- 1College of Chemistry and Chemical Engineering, Qufu Normal University, Jining, China
- 2Soundgroup New Energy Technology Development Co., Ltd., Beijing, China
- 3Department of Nuclear Science and Engineering, Massachusetts Institute of Technology, Cambridge, MA, United States
- 4Military Power Sources Research and Development Center, Research Institute of Chemical Defense, Beijing, China
- 5National Center for Nanoscience and Technology, Chinese Academy of Sciences, Beijing, China
With the increasing demand for green energy due to environmental issues, developing batteries with high energy density is of great importance. Li-S batteries, since their big breakthrough in 2009, have attracted much attention in both academia and industry. In academia, significant progress has been made in improving the specific capacity, rate capacity, and cycle performance using various novel strategies. However, the performance is hugely different when these strategies are extended to mass production, indicating a significant difference between academic research, and industrial production. In this brief review, we discussed the gap between the academic research and commercialization in detail based on literature reports and to our more than 10 years' experience on Li-S pouch cells, which including cathodes, anodes, separators, interlayers, electrolytes, and additives. The problems, which existing in pouch cells by using the materials and technologies developed by academic research using coin cells, was analyzed. We expected that this review could be helpful to both academic research and industrial commercialization of Li-S batteries.
Introduction
With the fast growth of population and economy, the demand for clean energy is increasing rapidly. Traditional Li-ion batteries are more and more difficult in satisfying the demand due to their limited capacity and energy density (Bruce et al., 2011; Lu et al., 2013). The energy density of traditional Li-ion batteries can hardly go beyond 300 Wh/kg. Other storage devices, such as supercapacitors, are representative of high-power devices, whereas their energy density is much lower than Li-ion battery (Simon et al., 2014; Yan et al., 2018). Therefore, it is highly imperative to develop high-energy storage systems to satisfy the increasing energy demand. Lithium-sulfur (Li-S) batteries with a much higher energy density have attracted more and more attentions (Ji et al., 2009; Manthiram et al., 2014; Sun et al., 2017; Tan et al., 2017; Li Z. et al., 2018). As one of the richest elements in the earth's crust, sulfur delivers a high theoretical capacity of ~1,675 mAh/g, which is much higher than those cathode materials in Li-ion batteries. A Li-S cell works based on the following conversion reaction: 2Li + S ↔ Li2S, leading to an overall theoretical cell capacity of ~1,167 mAh/g (Ji et al., 2009). Based on an average discharge voltage of 2.15 V, the theoretical gravimetric energy density of a Li-S cell is ~2,510 Wh/kg, which is much higher than that of the traditional Li-ion batteries. However, Li-S batteries suffer from the electrochemical intermediates (polysulfides) dissolution, which causes poor cyclability and lithium anode corrosion, poor electronic conductivity, and significant volume change during cycling (Wang et al., 2014; Li et al., 2016).
A large number of academic researches have been reported on Li-S batteries, and many of them achieved reversible capacities over 1,000 mAh/g (based on sulfur), whereas they are still far away from the industrial production. A big gap between industry and academic research exists in Li-S batteries, just like two parallel lines. In this review, we analyzed the big gap between academia and industry, and hope to give guidance to promote the commercialization of Li-S batteries.
Gaps Between Academia and Industry
To date, there are no commercial Li-S batteries in the market. In this paper, the industry of Li-S batteries is mainly the pilot-scale production in many companies and universities. The situation of many critical factors for Li-S batteries in academia and industry researches is presented in Figure 1. Scientists involving in academic research of Li-S batteries developed very fast and achieved fruitful results in the past decades. However, the commercialization process of Li-S batteries developed very slowly, therefore, there still has no product in the market. The development of Li-S batteries in academia is as fast as taking a bullet train, but the development in the industry is as slow as running. In academia, various advanced carbon materials have been synthesized in many research articles, and most of the carbon materials can be hardly produced on a large scale. However, the commercially available carbon materials that are suitable for the industrial production of Li-S batteries are rarely studied. Besides, high rate capabilities of more than 10 C (1 C = 1,675 mA/g) and long life-span over 1,000 cycles have been reported in many research papers based on coin cells, but the charge/discharge rate can hardly exceed 0.2 C, and the cycle life is no more than 300 cycles in pouch cells (Hu et al., 2016; Weller et al., 2017; He et al., 2018). Furthermore, the Coulombic efficiency is commonly reported to be more than 99% in many research papers, but the Coulombic efficiency in pouch cells can hardly reach 98%. The reason can be addressed to the amount of electrolyte, lithium nitrate (LiNO3) additive, and lithium used in the cells. To a certain level, the more LiNO3 used, the higher the Coulombic efficiency and longer cycle life, which is due to the consumption of LiNO3 upon cycling (Barghamadi et al., 2016; Adams et al., 2017; Zhang et al., 2018). However, the addition of LiNO3 can lead to serious safety problems for Li-S batteries. The combination of sulfur, carbon, and nitrate is the composition of a bomb, which can be dangerous. Thus, in industry people try to find a replacement for LiNO3 and pay much more attention to the safety issues.
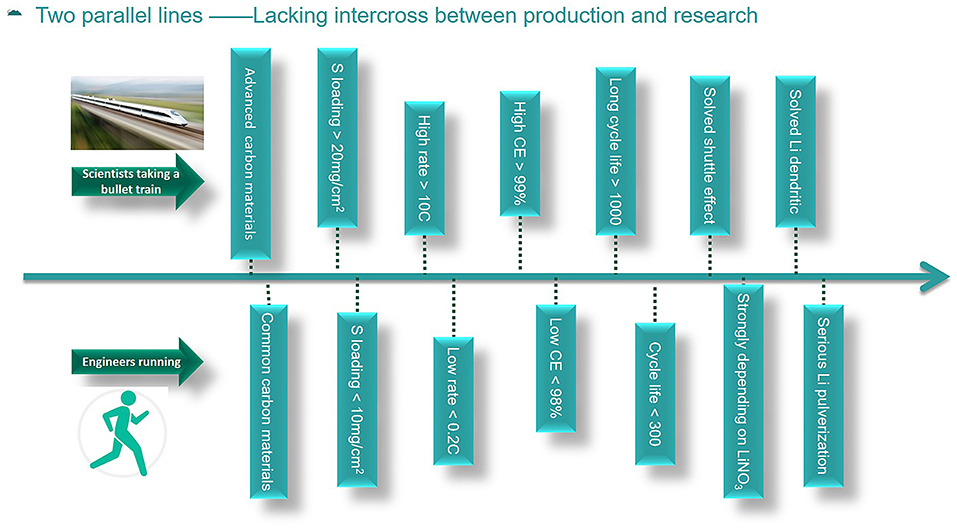
Figure 1. The status of some key factors of academic research and industry production for Li-S batteries.
In academia, researchers have reported many solutions to solve the polysulfides shuttle effect, such as the use of coating layers on electrode and separator, interlayers between cathode and separator etc. (Kong et al., 2013; Luo et al., 2016; Abbas et al., 2017; Park et al., 2017; Pei et al., 2018). Whereas, when considering about cost and processing of those technics, most of the methods can be hardly used in pouch cells. What's more, the dendritic Li growth is also a severe problem in Li-S batteries, and there are many academic reports show that the problem has been solved by using protective layers on lithium metal, solid electrolytes and electrolyte additives etc. (Ding et al., 2013; Li et al., 2016; Cheng et al., 2019). However, those methods can hardly work in a limited lithium amount pouch cells; thus pouch cells still suffer from low Coulombic efficiency, micro short-circuit, and short cycle life.
Current Status and Future Direction
Li-S batteries can hardly be commercialized unless the gaps between the practical productions and academic researches are filled in. In the following text, we will focus on the discussion of the anode, cathode, electrolyte, interlayer, additive, mass loading, and cell safety of Li-S batteries based on our more than 10 years' research experience on Li-S batteries in both coin cells and pouch cells.
Lithium Anode
Lithium metal is an ideal anode material because of its highest specific capacity of 3,860 mAh/g and the lowest potential of −3.04 V (vs. standard hydrogen electrode). However, lithium anode suffers from dendritic growth, significant volume change during repeated cycles, and low Coulombic efficiency. The significant volume change can lead to the pulverization of the anode and expand of the pouch case, which may cause sudden failure and serious safety problem of the cells (Xu et al., 2014; Lin et al., 2017). Pulverized lithium will lose electric contact with the lithium foil and can result in rapid deteriorate of electrochemical performance when the lithium amount is limited, and it is very active, which can generate a large amount of heat and get fire when exposing to air. This problem can hardly be observed in coin cells because of the much excess lithium is used, low energy capacity, and the use of stainless steel case. However, in pouch cells, the aluminum plastic case is not as strong as the stainless steel ones, and the energy capacity is thousand times higher than that of the coin cells; thus we should pay special attention to the case design of Li-S pouch cells. Figure 2 shows the severe corrosion and pulverization of lithium foil in a 3.5 Ah pouch cell after 89 cycles, which leads to the loss of contact and specific area increase of lithium electrode. This further makes the side reactions of lithium and electrolyte aggravated, ultimately resulting in the exhaust of electrolyte, a sudden drop of capacity, and the failure of cells (Cheng et al., 2017).
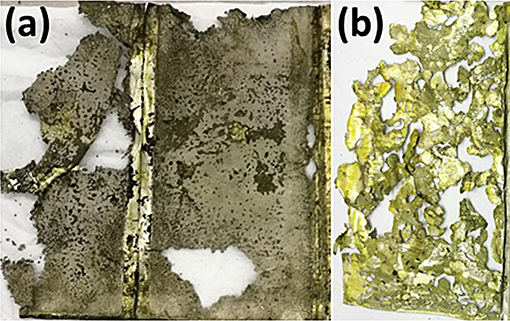
Figure 2. The optical morphology of (a) cycled Li foil electrode with a thickness of 160 μm in a pouch cell with a capacity of 3.5 Ah after 89 cycles at 200 mA/g and (b) detached Li fragments from the Li foil.
As we mentioned before, there already have many articles that focus on the improvement of lithium anode problems, but few of them can be used in pouch cells. Price and craft are something we need to consider, but the most important is the difference in the energy capacity of coin cells used in academic researches and pouch cell production. With a bulk density of 0.534 g/cm3, lithium foil can deliver a theoretical areal capacity of ~1 mAh/cm2 with a thickness of 5 μm. Typically, in coin cell researches, the energy capacity of the cathode is <2 mAh/cm2. If we use a lithium disc with a thickness of 0.5 mm, which is 100 mAh/cm2, then the energy capacity of lithium is fifty more times higher than that of the cathode. The excess of lithium in many reports is even higher than this. Thus, many of the problems of lithium can hardly be observed in coin cells, because there always has plenty of new lithium to replace the dead lithium. However, in pouch cells, considering the overall energy density, we cannot use too much excess lithium. In academia, the performance of lithium can be improved by building artificial SEI layers (Li et al., 2016), using modified electrolytes (Scheers et al., 2014), and constructing 3D current collectors (Yang et al., 2015; Wang S. H. et al., 2017). These strategies can greatly buffer the growth of Li dendrites and primarily improve electrochemical performance. For example, Guo group reported a 3D collector with submicron skeleton (Yang et al., 2015). The results demonstrate that the growth of Li dendrites can be effectively suppressed, leading to the Li anode can work for 600 h without short circuits and presents low voltage hysteresis. However, most of the researches are based on deficient energy capacity (<3 mAh/cm2) (Ji et al., 2009; Jing et al., 2015; Zhang et al., 2015; Li et al., 2016; Li Z. et al., 2018), but in pouch cell, as a double side anode, the energy capacity should be at least 10 mAh/cm2, which is based on the loading of sulfur is 5 mg/cm2, and specific capacity is 1,000 mAh/g. Thus, most of the methods do not work in pouch cells.
For industry, lithium foil is the most suitable anode material for Li-S batteries at present due to its easy processibility, commercial availability, and feasible operation in battery assembly. In pouch cells, lithium foil not only works as the anode but also works as the current collector. As a result, the energy capacity of lithium is usually designed to triple that of the cathode in pouch cells to ensure the cell works well.
In order to beat the traditional Li-ion batteries, the areal capacity of pouch cells is required to be at least 5 mAh/cm2, then the thickness of lithium foil should be at least 25 μm, and the triple is 75 μm. In pouch cells with double side coated cathode, the thickness should be 150 μm. In the first cycle, only the surface 25 μm lithium of the lithium foil will be stripped and take part in the redox reaction with sulfur. Thus, the protective layers, such as artificial SEI layers mentioned above, will detach from lithium foil after discharge. After charge, lithium will deposit on the remained lithium foil randomly and cause significant volume change, which can break the artificial SEI layers seriously. Moreover, the area of the electrode in pouch cells is much larger than that of the coin cells, and such large and uniform coating layers are tough to make. Novel 3D current collectors such as porous conductive foam, hollow carbon fiber cloth, could be a good choice after optimization for lithium plating (Yang et al., 2015; Wang S. H. et al., 2017). For pouch cells, the volume changes and performance of Li anode could be significantly relieved and improved by employing novel 3D current could support the lithium foil with thickness of 150 μm. Related work needs to be done, verifying the effect on improvement of Li anode in pouch cells.
Cathode
In the past two decades, most researchers who are working on Li-S batteries are mainly focused on the development of novel cathode materials to improve the electrochemical performance, including the improvement the electronic conductivity of sulfur composites, suppression the polysulfides shuttle effect by absorbents, and promotion reaction kinetics of sulfur species using catalysts (Wang et al., 2015; Cleaver et al., 2018). Various advanced carbon materials that are working as a conductive matrix, such as carbon nanotubes (Wang et al., 2013), graphene (Wang et al., 2014; Li et al., 2015), porous carbon (Zheng et al., 2014), and hybrid carbon (Yang et al., 2014), and most of them are usually fabricated in a complex and high-cost process.
Only the traditional carbon materials (e.g., carbon nanotubes and acetylene black) (Miao and Yang, 2013; Wang et al., 2013), which are commercially available at low cost, are practically applied in industrial production. Many carbon materials with the high specific surface area may not be suitable for commercialization due to the additional side reactions, low volumetric capacities, need more binder, and difficulties in the slurry casting process of cathodes. As a reference in Li-ion batteries industry, the specific surface area of active materials is generally <1 m2/g, and only 1–3 wt.% of binder is used in the cathodes. However, the required amount of binders in Li-S batteries is often up to 10 wt.% in the cathode to stick together with those advanced carbon materials with high specific surface area, thus unavoidably lowering the overall energy density of cells. At present, the cathodes we used in pouch cells are usually a mixture of the commercial carbon materials (e.g., acetylene black, CNT, graphene, etc.), sulfur, and binder (3–6 wt.%) to minimize the cost and maximize the mass production and overall capacity of the products.
Another issue we should pay special attention to is the loading content of sulfur in the electrodes, which is vital to determine the specific energy density of Li-S batteries. However, people may not be aware of the significant effect of different sulfur content on the electrochemical performance of cells. In many previous reports, the weight ratio of pure sulfur within cathode is no more than 50% for coin cells (Ji et al., 2011; Zoo and Manthiram, 2013; Zheng et al., 2014; Zhou et al., 2015; Du et al., 2016; Fang et al., 2017; Wang Q. Q. et al., 2017). In our long-term experiments, sulfur is usually designed to be 75–78 wt.% to achieve specific energy of 400 Wh/g for Li-S pouch cells. To highlight the influence of weight ratio of sulfur on the absolute amount of sulfur, we establish relation between specific sulfur mass (y-axis) and sulfur weight ratio (x-axis). Assuming that the amount of additives (including conductive agent and binder) is 1 mg/cm2, the equation can be expressed as y = x/(1−x) and plotted in Figure 3. When sulfur content increases from 25 wt% to 50 or 75 wt.%, the absolute amount of sulfur rises significantly (Figure 3). For example, 50 wt.% sulfur is comprised of 1 mg sulfur and 1 mg additives (including conductive agent and binder). If the sulfur weight ratio increase to 75 wt.%, 3 mg of sulfur will be needed, which means the amount of sulfur triples the value of the electrode with 50 wt.% sulfur. Furthermore, if the weight ratio of sulfur is promoted to 90 wt.%, the amount of sulfur is 9 times the value of the electrode with 50 wt.% sulfur. Therefore, it is very challenging to ensure a reversible capacity of 1,000 mAh/g and 75–78 wt.% sulfur content within cathode for the pouch cells. Another issue is the area of the cathode electrode in coin cells. Some researchers reported very high sulfur content in the cathode with a tiny electrode (much <1 cm2) (Chang et al., 2016; Fang et al., 2016; Song et al., 2018), in such case, the stainless steel case also acts as a current collector for the cathode and the area of electrode changed. People may not aware of this effect in coin cells, but this situation will not happen in pouch cells, as the electrode area is the same as the current collector (Cheng et al., 2017). Thus, many of the electrochemical performance in coin cells can be hardly repeated in pouch cells. Besides, it should be noted that researchers are imperatively needed to optimize the structure of cathodes and cathode materials synthesis process.
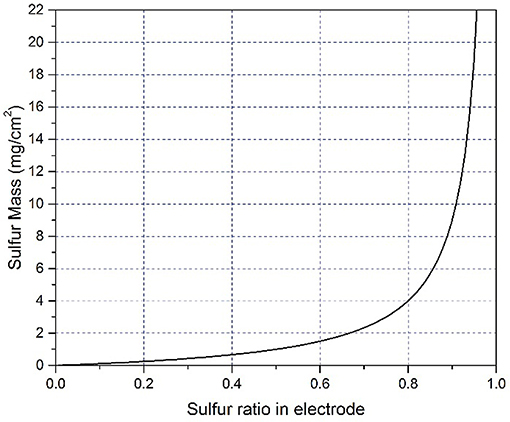
Figure 3. The curve of the relationship between sulfur weight ratio and specific sulfur mass in the electrode. Assuming that the amount of additives (including conductive agent and binder) is 1 mg/cm2.
Separator, Interlayer, and Adsorbent
In academic researches for Li-S batteries, multi-functional separators or interlayers can effectively suppress the shuttle effect of lithium polysulfides, thus improving the electrochemical performance of batteries (Chung et al., 2015; Ma et al., 2016; Li M. et al., 2018). There are two main pathways for preparing the multi-functional separators: (1) modifying the composition and structure of separator to improve the ionic selectivity and suppress the diffusion of lithium polysulfides, and (2) adding a blocking layer between the separator and cathode/anode to inhibit the transport of lithium polysulfides.
For example, an activated carbon nanofiber layer was filtered onto a polypropylene separator as a functional separator for Li-S batteries (Chung et al., 2015). The porous activated carbon nanofiber films were demonstrated to adsorb the lithium polysulfides and restrain their diffusion, thus suppressing the shuttle effect. It is also suggested that this separator can effectively enhance the utilization of sulfur. The separators modified with polypyrrole nanotubes can inhibit the migration of lithium polysulfides and suppress the shuttle effect by strong adsorption of polypyrrole to lithium polysulfides and excellent wettability between polypyrrole and separator, thus improving the electrochemical performance of Li-S batteries (Ma et al., 2016). Novel separators have gained increasing attention. Wang et al. report a kind of novel separator of graphdiyne (GDY)-modified polyimide (PI) separator (Figure 4) (Wang et al., 2019). The working mechanism involves an interaction effect between polysulfides and GDY including chemical adsorption and physical obstruction, as shown in Figure 4A. After introducing novel separator, the battery with GDY-PI separator delivers obvious improved cycling performance compared to these common separators (Figure 4B), demonstrating the effective interaction between acetylenic bonds of GDY and lithium polysulfides. In general, by using a modified separator to reduce the lithium polysulfides shuttle effect, the electrochemical performance improved significantly. It is noted that the electrochemical data are collected using coin cells with the mass loading of sulfur rather low (<1.5 mg/cm2) and low absolute weight of sulfur (<1 mg). When the modified separators employed in pouch cells, the advantage is generally rather limited due to the limited adsorption capacity of these separators with high sulfur loading in the electrode (>5 mg/cm2). Increasing the amount of additives on separators would anchor more lithium polysulfides and improve the performance of pouch cells, but the overall specific capacity reduces, and the cost inevitably increases. There should have a balance between specific capacity and sulfur content/loading. Higher sulfur content/loading usually leads to poorer electrochemical performance. What we experienced now in pouch cells is that the sulfur content can hardly go over 75 wt.%, and sulfur loading is <8 mg/cm2 in the cathode to ensure excellent electrochemical performance. Also, some other issues should be specially noted as well, referring to the commercialization of LI-S batteries. For example, the materials, especially in type of powder, which is used to modify the separators could be detached from separators with extended cycling, result in the failure of the modified separators. The cost and weight of modified materials also should be carefully evaluated in pouch cells, which directly influence the price, and energy density of commercial battery packs.
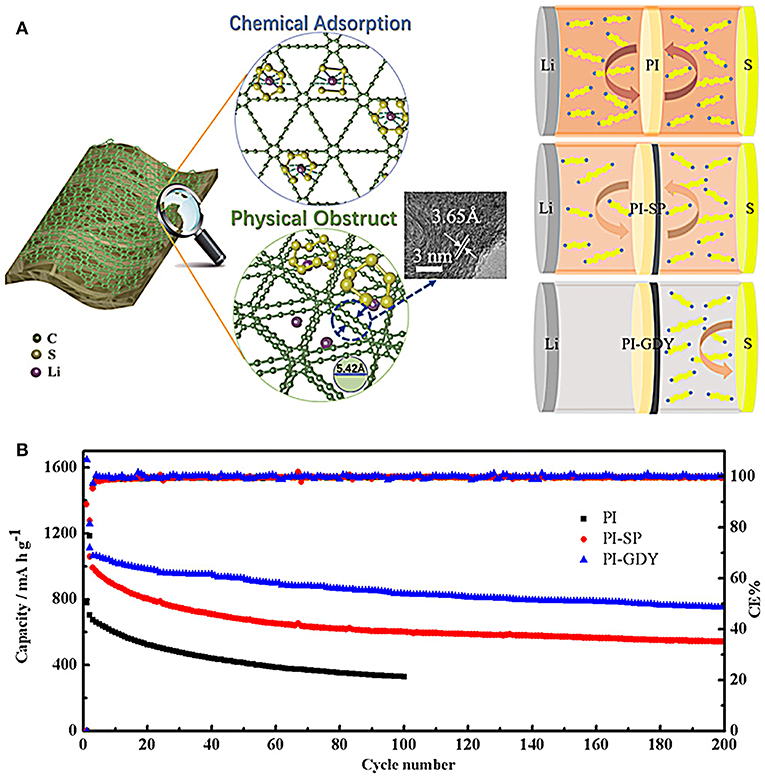
Figure 4. (A) Work mechanism between polysulfides and GDY. (B) Cycle performance with PI, PI-SP, and PI-GDY separators at 0.5 C. Reproduced from Chung et al. (2015). Copyright© 2019 American Chemical Society.
Placing an adsorption interlayer between the cathode and separator not only enhances the conductivity and the utilization of cathode but also relieves the shuttle effect of lithium polysulfides (Manthiram et al., 2014). Interlayers play a similar role as the modified separators. Therefore, interlayers also suffer from similar problems with modified separators when they are introduced in pouch cells. The mass and thickness of interlayers should be considered due to the decrease of overall energy density for both gravimetric and volumetric energy density. In addition, it is worth noting that the introduction of interlayer will make the assembly process complicated and increase the cost of cells.
Adsorbents such as Al2O3, TiO2, and MnO2 are widely reported to bind polysulfides through physical and/or chemical interactions, which could be a right choice for alleviating shuttle effect of polysulfides and thus improve the performance of Li-S batteries (Wei Seh et al., 2013; Liu et al., 2015; Tao et al., 2016; Wu et al., 2019). However, the role of absorbents may be meaningless for pouch cells in industrial production. For the absorption experiment in many reports, the polysulfide concentration is very low (e.g., 0.5–3 mM), and the ratio of absorbent to polysulfides is very high. We listed the ratio of absorbent to polysulfides in Table 1, which is calculated from the absorption experiment in the literatures (Hart et al., 2015; Pang and Nazar, 2016; Tao et al., 2016; Wu et al., 2019). Most of the literatures did not provide the mass of the absorbent in the polysulfides absorption experiments. From Table 1 we can see that the smallest ratio is around 1.7 and the highest one is more than one thousand. The absorption interaction is obvious under such a high ratio, and it is impossible to use such ratio in a real cell. In a commercial pouch cell, the concentration could be supersaturating to as high as 10 M, which is four orders of magnitude higher than that of those polysulfides solution. Considering of the sulfur content, the ratio of polysulfides absorbent to sulfur should be much lower (<0.3). Thus, if the amount of adsorbent is small, the absorption interaction is negligible. If we use a hefty dose of adsorbent to achieve satisfying adsorption effect, it will increase the weight of cells dramatically, leading to a decrease in the energy density of batteries and an increase in the cost.
Mass Loading
If the mass loading of sulfur on the cathode electrode (single side) is 5 mg/cm2, the theoretical areal capacity is as high as 8.4 mAh/cm2. In an industrial process, sulfur will be coated on two sides of aluminum foil, meaning that the theoretical areal capacity of the sulfur cathode is 16.8 mAh/cm2. In some literatures, it is claimed that the mass loading of sulfur is more than 10 mg/cm2 (Fang et al., 2016; Chung and Manthiram, 2018; Song et al., 2018). For example, Chung et al. revealed a coaxial-graphene-coated cotton-carbon cathode of Li-S batteries with sulfur loading as high as 57.6 mg/cm2 (Chung and Manthiram, 2018). Although the cathode delivers impressive electrochemical performance using CR2032 coin cells, whereas sulfur loading beyond 10 mg/cm2 is too high and not feasible for pouch cells due to severe electrochemical polarization. In addition, for industrial process, the thickness of electrodes (single side) of Li-ion batteries is usually 100–120 μm, whereas, the value for Li-S batteries could more than 200 μm, which is mainly due to the much higher porosity of the cathodes (>60%, usually around 70%). The volumetric energy density will be largely reduced due to the large porosity. Thus, the porosity of electrodes for Li-S batteries should be optimized to maximize their volumetric capacity. Moreover, in Li-S pouch cells, significant cell volume changes during operation will bring an enormous challenge for manufacture cathodes, design of the individual cells, and cell packs.
Electrolyte
The electrolyte is a critical factor because its dose largely determines the energy density of Li-S batteries and has drawn sharply increasing attention in recent years (Pang et al., 2016; Judez et al., 2017; Watanabe et al., 2017; Liu et al., 2018; Ye et al., 2018). It is vital to select electrolyte of Li-S batteries. Carbonates are a suitable choice for Li-ion batteries, whereas the choice changes for Li-S batteries. The selection starts with liquid electrolytes, including aliphatic amines, carbonates and then ethers (Manthiram et al., 2014). So far, LiN(SO2CF3)2 (LiTFSI) lithium salt in mixtures of 1,2-dimethoxyethane (DME) and 1,3-dioxolane (DOL) has been the most used liquid electrolyte for Li-S batteries. In addition, ionic liquids could be a good choice for the electrolyte of Li-S batteries, owing to their incredible properties including non-volatility, high thermal stability, and high ionic conductivity (Watanabe et al., 2017).
For Li-ion batteries, the regular dose of electrolyte is ~3 g/Ah in the industrial production process. Here, we refer to the parameters of 465473-type pouch cells (Figure 5), which are usually used in the small-scale test for Li-ion batteries to roughly estimate the specific energy of Li-S batteries and highlight the importance of electrolyte. The detailed parameters are listed in Table 2. The layer number of cathode and anode are 10 and 11 layers, respectively. The pouch cells are assembled using a lamination process. It is noted that the capacity of sulfur composites has a reversible value of 1,000 mAh/g (based on sulfur mass). Assuming that the amount of electrolyte in the Li-S pouch cell is 3 g/Ah for a 5 mAh/cm2 energy density sulfur cathode (5 mg/cm2 single side), thus the electrolyte usage is 15 mg/cm2, which is equal to an E/S ratio of 3.
The capacity of lithium foil is 15 mAh/cm2, which is designed to triple that of sulfur, then the thickness of lithium foil is 150 μm (75 μm for one side), and the weight of lithium foil is around 8.1 mg/cm2. For a 1 Ah pouch cell, the weight of the jellyroll is estimated to be ~6.6 g, and the energy density is calculated to be only ~320 Wh/kg. If the mass of electrolyte is reduced to 1 g/Ah, and the weight of pouch cells is decreased to ~4.6 g, the specific energy can reach 459 Wh/kg. Thus, it is vital to minimize the amount of electrolyte used in pouch cells for Li-S batteries to maximize their specific capacity and energy. As for coin cells, it is demonstrated that a coin cell with low E/S ratio of 4.2 and high sulfur loading of 57.6 mg/cm2 still delivers impressive specific capacity (Chung and Manthiram, 2018), however, with such high E/S ratio, the specific energy is <270 Wh/kg for pouch cells. If an excessive electrolyte (E/S ratio > 11 mL/g) is used (McCloskey and McCloskey, 2015), the specific energy of pouch cells could be <140 Wh/kg, which is even lower than that of the advanced Li-ion batteries. As claimed in a previous report, only small E/S ratios enable high energy density cells (Hagen et al., 2014).
The solid electrolyte is an idea choice referring to the capability of blocking the shuttle effect of polysulfides and safety problem (Pang et al., 2016; Judez et al., 2017; Liu et al., 2018). Recently, Judez et al. have reported a lithium bis(fluorosulfonyl)imide/poly(ethylene oxide) (LiFSI/PEO) polymer used as solid electrolyte for Li-S batteries (Judez et al., 2017). The batteries with LiFSI/PEO solid polymer electrolytes could effectively suppress the shuttle effect of polysulfides which usually occur in the batteries with liquid electrolytes (Figure 6A). The LiFSI/PEO solid polymer electrolyte membrane is free-standing and transparent (Figure 6B), and exhibits an impressive ion-transport behavior comparable to that of conventional LiTFSI/PEO electrolyte (Figure 6C). The cell with LiFSI/PEO electrolyte delivers high areal capacity of 0.5 mAh cm−2, relatively good rate capacity and a discharge capacity as high as 800 mAh with Coulombic efficiency of 95% (Figure 6D).
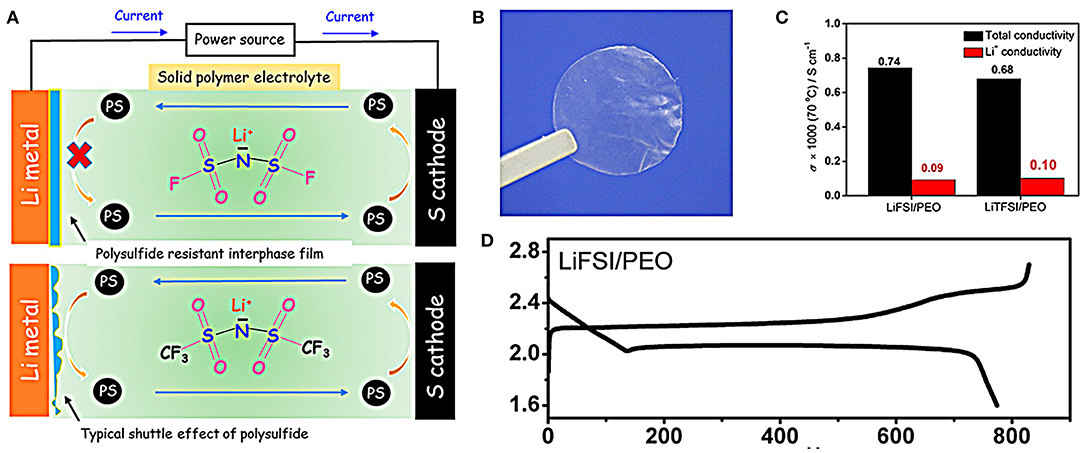
Figure 6. (A) Work schematic diagram of batteries with solid and liquid electrolyte. (B) Digital photo of the as-prepared membrane of the LiFSI/PEO electrolyte. (C) Total and Li+ conductivity of the LiFSI/PEO and LiTFSI/PEO electrolytes at 70°C. (D) Discharge curves of the Li-S cell using the LiFSI/PEO electrolyte. Reproduced from Chung and Manthiram (2018). Copyright© 2017 American Chemical Society.
Although solid electrolyte will be ultimate for commercialization of Li-S batteries, there is a long way to go before the real application of solid electrolyte on pouch cells and battery packs. Many severe issues should be noted on the solid electrolyte including the optimization of the interface between electrode and electrolyte, the improvement of Li+ migration in the solid electrolyte, and production cost, the cycling life, and rate capacity of batteries.
Additive
If lithium metal is directly exposed to the electrolyte, many side reactions occur at the interface between lithium and electrolyte, leading to the severe corrosion of lithium. Thus, scientists devote themselves to minimize the environmental exposure of lithium metal in the electrolyte by adding some additives (Ding et al., 2013). Moreover, compact passivation film forms on the surface of lithium metal after the addition of additives, leading to improved stability and extended cycling performance for Li-S batteries. At present, LiNO3 is the most commonly used additive in the electrolyte to improve the electrochemical performance of Li-S batteries (Adams et al., 2017). However, only use nitrate is hard to effectively protect lithium metal due to its continuous consumption caused by the breakdown of the passivation film during repeated discharge/charge process. It is suggested that metal ions can also be used as electrolyte additives and form metal or alloy layers on the lithium surface to enhance the stability of lithium anode. Gao group introduced lanthanum nitrate (La(NO3)3) as an electrolyte additive for Li-S batteries (Tao et al., 2016). After the addition of La(NO3)3, La3+ ions are rapidly reduced by lithium metal to lanthanum metal, which then reacts with polysulfides ions (Sn2−) to produce polysulfides lanthanum, such as La2S3. The formed La2S3, together with Li2S2/Li2S and LixSOy constitute the passivation film on the surface of Li metal, leading to obvious improvement in the electrochemical performance. Zeng et al. have investigated the effect of additives of transition metal cations on Li-S batteries (Zeng et al., 2019). The results suggest that some transition cations especially Zn cations exhibit a positive effect on enhancing rate capability and Coulombic efficiency of Li-S batteries. Although those additives mentioned above can remarkably promote the performance of coin cells, the improvement could be largely compromised for pouch cells. Lithium used in coin cells are much smaller than in pouch, and lithium plating and stripping phenomena are more local than global. At present, the only effective electrolyte additive for pouch cells is still LiNO3, which improved the Coulombic efficiency significantly, but batteries still suffer from short circuit, and lithium pulverization. Other additives like La(NO3)3, transition metal cations may worth trying in pouch cells. The kind of additives should be rationally selected, and the additive amount should be carefully optimized in consideration of actual performance improvement and cost of batteries.
Safety
Safety is the most critical factor when it comes to the daily usage and commercialization of Li-S batteries. The enhancement of safety of Li-S batteries can be achieved by modifying metal anodes (Xu et al., 2014; Lin et al., 2017), optimizing cathode materials (Wang et al., 2015; Cleaver et al., 2018), designing new separators (Chung et al., 2015; Ma et al., 2016; Li M. et al., 2018; Wang et al., 2019), selecting suitable electrolyte (Pang et al., 2016; Judez et al., 2017; Liu et al., 2018), adding additives (Liu et al., 2016; Zeng et al., 2019) related discussions can be found in the above sections. Here, we mainly discuss safety involving the choice of solvent and the recycling of lithium. As discussed above, the most commonly used electrolyte is 1 M LiTFSI in 1:1 w/w DOL/DME with lithium nitrate as additive. The boiling point of 1,3-dioxolane and 1,2-dimethoxyethane is 78 and 83°C (at 100 kPa), respectively. They are both highly flammable, thus leading to large potential safety problems. However, few published works are focusing on the safety problems of Li-S batteries. It is necessary to seek new solvents with high boiling point and chemical stability for safe Li-S batteries. Using a mixture of several solvents could be a good choice. The ionic liquid is a promising electrolyte, but its cost needs to be further reduced. It should be noted that the low solubility of sulfur in ionic liquid would result in inferior utilization of sulfur with poor electrochemical performance. Solid-state electrolytes will be the ultimate choice for Li-S batteries.
Moreover, as the limited lithium source on earth, recycling of the lithium source form spent Li-S batteries is important if Li-S is commercialized in the further. The disposal and recycling of spent Li-S batteries are hazardous. After cycling, the pulverized lithium metal is highly reactive, and the organic solvent is quite flammable, which could catch fire easily when spent Li-S batteries are opened and disposed of in the air. Detailed studies need to be taken and special attention should be specially paid.
Conclusion
We present the differences between the coin cell and the pouch cell in this review. Undoubtedly, there is a long way to go from coin cells to pouch cells. When doing the research in coin cells, we should always consider to use more realistic parameters for sulfur content, loading, lithium mass, etc., but not just show fantastic data. Many materials and methods available for coin cells generally are not suitable for pouch cells. Engineers need to check and choose appropriate and effective strategies for pouch cells in order to realize the commercialization of Li-S batteries. We suggest that the future researches on commercial Li-S batteries should focus on the following points:
1) The modification of lithium metal with multifunctional and cost-effective current collectors or stabilized coating layers to buffer the infinite volume change of lithium and protect lithium from corrosion. Lithium dendrites should be specially paid and suppressed as much as possible to avoid the occurrence of safety problems.
2) The development of cathode preparation craft using common carbon (for example, super P carbon, black acetylene carbon, and carbon nanotube) and sulfur species on a large scale. The cathode materials exhibit not only good electrochemical performance but also are low-cost to the competitiveness of commercially available Li-S batteries.
3) Exploration of novel separators to minimize the transport of lithium polysulfides, suppress shuttle effect, and enhance the utilization of the efficiency of sulfur. Moreover, the cost should be carefully evaluated.
4) Selection suitable electrolytes and additives for pouch cells. The selected new additives or electrolytes should be tested and verified under certain sulfur loading and limited excess of lithium. Solid electrolytes will be the ultimate choice for commercially available Li-S batteries.
5) Optimization of sulfur mass loading for maximizing the capacity of pouch cells. It is unrealistic for blindly pursuing high sulfur content for more than 10 mg/cm2 in pouch cells. The sulfur mass loading should be cautiously designed for commercially available Li-S batteries' competitive energy density, cycling life, and low cost.
6) Reliable test methods are required to assess the safety of Li-S batteries. More advanced technologies in material processing, cell manufacture, cell package, and cell control & management need to be developed.
7) Development of all-solid-state Li-S batteries.
In the near future, we will focus on the application of Li-S batteries on uncrewed aerial vehicles. The Li-S pouch cells are assembly using cost-effective materials including common carbon, separator modified with commercial material, suitable additives, etc. The battery packs are initially designed to be ≥400 Wh kg−1 energy density and ≥100 cycles.
Author Contributions
KZ and CW wrote the article. CW and LM came up with the topic and revised the manuscript. ZC and FK helped with the discussion and collected information from the literature. YY, WW, and AW revised the manuscript and gave suggestions.
Funding
This work was supported by the Young Scientists Fund of the National Natural Science Foundation of China, Grant No. 51602223 and Scientific Research Foundation of Qufu Normal University (613710).
Conflict of Interest
The authors declare that the research was conducted in the absence of any commercial or financial relationships that could be construed as a potential conflict of interest.
References
Abbas, S. A., Ding, J., Wu, S. H., Fang, J., Boopathi, K. M., Mohapatra, A., et al. (2017). Modified separator performing dual physical/chemical roles to inhibit polysulfide shuttle resulting in ultrastable Li–S batteries. ACS Nano 11, 12436–12445. doi: 10.1021/acsnano.7b06478
Adams, B. D., Carino, E. V., Connell, J. G., Han, K. S., Cao, R., Chen, J., et al. (2017). Long term stability of Li-S batteries using high concentration lithium nitrate electrolytes. Nano Energy 40, 607–617. doi: 10.1016/j.nanoen.2017.09.015
Barghamadi, M., Best, A., Hollenkamp, A. F., Mahon, P., Musameh, M., Rüther, T., et al. (2016). Optimising the concentration of LiNO3 additive in C4mpyr-TFSI electrolyte-based Li-S battery. Electrochim. Acta 222, 257–263. doi: 10.1016/j.electacta.2016.10.169
Bruce, P. G., Freunberger, S. A., Hardwick, L. J., and Tarascon, J. M. (2011). Li–O2 and Li–S batteries with high energy storage. Nat. Mater. 11:19. doi: 10.1038/nmat3191
Chang, C. H., Chung, S. H., and Manthiram, A. (2016). Effective stabilization of a high-loading sulfur cathode and a lithium-metal anode in Li-S batteries utilizing SWCNT-modulated separators. Small 12, 174–179. doi: 10.1002/smll.201502505
Cheng, Q., Li, A., Li, N., Li, S., Zangiabadi, A., Li, T.-D., et al. (2019). stabilizing solid electrolyte-anode interface in li-metal batteries by boron nitride-based nanocomposite coating. Joule 3, 1510–1522. doi: 10.1016/j.joule.2019.03.022
Cheng, X.-B., Yan, C., Huang, J.-Q., Li, P., Zhu, L., Zhao, L., et al. (2017). The gap between long lifespan Li-S coin and pouch cells: the importance of lithium metal anode protection. Energy Storage Mater. 6, 18–25. doi: 10.1016/j.ensm.2016.09.003
Chung, H.-S, Han, P., Singhal, R., Kalra, V., and Manthiram, A. (2015). Lithium–sulfur batteries: electrochemically stable rechargeable lithium–sulfur batteries with a microporous carbon nanofiber filter for polysulfide. Adv. Energy Mater. 5:1500738. doi: 10.1002/aenm.201570098
Chung, H. S., and Manthiram, A. (2018). Designing lithium-sulfur cells with practically necessary parameters. Joule 2, 710–724. doi: 10.1016/j.joule.2018.01.002
Cleaver, T., Kovacik, P., Marinescu, M., Zhang, T., and Offer, G. (2018). Perspective—commercializing lithium sulfur batteries: are we doing the right research? J. Electrochem. Soc. 165, A6029–A6033. doi: 10.1149/2.0071801jes
Ding, F., Xu, W., Graff, G. L., Zhang, J., Sushko, M. L., Chen, X., et al. (2013). Dendrite-free lithium deposition via self-healing electrostatic shield mechanism. J. Am. Chem. Soc. 135, 4450–4456. doi: 10.1021/ja312241y
Du, W. C., Zhang, J., Yin, Y. X., Guo, Y. G., and Wan, L. J. (2016). Sulfur confined in sub-nanometer-sized 2 D graphene interlayers and its electrochemical behavior in lithium–sulfur batteries. Chem. Asian J. 11, 2690–2694. doi: 10.1002/asia.201600449
Fang, R., Zhao, S., Hou, P., Cheng, M., Wang, S., Cheng, H. M., et al. (2016). 3D interconnected electrode materials with ultrahigh areal sulfur loading for Li–S batteries. Adv. Mater. 28, 3374–3382. doi: 10.1002/adma.201506014
Fang, R., Zhao, S., Sun, Z., Wang, D. W., Cheng, H. M., and Li, F. (2017). More reliable lithium-sulfur batteries: status, solutions and prospects. Adv. Mater. 29:1606823. doi: 10.1002/adma.201606823
Hagen, M., Fanz, P., and Tübke, J. (2014). Cell energy density and electrolyte/sulfur ratio in Li–S cells. J. Power Sources 264, 30–34. doi: 10.1016/j.jpowsour.2014.04.018
Hart, C. J., Cuisinier, M., Liang, X., Kundu, D., Garsuch, A., and Nazar, L. F. (2015). Rational design of sulphur host materials for Li–S batteries: correlating lithium polysulphide adsorptivity and self-discharge capacity loss. Chem. Commun. 51, 2308–2311. doi: 10.1039/C4CC08980D
He, J., Chen, Y., and Manthiram, A. (2018). Vertical Co9S8 hollow nanowall arrays grown on a Celgard separator as a multifunctional polysulfide barrier for high-performance Li–S batteries. Energy Environ. Sci. 11, 2560–2568. doi: 10.1039/C8EE00893K
Hu, G., Xu, C., Sun, Z., Wang, S., Cheng, H. M., Li, F., et al. (2016). 3D graphene-foam–reduced-graphene-oxide hybrid nested hierarchical networks for high-performance li–S batteries. Adv. Mater. 28, 1603–1609. doi: 10.1002/adma.201504765
Ji, L., Rao, M., Zheng, H., Zhang, L., Li, Y., Duan, W., et al. (2011). Graphene oxide as a sulfur immobilizer in high performance lithium/sulfur cells. J. Am. Chem. Soc. 133, 18522–18525. doi: 10.1021/ja206955k
Ji, X., Lee, K. T., and Nazar, L. F. (2009). A highly ordered nanostructured carbon–sulphur cathode for lithium–sulphur batteries. Nat. Mater. 8:500. doi: 10.1038/nmat2460
Jing, K.-H., Kong, L.-L., Liu, S., Li, R.-G., and Gao, P.-X. (2015). Protected lithium anode with porous Al2O3 layer for lithium–sulfur battery. J. Mater. Chem. A 3, 12213–12219. doi: 10.1039/C5TA01490E
Judez, X., Zhang, H., Li, C., González-Marcos, J. A., Zhou, Z., Armand, M., et al. (2017). Lithium Bis(fluorosulfonyl)imide/Poly(ethylene oxide) polymer electrolyte for all solid-state Li–S cell. J. Phys. Chem. Lett. 8, 1956–1960. doi: 10.1021/acs.jpclett.7b00593
Kong, W., Yan, L., Luo, Y., Wang, D., Jiang, K., Li, Q., et al. (2013). Ultrathin MnO2/graphene oxide/carbon nanotube interlayer as efficient polysulfide-trapping shield for high-performance Li–S batteries. Adv. Funct. Mater. 27:1606663. doi: 10.1002/adfm.201606663
Li, H., Yang, X., Wang, X., Liu, M., Ye, F., Wang, J., et al. (2015). Dense integration of graphene and sulfur through the soft approach for compact lithium/sulfur battery cathode. Nano Energy 12, 468–475. doi: 10.1016/j.nanoen.2015.01.007
Li, M., Wang, C., Miao, L., Xiang, J., Wang, T., Yuan, K., et al. (2018). A separator-based lithium polysulfide recirculator for high-loading and high-performance Li–S batteries. J. Mater. Chem. A 6, 5862–5869. doi: 10.1039/C8TA00459E
Li, N. W., Yin, Y. X., Yang, C. P., and Guo, Y. G. (2016). An artificial solid electrolyte interphase layer for stable lithium metal anodes. Adv. Mater. 28, 1853–1858. doi: 10.1002/adma.201504526
Li, Z., He, Q., Xu, X., Zhao, Y., Liu, X., Zhou, C., et al. (2018). A 3D nitrogen-doped graphene/TiN nanowires composite as a strong polysulfide anchor for lithium–sulfur batteries with enhanced rate performance and high areal capacity. Adv. Mater. 30:1804089. doi: 10.1002/adma.201804089
Lin, D., Liu, Y., and Cui, Y. (2017). Reviving the lithium metal anode for high-energy batteries. Nat. Nanotechnol. 12:194. doi: 10.1038/nnano.2017.16
Liu, S., Li, G. R., and Gao, X. P. (2016). Lanthanum nitrate as electrolyte additive to stabilize the surface morphology of lithium anode for lithium–sulfur battery. ACS Appl. Mater. Interfaces 8, 7783–7789. doi: 10.1021/acsami.5b12231
Liu, X., Li, X., Li, H., and Wu, H. B. (2018). Recent progress of hybrid solid-state electrolytes for lithium batteries. Chem. Eur. J. 24, 18293–18306. doi: 10.1002/chem.201803616
Liu, X., Shan, Z., Zhu, K., Du, J., Tang, Q., Tian, J., et al. (2015). Sulfur electrode modified by bifunctional nafion/γ-Al2O3 membrane for high performance lithium–sulfur batteries. J. Power Sources 274, 85–93. doi: 10.1016/j.jpowsour.2014.10.039
Lu, L., Han, X., Li, J., Hua, J., and Ouyang, M. (2013). A review on the key issues for lithium-ion battery management in electric vehicles. J. Power Sources 226, 272–288. doi: 10.1016/j.jpowsour.2012.10.060
Luo, L.-S., Chung, H., and Manthiram, A. (2016). A trifunctional multi-walled carbon nanotubes/polyethylene glycol (MWCNT/PEG)-coated separator through a layer-by-layer coating strategy for high-energy Li–S batteries. J. Mater. Chem. A 4, 16805–16811. doi: 10.1039/C6TA07709A
Ma, G., Huang, F., Wen, Z., Wang, Q., Hong, H., Jina, J., et al. (2016). Enhanced performance of lithium sulfur batteries with conductive polymer modified separators. J. Mater. Chem. A 4, 16968–16974. doi: 10.1039/C6TA07198H
Manthiram, A., Fu, Y., Chung, S. H., Zoo, C., and Su, Y. S. (2014). Rechargeable lithium–sulfur batteries. Chem. Rev. 114, 11751–11787. doi: 10.1021/cr500062v
McCloskey, B. D., and McCloskey, B. D. (2015). Attainable gravimetric and volumetric energy density of Li–S and Li ion battery cells with solid separator-protected li metal anodes. J. Phys. Chem. Lett. 6, 4581–4588. doi: 10.1021/acs.jpclett.5b01814
Miao, X.-L, Wang, K.-W, Wang, B.-A, Yuan, K.-G., and Yang, Y.-S. (2013). A high sulfur content composite with core–shell structure as cathode material for Li–S batteries. J. Mater. Chem. A 1, 11659–11664. doi: 10.1039/c3ta12079a
Pang, Q., Liang, X., Kwok, C. Y., and Nazar, L. F. (2016). Advances in lithium–sulfur batteries based on multifunctional cathodes and electrolytes. Nat. Energy 1:16132. doi: 10.1038/nenergy.2016.132
Pang, Q., and Nazar, L. F. (2016). Long-life and high-areal-capacity Li–S batteries enabled by a light-weight polar host with intrinsic polysulfide adsorption. ACS Nano 10, 4111–4118. doi: 10.1021/acsnano.5b07347
Park, J., Yu, B.-C., Park, J. S., Choi, J. W., Kim, C., Sung, Y.-E., et al. (2017). tungsten disulfide catalysts supported on a carbon cloth interlayer for high performance Li–S battery. Adv. Energy Mater. 7:1602567. doi: 10.1002/aenm.201602567
Pei, F., Lin, L., Ou, D., Fang, X., and Zheng, N. (2018). A two-dimensional porous carbon-modified separator for high-energy-density Li-S batteries. Joule 2, 323–336. doi: 10.1016/j.joule.2017.12.003
Scheers, J., Fantini, S., and Johansson, P. (2014). A review of electrolytes for lithium–sulphur batteries. J. Power Sources 255, 204–218. doi: 10.1016/j.jpowsour.2014.01.023
Simon, P., Gogotsi, Y., and Dunn, B. (2014). Where do batteries end and supercapacitors begin? Science 343:1210. doi: 10.1126/science.1249625
Song, Y., Zhao, W., Kong, L. G., Zhang, L., Zhu, X., et al. (2018). Synchronous immobilization and conversion of polysulfides on a VO2–VN binary host targeting high sulfur load Li–S batteries. Energy Environ. Sci. 11, 2620–2630. doi: 10.1039/C8EE01402G
Sun, Z., Zhang, J., Yin, L., Hu, G., Fang, R., Cheng, H. M., et al. (2017). Conductive porous vanadium nitride/graphene composite as chemical anchor of polysulfides for lithium-sulfur batteries. Nat. Commun. 8:14627. doi: 10.1038/ncomms14627
Tan, J., Liu, D., Xu, X., and Mai, L. (2017). In situ/operando characterization techniques for rechargeable lithium–sulfur batteries: a review. Nanoscale 9, 19001–19016. doi: 10.1039/C7NR06819K
Tao, X., Wang, J., Liu, C., Wang, H., Yao, H., Zheng, G., et al. (2016). Balancing surface adsorption and diffusion of lithium-polysulfides on nonconductive oxides for lithium–sulfur battery design. Nat. Commun. 7:11203. doi: 10.1038/ncomms11203
Wang, C., Su, K., Wan, W., Guo, H., Zhou, H., Chen, J., et al. (2014). High sulfur loading composite wrapped by 3D nitrogen-doped graphene as a cathode material for lithium–sulfur batteries. J. Mater. Chem. A 2, 5018–5023. doi: 10.1039/C3TA14921H
Wang, C., Wan, W., Chen, J.-T., Zhou, H.-H., Zhang, X.-X., Yuanb, L.-T, et al. (2013). Dual core–shell structured sulfur cathode composite synthesized by a one-pot route for lithium sulfur batteries. J. Mater. Chem. A 1, 1716–1723. doi: 10.1039/C2TA00915C
Wang, C., Wang, X., Wang, Y., Chen, J., Zhou, H., Huang, Y., et al. (2015). Macroporous free-standing nano-sulfur/reduced graphene oxide paper as stable cathode for lithium-sulfur battery. Nano Energy 11, 678–686. doi: 10.1016/j.nanoen.2014.11.060
Wang, Q. Q., Huang, J. B., Li, G., Lin, Z., Liu, B. H., and Li, Z. (2017). A facile and scalable method to prepare carbon nanotube-grafted-graphene for high performance Li-S battery. J. Power Sources 339, 20–26. doi: 10.1016/j.jpowsour.2016.11.038
Wang, S. H., Yin, Y. X., Zuo, T. T., Dong, W., Li, J. Y., Shi, J. L., et al. (2017). Stable li metal anodes via regulating lithium plating/stripping in vertically aligned microchannels. Adv. Mater. 29:1703729. doi: 10.1002/adma.201703729
Wang, Y., He, J., Zhang, Z., Liu, Z., Huang, C., and Jin, Y. (2019). Graphdiyne-modified polyimide separator: a polysulfide-immobilizing net hinders the shuttling of polysulfides in lithium–sulfur battery. ACS Appl. Mater. Interfaces 11, 35738–35745. doi: 10.1021/acsami.9b11989
Watanabe, M., Thomas, M. L., Zhang, S., Ueno, K., Yasuda, T., and Dokko, K. (2017). Application of ionic liquids to energy storage and conversion materials and devices. Chem. Rev. 117, 7190–7239. doi: 10.1021/acs.chemrev.6b00504
Wei Seh, Z., Li, W., Cha, J. J., Zheng, G., Yang, Y., McDowell, M. T., et al. (2013). Sulphur–TiO2 yolk–shell nanoarchitecture with internal void space for long-cycle lithium–sulphur batteries. Nat. Commun. 4:1331. doi: 10.1038/ncomms2327
Weller, C., Thieme, S., Härtel, P., Althues, H., and Kaskel, S. (2017). Intrinsic shuttle suppression in lithium-sulfur batteries for pouch cell application. J. Electrochem. Soc. 164, A3766–A3771. doi: 10.1149/2.0981714jes
Wu, D. S., Shi, F., Zhou, G., Zoo, C., Liu, C., Liu, K., et al. (2019). Quantitative investigation of polysulfide adsorption capability of candidate materials for Li-S batteries. Energy Storage Mater. 13, 241–246. doi: 10.1016/j.ensm.2018.01.020
Xu, W., Wang, J., Ding, F., Chen, X., Nasybulin, E., Zhang, Y., et al. (2014). Lithium metal anodes for rechargeable batteries. Energy Environ. Sci. 7, 513–537. doi: 10.1039/C3EE40795K
Yan, Y., Luo, Y., Ma, J., Li, B., Xue, H., and Pang, H. (2018). Facile synthesis of vanadium metal-organic frameworks for high-performance supercapacitors. Small 14:1801815. doi: 10.1002/smll.201801815
Yang, C. P., Yin, Y. X., Zhang, S. F., Li, N. W., and Guo, Y. (2015). Accommodating lithium into 3D current collectors with a submicron skeleton towards long-life lithium metal anodes. Nat. Commun. 6:8058. doi: 10.1038/ncomms9058
Yang, X., Zhang, L., Zhang, F., Huang, Y., and Chen, Y. (2014). Sulfur-infiltrated graphene-based layered porous carbon cathodes for high-performance lithium–sulfur batteries. Acs Nano, 8, 5208–5215. doi: 10.1021/nn501284q
Ye, Y., Wu, F., Xu, S., Qu, W., Li, L., and Chen, R. (2018). Designing realizable and scalable techniques for practical lithium sulfur batteries: a perspective. J. Phys. Chem. Lett. 9, 1398–1414. doi: 10.1021/acs.jpclett.7b03165
Zeng, W., Cheng, C. S., and Ng, Y.-K. (2019). Effects of transition metal cation additives on the passivation of lithium metal anode in Li-S batteries. Electrochim. Acta 319, 511–517. doi: 10.1016/j.electacta.2019.06.177
Zhang, L., Ling, M., Feng, J., Mai, L., Liu, G., Guo, J., et al. (2018). The synergetic interaction between LiNO3 and lithium polysulfides for suppressing shuttle effect of lithium-sulfur batteries. Energy Storage Mater. 11, 24–29. doi: 10.1016/j.ensm.2017.09.001
Zhang, Y. J., Wang, W., Tang, H., Bai, W. Q., Ge, X. L., Wang, X. L., et al. (2015). An ex-situ nitridation route to synthesize Li3N-modified Li anodes for lithium secondary batteries. J. Power Sour. 277, 304–311. doi: 10.1016/j.jpowsour.2014.12.023
Zheng, S., Yi, F., Li, Z., Zhu, Y., Xu, Y., Luo, C., et al. (2014). Copper-stabilized sulfur-microporous carbon cathodes for Li–S batteries. Adv. Funct. Mater. 24, 4156–4163. doi: 10.1002/adfm.201304156
Zhou, Y., Zhou, C., Li, Q., Yan, C., Han, B., Xia, K., et al. (2015). Enabling prominent high-rate and cycle performances in one lithium–sulfur battery: designing permselective gateways for Li+ transportation in holey-CNT/S cathodes. Adv. Mater. 27, 3774–3781. doi: 10.1002/adma.201501082
Keywords: lithium-sulfur batteries, commercialization, academic research, energy density, gap
Citation: Zhu K, Wang C, Chi Z, Ke F, Yang Y, Wang A, Wang W and Miao L (2019) How Far Away Are Lithium-Sulfur Batteries From Commercialization? Front. Energy Res. 7:123. doi: 10.3389/fenrg.2019.00123
Received: 15 August 2019; Accepted: 21 October 2019;
Published: 15 November 2019.
Edited by:
Ali Eftekhari, Queen's University Belfast, United KingdomReviewed by:
Xifei Li, Xi'an University of Technology, ChinaHuan Pang, Yangzhou University, China
Liqiang Mai, Wuhan University of Technology, China
Copyright © 2019 Zhu, Wang, Chi, Ke, Yang, Wang, Wang and Miao. This is an open-access article distributed under the terms of the Creative Commons Attribution License (CC BY). The use, distribution or reproduction in other forums is permitted, provided the original author(s) and the copyright owner(s) are credited and that the original publication in this journal is cited, in accordance with accepted academic practice. No use, distribution or reproduction is permitted which does not comply with these terms.
*Correspondence: Chao Wang, Y2hhb3dAbWl0LmVkdQ==; Lixiao Miao, bWlhb2x4QGJpdC5lZHUuY24=
†These authors have contributed equally to this work