- Department of Space, Earth and Environment, Chalmers University of Technology, Gothenburg, Sweden
Carbon capture and storage (CCS) is expected to play a key role to achieve deep emission cuts in the energy intensive industry sector. The implementation of carbon capture comes with a considerable investment cost and a significant effect on the plants operating cost, which both depend on site conditions, mainly due to differences in flue gas flow and composition and depending on the availability of excess heat that can be utilized to power the capture unit. In this study we map the costs required to install and operate amine-based post-combustion CO2 capture at all manufacturing plants in Sweden with annual emissions of 500 kt CO2 or more, of both fossil and of biogenic origin, of which there are 28 plants (including a petrochemical site, refineries, iron and steel plants, cement plants and pulp and paper mills). The work considers differences in the investment required as well as differences in potential for using excess heat to cover the steam demand of the capture process. We present the resulting total CO2 capture costs in the form of a marginal abatement cost curve (MACC) for the emission sources investigated. Cost estimations for a transport and storage system are also indicated. The MACC shows that CO2 capture applied to 28 industrial units capture CO2 emissions corresponding to more than 50% of Swedish total CO2 emissions (from all sectors) at a cost ranging from around 40 €/t CO2 to 110 €/t CO2, depending on emission source. Partial capture from the most suited sites may reduce capture cost and, thus, may serve as a low-cost option for introducing CCS. The cost for transport and storage will add some 25 to 40 €/t CO2, depending on location and type of transportation infrastructure.
Introduction
In order to limit global warming in line with The Paris Agreement – to limit warming to well below 2°C – requires global emissions to become zero around the middle of the century. It is also likely that emissions has to be net-negative in the second half of the century since the global society most likely will overshoot the carbon budget required to stabilize climate at a temperature well below 2°C [e.g., (IEA, 2013; Rogelj et al., 2018)]. The basic industries, such as pulp and paper, cement, (petro) chemicals, and ferrous- and non-ferrous metal plants, are large point sources of CO2 emissions and deep cuts in their emissions are therefore required over the next decades. This is a challenge since it will not be sufficient with incremental measures such as improved efficiency and introduction of best available process technologies. Instead, transformative changes in the processes are required. There are only a few such options of which carbon capture and storage (CCS) is one (De Pee et al., 2018). Since CCS can mitigate up to 80–95% of the CO2 emissions from flue gases, it offers a promising mitigation option if applied to the basic industry. Since CCS requires significant amounts of energy, it is important to find ways to integrate the capture process with the rest of the process to achieve as efficient capture as possible.
In this work, we focus on amine-based carbon capture as a reference capture technology. Post combustion capture is a mature capture technology and the processes involved (amine scrubbing of CO2) has been applied in industry for many years. Post combustion is applied in CCS schemes in a number of relatively large-scale projects around the world (Global CCS Institute, 2019), mainly to power plants, and can therefore be seen as proven technology with a TRL level of 8–9, although when applied to industrial emission sources it must be tested and demonstrated before full scale implementation. Other technologies for carbon capture are also promising in specific industrial applications. For example, although less mature, oxy-fuel combustion was evaluated as the least-cost option for a cement plant (Garðarsdóttir et al., 2019), and both oxy-fuel combustion and chemical looping combustion seem promising in terms of energy penalty when CO2 is captured from fluid catalytic cracker plants in oil refineries (Güleç et al., 2020). However, amine-based post combustion is currently the only technology with a potential to be more generally viable, especially when retrofitting existing plants. Thus, the other capture technologies are either less mature, have not been tested at scale or would require that the existing industry process is replaced or redesigned making it difficult to assess not only the technology performance but also the cost of capture.
Yet, the specific capture cost (€/t CO2) applying post combustion, will depend on which process to which it is applied, such as if there is access to internal excess heat to power part of the capture process and on the CO2 concentration in the flue gas and the size of the flue gas flow. The capture cost typically decreases with increased concentration in the flue gas and increased size of the flue gas flow (Garðarsdóttir et al., 2018), although this is not necessarily valid in the cases where there is access to excess heat within the process to which CCS is applied. Two recent examples from the iron and steel industry are given by Sundqvist et al. (2018), who investigate alternatives for partial CO2 capture in the steel industry by utilizing excess heat to power the capture process, and Mandova et al. (2019) who explore the CO2 emission reduction potential of bio-CCS in European steel industry. An example from the cement industry is the techno-economic case study assessment presented by Jakobsen et al. (2017), who conclude, amongst other things, that economy of scale of full-scale capture (in terms of specific capture cost) is nearly outweighed by higher steam cost compared to partial capture, in which case the steam demand can be covered by excess heat.
Literature on carbon capture in petroleum refineries include, for example, a study by Andersson et al. (2016), who did a techno-economic case-study based assessment of excess heat-driven carbon capture, and showed how the specific cost for carbon capture increases with the amount of carbon captured due to decreasing availability of excess heat of sufficiently high temperature. Another example is the study of Berghout et al. (2019) who assessed deployment pathways for emissions reductions in refineries by considering carbon capture in combination with other mitigation options. Several studies have investigated the possibility for carbon capture in the pulp and paper industry [see e.g., Onarheim et al. (2017) and references therein]. Based on such studies it may be concluded that the potential for post-combustion technology is more promising for chemical market pulp mills than for integrated pulp and paper mills due to potentially larger amounts of excess heat available in chemical market pulp mills that can be used to cover the heat demand of the capture process. For systematic reviews of academic literature on industrial CCS including its cost, see Kuramochi et al. (2012) and Leeson et al. (2017). In their review they conclude that reported costs for CCS vary within a large range and that the uncertainty in future costs of industrial CCS is significant.
Onarheim et al. (2015) mapped the potential for CCS in the Nordic countries and highlight the sources with highest potential. Following their work, our recent study, (Garðarsdóttir et al., 2018), mapped the investment required to install carbon capture (amine absorption) at all industrial sites in Sweden with annual emissions of 500 kt CO2 or more (fossil and biogenic), which corresponds to more than 80% of the CO2 emissions from the basic industry. While site-specific conditions were considered for the estimation of capital costs, the steam cost was assumed to be the same for all sites in this study. The study concludes that there are large differences in the investment required between industrial sectors and even between industrial sites within the same sector where, as mentioned above, the size of the CO2 source and the CO2 concentration are important factors. In the case of Sweden, steel mills, cement plants, and the recovery boiler of large pulp mills require a relatively low specific investment. Although, the investment is a considerable share of the total CO2 capture cost, the cost of steam is generally the dominating cost item. As discussed by Biermann et al. (2018), the steam cost depends on the current plant energy system, e.g., the amount of excess heat available, access to a steam cycle, and capacity of the present steam generation equipment. The cost of steam will also depend on energy market conditions and different steam generation options may be favored over time or dependent on time of the year or day. Consequently, and as also supported by several of the papers cited above, the cost of steam will be highly site specific and in cases where there is excess heat available to generate the steam required for the capture process, this has the potential to significantly reduce the cost of carbon capture.
This work follows our previous work (Garðarsdóttir et al., 2018) using Sweden as a case study. Sweden is a heavily industrialized region and in addition to being representative for a region with large industrial emission sources, there are also large biogenic emission sources whereas electricity and heat generation have low fossil-fuel based carbon emissions (23 g CO2/kWh produced), with plans to phase out or shift fuel in the remaining fossil-fuel plants.
The long-term climate goal set by the Swedish Government is that Sweden should have net zero greenhouse gas emissions by Year 2045, which translates to 85% reduction from domestic emissions where the remaining 15% can be met by measures abroad, so called negative emissions from bio-CCS (BECCS) or land use change measures (Swedish Ministry of the Environment, 2017). In 2017, the total Swedish emissions of fossil greenhouse gases were approximately 53 Mt of CO2 equivalents per year of which 43 Mt are CO2 emissions. More than one third of the fossil-fuel CO2 emissions originates from the basic industry (oil refineries 3 Mt/year, minerals/cement 3 Mt/year, iron and steel 6 Mt/year, chemicals 1.5 Mt/year) [Naturvårdsverket (Swedish Environmental Protection Agency), 2018]. The large point sources of biogenic CO2 emissions are market pulp mills and integrated pulp and paper mills. This adds another 20 Mt/year of CO2 to the total emissions (Swedish Environmental Protection Agency [SEPA], 2016b). In Sweden, very few, if any, new industrial plants can be assumed to be built within the foreseeable future, which means that CCS should be considered as a retrofit option for existing sites. Due to the magnitude of emissions from the pulp and paper industry, there is significant potential for negative emissions by means of BECCS. The potentially significant contribution of BECCS for national greenhouse gas reduction is similar to a country like Brazil, for which it has been concluded that carbon capture from biogenic sources in ethanol production could play an important role for carbon mitigation provided sufficiently strong climate policy are put in place (Rochedo et al., 2016). However, an important difference between the Swedish biogenic emission sources investigated in this work and the Brazilian cases is that the Swedish emission sources are in the form of pulp and paper plants, which are much larger than the ethanol plants in Rochedo et al. (2016). This, together with their coastal location, makes transport (by ship) much less costly than the costs of the large (inland) pipeline network required to be established for ethanol plant capture in Brazil.
As in our previous work (Garðarsdóttir et al., 2018) we investigate industrial emission sources in Sweden of at least 500 kt CO2/a. In this study we extend our previous study by also considering differences between the site’s potential for using excess heat to cover the heat demand of an amine-based capture process. This is achieved by indicatively mapping the energy systems of the industrial plants to estimate the cost of steam at the individual sites. As a result, total CO2 capture costs are presented as a marginal abatement cost curve (MACC) for all Swedish industrial sites with CO2 emissions exceeding 500 kt/a. A curve indicating the cost for a transport and storage system connecting successively more emission sources is also generated. Thus, the work provides the societal cost for amine-based carbon capture based on site specific conditions for existing industrial sites within the basic industry.
Materials and Methods
To estimate the availability of industrial low-cost heat for CO2 capture, an inventory of Swedish industrial sites and their excess heat levels was conducted utilizing the Chalmers Industrial Case Study Portfolio (ChICaSP) (Svensson et al., 2019).
Chalmers Industrial Case Study Portfolio
A detailed description of the ChICaSP can be found in Svensson et al. (2019). In short, it includes the 65 industrial sites in Sweden totaling (fossil+biogenic) CO2 emissions >50 kt/a in 2016 within the mineral extraction and manufacturing sectors and includes data with a focus on process heat use and carbon dioxide emissions. The type of data included in CHICaSP is reported annually and openly from government agencies, industry organizations and similar, as shown in Table 1. In addition, the database also contains site specific information available from various research projects as exemplified in Table 2, giving more detailed information on the energy system of individual sites, although the coverage and consistency between sites are lower.
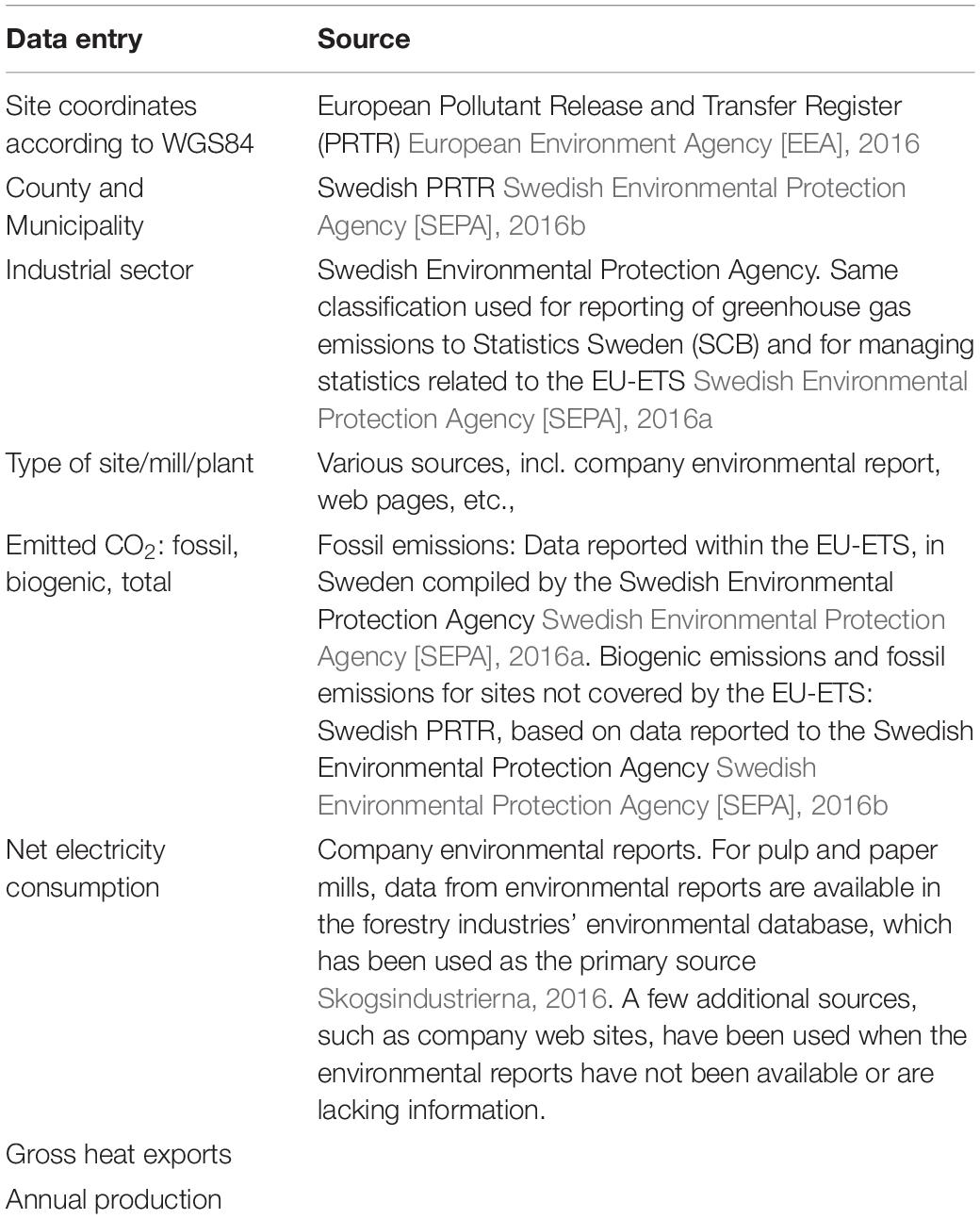
Table 1. Publicly available data categories summarized for all industry sites in the ChICaSP data base.
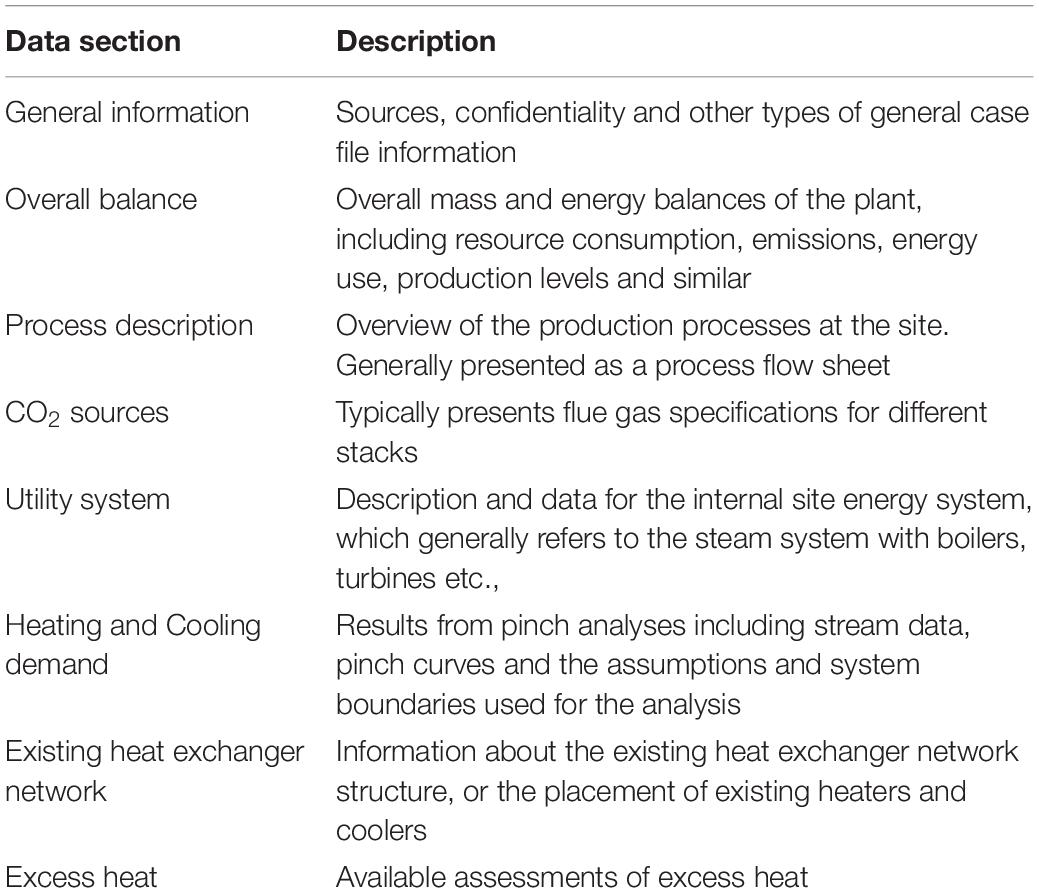
Table 2. Case specific data categories summarized in the ChICaSP data base when available for the specific industry site.
In this study, ChICaSP was used to identify the industrial sites with total fossil and biogenic CO2 emissions of above 500 kt per year or more, a limit which was chosen arbitrarily to include the majority of the emission and focus on the units for which the specific capture cost is expected to be the lowest. The 500 kt threshold give a total of 28 industrial plants investigated in this work and accounting for more than 80% of the CO2 emissions from the basic industry and with the distribution of the CO2 emissions between the sites given in Table 3. The estimation of the availability of low-cost heat for carbon capture at the investigated sites by the case study portfolio as further described in the following section.
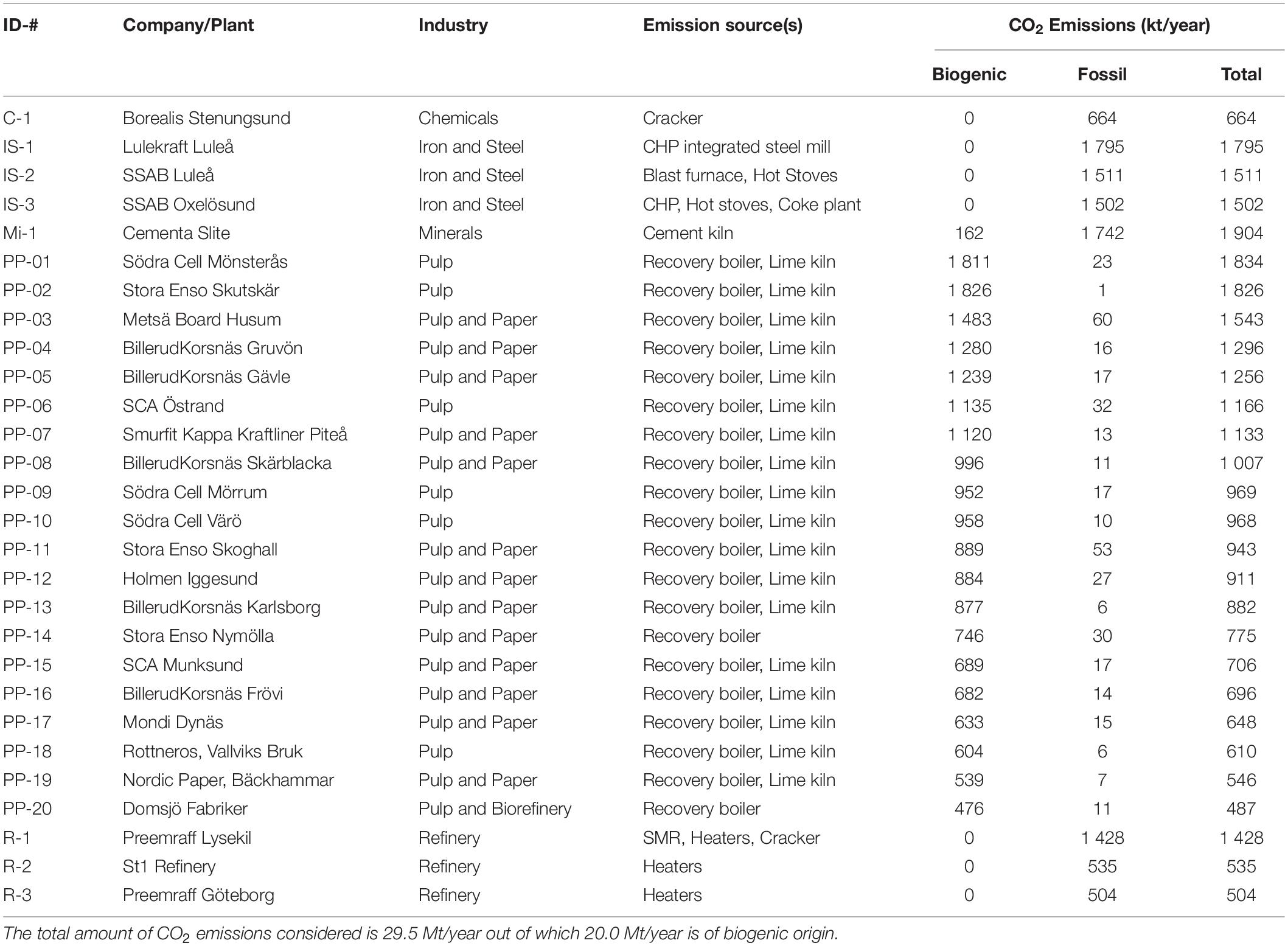
Table 3. Industrial plants considered in the study, i.e., all Swedish industrial plants with annual CO2 emissions of 500 kt or more (Year 2016 data).
Mapping of Site-Specific Industrial Excess Heat Levels
In this work, we define the term excess heat as all heat that is or can be made available at the site at a lower cost than the cost required for new steam generation capacity. This implies that also heat that would require some investment, e.g., in waste heat boilers or retrofits of heat exchanger networks, is considered as a potential excess heat source. Consequently, excess heat may refer to heat generated from cooling of process streams as well as heat from waste heat boilers from currently unutilized off-gases, or from utilizing spare capacity in the site’s existing utility system. We also include steam that is currently utilized for low-pressure condensing power generation. However, it is assumed that heat for carbon capture should not compete with current district heating deliveries.
The steam temperature required for regenerating the amine was considered to be 130°C (3 bar), which also sets the temperature requirement for the excess heat. The heat demand for carbon capture depends on a number of factors in solvent and process design and site conditions but is typically in the range of 2.5–3.5 MJ/kg CO2 captured. The quantity of excess heat at a site expressed in MJ per kg of carbon emitted can be compared to the heat demand of carbon capture to give an indication of the feasibility of using excess heat for the capture process.
Since data on process heating and cooling demands were not available with the same level of detail for all industrial sites, and furthermore, may change with plant retrofits for increased heat recovery, only indicative estimations were sought for the excess heat assessments. In this work, excess heat-driven carbon capture was considered if the amount of excess heat at sufficient temperature was estimated to be at least around 1 MJ per kg CO2 emitted, i.e., if about one third of the heat required for capture of all the emitted CO2 could be provided by excess heat. The chosen value is considered a reasonable assumption to represent a trade-off, which does not exclude too many sites to be of interest for excess heat-driven capture (which would be the case with a higher cut-off value) and also ensures that partial capture plants sized by the availability of excess heat gets acceptable economy of scale or that sites with 90% capture attain a significant reduction in capital costs for new heat production when excess heat is considered.
The excess heat estimation was made based on the data available in ChICaSP. Of the 28 industrial sites included in the analysis, data on the plant energy system detailed enough for a quantitative (MJ/kg CO2) or descriptive (above or below approximately 1 MJ/kg CO2) estimate was available for 12 sites (43%). For the remaining 16 sites, the excess heat potential was estimated based on results and experience from studies of similar process plants and model mills. In particular, 14 of these remaining sites are of a type of pulp and paper mill for which detailed models are available (Kraft market pulp mills, TMP mills, integrated and non-integrated mills), developed mainly within the Swedish research program FRAM (Future Resource Adapted Mill) (Delin et al., 2005). An estimate of the excess heat available for capture was made using the process models for a standard mill and the information about the type of mill available from the ChICaSP. The energy system of the remaining two sites (a cement plant and an oil refinery) were estimated by extrapolating from similar sites in ChICaSP. It should, thus, be noted that the data quality of the estimated excess heat potential varies from actual site measurement data to data acquired from site modeling based on statistics for the type of industry.
Cost Estimations
We evaluate the costs for CCS assuming a standard MEA-based CO2 absorption process is adopted for all industrial processes. Consequently, we do not account for potential future technology development such as new absorbents or the adoption of more suitable capture technologies for specific industrial processes. The resulting marginal abatement cost curve may therefore be regarded as a conservative estimate of CCS in the Swedish industrial sector with respect to its focus on high TRL options.
The investment cost for CO2 capture applied in this study is adopted from our previous work (Garðarsdóttir et al., 2018). In that work, the capital cost (CAPEX) was estimated with a detailed individual factor estimation method and considered the treated volume flow of gases and the flue gas CO2 concentration of the individual stacks at each site. The costs were calculated for 90% capture rate. The annualized CAPEX is calculated with 25 years lifetime (out of which 3 years are for construction) and a 7.5% rate of return.
The transport and storage costs are estimated based on the work by Kjärstad et al. (2016) and adopted to the present analysis by Garðarsdóttir et al. (2018). The transport and storage solution includes storage in the Norwegian North Sea or Baltic Sea1 and transport by ship from five hubs distributed near the Swedish coast in proximity to large emission sources. As an approximation, these are assumed to correspond to Hub 1-2 and 4-6 in Kjärstad et al. (2016), [see also Figure 1 of Kjärstad et al. (2016)], which shows these transport hubs on a map). Note, however, that the costs of the transport hubs do not include the costs for an onshore collection system from sources to the hub. The cost estimation assumes that the entire investment cost for a transport hub that connects all relevant emission sources to a storage site is taken once the first source is connected to that hub. The specific investment cost for operating at a specific hub is, thus, decreased as more sources and larger flows of CO2 is handled at each hub, respectively. The sources are assumed to be connected in order of specific capture cost, i.e., the source with the lowest specific capture cost is connected first. Each hub is also associated with a fixed specific operating cost, which in this work is set to 9 €/t CO2 transported. The assumption that the transport cost is independent of the distance is reasonable for ship transports as, e.g., Kjärstad et al. (2016) showed that there is only a weak cost dependence on distance for ship transport. The storage cost differs depending on which storage location is connected to each hub and is either 7 or 15 €/t CO2 (Garðarsdóttir et al., 2018). For more details on what is included in the cost of the transport and storage infrastructure see Kjärstad et al. (2016).
Operating expenditures (OPEX) are dominated by the cost of heat supply for solvent regeneration, but also include other utilities, maintenance, and labor. The operational costs are divided into fixed and variable OPEX. Fixed costs include maintenance and labor costs and are not dependent on the plant utilization. The annual maintenance cost is estimated as 4% of the investment. Labor cost for operators and engineers is set to 820 k€/a independent of plant size. All utilities are considered to be delivered by external systems and are, thus, considered as pure operational costs (i.e., no investments are required). Utilities include the cost of steam, electricity and cooling water required to run the process and are directly connected to the amount of CO2 captured. The specific steam demand (Dsteam; tonne of steam/kg CO2 captured) depends on the initial CO2 concentration and the capture rate as the energy to separate CO2 from the gas stream is higher the lower the CO2 concentration. The specific steam demand will also depend on the design of the absorption process and the solvent used; however, only simple cycle with MEA is considered in this work. The price of steam (Psteam; €/t) depends on the site and energy market conditions. The specific steam cost (Csteam; €/kg CO2 captured) is given by the following correlation with the steam demand derived from the estimates in Garðarsdóttir et al. (2018).
where XCO_2 is the volume fraction in percent of CO2 in the inlet stream. The electricity and cooling duty are not as dependent on the CO2 concentration of the inlet stream and the site-specific conditions as the steam demand and therefore their specific costs are kept constant in the cost estimation.
The price of steam (Psteam) was estimated based on the indicative availability of excess heat estimated for the sites. The cost for erecting a new boiler and steam cycle on site results in a cost of steam of 20 €/MWh with the assumptions used in Ali et al. (2018). However, if excess heat can be used to generate parts of the required steam, the cost is obviously lower. Table 4 gives one example for each type of industry of how the cost of steam may be affected depending on the steam demand. The pulp mill as well as the steel mill have relatively large steam cycles on site from which steam could be bled. For these plants, the cost is related to the loss in electricity production from the steam cycles. The cement plant and the refinery have some excess heat in the form of warm off-gases that could be used to generate low-pressure steam. In these cases, steam costs are related to the cost of the waste heat boilers. The steel mill also has excess heat within the process that may be recovered, e.g., from flue gas heat recovery, coke dry quenching, and dry slag granulation. The excess heat sources are, thus, more diversified for the steel mill than for the other plants.
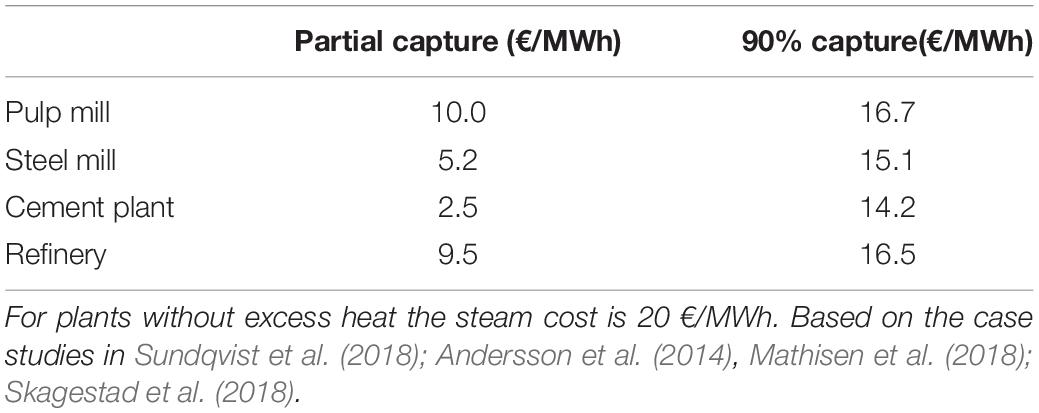
Table 4. Example for one particular site of each industrial sector of the assumed cost of steam for carbon capture through amine absorption for plants with excess heat above 1 MJ/kg CO2 generated depending on type of industry and degree of capture.
The cost levels indicated in Table 4 were applied for estimating site-specific steam costs according to the identified excess heat classifications. Note, however, that Table 4 is based only on an example of one particular site per industrial sector. If the excess heat potential was estimated to be low, the steam cost was taken at the level of 20 €/MWh, corresponding to the costs of new boiler and steam cycle capacity.
If the excess heat potential for a particular site was estimated to be high (i.e., higher than the above mentioned threshold of 1 MJ/kg emitted CO2), the steam cost for capturing up to 1/3 of the site emissions was taken at a cost level corresponding to the average cost of steam up to 1 MJ/kg while the steam cost for the rest of the CO2 emissions captured was taken as the cost assumed for 90% capture from the entire site (20 €/MWh). The petrochemical plant was assumed to follow the same steam cost profile as the refineries. In case of partial capture, the 1/3 of the CO2 at the site with lowest specific capture cost was captured utilizing the available excess heat. It is worth noting that the steam cost model neglects the fact that specific investment costs depend on the capacity needed, and instead follows the assumption that steam cost is included as a utility cost.
Results
Figure 1 gives the marginal abatement cost curve (MACC) for capture for the 28 plants in Table 3 (with 90% capture rate) together with the corresponding curve for transport and storage from these sites. The reason for the number of emission sources (steps in the figure) being much higher than 28 is that several of the sites contain multiple emission sources.
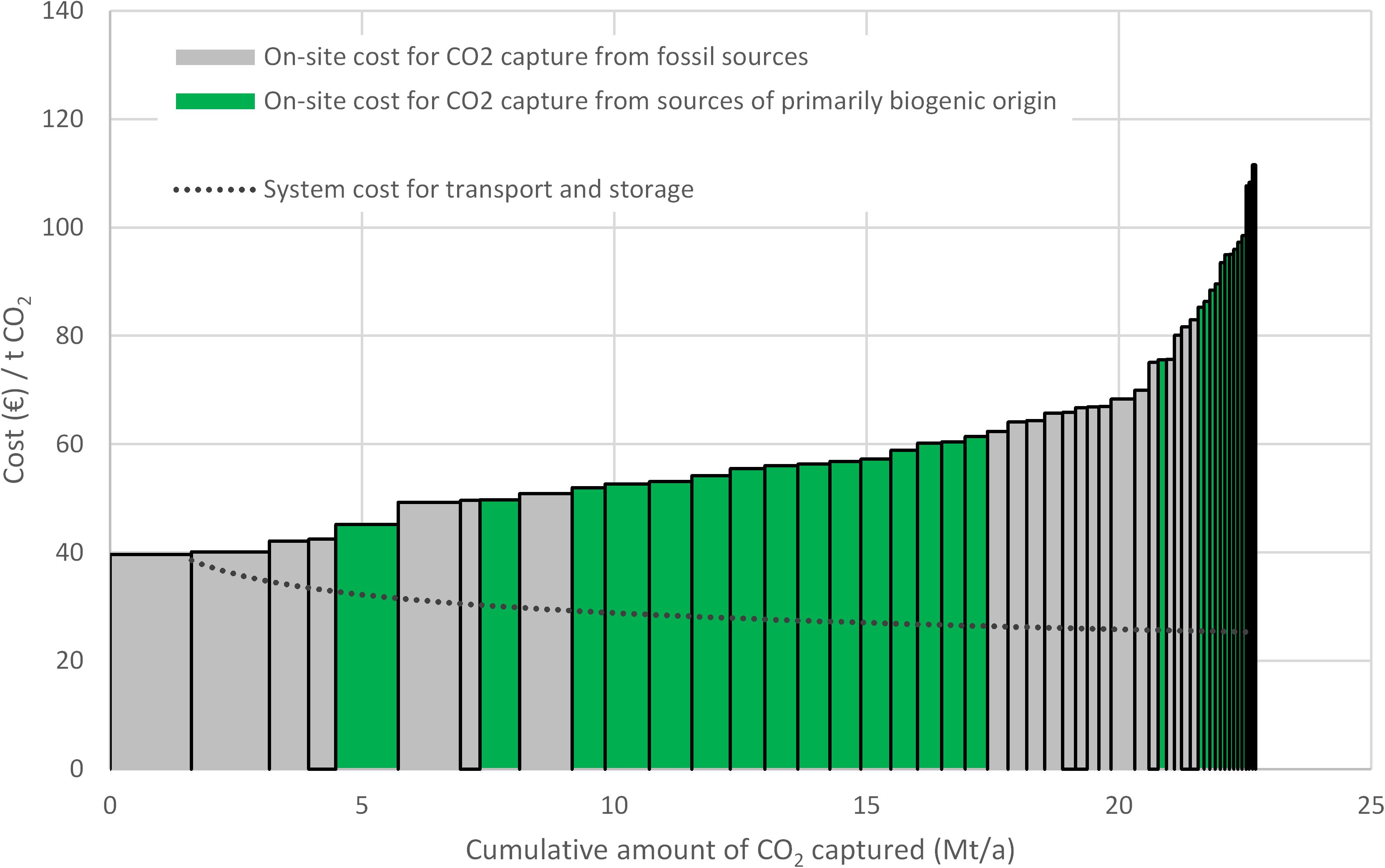
Figure 1. Marginal abatement cost curve for carbon capture and corresponding costs for a transport and storage system (including capital and operating costs) from Swedish emission sources >500 kt CO2/a. It should be noted that the cost for ship transport and storage at a specific point of the curve is not directly addable to the capture cost for any specific emission source – as the transport and storage cost for one plant will depend on the volumes of CO2 handled by the entire system.
Applying capture to the 28 industrial units investigated in this work corresponds to a reduced emission of around 23 Mt CO2/a, which is more than 50% of Swedish total CO2 emissions (from all sectors). Another way to see it is that since the Swedish forestry management currently gives an increase in the carbon stock in the forests, Sweden’s 20 Mt of fossil fuel emissions are more than offset by applying capture on the 28 plants. From Figure 1 it can be seen that the cost of applying CO2 capture, transport and storage (adding the two curves) to the 28 industrial units is ranging from around 80–135 €/t CO2. Yet, due to that a transport infrastructure consisting of hubs and ship transport can be organized in different ways – during a ramp up of CCS – adding the curves in this way will only give an approximate cost at a certain amount of CO2 captured (abscissa value). The details of the capture costs are presented in Table 5.
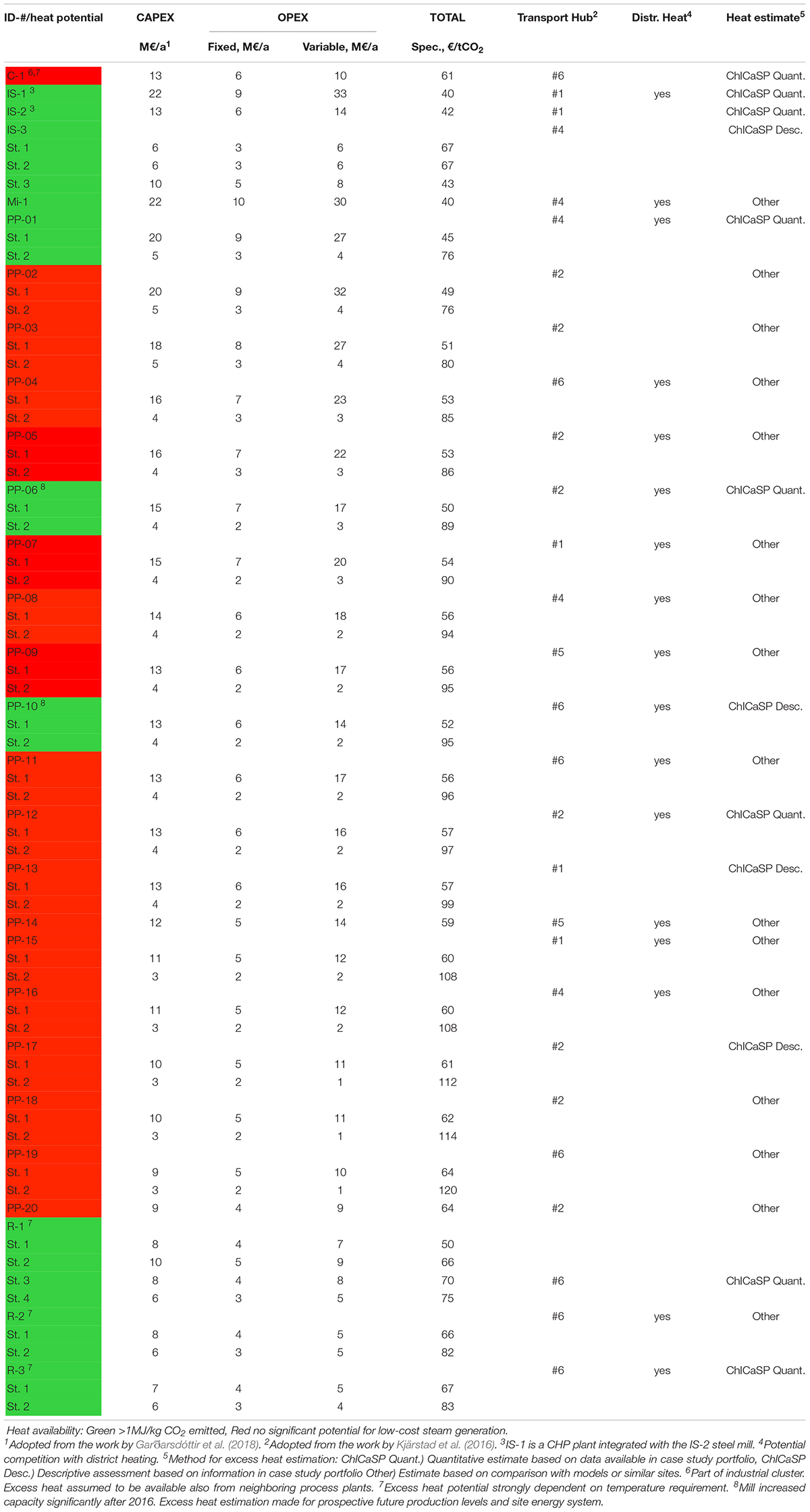
Table 5. Mapping of potential for implementing carbon capture and storage at Swedish emission sources >500 kt/a.
The difference in capture cost of 40–110 €/t CO2 is considerable, although not surprising given the heterogeneity of the emission sources. Low-cost sources typically have high CO2 concentrations, large volume flows, and availability of excess heat and are found, e.g., in the iron and steel and cement industry (such as IS-1, IS-2 and Mi-1 in Table 5). The sources with highest cost correspond to low-volume sources for which no excess heat is available for capture. In this study, these are mainly the lime kilns in the pulp and paper mills, which stand for only a minor share of total site emissions and therefore suffer from poor economy of scale. As can be seen, a considerable part of the total emissions captured can be captured at capture costs below 70 €/t CO2. It should be noted that 15 Mt out of the 23 Mt CO2 captured are of biogenic origin.
As shown in Figure 1, the transport and storage costs range from around 40 €/t CO2 for a small system to around 25 €/t CO2 for a large system. These cost estimates are based on the assumptions described in section “Materials and Methods.” For further clarification, it should be noted that the cost for ship transport and storage is not directly addable to the capture cost – as the specific cost for the specific plant will depend on the volumes of CO2 handled by the entire system. The cost for transport and storage should correspond to the volume treated by the system and not the volume of the specific plant. These costs also assume that the sources are implemented in the order presented in the MACC.
Figure 2 illustrates the impact of excess heat utilization on the capture cost for the emission sources. The consideration of excess heat availability (black dotted line) in the cost estimations yields only moderate cost reductions for total site carbon capture (red dashed line) The reason for this is that it is not possible to power 90% capture for the total site emissions by excess heat alone, but an investment in new steam generation capability to cover the remaining heat demand is required and this steam will come at full-cost. This cost assessment considers 1 MJ of excess heat per kg of CO2 emitted for all plants with excess heat even if for some sites, significantly more heat could be available. The fact that excess heat is not capable of powering 90% capture of the site emissions is, however, true for all sites considered.
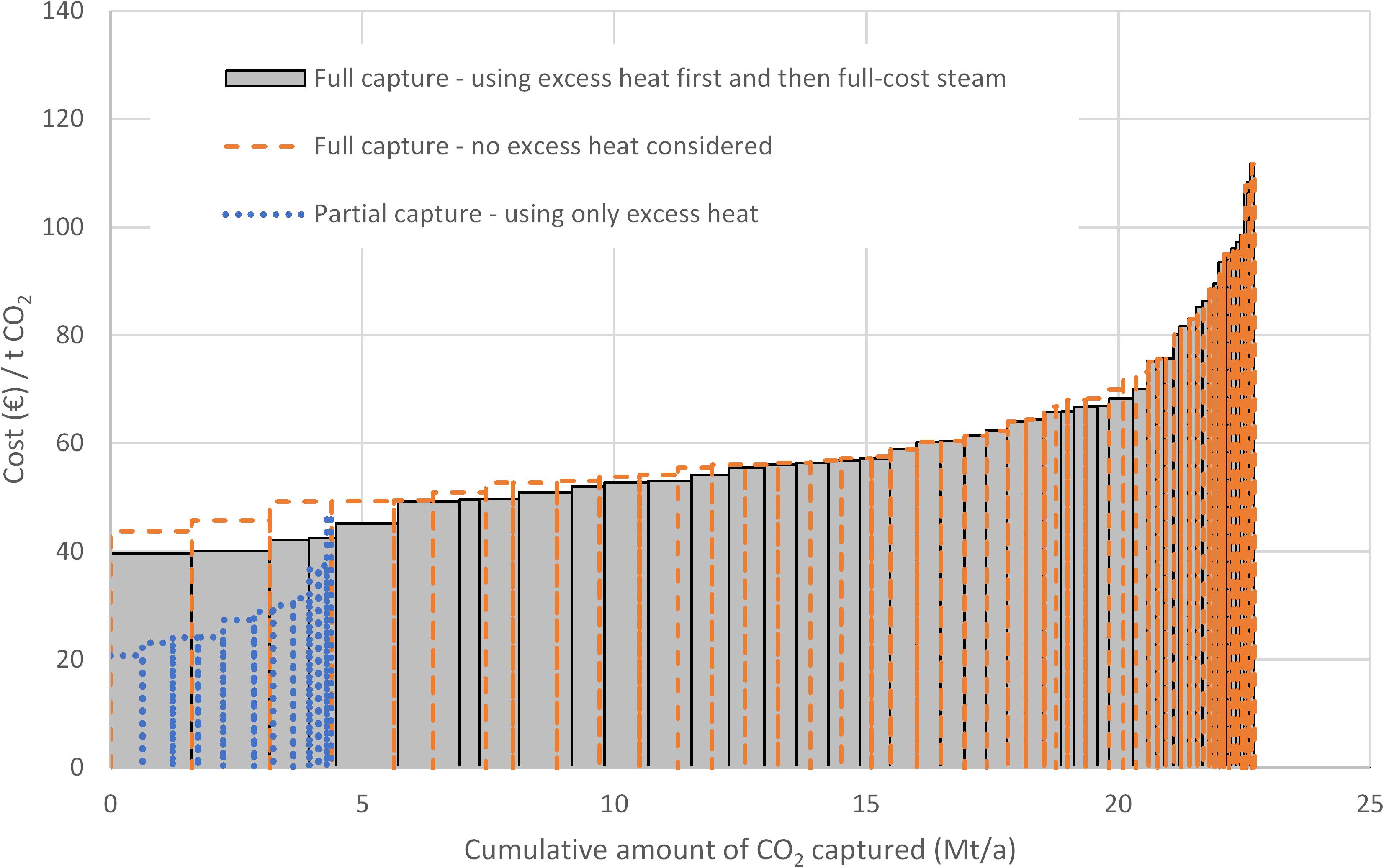
Figure 2. Effect of excess heat on capture costs for Swedish emission sources >500 kt CO2/a. The black dotted line is the same as in Figure 1. The red dashed line represents 90% capture of total site emissions using only full-cost steam. The blue line represents partial capture of the CO2 that can be captured by means of 1 MJ of excess heat per kg CO2 emitted at a given site.
The effect on the capture cost by being able to fully exclude new steam generation capacity is illustrated by the cost for partial capture, which is the amount of CO2 possible to capture by using excess heat (Biermann et al., 2018). This allows for more significant capture cost reductions, as also shown in Figure 2 (see blue line). To derive the results shown in Figure 2, capture was considered only for the sites estimated to have more than 1 MJ of excess heat available per kg of CO2 emitted. This level of excess heat availability was used to determine the amount of CO2 captured for these sites also if more excess heat may be available. Note that industry-specific, and not site-specific, costs of excess heat were considered. The avoidance potential is naturally reduced by only considering excess heat-driven carbon capture, resulting in about 4.5 Mt/year captured (blue solid curve in Figure 2) at capture costs below 30 €/t CO2 as can be seen from the solid blue curve in Figure 2. Partial capture is to be considered as an early mover option that may develop over time or to be combined with other low-carbon technologies. It should be noted that the total system costs might be increased if later deciding to capture the remaining emissions.
Discussion
For the refineries and the petrochemical cluster in Stenungsund, the potential of excess heat utilization was found to be heavily temperature dependent. For example, considering process streams that are currently cooled in air or water coolers in Stenungsund, about 10 MW of heat is available >130°C (used in this work), while 20 MW and 60 MW is available at temperatures >110°C and >95°C, respectively. Thus, at >130°C, Stenungsund is not deemed to have potential for low-cost steam generation above 1 MJ per kg of CO2 emitted. However, at >110°C or >95°C there is a potential. For these types of industrial processes, new solvents that allows for lower regeneration temperatures could significantly increase the potential for excess heat-driven carbon capture.
Utilization of excess heat for carbon capture competes with other heat utilization. In particular, in Sweden today, heat is often delivered to district heating networks. However, it should be noted that CCS and district heating does not necessarily compete about heat from the same temperature levels. District heating generation is non-phase changing and can be supplied by low-temperature sensible heat while the reboiler of the capture process requires heat at constant temperature for evaporation. Consequently, heat may still remain available for district heating after the full potential for excess heat-driven carbon capture has been exploited. A more direct competition for the heat is observed between carbon capture and power generation in low-pressure steam turbines. In this aspect, the development of the decarbonization of the electricity market is important to consider in the decision between using excess heat for electricity generation or for carbon capture. In a decarbonized electricity system, more emissions are avoided by using the heat for the capture process.
In this study, we considered site-specific conditions such as geographic location, characteristics of individual emission sources and excess heat availability. However, the effect of other criteria such as space availability at the industrial sites, and seasonal variations in heat availability and/or emissions remain to be investigated. In regions with water scarcity, this may be a critical factor to consider [see e.g., (Merschmann et al., 2013)], but this is not critical in the Swedish context.
Furthermore, the impact of partial capture on CO2 transportation costs have not been investigated in detail in this work. It was assumed that the entire cost of a transport hub was taken as soon as the first emission source was connected to that hub. This results in high specific investment costs for CO2 transport if only low volumes of CO2 (e.g., few sources, partial capture) are transported to storage. This assumption corresponds well with the fact that transportation costs are considerably higher for partial CO2 capture due to poor economy of scale of transport infrastructure (particularly from emission sources to transport hubs).
The transformation required in the industrial sector for reaching not only required emission reductions, but also energy efficiency and renewable energy targets, is likely to involve major changes in the existing industrial processes and its associated infrastructure including the close down of some plants. Besides these changes, new products, processes and technologies can be expected to emerge. This includes, for example, the integration of new biobased processes in (petro) chemical process plants (causing a shift from fossil to more biogenic sources of CO2), improvements in energy efficiency (reducing the amount of excess heat), and process electrification (reducing or eliminating process CO2 emission as well as affecting excess heat availability). The analysis in this study does not provide a picture of the costs of carbon capture and storage to the future zero-emitting industry but to the present industry. This picture is to serve as an indication of potential cost levels, and how these are affected by various site-specific conditions, for the starting point rather than for the end-game. The results show that to achieve cost efficient carbon capture CCS should be considered in the transformation of the industrial sector. Furthermore, policy instruments that are efficiently strong to allow for CCS are crucial for its implementation; sufficiently high costs of emission allowances within the EU-ETS system for the fossil-fuel based emissions and that policy instruments (EU-ETS or other instrument) need to recognize negative emissions so as to allow for capture and storage of biogenic emissions.
Conclusion
This work estimates the total costs for amine-based CO2 capture at all (28) Swedish industrial plants that emits 500 kt CO2 or more per year. The costs and potential captured emissions are presented in the form of a marginal abatement cost curve (MACC) for industrial post-combustion capture in Sweden. The work maps the plants’ energy systems and estimates the cost of steam required for carbon capture at each specific site. The mapping considers the potential for low-cost steam generation by utilizing excess heat from process cooling, and available capacity in the existing on-site energy system.
The MACC shows that CO2 capture applied to the 28 industrial sites capture CO2 emissions corresponding to more than 50% of Swedish total CO2 emissions (from all sectors). When costs for a transport and storage system is included, this can be achieved at a cost ranging from around 80 €/t CO2 to 135 €/t CO2, depending on emission source. The results show a considerable difference in capture cost between emission sources (40–110 €/t) and that around 2/3 of the emission from the >500 kt/a sources could be captured at a cost of 70 €/t. Partial capture can reduce capture cost and, thus, may serve as a low-cost option for introducing CCS.
Applying the estimations of available excess heat for powering capture in the cost estimations, only yield moderate cost reductions at 90% capture rate. The main reason is that 90% carbon capture is not possible to power without investment in new steam generation capacity in any of the cases considered. The effect on the capture cost by only capturing the amount of CO2 which can be covered by excess process heat – the partial capture cases – yield capture costs in the range of 20–40 €/t. This is, however, only an option for a limited amount of the emissions (around 4.5 Mt/a compared to 23 Mt/a in the 90% capture case).
The case study portfolio and database, ChICaSP, utilized is considered a valuable tool including detailed site data for more than 40% of the plants considered and data for an indirect assessment for the remaining plants utilizing experience and external sources. To further improve the estimation more case studies should be performed along with an assessment of mitigation options besides carbon capture, like electrification and increased biomass utilization.
Data Availability Statement
The datasets for this study can be found in the cited articles as well as in the tables provided.
Author Contributions
FJ and FN conceived the study together and ES provided significant parts of the data processing and evaluation. All authors discussed and interpreted results and jointly wrote the manuscript.
Funding
This work was co-financed by the Swedish Energy Agency (ZEROC project) and the Mistra Carbon Exit Project. This work has benefitted from an earlier review of an abstract to the 14th Int. Conf. on Greenhouse Gas Control.
Conflict of Interest
The authors declare that the research was conducted in the absence of any commercial or financial relationships that could be construed as a potential conflict of interest.
Footnotes
- ^ It should be noted that storage in the Baltic Sea is not a near-term option due to lack of detailed geological data, in spite of significant storage potential.
References
Ali, H., Eldrupa, N. H., Normann, F., Andersson, V., Skagestad, R., Mathisen, A., et al. (2018). Cost estimation of heat recovery networks for utilization of industrial excess heat for carbon dioxide absorption. Int. J. Greenh. Gas Control 74, 219–228. doi: 10.1016/j.ijggc.2018.05.003
Andersson, V., Franck, P. -Å, and Berntsson, T. (2016). Techno-economic analysis of excess heat driven post-combustion CCS at an oil refinery. Int. J. Greenh. Gas Control 45, 130–138. doi: 10.1016/j.ijggc.2015.12.019
Andersson, V., Jilvero, H., Franck, P. -Å, Normann, F., and Berntsson, T. (2014). Efficient utilization of industrial excess heat for post-combustion CO2 capture: an oil refinery sector case study. Energy Procedia 63, 6548–6556. doi: 10.1016/j.egypro.2014.11.691
Berghout, N., Meerman, H., van den Broek, M., and Faaij, A. (2019). Assessing deployment pathways for greenhouse gas emissions reductions in an industrial plant – A case study for a complex oil refinery. Appl. Energy 236, 354–378. doi: 10.1016/j.apenergy.2018.11.074
Biermann, M., Normann, F., Johnsson, F., and Skagestad, R. (2018). Partial Carbon Capture by Absorption Cycle for Reduced Specific Capture Cost. New York, NY: American Chemical Society.
De Pee, A., Pinner, D., Roelofsen, O., Somers, K., Speelman, E., and Witteveen, M. (2018). Decarbonization of Industrial Sectors: the Next Frontier. New York, NY: McKinsey & Company.
Delin, L., Berglin, N., Lundström, A., Samuelsson, Å, Backlund, B., and Sivard, Å (2005). Bleached Market kraft Pulp Mill - FRAM Report No. 9. Stockholm: STFI-Packforsk.
European Environment Agency [EEA] (2016). European Pollutant Release and Transfer Register (E-PRTR). Copenhagen: European Environment Agency. Available online at: http://prtr.eea.europa.eu/#/facilitylevels (accessed September 30, 2018).
Garðarsdóttir, S. Ó, de Lena, E., Romano, M., Roussanaly, S., Voldslund, M., Pérez-Calvo, J. F., et al. (2019). Comparison of technologies for CO2 Capture from cement production—Part 2: cost analysis. Energies 12:542. doi: 10.3390/en12030542
Garðarsdóttir, S. Ó, Normann, F., Skagestad, R., and Johnsson, F. (2018). Investment costs and CO2 reduction potential of carbon capture from industrial plants – A Swedish case study. Int. J. Greenh. Gas Control 76, 111–124. doi: 10.1016/j.ijggc.2018.06.022
Global CCS Institute, (2019). CO2RE Database. Available: https://CO2re.co/ (accessed January 13, 2020).
Güleç, F., Meredith, W., and Snape, C. E. (2020). Progress in the CO2 capture technologies for fluid catalytic cracking (FCC) Units—A review. Front. Energy Res. 8:62. doi: 10.3389/fenrg.2020.00062
Jakobsen, J., Roussanaly, S., and Anantharaman, R. (2017). A techno-economic case study of CO2 capture, transport and storage chain from a cement plant in Norway. J. Clean. Prod. 144, 523–539. doi: 10.1016/j.jclepro.2016.12.120
Kjärstad, J., Skagestad, R., Eldrup, N. H., and Johnsson, F. (2016). Ship transport—A low cost and low risk CO2 transport option in the Nordic countries. Int. J. Greenh. Gas Control 54, 168–184. doi: 10.1016/j.ijggc.2016.08.024
Kuramochi, T., Ramírez, A., Turkenburg, W., and Faaij, A. (2012). Comparative assessment of CO2 capture technologies for carbon-intensive industrial processes. Prog. Energy Combust. Sci. 38, 87–112. doi: 10.1016/j.pecs.2011.05.001
Leeson, D., Mac Dowell, N., Shah, N., Petit, C., and Fennell, P. S. (2017). A Techno-economic analysis and systematic review of carbon capture and storage (CCS) applied to the iron and steel, cement, oil refining and pulp and paper industries, as well as other high purity sources. Int. J. Greenh. Gas Control 61, 71–84. doi: 10.1016/j.ijggc.2017.03.020
Mandova, H., Patrizio, P., Leduc, S., Kjärstad, J., Wang, C., Wetterlund, E., et al. (2019). Achieving carbon-neutral iron and steelmaking in Europe through the deployment of bioenergy with carbon capture and storage. J. Clean. Prod. 218, 118–129. May., doi: 10.1016/j.jclepro.2019.01.247
Mathisen, A., Skagestad, R., Eldrup, N. H., and Haugen, H. A. (2018). “CO2 capture scenarios for a cement plant,” in Proceedings of the 14th International Conference of Greenhouse Gas Control Technologies. Available online at: www.ssrn.com/index.cfm/en/energyrn/ads/05132019ann003/
Merschmann, P. R. C., Vasquez, E., Szklo, A. S., and Schaeffer, R. (2013). Modeling water use demands for thermoelectric power plants with CCS in selected Brazilian water basins. Int. J. Greenh. Gas Control 13, 87–101. doi: 10.1016/j.ijggc.2012.12.019
Naturvårdsverket (Swedish Environmental Protection Agency), (2018). Utsläpp av växthusgaser från industrin (in Swedish - Emissions of greenhouse gas emissions from industry). Available at: http://www.naturvardsverket.se/Sa-mar-miljon/Statistik-A-O/Vaxthusgaser-utslapp-fran-industrin/ (accessed April 16, 2019).
Onarheim, K., Mathisen, A., and Arasto, A. (2015). Barriers and opportunities for application of CCS in Nordic industry—A sectorial approach. Int. J. Greenh. Gas Control 36, 93–105. doi: 10.1016/j.ijggc.2015.02.009
Onarheim, K., Santos, S., Kangas, P., and Hankalin, V. (2017). Performance and cost of CCS in the pulp and paper industry part 2: economic feasibility of amine-based post-combustion CO2 capture. Int. J. Greenh. Gas Control 66, 60–75. doi: 10.1016/j.ijggc.2017.09.010
Rochedo, P. R. R., Costa, I. V. L., Império, M., Hoffmann, B. S., Merschmann, P. R. C., Oliveira, C. C. N., et al. (2016). Carbon capture potential and costs in Brazil. J. Clean. Prod. 131, 280–295. doi: 10.1016/j.jclepro.2016.05.033
Rogelj, J., Shindell, D., Jiang, K., Fifita, S., Forster, P., Ginzburg, V., et al. (2018). “Mitigation pathways compatible with 1.5°Cin the context of sustainable development,” in Global Warming of 1.5°C. An IPCC Special Report on the Impacts of Global Warming of 1.5°C Above Pre-Industrial Levels and Related Global Greenhouse Gas Emission Pathways, in the Context of Strengthening the Global Response to the Threat of Climate Change, eds D. Roberts, J. Skea, P. R. Shukla, A. Pirani, and W. Moufouma-Okia, C. Péan, et al. (London: IntechOpen).
Skagestad, R., Gargarsdóttir, S. Ó, Normann, F., Anheden, M., and Wolf, J. (2018). “A case study of partial capture of CO2 from a pulp mill – the CO2 capture cost,” in Proceedings of the 14th International Conference of Greenhouse Gas Control Technologies. Available online at: www.ssrn.com/index.cfm/en/energyrn/ads/05132019ann003/
Skogsindustrierna (2016). Skogsindustriernas Miljödatabas Forest Industries Environmental Database. Stockholm: Swedish Forest Industries Federation. Available online at: http://miljodatabas.skogsindustrierna.org/ (accessed August 31, 2018).
Sundqvist, M., Biermann, M., Normann, F., Larsson, M., and Nilsson, L. (2018). Evaluation of low and high level integration options for carbon capture at an integrated iron and steel mill. Int. J. Greenh. Gas Control 77, 27–36. doi: 10.1016/j.ijggc.2018.07.008
Svensson, E., Bokinge, P., Harvey, S., and Normann, F. (2019). Chalmers Industrial Case Study Portfolio - Contents, Structure and Example Applications. Göteborg: Chalmers University of Technology.
Swedish Environmental Protection Agency [SEPA] (2016a). Statistik och Uppföljning. Stockholm: Swedish Environmental Protection Agency. Available online at: https://www.naturvardsverket.se/Miljoarbetei-samhallet/Miljoarbete-i-Sverige/Uppdelat-efter-omrade/Utslappshandel/Resultat-ochuppfoljning (accessed March 31, 2018).
Swedish Environmental Protection Agency [SEPA] (2016b). Swedish Pollutant Release and Transfer Register (PRTR). Stockholm: Swedish Environmental Protection Agency. Available online at: https://utslappisiffror.naturvardsverket.se/Sok/ (accessed March 31, 2018).
Keywords: CCS, CO2 capture, MACC, industrial, case study
Citation: Johnsson F, Normann F and Svensson E (2020) Marginal Abatement Cost Curve of Industrial CO2 Capture and Storage – A Swedish Case Study. Front. Energy Res. 8:175. doi: 10.3389/fenrg.2020.00175
Received: 21 April 2020; Accepted: 06 July 2020;
Published: 11 August 2020.
Edited by:
Graeme Douglas Puxty, Energy, Commonwealth Scientific and Industrial Research Organisation (CSIRO), AustraliaReviewed by:
Paul Hubert Feron, Commonwealth Scientific and Industrial Research Organisation (CSIRO), AustraliaAlexandre Szklo, Federal University of Rio de Janeiro, Brazil
Copyright © 2020 Johnsson, Normann and Svensson. This is an open-access article distributed under the terms of the Creative Commons Attribution License (CC BY). The use, distribution or reproduction in other forums is permitted, provided the original author(s) and the copyright owner(s) are credited and that the original publication in this journal is cited, in accordance with accepted academic practice. No use, distribution or reproduction is permitted which does not comply with these terms.
*Correspondence: Filip Johnsson, ZmlsaXAuam9obnNzb25AY2hhbG1lcnMuc2U=