Introduction
In a reference assessment on fuel cells (FCs) published about 10 years ago, emphasis was on materials challenges to solve pending problems and reach the market (Steele and Heinzel, 2001). More than 150 years after the discovery of FCs by Grove and Schönbein, the diversity of prototype systems was enormous, the utilization and commercialization of a few systems was a fact, but we were far behind a wide availability of these systems as commercial devices.
In the last decade this scenario changed considerably, FCs have moved past the R&D stage and do not just hold technological promise. Proton exchange membrane (PEMFCs), alkaline (AFCs), phosphoric acid (PAFCs), molten carbonate (MCFCs), direct methanol (DMFCs), and solid oxide fuel cells (SOFCs) are all commercially available in a fast growing market. The production is reaching 100,000 units per year while the power provided by all these systems reached the 150 MW level. MCFCs have the largest power share (Figure 1) while PEMFCs dominate in number (Figure 2). SOFCs are emerging both in number and power, but we can also find reference to sales of other FC types (Carter et al., 2012; Carter and Wing, 2013).
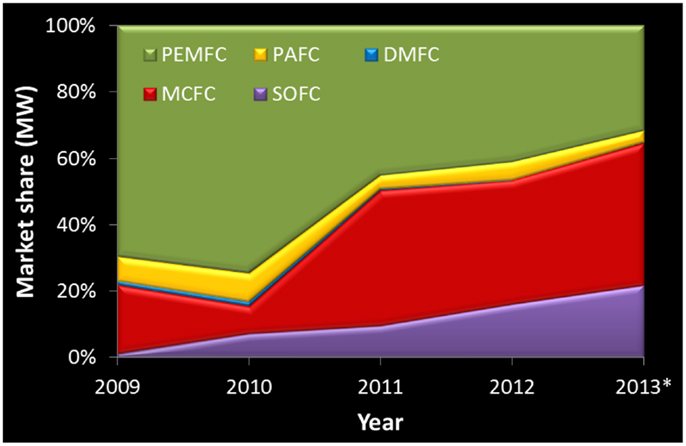
Figure 1. Fuel cell market share with respect to total power shipped per year. Values for AFCs not high enough to appear in this figure. *Numbers for 2013 are based on estimates (Carter et al., 2012; Carter and Wing, 2013).
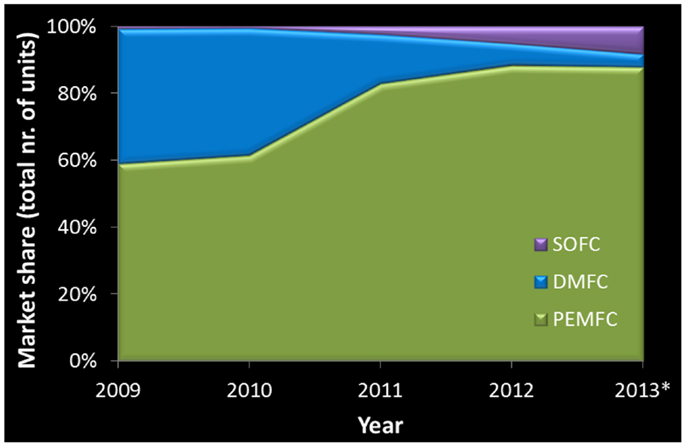
Figure 2. Fuel cell market share with respect to the total number of units sold per year. Systems not listed correspond to sales below 100 units per year. *Numbers for 2013 are based on estimates (Carter et al., 2012; Carter and Wing, 2013).
Performance is also changing quickly. As an example, the 2012 expected system cost for PEMFCs was $47/kW (based on existing technologies and assuming a production of 500,000 units per year). This estimate represents a 50% decrease since 2007 and an 83% decrease since 2002 (Spendelow and Marcinkoski, 2012). A significant stack cost reduction is still anticipated for the coming years (U.S. Department of Energy’s Office of Energy Efficiency and Renewable Energy, 2012). In parallel, the PEMFC power density increased from 583 mW/cm2 in 2007 to 984 mW/cm2 in 2012. This corresponds to an equally impressive 69% increase in performance alongside of a huge cost reduction (Spendelow and Marcinkoski, 2012). Innovation in materials and systems was critical to reach these remarkable changes.
The present FC market portrays the conventional perspective where higher temperature FCs (>500°C) were expected to be used mostly in large stationary power applications, while several low temperature FCs showed great potential for transportation and portable applications. Interestingly, for most power ranges only a couple of FC systems seem to qualify (Figure 3). However, one of the challenging aspects in FC development is the impressive diversity of concepts, to a large extent derived from the size flexibility of modular systems based on single cells. This means that some types of FCs are attempting to adjust to unexpected fields of application, namely to enter into the large market of secondary batteries. As example, the so-called μ-SOFC, with a modest power, is clearly compatible with portable applications. This is precisely the opposite of the initial aim behind SOFC development. The entire concept for a μ-SOFC is quite distinct from those envisaged for large power plants, but, somewhat surprisingly, the announced base materials are in all aspects identical (Evans et al., 2009). Research is paving the way to this impressive versatility.
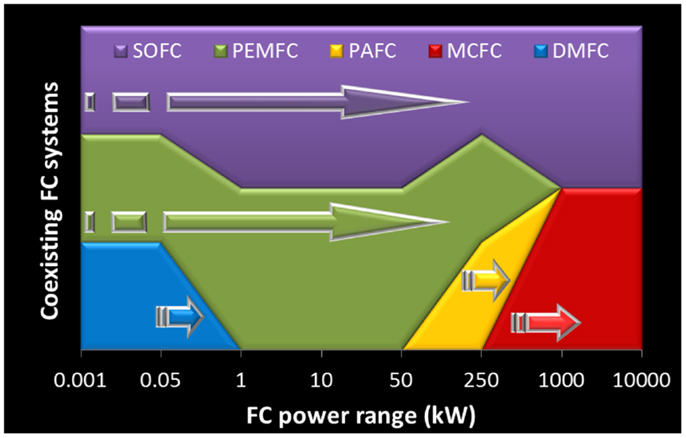
Figure 3. Coexisting fuel cell systems as a function of power (variable scale length for easier visualization). Arrows depict the range of announced power performance available in the market. Target fuel cell power range and remaining information adapted from Steele and Heinzel (2001), Carter et al. (2012), and Carter and Wing (2013).
As complex systems involving also mass transport, heat management, and electrical power conversion, the design of individual cells and systems is equally important with respect to performance. Throughout the years we had cycles of interest in flat, tubular, mixed flat, and tubular designs, besides interesting attempts addressing specific possibilities of operation namely as single chamber fuels cells. Obviously, not all designs are adequate for all types of fuels cells. The dominant preference for flat cells, due to the availability of suitable mass production technologies for polymers, metals, ceramics, and even composites, still leaves an open range of possible cell concepts. Innovative cell and system design try to circumvent the existing materials constraints.
A Materials Challenge
Fuel cells involve ionic transport and electrochemical reactions where electrolyte and electrode properties play a major role in cell performance. However, a range of complementary materials is also needed to ensure equally relevant functions like charge transport and/or cell interconnection, sealing, or catalysis. Also, the expected life-time of such functional materials might reach many thousands of hours, without degradation of individual properties or interfaces. These demanding targets should be achieved with cheap materials and mass production technologies. This explains the core role of materials science and engineering in FC progress. In the following paragraphs a few developments will be highlighted.
Electrolytes must possess specific combinations of chemical and physical properties, also adequate shapes if not self-sustained, as in the case of liquid electrolytes, where a matrix is needed to provide the required dimensional stability. Here, the matrix porosity and pore size distribution must be properly designed to ensure suitable pore filling and ideal contact with the electrode material and gas. In the case of solid electrolytes, the apparently simpler solution provided by the possible adequacy of single-phase dense membranes must again correspond to a suitable balance between mechanical stability and ionic transport. Interestingly, the two requirements of mechanical stability and ionic transport cross the entire range of electrolyte membranes where we need a backbone with dimensional/mechanical stability and also (regions of) high ionic mobility. For different types of electrolytes, these requirements are attained following distinct strategies. Even when both functions can be obtained from one single material (polymers or ceramic electrolytes) we see alternative possibilities being exploited, namely using composites, including intimate mixture of two phases or even layered materials. Composites tend to provide a tunable combination of properties, but processing technologies often become more complex and expensive. Also, new compatibility problems are frequently introduced in this manner. There are, yet, no final and definitive solutions.
A deeper understanding of ionic motion in polymers and oxides provides nowadays a comprehensive guidance to search new ionic conductors in these completely distinct families of materials. Polymers with dominant protonic conduction but with higher thermal and dimensional stability, either related to classical Nafion membranes or with alternative compositions (e.g., functionalized non-fluorinated membranes), are intensively searched (Kreuer et al., 2004). One of the driving ideas is to obtain in distinct regions of the membrane the required dimensional stability and protonic transport. More recently, polymer membranes with dominant OH− conduction equally entered the race (Thomas et al., 2012). Alkaline conditions are especially interesting for being compatible with the utilization of non-precious metal catalysts at low temperature.
Recent progress in the field of ceramic oxide-ion and protonic conductors moved away from the classical fluorite-related and perovskite-type structures, respectively. Complex oxide structures with bendable constituent blocks and polarizable cations show highly promising performance in the case of oxide-ion conductors (Tealdi et al., 2010). However, state of the art technological developments still rely on conservative zirconia or ceria-based electrolytes. The long-term stability of newly developed ceramic electrolytes and adequacy of electrode materials still deserve considerable attention.
Electrode materials are asked to possess the required electro-catalytic properties for fast electrode kinetics, also high electronic conductivity for charge transport. Since reactants/products of reaction must be transported to/from the electrode/electrolyte contacts, electrode porosity must be designed to ensure adequate mass and charge transport, as well as maximum length of active reaction sites per unit surface area. If mixed ionic and electronic conductors, electrode materials are able to delocalize the electrode reaction from the electrode/electrolyte/gas interface, lowering electrode polarization losses. Composite electrodes try to group the required combination of properties, often unattainable in a single-phase material. Again, in different systems we find parallel research trends focusing on single-phase or composite electrodes.
In PEMFCs, lowering the noble-metal loads (usually platinum-based) in electrode materials due to their high cost is one of the critical issues. As alternatives, besides the already mentioned attempt to move to OH− conducting membranes, large effort is dedicated to electrode materials compatible with the PEMFC acidic environment. Research trends range from simple alloying of platinum with cheaper metals, exploitation of semiconducting metal oxide particles and tailoring of high surface area carbon supports, to the search of chemically distinct alternative non-precious metal-based materials. Fe- or Co-N4 macrocycles such as porphyrin complexes are amongst the most promising examples of non-precious metal-based electrocatalysts for the oxygen reduction reaction (Chen et al., 2011).
Improved long-term stability of MCFC electrodes, either obtained from new combinations of materials or from tuned electrolyte composition, is quite important (Cassir et al., 2012; Kulkarni and Giddey, 2012). In fact, while several alloys, coatings or even entire ceramic electrodes might demonstrate significant endurance, the adjustment of the acidic-basic characteristics of the molten carbonates (with additives) has a huge influence on the stability of electrode materials. In the case of MCFCs we have one of the most demanding requirements on chemical compatibility between electrode and electrolyte.
Materials science and engineering is crucial to solve most pending problems and challenges. We are now able to understand and attempt exploiting the compositional, structural, and microstructural design of materials performance at unprecedented levels. Starting at the unit cell size and moving through the multi-nanometer to the multi-micrometer length scale, with adequate doping, tuning of structural features, formation of core-shell, or even composite microstructures, we can adjust a large range of properties. As elucidating examples of induced mixed ionic and electronic conduction, with a variety of potential applications, we recall here the classical doping effects in fluorite-type solid solutions like ZrO2-CeO2-Y2O3 (Cales and Baumard, 1984) to generate both oxide-ion and electronic conductivity. Moving to other length scales, we have recent examples of tunable ionic and electronic conductivity based on structural or microstructural effects in perovskite-type oxides like (Ba,Sr)(Co,Fe,Mo)O3-δ (Demont et al., 2013) or (La,Sr)(Ga,Mg)O3-δ (Gomes et al., 2006), and also in conventional cermets used as SOFC anodes (Iwaia et al., 2010). In the first case, formation of distinct nanosized domains inside grains yields the unusual combination of properties. In the second case, core-shell type microstructures offer distinct pathways for dominant ionic and electronic transport. Lastly, in cermets, phases with distinct characteristics provide the required combined performance. Schematic representations of these examples are provided in Figure 4. Heterostructures, where distinct layers of materials with nanosized thickness are assembled, could also be invoked here for providing unique ionic and electronic transport properties (Schichtel et al., 2009). Overall, the capability for property tuning extended considerably in the last years from classical simple compositional and microstructural effects in single-phase materials or composites. Some of the most recent results open new possibilities for the design of materials for performance.
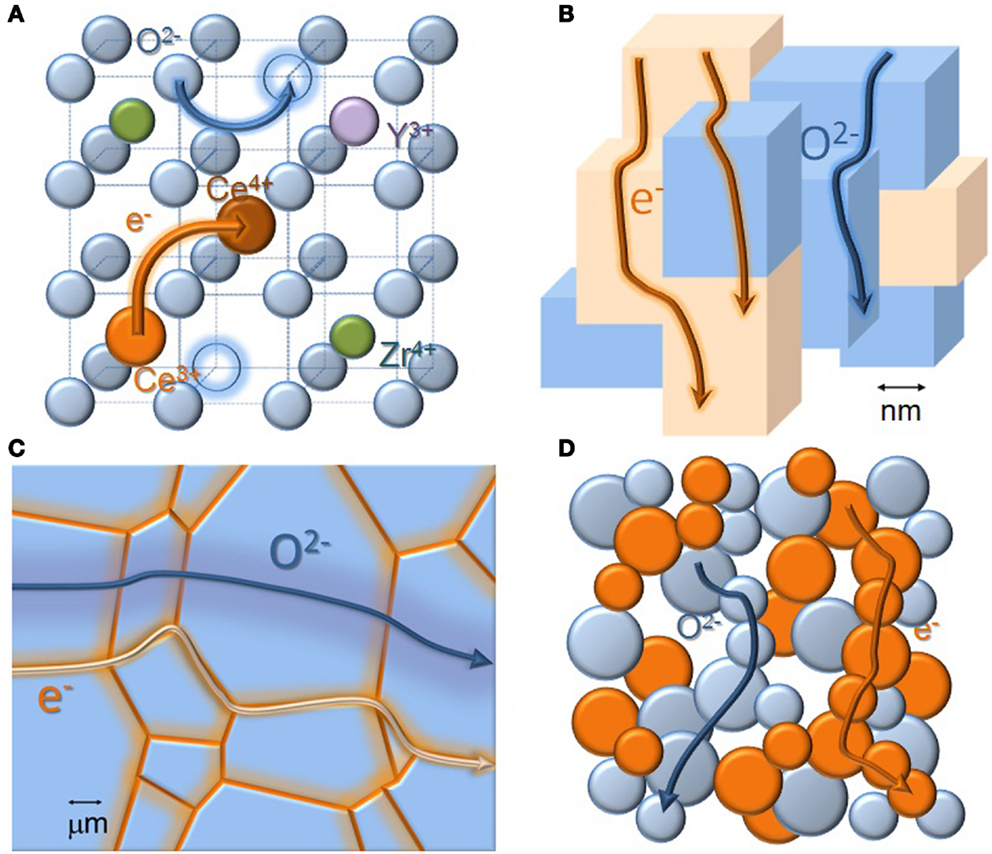
Figure 4. Property tuning at all length scales. (A) Classical compositional tools to tune the ionic and electronic conductivity in doped zirconia-based electrolytes. Yttrium-doping can be used to generate mobile oxide-ion vacancies (open circles). Doping with cerium enhances the electronic conductivity under specific ranges of oxygen partial pressure (small polaron hopping between C3+ and Ce4+) (Cales and Baumard, 1984). Arrows indicate neighboring lattice positions involved in defect motion. For different materials, different dopants open the possibility of multiple property adjustments: electrical transport, thermal expansion, chemical stability, etc. (B) Multi-nanometer domains inside larger oxide grains, with distinct electrical transport characteristics, namely dominant electronic or mixed ionic and electronic conductivity. These nano-domains are formed due to cation ordering in specific perovskite-type oxides like (Ba,Sr)(Co,Fe,Mo)O3-δ. Drawing inspired in (Demont et al., 2013). Possible tuning of properties at nanosized level has an obvious immense potential in fuel cell and allied applications. (C) Mixed conduction induced by selective (Fe) grain boundary doping of one (La,Sr)(Ga,Mg)O3-δ-type perovskite, dominant oxide-ion conductor (Gomes et al., 2006). Core-shell type microstructures provide the possibility of tuned properties at the grain-size scale without massive utilization of mixed valence cations, a situation seldom exploited up to now. (D) Scheme of mixed oxide-ion and electron transport in a typical porous anode cermet used in SOFCs. 3D imaging and modeling of such microstructures can be used to improve the performance of all types of composite electrodes (Iwaia et al., 2010).
Looking at a completely distinct strategy in the field of FCs, we find the biological FCs (also called biofuel cells). In these systems electrochemical reactions involve microbes or enzymes located either in one or in both electrode compartments (Rabaey and Verstraete, 2005; Zhao et al., 2009). Considering the inherent characteristics of such FCs, they are likely to become competitive for some niche applications involving sensing and monitoring of specific environments. Here, the optimization of performance depends strongly on advances in the biological and electrochemical understanding of such complex systems, another challenging avenue of research.
Complementary Technologies
Research on FCs is also highly important for being the source of inspiring ideas for allied technologies where ionic transport or mixed ionic and electronic transport are exploited in distinct manners. Electrochemical membranes with one dominant or multiple charge carriers can be used in applications ranging from water electrolysis to partial oxidation of methane (POM) or even separation of carbon dioxide. We could as well mention here the electrochemically assisted synthesis of a variety of other chemicals and separation of oxygen and hydrogen, amongst other uses. In many of these applications we are well behind the present stage of FC development and research needs are enormous. A few examples are detailed in the following paragraphs.
Hydrogen production from water electrolysis can be obtained from a FC system simply changing the operating mode from galvanic to electrolytic, either using proton or oxide-ion conductors. The overlap in materials and concepts for both applications is thus inevitable. As example, known FC anodes also reveal promising performance as cathodes in the electrolysis mode (Yang and Irvine, 2008). However, since reactions are reversed, the electrodes will be unevenly displaced from equilibrium conditions when operating in galvanic or electrolytic modes and new constraints and/or benefits must be assessed. The need and potential for electrode optimization is enormous.
Partial oxidation of methane is crucial for the chemical conversion of natural gas into a variety of high added value chemicals, namely hydrogen. SOFCs can be operated under controlled conditions to obtain simultaneously the POM and electrical power (Zhan et al., 2006). Nevertheless, the relative advantage of a classical SOFC design for the POM is partly conditioned by the sophistication of the entire system when compared to the simplicity of single-phase mixed conducting membranes. Interestingly, the ideal mixed conducting characteristics of SOFC electrode materials resemble the membrane requirements for the POM. However, a SOFC electrode is expected to work under modest oxygen activity gradients, since cathodic and anodic FC chambers are isolated. On the contrary, ceramic membranes for the POM must be exposed to large oxygen activity gradients (air versus methane), often responsible for asymmetric chemical expansion of membrane materials with subsequent mechanical failure. Finding the adequate compromise between electrical properties and chemical (redox) stability is quite puzzling.
In carbon dioxide separation membranes, the oxide-ion conductivity of ceramic electrolytes is combined with the carbonate-ion conductivity of molten alkaline carbonates. Counter-flow of oxide and carbonate-ions provides the required net transport of CO2 (Li et al., 2009). Nevertheless, the ionic conductivity of both phases should match for maximum process efficiency, which is only possible at quite high temperatures, given the distinct temperature dependencies of ionic conductivity in oxide-ion conductors and molten carbonates. Few ceramic oxide-ion conductors survive in a molten carbonate environment. The exact role of other ionic species present in the melt still needs to be fully elucidated.
Final Remarks
Progress in materials science and engineering is driving most changes in the field of FCs and allied technologies, but there is still a long way to go. Compositional, structural, and microstructural design of FC materials is yielding unparalleled performance levels based on an enhanced understanding of materials characteristics. This also explains the publication of thousands of manuscripts every year on FC related subjects, a trend that is growing and also found with respect to the number of registered patents. This section, dedicated to FCs research, under the journal Frontiers in Energy Research is committed to play a significant role in this challenge.
References
Cales, B., and Baumard, J. F. (1984). Mixed conduction and defect structure of ZrO2-CeO2-Y2O3 solid solutions. J. Electrochem. Soc. 131, 2407–2412. doi: 10.1149/1.2115267
Carter, D., Ryan, M., and Wing, J. (2012). The Fuel Cell Industry Review 2012. Fuel Cell Today. Available at: http://www.fuelcelltoday.com/analysis/industry-review
Carter, D., and Wing, J. (2013). The Fuel Cell Industry Review 2013. Fuel Cell Today. Available at: http://www.fuelcelltoday.com/analysis/industry-review
Cassir, M., McPhail, S. J., and Moreno, A. (2012). Strategies and new developments in the field of molten carbonates and high-temperature fuel cells in the carbon cycle. Int. J. Hydrogen Energy 37, 19345–19350. doi:10.1016/j.ijhydene.2011.11.006
Chen, Z., Higgins, D., Yu, A., Zhang, L., and Zhang, J. (2011). A review on non-precious metal electrocatalysts for PEM fuel cells. Energy Environ. Sci. 4, 3167–3192. doi:10.1039/c0ee00558d
Demont, A., Sayers, R., Tsiamtsouri, M. A., Romani, S., Chater, P. A., Niu, H., et al. (2013). Single sublattice endotaxial phase separation driven by charge frustration in a complex oxide. J. Am. Chem. Soc. 135, 10114–10123. doi:10.1021/ja403611s
Evans, A., Bieberle-Hütter, A., Rupp, J. L. M., and Gauckler, L. J. (2009). Review on microfabricated micro-solid oxide fuel cell membranes. J Power Sources 194, 119–129. doi:10.1016/j.jpowsour.2009.03.048
Gomes, E., Figueiredo, F. M., and Marques, F. M. B. (2006). Mixed conduction induced by grain boundary engineering. J. Eur. Ceram. Soc. 26, 2991–2997. doi:10.1016/j.jeurceramsoc.2006.02.017
Iwaia, H., Shikazono, N., Matsui, T., Teshima, H., Kishimoto, M., Kishida, R., et al. (2010). Quantification of SOFC anode microstructure based on dual beam FIB-SEM technique. J. Power Sources 195, 955–961. doi:10.1016/j.jpowsour.2009.09.005
Kreuer, K. D., Paddison, S. J., Spohr, E., and Schuster, M. (2004). Transport in proton conductors for fuel-cell applications: simulations, elementary reactions, and phenomenology. Chem. Rev. 104, 4637–4678. doi:10.1021/cr020715f
Kulkarni, A., and Giddey, S. (2012). Materials issues and recent developments in molten carbonate fuel cells. J. Solid State Electrochem. 16, 3123–3146. doi:10.1007/s10008-012-1771-y
Li, Y., Rui, Z., Xia, C., Anderson, M., and Lin, Y. S. (2009). Performance of ionic-conducting ceramic/carbonate composite material as solid oxide fuel cell electrolyte and CO2 permeation membrane. Catal. Today 148, 303–309. doi:10.1016/j.cattod.2009.08.009
Rabaey, K., and Verstraete, W. (2005). Microbial fuel cells: novel biotechnology for energy generation. Trends Biotechnol. 23, 291–298. doi:10.1016/j.tibtech.2005.04.008
Schichtel, N., Korte, C., Hesse, D., and Janek, J. (2009). Elastic strain at interfaces and its influence on ionic conductivity in nanoscaled solid electrolyte thin films-theoretical considerations and experimental studies. Phys. Chem. Chem. Phys. 11, 3043–3048. doi:10.1039/b900148d
Spendelow, J., and Marcinkoski, J. (2012). Fuel Cell System Cost – 2012, DOE Fuel Cell Technologies Program Record. Available at: http://www.hydrogen.energy.gov/pdfs/12020_fuel_cell_system_cost_2012.pdf
Steele, B. C. H., and Heinzel, A. (2001). Materials for fuel-cell technologies. Nature 414, 345–352. doi:10.1038/35104620
Tealdi, C., Mustarelli, P., and Islam, M. S. (2010). Layered LaSrGa3O7-based oxide-ion conductors: cooperative transport mechanisms and flexible structures. Adv. Funct. Mater. 20, 3874–3880. doi:10.1002/adfm.201001137
Thomas, O. D., Soo, K. J. W. Y., Peckham, T. J., Kulkarni, M. P., and Holdcroft, S. (2012). A stable hydroxide-conducting polymer. J. Am. Chem. Soc. 134, 10753–10756. doi:10.1021/ja303067t
U.S. Department of Energy’s Office of Energy Efficiency and Renewable Energy. (2012). Fuel Cell Technologies Program Multi-Year Research, Development, and Demonstration Plan. Available at: http://www1.eere.energy.gov/hydrogenandfuelcells/mypp/index.html
Yang, X., and Irvine, J. T. S. (2008). (La0.75Sr0.25)0.95Mn0.5Cr0.5O3 as the cathode of solid oxide electrolysis cells for high temperature hydrogen production from steam. J. Mater. Chem. 18, 2349–2354. doi:10.1039/b800163d
Zhan, Z., Lin, Y., Pillai, M., Kim, I., and Barnett, S. A. (2006). High-rate electrochemical partial oxidation of methane in solid oxide fuel cells. J. Power Sources 161, 460–465. doi:10.1016/j.jpowsour.2006.04.139
Keywords: fuel cells, mixed conducting membranes, CO2 separation membranes, partial oxidation of methane, steam electrolysis
Citation: Marques FMB (2013) Grand challenges in fuel cells: materials issues at all length scales. Front. Energy Res. 1:5. doi: 10.3389/fenrg.2013.00005
Received: 28 October 2013; Accepted: 06 November 2013;
Published online: 21 November 2013.
Reviewed by:
Ugo Bardi, Università di Firenze, ItalyCopyright: © 2013 Marques. This is an open-access article distributed under the terms of the Creative Commons Attribution License (CC BY). The use, distribution or reproduction in other forums is permitted, provided the original author(s) or licensor are credited and that the original publication in this journal is cited, in accordance with accepted academic practice. No use, distribution or reproduction is permitted which does not comply with these terms.
*Correspondence:Zm1hcnF1ZXNAdWEucHQ=