- Department of Chemical and Biological Engineering, Monash University, Clayton, VIC, Australia
The automotive shredder residue (ASR) is generated as an inevitable waste after the shredding process of end-of-life vehicles. Typically, the ASR ends up in a landfill in the absence of any existing processing options. The ASR comprises rubber, wood, plastics, textile, metals, and other materials, such as paint and glass (10%), which can be recycled and reused. Given these attributes, the ASR is a potential feedstock for energy production and metal recovery. In this study, ASR was first pretreated because untreated ASR (as received) is fluffy and heterogeneous and, therefore, is difficult to feed into a reactor. Subsequently, the pyrolysis process was conducted with this pretreated ASR for energy recovery. From the thermochemical calculations, an optimized temperature of 500°C was chosen for pyrolysis of the pretreated ASR to ensure that metals would not be further oxidized and polymers could be separated from the metals in the form of volatile gases, oil, and char. Bench-scale pyrolysis tests were conducted on an integrated continuous stirred tank reactor–distillation column pyrolysis system. The product gas composition had hydrogen and methane content of 30% and 26% (v/v), respectively, contributing to the heating value of the gas obtained. The pyrolysis oil was further distilled using fractional distillation apparatus for gasoline and diesel-grade products. The physicochemical characterization of the pretreated ASR pyrolysis oil and its distillates was also carried out. The thermochemical equilibrium predictions showed a similar trend with the experimental pyrolysis results. In addition, the residual char analysis indicated the presence of a significant amount of metals—silicon, titanium, aluminum, and iron. Thus, this work generated information on processing pretreated ASR for the production of fuel and insights on metal recovery that can be recovered from the residual pyrolysis char.
Introduction
A steady increase in end-of-life vehicles (ELVs) is the key driver for generating automotive shredder residue (ASR) waste. Given an average weight of 1,500 kg per vehicle, globally, about 1 million tons of waste is produced before recycling. With a growing population, ELV ASR waste has become a global environmental concern due to its complex composition and inability to degrade (Sakai et al., 2014) in an environmental manner. In an ELV, 75% constitutes ferrous metals and recyclable materials (Cossu and Lai, 2015), and the remaining 25% is ASR. The ASR generated after processing an ELV is also known as “auto fluff” (Mayyas et al., 2017). The ASR is typically comprised of rubber (20%), wood (2–5%), plastics (19–35%), textile (10–40%), metals (8%), and other materials, such as paint and glass (10%), which can be recycled and reused. As stated earlier, the composition of the ASR is heterogeneous, and the physical characteristics are fluffy in nature, making its mechanical recycling difficult. Hence, the ASR is destined for landfills or incineration.
There are two impediments to the recycling of ASR: one is the heterogeneity of the ASR as received, and the other is the fluffiness of the ASR. These impediments, in turn, affect the selection of the thermochemical process for the recycling of ASR, particular the difficulty in feeding the fluffy and very heterogeneous materials into a reactor. Hence, in our previous work (Vijayan et al., 2021), we reported a low-temperature procedure to “homogenize” the sample to a feedable particulate form by pretreatment and named it pretreated ASR. This pretreated ASR consists of both plastics and metals and, when ground and sieved, converts to a desired uniform size range. Hitherto, most of the authors from the literature have shown pyrolysis as a suitable treatment for ASR in the recovery of energy and materials.
Most authors found that the pyrolysis products, such as the produced gas and pyrolysis oil, had a high energy content (Buekens and Zhou, 2014; Cossu and Lai, 2015; Notarnicola et al., 2017), and the left-out residue is char with less energy content. The yield of the pyrolysis products depends upon the composition of the ASR and the operating parameters in the pyrolysis. In literature, the pyrolysis oil research work is limited with characterization; those results show that pyrolysis oil can be a good source for secondary fuel, such as petrol and diesel fractions, and the gaseous products can be utilized as an energy/heat source. In various small-scale studies, pyrolysis has converted ASR fractions into gases and char using different reactors and a range of temperatures with and without catalysts (Vermeulen et al., 2011; Anzano et al., 2017; Maric et al., 2018). The reactors used in ASR's pyrolysis are batch/semi-batch tubular furnace and rotary kiln reactors. All the reactors are heated using an electrical furnace, and nitrogen or argon gas is used as inert gas for the process with varying mass flow.
Besides the energy recovery, these studies have ignored the high-to-moderate metallic content of the ASR carbonaceous residues, which can cause disposal problems (Mayyas et al., 2017). The residual carbonaceous residues can be further explored for metal recovery. The studies on the separation and recovery of metals from ASR are limited (Ferella et al., 2015). Most studies focused on ASR material recycling on its use as a filler in concrete, ceramic binders in asphalts, and secondary raw material (Mayyas et al., 2017). However, the metals represent about 12 wt% of the initial weight of the ASR (Mallampati et al., 2015), thus, making the recovery of these metals worthwhile. Therefore, it is essential to determine effective routes for the recovery of these metals.
The first two objectives of this theoretical and experimental study are to prepare pretreated ASR and then investigate the effect of temperature during pyrolysis through thermochemical calculations using the FactSage software within the temperature range between 300 and 1,000°C. Based on the thermochemical calculations, the pretreated ASR pyrolysis experiments are then carried out in a bench-scale reactor with an optimized range for low-temperature pyrolysis. Subsequently, the products obtained from the process are characterized for energy recovery and metal concentration. In addition, the pyrolysis oil was further distilled into different hydrocarbon fractions and assessed for its fuel composition.
Materials and Methods
Pretreated Automotive Shredder Residue
The ASR was heterogeneous and fluffy when received from a commercial supplier in Victoria, Australia. The ASR (as received) consists of mainly plastics, metals, glasses, and a few textile components. Generally, as noted from the literature, the ASR consists of plastics, metals, rubber, fiber, textiles, and glasses (Notarnicola et al., 2017). This variation in the composition of the ASR depends on the input to the shredding unit. For easier feeding into the pyrolysis reactor, a homogeneous mixture with particulate character and uniform particle size distribution was prepared by pretreatment, as described by Vijayan et al. (2021). In the pretreatment of ASR, the sample was heated at 190°C in a furnace, then ground and sieved to 90–106 μm to bring particulate nature and uniform size.
Sample Analysis
The proximate analysis of the pretreated ASR sample is determined in a thermogravimetric analyzer (TGA), model STA 449F3, NETZSCH, Germany, according to the AS2434 standards. Approximately 10 ± 1 mg of pretreated ASR sample was taken to be analyzed by the TGA to obtain a simultaneous mass loss and differential mass profile with respect to time and temperature. The conditions were carried out initially in a nitrogen environment, with a heating rate of 10°C/min up to 105°C, isothermal at 105°C for 20 min, then heating up to 900°C at 10°C/min, and isothermal at 900°C for 7 min, and finally cooling to 550°C at 50°C/min in a nitrogen environment and isothermal in the air at 550°C for 40 min. A blank correction was also performed with the same process conditions to be subtracted from the measurement data. The runs were carried out in triplicate, and the average values were represented.
The major inorganics in the pretreated ASR were analyzed using x-ray fluorescence spectroscopy (XRF-EDX-720, Shimadzu Corp, Japan). This technique offers a qualitative multielement detection range from 6C/11Na to 92U with a voltage of 15–50 kV in the air atmosphere. In addition, runs were carried out in triplicate after the sample of pretreated ASR was made into ash in a muffle furnace at 900°C for 6 h.
X-ray diffractograms were acquired in the Rigaku Mini Flex 600 operating in Bragg–Brentano geometry and with unfiltered Cu Kα radiation at a scanning rate of 1.3°min−1 over a range of 2θ = 10°-80° to identify crystalline mineral matter in pretreated ASR and pyrolysis char. The phase identification was analyzed using the MATCH software version 3. Before analysis, the solid products were burnt to ash at a temperature of 600°C for 2 h in a muffle furnace to remove carbon without devolatilization of the minerals. Replicates were performed when required.
Carbon number distribution in the pyrolysis oil, heavy oil, and distillates was determined using the Shimadzu GC 2010 flame ionization detector fitted with a 30-m length × 0.25-mm ID × 0.25-μm column. The GC and FID temperatures were 300°C, and the oven was held at 35°C for 5 min and then ramped to 300°C at 3°C/min in the presence of carrier gas helium with a split ratio of 50 and column flow rate of 2.5 ml/min.
The collected noncondensable gas was analyzed in gas chromatography–flame ionization detector (Model: Agilent Technologies 7890 A GC system, USA). A certain volume of the gas was injected into the GC system. The total run was about 32 min with a column temperature at 140°C with helium as carrier gas. The GC instrument was calibrated based on a three-point calibration curve before analyzing the gas samples. The data were estimated by automated integration of the area under the resolved chromatographic profile. The composition data were collected, averaged, and presented in terms of gas concentration (N2-free basis). The thermal decomposition of the ASR pyrolysis oil was analyzed through TGA. Approximately 12 ± 1 mg of ASR pyrolysis sample was taken for analysis. The conditions were carried out in a nitrogen environment (50 ml/min), 30 to 600°C at 10°C/min. A blank correction was also performed at the same process condition subtracting from the measurement data.
Ultimate analysis (CHNS) of the pretreated ASR, pyrolysis oil, heavy oil, and distillates were performed using FLASH 2000 CHNS analyzer (Thermo Scientific) operating based on dynamic flash combustion of the sample. The reactor temperature was 950°C with helium as the carrier gas at 140 ml/min, and oxygen is injected at a 250-ml/min flow rate for 5 s. Finally, a thermal conductivity detector (TCD) was detected with a total run time of 10 min. The oxygen content was determined by subtracting the total content of other analyzed elements from 100%. Each run was repeated in duplicate.
The higher heating value was calculated based on the elemental composition according to empirical Boie's formula (Equation 1) as given below:
The FactSage (version 7.3), a thermochemical software, predicted the possible equilibrium products under given pyrolysis conditions. The elemental inputs for the calculations were from the XRF and the ultimate analysis of the pretreated ASR. The process condition was in temperatures ranging from 300 to 1,000°C under 1 atm absolute pressure and nitrogen as an inert gas with a 20-ml/min flow rate. The “Equilib” module in FactSage software was used to predict the possible products under thermodynamic equilibrium.
Experimental Procedure for Pretreated Automotive Shredder Residue Pyrolysis
The pyrolysis tests were conducted using an integrated continuous stirred tank reactor– distillation column (CSTR-DC) pyrolysis system; a schematic diagram is shown in Figure 1. The pyrolysis reactor was customized at the Monash University, Clayton, Victoria, Australia, for various purposes, where it can be used in continuous or batch mode operation. The CSTR-DC pyrolysis reactor has been operated as a batch reactor for pyrolysis of pretreated ASR. The detailed reactor description and the capabilities are covered by Auxilio et al. (2017). The temperature is monitored by the thermocouples T1, T2, and T3 controlled by digital controllers when the CSTR with the agitator stirring up to 125 rpm is heated in an electric furnace to 500°C. The vapors from the CSTR during the pyrolysis process pass through the distillation column (DC), having two separate heating zones. The lower heating zone is maintained at 350°C, and the 295°C at the upper zone, ensuring the boiling points of hydrocarbon are above 295°C, which are monitored by thermocouples T4 and T5, respectively. The solid borosilicate beads (1 mm in diameter) were loaded at the bottom of the DC. The condensable vapors, passing through the condenser maintained at −20°C, called the pyrolysis oil, were collected in a conical flask and weighed. The noncondensable gas, vented from the second condenser (0°C), is collected in Tedlar sampling bags and then analyzed in a gas chromatography analyzer.
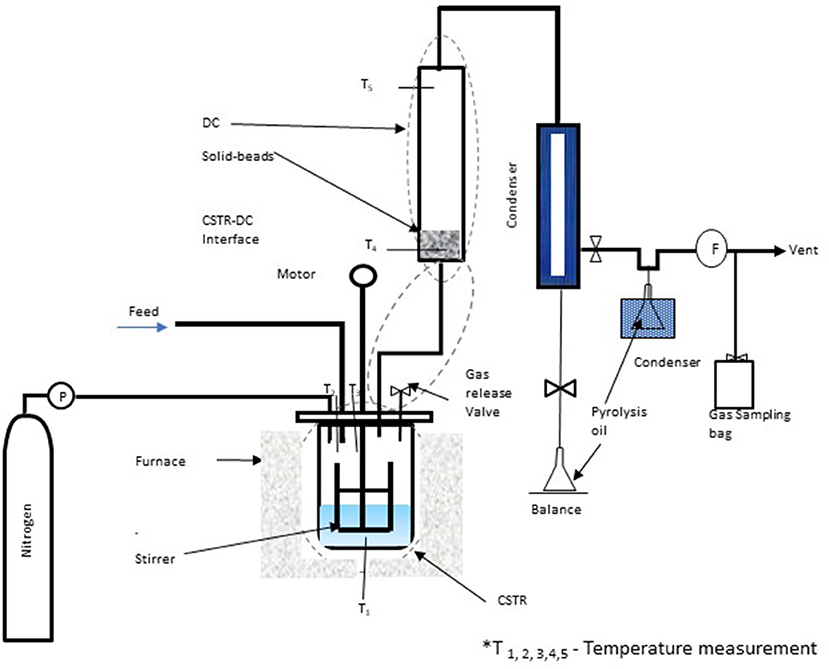
Figure 1. Schematic diagram of CSTR- DC pyrolysis reactor for pretreated ASR (Auxilio et al., 2017).
Approximately 2 kg of pretreated ASR was preloaded into the reactor for the pyrolysis run. The temperature for the pyrolysis reactor was gradually increased from ambient temperature to 500°C at a heating of 1.5°C/min. The pyrolysis system was purged with nitrogen during the heating to expel air. The nitrogen purge was stopped when the agitator was started, which gradually increased and remained constant after reaching 125 rpm. The total processing time for the pyrolysis run was 5 h after reaching steady state. The evolution of the vapors from the pyrolysis system was noticed when the temperature reached 280°C. When the desired pyrolysis temperature is attained, i.e., 300–500°C, the pyrolysis product, such as the pyrolysis oil, was collected from the outlet of condenser 1. In addition, the noncondensable gas was collected in a gas bag from the outlet of the second condenser. After the run, the CSTR is dismantled, cleaned, and the pyrolysis solid residue in the CSTR is collected and weighed.
Experimental Procedure for Distillation of Automotive Shredder Residue Pyrolysis Oil
The pyrolysis oil from the pretreated ASR pyrolysis process was collected at two temperature ranges: the first set was 280–350°C, and the second set of pyrolysis oil was collected in the temperature range of 350–500°C. As shown in Figure 2, The pyrolysis oil was heated in the heating mantle. The temperature chosen for the fractionating column was 220, 250, and 280°C based on the crude oil distillation temperature range. The emitted vapors were then condensed and collected in a flask.
Results and Discussion
In this section, properties of pretreated ASR are characterized, followed by thermochemical calculations based on FactSage software to identify possible equilibrium products during the pyrolysis of pretreated ASR in the given temperature range and pressure. Subsequently, the pretreated ASR pyrolysis process was carried out with the obtained temperature boundaries in the bench-scale reactor. The products from the pyrolysis process are characterized for their physical and chemical properties and compared with the predicted products from the thermochemical calculations. The obtained pyrolysis oil was distilled into different fractions and characterized for potential use as fuel. Finally, a Sankey diagram for the mass balance of the pretreated ASR pyrolysis process was drawn.
Sample Characterization of Pretreated Automotive Shredder Residue
The properties of the pretreated ASR, such as the proximate, ultimate analysis, have been carried out in triplicate, and the average values are listed in Table 1. The high volatile content is due to plastics in the pretreated ASR. The fixed carbon of the pretreated ASR was low or negligible, which was not observed in previous literature. The plausible reason for this unusual behavior is variation in the ASR composition (as received). The low fixed carbon of the pretreated ASR suggests that the pyrolysis process is more appropriate than any other method in thermochemical conversion for energy recovery. Hence, the pyrolysis behavior of the pretreated ASR was analyzed through TGA. The degradation step having the onset, end set, and maximum temperatures of pretreated ASR were at 216, 450, and 373°C, respectively, as seen from Figure 3. Based on these results, the initial temperature boundaries for thermochemical calculations were chosen and further discussed in the next section.
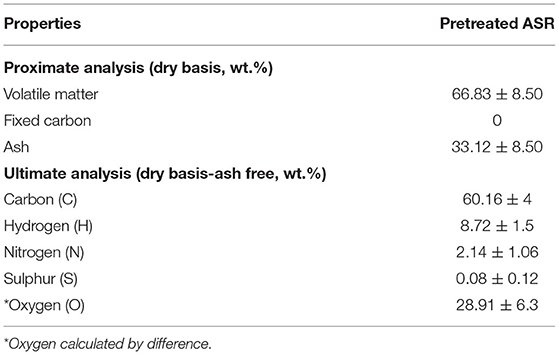
Table 1. Proximate and ultimate analysis of pretreated ASR (Vijayan et al., 2021).
Thermochemical Calculations
This section discusses the results of the thermochemical calculations of the pyrolysis of pretreated ASR samples under given pyrolysis conditions. The elemental input for the FactSage software to predict the possible products are tabulated in Table 2. In addition, the effect of temperature has been investigated on the distribution of the predicted product discussed in detail in this section.
Mass Balance
The mass balance of the predicted solid and gas phase products in the temperature range between 300 and 1,000°C was estimated. Figure 4 exhibits the weight percentage of the solid phase (char-carbon and other solids, such as compounds of silicon, calcium, and sodium) and total gas phase products (condensable and noncondensable gases) predicted at given temperatures. As seen from Figure 4, the carbon content decreased with increased temperature due to higher carbon conversion. The carbon-containing gas-phase products such as CO and CH4 also account for the distribution of the carbon content. It is observed that when carbon content increases in the solid phase products, there is a decrease in the gas phase products. The carbon content increases with an increase in temperature. This is due to the thermal decomposition of CH4 starting at 500°C, which gives rise to hydrogen and solid carbon. Also, the carbon molecules react with oxygen to form CO and CO2, which are the majority of the gases. As observed from Figure 4, these gases are emitted at a lower temperature, and therefore, the gas decreases with an increase in temperature. The predicted product distribution varied with an increase in temperature.
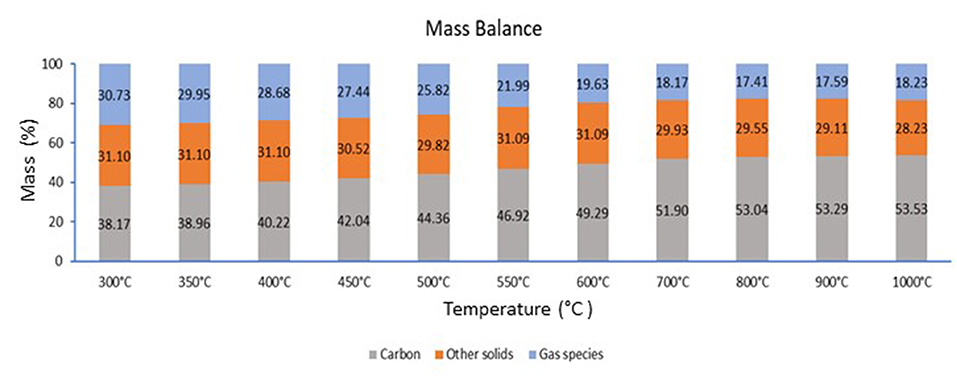
Figure 4. Mass balance of the predicted products obtained from the thermochemical calculation at different pyrolysis temperature.
Predicted Gas Phase
The major gases contributing to the fuel's heating value are plotted on a nitrogen-free basis and normalized in Figure 4. The devolatilization of the pretreated ASR sample may result in gaseous species, such as H2, CO, and CH4 formation. Higher CO is found with increasing temperature due to higher carbon conversion, as seen in Figure 5. The H2 content increases when the temperature increases. There is a steady decline in CH4 formation with an increase in temperature, and beyond 500°C, the formation is very low, whereas the H2 content increases. Thus, from the results of predicted gas-phase products, the ideal temperature range for processing the pretreated ASR in the pyrolysis reactor can be between 400 and 500°C for obtaining a high amount of gas products. A similar study (Evangelopoulos et al., 2018) was found to have a temperature range between 400 and 500°C for pyrolysis of ASR.
Predicted Solid-Phase Compounds
The pretreated ASR is a mixture of both plastics and metals, where the plastics get converted into gas phases, and the metals are collected along with the char when processed in the reactor. As the temperature is an important parameter in the decomposition of plastics into gaseous fuel, it is also essential that metal contents are concentrated without further oxidation during the pyrolysis process. This concentrated metal can be separated from the pyrolysis char at a later stage. The crystalline constituents from the predicted solid-phase species as a function of temperature are tabulated in Table 3. The major predicted solid phase products include albite (high and low), diopside, anorthite, hedenbergite, wollastonite, anorthite, fayalite, tridymite, and quartz. The sodium content is in the form of sodium aluminosilicates, while Al2O3 reaction with SiO2 forms as albite in the solid-phase products and is found between the temperature range of 300°C and 1,000°C. As stated from elemental composition, a large amount of Ca is present in pretreated ASR ash. The predicted solid-phase products have calcium in the form of silicates. As the temperature increases, CaO reacts with the SiO2 and Al2O3 to produce anorthite, as predicted from the solid phase, whereas CaO reacts with SiO2, and MgO forms the diopside and is stable from 400 to 1,000°C as the melting point of the diopside is 1,391°C. The reaction of CaO with SiO2 leads to the formation of wollastonite between 700 and 1,000°C. The presence of potassium in a high melting (1,686°C) aluminosilicate–leucite is formed in the predicted solid phase as the reaction between Al2O3 and SiO3. A reduction reaction of Fe2O3 in the presence of reducing gases, such as H2 and CH4, forms cementite. From the elemental composition of pretreated ASR ash, the SiO2 (quartz) phase is predominant and remains the same until 800°C. The transition temperature from quartz to the tridymite phase is at 870°C (Lider and Yurtseven, 2014), and it is observed from Table 3 that tridymite is formed from 900°C. The predicted temperature is close to the temperature in the reactor.
Experimental Work
Based on the theoretical calculations, the temperature boundaries were chosen for pyrolyzing the pretreated ASR in the batch reactor (CSTR-DC). This section discusses product distribution and the characterization of each obtained product's composition in detail. In addition, the pyrolysis oil is distilled into different hydrocarbon fractions to assess its potential use as fuel. One of the main objectives of this work is to concentrate metals, while processing pretreated ASR in the reactor, where the solid residues are collected at the bottom of the reactor. Finally, the solid residues obtained from the pyrolysis process are assessed for possible metal recovery.
Gas Composition
In the pyrolysis process of pretreated ASR in the CSTR-DC, the noncondensable gases were collected at each temperature and analyzed for their composition. The evolution of gaseous products started at 300°C during pyrolysis of pretreated ASR. Figure 6 illustrates the gas composition obtained from 300 to 500°C of the produced gas as a function of temperature, nitrogen-free basis. The devolatilization of the pretreated ASR results in gaseous products, including H2, CH4, CO, CO2, and other light hydrocarbons. The H2, CO, and CH4 concentrations increase as the pyrolysis temperature increases from 400 to 500°C, attributed to the onset of secondary pyrolysis (De Marco et al., 2007; Joung et al., 2007; Sung-Jin et al., 2010). The majority of CO2 concentrations are up to 400°C (44–73% vol%); this may limit the heating value of the gas mixture, whereas at 500°C, the CO2 (3% vol%) concentration is less compared with other temperatures. The heating values of the produced gases with the function of temperature are exhibited in Table 4. The heating value of the gaseous mixture obtained at 500°C is 12.65 MJ/m3. In other studies on ASR pyrolysis, the production of CO2 content is due to the high amount of plastic material in the raw material that is pyrolyzed at low temperatures (Sung-Jin et al., 2010; Adrados et al., 2012; Evangelopoulos et al., 2018). Beyond 400°C, CO2 concentration is reduced, and there are notably high concentration percentages of H2 and CH4 as seen in Figure 6. The increase in H2 with an increase in temperature is due to the aromatization of char that leads to the formation of H2 (Notarnicola et al., 2017). The CO is formed from the thermal decomposition of the carboxylic groups present in the sample. The amount of CO and CO2 is determined by the Boudouard reaction, favored by increasing temperature. This shifts the equilibrium toward CO at a higher temperature, increasing CO with increased temperature. In addition, it also depends upon the oxygen content present. However, the concentration of gaseous products tends to fluctuate over the temperature ranges.
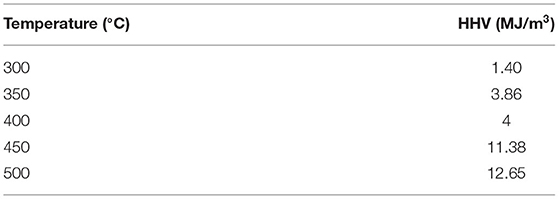
Table 4. The higher heating value of the gas from pretreated ASR pyrolysis process as a function of temperature.
The gas concentration from the pretreated ASR pyrolysis process were well in agreement with the gas phase predicted by the thermochemical calculations based on equilibrium conditions. Therefore, the obtained gas can be used as fuel, a heating source within the process, or as one raw material for producing chemicals.
Solid Residues From Pretreated Automotive Shredder Residue Pyrolysis
The unreacted carbon remains in the char after the plastics present in the pretreated ASR are devolatilized, and the metals are concentrated along with the char. As observed from Table 5, the pretreated ASR's hydrogen content decreased when pyrolysis temperature was applied. This is due to the loss of the carboxylic functional group by devolatilization with an increase in pyrolysis temperature (Martín-Lara et al., 2021). The higher heating value of the ASR pyrolysis solid residue obtained at 500°C was 15.2 MJ/kg, whereas 24.9 MJ/kg was for the pretreated ASR. For any fuel, the HHV is influenced by the hydrogen content. Since the HHV of the pyrolysis solid residue is low, previous researchers did not consider further use of the residue, and thus, it was suggested to be landfilled (Notarnicola et al., 2017). However, in the predicted solid-phase compounds in Table 3, we can observe that the presence of metals is either in elemental form or in oxide form. The melting point of these metals is higher than the chosen pyrolysis temperature of 500°C. Hence, as expected along with the char, the metals remain unaltered in the ASR pyrolysis solid residue. One of the objectives of this work is to assess the recovery of metals from the solid residues following pyrolysis; the results suggest that this is possible. A detailed characterization of metal and mineral transformation in the pyrolysis solid residue from pyrolyzing pretreated ASR is discussed in this section.
SEM-EDX Analysis
The morphology of the pretreated ASR pyrolysis char depicted in the figure shows a fibrous structure. As observed from Figure 7, the char has different particle sizes, resulting in particle fragmentation, agglomeration, or swelling. However, there is no obvious observation of particle swelling or agglomeration in the samples. Morphology shows irregular and rod-shaped particles in the char from the pyrolyzed pretreated ASR. The thermal stress due to the rapid temperature change during the pyrolysis process results in the fragmentation of particles while releasing volatile matter (Li et al., 2014). The EDX analysis elucidates the mineral composition at the indicated locations within the particles. Silicon and calcium are the major metals in the compounds of pyrolysis solid residue. Moreover, traces of sodium, aluminum, and titanium were also detected. These results confirm that the metals are concentrated in the solid residue from the pretreated ASR pyrolysis process. The metals from the pyrolysis solid residue can potentially be leached out as a part of the recovery of metals. The results corresponded with the results obtained with XRD analysis and are discussed in the next section.
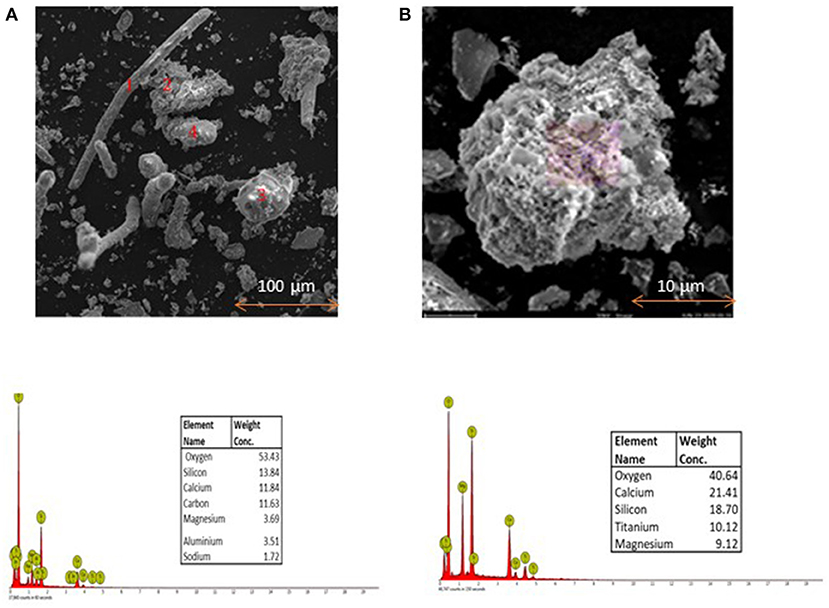
Figure 7. Scanning Electron Micrograph (A). Combined analysis (B). An individual particle of ASR pyrolysis solid residue obtained at 500°C.
Crystalline Constituents in the Automotive Shredder Residue Pyrolysis Solid Residue
The x-ray diffraction pattern of the pretreated ASR pyrolysis solid residue is shown in Figure 8. It was observed that the peaks detected in the XRD pattern of the ASR pyrolysis solid residue obtained at 500°C were consistent with mineral identification from the predicted solid-phase results based on thermodynamic equilibrium. For example, compounds, including quartz, hedenbergite, diopside, albite, and fayalite, were high in concentration from the predicted solid phase (Table 3), and these compounds were also detected in the diffractograms obtained from the pyrolysis solid residue. The diffractograms could not find a few compounds from the predicted solid phase with a low crystalline structure or amorphous nature. It was also found that silica was the dominant phase in the pyrolysis residue. The majority of silica in the crystalline phases of the pretreated ASR pyrolysis residue occurred as quartz. The calcium in the sample is contained in the form of silicates, such as diopside, hedenbergite, and wollastonite. It was also observed that sodium in the sample was in the form of albite. As seen from Table 3, the melting points for all the mentioned compounds are above 1,000°C, and further structural transformation will not occur with the chosen pyrolysis temperature of 500°C. Thereby, no loss of metals during pyrolysis of the pretreated ASR was evident, and these metals can, therefore, be recovered from the pyrolysis residue in the subsequent processing stages. There was no significant difference between the equilibrium predictions and the experimental results.
Pretreated Automotive Shredder Residue Pyrolysis Oil
During the pyrolysis process of pretreated ASR in the CSTR-DC reactor, the condensable gases generated are passed through the condenser, and the pyrolysis oil is collected. Most of the researchers have studied ASR pyrolysis oil in terms of yield. For instance, Evangelopoulos et al. (2018) found 32% pyrolysis oil yield at 500°C. However, there is only less information in the literature on the characterization of ASR pyrolysis oil. This section discusses the characterization of oil from pretreated ASR pyrolysis, which will be useful in separating the individual components if required.
GC-FID Analysis
The selectivity of the hydrocarbon compounds in the pretreated ASR pyrolysis oil obtained at different temperatures is represented in terms of concentration GC-FID data in Figure 8. The carbon atom distribution in the pretreated ASR pyrolysis oil from the GC-FID data was in the C6-C16 range. This indicates the oil produced was a mixture of gasoline (C5-C11) and diesel (C12-C27), while predominantly in the gasoline fraction. As seen from Figure 9, benzene and toluene are high in concentrations at 400°C−500°C. This is formed due to the degradation of plastics in the pretreated ASR pyrolysis process at a temperature range between 400 and 500°C resulting in an aromatization reaction (Evangelopoulos et al., 2018). This correlates with the increase in hydrogen content with temperature, as seen from the previous section of gas composition. The largest mass fractions are obtained at 400°C−500°C. Hexadecane adds to the calorific value of the fuel, and this is detected from the pretreated ASR pyrolysis oil obtained at a temperature of 500°C. The ultimate analysis and HHV are shown in Table 6. The carbon content in the pyrolysis oil is in the range between 82 and 85 wt%. The HHV for the pyrolysis oil obtained at 350–450°C has a similar range of 34 MJ kg−1, and for the 500°C, it is 35 MJ kg−1, which indicates that this oil can be used as an energy source.
Characterization of Pretreated Automotive Shredder Residue Pyrolysis Oil Through Thermogravimetric Analyzer
The mass loss profile and derivative thermogravimetric (DTG) curve for the pyrolysis oil obtained at different temperatures were analyzed in TGA, and the results are depicted in Figures 10A,B. There are two mass loss peaks for each temperature from the TGA curve of the pretreated ASR pyrolysis oil. The total mass loss is 79.08, 72.12, 64.8, and 3.31% for 350, 400, 450, and 500°C, respectively. The pretreated ASR oil obtained after pyrolysis at 350, 400, and 450°C have the similar temperature zones from 30–150°C to 151–300°C, whereas the temperature zone for the pretreated ASR pyrolysis oil obtained at 500°C is from 30 to 250°C. As seen from Figure 10B, the decomposition step for the temperature zone 30°C−150°C has a peak temperature at 115°C, for all the three pyrolysis oils obtained at 350, 400, and 450°C. However, the peak temperature for the oil obtained at 500°C is 110°C. It was also noted that the pyrolysis oil obtained at 500°C was highly volatile and resulted in great mass loss, while in the TGA, it runs. The second temperature zone, 151–300°C, has the peak temperature at 200°C, for pyrolysis oil obtained at 350, 400, and 450°C. The peak temperature for the oil obtained at 500°C is 179°C. This is attributed to the devolatilization of hydrocarbons at boiling points below 300°C. These results can set the temperature range for distillation of the pretreated ASR pyrolysis oil for fuel upgrading.
The GC analysis of the pyrolysis oil revealed to be similar to mixed gasoline–diesel oil, which requires a distillation process to upgrade to fuel grade. The decomposition temperature obtained through the TGA provides partial insights on temperature boundaries for a subsequent distillation process of the pyrolysis oil that should that be envisaged.
Distillation of Automotive Shredder Residue Pyrolysis Oil
This section reports results from two distillation experiments from the pyrolysis oil obtained at 280–350°C and 350–500°C. The distillation procedure is similar to that in the Experimental procedure for pretreated automotive shredder residue pyrolysis section for both experiments. The distillation temperature was chosen based on the boiling point of the hydrocarbon ranges. As identified in the previous section, C6–C16 range hydrocarbon compounds are present in the pyrolysis oil. The fractional distillation of the compounds obtained at three different temperatures was collected and analyzed. The distillate, namely, Fraction 1 was collected at 220°C, Fraction 2 at 250°C, and Fraction 3 at 280°C. The first distillation experiments from the 280–350°C-obtained pyrolysis oil resulted in 24% of Fraction 1, 3% of Fraction 2, and 5.4% of Fraction 3. The mass yield of the second set of experiments had 21% of Fraction 1, 8% of Fraction 2, and 5.8% of Fraction 3. The ultimate analysis of the pyrolysis oil obtained at two different temperatures and respective fractions is shown in Table 7. We noticed that the pyrolysis oil and the distillates have 81–87% carbon content. The HHV of these samples was between 40 and 47 MJ kg−1. Figures 11A,B show that the fractions obtained in the two distillation sets of experiments showed carbon ranges as gasoline and diesel-grade products.
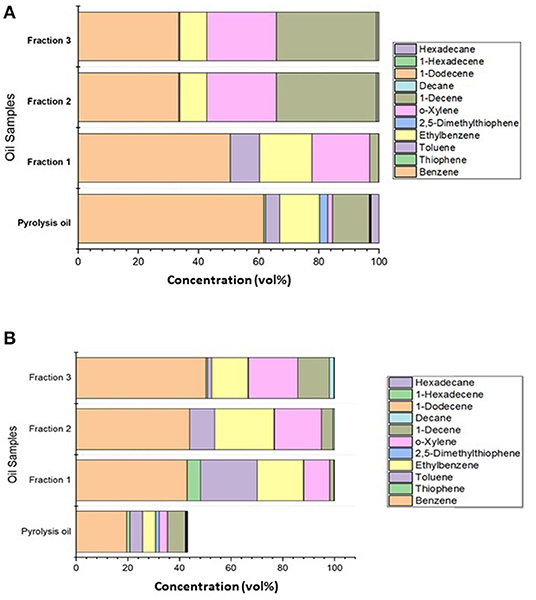
Figure 11. (A) GC-FID analysis of the pretreated ASR pyrolysis oil obtained at 280–350°C and its distillates. (B) GC-FID analysis of the pretreated ASR pyrolysis oil obtained at 350–500°C and its distillates.
Mass Balance During Pyrolysis of Pretreated Automotive Shredder Residue
The Sankey diagram in Figure 12 shows the mass balance for the pretreated ASR pyrolysis process conducted at 350–500°C and the pyrolysis oil separation process carried out in a commercial rotary kiln pyrolyzer that process 10 tons per day of solid waste. For example, if 10 tons of pretreated ASR is processed per day, the products were composed of 61.56% of pyrolysis oil, 29.09% of solid char, and 9.35% of pyrolysis gas. The pyrolysis gas can be either used to synthesize chemicals or for heating the pyrolyzer via combustion. Generally, the solid char is sent to the landfill, but in our process, the metal content present intact in the solid char can be recovered by the leaching process. The main output of the process is the pyrolysis oil distilled for the different fractions with respect to the hydrocarbon separation temperature. The 61% pyrolysis oil's distillation resulted in 18% gasoline grade, 4% diesel grade, and the remaining 40% is residual oil. Therefore, pretreated ASR pyrolysis oil can be recovered as gasoline and diesel-grade products.
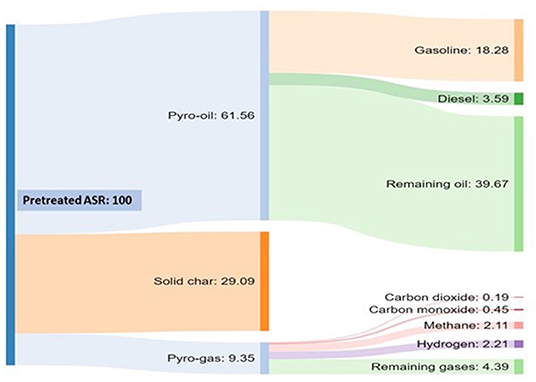
Figure 12. Representation of mass balance of pretreated ASR pyrolysis process at 350–500°C by Sankey diagram.
Conclusion
Pyrolysis is suitable for all the thermochemical conversion methods to convert pretreated ASR for energy and metal recovery. This paper presents the results of theoretical and experimental work on the pyrolysis of pretreated ASR residues.
The pyrolysis runs of pretreated ASR were carried out in the temperature range of 350–500°C in the CSTR-DC reactor. In addition, the thermochemical calculation was performed before the pyrolysis runs to identify the possible equilibrium products at a given temperature range. The thermochemical calculations and experimental work resulted in similar product distribution and composition trends. The products obtained from the pretreated ASR pyrolysis process in the CSTR-DC reactor were 61% pyrolysis oil, 29% solid residue, and 9% pyrolysis gas. The obtained distillate fraction's HHV is in the range of 42–47 MJKg−1. The distilled fractions from the obtained pyrolysis oil can be used as a fuel resource. The solid residue is composed of metals that can be potentially leached out. This would be a value addition, partially replacing, although partly, extraction of the minerals from the earth's crust. It is concluded that pyrolysis of pretreated ASR at 350–500°C is a promising energy and resource recovery process.
Data Availability Statement
The raw data supporting the conclusions of this article will be made available by the authors, without undue reservation.
Author Contributions
SV and SB: conceptualization. SV and MK: investigation. SV: writing—original draft preparation. SB: writing—review and editing and project administration. All authors have read and agreed to the published version of the manuscript.
Funding
This article is for the project funded by the ARC Discovery Project Thermal Isolation: A Novel Pathway to Transforming Complex Waste (DP180101436). SV acknowledges the Australian Research Council for her living scholarship and Monash University for her tuition scholarship.
Conflict of Interest
The authors declare that the research was conducted in the absence of any commercial or financial relationships that could be construed as a potential conflict of interest.
Publisher's Note
All claims expressed in this article are solely those of the authors and do not necessarily represent those of their affiliated organizations, or those of the publisher, the editors and the reviewers. Any product that may be evaluated in this article, or claim that may be made by its manufacturer, is not guaranteed or endorsed by the publisher.
References
Adrados, A., De Marco, I., Caballero, B. M., López, A., Laresgoiti, M. F., and Torres, A. (2012). Pyrolysis of plastic packaging waste: a comparison of plastic residuals from material recovery facilities with simulated plastic waste. Waste Manage. 32, 826–832. doi: 10.1016/j.wasman.2011.06.016
Anzano, M., Collina, E., Piccinelli, E., and Lasagni, M. (2017). Lab-scale pyrolysis of the automotive shredder residue light fraction and characterization of tar and solid products. Waste Manage. 64, 263–271. doi: 10.1016/j.wasman.2017.03.013
Auxilio, A. R., Choo, W.-L., Kohli, I., Chakravartula Srivatsa, S., and Bhattacharya, S. (2017). An experimental study on thermo-catalytic pyrolysis of plastic waste using a continuous pyrolyser. Waste Manage. 67, 143–154. doi: 10.1016/j.wasman.2017.05.011
Buekens, A., and Zhou, X. (2014). Recycling plastics from automotive shredder residues: a review. J. Material Cycles Waste Manage. 16, 398–414. doi: 10.1007/s10163-014-0244-z
Cossu, R., and Lai, T. (2015). Automotive shredder residue (ASR) management: an overview. Waste Manage. 45, 143–151. doi: 10.1016/j.wasman.2015.07.042
De Marco, I., Caballero, B. M., Cabrero, M. A., Laresgoiti, M. F., Torres, A., and Chomón, M. J. (2007). Recycling of automobile shredder residues by means of pyrolysis. J. Anal. Appl. Pyrolysis 79, 403–408. doi: 10.1016/j.jaap.2006.12.002
Evangelopoulos, P., Sophonrat, N., Jilvero, H., and Yang, W. (2018). Investigation on the low-temperature pyrolysis of automotive shredder residue (ASR) for energy recovery and metal recycling. Waste Manage. 76, 507–515. doi: 10.1016/j.wasman.2018.03.048
Ferella, F., De Michelis, I., Scocchera, A., Pelino, M., and Vegliò, F. (2015). Extraction of metals from automotive shredder residue: preliminary results of different leaching systems. Chin. J. Chem. Eng. 23, 417–424. doi: 10.1016/j.cjche.2014.11.014
Joung, H. T., Seo, Y. C., Kim, K. H., Hong, J. H., and Yoo, T. W. (2007). Distribution and characteristics of pyrolysis products from automobile shredder residue using an experimental semi-batch reactor. Korean J. Chem. Eng. 24, 996–1002. doi: 10.1007/s11814-007-0110-y
Li, C., Xia, Z. X., Qiao, X. L., Li, W. B., and Fang, M. X. (2014). The investigation on fragmentation behavior of lignite coal during fluidized bed pyrolysis. Adv. Mat. Res. 953–954, 1254–1260. doi: 10.4028/www.scientific.net/AMR.953-954.1254
Lider, M. C., and Yurtseven, H. (2014). α-β Transition in quartz: temperature and pressure dependence of the thermodynamic quantities for β-quartz and β-cristobalite as piezoelectric materials. 3D Res. 5, 28. doi: 10.1007/s13319-014-0028-1
Mallampati, S. R., Lee, C. H., Truc, N. T. T., and Lee, B.-K. (2015). Quantitative analysis of precious metals in automotive shredder residue/combustion residue via EDX fluorescence spectrometry. Int. J. Environ. Anal. Chem. 95, 1081–1089. doi: 10.1080/03067319.2015.1085521
Maric, J., Berdugo Vilches, T., Thunman, H., Gyllenhammar, M., and Seemann, M. (2018). Valorization of automobile shredder residue using indirect gasification. Energy Fuels 32, 12795–12804. doi: 10.1021/acs.energyfuels.8b02526
Martín-Lara, M. A., Piñar, A., Ligero, A., Blázquez, G., and Calero, M. (2021). Characterization and use of char produced from pyrolysis of post-consumer mixed plastic waste. Water 13, 1188. doi: 10.3390/w13091188
Mayyas, M., Pahlevani, F., Maroufi, S., Liu, Z., and Sahajwalla, V. (2017). Waste conversion into high-value ceramics: carbothermal nitridation synthesis of titanium nitride nanoparticles using automotive shredder waste. J. Environ. Manage. 188, 32–42. doi: 10.1016/j.jenvman.2016.11.079
Notarnicola, M., Cornacchia, G., De Gisi, S., Di Canio, F., Freda, C., Garzone, P., et al. (2017). Pyrolysis of automotive shredder residue in a bench scale rotary kiln. Waste Manage. 65, 92–103. doi: 10.1016/j.wasman.2017.04.002
Sakai, S.-I., Yoshida, H., Hiratsuka, J., Vandecasteele, C., Kohlmeyer, R., Rotter, V. S., et al. (2014). An international comparative study of end-of-life vehicle (ELV) recycling systems. J. Material Cycles Waste Manage. 16, 1–20. doi: 10.1007/s10163-013-0173-2
Sung-Jin, C., Hae-Young, J., Yong-Chil, S, and Woo-Hyun, K. (2010). Studies on gasification and melting characteristics of automobile shredder residue. Environ. Eng. Sci. 27, 577–586. doi: 10.1089/ees.2009.0389
Vermeulen, I., Van Caneghem, J., Block, C., Baeyens, J., and Vandecasteele, C. (2011). Automotive shredder residue (ASR): Reviewing its production from end-of-life vehicles (ELVs) and its recycling, energy or chemicals' valorisation. J. Hazard. Mater. 190, 8–27. doi: 10.1016/j.jhazmat.2011.02.088
Keywords: pretreated ASR, pyrolysis, distilled oil, thermochemical calculation, metal recovery
Citation: Vijayan SK, Kibria MA and Bhattacharya S (2022) A Study on Pyrolysis of Pretreated Automotive Shredder Residue—Thermochemical Calculations and Experimental Work. Front. Sustain. 3:811226. doi: 10.3389/frsus.2022.811226
Received: 08 November 2021; Accepted: 08 February 2022;
Published: 24 March 2022.
Edited by:
Ioanna Vasiliadou, Democritus University of Thrace, GreeceReviewed by:
Christian Manera, Federal University of Rio Grande Do Sul, BrazilGeorge Tsalidis, Delft University of Technology, Netherlands
Copyright © 2022 Vijayan, Kibria and Bhattacharya. This is an open-access article distributed under the terms of the Creative Commons Attribution License (CC BY). The use, distribution or reproduction in other forums is permitted, provided the original author(s) and the copyright owner(s) are credited and that the original publication in this journal is cited, in accordance with accepted academic practice. No use, distribution or reproduction is permitted which does not comply with these terms.
*Correspondence: Sankar Bhattacharya, c2Fua2FyLmJoYXR0YWNoYXJ5YUBtb25hc2guZWR1