- 1Key Lab of Pulp and Paper Science and Technology of Ministry of Education, Qilu University of Technology, Jinan, China
- 2State Key Lab of Pulp and Paper Engineering, South China University of Technology, Guangzhou, China
In the case of development and utilization of bio-oils, a quantitative chemical characterization is necessary to evaluate its actual desired characteristics for downstream production. This paper describes an analytical approach for the determination of families of lightweight chemicals from bio-oils by using GC-MS techniques. And on this basis, new explorations in the field of influence factors, such as feedstocks, pyrolysis temperatures, and low-temperature pretreatment, on the composition and products yields of bio-oil were further investigated. Up to 40% (wt.%) of the bio-oil is successfully quantified by the current method. Chemical functionalities in the bio-oil correlate strongly with the original feedstocks because of their different chemical compositions and structure. Pyrolysis temperature plays a vital role in the yields of value-added compounds, both overall and individually. Higher temperature favored the generation of small aldehydes and acids, accompanied by a reduction of phenols. The optimal temperatures for maximum furans and ketones yields were 520 and 550°C, respectively. The low-temperature pretreatment of biomass has a good enrichment for the lightweight components of the bio-oils. In this case, much higher amounts of compounds, such as furans, ketones, and phenols were produced. Such a determination would contribute greatly to a deeper understanding of the chemical efficiency of the pyrolysis reaction and how the bio-oils could be more properly utilized.
Introduction
Among the biomass thermochemical conversion processes and technologies, pyrolysis is a particularly promising route to produce liquid fuels and value-added chemicals from solid biomass feedstock and is now widely studied (Bridgwater et al., 1999; Dinesh et al., 2006). The resulting “pyrolysis oil” or “bio-oil” can be obtained with yields up to 70–80 wt.% (dry feed basis) depending on the relative amount of cellulose and lignin in the wood material. As bio-oil is significantly denser than its parent biomass, it can be more economically and efficiently transported to a centralized location to be used as a feedstock for further processing, such as by gasification or Fischer–Tropsch synthesis, etc. to produce transportation fuels (Demirbas, 2009a,b; Lu et al., 2009).
Bio-oils are composed of differently sized molecules derived primarily from the depolymerization and fragmentation reactions of three key biomass building blocks, i.e., cellulose, hemicellulose, and lignin, resulting in its composition and properties of considerable difference from those of petroleum-based fuel oils (Yang et al., 2007). The physical properties of bio-oils are well-described in the literature (Dobele et al., 2007; Abdelnur et al., 2013). Despite its dark brown viscous appearance, elemental analysis of bio-oil reveals that it contains relatively little sulfur and nitrogen, but has a high oxygen content, typically near 40 wt.% and as high as 50 wt.% including water. Bio-oils are highly oxygenated, complex mixtures, viscous, relatively unstable, and susceptible to aging. The lower heating value (LHV) of bio-oils is only 40–45% of that exhibited by hydrocarbon fuels. The high water content and the low LHV are detrimental for ignition. Moreover, organic acids in the bio-oils are highly corrosive to common construction materials. These inherent drawbacks make it hardly available to fuel application directly (Helena and Ralph, 2001; Mckendry, 2002).
Another point of view (Jean et al., 2001) is that industrial production of bio-oil should focus in the short term on its utilization for the manufacture of higher value chemicals and/or materials other than fuels. Recent detailed analyses have shown that pyrolysis bio-oils contain more than 400 compounds. And these chemical functionalities in the bio-oil correlate strongly with the feed composition and the pyrolysis processing conditions. Even though it remains a challenge to identify every compound in a bio-oil sample, a large number of previous studies have been consistent with the qualitative analysis of the bio-oils. From a chemical point of view, bio-oil is an extremely complex mixture of organic components, including various types of oxygen-containing organic compounds derived from biomass components of cellulose, hemicellulose, and lignin pyrolysis, such as organic acids, esters, alcohols, aldehydes, ketones, furans, phenols, and dehydrated carbohydrates (Serdar, 2004; Demirbas, 2009a,b).
Because of the complexity, some simplified analytical methods were used to characterize bio-oil. Chemical characterization of pyrolysis oils has generally been based on the fractionation of the oils into different classes of chemical functionality by using solvent extraction, adsorption chromatography, molecular distillation, etc. and then the different fractions obtained were further characterized using more than one analytical techniques, such as GC-MS, HPLC, thermogravimetric techniques, gel permeation chromatography (GPC), etc. with focusing on its different chemical information (Kai et al., 1998; Chiaberge et al., 2014; Lindfors et al., 2014). According to Meier (1999), typical portions of the important fractions in bio-oils are: around 20 wt.% water, around 40 wt.% GC-detectable compounds, around 15 wt.% non-volatile HPLC detectable compounds, and around 15 wt.% high molar mass non-detectable compounds. Garcia et al. (2007) described an analytical approach to identify the chemical composition of bio-oils in terms of macro-chemical families. The bio-oils were first fractionated using different polar organic solvents, and then the fractions were analyzed by GPC, GC-MS, and elemental analyzer. A thorough description of bio-oil composition as a mixture of water, monolignols, polar compounds with moderate volatility, sugars, extractive-derived compounds, heavy polar and non-polar compounds, MeOH–toluene insolubles, and volatile organic were obtained. Guo et al. (2010) separated bio-oil into three fractions by molecular distillation, i.e., a light fraction, a middle fraction, and a heavy fraction. The chemical composition of the three fractions and the crude bio-oil was analyzed by GC–MS, and the pyrolysis characteristics were measured by a thermogravimetric analyzer coupled with Fourier transform infrared spectroscopy (TG–FTIR). Different physical and chemical characteristics were noted and illustrated among the three fractions. By using nuclear magnetic resonance spectroscopy (NMR), including 1H, 13C, and DEPT spectra, Charles et al. (2009) characterized and compared fast-pyrolysis bio-oils from six different feedstocks. NMR spectroscopy provides important information not only of the kinds of chemicals in bio-oils but also of their relative concentrations, especially for the highly substituted aromatic groups that were not detected by other means.
Although a lot of progress has been made in the field of bio-oil fractionation and the subsequent analysis, most of these studies narrowed their interest to qualitative analysis. Quantitative chemical characterization of bio-oils has always been a challenging undertaking, and the literature on this issue is very scarce apart from a few chemical species were examined and reported. Branca et al. (2003) quantified 40 compounds of bio-oils from low-temperature pyrolysis of wood by the internal standard method, using fluoranthene as internal standard. And the yields of a significant number of compounds on dependence of the reaction temperature and heating rate were also provided. The major compositions of the pyrolysis liquids were considered from acetic acid, hydroxypropanone, hydroxyacetaldehyde, levoglucosan, formic acid, syringol, and 2-furaldehyde. de Wild et al. (2009) analyzed most of lightweight organic species that were representative for typical thermal degradation products from lignocellulosic biomass with GC-MS. The weight of those unknown components was estimated by a semi-quantitative calibration using the GC-data of the internal standards with the nearest retention time on the GC column. The results show that the yields of individual chemicals are generally below 1 wt.% (based on dry feedstock weight), and only certain groups of thermal degradation products like C2–C4 oxygenates and phenols are formed in higher yields up to 3 wt.%. By employing a series of improved analytical methods, the International Energy Agency-European Union (IEA-EU) round robin test was carried out in 12 laboratories with focus on comparing the accuracy of methods to provide instructions for handling and analysis of bio-oils (Meier, 1999; Oasmaa and Meier, 2005). The results showed that even though the repeatability of the physical analyses was good; there were very large quantitative differences between different laboratories for chemical characterization. Relevant researchers thus suggested that proper standard solutions with known amounts of compounds have to be used for quantitative analyses, and a lot of experimental work and methods adjustment should be needed to achieve accurate and consistent results between laboratories.
Based on the above literature review of the research and development advances in studies on pyrolysis liquids, it can be concluded that the present state of knowledge has been focused solely on the fractionation, qualitative characterization, and even quantification was limited to a few species for the optimal conditions of fast pyrolysis (corresponding to maximum yields of bio-oils). However, in the current state of art, an accurate and relatively fast method is urgently needed for a quantitative analyses of the most valuable components of bio-oils. By this method, it may help us to evaluate and determine what kind of bio-oil has particular desired characteristics for downstream production of fuels or chemicals.
The experimental investigations in our present work are therefore set to serve two main purposes: (a) to develop an effective quantitative analysis method for lightweight components of bio-oils by using GC-MS techniques. Thus, yields up to 40 wt.% of the bio-oils can be quantified, and this part usually contains the highest commercial value either used as fuel or chemicals and (b) to determine the yields of a significant number of compounds on dependence of the feedstocks, pyrolysis temperatures, and especially staged pyrolysis conditions, in the view of providing evaluation criteria for the selection of the most appropriate feedstocks and pyrolysis conditions to produce the desired composition and yields of the products.
Materials and Methods
Materials
Four kinds of biomass feedstocks, i.e., bagasse, corncob, spruce, and pine, were selected as pyrolysis materials. The bagasse was collected from a sugar cane plant located in Jiangmen, China. The corncob was obtained from a farm in Changzhi, China. The spruce and pine wood used in this study were purchased from a local sawing mill in Guangzhou, China. All four feedstocks were first air dried and grounded, and then were sieved to a mean particle size of 0.180–0.425 mm. Ultimate analysis of the samples was determined by using an elemental analyzer (Vario EL, ELEMENTAR, Germany). For proximate analysis, the ash content and volatile content were determined based on Chinese National Standards GB/T 2677.3-1993 and GB/T 212-2001, while fixed carbon was calculated by difference. The acid insoluble lignin (klason lignin) and acid soluble lignin were determined based on GB/T2677.8-1994 and GB/T10337-2008, respectively. The extractives (benzene/ethanol 2:1, v/v), hemicellulose and cellulose content were analyzed according to GB/T10741-2008 and methods in reference (Shi and He, 2003). The results were shown in Table 1. All these samples were dried at 105°C for 8 h in an oven to about 6% moisture content before the pyrolysis experiment.
Preparation of Bio-Oils
Bio-Oils from Direct Pyrolysis
Direct fast pyrolysis of biomass was carried out in a self-designed fluidized-bed reactor in Guangzhou Institute of Energy Conversion. The schematic drawing of the fluidized-bed reactor was previously reported (Chang et al., 2011; Zheng et al., 2012). Briefly, the reactor uses nitrogen as the carrier gas, quartz sand as bed material, a screw feeder for feeding biomass, and a thermocouple for testing the reaction temperature that is heated by electricity. All the reaction system was online controlled by a computer. After reaction, the pyrolysis vapors were purged by nitrogen through a two-stage gas-solid cyclone separator to remove ashes and solid particles, then the vapors were condensed in a tubular heat exchanger, in which most of the light components were condensed and collected (Liquid 1) while the remaining volatiles were further isolated by a two-stage gas–liquid cyclone separator to obtain the Liquid 2. The mixed gases were further subjected to an absorption device, in order to ensure complete absorption of the liquid components and to purify the pyrolysis gases. Liquid 1 and Liquid 2 were combined and designated as bio-oil for further analysis. All pipes before tubular heat exchanger as well as the gas–solid cyclone separator were insulated by using heating tape to avoid the pre-condensing of the pyrolysis vapors.
After a number of preliminary experiments, the following optimum pyrolysis parameters were used: the feed rate was 10 kg h−1, the nitrogen flow was 11 m3 h−1, the particle size of quartz sand was 60–80 meshes, and its density was 2.6 g cm−3 with the bed height of 12 cm. The direct pyrolysis was performed at 480, 500, 520, 550, and 580°C, respectively, to explore the effect of pyrolysis temperature on the composition of bio-oils.
Bio-Oils from Staged Pyrolysis
Bio-oils, obtained by conventional rapid pyrolysis, are usually multicomponent mixtures of carbohydrate and lignin thermal decomposition products with low pH, high viscosity, and high water content, which limit its large-scale application as fuel. Based on different thermal stabilities of the main biomass constituents, staged pyrolysis, a new pyrolysis-based conversion route, was designed and applied to improve the quality of bio-oils and to generate more value-added chemicals from biomass. In the present work, staged pyrolysis experiments were first conducted with pine in an auger reactor at the temperature range of 260–320°C, and then the solid residues obtained were further pyrolyzed in a fluidized-bed reactor (10 kg h−1) at moderate temperature of 520°C. As the chemical composition and pyrolysis behavior of the resulting torrefied biomass (torrefaction treatment in the range of 260–320°C) were examined in detail in the previous work (Chang et al., 2012), what we now focus on is the impact of low-temperature pretreatment on changes of the composition of bio-oils as well as the enrichment effect on high value-added chemicals.
Low-temperature pyrolysis of pine was conducted in a stainless steel auger (screw) reactor, which mainly consists of a feed bunker (capacity of 6 kg), an electrically heated (3.2 kW) auger pyrolysis reactor, a collection bin, a temperature control unit, and a cooling system. The torrefaction temperatures were performed at 260, 280, 300, and 320°C, respectively. When the reactor reached the set temperature, the samples were transported down the length of the reactor tube [600 mm (L) × 100 mm (I.D.)] at a fixed speed (2 kg h−1) by means of a screw to maintain the residence time of the sample in the reactor pipe for 10 min. During the process, a nitrogen gas flow of 7 L min-1 was used as a carrier gas to eliminate the presence of oxygen and remove the volatiles out of the reactor. The torrefied samples were then collected in the collection bin and were used as feedstock for the second stage pyrolysis in a fluidized-bed reactor.
The second stage pyrolysis temperature was 520°C, at which the pine got the maximum bio-oil yield. The other operation parameters were consistent with that of the direct pyrolysis. Each experiment was repeated three times under the same conditions to confirm the reproducibility of each test and to obtain accurate results.
Analytical Methods
Qualitative Analysis
Qualitative analysis of bio-oils was conducted using a gas chromatography–mass spectrometer (GC–MS, 7890A-5975C, Agilent Technology, USA). About 200 mg bio-oils were dissolved in 5 mL of acetone. Before injection, diluted samples were first dehydrated with 1 g anhydrous sodium sulfate in a beaker, and then filtered through a 0.22 μm syringe-driven filter. The chromatographic separation was performed using a HP-INNO Wax capillary column (30 m × 0.25 mm × 0.25 μm). Helium (99.9995%) was used as carrier gas at a flow rate of 1 mL min−1. The injector (7683B ALS) and the GC–MS interface were kept at a constant temperature of 250°C. A sample volume of 1 μL was injected in the split mode with a split ratio of 20:1. The GC oven temperature ramps for the work were as follows: begin heating at 50°C that was first held for 2 min, and then raised to 90°C at a rate of 10°C/min, and after raised to 120°C at a rate of 4°C/min, and then raised to 230°C at a rate of 8°C/min, and this final temperature was held for 10 min.
The mass selective detector was operated in electron impact (EI) ionization mode. MS source and MS quadrupole temperatures were kept at 230 and 150°C, respectively. EI ionization energy was 70 eV and an m/z range from 33 to 500 was scanned. Solvent cut time of 2.8 min was used to avoid solvent influence. The identification of the peaks was based on computer matching of the mass spectra with the NIST 08 MS library and/or on the retention times of known species injected in the chromatographic column.
Quantitative Analysis
From the results of the qualitative analysis, the major compositions that displaying a relatively high content (based on the area%) in the bio-oils were identified. The standard compounds of these major compositions (19 compounds) were purchased from Sigma-Aldrich and directly used for qualitative or quantitative analysis.
These major 19 compounds of bio-oil were quantified by the external standard method. For each of the quantified compounds, calibration curves were prepared by injection of five standard solutions (40, 200, 400, 1000, and 2000 μg mL−1). For quantitative analysis of the other bio-oil compositions, several typical compounds, i.e., 1-hydroxy-2-propanone, acetic acid, furfural, and 2-methoxy-phenol were further employed as internal standards for quantifying ketones, acids, furans, and phenols compounds of bio-oils, respectively. The GC test parameters were the same as the above qualitative analysis. Injections of each standard or bio-oil samples were made at least in triplicate until acceptable peak reproducibility was achieved by overlapping and comparison of TIC. The product yield was then expressed as the mean of three replications ± SD for each sample are shown in Tables in Supplementary Material.
Evaluation by Standard Addition Method
Considering a situation that the bio-oil sample may have a matrix effect, which may also contribute to the analytical signals and affect the results, the standard addition method was used for quantitation and comparison to further evaluate the effectiveness and impact of the current calibration curve approach.
Experimentally, the chromatogram of the diluted pine bio-oil was recorded first. Then, a known and different amounts of each standard of interest (10 standards were tested) were added and all were diluted to the same volume as the blank one. The samples were tested under the same GC–MS conditions and the chromatogram was recorded. Based on the increase in the peak area and the results plotted, the original concentration of 10 compounds in bio-oil can be computed, which were designated as the actual concentration. The calculating concentration of 10 compounds was obtained based on the chromatogram of the original diluted pine bio-oil and the established external standard calibration curves. Comparison of actual concentration and calculating concentration of 10 compounds and the resulted relative error were listed in Table S1 in Supplementary Material, from which thorough investigation of the influence of the methodology on the quantitation results was available.
Results
Qualitative Analysis and Quantitative Approach
Although new approaches for analysis and characterization of the composition and structure of bio-oils are still being explored, especially for the relatively heavy components, such as dimers or trimers, it has reached a consensus that the main components of bio-oil is a variety of small molecules with oxygen-containing functional groups such as aldehydes, ketones, carboxylic acids, furans, phenols, dehydration carbohydrates, etc. (Dobele et al., 2007; Hyeon et al., 2010). Figure 1 shows the total ion chromatogram of bio-oil from pine pyrolysis at 520°C, and the main compositions (peak area percentage >1%) corresponding labels in Figure 1 were identified by computer matching and listed in Table 2.
From the qualitative analysis results, it could be seen that acetic acid is the principal acidic components of bio-oil, and furfural and furfuralcohol are major furans products. Ketones mainly composed of 1-hydroxy-2-propanone and a large number of cyclopentanones and cyclopentadiones. Levoglucosan, a typical pyrolysis product from cellulose pyrolysis, represents incomplete cracking of carbohydrates. A large number of methylated or methoxylated phenolic compounds that derived from lignin pyrolysis were also detected, such as 2-methoxy-phenol, 2-methoxy-4-methyl-phenol, 2-methoxy-4-vinylphenol, eugenol, vanillin, etc. and each of them occupies a relatively large percentage.
Based on an overall consideration of the qualitative results of bio-oils from different raw materials pyrolysis, 19 compounds that presented abundantly were identified and selected as standards, i.e., 1-hydroxy-2-propanone, acetic acid, furfural, 2-furanmethanol, 5-hydroxymethylfurfural, 3-methyl-1,2-cyclopentanedione, phenol, 3-methyl-phenol, 4-methyl-phenol, 2-methoxy-phenol, 2-methoxy-4-methyl-phenol, 4-ethyl-phenol, eugenol, (E)-isoeugenol, vanillin, 1,2-benzenediol, 3-methyl-1,2-benzenediol, 2,3-dihydro-benzofuran, and levoglucosan. The standard curves results show that at the concentration range of the first four standard solutions, i.e., from 40 to 1000 μg mL−1, calibration lines of each compound was excellent linear correlation (R2 ≥ 0.992). While the concentration of the standard was above 2000 μg mL−1, the calibration lines of some compound began to seem like quadratic polynomial. So the concentration range of 40–1000 μg mL−1 was used to prepare the injection samples to ensure the accuracy of the quantification.
There was a big difference in the coefficient of linear calibration curve of different compounds (see Figure S1 in Supplementary Material), showing the differences of quantitative correction factor from the chromatogram concept, such as that of 1-hydroxy-2-propanone, furfural, and phenol. Therefore, for chemical quantitation of bio-oil compositions, it might be necessary to calibrate the chromatographic systems by preparing standard solutions with as many of known standard compounds as possible. On the other hand, the linear coefficient of the standard compounds with similar structure and chemical properties had little difference, 2-methoxy-phenol and 2-methoxy-4-methyl-phenol, for example. This provides the basis of quantitation of other bio-oil components by using selected compound as internal standards.
Effect of Biomass Feedstock
After a large number of fluidized-bed pyrolysis experiments and the corresponding process adjustment and optimization, the bio-oils from bagasse, corncob, spruce, and pine pyrolysis that with the maximum yield at 500, 520, 520, and 520°C, respectively, were qualitatively and quantitatively analyzed and compared. The content comparison of bio-oils from different feedstock is shown in Figure 2. The identification and quantitation results of each single component are listed in Table S2 in Supplementary Material.
It can be seen from the results that the total lightweight organic components quantified by gas chromatography were 10–20 wt.% (yields always expressed as percent of the bio-oil mass). Among these, bio-oils from grasses material pyrolysis contain relatively low organic content, while that of spruce and pine pyrolysis oils have higher organic content. These differences in both major categories and each single compound content of the bio-oils may attribute to the differences in chemical composition and structure of the biomass feedstocks (Akwasi et al., 2008; Lv and Wu, 2012). Herbaceous biomass generally contains more hemicellulose and less lignin than woody biomass, resulting in more non-condensable gaseous products. In addition, the mineral matter of biomass, in combination with the organic composition, plays an important role in pyrolysis product yields and distribution (Raveendran et al., 1995). Higher mineral salts (ash content) may accelerate secondary depolymerization of pyrolysis volatiles and lead to the formation of low molecular gas species (Pushkaraj et al., 2010). Thus, the over yields of GC-detectable products from corncob and bagasse pyrolysis bio-oil were lower than that of spruce and pine.
On the whole of Figure 2, the major categories of four kinds of bio-oils were acids, ketones, phenols, and furans, followed by anhydrosugars, while alcohols, aldehydes, and esters were relatively low. The major organic acid was acetic acid, and it usually possessed the largest share. Bagasse bio-oil had the highest acetic acid content of 4.8 wt.% (Table S2 in Supplementary Material), while acetic acid content of spruce and pine pyrolysis oil was relatively low, around 2.3 wt.%. It has been accepted that the formation of acetic acid was mainly due to the breakage and removal of acetyl groups that originally linked to the xylose unit on C-2 position, and second, attributed to the ring-scission of uronic acid residues after the elimination of the carbonyl and O-methyl groups (Lv et al., 2010). Therefore, the differences in the content and the chemical structure of hemicellulose are the main cause of differences in acetic acid content of bio-oil. It had been noted that the acetyl content of softwood was about 1%, while that of hardwood and grasses was between 3 and 6% (Badal, 2003). The acetyl content of bagasse and corncob was higher than that of spruce and pine, resulting in higher acid content in pyrolysis bio-oil.
All the four feedstocks pyrolysis produced a large proportion of ketones, of which the total content was about 3–4.5 wt.%. And among these, 1-hydroxy-2-propanone has the highest yield and could reach up to 2.2 wt.%. The formation of small molecule ketones was complicated, while the cyclopentanones and cyclopentenones, whose molecular weight were a little larger, were mainly originated from the decomposition of sugar units and then recombination of the opened bonds. All these ketones could be derived from the pyrolysis of either cellulose and/or hemicellulose.
Furans, a common class of substances in bio-oil, can be attributed mainly to holocellulose decomposition. Although both cellulose and hemicellulose pyrolysis can produce furan compounds, our previous work has shown that hemicellulose definitely makes the greatest contribution to the formation of furfural while cellulose is more dedicated to the products of hydroxymethylfurfural and 2-furylmethanol (Lv et al., 2013). From the quantitative results, corncob pyrolysis oil has the highest content of furfural (0.5 wt.%), which is due to the highest hemicellulose content in corncob. The most abundance of 2-furylmethanol and hydroxymethylfurfural appeared in pine pyrolysis oil.
The identified and quantified anhydrosugar compounds were mainly levoglucosan and its dehydration or isomeric forms, which were generated from the direct decomposition of cellulose. The levoglucosan yield was ranging from 0.3 to 4.2 wt.% depending on the type of feedstock, among which corncob pyrolysis oil occupies the lowest and pine pyrolysis oil takes up the highest.
A considerable amount of alkylated, oxyalkylated phenols, which is mainly formed by the fracture of ether linkages and C–C bonds contained in the side chains of the lignin polymer, occupies a large proportion of the bio-oil, especially for wood feedstock. The total phenols yields of spruce and pine bio-oil were 5.1 and 4.7 wt.%, respectively, while corncob and bagasse bio-oils had relatively low content of phenolic compounds, i.e., 1.8 and 0.6 wt.%, respectively. The type and content of phenolic compounds in bio-oil were relevant to the content of lignin and its structural characteristics of the biomass feedstock. Based on its structural features, the phenolic compounds can be further divided into G-phenols (derived from guaiacyl), S-phenols (derived from syringyl), and H-phenols (derived from p-hydroxyphenyl) (Table S2 in Supplementary Material). The dependence of lignin subunits distribution from different feedstocks on phenols was illustrated in Figure 3.
It could be seen from Figure 3 that the phenolic compounds in spruce and pine pyrolysis bio-oils were mainly G-phenols, each account for more than 80% of the total phenols with major contributions from 2-methoxy-phenol, 2-methoxy 4-methyl-phenol, 2-methoxy-4-vinylphenol, isoeugenol, etc. This may be because of the softwood lignin that almost exclusively contains G-units. On the other hand, grasses lignin also contains more syringyl and p-hydroxyphenyl structural units than softwood lignin. This explains the phenomenon that e bagasse and corncob bio-oil contained a small amount of S-phenols while spruce and pine bio-oils were not.
Effect of Temperature
Although the fast-pyrolysis tests of four kinds of feedstocks have been executed for reactor temperatures in the range 480–580°C, in view of the large amount of data involved, the current work only chose pine as raw material for discussion of the effect of pyrolysis temperature on the composition distribution of bio-oils. The total yields and the trends of the lumped component classes, which have been grouped as AAE (alcohols, aldehydes, and esters), acids, furans, ketones, phenols, and anhydrosugars, were given in Figure 4. The details of the classification of 55 compounds and each single compound yield were listed in Table S3 in Supplementary Material.
As showed in Figure 4, the total yields of 55 chemical compounds quantified by GC–MS first increased and then decreased gradually with increasing temperature, with the maximum value emerged at 550°C, which correspond to 22.0 wt.% of the bio-oils. Among these, the most abundant species are hydroxypropanone (1.9–2.5 wt.%), acetic acid (2.1–3.3 wt.%), furfural (0.4–0.5 wt.%), 5-hydroxymethyl furfural (0.4–0.7 wt.%), 2-methoxy-4-methyl-phenol (0.2–0.8 wt.%), (E)-isoeugenol (0.2–1.1 wt.%), and levoglucosan (0.4–4.2 wt.%). By varying the pyrolysis temperature (480–580°C), the content of small molecule aldehydes, acids showed an increasing trend as temperature increased, while the phenols content decreased gradually from 5.5 to 3.9 wt.%. The yields of furans, ketones, and anhydrosugars varying as a function of pyrolysis temperature were similar to that of the total compounds, with the maximum yield of 2.6, 4.9, and 4.5 wt.%, respectively, emerged at either 520 or 550°C.
Figures 5A,B show the major carbohydrates derived compounds as functions of the pyrolysis temperature, including several major acids, aldehydes, ketones, and anhydrosugars. It could be seen that the yields of relatively larger molecular weight compounds, such as levoglucosan, 1,2-cyclopentanedione, 3-methyl-1,2-cyclopentanedione, etc. were first increased and then decreased with the maximum value at about 520–550°C, while that of the lower molecular compounds, such as acetic acid, butanedial, 2,3-butanedione, showed a continuous increasing trend with temperature elevated. This proved that as temperature increased, the relatively larger molecular furanones, cyclopentanones, and cyclopentenones in hemicellulose and cellulose were prone to bond breaking and reforming to generate lower molecular furan ring or cyclopentanone structures (Patrick and Paul, 1996; Kawamoto et al., 2009). It was worth noting that there was a big difference in the content of levoglucosan under different pyrolysis conditions by using different feedstocks. The content of levoglucosan in the bio-oils from bagasse, corncob, and spruce pyrolysis was between 0.3 and 0.9 wt.% in our previous work, while the pine pyrolysis oil contained much higher levoglucosan, which could reach up to 4 wt.%. This may be related to the different content of salts and metal ions in the feedstock. It has also been reported that the reaction paths of levoglucosan were highly dominated by the ash content. High content of salts and metal ions in feedstock were confirmed to favor the secondary decomposition of levoglucosan and further generation of small molecule aldehydes and ketones (Shen and Gu, 2009).
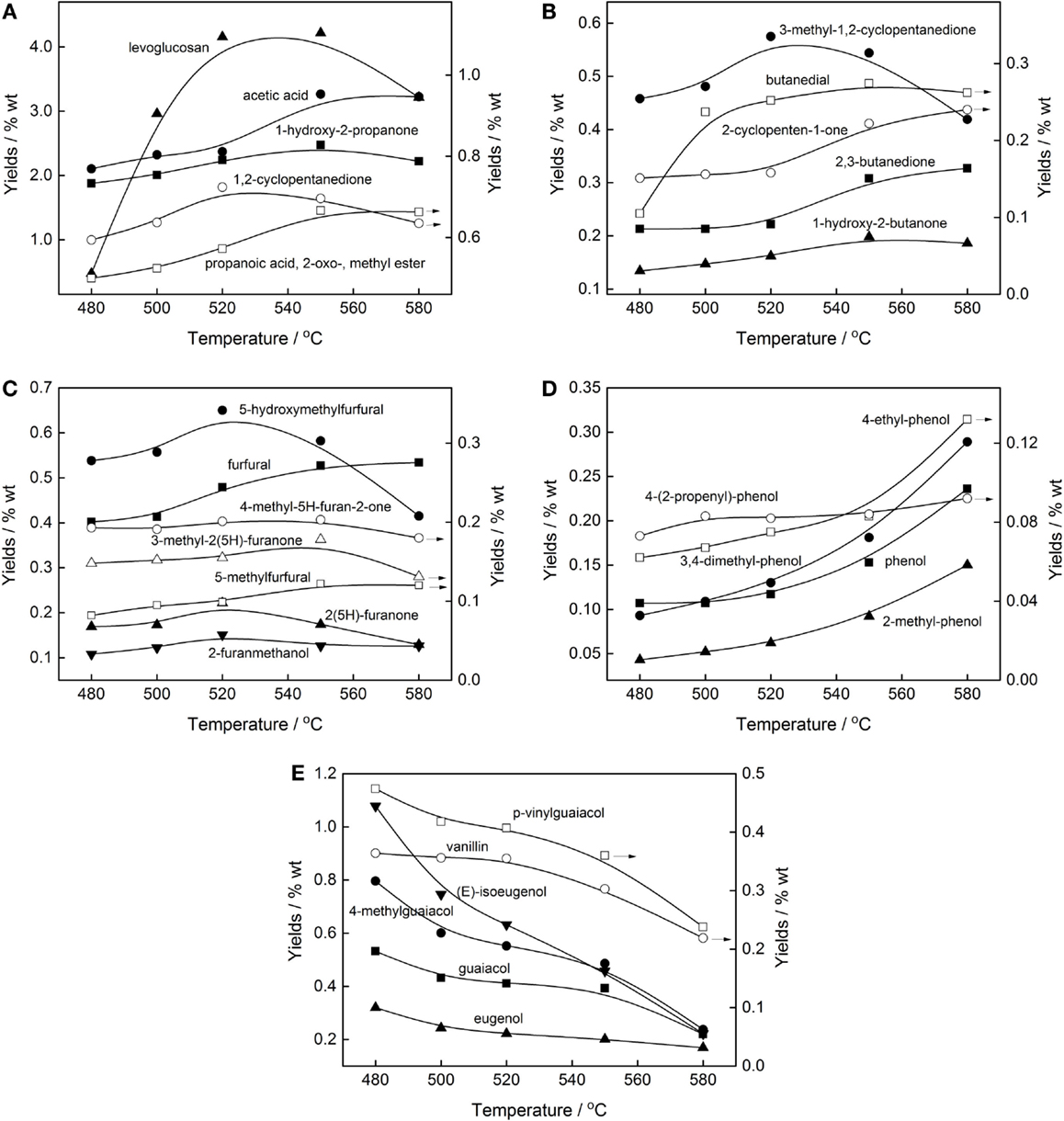
Figure 5. Influence of temperature on the yield of (A) major carbohydrates, (B) minor carbohydrates, (C) furans, (D) H-phenols, and (E) G-phenols of pine pyrolysis bio-oils.
Figure 5C gives the details of the yields of major furans varied with temperature. It can be observed that, pyrolysis temperature had a positive impact on the formation of furfural, i.e., its content showed an increasing trend with the increase of temperature. While for 5-hydroxymethylfurfural, after a maximum yield of 0.7 wt.% at 520°C was attained, as the temperature increased further, a sharp decrease in the amounts occurred because of its weak thermal stability and secondary vapor-phase degradation. This result confirms the hypothesis proposed by Shen and Gu (2009) that the furfural was produced from the secondary reaction of 5-hydroxymethylfurfural at high temperature, along with the formation of formaldehyde through the dehydroxymethylation reaction of the side chain of the furan ring.
Figures 5D,E show the H-phenols and G-phenols content varied as functions of pyrolysis temperature. Apparently, the temperature was indeed a critical parameter that affected not only the phenols yields but also the structure of phenolic compounds. At low temperatures, lignin began to depolymerize to the products that maintained its monomeric structure as much as possible, for example, (E)-isoeugenol, 4-methylguaiacol, p-vinylguaiacol, etc. all got their maximum yields at 480°C (Figure 5D). While the temperature elevated, the side chains of these aromatics were further broken and the methoxy group was removed, thereby generating more H-phenols (Figure 5E). These confirmed that some guaiacols and syringols were intermediate species, which gave their decline at higher temperature, and occurred secondary degradation to further form H-phenols and small molecule gases.
Effect of Low-Temperature Pretreatment
As the physicochemical properties of the torrefied biomass and the resulting bio-oils were examined previously (Chang et al., 2012), our main attentions in this paper were then paid to the influence of the low-temperature pretreatment on the chemical composition changes of the staged pyrolysis bio-oils compared to that of direct pyrolysis, especially for the content variation of furfural, levoglucosan, and phenols products, which represented the typical pyrolysis products of hemicellulose, cellulose, and lignin, respectively. Currently, only the staged pyrolysis of pine was discussed because of space limitation. Torrefaction experiments of pine were performed in an auger reactor at 260, 280, 300, and 320°C, separately; the resulting torrefied pine was used as feedstock for flash pyrolysis in fluidized-bed reactor at moderate temperature of 520°C. The obtained bio-oils were analyzed and compared. Determination of each single product was listed in Table S4 in Supplementary Material. The yields of various types of products compared to that of direct pyrolysis were plotted in Figure 6.
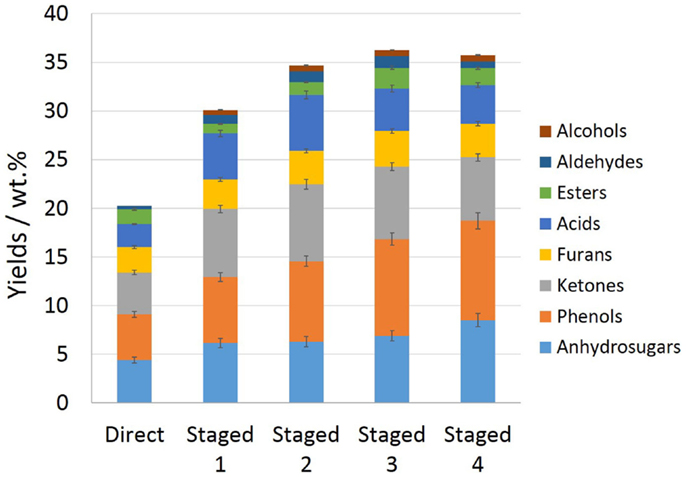
Figure 6. Chemical composition of pine bio-oil from direct and staged pyrolysis (staged 1, 2, 3, and 4 were representative of pretreatment temperature of 260, 280, 300, and 320°C, respectively, before pyrolysis in fluidized-bed reactor at 520°C).
From Figure 6 and Table S4 in Supplementary Material, it could be seen that, the low-temperature pretreatment or low-temperature torrefaction of biomass had a good enrichment for the light weight components of the bio-oils compared with the direct pyrolysis. The total yield of the chromatographic quantitative component was improved by 50–90%, i.e., reached to 31–38 wt.% based on the weight of the obtained bio-oils. The main categories of compounds such as phenols, ketones, furans, and anhydrosugars were all greatly improved. This is mainly due to the low-temperature pretreatment that removed most of the free water and partially bound water in the pine raw material, and the hemicellulose degraded to varying degrees depending on the treatment temperature, generating a small amount of methanol, acetic acid, 1-hyroxy-2-propanone, etc. Thus, the physicochemical properties of the raw material were improved after treatment. When the torrefied feedstock was further pyrolyzed, the water content of the obtained bio-oil decreased sharply, resulting in the increase of major organic chemicals content (Bourgois and Guyonnet, 1988). In addition, the decomposition of cellulose and lignin in torrefied biomass that was accelerated and deepened by torrefaction treatment was the most predominant reason for the enrichment of bio-oil components (Wu et al., 2010). On the other hand, the major components of bio-oil were not always increased linearly as the pretreatment increased further. For example, the total yield of low weight chemicals of bio-oil obtained by staged pyrolysis that torrefied first at 320°C was lower than that of pretreated at 300°C. Among them, the aldehydes, esters, ketones, acids, and furans compounds have similar trend as pretreatment temperature elevated. Higher pretreatment temperature may lead to the excessive depolymerization of the biomass feedstock and the resulted torrefied biomass component condensation or crosslinking, resulting in the decreased yield of bio-oil, and even the reduced content of the main compounds (Dobele et al., 2007).
Figure 7 provides the influence of pretreatment temperature on the yields of major compounds. Figures 7A,B show the effect on the yields of major carbohydrates derived products. It can be seen that higher pretreatment temperature has a positive impact on the yield of levoglucosan, and its increment was more obvious with the increase of pretreatment temperature. Compared with direct pyrolysis, LG content in the bio-oil obtained after pretreatment at 320°C increased about 60%, i.e., reached up to 6.7 wt.% of the total bio-oil.
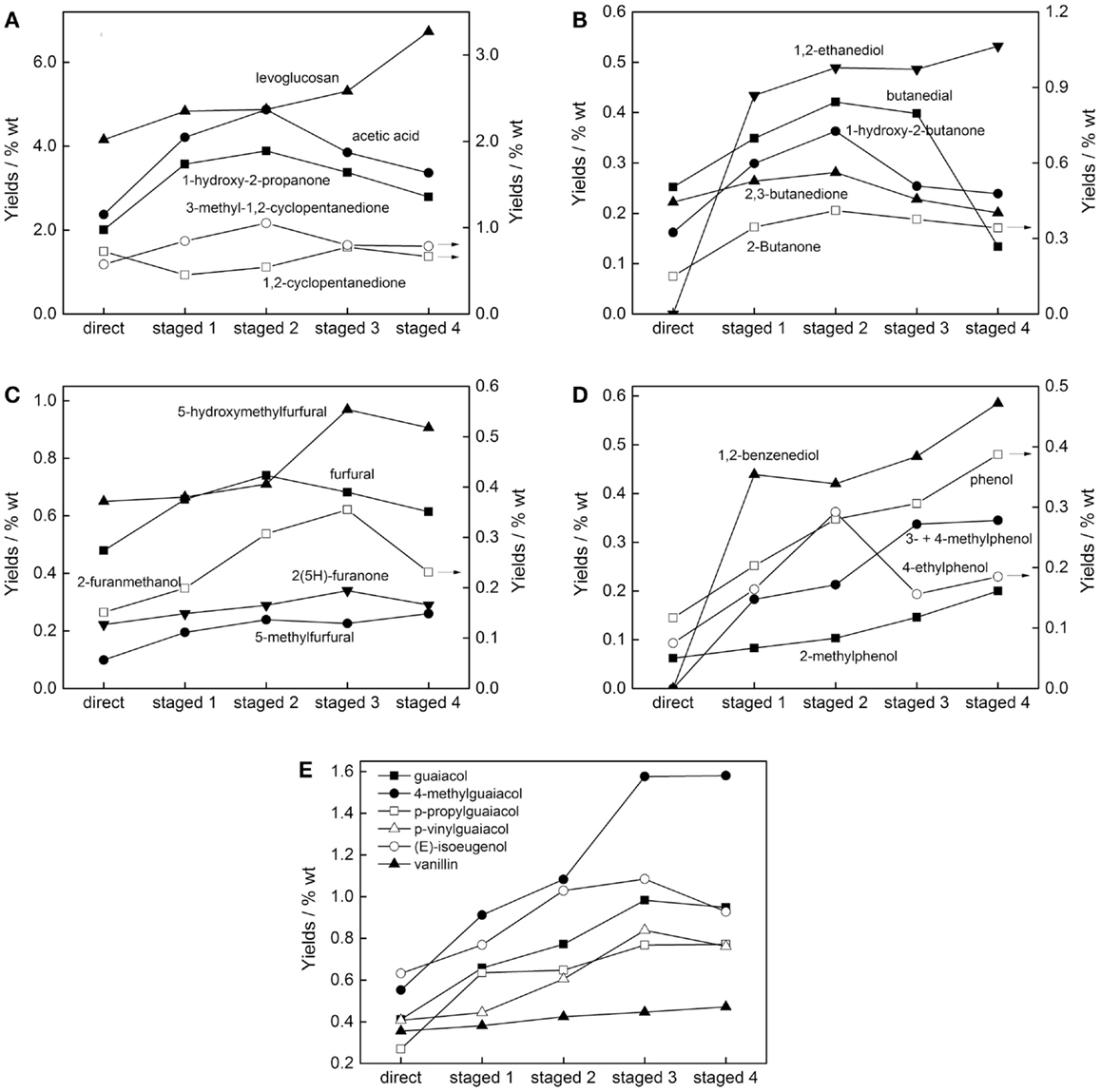
Figure 7. Influence of pretreatment temperature on the yields of (A) major carbohydrates, (B) minor carbohydrates, (C) furans, (D) H-phenols, and (E) G-phenols of pine pyrolysis bio-oils (staged 1, 2, 3, and 4 were representative of pretreatment temperature of 260, 280, 300, and 320°C, respectively, before pyrolysis in fluidized-bed reactor at 520°C).
The acids, especially acetic acid, increased after low-temperature treatment; while the pretreatment temperature was higher than 280°C, the acids began to decrease. There are similar trends for the products such as 1-hydroxy-2-propanone, butanedial, 1-hydroxy-2-butanone, etc., i.e., all got maximum yield when the pretreatment temperature was 280°C. This explains why the pH value of the staged pyrolysis bio-oil showed no increase or increased marginally compared to that by direct pyrolysis. The staged pyrolysis makes the water content of the bio-oil decreased because of torrefaction of biomass feedstock, thus all kinds of compounds, such as acetic acid, etc. were enriched to some extent.
Figure 7C shows the yields of furans varied with pretreatment temperature. As expected, furans products in the staged pyrolysis bio-oils such as furfural, 5-hydroxymethylfurfural, 2-furanmethanol, etc. also had a significant increase because of the low-temperature torrefaction. Wherein, the furfural got the maximum content of 0.7 wt.% when the pine was pretreated at 280°C first, while 5-hydroxymethylfurfural and 2-furanmethanol obtained the maximum increase when pretreated at 300°C, which accounted for 1.0 and 0.4 wt.%, respectively.
Figures 7D,E show the influence of staged pyrolysis on the yields of major H-phenols and G-phenols. With a low-temperature torrefaction, the phenolic compounds in the obtained bio-oils were greatly increased, and most of the phenols yields can be increased one to two times, such as guaiacol, 4-methylguaiacol, phenol, 1,2-benzenediol, etc. This was because the chemical composition of the biomass changed during torrefaction. When pretreated at low-temperature, primarily hemicellulose and even small amount of cellulose may be degraded to some extent depending on the temperature used, while the thermal stability of lignin was relatively higher and was rarely depolymerized (de Wild et al., 2009). Thus, the chemical composition of the resulting torrefied biomass was changed and the lignin content was increased, which further resulting in an increase of phenols yields in the staged pyrolysis bio-oils.
Discussion
The prior arts relating to bio-oil component quantification were more inclined to employ the internal standard method. Even this can reduce the workload to a certain extent, but it also may lead to large quantitative differences between different laboratories. Actually, finding a suitable internal standard for accurate chromatographic quantitative bio-oil components is difficult since the composition of bio-oil is so complex. So, proper standard solutions with known amounts of compounds need to be used for accurate quantitative analyses, especially for accurate quantification of the major compositions of the bio-oils. By comparing the coefficient of linear calibration curve of different compounds (Figure S1 in Supplementary Material), we found it necessary to calibrate the chromatographic systems with as many of known standard compounds as possible, while for the compounds with similar structure and chemical properties, their approximate linear coefficient makes it possible to be roughly calculated.
The comparison of our results obtained from the present methodology with that of elaborate standard addition method shows that most of our present experimental results were slightly lower than its actual yields due to the matrix effects of complex bio-oil (see Table S1 in Supplementary Material). In spite of this, the relative error of present quantitation was usually <5% except for vanillin and 1,2-benzenediol. This proves that the quantitation method here could easily provide us more accurate quantitative information about bio-oil components once we establish plenty of external standard curves.
According to the methodological steps, yields up to 40% (wt.% of the bio-oil) can be quantified; more over, the effects of pyrolysis conditions on the yields of different lightweight chemical families were easier and more realistically revealed. The overall yields of GC-detectable products from corncob and bagasse pyrolysis bio-oil were lower than that of spruce and pine, which should be mainly attributed to the more mineral salts, hemicellulose while less lignin content in grasses biomass than in woody biomass. These are more in line with commonly accepted expectations and published reports (Raveendran et al., 1995; Pushkaraj et al., 2010).
The influence of temperature on product distribution profiles as depicted in Figures 4 and 5 can give us optimal pyrolysis temperatures for maximum yields of each chemical families and individual components. Varies in the effect of temperatures confirmed the occurrence of secondary reactions during biomass pyrolysis. Higher temperature makes the relatively larger molecular furans, cyclopentanones, and phenols further bond breaking and reforming to similar kinds while simpler compounds, such as 5-hydroxymethylfurfural to furfural, G-phenols and S-phenols to H-phenols, accompanied by the generation of small molecule aldehydes, acids, etc. One thing we have to keep in mind is, when further extending the residence time at high temperature, the repolycondensation of pyrolysis products may dominate the secondary reactions. Future direction of characterizing heavy components of bio-oils will help to confirm these postulate theories.
As speculated, the observation also revealed that low-temperature pretreatment of biomass had a good enrichment effect for the light weight components of the bio-oils. The total yield of the chromatographic quantitative component was improved by 50–90%. It is rationalized as the low-temperature pretreatment removed most of the free water and partially bound water in the raw material. However, the deep-seated root cause of these enrichment effects has yet to be explored by mechanism investigation of staged pyrolysis of model compounds.
Conclusion
The knowledge of quantitative chemical characterization of bio-oils is valuable for designing pyrolysis reaction and evaluating its strategic importance as an extended range of applicable fuels and chemicals. To this end, 19 kinds of standard compounds (i.e., major components of bio-oil) were used as external standard for quantification, and standard addition method was further used to evaluate the effectiveness and impact of the current calibration curve approach. Consequently, this methodology was adopted for a new campaign to quantify lightweight components of bio-oils obtained under a wide range of pyrolysis parameters. The results showed more than 50 compounds and yield up to 40% (wt.% of the bio-oil) can be quantified by the present method. Yields of each chemical families and individual component correlate strongly with the original feedstocks and pyrolysis temperatures. In addition, the low-temperature pretreatment of biomass has a good enrichment for the light weight components of the bio-oils, which the total yield was improved by 50–90% depending on pretreatment temperature. The final data set of the obtained results will be used as the basis for tuning pyrolysis conditions and exploring proper utilization of different bio-oils.
Conflict of Interest Statement
The authors declare that the research was conducted in the absence of any commercial or financial relationships that could be construed as a potential conflict of interest.
Acknowledgments
We acknowledge support provided by the National Key Basic Research Program of China (No. 2013CB228101), the National High Technology Research and Development Program of China (No.2012AA101806), the National Science Foundation of China (31400517), and the Open Foundation of SKLPPE (No. 201437).
Supplementary Material
The Supplementary Material for this article can be found online at http://journal.frontiersin.org/article/10.3389/fenrg.2015.00028/abstract
References
Abdelnur, P. V., Vaz, B. G., Rocha, J. D., de Almeida, M. B. B., Teixeira, M. A. G., and Pereira, R. C. L. (2013). Characterization of bio-oils from different pyrolysis process steps and biomass using high-resolution mass spectrometry. Energy Fuels 27, 6646–6654. doi: 10.1021/ef400788v
Akwasi, A. B., Charles, A. M., Neil, G., and Kevin, B. H. (2008). Production of bio-oil from alfalfa stems by fluidized-bed fast pyrolysis. Ind. Eng. Chem. Res. 47, 4115–4122. doi:10.1021/ie800096g
Badal, C. S. (2003). Hemicellulose bioconversion. J. Ind. Microbiol. Biotechnol. 30, 279–291. doi:10.1007/s10295-003-0049-x
Bourgois, J., and Guyonnet, R. (1988). Characterization and analysis of torrefied wood. Wood Sci. Technol. 22, 143–155. doi:10.1007/BF00355850
Branca, C., Giudicianni, P., and Di Blasi, C. (2003). GC/MS characterization of liquids generated from low-temperature pyrolysis of wood. Ind. Eng. Chem. Res. 42, 3190–3202. doi:10.1021/ie030066d
Bridgwater, A. V., Meier, D., and Radlein, D. (1999). An overview of fast pyrolysis of biomass. Org. Geochem. 30, 1479–1493. doi:10.1016/j.biortech.2012.06.016
Chang, S., Zhao, Z., Zhang, W., Zheng, A., Wu, W., and Li, H. (2011). Comparison of chemical composition and structure of different kinds of bio-oils. J. Fuel Chem. Technol. 39, 746–753.
Chang, S., Zhao, Z., Zheng, A., He, F., Huang, Z., and Li, H. (2012). Characterization of products from torrefaction of sprucewood and bagasse in an auger reactor. Energy Fuels 26, 7009–7017.
Charles, A. M., Gary, D. S., and Akwasi, A. B. (2009). Characterization of various fast-pyrolysis bio-oils by NMR spectroscopy. Energy Fuels 23, 2707–2718. doi:10.1016/j.biortech.2010.04.024
Chiaberge, S., Leonardis, I., Fiorani, T., Cesti, P., Reale, S., and Angelis, F. D. (2014). Bio-oil from waste: a comprehensive analytical study by soft-ionization FTICR mass spectrometry. Energy Fuels 28, 2019–2026. doi:10.1021/ef402452f
de Wild, P. J., Uil, H. D., Reith, J. H., Kiel, J. H. A., and Heeres, H. J. (2009). Biomass valorisation by staged degasification: a new pyrolysis-based thermochemical conversion option to produce value-added chemicals from lignocellulosic biomass. J. Anal. Appl. Pyrolysis 85, 124–133. doi:10.1016/j.jaap.2008.08.008
Demirbas, A. (2009a). Biorefineries: current activities and future developments. Energy Convers. Manag. 50, 2782–2801. doi:10.1016/j.enconman.2009.06.035
Demirbas, M. F. (2009b). Biorefineries for biofuel upgrading: a critical review. Appl. Energy 86, S151–S161. doi:10.1016/j.apenergy.2009.04.043
Dinesh, M., Charles, U. P. J., and Philip, H. S. (2006). Pyrolysis of wood/biomass for bio-oil: a critical review. Energy Fuels 20, 848–889. doi:10.1021/ef0502397
Dobele, G., Urbanovich, I., Volpert, A., Kampars, V., and Samulis, E. (2007). Fast pyrolysis–effect of wood drying on the yield and properties of bio-oil. Bioresources 2, 699–706.
Garcia, P. M., Chaala, A., Pakdel, H., Kretschmer, D., and Roy, C. (2007). Characterization of bio-oils in chemical families. Biomass Bioenergy 31, 222–242. doi:10.1016/j.biombioe.2006.02.006
Guo, X. J., Wang, S. R., Guo, Z. G., Liu, Q. A., Luo, Z. Y., and Cen, K. F. (2010). Pyrolysis characteristics of bio-oil fractions separated by molecular distillation. Appl. Energy 87, 2892–2898. doi:10.1016/j.apenergy.2009.10.004
Helena, L. C., and Ralph, P. O. (2001). Biomass and renewable fuels. Fuel Process. Technol. 71, 187–195. doi:10.1016/S0378-3820(01)00146-1
Hyeon, S. H., Hyun, J. P., Young, K. P., Changkook, R., Dong, J. S., Young, W. S., et al. (2010). Bio-oil production from fast pyrolysis of waste furniture sawdust in a fluidized bed. Bioresour. Technol. 101, S91–S96. doi:10.1016/j.biortech.2009.06.003
Jean, N. M., Hooshang, P., and Christian, R. (2001). Separation of syringol from birch wood-derived vacuum pyrolysis oil. Sep. Purif. Technol. 24, 155–165. doi:10.1016/S1383-5866(00)00225-2
Kai, S., Eeva, K., Leena, F., and Anja, O. (1998). Characterization of biomass-based flash pyrolysis oil. Biomass Bioenergy 14, 103–113. doi:10.1016/S0961-9534(97)10024-1
Kawamoto, H., Morisaki, H., and Saka, S. (2009). Secondary decomposition of levoglucosan in pyrolytic production from cellulosic biomass. J. Anal. Appl. Pyrolysis 85, 247–251. doi:10.1016/j.jaap.2008.08.009
Lindfors, C., Kuoppala, E., Oasmaa, A., Solantausta, Y., and Arpiainen, V. (2014). Fractionation of bio-oil. Energy Fuels 28, 5785–5791. doi:10.1021/ef500754d
Lu, Q., Li, W. Z., and Zhu, X. F. (2009). Overview of fuel properties of biomass fast pyrolysis oils. Energy Convers. Manag. 50, 1376–1383. doi:10.1016/j.enconman.2009.01.001
Lv, G., and Wu, S. (2012). Analytical pyrolysis studies of corn stalk and its three main components by TG-MS and Py-GC/MS. J. Anal. Appl. Pyrolysis 97, 11–18. doi:10.1016/j.jaap.2012.04.010
Lv, G., Wu, S., and Lou, R. (2010). Characteristics of corn stalk hemicellulose pyrolysis in a tubular reactor. Bioresources 5, 2051–2062.
Lv, G., Wu, S., Yang, G., Chen, J., Liu, Y., and Kong, F. (2013). Comparative study of pyrolysis behaviors of corn stalk and its three components. J. Anal. Appl. Pyrolysis 104, 185–193. doi:10.1016/j.jaap.2013.08.005
Mckendry, P. (2002). Energy production from biomass (part 1): overview of biomass. Bioresour. Technol. 83, 37–46. doi:10.1016/S0960-8524(01)00118-3
Meier, D. (1999). “New methods for chemical and physical characterization and round robin testing,” in Fast Pyrolysis of Biomass: A Handbook, Vol. 1, ed. D. Meier (Newbury: CPL Press), 92–101.
Oasmaa, A., and Meier, D. (2005). Norms and standards for fast pyrolysis liquids1. round robin test. J. Anal. Appl. Pyrolysis 73, 323–334. doi:10.1016/j.jaap.2005.03.003
Patrick, A. H., and Paul, T. W. (1996). Influence of temperature on the products from the flash pyrolysis of biomass. Fuel 75, 1051–1059. doi:10.1016/0016-2361(96)00081-6
Pushkaraj, R. P., Justinus, A. S., Robert, C. B., and Brent, H. S. (2010). Influence of inorganic salts on the primary pyrolysis products of cellulose. Bioresour. Technol. 101, 4646–4655. doi:10.1016/j.biortech.2010.01.112
Raveendran, K., Anuradda, G., and Kartic, C. K. (1995). Influence of mineral matter on biomass pyrolysis characteristics. Fuel 74, 1812–1822. doi:10.1016/0016-2361(95)80013-8
Serdar, Y. (2004). Pyrolysis of biomass to produce fuels and chemical feedstocks. Energy Convers. Manag. 45, 651–671. doi:10.1016/j.biotechadv.2012.01.016
Shen, D. K., and Gu, S. (2009). The mechanism for thermal decomposition of cellulose and its main products. Bioresour. Technol. 100, 6496–6504. doi:10.1016/j.biortech.2009.06.095
Shi, S., and He, F. (2003). Analysis and Detection of Pulping and Papermaking, First Edn. Beijing: Chinese Light Industry Press.
Wu, Y., Zhao, Z., Chang, S., and Li, H. (2010). Low temperature pyrolysis characteristics of corn cob and eucalyptus. Trans. Chin. Soc. Agric. Eng. 26, 254–258.
Yang, H., Yan, R., Chen, H., Lee, D. H., and Zheng, C. (2007). Characteristics of hemicellulose, cellulose and lignin pyrolysis. Fuel 86, 1781–1788. doi:10.1016/j.fuel.2006.12.013
Keywords: pyrolysis, bio-oil, characterization, quantification, GC-MS
Citation: Lyu G, Wu S and Zhang H (2015) Estimation and comparison of bio-oil components from different pyrolysis conditions. Front. Energy Res. 3:28. doi: 10.3389/fenrg.2015.00028
Received: 10 February 2015; Accepted: 28 May 2015;
Published: 15 June 2015
Edited by:
Junye Wang, Athabasca University, CanadaReviewed by:
Charilaos Xiros, Bern University of Applied Sciences, SwitzerlandTianju Chen, Chinese Academy of Sciences, China
Copyright: © 2015 Lyu, Wu and Zhang. This is an open-access article distributed under the terms of the Creative Commons Attribution License (CC BY). The use, distribution or reproduction in other forums is permitted, provided the original author(s) or licensor are credited and that the original publication in this journal is cited, in accordance with accepted academic practice. No use, distribution or reproduction is permitted which does not comply with these terms.
*Correspondence: Shubin Wu, State Key Lab of Pulp and Paper Engineering, South China University of Technology, 381 Wushan Road, Guangzhou, Guangdong 510640, China,c2h1Ymlud3VAc2N1dC5lZHUuY24=