- UK Centre for Carbon Dioxide Utilisation, Department of Chemical and Biological Engineering, The University of Sheffield, Sheffield, United Kingdom
With “defossilisation” at the core of many sustainability goals within industry, the exploration of new synthesis routes to chemicals has never been more vital. As part of their Clean Futures initiative, Unilever Home Care has published the Carbon Rainbow, a scheme which categorizes chemical sources into different “colors,” depending on their derivation. One of the sustainability goals of the Carbon Rainbow is to phase out non-renewable “black” carbon from supply chains by 2030. This complements the goals of the Clean Futures initiative, which looks toward a Net-Zero impact from all products from a cradle-to-shelf scope by 2039. Given the substantial contributions to atmospheric CO2 emissions from the production and use of conventional surfactants, this paper reviews methods to form Linear Alkylbenzene Sulfonate (LAS) through means which look to utilize Carbon Rainbow-categorized carbon sources outside of traditional fossil sources. The focus when reviewing each method is the overall defossilization of the LAS production process. The inventories of new defossilised methods collated within this research will ultimately provide the backbone for a future study on sustainability assessment screening. Through a literature search and technological overview, the construction of a tree diagram showing many new routes to LAS-appropriate olefins has been accomplished, illustrating the breadth of technologies available that share the common goal of defossilization. The expanse of technologies works well as to provide options to the necessary companies, though also resulting in a vast array of options to consider and assess before pursuing the optimum route. In total, 19 technologies were reviewed, forming a map containing 27 different supply chain routes from feedstock to LAS-appropriate olefins. This research therefore also shows the need for a short-form sustainability screening in order to green-light technologies which are suitable for a long-form sustainability assessment before any new process is adopted.
Introduction
As companies within the chemical production industry move toward defossilized supply chains, efforts into sourcing new (currently not widely practiced in industry, particularly with reference to detergents) production routes which avoid using virgin fossil materials have stepped up greatly. This paper will provide an overview of these new routes with respect to the production of organic surfactants alongside the gradual construction of a chemical formulation tree diagram for straight chain alpha-olefins. For companies like Unilever with a high demand for organic surfactants and with ambitious sustainability goals (Unilever, 2020), the production of defossilized and sustainable olefins with lower impact on the environment is vital for said goals to be reached.
Olefins are one of the key building blocks when it comes to chemical synthesis. With established carbon-carbon and carbon-hydrogen bonds as well as the ability to bond with electrophiles, the possible organic products that start with olefins is nigh-on endless. With a significant role throughout many different industries (ICIS, 2022), breakthroughs into sustainable olefins hold an incredibly broad range of effect and could prove to be an invaluable step in the removal of fossil carbon in chemical supply chains.
The aim of this paper is to provide an overview of the technologies which can be used to defossilise the formulation of LAS-appropriate olefins, including any relevant life cycle inventory data which has been published for said technology. The information presented will then provide the basis for a new risk-based sustainability assessment screening method in order to assess which route is the optimum, in line with Unilever's sustainability goals.
The necessity of olefins and their current means of production
Olefin chemistry
As mentioned previously, olefins are used as core building blocks within chemical synthesis, due to their presence of existing carbon-carbon and carbon-hydrogen bonds along with a functional group which allows for the ability of many substitution and addition reactions (Klein, 2017). These reactions are testament to the versatility of olefins, justifying their prevalence as one of the most-utilized chemical intermediates in the synthesis industry.
Olefin use for linear alkylbenzene sulfonate
Acting as the molecule of investigation for this study, linear alkylbenzene sulfonate has a strong dependency on olefins, with C9 to C14 length alpha-olefins providing the backbone for the hydrophobic tail of the molecule. In the comparative LCA for LAS from selected renewable and petroleum routes, Fogliatti outlines the fact that after olefins in the supply chain, the processes for renewable and petroleum-based LAS are shared (Fogliatti et al., 2014). This means that investigation beyond the production of olefins with respect to LAS is not as relevant, and so an investigation as far as olefins is justified. Literary investigation of more recent research also shows that besides catalytic improvements to increase energy efficiency, there is little room for innovation into the “LAB production” step in Figure 1.
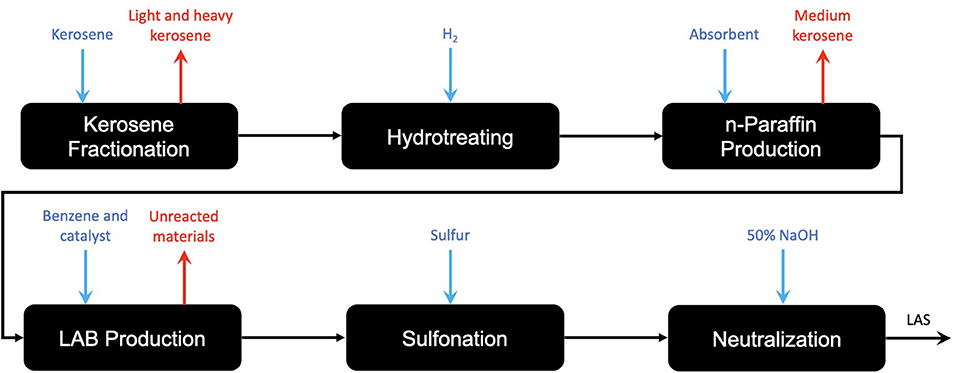
Figure 1. A process route diagram for the production of a renewable and a petroleum-based LAS production, illustrating the shared pathway following the production of the alkyl (olefin) route (after Fogliatti et al., 2014).
With respect to LAS, an olefin is required for production due to the reactive capabilities of the functional group. The C9 − 14 hydrocarbon chain is bonded to the benzene head of the molecule through the Friedel-Crafts alkylation of benzene, in which the C9 − 14 olefin is halogenated by an acid catalyst (usually hydrofluoric acid) before undergoing an addition reaction with the benzene (Yadav and Doshi, 2002). This forms the linear alkylbenzene molecule (LAB) which is then sulfonated forming the desired LAS molecule. The addition process for the two components for LAB is commercially known as the DETAL process and immediately follows the Pacol and DeFine units outlined in Figure 1. The key difference with the DETAL process is that the acid used is solid and not liquid, allowing for safer handling. The actual elemental basis of the catalyst is commercially unknown, though is suspected to be zeolite-based (Kocal et al., 2001). The reaction equation and mechanism are shown in Figure 2.
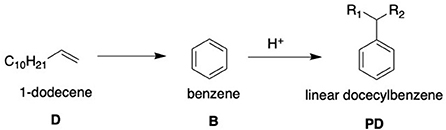
Figure 2. A diagram-aided equation showing the basis of the DETAL process using an acid catalyst (after Yadav and Doshi, 2002).
Current means of olefin production
Different methods of olefin production can be defined depending on the length of the olefins being produced. In keeping with the scope of the review, both short and medium chain olefin production have been considered, as both can eventually be used for LAS.
Short chain olefins (C2-C5)
As things stand, the most common method of olefin production is the cracking of longer chain alkanes via steam cracking (Rosli and Aziz, 2016). Such alkanes tend to be sourced from fractionated crude oil, allowing the introduction of fossil carbon into chemical supply chains.
Steam cracking involves heating alkanes (of length C2 and above) and steam to temperatures up to 900°C and at 2.2 barg, to break the long chain alkanes backbones. This produces shorter chain hydrocarbons, the unsaturated homologues of which are termed the light olefins. These are extracted through a variety of separation methods, with any unreacted materials being recycled back into the system (Rosli and Aziz, 2016). With reactions requiring high temperatures and pressures, as well as a reliance on fossil carbon feedstocks, the production of olefins from the steam cracking of hydrocarbons becomes a key hotspot when it comes to the sustainability of the final product. With a GWP of 1.45 kgCO2-eq per kg of ethylene produced from steam cracking (Wernet et al., 2016), alongside the 3.14 kg CO2 released at the point of degradation of said kg of ethylene, the lifetime contribution to global warming of a kilogram of fossil ethylene is far from insignificant. Steam cracking is generally used to produce lighter olefins within the range C2 to C4 (Rosli and Aziz, 2016), which could in theory be utilized to form medium chain olefins for use within the production of LAS through oligomerization.
Medium chain olefins (C9-C14)
Another process for olefin production, this time for longer olefins in the range C9 to C14 is the hybridized Pacol DeFine process (also shortened to simply the Pacol process). Commercialized by UOP in 1967, the Pacol process is the main way in which longer olefin chains are prepared for use within LAS production. The process begins with the thermocatalytic dehydrogenation of n-paraffins to both mono- and diolefins over a selective platinum catalyst. This endothermic reaction occurs within the Pacol reactor, requiring 747MJ/t of C12 monoolefin product (Meyers, 2016). This in turn produces high-quality hydrogen gas as a by-product. The mixture of mono- and diolefins is then fed into a DeFine reactor, saturating any diolefins into monoolefins. The final mixture is then passed through a stripper, removing any final light ends and hydrogen from the product stream (Meyers, 2016). This is illustrated by Figure 3.
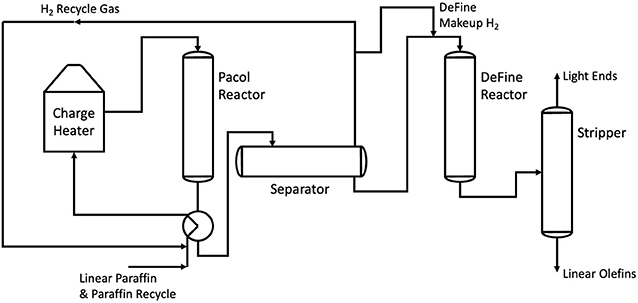
Figure 3. A process flow diagram showing the Pacol and DeFine reactors in series. Adapted from Meyers (2016).
In a similar vein to steam cracking, the Pacol process falls short in several ways when it comes to sustainability. The Pacol and DeFine process requires 1.098 GJ/t of electrical power, as well as 16.3 GJ of fuel fired heat (Meyers, 2016).
The issue surrounding the Pacol and DeFine process (along with other processes utilizing n-paraffins) is that they tend to form mixtures with a greater proportion of n-olefins. To produce α-olefins, the oligomerisation of ethylene is preferred, utilizing primarily fossil-sourced ethylene. These methods include the Shell higher olefin process and oligomerisation using a Ziegler-Natta catalyst (Franke et al., 1995; Forestière et al., 2009). Due to their prevalence within non-fossil supply chains, the process outline and inventory data for these processes is given in section α-Olefins from ethylene.
These traditional methods of producing olefins bring forward substantial issues for Unilever's climate targets. With respect to the Carbon Rainbow initiative, both methods rely heavily on fossil carbon feedstocks. This leads to the introduction of fossil carbon into the product supply chain, ultimately providing a pathway for fossil carbon to be introduced into the atmosphere. These processes also work heavily against the Clean Futures initiative, with positive GWPs for both processes across their respective product life cycles, dragging the product's environmental impact further from Net Zero. These sustainability hot spots provide a strong initiative for research into the defossilization of olefins and their production methods.
Technology overview for the formation of defossilized LAS-appropriate olefins
With respect to the scope of this review, reaction routes have been selected due to their eventual offering of defossilized feedstock options. All pathways will start from a defossilized feedstock and show the reactions between feedstocks and intermediates to form LAS-appropriate olefins (straight chain alpha-olefins of length C9 − 14).
It should also be noted that this review assumes (where necessary) a distributed production-based supply chain. defossilization often requires location specific materials, such as a point-source of CO2 or waste plastics from a collection facility. With this review focussing specifically on the technologies of chemical manipulation, it is therefore assumed that these materials are readily available, though further assessment of supply chain threats will be discussed in section Finalized formulation tree diagram and future work and further studies.
As a point on nomenclature, a degree naming system has been utilized to show how far each platform intermediate is from the final product, where first-degree platform chemicals being one significant reaction step from the LAS-appropriate olefins, second-degree platforms one step from them and so on.
Methods of olefin production from first-degree platform chemicals
The production of LAS-appropriate alpha-olefins can be broken down into reactions entailing several intermediate (or “platform”) chemicals. The production of these platform chemicals can then be defined, either from raw materials or previous-iteration platform chemicals, and so on. This results in a production tree-diagram, displaying the potential routes to LAS through non-fossil means.
With respect to the formation of LAS-appropriate olefins, two chemical intermediates were identified, long chain linear alkanes and ethylene. The reaction methods to form olefins from each intermediate are summarized below.
Olefins from linear alkanes
The production of olefins from long-chain linear alkanes can be broadly defined as cracking. As a process, cracking entails the splitting up of long-chain alkanes into shorter alkanes and olefins which are subsequently separated through distillation. Cracking can be broken down into two sub-categories. A detailed description of each method follows.
Fluidised catalytic cracking
Fluidised catalytic cracking (FCC) works by breaking down long chain into a mixture of shorter chain alkanes and olefins using a fluidised bed reactor (Gholami et al., 2021). The use of a catalyst means that cracking can be achieved at a much lower temperature than traditional steam cracking. The heavy hydrocarbon feed is vaporized and pumped through the catalytic fluidised bed at temperatures between 550 and 750°C. Simply put, this causes the breaking of carbon-carbon bonds within the long chain hydrocarbons, forming the desired mixture of shorter chain hydrocarbons. The product distribution can be altered through altering the temperature and pressure of the reactor, as well as the choice of catalyst used. This plant configuration is illustrated by Figure 4.
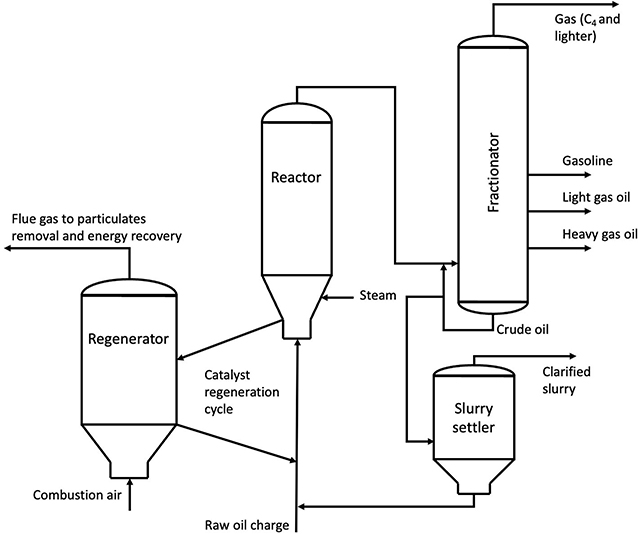
Figure 4. A schematic showing the FCC reactor configuration (after Gholami et al., 2021).
Commercially, cracking to alkanes and olefins of the appropriate length for LAS is not generally performed. Lighter olefins (C2-C5) are preferred due to their superior monetary value, however the possibility of C9-C14 olefins through cracking should not be disregarded, as the makeup of renewable hydrocarbon sources (for example bio-oil from waste biomass) can provide hydrocarbons which can be cracked to form these desirable medium length hydrocarbons.
Steam cracking
Steam cracking works in a very similar way to FCC as listed above, however does not utilize a catalyst, instead just relying on high heat and pressure delivered through high pressure superheated steam. Commercially, steam cracking tends to be favored due to the financial benefits of less-specialized plant and the avoidance of expensive catalysts (Akah et al., 2019).
In a similar vein to FCC, products from steam cracking tend to be much shorter than the desired olefins for LAS, however appropriate-length olefins can be formed through cracking and so should not be disregarded if handling long-chain hydrocarbon mixtures from renewable sources.
α-olefins from ethylene
As mentioned in section Medium chain olefins (C9-C14), the production of α-olefins via ethylene oligomerisation is the most popular method, utilizing fossil-based ethylene feedstocks (Franke et al., 1995). These processes however are entirely independent from the feedstock in question and are just as relevant in defossilized supply chains, hence their inclusion within this study. The two technologies of greatest impact within this field are listed below, with a combined inventory for both processes listed afterwards.
Shell higher olefin process (SHOP)
The methods outlined above are used once the target length of hydrocarbon chain (C9 to C14) has been achieved. The active chemistry of olefins also allows for the bonding of olefins to themselves in order to create longer-chain olefins, achieving the desired carbon chain length. Ethylene oligomerization to higher olefins is a process undertaken at a large scale, commercially known as the Shell Higher Olefin Process. As of 2014, over 1 million tons of olefins were derived from ethylene via SHOP each year, with a plant looking to expand global production by 20% currently under development in Qatar (Keim, 2013).
The SHOP process utilizes three different reactions (Griesbaum et al., 2010):
(1) Oligomerization of ethylene into olefins with a wide range of lengths
(2) Isomerization of short chain olefins (C4-C10) with long chain olefins (C20+) to move the functional C=C from the alpha position (between the first two carbons of the respective chains) to an internal position
(3) Metathesis of internally functional olefins, creating two similar length olefins in the C9 to C14 range.
The first of these reactions is conducted by passing ethylene over a nickel catalyst at a temperature of 90–100°C and a pressure of 100–110 bar, forming a mixture of even length linear olefins with a range of C4 to C40. This mixture is then distilled to separate the different chain length hydrocarbons. The subsequent 2 reactions then follow, with the isomerization taking place next by passing the alkenes over a solid potassium catalyst, internalizing the functional group of the olefins. The internally functional olefins are then mixed with respect to chain length, with long chain and short chain olefins reacting in a 1:1 ratio over an alumina/molybdate catalyst, forming 2 medium length olefins (C9-C14) of the optimal length for LAB/LAS application (Griesbaum et al., 2010).
Oligomerisation using Ziegler-Natta catalysts
Ziegler-Natta catalysts provide the basis to the most common method of producing α-olefins from ethylene. Discovered in 1953 by German Chemist Karl Ziegler, the hybridized titanium tetrachloride (TiCl4) and diethylaluminium chloride [(C2H5)2AlCl] was found to be efficient at combining ethylene monomers into longer-chain α-olefins at atmospheric pressure (Shamiri et al., 2014). The process occurs within a fluidised bed reactor, with a combined gas stream nitrogen and hydrogen used to fluidise the bed, which in turn provides the large catalyst surface area for the reaction to occur, as well as the removal of any latent heat from the highly exothermic reaction (Shamiri et al., 2013).
Inventory data for the oligomerisation of ethylene
Due to the industrial presence of both processes, finding accurate or reliable inventory data for both processes is nigh-on impossible. As a result, only one item of literature is frequently cited for inventory data for the oligomerisation of ethylene. The paper “A Life-Cycle Inventory for the Production of Petrochemical Intermediates in Europe,” led by German Chemist Marina Franke, outlines the two processes above, alongside the production of n-olefins via the Pacol and Olex processes, to provide an overall inventory for the production of olefins from fossil sources (Franke et al., 1995).
Using the supply chain diagram shown in Figure 5, Franke broke down the energy requirements and material balance for each process, providing an overall inventory for n-olefin production. This data was then used for the entry of olefin production within the Ecoinvent 3.8 database, which summarizes the mass and energy balances in a clearer way than Franke. These figures are given the Table 1.
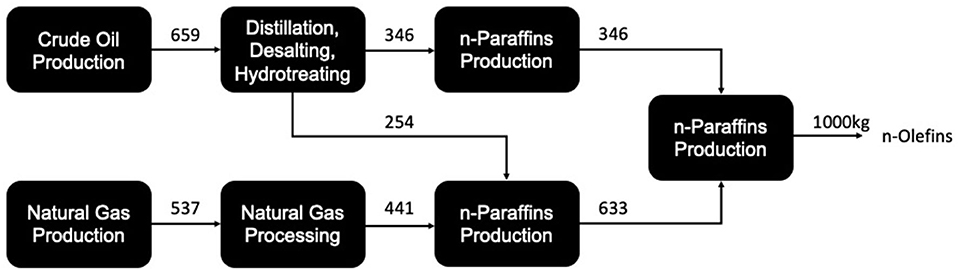
Figure 5. The production of olefins from fossil-based sources (process loss streams not included) (after Franke et al., 1995).
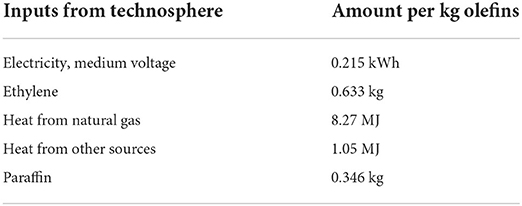
Table 1. Inventory data for the oligomerisation of ethylene (Franke et al., 1995; Wernet et al., 2016).
The issue with the combined inventory is the unknowing of how the energy inputs are distributed between each process. Despite this, the inventory does give a reasonable illustration of the energy requirement for the ethylene oligomerisation process.
Olefins from first-degree platform chemicals—formulation tree diagram
Now these methods have been identified, the first branches of a formulation tree diagram can be presented (Figure 6).
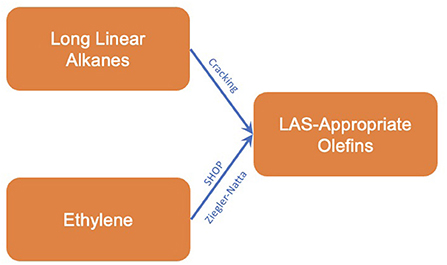
Figure 6. Tree diagram for the production of LAS-appropriate olefins from first-degree platform chemicals.
Production methods of first-degree platform chemicals
To complete the production map of LAS from renewable sources, methods to produce renewable platform chemicals must be sourced. The two first-degree platform chemicals discussed shown in Figure 6 both have multiple routes of production to be considered.
Long linear alkanes production
When considering alkanes for LAS-appropriate olefins, long chains (C20+) are necessary due to the cracking that the alkanes must face for the formation of the olefin. For sustainable long linear alkanes, two major technologies exist which both have the potential of using renewable carbon sources which align with Unilever's Carbon Rainbow initiative.
Pyrolysis of waste plastics
The pyrolysis of waste polymers leads to the formation of pyrolytic oil, a compound containing a wide distribution of alkane chains. Pyrolysis entails the “thermal degradation of polymeric materials by heating in absence of oxygen in an inert atmosphere” (Butler et al., 2011). There are many varieties of plant configuration when it comes to polymer pyrolysis, the most common of which is the use of a bubbling fluidised bed reactor. Here polymers are shredded and passed through a fluidised bed reactor at temperatures in the range of 400–800°C, breaking apart the polymer chains into shorter length hydrocarbons. The choice of catalyst, temperature and pressure fundamentally alter the final product distribution.
Within the literature, studies have investigated modeling the separation of pyrolytic oils and what length hydrocarbons can be expected from different pyrolysis scenarios. A study by the Warsaw University of Technology presented a model of various scenarios of pyrolytic oil production as well as final product distribution of the oil (Krzywda and Wrzesińska, 2021). The oil compositions in this study focussed on the production of alkanes and so differ from other pyrolytic oil compositions. From this study it can be calculated that pyrolytic oil has the potential to be a significant source of long chain alkanes, with a weight fraction of 32.64% being C20+ alkanes which could then be cracked into LAS-appropriate olefins (Krzywda and Wrzesińska, 2021).
From a life cycle analysis perspective, the literature can provide a wide array of studies. Given the commercial scale of pyrolysis already, reliable data can be sourced for the entire life cycle of a plastics to pyrolytic oil plant. One study split the production and use of plastic-sourced pyrolytic oil down into several stages, with a comprehensive mass and energy inventory for each stage (Jeswani et al., 2021). From a cradle-to-gate scope, the collection, sorting and production of 1 ton of pyrolytic oil required 1,410 kg of mixed plastic waste and utilized over 4,000 MJ of electrical energy. The reaction also required 10 kg of natural gas and formed 110 kg of char as a co-product. Therefore, as a process the pyrolysis of waste plastic does provide an alternative source of alkanes from non-virgin-fossil sources, yet at the expense of high electrical energy requirements (Jeswani et al., 2021).
Pyrolysis of waste biomass
Following a similar process to the pyrolysis of waste plastics, the pyrolytic oil derived from the pyrolysis of waste biomass can also be used to form long-chain hydrocarbons suitable for cracking to LAS-appropriate olefins. Whilst fundamentally the same process as with plastics, the pyrolysis of biomass does require a nickel catalyst and must be done in a hydrogen gas atmosphere to promote the formation of long linear alkanes (Demirba, 2003). This does limit the sustainability potential of the process due to the difficulties in producing hydrogen, however the process does unlock the potential to use biomass for the formation of linear alkanes. The product distribution of the liquid hydrocarbons formed is also presented by Demirbaş, showing alkane fractions for the pyrolysis of five different waste biomass feedstocks. All five feedstocks show a relatively normal distribution of fractions, with a mean fraction of all sources of between 23 and 24. Each distribution also contained at least a 70% share of alkanes with a carbon chain length of 20 and above, the suitable length for cracking to LAS-appropriate olefins.
With respect to life cycle inventory data, the production of pyrolytic oil from waste biomass has an obviously comparable impact on the environment when compared to the pyrolysis of waste plastics. An LCA of pyrolytic oil production for the use as a value-added chemical shows the electricity consumption to produce one ton of pyrolytic oil is 3319 MJ/t (Vienescu et al., 2017). Another study into the production of pyrolytic oil, in which the life cycle analysis of the production of pyrolytic oil for transport use was assessed (Steele et al., 2012). Whilst the inventory does not break down beyond a cradle-to-grave scope meaning the energy associated from a cradle-to-gate perspective, the aligned product distributions of pyrolytic oil fractions with the other studies mentioned reinforces the potential for pyrolysis to be used for the production of long linear alkanes.
Fischer-Tropsch synthesis of synthesis gas (syngas)
Syngas (the mixture of CO and H2) is a commercially used an intermediate for the formation of hydrocarbon fuels. Syngas is formed from a wide variety of resources through varying degrees of source, technology readiness level (TRL) and overall sustainability. These will be considered in the following section Production methods of second-degree platform chemicals (and above). This section will outline the process of converting syngas into hydrocarbons, the Fischer-Tropsch (FT) process.
Developed in Germany in 1925, before commercilization in 1936 as a means of deriving petroleum from coal, the FT process works as to generate CH2 monomer groups from CO and H2, forming water as a by-product (Schulz, 1999). This reaction takes place in the presence of a catalyst, selected specifically for application, as well as within a range of temperatures and pressures. For the typical formation of LAS-appropriate alkanes (then olefins), a cobalt catalyst is used at a temperature of 200°C and 25 bar within a packed column (Iribarren et al., 2013). The ratio of hydrogen to carbon monoxide within the syngas is required to be around 2:1 for the formation of hydrocarbons (Griffin and Schultz, 2012).
From an LCA perspective, the formation of LAS-appropriate alkanes from syngas via the FT process has a low impact on the environment due to the exothermic nature of the process. This means that the electricity and steam generation required for the FT process can be provided internally and still have a net generation of electricity which can be sold back to the grid (Navas-Anguita et al., 2019). From the study above by Schulz (1999), a comparable study completed at the University of Georgia (Okeke et al., 2020) which states that the only inputs required for the FT process are electricity and the cobalt catalyst lost when spent or due to separation losses. The University of Georgia study has broken down the entire process of producing electricity from the combustion of biologically sourced alkanes onto individual stages, including the inventory for the FT process and the associated product upgrade method. This data greatly increases the viability of the FT process as a defossilized and environmentally sustainable branch of a chemical formulation tree.
Ethylene production
When considering the production of ethylene to form LAS-appropriate olefins via the SHOP process, many more routes must be considered. This is in part due to the widespread interest in renewable ethylene production and its many uses as a platform chemical within many organic supply chains. With respect to the Carbon Rainbow, defossilized ethylene production methods exist for all categories of the Rainbow. The ethylene formation methods listed below are formed from either raw materials or the next (and final) stage of platform chemicals.
Ethylene from catalytic ethanol dehydration
The catalytic dehydration of ethanol is one of the most used practices for ethylene in the chemical industry (Mohsenzadeh et al., 2017). Whilst a variety of alternatives exist using differing catalysts and process conditions, the science behind the reaction remains unchanged. The dehydration reaction is endothermic, requiring 1,632 Jg−1 of heat (Mohsenzadeh et al., 2017), meaning the reaction conditions throughout all variations of the process are of high temperature and/or pressure. Fan et al. (2013) compiled a review of ethylene formation by catalytic dehydration of ethanol. This study showcased the wide variety of processes, their catalysts and process conditions in order to summarize how the process is achieved commercially. The most commonly used catalyst within industry is based on the acidic nature of gamma-alumina (γ-Al2O3). This allows for the reduction of ethanol by providing the alcohol functional group with a hydrogen ion, forming water, before the subsequent carbocation is formed into ethylene and the acidic nature of the catalyst is restored.
From an LCA perspective, the dehydration of ethanol to ethylene holds a large environmental burden through the high demand for heat. As part of a comparative LCA and TEA on bioethylene production, Yang et al. (2018) presented information on the formation of ethylene from biologically sourced ethanol, shown in Table 2. Whilst this example focuses on biological sources, the inventory data for ethanol reduction is independent of the source of ethanol. Table 2 concerns only the production of ethylene from ethanol, with the production of ethanol to be covered in the next section Ethanol production covering the production of second-degree platform chemicals.
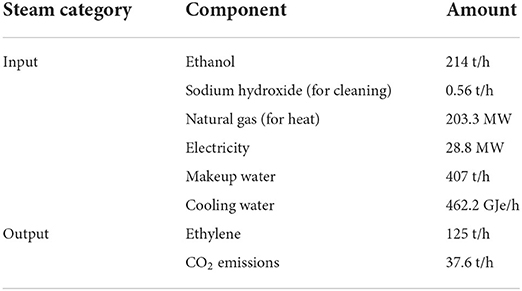
Table 2. A table showing the life cycle inventory of the reduction of ethanol to ethylene [derived from Yang et al. (2018)].
Ethylene from the pyrolysis of waste plastics
As described in section Pyrolysis of waste plastics, the pyrolysis of waste plastics can be undertaken as a means of producing platform chemicals for the eventual production of LAS-appropriate olefins. In section Pyrolysis of waste plastics, the pyrolysis oil formed prioritized the formation of long-chain alkanes for cracking to C9 − 14 alpha-olefins. In this section, the conditions of pyrolysis represent a more common distribution of pyrolytic oil, before the oil is cracked into ethylene.
The cracking process used here is of similar set up to the steam cracking outlined in section Fluidised catalytic cracking, which is favored due to its production of shorter olefins (ethylene). Despite taking on the environmental burden of the cracking and then reforming to LAS-appropriate olefins, this process does allow for utilization of all pyrolytic oil fractions.
The study used to show life cycle inventory data in section Fluidised catalytic cracking (Jeswani et al., 2021), also includes a separate inventory for the cracking of the pyrolytic oil down to ethylene. This process, in similar vein to the cracking processes covered in section Olefins from linear alkanes, is highly energy intensive, with over 1.5 GJ of electricity and auxiliary fuels required to produce 1 ton of ethylene in the cracking section alone. This, on top of the energy required to produce the pyrolytic oil (covered in section Pyrolysis of waste plastics), means the overall process of deriving ethylene from the pyrolysis of waste plastics struggles to work effectively toward a sustainable supply chain.
Formation of ethylene from methanol
The reduction of methanol into ethylene (or the “MTO” process, short for methanol-to-olefin) follows a straightforward mechanism of a two-stage dehydration of two methanol molecules, in turn forming one molecule of ethylene via dimethyl ether (DME) (Olah, 2005). The reaction takes place in a fluidised bed reactor, with a bed of acidic zeolite catalyst providing the reaction surface. The product then undergoes a series of separation stages, producing the two major outputs of ethylene and propylene, the latter of which can either be sold or cracked and reformed to ethylene (Keil, 1999). The MTO process has remained largely unchanged since its discovery by Mobil in the 1980s and since its commercilization in the decades since (Flowserve Corporation, 2019). As a result, literature from the 1990s is still frequently cited, with research on the UOP process (Keil, 1999) being cited by review papers on the MTO process (Ragaert et al., 2017; Gogate, 2019). The plant configuration of the UOP process, which was the first commercialized case of MTO, is outlined in Figure 7.
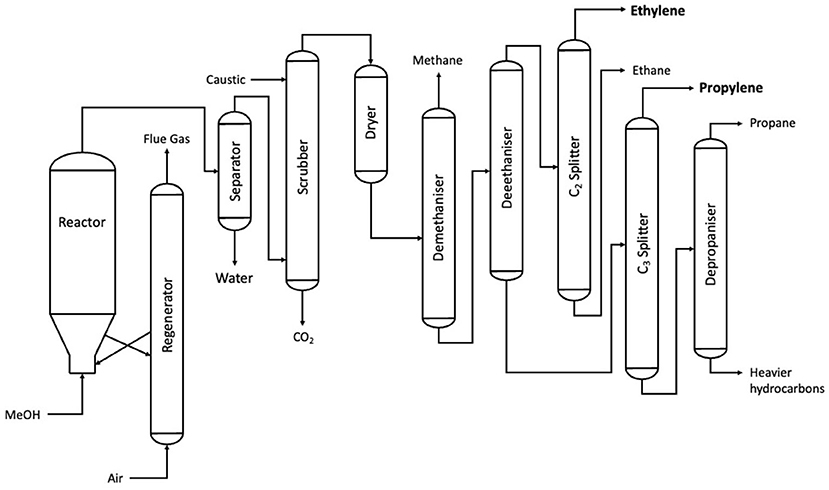
Figure 7. A process flow diagram for the UOP MTO process (after Keil, 1999).
The production of ethylene from methanol has been one of the most prominent processes with respect to renewable chemical production through the past three decades. World-renowned chemist George Olah advocated for a “methanol economy” in the 1990s and went on to publish several papers about the versatility of methanol alongside his colleagues Prakash and Goeppert of the University of Southern California. Since these early developments, the commercilization of the MTO process has continued with seven industrial installations as of 2019, all of which follow a similar process to the UOP process outlined in Figure 7. These processes were summarized by Gogate, who gave an in-depth summary of each process. Of the seven industrial installations of the MTO process, six are based in China, with the seventh in Belgium being licensed by UOP (Gogate, 2019). These facilities range in scale from 0.2 to 0.8 MM TPA and all operate at temperatures and pressures between 450 and 550°C and 1–5 atmospheres of pressure where listed.
With respect to life cycle inventory data, many companies withhold specific data as a means of protecting sensitive information from market rivals. One review however does provide data on several MTO processes, one of which being the UOP process. The production of ethylene from methanol requires 13 GJ energy per ton of ethylene produced according to a review by Utrecht University in 2008 (Ren et al., 2008), which cites data directly from UOP. Whilst this quantity is exceedingly high, it is worth noting that the product distribution of the UOP MTO process also contains significant fractions of other high value chemicals such as propylene, with 26% of the final product by weight accounting for ethylene. After a simple mass allocation, it can be estimated that ethylene from methanol produces 3.38 GJ per ton (Ren et al., 2008). This ratio is somewhat comparable to another study by Utrect University, which has a predicted yield of 37% and a GJ per ton value of 4.70 (Joosten, 1998).
The possibilities of defossilized methanol production are one of the main drivers for the use of the MTO process within defossilized chemical production. These methods will be outlined in the next section Methanol production when the formulation tree diagram is completed.
Direct formation of ethylene through electrochemical reduction of CO2
The final method of ethylene production to be assessed in this section is via the electrochemical reduction of CO2 into ethylene. The reduction of CO2 occurs in an electrochemical reactor, in which water and CO2 are introduced either side of an ion exchange membrane in the presence of an electrolyte. This, in short, splits the water into H+ and O2− ions, with the former then reacting with the CO2, forming reduced carbon compounds, such as carbon monoxide, ethanol and ethylene. These form on the cathode, being released as a gas which is then separated down into its individual components via separation (Berkelaar et al., 2022). This reactor setup is shown in Figure 8, for the example of CO2 to CO conversion.
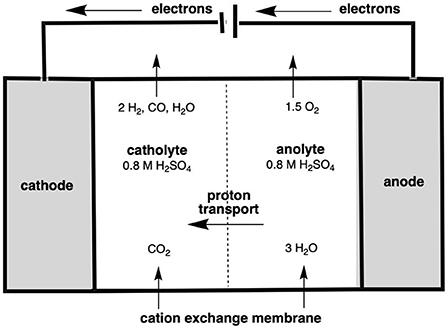
Figure 8. Electrochemical cell reactor showing the reduction of CO2 to CO (after Berkelaar et al., 2022).
The total formation of ethylene requires two CO2 molecules and results from a series of reduction reactions which all take place at the cathode. The first intermediate within the reaction set forms ethylene oxide, which is subsequently reduced to form ethylene under set process conditions and using a copper-based catalyst (Garza et al., 2018). In part, the study mapped out the possible products from the electrochemical reduction of CO2. The matrix of reactions presented in their paper “Mechanism of CO2 Reduction at Copper Surfaces: Pathways to C2 Products” shows how catalysis can be used to form a variety of products directly via electrochemical reduction. The route taken is ultimately decided by altering the “microenvironment” in which the reaction takes place (Kim et al., 2022).
Despite this, the direct reduction of CO2 to ethylene has not commercialized yet due to a low Faradaic efficiency (FE) and high electric potential requirements (Kas et al., 2015). Whilst further research into this in order to improve the efficiency, lab scale demonstrations have only reached FEs of around 70% (Bisztyga-Szklarz et al., 2021), with scaled up capabilities not fully understood. Nevertheless, the potential for direct CO2 to ethylene electrochemical reduction is present and must be considered, as future improvements could well lead toward a commercially viable form of the reaction.
With respect to inventory data, several life cycle assessments have been undertaken for direct CO2 to ethylene reduction, all of which are based upon process modeling and/or laboratory upscaling. The first analysis in this study considers a lab scale inventory, using a comparable process setup to the one shown in Figure 8 (Ai et al., 2022). The entire process is included within the scope, with a condensed inventory given in Table 3. From the inventory data in Table 3, a simple energy demand of 39.536 kWh per kg of ethylene can be calculated. Whilst the data presented here is of value, issues can be seen in the form of electrode production per kg of material falling below the decimal place threshold (with all electrode materials listed as 0.000 kg per kg ethylene). This would not be the case however at commercial scale, with the environmental effects of copper mining and processing proving detrimental to process sustainability.
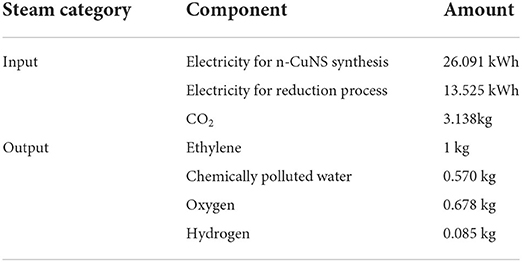
Table 3. LCI for the electrochemical reduction of CO2 to ethylene at lab scale (Ai et al., 2022).
A similar assessment of the Institute of Chemical Engineering Sciences in Singapore also presents lab-scale data, but also includes a “large-scale” model inventory based on the lab-scale experiments (Khoo et al., 2020). This process has a comparable energy requirement to the previously mentioned study, of 38.6 kWh per kg ethylene but represented at a scale by order of 1 ton ethylene. Whilst this data can be seen as useful, questions must be asked of the validity of the assumptions made within the model, in part due to the linearity between the lab-scale and the large-scale data not seeming to account for the additional inputs required for a commercial system, as well as again the impacts associated with electrode manufacture. These factors must be considered within future sustainability assessment of the process.
One final study to be included as part of this review looks to compare a variety of organic products from the electrochemical reduction of CO2 (Kibria Nabil et al., 2021). This study will be reviewed in greater detail when looking at the production of syngas in section Syngas production, though it also provides electrical energy requirements and global warming impacts (GWI) for the production of ethylene through electrochemical reduction. The electrical energy requirement is shown as around 30kWh per kg ethylene, comparable to the previous study by Khoo et al. (2020). The study also concludes that the production and separation of ethylene has the second lowest GWI (behind syngas) in a range of 2.00-2.94 kgCO2e/kg ethylene produced, due to “lowest separation energy required for [the] product[s]” (Kibria Nabil et al., 2021).
First-degree platforms from second-degree platforms and raw materials—formulation tree diagram
Following the review of sustainable ethylene and long linear alkanes production, the next degree of branches can be added to the formulation tree diagram (Figure 9).
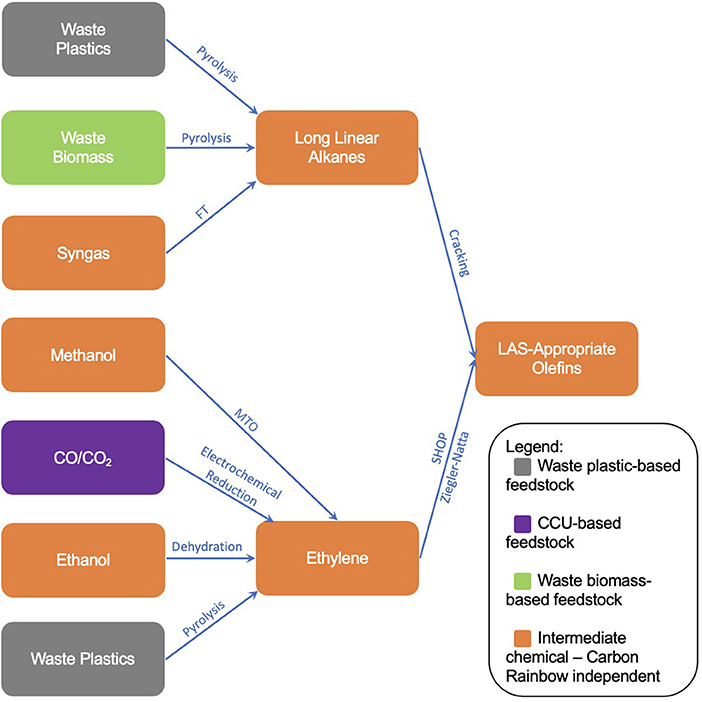
Figure 9. Tree diagram for the formulation of LAS-appropriate olefins from first- and second-degree platform chemicals.
Production methods of second-degree platform chemicals (and above)
To fit the scope of the review, the final degree of reactions must be considered to show all possible reaction routes from raw materials through to the desired product.
Syngas production
Syngas as a platform “chemical” represents a very versatile compound which can be found in several different routes to LAS-appropriate olefins via a variation of the Fischer-Tropsch process. A mixture of carbon monoxide and hydrogen, syngas holds many reaction possibilities with respect to the formation of hydrocarbons. With regards to production, there are several methods to produce syngas from defossilized feedstocks which are all considered to fit the scope of the review.
Gasification and pyrolysis of waste biomass
One of the main sources of defossilized syngas currently available at a commercial scale is the gasification of waste biomass. The gasification of waste biomass occurs over four different stages within the gasifier. The biomass is first dried at temperatures between 100 and 200°C, before being pyrolyzed. This stage is done in anaerobic conditions and produces biogases from the thermal decomposition of the waste biomass and at temperatures of around 800 to 1,000°C. The mixture of gases is then oxidized by introducing air and steam, forming the final mix of carbon dioxide, carbon monoxide and hydrogen, with waste tar and ash also produced (Kumar and Aarthi, 2020). Methane and water are also formed, though these react through the steam-methane reformation reaction, forming further molecules of carbon monoxide and hydrogen. Of these produced gases, carbon monoxide, carbon dioxide and hydrogen then undergo the water-gas shift (WGS) reaction, in which the desired ratio of hydrogen to carbon monoxide is achieved for a given application. This is reached through the addition or removal of water and adapting the pressure conditions of the mixture. The equation for the WGS reaction is shown in equation 1.
With respect to plant, the waste biomass is first pre-treated through drying and milling, before being preheated to 600°C at which the pyrolysis process begins. At this point, the biomass enters the gasifier which takes the form of one of three reactors, a fixed bed reactor, a fluidised bed reactor and an entrained flow reactor. The reactor used is dependent on the biomass input, the need of a catalyst and the potential for tar to form during the gasification process (Kumar and Aarthi, 2020). The syngas then undergoes the WGS reaction in a separate reactor (or series of reactors) in order to achieve the optimum ratio of hydrogen and carbon monoxide. For the application in section Fischer-Tropsch synthesis of synthesis gas (syngas) the desired ratio is 2:1, though the formation of alkanes can occur at rations of 0.6:1 and above (Griffin and Schultz, 2012).
In terms of process inventory data, many studies have been undertaken to assess the production of syngas through the gasification of waste biomass given its prevalence in the field of defossilized chemical supply chains. The online database of LCI data Ecoinvent 3.8 holds four entries for the formation of syngas from waste biomass gasification, with two concerning the use of a fixed bed gasifier and the other two the use of a fluidised bed gasifier. These entries are then split into entries for Switzerland and for “Rest of World,” but both utilize the same material and energy balances. From the inventory data, the main energy input from the technosphere is electricity, with around 86 MJ of electrical energy required for oxygen compression to form one ton of syngas (Wernet et al., 2016). Whilst this initially seems low, the gasification of waste biomass also involves the combustion of the biochar after thermal decomposition. This therefore means that the process is self-sustaining with respect to heat energy, providing an excess thermal output of 5 MWth (Jungbluth and Chudacoff, 2007). The inventory for fluidised bed configuration varies slightly, with the added necessity for silica sand and zeolite as the catalyst, though with a comparable required electrical input. Due to this self-sustaining nature, the use of gasification within defossilized supply chains is highly viable and justifies its research within this review as the high heats required do not require fossil-based fuels.
In a similar vein to gasification, pyrolysis also provides a potential route to syngas with the development of new technologies within recent years. Whilst pyrolysis has predominantly been used to form liquid pyrolytic oils as previously summarized, the use of microwave assisted pyrolysis of biomass to form gaseous products has been researched extensively, with a mass and energy summary published by the University of Minnesota in 2020 (Zhou et al., 2021). Here, a lab-scale pyrolysis system is accompanied by six 1.5 kW magnetrons, providing microwave radiation that aids in the thermal decomposition of the waste biomass at temperatures of 800 °C. The presence of this process gives light to the idea that new technologies are still being developed for techniques that are well integrated into supply chains and may compete against processes like biomass gasification within the timeframe of many industrial climate goals.
Gasification and pyrolysis of waste plastics
Like biomass, waste plastics can too be gasified to produce syngas. This follows a very similar set up to the biomass gasification outlined in the previous section, utilizing a largely self-perpetuating process in which waste plastics are milled and thermally decomposed to produce syngas. Unlike biomass however, the gasification of waste plastics is yet to be done on a widespread scale, meaning many studies are reliant on process modeling or data collected from large-scale pilot plants (Saebea et al., 2020). With regards to energy requirements, the gasification of waste plastics requires some energy for oxygen compression. As outlined by a computational LCA completed by the Japan Initiative for Marine Environment, which looks at utilizing waste plastics from the ocean, 222 MJ of electricity are required for every 1,000 NM2 of syngas produced. A somewhat comparable amount to the gasification of biomass, but utilizing an alternative feedstock that could be utilized in areas lacking in waste biomass production (Japan Initiative for Marine Environment., 2019).
Electrochemical reduction of CO2 to CO
As mentioned in section Direct formation of ethylene through electrochemical reduction of CO2 when discussing the potential for the formation of ethylene from CO2 via electrochemical reduction, the conversion of CO2 to CO is also made possible by a similarly configured process. The reduction of CO2 to CO is innately energy intensive given the stability of CO2 and so effective catalysis is required in order to allow the reaction to occur. The CO2-water electrochemical reduction reaction, as shown by Figure 8 in section Direct formation of ethylene through electrochemical reduction of CO2 can result in a variety of products, the simplest being the formation of CO with a by-product of H2, or syngas (Garza et al., 2018). With regards to the production of syngas compared to ethylene, recent research efforts have investigated ways in which the H2:CO ratio can be affected by different reaction conditions within the electrochemical reactor. As part of a research paper published in 2017, Hernández et al. (2017) carried out the research into factors affecting the syngas ratio, including the configuration of the reactor, reactor cell potential used, temperature, pressure and electrode materials. Chen et al. (2018) furthered this area by reviewing the technological challenges associated with commercial CO2 reduction, namely the efficient capture and purification of atmospheric CO2, the efficiency of the cells, sustaining catalytic density and the overall stability of the cells (Chen et al., 2018). Whilst these issues are substantial and are key to slowing the progress of commercial syngas production through this method, this technology has been proven at small scales and has the potential to become commercial in the future.
Life cycle assessments on the electrochemical reduction of CO2, as mentioned in section Direct formation of ethylene through electrochemical reduction of CO2, are based largely on simulated process data and sometimes the upscaling of lab-scale processes. Of the two assessments sourced as part of this review, both utilized simulated data generated from process modeling software. The first assessment was collated by Andrea Schreiber of the Institute of Energy and Climate Research, which utilized the process modeling and life cycle assessment software GaBi to generate inventory and impact for a small-medium scale syngas production site (Schreiber et al., 2020). The output syngas was modeled to have a H2:CO molar ratio of 2, the optimum for hydrocarbon production, with the process requiring an electrical input of 32.8 MJ/kg of syngas produced as its only energy requirement. The process also produces 1.5 kg of oxygen for every kilo of syngas, which can be separated and sold on as a by-product (Schreiber et al., 2020). The project also compared this data to the fossil-dependent process of steam-methane reforming which was not considered for this review due to the lack of defossilized methods of defossilized methane production.
The second assessment included in this review was compiled by Kibria Nabil et al. (2021) which looked to compare multiple products from the electrochemical reduction of CO2, including both syngas and ethylene which are both considered in this review. The assessment used data sourced from Aspen Plus and drew conclusions that the reduction of CO2 to syngas held the lowest energy requirement per unit mass of product produced, as shown in Figure 10.
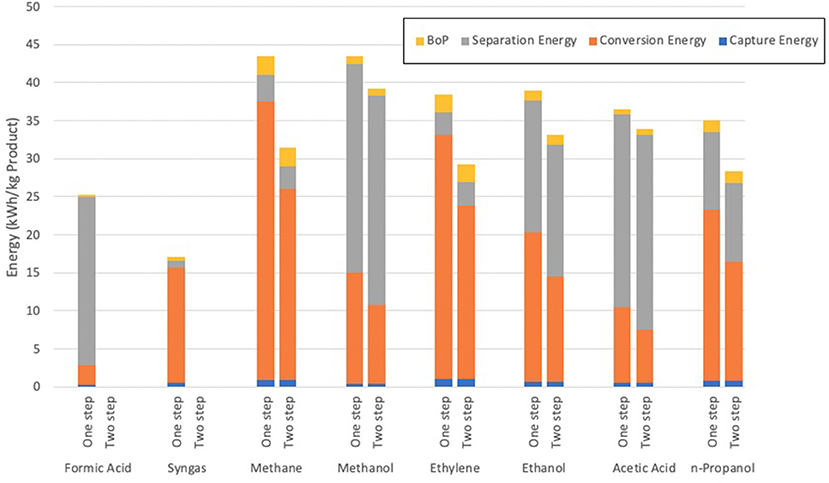
Figure 10. The required energy for the production of chemicals from the electrochemical reduction of CO2 (after Kibria Nabil et al., 2021).
As can be inferred from the graph, the total electrical energy requirement to produce syngas is around 18 kWh/kg, or about 65 MJ (Kibria Nabil et al., 2021). Whilst this figure is substantially higher than the study by Schreiber, it must be understood that a variety of factors have been assumed between these assessments which could well cause variation of results due to the low TRL nature of the process being assessed. The study also calculated a total GWI for the production and separation of syngas, with a final range of 1.66–2.13 kgCO2e/kg syngas produced. This was the lowest impact of the assessed products due to the low separation energy required to remove syngas from the product mixture.
Methanol production
Methanol from syngas and CO2
The reaction of the constituents of syngas (CO2/CO and H2) is the most used method of methanol production to date, with the defossilization of methanol simply depending on the syngas feedstock (International Renewable Energy Agency, 2021). This section therefore will simply review the gate-to-gate process of syngas to methanol, with the defossilized syngas methods outlined in section Syngas production providing apt solutions for methanol defossilization. This section will also focus on the differences between the reduction of typical syngas which contains higher concentrations of CO when compared to CO2, to the reduction of pure CO2 which is emerging as a viable option as a means of utilizing atmospheric CO2.
The process of producing methanol from syngas follows two reactions, from CO2 and CO respectively, with both reactions being exothermic, giving off a large amount of heat in the process.
The reactions shown in Equations 2 and 3 are subject to high pressure and temperature to achieve a fast rate of reaction, operating at 80 bar and 200°C (Giuliano et al., 2020) with a selectivity of over 99.8% methanol (Dieterich et al., 2020). The process is self-sustaining due to the exothermic nature of the reactions providing ample heat to sustain these temperatures, though external compression is required to maintain the high pressures. A review of methanol-producing technologies by Dr Guillermo Garcia-Garcia of the University of Sheffield estimates the electrical energy required to sustain these reactions is 0.17 MWh per ton of methanol (Garcia-Garcia et al., 2021). This figure only shows the process energy and not showing the energy required by the generation of the reactants.
With regards to newer technologies, the reaction of pure CO2 to methanol can also be achieved by reacting CO2 with H2 under similar conditions. This process however brings additional on-costs and environmental impacts through the need of carbon capture for a pure CO2 feed stream, as well as processes for the generation of H2, usually electrolysis. These additional processes add a significant demand, with Garcia-Garcia stating that “more than 80% of the energy needed to produce methanol from CO2 is required to produce renewable hydrogen, whilst around 10% is needed to capture CO2 from a fossil-fired power station.” This leads to the necessity for renewable energy sources for both processes if defossilized production is to be achieved. Despite these high energy demands, the commercilization of a CO2 to methanol plant has still been achieved. In 2011, Carbon Recycling International (CRI) in Iceland commissioned the George Olah Renewable CO2-to-Methanol Plant achieving an annual production exceeding 4,000 tons (International Renewable Energy Agency, 2021). The CRI plant utilizes geothermal heat for the electrolysis of water to supply hydrogen, a resource which, if available, can provide the necessary power for hydrogen at no operational release of fossil CO2 to the atmosphere. IRENA reports that on top of this facility, 23 other facilities have either been commissioned or are planned for completion soon, with a potential global capacity of over 700,000 tons per year should all of the facilities come to fruition (International Renewable Energy Agency, 2021).
Ethanol production
Fermentation of primary and secondary biomass
The fermentation of biomass to produce ethanol is the oldest biotechnological process in human history (Taveira et al., 2021), with humans utilizing biologically sourced sugars to form ethanol and CO2 for over 10,000 years. In present day, fermentation remains the most popular method of ethanol production, with over 90% of global production sourced from corn or sugarcane sugar fermentation (Leal et al., 2014). This constitutes what is known as first-generation production, in which the first and only use of the plant material is to produce ethanol. Second-generation bioethanol utilizes waste, lignocellulosic biomass, such as corn stover or wheat straw, in which the “leftovers” of the production of corn or wheat for food are treated and fermented. This method holds a wider social acceptance, due to the ongoing debate of “food vs. fuel” in certain regions in which access to fertile land is difficult and the use of land to form fuels can be regarded as unacceptable, especially if the land could be otherwise used for food production. Second-generation bioethanol does not fall under the food vs. fuel debate as both constituents are produced. This method therefore is prioritized within this technology review, though both methods are reviewed to ensure a wide scope is covered.
The process of producing second-generation bioethanol follows a linear reaction pathway, in which lignocellulosic biomass is pre-treated by a dry mill to crush the biomass into smaller particles, before being broken down further by acid and high-pressure steam. This pre-treatment allows for the large, complex lignocellulosic sugars to be broken down to smaller, cellulosic sugars which are suitable for fermentation. The mixture then undergoes enzymatic hydrolysis, in which the cellulosic materials are broken down into glucose and xylose, two simple sugars which are then fermented using an on-site manufactured yeast culture. This fermentation process produces what is referred to as a beer, a mixture of ethanol, water and residual solids, which are separated by a vapor-phase molecular sieve, with the separated ethanol having a purity of 99.5% (Humbird et al., 2011). The main variables within the process are pre-treatment method, yeast choice and the enzymatic hydrolysis/fermentation configuration (Humbird et al., 2011; Mejía-Barajas et al., 2018). Each of these is largely dependent on feedstock choice. With respect to pre-treatment, steam explosion is preferred to acidic degradation in certain biomasses with higher fractions of lignin, such as straw or bagasse (Robak and Balcerek, 2018). Then with regards to yeast and plant configuration, both are chosen based on the quantities of each fraction of lignin and hemicellulosic matter within the feedstock.
With regards to the environmental impact of second-generation biomass fertilization, there is currently no commercial-scale facility that can be used for a sustainability assessment. This is down to several reasons, the key of which being profitability, due to the high costs and challenges of breaking down the hemicellulosic materials into fermentable sugars. Therefore, as with previous low-TRL processes, the use of process simulation provides the main backbone to most life cycle and technoeconomic assessments which focus on second-generation ethanol production. This was illustrated by a review conducted by Tahereh Soleymani Angili of AGH University in Poland, which considered 46 different papers on bioethanol production, with most of them focusing on second-generation biomass (Angili et al., 2021). Of these reports, one of the most insightful was completed by Lei Wang of Imperial College London, in which inventories for five different pre-treatment methods were assessed for the fermentation of wheat straw, a common second-generation biomass with comparable properties to other common biomasses such as corn stover (Wang et al., 2013). Of these five scenarios, every single one produced surplus electricity by burning the sedimentary wastes produced during the fermentation process, ranging from 1.6 to 26.4 MW electricity for every 83,333 kg of wheat straw processed. As a result of this combustion, the CO2 produced per liter of bioethanol ranged from 3.76 to 4.89 kg, though these figures would be net-negative from a cradle-to-gate scope due to the CO2 utilized during the biomass production. One common issue however is the sheer cost associated with these pre-treatment processes, with high pressure steam, acid catalysts and enzymes all required in large quantity, pushing the affordability of ethanol produced far beyond other methods of ethanol production (Humbird et al., 2011; Mejía-Barajas et al., 2018).
For the fermentation of first-generation biomasses, the process is simplified considerably due to fewer required pre-treatment steps for the extraction of fermentable sugars. Generally, primary biomass can be categorized into two groups, starch-based and sugar-based (Angili et al., 2021). Starch-based bioethanol utilizes feedstocks such as corn or wheat, which require the enzymatic hydrolysis pre-treatment, but no further processes, such as steam explosion or acidic degradation. This hydrolysis step breaks down the complex starches in the crop into glucose for fermentation. Sugar-based feedstocks, such as sugarcane and beets do not require this step due to the high yields of glucose from simply milling and the addition of water as a solvent. Both options vastly improve the affordability of the ethanol produced, though at a detriment of the issues surrounding the food vs. fuel debate (Angili et al., 2021), with a reduction in price of over $1 USD/gallon reported by the techno-economic assessment conducted by NREL in 2011 (Humbird et al., 2011). Though these numbers will have changed over time with market fluctuations and inflation, the illustration of the contributions of the pre-treatment to the overall production costs remain relevant.
Ethanol from the fermentation of CO
The fermentation of carbon monoxide to form value-added chemicals has been a key industrial research focus of the last 10 years or so. New Zealand-based biotechnology company LanzaTech has been the consistent front-runner, with the development of a process that utilizes bacteria to “ferment” CO to products like ethanol being their focus since establishment in 2005 (LanzaTech, 2022b). The process can be broken down into several steps, each relatively straightforward. Once the gas is collected/generated, it is treated to ensure the optimal H2:CO ratio for the desired product [1.25 for ethanol (Griffin and Schultz, 2012)] before passing into the fermentation reactor. Here, the gas mixture is exposed to the microbes who utilize the CO as a carbon and energy source (Handler et al., 2015). The fermentation reaction produces ethanol and other alcohols up to a size of C4. The mixture is then separated by distillation, with unreacted gases recycled back into the feed gas stream (Liew et al., 2016).
Despite the efforts to achieve commercial scale, LanzaTech still do not operate at a significant industrial scale. Currently, only one commercial plant operates in China, though future developments look to achieve a global production of 600 Mt/yr ethanol “in the near term” (LanzaTech, 2022a).
Due to the competitive nature of their work, LanzaTech have not provided any life cycle inventory data to the public domain, making accurate assessment of the CO fermentation difficult. The closest that LanzaTech has come to publishing inventory data being a comparative assessment of the gas fermentation of biomass-sourced syngas, however the assessment does not provide a breakdown of individual processes within the study and includes stages outside the scope of this assessment (Griffin and Schultz, 2012).
The literature however can provide a life cycle inventory and assessment compiled by Handler et al. (2015), who cites “peer-reviewed literature, government reports, life cycle inventory databases, and LanzaTech process engineering estimates” as the input data sources for the investigation. This assessment focuses on the production of ethanol as a combustible fuel, quoting environmental impacts and process inputs in units per MJe ethanol produced. Manipulating this data to fit the scope of the report, it can be deduced that a heat and power input can be estimated at 5.54 MJ/kg ethanol produced, with additional needs for the treatment of waste and product transport (Handler et al., 2015).
Single pass conversion of syngas to ethanol
The formation of ethanol from syngas is currently not commercially viable. The two possible production methods are the FT process and the carbonylation of syngas-based methanol, both of which suffer from poor economic performance due to low selectivity and in the latter case multiple process steps (Jiao et al., 2016). This has left room for research into ways of modifying or adding to these processes to favor the formation of ethanol. The addition of an extra CH2 group to a methanol is difficult and requires a separate homologation reaction with separate catalysts (Miranda et al., 2020). As a means of combining the methanol synthesis and homologation processes, Kang et al. (2020) published a process design in which tandem catalysis is used to form a single pass reaction to form ethanol from syngas. This process achieves a considerably higher ethanol selectivity of 64%. As catalysts, the single pass process utilizes modified zinc/zirconium-, zeolite- and platinum-based catalysts at temperatures between 230 and 270°C (Kang et al., 2020).
Within the literature, this data is the closest to an energy balance, life cycle inventory or techno-economic assessment. Though the high costs associated expensive metals within the catalysts can be assumed.
This process was deemed appropriate for this review as a means of illustrating the potential modifications to wellestablished processes, as well as bringing light to the fact that traditional FT synthesis cannot support the production of ethanol at a commercial scale.
Finalized formulation tree diagram and future work
The final parts of the formulation tree diagram can now be added, resulting in the final formulation illustration shown in Figure 11. The full set of technologies has also been presented in Table 4. The paths shown within Figure 11 will provide the basis for a newly developed sustainability screening tool, in which each technology will be individually assessed counterfactually against a baseline of “black” (fossil) production routes, for example the cracking of fossil naphtha for ethylene or the gasification of coal for syngas. This analysis will work to assess and understand the viability of each of the supply chain routes presented in Figure 11, summarizing key advantages and disadvantages of each supply chain route and hotspotting key factors which refrain these supply chains from commercial adoption. The screen will also look to comment on how these defossilized supply chains will perform on a commercial scale, commenting on potential areas of concern with respect to supply chain distribution challenges, as well as how these challenges compare to those faced by current, fossil-based supply chains.
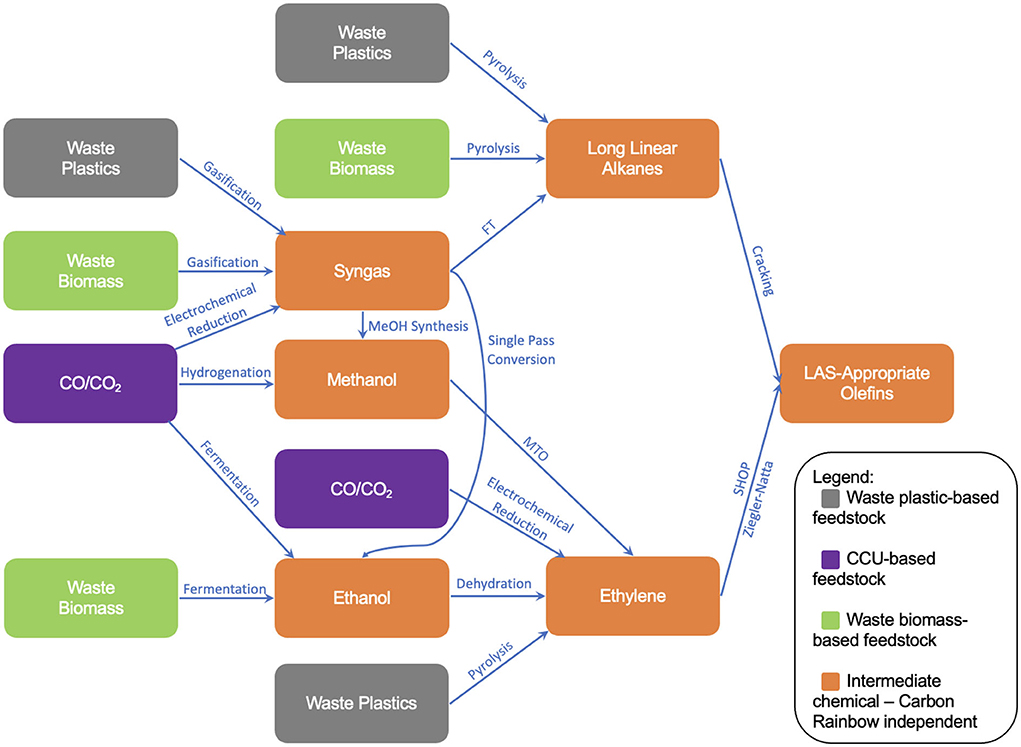
Figure 11. Finalized formulation tree diagram showing the new routes to LAS-appropriate olefins within the scope of this study.
Conclusion
As shown in this review, the potential for the defossilization of LAS-appropriate olefin supply chain is vast, with a wide variety of technologies utilizing different platform chemicals available. Due to the varying TRLs of the technologies presented, many routes fall short of the data needed for accurate sustainability assessments, such as life cycle or techno-economic analyses. As a result, whilst data is still scarce, companies must look to different ways of assessing sustainability and whether the adoption of specific processes will work toward the achievement of ambitious sustainability goals. This review, along with the tree diagram presented in Figure 11, will provide a series of potential formulation routes to be assessed by a novel risk-based sustainability screening assessment method. This will both work as to provide answers as to which route is the optimum in terms of sustainability, as well as provide a validity check of the new screening method.
Author contributions
EP is primary author. PS is research supervisor and edited the manuscript. Both authors contributed to the article and approved the submitted version.
Funding
This project has received funding from Unilever under a strategic partnership with PS at the University of Sheffield and in the form of a Ph.D. Studentship to EP. The work was also partly funded by the Engineering and Physical Sciences Research Council (EP/V011863/1) as part of the UKRI interdisciplinary Centre for Circular Chemical Economy.
Acknowledgments
The authors would like to acknowledge Dr. Katy Armstrong, Dr. Alastair Sanderson, and Dr. Chris Gibbs of Unilever PLC who have engaged in discussions inspiring this work.
Conflict of interest
The authors declare that the research was conducted in the absence of any commercial or financial relationships that could be construed as a potential conflict of interest.
Publisher's note
All claims expressed in this article are solely those of the authors and do not necessarily represent those of their affiliated organizations, or those of the publisher, the editors and the reviewers. Any product that may be evaluated in this article, or claim that may be made by its manufacturer, is not guaranteed or endorsed by the publisher.
References
Ai, L., Ng, S., and Ong, W. (2022). A prospective life cycle assessment of electrochemical CO2 reduction to selective formic acid and ethylene. Early View 20, 2200857. doi: 10.1002/cssc.202201700
Akah, A., Williams, J., and Ghrami, M. (2019). An overview of light olefins production via steam enhanced catalytic cracking. Catal. Surv. Asia 23, 265–276. doi: 10.1007/s10563-019-09280-6
Angili, T. S., Grzesik, K., and Kaltschmitt, M. (2021). Life cycle assessment of bioethanol production: a review of feedstock, technology and methodology. Energies 14, 2939–2957. doi: 10.3390/en14102939
Berkelaar, L., Linde, J., van der, Peper, J., Rajhans, A., Tiemessen, D., Ham, L., van der Berg, H., and van den (2022). Electrochemical conversion of carbon dioxide to ethylene: plant design, evaluation and prospects for the future. Chem. Eng. Res. Design 182, 194–206. doi: 10.1016/j.cherd.2022.03.034
Bisztyga-Szklarz, M., Mech, K., Marzec, M., Kalendarev, R., and Szaciłowski, K. (2021). In situ regeneration of copper-coated gas diffusion electrodes for electroreduction of CO2 to ethylene. Materials 14, 3171–3184. doi: 10.3390/ma14123171
Butler, E., Devlin, G., and McDonnell, K. (2011). Waste polyolefins to liquid fuels via pyrolysis: review of commercial state-of-the-art and recent laboratory research. Waste Biomass Valorization 2, 227–255. doi: 10.1007/s12649-011-9067-5
Chen, C., Khosrowabadi Kotyk, J. F., and Sheehan, S. W. (2018). Progress toward commercial application of electrochemical carbon dioxide reduction. Chem 4, 2571–2586. doi: 10.1016/j.chempr.2018.08.019
Demirba,ş, A. (2003). Hydrocarbons from pyrolysis and hydrolysis processes of biomass. Energy Sources 25, = 67–75. doi: 10.1080/00908310290142127
Dieterich, V., Buttler, A., Hanel, A., Spliethoff, H., and Fendt, S. (2020). Power-to-liquid via synthesis of methanol, DME or Fischer-Tropsch-fuels: a review. Energy Environ. Sci. 13, 3207–3253. doi: 10.1039/D0EE01187H
Fan, D., Dai, D. J., and Wu, H. S. (2013). Ethylene formation by catalytic dehydration of ethanol with industrial considerations. Materials 6, 101–115. doi: 10.3390/ma6010101
Flowserve Corporation (2019). Coal to Olefins (CTO) / Methanol to Olefins (MTO) API Production. Available online at: www.flowserve.com/en/searchresults/?term=coal%2520to%2520olefins (accessed October 31, 2022).
Fogliatti, D. P., Kemppainen, S. A., Kalnes, T. N., Fan, J., and Shonnard, D. R. (2014). Life cycle carbon footprint of linear alkylbenzenesulfonate from coconut oil, palm kernel oil, and petroleum-based paraffins. ACS Sustain. Chemistr. Eng. 2, 1828–1834. doi: 10.1021/sc5001622
Forestière, A., Olivier-Bourbigou, H., and Saussine, L. (2009). Oligomérisation des mono-oléfines par des catalyseurs homogènes. Oil Gas Sci. Technol. 64, 649–667. doi: 10.2516/ogst/2009027
Franke, M., Berna, J. L., Cavalli, L., Renta, C., Stalmans, M., and Thomas, H. (1995). Life-cycle inventory for the production of petrochemical intermediates in Europe. Tenside Surfac. Deterg. 32, 384–396. doi: 10.1515/tsd-1995-320505
Garcia-Garcia, G., Fernandez, M. C., Armstrong, K., Woolass, S., Styring, P., and Reviews, C. (2021). Analytical review of life-cycle environmental impacts of carbon capture and utilization technologies. ChemSusChem 14, 995–1015. doi: 10.1002/cssc.202002126
Garza, A. J., Bell, A. T., and Head-Gordon, M. (2018). Mechanism of CO2 reduction at copper surfaces: pathways to C2 products. ACS Cataly. 8, 1490–1499. doi: 10.1021/acscatal.7b03477
Gholami, Z., Gholami, F., Tišler, Z., Tomas, M., and Vakili, M. (2021). A review on production of light olefins via fluid catalytic cracking. Energies 14, 1–36. doi: 10.3390/en14041089
Giuliano, A., Freda, C., and Catizzone, E. (2020). Techno-economic assessment of bio-syngas production for methanol synthesis: a focus on the water–gas shift and carbon capture sections. Bioengineering 7, 1–18. doi: 10.3390/bioengineering7030070
Gogate, M. R. (2019). Methanol-to-olefins process technology: current status and future prospects. Petrol. Sci. Technol. 37, 559–565. doi: 10.1080/10916466.2018.1555589
Griesbaum, K., Behr, A., Biedenkapp, D., Voges, H.-W., Garbe, D., Paetz, C., et al. (2010). Hydrocarbons. in Ullman's Encyclopedia of Industrial Chemistry, 133–189.
Griffin, D. W., and Schultz, M. A. (2012). Fuel and chemical products from biomass syngas: a comparison of gas fermentation to thermochemical conversion routes. Environ. Progr. Sustain. Energy 31, 219–224. doi: 10.1002/ep.11613
Handler, R. M., Shonnard, D. R., Griffing, E. M., Lai, A., and Palou-Rivera, I. (2015). Life cycle assessments of ethanol production via gas fermentation: anticipated greenhouse gas emissions for cellulosic and waste gas feedstocks. Industr. Eng. Chemistr. Res. 55, 3253–3261. doi: 10.1021/acs.iecr.5b03215
Hernández, S., Farkhondehfal, M. A., Sastre, F., Makkee, M., Saracco, G., and Russo, N. (2017). Syngas production from electrochemical reduction of CO2: current status and prospective implementation. Green Chemistr. 19, 2326–2346. doi: 10.1039/C7GC00398F
Humbird, D., Davis, R., Tao, L., Kinchin, C., Hsu, D., Aden, D., et al. (2011). Process Design and Economics for Biochemical Conversion of Lignocellulosic Biomass to Ethanol. Pharmaceutical Extrusion Technology.
ICIS (2022). ICIS Petrochemicals Flowchart. Available online at: https://www.icis.com/explore/resources/icis-petrochemicals-flowchart/. (accessed October 31, 2022).
International Renewable Energy Agency (2021). Innovation Outlook: Renewable Methanol. Available online: https://www.irena.org/publications/2021/Jan/Innovation-Outlook-Renewable-Methanol (accessed October 31, 2022).
Iribarren, D., Susmozas, A., and Dufour, J. (2013). Life-cycle assessment of Fischer-Tropsch products from biosyngas. Renew. Energy 59, 229–236. doi: 10.1016/j.renene.2013.04.002
Japan Initiative for Marine Environment. (2019). Evaluation of Environmental Load Reduction Effect of Plastic Containers and Packaging Recycling Methods and Energy Recovery (LCA). Available online: https://www.nikkakyo.org/sites/default/files/JaIME_LCA.pdf.
Jeswani, H., Krüger, C., Russ, M., Horlacher, M., Antony, F., Hann, S., et al. (2021). Life cycle environmental impacts of chemical recycling via pyrolysis of mixed plastic waste in comparison with mechanical recycling and energy recovery. Sci. Total Environ. 769, 144483–144501. doi: 10.1016/j.scitotenv.2020.144483
Jiao, F., Li, J., Pan, X., Xiao, J., Li, H., Ma, H., et al. (2016). Selective conversion of syngas to light olefins. Science 351, 1065–1068. doi: 10.1126/science.aaf1835
Joosten, L. (1998). Process Data Descriptions for the production of synthetic organic chemicals—Input data for the MATTER study. Available online at: https://dspace.library.uu.nl/bitstream/handle/1874/8599/98028.pdf?isAllowed=yandsequence=1 (accessed October 31, 2022).
Jungbluth, N., and Chudacoff, M. (2007). Life cycle inventories of bioenergy. Data v2.0. Swiss Centre for Life Cycle Inventories. Available online at: https://www.researchgate.net/publication/313056035_Life_Cycle_Inventories_of_Bioenergy_Data_v20_2007 (accessed October 31, 2022).
Kang, J., He, S., Zhou, W., Shen, Z., Li, Y., Chen, M., et al. (2020). Single-pass transformation of syngas into ethanol with high selectivity by triple tandem catalysis. Nat. Commun. 11, 1–11. doi: 10.1038/s41467-020-14672-8
Kas, R., Kortlever, R., Yilmaz, H., Koper, M. T. M., and Mul, G. (2015). Manipulating the hydrocarbon selectivity of copper nanoparticles in CO2 electroreduction by process conditions. ChemElectroChem. 2, 354–358. doi: 10.1002/celc.201402373
Keil, F. J. (1999). Methanol-to-hydrocarbons: process technology. Microporous Mesopor. Mater. 29, 49–66. doi: 10.1016/S1387-1811(98)00320-5
Keim, W. (2013). Oligomerization of ethylene to α-olefins: discovery and development of the shell higher olefin process (SHOP). Angewandte Chemie – Int. Edit. 52, 12492–12496. doi: 10.1002/anie.201305308
Khoo, H. H., Halim, I., and Handoko, A. D. (2020). LCA of electrochemical reduction of CO2to ethylene. J. CO2 Utilizat. 41, 101229–101238. doi: 10.1016/j.jcou.2020.101229
Kibria Nabil, S., McCoy, S., and Kibria, M. G. (2021). Comparative life cycle assessment of electrochemical upgrading of CO2 to fuels and feedstocks. Green Chemistr. 23, 867–880. doi: 10.1039/D0GC02831B
Kim, C., Bui, J. C., Luo, X., Cooper, J. K., Kusoglu, A., Weber, A. Z., et al. (2022). Publisher Correction: Tailored catalyst microenvironments for CO2 electroreduction to multicarbon products on copper using bilayer ionomer coatings. Nature Energy 6, 11. doi: 10.1038/s41560-021-00920-8
Kocal, J. A., Vora, B., and v. Imai, T. (2001). Production of linear alkylbenzenes. Appl. Cataly. A: General 221, 295–301. doi: 10.1016/S0926-860X(01)00808-0
Krzywda, R., and Wrzesińska, B. (2021). Simulation of the condensation and fractionation unit in waste plastics pyrolysis plant. Waste Biomass Valorizat. 12, 91–104. doi: 10.1007/s12649-020-00994-7
Kumar, R. N., and Aarthi, V. (2020). From biomass to syngas, fuels and chemicals-A review. AIP Conference Proceed. 5, 2225. doi: 10.1063/5.0005864
LanzaTech (2022a). 2021 Annual Report. Available online at: https://lanzatech.com/download/2021-annual-report/. (accessed October 31, 2022).
LanzaTech (2022b). About – LanzaTech. Available online at: ?https://lanzatech.com/about/. (accessed October 31, 2022).
Leal, M. R. L. V., Valle, T. L., Feltan, J. C., and Carvalho, C. R. L. (2014). Other raw materials for producing ethanol. Sugarcane bioethanol — RandD for Productiv. Sustain. 14, 519–540. doi: 10.5151/BlucherOA-Sugarcane-SUGARCANEBIOETHANOL_47
Liew, F. M., Martin, M. E., Tappel, R. C., Heijstra, B. D., Mihalcea, C., and Köpke, M. (2016). Gas Fermentation-A flexible platform for commercial scale production of low-carbon-fuels and chemicals from waste and renewable feedstocks. Front. Microbiol. 7, 694–724. doi: 10.3389/fmicb.2016.00694
Mejía-Barajas, J. A., Alvarez-Navarrete, M., Saavedra-Molina, A., Campos-García, J., Valenzuela-Vázquez, U., Amaya-Delgado, L., et al. (2018). Second-generation bioethanol production through a simultaneous saccharification-fermentation process using kluyveromyces marxianus thermotolerant yeast. Special Topics Renew. Energy Syst. 18, 78052. doi: 10.5772/intechopen.78052
Meyers, R. A. (2016). Handbook of Petroleum Refining Processes. 4th edn. London: McGraw Hill Education.
Miranda, J. C., de C Ponce, G. H. S. F., Arellano-Garcia, H., Maciel Filho, R., and Wolf Maciel, M. R. (2020). Process design and evaluation of syngas-to-ethanol conversion plants. J. Clean. Product. 269, 122078–122102. doi: 10.1016/j.jclepro.2020.122078
Mohsenzadeh, A., Zamani, A., and Taherzadeh, M. J. (2017). Bioethylene production from ethanol: a review and techno-economical evaluation. ChemBioEng. Rev. 4, 75–91. doi: 10.1002/cben.201600025
Navas-Anguita, Z., Cruz, P. L., Martín-Gamboa, M., Iribarren, D., and Dufour, J. (2019). Simulation and life cycle assessment of synthetic fuels produced via biogas dry reforming and Fischer-Tropsch synthesis. Fuel 235, 1492–1500. doi: 10.1016/j.fuel.2018.08.147
Okeke, I. J., Sahoo, K., Kaliyan, N., and Mani, S. (2020). Life cycle assessment of renewable diesel production via anaerobic digestion and Fischer-Tropsch synthesis from miscanthus grown in strip-mined soils. J. Clean. Product. 249, 119358–119369. doi: 10.1016/j.jclepro.2019.119358
Olah, G. A. (2005). Beyond oil and gas: the methanol economy. Angewandte Chemie – Int. Edit. 44, 2636–2639. doi: 10.1002/anie.200462121
Ragaert, K., Delva, L., and Van Geem, K. (2017). Mechanical and chemical recycling of solid plastic waste. Waste Manag. 69, 24–58.
Ren, T., Patel, M. K., and Blok, K. (2008). Steam cracking and methane to olefins: Energy use, CO2 emissions and production costs. Energy 33, 817–833. doi: 10.1016/j.energy.2008.01.002
Robak, K., and Balcerek, M. (2018). Review of second generation bioethanol production from residual biomass. Food Technol. Biotechnol. 56, 174–187. doi: 10.17113/ftb.56.02.18.5428
Rosli, M. N., and Aziz, N. (2016). Simulation of ethane steam cracking with severity evaluation. IOP Conferen. Series Mater. Sci. Eng. 162, 012017. doi: 10.1088/1757-899X/162/1/012017
Saebea, D., Ruengrit, P., Arpornwichanop, A., and Patcharavorachot, Y. (2020). Gasification of plastic waste for synthesis gas production. Energy Rep. 6, 202–207. doi: 10.1016/j.egyr.2019.08.043
Schreiber, A., Peschel, A., Hentschel, B., and Zapp, P. (2020). Life cycle assessment of power-to-syngas: comparing high temperature co-electrolysis and steam methane reforming. Front. Energy Res. 8, 1–17. doi: 10.3389/fenrg.2020.533850
Schulz, H. (1999). Short history and present trends of Fischer-Tropsch synthesis. Appl. Cataly. A: General 186, 3–12. doi: 10.1016/S0926-860X(99)00160-X
Shamiri, A., Chakrabarti, M. H., Jahan, S., Hussain, M. A., Kaminsky, W., Aravind, P., et al. (2014). The influence of Ziegler-Natta and metallocene catalysts on polyolefin structure, properties, and processing ability. Materials 7, 5069–5108. doi: 10.3390/ma7075069
Shamiri, A., Hussain, M. A., Mjalli, F. S., Mostoufi, N., and Hajimolana, S. (2013). Dynamics and predictive control of gas phase propylene polymerization in fluidized bed reactors. Chinese J. Chem. Eng. 21, 1015–1029. doi: 10.1016/S1004-9541(13)60565-0
Steele, P., Puettmann, M. E., Penmetsa, V. K., and Cooper, J. E. (2012). Life-cycle assessment of pyrolysis bio-oil production. Forest Product. J. 62, 326–334. doi: 10.13073/FPJ-D-12-00016.1
Taveira, I. C., Nogueira, K. M. V., Oliveira, D. L. G., de Silva, R., and do, N (2021). Fermentation: Humanity's Oldest Biotechnological Tool. Front. Young Minds 9, 56. doi: 10.3389/frym.2021.568656
Unilever (2020). Unilever to eliminate fossil fuels in cleaning products by 2030 | News | Unilever global company website (accessed May 16, 2021).
Vienescu, D. N., Wang, J., le Gresley, A., and Nixon, J. D. (2017). A life cycle assessment of options for producing synthetic fuel via pyrolysis. Bioresour. Technol. 249, 626–634. doi: 10.1016/j.biortech.2017.10.069
Wang, L., Littlewood, J., and Murphy, R. J. (2013). Environmental sustainability of bioethanol production from wheat straw in the UK. Renew. Sustain. Energy Rev. 28, 715–725. doi: 10.1016/j.rser.2013.08.031
Wernet, G., Bauer, C., Steubing, B., Reinhard, J., Moreno-Ruiz, E., and Weidema, B. (2016). The ecoinvent database version 3 (part I): overview and methodology. Int. J. Life Cycle Assess. 21, 1218–1230. doi: 10.1007/s11367-016-1087-8
Yadav, G. D., and Doshi, N. S. (2002). Synthesis of linear phenyldodecanes by the alkylation of benzene with 1-dodecene over non-zeolitic catalysts. Organic Process Res. Develop. 6, 263–272. doi: 10.1021/op000044s
Yang, M., Tian, X., and You, F. (2018). Manufacturing ethylene from wet shale gas and biomass: comparative technoeconomic analysis and environmental life cycle assessment. Industr. Eng. Chemistr. Res. 57, 5980–5998. doi: 10.1021/acs.iecr.7b03731
Keywords: olefins, defossilization, screening, review, inventory, CCU, biomass, plastics
Citation: Platt EG and Styring P (2022) New olefin production routes—A review of defossilised supply chain technologies with regards to surfactant production. Front. Sustain. 3:1057491. doi: 10.3389/frsus.2022.1057491
Received: 29 September 2022; Accepted: 26 October 2022;
Published: 16 November 2022.
Edited by:
Bing Shen How, Swinburne University of Technology Sarawak Campus, MalaysiaReviewed by:
Chun Hsion Lim, Heriot-Watt University Malaysia, MalaysiaKin Wai Cheah, Teesside University, United Kingdom
Copyright © 2022 Platt and Styring. This is an open-access article distributed under the terms of the Creative Commons Attribution License (CC BY). The use, distribution or reproduction in other forums is permitted, provided the original author(s) and the copyright owner(s) are credited and that the original publication in this journal is cited, in accordance with accepted academic practice. No use, distribution or reproduction is permitted which does not comply with these terms.
*Correspondence: Peter Styring, cC5zdHlyaW5nQHNoZWZmaWVsZC5hYy51aw==