- 1Indian Agricultural Research Institute, Pusa, India
- 2National Academy of Agricultural Research Management, Hyderabad, India
Introduction: Tractarization is synonymous with farm mechanization in India. Tractor-trailers are extensively used for the transportation of farm inputs and produce on and off-road, exposing drivers to excessive vibration.
Objectives: The study was undertaken to assess tractor drivers’ vibration exposure while using trailers and to develop low-cost mitigation interventions.
Methodology: The whole-body vibrations were measured at the tractor seat during the transportation with a no, half (3715 kg soil) and full payload (5910 kg soil) trailer on two terrain conditions, namely, asphalt and farm terrains. The speeds recommended by ISO 5008-1979 of 10, 12 and 14 km/h on asphalt roads and 4, 5 and 7 km/h on farm roads, as well as actual working speeds preferred by the operator (18, 20 and 22 km/h on asphalt road and 8, 10 and 12 km/h on farm terrain), were selected for experiments. Two vibration reduction interventions, namely spring suspended single point hitch (I1) and polyurethane (PU) bush (I2), were developed and installed between the tractor and trailer. Whole-body vibration (WBV) was measured by repeating the experiments.
Results: The maximum vibration reduction on asphalt road at 22 km/h with I1 was found as 14.3, 19.03 and 23.1%, whereas on-farm terrain at 12 km/h was found as 15.16, 22.43, and 25.56% for no, half and full payload. Similarly, with I1 + I2 interventions, the maximum total vibration reduction at 22 km/h was 16.86, 21.12 and 25.51% on asphalt roads, whereas on-farm tertian at 12 km/h was 17.07, 23.77 and 28.67%. The average value of lower health guidance caution zone (HGCZ) limits on asphalt roads increased by 1.11, 0.95 and 0.92 h and on-farm tertian 1.55, 1.14 and 0.83 h with no, half, and full payload. The average value of upper HGCZ limits on asphalt roads increased by 3.13, 3.21 and 3.68 h and on-farm tertian by 2.24, 2.94 and 3.31 h with intervention.
Conclusions: This infers that with developed interventions an operator can safely perform for a longer duration and at higher operational speeds because of the reduced vibration.
1 Introduction
Tractors are the main prime mover on farms, and farm mechanization is a synonym for tractarization in India. The tractors are used for “on-the-farm and off-the-farm” operations. A tractor–trailer is a popular and cost-effective mode of transportation for commodities, agricultural produce, soils, etc., in rural India (Agro-Economic Policy Briefs, 2020). The total number of registered trailers in India is 2.27 million, and the tractors are approximately 9.42 million (Road Transport Yearbook, 2019-20). Singh (2001) also reported that the tractor–trailer is mostly used for transport activities and accounted for approximately 60% (600 h) of the average annual use. Almost every day of the year, during sowing and harvesting, tractors are operated for 12–14 h/day (Sorainen et al., 1998).
Operators of agricultural machinery are subjected to various hazards at work, including vibrations, which have a particularly damaging impact on human health (Kumar et al., 2001; Cvetanovic and Zlatkovic, 2013; Cutini et al., 2017; Benos et al., 2020; Chaturvedi et al., 2012). Tractor operators experience more vibration than other types of on-road vehicles (Mehta et al., 2000; Nupur et al., 2013). Tractor operators are generally subjected to whole-body vibrations (WBVs), transmitted through the driver seat and backrest, and segmental vibrations from the footrest and steering wheel (Singh et al., 2023) for a long duration. The magnitude of vibration is dependent on the type of terrain, travel speeds, amount of payload on the trailer, suspension systems, load distribution, and free play at the hitch point. These exposures have been reported beyond the recommended exposure action value (0.5 m/s2) as per ISO 2631-1997 (Nupur et al., 2013; Kumar et al., 2001). Exposure to WBVs is one of the factors that most influence the performance, comfort, and long-term health risks of tractor operators’ problems like back pain, spine degeneration, and spine disc disease on the 4–6-Hz resonance (Pope and Hansson, 1992; Pope et al., 1999; Hulshof and Veldhuijzen van Zanten, 1987; Bovenzi and Hulshof, 1999; Kumar et al., 2001; Khurmi and Gupta, 2005). Several epidemiological studies have demonstrated that mechanical vibrations cause musculoskeletal disorders (MSDs) in the driver workplace and that there is a relationship between WBV exposure and MSDs, especially for low back pain (LBP), associated with increased risk of injury (Bovenzi and Beta, 1994; Kumar et al., 1999). On the other hand, the level of WBV is affected by the type of operation and implementation coupled to the tractor, the speed of operation, and the terrain characteristics. Deo et al. (2021) conducted a study to measure the magnitude of WBV transmitted to the tractor’s operator, where a fully loaded double-axle trailer was attached to the tractor. The magnitude of WBVs on the driver seat in the longitudinal direction on asphalt terrain varied from 0.257 to 0.376 m/s2 and on farm terrain varied from 0.273 to 0.438 m/s2 under the selected conditions, whereas the vertical direction vibration on asphalt varied from 0.373 to 0.552 m/s2 and on farm terrain varied from 0.389 to 0.590 m/s2 under the selected conditions.
Several researchers have pointed out that transportation with single-axle tractor–trailers involves significantly high vibration levels and risk to the driver’s safety (Crolla and Dale, 1980; Scarlet et al., 2007; Deo et al., 2021). The free play at the existing ring and hook-type hitch attachment between the tractor and trailer system is a key factor in contributing to the overall vibration of the tractor drivers (Crolla and Dale, 1980).
The vibration isolator is a preventive measure for vibration exposure, by which the mechanical energy is converted into heat energy and dissipated in a vibratory system. The vibration has to be attenuated before reaching the seat. The vibration exposure to drivers in tractors was reduced using seats provided with passive (Sankar and Afonso, 1993; Mehta and Tewari, 2010) or active suspensions (Stikeleather and Suggs, 1970) and by insulated cabs (Hilton and Moran, 1975). A vibration isolator at the single-point hitch can reduce the vibration exerted by the existing ring and hook-hitching system. Significant vibration reduction in the tractor–trailer combination protects the driver. Considering the safety aspect of the operator, two interventions were developed in the present study and attached between the tractor and single-axle trailer. The WBVs were measured at the operator seats at “no, half, and full payload” at six levels of speeds as per ISO 5008 and normal working speeds of tractor–trailer combinations without and with interventions on two terrains. The reduction in WBVs, total vibration values, and lower and upper HGCZ limits and improvements in the working hours were computed from the measured WBV.
2 Materials and methods
The measurement of the WBV transmitted to the tractor driver during haulage operations under different operating conditions and the design and development of interventions for vibration reduction and evaluation were conducted at the Division of Agricultural Engineering, ICAR-Indian Agricultural Research Institute, New Delhi, India.
2.1 Selection of the tractor and trailer
A New Holland 3630 TX Plus 2WD Tractor was used for the experiments. The tractor’s fuel tank was completely filled, and it was operated without blasting by a 68-kg, 172-cm-tall driver with and without interventions. A 5-ton payload capacity trailer with 10 × 6 × 2-ft platform, 13-leaf suspension, 9–20-inch tires, and a ring-type hitch/tow eye of a single-axle/semi-trailer was used for the measurement of WBVs. The selected trailer used for the experiment during the weight measurement on the electronics weighing balance is shown in Figure 1.
A piezoelectric seat pad accelerometer (model: P364241) and an HVM200 Vibration Meter were used for the measurement of whole-body vibrations experienced by the tractor driver. The detailed specifications of the vibration meter and accelerometer are given in Table 1.
The recorded data in a vibration meter were monitored remotely using Wi-Fi and Bluetooth protocol in an Android mobile and analyzed using G4 Utility software installed in a personal computer (PC). The seat pad accelerometer was positioned on the seat pad and connected to the vibration meter through a four-pin, three-channel sensor connector. Before the measurement, the vibration meter was configured with the installed LD Atlas Android application on mobile, and then a 1/3 octave bandwidth was selected with sensor sensitivity values in the app. The multiplying factor (k) of frequency weighting Wd = 1.4 for the x- and y-directions and Wk = 1 for the z-axis were also applied to the app. The data were collected for a time duration of 2 min. The acceleration values were recorded according to the ISO 2631-1:1997 standard. A schematic diagram of the complete data collection approach is shown in Figure 2.
2.2 Development of interventions for reducing the vibration transmitted to the tractor driver
While measuring vibrations, it became apparent that suitable remedial measures were needed to reduce vibrations within standardized limits. The free play at the hitch point in the tractor–trailer combination was observed to be one of the induced sources of vibration affecting the tractor driver. The method to reduce vibration exposure to the driver was considered by keeping the vibration isolator at the hitch point in this study. The vibration isolator consists of two interventions, namely, parallel spring-suspended single-point hitch (I1) and polyurethane (PU) bush (I2). The existing hitching unit of the tractor was replaced with developed intervention I1, which dampens the longitudinal linear forces acting between the tractor and trailer. The design of a retrofit-type single-point hitch with spring suspension, considering the existing rear arrangement of the tractor, ensures compatibility with the developed hitch. The development of interventions involved measuring the force at the hitch point, selecting appropriate materials, and designing interventions.
2.2.1 Measurement of force
Tensile and compressive forces were measured at the existing hitch point during the haulage operation for the development of the interventions. During the starting and stopping of the tractor–trailer, the tensile and compressive forces acting at the hitch point were measured. Therefore, a three-point hitch dynamometer (Kumar et al., 2020) was used to determine both the forces acting at the hitch point. The forces acting on the hitch point were measured at the maximum speed considered in the study (22 km/h) with a fully loaded tractor–trailer on asphalt terrain. The maximum compressive force acting at the hitch point was 2,746 N at 22 km/h in the longitudinal direction.
2.2.2 Selection of materials
Spring and PU materials were selected for developing vibration reduction interventions. Spring is used for creating shock isolators (Ahmed et al., 2020). Repetitive impact loading occurs between the tractor and trailer. Chrome vanadium is used for shock and impact loads. Therefore, a chrome vanadium spring is selected for the intervention. Polyurethane is a unique elastic material chosen for its versatile hardness range. This material can replace rubber, plastic, and metal due to its exceptional abrasion resistance and physical properties. It has a higher load-bearing capacity than conventional rubber, making it suitable for various applications. Polyurethane exhibits remarkable resistance to oxygen, sunlight, and weather conditions. Therefore, spring and polyurethane were selected for vibration reduction intervention (Chaturvedi et al., 2012). The properties of the selected spring and polyurethane are listed in Table 2.
2.2.3 Spring design
In the tractor–trailer combination, while the tractor is in the moving condition, the longitudinal compressive forces were observed to act at the hitch point. Therefore, a compressive spring with two ground ends was selected to absorb the forces acting at the hitch point. The measured compressive force varied from 294.3 to 2746.8 N. It was assumed that the force acting on both parallel springs was equally distributed to each spring because each spring was placed at an equal distance from the center (Figure 3A). The design of the spring was based on the study at IIT Kharagpur (2014). Different spring indexes and wire diameters were used for designing the spring. The optimum spring index (7) and spring wire diameter (12 mm) were selected. As per the space constraint, the deflection of the spring was considered 50 mm. The coil mean diameter, mean load, stress amplitude, shear stress concentration factor, Wahl correction factor, mean shear stress, stress amplitude, ultimate strength, shear yield point, and shear endurance limit were calculated. The required calculated values were applied to the Soderberg equation, and the factor of safety was calculated as 1.298, which was greater than 1.2 (the desired factor of safety). Spring stiffness, number of turns, and spring length were also calculated. For optimizing the intervention design, a simple mass–spring system was simulated on MATLAB. It was observed that the frequency of the induced vibration was greater than the resonance point of the mass–spring system.
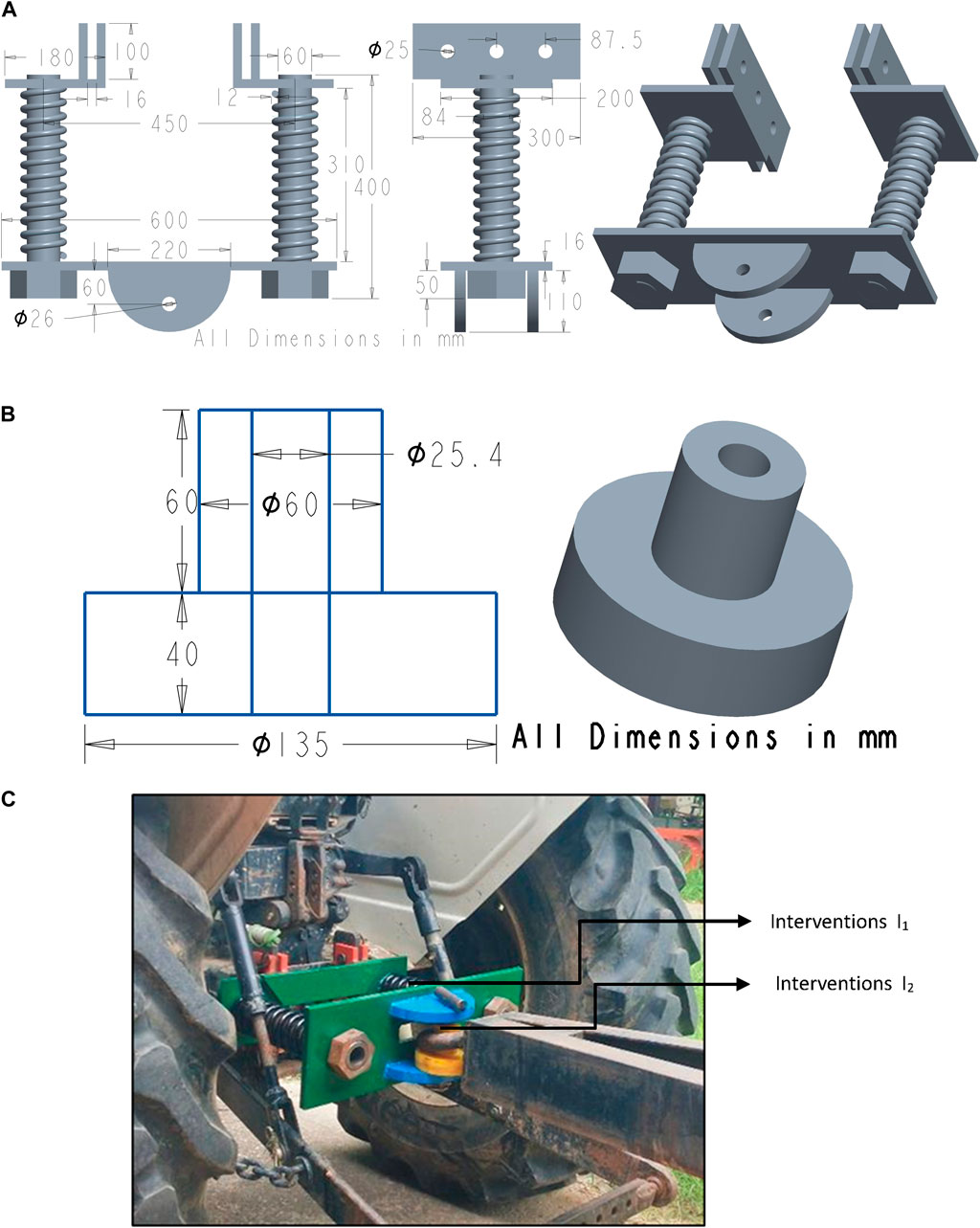
Figure 3. (A) CAD drawing of the spring-suspended tractor–trailer hitch (I1); (B) PU bush (I2); and (C) installed interventions I1 + I2.
Therefore, a spring with a length of 310 mm, a wire diameter of 12 mm, a coil diameter of 84 mm, and a spring stiffness of 24,525 N/m was selected for intervention I1. These springs were inserted into 60-mm-diameter, 400-mm-long shafts. The intervention (I1) comprises two shafts, two compression springs, two mounting end plates for connecting to the tractor, and a mounting plate for connecting to the tow eye of a trailer. The dimensions and CAD drawings of these components are shown in Figure 3A. The entire arrangement of the spring-suspended single-point hitch unit was designed to slide freely on the center shafts, which absorb the longitudinal load from the trailer. The design considerations and obtained values for the selected spring are given in Table 3.
2.2.4 PU bush
The dimensions of the tow eye hook in the trailer were considered for the design of the PU bush for intervention (I2). The reason for incorporating the PU bush along with intervention (I1) in the existing hitch system of the trailer is to reduce movement because of the free space between the locking pin and tow eye. The metal contact results in impact transmission due to the undulation of roads, changes in speed, and inertial forces of the trailer. The polyurethane bush with a collar, placed into a tow eye of the trailer, provided isolation during the metal-to-metal contact. The CAD drawings of the developed PU bush and the dimensions for the tractor–trailer tow eye hook are shown in Figure 3B. The developed interventions I1 and I2 attached together to the tractor are shown in Figure 3C.
2.3 Experimental plan
The WBV was measured at the tractor seat during the transportation with an empty (no load), half-load (3,715 kg soil), and full-load (5,910 kg soil) trailer under two terrain conditions, namely, asphalt and farm terrains, respectively. The speeds recommended by ISO 5008-1979 of 10, 12, and 14 km/h on asphalt roads and 4, 5, and 7 km/h on farm roads, as well as actual working speeds preferred by the operator (18, 20, and 22 km/h on asphalt road and 8, 10, and 12 km/h on farm terrain), were selected for experiments. The speeds of the tractor were monitored and maintained using the rpm of the tractor and selected gear. The experiment was conducted in three replications for each treatment under all conditions. The conducted experiments are summarized in Table 4.
2.4 Determination of the lower and upper health guidance caution zone limits
IS 13276 (Part 1):2000/ISO 2631-1 (1997) was used for the evaluation of exposure risk. Health risk prediction primarily depends upon vibration magnitude and duration of exposure in a day. The HGCZ limit is the area between two parallel lines of lower and upper limits corresponding to working/exposure hours. The vibration exposure below, inside, and above the zone shows minimal, moderate, and high health risks, respectively. Exposure duration for upper and lower HGCZ limits was calculated from the formula given below, as discussed by Griffin (1998) and Kumar et al. (2001):
where Tu and Tl are exposure durations at the upper and lower limits of the caution zone, respectively; T6 and T3 are exposure durations from 1–10 min at 6 m/s2 and 3 m/s2 rms acceleration for the health caution zone, respectively; and aw is frequency-weighted acceleration.
3 Results and discussion
The magnitude of WBVs was measured on the driver seat in three directions (x-, y-, and z-directions), and the total vibration value was computed (IS-13276-Part 1:2000) under both terrain conditions. All 12 speeds and 3 loads on the trailer without and with interventions were computed under the same operational conditions (Table 4). The upper and lower HGCZ durations were determined for predicting the health effect on the human body using the measured vibrations.
3.1 Asphalt terrain
3.1.1 Vibration in x-, y-, and z-directions
The WBV was measured on asphalt terrain at the selected speed ranges from 10 to 22 km/h.
Without intervention: The vibration values in x-, y-, and z-directions for an empty trailer at different speeds varied from 0.22 to 0.428, 0.126 to 0.264, and 0.378 to 0.698 m/s2, respectively. For half-load conditions without intervention, vibrations varied from 0.248 to 0.551, 0.157 to 0.352, and 0.424 to 0.888 m/s2 for three orthogonal directions, respectively. For full-load conditions, vibrations in three orthogonal directions varied from 0.293 to 0.612, 0.178 to 0.409, and 0.559 to 1.106 m/s2, respectively.
With interventions I1 and I1 + I2: The maximum reduction was achieved in the x-direction, followed by the z- and y-directions; moreover, the reduction was maximum in I1 + I2 for all operating conditions. The vibration reduction with I1 + I2 for no payload was 11.82%–25.0%, 5.48%–14.02%, and 6.08%–15.33%; for the half-load condition, it was 13.71%–28.13%, 6.37%–16.48%, and 8.02%–19.26%; for the full-load condition, it was 22.53%–37.25%, 9.55%–17.60%, and 10.2%–21.97% in x, y, and z-directions respectively.
3.1.2 Vibration total values (av)
The vibration total values (av) of weighted rms acceleration were computed from recorded vibrations and are given in Table 5. The total vibration values with three load conditions increased with operational speed. The vibration values obtained at normal operational speeds (18, 20, and 22 km/h) were relatively higher than the recommended speeds (10, 12, and 14 km/h) stated in ISO 5008: 2002, regardless of the load condition. The highest vibrations were observed when the vehicle was fully loaded and traveling at the highest speed of 22 km/h, while the minimum vibrations occurred at the lowest speed of 10 km/h under the no-load conditions. The total vibration value at the maximum recommended speed (14 km/h) and maximum working speed (22 km/h) at full load was reduced by 14.73% and 23.10% with I1 intervention, whereas with I1 + I2 reductions, the values were 16.41% and 25.51%.
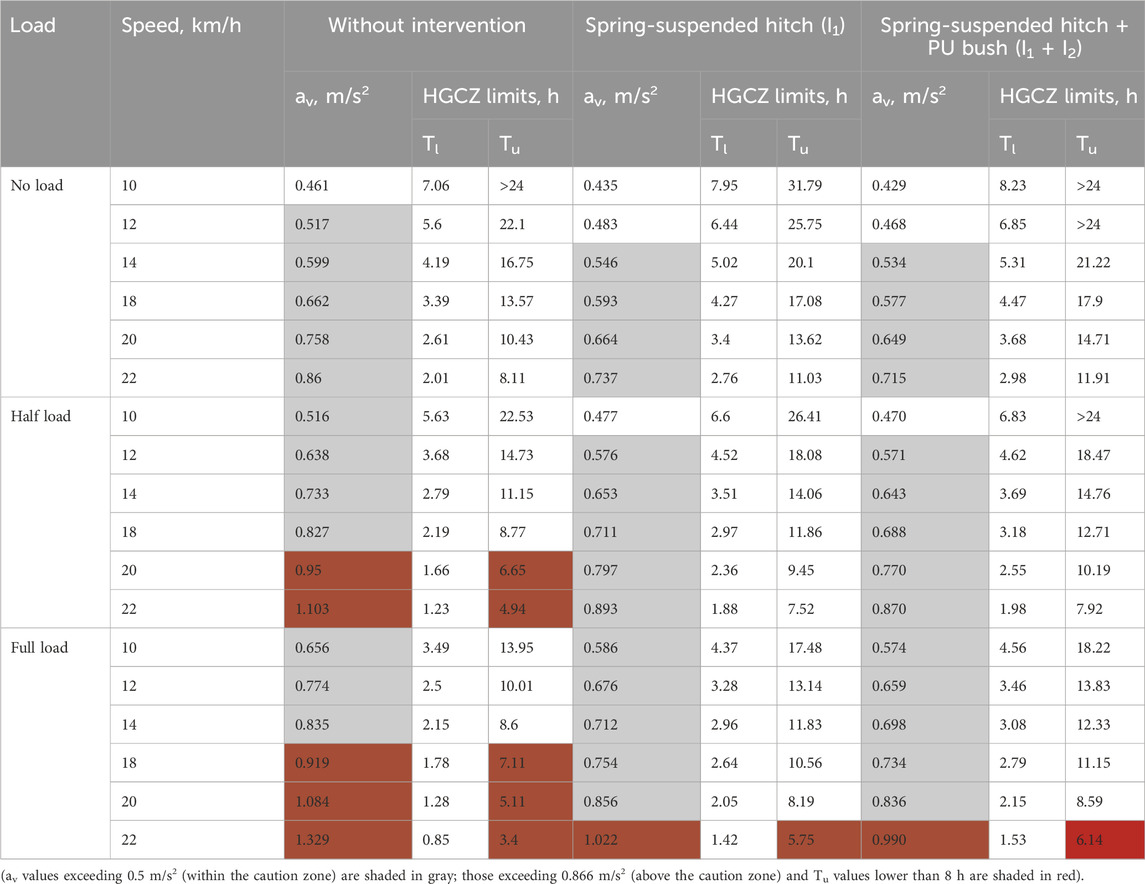
Table 5. Magnitude of total vibration values and daily exposure values (lower and upper HGCZ limits) on asphalt terrain with and without interventions.
3.1.3 HGCZ exposure duration limits
The HGCZ exposure duration limits (Tu and Tl) were calculated from the total vibration value (Table 5) using HGCZ values [as per ISO 2631-1: 1997 IS 13276 (Part 1):2000; Figure B.1 and Equation B.1]. The upper and lower recommended weighted rms accelerations at 8 h exposure duration were 0.866 and 0.433 m/s2, respectively, as obtained using Equation B.1. The recommended weighted rms acceleration for 8 h exposure is compared with the estimated total acceleration value for the experimental conditions. Operating the tractor above the caution zone is likely to be a high health risk and also a potential health risk within the caution zone. Table 5 shows that under all operating conditions except at 10 km/h with no load conditions, the driver was at potential health risk and, under some operating conditions, even at high health risk. Based on the upper HGCZ limit without intervention, the total vibration values at speeds more than 20 km/h with half load and also more than 18 km/h at full load were above the caution zone because the total acceleration value (Table 5) exceeded the recommended value (0.866 m/s2) for the 8-h exposure acceleration limit. At these operating conditions, Tu was less than 8 h under the same circumstances. Based on the upper HGCZ limit at the condition with interventions (I1, I1 + I2), only a speed of 22 km/h with full load was above the caution zone as the total acceleration value (Table 5) exceeded the recommended value of the 8-h exposure acceleration limit. Furthermore, Tu was less than 8 h under this operating condition (Table 5). For all other operating conditions (less than 22 km/h), Tu was more than 8 h, with the developed interventions indicating lesser severity of vibration magnitude. A graphical representation of change in Tu and Tl values of HGCZ without and with intervention at 22 km/h is shown in Figure 4A.
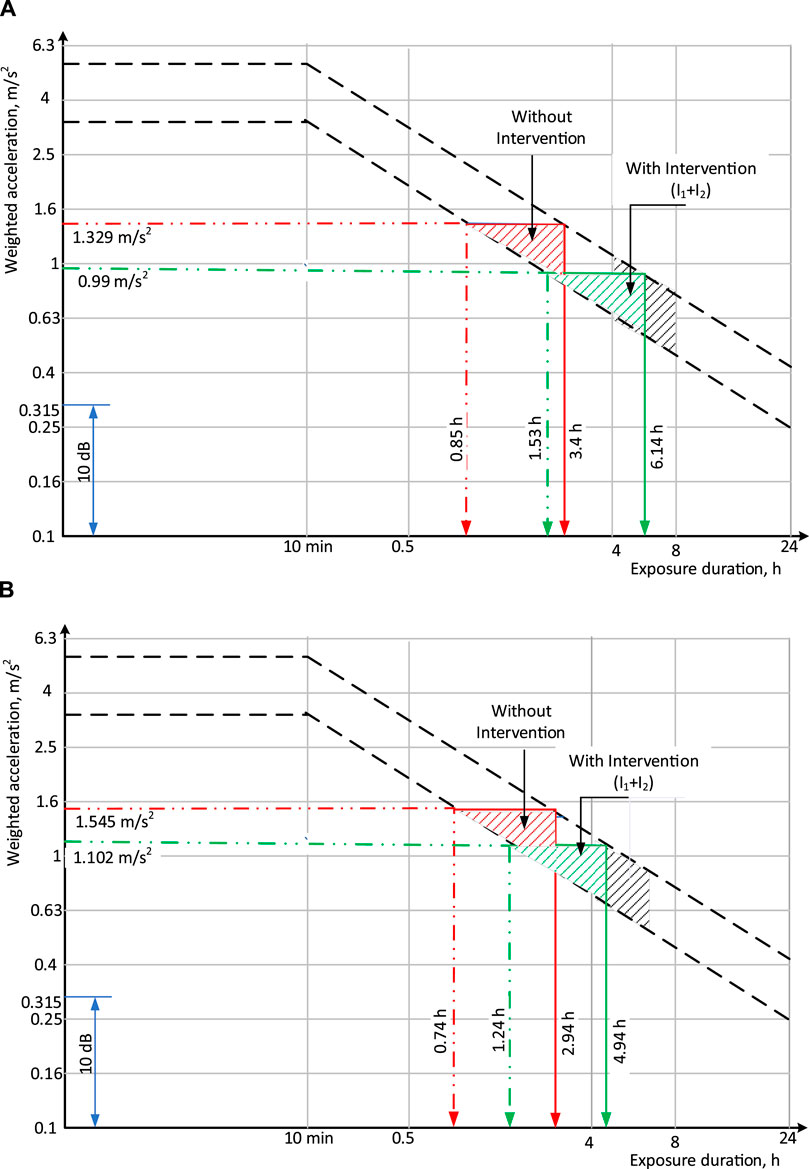
Figure 4. Graphical representation of lower and upper exposure limits with a fully loaded tractor–trailer (A) at 22 km/h on asphalt terrain and (B) at 12 km/h on farm terrain.
3.2 Farm terrain
3.2.1 Vibration in x-, y-, and z-directions
The WBV was also measured on farm terrain at the selected speeds from 4–10 km/h.
Without intervention: The vibration values in x-, y-, and z-directions for the no-load condition varied from 0.177 to 0.513, 0.112 to 0.35, and 0.260 to 0.779 m/s2, respectively. For the half-load condition, they varied from 0.213 to 0.602, 0.134 to 0.393, and 0.308 to 1.057 m/s2, respectively; similarly, for the full-load condition, they varied from 0.268 to 0.696, 0.181 to 0.448, and 0.437 to 1.305 m/s2, respectively.
With interventions I1 and I1 + I2: The maximum reduction in vibration was found in the x-direction, followed by the z- and y-directions; furthermore, reduction was higher with I1 + I2 than with I1. The vibration reduction with the intervention I1 + I2 for the no-load condition was achieved as 13.56%–26.90%, 6.25%–10.57%, and 7.69%–14.51%; for the half-load condition, it was 15.96%–30.26%, 6.72%–16.28%, and 9.42%–22.80%; for the full-load condition, it was 18.66%–35.34%, 8.29%–17.41%, and 9.61%–28.35% in the x-, y-, and z-directions, respectively.
3.2.2 Vibration total values (av)
Total vibration values, without and with intervention, for different operational conditions are given in Table 6. With the increase in speed, the total vibration values on farm terrain were observed to increase for all three selected load conditions. The vibration was higher when the vehicle was operating at normal working speeds (8, 10, and 12 km/h) than at the recommended speeds (4, 5, and 7 km/h) stated in ISO 5008: 2002, regardless of the load condition. The highest vibrations were observed when the vehicle was fully loaded and traveling at 12 km/h, while the minimum vibrations occurred at no load and 4 km/h (Table 6). The total vibration value at the maximum recommended 7 km/h and full load on farm roads was reduced by 27.79% and 30.10%, respectively, with interventions. Similarly, the total vibration value at a maximum working speed of 12 km/h and full load were reduced by 25.57% and 28.67%, respectively, with intervention I1 and I1 + I2.
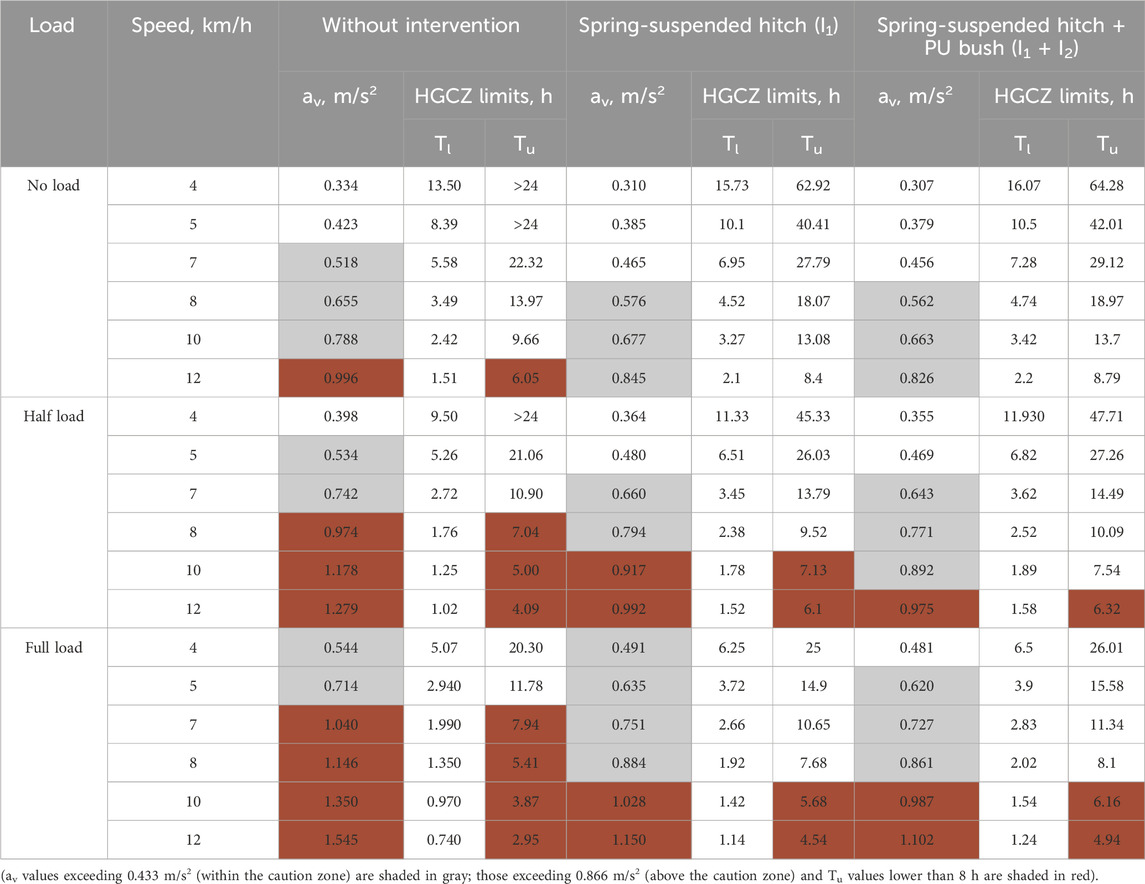
Table 6. Magnitude of total vibration values and daily exposure values (lower and upper HGCZ limits) on farm terrain with and without interventions.
3.2.3 HGCZ exposure duration limits
Table 6 shows that on farm roads without intervention under all operating conditions—except at 4 km/h with no-load and half-load conditions and 5 km/h at no-load conditions—the operator was at potential health risk as total vibration values exceeded the recommended lower HGCZ limit of 0.5 m/s2. The driver operating the tractor at 12 km/h with no load, 8–10 km/h with half load, and 7–12 km/h with full load was at higher health risk as the total vibration values exceeded the recommended upper HGCZ limit of 0.866 m/s2. With the application of intervention I1, the total vibration values exceeded the upper HGCZ limits at 12, 10, and 7–8 km/h with no-, half-, and full-load conditions, respectively, below the upper HGCZ. With I1 + I2, the exceeded upper HGCZ limits at 12, 8–10, and 7–8 km/h with no-, half-load, and full-load conditions, respectively, were below the upper HGCZ limits. Operating the tractor at 12 and 10–12 km/h with half-load and full-load conditions causes high health risks, so the driver should not work for 8 h. Graphical representation of change in Tu and Tl values of HGCZ without and with intervention at 12 km/h is shown in Figure 4B.
3.3 Enhancement of operational hours with developed interventions
Enhancement of working hours in the lower and upper HGCZs on both asphalt and farm terrains with interventions I1 and I1 + I2 at the maximum recommended and normal working speed is shown in Figures 5A, B.
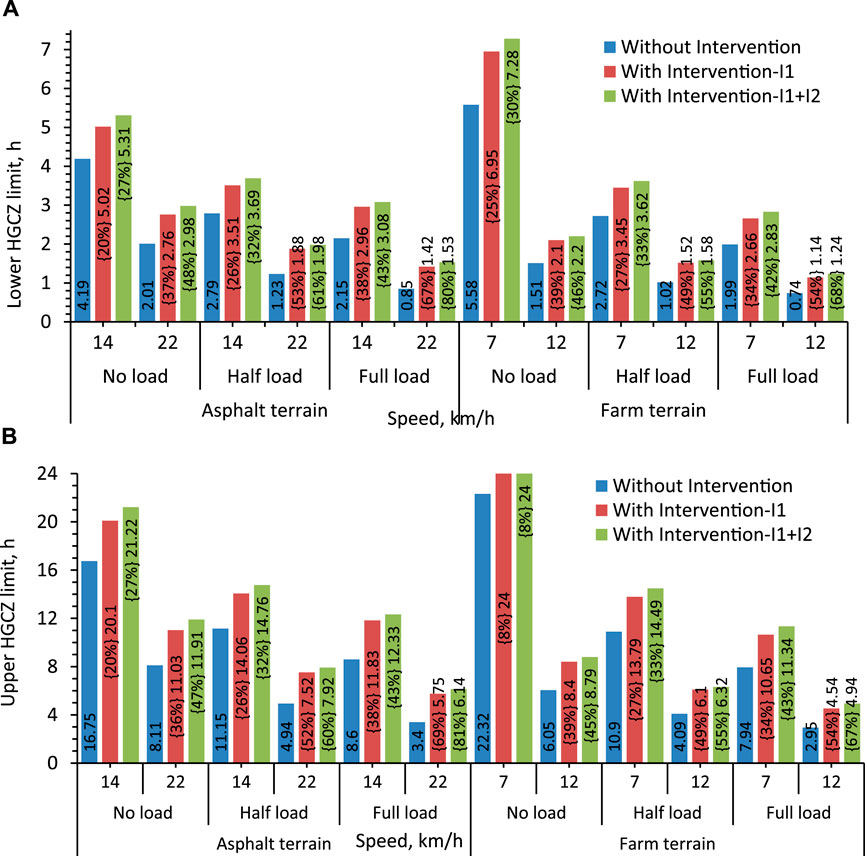
Figure 5. Working hours and its improvement (%age) in the HGCZ limit after the incorporation of interventions for asphalt and farm terrain. (A) Lower HGCZ limit. (B) Upper HGCZ limit.
On asphalt roads, with interventions, WBVs reduced; consequently, the working hours of tractors increased even at high speed and also from above the HGCZ to within the HGCZ. The increased working duration was computed by subtracting the lower limit from the lower HGCZ values and the upper limit from the upper HGCZ values, comparing conditions without intervention to those with interventions I1 and I1 + I2. The maximum duration at 22 km/h increased by 45, 39, and 34 min for lower HGCZ limits and 2.92, 2.58, and 2.35 h for upper HGCZ limits with an empty, half-loaded, and fully loaded tractor–trailer, respectively, by attaching the intervention I1. Similarly, by attaching both the intervention I1 + I2 at 22 km/h, the maximum duration increased by 58, 45, and 40.8 min for lower HGCZ limits and 3.8, 3, and 2.74 h for upper HGCZ limits with an empty, half-loaded, and fully loaded tractor–trailer.
On farm roads, increased duration was also observed with interventions. The maximum duration was increased at 12 km/h by 35.4, 30, and 24 min for lower HGCZ limits and 2.35, 2.01, and 1.59 h for upper HGCZ limits with an empty, half-loaded, and fully loaded tractor–trailer, respectively, with intervention I1. Similarly, with intervention I1 + I2 at 12 km/h, the maximum duration was increased by 41.4, 33.6, and 30 min for lower HGCZ limits and 2.74, 2.23, and 2 h for upper HGCZ limits with an empty, half-loaded, and fully loaded tractor–trailer.
The spring intervention I1 absorbed the longitudinal direction forces, reducing the vibration magnitude. Polyurethane intervention restricted the vertical movement of the hitch, reducing the vertical impact on the tractor and resulting in reduced vibrations in the vertical direction. The combination of both interventions reduced the total vibration value, enhancing the safe operational time for operators.
4 Conclusion
The measured vibration in the x-, y-, and z-directions increased with increasing speed and load on a trailer on both asphalt and farm terrains. The vibration with interventions in all three directions and total vibration reduced at all selected speeds and loads. The total vibration values on asphalt terrain varied from 0.441 to 0.860, 0.516 to 1.103, and 0.656 to 1.329 m/s2, whereas on farm road, they varied from 0.334 to 0.996, 0.398 to 1.279, and 0.544 to 1.545 m/s2 under no, half-, and full-load trailer conditions, respectively. The percentage vibration reduction by attaching the developed intervention in the x-direction was higher in all operating conditions, followed by the z-direction and y-direction. The maximum total vibration at 22 km/h on asphalt roads was reduced by 16.86%, 21.12%, and 25.51% under empty, half, and full-load tractor–trailer conditions, respectively, by attaching the intervention. Similarly, the reduction on farm terrain was 17.07%, 23.77%, and 28.67%. On asphalt roads, the average value of lower HGCZ limits increased by 1.11, 0.95, and 0.92 h under empty, half-, and full-load tractor–trailer conditions, respectively, by attaching the intervention. On farm terrain, the average value of lower HGCZ limits increased by 1.55, 1.14, and 0.83 h. On asphalt roads, the average value of upper HGCZ limits increased by 3.13, 3.21, and 3.68 h and also increased in farm terrain by 2.24, 2.94, and 3.31 h under no-, half-, and full-load tractor–trailer conditions, respectively, with the incorporation of interventions. This infers that an operator can safely perform 2–3 h more with the developed simple interventions. The operational speed with intervention for full load increased from 18 to less than 22 km/h and 7 to 10 km/h for asphalt and farm terrain, respectively, considering the Tu limit of 8 h.
Data availability statement
The original contributions presented in the study are included in the article/Supplementary Material; further inquiries can be directed to the corresponding author.
Author contributions
RN: investigation, methodology, writing–original draft and writing–review and editing. AK: funding acquisition, supervision, writing–original draft, and writing–review and editing. RK: data curation, software, supervision, validation, writing–original draft, and writing–review and editing. HK: conceptualization, supervision, and writing–review and editing. MK: supervision and writing–review and editing. VR: supervision and writing–review and editing. SP: data curation, formal analysis, and writing–review and editing.
Funding
The author(s) declare that financial support was received for the research, authorship, and/or publication of this article. The funds were provided by ICAR-IARI, New Delhi, and the Project Coordinator of the “ICAR-All India Coordinated Research Project on Ergonomics and Safety in Agriculture.”
Acknowledgments
The authors acknowledge the ICAR-Indian Agricultural Research Institute, New Delhi, and the “ICAR-All India Coordinated Research Project on Ergonomics and Safety in Agriculture” for providing necessary facilities and financial support.
Conflict of interest
The authors declare that the research was conducted in the absence of any commercial or financial relationships that could be construed as a potential conflict of interest.
Publisher’s note
All claims expressed in this article are solely those of the authors and do not necessarily represent those of their affiliated organizations, or those of the publisher, the editors, and the reviewers. Any product that may be evaluated in this article, or claim that may be made by its manufacturer, is not guaranteed or endorsed by the publisher.
References
Agro-Economic Policy Briefs (2020). Aiding the future of India’s farmers and agriculture complied by centre for management in agriculture (CMA) Indian Institute of management ahmedabad, prof. Poornima, verma. Available at: https://www.iima.ac.in/sites/default/files/2022-12/Policy_Brief_June-2020.pdf.
Ahmed, R. S., Atiyah, K. A., and Abdulsahib, I. A. (2020). Control of vibration by using dynamic vibration absorber. IOP Conf. Ser. Mater. Sci. Eng. 881 (1), 012080. doi:10.1088/1757-899x/881/1/012080
Benos, L., Tsaopoulos, D., and Bochtis, D. (2020). A review on ergonomics in agriculture. Part II: mechanized operations. Appl. Sci. 10 (10), 3484. doi:10.3390/app10103484
Bovenzi, M., and Betta, A. (1994). Low-back disorders in agricultural tractor drivers exposed to whole-body vibration and postural stress. Appl. Ergon. 25 (4), 231–241. doi:10.1016/0003-6870(94)90004-3
Bovenzi, M., and Hulshof, C. T. J. (1999). An updated review of epidemiologic studies on the relationship between exposure to whole-body vibration and low back pain (1986–1997). Int. Archives Occup. Environ. Health 72, 351–365. doi:10.1007/s004200050387
Chaturvedi, V., Kumar, A., and Singh, J. K. (2012). Power tiller: vibration magnitudes and intervention development for vibration reduction. Appl. Ergon. 43 (5), 891–901. doi:10.1016/j.apergo.2011.12.012
Crolla, D. A., and Dale, A. K. (1980). Ride vibration measurements of agricultural tractor and trailer combinations. Veh. Syst. Dyn. 9 (5), 261–279. doi:10.1080/00423118008968625
Cutini, M., Brambilla, M., and Bisaglia, C. (2017). Whole-body vibration in farming: background document for creating a simplified procedure to determine agricultural tractor vibration comfort. Agriculture 7 (10), 84. doi:10.3390/agriculture7100084
Cvetanovic, B., and Zlatkovic, D. (2013). Evaluation of whole-body vibration risk in agricultural tractor drivers. Bulg. J. Agric. Sci. 19 (5), 1155–1160.
Deo, M. M., Kumar, A., and Mani, I. (2021). Whole body vibration on drivers seat and fender with fully loaded double axle tractor-trailers under different operating conditions: whole body vibration on drivers seat and fender. J. AgriSearch 8 (2), 149–154. doi:10.21921/jas.v8i2.7300
Griffin, M. J. (1998). A comparison of standardized methods for predicting the hazards of whole-body vibrations and repeated shocks. J. Sound Vib. 215, 883–914. doi:10.1006/jsvi.1998.1600
Hilton, D. J., and Moran, P. (1975). Experiments in improving tractor operator ride by means of a cab suspension. J. Agric. Eng. Res. 20 (4), 433–448. doi:10.1016/0021-8634(75)90079-7
Hulshof, C., and Veldhuijzen van Zanten, B. (1987). Whole-body vibration and low-back pain: a review of epidemiologic studies. Int. Archives Occup. Environ. Health 59, 205–220. doi:10.1007/BF00377733
IIT Kharagpur (2014). Module 7-design of springs. Available at: https://www.coursehero.com/file/10491372/Lesson-20/.
IS 13276 (Part 1):2000/ISO 2631-1 (1997). Mechanical vibration and shock-evaluation of human exposure to whole body vibration.
Kumar, A., Mahajan, P., Mohan, D., and Varghese, M. (2001). IT—information technology and the human interface: tractor vibration severity and driver health: a study from rural India. J. Agric. Eng. Res. 80 (4), 313–328. doi:10.1006/jaer.2001.0755
Kumar, A., Mathew, V., Mohan, D., and Mahajan, P. (1999). Effect of whole body vibration on low back: a case-control study of tractor drivers in north India. Spine 24 (23), 2503–2513.
Kumar, R., Sahoo, P. K., Choudhary, A. K., and Indramani, I. (2020). Design, development and performance evaluation of tractor-drawn raised-bed pulse-planter for precision sowing of pigeonpea (Cajanus cajan). Indian J. Agric. Sci. 90 (9), 1800–1809. doi:10.56093/ijas.v90i9.106631
Mehta, C. R., Shyam, M., Singh, P., and Verma, R. N. (2000). Ride vibration on tractor-implement system. Appl. Ergon. 31 (3), 323–328. doi:10.1016/s0003-6870(99)00050-2
Mehta, C. R., and Tewari, V. K. (2010). Damping characteristics of seat cushion materials for tractor ride comfort. J. Terramechanics 47 (6), 401–406. doi:10.1016/j.jterra.2009.11.001
Natarajan, N., Bharathidhasan, S., Thanigaivelan, R., and Suresh, P. (2014). “Sisal fiber/glass fiber hybrid nanocomposite: the tensile and compressive properties,” in 5th International and 26th All India Manufacturing Technology, Design and Research Conference, Guwahati, Assam, 1–6.
Nupur, Y., Tewari, V. K., Thangamalar, R., Kumari, S., and Kumar, A. (2013). Translational vibration evaluation of tractor seats for ride comfort. Agric. Eng. Int. CIGR J. 15 (4), 102–112.
Pope, M. H., and Hansson, T. H. (1992). Vibration of the spine and low back pain. Clin. Orthop. Relat. Res. 279, 49–59. doi:10.1097/00003086-199206000-00007
Pope, M. H., Wilder, D. G., and Magnusson, M. L. (1999). A review of studies on seated whole body vibration and low back pain. Proc. Institution Mech. Eng. Part H J. Eng. Med. 213 (6), 435–446. doi:10.1243/0954411991535040
Road Transport Yearbook (2019-2020). Government of India, ministry of road transport and highways transport research wing. New Delhi, 23.
Sankar, S., and Afonso, M. (1993). Design and testing of lateral seat suspension for off-road vehicles. J. terramechanics 30 (5), 371–393. doi:10.1016/0022-4898(93)90012-M
Scarlett, A. J., Price, J. S., and Stayner, R. M. (2007). Whole-body vibration: evaluation of emission and exposure levels arising from agricultural tractors. J. Terramechanics 44, 65–73. doi:10.1016/j.jterra.2006.01.006
Singh, A., Nawayseh, N., Dhabi, Y. K., Samuel, S., and Singh, H. (2023). Digital agriculture: analysis of vibration transmission from seat to back of tractor drivers under multidirectional vibration conditions. Int. J. Industrial Eng. 30 (2). doi:10.23055/ijietap.2023.30.2.8773
Singh, G. (2001). Relationship between mechanization and agricultural productivity in various parts of India. Agric. Mech. Asia, Afr. Lat. Am. 32 (2), 68–76.
Sorainen, E., Penttinen, J., Kallio, M., Rytkönen, E., and Taattola, K. (1998). Whole-body vibration of tractor drivers during harrowing. Am. Industrial Hyg. Assoc. J. 59 (9), 642–644. doi:10.1202/0002-8894(1998)059<0642:wvotdd>2.0.co;2
Keywords: farm tractor–trailer, whole-body vibration, vibration reduction intervention, lower and upper health guidance caution zone limits, spring-suspended vibration absorber, polyurethane bush
Citation: Naveen R, Kumar A, Kumar R, Kushwaha HL, Khanna M, Ramasubramanian V and Poojith S (2024) Assessment of whole-body vibration and development of mitigation intervention for single-axle tractor–trailer combination. Front. Mech. Eng. 10:1426764. doi: 10.3389/fmech.2024.1426764
Received: 02 May 2024; Accepted: 12 September 2024;
Published: 30 September 2024.
Edited by:
Giuseppe Petrone, University of Naples Federico II, ItalyReviewed by:
Lorenzo Maccioni, Free University of Bozen-Bolzano, ItalyGiovanni Carabin, Free University of Bozen-Bolzano, Italy
Copyright © 2024 Naveen, Kumar, Kumar, Kushwaha, Khanna, Ramasubramanian and Poojith. This is an open-access article distributed under the terms of the Creative Commons Attribution License (CC BY). The use, distribution or reproduction in other forums is permitted, provided the original author(s) and the copyright owner(s) are credited and that the original publication in this journal is cited, in accordance with accepted academic practice. No use, distribution or reproduction is permitted which does not comply with these terms.
*Correspondence: Rajeev Kumar, cmFqZWV2aWl0a2dwMTFAZ21haWwuY29t