- 1Department of Agricultural Extension and Economics, Vit School of Agricultural Innovations and Advanced Learning, Vellore Institute of Technology, Vellore, Tamil Nadu, India
- 2Department of Engineering and Maintenance, Sanghavi Shoe Accessories Pvt. Ltd., Vellore, Tamil Nadu, India
Introduction: This study compares traditional and advanced shoe last manufacturing processes, emphasizing the integration of 3D scanning and the SDF (Sistema Definizione Forma) system to improve efficiency and precision.
Methods: In the traditional method, physical models are manually sculpted and digitized using mechanical digitizers. These are then machined via CNC systems, requiring manual finishing—particularly in toe and heel areas—due to clamping limitations. Branding is completed using conventional heat embossing tools. In contrast, the advanced method employs digital modeling tools (e.g., Rhino software) to directly create shoe last designs. These digital files are processed in SDF-enabled CNC machines, utilizing a dovetail gripping mechanism that allows full-surface precision turning and eliminates the need for manual finishing. Logos and markings are applied using laser printing.
Results: The SDF-based approach demonstrated over 70% improvement in production speed, an 80% reduction in manual intervention, and sub-millimetric dimensional accuracy. Surface finish, repeatability, and suitability for mass customization were also significantly enhanced.
Discussion: Findings support that the SDF-based method enables a more sustainable, scalable, and higher-quality production process compared to traditional methods, offering clear advantages for modern footwear manufacturing.
Highlight
• Introduces a comparative study between traditional and SDF-based shoe last manufacturing.
• Explains the SDF (Sistema Definizione Forma) system and its patented dovetail clamping mechanism.
• Demonstrates how SDF technology reduces manual intervention by 80% and improves production speed by over 70%.
• Shows sub-millimetric accuracy and deformation-free machining using 9-axis interpolated CNC systems.
• Presents a real-world case study from Sanghavi Shoe Accessories Pvt. Ltd. validating the efficiency and economic feasibility of SDF integration.
• Highlights sustainability benefits through reduced material waste, energy consumption, and operator dependency.
1 Introduction
Shoe lasts serve as the foundational components in footwear design and manufacturing, directly impacting the fit, comfort, and performance of the final product (International Organization for Standardization (ISO), 2018).
Figure 1 shows the difference between a handcrafted wooden shoe last and a digital 3D model. The traditional last reflects manual craftsmanship, while the digital model highlights the precision and efficiency of modern CAD-based workflows.
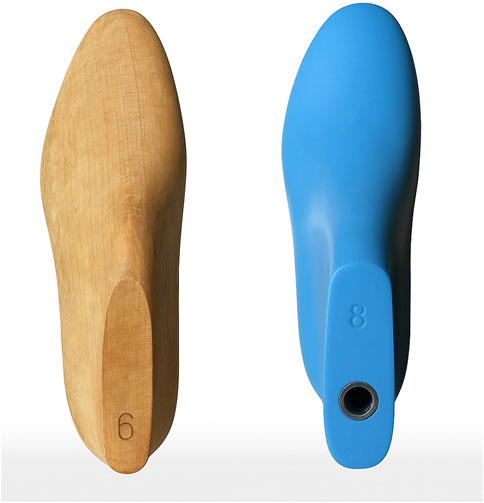
Figure 1. Comparison between a traditional wooden shoe last (left) and a digital 3D model (right) used in advanced CAD workflows.
Traditionally, the creation of shoe lasts has been rooted in manual craftsmanship or semi-mechanical methods, involving rough lathe turning, manual shaping with rasps and gauges, and refinement guided by physical templates or legacy models. While these approaches carry a legacy of artisanal expertise and offer creative flexibility, they are increasingly misaligned with the modern demands of precision, scalability, and production efficiency (Luximon, 2016).
Key limitations of traditional last making include dimensional inconsistencies between pairs, dependence on skilled labor, extended cycle times, and the risk of deformation particularly in critical zones such as the toe and heel due to mechanical pressure exerted by tailstock clamping in CNC operations. These challenges have driven the industry toward the adoption of advanced digital solutions.
Recent advances in computer-aided design (CAD), 3D scanning, and Computer Numerical Control (CNC) machining have transformed the capabilities of custom footwear production (Liu et al., 2020). The integration of smart manufacturing principles enabling greater accuracy, reduced labor, and shorter lead times, while predictive modeling using artificial intelligence is emerging as a new frontier in footwear customization (Kim et al., 2023).
One of the most transformative innovations in this space is the SDF (Sistema Definizione Forma) system, an advanced Italian-engineered technology that redefines the standards for last production. Central to the SDF system is a patented dovetail-style gripping mechanism positioned along the crest of the last. This unique configuration eliminates the need for traditional end-point clamping, thereby removing the potential for material distortion or geometric inaccuracies in sensitive areas. As a result, the entire surface of the last including complex and previously inaccessible regions like the tip and heel can be machined in a single, uninterrupted CNC cycle (Rossi et al., 2021; Luximon, 2016).
Powered by a 9-axis interpolating CNC platform, the SDF system enables multidirectional, high-speed milling with outstanding accuracy and surface finish. Systems such as the SDF4 can manufacture two pairs of lasts within a 7–8-min cycle, while the SDF6 extends this capability to three pairs per cycle. Minimal operator involvement further enhances repeatability and productivity.
This paper provides a structured comparative analysis between traditional and SDF-based shoe last manufacturing workflows. It evaluates key parameters including production efficiency, dimensional accuracy, machining cycle time, labor dependency, deformation risk, material utilization, and overall cost-effectiveness. The study combines theoretical evaluation with real-world case studies to assess the technical advantages and economic feasibility of integrating SDF technology within modern footwear manufacturing environments.
2 Methodology
This research adopts a case study–based approach to compare traditional and SDF-based shoe last manufacturing processes. The methodology involves detailed time studies to evaluate production efficiency across both workflows, supported by dimensional inspections to assess accuracy and repeatability of the manufactured lasts. Observations were conducted during critical stages including machining, clamping, and finishing to capture qualitative differences in process execution and operator involvement. Additionally, the study includes a comprehensive analysis of cost, cycle time, and material waste to evaluate the economic and operational advantages of the SDF system in a real-world production environment (Liu et al., 2020; Milani et al., 2009).
2.1 Traditional shoe last making
In the traditional method of shoe last manufacturing, the process begins with the creation of a model or prototype by the designer, based on various customer inputs such as brand design standards, fit specifications, and style requirements (Luximon, 2016). This initial modeling phase is time-intensive and typically takes between 3 and 4 h. Once the physical model is finalized, it is digitized using a mechanical digitizer, typically taking 20–30 min. The resulting file is then transferred to a CNC machine for machining operations. Rough turning is carried out first, usually taking around 3–4 min per pair, shaping the general form of the last from wooden or plastic blocks. Following this, the fine turning is performed in the CNC machine, which takes about 7–8 min to finish either two or three pairs, depending on the machine type and capacity. However, CNC machining in this method relies on tailstock-based clamping, which can introduce deformation particularly at critical zones like the toe and heel due to pressure exerted at both ends (Klocke, 2011).
Figure 2 illustrates the traditional tailstock-based clamping method used in CNC machining. This approach holds the shoe last at both ends, which often causes deformation in critical areas like the toe and heel due to clamping pressure.
As a result, manual finishing becomes necessary. The toe is hand-shaped and aligned with a physical template, typically requiring 5–10 min per pair. A similar process is repeated for the heel, also taking 5–10 min per pair. Once the last is geometrically complete, reference markings are added manually through heat stamping, a process that takes around 2 min per pair. The entire workflow concludes with a final round of visual inspection and quality control. Although rooted in skilled craftsmanship, this traditional method is labor-intensive and time-consuming, with numerous manual steps that can affect dimensional consistency, productivity, and repeatability (Stavropoulos, Giannoulis, Papacharalampopoulos, Foteinopoulos and Chryssolouris, 2016).
2.2 Traditional shoe last manufacturing workflow
Figure 3 illustrates the step-by-step process of model/prototype development based on customer requirements, detailing the duration and sequence of each activity. The procedure commences with the creation of the model or prototype, a 3–4 hour endeavor that transforms design input into a preliminary physical form. This is followed by digitization using a mechanical digitizer, taking approximately 20–30 minutes to capture the essential contours. Subsequent operations such as rough turning, toe and heel hand-shaping, reference marking, and final inspection ensure structural integrity, precision, and aesthetic finish, culminating in a visually verified and quality-assured product.
2.3 Advanced shoe lasts making using SDF technologies
In the advanced method of shoe last making using SDF (Sistema Definizione Forma) technology, the process is streamlined through digital modeling, precision CNC machining, and an innovative deformation-free clamping mechanism. The workflow begins with the creation of a digital last model by the designer using CAD software such as Rhino (Liu and Zhang, 2022), based on customer-provided specifications, previous physical lasts, or brand-specific design inputs. This digital modeling phase typically takes around 30 min to 1 h, depending on complexity, and accounts for approximately 99% of the design work.
Once the digital design is complete, the model is transferred to the SDF CNC system, where rough turning is performed within 3–4 min per pair. The SDF employs a patented dovetail gripping mechanism along the crest of the last, eliminating the need for tailstock-based clamping and enabling precise, deformation-free machining—even in critical areas like the toe and heel.
After machining, the physical last is fine-tuned and manually cross-verified against the original design inputs to ensure fidelity. Only then is the final physical last scanned using a 3D scanner, generating a high-accuracy digital version for documentation, archiving, or future reuse.
Figure 4 depicts the SDF clamping system, which uses a dovetail mechanism along the crest of the last. This innovative setup provides full surface access during CNC machining and eliminates deformation by avoiding end-point pressure.
The fine turning cycle is impressively efficient, taking only 7–8 min to finish two pairs in SDF4 or three pairs in SDF6. Once the machining is complete, the dovetail clamping sections are removed a quick process of about 1 min per pair. Instead of manual heat embossing, laser stamping is used for printing all reference markings, which takes approximately 1 min per pair and delivers a clean, modern finish. The process concludes with a final round of quality control. Thanks to 9-axis interpolated CNC machining (Monno et al., 2014; Torres et al., 2020), the SDF system offers sub-millimetric precision, consistent output quality, and significantly reduced manual intervention. Operators benefit from faster training cycles, reduced dependency on hand-finishing skills, and minimized rejection rates due to automated error detection and correction mechanisms. This makes the SDF-based method highly suited for modern, scalable, and quality-focused footwear production environments.
3 Comparative analysis
A detailed comparison between traditional and SDF-based shoe last manufacturing methods was conducted across key performance parameters including cycle time, manual intervention, accuracy, finish quality and scalability.
3.1 Production time and efficiency
The traditional method involves a total cycle time of 45–60 min per pair, including manual finishing and stamping. In contrast, the SDF system completes the entire process in 12–14 min per pair, representing a 70%–75% improvement in production speed. This drastic reduction enables higher throughput and more responsive manufacturing.
3.2 Manual intervention
Traditional workflows require substantial manual labor especially for toe and heel corrections resulting in variability and dependency on operator skill. The SDF system, with its 9-axis interpolated CNC machining and dovetail clamping, eliminates nearly all manual finishing, and reducing labor dependency by over 80%.
3.3 Dimensional accuracy and repeatability
The traditional approach often introduces geometric inconsistencies due to tailstock clamping, especially in sensitive areas like the toe and heel. The SDF method consistently achieves sub-millimetric tolerances (<0.5 mm) across all pairs, resulting in highly repeatable outputs even in large-scale production.
3.4 Surface quality and finish
Manual shaping in the traditional process results in variable surface finishes. The SDF system, through uninterrupted CNC cycles, delivers a uniform and premium-quality finish without requiring any post-processing.
3.5 Technology integration and scalability
The traditional process relies heavily on manual tools and semi-automated machinery, limiting scalability. In contrast, the SDF workflow is a fully digital pipeline (CAD–CNC–Laser), enabling faster operator training, mass customization, and seamless production scaling.
3.6 Sustainability
Reduced rework and minimal waste in the SDF workflow contribute to improved material efficiency and lower energy consumption. Laser stamping also reduces emissions compared to traditional heat embossing.
Table1 The comparative analysis highlights key differences between traditional and SDF-based shoe last manufacturing methods. It outlines variations in modeling time, digitization, machining processes, manual intervention, cycle time, dimensional accuracy, and scalability emphasizing the superior efficiency, precision, and automation of the SDF workflow.
4 Practical case study
At Sanghavi Shoe Accessories Pvt. Ltd., the implementation of the SDF CNC system has significantly transformed the shoe last manufacturing process. Prior to adoption, the traditional workflow involved manual model making, digitization, tailstock-based CNC turning, and hand-finishing of critical areas like the toe and heel. This process averaged 45–60 min per pair and often required skilled labor for corrections and rework due to deformation from mechanical clamping, especially at sensitive points.
With the integration of SDF4 and SDF6 machines, the company streamlined its production by shifting to a fully digital workflow. Now, last models are created in Rhino CAD, scanned using a 3D scanner, and directly sent to CNC. The patented dovetail gripping system in the SDF eliminates the need for tailstocks, enabling deformation-free machining and full surface access.
As a result, the total production time per last has been reduced to under 10 min, with rough turning (3–4 min), final finishing (7–8 min for 2–3 pairs), dovetail clamp removal (1 min/pair), and laser reference printing (1 min/pair). The need for manual finishing has been almost eliminated, while dimensional rejection rates have dropped below 1%. Additionally, the repeatability and accuracy of SDF machines have enabled consistent production quality even in bulk manufacturing, reducing operator fatigue and training time.
This case highlights the technical and economic advantages of transitioning from traditional craftsmanship to advanced, digitally integrated systems like SDF in modern footwear manufacturing (Sanghavi Shoe Accessories Pvt. Ltd, 2021).
5 Economic feasibility and return on investment
The initial capital investment for implementing SDF CNC systems such as the SDF4 or SDF6 typically ranges between ₹2 to ₹3 crores (approximately USD 240,000 to USD 360,000), inclusive of the machines, compatible 3D scanning systems, CAM software, and setup infrastructure. While this cost is significant, it is justified by the drastic improvements in efficiency, precision, and labor optimization (NEWLAST, 2011). With cycle times reduced from 45 to 60 min per pair (traditional method) to under 12 min using SDF, production capacity increases by more than 4–5 times. Moreover, the reliance on skilled labor for manual finishing is reduced by up to 70%, cutting ongoing operational expenses. The precision of the SDF system also reduces rejection rates and minimizes raw material waste, resulting in further savings.
Based on real-world data, manufacturers typically achieve a full return on investment within 30–36 months. These ROI estimates and associate cost savings align with the findings of (Larreina et al., 2013) who explore smart manufacturing execution systems (SMES) and their role in evaluating sustainability within production environments, and (Baid, 2022), who assessed the valuation strategies in mass shoe last companies. Furthermore, the studies by (Panagiotopoulou and Stavropoulos, 2023) on sustainability indexing, on life cycle analysis methodologies, and (Porevopoulos et al., 2024) on techno-economic evaluation and decision support for sustainable repair processes using DED AM, support the economic and environmental advantages observed in digitally integrated manufacturing processes such as SDF.
Over a 5- to 7-year period, the cumulative savings in labor, waste reduction, increased output, and lower rework costs can amount to 40%–50% compared to traditional workflows. This positions SDF technology not only as a modern manufacturing solution but also as a financially strategic upgrade for forward-thinking footwear companies (Monno et al., 2014; Torres et al., 2020).
Table 2 illustrates the cumulative production cost and return on investment over a 5-year period for both traditional and SDF-based manufacturing. The graph demonstrates that while SDF requires a higher initial investment, it achieves breakeven within 30–36 months and leads to significantly lower long-term costs due to faster cycles, reduced labor, and minimal rework.
6 Sustainability and waste reduction
In contrast, the SDF-based workflow leverages precise digital modeling and 9-axis interpolated CNC machining, which significantly reduces the need for rework and material wastage. The patented dovetail clamping mechanism allows uniform machining across the entire surface of the last without the risk of deformation, ensuring that each piece meets exact specifications from the first attempt. This precision translates to reduced consumption of raw materials and fewer rejected units (NEWLAST, 2011).
Moreover, the integration of 3D scanning and CAD systems promotes the reuse and modification of digital last designs without the need to create new physical models for every style variation. This capability supports mass customization while minimizing physical inventory and tooling waste. By eliminating multiple manual steps and optimizing tool paths through CAM software, energy usage is also minimized, leading to a lower carbon footprint per unit produced.
SDF systems are built with energy-efficient servo motors and smart control systems that reduce idle time and optimize machining cycles. Furthermore, laser marking, replacing heat embossing, consumes less energy and avoids the emissions associated with heated branding tools. These innovations collectively contribute to a leaner, greener production line aligned with global sustainability goals in footwear manufacturing (Nguyen et al., 2021; Kim et al., 2023; ASTM F2913-11, 2025; Reilly and Dhingra, 2020; Ritchie et al., 2022).
7 Conclusion
This comparative study demonstrates the transformative potential of integrating advanced technologies like 3D scanning, digital modeling, and the SDF (Sistema Definizione Forma) manufacturing system into the shoe last production process. While traditional methods reflect a legacy of artisanal craftsmanship, they no longer align with the increasing demands for speed, consistency, and customization in today’s global footwear market.
The SDF-based approach significantly outperforms traditional methods in every critical area dimensional accuracy, cycle time, repeatability, surface finish, and sustainability. Its dovetail clamping system, combined with 9-axis CNC machining and a fully digital workflow, allows manufacturers to achieve unmatched precision with minimal manual intervention and waste.
In an era where consumer expectations are shifting toward faster delivery, personalized fit, and eco-conscious products, adopting SDF technology is not just an operational improvement, it’s a strategic imperative. The digital transformation of shoe last manufacturing offers a competitive edge that is becoming essential rather than optional.
Footwear manufacturers, especially those aiming for scale and quality, must act now to future-proof their production lines. Investing in SDF systems today ensures enhanced productivity, reduced operational costs, and readiness for mass customization tomorrow. For stakeholders committed to innovation, precision, and sustainability, transitioning from legacy methods to advanced SDF-based workflows is not just timely, it’s essential.
8 Future scope
The evolution of shoe last manufacturing through technologies like SDF is only the beginning. Looking ahead, several promising developments can further elevate the efficiency, customization, and sustainability of the process:
• AI-Driven Size Prediction and Customization: Integration with artificial intelligence and machine learning can enable predictive size modeling based on foot scans and customer data, allowing for hyper-personalized last designs and reducing the need for trial fittings (Kim et al., 2023; Nguyen et al., 2021).
• Closed-Loop Digital Workflow: A fully closed-loop system—where foot data is scanned, modeled in CAD, manufactured via CNC, and validated through 3D scanning—can create a seamless and highly accurate design-to-production pipeline with real-time feedback and corrections.
• Use of Sustainable and Smart Materials: Experimentation with advanced bioplastics and recyclable composite blocks will support eco-friendly manufacturing. These materials can reduce the environmental footprint of last production while maintaining the required mechanical properties.
• Cloud-Based Last Libraries and Remote Collaboration: Cloud storage and digital libraries of standardized or custom last designs can enable remote sharing, quick access for global factories, and collaborative updates across different production locations.
These future advancements have the potential to further digitize and decentralize last manufacturing, enabling faster global production, reduced waste, and highly adaptive systems that align with the next-generation of smart, sustainable footwear production (Liu et al., 2020).
Data availability statement
The original contributions presented in the study are included in the article/supplementary material, further inquiries can be directed to the corresponding author.
Author contributions
GS: Validation, Writing – review and editing. AP: Formal Analysis, Resources, Writing – review and editing. BS Conceptualization, Resources, Writing – original draft, Writing – review and editing.
Funding
The author(s) declare that no financial support was received for the research and/or publication of this article.
Acknowledgments
I am thankful to Vellore Institute of Technology (VIT) for their support and guidance.
Conflict of interest
Author BS was employed by Sanghavi Shoe Accessories Pvt. Ltd.
The remaining authors declare that the research was conducted in the absence of any commercial or financial relationships that could be construed as a potential conflict of interest.
Generative AI statement
The author(s) declare that no Generative AI was used in the creation of this manuscript.
Publisher’s note
All claims expressed in this article are solely those of the authors and do not necessarily represent those of their affiliated organizations, or those of the publisher, the editors and the reviewers. Any product that may be evaluated in this article, or claim that may be made by its manufacturer, is not guaranteed or endorsed by the publisher.
References
ASTM F2913-11 (2025). Standard test method for measuring the coefficient of friction for evaluation of slip performance of footwear and test surfaces.
Baid, D. (2022). “Valuation of mass shoe last company limited,” in Managing disruptions in business: causes, conflicts, and control, rajagopal. Editor R. Behl (Cham: Springer International Publishing), 393–409. doi:10.1007/978-3-030-79709-6_20
International Organization for Standardization (ISO). (2018). Footwear — lasts — vocabulary and terminology (ISO 20882:2018). Geneva, Switzerland: ISO.
Kim, H., Park, J., Lee, S., Chen, Y., Kumar, A., Wang, T., et al. (2023). AI-powered customization in footwear: predictive fit modeling using foot scans. J. Intelligent Manuf. 34 (6), 1334–1347.
Larreina, J., Gontarz, A., Giannoulis, C., Nguyen, V. K., Stavropoulos, P., and Sinceri, B. (2013). 15.3 Smart Manufacturing Execution System (SMES): the possibilities of evaluating the sustainability of a production process.
Liu, J., and Zhang, X. (2022). Rhino-based digital design of ergonomic shoe lasts. Int. J. Industrial Des. 8 (2), 89–97.
Liu, Y., Zhang, M., Chen, L., Wang, Z., Patel, S., Huang, F., et al. (2020). Integration of CAD/CAM in custom footwear manufacturing. Computer-Aided Des. Appl. 17 (4), 755–763.
Milani, T. L., Braun, T., Krueger, B., Smith, J., Lopez, R., Tanaka, M., et al. (2009). 3D scanning for customized footwear manufacturing. J. Footwear Sci. 1 (1), 15–25.
Monno, M., Ferraris, E., Rossi, A., Caruso, G., Lee, D., Tiwari, S., et al. (2014). Multi-axis CNC machining for complex surface finishing. J. Manuf. Syst. 33 (4), 610–620.
Nguyen, T., Tran, P., Le, Q., Choi, S., Wang, M., Hernandez, L., et al. (2021). Towards smart factories: a review on AI integration in shoe manufacturing. Smart Manuf. Rev. 2 (1), 45–59.
Panagiotopoulou, V. C., and Stavropoulos, P. (2023). “On the sustainability indexing of carbon footprint reduction approaches for manufacturing industry,” in Production processes and product evolution in the age of disruption. Editors F. G. Galizia,, and M. Bortolini (Cham: Springer International Publishing), 404–412. doi:10.1007/978-3-031-34821-1_44
Porevopoulos, N., Tzimanis, K., Souflas, T., Bikas, H., Panagiotopoulou, V. C., and Stavropoulos, P. (2024). Decision support for repair with DED AM processes based on sustainability and techno-economical evaluation. Procedia CIRP 130, 9–14. doi:10.1016/j.procir.2024.10.048
Reilly, K., and Dhingra, R. (2020). Material innovation in sustainable footwear. J. Clean. Prod. 274, 123010. doi:10.1016/j.jclepro.2020.123010
Ritchie, J., Kumar, N., Zhao, Y., Sanders, E., Thomason, L., Gupta, R., et al. (2022). Green manufacturing in the footwear industry: an emerging paradigm. Sustain. Mater. Technol. 32, e00345.
Rossi, A., De Luca, P., Bianchi, M., Tan, K., Patel, R., Yamamoto, K., et al. (2021). Innovations in last manufacturing. Italian footwear journal.
Sanghavi Shoe Accessories Pvt. Ltd (2021). Adoption of SDF CNC systems for last production. Vellore, Tamil Nadu, India Internal Technical Report.
Stavropoulos, P., Giannoulis, C., Papacharalampopoulos, A., Foteinopoulos, P., and Chryssolouris, G. (2016). Life cycle analysis: comparison between different methods and optimization challenges. Procedia CIRP 41, 626–631. doi:10.1016/j.procir.2015.12.048
Keywords: shoe last making, 3D scanning, cnc machining, SDF technology, sistema definizione forma
Citation: Surya G, P. A and Suresh B (2025) A digitizing craftsmanship: a comparative study of traditional vs. SDF-based shoe last making using 3D scanning and computer numerical control technologies. Front. Mech. Eng. 11:1610798. doi: 10.3389/fmech.2025.1610798
Received: 13 April 2025; Accepted: 10 June 2025;
Published: 24 June 2025.
Edited by:
Kanak Kalita, Vel Tech Dr. RR and Dr. SR Technical University, IndiaReviewed by:
Mingzhi Wang, Harbin Institute of Technology, ChinaPanagiotis Stavropoulos, University of Patras, Greece
Copyright © 2025 Surya, P. and Suresh. This is an open-access article distributed under the terms of the Creative Commons Attribution License (CC BY). The use, distribution or reproduction in other forums is permitted, provided the original author(s) and the copyright owner(s) are credited and that the original publication in this journal is cited, in accordance with accepted academic practice. No use, distribution or reproduction is permitted which does not comply with these terms.
*Correspondence: Anbarasan P., YW5iYXJhc2FuLnBAdml0LmFjLmlu