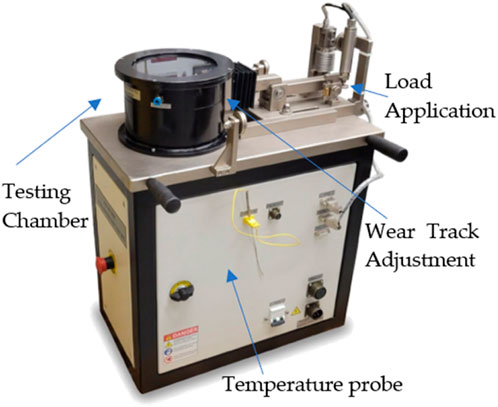
FIGURE 4. Koehler Pin-on-Disk (PoD) tribometer for tribological properties evaluation of sliding contact.
In order to determine the lubrication regime of the sliding tribo pair system in PoD experiments. The film parameter, lambda value, is calculated by
Where ho is the oil film thickness, RqA, and RqB are the RMS roughness amplitudes of the two bodies under siding contact. The oil film thickness is calculated by Hamrock and Downson relation for circular contact is given by:
Where Hc and Hmin are the dimensionless central and minimum oil film thickness. U, G, W, and k are the dimensionless speed, material, load, and elliptical parameters, respectively. The details of dimensionless numbers are given in (Stachowiak and Batchelor, 2013).
By utilizing Eeq = 117.2GPa, Req = 5 × 10-3 m along with the testing parameters for the PoD test listed in Tables 3–5, the predicted film parameter (lambda) is 1.463 with a composite surface roughness height of 0.49626 mm for pin and disc. This indicates that the tribopair runs under mixed/partial lubrication rather than
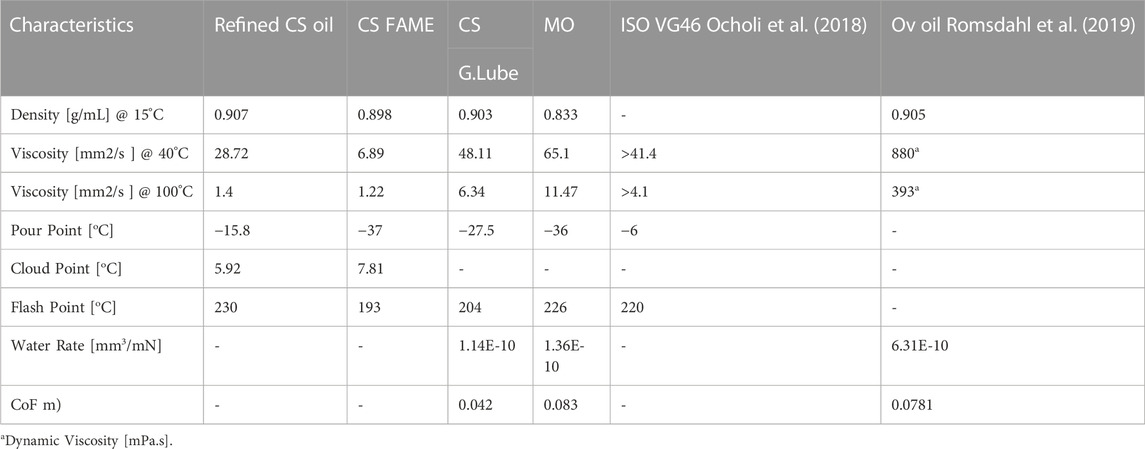
TABLE 3. Physicochemical Characteristics of CS-based Green Lubricant (CS-G.Lube), Ov Oil, mineral oil (MO), and Rapessed Oil-based Biolubricant (RO).
Boundary, elastohydrodynamic, or hydrodynamic lubrication regimes. The maximum Hertzian contact pressure for the tribopair is calculated according to (Stachowiak and Batchelor, 2013):
where a is the radius of the contact area:
Where Eeq and Req are the equivalent of Young’s Modulus and equivalent radius of curvature, respectively. In this case, the normal load of 50N produces the Hertzian contact stress of 68.47Mpa with a contact radius of 0.0117 mm with a local deformation of 93.88 nm. This indicates that no significant local deformation occurs in a sliding tribopair and ensures that contact is not under the EHL regime.
The Archard wear equation may express the wear of the pin; the specific wear rate (mm3/N.m) is given by:
where V is the wear volume (mm3), F is the normal load, and S is the wear sliding distance (mm). The wear volume is estimated by using the equation given below:
The 10 mm pins are made out of cast iron and further heat treated to HRC 52 hardness, and the disc is machined from steel to standard dimensions of 60 mm diameter and thickness of 12 mm. The tribopair (i.e., pin and disc) was lapped and polished. The primary surface characteristics were measured by Olympus DSX Opto-Digital Microscope, USA (Figure 5). In order to be very precise in measurements, the tests were repeated three times and recorded. The maximum error in CoF is ±0.0005.
4 Results and discussions
4.1 Characterization of CS-based green lubricant
4.1.1 Physicochemical characterization
The physiochemical characteristics of CS-based biolubricant are displayed in Table 3. Physicochemical Characteristics of CS-based Green Lubricant (CS-G.Lube), Ov Oil, mineral oil (MO), and Rapessed Oil-based Biolubricant (RO), are measured according to ASTM standards. The density of refined cottonseed oil was reduced from 0.9071 to 0.903, measured according to ASTM D7042. In addition, ASTM D97 and ASTM D92 were used to measure the pour and flash points, respectively. As a result, the pour point is improved to −27.5°C compared to refined cottonseed oil, which has the property to flow below 0°C. The flash point of cottonseed oil-based green lubricant is 204°C, comparable to commercial MO lubricant. The cotton green lubricant has a viscosity of 48.11 mm2/s, comparable to ISO VG46.
4.1.2 Evaluation of biolubricant tribological properties
A 60 mm steel disc having 12 mm thickness was manufactured, and 10 mm round pins loaded with 50N rotating with 300 rpm, simulating the typical internal combustion engine cylinder liner running with 0.21 m/s sliding speed. The operating conditions of the sliding contact tribopair are presented in Table 4. (Arumugam and Sriram, 2012). used a PoD machine (model TR-201C, Ducom Instruments Pvt. Ltd.) to test the discs made from cylinder liner material and the pins made from piston ring material. They compared the performance of four types of lubricants: rapeseed oil-based biolubricant with diesel contamination, synthetic lubricant (SAE 20W40) with diesel contamination, synthetic lubricant (SAE 20W40) with biodiesel contamination, and used synthetic lubricant (SAE 20W40). Similarly, the authors of the paper (Binfa Bongfa et al., 2019) simulated the piston top ring-liner situation by sliding a passenger car engine top ring on a cast iron disk using a pin-on-disk tribo-tester. They investigated the effect of neat palm fatty acid distillate (PFAD) and its ZDDP, MoDTC, and MyDTC formulations as lubricants on wear and friction control at the rubbing zone of the arrangement. The tests were conducted under the same load of 200N for a distance of 1500 m at room temperature (27°C). 0.5% (wt) molybdenum dialkyldithiocarbamates (MoDTC), doped PFAD produced lower friction and wear. In comparison, 0.1% (wt) ZDDP in the same PFAD offered a lower coefficient of friction but slightly higher wear when compared to a commercial premium engine oil tested for benchmarking. Specification of materials used in experiments is given in Table 5.
Figure 6 summarizes the frictional effect of bio lubricant compared with MO for sliding tribopair under constant load. A steady run follows the initial phase of the experiment, the constant oil film is formed, and the tribopair operates in a mixed lubrication regime. Compared to commercial oil, the bio-based lubricant has reduced CoF up to 50% in the mixed lubrication regime. It is also observed that the heat transfer rate of green lubricant is higher as compared to MO by analyzing the measured temperature data of the pin. Cycle-based data analysis was conducted to investigate the localized events and changes during the test.
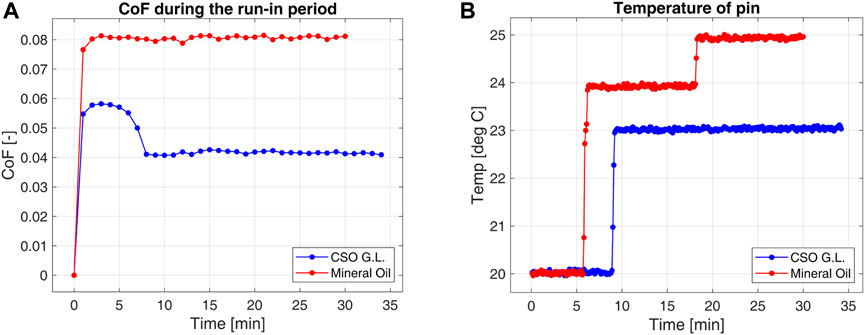
FIGURE 6. CoF (A) and pin temperature (B) variation for the green lubricant compared with the commercial mineral oil tested under sliding contact on a Pin-on-disk tribometer.
The lubrication mechanism of fatty acids and ester groups in lubricants is well-studied (Bowden et al., 1945; Bahari et al., 2017). The polarity of the carboxyl group generates a thin film of lubrication through the attraction towards the metallic surfaces of tribopair (Stachowiak and Batchelor, 2013). A single bond in saturated fatty acid (like stearic acid) (Lundgren et al., 2008) helps molecules to align in a straight chain. The aligned linear chains generate smooth interaction during sliding motion, decreasing friction. The lubrication mechanism of the biolubricant is shown in Figure 7.
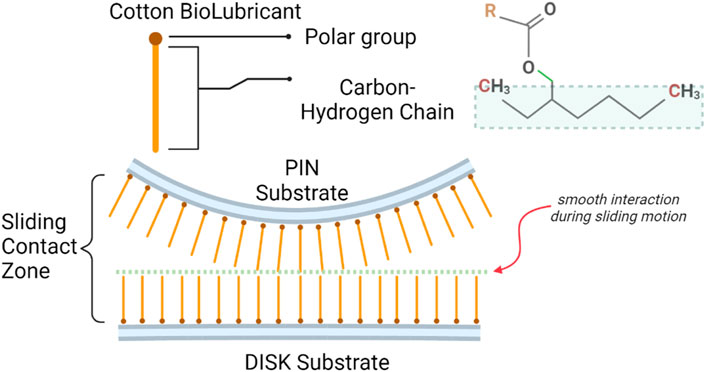
FIGURE 7. Mechanism of biolubricant molecular structure generating tribofilm at the metallic surface.
The saturated fatty acids and the ester group form a mono-molecular protective layer at the conjunction of sliding pair. Whereas unsaturated fatty acids (oleic and linoleic acids) (Lou Honary, 2011) have a bend in carbon chains due to double bonds failing to create a tribolayer and resulting in higher CoF and wear of pins.
4.1.3 Surface morphology and roughness analysis
The measured worn-out surface roughness parameters of sliding pair contact after conducting tests under mixed lubrication conditions with two different oils (MO and CS G. Lube) are listed in Table 6. In addition, the surface roughness heat map of the pin and disk tested with green lubricant and MO is shown in Figure 8 using an optical microscope 200X magnified.

TABLE 6. Measured surface roughness parameters for pins and discs after testing with CS-based green lubricant and Mineral Oil.
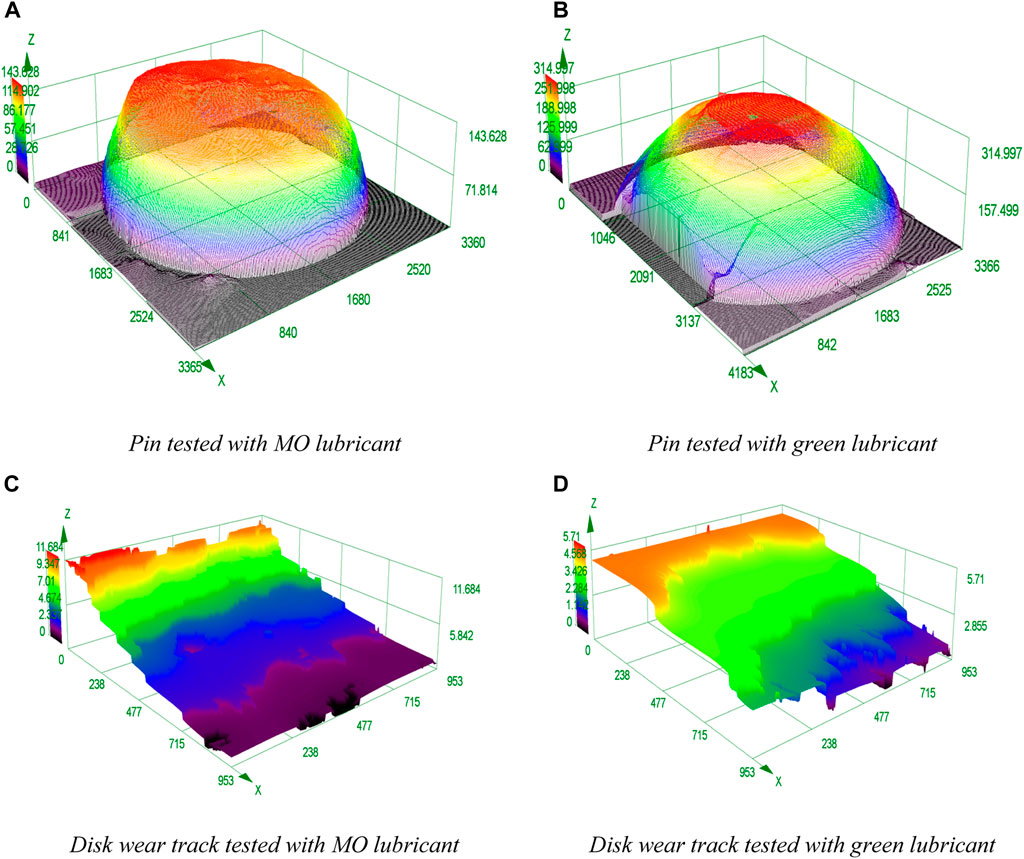
FIGURE 8. 3D Surface roughness heat maps and wear shapes for the pins and disk after wearing; the cut-off length is 80[mm], 200X magnified trio-pair surfaces obtained from an optical microscope. (A) pin tested with MO lubricant. (B) pin tested with green lubricant. (C) disk wear track tested with MO lubricant. (D) disk wear track tested with green lubricant.
The wear scar of the specimen lubricated with mineral oil is wavier shaped than the bio-lubricated specimen, indicating plastic deformation on the pin surface due to higher contact pressure (Ponter et al., 1985).
The wear rate measurement of pins resulted from wear loss analysis conducted on pins after testing, plotted in Figure 9. The pins subjected to cotton-based biolubricant have a wear rate of 1.14E-10 mm3/mN (with RSD = 3.8%). However, pins subjected to mineral oil have a higher wear rate of 1.36E-10 mm3/mN (with RSD = 4.92%).
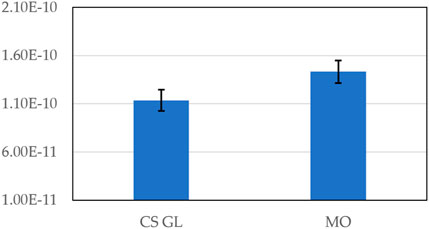
FIGURE 9. Specific wear rate [mm3/mN] measurements of pins when lubricated with cottonseed-based lubricant and MO.
In addition, the surface of the tribopair lubricated with MO has more grooves, cracks, and material transfer than with green lubricant. Therefore, adhesive wear is likely the primary source of initial wear in pins tested with mineral oil, as shown in Figure 10. Moreover, extensive plowing and wedge-like agglomerates on pins in the sliding direction parallel to wear are observed (Ponter et al., 1985; Ponter et al., 2006).
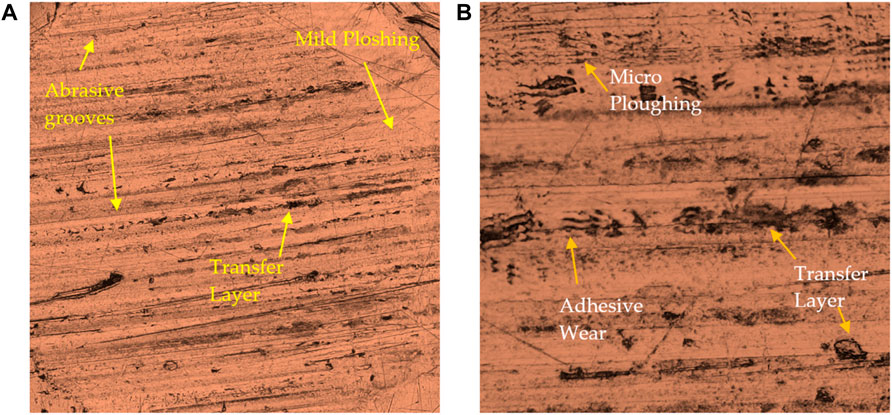
FIGURE 10. Worn pins (×200 Magnification) surfaces tested under (A) CS-based GL and (B) MO constant load of 50N with a sliding speed of 0.21 m/s. The sliding direction in the figures is parallel to the horizontal axis.
The role of AW/EP in mineral oil has limited effect compared to the tribofilm produced by bio lubricant in preventing contact between pin and steel disk. Thus, it can be concluded that the green lubricant has enhanced the lubrication of sliding contact under 50N load with the sliding speed of 0.21 m/s under mixed conditions.
4.1.4 FTIR spectra analysis
To determine the functional group of synthesized CME (biodiesel) and green lubricant were analyzed through FTIR spectroscopy. The results of CME in Figure 11 were analyzed and linked with the FTIR library of known signatures database.
The average surface roughness across the wear scar of the MO-lubricated specimen produces higher roughness than green lubricant. This suggests higher abrasive wear on the pin surface. Furthermore, the abrasive marks with plastic deformation also indicate the third-body abrasive wear mechanism. This concludes that higher surface roughness corresponds to high CoF—however, bio-lubricated specimens produced lower surface roughness.
The broad peak around 3,487 cm-1 indicates the presence of the O-H group. The predominant peaks noted at 2924.08 cm-1 and 2855 cm-1 (C-H symmetric and asymmetric weak stretch) are the methyl and methylene hydrocarbons in the green lubricant formulation. No triple bond region (C=C) was detected. However, the bending peaks of methylene and methyl groups are at 1,458.9 cm-1 and 1,379 cm-1, respectively. There are two peaks representing the ester formation, including carbonyl and C-O. One peak is at 1741.72 cm-1 (C=O medium stretch), which are carbonyl group and the second peak is at 1,014.37 cm-1, indicating the absorption of esters. There is no peak around 1,600, showing that no C=C is bounding in the lubricant. The peak centered at 1,249 and 1,172.39 cm-1 refers to the absorption of alcohol or large rings of cyclic ethers (aryl-O and C-H aromatic). The peak occurred at 1,458.98 cm-1 (which falls in the range of 1,615 and 1,495 cm-1 of the aromatic ring). These aromatic rings are followed by weak absorption at 3,013.22 cm-1 (C-H stretching). The narrow peak at 991.15 cm-1 is identified as a single vinyl terminal (C=CH2). The peak was obtained at 719.45 cm-1 (C-H weak rocking/alkanes (CH2)n). From the spectrum absorption, the region between 880 and 1,000 has multiple absorption spectra suppressed after the second transesterification process. The O-H group, which are oxygen-containing compounds and water, results in the biodegradability of the CME (Encinar et al., 2020).
4.2 Evaluation of the regression model
4.2.1 Model fitting and testing
Based on the experiments suggested by MINITAB Software, random experiments were run to remove systematic or basis in the response. The correlation between the independent factors and transesterification yield was evaluated using response surface methodology. Process variables A, B, C, and D represent reaction temperature(T), pressure(P), catalyst concentration (conc), and reaction time (RT). The output of all experiments is the yield of green lubricant. An empirical model was developed by fitting the second-order quadratic equation on the observed yield values. RSM suggests following Eq-2 (uncoded form) to predict the yield of green lubricant with R2 = 0.988. Higher values of R2 indicate that the developed model is significant and adequate to explain 98.68% (R2 Adj.) of variability observed in the yield of the experiments.
Process variables in the above equation with negative suggest that an increase in the variable will give lower yields. At the same time, a factor with a positive sign shows that an increase in the variable will increase yield output.
The residual plot (Figure 12) for the yield output for the second transesterification shows a good correlation between process variables and the output. The model’s diagnostic shows that observation no. 28 and 29 is unusual.
4.2.2 ANOVA analysis
In order to analyze the adequacy and significance of the fitted quadratic equation, variance analysis was performed in MINITAB Software. A summary of the analysis results is listed in Table 7. The F-value of the model has 11 degrees of freedom, suggesting that the predicted model is significant, while the p-value for lack of fit shows that it is not substantial. Process variables important in the model are shown by a very small p-value (<0.0001). The analysis shows that linear terms A, B, C, and D; quadratic terms A2, B2, C2, and D2 and the interaction terms AC, AD, BC, and BD are significant process variables in the model. The Preto chart in Figure 13 shows the standardized effect of essential process variables on response and yield.
The gray bar shows the insignificant variables that are not in the model. For example, among the four independent variables, the temperature significantly affects the yield of green lubricant with an F-value of 804.67. The critical linear variables are reaction time, pressure, and catalyst concentration.
The primary role catalyst is to accelerate the chemical reaction to convert CME (cotton-based Methyl ester) to bio lubricant. Early studies have shown that the production of green lubricant was higher for lower to intermediate concentrations and, at 1%, had no effect (Encinar et al., 2020).
Figure 14 shows the probability plot of experimental values and predicted values with a 95% confidence interval, which suggests that the developed RSM model prediction has a p-value <0.005. The standard deviation of experimental values and observed values is comparable. Similarly, the correlation plot of Figure 15 and the categorical grouping of the most critical variable, the temperature, is also plotted, confirming the adequacy of the fitted model. It also shows the excellent correlation plot at higher temperature values for maximum production of green lubricant. The interaction between all independent process variables for three levels (lower, central, and higher) is plotted in Figure 16.
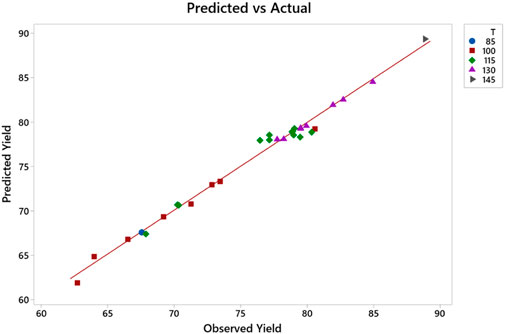
FIGURE 15. Correlation plot between observed and predicted yield of CS GL grouped with temperature category.
4.2.3 Effect of interaction between process variables on yield
The contour plot of response surfaces is presented in Figure 17. Figure 17A plots the relationship between temperature and pressure. A yield more significant than 90% can be obtained by setting a temperature higher than 175°C and pressure at 18 mmHg. Lower pressure values and lower temperature values have the lowest yield.
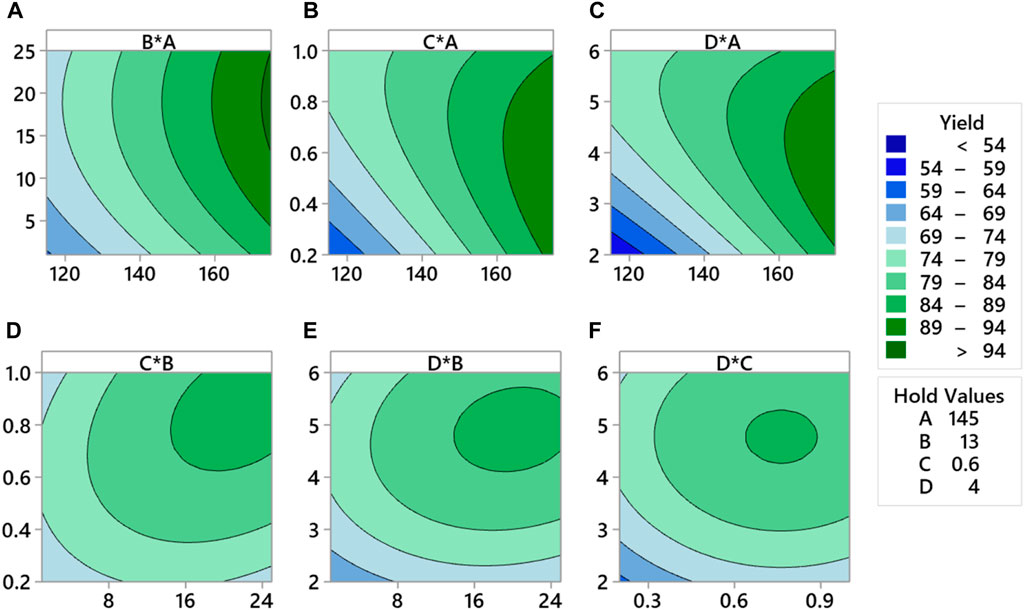
FIGURE 17. Response surface contour plot for CS-based green lubricant production for (A) pressure and temperature, (B) temperature and catalyst concentration, (C) temperature and reaction time, (D) interaction of pressure and catalyst concentration. (E) pressure and reaction time, and (F) reaction time and catalyst concentration process factors.
Figure 17B explains that high yield is obtained at high temperatures, and the catalyst concentration is kept between 0.2% and 0.97%. Although at high temperatures, unwanted kinetic changes occur during synthesis that will change the structure of methyl ester. Figure 17C explains that the yield of green lubricant is higher for higher temperature values and an increase in reaction time from 2.3 h to 5.7 h.
Figure 17D explains the interaction between pressure and catalyst concentration. The maximum yield contours are between 79% and 84%, which can be achieved by setting pressure values higher than 15 mmHg and the catalyst concentration to the maximum limit of 1%. However, high vacuum pressure in the bioreactor increases methanol removal and chemical reaction. The lowest limit of concentration is 0.63%. Therefore, it is mandatory to optimize the concentration of the TIS catalyst. Figure 17E illustrates the interaction between reaction time and pressure. The maximum production of green lubricant occurred at a higher pressure and higher reaction time of up to 5. The prolonged reaction time ensures equilibrium is achieved and reactants are converted to products. The yield range for this interaction is between 84% and 89%.
Figure 17F illustrates that the increase in concentration from 0.64% to 088% and reaction time from 4.36 h to 5.4 h yields production between 84% and 89%. Therefore, optimization must be run for maximum yield to determine the optimum values of process variables.
4.2.4 Optimization of optimal conditions
The optimal setting for independent variables suggested by RMS was determined by running optimization in MINITAB software. The single response variable, the yield of green lubricant, was optimized by setting the goal of maximizing green lubricant production. The optimizer determines pressure 19.42 mmHg, temperature 175°C, catalyst concentration 0.63%, and reaction time 4.02 h with a maximum desirable yield of 95%, shown in Figure 18. The vertical red line in Figure 14 represents the optimum setting with CI = 95% and the prediction interval between 88.37% and 92.83%. For these settings, the standard error (SE) of fit is 0.513, which estimates the variation in the mean yield of green lubricant.
4.3 Experimental validation of the RSM model
The predicted result of the RSM mathematical model at optimum conditions was validated through experiments. The comparison of the synthesis process and mathematical models is presented in Table 8. It shows a good agreement of experiments and models developed with a variation of ±0.28.
5 Conclusion
In this investigation, through a double transesterification process, bio lubricant has been synthesized. First, cottonseed methyl ester (CS-FAME) was produced in the first transesterification step. Then, in the second transesterification step, cottonseed-based bio lubricant was produced when CS-FAME reacted with 2ethyl-1hexanol in the presence of titanium isopropoxide (TIS). The DOE methodology focused on four independent input factors: reaction time, catalyst concentration, pressure, and temperature to determine the maximum yield. In addition, this work optimized variables of the second transesterification process for CME, and a mathematical model was developed using RSM.
The process variables included were pressure, temperature, catalyst concentration, and reaction time.
The optimal conditions calculated by ANOVA for maximum yield are 19.42 mmHg, 175°C temperature, 0.63% concentration, and reaction time of 4.02 h. As a result, the maximum production of green lubricant achieved experimentally was 95.98%.
In addition, the tribological performance of biolubricant and mineral oil under sliding motion was also investigated through PoD experiments, with 50N load and 0.21 m/s of sliding speed. As a result, it has been determined that the CoF of cottonseed-based green lubricant is better than mineral oils.
The experimental temperature measurement result shows that the heat transfer of green lubricant during sliding contact is higher than that of mineral oil. The CoF of green lubricant is 49% lower than commercial mineral oil. The surface analysis of worn pins showed that the wear of green lubricant is 19% improved compared to mineral oil. It has been proven that with the use of superior alcohol and a TIS catalyst a good yield of lubricant is possible in the second transesterification step. Compared to commercially available mineral oil, the biolubricant has high polarity toward metallic surfaces, which protects from metal-metal contact and helps reduce friction and wear. The temperature measurements at the pin signify that the thermal properties of bio lubricant are superior to mineral oil and can be used as thermal cooling liquids in e-axle/EDU components and batteries of hybrid/EV vehicles.
The future scope of this study is to examine the tribological performance of cottonseed-based biolubricant on reciprocating tribometer and cover all lubrication regimes. The mechanism of boundary layer formation of biolubricant is still unexplored and will be studied under different temperature ranges. Ultimately, the lubrication compatibility of biolubricant as base oil will be investigated through enriching conventional additives and friction modifiers.
Data availability statement
The original contributions presented in the study are included in the article/Supplementary material, further inquiries can be directed to the corresponding authors.
Author contributions
IG: Conceptualization, Data curation, Formal Analysis, Investigation, Methodology, Validation, Visualization, Writing–original draft, Writing–review and editing. SA: Supervision, Writing–review and editing. AU: Conceptualization, Supervision, Writing–review and editing, Investigation, Visualization.
Funding
The author(s) declare that no financial support was received for the research, authorship, and/or publication of this article.
Conflict of interest
The authors declare that the research was conducted in the absence of any commercial or financial relationships that could be construed as a potential conflict of interest.
Publisher’s note
All claims expressed in this article are solely those of the authors and do not necessarily represent those of their affiliated organizations, or those of the publisher, the editors and the reviewers. Any product that may be evaluated in this article, or claim that may be made by its manufacturer, is not guaranteed or endorsed by the publisher.
References
Ahmed, A., Ali, A., Mubashir, M., Lim, H. R., Khoo, K. S., and Show, P. L. (2023). Process optimization and simulation of biodiesel synthesis from waste cooking oil through supercritical transesterification reaction without catalyst. J. Phys. Energy 5 (2), 024003. doi:10.1088/2515-7655/acb6b3
Arumugam, S., and Sriram, G. (2012). Effect of bio-lubricant and biodiesel-contaminated lubricant on tribological behavior of cylinder liner–piston ring combination. Tribol. Trans. 55 (4), 438–445. doi:10.1080/10402004.2012.667517
Bahari, A., Lewis, R., and Slatter, T. (2017). Friction and wear response of vegetable oils and their blends with mineral engine oil in a reciprocating sliding contact at severe contact conditions. Proc. Institution Mech. Eng. Part J J. Eng. Tribol. 232 (3), 244–258. doi:10.1177/1350650117712344
Bekal, S., and Bhat, N. R. (2012). Bio-lubricant as an alternative to mineral oil for a CI engine—an experimental investigation with pongamia oil as a lubricant. Energy Sources, Part A Recovery, Util. Environ. Eff. 34 (11), 1016–1026. doi:10.1080/15567031003735303
Binfa Bongfa, M. K. A. H., Samion, S., Samin, P. M., and Bakar, A. R. A. (2019). Friction and wear study of passenger car piston top ring sliding on cast iron material lubricated with palm fatty acid distillate (PFAD). Asia International Conference on Tribology, Malaysia, Editor M. F. B. Abdollah (Malaysia: MYTRIBOS), 56–58.
Bowden, F. P., Gregory, J. N., and Tabor, D. (1945). Lubrication of metal surfaces by fatty acids. Nature 156 (3952), 97–101. doi:10.1038/156097a0
Carlucci, C., Degennaro, L., and Luisi, R. (2019). Titanium dioxide as a catalyst in biodiesel production. Catalysts 9, 75. doi:10.3390/catal9010075
Cecilia, J. A., Ballesteros Plata, D., Alves Saboya, R. M., Tavares de Luna, F. M., Cavalcante, C. L., and Rodríguez-Castellón, E. (2020). An overview of the biolubricant production process: challenges and future perspectives. Processes 8, 257. doi:10.3390/pr8030257
Das, B., and Lingfa, P. (2015). Energy analysis of karanja oil as a supplementary fuel for compression ignition engine. J. Urban Environ. Eng. 9 (2), 97–101. doi:10.4090/juee.2015.v9n2.097101
Djomdi, T., Leku, M. T., Djoulde, D., Delattre, C., and Michaud, P. (2020). Purification and valorization of waste cotton seed oil as an alternative feedstock for biodiesel production. Bioengineering 7, 41. doi:10.3390/bioengineering7020041
Dodos, G. S., Anastopoulos, G., and Zannikos, F. (2010). Tribological evaluation of biobased lubricant basestocks from cottonseed and soybean oils. SAE Int. J. Fuels Lubr. 3 (2), 378–385. doi:10.4271/2010-01-1545
Encinar, J. M., Nogales-Delgado, S., Sánchez, N., and González, J. F. (2020). Biolubricants from rapeseed and Castor oil transesterification by using titanium isopropoxide as a catalyst: production and characterization. Catalysts 10, 366. doi:10.3390/catal10040366
Ge, J. C., Yoon, S. K., and Song, J. H. (2022). Combustion and emission characteristics of a diesel engine fueled with crude palm oil blends at various idling speeds. Appl. Sci. 12, 6294. doi:10.3390/app12136294
Gul, M., Zulkifli, N. W. M., Masjuki, H. H., Kalam, M. A., Mujtaba, M. A., Harith, M. H., et al. (2020). Effect of TMP-based-cottonseed oil-biolubricant blends on tribological behavior of cylinder liner-piston ring combinations. Fuel 278, 118242. doi:10.1016/j.fuel.2020.118242
Hassan Ab, A., Nasir, A., and Rachel, U. (2006). Investigation on the use of palm olein as lubrication oil. Leonardo El J. Pract. Technol. 5, 1–8.
Jedrzejczak, A., Batory, D., Prowizor, M., Dominik, M., Smietana, M., Cichomski, M., et al. (2020). Titanium(IV) isopropoxide as a source of titanium and oxygen atoms in carbon based coatings deposited by Radio Frequency Plasma Enhanced Chemical Vapour Deposition method. Thin Solid Films 693, 137697. doi:10.1016/j.tsf.2019.137697
Li, K., Zhang, X., Du, C., Yang, J., Wu, B., Guo, Z., et al. (2019). Friction reduction and viscosity modification of cellulose nanocrystals as biolubricant additives in polyalphaolefin oil. Carbohydr. Polym. 220, 228–235. doi:10.1016/j.carbpol.2019.05.072
Lou Honary, E. R. (2011). Biobased lubricants and greases: technology and products. In Editor U. Chichester John Wiley and Sons.
Lundgren, S. M., Ruths, M., Danerlov, K., and Persson, K. (2008). Effects of unsaturation on film structure and friction of fatty acids in a model base oil. J. Colloid Interface Sci. 326 (2), 530–536. doi:10.1016/j.jcis.2008.05.068
Mahata, S., Mondal, B., Mahata, S. S., Usha, K., Mandal, N., and Mukherjee, K. (2015). Chemical modification of titanium isopropoxide for producing stable dispersion of titania nano-particles. Mater. Chem. Phys. 151, 267–274. doi:10.1016/j.matchemphys.2014.11.065
Minitab, I. (2018). Minitab, 20.2. Available at: http://www.minitab.com/en-US/products/minitab/.
Ocholi, O., Menkiti, M., Auta, M., and Ezemagu, I. (2018). Optimization of the operating parameters for the extractive synthesis of biolubricant from sesame seed oil via response surface methodology. Egypt. J. Petroleum 27 (3), 265–275. doi:10.1016/j.ejpe.2017.04.001
Panchal, T. M., Patel, A., Chauhan, D. D., Thomas, M., and Patel, J. V. (2017). A methodological review on bio-lubricants from vegetable oil based resources. Renew. Sustain. Energy Rev. 70, 65–70. doi:10.1016/j.rser.2016.11.105
Ponter, A. R. S., Chen, H. F., Ciavarella, M., and Specchia, G. (2006). Shakedown analyses for rolling and sliding contact problems. Int. J. Solids Struct. 43 (14-15), 4201–4219. doi:10.1016/j.ijsolstr.2005.05.046
Ponter, A. R. S., Hearle, A. D., and Johnson, K. L. (1985). Application of the kinematical shakedown theorem to rolling and sliding point contacts. J. Mech. Phys. Solids 33 (4), 339–362. doi:10.1016/0022-5096(85)90033-x
Quinchia, L. A., Delgado, M. A., Reddyhoff, T., Gallegos, C., and Spikes, H. A. (2014). Tribological studies of potential vegetable oil-based lubricants containing environmentally friendly viscosity modifiers. Tribol. Int. 69, 110–117. doi:10.1016/j.triboint.2013.08.016
Reddy, K. S. V. K., Kabra, N., Kunchum, U., and Vijayakumar, T. (2014). Experimental investigation on usage of palm oil as a lubricant to substitute mineral oil in CI engines. Chin. J. Eng. 2014, 1–5. doi:10.1155/2014/643521
Rokni, K., Mostafaei, M., Dehghani-Soufi, M., and Kahrizi, D. (2022). Microwave-assisted synthesis of trimethylolpropane triester (bio-lubricant) from camelina oil. Sci. Rep. 12 (1), 11941. doi:10.1038/s41598-022-16209-z
Romsdahl, T., Shirani, A., Minto, R. E., Zhang, C., Cahoon, E. B., Chapman, K. D., et al. (2019). Nature-guided synthesis of advanced bio-lubricants. Sci. Rep. 9 (1), 11711. doi:10.1038/s41598-019-48165-6
Saboya, R. M. A., Cecilia, J. A., García-Sancho, C., Sales, A. V., de Luna, F. M. T., Rodríguez-Castellón, E., et al. (2017). Synthesis of biolubricants by the esterification of free fatty acids from castor oil with branched alcohols using cationic exchange resins as catalysts. Industrial Crops Prod. 104, 52–61. doi:10.1016/j.indcrop.2017.04.018
Schramm, J. (2003). Application of a biodegradable lubricant in a diesel vehicle. SAE technical paper.
Shahabuddin, M., Mofijur, M., Rizwanul Fattah, I. M., Kalam, M. A., Masjuki, H. H., Chowdhury, M. A., et al. (2022). Study on the tribological characteristics of plant oil-based bio-lubricant with automotive liner-piston ring materials. Curr. Res. Green Sustain. Chem. 5, 100262. doi:10.1016/j.crgsc.2022.100262
Sharma, U. C., and Sachan, S. (2019). Friction and wear behavior of karanja oil derived biolubricant base oil. SN Appl. Sci. 1 (7), 668. doi:10.1007/s42452-019-0706-y
Siraskar, G. (2018). “Experimental investigation on usage of cottonseed oil and esterifies cottonseed oil as lubricant in IC engines,” in Proceedings of 194th, the IIER international conference, Bangkok, Thailand, October 5–6, 2018.
Siraskar, G., Wakchaure, V., and Jahagirdar, R. (2021). Diesel engine emission characteristics for cotton seed (CS) trimethylolpropane (TMP) ester (CSTE) as lubricant. Arabian J. Geosciences 14 (18), 1927. doi:10.1007/s12517-021-08232-7
Spiridonova, J., Katerski, A., Danilson, M., Krichevskaya, M., Krunks, M., and Oja Acik, I. (2019). Effect of the titanium isopropoxide:acetylacetone molar ratio on the photocatalytic activity of TiO(2) thin films. Molecules 24 (23), 4326. doi:10.3390/molecules24234326
Stachowiak, G., and Batchelor, A. W. (2013). Engineering tribology. 4th Edition ed. Elsevier: Butterworth-Heinemann.
Ulanova, A. A., Stolpovskaya, N. V., Chertov, S. S., Kruzhilin, A. A., and Shikhaliev, K. S. (2022). Modification of epoxidized methyl esters of sunflower oil fatty acids with some diols. IOP Conf. Ser. Earth Environ. Sci. 1052 (1), 012094. doi:10.1088/1755-1315/1052/1/012094
Unruean, P., Nomura, K., and Kitiyanan, B. (2022). High conversion of CaO-catalyzed transesterification of vegetable oils with ethanol. J. Oleo Sci. 71 (7), 1051–1062. doi:10.5650/jos.ess21374
Keywords: green lubricant, cottonseed oil, 2ethyl-1hexanol, transesterification, tribology, friction, wear
Citation: Ghumman ISS, Afaq SK and Usman A (2023) Frictional performance of chemically modified cottonseed-based fossil-free biolubricant oil in a sliding tribopair. Front. Mech. Eng 9:1281406. doi: 10.3389/fmech.2023.1281406
Received: 22 August 2023; Accepted: 03 October 2023;
Published: 24 October 2023.
Edited by:
Pao-Chang Huang, National Defense University, TaiwanReviewed by:
Yew Heng Teoh, Universiti Sains Malaysia Engineering Campus, MalaysiaKimaya Prakash Vyavhare, Kennametal, United States
Copyright © 2023 Ghumman, Afaq and Usman. This is an open-access article distributed under the terms of the Creative Commons Attribution License (CC BY). The use, distribution or reproduction in other forums is permitted, provided the original author(s) and the copyright owner(s) are credited and that the original publication in this journal is cited, in accordance with accepted academic practice. No use, distribution or reproduction is permitted which does not comply with these terms.
*Correspondence: Ali Usman, YWxpLnVzbWFuQGx0dS5zZQ==; I. S. S. Ghumman, aW1yYW4uc2FqaWRAaGl0ZWN1bmkuZWR1LnBr