- 1Bioenergy Research, USDA-ARS, National Center for Agricultural Utilization Research, Peoria, IL, United States
- 2Members of the DOE Center for Advanced Bioenergy and Bioproducts Innovation, University of Illinois, Urbana-Champaign, Urbana, IL, United States
- 3Wheat, Sorghum and Forage Research Unit, USDA-ARS, University of Nebraska, Lincoln, NE, United States
- 4Agroecosystem Management Research Unit, USDA-ARS, University of Nebraska—East, Lincoln, NE, United States
- 5Department of Agricultural and Biological Engineering, University of Illinois at Urbana-Champaign, Urbana, IL, United States
Three crops of warm-season grasses are being developed for biomass production on northern rain-fed marginal farmland: big bluestem (BBS), switchgrass (SG), and a low diversity mixture of grasses (LDM). In this study, biomass harvested from established fields were compared for pelletization and subsequent conversion to sugars and ethanol. Each biomass was successfully pelletized to similar bulk densities without adding a binder at a commercial feed operation. Pelletizing increased the bulk density by 407% on average and was equally effective on all three biomass samples (528–554 kg/m3). Chemical analysis of the samples indicated that glucan and xylan contents were slightly reduced during pelletizing (by 23 and 16 g/kg, respectively), as well as theoretical ethanol yields, which are based upon total carbohydrate contents. Pellets and milled straws were pre-treated with either liquid hot-water or low-moisture ammonium hydroxide (LMA) and subsequently hydrolyzed with cellulases. Glucose and total sugar yields were similar for non-pellets and pellets using either pre-treatment; carbohydrates present in pellets were more efficiently recovered compared to non-pellets. LMA pretreated samples were separately hydrolyzed and fermented to ethanol using Scheffersomyces stipitis yeast. Hydrolysis recovered 69.7–76.8% of the glucose and 66.5–73.3% of the xylose across all samples. Glucose yields were 251–279 g/kg, db and were significantly lower for SG as compared to the other biomass samples. Recovered sugars were fermented to ethanol at 77.7–86.7% of theoretical yield. Final ethanol yields (245.9–275.5 L/Mg, db) were similar for all of the grasses and estimated to equate to production levels for BBS, LDM, and SG of 1,952, 2,586, and 2,636 l of ethanol per ha, respectively.
Introduction
Perennial warm-season (C4) grasses have been proposed as a sustainable resource for producing sugars, chemicals, and fuels using thermo-chemical and biochemical processes. The U.S. has sufficient resources to grow an estimated 171 Tg yr−1 of biomass from bioenergy grasses by 2022 (Turhollow et al., 2014). Perennial warm-season grasses are favored for biomass production because of their high productivities and low input requirements. In the case of switchgrass (SG, Panicum virgatum L.), it has been calculated that its conversion to fuel ethanol would reduce greenhouse gas emissions by 94% compared to gasoline, and the bioethanol would have a total net energy balance of 540% (Schmer et al., 2008). Perennial, warm season grasses are ideal for inclusion in rainfed systems with variable precipitation because of their high water use efficiency and developed deep rooting systems which also serve to stabilize and improve soil quality (Liebig et al., 2008; Blanco-Canqui et al., 2017). They are also nutrient-use efficient because nitrogen and essential elements are translocated to the soil, roots, and rhizomes during and after senescence (Vogel et al., 2002; Mulkey et al., 2008).
The United States Department of Agriculture has an ongoing long-term project to develop biomass varieties of native prairie grasses for growth on marginal lands in the Great Plains and Upper Midwest (Anderson et al., 2016). Development of suitable cultivars is particularly difficult because they need to perform well on marginal (e.g., low productivity, high erosion potential, low profitability) rain-fed farmland to minimize land use change from growing row crops. Therefore, in addition to high production, other important traits include drought resistance, quick, and dependable establishment, resistance to lodging, low-nutrient demands, resistance to pathogens and insects, and high winter survival rates (e.g., over-wintering) (Sarath et al., 2008). Breeding and management research requires a long-term commitment because of the need to study establishment and multiple production years on these traits. U.S.D.A., through its northern bioenergy centers, is developing and evaluating three native prairie-based bioenergy cropping systems: switchgrass, big bluestem (Andropogon gerardii Vitman), and a low-diversity grass mixture (Anderson et al., 2016).
Of these perennial bioenergy crops, SG is perhaps the most highly developed as judged by past field studies (McLaughlin and Kszos, 2005; Moore et al., 2014), available biomass cultivars, traditional, and molecular breeding research (Lipka et al., 2014; Vogel et al., 2014; Biswal et al., 2018), and other available tools (e.g., NIR calibrations) (Vogel et al., 2011; Serapiglia et al., 2017). Big bluestem (BBS) is a bioenergy crop of growing interest because of its high productivity, good genetic diversity, and ecological role as the dominant prairie species (Moore et al., 2014; Zhang et al., 2015). Yet development of BBS as a bioenergy crop has lagged considerably behind that of SG (Zhang et al., 2015). Finally, there is interest in cultivating pastures containing multiple species to emulate natural prairies for possible ecological benefits (Tilman et al., 2006). However, it is a challenge to develop a mixture of grasses that maintains both diversity and high production over multiple years and cuttings. The crops selected here represent a significant advance over previously cultivated grasses. For example, Liberty Switchgrass™ is the first bioenergy developed variety released by the USDA (Vogel et al., 2014), following a long breeding and selection process for high productivity and good over-wintering survival, and is only presently being evaluated in commercially relevant field plots. Likewise, the BBS crop used for this study is a mixture of two cultivars to maximize yield and stand health. There is also a need for further testing of polyculture plantings of grasses for bioenergy production given the sparsity of past studies using defined grass mixtures in very limited geographical growth regions (Robertson et al., 2017). Here, we describe a relevant mixture of grasses based on established high production grasses amenable to cutting and processing to value-added products. This unique low diversity mixture (LDM) is comprised of BBS, indiangrass (Sorghastrum nutans (L.) Nash), and sideoats grama [Bouteloua curtipendula (Michx.) Torr.].
Each has shown good establishment and persistence in production fields located on marginal rain-fed farmland located in northeastern Nebraska (Blanco-Canqui et al., 2017). Earlier research established that all three crops were equally beneficial for improving soil quality (Blanco-Canqui et al., 2017).
However, conversion of harvested biomass to ethanol requires transporting the biomass to the biorefinery gate, pre-treating it to deconstruct the cell wall structure, extracting the carbohydrates as fermentable sugars using cellulases and other related enzymes, and fermenting the freed sugars to ethanol or other biofuels (for a review: Dien and Bothast, 2009). Therefore, the suitability of a bioenergy crop depends on more than solely crop yield. This study evaluates the performance of these three promising bioenergy crops for pre-processing and bioconversion to ethanol.
A major impediment to using herbaceous bioenergy crops for industrial-scaled bioconversion is solving the logistical supply challenge of getting the biomass to the biorefinery gate (Hansen et al., 2015). Biorefineries are projected to be very large and to require considerable quantities of biomass to operate at cost-effective scales. For example, U.S. Department of Energy (DOE) cellulosic ethanol cost estimates are based upon a plant consuming 2,000 metric ton/day (Humbird et al., 2011). Meanwhile, chopped or baled grass is difficult to store, transport, and process on the front end because it has low-bulk density and poor flow properties. This challenge can be addressed by densifying and reforming the biomass. There are several available methods for densifying and reforming biomass of which the pellet mill and briquette press are the most popular that are compatible with biochemical conversion (Tumuluru et al., 2011). A pellet mill has several advantages in terms of low machine maintenance, efficient, and effective densification, and pellets have better handling properties compared to briquettes (Tumuluru et al., 2011). It is also the most common densification method used for biochemical processes. In this study, pellets were compared to non-pellets (e.g., baled biomass). Furthermore, this study is unique in that an ongoing commercial feed mill was used to manufacture the pellets. Use of a pre-existing commercial plant located nearby can save on capital costs (if also used for processing forages) and as done here allows for processing to be trialed on a multi-ton scale, which is also afforded by the scale of the crop field trial conducted here. A successful outcome from using a commercial feed mill is uncertain because unlike forages, which are harvested green (for example Guretzky et al., 2011), bioenergy crops (as discussed later) are typically harvested at senescence.
While none of the bioenergy cultivars evaluated here, and especially the LDM, have been previously evaluated in this format, the literature supports our choice to include a pelletizing step in this study. Numerous past studies have sought to evaluate the interaction of pelletization and bioconversion processes. Prior studies have included corn stover (Theerarattananoon et al., 2012; Ray et al., 2013; Bals et al., 2014; Hoover et al., 2014), switchgrass (Rijal et al., 2012; Wolfrum et al., 2017), or post-harvest created mixes of biomass (Shi et al., 2013; Wolfrum et al., 2017). Two of these studies pelletized corn stover with ammonium fiber expansion (AFEX) pre-treatment (Bals et al., 2014; Hoover et al., 2014). Other studies used a conventional pelletizing process followed by either pre-treatments with dilute-acid (Rijal et al., 2012; Ray et al., 2013; Wolfrum et al., 2017), ionic liquids (Shi et al., 2013), or ammonium hydroxide at room temperature (Rijal et al., 2012). Much of the literature concerns the influence of pellets on chemical composition and biochemical conversion. This is understandable given that pelletizing biomass involves heating and high-pressure steps likely to alter the chemical and certainly the physical nature of the biomass (Stelte et al., 2012). Results from compositional analyses are somewhat mixed with studies reporting either no effect by pelletization (Theerarattananoon et al., 2012; Wolfrum et al., 2017) or a slight reduction in glucose and/or xylose contents (Rijal et al., 2012; Ray et al., 2013; Shi et al., 2013; Bals et al., 2014). Results for sugar or ethanol yields are somewhat more promising with studies reporting either the same or slight increases in yields using pellets vs. non-pellets. To our knowledge, this is the first study that we are aware of to process bioenergy crops using a commercial-scaled feed mill. It is also the first to report on processing of LDM biomass and a mixture of BBS.
Pre-treatment is the heart of the ethanol production process and is among its most expensive unit operations (Lynd et al., 2017). We have chosen to compare the crops using two pre-treatment techniques: liquid hot water (LHW) and low-moisture ammonium hydroxide (LMA). Liquid hot-water, as its name implies, reacts biomass in the presence of hot-water (e.g., 180–200°C) (Mosier et al., 2005a). It has been a popular choice in the literature because it combines some of the advantages of an acid catalyzed pre-treatment without the disadvantages of using a mineral acid (Mosier et al., 2005b). It also generally produces lower amounts of inhibitors compared to dilute-acid pre-treatment. LMA is relatively new and involves treating low-moisture biomass with ammonium hydroxide (Kim et al., 2016). It is of interest because it employs a static reactor and does not require a dewatering step. We included both pre-treatments to evaluate the biomass samples using both acid and base based pre-treatments.
To summarize, in this study established production fields of BBS, LDM, and SG were harvested, field dried, and formed into round bales. Biomass yields for BBS, LDM, and SG were 7.4, 9.4, and 9.6 Mg/ha, respectively. The bales were transported to a nearby alfalfa feed operation and converted into pellets. These pellets were characterized for bulk density and chemical composition. Ground and pelletized biomasses were pre-treated with LHW and LMA. LHW pre-treated samples were evaluated for enzymatic conversion to sugars and LMA pre-treated samples for conversion to sugars and ethanol, the latter using a yeast that is capable of fermenting both glucose and xylose. The goal was to determine which crop(s) is most suited as a feedstock for bioethanol production.
Materials and Methods
Chemicals and Media
All media and chemicals were research grade and purchased from either Fisher Scientific or Sigma Aldrich Chemicals. The enzymes used were commercial formulations of cellulases (140 mg protein/ml CTEC3, Novozymes Inc.) and hemicellulases (HTEC2, 109 mg protein/ml). Enzyme activities were measured using previously reported methods (Dien et al., 2008). The yeast Scheffersomyces stipitis Y-50871 (ARS Culture Collection, Peoria, IL) was used for fermentations. This strain has been extensively evolved and selected for ethanol fermentation of glucose/xylose sugars prepared from alkaline pre-treated biomass (Slininger et al., 2015).
Biomass Samples and Pelletizing
The sample set included BBS, Liberty SG, and a LDM consisting of BBS, indiangrass, and “Butte” sideoats grama. BBS was seeded as an equal blend of “Bonanza” and “Goldmine” and indiangrass as an equal blend of “Scout” and “Warrior,” both on a pure live seed basis. The grasses were harvested in November 2013 from established fields after the first killing frost using commercial field-scale equipment. Grass was harvested with a John Deer 4990 forage harvester equipped with a John Deere 990 rotary head into windrows then packaged into net-wrapped round bales, using a John Deere 569 MegaWide round baler with net wrap, immediately after harvest. Bale weights ranged from 1,450 to 1,750 pounds. Plots were located near Mead, NE (Blanco-Canqui et al., 2017).
Approximately 18 Mg of each feedstock was coarsely ground and pelletized by our commercial partner Dehy Alfalfa Mills (Lyons, NE). Large amounts of each biomass were processed to demonstrate they can be processed at a commercial plant. Round bales were transported to the plant where they were sequentially milled using a tub grinder, and hammer mill. Milled biomass was dried in a ring drier, steam conditioned, and pelletized using a ring die pellet mill (Figure 1). The pellet mill settings were ¼” (6.35 mm) pellet diameter with a length of 3/8”−1 1/4” (9.525–31.75 mm).
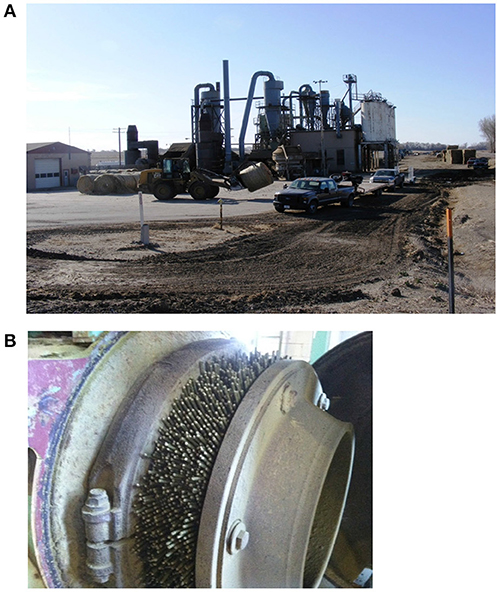
Figure 1. (A) Commercial feed plant that pelletized biomass samples (Dehy Alfalfa Mills, Lyons, NE). (B) Industrial pellet mill used for this study. Pellets were formed without the use of a binder.
Hammer Milling, Energy Usage, and Particle Size Determinations
Samples were tested for fine grinding as is required for some biomass conversion technologies (e.g., fast pyrolysis). Pelletized and raw biomass samples were ground to pass through a 2.0 mm screen using a hammer mill (1100 W, model MHM4, Glen Mills, Clifton, NJ). Energy usage required for milling was determined using an electrical meter. The distribution of particle sizes was determined by passing the ground biomass through a series of screens with increasingly fine meshes and afterwards weighing the amounts retained on each screen; particles that passed through the smallest screen size (e.g., 38 μm) were classified as fines. Particle sizes were determined using a sonic shifter (ATM model LP3, AdvanTech, New Berlin, WI) equipped with U.S. no. 30, 40, 60, 120, 325, and 400 screens (600, 425, 250, 125, 45, and 38 μm openings).
Physical and Chemical Characterization
Bulk densities were measured by filling a tared 600 ml Pyrex beaker with pellets and dividing the weight of the biomass by the filled volume. The volume of the beaker was determined based upon filling it with an equal volume of water. Each measurement was performed in triplicate.
Mass, length, and diameter distributions of pellets were determined by measuring 100 individual pellets using an analytical balance and calibrated caliper. Mean densities were determined by measuring the individual volume and mass for 18 pellets for each biomass. Volume was calculated by measuring the diameter and height using a calibrated caliper and calculated assuming each pellet was cylindrical in shape.
Moisture contents were measured by monitoring weight loss after samples had been dried at 105°C for 18 h. Chemical composition of water/ethanol extracts, structural carbohydrates, and lignin analysis was conducted using the two-stage acid digestion method (Sluiter et al., 2008). Soluble sugars (sucrose, glucose, and fructose) and starch were measured as previously reported (Dien et al., 2006). Each sample was analyzed in duplicate.
Pre-treatments
LHW pre-treatments were conducted as previously described (Serapiglia et al., 2017). Briefly, milled samples were pre-treated at 10% w/w solids in sealed serum bottles. Serum bottles (2 ea.) were placed in stainless steel reactors, which were fitted into an infrared reactor system and heated to 190°C for 15 min before being water-cooled to 40°C. Reactors were heated at 2.5°C/min.
LMA pre-treatments were conducted as follows. Milled biomass (6.0 g dry basis) and concentrated ammonium hydroxide solution (4.9 ml of 28%w/w ammonia content) were placed in a steel mini-reactor and immediately sealed with a screw cap steel lid. The reactor was mixed at 30°C for 40 min at 6 rpm (clockwise followed by counter-clockwise) using a computer controlled infra-red reactor system (Mathis Labomat model BFA12, Switzerland). Once mixed, the reactor was placed upright in a static heating oven set to 110°C and incubated for 72 h. The reactor was removed from the oven, allowed to cool, and the contents transferred to a Pyrex™ tray, which had been placed in a chemical fume hood. The ammonia was allowed to evaporate for 36–48 h. The biomass was briefly milled (e.g., 30–60 s) in a coffee mill to remove clumps that might have formed during pre-treatment. An aliquot was used to determine moisture content prior to enzymatic digestion and subsequently discarded.
Enzymatic Digestion and Fermentation
Enzymatic sugar release assays were modified from the methods of the National Renewable Energy Laboratory (NREL, Golden, CO, USA) and run at 3% w/w solids in 0.1 M sodium citrate buffer (pH = 4.8). Samples were saccharified using cellulase (CTEC3 26 mg/g glucan) and xylanase (HTEC2 0.96 mg/g forage). Thymol (25 μg/L) was added to prevent spoilage. The reactions were gently mixed (50 rpm) and incubated at 50°C for 72 h.
Yeast were routinely grown in YPD (yeast extract, peptone and dextrose medium formulated per L: 10 g yeast extract, 20 g peptone, and 20 g dextrose) supplemented with agar when preparing solid media (Bacto agar, 15 g/l). YP (yeast extract and peptone) was sterilized by heating at 121°C for 15 min in an autoclave (15 min cycle) and supplemented with filter sterilized glucose solution (400 g/l). Hydrolysates were filter sterilized and likewise supplemented with YP without inclusion of the glucose.
Separate hydrolysis and fermentation (SHF) was used for converting the biomass into ethanol. Hydrolysis and fermentation was performed using 50 ml Corning Pyrex™ glass wide-mouth screw cap bottles. The bottles were sealed with solid orange caps during hydrolysis and substituted with silicon foam caps for fermentation. For hydrolysis, 3.75 g of LMA pre-treated and air-dried biomass was diluted in 30.25 ml of dH2O and adjusted to a pH of 4.8–5.0. Cellulase (CTEC3, 36 mg/ g gucan) and xylanase (HTEC2, 4.2 mg/g forage) were added and biomass digested at 50°C, while mixing at 150 rpm for 72 h using a shaker/incubator (Innova, New Brunswick Scientific, NJ, USA). Bottles were cooled to 30°C before adding 2.75 ml of 10x YP and sodium phosphate buffer (pH 6.5, 0.1 M). The medium was inoculated with S. stipitis to a beginning OD600 = 1.0. Fermentations were sampled at 72 and 96 h for sugars and fermentation products.
The seed culture was prepared by transfer of a colony freshly grown on solid media into 10 ml of YPD. The pre-seed culture was grown over-night and 1 ml transferred to a 50 ml culture, which likewise was grown overnight, and the cells harvested, and concentrated to an OD600 = 50 with distilled H2O. Pre-cultures were grown at 30°C with mixing at 150 rpm in Erlenmeyer flasks sealed with porous silicon plugs using a shaker/incubator.
Analytical Methods
Sugars and fermentation production were determined using high performance liquid chromatography (HPLC). Samples were injected (20 μL) onto a Spectra System HPLC system (Thermo Electron Corporation, CA, USA) equipped with an auto-injector, isocratic pump, column heater, refractive index detector, and computer running analysis software Chromquest ver 2.5 (Thermo Electron Corporation). Analytes were separated using either an organic acid column (Aminex HPX-87H Column, 300 × 7.8 mm, Bio Rad Laboratories, Inc., Hercules, CA, USA) with 5 mM sulfuric acid as the mobile phase at 65°C or sugar column (Aminex HPX-87P Column, 300 × 7.8 mm, Bio Rad Laboratories) with water at 80°C. Flow rates of the mobile phases were 0.6 ml/min for both column separations. Galactose and xylose were determined by values from the sugar column and correlated with those measured using the organic acid column, on which the two sugars co-elute. Glucose and arabinose were taken as the average between the two runs. Acetic acid, ethanol, and glycerol were measured using the organic acid column. Enzyme protein contents were measured using the Bradford protein assay (Bradford, 1976).
Yields and conversion efficiencies were calculated as described (Dien, 2010).
Results were tested for significant differences (p < 0.05) using a 2-way ANOVA on biomass type and form (SigmaPlot 13.0, Systat Software, Inc.). Pairwise multiple comparisons were analyzed using the Holm-Sidak method (SigmaPlot 13.0, Systat Software, Inc.). All experiments included 2 or 3 levels of replication as indicated in the text.
Results
Pelletization
Big bluestem, switchgrass, and a low-diversity prairie grass mixture, which consisted of BBS, indiangrass, and sideoats grama, were separately pelletized at a commercial pellet feed mill using ~18 metric tons of each biomass. Differences in bulk density are visually contrasted in Figure 2. The straws were condensed from a beginning density of 128–133 kg/m3 to a final density of 528–554 kg/m3, which is a 407% increase in bulk density across all biomasses. Pellet mean diameters (6.52–6.58 mm) were close to the specified diameter (6.35 mm) with relatively low standard deviations (1.41–1.57%). A significant difference was detected between the mean diameter of LDM vs. SG pellets (p < 0.05) (Table 1). The distributions of pellet weights and lengths had large standard deviations and were skewed to the right (Table 1). For example, relative standard deviations for pellet weights were 36.2–40.0%. LDM pellets weighed more than BBS and SG pellets (p < 0.05), however significance differences were not observed among pellet lengths. Finally, BBS pellets were less dense (0.98 ± 0.08 g/ml, p < 0.05) than either LDM (1.06 ± 0.05) or SG (1.08 ± 0.07 g/ml) pellets.
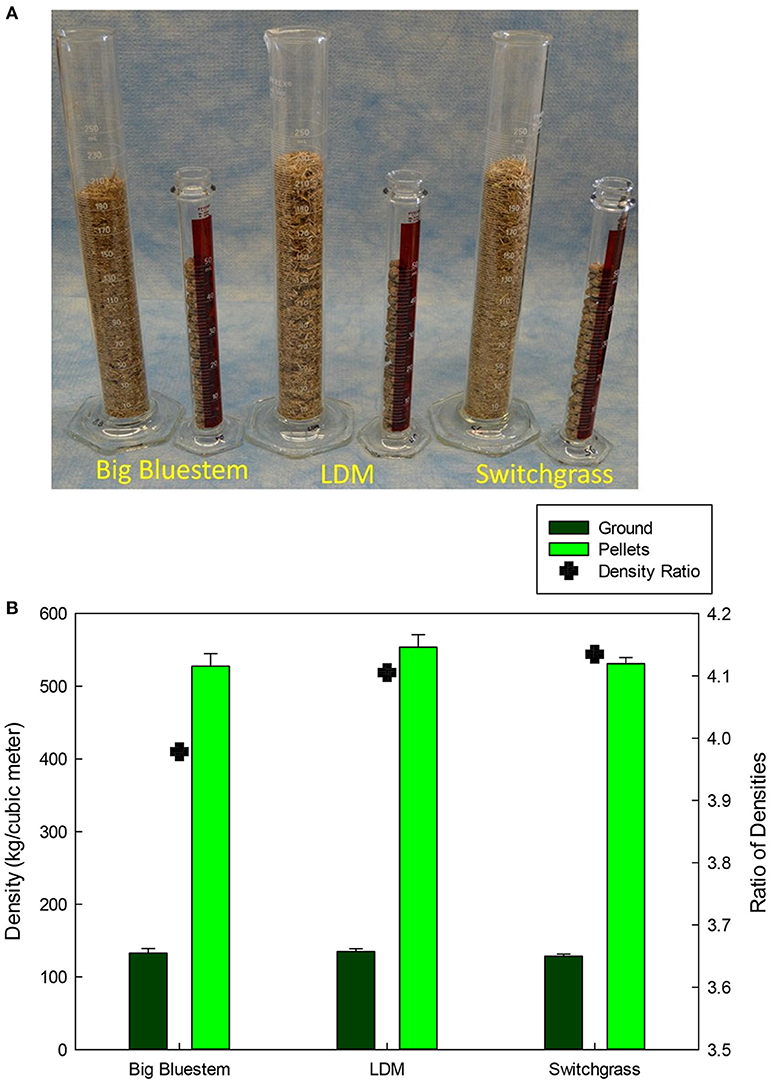
Figure 2. (A) Bulk densities visually compared for 25 g of pelletized and coarsely milled grass samples. (B) Graph showing differences in bulk densities between pelletized and coarsely ground samples and among different grasses. Densities were the same across crop and significantly different between pellets and non-pellets (p < 0.001). Legend: dark green is ground; green is pelletized, and cross is the ratio of bulk densities (right hand axis).
Composition and Milling
Compositions of the grasses were measured before and after pelletization and had mass closures of 91.5–95.8% (Table 2). Glucan and xylan contents (337 and 221 g/kg, db, respectively) were within the range of previously reported results for post-frost harvested switchgrass (309–385 g/kg, db and 200–246 g/kg, db), albeit toward the lower end (Dien et al., 2006, 2013; Kim et al., 2011; Rijal et al., 2012; Wolfrum et al., 2017). BBS glucan and xylan contents (340.1 and 199.6 g/kg, db) are in agreement with NREL published results (362 and 212 g/kg, db) (Wiselogel et al., 1996).
Pelletization led to compositional changes for the grasses. Biomass samples are prepared for compositional analysis by extracting soluble material with water and ethanol solutions. It is notable that pelletizing increased water-ethanol extractable material by 3–5% w/w across all three of the biomasses. Pelletizing also decreased glucan and xylan contents by 1–3% w/w. Differences in glucan and xylan contents between non-pellets and pellets were statistically significant (p < 0.05) for each biomass type. However, acid insoluble and soluble lignin contents were unaffected by pelletization. Maximum or theoretical ethanol yields are calculated based upon carbohydrate contents (Dien, 2010). As a result, theoretical ethanol yields were lower for pellets (~400 g/kg) vs. non-pellets (slightly >400 g/kg) (p < 0.05) (Figure 3). Maximum ethanol yields from pelleted biomass were comparable to each other (p > 0.05) and similar to that of corn stover, as calculated from average compositional data published by the U.S. DOE (Humbird et al., 2011). Reduction in carbohydrate contents represents an added cost incurred from pelletizing.
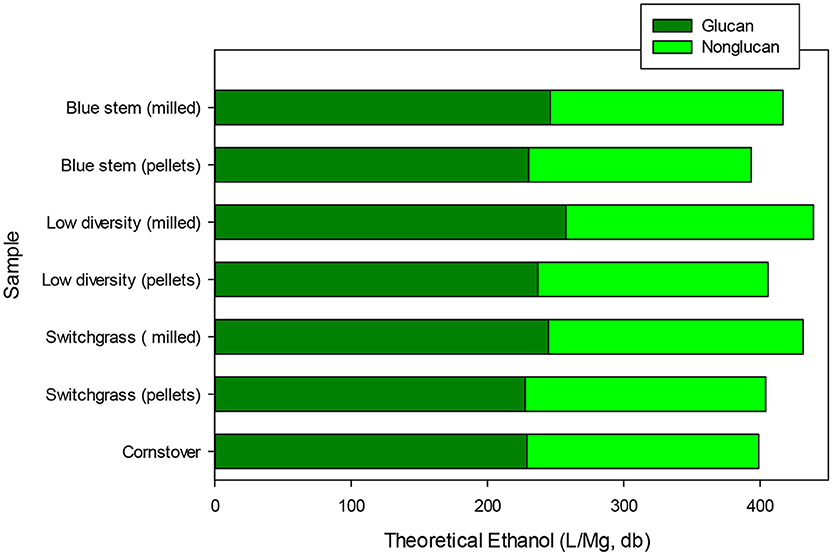
Figure 3. Calculated maximum ethanol yields for pelletized and non-pelletized grass samples and comparison to expected yield from corn stover. Ethanol yields were calculated based upon carbohydrate contents assuming 100% recovery of neutral sugars using previously reported methods (Dien, 2010). Corn stover carbohydrate composition is based upon results from a large sampling study (Humbird et al., 2011).
The pellets were ground using a hammer mill to reduce experimental sampling error with conversion. The pellets milled more uniformly than the non-pellets. The ground pellets contained 8.1 and 4.1% fewer 180 micron particles and fines than the non-pellets, respectively (Table 3). BBS pellets and non-pellets took much less energy to mill than LDM and SG (p < 0.05) even though all had similar lignin contents. While further testing is warranted, favorable milling characteristics might be an important advantage for bioconversion if grinding is required prior to pre-treatment.
Pre-treatment and Low-Solids Enzymatic Conversion
The biomass samples were next evaluated for neutral sugar yields using either LHW or LMA pre-treatment followed by digestion with cellulases and hemicellulases. LHW (also termed hydrothermal) pre-treatment consists of simply heating the biomass to a high temperature in water. The natural acidity of water, which is enhanced as the water is heated, acts as a catalyst. Following the LHW pre-treatment, the whole hydrolysate is pH adjusted to pH 5.0 and digested with a commercial cellulose and hemicellulose preparations to end hydrolyze cell wall carbohydrates to saccharides. Glucose yields (per kg of beginning biomass) were 262–357 g/kg and the yield of total fermentable sugars (e.g., glucose, galactose, and xylose) were 438–530 g/kg (Figure 4A). This represented 70–98% of the available glucan and 72–91% of the total fermentable sugars (Figure 4B). Glucose and total sugar yields were either not impacted or improved by pelletization (p < 0.05). Total sugar yields were ranked LDM > BBS > SG (p < 0.05; Figure 4A).
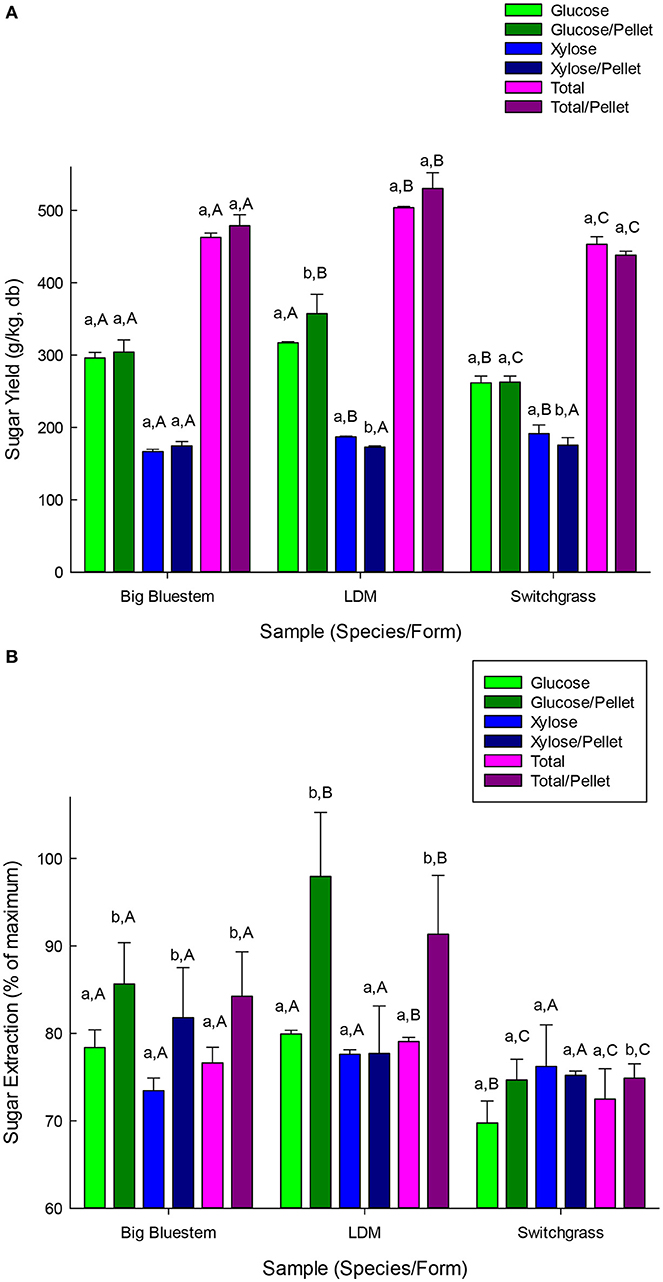
Figure 4. (A) Yield of neutral sugars from pelletized and non-pelletized samples pretreated with liquid hot-water pretreatment followed by enzyme hydrolysis using commercial cellulases and hemicellulases. Results are mean of triplicate runs and error bars are standard deviations. Different lower-case letters represent significant differences based upon pellet vs. non-pellets and different capital letters represent significant differences based upon species for either pelleted or non-pelleted samples (p < 0.05). (B) Sugar yield efficiencies (e.g., % sugars recovered) from pelletized and non-pelletized samples pretreated with liquid hot-water pretreatment followed by enzyme hydrolysis using commercial cellulases and hemicellulases. Results are mean of triplicate runs and error bars are standard deviations. Legend: reported on figure. Different lower-case letters represent significant differences based upon pellet vs. non-pellets and different capital letters represent significant differences based upon species for either pelleted or non-pelleted samples (p < 0.05).
Ammonium based pre-treatments operate by a different chemistry than LHW. The alkaline pH partially dissolves hemicellulose and cleaves some lignin cross linkages. In the special case of true grasses (Poaceae or Gramineae), alkali is thought to also improve digestibility by saponification of arabinose ferulic acid ester bonds linking lignin and xylan (Vogel, 2008). Following LMA pre-treatment, ammonia was removed by evaporation and the hydrated whole hydrolysate treated with commercial enzymes to extract the monosaccharides. For LMA pre-treated and saccharified samples, glucose yields (per kg of beginning biomass) were 272–326 g/kg and the yield of total fermentable sugars were 451–510 g/kg (Figure 5A). This represented 68–89% of the available glucan and 71–87% of the total fermentable sugars (Figure 5B). Glucose and total sugar yields were either not impacted or improved by pelletization (p < 0.05). Total sugar yields for pellets did not vary with species (p > 0.05) and were slightly higher for BBS and SG than LDM (p < 0.05) for non-pellets (Figure 5A).
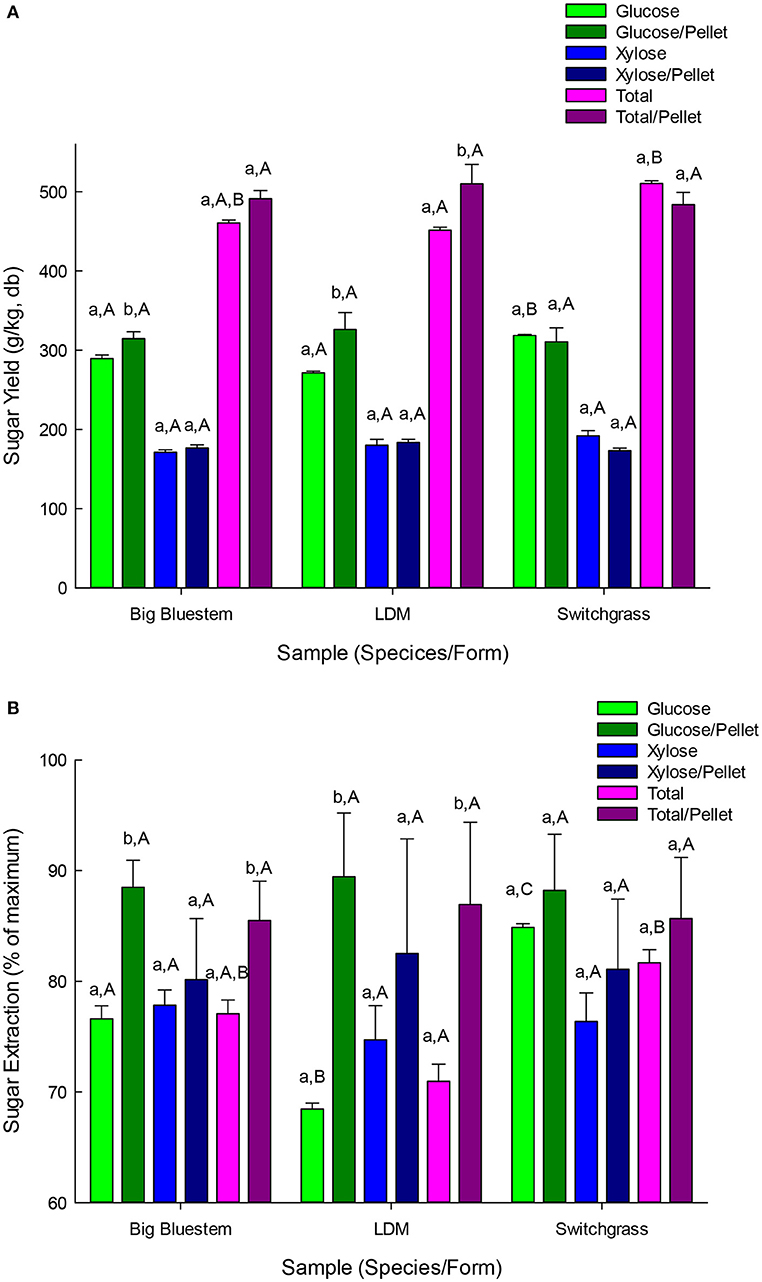
Figure 5. (A) Yield of neutral sugars from pelletized and non-pelletized samples pretreated with LMA pretreatment followed by enzyme hydrolysis using commercial cellulases and hemicellulases. Results are mean of triplicate runs and error bars are standard deviations. Different lower-case letters represent significant differences based upon pellet vs. non-pellets and different capital letters represent significant differences based upon species for either pelleted or non-pelleted samples (p < 0.05). (B) Sugar yield efficiencies (e.g., % sugars recovered) from pelletized and non-pelletized samples pretreated with liquid hot-water pretreatment followed by enzyme hydrolysis using commercial cellulases and hemicellulases. Results are mean of triplicate runs and error bars are standard deviations. Different lower-case letters represent significant differences based upon pellet vs. non-pellets and different capital letters represent significant differences based upon species for either pelleted or non-pelleted samples (p < 0.05).
Overall, yields were higher and more consistent across grass samples for the LMA vs. LHW pre-treatment. For either pre-treatment, pelletization was either favorable or neutral for glucose and total sugar yields.
Ethanol Fermentation
Next, ethanol yields were compared following SHF. To prepare biomass for ethanol fermentation, the different biomass feedstocks were pre-treated with LMA and the whole hydrolysate saccharified at 10% w/w solids. LMA was selected over LHW because sugar yields using the former were more consistent across the different biomass feedstocks. The hydrolysate was supplemented with nutrients, and fermented to ethanol using S. stipitis yeast.
Pre-treatment and enzymatic hydrolysis (e.g., pre-fermentation) recovered 69.7–76.8% and 70.1–77.1% of the available glucose and xylose, respectively (Table 4). Glucose yields were slightly but significantly (p < 0.05) lower for SG vs. the other two grasses, as was also observed for LHW pre-treatment. Xylose yields did not vary among species (p > 0.05).
Glucose and xylose yields [g/kg, db] were reduced 6.4 and 9.4, respectively, for pellets vs. non-pellets averaged across all biomasses (p < 0.05). This reduced yield can be directly attributed to the lower sugar contents observed for pellets vs. non-pellets because pellets were more digestible for glucose (p < 0.05, 3.3% greater glucose efficiency for pellets vs. non-pellets) and not statistically different for xylose efficiencies (p > 0.05). Overall, efficiencies at which free sugars were recovered were less than observed for the low-solids hydrolysates, which is to be expected because of increases in concentration of soluble enzyme inhibitors (acetic acid, lignin derived aromatics, etc.) and end-product inhibition.
Ethanol titers were 18.8–20.5 g/L of fermentation culture following the 96 h fermentations and yields were similar between pellets and non-pellets for the entire biomass set (Table 4). Glucose was exhausted within the first 48 h (data not shown) and residual xylose was on average 4.7 ± 2.0 g/L. Glucose was fermented prior to xylose (data not shown) as previously reported (Slininger et al., 2015). The ethanol yields were 77.7–86.7% of theoretical based on the beginning concentrations of glucose and xylose. Ethanol titers and yield efficiencies for the pellets and non-pellets were similar; indicating that pelletizing did not diminish the value of the grasses as a fermentation carbon source. Overall, process yields were 194.0–217.4 g of ethanol per kg of biomass (db). Ethanol yields and efficiencies were similar for all three grass crops.
Discussion
Composition and Pre-processing
Across the ground grasses, there was no significant differences for glucan or xylan contents. Switchgrass did contain more acetate (35.7 g/kg vs. 29.7 g/kg), which is important because it can adversely affect fermentation. In addition, lignin content was lower for LDM (169.3 g/kg) compared to the other two grasses. Most important, all three grass crops had similar theoretical ethanol yields on a mass basis and for non-pellets this value exceeded that of corn stover (Figure 3).
If the biomass needs to be trucked to the factory gate, densifying should allow for more efficient transport. Trucks operate most effectively when filled with cargo to their weight limit. For a truck with a trailer volume of 70–90 m3, this requires a minimum bulk density of 270–320 kg/m3 (Thoreson et al., 2010). The mean bulk densities for the three pelletized biomass samples (528–554 kg/m3) consistently exceed this limit (Figure 2). In contrast, prior to compacting (128–135 kg/m3), the trucks would be operating at <50% efficiency. The denser pellets are also expected to be more convenient to store vs. round bales or chopped grass or at least this was found to be the case in this laboratory.
Bulk densities of grasses for different presentations are reviewed by Sokhansanj et al. (2009). Ground SG (1.5 mm loose fill) has a bulk density of 120 kg/m3, like that reported here. Round baled SG is compressed to 140–180 kg/m3. Pellets (6.24 mm diameter) are reported as 500–700 kg/m3, though a value below 400 kg/m3 has also been reported (Gilbert et al., 2009). Pellet densities reported here fall within the accepted range. Pellet properties vary based upon biomass feed moisture and particle size as well as process temperature and pressure (Tumuluru et al., 2011). Presumably, properties would also vary with harvest maturity (Tumuluru et al., 2011) and in that regard SG pellets destined for feed would be harvested at an earlier maturity to improve nutritive value. However, post-frost harvest is favored for bioenergy crops because nutrients are translocated to the soil post-frost (Dien et al., 2006). In forage systems, grasses are often cut multiple times throughout a season because harvest maturity is known to play a significant role in determining feed quality. Likewise, harvest maturity can affect mass-based conversion yields (Dien et al., 2006, 2013). In this study, grasses were harvested after a killing frost. In temperate regions, a single annual harvest is required to maintain healthy highly productive stands of switchgrass (Sanderson et al., 1999; Monti et al., 2008; Mitchell and Schmer, 2012). Single cut systems also consume less energy than multiple harvest systems (McLaughlin and Kszos, 2005). While biomass yield is maximum at post-anthesis stage, post-frost harvest is recommended with ~50–60% of shoot nitrogen remobilized to the rhizomes (Sarath et al., 2014). This minimizes soil nutrient removal (Dien et al., 2006; Sarath et al., 2014) and helps to ensure a healthy productive stand, especially when under drought conditions (Mitchell and Schmer, 2012).
Therefore, further studies are warranted to determine the effect of harvest maturity on pellet processing and feed value in the event of dual use for SG. BBS has similar reported bulk densities as SG: 46.6 kg/m3 for chopped straw and 467–618 kg/m3 for pellets (Theerarattananoon et al., 2012). An important advantage of manufacturing pellets is the possibility of making a uniform feedstock using multiple readily available sources of biomass (Shi et al., 2013; Wolfrum et al., 2017), for a highly favorable supply logistics outcome (Ray et al., 2017). This study demonstrates that it is likewise possible to manufacture pellets using heterogeneous grasses harvested from a field planted with multiple plant species.
Forming pellets led to small but significant (p < 0.05) decreases in glucans (2.6% on average) and xylans (1.7%) for all the feedstocks. Most, but not all (Theerarattananoon et al., 2012; Wolfrum et al., 2017), previous studies also reported decreased glucan (1–4%) and xylose (2–4%) contents for pellets compared to beginning straws (Rijal et al., 2012; Ray et al., 2013; Shi et al., 2013; Bals et al., 2014). Varied results are not surprising because pelletizing involves a combination of heat and high pressure to compress biomass and form durable pellets. Formation of durable pellets depends upon operating above the glass transition state for lignin and forming cross linkages between carbohydrates, lignin, and other plant cell components (Kaliyan and Morey, 2010; Tumuluru et al., 2011). Decreased glucan and xylan contents did not appear to be correlated with feedstock type. The techniques used here might also overlook changes in lignin composition. Combinations of carbohydrates and lignin extractives form compounds termed pseudo-lignin, which are detected as Klason lignin (Sannigrahi et al., 2011). Likewise, scale did not play a role, though this study is the first to use pellets made by an existing commercial plant. Finally, the reader is cautioned that observed decreases in carbohydrate contents are near the practical detection limits of standard analytical methods (1–3% relative standard deviations) used to determine composition (Templeton et al., 2010), which is compounded in the case of mixtures by the opportunity for additional sampling error.
Conversion of Biomass to Sugars and Ethanol
Conversion yields were next measured by pre-treating pellets and non-pellets and measuring glucose and xylose released following enzymatic hydrolysis. Two pre-treatments were selected for this study: liquid hot-water and low moisture ammonium pre-treatments. LHW involves pre-treating biomass at high temperatures solely with water (Mosier et al., 2005a). LHW was selected because it avoids the use of a mineral catalyst (e.g., sulfuric acid), has been reported to minimize the formation of furfural because xylan is not hydrolyzed all the way to xylose (Mosier et al., 2005b), and has been successfully applied in the past to switchgrass (Kim et al., 2011). LMA is similar to low moisture anhydrous ammonium pre-treatment (LMAA) (Yoo et al., 2011) but in which ammonium is added as a concentrated ammonium hydroxide solution. LMA was selected as a representative alkaline pre-treatment because it is simple to implement, and ammonia pre-treated biomass does not require extensive conditioning prior to fermentation (Dien et al., 2013). Biomass is treated as a moist solid and is incubated in a static oven following a brief mixing step. It is envisioned that the ammonia and biomass will be mixed before being incubated in a large static tank in order to save energy and capital costs (Nghiem et al., 2016). Two pre-treatment technologies were selected because they reflect two different chemistries (e.g., acid and base). LHW and LMA pre-treated samples were assayed for sugar yields in low-solids digestions. LMA pre-treated samples were also used for two-stage high solids hydrolysis and ethanol fermentation (SHF).
LHW proved to be an effective pre-treatment. Across all samples, 72.5–81.8% of total neutral carbohydrates were recovered as monosaccharides following treatment with cellulases and hemicellulases. A prior study also using LHW and switchgrass with similar analytical methods reported a higher glucose yield (>80% glucan vs. 70% here) and a comparable xylan yield (>80% xylan vs. 76% here) (Kim et al., 2011). The higher yield in this prior study could have arisen from using different SG varieties, a higher pre-treatment temperature (200°C vs. 190°C), and a longer enzymatic hydrolysis time (168 vs. 96 h).
This is the first study that we are aware of to apply LMA/LMAA to SG (Kim et al., 2016), and the glucose and xylose recoveries reported here (85% of glucan and 76% of xylan) are favorable compared to those reported using other ammonia based pre-treatments with SG. One study that used dilute ammonium hydroxide at lower solids (15%) and higher temperatures (170°C for 20 min) than here, reported glucose and xylose hydrolysis efficiencies of 66.9–90.5% and 60.1–84.2%, respectively (Dien et al., 2013). LMA appears to be more effective than dilute ammonium hydroxide when pre-treating similar maturity SG; the higher values from the other study were for the SG samples harvested at mid-maturity. Another study that compared both AFEX (50% solids, 140–150°C, 20 min) and soaking in aqueous ammonia (SAA) (11.5% solids ammonium hydroxide solution, 90°C, 24 h) pre-treatments, observed slightly lower results: ~80% glucose and ~65% xylose yields (Kim et al., 2011). SAA has also been tested on pelletized SG (14% solids, 60°C, 6 h, 0.9 g NH3: 1.0 g biomass) with glucose and xylose yields of up to 95.2 and 77.6%, respectively. Our yields for LMA SG pellets are slightly lower for glucose (88.2%) and slightly higher for xylose (81.1%). Still, LMA is viewed as a technical advance to SAA (Kim et al., 2016). The reduction of water afforded by using LMA (or AFEX) facilitates recovery of ammonia, avoids energy wasted heating excess water during pre-treatment, and reduces the water footprint of the process.
A significant advantage of LMA pre-treatment is that hydrolyzed sugars can be fermented to ethanol without requiring a conditioning step to remove inhibitors, as is often required in the case of dilute-acid pre-treatment. LMA biomasses were converted to ethanol using a two-stage process: biomass was hydrolyzed to sugars and the sugars fermented to ethanol. A two-stage process allowed for optimal temperatures to be applied for enzymatic hydrolysis (50°C) and fermentation (30°C). The overall ethanol conversion efficiencies on a beginning biomass basis were 63.7–71.1%, which includes inefficiencies incurred during hydrolysis and fermentation. Overall ethanol efficiencies represent an advance from a prior study by this laboratory using SG pre-treated with dilute ammonium hydroxide and a Saccharomyces cerevisiae engineered for xylose fermentation (41.0–56.4% of theoretical) (Dien et al., 2013).
Comparison of Sugar and Ethanol Yields for Pellets and Non-pellets
No reduction in conversion yields were observed for pelleted and non-pelleted samples for the low-solids digestion assays or for ethanol yields. However, a 2 and 5% reduction in glucose and xylose yields (g/kg biomass, db), respectively was significant (p < 0.05) following the high-solids LMA hydrolysis even though hydrolysis efficiencies were mostly higher for pellets vs. non-pellets. Differences in results between the low and high solids hydrolysates can be caused by concentration of soluble inhibitors in the latter. Ethanol yields were the same for pellets and non-pellets, which suggests that sugar hydrolysis continued during the fermentation and that the final extent of hydrolysis was the same for pellets and non-pellets.
This conclusion that pelletization does not reduce bioconversion yields agrees with other related studies. Studies that use dilute-acid or ionic liquid did not observe a significant difference in product yields between non-pellets and pellets (Rijal et al., 2012; Theerarattananoon et al., 2012; Ray et al., 2013; Shi et al., 2013; Wolfrum et al., 2017) with one exception. Corn stover pellets treated with a low severity dilute acid, washed, and converted using SSF gave a higher ethanol yield efficiency (84% of theoretical) vs. the ground straw (68% of theoretical) (Ray et al., 2013). However, in the same study, when a pilot scale dilute-acid reactor was used, no difference was observed under optimal reaction conditions. In general, high severity or more effective pre-treatments (e.g., ionic liquid) would hide subtle differences in biomass properties associated with pelletizing. A study applying ammonium pre-treatment conducted at ambient temperature using switchgrass did not reveal any differences in glucan conversion, but xylan conversion was increased 10% (Rijal et al., 2012). A previously mentioned study that used SAA reported a 76% improvement in glucose yield from pelletizing (Nahar and Pryor, 2014). Processes that used AFEX pre-processed pellets did not report improved hydrolysis sugar yields, perhaps, because AFEX is a highly effective pre-treatment on herbaceous biomass in general. However, one of the AFEX studies emphasized that lower adsorption of water by the pellets compared to the straw led to a more efficient hydrolysis at high-solids because biomass did not need to be fed into the reactor over time (Bals et al., 2014). We have also observed noticeably more free water is present following high-solids dilute-acid pre-treatment of SG pellets vs. ground straw (personal observation by Dien). In summary, pelletizing does not lower product yields and might slightly promote conversion efficiency.
The aforementioned logistical advantages have to be balanced against the added cost and energy inputs associated with making pellets. A typical biorefinery is expected to be scaled to process 2,000 Mg/day of biomass. At this scale, baled SG is estimated to cost $80.64 /Mg at the factory gate and baling and transport will consume equivalent to 8.5% of the higher heating value (HHV) of the biomass. In contrast to baled SG, pellets are estimated to cost less ($71.76/Mg) and consume less energy (7.8% HHV) (Sokhansanj et al., 2009). The major energy used to make pellets goes to drying the biomass. It has been suggested adapting the process for bioenergy crops to increase drying efficiency can afford considerable energy and cost savings (Lamers et al., 2015). However, densifying the biomass may be necessary to reduce financial risks associated with relying on a regional feedstock. In other words, increased investor risk has an associated cost and eliminating this risk is expected to more than make up for the cost of pelletizing (Hansen et al., 2015).
Comparison of Feedstocks
There was no significant difference among the samples based upon ethanol yields following SHF. However, standard deviations tend to be higher for fermentation studies than for the beginning hydrolysis step perhaps because of the added yeast fermentation step. In this case, BBS and LDM had significantly higher glucose yields compared to that of SG. Xylose yields were similar among the grasses. The 3-year average biomass yields for BBS, LDM, and SG were 7.4, 9.4, and 9.6 Mg/ha. Therefore, differences in conversion yields are minor compared to those observed for biomass production. These crop productivities translate to ethanol production levels of 1,952, 2,586, and 2,636 l of ethanol per ha.
Conclusion
Three new field grown bioenergy grass crops were compared for composition, response to commercial scaled pelleting, and processing to sugars and ethanol. LDM had a higher glucan content than either BBS or SG (p ≤ 0.01) but no differences were observed for total fermentable carbohydrates and ethanol yields per ton of biomass. On a land basis, the estimated productivities were 1,952, 2,586, and 2,636 l of ethanol per ha.
The use of pellets compared to straw does not impact sugar and ethanol yields. This was found to be the case with LHW (sugars) and LMA (sugars and ethanol) pre-treatments. We did see a slight reduction in glucan and xylan contents associated with the pellets (p = 0.014), which agrees with most but not all prior reports. The conflicting conclusions might be attributed to (in this case) use of a commercial scale feed plant and likely variation in conditions used to form pellets across studies. This study demonstrates the promise of BBS, LDM, and SG for bioenergy production and notably demonstrates their processing from field through fermentation. Future research will be directed at evaluating additional production years of the LDM and to further improve biomass yields for BBS, so it is comparable to the other two crops used in this study.
Author Contributions
BD and RM performed several experiments and drafted the manuscript. PS aided in fermentations. VS performed the milling experiment. All authors gave critical comments and helped to prepare the final manuscript.
Funding
This work was funded by the Agricultural Research Service (ARS, USDA), DOE Center for Advanced Bioenergy and Bioproducts Innovation (U.S. Department of Energy, Office of Science, Office of Biological and Environmental Research under Award Number DE-SC0018420 and by the Agriculture and Food Research Initiative Competitive Grant no. 2011-68005-30411 from the USDA National Institute of Food and Agriculture. Any opinions, findings, and conclusions or recommendations expressed in this publication are those of the author(s) and do not necessarily reflect the views of the U.S. Department of Energy.
Disclaimer
The mention of trade names or commercial products in this article is solely for the purpose of providing specific information and does not imply recommendation or endorsement by the U.S. Department of Agriculture. USDA is an equal opportunity provider and employer.
Conflict of Interest Statement
The authors declare that the research was conducted in the absence of any commercial or financial relationships that could be construed as a potential conflict of interest.
Acknowledgments
Patricia J. O'Bryan and Victoria Nguyen for technical help, Debra Palmquist for statistical help, Novozymes Inc. for supplying the enzymes, Ben Fann, Bill Bickmeier, Jordan Leach, and Suanne Kallis for field work and transporting bales, and Dehy Alfalfa Mills for processing the biomass to pellets.
References
Anderson, W. F., Sarath, G., Edme, S., Casler, M. D., Mitchell, R. B., Tobias, C. M., et al. (2016). Dedicated herbaceous biomass feedstock genetics and development. BioEnergy Res. 9, 399–411. doi: 10.1007/s12155-015-9709-8
Bals, B. D., Gunawan, C., Moore, J., Teymouri, F., and Dale, B. E. (2014). Enzymatic hydrolysis of pelletized AFEX™-treated corn stover at high solid loadings. Biotechnol. Bioeng. 111, 264–271. doi: 10.1002/bit.25022
Biswal, A. K., Atmodjo, M. A., Li, M., Baxter, H. L., Yoo, C. G., Pu, Y., et al. (2018). Sugar release and growth of biofuel crops are improved by downregulation of pectin biosynthesis. Nat. Biotechnol. 36, 249–257 doi: 10.1038/nbt.4067
Blanco-Canqui, H., Mitchell, R. B., Jin, V. L., Schmer, M. R., and Eskridge, K. M. (2017). Perennial warm-season grasses for producing biofuel and enhancing soil properties, an alternative to corn residue removal. GCB Bioenergy 9, 1510–1521. doi: 10.1111/gcbb.12436
Bradford, M. M. (1976). A rapid and sensitive method for the quantitation of microgram quantities of protein utilizing the principle of protein-dye binding. Anal. Biochem. 72, 248–254. doi: 10.1016/0003-2697(76)90527-3
Dien, B. S. (2010). “Mass balances and analytical methods for biomass pretreatment experiments,” in Biomass to Biofuels: Strategies for Global Industries, eds A. A. Vertès, N. Qureshi, H. P. Blaschek, and H. Yukawa (West Sussex: John Wiley & Sons, Ltd), 213–231. doi: 10.1002/9780470750025
Dien, B. S., and Bothast, R. J. (2009). “A primer for lignocellulose biochemical conversion to fuel ethanol,” in The Alcohol Text Book, 5th edn, eds W. M. Ingledew, D. R. Kelsall, G. D. Austin, and C. Kluhspies (Nottingham: Nottingham University Press), 541
Dien, B. S., Jung, H.-J. G., Vogel, K. P., Casler, M. D., Lamb, J. F., Iten, L., et al. (2006). Chemical composition and response to dilute-acid pretreatment and enzymatic saccharification of alfalfa, reed canarygrass, and switchgrass. Biomass Bioenergy 30, 880–891. doi: 10.1016/j.biombioe.2006.02.004
Dien, B. S., O'Bryan, P. J., Hector, R. E., Iten, L. B., Mitchell, R. B., Qureshi, N., et al. (2013). Conversion of switchgrass to ethanol using dilute ammonium hydroxide pretreatment: influence of ecotype and harvest maturity. Environ. Technol. 34, 1837–1848. doi: 10.1080/09593330.2013.833640
Dien, B. S., Ximenes, E. A., O'Bryan, P. J., Moniruzzaman, M., Li, X.-L., Balan, V., et al. (2008). Enzyme characterization for hydrolysis of AFEX and liquid hot-water pretreated distillers' grains and their conversion to ethanol. Biores. Technol. 99, 5216–5225. doi: 10.1016/j.biortech.2007.09.030
Gilbert, P., Ryu, C., Sharifi, V., and Swithenbank, J. (2009). Effect of process parameters on pelletisation of herbaceous crops. Fuel 88, 1491–1497. doi: 10.1016/j.fuel.2009.03.015
Guretzky, J. A., Biermacher, J. T., Cook, B. J., Kering, M. K., and Mosali, J. (2011). Switchgrass for forage and bioenergy: harvest and nitrogen rate effects on biomass yields and nutrient composition. Plant Soil. 339, 69–81. doi: 10.1007/s11104-010-0376-4
Hansen, J. K., Jacobson, J. J., Cafferty, K. G., Lamers, P., and Roni, M. (2015). Quantifying Supply Risk at a Cellulosic Biorefinery. No. INL/CON-15-34705. Falls, ID: Idaho National Lab.(INL).
Hoover, A. N., Tumuluru, J. S., Teymouri, F., Moore, J., and Gresham, G. (2014). Effect of pelleting process variables on physical properties and sugar yields of ammonia fiber expansion pretreated corn stover. Biores. Technol. 164, 128–135. doi: 10.1016/j.biortech.2014.02.005
Humbird, D., Davis, R., Tao, L., Kinchin, C., Hsu, D., Aden, A., et al. (2011). Process Design and Economics for Biochemical Conversion of Lignocellulosic Biomass to Ethanol: Dilute-Acid Pretreatment And Enzymatic Hydrolysis Of Corn Stover. Golden, CO: National Renewable Energy Laboratory (NREL).
Kaliyan, N., and Morey, R. V. (2010). Natural binders and solid bridge type binding mechanisms in briquettes and pellets made from corn stover and switchgrass. Biores. Technol. 101, 1082–1090. doi: 10.1016/j.biortech.2009.08.064
Kim, J. S., Lee, Y., and Kim, T. H. (2016). A review on alkaline pretreatment technology for bioconversion of lignocellulosic biomass. Biores. Technol. 199, 42–48. doi: 10.1016/j.biortech.2015.08.085
Kim, Y., Mosier, N. S., Ladisch, M. R., Pallapolu, V. R., Lee, Y., Garlock, R., et al. (2011). Comparative study on enzymatic digestibility of switchgrass varieties and harvests processed by leading pretreatment technologies. Biores. Technol. 102, 11089–11096. doi: 10.1016/j.biortech.2011.06.054
Lamers, P., Roni, M. S., Tumuluru, J. S., Jacobson, J. J., Cafferty, K. G., Hansen, J. K., et al. (2015). Techno-economic analysis of decentralized biomass processing depots. Biores. Technol. 194, 205–213. doi: 10.1016/j.biortech.2015.07.009
Liebig, M. A., Schmer, M. R., Vogel, K. P., and Mitchell, R. B. (2008). Soil carbon storage by switchgrass grown for bioenergy. Bioenergy Research 1, 215–222. doi: 10.1007/s12155-008-9019-5
Lipka, A. E., Lu, F., Cherney, J. H., Buckler, E. S., Casler, M. D., and Costich, D. E. (2014). Accelerating the switchgrass (Panicum virgatum L.) breeding cycle using genomic selection approaches. PLoS ONE 9:e112227. doi: 10.1371/journal.pone.0112227
Lynd, L. R., Liang, X., Biddy, M. J., Allee, A., Cai, H., Foust, T., et al. (2017). Cellulosic ethanol: status and innovation. Curr Opin Biotechnol. 30, 202–211. doi: 10.1016/j.copbio.2017.03.008
McLaughlin, S. B., and Kszos, L. A. (2005). Development of switchgrass (Panicum virgatum) as a bioenergy feedstock in the United States. Biomass Bioenergy 28, 515–535. doi: 10.1016/j.biombioe.2004.05.006
Monti, A., Bezzi, G., Pritoni, G., and Venturi, G. (2008). Long-term productivity of lowland and upland switchgrass cytotypes as affected by cutting frequency. Biores. Technol. 99, 7425–7432. doi: 10.1016/j.biortech.2008.02.034
Moore, K. J., Birrell, S., Brown, R. C., Casler, M. D., Euken, J. E., Hanna, H. M. others., et al. (2014). Midwest vision for sustainable fuel production. Biofuels 5, 687–702. doi: 10.1080/17597269.2015.1015312
Mosier, N., Hendrickson, R., Ho, N., Sedlak, M., and Ladisch, M. R. (2005a). Optimization of pH controlled liquid hot water pretreatment of corn stover. Biores. Technol. 96, 1986–1993. doi: 10.1016/j.biortech.2005.01.013
Mosier, N., Wyman, C., Dale, B., Elander, R., Lee, Y., Holtzapple, M., et al. (2005b). Features of promising technologies for pretreatment of lignocellulosic biomass. Biores. Technol. 96, 673–686. doi: 10.1016/j.biortech.2004.06.025
Mulkey, V., Owens, V., and Lee, D. (2008). Management of warm-season grass mixtures for biomass production in South Dakota USA. Biores. Technol. 99, 609–617. doi: 10.1016/j.biortech.2006.12.035
Nahar, N., and Pryor, S. W. (2014). Reduced pretreatment severity and enzyme loading enabled through switchgrass pelleting. Biomass Bioenergy 67, 46–52. doi: 10.1016/j.biombioe.2014.04.027
Nghiem, N. P., Senske, G. E., and Kim, T. H. (2016). Pretreatment of corn stover by low moisture anhydrous ammonia (LMAA) in a pilot-scale reactor and bioconversion to fuel ethanol and industrial chemicals. Appl. Biochem. Biotechnol. 179, 111–125. doi: 10.1007/s12010-016-1982-2
Ray, A. E., Hoover, A. N., Nagle, N., Chen, X., and Gresham, G. L. (2013). Effect of pelleting on the recalcitrance and bioconversion of dilute-acid pretreated corn stover under low-and high-solids conditions. Biofuels 4, 271–284. doi: 10.4155/bfs.13.14
Ray, A. E., Li, C., Thompson, V. S., Daubaras, D. L., Nagle, N. J., and Hartley, D. S. (2017). “Biomass blending and densification: impacts on feedstock supply and biochemical conversion performance.” in Biomass Volume Estimation and Valorization for Energy, ed, J. S. Tumuluru (Rijeka: InTech), 15.
Rijal, B., Igathinathane, C., Karki, B., Yu, M., and Pryor, S. W. (2012). Combined effect of pelleting and pretreatment on enzymatic hydrolysis of switchgrass. Biores. Technol. 116, 36–41. doi: 10.1016/j.biortech.2012.04.054
Robertson, G. P., Hamilton, S. K., Barham, B. L., Dale, B. E., Izaurralde, R. C., Jackson, R. D., et al. (2017). Cellulosic biofuel contributions to a sustainable energy future: choices and outcomes. Science 356:eaal2324 doi: 10.1126/science.aal2324
Sanderson, M. A., Read, J. C., and Reed, R. L. (1999). Harvest management of switchgrass for biomass feedstock and forage production. Agron. J. 91, 5–10. doi: 10.2134/agronj1999.00021962009100010002x
Sannigrahi, P., Kim, D. H., Jung, S., and Ragauskas, A. (2011). Pseudo-lignin and pretreatment chemistry. Energy Environ. Sci. 4, 1306–1310. doi: 10.1039/C0EE00378F
Sarath, G., Baird, L. M., and Mitchell, R. B. (2014). Senescence, dormancy and tillering in perennial C4 grasses. Plant Sci. 217, 140–151. doi: 10.1016/j.plantsci.2013.12.012
Sarath, G., Mitchell, R. B., Sattler, S. E., Funnell, D., Pedersen, J. F., Graybosch, R. A., et al. (2008). Opportunities and roadblocks in utilizing forages and small grains for liquid fuels. J. Ind. Microbiol. Biotechnol. 35, 343–354. doi: 10.1007/s10295-007-0296-3
Schmer, M. R., Vogel, K. P., Mitchell, R. B., and Perrin, R. K. (2008). Net energy of cellulosic ethanol from switchgrass. Proc. Nat. Acad. Sci. U.S.A. 1052, 464–469. doi: 10.1073/pnas.0704767105
Serapiglia, M. J., Dien, B. S., Boateng, A. A., and Casler, M. D. (2017). Impact of harvest time and switchgrass cultivar on sugar release through enzymatic hydrolysis. BioEnergy Res. 10, 377–387. doi: 10.1007/s12155-016-9803-6
Shi, J., Thompson, V. S., Yancey, N. A., Stavila, V., Simmons, B. A., and Singh, S. (2013). Impact of mixed feedstocks and feedstock densification on ionic liquid pretreatment efficiency. Biofuels 4, 63–72. doi: 10.4155/bfs.12.82
Slininger, P. J., Shea-Andersh, M. A., Thompson, S. R., Dien, B. S., Kurtzman, C. P., Balan, V., et al. (2015). Evolved strains of Scheffersomyces stipitis achieving high ethanol productivity on acid-and base-pretreated biomass hydrolyzate at high solids loading. Biotechnol. Biofuels 8:60. doi: 10.1186/s13068-015-0239-6
Sluiter, A., Hames, B., Ruiz, R., Scarlata, C., Sluiter, J., Templeton, D., et al. (2008). Determination of structural carbohydrates and lignin in biomass. Lab. Anal. Proc. 1617, 1–16.
Sokhansanj, S., Mani, S., Turhollow, A., Kumar, A., Bransby, D., Lynd, L., et al. (2009). Large-scale production, harvest and logistics of switchgrass (Panicum virgatum L.) – current technology and envisioning a mature technology. Biofuels Bioproducts Biorefining 32, 124–141. doi: 10.1002/bbb.129
Stelte, W., Sanadi, A. R., Shang, L., Holm, J. K., Ahrenfeldt, J., and Henriksen, U. B. (2012). Recent developments in biomass pelletization–A review. BioResources 7, 4451–4490.
Templeton, D. W., Scarlata, C. J., Sluiter, J. B., and Wolfrum, E. J. (2010). Compositional analysis of lignocellulosic feedstocks. 2. method uncertainties. J. Agri. Food Chem. 58, 9054–9062. doi: 10.1021/jf100807b
Theerarattananoon, K., Xu, F., Wilson, J., Staggenborg, S., Mckinney, L., Vadlani, P., et al. (2012). Effects of the pelleting conditions on chemical composition and sugar yield of corn stover, big bluestem, wheat straw, and sorghum stalk pellets. Bioprocess Biosyst. Eng. 35, 615–623. doi: 10.1007/s00449-011-0642-8
Thoreson, C. P., Darr, M. J., and Webster, K. E. (2010). “Corn stover densification methods and their large-scale logistical impacts—preliminary analysis,” in American Society of Agricultural and Biological Engineers (Pittsburgh, PA).
Tilman, D., Hill, J., and Lehman, C. (2006). Carbon-negative biofuels from low-input high-diversity grassland biomass. Science 314, 1598–1600. doi: 10.1126/science.1133306
Tumuluru, J. S., Wright, C. T., Hess, J. R., and Kenney, K. L. (2011). A review of biomass densification systems to develop uniform feedstock commodities for bioenergy application. Biofuels Bioproducts Biorefining 5, 683–707. doi: 10.1002/bbb.324
Turhollow, A., Perlack, R., Eaton, L., Langholtz, M., Brandt, C., Downing, M., et al. (2014). The updated billion-ton resource assessment. Biomass Bioenergy 70, 149–164. doi: 10.1016/j.biombioe.2014.09.007
Vogel, J. (2008). Unique aspects of the grass cell wall. Curr. Opin. Plant Biol. 113, 301–307. doi: 10.1016/j.pbi.2008.03.002
Vogel, K., Mitchell, R., Casler, M., and Sarath, G. (2014). Registration of ‘Liberty’switchgrass. J. Plant Regis. 8, 242–247. doi: 10.3198/jpr2013.12.0076crc
Vogel, K. P., Brejda, J. J., Walters, D. T., and Buxton, D. R. (2002). Switchgrass biomass production in the Midwest USA. Agron. J. 94, 413–420. doi: 10.2134/agronj2002.0413
Vogel, K. P., Dien, B. S., Jung, H. G., Casler, M. D., Masterson, S. D., and Mitchell, R. B. (2011). Quantifying actual and theoretical ethanol yields for switchgrass strains using NIRS analyses. BioEnergy Res. 4, 96–110. doi: 10.1007/s12155-010-9104-4
Wiselogel, A., Shaine, T., and Johnson, D. (1996). “Biomass feedstock resources and composition.” in Handbook on Bioethanol: Production and Utilization, 1 edn, eds C. Wyman (Washington, DC: CRC press), 105–118.
Wolfrum, E. J., Nagle, N. J., Ness, R. M., Peterson, D. J., Ray, A. E., and Stevens, D. M. (2017). The effect of biomass densification on structural sugar release and yield in biofuel feedstock and feedstock blends. BioEnergy Research 10, 478–487. doi: 10.1007/s12155-017-9813-z
Yoo, C. G., Nghiem, N. P., Hicks, K. B., and Kim, T. H. (2011). Pretreatment of corn stover using low-moisture anhydrous ammonia (LMAA) process. Biores. Technol. 102, 10028–10034. doi: 10.1016/j.biortech.2011.08.057
Keywords: bioethanol, bioenergy crops, pellets, sugars, grasses
Citation: Dien BS, Mitchell RB, Bowman MJ, Jin VL, Quarterman J, Schmer MR, Singh V and Slininger PJ (2018) Bioconversion of Pelletized Big Bluestem, Switchgrass, and Low-Diversity Grass Mixtures Into Sugars and Bioethanol. Front. Energy Res. 6:129. doi: 10.3389/fenrg.2018.00129
Received: 08 May 2018; Accepted: 16 November 2018;
Published: 04 December 2018.
Edited by:
J. Richard Hess, Idaho National Laboratory (DOE), United StatesReviewed by:
Nick John Nagle, National Renewable Energy Laboratory (DOE), United StatesNalladurai Kaliyan, University of Georgia, United States
Kamalakanta Sahoo, Forest Products Laboratory (USDA), United States
Copyright © 2018 Dien, Mitchell, Bowman, Jin, Quarterman, Schmer, Singh and Slininger. This is an open-access article distributed under the terms of the Creative Commons Attribution License (CC BY). The use, distribution or reproduction in other forums is permitted, provided the original author(s) and the copyright owner(s) are credited and that the original publication in this journal is cited, in accordance with accepted academic practice. No use, distribution or reproduction is permitted which does not comply with these terms.
*Correspondence: Bruce S. Dien, YnJ1Y2UuZGllbkBhcnMudXNkYS5nb3Y=