- 1Department of Civil and Environmental Technology, Faculty of Technology, University of Sri Jayewardenepura, Nugegoda, Sri Lanka
- 2Department of Process, Energy and Environmental Technology, Faculty of Technology, Natural Sciences and Maritime Sciences, University of South-Eastern Norway, Porsgrunn, Norway
Massively using conventional plastics has led to significant environmental issues, including harm to ecosystems, wildlife, and human health, contributions to greenhouse gas emissions, and resource depletion through their extraction and production. Thus, there is an urgent imperative to seek sustainable alternatives like bio-composites. This research established the viability of banana peels and cassava starch for eco-friendly bio-composite sheets, offering insights into their properties and performance The bio-composite materials, composed of banana peels, cassava starch, banana stem fiber, glycerol, and acetic acid, were prepared in different weight-based proportions. The preparation process involved cleaning, drying, blending, and molding the materials to produce consistent bio-composite samples. The properties and performance of the composite samples were assessed for water absorption, moisture content, and tensile strength. Notably, the combination of banana peels and cassava in a 1:2 ratio, along with banana stem fiber, demonstrated favorable attributes, including reduced water absorption (ranging from 6.42 to 30.91%), desirable moisture content (ranging from 8.06 to 11.27%), and increased tensile strength (ranging from 5.345 to 11.892 MPa). These findings confirm the viability of using banana peels and cassava starch in producing bio-composite sheets, offering a sustainable alternative to conventional plastics. This study contributes to the field of sustainable materials by providing insights into the properties and performance of bio-composites, thereby supporting the development of eco-friendly bio-composite sheets.
1 Introduction
Plastics are adaptable materials that can be shaped into many different shapes and forms, making them widely employed in a variety of industries, including packaging, construction, automotive, electronics, and healthcare. In 2022, the total amount of plastic produced globally was an astounding 400.3 million metric tons. Asia is the world’s top manufacturer of plastics. In 2022, China alone accounted for 32% of global manufacturing. China has manufactured 6 to 12 million metric tons of plastic items per month in the past few years. With a projected 17 percent of global plastic manufacturing in 2022, North America comes in second place (Pilapitiya and Ratnayake, 2024). According to projections, if business as usual continues, global plastic pollution will exceed 66.1 MT/y by 2050. The imbalance between the amount of plastic used and the ability to manage the plastic at the end of its life will result in roughly 70 million tons of plastic ending up in the environment by 2024 (Yan et al., 2024).
“Polymeric material that may contain other substances to improve performance and/or reduce costs” is what the International Union of Pure and Applied Chemistry defines as plastic (Pilapitiya and Ratnayake, 2024). The word “plastic” originally meant “pliable and easily shaped.” It was only recently given a name for a class of materials known as polymers. The word “polymer” means “of many parts,” and molecules are arranged in long chains to form polymers. In nature, polymers are everywhere. A particularly prevalent natural polymer is cellulose, which is the substance that builds up plant cell walls. Plastics are any of a wide range of complex organic compounds created by polymerization that can be moulded, extruded, cast into different shapes and films, or pulled into filaments and used as textile fibres (Meena et al., 2020).
Plastic pollution is a global issue. An estimated 19–23 million tonnes of plastic waste spill into lakes, rivers, and oceans annually, contaminating aquatic ecosystems. The presence of plastic pollution can modify environments and disrupt natural processes, diminishing the capacity of ecosystems to cope with climate change. This, in turn, has a direct impact on the livelihoods, food production capacities, and overall social well-being of millions of people (Dave and Macwan, 2024). Also, microplastic pollution has spread to every edge of the aquatic ecosystem, from the seafloor sedimentary rocks to the top-ranked pelagic layer, due to the misuse, mishandling, and abuse of plastics. Fish species have easy access to microplastics since they are prevalent in aquatic environments (Bhuyan, 2022). The repercussions of plastic pollution on our ecosystem include groundwater pollution, disruption of the food chain, animal deaths, land pollution, toxic potential, air pollution, and expensiveness (Obebe and Adamu, 2020).
Bio-composites are thought to be the most effective substitute materials for dealing with these issues while also ensuring a sustainable and environmentally friendly environment (Trivedi et al., 2023). On the other hand, bio-composite materials made of renewable resources, such as plant fibers, are gradually replacing traditional synthetic and non-biodegradable materials, enabling a reduction in greenhouse gas emissions in particular (Rahman et al., 2023). Bio-composites are composites that are created with biomaterials. In general, bio-composites are composites made of biopolymers and natural fibers reinforced with reinforcement (Mahmud et al., 2023). Reinforcing materials, which can be synthetic or natural fibers, are added to a matrix material (such as resins or biopolymers) to form bio-composites. Fiber-reinforced polymer composite materials with bio-based fibers and/or bio-based matrix are referred to as “bio-composite” (Elnashar and Karakuş, 2023). The potential of these materials to replace traditional materials that are non-renewable, recalcitrant, or produced through techniques that release pollutants is being thoroughly investigated (Mahmud et al., 2023).
Despite the growing interest in bio-composites, there is a significant gap in the literature concerning the use of locally available biowaste materials, such as banana peels and cassava starch, in developing eco-friendly bio-composites. This article introduces a novel approach to bio-composite production by leveraging widely available biowaste materials in Sri Lanka. The innovative aspect lies in the specific combination of banana peels and cassava starch, supplemented with banana stem fiber, glycerol, and acetic acid, to enhance the mechanical and physical properties of the composite. The study not only addresses the environmental issues associated with plastic waste but also contributes to waste management by repurposing agricultural residues into valuable materials.
The blending of banana peels, cassava starch, and banana stem fibre in this research stems from the aim to harness the unique properties of each component for the development of bio-composite materials. Banana peels contribute starch to bio-composite, while cassava starch acts as a binder, promoting cohesion. The incorporation of banana stem fibre introduces additional reinforcement, augmenting tensile strength. Glycerol is used as a plasticizer. Plasticizers enable increased compound processing characteristics, while the end-use product also provides adaptability. It has no odour and is colourless. Acetic acid is used as a preservative. It helps the molecules in starch stay disrupted even after heating. It also acts to dissolve the starch. This synergistic blending seeks to capitalize on the diverse attributes of these natural materials, aiming for a well-balanced composition that not only minimizes environmental impact but also offers enhanced mechanical and biodegradable characteristics. The rationale behind this blending strategy lies in the potential to create bio-composites with overall performance by combining the strength of banana stem fibre with the cohesive and sustainable qualities of banana peels and cassava starch.
The primary objectives of this research are twofold: to produce bio-composite sheets using banana peels, cassava starch, and banana stem fibers, and to reduce the environmental impacts of conventional plastic products by replacing them with eco-friendly alternatives. By leveraging the unique properties of these natural materials, this study aims to develop bio-composites that not only exhibit enhanced mechanical strength and biodegradability but also contribute to mitigating plastic pollution. The research endeavors to optimize the composition of these bio-composites to achieve a balance between performance and sustainability. Ultimately, this work seeks to provide a viable solution for reducing plastic waste, promoting environmental sustainability, and advancing the development of green materials.
2 Materials and methods
The primary materials used in this study were banana peels and cassava starch, both sourced locally from Sri Lanka. Additionally, banana stem fiber was incorporated to enhance the mechanical properties of the composites. Glycerol and acetic acid were used as plasticizers and binding agents, respectively.
2.1 Material extraction processes
2.1.1 Banana peel preparation process
The banana peels were collected and thoroughly washed to remove any dirt or contaminants. Then carefully cut into small, manageable pieces. These pieces were placed in a container with distilled water and brought to a boil, maintaining the boil for approximately 30 min to soften the peels and facilitate further processing. After boiling, the water was separated from the banana peels, ensuring that the water part was removed (Rusdi et al., 2020; Azieyanti et al., 2020). Distilled water was added to the banana peels, and a blender was used to thoroughly blend them until a consistent paste-like texture was achieved. Once blended, the excess water was removed from the peel paste by draining or squeezing. The peel paste was then placed under sunlight to undergo the drying process, ensuring that it was completely dried. After sun drying, the prepared banana peels were obtained and were ready for further use.
2.1.2 Preparation of cassava starch
Fresh cassava was collected, and the peels were carefully removed, ensuring that only the starchy part was retained. The cassava was then cut into small slices or thin pieces for better drying and processing. The cassava slices were allowed to dry naturally under the sun until they were completely dry. Once dried, a blender was used to grind the cassava slices until a fine powder or small particle size was obtained. The ground cassava starch was then sieved to ensure uniform particle size, removing any larger particles that could affect the consistency of the bio-composite.
2.1.3 Preparation of banana stem fibre
Fresh banana stems were obtained, and then the outer layers of the stem were carefully peeled away to expose the inner fibres. Using a knife, the fibres were separated from the core, ensuring their integrity and cleanliness. The separated fibres were thoroughly rinsed under cold water to eliminate any dirt or impurities. After rinsing, the fibres were left to air dry naturally in a well-ventilated area until they achieved complete dryness. Once dried, the fibres were gently untangled and refined to make them ready for use. To prepare the fibers for composite production, they were cut into short lengths. The prepared banana stem fiber was stored in a cool and dry location, such as an airtight container, for future utilization.
2.2 Bio-composite production process
Figure 1 depicts the steps in production process. The prepared and dried banana peel samples were blended until a homogeneous mixture was obtained. Gradually, the previously prepared and dried banana stem fibre was added to the blender, and the blending continued until the fibres were evenly distributed within the mixture. The cassava starch was introduced into the blender and thoroughly mixed with the banana peel and fibre mixture, ensuring a well-incorporated and consistent composition. Glycerol was added to the mixture as a plasticizer, enhancing the flexibility and durability of the bio-composite material. Finally, acetic acid was introduced as a cross-linking agent, enhancing the overall strength and stability of the bio-composite. The entire mixture was blended again, ensuring all the components were well combined to form a uniform blend (Amin et al., 2019; Sultan and Johari, 2017; Azieyanti et al., 2020). The blended mixture was then transferred to a mould that matched the desired shape and size of the bio-composite product. The mould was placed into a heat press machine, and the temperature was set to 180°C. The material was allowed to undergo pressing for approximately 10 min, facilitating the fusion, and shaping of the bio-composite. Once the pressing was complete, the mold was carefully removed from the heat press, and the bio-composite was left to cool and solidify. For improved results, the sample was transferred to an oven set at 110°C for approximately 15 min to further enhance the drying process. After the cooling and drying processes, the final bio-composite sheet was obtained, ready for further testing and application.
Table 1 depicts the experimental set up which was followed. In Trail 01, denoted by Samples 1.1, 1.2, and 1.3, the focus lies on altering the primary constituents of the bio-composite. Trail 02 introduces variations in acetic acid content, featuring Samples 2.1, 2.2, and 2.3. Trail 03, comprising Samples 3.1, 3.2, and 3.3, explores the impact of changing cassava starch percentages. Trail 04 investigates the influence of varying banana stem fibre proportions with Samples 4.1, 4.2, and 4.3.
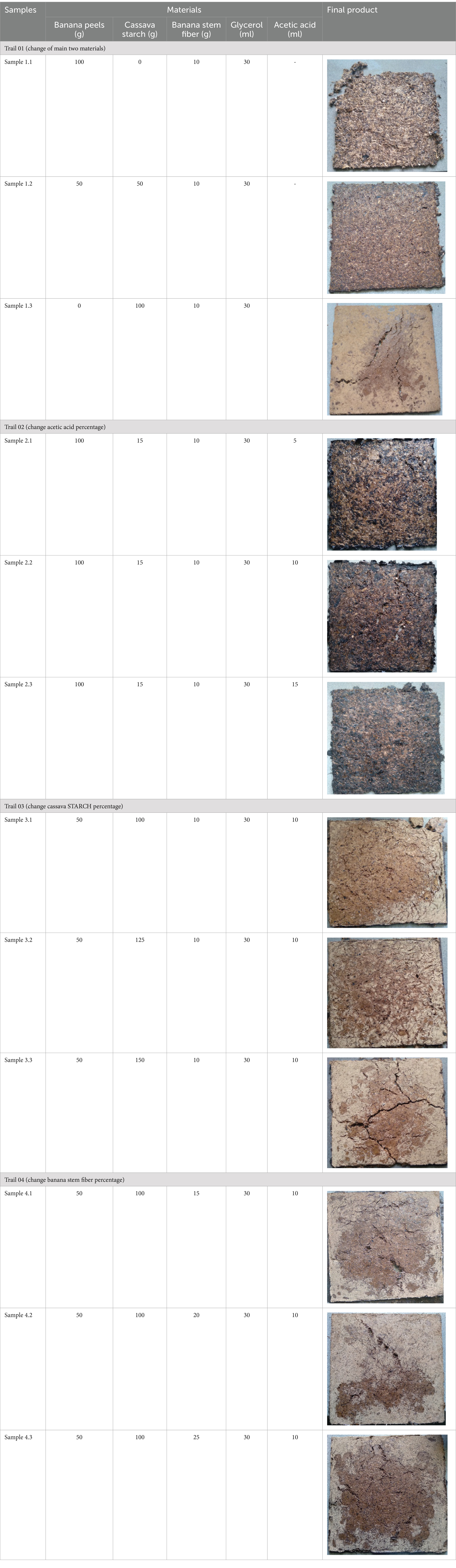
Table 1. Material compositions employed in the production of bio-composite samples and the final product obtained through four distinct trails.
2.3 Quality evaluation of bio-composite samples
2.3.1 Water absorption test
The water absorption test comprised the following steps: Initially, a 1 cm by 2 cm portion of the bio-composite sample was cut and weighed to establish its starting weight. Subsequently, a clean beaker was filled with 100 mL of room-temperature water, into which the sample was delicately immersed to ensure complete submersion. The sample was left to soak in the water for 24 h. Following this soaking period, the sample was extracted from the water, excess surface moisture was carefully removed, and its final weight was promptly measured (Sultan and Johari, 2017; Chapain et al., 2021). The water uptake was then computed using the formula:
2.3.2 Moisture content test
Each sample was obtained and cut into small pieces with a size of 1.5 cm2. The initial weight of each sample was recorded accurately. An oven was preheated to a temperature of 85°C. The sample pieces were placed in the oven and allowed to dry for 1 day. After 1 day, the samples were removed from the oven and the final weight of each sample was recorded accurately (Wahyuningtiyas and Suryanto, 2017; Vijayalaksmi et al., 2022). The moisture content of each sample was calculated using the following formula:
2.3.3 Biodegradability test
For the biodegradability test, a piece of bio-composite material was pre-weighed (Wi) and placed under a polybag set up containing soil. The sample was positioned at a depth of 5 cm from the surface of the soil. An appropriate amount of water was sprinkled on the soil to enhance microbial enzymatic activities. This step promoted the biodegradation process of the bio-composite material. The samples were maintained in the soil for approximately 15 days. At intervals of 4 days, get the sample and measure the weight. (Amin et al., 2019; Sultan and Johari, 2017; Wahyuningtiyas and Suryanto, 2017). The biodegradability of each sample was calculated using the following formula:
2.3.4 Tensile test
Initial sample preparation involved cutting appropriate specimens from bio-composite sheets, adhering to defined dimensions, and ensuring sample sufficiency. Subsequently, a universal testing machine, configured in compliance with ASTM D 638 guidelines and the manufacturer’s instructions, was set up for the evaluation. The testing machine was initiated, and tension was systematically applied to the samples at a predefined testing speed of 5 mm/min until a fracture occurred. Throughout the test, continuous recordings were made of the force applied (load) and deformation values. Finally, the tensile strength of the bio-composite samples was determined (Chapain et al., 2021; Babalola and Olorunnisola, 2019).
3 Results and discussion
3.1 Water absorption test
The water absorption test results, illustrated in the graph, provide a comprehensive understanding of the samples’ water uptake behavior (Figure 2).
Due to a crack in sample 1.1, it was not subjected to further testing. Sample 1.2 (Equal Parts Banana Peels and Cassava Starch) displays a moderate water absorption of 28.72%, suggesting that the combination of banana peels and cassava starch may contribute to a more balanced water absorption profile. This reduction could be attributed to a more optimized blend, where the proportion of hydrophilic components may have been minimized, resulting in a decreased affinity for water. Sample 1.3 (Cassava Starch Only) exhibits the second-highest water absorption at 34.85%, possibly indicating a higher affinity for water due to the lack of water-resistant components like banana stem fibre. When changing acetic acid (Samples 2.1 to 2.3), increasing the acetic acid content from 5 ml (Sample 2.1) to 10 ml (Sample 2.2) and 15 ml (Sample 2.3) appears to result in decreasing water absorption. This trend may be attributed to the acid’s role in promoting cross-linking and enhancing the material’s water resistance. Also, when changing cassava starch (Samples 3.1 to 3.3), increasing the cassava starch content from 100 g (Sample 3.1) to 125 g (Sample 3.2) and 150 g (Sample 3.3) shows a potential trend towards lower water absorption. This may indicate that a higher starch content contributes to improved water resistance. Changing Banana Stem Fiber (Samples 4.1 to 4.3): Increasing the banana stem fibre content from 15 g (Sample 4.1) to 20 g (Sample 4.2) and 25 g (Sample 4.3) suggests a positive correlation with increased water absorption. This may be due to the fiber’s ability to hold water, leading to higher absorption.
For low water absorption, Sample 1.2 (equal parts banana peels and cassava starch) and Sample 2.3 (with 15 ml acetic acid) show promising characteristics. Further optimization may involve adjusting the cassava starch content, with Sample 3.3 demonstrating a potential trend towards lower water absorption. It is crucial to balance the inclusion of banana stem fibre, as seen in Sample 4.1, to avoid excessive water absorption.
Contrasting with Rahmatiah Al Faruqy and Liew’s (2016) cassava-based sheets, which recorded a water absorption of 39.48%, the formulations in this study showcase a broader range of water absorption percentages. Additionally, Vijayalaksmi et al.’s (2022) formulation, which incorporated banana peel starch, corn starch, vinegar, glycerine, and distilled water, reported significantly higher water absorption percentages (215.35, 100.54, and 88.97%). Saputri et al. (2024) conducted research to produce sheets with cassava starch reinforced with banana bunch cellulose, resulting in water vapor absorption values ranging from 10.14 to 15.93%. Furthermore, Norafifah Izzati et al. (2024) conducted research with tapioca and banana peels, finding water absorption values ranging from 50 to 250%. This comparative analysis underscores the nuanced impact of the specific bio-composite composition presented in the current study on water absorption properties.
3.2 Moisture content test
Moisture content plays a crucial role in the physical and mechanical properties of bio-composites, as excessive moisture can lead to structural degradation, reduced strength, and compromised performance. The following result, Figure 3, provides the moisture content characteristics of each sample.
Sample 1.2 (11.6%) and Sample 1.3 (12.08%) both involve changes in the main material composition, with Sample 1.2 having an equal blend of banana peels and cassava starch, while Sample 1.3 consists entirely of cassava starch. The minimal difference in moisture content between these samples suggests that the proportion of banana peels in the blend may not significantly influence moisture absorption. The variation in acetic acid concentration in Samples 2.1 (13.24%), 2.2 (28.26%), and 2.3 (25.86%) shows an interesting trend. Sample 2.1, with the lowest acetic acid concentration, has the lowest moisture content, while Samples 2.2 and 2.3, with higher acetic acid concentrations, exhibit higher moisture content. This contradicts the water absorption results, suggesting that factors beyond acetic acid concentration may influence moisture content. The increase in cassava starch content from Samples 3.1 (8.06%) to 3.3 (4.55%) results in a decrease in moisture content. This suggests that higher cassava starch concentrations contribute to reduced moisture absorption, possibly due to the water-resistant nature of starch. Samples 4.1 (9.71%), 4.2 (9.81%), and 4.3 (11.27%) show slight variations in moisture content with changing banana stem fibre content. While the differences are marginal, the higher fibre content in Sample 4.3 may contribute to a slightly higher moisture content. Samples with lower moisture content, such as 3.3 (4.55%) and 3.2 (6.25%), could be considered for applications where minimal moisture absorption is desired.
Vijayalaksmi et al. (2022) formulated a bio-composite incorporating banana peel starch, corn starch, vinegar, glycerine, and distilled water, which exhibited moisture content percentages of 6.58, 33.73, and 12.81%, respectively. Comparing these values with the obtained results, it can be observed that the bio-composite samples show a similar trend in terms of moisture content. In another study, Wahyuningtiyas and Suryanto (2017) reported moisture content percentages of 44.44, 55.55, 66.66, and 88.88%, respectively. When comparing these values with the obtained results, it is evident that the bio-composite plate samples in this study exhibit significantly lower moisture content percentages.
3.3 Tensile strength test
The evaluation of tensile strength is a fundamental aspect of assessing the mechanical performance and suitability of bio-composite materials (Figure 4).
As the Samples 1.1 and 3.3 were cracked, tensile strengths were not measured for the test. Sample 1.2 (0.2143 MPa) and Sample 1.3 (0.621 MPa) involve changes in the main material composition. The considerable increase in tensile strength in Sample 1.3, where cassava starch replaces banana peels, suggests that cassava starch contributes to enhanced tensile strength. This may be attributed to the structural characteristics of starch that enhance material cohesion. The variation in acetic acid concentration in samples 2.1 (0.4787 MPa), 2.2 (0.278 MPa), and 2.3 (0.1125 MPa) reveals a decreasing trend in tensile strength with increasing acetic acid concentration. The higher acetic acid concentrations in Samples 2.1 and 2.2 may contribute to increased cross-linking, resulting in improved tensile strength. The increase in cassava starch content from Sample 3.1 (5.345 MPa) to 3.2 (3.899 MPa) leads to a decrease in tensile strength. This could indicate that an excessive amount of cassava starch may compromise the material’s tensile strength, highlighting the importance of an optimal starch ratio. Samples 4.1 (10.681 MPa), 4.2 (10.469 MPa), and 4.3 (11.892 MPa) show variations in tensile strength with changing banana stem fibre content. Sample 4.3, with the highest fibre content, demonstrates the highest tensile strength. This suggests that an increased amount of banana stem fibre may contribute positively to tensile strength.
Sample 4.3, with 11.892 MPa tensile strength, stands out as having the highest strength among the samples tested. This blend, incorporating higher levels of banana stem fibre, demonstrates promising mechanical performance.
Rahmatiah Al Faruqy and Liew (2016) reported a tensile strength of 4.5 MPa for cassava-based samples prepared with newspaper pulp. Chodijah et al. (2019) investigated banana peel-based samples and found tensile strengths ranging from 2.6286 to 10.5620 MPa. Similarly, Saputri et al. (2024) demonstrated that cassava starch reinforced with banana bunch cellulose had tensile strength values varying from 2.92 to 6.72 MPa. Additionally, Norafifah Izzati et al. (2024) conducted research with tapioca and banana peels, revealing tensile strengths between 4.49 and 14.35 MPa. In comparison, the current study’s results, particularly those of Samples 3.1, 4.1, 4.2, and 4.3, with tensile strengths of 5.345, 10.681, 10.469, and 11.892 MPa, respectively, demonstrate that our bio-composite formulations achieve good tensile strengths compared to those reported in the literature, thereby supporting the validity and effectiveness of our experimental results.
3.4 Bio-degradability test
Analysis of the biodegradability test results demonstrated a noticeable correlation between increased microbial activity and the degradation of the bio-composite samples, highlighting the role of natural processes in breaking down the material. Below, Table 2 shows the result that was obtained from the test.
Table 2 displays the results of the biodegradability test conducted under aerobic conditions. The polybag setup, with its open top, maintained moisture levels while allowing air exchange, thus facilitating aerobic microbial processes. Under these conditions, the photos show how the bio-composite samples deteriorate over time (Table 3).
The biodegradability test results for the bio-composite samples reveal intriguing variations in the degradation rates, reflecting the impact of different formulations on the materials’ susceptibility to microbial activity. Sample 4.1 stands out with an exceptional increase from 31.28 to 97.55% within the first 8 days, indicating a highly favourable biodegradation response. Similarly, Samples 3.1, 4.2, and 4.3 demonstrate significant improvements over successive intervals, highlighting the overall biodegradable nature of our bio-composite formulations. These outcomes suggest that the integration of banana peels, cassava starch, and banana stem fibre in our bio-composite materials fosters favourable conditions for accelerated biodegradation.
While certain blends exhibit promising biodegradability, it is crucial to exercise caution when drawing definitive conclusions. The study provides valuable insights into short-term behaviour, but a comprehensive understanding of long-term environmental impact requires extended investigations. Additionally, considering potential byproducts and variations in soil conditions is essential for a more nuanced assessment. The encouraging trends observed hint at the potential of the current formulations, yet the study’s current scope urges careful interpretation and prompts further exploration into the intricate dynamics of bio-composite biodegradation for a thorough assessment.
In comparison, Saputri et al. (2024) reported that cassava starch reinforced with banana bunch cellulose samples exhibited biodegradability ratings ranging from 29.81 to 50.69%. Furthermore, Arjun et al. (2023) prepared biodegradable plastic from banana peels, observing rapid degradation within the initial 6 days, with weight reduction from 72.05 g to 44.70 g and complete decomposition expected within 60 days. Additionally, Ragadhita et al. (2022) studied their research based on cassava starch and banana peels, finding that the highest percentage of weight loss within 2 weeks was 89%. This suggests that the integration of banana peels, cassava starch, and banana stem fiber in our bio-composite materials fosters highly favorable conditions for accelerated biodegradation.
Most conventional plastic plates are made from materials like polystyrene or polypropylene (Ncube et al., 2021). Because of its high level of hydrophobicity, polyethylene (PE) cannot dissolve in aqueous environments, posing a challenge to the biodegradation of PE. The process of PE biodegradation involves several factors, including the preparation and pretreatment of polymers used in microbial degradation studies, the use of solvents to aid in the dissolution of PE substrates, and the secretion of various substances by microorganisms. Consequently, the biodegradation of PE is intricate, making it challenging to characterize and determine the mechanism of degradation (Zhang et al., 2022). Polypropylene takes 20 to 30 years to completely decompose after it is dumped in a landfill. Because of the potential for hazardous chemicals like lead and cadmium to be employed during manufacture, this feature raises serious environmental concerns (Nakatani et al., 2022). In comparison to plates made from traditional materials such as polystyrene or polypropylene, the prepared samples in this study exhibit accelerated degradation, indicating a positive step towards reducing the environmental impact of disposable plastic products.
4 Conclusion
The main objective of this research was to investigate the use of bio-composite sheets through the utilization of banana peels, cassava starch, and banana stem fibre to produce bio-composite plates as an alternative to conventional plastics. First, bio-composite sheets were successfully produced by using banana peels, cassava starch, banana stem fibre, glycerol, and acetic acid after a broad sample preparation and testing procedure. Water absorption tests, moisture content tests, tensile strength tests, and biodegradability tests were carried out to evaluate the produced bio-composite materials. Based on the results obtained, samples 3.1, 4.1, 4.2, and 4.3 demonstrated good performance with lower water absorption (30.91, 6.43, 13.48, and 27.74%). Tensile strength results surpassed the values reported in the literature (compared to bio-composite materials), indicating the potential for enhanced mechanical properties in the bio-composite samples. The comprehensive testing and analysis provided valuable insights into the properties and performance of the bio-composite samples. To conclude, this research successfully explored the feasibility of using banana peels, cassava starch, banana stem fibre, glycerol, and acetic acid to produce bio-composite sheets. Further to that, this study contributes to the growing body of knowledge in the field of sustainable materials and offers potential applications for eco-friendly alternatives to conventional plastics.
Data availability statement
The original contributions presented in the study are included in the article/supplementary material, further inquiries can be directed to the corresponding author.
Author contributions
GI: Conceptualization, Data curation, Formal analysis, Methodology, Writing – original draft. PK: Conceptualization, Supervision, Validation, Visualization, Writing – review & editing. GS: Writing – review & editing.
Funding
The author(s) declare that financial support was received for the research, authorship, and/or publication of this article. This research did not receive any specific grant from funding agencies in the public, commercial, or not-for-profit sectors. However, authors would like to acknowledge the academic collaboration support for this research by the Norwegian Partnership Programme for Global Academic Cooperation (NORPART) project with grant number NORPART-2021/10175.
Conflict of interest
The authors declare that the research was conducted in the absence of any commercial or financial relationships that could be construed as a potential conflict of interest.
Publisher’s note
All claims expressed in this article are solely those of the authors and do not necessarily represent those of their affiliated organizations, or those of the publisher, the editors and the reviewers. Any product that may be evaluated in this article, or claim that may be made by its manufacturer, is not guaranteed or endorsed by the publisher.
References
Amin, M. R., Chowdhury, M. A., and Kowser, M. A. (2019). Characterization and performance analysis of composite bioplastics synthesized using titanium dioxide nanoparticles with corn starch. Heliyon 5:e02009. doi: 10.1016/j.heliyon.2019.e02009
Arjun, J., Manju, R., Rajeswaran, S. R., and Chandhru, M. (2023). Banana peel starch to biodegradable alternative products for commercial plastics. GSC Biol. Pharm. Sci. 22, 234–244. doi: 10.30574/gscbps.2023.22.2.0066
Azieyanti, N. A., Amirul, A., Othman, S. Z., and Misran, H. (2020). “Mechanical and morphology studies of bioplastic-based banana peels” in Journal of Physics: Conference Series, vol. 1529 (IOP Publishing), 032091.
Babalola, O.A., and Olorunnisola, A.O., (2019). “Evaluation of coconut (Cocos nucifera) husk fibre as a potential reinforcing material for bioplastic production.” in Materials Research Proceedings. pp. 11.
Bhuyan, M. S. (2022). Effects of microplastics on fish and in human health. Front. Environ. Sci. 10:250. doi: 10.3389/fenvs.2022.827289
Chapain, K., Shah, S., Shrestha, B., Joshi, R., Raut, N., and Pandit, R. (2021). Effect of plasticizers on the physicochemical properties of bioplastic extracted from banana peels. J. Inst. Sci. Technol. 26, 61–66. doi: 10.3126/jist.v26i2.41423
Chodijah, S., Husaini, A., and Zaman, M. (2019). “Extraction of pectin from banana peels (musa paradiasica fomatypica) for biodegradable plastic films” in Journal of Physics: Conference Series, vol. 1167 (IOP Publishing), 012061.
Dave, P. N., and Macwan, P. M. (2024). “Biocomposites with natural fibers” in Advances in biocomposites and their applications (Woodhead Publishing), 81–120.
Elnashar, M., and Karakuş, S. (2023). “Introductory chapter: introduction to biocomposites–new insights” in Biocomposites-Recent Advances (IntechOpen).
Mahmud, M. A., Belal, S. A., and Gafur, M. A. (2023). Development of a biocomposite material using sugarcane bagasse and modified starch for packaging purposes. J. Mater. Res. Technol. 24, 1856–1874. doi: 10.1016/j.jmrt.2023.03.083
Meena, P.K., Prajapati, R., Sherekar, S., Sreeja, R., and Claudia, K.L., (2020). Development and evaluation of biodegradable plastic using banana peel starch. Doctoral dissertation, Department of processing and Food Engineering.
Mohanty, A. K., Misra, M., and Drzal, L. T. (2001). Surface modifications of natural fibers and performance of the resulting biocomposites: an overview. Comp. Interfaces 8, 313–343. doi: 10.1163/156855401753255422
Nakatani, H., Ohshima, Y., Uchiyama, T., and Motokucho, S. (2022). Degradation and fragmentation behavior of polypropylene and polystyrene in water. Sci. Rep. 12:18501. doi: 10.1038/s41598-022-23435-y
Ncube, L. K., Ude, A. U., Ogunmuyiwa, E. N., Zulkifli, R., and Beas, I. N. (2021). An overview of plastic waste generation and management in food packaging industries. Theatr. Rec. 6:12. doi: 10.3390/recycling6010012
Norafifah Izzati, A. R., Hanis Madihah, A. M., Nurazzi, N. M., and Haafiz, M. M. (2024). The Effect of Cellulose Loadings on the Properties of Tapioca/Banana Peels Starch Bioplastics. PREPRINT (Version 1) Available at Research Square. doi: 10.21203/rs.3.rs-4210538/v1
Obebe, S. B., and Adamu, A. A. (2020). Plastic pollution: causes, effects and preventions. Int. J. Eng. Appl. Sci. Technol. 4, 85–95. doi: 10.33564/IJEAST.2020.v04i12.011
Pilapitiya, P. N. T., and Ratnayake, A. S. (2024). The world of plastic waste: a review. Cleaner Mat. 11:100220. doi: 10.1016/j.clema.2024.100220
Ragadhita, R., Fiandini, M., Nofiani, R., Farobie, O., Nandiyanto, A. B. D., Hufad, A., et al. (2022). Biomass composition (cassava starch and Banana (Musa sp.) peels) on mechanical and biodegradability properties of bioplastic for supporting sustainable development goals (SDGs). J. Eng. Sci. Technol. 18, 228–238.
Rahman, M. M., Maniruzzaman, M., and Yeasmin, M. S. (2023). A state-of-the-art review focusing on the significant techniques for naturally available fibers as reinforcement in sustainable bio-composites: extraction, processing, purification, modification, as well as characterization study. Results Eng. 20:101511. doi: 10.1016/j.rineng.2023.101511
Rahmatiah Al Faruqy, M. S., and Liew, K. C. (2016). Properties of bioplastic sheets made from different types of starch incorporated with recycled newspaper pulp. Trans. Sci. Technol 3, 257–264.
Rusdi, S., Destian, R. A., Rahman, F., and Chafidz, A. (2020). “Preparation and characterization of bio-degradable plastic from banana Kepok peel waste” in Materials science forum, vol. 981 (Trans Tech Publications Ltd.), 132–137.
Saputri, C. A., Julyatmojo, F. A., Febrina, M., Mahardika, M., and Maulana, S. (2024). “Characteristics of bioplastics prepared from cassava starch reinforced with banana bunch cellulose at various concentrations” in IOP Conference Series: Earth and environmental science, vol. 1309 (IOP Publishing), 012006.
Sultan, N. F. K., and Johari, W. L. W. (2017). The development of banana peel/corn starch bioplastic film: a preliminary study. Bioremed. Sci. Technol. Res. 5, 12–17. doi: 10.54987/bstr.v5i1.352
Trivedi, A. K., Gupta, M. K., and Singh, H. (2023). PLA based biocomposites for sustainable products: a review. Adv. Indust. Eng. Polymer Res. 6, 382–395. doi: 10.1016/j.aiepr.2023.02.002
Vijayalaksmi, M., Govindaraj, V., Anisha, M., Vigneshwari, N., Gokul, M., Nithila, E. E., et al. (2022). Synthesis and characterization of Banana Peel starch-based bioplastic for intravenous tubes preparation. Mat. Today Commun. 33:104464. doi: 10.1016/j.mtcomm.2022.104464
Wahyuningtiyas, N. E., and Suryanto, H. (2017). Analysis of biodegradation of bioplastics made of cassava starch. J. Mech. Eng. Sci. Technol. 1, 24–31. doi: 10.17977/um030v1i12017p024
Yan, H., Cordier, M., and Uehara, T. (2024). Future projections of global plastic pollution: scenario analyses and policy implications. Sustain. For. 16:643. doi: 10.3390/su16020643
Keywords: bio-composite, banana peels, banana stem fiber, cassava starch, sustainability, alternative materials
Citation: Ishara GKK, Koliyabandara PA and Samarakoon G (2024) Eco-friendly bio-composite sheets: a study on the utilization of banana peels, cassava starch, and banana stem fibers. Front. Sustain. 5:1410986. doi: 10.3389/frsus.2024.1410986
Edited by:
Muhammad Asad Ur Rehman Naseer, Bahauddin Zakariya University, PakistanReviewed by:
Vinay Mohan Pathak, University of Delhi, IndiaPawan Kumar Rakesh, National Institute of Technology Uttarakhand, India
Copyright © 2024 Ishara, Koliyabandara and Samarakoon. This is an open-access article distributed under the terms of the Creative Commons Attribution License (CC BY). The use, distribution or reproduction in other forums is permitted, provided the original author(s) and the copyright owner(s) are credited and that the original publication in this journal is cited, in accordance with accepted academic practice. No use, distribution or reproduction is permitted which does not comply with these terms.
*Correspondence: Gamunu Samarakoon, Z2FtdW51LmFyYWNoY2hpZ2VAdXNuLm5v